Что такое сухой пленочный фоторезист. Как наносится сухой пленочный фоторезист на печатные платы. Какие преимущества имеет технология сухого пленочного фоторезиста. Какие этапы включает процесс изготовления печатных плат с помощью сухого пленочного фоторезиста. Как правильно использовать сухой пленочный фоторезист для получения качественных печатных плат.
Что представляет собой сухой пленочный фоторезист?
Сухой пленочный фоторезист — это светочувствительный полимерный материал, который используется в производстве печатных плат и микроэлектронных устройств. Он поставляется в виде тонкой сухой пленки, которая ламинируется на поверхность заготовки печатной платы.
Основные компоненты сухого пленочного фоторезиста:
- Фоточувствительный полимер
- Фотоинициатор
- Связующее вещество
- Пластификатор
- Краситель
При воздействии ультрафиолетового излучения происходит фотохимическая реакция, в результате которой экспонированные участки полимеризуются и становятся нерастворимыми в проявителе. Неэкспонированные участки удаляются при проявлении, формируя рисунок схемы на поверхности платы.
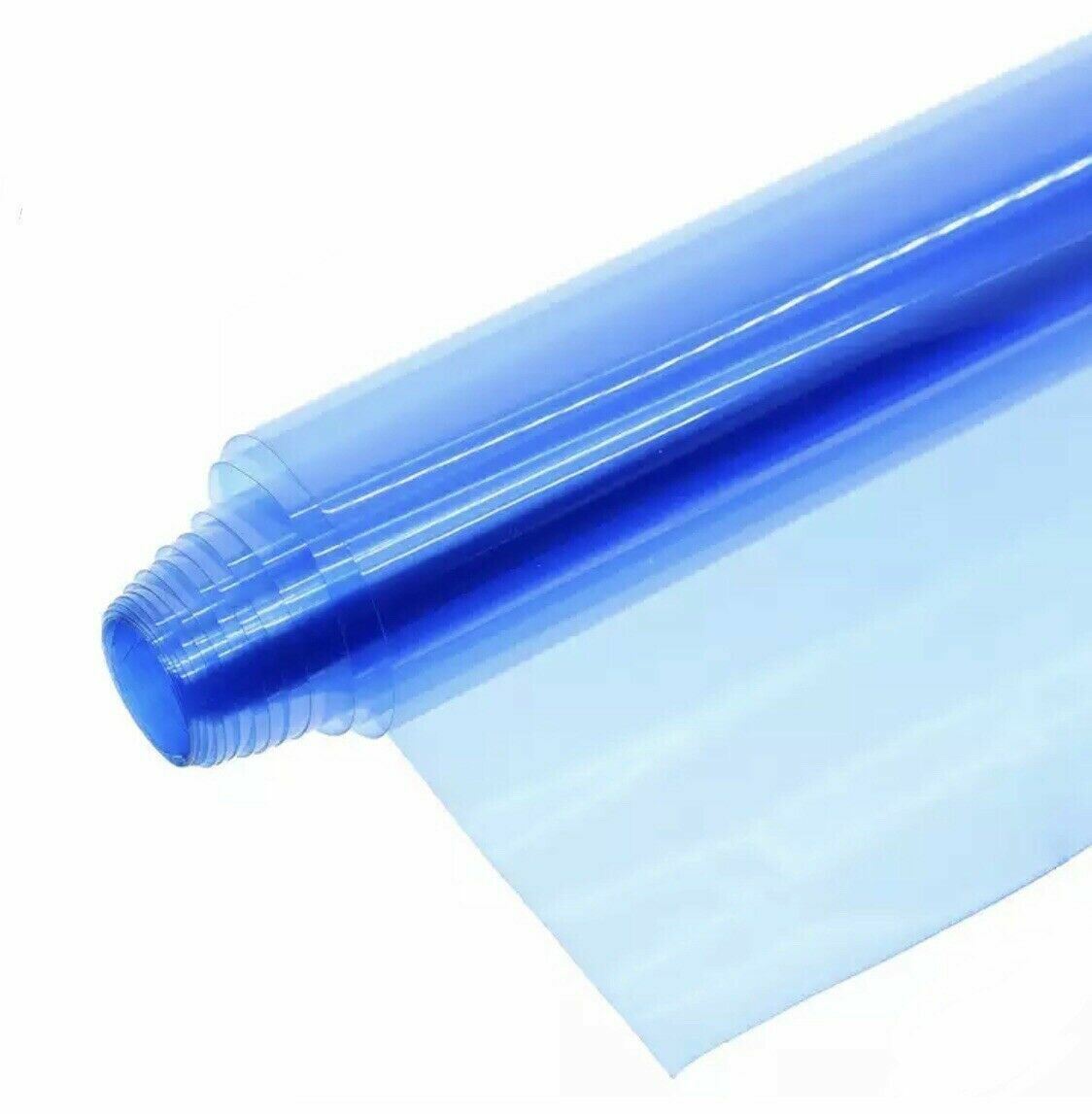
Преимущества технологии сухого пленочного фоторезиста
По сравнению с жидкими фоторезистами, сухие пленочные фоторезисты имеют ряд важных преимуществ:
- Высокая разрешающая способность (до 25 мкм)
- Равномерная толщина покрытия по всей поверхности
- Отсутствие краевых наплывов
- Высокая производительность процесса нанесения
- Отсутствие растворителей и летучих веществ
- Простота в обращении и хранении
- Возможность автоматизации процесса
Эти преимущества делают сухие пленочные фоторезисты оптимальным выбором для массового производства печатных плат высокой плотности.
Процесс нанесения сухого пленочного фоторезиста
Нанесение сухого пленочного фоторезиста на заготовку печатной платы осуществляется методом ламинирования с помощью специального оборудования — ламинатора. Процесс включает следующие основные этапы:
- Очистка и подготовка поверхности заготовки
- Предварительный нагрев заготовки
- Удаление защитной пленки с фоторезиста
- Прикатка фоторезиста к поверхности заготовки с помощью валиков
- Нагрев и прессование для обеспечения хорошей адгезии
- Охлаждение заготовки с нанесенным фоторезистом
Температура и давление в процессе ламинирования подбираются в зависимости от типа используемого фоторезиста и материала основания печатной платы.
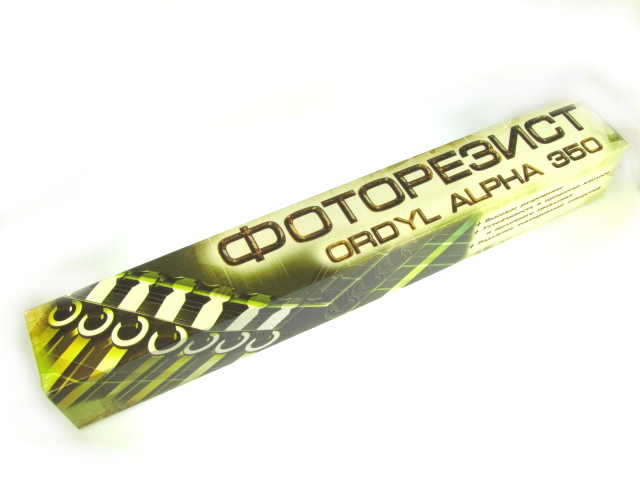
Экспонирование сухого пленочного фоторезиста
После нанесения фоторезиста выполняется его экспонирование через фотошаблон. Для этого используются специальные установки с ультрафиолетовыми лампами. Основные параметры процесса экспонирования:
- Интенсивность УФ-излучения
- Длина волны излучения
- Время экспозиции
- Расстояние между источником излучения и поверхностью платы
Правильный подбор параметров экспонирования критически важен для получения качественного изображения. Недостаточная экспозиция приводит к неполной полимеризации фоторезиста, а избыточная — к уширению линий рисунка.
Проявление сухого пленочного фоторезиста
После экспонирования выполняется проявление фоторезиста в щелочном растворе. В процессе проявления неэкспонированные участки фоторезиста растворяются и удаляются, формируя рисунок схемы. Основные параметры процесса проявления:
- Состав и концентрация проявителя
- Температура проявителя
- Время проявления
- Метод подачи проявителя (распыление, погружение)
Качество проявления контролируется визуально и с помощью микроскопа. После проявления выполняется промывка платы деионизованной водой и сушка.

Травление меди и удаление фоторезиста
Следующим этапом является травление незащищенных участков медной фольги в растворе хлорного железа или персульфата аммония. Фоторезист при этом выполняет роль защитной маски. После травления фоторезист удаляется в щелочном растворе.
Основные требования к процессу травления:
- Равномерность травления по всей поверхности
- Отсутствие подтравливания под маску фоторезиста
- Минимальное боковое подтравливание проводников
Качество травления контролируется визуально и измерением геометрических размеров элементов схемы.
Контроль качества печатных плат
На заключительном этапе производится контроль качества изготовленных печатных плат. Основные параметры, подлежащие проверке:
- Отсутствие дефектов рисунка схемы (обрывы, короткие замыкания)
- Соответствие размеров элементов проектным значениям
- Качество поверхности проводников
- Адгезия проводящего рисунка к основанию
- Толщина медного покрытия
Для контроля используются оптические микроскопы, измерительные микроскопы, тестеры неразрывности цепей и другое специализированное оборудование.
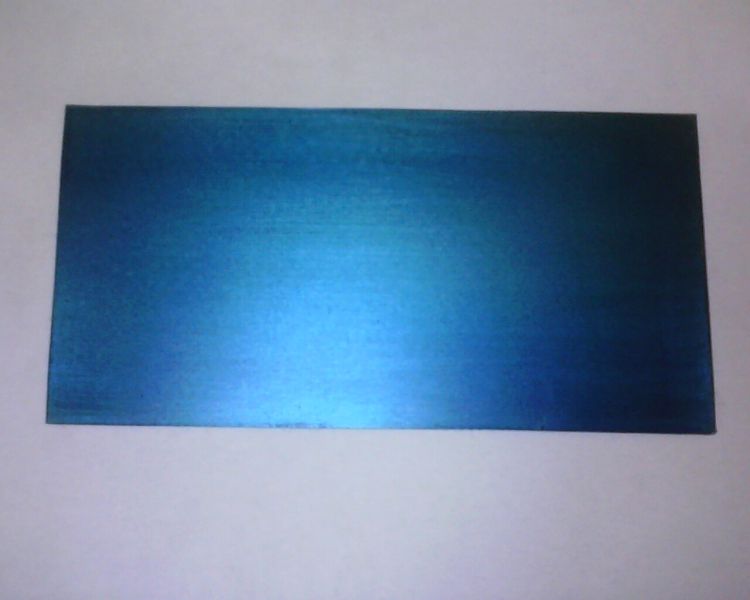
Рекомендации по работе с сухим пленочным фоторезистом
Для получения высококачественных печатных плат при использовании технологии сухого пленочного фоторезиста рекомендуется соблюдать следующие правила:
- Строго соблюдать технологические режимы на всех этапах процесса
- Использовать качественные материалы и химические реактивы
- Обеспечить чистоту рабочего места и оборудования
- Контролировать влажность и температуру в помещении
- Защищать фоторезист от воздействия УФ-излучения до момента экспонирования
- Своевременно обслуживать и калибровать оборудование
- Регулярно проводить контроль качества на всех этапах
Соблюдение этих рекомендаций позволит обеспечить стабильно высокое качество изготавливаемых печатных плат.
Области применения сухого пленочного фоторезиста
Технология сухого пленочного фоторезиста широко применяется в следующих областях:
- Производство многослойных печатных плат
- Изготовление гибких и гибко-жестких печатных плат
- Производство СВЧ-плат
- Изготовление прецизионных датчиков
- Производство солнечных элементов
- МЭМС-технологии
Благодаря высокой разрешающей способности и технологичности, сухие пленочные фоторезисты позволяют изготавливать печатные платы и электронные устройства с высокой плотностью монтажа.

Перспективы развития технологии сухого пленочного фоторезиста
Основные направления совершенствования технологии сухого пленочного фоторезиста:
- Повышение разрешающей способности (до 10 мкм и менее)
- Улучшение адгезионных свойств
- Повышение стойкости к агрессивным средам
- Разработка новых типов фоторезистов для специальных применений
- Автоматизация и роботизация процессов нанесения и обработки
Развитие технологии позволит создавать все более миниатюрные и сложные электронные устройства, отвечающие растущим требованиям рынка.
Профессиональные методы прототипирования печатных плат. Распечатать на принтере или фрезеровать, ни слова про утюг / Хабр
Наверняка каждый радиолюбитель сталкивался с необходимостью самостоятельно изготавливать печатную плату, ведь не всегда целесообразно оплачивать и ждать заказ из Китая. И наверняка держа в руках утюг, вы задавались вопросом: «а как-же обстоит дело с прототипированием печатных плат у профи, наверняка же у них есть какой-то волшебный прибор для этих целей?». Только представьте, нажал кнопку и без лишнего шума и пыли получил готовую печатную плату! И такие способы есть! Но в каждой бочке мёда есть своя ложка дёгтя.
В этой статье не будет переводов или информации из рекламных проспектов, будет только мой личный опыт изготовления печатных плат для прототипирования электроники на 3х осевом ЧПУ LPKF ProtoMat S63 и специализированном принтере Voltera V-One.
Введение
Как вы знаете, существует два основных метода изготовления печатных плат: аддитивный и субтрактивный.
Субтрактивный метод предполагает формирование токопроводящего рисунка путем удаление лишней меди с пробельных мест. Этот способ наиболее знаком радиолюбителям. С помощью «лазерного утюга» или пленочного фоторезиста наносится защитный рисунок, затем травим плату в хлорном железе или чем-то подобном. Также возможно удаление лишней фольги путем фрезерования. Для этих целей радиолюбители с помощью бубна используют обычные ЧПУ.
Аддитивные методы не предполагают использование медной фольги, токопроводящий рисунок как правило, наращивается электрохимическими методами. В радиолюбительской практике встречались попытки с токопроводящим клеем, но реально рабочей технологии я лично не встречал.
Для реализации обоих методов существует специализированное оборудование, о представителях которого далее и пойдёт речь.
Voltera V-One
Voltera V-One позиционируется как 3D принтер для полного цикла создания двухсторонних печатных плат и их сборки.
Технология очень заманчивая. Тем более, на тестовом образце все выглядит ну очень нарядно. В работе принтер выглядит просто завораживающе!
Изготовление платы включает в себя следующие этапы.
1. С помощью специализированного ПО обрабатываем гербер файлы печатной платы для управления принтером. ПО, к слову сказать, очень неплохое, ни чего общего не имеет с колдовством в ArtCAM и MACh4, если вы понимаете о чем я…
2. Устанавливаем в принтер заготовку из стеклотекстолита или иную подложку, заранее ее обезжирив и придав шероховатость с помощью мелкой наждачки. Подложка не имеет фольгированного слоя, т.к. проводники будут распечатаны. Производим калибровку принтера.
3. На принтер устанавливается шпиндель со сверлом, и он сам сверлит отверстия. Очень удобная опция, сверлить текстолит я не очень люблю.
4. Устанавливаем головку для печати с тюбиком спец пасты. И принтер распечатывает токопроводящий рисунок. Переворачиваем плату, калибруем принтер, и печатаем вторую сторону. Затем паста оплавляется нижним подогревом принтера. Получаем готовые печатные проводники в металле.
5. Меняем тюбик на паяльную пасту. Принтер наносит пасту на контактные площадки. Расставляем электронные компоненты. Включаем подогрев, паста оплавляется, компоненты припаиваются.
6. С помощью специальной оснастки запрессовываем медные гильзы в переходные отверстия. И собственно плата полностью готова. Остается только руками распаять выводные компоненты.
Согласитесь, идеальный план, это просто мечта для любого электронщика! Но а как же обстоит на деле?! А вот тут начинается просто бочка дегтя. На фотографии показан лучший результат, который смогли получить за день танцев с бубном.
Нормально откалибровать сопло экструдера так и не получилось, что только не делали. Добиться достаточной подачи пасты тоже не получилось, этот параметр настраивается и определяется скоростью выдавливания. Также оказалось достаточно сложно совместить отверстия с рисунком проводников. На следующем фото видно, что отверстия немного гуляют, где-то более-менее попадают по центру, а где-то совсем не попадают.
Про идею с гильзами для переходных отверстий я, пожалуй, просто не буду комментировать. Сами все видите. Только скажу, что каждый переход надо обязательно прозванивать.
Еще одна проблема связана с самим секретным составом печатных проводников. Как видно на картинках, паяльная паста при оплавлении не дает достаточного протекания. Замечу, что все расходные материалы были из одной коробки с принтером. Припаять что-то к плате паяльником практически не реально. Особенно если плата какое-то время полежала на воздухе, припой ни в какую к ней не берется.
Может быть нужно было проявить больше упорства и еще пару дней поколдовать с настройками, а может быть что-то с руками не то. Но в итоге я от этой затеи отказался. Дальше выводы делайте сами.
LPKF ProtoMat S63
LPKF ProtoMat S63 позиционируется как машина для изготовления моделей печатных плат. Думаю, что подробно описывать процесс фрезерования плат не имеет смысла, как работают ЧПУ вы и так знаете. Но на некоторых особенностях заострим внимание.
Я проработал с ним уже больше трех лет. И не смотря на ряд конструктивных недочетов и глюков, очень доволен этим станком. Удобное программное обеспечение. Отлично совмещает стороны. Сам подбирает подходящие фрезы и в процессе резки сам их меняет. Позволяет стабильно получать платы по третьему классу. При определенной сноровке можно добиться четвертого класса точности.
Кстати, если дооснастить станок специальной оснасткой, то он тоже сможет наносить паяльную пасту. Вот только выпечку сам не сможет.
Если вам будет интересно, про этот станок с его капризами я расскажу отдельно.
Заключение
Конечно «профессиональные методы» — это громко сказано. Ни один из рассмотренных станков не является профессиональным. Но и любительскими их назвать язык не поворачивается.
Voltera V-One очень интересная и привлекательная игрушка. Требует очень сложной настройки. Размер печатной платы совсем небольшой. Проводимость печатных проводников сильно отличается от меди, делать на нем что-то прецизионное или аналоговое можно даже не пытаться, печатная плата будет сильно искажать работу схемы. Мне кажется, что эта технология еще очень сырая, в своей работе я не готов этим пользоваться. Может быть такой принтер неплохо показал бы себя где-то в школьном кружке, чтобы собирать какие-нибудь небольшие шилды к ардуино. Я думаю, что приловчиться к нему и изготавливать небольшие односторонние платы вполне возможно. Обычно цифровые устройства не так требовательны к проводимости печатных проводников. И здорово, что он сам может сразу припаять электронные компоненты… наверное может…
Фрезеровка печатных плат на LPKF ProtoMat S63 — это отличный инструмент для прототипирования. Но тоже требует определенной сноровки. В отличии от обычных ЧПУ, этот станок неплохо оптимизирован под печатные платы. Также программная обработка герберов не занимает времени. У меня изготовление двухсторонней печатной платы с хорошей плотностью до дециметра площадью занимает до двух часов. Это позволяет оттрассировать, изготовить и собрать прототип печатной платы в пределах одного рабочего дня.
Оба этих устройства обладают идентичными недостатками. Стоимость оборудования просто космос. Подходят только оригинальные расходные материалы, которые тоже совсем недешевые. Итоговая стоимость печатной платы выходит дороже, чем заказать на производстве. Но потенциально это все прилично экономит время на проектирование. А как известно, дорога ложка к обеду.
Еще одна особенность прототипирования печатных плат в том, что чертежи требуют серьезной адаптации под технологию изготовления. Самое очевидное — это размеры переходных отверстий. Либо они делаются под гильзу, либо под пайку проволочной перемычки. Это сильно увеличивает наружный диаметр переходного отверстия. И тут либо размер платы придётся увеличивать, либо полностью все перетрассировывать для финальной версии.
Почему не стоит связываться с обычными трех осевыми ЧПУ для изготовления прототипов печатных плат? Ответ прост: при прототипировании мне необходима печатная плата, а не плясать с бубном над станком. Для меня этот вопрос был закрыт больше 15 лет назад, я пытался адаптировать ЧПУ для этих нужд, плюнул и перешел на пленочный фоторезист.
Почему бы не делать печатные платы, как и все нормальные радиолюбители, утюгом или фоторезистом? Тут тоже все просто. На предприятии даже из-за припоев и флюсов с санитарными службами могут возникнуть проблемы. А представьте теперь, что у вас появляется достаточно токсичная химия, которая требует специальных условий работы и утилизации. Это дома можно вылить остатки хлорного железа в унитаз, а юр лицо за это может схлопотать приличный штраф.
Текст вышел достаточно объемный. Если я что-то упустил, задавайте вопросы в комментариях, может быть на какие-то я смогу ответить. Спасибо за внимание!
Страничка эмбеддера » Пленочный фоторезист от Pah’а.

А вот и еще одна статейка от Pah’а. И, как всегда, спасибо ему огромное. —BSVi
В сети есть куча холиваров. Каждая сторона с пеной у рта доказывают правоту своей точки зрения. Кто-то спорит про преимущества ассемблера перед С, AVR перед PIC`ами, утюга перед фоторезистом, а мы с BSVi`ем спорили про то – что-же лучше пленочный резист или жидкий.
Сразу оговорюсь, я категорически за фоторезист, хотя пробовал ЛУТ только один раз в своей жизни пару недель назад и получил откровенное унылое неудовлетворение :). Я конечно понимаю, что это несовершенство моей технологии, бла-бла-бла, я видел множество качественных плат, сделанных ЛУТ`ом, но… но мне ужасно не понравился процесс, нестабильность результатов, да и при необходимости повторить хотя бы десяток плат моя врожденная лень возьмет верх. Да в промышленности юзают резист, а ведь это чего-то да стоит.
Этим способом я изготавливаю платы около 5 лет. Меня самого удивило, что качественный результат получился с первого раза.
Как я выбрал пленку? Когда я первый раз пришел в магазин, то хотел брать POSITIV 20, он был дороговат, и, для пробы, я решил взять стеклотекстолит с нанесенной пленкой. Я был очень доволен результатом. Я не трачу время на нанесение, сушку, и получаю отличный результат. Остальные плюсы я опишу в тексте. Мой резист выглядит как и все остальные, марку не знаю, можете не спрашивать, у нас он продается в листах А4
Фоторезист абсолютно не имеет запаха, он негативный. То есть остается то, что засветилось, шаблон надо делать негативным. Сверху на нем пленка, которая снимается перед проявлением, в отличии от резиста BSVi`я, снимается она за 0,0112 сек руками без всяких приспособлений и заклинаний)). Я просто провожу пальцем по краю перпендикулярно плоскости платы в сторону фоторезиста, и пленка отстает.
По поводу фотошаблона: я читал про кальку, но у меня так ни разу и не получилось ее использовать, она жевалась принтером, тонер некачественно прилипал. С первого раза я решил попробовать пленку для печати, и результат меня устроил. Вообще же я складываю пленку в два раза обычно, но я делал и в один. Так-же, я делал на офисной бумаге, один раз вышло нормально, но плата была покрыта медью во всех свободных местах, во второй раз половина платы сползла. Но это было от безысходности, так, для общего развития.
Далее, готовим шаблоны. Как я уже говорил, я обычно их складываю в два слоя, один для пробы решил сделать в один слой. Склеиваю я их обычным скотчем по одной стороне, я думаю все ясно из рисунка:
При засветке я использую обычную УФ лампу под цоколь E-27, никаких трубок с балластами, а тем более кварцевые лампы я не использую.
Для засветки, я соорудил следующий ядреный коллайдер:
Стекло – обыкновенное оконное 3мм, все отлично засвечивается, свечу я 1 минуту, этого достаточно. Далее все ясно- ложим шаблон на стеклотекстоли и светим 🙂
Для проявки, я использую кальцинированную соду (бикарбонат натрия, если кто не в курсе), концентрацию никогда не контролирую, емкость — обычно лоток из под мяса, ложу от пол чайной ложки, до одной. В этот раз проявлял около минуты (чуть меньше), перепроявить достаточно трудно, если минут 5 полежит- у меня ничего не отставало, при проявке – провожу губкой, достаточно удобно, количество соды видно на фотографии:
После проявки получаем следующее(напомню, что один шаблон мы делали в один слой):
Да… Факир был пьян, и фокус не удался… Та плата, что в один слой — явно не получилась. Для отмазки представляю другую, шаблон так же сделан в один слой:
Травлю я в своей травилке, единственное — шланг у нее забивался, и я поставил аквариумный распылитель, больше таких проблем не было, да «пузыристость» повысилась — стала более насыщенной. Перед травлением опускаю плату в хлорное железо на несколько секунд, и контролирую качество проявки- в недопроявленных местах медь будет более светлая(блестящая):
При травлении процесс контролирую следующим образом- за травилкой ставлю настольную лампу, и на просвет наблюдаю ход травления. Таким образом, я не вытаскиваю плату, да и видно лучше- тончайший слой меди уже не просвечивается. Правда в этот раз у меня хлорное железо превратилось в какое-то зеленное зелье и оно не просвечивалось (древнее как фикалии мамонта), хотя такой случай был впервые.
После травления получаем результат:
Дорожки 0,1 мм получаются без усилий, расстояние между ними тоже, но при этом приходится при проявке использовать зубную счетку, что б не осталось лака между дорожками.
Ввиду ограниченности времени, продолжим немного попозже.
Разработка технологии и применение сухого пленочного фоторезиста
%PDF-1.7 % 1 0 объект > /Метаданные 2 0 R /Контуры 3 0 R /Страницы 4 0 Р /StructTreeRoot 5 0 R /Тип /Каталог /ViewerPreferences > >> эндообъект 6 0 объект Полупроводники — травление) /Заголовок (Технология разработки и нанесения сухого пленочного фоторезиста) >> эндообъект 2 0 объект > транслировать приложение/pdf

Полупроводники — Травление

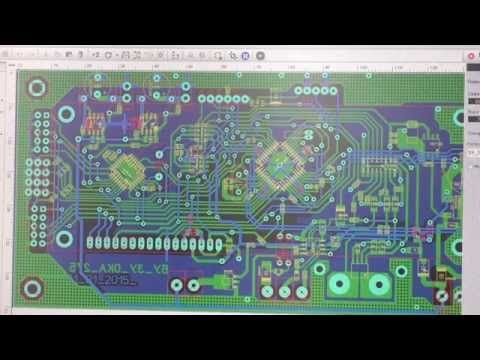
yj||v[i4N..Ʌ?+~u?T>,{[>|{|/Vڽws҉,vԍlQN>yA»ç?Tn3䙨E1{f6 *g;GxZӖ=8сFk»t _+%ѸƧh\Qr=’ JMVBRcƌjLpBFk8`0Ӊճ[ÿ-30E)uǟVdJ>>C0MyN2BP)>İoj;n&9Y +I& h%W*{j/o>V3(rx6Nwmzy!=0Lg:=JclHP9a:m m_g:c)l(S|c’
*Q8