Что представляют собой анодные блоки для алюминиевых электролизеров. Из каких материалов они изготавливаются. Как происходит процесс производства анодных блоков. Какие требования предъявляются к их свойствам. Как анодные блоки используются при электролизе алюминия.Далее основной текст статьи:
Что такое анодные блоки для алюминиевых электролизеров
Анодные блоки являются важнейшим компонентом алюминиевых электролизеров с предварительно обожженными анодами. Они представляют собой крупные угольные блоки, которые служат для подвода электрического тока в процессе электролитического получения алюминия.
Основные характеристики анодных блоков:
- Изготавливаются из нефтяного кокса и каменноугольного пека
- Имеют форму прямоугольных блоков
- Подвергаются предварительному обжигу при высокой температуре
- Обладают высокой электропроводностью
- Медленно расходуются в процессе электролиза
Анодные блоки крепятся к токоподводящим штангам и погружаются в расплав криолит-глиноземного электролита в электролизной ванне. В процессе электролиза они постепенно расходуются, участвуя в анодной реакции окисления.
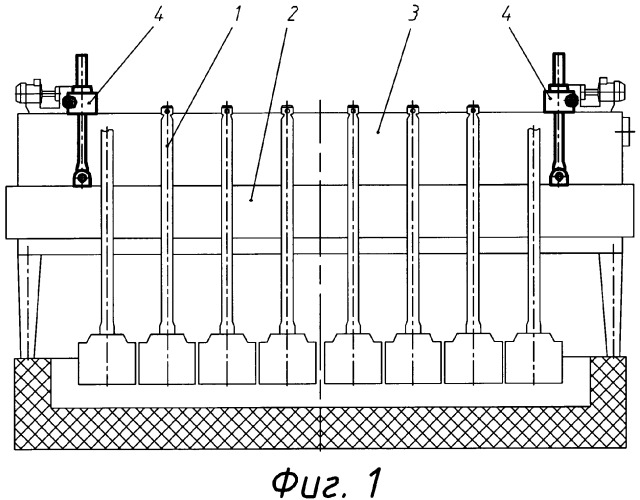
Материалы для производства анодных блоков
Основными материалами для изготовления анодных блоков являются:
- Нефтяной кокс (прокаленный) — 65-75%
- Пековый кокс — 15-20%
- Каменноугольный пек (связующее) — 13-15%
Нефтяной кокс получают в процессе коксования тяжелых нефтяных остатков. Он обладает низкой зольностью и высоким содержанием углерода. Пековый кокс является побочным продуктом коксохимического производства. Каменноугольный пек служит связующим материалом.
Качество исходного сырья во многом определяет свойства готовых анодных блоков. Поэтому к материалам предъявляются строгие требования по химическому составу, зольности, содержанию примесей.
Технология производства анодных блоков
Процесс изготовления анодных блоков включает следующие основные стадии:
- Подготовка сырья (дробление, измельчение, прокаливание)
- Приготовление анодной массы (смешивание наполнителей и связующего)
- Формование заготовок (прессование или виброуплотнение)
- Обжиг заготовок (при температуре 1100-1300°C)
- Механическая обработка обожженных блоков
На стадии смешивания очень важно добиться равномерного распределения связующего по всему объему массы. Обжиг придает блокам окончательные физико-механические свойства. При этом происходит коксование связующего и формирование прочной углеродной структуры.

Требования к свойствам анодных блоков
Основные показатели качества анодных блоков для алюминиевых электролизеров:
- Кажущаяся плотность — не менее 1,50-1,55 г/см3
- Удельное электросопротивление — не более 60-65 мкОм·м
- Предел прочности при сжатии — не менее 30-35 МПа
- Зольность — не более 0,5-0,6%
- Реакционная способность по CO2 — не более 12-15 мг/см2·ч
Важное значение имеет также однородность свойств по объему блока. Характеристики должны соответствовать требованиям на протяжении всего срока службы анода в электролизере.
Применение анодных блоков в производстве алюминия
Анодные блоки используются в электролизерах с предварительно обожженными анодами для получения первичного алюминия. Основные функции анодов в процессе электролиза:
- Подвод электрического тока к электролиту
- Участие в анодной реакции окисления
- Выделение анодных газов (в основном CO2)
В современных мощных электролизерах устанавливается от 20 до 40 анодных блоков. По мере расходования аноды периодически заменяются на новые. Срок службы анодного блока составляет 20-30 суток.
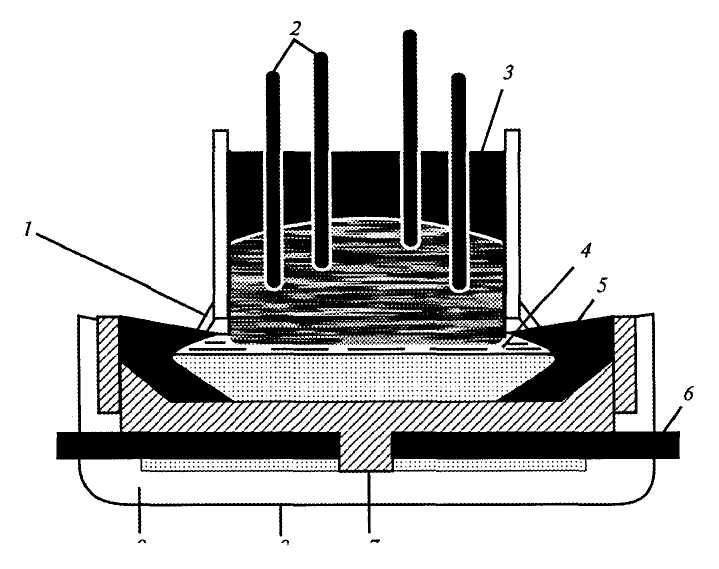
Влияние качества анодов на показатели электролиза
Качество анодных блоков оказывает существенное влияние на технико-экономические показатели производства алюминия:
- Удельный расход электроэнергии
- Выход по току
- Качество получаемого металла
- Срок службы электролизера
Применение анодов с улучшенными характеристиками позволяет снизить расход электроэнергии на 1-2%, увеличить выход по току на 0,5-1%, повысить качество алюминия.
Перспективные направления совершенствования анодов
Основные направления работ по улучшению свойств анодных блоков:
- Повышение чистоты и качества исходного сырья
- Оптимизация гранулометрического состава наполнителей
- Совершенствование технологии смешивания и формования
- Применение новых видов связующих материалов
- Модифицирование структуры углерода добавками
Перспективным является создание крупногабаритных анодов повышенной плотности с улучшенными эксплуатационными характеристиками. Это позволит увеличить единичную мощность электролизеров и снизить себестоимость производства алюминия.
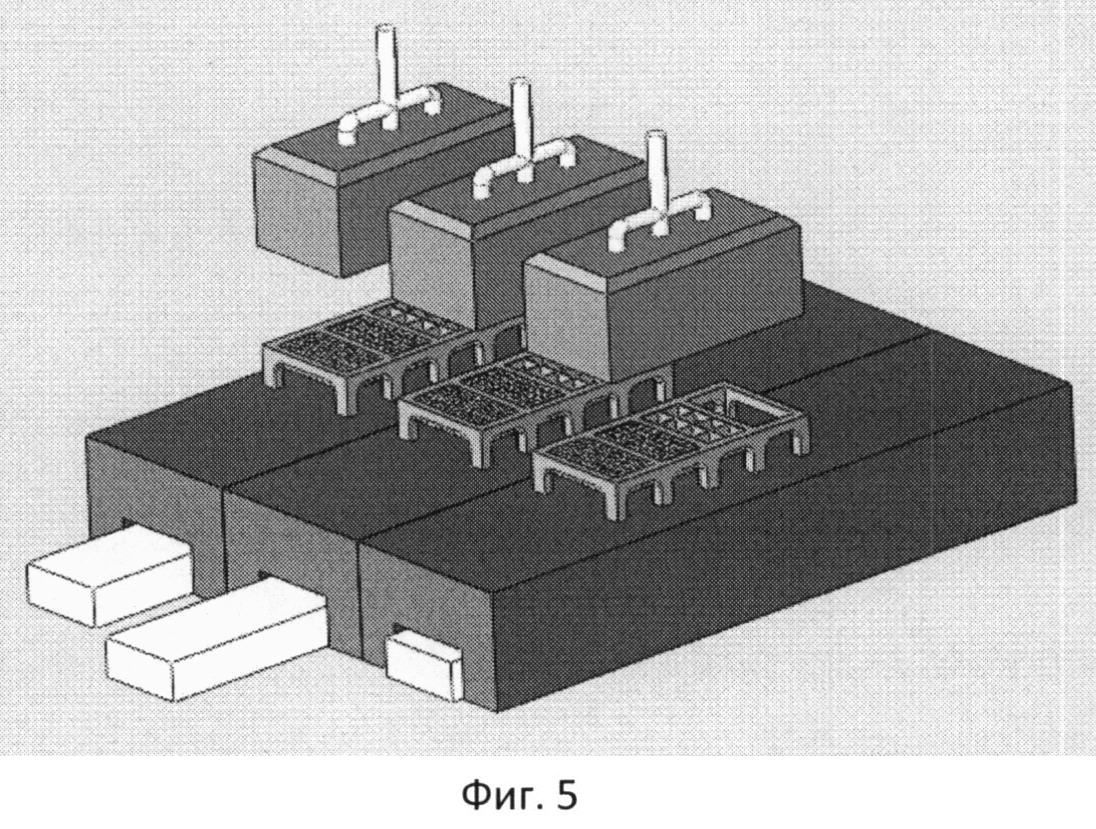
Анодный блок — Большая Энциклопедия Нефти и Газа, статья, страница 2
Cтраница 2
Анодный блок изготовляется из меди и представляет собой массивный цилиндр, в котором по радиусу располагаются полости с зазорами во внутренней части, образующие резонаторы. [16]
Анодный блок состоит из графитовых плит толщиной 50 мм и шириною 250 мм, монтируемых на стальном анодном днище, которое одновременно служит для подвода тока к анодным плитам с помощью специальных контактных устройств без применения свинца. [17]
Показатели работы электролизеров Хукер с графитовыми анодами.| Зависимость выхода по току от плотности тока на электролизерах. [18] |
Анодный блок имеет форму неглубокой чаши. Аноды из графитовых пластин устанавливают вертикально в анодной чаше рядами, высота анодов около 750 мм. Подвод тока к, анодам осуществляется с помощью медных шин, вставляемых в виде решетки в нижнюю часть анодной чаши в пространстве между головками графитовых анодов.
Анодные блоки состоят каждый из пяти графитовых плит, залитых свинцом в пазах медной решетки, установленной на металлическом днище. Центральный циркуляционный проход между электродными элементами отсутствует. Предполагается, что циркуляция электролита осуществляется за счет подъема его вместе с пузырьками хлора вдоль вертикально расположенных анодов и опускания освобожденного от газовых пузырьков анолита через полости в анодных пространствах у боковых продольных стенок корпуса электролизера. [20]
Конструкция лампы бегущей волны с замедляющей системой в виде. [21] |
Анодный блок, имеющий сечение, показанное на рис. 13 — 54 е, изготавливается из медного цилиндра, на внутренней стороне которого выбираются пазы.
[22]
Анодные блоки изготавливают из малозольных и малосернистых коксов. [23]
Схема электролизера для получения тройного сплава. [24] |
Анодные блоки 2 квадратного сечения подвешивают на стальных штангах 6 в два ряда над зеркалом расплавленного свинца. Ток к анодам от анодных шин 7 подводится по стальным штангам-подвескам, которые нижней частью заделываются в тело анода и заливаются чугуном. [25]
Анодный блок может даже расколоться, что приведет к расстройству технологического режима электролиза. Для предотвращения нарушений технологии аноды должны быть достаточно механически прочными и термически стойкими. [26]
Анодные блоки, как указывалось выше, независимо от вида прессования прессуются в горячем виде. Поэтому первыми физическими процессами, имеющими место при нагревании зеленого блока в процессе обжига, являются термическое расширение материала и расширение его за счет снятия остаточной деформации, образовавшейся при прессовании. Однако величина этих двух видов расширения незначительна и не оказывает заметного влияния на конечные свойства обожженной продукции.
[27]
Новый анодный блок устанавливают на место извлеченного таким образом, чтобы его нижняя поверхность находилась на одном уровне с нижней поверхностью рядом стоящих анодов. Перед заменой анодный блок очищают от утепляющей глиноземной засыпки и освобождают от застывшей вокруг него корки электролита. После замены новый блок присыпают глиноземом для предохранения боковых его поверхностей от окисления и сокращения их теплоотдающей способности. [28]
Устройство многорезонаторного магнетрона. [29] |
Анодный блок многорезонаторного магнетрона ( рис. 5 — 1) представляет собой невысокий медный цилиндр с рядом отверстий, параллельных оси цилиндра. Вместе со щелями, соединяющими эти отверстия с центральным, они образуют объемные резонаторы. Таким образом, анодный блок представляет собой систему связанных контуров.
[30]
Страницы: 1 2 3 4 5
Анодный блок алюминиевого электролизера
Изобретение относится к анодному блоку алюминиевых электролизеров. Анодный блок алюминиевого электролизера выполнен с расположенными на его нижней рабочей поверхности каналами, для этого в подошве анода размещены изготовленные из алюминиевого прутка алюминиевые решетки, расположенные под наклоном таким образом, что верхний торец нижележащей решетки плотно контактирует с нижним торцом вышележащей решетки, которые при нагреве до рабочей температуры расплавляются с образованием каналов для удаления анодных газов. Обеспечивается сохранение падения напряжения в электролите, связанного с ускоренным отводом газа из-под анода, и обеспечение требуемой циркуляции электролита в районах подачи глинозема. 4 з.п. ф-лы, 2 ил.
Изобретение относится к цветной металлургии, в частности к электролитическому получению алюминия, а именно к анодному устройству алюминиевых электролизеров.
Известен Обожженный анод алюминиевого электролизера (RU 2239005 от 25.11.2002, опубл. 27.10.2004 Бюл. №30.
Техническим результатом изобретения является сохранение падения напряжения в электролите, связанного с ускоренным отводом газа из-под анода, и обеспечение требуемой циркуляции электролита в районах подачи глинозема. Технический результат достигается тем, что обожженный анод содержит анодный блок с одним или несколькими вертикальными каналами на его нижней рабочей поверхности. Вертикальные каналы выполнены с дифференцированным углублением по протяженности в виде участка с фиксированным равномерным углублением, равным 0,25-0,30 высоты блока, или с фиксированным углублением, равным 0,25-0,30 высоты блока и выполненным с наклоном до 3°, и сопряженного с ним участка с постепенным углублением до 0,75 высоты блока. Место сопряжения участков расположено в пределах 0,45-0,75 длины блока при расположении каналов вдоль его продольной оси или ширины блока при расположении каналов поперек его продольной оси. При использовании нескольких вертикальных каналов они расположены с шагом 0,35-0,5 от ширины блока при их расположении вдоль его продольной оси или с шагом 0,25-0,33 от длины блока при их расположении поперек его продольной оси.
Несмотря на достоинства известного устройства для изготовления таких анодов требуется сложная технология изготовления.
Известна практика использования предварительно обожженных анодов с углеродными анодными блоками, которые содержат одну или несколько канавок в их нижней части, чтобы способствовать удалению газовых пузырьков и препятствовать их накоплению, что должно привести к решению вышеназванных проблем и снизить расход энергии, как показано в Light Metals 2005 «Energy saving in Hindalco’s Aluminium Smelter», S.C. Tandon & R.N. Prasad. Канавки позволяют сократить среднюю длину свободного пробега газовых пузырьков под анодом для выхода из межэлектродного пространства и, следовательно, уменьшить размер пузырьков, которые образуются под анодом.
Выгода от использования канавок уже изучена и доказана, например, в Light Metals 2007 p. 305-310 «The impact of slots on reduction cell individual anode current variation», Geoff Bearne, Dereck Gadd, Simon Lix или Light Metals 2007 p. 299-304 «Development and deployment of slotted anode technology at Alcoa», Xiangwen et al.
Также из нижеследующих документов известно:
— WO 2006/137739 использование меньших канавок (порядка от 2 до 8 мм), чем используемые обычно (порядка от 8 до 20 мм), чтобы оптимизировать полезную углеродную массу и поверхность обмена;
— US 7179353 использование анодного блока, имеющего канавки, выходящие лишь на одну боковую сторону анодного блока и, в частности, к центру электролизера, чтобы улучшить растворение глинозема.
Хорошо известно ограничение в использовании этих канавок вследствие того, что глубина канавок относительно нижней поверхности анодных блоков ограничена, чтобы не нарушить механическую и физическую целостность углеродных анодных блоков. При этом углеродные анодные блоки постепенно расходуются в ходе реакции электролиза на высоту, превышающую глубину канавок, так что продолжительность существования канавок в аноде меньше срока службы анода. Следовательно, в течение некоторого времени на протяжении срока службы анодов нижняя часть анодных блоков уже не имеет никакой канавки. В таком случае становятся заметными проблемы, упомянутые выше для анодов без канавок.
Проблема отвода анодных газов и, в частности, диоксида углерода (углекислый газ), которые, естественно, накапливаются в форме газовых пузырьков под нижней стороной анода, обычно, по существу, плоской и горизонтальной, что влияет на общую стабильность электролизера заявлена ив RU №2559381 от 21.07.2010, опубл. 10.08.2015 Бюл. №22,. Данный аналог можно взять за прототип.
Задачей изобретения является разработать обожженный анод алюминиевого электролизера, конструкция которого обеспечивала бы возможность уменьшения толщины газового слоя у нижней рабочей поверхности блока, равномерный и ускоренный сход газа с рабочей поверхности и возможность регулирования потоков сходящего газа практически в течение всего периода эксплуатации анода при сохранении достаточной механической прочности блока, что позволит сохранить снижение падения напряжения в электролите, связанного с ускоренным отводом газа из-под анода, и обеспечить требуемую циркуляцию электролита в районах подачи глинозема в период работы анода.
Достигается это введением в анод электропроводящего материала с сопротивлением, меньшим сопротивления угольной части анода, при этом электропроводящим материалом являются решетки, изготовленные из алюминиевых прутков диаметром 3…10 мм, которые наклонно размещают в аноде под углом 4…8° по отношению к горизонтальной поверхности таким образом, что верхний торец расположенный нижележащей решетки плотно контактирует с нижним торцом вышележащей решетки, при этом, верхний торец самой верхней решетки размещен от верхней кромки анода на расстоянии равном 0,20…0,25 высоты Н анода, нижний торец нижней решетки размещен на расстоянии от подошвы анода, равном 0,03…0,06 высоты Н анода, боковые и торцевые стороны решеток спрятаны вглубь анода на расстояние от боковых и торцевых стенок анода, равном 0,03…0,06 высоты Н анода, а газоотводящие канавки на подошве анода формируются в результате плавления введенных в анод алюминиевых решеток.
Целесообразность введения в анод электропроводящего материала с сопротивлением, меньшим сопротивления угольной части анода обеспечивает прохождение электрического тока через анод с более низким падением в нем напряжения.
Целесообразность использования для этих целей решеток размером ячейки от 50×50 до 100×100 мм, изготовленных из алюминиевых прутков диаметром 3…10 мм, обосновывается следующим. При плавлении алюминиевых прутков на подошве анода образуются канавки шириной от 3 до 10 мм и высотой от 2 до 5 мм, по которым анодные газы, образующиеся в результате окисления анода, движутся к боковым и торцевым сторонам анода, увеличивая циркуляцию электролита по всему его периметру. При этом под каждой ячейкой размером от 50×50 до 100×100 мм, в зависимости от общего габарита анода, образуется от 0,1 до 3,0% общего объема образующихся анодных газов, которые практически сразу же отводятся по газоотводящим канавкам в межанодное пространство.
Наличие на подошве анода канавок шириной до 10 мм и высотой до 5 мм увеличивает полезную площадь анода, контактирующую с электролитом, в среднем на 3…5%, что на такую же величину уменьшает плотность тока в аноде и, соответственно сопротивление последнего.
Размещение решеток под углом 4…8° по отношению к горизонтальной поверхности обеспечивает постепенное плавление прутков, по мере сгорания анода, а также исключает деформацию решеток при формовке анода.
Плотный электрический контакт между торцами смежных решеток обеспечивает минимальное падение напряжения при прохождении через них электрического тока.
Размещение верхнего торца самой верхней решетки на расстоянии от верхней кромки анода, равном 0,20…0,25 высоты Н анода обусловлено необходимостью исключения попадания в анодный огарок металлического алюминия, из которого изготовлены решетки. Как привило, высота анодного огарка составляет 0,1…0,2 первоначальной высоты анода и заявляемое ограничение высоты размещения обеспечивает полный переход расплавленного алюминия из анода в электролит и далее в слой прикатодного жидкого алюминия.
Размещение нижнего торца нижней решетки на расстоянии от подошвы анода, равном 0,03…0,06 высоты Н анода обусловлено тем, что в период обжига анода при температуре 1200…1400°С и выше исключается уход расплавленного алюминия из тела анода.
Удаление боковых и торцевых сторон решеток вглубь анода на расстояние от боковых и торцевых сторон анода, равное 0,03…0,06 высоты Н анода обосновывается следующим. Как правило, высота эксплуатируемых обожженных анодов находится в диапазоне 600…900 мм. Следовательно, в новом аноде боковые и торцевые стороны решеток защищены слоем угольного анода толщиной 3…5 мм. После установки анода в электролизер и его нагрева до рабочей температуры защитный слой окисляется, открывая таким образом газоотводящие канавки, образующиеся на подошве анода после плавления решетки.
Заявляемое устройство поясняется графически. На фиг. 1 изображен разрез А-А обожженного анода; на фиг. 2 — разрез Б-Б фиг. 1 — расположение сетки в аноде до его установки в электролизер; на фиг. 3 расположение газоотводящих канавок на подошве эксплуатируемого анода, где: 1 — обожженный анод; 2 — алюминиевые решетки; 3 — газоотводящие каналы на подошве анода; 4 — подпорные алюминиевые прутки.
Работа устройства осуществляется следующим образом.
На дно пресс-формы (на фиг. не показана), где происходит формовка анода 1, засыпается слой анодной массы высотой, равной 0,06…0,10 высоты Н анода. Далее на этот слой устанавливаются алюминиевые решетки 2, скрепленные между собой в торцах по принципу «елочка». Такое скрепление решеток обеспечивает возможность регулирования угла их наклона относительно горизонтальной поверхности. Фиксация решеток в пресс-форме под требуемым углом осуществляется с помощью вертикально устанавливаемых алюминиевых прутков 3. После фиксации решеток и проверки зазоров между ними и торцевыми и боковыми сторонами пресс-формы последняя заполняется анодной массой. После заполнения, анодная масса прессуется, ее насыпной объем уменьшается примерно в 2 раза. Таким образом, получается, что нижний торец нижней решетки оказывается защищенным слоем угольного анода толщиной 3…5 мм, который при обжиге анода исключает риск утечки из него расплавленного алюминия. При этом решетки вместе с прессуемой анодной массой движутся вниз, уменьшая свой угол наклона по отношению к горизонтальной поверхности от 8…16° до 4…8°. Деформируемые при этом подпорные алюминиевые прутки после установки анода в электролизер служат дополнительными проводниками тока.
После установки анода в электролизер и его нагрева до рабочей температуры защитный угольный слой на подошве анода, его боковых и торцевых сторонах окисляется, обнажая таким образом решетку. По мере плавления решетки на подошве анода образуются газоотводящие канавки 4, по которым образующиеся анодные газы удаляются из-под анода.
Техническим результатом изобретения является сохранение падения напряжения в электролите, связанного с ускоренным отводом газа из-под анода, и обеспечение требуемой циркуляции электролита в районах подачи глинозема.
1. Анодный блок алюминиевого электролизера, содержащий нижнюю рабочую поверхность, отличающийся тем, что в его нижней рабочей поверхности размещены изготовленные из прутков алюминиевые решетки, расположенные одна под другой под углом к горизонтальной нижней рабочей поверхности с обеспечением контактирования верхнего торца нижележащей решетки с нижним торцом вышележащей решетки для образования каналов для удаления анодных газов при расплавлении прутков при нагреве анода до рабочей температуры.
2. Анодный блок по п. 1, отличающийся тем, что алюминиевые решетки выполнены с размером ячейки от 50×50 до 100×100 мм и изготовлены из прутков диаметром 3…10 мм.
3. Анодный блок по п. 1, отличающийся тем, что верхний торец решетки размещен от верхней кромки анода на расстоянии равном 0,20…0,25 высоты Н анода.
4. Анодный блок по п. 1, отличающийся тем, что нижний торец решетки размещен на расстоянии от подошвы анода, равном 0,03…0,06 высоты Н анода.
5. Анодный блок по п. 1, отличающийся тем, что боковые и торцевые стороны решеток заглублены в анод на расстояние от боковых и торцевых стенок анода, равное 0,03…0,06 высоты Н анода.
Что такое анодный угольный блок?
1. Что такое анодный угольный блок?
Анодный угольный блок относится к угольному блоку, изготовленному из нефтяного кокса и пекового кокса в качестве заполнителя и каменноугольного пека в качестве связующего, который используется в качестве анодного материала для предварительно обожженного алюминиевого электролизера. Этот тип углеродного блока был обожжен и имеет стабильную геометрию. Поэтому его также называют предварительно обожженным анодным углеродным блоком, а также угольным анодом для электролиза алюминия.
2. Введение анодного углеродного блока
Углеродные и графитовые материалы представляют собой неметаллические твердые материалы, в основном состоящие из углеродных элементов, в которых углеродные материалы в основном состоят из неграфитовых углеродных материалов, а графитовые материалы представляют собой материалы. в основном состоит из графитового углерода. Для удобства иногда углеродные и графитовые материалы вместе называются углеродными материалами.
Углеродные изделия можно разделить на графитовые электроды, угольные блоки, графитовые аноды, угольные электроды, пасты, электроуглерод, углеродное волокно, специальные графиты, графитовые теплообменники и др. По допустимой плотности тока графитовые электроды можно разделить на графитовые электроды обычной мощности, электроды высокой мощности и электроды сверхвысокой мощности. В зависимости от использования углеродные блоки можно разделить на угольные блоки для доменной печи, алюминиевые углеродные блоки, блоки для электропечей и т. д. В зависимости от глубины обработки углеродные продукты можно разделить на углеродные продукты, графитовые продукты, углеродные волокна и графит. волокна и т. д. В зависимости от сырья и производственных процессов углеродные продукты можно разделить на графитовые продукты, углеродные продукты, углеродные волокна, специальные графитовые продукты и т. д. В зависимости от содержания золы углеродные продукты можно разделить на продукты с большим содержанием золы. и продукты с меньшей зольностью (с зольностью менее 1%).
3. Стоимость анодного угольного блока
Электролизер делится на самообжигающий и предварительно обжигающий. Соответственно, угольный анод, используемый в самообжигающемся баке, называется анодной пастой. Угольный анод, используемый в резервуаре для предварительного обжига, называется анодным угольным блоком. Цена анодного углеродного блока относительно высока, потому что его нужно сначала обжечь, а процессов больше.
Новости
- Новости компании
- Выставки и события
- Новости отрасли
Продукция
- Стальной продукт
- Стальная плита
- Стальная заготовка
- Стальной Блум
- Горячекатаная сталь
- Горячекатаная стальная катушка
- Горячекатаный стальной лист
- Горячекатаный стальной лист
- Горячекатаная полоса
- Маринованные катушки
- Холоднокатаная сталь
- Холоднокатаная катушка
- Холоднокатаный стальной лист
- Полоса холоднокатаной стали
- Оцинкованная сталь в рулонах
- Оцинкованный стальной лист
- Белая катушка
- Лист белой жести
- Катушка из оцинкованной стали с полимерным покрытием
- Сырье для производства стали
- Железный
- Концентрат железной руды
- Железо прямого восстановления (сталь DRI)
- Стальная гранула
- Горячебрикетированное железо (железо ГБЖ)
- Цветные металлы
- Медный катод
- Алюминиевый слиток
- Углеродный продукт
- Графитовый электрод
- Графитовый электрод UHP 600 мм
- Анодный углеродный блок
- Графитовый электрод
Анодный угольный блок — Huaruo (Shanghai) Industrial Co.

Анодный угольный блок Обзор
Он участвует в электрохимических реакциях и направляет ток в электролитическую ячейку. Каждый угольный блок анода предварительно собран из 1 ~ 3 угольных блоков анода, направляющего стержня анода и стального захвата (см. сборку угольного блока анода). Одноанодная группа является наиболее распространенной. Количество и размер группы углеродных блоков зависит от емкости и плотности тока электролитической ячейки (обычно 10 ~ 40 групп).
Углеродные блоки расположены симметрично с левой и правой сторон анодной горизонтальной шины в пазу, а алюминиевый направляющий стержень угольных блоков закреплен на горизонтальной шине поворотным зажимом. Алюминиевый направляющий стержень играет двойную роль: передает ток и подвешивает углеродные блоки.
Анодный угольный блок Использование
Аноды представляют собой большие угольные блоки, которые используются для проведения электричества в процессе восстановления алюминия. Анодный материал для предварительно обожженного алюминиевого электролизера. Он состоит из нескольких угольных блоков анода и механизма подъема анода. Предварительно обожженный анод является важной частью предварительно обожженного анодного алюминиевого электролизера. Аноды представляют собой положительные электроды, обычно изготавливаемые из измельченного прокаленного нефтяного кокса и жидкого пека, сформированные в виде прямоугольных блоков и обожженные. Эти анодные блоки прикреплены к стержням и подвешены в электролизере, где они медленно расходуются в процессе плавки алюминия.
Катодный уголь в сравнении с анодным углеродом
1. Различные диапазоны содержания золы. Зольность катодного угольного блока составляет от 8% до 15%, а зольность катодного угольного блока выше, иногда достигает 30%. Поэтому его можно определить по золе в угольных окурках анода и катодном угольном блоке, разбитом на размер 100 мм.
2. Различные секционные элементы. Основным составом угольных анодных огарков является прокаленный нефтяной кокс, поэтому его поперечное сечение имеет явную пористость и определенный металлический блеск, в то время как катодный угольный блок не имеет этой характеристики.
Процесс производства угольных блоков
1. Процесс производства углеродных блоков состоит из нескольких этапов, начиная с утверждения материала, испытаний на одобрение всех материалов, используемых в системах питьевой воды, и тестирования основных характеристик каждого материала перед производством. из углеродных блоков.
2. Смешайте материал перед формованием или экструдированием. В процессе формования материал загружается в форму, сжимается и нагревается до образования спеченного блока. После охлаждения угольный блок извлекают из формы. В процессе непрерывного формования материал нагревается в шнеке или во внешней форме.
3. Характеристики углеродных блоков, изготовленных методом формования и экструзии, аналогичны, и основные процессы аналогичны. Типичные ограничения, связанные с производством углеродных блоков, связаны с производственным оборудованием, которое можно использовать для производства углеродных блоков заданного размера. Подводя итог, угольный блок является эффективным и широко используемым методом фильтрации.
Производство алюминия с углеродными анодами
В процессе восстановления алюминия аноды в виде больших углеродных блоков используются для проведения электричества. Процессы изготовления угольных анодов и графитовых электродов очень похожи и в некоторых случаях совпадают. Анодный эффект в алюминиевом производстве — явление, при котором низкая концентрация глинозема в электролите приводит к увеличению сопротивления электролизера, нестабильности электролизера и снижению выхода алюминия.
Technical specification:
No | Item | Unit | Guarantee Value |
1 | Apparent Density | g/cm3 (мин) | 1,52 |
2 | Удельное электрическое сопротивление | Электрическое сопротивление | 9,0 мкОм0162|
3 | Compress strength | Mpa (min) | 30 |
4 | Thermal Conductivity | W/mk( max) | 4. |
5 | Flexural Strength | Mpa(Min) | 38 |
6 | Permeability | NPm(Max) | 2.0 |
7 | Thermal Exposure | 10-6/k | 5.0 |
8 | Ash | %(Max) | 0.5 |
9 | Fe | ppm(Max) | 500 |
10 | Si | ppm(Max) | 350 |
11 | V | ppm(Max) | 350 |
12 | Na | ppm(Max) | 500 |
Продукция
- Стальной продукт
- Стальная плита
- Стальная заготовка
- Стальной Блум
- Горячекатаная сталь
- Горячекатаная стальная катушка
- Горячекатаный стальной лист
- Горячекатаный стальной лист
- Горячекатаная полоса
- Маринованные катушки
- Холоднокатаная сталь
- Холоднокатаная катушка
- Холоднокатаный стальной лист
- Полоса холоднокатаной стали
- Оцинкованная сталь в рулонах
- Оцинкованный стальной лист
- Белая катушка
- Лист белой жести
- Катушка из оцинкованной стали с полимерным покрытием
- Сырье для производства стали
- Железный
- Концентрат железной руды
- Железо прямого восстановления (сталь DRI)
- Стальная гранула
- Горячебрикетированное железо (железо ГБЖ)
- Цветные металлы
- Медный катод
- Алюминиевый слиток
- Углеродный продукт
- Графитовый электрод
- Графитовый электрод UHP 600 мм
- Анодный углеродный блок
- Графитовый электрод
Последняя информация
- NDRC: Работа черной металлургии с января по октябрь 2022 г.