Как обеспечить эффективную защиту металлоконструкций от коррозии. Какие существуют методы антикоррозионной обработки. Какое оборудование применяется для антикоррозионной защиты. Какие материалы используются для защиты от коррозии.
Методы антикоррозионной защиты промышленного оборудования
Антикоррозионная защита является важнейшим элементом обеспечения долговечности и надежности металлических конструкций и оборудования в промышленности. Существует несколько основных методов защиты металла от коррозии:
- Нанесение защитных покрытий (лакокрасочных, полимерных, металлических)
- Электрохимическая защита (катодная, протекторная)
- Легирование металлов
- Ингибирование коррозионной среды
- Рациональное конструирование
Выбор метода зависит от условий эксплуатации оборудования, агрессивности среды, требований к сроку службы и других факторов. Часто применяется комбинация нескольких методов для достижения максимального защитного эффекта.
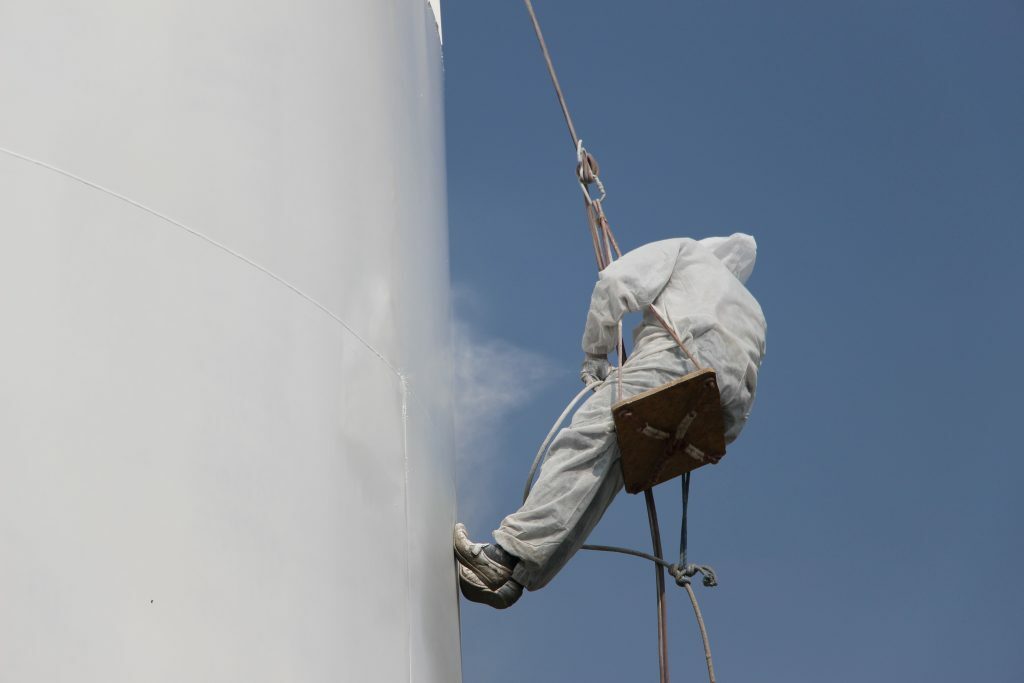
Виды защитных антикоррозионных покрытий
Нанесение защитных покрытий является наиболее распространенным способом антикоррозионной защиты промышленного оборудования. Основные виды покрытий включают:
- Лакокрасочные покрытия
- Металлические покрытия (цинкование, хромирование и др.)
- Полимерные покрытия
- Керамические покрытия
- Комбинированные многослойные покрытия
Каждый тип покрытия имеет свои преимущества и ограничения. Например, цинковые покрытия обеспечивают катодную защиту стали, но подвержены коррозии в кислых средах. Полимерные покрытия химически стойки, но могут иметь недостаточную адгезию к металлу.
Оборудование для нанесения антикоррозионных покрытий
Для качественного нанесения защитных покрытий применяется специализированное оборудование:
- Установки безвоздушного распыления
- Аппараты воздушного распыления
- Электростатические распылители
- Оборудование для порошковой окраски
- Линии горячего цинкования
- Установки газотермического напыления
Выбор оборудования зависит от типа наносимого покрытия, размеров и формы обрабатываемых изделий, требуемой производительности. Современные установки обеспечивают высокое качество покрытия при минимальных потерях материала.
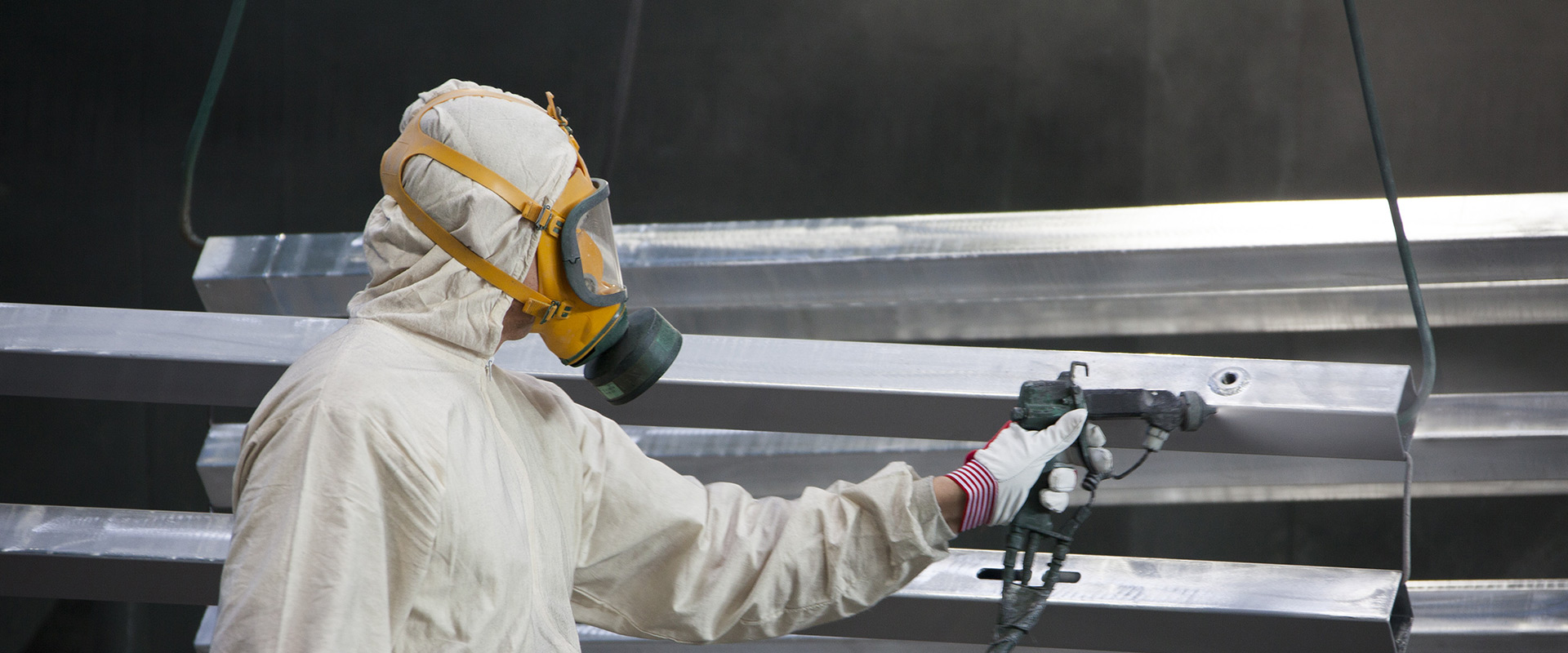
Подготовка поверхности перед нанесением защитных покрытий
Качественная подготовка поверхности металла — ключевой фактор, определяющий долговечность антикоррозионного покрытия. Основные этапы подготовки включают:
- Очистка от загрязнений (обезжиривание)
- Удаление продуктов коррозии (ржавчины, окалины)
- Создание необходимой шероховатости
- Обеспыливание
- Нанесение конверсионных покрытий (фосфатирование, оксидирование)
Для подготовки поверхности применяются механические (абразивоструйная обработка), химические (травление) и комбинированные методы. Выбор метода зависит от исходного состояния поверхности и требований к качеству подготовки.
Электрохимические методы защиты от коррозии
Электрохимическая защита позволяет предотвратить коррозию металлических конструкций путем смещения их электродного потенциала. Различают следующие виды электрохимической защиты:
- Катодная защита — подключение защищаемой конструкции к отрицательному полюсу источника постоянного тока
- Протекторная защита — использование более активного металла (протектора) в качестве анода
- Анодная защита — смещение потенциала металла в область пассивного состояния
Электрохимическая защита широко применяется для защиты подземных трубопроводов, резервуаров, морских сооружений. Она позволяет обеспечить защиту в местах повреждения покрытия.
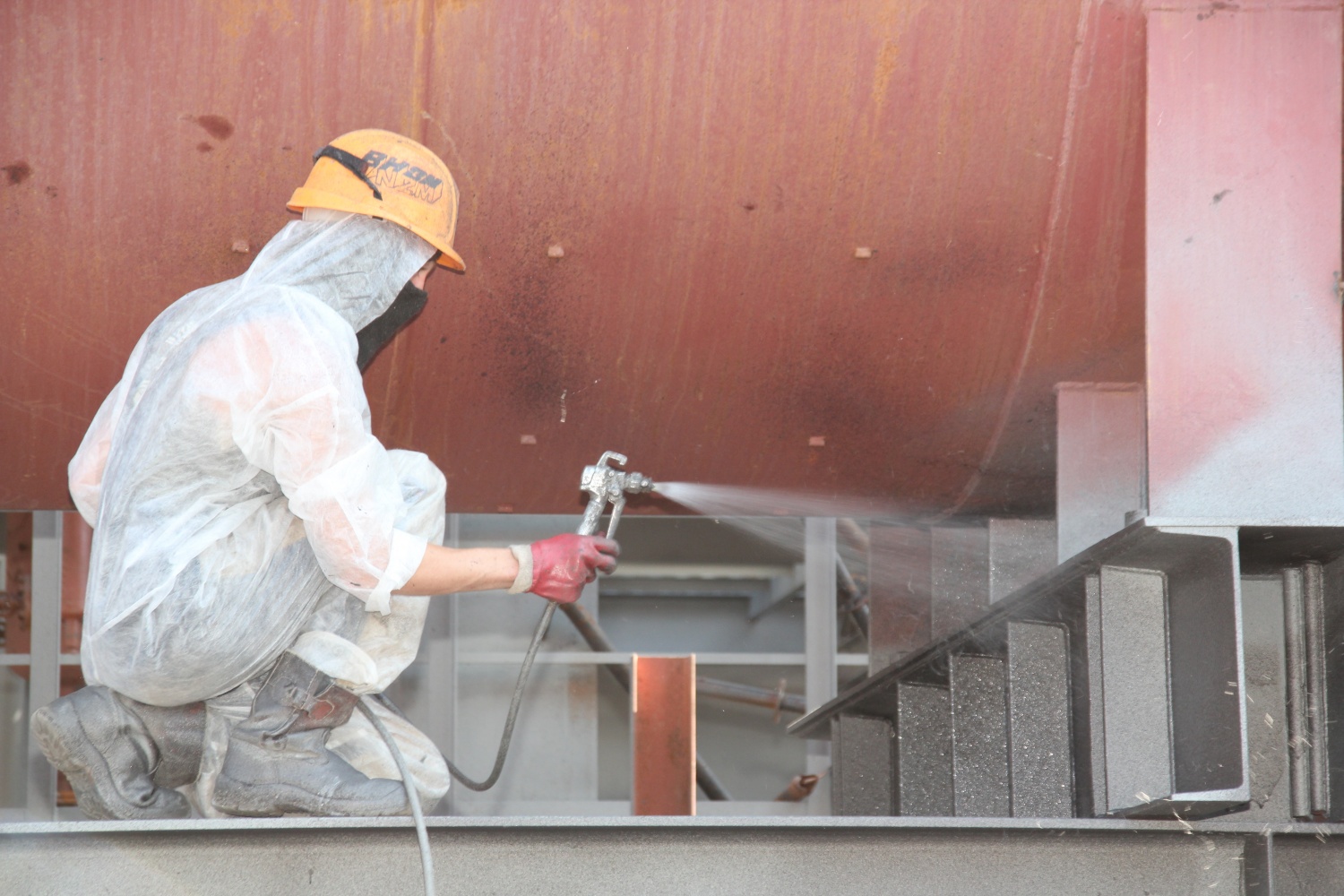
Ингибиторы коррозии и их применение
Ингибиторы коррозии — вещества, которые при добавлении в коррозионную среду значительно снижают скорость коррозии металлов. По механизму действия различают:
- Анодные ингибиторы — замедляют анодный процесс
- Катодные ингибиторы — замедляют катодный процесс
- Смешанные ингибиторы — влияют на оба процесса
- Летучие ингибиторы — защищают в паровой фазе
Ингибиторы применяются для защиты оборудования нефтедобычи, систем охлаждения, при кислотной обработке металлов. Их использование позволяет существенно продлить срок службы оборудования.
Коррозионностойкие материалы в промышленном оборудовании
Применение коррозионностойких материалов позволяет обеспечить длительный срок службы оборудования без дополнительной защиты. К таким материалам относятся:
- Нержавеющие стали
- Титан и его сплавы
- Никелевые сплавы
- Алюминиевые сплавы
- Полимерные композиционные материалы
Выбор материала зависит от условий эксплуатации и требований к конструкции. Несмотря на высокую стоимость, применение коррозионностойких материалов часто оказывается экономически оправданным за счет увеличения срока службы оборудования.
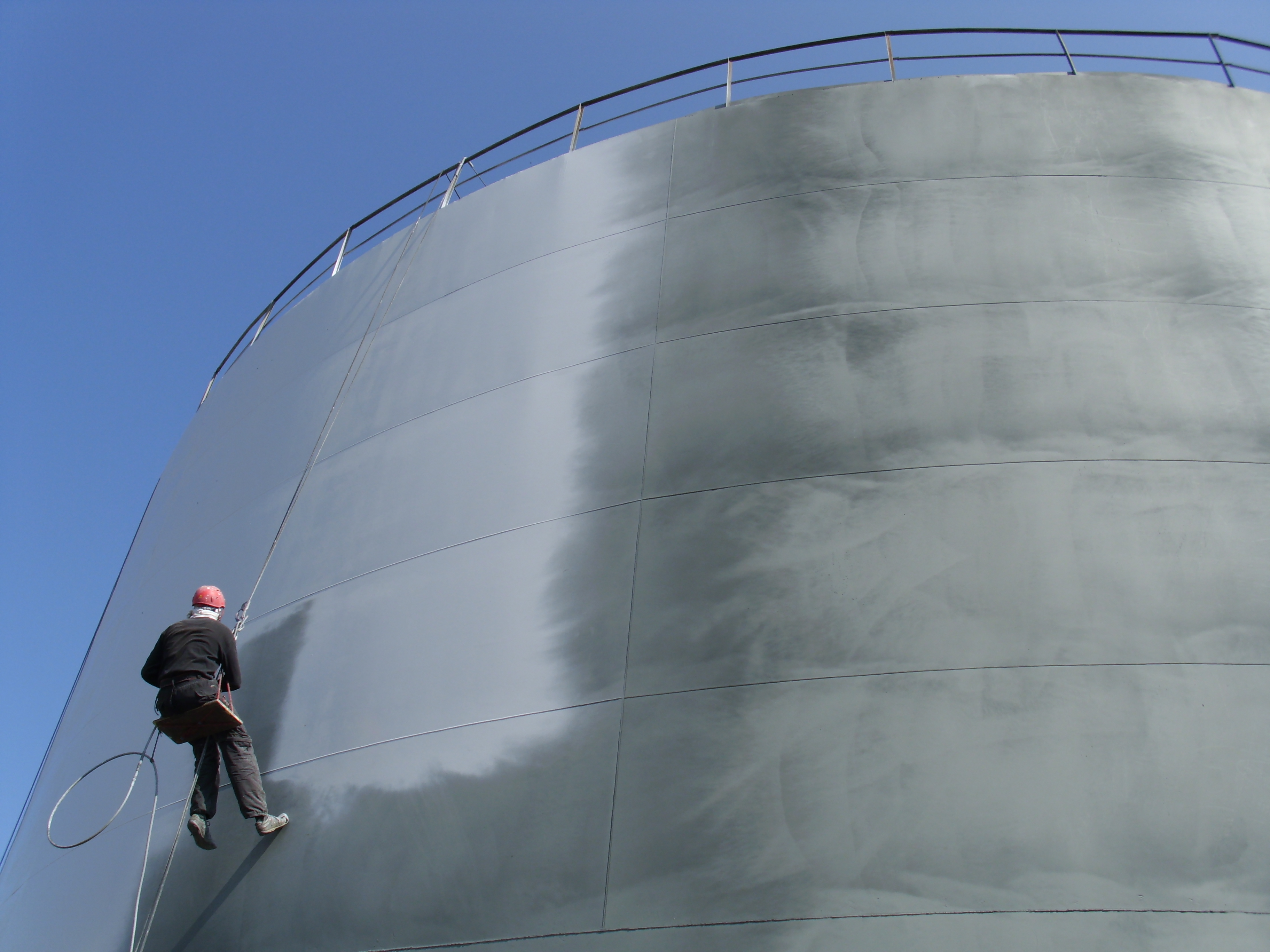
Контроль качества антикоррозионной защиты
Для обеспечения эффективности антикоррозионной защиты необходим регулярный контроль ее качества. Основные методы контроля включают:
- Визуальный осмотр
- Измерение толщины покрытия
- Определение адгезии покрытия
- Испытания на коррозионную стойкость
- Электрохимические измерения
- Неразрушающий контроль (УЗК, рентген)
Регулярный мониторинг состояния защитных покрытий и своевременное устранение дефектов позволяют значительно продлить срок службы оборудования и избежать аварийных ситуаций.
Антикоррозионная защита и обработка металлоконструкций, труб и трубопроводов: что такое и как выполняется
456656 г. Копейск, Челябинской области, ул. Мечникова,1
8 (35139) 2-10-01, 2-10-02
Заказать звонок
Главная
/
О компании
/
Статьи
/
Антикоррозийная защита
Содержание
- Цели антикоррозийной защиты
- Как выполняется антикоррозийная обработка
- Методы антикоррозионной защиты
- Правила проведения обработки
Чтобы металлические конструкции могли служить много лет, необходимо провести антикоррозионную защиту металла. Разрушительное действие атмосферы и агрессивных сред приводит к тому, что материал постепенно утрачивает свои качества и теряет внешний вид. В таком случае металлу требуется защита от коррозии.
Цели антикоррозийной защиты
Долговечность и надежность различных металлических деталей, трубопроводов, строительных конструкций и множества других изделий из металла зависит от качественного антикоррозионного покрытия. Для антикоррозийной обработки металлоконструкций, станков, строительного и сельскохозяйственного оборудования применяются специальные краски.
У износостойких покрытий очень широкая сфера применения. Например, антикоррозионная защита необходима трубам и трубопроводам, строительным металлоконструкциям, транспорту (как строительному, так и железнодорожному). Кроме того, в защите нуждаются мосты, гидросооружения, цистерны, эстакады и любые другие металлические конструкции, контактирующие с агрессивной средой.
Обеспечить металлу надежную защиту от коррозии и продлить срок эксплуатации металлоконструкций можно с помощью антикоррозионных красок. Их используют при работе с металлическими конструкциями сложного профиля, в том числе крупногабаритными.
Как выполняется антикоррозийная обработка
Защита металла от коррозии проходит в несколько этапов:
- Сначала специалисты ищут повреждения, тщательно обследуя поверхность конструкции. На этом этапе нужно установить вид коррозии, определить степень повреждения и оценить, как внешние факторы влияют на металл.
- Следующий шаг — подготовка. Специалисты устраняют следы коррозии, удаляют загрязнения, окалину, химический налет. В соответствии с ГОСТ и международными стандартами ISO поверхность металлоконструкции проходит абразивную чистку с помощью пескоструйной аппаратуры.
- После подготовки надо выбрать материал для покрытия. Здесь учитывается множество нюансов — тип конструкции, состояние объекта и внешней среды, предполагаемая стоимость работ.
- На этапе обработки антикоррозионным покрытием специалисты наносят защитный материал.
В некоторых случаях нужно предварительно загрунтовать поверхность. Нанесение каждого слоя сопровождается межслойной подготовкой. Что касается состава антикоррозийного покрытия, то обычно оно состоит из эмали и грунтовки. Грунтовка, обеспечивающая сцепление между металлом и покрытием, становится первым слоем. Второй слой выполняет функцию барьера, который защищает металлоконструкцию от повреждений. Финишный слой обеспечивает антикоррозийную защиту, препятствует УФ-излучению, и придает конструкции достойный вид.
- Финальный этап обработки — контроль. Когда работы по антикоррозионной защите завершены и материал высох, специалисты оценивают покрытие, внимательно осматривая поверхность.
Методы антикоррозионной защиты
Отличаются не только составы защитных материалов, но и способы их нанесения.
-
Наиболее распространенный метод — покраска. Жидкое антикоррозийное вещество либо распыляют на обрабатываемую поверхность, либо наносят валиком или кистью.
Высыхая, краска образует плотно прилегающую к изделию защитную пленку. К сожалению, такой простой метод обладает своими недостатками: краска может пропускать воздух и влагу, что в дальнейшем приводит к коррозии. По этой причине перед покраской поверхность грунтуют.
- Второй метод – грунтование. Этот метод более эффективен, поскольку грунтовка, содержащая оксид цинка и мелкодисперсный порошок цинка, защищает металл гораздо надежнее.
- Еще один популярный метод защиты от повреждений — нанесение металлических антикоррозионных покрытий. Это гальванизация, плазменное или сверхзвуковое напыление, электроискровая обработка. Такой метод позволяет избежать последствий при повреждении металлоконструкции, но важно учитывать, из каких элементов она выполнена.
-
Наконец, защитить металлические изделия можно с помощью керамического покрытия. Чтобы достичь желаемого уровня адгезии керамики с металлом, нужно сильно прогреть материалы.
Именно поэтому метод применим только при создании высокотемпературных конструкций.
Правила проведения обработки
Выполнение антикоррозийной защиты не обходится без подготовки поверхности. Для этого нужно сделать следующее:
- Устранить очаги ржавчины, удалить растрескавшийся лак или краску.
- Тщательно очистить и высушить поверхность.
- Использовать специальные инструменты при нанесении защитного покрытия.
- Следить за тем, чтобы антикоррозионная обработка осуществлялась систематически.
Предприятия, чья деятельность связана с агрессивной средой, используют ингибиторы и удаляют проводящие ржавчину сварные соединения.
Рекомендуется обратить внимание на отдельные СНиПы:
- Пропитка изделий веществами с высокой химической устойчивостью.
- Оклеивание пленкой.
- Применение лакокрасочных материалов, оксидных и металлизированных покрытий.
Правила, разработанные для защиты конструкций от ржавчины, всегда содержат информацию о составе смесей. Они делятся на агрессивные, слабоагрессивные и неагрессивные.
Таким образом, антикоррозионная защита – это необходимая мера для длительного и безопасного использования металлических конструкций.
Назад к списку
Читайте также
Обработка металла
Покраска металла
Плазменная резка металла
Пескоструйная обработка
Какое оборудование нужно для антикоррозийной обработки?
Многие думают, что нанесение антикоррозийного покрытия – это сложный, трудоемкий процесс, требующий использования различного профессионального оборудования, к которому не у каждого есть доступ. На самом деле, подготовить поверхность металла и нанести антикоррозийный состав возможно при помощи подручных средств. Инструменты, которые понадобятся – найдутся в любом хозяйственном магазине.
Но, если у вас есть доступ к профессиональному оборудованию, то оно существенно облегчит вам задачу в подготовке поверхности и нанесении состава для холодного цинкования. Процесс пройдет легче, потребует меньше усилий и займет гораздо меньше времени.
Мы подскажем – какое оборудование сможет вам пригодиться для антикоррозийной обработки.
Пескоструйный аппарат
Пескоструйную очистку так же называют абразивной или абразивоструйной.
Пескоструйный аппарат поможет быстро и качественно подготовить поверхность металла к нанесению – очистить ее от грязи, старых покрытий, появившейся ржавчины и даже окалины.
Аппарат работает при помощи сухой абразивной смеси, которая подается под большим давлением воздуха из специального «пистолета».
В качестве абразива используется просеянный песок и дробь с показателем влажности, не превышающей 2%. Размер отверстий в приспособлении для просеивания песка может составлять от 1 до 1,2 мм.
Воздух под давлением подается по шлангу из компрессорной установки в пескоструйный аппарат, в резервуаре которого происходит его соединение с абразивной массой. Далее соединение выдувается в пистолет аппарата, и с помощью высокого давления подается на рабочую поверхность.
Внимание! Неосторожная работа с пескоструем может привезти к деформации металлической конструкции. Не рекомендуется применять давление более 4 атмосфер. |
В ходе абразивной обработки насадка для пескоструйной абразивной очистки поверхности деформируется под воздействием песка, расход рабочего диаметра в 1,5-2 часа – это примерно половина срока службы насадки. Так что будьте готовы к частой замене насадке, особенно если у вас большая площадь конструкции.
По завершению абразивной очистки с обработанной поверхности удаляют остатки песка и пыли, путем обдувания простым воздухом. Такую очистку рекомендуется проводить в специальной камере или отдельном помещении, специально приспособленном для подобных работ.
Если вам необходимо соответствовать ГОСТу, то подготовка металлических материалов к окрашиванию регламентируется в ГОСТ 9.402-2004.
В зависимости от поставленной задачи, пескоструйная очистка с помощью мойки высокого давления может осуществляться с применением разных степеней очистки.
Применение поверхностной абразивной обработки деталей из металла и металлических конструкций фасадов, позволяет получить поверхностям средний показатель чистоты. То есть, на обработанных объектах, при визуальном осмотре, все же можно будет обнаружить окалины и пятна.
Глубокая абразивная обработка дает возможностью полностью исключить присутствие на металлических поверхностях, подвергшихся абразивной очистке, даже следы бывшей ржавчины или окалин. В данном случае металлическая поверхность может быть зачищена добела.
Легкая пескоструйная обработка металла позволяет удалить с его поверхности ржавые пятна и отслоившиеся окалины, в результате при поверхностном осмотре объект будет выглядеть сравнительно чистым.
Профессионалы могут проводить с помощью пескоструя и обезжиривание поверхности.
Пескоструйные аппараты бывают нескольких видов: пневмораспылители пескоструйные эжекторного типа, пескоструйные установки эжекторного типа, пескоструйные установки напорного типа и пескоструйные камеры.
Другие способы очистки с помощью оборудования
Также для очистки поверхности металла могут применяться аппараты струйной очистки сжатым воздухом или водой под высоким давлением. Их можно подразделить на несколько видов.
Абразивная струйная очистка сжатым воздухом
Абразивная струйная очистка сжатым воздухом осуществляется при подаче абразива в поток воздуха и направлении образующейся воздушно-абразивной смеси с высокой скоростью из сопла на очищаемую поверхность. Абразив может быть впрыснут в воздушный поток из емкости, находящейся под давлением, или увлечен этим воздушным потоком в процессе всасывания из емкости, не находящейся под давлением. Этим способом очищают поверхности с помощью дробеструйных аппаратов.
Абразивная струйная очистка с вакуумом или всасывающей головкой
Этот метод аналогичен абразивной струйной очистке сжатым воздухом с той разницей, что сопло заключено внутри всасывающей головки, которая герметично закреплена на стальной очищаемой поверхности и служит для сбора отработанного абразива и загрязнений. В качестве альтернативного варианта воздушно-абразивный поток может быть подан на металлическую поверхность при использовании пониженного давления во всасывающей головке, т.е за счет эжекции. Этот метод имеет название вакуум-бластинг.
Абразивная струйная очистка с впрыскиванием влаги
Этот метод аналогичен абразивной струйной очистке сжатым воздухом с той разницей, что в воздушно-абразивный поток добавляют незначительное количество жидкости (обычно чистую пресную воду), что создает метод струйной очистки, при котором не образуется пыли в диапазоне размера взвешенных частиц менее 50 мкм. Расход воды составляет 15-25 л/ч.
Влажная абразивная струйная очистка со сжатым воздухом
Этот метод аналогичен абразивной струйной очистке сжатым воздухом и отличается тем, что в поток добавляют жидкость (обычно чистую, пресную воду). При этом очистка поверхности производится потоком воды, воздуха, абразива. При влажной абразивной очистке используют смесь абразива с водой в соотношении от 1:2 до 1:6.
Суспензионная струйная очистка
Суспензионная струйная очистка заключается в подаче дисперсии мелких абразивных частиц в воде или другой жидкости на очищаемую поверхность.
Струйная очистка жидкостью под давлением
Абразив (или смесь абразивов) вводят в поток жидкости (обычно чистой пресной воды), и этот поток направляют через сопло на очищаемую поверхность. Поток представляет собой, главным образом жидкость, находящуюся под давлением, а количество добавленных абразивов, как правило, меньше, чем в случае влажной абразивной струйной очистки сжатым воздухом.
Этот метод основан на воздействии кинетической энергии высоконапорной водяной струи на обрабатываемую поверхность. При этом струя воды позволяет удалять с поверхности загрязнения и отложения любой физической природы и химического состава: ржавчину, консервационные смазки, лакокрасочные покрытия, битум, смолы, нагар, окалину и т. д. Введение в струю абразива позволяет легко удалять поверхностные слои металла.
Давление воды зависит от типа удаляемых загрязнений, таких как водорастворимые вещества, рыхлая ржавчина и красочные покрытия со слабым сцеплением. Если в процессе очистки использовались поверхностно-активные вещества, необходимо ополаскивание чистой, пресной водой.
Методы водной струйной очистки
Водная струйная очистка может быть высокого давления – от 70 до 170Мпа и сверхвысокого давления – свыше 170Мпа. Гидроструйную очистку при высоком давлении называют «гидро-джеттинг».
- Гидроджеттинг под сверхвысоким давлением (более 170 МПа) применяется для полного удаление всех Пк и ржавчины. Результат сравним с сухим бластингом, но на поверхности после сушки наблюдаются проблески ржавчины.
- Гидроджеттинг под высоким давлением. (70 −170 МПа) позволяет удалить большинство красок и продуктов коррозии. Магнетиты (черные окислы) и прочно держащиеся покрытия могут остаться, хотя они с некоторыми трудностями также поддаются удалению.
- Гидроочистка под средним давлением (35-70 МПа) позволяет удалить непрочно держащиеся краску, ржавчину, загрязнения. Но черный железный оксид (магнетит) останется. Однородная поверхность не может быть получена.
- Гидроочистка под низким давлением (до 35 МПа) позволяет удалить соли, загрязнения, шелушащуюся краску. В основном это промывка поверхности.
- Гидроочистка под низким давлением с применением абразива. 0,6-0,8 МПа. Скорость очистки — 10-16 м²/час в зависимости от удаляемого материала. Позволяет уменьшить расход абразива, пылеобразование, избежать образования искр. Результат сравним с сухим бластингом, но на поверхности после сушки наблюдаются проблески ржавчины.
В настоящее время данные технологии активно используются там, где необходимо быстро, качественно и безопасно выполнить работы по очистке и подготовке поверхности. Такое оборудование многофункционально и позволяет выполнять широкий спектр работ в различных отраслях промышленности.
Агрегаты высокого и сверхвысокого давления представляют собой высоко-эффективное, экологически чистое и энергосберегающее оборудование на базе водоструйных технологий высокого давления. Чистка металлической поверхности высоким и сверхвысоким давлением водяной струи не вызывает нарушений в структуре металла.
Воздействие водяной струи высокого или сверх высокого давления на поверхность можно подразделить на:
- Гидравлическое – однородная струя воды;
- Гидродинамическое – удары струей по поверхности;
- Гидроабразивное – смешанная струя воды и абразива.
Покрасочное оборудование
Кром помощи в очистке поверхности, упростит и ускорит работу покрасочное оборудование. В окраске различных поверхностей используется два типа оборудования: аппараты безвоздушного распыления и пневматические (воздушные) распылители.
Безвоздушная покраска
Самыми распространенными способами безвоздушной окраски является применение окрасочного пистолета, а так же аппаратов безвоздушного распыления.
Принцип работы способа безвоздушного распыления – применение воздуха, как тормозящей силы, снижающей скорость потока, а распыление краски происходит под большим давлением.
Метод считается более выгодным, чем воздушное распыление, так как экономится краска и меньше загрязняется атмосфера. При таком способе нанесения используется меньше растворителя, а также уменьшается количество слоев, за счет увеличения толщины каждого слоя. Чтобы распылять покрытие таким способом, не нужно долго обучаться, процесс достаточно прост и понятен. В результате покраска происходит быстрее, все вокруг пачкается меньше, а краска экономится.
Оборудование для безвоздушной покраски выгодно применять там, где нужно покрыть большую площадь поверхности. Методика просто незаменима в покраске крупных конструкций промышленных масштабов. Очень часто безвоздушное распыление применяется при антикоррозийной обработке автомобилей, крыш, потолков, стен, фасадов и других конструкций из металла.
Современные аппараты отличаются простотой использования, безопасностью в обслуживании и бесшумной работой. Кроме того, такое оборудование очень мобильно и поэтому легко транспортируется в нужное место. Несмотря на то, что для этого метода используется различные аппараты, все они имеют общий принцип работы и схожую конструкцию, так что вы быстро научитесь работать с любым аппаратом.
Обычно, такой аппарат состоит из: краскопульта, окрасочного безвоздушного сопла, насоса мощностью от 22 до 500 атмосфер и специальных шлангов, рассчитанных на работы под высоким давлением.
Насос в устройствах используется поршневого или мембранного типа, он перекачивает краску по направлению к распылителю. Для работы насоса используется электрический или пневматический мотор, а также бензиновый двигатель – в особо крупных аппаратах. Далее при помощи насоса антикоррозийные составы под высоким давлением проходят через сопло небольшого диаметра. Это приводит к распылению краски по поверхности металла в виде очень мелких частичек. Для человеческого глаза это выглядит, как сплошное, качественное покрытие.
Пневматическое (воздушное) распыление
Пневматическое распыление – самый распространенный вид нанесения различных лакокрасочных материалов. Так как антикоррозийные средства и составы для холодного цинкования схожи по структуре с красками, то пневматическое распыление помогает и тут быстрее и качественнее справится с работой.
Пневматическое распыление подразделяют на несколько видов.
- С подогревом покрасочного материала
Применяется в основном для экономии на растворителях. При нагреве, многие ЛКМ становятся более жидкими и не нуждаются в разбавлении. Однако, такой способ подходит далеко не всем краскам и составам, а только тем, кто не меняет свою структуру при нагревании. Для большинства качественных антикоррозийных покрытий и составов для холодного цинкования этот способ нанесения не подходит, так как не рекомендуется их нагревать.
- Без подогрева состава
Пневматические распылители без нагрева ЛКМ подходят для применения практически любых красок и составов. Из минусов этого способа можно назвать большой расход растворителя для разбавления, расход краски на окружающие поверхности. Необходимы условия хорошей вентиляции и система очистки воздуха.
Аппарат пневматического распыления обычно называют установкой, которая состоит из: масловлагоотделителя, централизованной линии сжатого воздуха или передвижного, переносного компрессора, краскопульта, шлангов для подачи краски и сжатого воздуха, красконагнетательного бака с перемешивающим устройством и редуктором. Установки применяются разные, каждая имеет свои плюсы и минусы. Так большие установки массой 140-170 кг обладают большой мощностью и производительностью, а их более компактные варианты мобильнее, меньше весят, но имеют мощность в десятки раз меньше. В любом случае, переносные аппараты всегда выгоднее стационарных.
Краскораспылители
Если нет возможности или необходимости использовать тяжелое пневматическое оборудование, можно воспользоваться стандартными краскораспылителями.
Краскораспылители так же подразделяют на:
- Высокого давления — от 3 до 6 кгс/см2;
- Низкого давления – 2,5-3 кгс/см2.
Также краскораспылители бывают внутреннего и наружного смешивания. Подача краски в распылитель может происходить из маленького бачка, прикрепленного прямо к краскопульту, который называют «стаканом», а также может подаваться через шнур из красконагнетательного бака. «Стаканы» выгоднее использовать, если нужно покрывать небольшой или труднодоступный участок, они более мобильны. А большие баки – для больших площадей.
Электроокрашивание
Достаточно новый и пока не очень распространенный способ окрашивания с помощью распыления в поле высокого напряжения. Его суть заключается в переносе в электрическом поле высокого напряжения заряженных частиц краски. Электрическое поле создается между двумя электродами, один из которых – изделие, которое окрашивается, а другой – краскораспылительное коронирующее устройство. Изделие заземляют, а к краскораспылителю подключают высокое напряжение (зачастую отрицательное). Лакокрасочный состав подается к краскораспылителю (на коронирующую кромку), где отрицательно заряжается, и под действием электрических сил распыляется. Поток распыленного лакокрасочного материала направляется к окрашиваемому изделию и осаждается на его поверхности. Электроокрашиванием наносят защитные слои как на металлические, так и на неметаллические поверхности.
Ручные краскораспылители характеризуются достаточно маленькой производительностью, хотя имеют ряд преимуществ: небольшой расход лакокрасочного материала (отсутствие его потерь), возможность окрашивать изделия решетчатой структуры и т.д.
На стационарных установках окрашиваются детали достаточно простой формы: корпуса стиральных машин, кузова автомобилей, корпуса различных приборов, электродвигателей, холодильников и т.п.
Используя перечисленное оборудование, вы сможете сделать антикоррозийную обработку легче, быстрее и качественнее. Но, каждый наш состав для холодного цинкования не нуждается в обязательном использовании сложного оборудования, может быть применен с помощью элементарных инструментов.
На нашем сайте представлены цинкосодержащие грунтовки, которые вы можете наносить всеми перечисленными в статье методами. В том числе, Барьер-Грунт — цинкосодержащий грунт для металла (96% цинка в составе) для антикоррозийной защиты. По своим защитным характеристикам сравним с горячим цинкованием, а также обладает всеми преимуществами лакокрасочных антикоррозионных покрытий.
Есть вопросы по выбору состава? Обращайтесь в представительство в вашем городе:
в Санкт-Петербурге: +7 (812) 603-41-53, +7 (921) 927-58-47
в других городах: 8 (800) 707-53-17
e-mail: [email protected]
Проектирование оборудования для защиты от коррозии в суровых промышленных условиях
Антикоррозионный эффект защитного покрытия может варьироваться в зависимости от состава материала. Предоставлено: Moxa
Металлические поверхности промышленного оборудования подвержены риску коррозии, что может привести к необратимому структурному повреждению оборудования или даже к неисправности. Коррозия ежегодно причиняет миллиарды долларов убытков в промышленности по всему миру. Производители должны обеспечить защиту своего оборудования от воздействия коррозии в промышленных условиях.
Стандарт ISO 9223 по коррозии металлов и сплавов определяет два метода оценки атмосферной коррозионной активности объекта. Предоставлено: Moxa
Технология помогает предприятиям защитить свое оборудование и обеспечить непрерывную работу. Давайте обсудим основные причины коррозии и предложим способы решения этой проблемы в суровых промышленных условиях.
Стандарт ISO 9223 по коррозии металлов и сплавов определяет два метода оценки атмосферной коррозионной активности объекта. Стандарт определяет категории коррозии в зависимости от атмосферной влажности и загрязнения.
Категории C1, C2, C3, C4, C5 и CX, где CX является самым суровым, присваиваются различным внутренним и наружным помещениям на основе испытаний на месте, проведенных для регистрации скорости осаждения коррозионных материалов, и путем расчета коэффициента защиты. для местоположения. В таблице 1 перечислены категории коррозии, применимые для различных внутренних и наружных применений.
Стандарт ISO 9226 также определяет категории коррозионной активности C1, C2, C3, C4 и C5 для некоторых стандартных металлических образцов на основании скорости их коррозии, как показано в таблице 1.
Производители оборудования могут использовать категории коррозионной активности, определенные стандартом ISO-9223, в качестве основы для выбора оптимального коррозионно-стойкого материала или реализации защитных мер для своего оборудования. Стандарт ISO-9223 не учитывает конструкцию и режим работы изделия, что также может повлиять на его устойчивость к коррозии.
Наука о коррозии
Коррозия – это химическая реакция, возникающая при химическом воздействии газов или жидкостей на открытые поверхности металлов, что приводит к окислению металлов. Хотя некоторые металлы имеют встроенную способность противостоять коррозии, высокие температуры и присутствие кислот и солей в окружающей среде могут ускорить коррозию металлов. Кроме того, высокоактивный металл легко подвергается коррозии. Коррозия ставит под угрозу стабильность металлов, вызывая энтропийные изменения в металле.
Помимо состава используемых материалов механические факторы и факторы окружающей среды могут вызывать коррозию в промышленном оборудовании. Предоставлено: Moxa
Помимо состава используемых материалов механические факторы и факторы окружающей среды могут вызывать коррозию в промышленном оборудовании. Непрерывная нагрузка или нагрузка на деталь машины или соединение может ускорить разрушение детали, вызывая коррозию. Газы и жидкости, присутствующие в рабочей среде, могут вызвать коррозию или ускорить износ металлических поверхностей.
В типичной промышленной среде присутствует много агрессивных элементов, таких как вода, кислород и двуокись углерода. Кроме того, хлор и сульфиды также обладают высокой коррозионной активностью. Чрезвычайно клейкая природа этих элементов делает их ключевыми триггерами коррозии металлов. Еще одним фактором, вызывающим коррозию в промышленных условиях, являются высокие рабочие температуры. Промышленные продукты обычно имеют конструкцию без вентилятора, что помогает поддерживать стабильность системы. Однако рабочая среда с постоянными высокими температурами может ускорить коррозию металлов.
Предотвращение коррозии в промышленности
Коррозия представляет серьезную опасность для промышленного оборудования, вызывая функциональные и структурные повреждения. Поскольку все больше и больше промышленной деятельности происходит в суровых и суровых промышленных условиях, растет потребность в продуктах, разработанных для того, чтобы противостоять коррозионному воздействию природных элементов, таких как пыль, ветер, дождь, соль и снег. Современные технологии добились значительного прогресса в снижении последствий коррозии и во многих случаях в замедлении коррозии, что приносит пользу промышленным операторам. Кроме того, стоимость антикоррозионных технологий составляет лишь часть стоимости замены поврежденного оборудования.
Два основных преимущества коррозионностойкого промышленного оборудования:
Лучшая производительность: Чем стабильнее продукт, тем точнее результаты применения. Многие промышленные продукты требуют непрерывной работы оборудования, иногда в суровых промышленных условиях. Оборудование, не подверженное коррозии, может гарантировать стабильную работу и лучшую производительность, что, в свою очередь, приводит к повышению производительности.
Меньшие затраты на обслуживание и более длительный срок службы: До появления Интернета вещей многие отрасли полагались на человеческие усилия по проверке и обслуживанию устройств и оборудования на месте. Хотя эта дорогостоящая бизнес-модель больше не нужна, так как устройства и оборудование, расположенные даже в самых отдаленных и удаленных районах, можно легко контролировать и обслуживать с помощью решений для удаленного мониторинга, проектирование коррозионностойкого оборудования и использование антикоррозионной защиты могут продлить срок их службы и значительно сократить техническое обслуживание. расходы.
Важнейшие аспекты предотвращения коррозии в промышленном оборудовании включают в себя выбор подходящих материалов, соответствующих среде применения, разработку продуктов, минимизирующих коррозию, использование производственных технологий, предотвращающих ее, и использование внешних механизмов для защиты промышленного оборудования.
Антикоррозийный эффект защитного покрытия может варьироваться в зависимости от состава материала. Предоставлено: Moxa
Выбор материалов
Выбор правильных материалов является ключевым фактором в предотвращении коррозии оборудования. Стандарт ISO 9223 определяет категории коррозионной активности, которые можно использовать в качестве руководства при выборе материала и комбинировании материалов. Хотя трудно найти материалы, на 100 % устойчивые к воздействию агрессивных элементов, тщательный выбор материалов, особенно при их сочетании в изделии, может уменьшить коррозию. Хорошее понимание процесса коррозии в металлах и знание их механических свойств и прочности металла, необходимой для противостояния его воздействию, имеет большое значение при создании коррозионно-стойкого оборудования.
Когда два разнородных материала объединяются в продукт, свободные электроны перемещаются между ними, вызывая коррозию в долгосрочной перспективе. Если два объединенных материала имеют высокую разность электрических потенциалов, вероятность коррозии намного выше. Таким образом, производители оборудования должны тщательно выбирать материалы, используемые при создании промышленного оборудования для использования в промышленных условиях. Они должны выбирать материалы, способные противостоять агрессивным средам, характеризующимся высокой температурой, влажностью и высокими значениями pH. Производители должны выбирать материалы с более низкой разностью электрических потенциалов при их комбинировании.
Дизайн изделия
Элементы конструкции, которым не уделяется должного внимания, могут оказаться слабым звеном в борьбе с коррозией. При проектировании продуктов инженеры-механики должны тесно сотрудничать с инженерами по коррозии, чтобы избежать щелей и перегруженных конструкций, которые могут вызвать точечную коррозию. Локальная интрузивная точечная коррозия может распространяться на большую площадь поверхности, тем самым ускоряя повреждение продукта. Например, точечная коррозия может ускориться и привести к повреждению конструкции оборудования при контакте с хлоридами в воздухе.
Другие методы проектирования, которые могут помочь предотвратить коррозию, включают:
- Увеличение толщины деталей оборудования с учетом воздействия коррозии и, таким образом, увеличение срока службы оборудования
- Использование аналогичных материалов во всем оборудовании для предотвращения гальванической коррозии
- Сведение к минимуму разницы температур поверхности оборудования, подвергающегося воздействию экстремально высоких/низких температур
- Предотвращение концентрации нагрузки на определенные части оборудования
- Избегайте контакта с другими вызывающими коррозию частями или оборудованием
Местоположение и направление, в котором продукт развертывается и используется, также играют роль в сдерживании воздействия коррозионных элементов. Разработчики промышленных продуктов должны тщательно учитывать эти факторы при проектировании и развертывании оборудования.
Производственный процесс
Производственный процесс может привести к неявным очагам коррозии в продуктах. Например, конструкция может привести к тому, что нагрузка будет сосредоточена на определенных деталях, особенно на соединениях, которые подвержены коррозии при воздействии на них коррозионно-активных элементов. Эти части оборудования требуют дополнительной изоляционной защиты. Кроме того, металлы имеют тенденцию поглощать водород в процессе плавки и гальваники, который затем проникает в слой покрытия, делая его неэффективным. Внешние коррозионные факторы могут усилить повреждение частей оборудования, имеющих внутренние повреждения. В производственный процесс необходимо ввести стадию дегидрирования, чтобы устранить эффекты поглощения водорода металлами.
Покрытие деталей оборудования различными химическими веществами может сделать компоненты более тяжелыми и дорогостоящими, тем самым снижая конкурентоспособность продукции. Следовательно, для снижения стоимости продукта и усиления защиты от агрессивных сред требуется другой тип защитного механизма, например, защитная краска. Такие краски должны иметь низкое содержание водорода, защищать от осмоса воды и обладать высокой устойчивостью к ионизации. Покрытие деталей машин одним или двумя слоями краски, специально созданной для этой цели, помогает избежать образования пузырей на поверхности материала и уменьшает повреждения, вызванные разницей плотности между используемым материалом и окружающей средой.
Водно-осмотическая краска менее устойчива к коррозии, чем краска на основе порошка. Осматическая активность вызывает появление пузырей в слое покрытия. Осмотические пузыри могут образовываться между краской и основной подложкой, между слоями краски или внутри матрицы одного слоя композитной пленки краски. Пример вздутия, вызванного осмосом воды на металлической подложке, покрытой водорастворимой пленкой на основе соли, показан на следующей диаграмме. Когда пленка вступает в контакт с водой/низкой концентрацией электричества, вода начинает просачиваться внутрь. Когда концентрация воды одинакова с обеих сторон пленки покрытия, пленка выскакивает, образуя волдырь.
Адгезионная способность краски является еще одним ключевым фактором предотвращения коррозии; чем более клейкая краска, тем более сильную защиту она обеспечивает из-за ее устойчивости к воздействию поверхностных загрязнений или оксидов.
Внешние защитные механизмы
Более дешевым способом защиты металлов от коррозии является нанесение защитного покрытия. Антикоррозионный эффект защитного покрытия может варьироваться в зависимости от состава его материала. Цинк обычно используется в качестве одного из компонентов защитного слоя. Алюминий также добавляется в слой покрытия для защиты металлов от коррозии из-за его способности эффективно блокировать внешние коррозионные факторы. Алюминий обеспечивает лучшую устойчивость к окислению и имеет более подходящую внутреннюю структуру, чтобы блокировать внешние коррозионные факторы. Он также известен своей высокой термостойкостью и может выдерживать воздействие сильного внешнего тепла.
Известно, что изделия, покрытые алюминием, в два раза лучше защищают от поверхностной коррозии по сравнению с изделиями, покрытыми цинком. Материалы с высокой концентрацией хрома или молибдена также могут быть эффективными в качестве защитного покрытия. Например, машиностроители могут использовать в своих машинах материалы из нержавеющей стали или алюминия, чтобы противостоять воздействию агрессивных сред.
Антикоррозионная технология также включает методы активной защиты и пассивной защиты. Активная защита основана на использовании внешнего механизма для уменьшения или сопротивления коррозии, в то время как пассивная защита основана на защите, основанной на антикоррозионной способности материала, используемого в продуктах. Активную защиту от коррозии можно разделить на катодную защиту и анодную защиту.
Катодная защита: Этот метод заключается в подаче стабильного постоянного тока через защитный металл для компенсации делокализованного электрона и приведении коррозионно-активного электронного потенциала к отрицательной полярности, где скорость окисления медленнее.
Анодная защита: В этом методе используется контроль коррозионного фактора окружающей среды для металлов с большей реакционной способностью, так что коррозия возникает только при положительной полярности и защищает компонент при отрицательной полярности.
Оба эти метода имеют свои преимущества и недостатки. Наиболее идеальным способом является объединение обоих этих методов для снижения отрицательного электрического потенциала и повышения положительного потенциала, тем самым максимизируя разность потенциалов. Это может поглощать больше внешних делокализованных электронов и коррозионных факторов, обеспечивая максимальную защиту от коррозии. Эти активные защитные методы увеличивают защиту от поверхностной коррозии металлов до 30% при измерении методом площади. Однако эти методы защиты обеспечивают ограниченную защиту оборудования с соединениями и кромками.
В сценарии с высокой коррозионной активностью оценка среды применения и выявление существующих коррозионных факторов являются первыми шагами к проектированию продукта. Использование материалов, подходящих для среды применения, и оптимизация производственного процесса могут помочь обеспечить внутреннюю защиту от агрессивных сред. Если рабочая среда слишком сурова и выходит за рамки того, что может выдержать большинство металлов, то единственный выход — использовать внешние методы защиты. Интегрированный механизм защиты, такой как сочетание методов катодной и анодной защиты, может стать идеальным решением для повышения прочности конструкции промышленного оборудования и повышения стабильности продукта.
Есть ли у вас опыт и знания по темам, упомянутым в этом содержании? Вам следует подумать о том, чтобы внести свой вклад в нашу редакционную команду CFE Media и получить признание, которого вы и ваша компания заслуживаете. Нажмите здесь, чтобы начать этот процесс.
Что такое защита от коррозии? – Cor Pro
Cor-Pro Systems, Inc. является ведущим поставщиком средств защиты от коррозии на побережье Мексиканского залива.
Имея предприятие площадью 150 000 квадратных футов в Хьюстоне, оснащенное первоклассным оборудованием для превосходной защиты от коррозии, Cor-Pro Systems работает с отраслями, которым требуется самое высокое качество услуг по борьбе с коррозией в этом районе.
Cor-Pro Systems является экспертом в решении проблем, связанных с коррозией. Используя последние тенденции и технологии, Cor-Pro Systems может работать с любыми проблемами коррозии и применять решения, специально разработанные для определенной работы.
Системы Cor-Pro предлагают индивидуальные решения по защите от коррозии.
Коррозия является одной из основных проблем, с которыми сталкиваются практически все отрасли промышленности. Важно знать последствия коррозии, риски, связанные с коррозионными объектами и оборудованием, а также преимущества получения высококачественных услуг по защите от коррозии от авторитетных компаний. Что такое защита от коррозии? На этой странице представлены ответы.
Что такое защита от коррозии?
Защита от коррозии — это применение антикоррозионных химикатов для предотвращения повреждений оборудования или объектов, вызванных коррозионными агентами. Для борьбы с различными формами коррозии в различных материалах Cor-Pro Systems предлагает нашим клиентам следующие методы защиты от коррозии.
Ингибиторы коррозии
Ингибиторы коррозии — это химические вещества, добавляемые в оборудование для образования тонкого слоя защиты от катализаторов коррозии. Наши специалисты могут применять эти добавки даже во время работы машины.
Покрытия
Покрытие — самый простой способ защитить ваше оборудование. Покрывающие материалы, такие как эпоксидная смола, уретан и цинк, могут добавить дополнительный уровень защиты вашим объектам при правильном нанесении и отверждении.
Абразивоструйная очистка
Абразивоструйная очистка использует высокоскоростную машину, которая продвигает среду к поверхности материала. С помощью абразивоструйной очистки вы можете контролировать ущерб, вызванный коррозией, и подготовить его к нанесению антикоррозионных материалов.
Понимая природу ваших потребностей в защите от коррозии, Cor-Pro Systems предоставит специализированные решения, основанные на потребностях и спецификациях клиентов.
Преимущества надлежащей защиты от коррозии
Отрасли, особенно те, которые подвергаются воздействию самых агрессивных коррозионных агентов, таких как соленая вода и почва, могут значительно выиграть от качественных услуг по защите от коррозии.
- Качественная защита от коррозии может продлить срок службы вашего оборудования на 250 %.
- Защита от коррозии может снизить затраты на ремонт из-за коррозионного повреждения.
- Защищенное оборудование может избежать перерывов в обслуживании и сбоев в работе .
- Защита от коррозии может спасти жизнь от травм, вызванных выветренным оборудованием и объектами.
- Предотвращая травмы и ущерб от коррозии оборудования, компании могут избежать юридических и экологических обязательств .
Обладая почти 30-летним опытом решения проблем с коррозией на побережье Мексиканского залива, Cor-Pro Systems может гарантировать клиентам, что все эти преимущества достигаются за счет качественных методов защиты от коррозии.