Как правильно развести печатную плату. Какие существуют типы печатных плат. Как выбрать оптимальное количество слоев. Какие есть тонкости при разводке аналоговых и цифровых схем. На что обратить внимание при проектировании высокочастотных устройств.
Основные типы печатных плат и их особенности
Существует несколько основных типов печатных плат (ПП):
- Односторонние ПП — самые простые и дешевые, но имеют низкую плотность монтажа
- Двусторонние ПП — наиболее распространены, обеспечивают хороший баланс между стоимостью и функциональностью
- Многослойные ПП — позволяют достичь высокой плотности монтажа, но более дороги в производстве
При выборе типа ПП нужно учитывать сложность схемы, требуемую плотность монтажа, условия эксплуатации устройства и стоимость производства. Для большинства любительских проектов оптимальны двусторонние платы.
Особенности разводки аналоговых схем
При разводке аналоговых схем важно соблюдать ряд правил:

- Разделять цепи питания и сигнальные цепи
- Минимизировать длину сигнальных проводников
- Использовать заземляющие полигоны для экранирования
- Размещать блокировочные конденсаторы максимально близко к микросхемам
- Избегать образования замкнутых контуров в проводниках
Соблюдение этих правил позволяет минимизировать наводки и помехи в аналоговых схемах.
Тонкости разводки цифровых схем
При проектировании цифровых устройств нужно обратить внимание на следующие моменты:
- Согласование импедансов линий передачи сигналов
- Минимизация длины критичных по времени сигналов
- Использование развязывающих конденсаторов по питанию
- Правильная разводка тактовых сигналов
- Экранирование высокочастотных сигналов
Для высокоскоростных цифровых схем часто требуются многослойные платы с выделенными слоями питания и земли.
Выбор оптимального количества слоев печатной платы
Количество слоев ПП влияет на сложность разводки, стоимость производства и электрические характеристики платы. Общие рекомендации по выбору числа слоев:

- 2 слоя — для простых схем и прототипов
- 4 слоя — оптимально для большинства проектов средней сложности
- 6 и более слоев — для сложных высокочастотных устройств
При этом увеличение числа слоев не всегда оправдано — часто лучше оптимизировать компоновку на меньшем числе слоев.
Особенности проектирования высокочастотных устройств
Разработка ВЧ и СВЧ устройств требует учета дополнительных факторов:
- Использование специальных ВЧ материалов для плат
- Расчет волнового сопротивления линий передачи
- Минимизация паразитных емкостей и индуктивностей
- Экранирование критичных цепей
- Оптимизация топологии для минимизации отражений сигналов
Для ВЧ устройств часто применяют специализированные САПР, учитывающие особенности распространения ВЧ сигналов.
Автоматическая и ручная трассировка: преимущества и недостатки
Современные САПР предоставляют возможности как автоматической, так и ручной трассировки плат. Основные особенности:
- Автотрассировка позволяет быстро получить результат, но часто требует доработки
- Ручная трассировка дает наилучший результат, но требует больше времени
- Оптимально сочетание автоматической и ручной трассировки
- Для критичных цепей рекомендуется ручная трассировка
Выбор метода трассировки зависит от сложности схемы, требований к качеству разводки и доступного времени на проектирование.

Технологические ограничения при проектировании печатных плат
При разработке топологии ПП нужно учитывать ограничения технологического процесса изготовления:
- Минимальная ширина проводников и зазоров
- Минимальный диаметр отверстий
- Допуски на размеры элементов платы
- Ограничения по соотношению сторон отверстий
- Минимальное расстояние между проводниками разных слоев
Несоблюдение технологических ограничений может привести к браку при производстве плат или проблемам при монтаже компонентов.
Современные тенденции в проектировании печатных плат
Развитие технологий производства и монтажа электронных устройств влияет на подходы к проектированию ПП:
- Уменьшение проектных норм до десятков микрон
- Применение встроенных пассивных компонентов
- Использование гибких и гибко-жестких плат
- 3D-MID технологии для создания трехмерных схем
- Технологии монтажа кристаллов непосредственно на плату
Новые технологии позволяют создавать более компактные и функциональные устройства, но требуют применения специализированных САПР и производственных процессов.

Мини-FAQ по разводке печатных плат, особенно аналоговых. [Вегалаб-Викизона]
Коротко о проектировании печатных плат для преимущественно аналоговых устройств.
Во-первых, несколько слов о разводке цепей питания, особенно при двуполярном питании.
Распространенная ошибка: емкости блокировки по «+» и по «-» питаний аналоговых микросхем (напр. ОУ) брошены на земляной слой далеко друг от друга, в результате чего по земляному слою течет контурный ток потребления. «Физика» тут простая — при усилении больших сигналов, выходные каскады практически всех аналоговых микросхем переходят в режим AB, и токи потребления по отдельным («+» и «-») цепям питания начинают содержать много высших гармоник сигнала. При несовпадении мест заземления блокировочных конденсаторов для «+» и «-», эти токи начинают «растекаться» по земляным цепям, формируя помеху в них. Именно поэтому блокировочные емкости от «+» и «-» в подавляющем большинстве случаев надо стараться располагать так, чтобы расстояние между точками их присоединения к земляному слою было минимальным.
На величине (номинале) керамических конденсаторов, если они используются совместно с оксидными, экономить не следует, т.к. рекомендации по установке «0,1 мкФ» давно устарели — ESR современных оксидных конденсаторов номиналом 100…220 мкФ снизилось до величин менее 0,1 Ома, поэтому для предотвращения появления явного резонанса на индуктивности монтажа (~10…20 нГн) сейчас требуется значительно бОльший номинал «высокочастотных» емкостей, ОТ 0,68…1 мкФ. 2)}$.
Резисторы в цепях питания каждой ИМС сильно упрощают разводку, т.к. служат перемычками, и позволяют «+» и «-» питания развести вплотную друг к другу, что весьма желательно для снижения излучений сигнальных/выходных токов цепями питания.
Увеличивать ширину шин питания (до резисторов) в малосигнальных цепях выше примерно 0,5…0,7 мм нет никакого смысла, ширину слаботочных сигнальных проводников (кроме СВЧ согласованных линий) как правило, тоже нет смысла делать больше, чем это нужно для обеспечения технологичности плат (0.127…0.254…0.508 мм в зависимости от возможностей производства). БОльшая ширина лишь увеличивает паразитные емкости. Исключения из этого правила: при разводке плат без металлизации отверстий контактные площадки приходится делать как можно бОльшего размера для обеспечения механической прочности, с той же целью на однослойных платах уширяют дорожки там, где это возможно. Если есть место, то шины земли (а иногда и питания) вполне можно уширять, вплоть до сплошной «заливки» медью (формирование полигонов).
Далее, весьма желательно разделять «сигнальную» и «силовую» земли, чтобы избежать протекания токов питания/нагрузки/помех по «сигнальной» земле. В простых (чисто аналоговых) схемах это элементарно делается на 2-слойной плате, чуть сложнее — на «1,5» слойной (однослойной с навесными шинами/перемычками). В более сложных случаях (запутанная схема, много источников питания, высокая плотность монтажа) проще воспользоваться двухслойной или «2,5» — слойной платой, то есть поставить дополнительные близко расположенные шины питаний/земли на плату, как это часто делалось на платах старых компьютеров и даже в хорошей бытовой технике. Если нет требований по жестким условиям эксплуатации и в схеме нет высокоомных или особо критичных к паразитным емкостям цепей, то в большинстве случаев сегодня наиболее практичным вариантом будет использование многослойной платы (особенно, если серия невелика).
Как уже говорилось, для подавления перекрестных помех по «земле» в низкочастотных устройствах цепи «земли» следует разделять на «сигнальные» (для разводки которых, как правило, используется правило «звезды», с использованием проводников обычной ширины) и «силовые» (которые лучше разводить «сеткой», широкими трассами — полигонами или выполнять в виде по возможности цельного слоя). Соединяют их в одной точке («мекке»), обычно около «земли» входного (иногда — выходного) разъема. В многоканальных устройствах можно сделать несколько «сигнальных» земель, свою для каждого канала.
В ВЧ устройствах есть своя специфика — там, как правило, нужна минимальная индуктивность именно «сигнальной» земли, однако «развязать» сигнальную и силовую земли практически невозможно (из-за сильной индуктивной связи), поэтому их, как правило, не разделяют, а объединяют в общий сплошной слой без сколько-нибудь больших разрезов.
Существует также изящный (но весьма трудоемкий) метод подавления помех по «земле» без явного разделения земель, особенно полезный при использовании двусторонних плат — максимальное сохранение цельного слоя «земли» на одной из сторон (т.е. фактически однослойная разводка схемы на другой стороне, с минимумом «перемычек»), тщательный анализ контуров протекания токов питания по этой земляной плоскости и нахождение эквипотенциальных точек, т.е. точек, разность потенциалов между которыми при протекании по «земле» токов в цепях питания/нагрузки остается близкой к нулю. Эти точки и используются в качестве выводов «сигнальной» земли. Вид контуров протекания токов при необходимости можно изменять, вводя дополнительные разрезы или наоборот, делая перемычки в возникших по условиям разводки разрезах земляного слоя.
Самое подробное изучение вопросов топологии/протекания токов и т.п. было выполнено при создании методик проектирования устройств, устойчивых к ЭМИ импульсу, возникающему при взрыве ядерных боеприпасов или ЭМИ-генераторов импульсного действия. К сожалению, публикации на эту тему разрознены, и к тому же часто до сих пор «под грифом». Одну из иллюстративных статей я отсканировал, но не могу сюда прикрутить — выбран лимит на число вложений.
О конструировании ПП. Необходимо сразу отметить, что иногда встречающийся прямолинейный подход — «чем больше слоев — тем лучше» — для чисто аналоговых (а частично и для цифровых) схем «не катит». Слишком много привходящих факторов.
Одно/двухслойные ПП на гетинаксе/стеклотекстолите без металлизации отверстий — в настоящее время адекватны только для очень простых устройств в большой (»10000) серии. Главные минусы — низкая надежность в жестких условиях эксплуатации (из-за отслоения контактных площадок/проводников при механических вибрациях и термоциклах, набора влаги/флюсов через стенки отверстий), а также сложность (и дороговизна) качественной разводки сколько-нибудь сложных схем. Плотность монтажа низкая (обычно не более 3…4 выводов на квадратный сантиметр общей площади платы). Достоинство — крайняя простота и дешевизна в производстве (при больших объемах и проектных нормах порядка 0.38 мм — менее $0.3/кв. дм) за счет отсутствия металлизации и возможности замены сверления отверстий их пробивкой.
Двухслойные ПП с металлизацией отверстий — наиболее надежны в жестких условиях эксплуатации, имеют самые лучшие «изоляционные» свойства, наименьшие паразитные емкости проводников. Могут быть изготовлены с наименьшей общей толщиной и с наиболее жесткими проектными нормами, наиболее прочны механически при равной толщине. Но организовывать сплошные слои земли/питания на них сложно, обычно удается сделать более-менее сплошным только один слой, как правило, «земли», и то при плотной разводке это требует немалых трудозатрат.
Однако тот факт, что достаточно плотная (с шагом порядка сантиметра), даже не очень регулярная, решетка межсоединений «земли»/питаний по эффективному импедансу (паразитной индуктивности) мало уступает сплошному слою вплоть до частот порядка 60…100 мегагерц, позволяет обходиться двухслойными (наиболее надежными) платами при разработке достаточно сложных и плотно скомпонованных устройств (с плотностью выводов 10…12 и более на кв. см. общей площади платы). При грамотной разводке, естественно.
Главный минус двухслоек — трудоемкость (дороговизна) разработки действительно качественной топологии. Эквивалент платы, которая на 4-6 слоях разводится по типовым инструкциям студентом в течение нескольких часов (нередко в полуавтоматическом режиме), в двухслойном исполнении требует от нескольких дней работы квалифицированного специалиста. Внесение даже относительно небольших изменений в двухслойном варианте, в отличие от многослойного, может оказаться нетривиальным и потребовать почти полной переделки проекта.
Поэтому применение двухслойных плат для сложных устройств оправданно в основном в двух случаях.
Первый случай — обеспечение предельно высокой надежности и улучшение «аналоговых» характеристик платы (минимизация утечек, паразитных емкостей и т.п.).
Второй случай — достаточно большой тираж устройства, когда разница в цене плат и уменьшение потерь на брак после сборки перекрывают рост стоимости разработки/доводки конструкции. Разница в цене 2 и 4…6-слойных печатных плат с проектными нормами 0.127 в промышленных количествах составляет всего $1.6…2 за кв. дм, брак многослоек хорошего качества после печной пайки порядка нескольких десятых долей процента, поэтому идея сэкономить, применив двухслойку, может сработать только при тираже от ~500…1000 штук.
В мелкой же серии, как правило, проще и на круг дешевле сделать многослойку, несмотря на то, что «аналоговые» свойства (типа паразитных емкостей на единицу площади проводника и качества изоляции) из-за меньших толщин диэлектрика и ряда других причин у них существенно (в разы) хуже, чем у двухслойных плат. По этим причинам в настоящее время повышение коммутационных возможностей ПП стараются производить не столько за счет роста числа слоев свыше 4…6 (8), сколько путем ужесточения проектных норм — это снижает емкости проводников. Сегодняшний стандарт на ширину проводников и зазор между ними — 0.127…0.102 мм, уже не редкость и 0.076. Советские «0.3…0.25 мм» — для плат под обычные условия применения давно стали достоянием истории.
Соответственно, двухслойная плата, но с проектными нормами 0.102…0.076 обычно позволяет обеспечить бОльшую плотность цепей, чем 4-слойная с проектными нормами 0.15…0.25. Причина далеко не пропорционального роста плотности разводки при увеличении числа слоев состоит в том, что контактные площадки переходных отверстий, диаметр которых намного больше ширины проводника, «рубят» каналы трассировки (одно отверстие мешает прокладке ~3 трасс в каждом из слоев).
Использование многослойных плат становится технически необходимым в основном при создании сильно высокочастотных (» 200 МГц) и одновременно плотно скомпонованных цифровых и цифро-аналоговых устройств (чисто аналоговые, типа радиочастотных усилителей/модуляторов/детекторов, прекрасно живут и на двух слоях) или при применении микросхем с высокой плотностью выводов (особенно в корпусах BGA).
Основная проблема многослоек, кроме худших параметров изоляции — значительно худшая долговременная надежность контактов к внутренним слоям в жестких условиях эксплуатации (вибрации, механические нагрузки, термоциклирование), особенно когда это отверстия для впайки механически нагруженных штыревых компонентов (например, разъемов). Электротест тут не очень помогает, т.к. выявить все платы с потенциально ненадежными переходными отверстиями сразу после изготовления (и забраковать) практически невозможно. Вызвано это тем, что контакт к внутренним слоям в подавляющем большинстве случаев осуществляется только по тонкому (обычно не более 35 мкм, сейчас чаще 18 мкм) торцу фольги в отверстии. Разница в температурных коэффициентах расширения и модуля Юнга диэлектрика и меди при вибрациях и термоциклировании приводят к образованию отслоений/срезов металлизации. В «мягких» условиях это сказывается меньше, однако деградация плат в эксплуатации остается одной из основных причин отказов, к примеру, материнских плат ноутбуков. Причина разницы в надежности соединений с внешними и внутренними слоями в том, что при металлизации отверстий в производстве плат, металлом покрываются не только стенки отверстий, но и дорожки на внешних слоях, образуя своего рода «пустотелую заклепку». Именно поэтому в жестких условиях эксплуатации двухслойка оказывается гораздо надежнее многослоек — даже отслоение металлизации от стенок отверстий не ведет к нарушению контактов.
Существует технология изготовления многослоек склейкой уже просверленных и металлизированных двухслойных заготовок, когда переходы между парными слоями столь же надежны, как и в двухслойках, и при этом не занимают места на остальных слоях. Но такая технология дорога, сильнее подвержена ошибкам совмещения слоев и не очень проста в разводке, поэтому используется редко.
Большинство многослойных плат в мире производится с только сквозными отверстиями (плюс иногда микровиа, см. ниже). Ранее (до широкого распространения технологии microvia) было также популярно применение «глухих» отверстий, когда отверстие в плате сверлится не насквозь, а только на небольшую глубину — для формирования переходов с наружных на один-два нижележащих слоя. Для повышения надежности контакта к внутренним слоям, кстати, часто перед металлизацией специально травят диэлектрик (растравливают отверстия), чтобы фольга внутренних слоев слегка выступила внутрь отверстия и лучше покрывалась при металлизации (при применении такой технологии внутри металлизированных отверстий видны небольшие сужения в местах выхода фольги внутреннего слоя).
В сочетании с дублированием отверстий это позволяет гарантировать достаточную для критических приложений надежность контактов.
Существуют и «эксклюзивные» варианты, к примеру, мне однажды пришлось делать 18-слойную ПП (точнее, многокристальный модуль) общей толщиной 2.6 мм с несколькими видами диэлектриков, проектными нормами проводник/зазор в одном из слоев вплоть до 0.038 мм, скрытыми микропереходами и диаметром сквозных переходных отверстий менее 0.1 мм. Однако надежность этих плат по термоциклированию оказалась существенно ниже (чего изготовитель и не скрывал), а стоимость и сроки поставки — много выше, чем для типовых решений.
Практически при разводке многослойных плат внутренние слои желательно отдавать под цепи земли/питания, разводя сигнальные проводники на внешних слоях, а также по возможности дублировать переходные отверстия, ведущие на внутренние слои, тем более что это снижает паразитную индуктивность цепей земли/питания. Естественно, надежность контакта в любых переходных отверстиях можно повысить путем их дублирования при разработке топологии, для ответственных цепей это иногда даже прямо предписывается правилами проектирования.
Требования по повышению плотности монтажа при сохранении надежности в производстве BGA корпусов и портативной техники привели к разработке технологии микропереходов (microvia), когда кроме обычных (сквозных) переходных отверстий на плате с одной или обоих сторон формируются (обычно лазером) глухие отверстия-переходы на нижележащий слой, металлизируемые в одном цикле с металлизацией сквозных отверстий. Размер контактной площадки под такой переход (0.2…0.35 мм) гораздо меньше, чем под сквозное или «глухое» отверстие, и не нарушается трассировка в остальных слоях. К тому же в ряде случаев microvia может быть размещен прямо на контактной площадке SMD элемента без риска ухода заметной части припоя в отверстие ввиду его малого размера и глубины (не более 0.1…0.15 мм). Это очень сильно повышает плотность разводки, т.к. обычные переходные отверстия на площадках SMD элементов размещать, как правило, нельзя (или приходится применять т.н. «забивку» или закрытие отверстий медью, что сложно и дорого). Microvia можно также сформировать и во внутренних слоях, но это существенно сложнее и дороже в производстве.
Несколько слов про толщину меди и покрытия плат. Основная часть плат делается на материалах с толщиной фольги 35, 18 и 9 мкм, при этом во время металлизации отверстий на наружных слоях наращивается еще по 15-25 мкм меди (в отверстиях должно быть ~ 20 мкм). Платы с проектными нормами 0.127 и менее часто делаются на материале с толщиной фольги ~9 мкм (чем тоньше фольга, тем меньше искажение формы рисунка из-за бокового подтрава проводников). Беспокоиться о «малости сечения меди» не стоит, т.к. печатные проводники ввиду хорошего охлаждения допускают гораздо бОльшие плотности тока (~100 А/кв.мм), чем монтажный провод (3…10 А/кв. мм). Итоговая толщина во внешних слоях за счет осаждения меди при металлизации отверстий, естественно, оказывается больше, чем у исходной фольги. Cопротивление плоских проводников зависит от их геометрии в плане по простому закону: сопротивление квадрата х число квадратов. Сопротивление квадрата не зависит от его абсолютного размера, а только от толщины и проводимости материала. То есть, сопротивление проводника шириной 0,25 мм и длиной 10 мм (т.е. 40 квадратов) такое же, как при ширине 2,5 и длине 100. Для медной фольги 35 мкм это около 0,0005 Ом/квадрат. На промышленных платах при металлизации отверстий на фольгу наращивается дополнительный слой меди, так что сопротивление квадрата падает еще процентов на 20 по сравнению с приведенным выше. Облуживание же, даже «жирное», мало влияет на сопротивление, его цель — повысить теплоемкость проводников, чтобы они не сгорали от кратковременного ударного тока. Применяя коррекцию фотошаблонов (т.е. вводя поправки на подтравы) и анизотропное травление, изготовителям удается обеспечить производство плат с толщиной исходной фольги до 30-40% от проектных норм, т.е. при использовании самой толстой фольги 105 мкм (а с учетом осаждения меди — где-то 125-130 мкм) проектные нормы могут быть только от 0.3…0.35 мм.
Более существенным ограничением для силовых схем является то, что допустимый ток, пропускаемый через переходное отверстие, зависит в основном от его диаметра, так как толщина металлизации в нем невелика (15…25 мкм) и, как правило, не зависит от толщины фольги. Для отверстия диаметром 0.5 мм при толщине платы 1.5 мм допустимый среднеквадратичный ток порядка 0.4 А, для 1 мм — примерно 0.75 А. При необходимости пропустить по переходным отверстиям бОльший ток рациональным решением будет использование не одного большого, а набора мелких переходных отверстий, особенно при их плотном размещении в «шахматном» или «сотовом» порядке — в вершинах сетки из ромбов или шестиугольников. Дублирование переходных отверстий также дает выигрыш в надежности, поэтому часто применяется и в критических цепях (в том числе сигнальных) при разработке аппаратуры для особо ответственных применений (например, систем жизнеобеспечения).
Покрытия проводников плат бывают изолирующие и/или защитные. «Паяльная маска» — это защитное изолирующее покрытие, в котором сформированы окна в местах контактных площадок. Проводники могут быть оставлены медными, или покрыты слоем металла, защищающего их от коррозии (оловом/припоем, никелем, золотом и пр.). Каждый вид покрытия имеет достоинства и недостатки. Покрытия бывают тонкослойные, толщиной в доли микрона (как правило, химические), и толстослойные (гальванические, горячее лужение). Паяльную маску лучше всего наносить на голую медь или тонкослойное покрытие, при ее нанесении на луженые дорожки она держится хуже и при пайке проявляется капиллярный эффект — затекание припоя/отрывы маски. Золотое покрытие бывает обоих видов, химическое (тонкое) и гальваническое (требующее для своего выполнения электрического соединения проводников, например, на разъеме). В крупносерийном производстве также популярен вариант покрытия чисто медных (нелуженых) контактных площадок плат флюсоподобным лаком (organic coating, OSP). Выбор вида покрытия зависит от технологии монтажа и типа деталей. Для ручного монтажа (и автоматического при деталях типоразмера от 0805 и крупнее) в подавляющем большинстве случаев оптимальный вариант — горячее лужение площадок (HASL) с маской по меди. Для более мелких деталей и автоматического монтажа, если нет требований по особо малым утечкам на плате, один из лучших вариантов — химическое (иммерсионное) золото (Flash Gold) или иммерсионное олово.
Химзолото стоит в нормальном мире очень дешево, практически столько же, сколько горячее лужение, и при этом обеспечивает идеально ровные посадочные места для элементов, без бугорков припоя. Однако при изготовлении плат в РФ зачастую лучше заказывать покрытие не иммерсионным золотом, а иммерсионным оловом или серебром — их растворы не так экономят. При пайке плат с тонкими покрытиями, в том числе Flash Gold, их надо паять быстро и/или заливать нейтральным флюсом во избежание окисления меди через поры покрытия, а при автоматической пайке — желательно еще и использовать среду нейтрального газа (азот, фреон).
Ниже приложена наиболее доходчивая (на мой взгляд) литература по данному вопросу, а также пример двухслойной компьютерной платы разработанного мной около 10 лет измерителя микропрофилей (профилометра), в которой меры по обеспечению качества топологии применены без фанатизма, только частично. Однако и этого оказалось достаточно, чтобы безо всяких экранировок, в работающем ПК с его помехами (и собственной силовой частью — управлением коллекторным двигателем) обеспечить разрешение в несколько атомов, многократно превзойдя требования ТЗ (использованные ОУ — всего лишь TL084/LM324). Прибор выпускался до самого последнего времени и был единственным в РФ профилометром 1 класса точности.
Сергей Агеев ака sia_2
Работа в Eagle CAD. Часть 3. Автоматическая трассировка плат
Ленивый я стал, раньше все разводил ручками. А сейчас, делая плату с тремя микрухами логики и одним мелким проциком, понял, что одним слоем я никак не обойдусь. А раз так, то гулять так гулять. В Eagle есть автотрассировщик который довольно шустро разводит по двум слоям и при этом имеет много настроек, постараюсь дать их описание, а также общие рекомендации по трассировке.
Расставляем компоненты
Один из главных недостатков Eagle CAD — отсутствие авторасстановщика компонентов. Это минус, т.к. от оптимальной расстановки зависит очень много. Но не беда, расстановку можно делать и вручную, главное делать это сразу же, по мере добавления деталей на схему. Словно мы хотим развести все вручную. Если сначала нарисовать схему, а потом пытаться расставить, то получится такая каша, что понять что то там будет совсем нереально. А так мы сожрем этого слона по кусочкам, сильно облегчив автороутеру жизнь.
Был у меня вот такая схема:
зазырить в полный рост
Не бог весть какая сложная, но тем не менее в ней хватает дискретной логики, а логику разводить всегда мерзко. Врукопашную на нее ушел бы весь вечер, не меньше.
После ручной расстановки получилось что то похожее на это:
Параметры DRC я выставил исходя из условий изготовления джедайским лазерным утюгом. А именно — зазоры 0.3мм, минимальная дорожка 0.2мм, пятачки и переходки побольше, чтобы не меньше чем 1.8мм в диаметре — мне еще их без станка сверлить и попадать переходки между слоями.
Осталось нажать кнопу Auto (Автотрассинг) и настроить параметры трассировки:
Сразу скажу, что я хоть и знаю что значит большинство параметров, но сказать как лучше их выстроить не подскажу. У меня не очень большой опыт работы с этим трассировщиком (предпочитаю юзать Топор)
Вкладка General
- Preferred Direction — предпочтительное направление по слою. Стратегия трассировки довольно проста — по одному слою мы идем в одну сторону, а по другому перпендикулярно. Исходя из этого, любую схему можно теоретически развести без пересечений. На практике — утыкаемся в дырки, детали, и толщину проводников и все не так гладко. Но в целом идея ясна. Обычно поверху идем вертикально, по низу горизонтально. Хотя можно и поменять.
- Routing Grid — шаг сетки. Чем мельче, тем роутеру проще будет, но тем больше у него вариантов, а значит трассировка будет дольше.
Минимальный шаг 0.8mil вроде бы. Я обычно ставлю 2mil
- Via shape — форма переходных дырок. Обычно делаю круглые, они обходятся проще. Но квадратную сложней сорвать при сверлении т.к. ее площадь квадрата при равном радиусе (Вспомнилось тут… «К верхнему днищу бака приварено треугольное отверстие диаметром три на четыре». Гы гы) будет больше, а значит она крепче будет за текстолит держаться. Для наколеночного производства это критично.
Содержимое всех дальнейших вкладок одинаковое, поэтому я вначале опишу что там зачем, а потом расскажу, что внутри можно подкрутить.
Вкладка Follow-me — настройка полуавтоматического трассировщика. Задает стратегию работы инструмента Follow-me. Т.е. когда тыкаешь начало и конец трассы, а трассер сам тебе предлагает вариант прокладки маршрута.
Вкладка Busses — стратегия прокладки шин. Помните, что можно кидать на схемотехнике шины. Синая такая линия. К которой подсоединяются именованые проводнички. Она не только визуально направляет взгляд и дает соответствие схемы гостам, но и как бы обьединяет проводники в шину, что учитывается трассировщиком. Шины разводятся в первую очередь.
Route — первичная трассировка. Идет сразу после шин. Пробрасывает как бы черновой вариант.
Optimize1…n — Оптимизации чернового варианта, подгон их под заданные параметры. Т.е. если в черновом варианте у нас стопитцот дырок получилось, но нам это совсем не надо, то в оптимизациях мы задаем правила, чтобы число дырок от итерации к итерации снизить к минимуму. За один прием сразу это сделать не получится, орел же птица, а у птиц мозга немного. Поэтому тут нужна целая стая последовательных оптимизаций — коллективный разум. Их там можно вручную надобавлять очень много. Но и ждать придется долго. Я бывало и на ночь ставил 🙂
А теперь о том, что внутри вкладок и что за что отвечает. А там цены действий. Орел птица не только гордая, но и жадная. Поэтому при трассировке оперирует понятием цены. Если мы сказали, что много дырок слишком дорого, то он будет пытаться дырки избегать, чтобы снизить цену.
Layer Cost — цена слоя. Можно указывать приоритет одного слоя над другим. Например, можно нижний слой сделать очень дешевым, а верхний очень дорогим. В результатет разводка пойдет по максимуму внизу, а сверху разве что перемычек настрогает. Но тут тоже не все так просто, одной ценой слоя не обойтись.
Maximum — разные максимумы
- Via — максимальное число переходных дырок. На Route можно поставить и побольше, а вот в оптимизациях последовательно загнать в минимум.
- Segments — максимально число сегментов в дороге. Сегмент, как я понял, это кусок дорожки от дырки до дырки, или от дырки до компонента.
- ExtdSteps — не совсем догнал что за параметр. Как то связан с максимальным числом поворотов дорожки.
- Ripup Level — число уровней отката.
Тут небольшое отступление о работе алгоритма трассировки. Если упрощенно, то там такая схема: Вначале роутим что можем, максимально следуюя правилу минимальной цены. Потом смотрим где у нас пересечения, рипупим (люблю это слово, да…) мешающие дорожки, роутим еще раз, но уже идем на компромисы, повышая цену. И так далее. Глубина рипупа дорожек это и есть Ripup Level. Логика подсказывает, что чем он глубже, тем больше маневра у роутера, но тем дольше будет трассировка.
- Ripup Steps — число попыток отката дорожки. Чем больше тем лучше, но и тем дольше.
- Ripup Totals — сколько одновременно дорожек рипупится. Опять же все упирается в мощность компа.
Cost — Цены элементов
- Via — цена переходной дырки. Сделаешь мало — орел тебе всю плату проклюет. Задолбаешься сверлить. Много — у него крыша от жадности сьедет и развести он не сможет. Рекомендую на первичном прогоне не жадничать, а число их уменьшать на оптимизации.
- NonPrefs — цена ухода с выбранного направления.
В вкладке General мы выбрали линию партии для каждого слоя, а тут указывается цена ухода с направления. Сделаешь мало, дороги будут круголять. Много — пойдут как истинные трактористы — строго по вертикали или горизонтали. Цену, имхо, лучше вначале сделать высокой, а потом понижать по мере оптимизации. Чтобы вначале он все развел вверх-вниз/влево-вправо, пусть и с миллионом дырок, а потом посрезал излишки.
- ChangDir — цена смены направления. При высокой цене будет пытаться пустить напрямик, а при малой может и повилять.
- OrtStep/DiagStep — цена диагональных и ортогональных телодвижений. Честно говоря, даже не знаю что там и менять. Да и в мануале советуют осторожней обращаться с этой величиной, дабы птыц не сьехал в маразм. Можно не трогать.
- ExtStep — толком не просек что за опция, как то связано с заломом дорожек под 45 градусов относительно курса партии для конкретного слоя. В документации на Eagle рекомендуют сделать помельче для Route и побольше для оптимизаций.
- Bonus Step/Malus Step — разница в стоимости между плохими и хорошими зонами. Хорошая зона — чистое поле. Плохая — возле компонентов. Например, между площадок smd резистора. Если сделать большую разницу, то трассировщик пожадничает и, например, сделает еще одну переходную дырку (т.к. ее цена ниже окажется), чтобы обойти резистор, а не пускать дорожку под ним.
- PadImpact/SMDImpact — цена площадок возле контактов (плохая зона). Если мало, то стараемся держаться подальше от дорожек. Если выставить побольше, то будет более терпимой и приоритетом тут будет больше курс слоя.
- Bus Impact — это правила для шин. Если сделать эту цену побольше, то трассировщик первым делом постарается кинуть линии шины напрямки. А если не жадничать, то она может еще и покруголяет.
- Hugging — цена близко расположенных дорожек. Чем больше цена, тем плотней будут стараться идти дорожки, но не ближе чем DRC позволяет! Лучше сделать побольше для роутинга — проще развести первичку будет, а потом поменьше для оптимизаций, чтобы он их разредил и нам проще было плату травить.
- Что такое Avoid и Polygon я так и не догнал. Что то связано с силовыми полигонами на многослойных платах.
Когда все настроили, жмем ок и можно идти заваривать чай, а то лечь спать. Процесс неторопливый и медитативный. В результате роутинга вначале получится что то подобное:
Что поначалу вызвает неслабый батхерт и производство кирпичей в промышленном масштабе. Но не все так плохо, скорей всего оптимизатору удасться из этого кошмара что нибудь нарулить.
Вот, после третьей оптимизации, уже гораздо приличней:
Потом, когда процесс остановится, надо посмотреть сколько процентов. Если внизу окна будет 100% — значит вся плата разведена полностью. У меня вот загорелось 99.2% и видно, что одну дорогу он таки не осилил.
Ее надо пробросить вручную.
Заходим в File — Run. Запускаем скрипт statistic-brd.ulp и смотрим что у нас получилось. Выдало, что у нас 82 переходные дырки. Терпимо, но, честно говоря, не фонтан. Я на этой схеме птичкой добивался около 70 (но того результата у меня не сохранилось и я тут просто заново, ради статьи, запустил автороутинг).
Если сейчас внимательно начать разглядвать плату, то наверняка можно будет найти кучу путей, где можно сооптимизировать, выкинув лишние дырки. В среднем дырок на 10 можно будет ее сократить вручную. Заодно убрать много кривых и некрасивых мест.
Но все же мне не нравится как трассирует орел, поэтому я в орле развожу либо вручную, либо составляю нетлист, а остальное делаю уже топором.
О совершенно убийственной штуке под названием TopoR я расскажу в следующей статье.
Базовые рекомендации разработчику печатных плат | others
Что самое важное при разработке печатных плат (PCB)? Давайте рассмотрим несколько основных моментов, о которых следует всегда помнить разработчику, если он хочет создать по-настоящему технологичные в изготовлении, функциональные и надежные платы. Здесь приведен перевод статьи [1] (автор David Marrakchi), опубликованной на сайте Altium.
Когда Вы начинаете новый проект платы, довольно просто отбросить эти основные советы, потому что мысли в основном сосредоточены на дизайне схемы и/или ПО. Но это скорее всего позже приведет к неприятным последствиям, которые уже сложно будет исправить и они доставят много головной боли. Схема будет работать не так качественно, как ожидалось, у сборщика появятся трудности в производстве, и т. п. Ниже рассмотрены несколько самых важных моментов, помогающих разработать хорошие, качественные печатные платы.
[1. Следует хорошо знать и использовать спецификации производства]
Перед тем, как начать непосредственную разводку, уделите некоторое время на изучение ограничений, которые накладывает производитель при производстве плат. Можно позвонить производителю, написать ему email с просьбой выслать его требования по минимально допустимой ширине дорожки, минимальному расстоянию между дорожками и т. п. Часто эта информация находится на сайте производителя (типичный пример см. в [10]), и требования к параметрам изготовляемой платы делятся по классам точности (от класса точности зависит цена производства).
Для чего это нужно? Чтобы предварительно настроить правила трассировки (Design Rules), систему проверки дизайна на соответствие заданным ограничениям (Design Rules Check, DRC). Если изначально соблюдать правила заданной технологии, то будет проще выполнить всю работу, не потребуется тратить лишнее время на исправление ошибок, которые могут выявиться на этапе производства.
[2. Тщательно размещайте компоненты]
Стадия разработки, когда Вы размещаете компоненты на PCB, требует как искусства, так и научных знаний. Требуется выбрать стратегию размещения, реализующую наиболее выгодный компромисс по удовлетворению требований к разработке. Этот процесс может быть сложным, и от того, как Вы расположите детали на плате, будет зависеть как сложность производства изделия, так и его работоспособность.
При размещении компонентов полезно пользоваться функцией привязки к координатной сетке (snap-to-grid), эта опция должна быть разрешена. Обычно для первичного размещения деталей используют шаг координатной сетки 50 mil. Хотя размещение обычно начинают с выбора места и положения коннекторов, светодиодов, кнопок, схем питания, деталей точных схем, критических узлов и т. д., есть несколько специальных моментов, которые следует учитывать:
Ориентация. Убедитесь, что ориентация похожих компонентов совпадает. Например, электролитические конденсаторы, диоды и т. п. по возможности должны направлять свой положительный электрод в одну сторону. Это поможет в эффективной и безошибочной пайке.
Размещение. Современное технологическое оборудование автоматического монтажа позволяет применять минимальные интервалы между компонентами до 0.2 мм и от края платы 1 мм. Однако использование таких предельных значений в разработке вряд ли оправдано, потому что усложняет монтаж и ремонтопригодность изделия, снижает его надежность. Рекомендуется сохранять интервалы между компонентами не менее 0.5 — 1.25 мм (в зависимости от типа корпуса).
Избегайте размещения компонентов со штыревыми выводами на стороне пайки (нижняя часть платы, Bottom).
Организация. Рекомендуется размещать все монтируемые на поверхность детали (Surface Mount, SMT, или SMD) только на одной стороне платы (обычно на верхней, Top). Одностороннее размещение деталей упрощает и удешевляет монтаж. Если плата сложная, и на ней есть как SMD-компоненты, так и компоненты со штыревыми выводами (through-hole, TH), то TH-компоненты разместите (по возможности) на верхней стороне платы, а SMD-компоненты на нижней. Это минимизирует операции по сборке (монтажу) платы.
Следует учесть, что если на плате имеются смешанные по технологии пайки компоненты (есть как TH, так и SMD детали), то это заставит производителей предпринимать дополнительные шаги для сборки платы, что удорожает производство.
Хороший выбор ориентации компонентов | Плохая ориентация компонентов |
Хорошее размещение компонентов | Плохое размещение компонентов |
Если Вы не нашли компонент в библиотеке, то потребуется его создать. Уделите особое внимание зазорам между контактными площадками и окнам в маске. Маска должна обязательно образовывать окна для каждого вывода, не делайте общее окно для группы выводов. Не соблюдение этого правила может привести к коротким замыканиям мостиками припоя между выводами.
Маска разделяет промежутки между выводами, снижая риск образования замыканий припоем. | Неправильно созданные окна в маске для выводов микросхемы, повышенный риск наплыва припоя между выводами. |
Автотрасировщик может подсказать, насколько хорошо выполнено размещение деталей (см. далее).
[3. Разделение по функционалу]
Скорее всего Вы уже знаете, что мощные схемы, где есть высокие напряжения и большие импульсные токи, могут генерировать значительные помехи, влияющие на работку маломощных прецизионных схем. Чтобы снизить факторы помех, выполните следующие рекомендации:
Разделение. Убедитесь, что шина высокоточной земли и шина земли схем управления или шина земли чувствительных аналоговых схем разведены отдельно. Если они требуют соединения, то должны соединяться друг с другом только в одной точке, максимально близко к месту входа тока питания на плату. Общий принцип — ток потребления, протекающий по шине земли от мощной части схемы, не должен вносить помехи своим падением напряжения на другие, чувствительные части схемы.
Размещение. Если Вы размещаете заливку земли (ground plane) на внутреннем слое платы, то убедитесь, что существуют многочисленные надежные, с низким импедансом соединения этой заливки с другими проводниками земли, находящимися на верхней и нижней сторонах платы. Это снизит риск наводки токами питания помех на чувствительные сигналы управления. Основная рекомендация — стараться отделять друг от друга цифровую и аналоговую земли, идеальный вариант полная их изоляция друг от друга (применяется в особо точных приборах).
Развязка. Чтобы снизить емкостные паразитные связи из-за размещения проводников над большими заливками земли/питания и под ними, постарайтесь выполнить разводку таким образом, чтобы аналоговые сигнальные проводники проходили только над/под аналоговой заливкой земли и пересекали только аналоговые проводники. Это поможет снизить влияние помех от импульсных напряжений и токов, генерируемых быстро переключающимися цифровыми сигналами.
Пример разделения на плате цифровой (DIGITAL) и аналоговой (ANALOG) частей схемы:
[4. Трассировка питания, земли и сигналов]
Когда компоненты размещены, самое время заняться шинами питания, земли и важными сигнальными проводниками, которые Вы хотите развести качественно, чтобы на них было меньше всего посторонних помех. На этой стадии разработки нужно учитывать следующее:
Размещение заливок питания и земли (Power Plane, Ground Plane). Если плата многослойная, то всегда рекомендуется заливки земли и питания разместить на двух внутренних слоях, и разместить их друг относительно друга симметрично, желательно чтобы каждая такая заливка занимала всю площадь платы. Это поможет защитить плату от изгибов и перенапряжений, что может повлиять на правильность позиционирования компонентов при монтаже. Если плата двухсторонняя, то для питания интегральных схем рекомендуется использовать широкие, прямолинейно проложенные проводники, без образования петель. Идеальный вариант — залить все свободное пространство платы шиной земли, как на верхней, так и на нижней стороне платы, а шины питания (+5V, +3.3V) развести широкими, максимально прямолинейными проводниками, без образования лишних петель при переходе от одной микросхемы к другой, с минимизацией переходов между слоями.
Сигнальные проводники. После прокладки питания разведите ответственные сигнальные цепи в соответствии с рекомендациями по построению Вашей схемы. Всегда рекомендуется такие проводники делать максимально короткими, проводимыми непосредственно от компонента к компоненту. При плотной разводке когда возникают сложности в трассировке и необходимо делать переходы с одной стороны платы на другую (с помощью металлизированных переходных отверстий, via) старайтесь размещать горизонтальные проводники на одной стороне платы и соответственно вертикальные на противоположной.
Определение толщины проводников. Когда ток течет через медные проводники платы, он может их довольно сильно нагревать. Чем больше ширина проводника, тем меньше его сопротивление, и меньше нагрев. Но нельзя бесконечно увеличивать ширину проводника, нужен определенный компромисс. Поэтому управление шириной проводников — один из многих способов сбалансировать нагрев печатной платы и уменьшить сопротивление проводников.
Скорее всего Ваша разработка будет иметь цепи разного класса — одни проводники будут передавать большие токи, другие маленькие. Этот факт будет диктовать необходимую ширину проводников на плате. Базовая рекомендация — для слаботочных аналоговых и цифровых цепей рекомендуется делать проводники шириной 10 mil (mil равен одной тысячной дюйма, или 0.0254 мм). Когда цепи будут передавать ток больше 0.3A, их следует делать шире. Есть удобный онлайн-калькулятор [2], упрощающий процесс вычисления параметров проводников. В следующей таблице приведены грубые рекомендации по выбору толщины проводников в зависимости от силы тока. Следует также учитывать длину проводников. Длинные проводники следует стараться делать шире, если по ним протекают значительные токи, это позволит снизить сопротивление проводника и падение напряжения на нем. Небольшой совет — если есть возможность сделать ширину проводников больше, чем требуется, то сделайте это! Когда Вы с запасом отвечаете требованиям как производителя, так и дизайна, меньше шансов того, что плата окажется бракованной, или будет работать не так, как ожидалось.
Ширина дорожки | Допустимый ток |
10 mil | 0.3 A |
15 mil | 0.4 A |
20 mil | 0.7 A |
25 mil | 1.0 A |
50 mil | 2.0 A |
100 mil | 4.0 A |
150 mil | 6.![]() |
Назначьте цепям питания (GND, VCC и т. п.) отдельный класс, и назначьте ему увеличенную минимальную ширину проводника. Тогда автороутер будет прокладывать эти цепи проводниками заданной толщины. Дополнительное преимущество — по толщине проводников проще ориентироваться в разводке платы.
Контактные площадки SMD. Паяльная паста, и особенно расплавляемый припой ведет себя как обычная жидкость, обладающая поверхностным натяжением. В момент пайки это натяжение может смещать монтируемый компонент (особенно это касается SMD-резисторов и конденсаторов). Поэтому не только важно, чтобы паяльная паста имела достаточную влажность и вязкость, но также чтобы размеры площадок для пайки SMD-компонентов строго соответствовали рекомендованным (рекомендуемые размеры площадок можно узнать в даташите на компонент). Если не соблюдать это правило, например если предусмотрено «универсальное» посадочное место для пайки как корпуса 0805, так и корпуса 1208, то поверхностное натяжение расплавленного припоя может привести к перекосу компонентов и даже «могильным камешкам» (thumbstone).
Подсоединение проводников к контактным площадкам. Обратите внимание на разводку проводников по отношению к местам пайки (контактным площадкам) с целью избежать поворота SMD-компонента при пайке. На рисунках ниже показаны примеры правильной и неправильной разводки по отношению к контактным площадкам.
Предпочтительная разводка проводников (стрелками показана миграция припоя):
Нежелательная разводка, которая может привести к повороту SMD-компонента при пайке (стрелками показана миграция припоя):
Диаметры сверл и переходные отверстия. Насколько это возможно, снизьте ассортимент диаметров отверстий, используемых на печатной плате для монтажа TH-компонентов и переходов между слоями. Постарайтесь минимизировать количество сквозных и слепых переходных отверстий для разводки сигнальных проводников (это не касается отверстий, предназначенных для соединения накоротко заливок медью шин земли и питания). По возможности совсем исключите из дизайна слепые переходные отверстия. Это повысит технологичность, надежность платы, её пригодность для ремонта и тестирования.
Зазоры. При разводке необходимо оставлять достаточно места между проводниками различных цепей (зазор, clearance). Почему? Если Вы слишком близко проложите проводники, то повышается риск коротких замыканий между дорожками, образующихся в процессе производства платы. Помните, что процесс производства PCB не на 100% точен, поэтому всегда необходимо для безопасности выдерживать зазор минимум от 7 до 10 mil между соседними дорожками и контактными площадками для пайки деталей.
Особенно важны зазоры между проводником и контактными площадками для пайки. Минимальный допустимый зазор, как и толщина проводников, в общем случае определяется классом точности печатной платы [8], однако хорошей рекомендацией будет не допускать зазоры между контактными площадками и между контактными площадками и токопроводящим рисунком других цепей меньше 7 mil, лучше всего делать зазоры 10 mil. Слишком маленькие зазоры повышают риск возникновения коротких замыканий из-за мостиков припоя и ошибок в производстве самой печатной платы. Также зазоры нужно увеличивать, если проводник находится под высоким напряжением относительно других цепей.
При разводке проводников включите привязку к координатной сетке (snap-to-grid). Шаг координатной сетки 50 mil будет хорошим начальным выбором. Снижение шага до 25 mil может помочь в работе по разводке более плотной платы. Выключение привязки к координатной сетке (или включение очень мелкого шага) может понадобится при подключении проводников к выводам компонентов, которые используют необычный шаг выводов.
Общей практикой является ограничение направлений разводки горизонтальными, вертикальными проводниками, и проводниками под 45 градусов. При прокладке тонких проводников избегайте острых углов при поворотах трассы. Проблема здесь состоит в том, что внешний угол может быть вытравлен сильнее, в результате чего в этом месте проводник получится слишком тонким. Для резких поворотов проводника используйте скругление углов сегментами, направленными под 45 градусов.
Монтажные отверстия. Не забывайте оставлять достаточный интервал между монтажным отверстием и токопроводящим рисунком, чтобы металлическая стойка, винт или шайба не вызвали нежелательного замыкания. Помните, что паяльная маска не может служить хорошим изолятором — она слишком тонкая, и легко разрушается от механического воздействия.
[5. Борьба с нагревом]
Сталкивались ли Вы с ситуациями, когда из-за повышенной температуры ухудшалась работа схемы или даже она вовсе выходила из строя? Эта проблема часто возникает, если не уделить достаточно внимания рассеиваемой компонентами мощности и охлаждению. Ниже приведено несколько советов, помогающих избежать проблем с перегревом и пайкой.
Идентифицируйте проблемные компоненты. Сначала нужно определить, какие компоненты на плате будут больше всего нагреваться. В этом может помочь изучение даташита на компонент и проверка его реальных условий работы в схеме. Обращайте внимание на термосопротивление корпуса (параметр Thermal Resistance) и рекомендации по монтажу и использованию компонента. Конечно, при необходимости должны быть добавлены радиаторы и вентиляторы, чтобы снизить температуру компонента. Также нужно стараться удалить сильно нагревающиеся компоненты от других нагревающихся компонентов и деталей, чувствительных к нагреву (например, от электролитических конденсаторов).
Добавление термобарьера. Термобарьер для пайки (Thermal Relief) — очень полезная технология, улучшающая технологичность платы для процесса её монтажа. Особенно это критично для плат, которые паяются в массовом производстве методом «волна припоя» (wave soldering) и для сборки сложных многослойных плат. Без наличия термобарьера на штыревых выводах компонентов, подключенных к заливке земли (и даже иногда для пайки SMD-компонентов на заливку меди) трудно контролировать температуру припоя в месте пайки. Термобарьер помогает качественной пайке, припой хорошо растечется по всему металлизированному отверстию или месту пайки, что уменьшает риск образование «ложной» пайки.
Общая рекомендация — всегда используйте термобарьер для любого сквозного отверстия, предназначенного для пайки. Также это касается и массивных точек пайки SMD-компонентов, когда они находятся на заливках меди. Исключением из этого правила могут быть случаи, когда такая заливка специально предназначена для охлаждения компонента, но в таком случае должны быть предусмотрены специальные условия для пайки (например, нижний подогрев платы). Типичный термобарьер для места пайки штыревого вывода:
В дополнение термобарьерам применяйте скругления металлом к площадке пайки (teardrops) в тех местах, где проводник, покрытый маской, соединяется с местом пайки, свободным от маски. Это поможет снизить механический и термальный стресс, наносимый проводникам при пайке, будет меньше риск их повреждения и расслоения.
[6. Пользуйтесь автороутером!]
Многие разработчики слепо верят, что автоматический трассировщик мало чем может помочь в разводке. Основная аргументация такого подхода — программный автомат никогда не сможет лучше человека учесть все нюансы разработки. Но это ошибка! Если правильно составить стратегию разводки и соответствующим образом выбрать ограничения дизайна, то автороутер может сэкономить Вам много времени, избавив от монотонной работы [6]. Конечно, автороутер не может выполнить за Вас почти всю работу (за исключением совсем простых проектов). Ваша задача корректировать его поведение и вручную разводить проблемные и особо ответственные цепи, чередуя итерации автоматической и ручной разводки.
Также не стоит впадать в другую крайность и считать, что автороутер может решить все Ваши проблемы. Автотрассировщики, сколь хороши они ни были, никогда не заменят целиком трассировку саму по себе, и должны использоваться только по нескольким причинам, включая следующие:
Размещение компонентов. Автороутер может помочь приблизительно оценить, насколько оптимально расположены компоненты на печатной плате. Вы можете попробовать использовать автороутер после того, как разместите все свои компоненты, чтобы результат разводки автороутера показал, насколько качественную разводку при таком размещении можно получить. Если автороутер развел меньше 85%, то этот может означать, что требуется более тщательно подобрать места для расположения деталей на плате.
Узкие места трассировки. Также можно использовать автороутер для выявления проблемных мест и других критических точек соединений, которые сразу не видны в процессе размещения компонентов.
Подсказка. И наконец, автороутер можно использовать как источник новых идей в поиске пути трассировки некоторых соединений. Быстрый запуск автотрассировщика может показать новый путь для разводки, который Вы ранее не рассматривали.
Помимо этих причин не рекомендуется полностью полагаться на результат автоматической разводки. Почему? Скорее всего автоматическая разводка не будет достаточно точна, и особенно если Вы любите красивую/симметричную разводку, то автороутер наверняка разочарует. И что более важно — ручная трассировка (при условии наличии достаточного опыта) позволит наиболее качественно выполнить все соединения. Трассировка — кропотливый процесс, требующий терпения и любви к своей работе, чтобы можно получить желаемые результаты. ИМХО самый оптимальный вариант — комбинировать итерации ручной разводки и запуска автороутера, чтобы максимально ускорить получение удовлетворительного результата.
[7. Используйте переходные отверстия для отвода тепла]
Последний совет касается того, как можно использовать переходные отверстия (via). Они не только могут предоставить соединение между слоями платы, но также дополнительный способ теплоотвода.
Это становится особенно удобно, если у применяемого мощного компонента есть специальная контактная площадка для отвода тепла (die), предназначенная для пайки на площадку фольги. Если Вы сделаете на этой контактной площадке несколько переходных отверстий до полигона на обратной стороне платы, то тепло будет лучше рассеиваться, и система будет работать надежнее.
[8. Тщательно проверяйте свою работу]
Всегда рекомендуется воспользоваться инструментами автоматической проверки, чтобы не быть озадаченным проблемами, возникающими в процессе производства, сборки и тестирования. К таким инструментам относятся проверка электрических правил (Electrical Rules Check, ERC) и проверка правил разводки (Design Rules Check, DRC), они проверяют, удовлетворяет ли дизайн установленным ограничениям. Эти две системы контроля позволяют просто управлять зазорами, шириной проводников, общими шагами производства, требованиями к высокоскоростным цепям.
Когда тесты ERC и DRC [3, 4] покажут отсутствие ошибок, рекомендуется на всякий случай проверить трассировку каждого сигнала, чтобы убедиться в том, что ничего не упустили. Собственно для этой цели и выполняется рисование принципиальной схемы в таких системах разработки плат, как Altium Designer и других подобных. Если принципиальная схема создана правильно то наверняка и печатная плата не будет содержать грубых ошибок после успешного прохождения тестов ERC и DRC.
Убедитесь, что печатная плата содержит качественную маркировку шелкографией важных мест, и имеются специальные маркеры, предназначенные для автоматизированной сборки и тестирования. Размещение шелкографии и SMD-компонентов только на верхней стороне платы не только удешевляет производство самой платы, но и еще позволяет быстрее определить верхнюю сторону платы при ручном монтаже.
Некоторые интегрированные системы разработки создают трехмерные модели готовой, смонтированной печатной платы [7]. 3D-модель еще до сборки помогает лучше разобраться в технологичности платы, позволяет бросить общий взгляд на готовое изделие и выявить недостатки, которые были незаметны на этапе разработки. Например, компоненты с металлическим корпусом (радиатор, кварцевый резонатор, батарея) могут вызвать неожиданные замыкания с токопроводящим рисунком. Трехмерная модель позволяет лучше выявить места возможных проблем.
[Ссылки]
1. Top 5 PCB Design Guidelines Every PCB Designer Needs to Know site:altium.com.
2. Trace Width Calculator site:4pcb.com.
3. Electrical Rules Check (ERC) site:altium.com.
4. Design Rules Check (DRC) site:altium.com.
5. Использование Altium Designer для разводки печатных плат.
6. Эффективная трассировка печатных плат в Eagle.
7. Eagle3D: как сделать объемную модель печатной платы.
8. Классы точности печатных плат (PCB).
9. The Top 10 PCB Routing Tips for Beginners site:autodesk.com.
10. JLCPCB Capabilities.
Примеры трассировок печатных плат
Автор pcbdesigner. ru На чтение 5 мин. Опубликовано Обновлено
Ознакомиться с самыми последними вариантами выполнения трассировки (разводки) печатных плат можно в галерее выполненных работ Сайта разработчика печатных плат
Здравствуйте, уважаемые посетители сайта PCBdesigner.ru. Раздел мои работы посвящен вопросам разработки печатных плат, а именно вопросам их разводки (слово звучит не совсем красиво, правильнее всего все таки говорить «трассировки», но я буду употреблять оба выражения), выполнению сопровождающей этот процесс конструкторской документации (включающей примеры выполнения детальных, сборочных чертежей печатных плат, спецификации).
Совершенно очевидно: поскольку эта статья называется «Пример трассировки печатной платы», то об этом и пойдет речь.
Ниже представленные рисунки иллюстрируют один из примеров разводки печатной платы. Для вашего удобства приведены примеры трассировки нескольких печатных плат пронумерованные арабскими цифрами. К каждому примеру выполнения проводящего рисунка (разводки) печатной платы дано краткое описание сопровождающееся перечислением касающихся трассировки печатных плат характерных особенностей.
На рисунке 1 представлен пример разводки печатной платы. Основными характеристиками данного печатного узла являются: конструкция, элементная база, проводящий рисунок (результат разводки), класс точности, которые, соответственно, будут определять сложность выполнения трассировки плат.
Рисунок 1.1 – Общий вид трассировки двух сторон печатной платы 1 в приложении PCB программы P-CADПример конструкции разведенной печатной платы
Контур платы выполнен прямоугольным – средних размеров, по углам имеются фаски, присутствуют крепежные отверстия общим количеством 6 штук, трассировка платы выполнена двухсторонней, расположение элементов – одностороннее. Сверху узла по короткой стороне расположен соединитель (разъем), крепление которого обеспечивается винтами, см. пример сборочного чертежа.
Элементная база печатного узла с выполненной трассировкой
Среди факторов определяющих сложность, как результат, плотность проводящего рисунка (трассировки, в простонародии – «разводки») немалую роль играет элементная база.
Узел содержит как элементы поверхностного (SMD) монтажа, так и компоненты сквозного, среди которых, два разъема, часть конденсаторов, резисторов, микросхем, один резонатор.
Типоразмеры элементов поверхностного монтажа начинаются от 0805. В общем случае данный пример трассировки печатной платы содержит 165 элементов. Имеется одна микросхема типа QFP, имеющая четырехстороннее расположение выводов.
Проводящий рисунок разводки печатной платы
Из приведенного примера разводки печатной платы видно: плотность прилегания друг к другу проводников небольшая, поэтому вполне хватает 3 класса точности. Расположение печатного рисунка соответствует правилам трассировки печатных плат. Области металлизации отсутствуют, если вас интересуют примеры металлической сплошной заливки — рекомендую ознакомиться изучить печатные платы с проводящим рисунком (пример разводки печатной платы с заливкой).
Анализируя привиденный пример разводки печатной платы, очевидно, что проводящий рисунок (разводка) данного примера впоследствии может быть усовершенствована, без сильного изменения трассировки ввиду наличия достаточной свободной области отсутствия проводящего рисунка правого верхнего угла.
Комплексный подход к проектированию печатной платы от «А» до «Я» одного из проектов (начиная с принципиальной электрической схемы – заканчивая разработкой конструкторской документации) представлен в статье «Проект радиоприемника своими руками».
Для общего представления и ознакомления, ниже приведены примеры трассировок печатных плат.
Рисунок 2.1 – Пример разводки печатной платы 2 в приложении PCB программы P-CAD Рисунок 2.2 – Печатная плата 2 проводящий рисунок верхней стороны Рисунок 2.3 – Печатная плата 2 проводящий рисунок нижней стороны Рисунок 2.4 – Компоновка верхней стороны печатной платы 2 Рисунок 2.5 – Компоновка нижней стороны печатной платы 2 Рисунок 3.1 – Образец трассировки двухсторонней печатной платы 3 в приложении PCB программы P-CAD Рисунок 3.2 – Образец трассировки верхней стороны печатной платы 3 Рисунок 3.3 – Образец трассировки нижней стороны печатной платы 3 Рисунок 3.4 – Расположение элементов верхней стороны печатной платы 3 Рисунок 3.5 – Расположение элементов нижней стороны печатной платы 3 Рисунок 4.1 – Общий вид трассировки двух сторон печатной платы 4 в приложении PCB программы P-CAD Рисунок 4.2 – Разводка верхней стороны печатной платы 4 в приложении PCB программы P-CAD Рисунок 4.
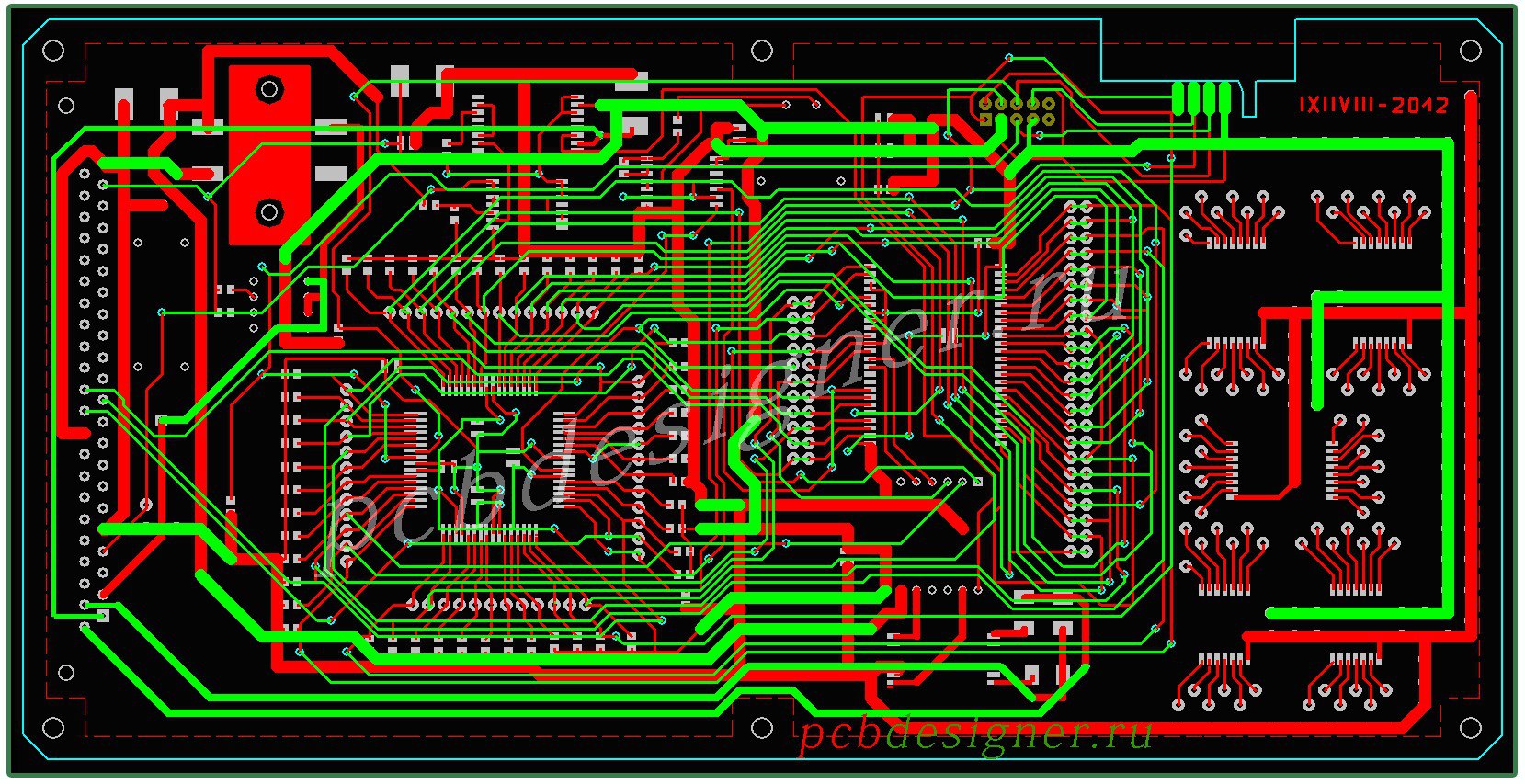
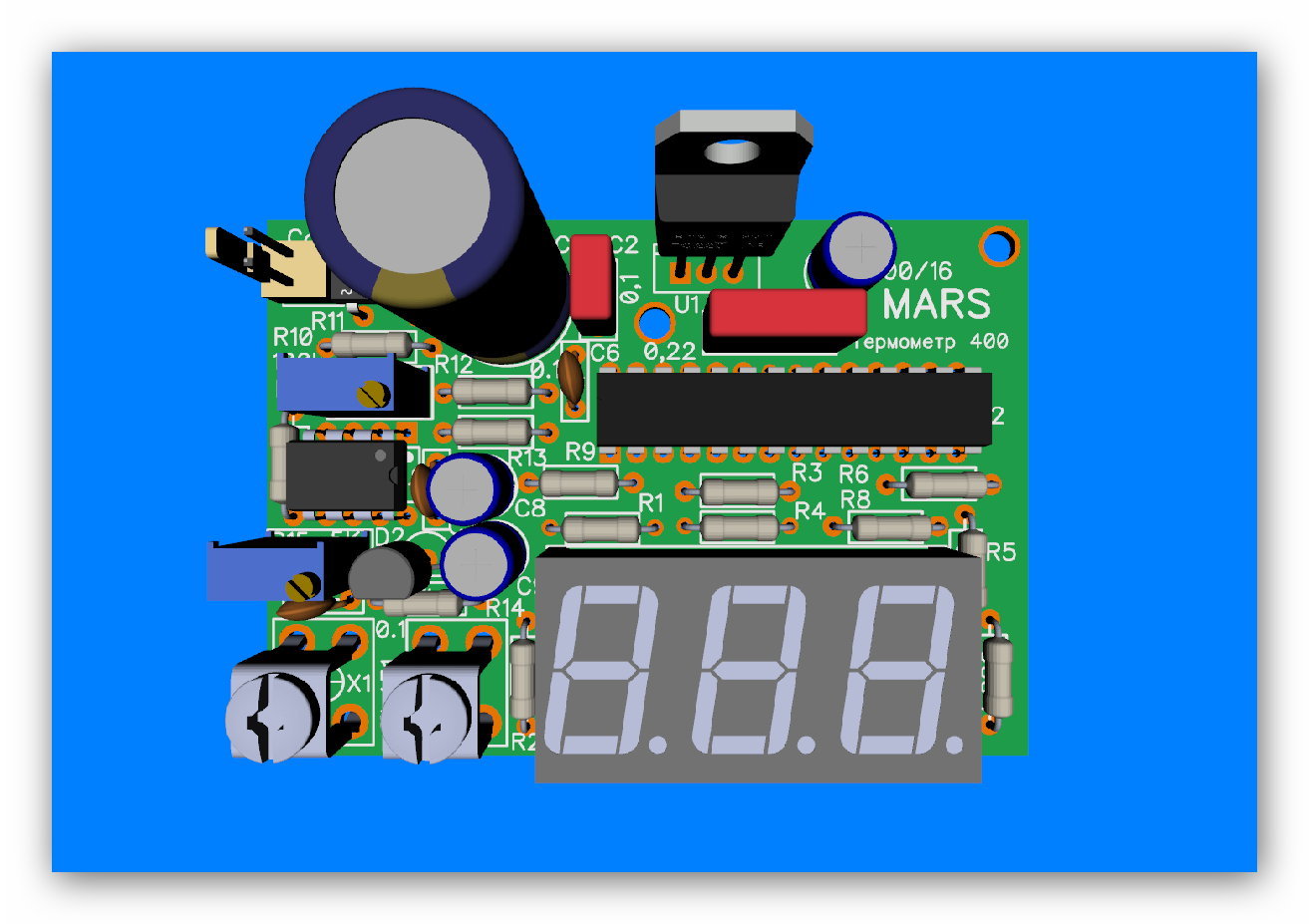
Делаем печатную плату
Что такое печатная платa
Печа́тная пла́та (англ. printed circuit board, PCB, или printed wiring board, PWB) — пластина из диэлектрика, на поверхности и/или в объёме которой сформированы электропроводящие цепи электронной схемы. Печатная плата предназначена для электрического и механического соединения различных электронных компонентов. Электронные компоненты на печатной плате соединяются своими выводами с элементами проводящего рисунка обычно пайкой.
В отличие от навесного монтажа, на печатной плате электропроводящий рисунок выполнен из фольги, целиком расположенной на твердой изолирующей основе. Печатная плата содержит монтажные отверстия и контактные площадки для монтажа выводных или планарных компонентов. Кроме того, в печатных платах имеются переходные отверстия для электрического соединения участков фольги, расположенных на разных слоях платы. С внешних сторон на плату обычно нанесены защитное покрытие («паяльная маска») и маркировка (вспомогательный рисунок и текст согласно конструкторской документации).
В зависимости от количества слоёв с электропроводящим рисунком, печатные платы подразделяют на:
-
односторонние (ОПП): имеется только один слой фольги, наклеенной на одну сторону листа диэлектрика.
-
двухсторонние (ДПП): два слоя фольги.
-
многослойные (МПП): фольга не только на двух сторонах платы, но и во внутренних слоях диэлектрика. Многослойные печатные платы получаются склеиванием нескольких односторонних или двухсторонних плат.
По мере роста сложности проектируемых устройств и плотности монтажа, увеличивается количество слоёв на платах.
Основой печатной платы служит диэлектрик, наиболее часто используются такие материалы, как стеклотекстолит, гетинакс. Также основой печатных плат может служить металлическое основание, покрытое диэлектриком (например, анодированный алюминий), поверх диэлектрика наносится медная фольга дорожек. Такие печатные платы применяются в силовой электронике для эффективного теплоотвода от электронных компонентов. При этом металлическое основание платы крепится к радиатору. В качестве материала для печатных плат, работающих в диапазоне СВЧ и при температурах до 260 °C, применяется фторопласт, армированный стеклотканью (например, ФАФ-4Д), и керамика. Гибкие платы делают из полиимидных материалов, таких как каптон.
Какой материал будем использовать для изготовления плат
Самые распространненые, доступные материалы для изготовления плат — это Гетинакс и Стеклотекстолит. Гетинакс-бумага пропитанная бакелитовым лаком, текстолит стекловолокно с эпоксидкой. Однозначно будем использовать стеклотекстолит!
Стеклотекстолит фольгированный представляет собой листы, изготовленные на основе стеклотканей, пропитанных связующим на основе эпоксидных смол и облицованные с двух сторон медной электролитической гальваностойкой фольгой толщиной 35 мкм. Предельно допустимая температура от -60ºС до +105ºС. Имеет очень высокие механические и электроизоляционные свойства, хорошо поддается механической обработке резкой, сверлением, штамповкой.
Стеклотекстолит в основном используется одно или двухсторонний толщиной 1.5мм и с медной фольгой толщиной 35мкм или 18мкм. Мы будем использовать односторонний стеклотекстолит толщиной 0.8мм с фольгой толщиной 35мкм (почему будет подробно рассмотрено далее).
Методы изготовления печатных плат дома
Платы можно изготавливать химическим методом и механическим.
При химическом методе в тех местах где должны быть дорожки (рисунок) на плате на фольгу наносится защитный состав (лак, тонер, краска и т.д.). Далее плата погружается в специальный раствор (хлорное железо, перекись водорода и другие) который «разъедает» медную фольгу, но не действует на защитный состав. В итоге под защитным составом остается медь. Защитный состав в дальнейшем удаляется растворителем и остаётся готовая плата.
При механическом методе используется скальпель (при ручном изготовлении) или фрезерный станок. Специальная фреза делает бороздки на фольге, в итоге оставляя островки с фольгой — необходимый рисунок.
Фрезерные станки довольно дорогое удовольствие, а также сами фрезы дороги и имеют небольшой ресурс. Так что, этот метод мы не будем использовать.
Самый простой химический метод — ручной. Ризографом лаком рисуются дорожки на плате и потом травим раствором. Этот метод не позволяет делать сложные платы, с очень тонкими дорожками — так что это тоже не наш случай.
Следующий метод изготовления плат — с помощью фоторезиста. Это очень распространненая технология (на заводе платы делаются как раз этим методом) и она часто используется в домашних условиях. В интернет очень много статей и методик изготовления плат по этой технологии. Она дает очень хорошие и повторяемые результаты. Однако это тоже не наш вариант. Основная причина — довольно дорогие материалы (фоторезист, который к тому же портится со временем), а также дополнительные инструменты (УФ ламка засветки, ламинатор). Конечно, если у вас будет объемное производство плат дома — то фоторезист вне конкуренции — рекомендуем освоить его. Также стоит отметить, что оборудование и технология фоторезиста позволяет изготовливать шелкографию и защитные маски на платы.
С появлением лазерных принтеров радиолюбители стали активно их использовать для изготовления плат. Как известно, для печати лазерный принтер использует «тонер». Это специальный порошок, который под температурой спекается и прилипает к бумаге — в итоге получается рисунок. Тонер устойчив к различным химическим веществам, это позволяет использовать его как защитное покрытие на поверхности меди.
Итак, наш метод состоит в том, чтобы перенести тонер с бумаги на поверхность медной фольги и потом протравить плату специальным раствором для получения рисунка.
В связи с простотой использования данный метод заслужил очень большое распространение в радиолюбительстве. Если вы наберете в Yandex или Google как перенести тонер с бумаги на плату — то сразу найдёте такой термин как «ЛУТ» — лазерно утюжная технология. Платы по этой технологии делаются так: печатается рисунок дорожек в зеркальном варианте, бумага прикладывается к плате рисунком к меди, сверху данную бумагу гладим утюгом, тонер размягчяется и прилипает к плате. Бумага далее размачивается в воде и плата готова.
В интернет «миллион» статей о том как сделать плату по этой технологии. Но у данной технологии есть много минусов, которые требуют прямых рук и очень долгой пристройки себя к ней. То есть ее надо почувствовать. Платы не выходят с первого раза, получаются через раз. Есть много усовершенствований — использовать ламинатор (с переделкой — в обычном не хватает температуры), которые позволяют добиться очень хороших результатов. Даже есть методы построения специальных термопрессов, но все это опять требует специального оборудования. Основные недостатки ЛУТ технологии:
-
перегрев — дорожки растекаются — становятся шире
-
недогрев — дорожки остаютяся на бумаге
-
бумага «прижаривается» к плате — даже при размокании сложно отходит — в итоге может повредится тонер.
Очень много информации в интернете какую бумагу выбрать.
-
Пористый тонер — после снятия бумаги в тонере остаются микропоры — через них плата тоже травится — получаются изъеденные дорожки
-
повторяемость результата — сегодня отлично, завтра плохо, потом хорошо — стабильного результат добиться очень сложно — нужна строго постоянная температура прогрева тонера, нужно стабильное давление прижима платы.
К слову, у меня этим методом не получилось сделать плату. Пробовал делать и на журналах, и на мелованной бумаге. В итоге даже платы портил — от перегрева вздувалась медь.
В интернет почему-то незаслуженно мало информации про еще один метод переноса тонера — метод холодного химического переноса. Он основан на том факте, что тонер не растворяется спиртом, но растворяется ацетоном. В итоге, если подобрать такую смесь ацетона и спирта, которая будет только размягчать тонер — то его можно «переклеить» на плату с бумаги. Этот метод мне очень понравился и сразу дал свои плоды — первая плата была готова. Однако, как оказалось потом, я нигде не смог найти подробной информации, которая давала бы 100% результат. Нужен такой метод, которым плату мог сделать даже ребёнок. Но на второй раз плату сделать не вышло, потом опять и пришло долго подбирать нужные ингридиенты.
В итоге после долгих была разработана последовательность действий, подобраны все компоненты, которые дают если не 100% то 95% хорошего результата. И самое главное процесс настолько простой, что плату может сделать ребенок полностью самостоятельно. Вот этот метод и будем использовать. (конечно его можно и далее доводить до идеала — если у вас выйдет лучше — то пишите). Плюсы данного метода:
-
все реактивы недорогие, доступные и безопасные
-
не нужны дополнительные инструменты (утюги, лампы, ламинаторы — ничего, хотя нет — нужна кастрюля)
-
нет возможности испортить плату — плата вообще не нагревается
-
бумага отходит сама — видно результат перевода тонера — где перевод не вышел
-
нет пор в тонере (они заклеиваются бумагой) — соответственно нет протравов
-
делаем 1-2-3-4-5 и получаем всегда один и тот же результат — почти 100% повторяемость
Прежде чем начать, посмотрим какие платы нам нужны, и что мы сможем сделать дома данным методом.
Основные требования к изготовленным платам
Мы будем делать приборы на микроконтроллерах, с применением современных датчиков и микросхем. Микросхемы становятся все меньше и меньше. Соответственно необходимо выполнение следующих требований к платам:
-
платы должны быть двух сторонними (как правило развести одностороннюю плату очень сложно, сделать дома четырехслойные платы довольно сложно, микроконтроллерам нужен земляной слой для защиты от помех)
-
дорожки должны быть толщиной 0.2мм — такого размера вполне достаточно — 0.1мм было бы еще лучше — но есть вероятность протравов, отхода дорожек при пайке
-
промежутки между дорожками — 0.2мм — этого достаточно практически для всех схем. Уменьшение зазора до 0.1мм чревато сливанием дорожек и сложностью в контроле платы на замыкания.
Мы не будем использовать защитные маски, а также делать шелкографию — это усложнит производство, и если вы делаете плату для себя, то в этом нет нужды. Опять же в интернет много информации на эту тему, и если есть желание вы можете навести «марафет» самостоятельно.
Мы не будем лудить платы, в этом тоже нет необходимости (если только вы не делаете прибор на 100лет). Для защиты мы будем использовать лак. Основная наша цель — быстро, качественно, дёшево в домашних условиях сделать плату для прибора.
Вот так выглядит готовая плата. сделанная нашим методом — дорожки 0.25 и 0.3, расстояния 0.2
Как сделать двухстороннюю плату из 2-ух односторонних
Одна из проблем изготовления двухсторонних плат — это совмещение сторон, так чтобы переходные отверстия совпадали. Обычно для этого делается «бутерброд». На листе бумаги печатается сразу 2 стороны. Лист сгибается пополам, на просвет точно совмещаются стороны с помощью специальных меток. Внутрь вкладывается двухсторонний текстолит. При методе ЛУТ такой бутерброд проглаживается утюгом и получается двухсторонняя плата.
Однако, при методе холодного переноса тонера сам перенос осуществляется с помощью жидкости. И поэтому очень сложно организовать процесс смачивания одной стороны одновременно с другой стороной. Это конечно тоже можно сделать, но с помощью специального приспособления — мини пресса (тисков). Берутся плотные листы бумаги — которые впитывают жидкость для переноса тонера. Листы смачиваются так, чтобы жидкость не капала, и лист держал форму. И дальше делается «бутерброд» — смоченный лист, лист туалетной бумаги для впитывания лишней жидкости, лист с рисунком, плата двухсторонняя, лист с рисунком, лист туалетной бумаги, опять смоченный лист. Все это зажимается вертикально в тиски. Но мы так делать не будем, мы поступим проще.
На форумах по изготовлению плат проскочила очень хорошая мысль — какая проблема делать двухстороннюю плату — берем нож и режем текстолит пополам. Так как стеклотекстолит — это слоеный материал, то это не сложно сделать при опредленной сноровке:
В итоге из одной двухсторонней платы толщиной 1.5мм получаем две односторонние половинки.
Далее делаем две платы, сверлим и все — они идеально совмещены. Ровно разрезать текстолит не всегда получалось, и в итоге пришла идея использовать сразу тонкий односторонний текстолит толщиной 0.8мм. Две половинки потом можно не склеивать, они будут держаться за счет запаяных перемычек в переходных отверстиях, кнопок, разъемов. Но если это необходимо без проблем можно склеить эпоксидным клеем.
Основные плюсы такого похода:
-
Текстолит толщиной 0,8мм легко режется ножницами по бумаге! В любую форму, то есть очень легко обрезать под корпус.
-
Тонкий текстолит — прозрачный — посветив фонарем снизу можно легко проверить корректность всех дорожек, замыкания, разрывы.
-
Паять одну сторону проще — не мешают компоненты на другой стороне и легко можно контролировать спайки выводов микросхем— соединить стороны можно в самом конце
Минусы:
-
Сверлить надо в два раза больше отверстий и отверстия могут чуть-чуть не совпасть
-
Немного теряется жёсткость конструкции если не склеивать платы, а склеивать не очень удобно
-
Односторонний стеклотекстолит толщиной 0.8мм трудно купить, в основном продается 1.5мм, но если не удалось достать, то можно раскроить ножем более толстый текстолит.
Перейдем к деталям.
Необходимые инструменты и химия
Нам понадобятся следующие ингридиенты:
-
стеклотекстолит 0.8мм 1-сторонний
-
губка пружинка для мытья посуды
-
фейри или другая жидкость для мытья посуды
-
ацетон (Не забывайте что его пары ядовиты! Работайте в хорошо провертриваемом помещении!)
-
жидкость для снятия лака без ацетона (например ЛАСКА, она точно подходит). Обязательно проверьте жидкость. сейчас очень много подделок, в которые добавлен ацетон. Для проверки надо смочить распечатку на бумаге этой жидкостью, тонер не должен поплыть!
-
спирт технический (ИЗОПРОПАНОЛ — Изопропиловый спирт абслолютированный 99.7% безводный), можно и медицинский, но его сейчас трудно купить
-
туалетная бумага мягкая двух-слойная (например Zewa)
-
шприц пластиковый на 2-3мл
-
фото бумага LOMOND 0102145 85gsm InkJet Photo Paper
-
принтер лазерный чернобелый с высоким разрешением — больше 600dpi. Например HP LaserJet P1102. Картридж можно использовать неоригинальный. Например — Profline отлично подходит.
-
Ножницы, лучше швейный для раскроя ткани
-
сверла 0.6, 0.8, 1мм
-
маркер для корректировки плат Edding 140S
-
минидрель из моторчика (ниже будет рассказано как ее сделать)
-
гидроперит (приобретается в аптеке)
-
лимонная кислота (в хозяйсвтенном магазине или супермаркете)
-
соль каменная (без йода)
-
емкость для травления — например пластиковый контейнер
Теперь когда все это есть, делаем по шагам.
1. Компоновка слоев платы на листе бумаги для печати c помощью InkScape
Inkscape — это высококачественный профессиональный инструмент для работы с векторной графикой для Windows, Mac OS X и Linux. Он широко используется любителями и профессионалами по всему миру для создания иллюстраций, иконок, логотипов, диаграмм, карт, а также веб-графики. Inkscape использует открытый стандарт SVG (Scalable Vector Graphics) от W3C в качестве формата по-умолчанию, а также сам является свободным и открытым программным обеспечением.
Эта программа очень хороша для компоновки рисунка будущей платы. На выходе программы трассировки платы Kicad (или другой) мы получаем рисунок каждого слоя в формате svg или pdf. С помощью этой программы можно импортировать на один лист каждый слой (то есть несколько svg файлов), если необходимо отразить их зеркально и разместить их на листе в нужном количестве. Получившийся рисунок можно сохранить в pdf формате или сразу распечтать.
Давайте посмотрим как это делается.
-
Создаем новый документ в InkScape
-
Выбираем «Файл — Импортировать» и выбираем наши файлы svg слоев платы. ОБЯЗАТЕЛЬНО делать импортирование, иначе можно измениться геометрия рисунка! В итоге получается 2 объекта (можно импортировать по одному):
-
Далее растаскиваем два чертежа и необходимый слой платы (если в Kicad делали оба слоя не зеркальные — то F.Cu слой надо сделать зеркальным) делаем зеркальным (кнопка V — вертикально или H — горизонтально, все равно как, больше для наглядности). Располагаем их рядом, чтобы можно было разрезать — достаточно зазора 2-3мм. Для большей точности можно использовать поля с милиметрами в панели инструментов:
-
Если нам надо поместится в печатную плату определенного размера — то можно сделать прямоугольник нужного размера и внутри его располагать наши рисунки. !Перед печатью нужно удалить все лишние элементы!, если оставить то может в итоге выйти не черный цвет.
-
Лучше сразу печатать 2 копии — чтобы сразу посмотреть какая вышла лучше или если не выйдет с первого раз то останется вторая. В этом редакторе легко можно скопировать и сделать второй экземпляр.
-
Выбираем Файл — сохранить Как — формат PDF и сохраняем. Если вы будете печатать непосредственно из Inkscape, то обязательно проверяйте геометрию, диагональные расстояния сверьте линейкой, иначе плата не выйдет. При печати лучше выбирать Тип печати — ВЕКТОРНЫЙ.
Естественно, если вы например делаете несколько плат сразу, то можно на одном листе расположить нужное количество чертежей.
Небольшие советы:
-
Старайтесь оставить отступы от краев, потому что принтер может плохо печатать ближе к краю.
-
Если плата небольшая, то лучше разместить так, чтобы рисунок занимал пол страницы, тогда можно лист фотобумаги разрезать на 2 части при печати и использовать 2 раза.
-
На печати не должно быть никаких серых областей — все только черно-белое!
-
Обязательно проверяйте посадочные места перед изготовлением платы — приложите микросхемы к распечатанным областям на обычном листе бумаги, или прямо к монитору
-
Внимательно следите за зеркальным слоем — проверить очень легко — после печати — переверните лист и на просвет убедитесь, что все соответсвует рисунку в Kicad.
-
Перед началом изготовления выберите лучшую копию — где больше тонера, где он лучше лежит и т. д.
-
Старайтесь, чтобы сама плата была не большой — не больше 10см х 10 см, иначе ее будет сложно равномерно прижать чертеж к плате. То есть если плата большая, лучше сделать каждую сторону за отдельный заход.
-
Если что-то пошло не так, не переживайте, все можно повторить заново.
-
Оставьте небольшой отступ по длинной стороне итогового чертежа, например 2см, чтобы держать вырезанный рисунок руками.
-
Сама плата должно быть хотя бы на 3мм больше с каждого края чертежа
Вот идеальный вариант:
Еще раз напишу — все добавленные прямоугольники необходимо удалить! Оставить только рисунки платы!
2. Печатаем на принтере рисунок платы
Для нашего метода изготовления плат нужна специальная бумага. Ее подбор — это большая сложная работа. Перепробовав разные бумаги: факсовая, журналы, мелованная, обычная, наконец то была найдена идеальная бумага. Какая бумага нам нужна:
-
Она должна быть легко доступна
-
Недорогая
-
Тонкая, и в то же время не рвущаяся при размачивании
-
Бумага с глянцевым слоем
-
Хорошо и быстро впитывающая влагу (наш раствор), и при этом не коробящаяся при намокании
-
Она должна подходить для лазерного принтера, чтобы не мучиться с приклеиванием бумаги и т. д.
Итак, наш выбор — это бумага фотобумага Lomond (см выше точное название).
Печатать нужно на максимальном расходе тонера. В Windows идем в принтеры, находим нужный принтер и на нем нажимаем правой кнопкой мышки — свойства. Идем на закладку «Параметры устройства» и выбираем плотность печати — максимальная (например 5). В linux такой настройки в драйверах нет, пришлось ставить виртуальную машину с Windows.
Без этой настройки перевод может не получится, и тонер может быть более пористым. При печати также выбираем свойства и чернобелую печать и максимальное разрешение:
Данные настройки могут отличаться для разных принтеров, важно чтобы было максимальное качество печати и расход картриджа. После печати ни в коем случае не трогать руками сам рисунок платы, чтобы не оставить на нем жирных следов!
!При печати PDF файла — обязательно следите за тем, чтобы масштаб был 100% или реальный размер. Adobe PDF любит автоматически размещать на листе меняя масштаб! В этом случае ничего не выйдет.
Теперь вырезаем ножницами рисунок который получился лучше всего. С одного края оставляем 2см бумаги, чтобы держать листок руками (лучше по длинной стороне платы). Режем близко к рисунку 2-3 мм от самого рисунка, чтобы видеть границы рисунка. Кладем его рядом, и он ждет своей участи.
3. Готовим раствор для химического перевода
Сам рецепт очень простой. Берем 2 части жидкости для снятия лака и 1 часть ацетона (например 10мл жидкости и 5мл ацетона). Отмерить можно как угодно — шприцом, мерным стаканчиком. На одну плату 100х50мм идет 2-3мл раствора, так что обычно 30мл хватает на долго, тоесть можно все сразу не смешивать. Хранить такой раствор надо обязательно в плотно закрытой емкости. Очень удобно использовать бутылки стеклянные от физраствора из аптеки с резиновыми крышками:
Ацетон более летучий, так что при длительном хранении может нарушится пропорция. Лучше раствор готовить сразу, и очень долго не хранить. Смешали, немного поболтали и все готово.
4. Готовим стеклотекстолит
На этом этапе лучше сразу подготовить рабочее место где вы будете переводить рисунок на плату. Подойдет стол или табуретка. Сверху лучше положить широкую доску толщиной 2 см или мебельный щит — нужна ровная массивная поверхность. В центр доски кладем 1 лист двухслойной туалетной бумаги.
Для хорошего качества перевода тонера плату необходимо подготовить. Делается это в два этапа. Сначала нашей железной губкой пружинками натираем плату круговыми движениями до блеска. Так как плата у нас тонкая — то лучше положить ее на что-то жесткое. Придерживаем за край и движениями от себя зачищаем плату. Должны уйти все следы окислов, царапины мелкие, отпечатки пальцев. Плата должна блестеть как зеркало, примерно так (для сравнения слева вверху необработанная поверхность):
После этого капаем каплю Фейри в центр платы и хорошо вспениваем руки и саму плату. Моем, трем прямо 2-3 минуты. После этого промываем холодной водой. Держим строго за края платы. Никаких следов от рук остаться не должно. После этого плата готова для перевода. Стряхиваем воду и кладем нашу плату на лист туалетной бумаги, которую мы подготовили. Из шприца выдавливаем пару больших капель нашего раствора на плату и протираем ее куском туалетной бумаги на сухо. На этом этапе следим, чтобы на плату не попали ворсинки, пыль, волосы и т. д. Если у вас грязное помещение, то надо сначала навести порядок.
5. Переводим рисунок
Итак, мы добрались до самого ответственного момента — он него зависит качество полученной платы. Самое приятное тут, что если вдруг что-то пойдет не так, то всегда можно начать сначала и переделать плату заново. Сама плата на этом этапе не портится, и этот этап можно повторять, пока не выйдет идеально.
Переводим рисунок (прежде чем делать — прочитайте несколько раз, делать надо все строго последовательно и быстро).
-
Набираем в шприц наш приготовленный раствор — достаточно около 2-3мл.
-
Кладем нашу подготовленную плату на туалетную бумагу медной поверхностью вверх. На медь наносим с помощью шприца много-много капелек, покрывая всю плату тонким слоем раствора. Шприц здесь очень помогает экономить раствор и равномерно наносить его на плату. Лучше чтобы это была цельная лужа без промежутков.
-
Теперь быстро кладем вырезанный чертеж рисунка платы самим рисунком ВНИЗ и белой стороной бумаги вверх на смоченную раствором плату. Класть лучше держа за тот кусочек, который мы специально оставили. Бумага должна лечь ровно по плате и сразу начнем промокать. Двигать ее в этот момент нельзя! Так что лучше потренироваться с водой, чтобы она ложилась ровно по границе платы. -
По мере промокания бумаги берем пластиковую карту (например карту скидок какого-то магазина) и проводим ей от того места где мы держим бумагу до края, выдавливая лишнюю жидкость и распрямляя наш чертеж. -
Теперь начинаем считать до 10, кладем сверху 2 куска туалетной бумаги и через 10 секунд придавливаем нашу плату грузом весом около 3кг. Можно использовать кастрюлю с ровным дном, налив туда воды (лучше теплой) или что-то похожее. Дно должно быть очень ровным. Поставили кастрюлю на плату — и надавали на нее половиной своей массы на секунд 5. Теперь ждем 5 минут.
-
Через 5 минут снимаем кастрюлю и достаем нашу плату. Бумага должна стать практически белой, рисунка почти не видно. Это значит, что она высохла. Если это не так, то пусть полежит досохнет. На ощупь она должна стать полностью сухой.
Очень важно чтобы обе поверхности пресса были ровные без выступов и дырок. У нас должен получится ровный гладкий пресс. Большую массу тут нельзя применять. Я пробовал делать это с грузом в 10кг — дорожки расплывались. Вес груза 3-4 кг является идеальным. Вы можете попробовать разные варианты, пока не набьете руку, но в принципе этот этап получается обычно сразу и легко.
Теперь необходимо удалить бумагу, чтобы рисунок остался на плате. Если попробовать сделать как в методе ЛУТ, поместить плату под теплую воду, чтобы бумага размокла. То бумага размокнет, но на плате останется тонка пленка фото слоя, которая будет мешать травлению. Если его продолжать удалять щеткой или руками, то повысится пористось тонера и не выйдут полигоны. В общем каким то случайным образом получилось снять бумагу другим методом, который отлично работает на 95% (иногда не выходит, но после небольшой сноровки получается с первого раза). Лучше этот этап внимательно посмотреть на видео несколько раз, там подробно видно как все работает. По сути это ключевой момент всей технологии.
Нам понадобится изопропиловый спирт 97% (см выше) и старая зубная щетка. Окунаем щетку в спирт, и смачиваем сверху нашу бумагу. Она становится немного маслянистой, и в отличие от воды остается полностью целой, не разбухает, не размокает. С того края, где у нас была лишняя бумага без рисунка немного отгибаем бумагу и щеткой заливаем спирт между бумагой и платой. Нам надо намочить бумагу сверху спиртом и подлить его между бумагой и платой. Подливаем спирт несколько раз, бумагу можно прижимать обратно к плате, чтобы спирт стал проникать на зону чертежа. Теперь начинаем очень медленно, желательно с равномерной, силой тянуть листок бумаги. Вы должны почувствовать как бумага отходит от тонера, а он остается на плате.
Когда пройдете 1см, то опять подливаем спирт сверху и между бумагой, она должна быть постоянно смоченной. Продолжаем тянуть и подливать сприт, пока вся бумага не отойдет от тонера.
В итоге у вас в руках должна остаться бумага БЕЗ ТОНЕРА. А на плате остаться ТОНЕР. Бумага здесь является контрольным инструментом — если часть тонера отвалится, то он останется на БУМАГЕ! То есть вы сразу увидите, как получилось перевести тонер. Например черная точка — это часть дорожки. Бумага должна быть абсолютно без тонера.
Хороший результат если тонер отвалился с части полигонов — плата подойет. Если тонер отвалился с пары дорожек — то не беда — можно подреставрировать. Если же отошли большие куски — значит что-то не то, малый груз, грязная плата, где-то попали ворсинки. Всю процедуру надо повторить. Тонер надо смыть ацетоном, и опять начать сначала, с подготовки текстолита.
Если у вас небольшие куски тонера отвалились, то проще не переделывать плату, а воспользоваться маркером. Он отлично подкрашивает нужные участки. Красить лучше как бы ставя много точек с небольшим нажимом. Оставленный рисунок должен быть плотный и видным как наплыв черного лака. Красить надо минимум в 2 слоя. Вот на дорожке видим отвалился тонер:
На бумаге тоже это будет видно:
А вот так выглядит плата после реставрации (маркер просто идеальный, в конце фото платы после травления):
Плата готова для травления. На этом этапе вы можете еще раз проверить все хорошо. Возьмите яркий источник света и посветите на плату, и наклоняйте ее из стороный в сторну как бы ловя солнечный зайчик. Если в тонере есть поры, или где-то он плохо прилип, то вы без сомнения увидите отблески меди обычно на полигонах. Это говорит скорее всего о том, что у вас сел картридж или низкое разрешение принтера. Можно оставить — плата скорее всего получится, но дорожки могут быть пористыми или переделать.
В нашем методе после высыхания тонер будет иметь белый налет, на нем остается фото слой — он дополнительно защищает поры тонера. Осталось протравить плату.
Если вдруг у вас не получается этот этап, то все равно плату можно сделать — сняв слой бумаги обычным методом как в ЛУТ технологии — размочив в теплой воде, плата получится хорошо — но будет не так идеально на полигонах.
Внимание! Прежде чем травить плату, еще раз проверьте рисунок, там ли находятся отверстия, те ли корпуса под микросхемы, нет ли разрывов на дорожкам. Тут еще можно все переделать. После того как вы протравите плату, придется только работать ножом и проводками. !При переносе тонера, если сдвинуть бумагу или сильно давить картой при выравнивании, может измениться геометрия рисунка. Обязательно проверьте линейкой по диагональным точкам расстояние!
6. Травим плату
В интернет рассмотрено очень много травильных растворов. Самый известный — хлорное железо. Но так как мы занимаемся платами дома, будем использовать самый чистый и безопасный раствор — перекись водорода. Абсолютно безвредная жидкость, можно выливать в раковину, конечно нельзя ПИТЬ.
Минус у нашего раствора один — его нельзя хранить. То есть готовится он на раз. Но с другой стороны его плюс — недорогая стоимость и доступность всех ингридиентов.
Готовим раствор для травления, лучше это делать например в обычной литровой банке, удобно помешивать.
-
Наливаем в банку 50мл теплой воды.
-
Кладем туда 3 таблетки Гидроперита (1 таблетка 1.5г в упаковке 8 таблеток) и помешиваем круговыми движениями, пока она полностью не растворится! Должен получится 3% раствор перекиси водорода.
-
Кладем 15 грамм Лимонной кислоты (можно 20) и 5 гр (чайную ложку) НЕ ЙОДИРОВННОЙ СОЛИ. Все это опять помешиваем круговыми движениями до полного растворения.
Теперь выливаем этот раствор в плоскую емкость, контейнер, и в него кладем нашу плату. Лучше класть плату дорожками вниз! В этом случае процесс будет идти быстрее. Иначе на поверхности платы будет образовываться нерастворимый осадок, который будет мешать травлению. Сразу должен пойти процесс — вся плата должна покрыться пузырьками. Ждем где-то около 20-30 минут и все должно быть готово. Иногда немного дольше — 40минут. Контролировать процесс очень легко — светим фонариком снизу контейнера, и мы должны увидеть рисунок платы. В процессе травления раствор становится сначала зеленый, а потом, когда вся кислота уже прореагировала и стала солью — синий. Если раствор пенится и пузырится, вы перебрали с солью. Капните туда еще немного перекиси и воды. Сильное пузырение может повредить тонер. Когда пузырение прекратится — плата готова.
Если все протравилось — нет точек лишних и т.д. — то достаем плату, еще раз смотрим внимательно и промываем теплой водой, можно добавить немного соды, чтобы нейтрализовать лимонную кислоту. Если плату вы сразу не будете запаивать, то можно оставить тонер как защиту меди. Второй вариант снять тонер ацетоном и покрыть плату спиртоканифольным флюсом. Качество готовой платы вы можете оценить по этому фото (дорожки 0.25):
7. Сверлим отверстия
Не смотрите на то, какие сверла указаны в KICAD, эти размеры используются при сверлении на заводе, при очень точно центровке. При ручной сверловке, подбирайте сверла как можно меньшего диаметра, по деталям, которые будут в эти отверстия запаиваться (Ориентируйтесь на список свёрел, приведенный ниже).
Посмотрим какие свёрла нам могут понадобиться:
-
Сверло диаметр 0.6мм — тоньше сверла не нужны, это самое тонкое которое нужно. Чем тоньше сверло, тем более точно вы попадаете в разметку, поэтому этим сверлом можно сверлить ответсвенные переходные отверстия там где нужна особая точность. Потом отверстие можно рассверлить любым нужным сверлом. Такая двухэтапная сверловка будет гораздо точнее, чем сразу сверлить нужным сверлом. Если брать тонкую проволку на переходные отверстия, то оно подойдет для них (например из витой пары).
-
Сверло диаметр 0.7мм — самое ходовое сверло, под все выводные компоненты можно сверлить им — резисторы, конденсаторы, кварцы, монтажные провода, переходные отверстия.
-
Сверло диаметр 0.8мм — можно использовать для отверстий под монтажные провода и некоторые разъемы.
-
Сверло диаметр 1мм — подходит для разъемов типа PIN 2.54 — штыри. Можно конечно попробовать 0.8 — но его чуть-чуть не хватает.
-
Сверло диаметр 2мм — хорошо подходит для монтажных отверстий под маленькие шурупы — крепление платы к корпусу
-
Сверло диаметр 3мм — монтажные отверстия под болты М3
Чтобы упростить себе работу, сверлить надо только те отверстия где подходит дорожка, и второе отверстие просверлить уже потом, когда запяете переходные отверстия. Чтобы не склеивать плату, для обеспечения жесткости, можно добавить неоходимые переходы по земляным полигонам по краям платы.
Сверла такого диаметра нельзя зажать в обычную дрель. Нужна специальная мини-дрель. Можно использовать готовые — например Дремель или специальный мини станок для сверления плат, но гораздо проще и дешевле сделать минидрель из моторчика.
Делаем мини дрель
Для того чтобы сделать мини дрель нужен только моторчик и цанговый патрон для маленьких сверл. Мотор лучше выбрать с высокими оборотами — около 10тыс оборотов в минуту. Отличный мотор R380-2580. При 12в питании выдает 14тыс оборотов. Диаметр вала — 2.3мм.
Цанговый патрон бывает двух видов — набор цанг на фиксированный диаметр сверла:
Автоматический цанговый набор:
Мы рекомендуем первый вариант — он дешевле. Далее необходимо к мотору припаять провода и выключатель (лучше кнопку). Кнопку лучше разместить на корпусе, чтобы удобнее было быстро включать и выключать моторчик. Остается подобрать блок питания, можно взять любой блок питания на 7-12в током 1А (можно и меньше), если такого блока питания нет, то может подойти зарядка по USB на 1-2А или батарейка Крона (только надо пробовать — не все зарядки любят моторы, мотор может не запустится).
Дрель готова, можно сверлить. Но вот только необходимо сверлить строго под углом 90градусов. Можно соорудить мини станок — в интернет есть различные схемы:
Но есть более простое решение.
Кондуктор для сверления
Чтобы сверлить ровно под 90 градусов достаточно изготовить кондуктор для сверления. Мы будем делать вот такой:
Изготовить его очень легко. Берем квадратик любого пластика. Кладем нашу дрель на стол или другую ровную поверхность. И сверлим в пластике нужным сверлом отверстие. Важно обеспечить ровное горизонтальное смещение дрели. Можно прислонить моторчик к стене или рейке и пластик тоже. Далее большим сверлом рассверлить отверстие под цангу. С обратной стороны рассверлить или срезать кусок пластика, чтобы было видно сверло. На низ можно приклеить нескользящую поверхность — бумагу или резинку. Такой кондуктор надо сделать под каждое сверло. Это обеспечит идеально точное сверление!
Такой вариант тоже подойдет, срезать сверху часть пластика и срезать уголок снизу.
Вот как производится сверление с его помощью:
Зажимаем сверло так, чтобы оно торчало на 2-3мм при полном погружении цанги. Ставим сверло на место где надо сверлить (при травлении платы у нас будет оставаться метка где сверлить в виде мини отверстия в меди — в Kicad мы специально ставили галку для этого, так что сверло будет само вставать туда), прижимаем кондуктор и включаем мотор — отверстие готово. Для подстветки можно использовать фонарик, положив его на стол.
Как уже мы писали ранее, сверлить можно только отверстия с одной стороны — там где подходят дорожки — вторую половину можно досверлить уже без кондуктора по направляющему первому отверстию. Это немного экономит силы.
8. Лужение платы
Зачем лудить платы — в основном для защиты меди от корозии. Основной минус лужения — перегрев платы, возможная порча дорожек. Если у вас нет паяльной станции — однозначо — не лудите плату! Если она есть, то риск минимальный.
Можно лудить плату сплавом РОЗЕ в кипящей воде, но он дорого стоит и его сложно достать. Лудить лучще обычным припоем. Чтобы сдеалать это качественно, очень тонким слоем надо сделать простое приспособление. Берем кусочек оплетки для выпайки деталей и одеваем ее на жало, прикручиваем проволокой к жалу, чтобы она не соскочила:
Плату покрываем флюсом — например ЛТИ120 и оплетку тоже. Теперь в оплетку набираем олово и ей водим по плате (красим)— получается отличный результат. Но по мере использования оплетка расподается и на плате начинают оставаться ворскинки медные — их обязательно надо убрать, а то будет замыкание! Увидеть это очень легко посветив фонарем с обратной стороны платы. При таком методе хорошо использовать или мощный паяльник (60ват) или сплав РОЗЕ.
В итоге, платы лучше не лудить, а покрывать лаком в самом конце— например PLASTIC 70, или простой акриловый лак купленный в автозапчастях KU-9004:
Тонкий тюнинг метода переноса тонера
В методе есть два момента, которые поддаются тюнингу, и могут не получиться сразу. Для их настройки, необходимо в Kicad сделать тестовую плату, дорожки по квадратной спирали разной толщины, от 0.3 до 0.1 мм и с разными промежутками, от 0.3 до 0.1 мм. Лучше сразу распечатать несколько таких образцов на одном листе и провести подстройку.
Возможные проблемы, которые мы будем устранять:
1) дорожки могут менять геометрию — растекаться, становится шире, обычно очень не значительно, до 0.1мм — но это не хорошо
2) тонер может плохо прилипать к плате, отходить при снятии бумаги, плохо держаться на плате
Первая и вторая проблема взаимосвязаны. Решаю первую, вы приходите ко второй. Надо найти компромисс.
Дорожки могут растекаться по двум причинам — слишкой большой груз прижима, слишком много ацетона в составе полученной жидкости. В первую очередь надо попробовать уменьшить груз. Минимальный груз — около 800гр, ниже уменьшать не стоит. Соответственно груз кладем без всякого прижима — просто ставим сверху и все. Обязательно должно быть 2-3 слоя туалетной бумаги для хорошего впитывания лишнего раствора. Вы должны добиться того, что после снятия груза, бумага должна быть белая, без фиолетовых подтеков. Такие подтеки говорят о сильном расплавлении тонера. Если грузом отрегулировать не получилось, дорожки все равно расплываются, то увеличиваем долю жидкости для снятия лака в растворе. Можно увеличить до 3 части жидкости и 1 часть ацетона.
Вторая проблема, если нет нарушения геометрии, говорит о недостаточном весе груза или малом количестве ацетона. Начать опять же стоит с груза. Больше 3кг смысла не имеет. Если тонер все равно плохо держится на плате, то надо увеличить количество ацетона.
Эта проблема в основном возникает, когда вы меняете жидкость для снятия лака. К сожалению, это не постоянный и не чистый компонент, но на другой его заменить не получилось. Пробовал заменить его спиртом, но видимо получается не однородная смесь и тонер прилипает какими-то вкраплениями. Также жидкость для снятия лака может содержать ацетон, тогда ее надо будет меньше. В общем, такой тюнинг вам надо будет провести один раз, пока не закончится жидкость.
Плата готова
Если вы не будете сразу запаивать плату, то ее необходимо защитить. Самый простой способ сделать это — покрыть спиртоканифольным флюсом. Перед пайкой это покрытие надо будет снять например изопропиловым спиртом.
Альтернативные варианты
Вы также можете сделать плату:
Дополнительно, сейчас набирает популярность сервис изготовления плат на заказ — например Easy EDA. Если необходима более сложная плата (например 4-х слойная) — то это единственный выход.
Колхозим печатную плату (фотолитография в домашних условиях)
Очередной раз попросили показать-рассказать, как делать платы, подумал а чего бы не запилить обзор колхоз-технологии.Печатная плата односторонняя (использован только нижний слой), металлизация все как-то откладывается на потом.
Итак, на выходе из программы трассировки (я уже много лет пользуюсь Autodesk Eagle) нижний слой(!) и маска gerber и exellon. Для удобства, экселлон модифицирую, путем изменения всех отверстий на 0.4мм, так проще попадать.
Прежде всего нужно подготовить фотошаблоны. Для этого использую замечательный, безотказный и простой как 3 копейки GERBV. В новый проект добавляю слои (нижний слой меди, маску, модифицированную сверловку), изменяю цвет фона на черный, цвета слоев маски и меди — белый, сверловка — черная.
Как на картинке
Активирую слои меди и сверловки, экспортирую в png, разрешение (в правом нижнем углу окна экспорта) выставляю 1200DPI, это важно. Тоже самое со слоем маски.
Далее, в редакторе Inkscape. В настройках редактора (Правка-Параметры), в разделе «Растр» выставляю те же разрешение по-умолчанию для импорта те же 1200DPI (это нужно сделать один раз и забыть). При импорте указываю «DPI изображения»: по-умолчанию.
Картинка
После, импортирую получившиеся картинки, расставляю как мне нравится. И отправляю на печать, принтер лазерный
пленка KIMOTO OHP/DTP
Купить можно у рекламщиков, там же продается спрей KRUSE Toner Density, которым, не то, чтобы обильно но хорошо поливаю получившийся шаблон. Это действо увеличивает плотность тонера, и как следствие контраст фотошаблона.
получается как-то так:
Вырезаю текстолит с запасом, обезжириваю (растворитель и изопропиловый спирт — это вообще два главных химиката, всегда нужны). Накатываю пленочный негативный фоторезист, уже несколько лет использую Ordyl Alpha 350 — доволен как слон. Если фоторезист плохо липнет (скорее всего кончился срок годности) — плату можно подогреть феном или утюгом.
Про фоторезист
Продается, например, в чипдипе, да еще много где. Выглядит в коробке вот так:Тонкикий слой фоторезиста покрыт с двух сторон пленкой, полиэтиленовой (матовой и тянущейся) со стороны клеевого слоя, и лавсановой (глянцевой) с лицевой стороны.
Лепить можно под водой или на мыло (как самоклейку), но такой способ проходит только со свежим фоторезистом. Поэтому клею на сухую, постепенно снимая матовую пленку и разглаживая и прижимая от центра к краям. Ничего сложного — потренироваться разве что немного. Если есть ламинатор с регулируемой температурой — вообще отличный вариант, но мой ламинатор прекрасно работавший с ПФ-ВЩ-50, ордил явно перегревает, а переделывать — лень.
После того, как фоторезист на текстолит накатан, на несколько капель воды леплю фотошаблон. Тонером вниз, к плате, это важно! И засвечиваю матрицей UV-светодиодов, расстояние — около 10 см, время экспозиции 7-8 секунд.
На фоторезисте должен отпечататься рисунок будущей платы, он хорошо на глаз заметен.
Картинка
Для более качественного результата — еще запекаю плату в печке с температурой 80 градусов в течении нескольких минут, это улучшает полимеризацию фоторезиста. Но можно и обойтись.
Далее проявка, подойдет любой щелочной раствор: каустическая или кальцинированная сода, канцелярский клей. Я пользуюсь «кротом» из хозмага, 1-2мл крота на 500мл воды, комнатной температуры. Можно более агрессивный раствор, тогда проявляется порядком быстрее, но бывает лохматит старый фоторезист, так что лучше подождать пару лишних минут.
Платы в проявочном растворе
Важно, после того, как кажется, что весь лишний фоторезист смыт еще подождать 10%-15% времени проявки, потому как даже тонкая, невидимая глазу, пленка помешает травлению.
Результат проявки:
Травление, в горячем хлорном железе, грею градусов до 60, даже старый раствор травит минут за 10 максимум. Но можно травить, в чем душа пожелает, соляная кислота, раствор лимонки и соли, персульфат аммония — все подойдет.
Уже ненужные остатки фоторезиста смываются растворителем или ацетоном.
Крупным планом
Если не нарушать технологию, получается довольно качественно. Дорожка 8mil (0.2мм) — без труда и главное — стабильно.Далее маска, я использую двухкомпонентную FSR-8000, продается много где, а килограммами — в резоните. Маска шикарная, прощает много косяков, имеет великолепную адгезию к текстолиту и меди. В общем это та самая маска, которую используют на производствах. В резоните продается в банках, не дорого.
Банки с маской
Как видно — просрочена она летом 2016 года, сейчас на дворе апрель 2019, и это никак не сказывается на результате. Единственное — храню в холодильнике.
Маска мешается с отвердителем в пропорциях 3:1 по весу, наваливаю 6 грамм маски и 2 грамма отвердителя, тщательно перемешиваю. Замешиваю не на один раз, а сразу побольше. Во-первых так точнее выходит отмерить компоненты, а во-вторых это очень «грязный» процесс. Смешанная маска без потери свойств прекрасно хранится в холодильнике неделями, а то и месяцами. В общем чудо как хороша. Главное — если храните дома, обязательно в герметичном пакете, иначе вся еда провоняет маской. Если не любите колбасу со вкусом FSR-8000 — зиплок лучший друг.
еще картинки
Платы обезжириваю изопропиловым спиртом, за неимением трафаретного принтера леплю на малярный скотч к подложке, подложку на тот же скотч к столу, чтобы не двигалось.
Сверху трафаретную сетку, натянутую на рамку. Можно купить на алиэкспрессе (ищется: трафаретная печать рамка) как готовую, так и сетку отдельно, а рамку сообразить из деревяшек. Заклеиваю лишнее тем же малярным скотчем, вываливаю некоторое количество маски
и тщательно растираю резиновым шпателем. Дырок на плате еще нет, поэтому церемониться не нужно, можно возюкать шпателем до получения результата.
Результат примерно такой:
5 минут при комнатной температуре, чтобы маска окончательно растеклась и выравнилась и в печку минут на 30-40-60, сколько не жалко времени. Чем выше температура, тем быстрее сохнет, но не более 95 градусов, иначе потом шкуркой снимать. У меня оптимально получается 80 градусов и 30-40 минут.
После сушки и остывания, маска перестает липнуть. Накладываю фотошаблон (это самый геморройный и творческий процесс), и засвечиваю той же UV-матрицей светодиодов 40 секунд.
Картинки
После засветки, в том же щелочном растворе проявляю, занимает времени чуть дольше, чем фоторезист, зато не менее красиво. Кисточка опять же помогает, но немного портит глянцевость и красоту маски. Правило то же, после того, как показалось, что вся ненужная маска смылась — нужно подождать еще 10-15% времени проявки.
Еще
После, самый долгий процесс дубления маски в печке при температуре 130 градусов. Минимум выходит около часа. По-хорошему, еще дольше.
После запекания, маска становится сильно твердой и снять её можно только механически (наждачкой или напильником).
В качестве печки использую самый дешевый гриль с подключенным китайским PID-регулятором или печку для оплавления.
Устройства для выпекания
печка разпечка два
Далее, сверловка. Из слоя меди и сверловки с помощью FlatCam (тут нужно не забыть и с помощью 2-side pcb tool отзеркалить картинку) готовится gcode для станка, плата закрепляется, по двум самым дальним отверстиям центруется.
, а дальше работает станок, а я пью чай, иногда заменяя сверло и фрезу.
Конечно можно сверлить и вырезать вручную, но на станке быстрее и удобнее.
Результат, не без косяков, но вполне достойный.
Ну и бонусом:
Паста — детальки — выпечка
Приборы и материалы:
Магазины рекламировать не буду, использовалось следующее
Фоторезист Ordyl Aplha 350, легко покупается в локальных магазинах
Маска паяльная FSR-8000, а покупал в резоните килограммами, можно найти в розничных магазинах, поисковик без труда выдаст десятки предложений
Пленка KIMOTO и усилитель плотности тонера Kruse toner density, можно найти дорого в интернете, или дешево у рекламщиков и их поставщиков.
PID-регулятор китайский REX C100 с твердотельным реле, гриль самый дешевый из ближайшего гипермаркета.
Трафаретная сетка и рамка с трафаретной сеткой находятся на алиэкспрессе по запросу «трафаретная печать»
CNC2418 — китайский, обзоров тысячи. Продавцов на али еще больше. Сверла и фрезы там же.
По поводу срока годности
Нашел в загашнике маску (та же самая марка, цвет другой), купленную в 2011м году. Хранилась на полке, при комнатной температуре. Отвердитель высох и превратился в камень, а сама маска загустела и местами подсохла. Размешал с отвердителем купленным в 2015м году результат на картинке:Оплатите сборы — Иммиграция и гражданство
Какой тип заявки вы подаете?
- Временное место жительства
За что вы платите?
- Электронное разрешение на поездку (eTA)
- International Experience Canada (рабочий отпуск, международный кооператив или молодые специалисты)
- Разрешение на учебу (с продлением)
- Разрешение на временное проживание
- Гостевая виза (включая супервизу) или для продления срока пребывания
- Разрешение на работу (с продлением)
- ПМЖ
На какую программу или документ на постоянное жительство вы подаете заявление?
- Agri-food пилот
- Атлантический иммиграционный пилот
- Сиделки
- Экспресс-въезд
За что вы платите?
- приложение Express Entry
- добавление супруга или ребенка-иждивенца после того, как я уже подал заявку
- Плата за право постоянного проживания (RPRF)
- Путь на постоянное место жительства медицинского работника
- Гуманитарные и милосердные
- Карта постоянного жителя
- Проездной документ постоянного жителя
- Допуск класса
- Охраняемое лицо
- Номинант от провинции — не Express Entry
- Программа бизнес-иммиграции Квебека
- Квалифицированные рабочие, отобранные в Квебеке
- Плата за право на постоянное проживание — не экспресс
- Пилотная иммиграционная служба для сельских и северных районов
- Самостоятельно занятые
- Стартап виза
- Временный государственный полис для неработающих строительных рабочих в районе Большого Торонто (GTA)
- Семейное спонсорство
За что вы платите?
- Усыновленные дети и др. Родственники
- Родители, бабушки и дедушки
- Супруг, партнер или дети
- Гражданство
За что вы платите?
- Взрослый (18 лет и старше)
- Незначительное (до 18 лет)
- Взрослый без гражданства (18 лет и старше), родившийся от канадского родителя
- Свидетельство о гражданстве (подтверждение гражданства)
- Найдите запись о гражданстве
- Отказаться от гражданства
- Возобновите гражданство
- Доступ к запросу информации
- Недопустимость
За что вы платите?
- Разрешение на возврат в Канаду
- Реабилитация
- Разрешение на временное проживание
- Другие приложения и услуги
За что вы платите?
- Биометрия
- Соблюдение требований работодателя
- Подтвердите свой статус или замените иммиграционный документ
Калькулятор комиссий PayPal: Взимает ли PayPal комиссию за каждую транзакцию?
PayPal стал одним из лучших способов безопасной отправки средств в Интернете.
Тысячи интернет-компаний, включая продавцов eBay и Amazon, будут использовать PayPal для покупок товаров в качестве альтернативы карточным платежам.
Если вы получаете определенную сумму денег в месяц на свой счет PayPal, вам придется платить комиссию.
Express.co.uk разбивает все комиссии и сборы, которые вам придется заплатить, если вы продаете через PayPal.
Взимает ли PayPal комиссию за каждую транзакцию?
Короче говоря, нет, PayPal не будет взимать комиссию за транзакцию, если вы используете эту услугу для личного использования с небольшими суммами, но она будет взимать плату с вас, если вы ведете бизнес с помощью PayPal.
Personal
PayPal — это бесплатная услуга, которую нужно настроить, поэтому вы можете бесплатно открыть счет для перевода средств через Интернет.
Согласно PayPal.com: «В США нет комиссии за отправку денег семье и друзьям, когда вы используете только свой баланс PayPal или банковский счет, или комбинацию баланса PayPal и банковского счета.
«Существует комиссия за отправку денег в качестве личного платежа с помощью дебетовой или кредитной карты».
С вас не будет взиматься комиссия, если вы совершите какие-либо транзакции, если только вы не отправите платеж кому-либо в другой стране.
Узнать, сколько стоит комиссия для каждой отдельной страны, можно на их официальном сайте.
Вы также можете бесплатно снимать деньги через PayPal.
Business
Вы можете легко вести бизнес, используя PayPal в качестве основного источника покупок в Интернете.
Если вы это сделаете, вам нужно будет платить комиссию в зависимости от того, сколько вы зарабатываете на своем счете PayPal.
Согласно eBay, вот ставки и процентные сборы для PayPal:
«Если вы получаете до 1500 фунтов стерлингов на свой счет PayPal в месяц, с вас будет взиматься 3.4 процента и 20 пенсов за каждый платеж, произведенный на ваш счет PayPal, если вы получили более 1500 фунтов стерлингов на свой счет PayPal, вы будете платить 2,9 процента и 20 пенсов за каждую полученную транзакцию.
«Если вы получаете более 6000 фунтов стерлингов на свой счет PayPal, вы платите только 2,4 процента и 20 пенсов за каждую транзакцию. Если вы получите более 15000 фунтов стерлингов на свой счет PayPal, вы будете платить 1,9 процента и 20 пенсов за каждую транзакцию ».
Использование BNB для оплаты комиссий
В соответствии с техническим документом Binance, вы можете использовать BNB для оплаты любых комиссии на платформе Binance.Когда вы держите BNB и используете BNB для оплаты торговых сборов, вы получите значительную скидку в зависимости от количества времени, прошедшего с момента запуска Binance в 2017 году.
ВРЕМЯ | 1 год | 2-й год | 3-й год | 4-й год | 5 год |
Ставка дисконтирования | 50% | 25% | 25% | 6.75% | Без скидки |
ПРИМЕЧАНИЕ: ВРЕМЯ рассчитывается с момента создания Binance в июле 2017 года, а не время регистрации аккаунта.
FAQ
1. Логика конвертации BNB в другие монеты.
Если вы торгуете BNB для получения NEO, наша система рассчитает комиссию на основе соотношения обмена NEO на BNB по рыночной цене, которая основана на рыночной цене NEO / BTC и BNB / BTC.
Коэффициент обмена NEO / BNB = NEO / BTC [рыночная цена] / (BNB / BTC [рыночная цена]). Binance обновляет рыночную цену каждую секунду.
2. Могу ли я включить / выключить 【 Использование BNB для оплаты сборов】 функция?
Да, вы можете в любое время включить или выключить эту функцию в Центре пользователя — «Панель управления». Вы также можете найти уведомление на торговой странице о текущем статусе этой функции.
Центр пользователя
торговая страница
3.