Как выполнить металлизацию отверстий на печатной плате в домашних условиях. Какие существуют методы металлизации. Какие материалы и инструменты потребуются для металлизации отверстий. Каковы основные этапы процесса металлизации.
Что такое металлизация отверстий печатных плат
Металлизация отверстий — это процесс нанесения проводящего металлического покрытия на стенки отверстий в печатной плате для обеспечения электрического соединения между слоями платы. Это ключевой этап при изготовлении многослойных и двусторонних печатных плат.
Основные цели металлизации отверстий:
- Создание электрического контакта между проводящими слоями платы
- Повышение надежности соединений
- Улучшение теплоотвода
- Упрощение монтажа компонентов
В промышленности для металлизации используют сложные химические и гальванические процессы. Но в домашних условиях можно применить более простые методы.
Основные методы металлизации отверстий в домашних условиях
Для металлизации отверстий печатных плат в домашних условиях чаще всего используются следующие методы:
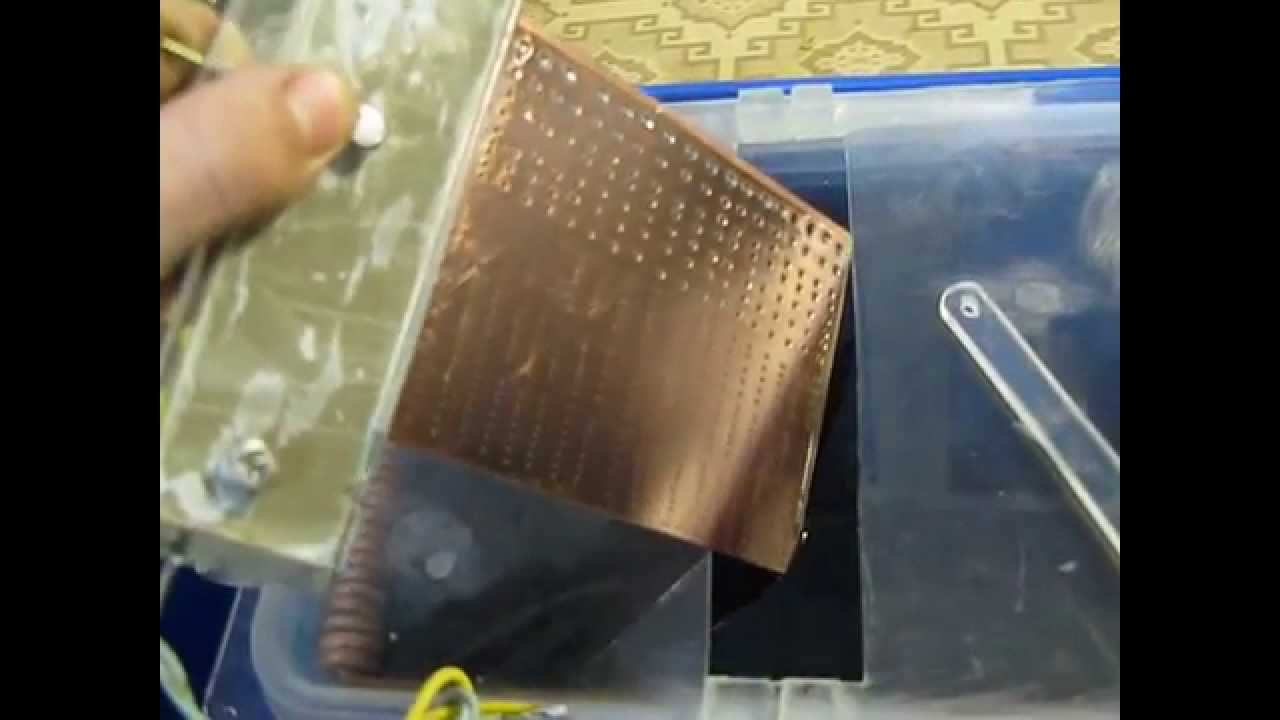
1. Химическое осаждение меди
Суть метода заключается в химическом осаждении тонкого слоя меди на стенки отверстий из специального раствора. Основные этапы:
- Подготовка и очистка поверхности
- Сенсибилизация поверхности
- Активация
- Химическое меднение в растворе
- Усиление слоя гальваникой
Преимущества метода — возможность получить качественное покрытие. Недостатки — сложность процесса и использование агрессивных химикатов.
2. Графитирование
При этом методе на стенки отверстий наносится токопроводящий слой графита. Последовательность действий:
- Подготовка поверхности
- Нанесение графитовой пасты или спрея
- Удаление излишков графита
- Запекание для улучшения адгезии
Достоинства — простота и доступность. Недостатки — не очень высокая проводимость и надежность.
3. Механическая металлизация
Этот метод подразумевает вставку и фиксацию в отверстиях металлических проводников. Варианты:
- Впаивание тонкой проволоки
- Установка специальных заклепок
- Расклепывание медных штифтов
Плюсы — не требует химикатов. Минусы — трудоемкость при большом количестве отверстий.
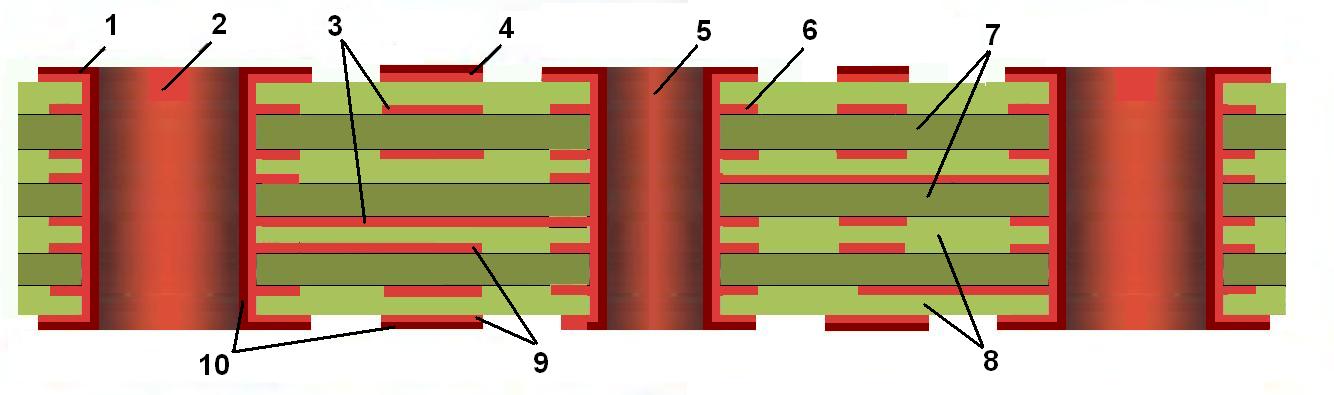
Инструменты и материалы для металлизации отверстий
Для выполнения металлизации отверстий печатных плат в домашних условиях потребуются следующие инструменты и материалы:
- Сверлильный станок или ручная дрель
- Сверла нужного диаметра
- Химические реактивы (в зависимости от метода)
- Емкости для растворов
- Кисточки или губки для нанесения составов
- Термофен или паяльная станция
- Мультиметр для проверки
- Средства индивидуальной защиты
Точный набор зависит от выбранного метода металлизации. Важно соблюдать технику безопасности при работе с химикатами.
Процесс химической металлизации отверстий
Рассмотрим более подробно этапы химического метода металлизации, как наиболее эффективного:
1. Подготовка поверхности
Включает очистку, обезжиривание и придание шероховатости стенкам отверстий для лучшей адгезии. Можно использовать мелкую наждачную бумагу и спирт.
2. Сенсибилизация
Обработка поверхности раствором хлорида олова для создания центров кристаллизации. Типовой состав — 10 г/л SnCl2 и 40 мл/л HCl.
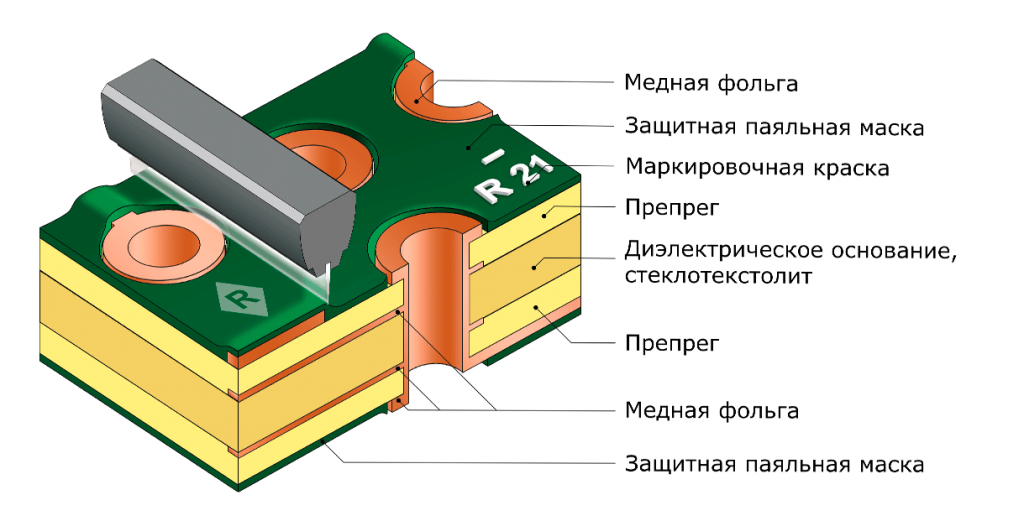
3. Активация
Погружение платы в раствор хлорида палладия для образования каталитических центров роста меди. Используется раствор 0,1-0,5 г/л PdCl2.
4. Химическое меднение
Осаждение тонкого слоя меди из раствора, содержащего сульфат меди, ЭДТА, формальдегид и гидроксид натрия. Время 15-30 минут при 20-30°C.
5. Гальваническое усиление
Наращивание слоя меди электролитическим способом до требуемой толщины, обычно 25-30 мкм.
Важно тщательно соблюдать режимы и время обработки на каждом этапе для получения качественного покрытия.
Особенности графитирования отверстий
Метод графитирования отверстий печатных плат имеет ряд особенностей:
- Используются специальные графитовые пасты или спреи
- Нанесение выполняется кисточкой или распылением
- Важно добиться равномерного покрытия стенок
- Излишки графита удаляются продувкой или протиркой
- Для улучшения адгезии проводится термообработка
- Проводимость ниже, чем при химическом меднении
Преимущества метода — простота, доступность материалов, отсутствие агрессивной химии. Подходит для прототипов и несложных плат.
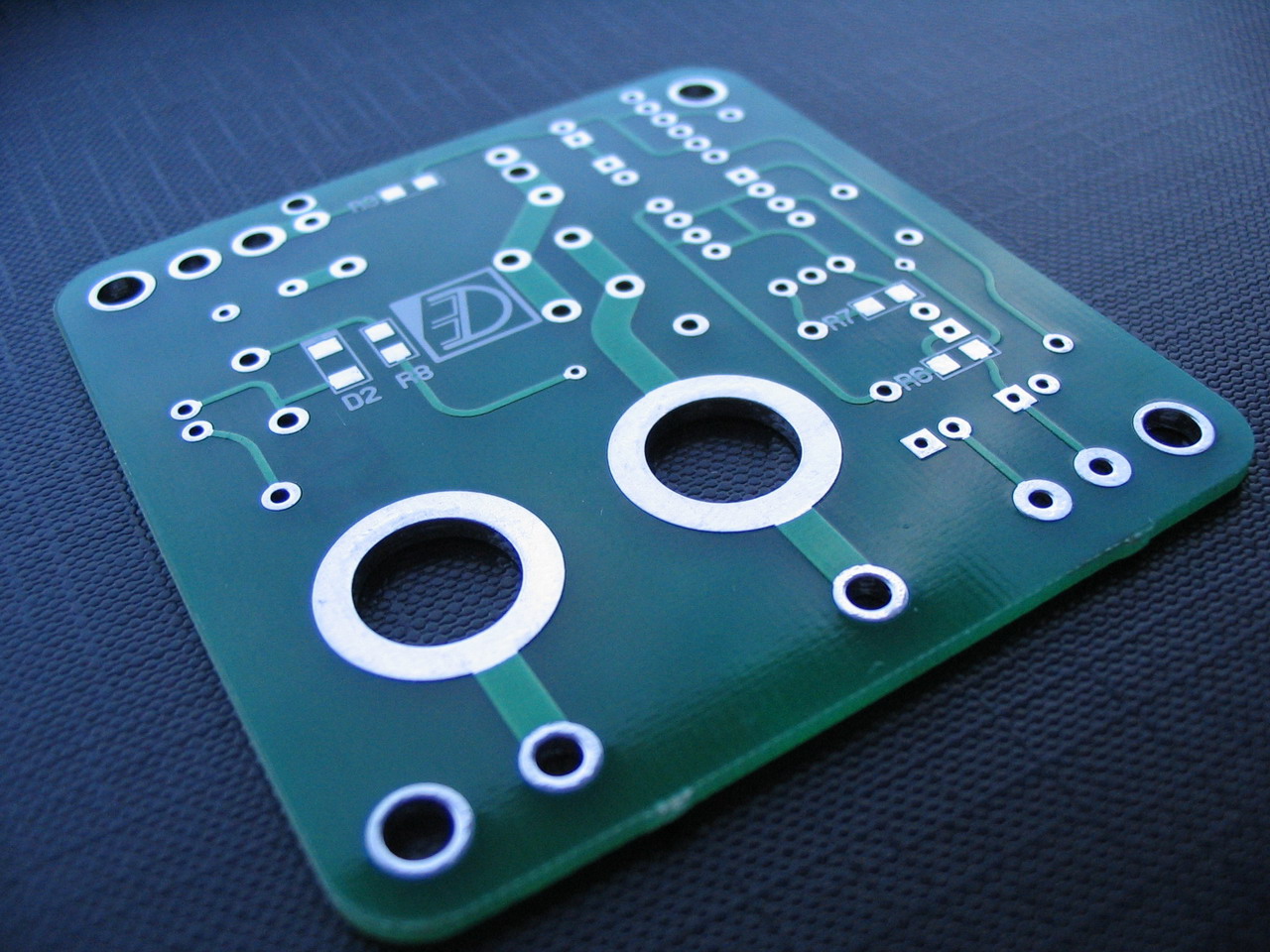
Механические способы металлизации отверстий
При механической металлизации используются следующие варианты:
Впаивание проволоки
В просверленные отверстия вставляется тонкая медная проволока и припаивается с двух сторон платы. Простой, но трудоемкий способ.
Установка заклепок
В отверстия устанавливаются специальные металлические заклепки и расклепываются. Обеспечивает надежный контакт.
Расклепывание штифтов
Медные штифты вставляются в отверстия и расклепываются с двух сторон. Требует специального инструмента.
Механические методы не требуют химической обработки, но более трудоемки при большом количестве отверстий.
Проверка качества металлизации отверстий
После выполнения металлизации необходимо проверить качество полученных соединений:
- Визуальный осмотр на равномерность покрытия
- Проверка электрического сопротивления мультиметром
- Тест на адгезию покрытия
- Микрошлиф для оценки толщины слоя
- Испытание на устойчивость к термоциклированию
При обнаружении дефектов может потребоваться повторная обработка проблемных участков или всей платы.
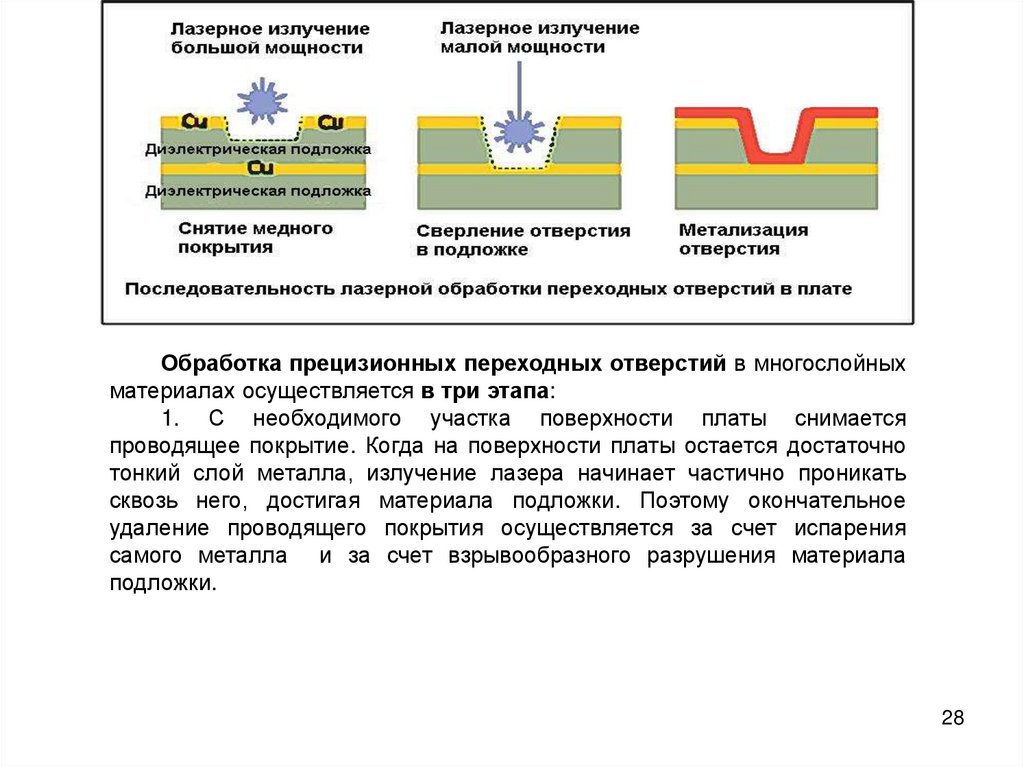
Меры безопасности при металлизации отверстий
При выполнении металлизации отверстий печатных плат в домашних условиях важно соблюдать следующие меры безопасности:
- Работать в хорошо проветриваемом помещении
- Использовать защитные очки, перчатки, халат
- Не допускать попадания химикатов на кожу и в глаза
- Соблюдать осторожность при нагреве растворов
- Утилизировать отработанные растворы правильно
- Иметь под рукой средства нейтрализации химикатов
Безопасность при работе с химическими веществами должна быть приоритетом. При отсутствии опыта лучше начинать с более безопасных механических методов.
Металлизация отверстий в картинках (часть І, приготовление активатора)
Давно собирался описать процесс металлизации в подробностях, но все никак не мог завершить эксперименты с разными добавками в активатор (и их количеством), вылизывал все технологические шаги. Ну и какое-то время просто не мог окончательно определиться с тем, какой вариант описывать. После некоторых колебаний решил все-таки описывать вариант с добавкой жидкого мыла. Выбор на этот вариант пал по двум причинам: реактивы доступнее и после термолиза заготовка отмывается гораздо легче. Второй пункт особенно важен в этой технологии, поскольку городить вторую гальванику как-то не улыбалось (хотя «на коленке» я этот вариант отмывания продуктов пиролиза и попробовал). Из минусов — необходимость делать активацию быстро, но тут сложно сказать, минус это или плюс.Итак.
Небольшой экскурс в теорию, историю и воздание должного людям, которые сделали этот метод доступным для любителей.
В основе этого метода лежит способность некоторых соединений меди разлагаться под действием тепла с выделением металлической меди. Этот метод появился в результате работ над беспалладиевыми технологиями металлизации начатых еще во времена бывшего СССР. После развала СССР работа не была остановлена и в начале 90-х группа химиков из Новосибирского Института химии твердого тела и механохимии возглавляемая Олегом Ивановичем Ломовским получила последний патент на эту технологию. Собственно говоря, тот метод, описание которого приведено ниже, это только адаптация технологии описанной в патенте.
Ну а теперь, когда все нужные реверансы сделаны, перейду к, собственно, технологии.
ВНИМАНИЕ! ВСЕ РАБОТЫ ПО ПРИГОТОВЛЕНИЮ РАСТВОРА И ОБРАБОТКЕ ПЛАТЫ ВЫПОЛНЯЮТСЯ В ПЕРЧАТКАХ!
В процессе обработки в активаторе поверхности платы касаться категорически не рекомендуется, даже если руки в перчатках. Это уже забота о результате, а не о руках.
Для работы понадобятся следующие реактивы и приборы:
Реактивы:
1. Сульфат меди (ІІ) (он же медный купорос)
Нужен именно реактив, Ч (чистый) или ЧДА (чистый для анализа). Можно, конечно и ХЧ (химически чистый) или ОСЧ (особо чистый), но мне такой не попадался. Купорос, который продается в магазинах сад-огород может содержать неизвестное количество примесей.
2. Фосфорноватистокислый кальций (он же гипофосфит кальция, он же фосфинат кальция).
Тоже Ч или ЧДА (и, конечно же, ХЧ или ОСЧ).
3. Дистиллированная вода. Вполне подойдет та, что продается в автомагазинах.
Аптечный нашатырный спирт тоже подойдет, но его придется лить больше и скорректировать количество воды (сколько именно — я не считал, но, полагаю, с этой задачей из школьного курса химии справятся все).
5. Жидкое мыло. Подойдет любое, но по возможности стоит брать то, в котором поменьше всяких добавок (оно, обычно, еще и дешевле). Так же стоит отдавать предпочтение мылу с нейтральным pH, такое мыло, обычно усиленно подчеркивает этот факт на упаковке.
Инструменты и материалы:
1. Бытовые весы с разрешением хотя бы в 1 грамм (точнее, на самом деле и не нужно).
2. Две емкости в которых готовится раствор, стеклянные или пластиковые. Емкость первой где-то от литра и больше. Емкость второй — около полулитра.
3. Пластиковый судок с плотно закрывающейся крышкой. Это будет рабочая емкость в которой активатор хранится и в которой же обрабатываются платы.
5. Несколько влажных салфеток для рук (если есть старые высохшие — это даже лучше). Крайне желательно подобрать такие, которые без каких-либо добавок. Салфетки перед использованием надо положить в теплое место и просушить. Эти салфетки будут использоваться для фильтрации. Поскольку осадка много, обычные бумажные салфетки не выдерживают. К тому же они впитывают слишком много жидкости и таким образом влияют на состав, что не желательно.
6. Большой шприц на 20 или (лучше) на 60мл.
ВНИМАНИЕ! Заключительные этапы приготовления раствора (начиная с шага 7) лучше проводить на открытом воздухе или под вытяжкой. Все-таки, аммиак изрядно вонюч. Приготовленный раствор воняет значительно меньше и им вполне можно пользоваться в помещении.
Раствор готовится так:
(Для тех, кто смотрел другие рецепты, уточню, что рецепт «удвоенный» по количеству компонентов, «одинарного» маловато для удобной работы.)
1. Наливаем 140мл дистиллированой воды в первую емкость:
Для ускорения следующего шага воду желательно подогреть в микроволновке градусов до 35-40.
2. Насыпаем 30грамм купороса:
Затем тщательно перемешиваем до полного растворения в воде. Когда весь купорос растворится, получаем вот такую жидкость голубого цвета:
3. Насыпаем 22грамма гипофосфита кальция:
И мешаем получившуюся смесь несколько минут. Раствор быстро становится белесым, это выделяется сульфат кальция (гипс), который не растворим в воде:
4. Во вторую емкость ставим воронку, в воронку кладем салфетки:
5. Акуратно сливаем жидкость из первой емкости в воронку. При этом нужно периодически взбалтывать осадок, что бы он не остался в первой емкости. Когда фильтрация закончена получаем вот такую картину:
6. Через осадок проливаем 100мл воды. При этом осадок становится немного белее. Дожидаемся пока вся жидкость стечет, снимаем лейку и получаем раствор гипофосфита меди в воде:
7. В раствор добавляем с помощью шприца 40мл аммиачной воды в раствор. Если шприц большой, то это можно сделать за один раз, с 20-кой прийдется сделать два захода. Выдавливать аммиачную воду в раствор удобнее всего опустив кончик шприца прямо в раствор, это позволяет избежать разбрызгивания. Если нужно делать два захода, то между заходами кончик шприца следует ополоснуть в дистиллированой воде. Раствор мгновенно густеет и в нем появляются белые хлопья:
Медленно помешиваем раствор до полного исчезновения хлопьев и превращения раствора в однородную жидкость темно-синего цвета:
Этот раствор уже воняет значительно меньше и продолжить процесс можно в помещении, при необходимости.
8. Добавляем в раствор 5-6мл жидкого мыла:
9. Добавляем в раствор 8-10 грамм гипофосфита кальция:
Еще раз тщательно перемешиваем. Гипофосфит не растворяется полностью, но нерастворившийся осадок тоже нужен, он будет поддерживать концентрацию ионов гипофосфита в растворе по мере использования. Продолжая помешивать переливаем раствор в рабочую емкость. При этом нужно следить, что бы осадок полностью перелился вместе с остальным раствором. Активатор готов.
Активатор стабилен и может храниться долгое время. В процессе использования нужно следить за тем, что бы на дне все время был осадок гипофосфита кальция и при необходимости досыпать пару грамм. Если этого не делать, могут появляться неметаллизированные отверстия.
В следующей части я опишу собственно процесс металлизации.
Металлизация отверстий печатных плат в домашних условиях
С необходимостью этого сталкиваются в основном те, кто использует в конструировании образцы гетинакса с двухсторонним фольгированием. Чтобы впоследствии на плате собрать рабочую схему, нужно добиться качественного эл/контакта между ее токопроводящими слоями. Судя по отзывам на соответствующих форумах, существует несколько апробированных и относительно несложных для исполнения в домашних условиях методик металлизации отверстий печатных плат.
Это можно сделать по-разному, используя те или иные реактивы и приемы. У каждого опытного мастера-любителя – своя излюбленная технология. Рассмотрим наиболее распространенные в домашних условиях способы серебрения и графитирования отверстий. Они привлекательны не только простотой исполнения, но и доступностью хим/препаратов.
Серебрение
Подготовительные мероприятия
Технология основана на том, что под воздействием ультрафиолета нитрат серебра (более известный как ляпис AgNO3) разлагается на компоненты, один из которых – чистый металл.
- Отверстия в плате зачищаются.
- Каждое из них обрабатывается раствором (25±5%) азотнокислого серебра.
- Далее – просушка печатной платы. Чтобы ускорить течение химической реакции, целесообразно для этих целей использовать УФ-лампу. В результате на гетинаксе (в районе отверстий) останутся лишь отдельные вкрапления серебра.
Получение токопроводящего слоя
Для этого понадобится медь. Ее получают из раствора. Металл осаждается на подготовленную «основу» из серебра, тем самым обеспечивая в дальнейшем надежный эл/контакт между всеми элементами схемы.
Состав раствора (из расчета на 100 мл теплой воды)
Купорос медный 2 и натр едкий 4 (в г) + глицерин 3,5 + 25% спирт нашатырный 1+ 10% формалин 11±4 (в мл).
Данный раствор крайне неустойчив, и срок его пригодности ограничен. Поэтому препарат готовить про запас бессмысленно. Только в нужном количестве и перед непосредственным применением, когда первичная обработка отверстий (серебрение) уже выполнена. Процентное соотношение компонентов в зависимости от требуемого объема раствора несложно рассчитать по приведенному рецепту.
Усиление отверстий
Выполненной металлизации достаточно лишь в случае, если при монтаже электронной схемы предполагается работать с миниатюрными радиодеталями. Но, как показывает практика, слоя хватает на один раз. Следовательно, говорить о ремонтопригодности печатной платы уже не приходится. Именно поэтому толщина металлизированного слоя увеличивается гальваническим способом, как никелирование, например.
Состав раствора (из расчета на 1 000 мл)
Концентрированная кислота, серная (70 мл) + медный купорос (250 г).
- «Минус» – на фольгированном покрытии платы, «плюс» – на пластинке из меди. Она располагается параллельно обрабатываемому образцу.
- Плотность тока (А/см2) выбирается в диапазоне 0,02 – 0,3.
- Напряжение (В): 3,5±0,5.
- Приемлемая температура (ºС) в гальванической ванне – от 20 до 28.
Более качественный, однородный слой получается при меньшем токе. Но это увеличивает время протекания процесса металлизации отверстий.
Графитирование
Еще один несложный в исполнении способ металлизации. Отличие в том, что для первичной обработки отверстий вместо серебрения делается графитирование. Чаще всего любители используют магазинный аэрозоль CRAMOLIN «GRAPHITE». Откладывающиеся на поверхности мелкодисперсионные фракции графита достаточно вдавить в подготовленные отверстия. Это несложно сделать небольшим шпателем, скребком. Как их изготовить своими руками, пояснять не нужно.
Для удаления излишков, пока паста еще влажная, плата встряхивается. Фракции, налипшие на ее поверхность, смываются растворителем или убираются мелкой (шлифовочной) наждачкой. Остается лишь тонкой иглой прочистить отверстие.
В результате в нем получается тончайший токопроводящий слой. Такой способ удаления пасты имеет минус – не все фракции выводятся из отверстия, что уменьшает его диаметр. Более качественный результат достигается методом продувки. В домашних условиях можно задействовать пылесос.
Описанные способы металлизации отверстий – не единственные. Но именно их в свое время апробировал автор, и они доказали свою эффективность и удобство в реализации.
Металлизация отверстий печатной платы без применения химических реактивов
Дата: 6 Июня 2014. Автор: Алексей
Начну сразу с того что я уже пытался осаждать медь в отверстия методом гальваники и ничего из этого у меня не получилось. Да и еще литр аммиака в комнате разлил, так меня чуть из дома не выгнали. Пришлось вернутся к пропайке проводков вставленных в отверстия. Но это опять надоело да и с плавным параллельно использованием микроконтроллеров от ST часто возникал вопрос о установке переходного отверстия под МК. Вот тут пропайка проволочки никак не подходит. Опять полез в интернет за идеями. Благо таких как я замороченных этой темой много. Искал, искал и наткнулся на тему где говорили о так называемых пресовочных втулках(заклепках), мол вставил в отверстие заклепал и на те переход. Ну думаю надо такими обзавестись. В России я их не нашел. Может плохо искал, но друзья Китайцы из АлиЕкспресса с удовольствием отправили мне два мешка по 1000 и 1400 заклепок в каждом. После заказа полез искать приблуду чем сие чудо клепать. Долго искал и на одном из форумов нашел ссылку на немецкий сайт. О ужас! 360 евро за какой-то степлер!!! Это перебор. Короче есть у меня для поделок маленький токарный станочек и лекции по ТММ из института))) Кто изучал, поймет. И родной АВТОКАД))) Вот думаю получу клепочки и смастеру свой степлер с блекджеком и ш….. А пока решил опробовать еще одну интересную технологию. Люди предлагают для начала клепать проволоку в переходных отверстиях от кабеля UTP-5E. Ну думаю дай и я попробую. И не плохо получилось. Правда не сразу))) Вот об ентой технологии я хочу рассказать.
Что нам понадобится.
1. Протравленная плата. (Кто как, а я по этой технологии делаю) 2. Сверло. (я использую твердосплавные) 3. Молоток. (маленький как в детстве для колки орехов) 4. Выколотка 3мм. (Это типа кернера, но с тупым концом) продается в запчастях 5. Бокорезы. (именно бокорезы, а не кусачки) 6. Терпение и пиво. (можно чай)Теперь собственно где сверлить и что клепать.
На этих двух фотографиях хорошо видны пады под микросхемами. Их высота должна быть ниже брюха микросхемы. Диаметр падов я использую по умолчанию 1,2 мм, а отверстие сверлю 0,5 мм вот таким сверлом.
Для сравнения положил проволочку из жилы UTP-5E. Далее нужно немного дороботать выколотку. У нее конец сделан плоским и по началу я ей пробовал клепать, но после двух перебитых проводников решил немного ее допилить. Смысл вот в чем. Края очень острые и если слегка перекосить и попасть по тонкому проводнику, то бац и кромкой перерубаем проводник. Не хорошо. Поэтому я на наждаке немного скруглил кончик.
Далее дорабатываем тиски, а точнее наковальню на них.
В чем заключается доработка. Вот эти четыре вмятины я сделал кернером. У них разная глубина. Зачем они нужны? После того как просунули проволоку в переход ее нужно отрезать. А сколько? Вот для этой цели используется средняя самая большая вмятина. Пронизываем переходное отверстие проволокой и кладем на наковальню. проволока должна попасть в большое углубление. Далее чикаем сверху проволоку под корень и переносим плату на маленькую вмятину. Оно у меня самая правая. Так как углубление меньше, то часть проволоки вылезает наружу. Тут с глубинами вмятин надо экспериментировать, как со временем засветки резиста))) Поэтому у меня их четыре.
Далее аккуратно ставим на проволоку выколотку и бацц. Но не сильно, а то можно плату пробить насквозь)))
Вот что получается.
Далее переворачиваем плату и на ровной плоскости по второй стороне проволоки бацц и все. Далее таким макаром клепаем все переходные отверстия. Если нужно сделать переход для ножки микросхемы, то для DIP можно пропаять сверху, а для, например подстроечных резисторов где подлезть нельзя, делаем переходное отверстие вплотную с площадкой для детали и там клепаем. Далее по вкусу, лудим паяльником или сплавом РОЗЕ, или еще как. Но самое главное это переходы. их нужно лудить так. Берем паяльник с круглым острым жалом. Набираем припой, заливаем переходное отверстие(упс, уже не отверстие) флюсом, я использую ЛТИ-120, и тыкаем в цетр острием жала. Ждем немного пока пад прогреется и олово само стечет на него. Все. При таком лужении капелька получается маааааленькая, а за счет принципа спайки двух ног( это когда при пайке SOIC микрух можно ляпнуть на две ноги, а потом матерясь пытаться снять лишний припой) она наглухо спаивает пад и проволоку воедино.
Вот готовая плата.
А это в собранном виде и в работающем состоянии. Вроде все работает.
Да, вот еще, не забудьте перед напайкой деталей прозвонить все проводники на тему разрыва. Все же это механическая металлизация. Ну вот и все. Удачных плат и жаркого лета)))
Зы! Пришли клепки. Как этот бисер клепать???
Правда под ноги с растоянием 2,54 они не подошли.
Виталий 03.12.14
это не заклёпки, это люверсы ))) для тканей www.youtube.com/watch? v=z7BGVtT6BBw
Алексей 03.12.14
Да какая разница)) Все равно для микросхем не подходит. Да и клепальник я так и не сделал. Короче лежат у меня два мешка и радуются.
ПосетительВя 24.04.15 21:54
я когда занимался радиовредительством о кроватках под МС только слышал. А что бы микруха при эвакуации не тянула за собой дорожки пользовался фольгой от остатков. опытным путём определяется ф сверла, (зачищенная от остатков клея фольга обычно сворачивается в трубочку только в другую сторону)втыкается трубочка в отвертсие и развальцовывается иглой. После с другой стороны обрезается лишнее и так же вальцуется. Долго, нудно, но того стоит…
Алексей 26.04.15 10:26
Жду из Китая плату управления для MACh4, хочу все таки попробовать сначала сверлить, а потом химически металлизировать. Слышал что есть набор меднения диэлектриков. Хочу найти такой и попробовать.
Алексей 15.09.15 22:36
В свое время (в году так 2000ом) видел мешки с «заклепками» для металлизации отверстий 2хсторонних печатных плат. Было это в Питере на рынке «Юнона». И выглядели они как обычные втулки, только очень мелкие. Так как я не занимался профессионально электроникой, то мне они как бы и не нужны были… Думаю что и щас их там можно найти если поспрашивать…
Алексей 16.09.15 08:25
Узнавал, есть такие. Немецкие. Цена заклёпок + крёпальник стоит столько денег, что мне проще в Китае заказать готовые на всю оставшуюся жизнь. Сейчас Китай делает платы пр 1$ за платку 5см на 5см, при заказе 10 шт. А если мне нужно сделать самому, то если много переходов, клепаю, а если мало, то перемычки впаиваю. Да и еще я в Москве живу и ради заклёпок в Питер ехать… )))
Металлизация отверстий в домашних условиях
Металлизация отверстий в печатных платах
Технология металлизации
С помощью этого метода прямой металлизации отверстий можно добиться качественных результатов при изготовлении двухсторонних печатных плат в домашних условиях. Главным условием 100% прямой металлизации отверстий в этой технологии, является правильное приготовления активатора поверхности диэлектрика на основе аммиачного комплекса гипофосфита меди и соблюдение некоторых правил при активации поверхности этим раствором.
Как приготовить этот активатор на основе гипофосфита меди для прямой металлизации отверстий, подробно описано в этой статье.
Процесс прямой металлизации
Далее технология металлизации будет описана виде фото-галереи с некоторыми пояснениями. Все фотки кликабельны. Также наведя на фото мышкой, можно прочитать описание к ней во всплывающем окне.
Сразу хочу сказать, эта платка тестовая и делалась только для описания этого процесса.
Сверление отверстий
Итак берем текстолит, подготавливаем поверхность для нанесения фоторезиста (с одной стороны). Клеим фоторезист на одну сторону, берем фотошаблон с центрами будущих отверстий платы, засвечиваем, проявляем фоторезист (этот этап я к сожалению не смог сфотографировать, но думаю тут все понятно). Как только проявили фоторезист, с другой стороны платы клеим скотч для защиты меди и травим плату в персульфате аммония или хлорном железе:
Платка вытравилась, нужно смыть фоторезист. Для этого кидаем плату в едкий натр (NaOH) или средство «Крот» на 10 минут, затем фоторезист легко смывается с поверхности платы. Можно не смывать фоторезист на этом этапе, а смыть его после сверловки отверстий. Как только смыли фоторезист, то на медной фольге видны центры будущих отверстий, вот по ним сверлим отверстия на станочке или вручную. После сверловки отверстий, с другой стороны текстолита будут заусенцы, которые нужно будет удалить:
Для чего зашкуриваем плату с обоих сторон мелкой шкуркой, потом круговыми движениями иголки, поправляем отверстия и тем самым убираем оставшиеся заусенцы. После этого опять зашкуриваем печатную плату мелкой шкуркой:
Активация диэлектрика
На следующем этапе берем персульфат аммония и приготовленный раствор активатора на основе гипофосфита меди. Сначала травим плату в персульфате аммония 20 секунд (для придания меди миро-шероховатости), затем не касаясь меди пальцами, промываем плату в воде и опускаем в раствор активатора на 1 минуту. Платку в растворе нужно постоянно покачивать, чтобы отверстия гарантированно наполнились активатором.
Вынимаем плату из активатора, даем стечь лишнему раствору с поверхности и не стряхивая плату (самое главное, чтобы отверстия были наполнены активатором) производим термический удар (нагрев) любым доступным способом при температуре 150 градусов в течении 10 минут. Самое главное в этом процессе, следить за тем, чтобы раствор не выкипел из отверстий, а равномерно испарился.
Плата в конце процесса термоудара потемнеет, что является признаком удачного разложения гипофосфита меди на металлическую медь, на которую и будет производится прямая металлизация:
Подготовка платы перед гальваникой
После термоудара даем плате остыть, затем если необходимо, прочищаем отверстия иголкой и обязательно моем моющем средством. До печатной платы руками не касаемся:
Гальваника печатной платы
Опускаем плату в гальваническую ванну и начинаем процесс прямой металлизации. Держим плату в гальванике около 2 часов, постоянно покачивая плату, ток 2 ампера на дм.кв. Процесс покрытия медью заканчиваем, вытаскиваем плату и смотрим на качество металлизации, она 100%. Зашкуриваем поверхность мелкой шкуркой:
Формируем дорожки печатной платы
Теперь перейдем собственно к изготовлению самой печатной платы. Для этого клеим фоторезист на одну сторону печатной платы, готовим фотошаблон без центров отверстий, ровняем его на плате по отверстиям, засвечиваем и проявляем. Смотрим, что бы отверстия были качественно накрыты тентами фоторезиста (если тенты порваны, то заливаем отверстия лаком), иначе после травления в хлорном железе, металлизация в этих местах протравится и вся работа пойдет насмарку:
После проявки фоторезиста, засвечиваем платку еще раз, для более качественного закрепления фоторезиста. Заклеиваем скотчем обратную сторону платы и травим в персульфате аммония или хлорном железе.
Вообще этот этап можно пропустить, то есть изначально клеить фоторезист с обоих сторон, засвечивать и проявлять, затем травить обе стороны платы в хлорном железе одновременно:
Данная статья опубликована на сайте whoby.ru. Постоянная ссылка на эту статью находится по этому адресу http://whoby.ru/page/metgfmed
Читайте статьи на сайте первоисточнике, не поддерживайте воров.
Как сделали одну сторону, то же самое делаем с другой стороны печатной платы. Приклеиваем фоторезист, выравниваем шаблон по отверстиям, засвечиваем, проявляем. После проявки смотрим на качество тентов над отверстиями, если некоторые порваны, то корректируем (лаком), затем засвечиваем еще раз:
Заклеиваем скотчем и травим в персульфате или хлорном железе, Затем берем едкий натр (NaOH):
И смываем фоторезист с обеих сторон платы. Смотрим качество металлизации, протравы под тентами (если они есть). Все в порядке, теперь плату нужно покрыть оловом.
Лужение платы сплавом розе
Что бы олово качественно покрыло проводники, нужно подготовить поверхность меди. Для этого кидаем плату в раствор лимонной кислоты 20 мл воды, чайная ложка лимонки, для очистки от окислов.
Затем готовим раствор, в котором будем лудить плату. Для чего берется один пузырек глицерина 20 мл. 100 мл воды и чайная ложка лимонной кислоты. Затем этот раствор нагревается до кипения и в него кладется сплав Розе:
Опускаем плату в раствор и движениями губки покрываем проводники оловом. На этом этапе главным является заполнение всех отверстий оловом. Затем вытаскиваем плату из раствора и греем над газом до расплавления сплава Розе. Как только сплав расплавится, быстро ударом стряхиваем лишний припой из отверстий. Важно, что бы не осталось припоя в отверстиях, для этого смотрим на просвет:
Еще раз опускаем платку в глицериновый раствор, но уже без сплава Розе в нем и нагреваем до кипения. Движениями губки удаляем лишний припой с проводников. Если одно или несколько отверстий опять заполнятся оловом, то повторяем операцию со встряхиванием. В результате получилась вот такая симпатичная платка с металлизацией отверстий:
Заключение
Как видите, ни чего сложного в прямой металлизации отверстий с помощью гипофосфита меди нет. Платы получаются достойного качества.
Советую для начала опробовать эту технологию прямой металлизации сначала на маленьких платах, чтобы появился опыт, а уже потом делать более сложные платы.
Основоположником данного метода активации является группа химиков из Новосибирского Института химии твердого тела и механохимии возглавляемая Олегом Ивановичем Ломовским. Она получила последний патент на эту технологию.
В развитии этой технологии была проведена большая работа пользователем JIN с форума vrtp.ru (ссылка на тему форума). Благодаря которой этот метод вышел в массы радиолюбителей.
Затем продолжил эти начинания пользователь evsi с форума Радиокот (ссылка на профиль форума). Подробный рецепт этого активатора был им опубликован на сайте Easyelectronics.ru (ссылка на статью).
Автор статьи: Admin Whoby.Ru
Если вам понравилась статья, нажмите на кнопку нужной социальной сети расположенной ниже. Этим действием вы добавите анонс статьи к себе на страницу. Это очень поможет в развитии сайта.
металлизация отверстий
После первых удачных разработок, где в дырки для простоты (и быстрого получения результата) забивались медные клепки, появилось желание металлизировать отверстия :
Гипофосфит меди (раствор активатора)
Дигидрат гипофосфит диаминмеди два
Раствор:
Гипофосфит кальция (кальций фосфорноватистокислый) — 20 гр. [Ca(Ph3O2)2]
Медный купорос (Медь 2 сернокислая 5вод) — 25 гр. [CuSO4·5h3O] (кстати в магазинах для садоводов продается)
Аммиак (аптечный 10%), = 10%-й водный раствор гидроксида аммония — 50 мл. (Nh4+h30)
Дистиллированная вода 100 мл.
Моющее средство «Капля» — 3 гр. (вода, ПАВ, хлорид натрия, консервант, парфюмерная композиция, лимонная кислота, СИ 19140, 42090)
1. Медный купорос 25гр + вода 50ml = долго (+осадок)
2. Гипофосфит кальция 15гр + вода 50ml = долго
3. 1 вливаем в 2. (перемешать) = +осадок
4. фильтр (осадок выкинуть)
5. + 50 мл. аптечного 10% аммиака
6. + 5 грамм гипофосфита кальция
7. + моющее средство (жидкое мыло)- 3 гр
Плату зачищаем с абразивным моющим средством без фанатизма, промываем тщательно.
По окончании промывки вода должна «липнуть» к заготовке, стекая с нее крайне неохотно.
Тщательно стряхиваем, опускаем в активатор горизонтально , не касаемся дна.
Несколько раз 2-3 сек
вынимаем горизонтально на поверхностью.
Жидкость должна равномерно затечь во все отверстия
Наклоняем и краем касаемся края емкости, чтобы излишки активатора стекли обратно (без фанатизма).
Закрывает емкость с активатором
наклоняем под разными углами, стараясь дать возможность активатору растечься как можно равномернее.
Потом кладем в печку выставляем 125С и держим 12-15 минут.
Потом 175С и держим 7-8минут
открываем дверку и даем остыть мин до 100С.
Моющим средством без абразива и мягкой губкой легко отмываем (пока без воды).
Мочалкой продавливаем моющее средство сквозь все отверстия спокойно не торопясь , стараясь ничего не пропустить.
Далее струей воды, промываем все отверстия.
не нужно отмывать все до единого пятна.
Активатор храниться долго, главное чтобы аммиак из него не испарился, то есть храним герметично (в темноте).
Значит емкость лучше — бутылка где минимум не занятого жидкостью пространства.
У меня хранился на балконе месяц до -10С доходило.
Раз 10 пользовался без проблем (свойства активатора сохранялись).
Активатор стабилен и может храниться долгое время. В процессе использования нужно следить за тем, что бы на дне все время был осадок гипофосфита кальция и при необходимости досыпать пару грамм.
Если этого не делать, могут появляться неметаллизированные отверстия.
электролиз
Раствор:
10 гр. медного купороса растворяется
в 100 мл. воды
туда доливаем 1см3 (=1мл) серной кислоты (электролит для свинцовых автомобильных аккумуляторов) = раствор серной кислоты
Блескообразующую добавку RV-T по возможности.
Электроды надо закрывать полностью
Емкость:
посередине катод — МИНУС(наша плата), двигается влево / вправо (ардуина + серво двигатель на пластмассовых внутренностях CD ROMа)
по бокам анод — это ПЛЮС .
Даем ток 2А из расчета на 1дм2 платы. Моя первая установка для электролиза выглядела так:
Электролит живет долго, главное следить за его чистотой (фильтровать, через ватные диски или марлю).
Электролит у меня хранится в обычной пластмассовом пищевом контейнере (хранить можно где угодно).
Использовать печку для приготовления пищи понятно нельзя. Пробовал нагревать плату на плите и по неопытности пережарил плату вплоть до размягчения текстолита — вонь была ужасная. Пришлось купить обычную печку 25$ (до 250С) и сразу процесс пошел в правильном направлении. Результат после 10мин электролиза. К сожалению МИНУС был подан только на одну сторону платы (вторая была без потенциала), но надо признаться все очень даже обнадеживающе :
дырки 0.4мм
Фоткал подсвечивая снизу фонариком.
В результате надо сделать вывод, что медь в дырках осаждается, хотя и не достаточно равномерно (есть заметные проплешины).
Не нужным эффектом является также осаждение меди на всей плоской поверхности платы, увеличивая и без того достаточную толщину меди 0.35мм.
Дело в том , что медь расходуется довольно интенсивно и Анод на глазах исчезает.
Может быть имеет смысл все закрывать маской из чего нибудь и оставлять только дырки?
Хлоррид паладия , метод подороже
Серебрение , Активатор — нитрат серебра (ляпис AgNO3)
Купорос медный 2 и натр едкий 4 (в г) + глицерин 3,5 + 25% спирт нашатырный 1+ 10% формалин 11±4 (в мл).
Не хранится долго
Графитирование
ручная металлизация без химии
LPKF рекламирует чудо пасту для металлизации отверстий без химии, т.е. без электролиза.
Просто втираем пасту в отверстия и греем плату.
Но найти в интернете в открытом доступе нельзя , на али тоже естественно нет.
По запросу прислали цены для России такие:
Полный набор:
115790 Базовый набор для металлизации ProConduct € 970,00.
Или его компоненты:
116110 Паста полимерная для ProConduct 20х2,9гр. € 222,00
116159 ProConduct foil consumable set (Пленки) € 109,36
115891 LPKF — Cleaner for ProConduct(Очиститель) € 37,38
Какие ключевые слова ищем в интернете
Pcb plating foil
protection film
hot air convection oven
pcb plating paste plumber
conductive copper paste
electrically conductive paste
Carbon Conductive Assembly Paste
Through-Hole Plating With Rivets
Chemical-Free Through-Hole Plating
Through-Hole Electroplating
Galvanization
liquid tin
Immerse tin plating
No-clean, lead-free solder paste is a modified rosin based paste, which allows repeatability and consistency. The Patented Nihon Superior nickel stabilized tin/copper eutectic alloy has a melting point of 227°C. Size: 250 gram jar
Химическое лужение
20 г хлористого олова SnCl2 • 2h3O;
40 г концентрированной серной кислоты h3SO4;
80 г тиомочевины;
5 г препарата ОС-20;
до 1 л дистиллированной воды
Металлизация отверстий в картинках (часть ІІ, подготовка к гальванике)
Продолжение описания процесса металлизации отверстий в домашних условиях начатое в первой части.
Напоминаю: РАБОТАЕМ В ПЕРЧАТКАХ!
Применительно к данному этапу ВАЖНО ПОМНИТЬ СЛЕДУЮЩЕЕ:
1. ЗАГОТОВКИ РУКАМИ КАСАТЬСЯ НЕЛЬЗЯ, ДАЖЕ В ПЕРЧАТКАХ!
2. ОТКРЫТАЯ ЕМКОСТЬ С АКТИВАТОРОМ ЯВЛЯЕТСЯ ИСТОЧНИКОМ АММИАКА! ДЕРЖИТЕ ГОЛОВУ ПОДАЛЬШЕ ОТ НЕЕ!
Приборы и инструменты:
1. Электропечь или аэрогриль. От них требуется возможность оперативно регулировать температуру. Если у вас есть термостатированная (хотя бы до +-5 градусов) печь или печь способная выдерживать температуру по заданному профилю (например, покупная/самодельная печь для пайки SMD) это даже лучше. Если такой печи нет и, в лучшем случае, имеется лишь «показометр» в виде регулятора или термометра с точностью +- пол-слона, то понадобится так же термометр способный мерять температур в диапазоне до 200 градусов. Термопара и тестер вполне подойдут.
2. Медицинский зажим (лучше длинный). Кто не в курсе, эта штука выглядит вот так:
Материалы:
1. Моющее средство с мягким абразивом.
2. Моющее средство без абразива.
Вот тот комплект моющих средств, которым я сейчас пользуюсь:
3. Две мягких губки, одна используется с первым моющим средством, другая — со вторым. И путать их не желательно.
4. Самая мелкозернистая шкурка, какую удастся найти или абразивный брусок (твердый поролон с нанесенным абразивом) с наибольшим номером (то есть наименьшим размером зерна).
Подготовка платы к процессу активации делается так:
1. Сверлим все отверстия в заготовке, причем сразу нужного диаметра. Сверлить нужно твердосплавными сверлами и на станке (дремель со станиной для сверления вполне подходит, думаю, с аналогичной проксоновской конструкцией, равно как и с самодельными сверлильными станками проблем не будет тоже).
Если сверлить несколько заготовок сразу или под заготовку подкладывать кусок ненужного стеклотекстолита, то заготовки не будут требовать зачистки отверстий совсем, так что шаг #3 можно пропустить. Следует помнить, что «подкладку» не стоит использовать дважды, в местах, где уже есть отверстия она работать не будет и появятся заусенцы. Ну и есть заметный риск сломать сверло.
2. Тщательно проверяем все отверстия на предмет попавшей стружки, завернувшихся заусенцев и прочего.
3. Зачищаем заготовку шкуркой или абразивным бруском. Особых усилий прикладывать не нужно, достаточно довести поверность меди непосредственно вокруг отверстий до уровня остальной меди (на ощупь отверстия перестают ощущаться как выступающие).
4. Тшательно промываем заготовку и проверяем чистоту отверстий. При необходимости отверстия нужно тщательно прочистить и еще раз промыть. На вид все отверстия одного диаметра должны выглядеть одинаково.
5. Моем заготовку губкой с абразивным моющим средством. Тщательно проходимся по всей поверхности заготовки, включая углы и края.
6. Тщательно промываем плату под струей воды. Когда моющее средство смыто с обеих сторон, еще раз проходимся струей воды по отверстиям, удерживая плату перпендикулярно струе, таким образом давая ей возможность промыть отверстия. По окончании промывки вода должна «липнуть» к заготовке, стекая с нее крайне неохотно. Если это не так, повторяем пункти #5 и #6 до получения нужного результата. На выходе этого шага заготовка выглядит примерно так:
Самый правый ряд отверстий (увы, его плохо видно даже на полноразмерной фотке) имеет диаметр 0.3.
7. Тщательно стряхиваем воду с заготовки и начинаем обрабатывать активатором. Для этого емкость с активатором открываем и удерживая заготовку за края или за углы не торопясь опускаем ее в активатор, но ни в коем случае не касаемся дна (там есть нерастворенный гипофосфит, который может вступать в реакцию с незащищенной медью). Через 2-3 секунды так же не торопясь приподнимаем заготовку так, что бы ее поверхность оказалась чуть выше поверхности активатора. При этом вокруг отверстий слой активатора быстро светлеет, поскольку активатора протекает в отверстия и слой тановится тоньше. Необходимо убедиться, что это произошло вокруг всех отверстий. Вокруг совсем мелких отверстий, типа 0.2-0.3-0.4, это происходит с некоторой задержкой, все-таки жидкости требуется некоторое время, что бы протечь через такое маленькое отверстие. Если этого не произошло, так же плавно опускаем заготовку в активатор на 2-3 секунды и так же плавно приподнимаем. Таких повторов имеет смысл делать 3-4, не больше и как только все отверстия смочились активатором, обработку следует закончить (см. следующий шаг). Если этого не произошло, то имеет место проблема с отверстиями, следует смыть активатор под струей воды и вернуться к шагу #4.
8. Как только все отверстия смочены активатором, поднимаем заготовку над активатором и поворачиваем одним углом вниз и даем возможность излишкам активатора стечь обратно в емкость. Касаясь углом заготовки стенки емкости с активатором (обеими сторонами) снимаем излишки жидкости. Особо усердствовать тут не надо, достаточно будет если активатор не будет капать сам с горизонтально расположенной заготовки. Отверстия продувать тоже не нужно. Если в каком-то из отверстий пленка активатора лопнула, ничего страшного, но самому что-либо делать для очистки отверстий не нужно.
9. Как только излишки активатора стекли в емкость, закрываем емкость с активатором, а заготовку наклоняем под разными углами, стараясь дать возможность активатору растечься как можно равномернее. В процессе заготовка потихоньку подсыхает и активатор перетекает все менее охотно. Как только активатор более-менее ровно распределен по поверхности можно переходить к термообработке. На выходе этого шага заготовка должна выглядеть примерно так:
10. Кладем плату в печь на подставки (я использую маленькие обрезки 2-мм стеклотекстолита), которые касаются заготовки только на самых краях (и ни в коем случае не на отверстиях). Сверху, при необходимости, устанавливаем спай термопары. Его нужно установить подальше от отверстий, но так, что бы он непосредственно касался платы.
11. Включаем нагрев и доводим температуру до 125 (+-5) градусов. При этой температуре заготовку нужно выдержать не менее 10 минут, лучше 12-15. К концу этого интервала плата приобретает следующий вид:
(сорри, из-за засветки от лампы аэрогриля сделать снимок получше не удается, а когда лампа гаснет, то тоже слишком темно, что бы увидеть цвет заготовки).
12. Доводим температуру до 175 (+-5) градусов и выдерживаем при такой температуре 5 минут, лучше 7-8.
13. По истечении времени выключаем печь и открываем крышку (но заготовку не трогаем) давая заготовке остыть. Заготовка при этом выглядит примерно так:
Как только ее температура опустится ниже 100 градусов, заготовку можна доставать. Для этого удобно пользоваться зажимом. Желательно не сильно усердствовать (зажимом довольно легко повредить фольгу на плате) и брать плату за самый край.
14. Слегка ополаскиваем плату в горячей, а затем в теплой воде. После этого снимаем зажим приступаем к отмывке.
15. На плату наливаем много моющего средства без абразива и мягкой губкой легонько начинаем отмывать (пока без воды). Затем переворачиваем плату и повторяем с другой стороны. Затем смываем пену полностью, ополаскиваем мочалку и снова наливаем моющее средство. Теперь мочалкой продавливаем моющее средство сквозь все отверстия, стараясь ничего не пропустить. Наконец смываем всю пену и промываем еще раз заготовку струей воды, стараясь промыть все отверстия. На выходе плата должна выглядеть примерно так:
Во время отмывки усилий прикладывать не нужно, так же не нужно отмывать все до единого пятна. Что смылось, то смылось, что нет, то нет. Попытка отмыть все вероятнее всего приведет к обрыву электрического контакта с медью в отверстиях и к браку. На простоту отмывки и качество заготовки на выходе напрямую влияет равномерность исходного слоя активатора. Применение абразивов на этом этапе также не желательно по той же причине.
Вот, собственно, и все, плата готова к гальванике.
P.S. Заготовка, на которой делались фотки, после 5 минут гальваники (3А/дм2):
Если присмотреться, можно заметить, что отверстия в плате имеют ровный слой меди. Крошечные участки не закрытые медью в самых больших отверстиях затянутся еще за 3-4 минуты.
Update Крупным планом:
До гальваники:
После гальваники:
Платы снимались еще мокрые, так что в отверстиях есть вода, она несколько мешает разглядеть подробности.
Металлизация переходных отверстий печатной платы кабельными наконечниками
Помню, в детстве, когда фольгированный гетинакс делался самостоятельно, с помощью клея «БФ» и утюга, у нас была мечта – пустотелые заклёпки.
В каком-то журнале публиковалась технология их изготовления. Предлагалось протянуть полоску фольги через коническое отверстие (подобие фильерной доски), чтобы получилась трубочка. Потом нужно нарезать трубочку и расклепать с двух сторон в плате.
Похоже, статья была неполная, потому что я до сих пор с трудом представляю, как можно реализовать её на практике в домашних условиях, начиная с изготовления фильеры.
Трудов было затрачено немало, но ничего путного так и не получилось. Конфигурация фильеры должна быть непростой, рабочая поверхность — отполированной, заготовка для неё — калёной, а самое главное – ширина полоски должна быть выдержана с довольно высокой точностью. Разрезать получающуюся трубку – ещё одна задача, да и расклепать тоже весьма непросто.
Недавно понадобилось мне сделать двустороннюю печатную плату. И не просто двустороннюю, а обязательно с переходами между слоями, так как при пайке доступа к противоположной стороне не будет. И не просто с переходами, а с достаточно мощными переходами, потому что по этим переходам предполагается протекание сравнительно больших токов.
Первой мыслью было сделать дополнительные площадки и соединить слои медными заклёпками из подходящего провода, но подсознание протестовало – решение-то неуклюжее…
но как-то не ассоциировались они у меня с заклёпками, пока у одного наконечника не свалился изолятор…
Вот тут-то всё и встало на свои места. В первый момент в голову стали приходить всякого рода развальцовки с фигурной формой рабочей части, весьма желательно, из подзакалённой стали, с отполированной поверхностью. Но, в конечном итоге, решил не заморачиваться и работать подручным инструментом.
↑ Инструмент
Кусачки, пассатижики, керн по диаметру отверстий и молоток. Конусное шило – важный инструмент в этом деле. У меня было заточенное в незапамятные времена (сейчас даже не представляю для чего), сверло – как раз впору пришлось. Ну и самое главное – многофункциональный инструмент, в домашнем обиходе именуемый «консервная банка», играющий роль наковальни.
Эксперименты показали, что получается вполне функционально, не по заводскому, конечно, но это не важно — неровные края заклёпок скрываются под припоем.
↑ Реализация
Вставляем развальцованную трубку в плату. Лучше, если отверстие в ПП будет максимально соответствовать наружному диаметру трубки наконечника, трубка должна входить плотно, с трудом. Максимально осаживаем пальцами. Специальную трубчатую осадку с молотком применять не стал. Получающийся в результате неполного прилегания развальцовки к плате запас, как раз и идёт на развальцовку заклёпки с другой стороны платы.
Обкусываем заклёпку заподлицо с фольгой. Как показала практика, обкусывать лучше всего бокорезами с плоскими (без фаски) режущими поверхностями.
Трубка, естественно, сжимается на резе, я пробовал, перед обкусыванием, вставлять внутрь трубки кусок обмоточного провода, но результат получился не шибко складным. Оказалось, что гораздо проще вставить со стороны развальцовки подходящее конусное шило и расправить этот сжим.
Дальше совсем просто. Осталось взять керн и развальцевать получившуюся заклёпку.
Пара лёгких ударов по выступающим краям и новенькая заклёпка стоит на своём месте. Иногда, по ситуации, бывает нужно слегка расширить отверстие конусным шилом.
Обрезок наконечника — сплющенную трубку слегка сжимаем пассатижами,
Расправляем шилом, вставляем в плату и развальцовываем расправленный конец
Получаем новую заготовку для пустотелой заклёпки
А дальше – всё по кругу… Вот результат – плата односторонняя
С другой стороны
С другой стороны.
В плату вставлены как раз те детали, из за которых всё и затевалось.
Надеюсь, моя идея использования кабельных наконечников пригодится согражданам.
Спасибо за внимание!
Металлизация отверстий печатных плат в домашних условиях — пошаговая инструкция
С необходимостью этого сталкиваются в основном те, кто использует в конструировании образцы гетинакса с двухсторонним фольгированием. Чтобы впоследствии на плате собрать рабочую схему, нужно добиться качественного эл/контакта между ее токопроводящими слоями. Судя по отзывам на соответствующих форумах, существует несколько апробированных и относительно несложных для исполнения в домашних условиях методик металлизации отверстий печатных плат.
Это можно сделать по-разному, используя те или иные реактивы и приемы. У каждого опытного мастера-любителя – своя излюбленная технология. Рассмотрим наиболее распространенные в домашних условиях способы серебрения и графитирования отверстий. Они привлекательны не только простотой исполнения, но и доступностью хим/препаратов.
Серебрение
Подготовительные мероприятия
Технология основана на том, что под воздействием ультрафиолета нитрат серебра (более известный как ляпис AgNO3) разлагается на компоненты, один из которых – чистый металл.
- Отверстия в плате зачищаются.
- Каждое из них обрабатывается раствором (25±5%) азотнокислого серебра.
- Далее – просушка печатной платы. Чтобы ускорить течение химической реакции, целесообразно для этих целей использовать УФ-лампу. В результате на гетинаксе (в районе отверстий) останутся лишь отдельные вкрапления серебра.
Получение токопроводящего слоя
Для этого понадобится медь. Ее получают из раствора. Металл осаждается на подготовленную «основу» из серебра, тем самым обеспечивая в дальнейшем надежный эл/контакт между всеми элементами схемы.
Данный раствор крайне неустойчив, и срок его пригодности ограничен. Поэтому препарат готовить про запас бессмысленно. Только в нужном количестве и перед непосредственным применением, когда первичная обработка отверстий (серебрение) уже выполнена. Процентное соотношение компонентов в зависимости от требуемого объема раствора несложно рассчитать по приведенному рецепту.
Усиление отверстий
Выполненной металлизации достаточно лишь в случае, если при монтаже электронной схемы предполагается работать с миниатюрными радиодеталями. Но, как показывает практика, слоя хватает на один раз. Следовательно, говорить о ремонтопригодности печатной платы уже не приходится. Именно поэтому толщина металлизированного слоя увеличивается гальваническим способом, как никелирование, например.
- «Минус» – на фольгированном покрытии платы, «плюс» – на пластинке из меди. Она располагается параллельно обрабатываемому образцу.
- Плотность тока (А/см2) выбирается в диапазоне 0,02 – 0,3.
- Напряжение (В): 3,5±0,5.
- Приемлемая температура (ºС) в гальванической ванне – от 20 до 28.
Более качественный, однородный слой получается при меньшем токе. Но это увеличивает время протекания процесса металлизации отверстий.
Графитирование
Еще один несложный в исполнении способ металлизации. Отличие в том, что для первичной обработки отверстий вместо серебрения делается графитирование. Чаще всего любители используют магазинный аэрозоль CRAMOLIN «GRAPHITE». Откладывающиеся на поверхности мелкодисперсионные фракции графита достаточно вдавить в подготовленные отверстия. Это несложно сделать небольшим шпателем, скребком. Как их изготовить своими руками, пояснять не нужно.
Для удаления излишков, пока паста еще влажная, плата встряхивается. Фракции, налипшие на ее поверхность, смываются растворителем или убираются мелкой (шлифовочной) наждачкой. Остается лишь тонкой иглой прочистить отверстие.
В результате в нем получается тончайший токопроводящий слой. Такой способ удаления пасты имеет минус – не все фракции выводятся из отверстия, что уменьшает его диаметр. Более качественный результат достигается методом продувки. В домашних условиях можно задействовать пылесос.
Описанные способы металлизации отверстий – не единственные. Но именно их в свое время апробировал автор, и они доказали свою эффективность и удобство в реализации.
Металлизация отверстий в печатных платах
Технология металлизации
С помощью этого метода прямой металлизации отверстий можно добиться качественных результатов при изготовлении двухсторонних печатных плат в домашних условиях. Главным условием 100% прямой металлизации отверстий в этой технологии, является правильное приготовления активатора поверхности диэлектрика на основе аммиачного комплекса гипофосфита меди и соблюдение некоторых правил при активации поверхности этим раствором.
Как приготовить этот активатор на основе гипофосфита меди для прямой металлизации отверстий, подробно описано в этой статье.
Процесс прямой металлизации
Далее технология металлизации будет описана виде фото-галереи с некоторыми пояснениями. Все фотки кликабельны. Также наведя на фото мышкой, можно прочитать описание к ней во всплывающем окне.
Сразу хочу сказать, эта платка тестовая и делалась только для описания этого процесса.
Сверление отверстий
Итак берем текстолит, подготавливаем поверхность для нанесения фоторезиста (с одной стороны). Клеим фоторезист на одну сторону, берем фотошаблон с центрами будущих отверстий платы, засвечиваем, проявляем фоторезист (этот этап я к сожалению не смог сфотографировать, но думаю тут все понятно). Как только проявили фоторезист, с другой стороны платы клеим скотч для защиты меди и травим плату в персульфате аммония или хлорном железе:
Платка вытравилась, нужно смыть фоторезист. Для этого кидаем плату в едкий натр (NaOH) или средство «Крот» на 10 минут, затем фоторезист легко смывается с поверхности платы. Можно не смывать фоторезист на этом этапе, а смыть его после сверловки отверстий. Как только смыли фоторезист, то на медной фольге видны центры будущих отверстий, вот по ним сверлим отверстия на станочке или вручную. После сверловки отверстий, с другой стороны текстолита будут заусенцы, которые нужно будет удалить:
Для чего зашкуриваем плату с обоих сторон мелкой шкуркой, потом круговыми движениями иголки, поправляем отверстия и тем самым убираем оставшиеся заусенцы. После этого опять зашкуриваем печатную плату мелкой шкуркой:
Активация диэлектрика
На следующем этапе берем персульфат аммония и приготовленный раствор активатора на основе гипофосфита меди. Сначала травим плату в персульфате аммония 20 секунд (для придания меди миро-шероховатости), затем не касаясь меди пальцами, промываем плату в воде и опускаем в раствор активатора на 1 минуту. Платку в растворе нужно постоянно покачивать, чтобы отверстия гарантированно наполнились активатором.
Термоудар
Вынимаем плату из активатора, даем стечь лишнему раствору с поверхности и не стряхивая плату (самое главное, чтобы отверстия были наполнены активатором) производим термический удар (нагрев) любым доступным способом при температуре 150 градусов в течении 10 минут. Самое главное в этом процессе, следить за тем, чтобы раствор не выкипел из отверстий, а равномерно испарился.
Плата в конце процесса термоудара потемнеет, что является признаком удачного разложения гипофосфита меди на металлическую медь, на которую и будет производится прямая металлизация:
Подготовка платы перед гальваникой
После термоудара даем плате остыть, затем если необходимо, прочищаем отверстия иголкой и обязательно моем моющем средством. До печатной платы руками не касаемся:
Гальваника печатной платы
Опускаем плату в гальваническую ванну и начинаем процесс прямой металлизации. Держим плату в гальванике около 2 часов, постоянно покачивая плату, ток 2 ампера на дм.кв. Процесс покрытия медью заканчиваем, вытаскиваем плату и смотрим на качество металлизации, она 100%. Зашкуриваем поверхность мелкой шкуркой:
Формируем дорожки печатной платы
Теперь перейдем собственно к изготовлению самой печатной платы. Для этого клеим фоторезист на одну сторону печатной платы, готовим фотошаблон без центров отверстий, ровняем его на плате по отверстиям, засвечиваем и проявляем. Смотрим, что бы отверстия были качественно накрыты тентами фоторезиста (если тенты порваны, то заливаем отверстия лаком), иначе после травления в хлорном железе, металлизация в этих местах протравится и вся работа пойдет насмарку:
После проявки фоторезиста, засвечиваем платку еще раз, для более качественного закрепления фоторезиста. Заклеиваем скотчем обратную сторону платы и травим в персульфате аммония или хлорном железе.
Вообще этот этап можно пропустить, то есть изначально клеить фоторезист с обоих сторон, засвечивать и проявлять, затем травить обе стороны платы в хлорном железе одновременно:
Данная статья опубликована на сайте whoby.ru. Постоянная ссылка на эту статью находится по этому адресу http://whoby.ru/page/metgfmed
Читайте статьи на сайте первоисточнике, не поддерживайте воров.
Как сделали одну сторону, то же самое делаем с другой стороны печатной платы. Приклеиваем фоторезист, выравниваем шаблон по отверстиям, засвечиваем, проявляем. После проявки смотрим на качество тентов над отверстиями, если некоторые порваны, то корректируем (лаком), затем засвечиваем еще раз:
Заклеиваем скотчем и травим в персульфате или хлорном железе, Затем берем едкий натр (NaOH):
И смываем фоторезист с обеих сторон платы. Смотрим качество металлизации, протравы под тентами (если они есть). Все в порядке, теперь плату нужно покрыть оловом.
Лужение платы сплавом розе
Что бы олово качественно покрыло проводники, нужно подготовить поверхность меди. Для этого кидаем плату в раствор лимонной кислоты 20 мл воды, чайная ложка лимонки, для очистки от окислов.
Затем готовим раствор, в котором будем лудить плату. Для чего берется один пузырек глицерина 20 мл. 100 мл воды и чайная ложка лимонной кислоты. Затем этот раствор нагревается до кипения и в него кладется сплав Розе:
Опускаем плату в раствор и движениями губки покрываем проводники оловом. На этом этапе главным является заполнение всех отверстий оловом. Затем вытаскиваем плату из раствора и греем над газом до расплавления сплава Розе. Как только сплав расплавится, быстро ударом стряхиваем лишний припой из отверстий. Важно, что бы не осталось припоя в отверстиях, для этого смотрим на просвет:
Еще раз опускаем платку в глицериновый раствор, но уже без сплава Розе в нем и нагреваем до кипения. Движениями губки удаляем лишний припой с проводников. Если одно или несколько отверстий опять заполнятся оловом, то повторяем операцию со встряхиванием. В результате получилась вот такая симпатичная платка с металлизацией отверстий:
Заключение
Как видите, ни чего сложного в прямой металлизации отверстий с помощью гипофосфита меди нет. Платы получаются достойного качества.
Советую для начала опробовать эту технологию прямой металлизации сначала на маленьких платах, чтобы появился опыт, а уже потом делать более сложные платы.
Основоположником данного метода активации является группа химиков из Новосибирского Института химии твердого тела и механохимии возглавляемая Олегом Ивановичем Ломовским. Она получила последний патент на эту технологию.
В развитии этой технологии была проведена большая работа пользователем JIN с форума vrtp.ru (ссылка на тему форума). Благодаря которой этот метод вышел в массы радиолюбителей.
Затем продолжил эти начинания пользователь evsi с форума Радиокот (ссылка на профиль форума). Подробный рецепт этого активатора был им опубликован на сайте Easyelectronics.ru (ссылка на статью).
Автор статьи: Admin Whoby.Ru
Еще записи по теме
металлизация отверстий
После первых удачных разработок, где в дырки для простоты (и быстрого получения результата) забивались медные клепки, появилось желание металлизировать отверстия :
Гипофосфит меди (раствор активатора)
Дигидрат гипофосфит диаминмеди два
Раствор:
Гипофосфит кальция (кальций фосфорноватистокислый) — 20 гр. [Ca(Ph3O2)2]
Медный купорос (Медь 2 сернокислая 5вод) — 25 гр. [CuSO4·5h3O] (кстати в магазинах для садоводов продается)
Аммиак (аптечный 10%), = 10%-й водный раствор гидроксида аммония — 50 мл. (Nh4+h30)
Дистиллированная вода 100 мл.
Моющее средство «Капля» — 3 гр. (вода, ПАВ, хлорид натрия, консервант, парфюмерная композиция, лимонная кислота, СИ 19140, 42090)
1. Медный купорос 25гр + вода 50ml = долго (+осадок)
2. Гипофосфит кальция 15гр + вода 50ml = долго
3. 1 вливаем в 2. (перемешать) = +осадок
4. фильтр (осадок выкинуть)
5. + 50 мл. аптечного 10% аммиака
6. + 5 грамм гипофосфита кальция
7. + моющее средство (жидкое мыло)- 3 гр
Плату зачищаем с абразивным моющим средством без фанатизма, промываем тщательно.
По окончании промывки вода должна «липнуть» к заготовке, стекая с нее крайне неохотно.
Тщательно стряхиваем, опускаем в активатор горизонтально , не касаемся дна.
Несколько раз 2-3 сек
вынимаем горизонтально на поверхностью.
Жидкость должна равномерно затечь во все отверстия
Наклоняем и краем касаемся края емкости, чтобы излишки активатора стекли обратно (без фанатизма).
Закрывает емкость с активатором
наклоняем под разными углами, стараясь дать возможность активатору растечься как можно равномернее.
Потом кладем в печку выставляем 125С и держим 12-15 минут.
Потом 175С и держим 7-8минут
открываем дверку и даем остыть мин до 100С.
Моющим средством без абразива и мягкой губкой легко отмываем (пока без воды).
Мочалкой продавливаем моющее средство сквозь все отверстия спокойно не торопясь , стараясь ничего не пропустить.
Далее струей воды, промываем все отверстия.
не нужно отмывать все до единого пятна.
Активатор храниться долго, главное чтобы аммиак из него не испарился, то есть храним герметично (в темноте).
Значит емкость лучше — бутылка где минимум не занятого жидкостью пространства.
У меня хранился на балконе месяц до -10С доходило.
Раз 10 пользовался без проблем (свойства активатора сохранялись).
Активатор стабилен и может храниться долгое время. В процессе использования нужно следить за тем, что бы на дне все время был осадок гипофосфита кальция и при необходимости досыпать пару грамм.
Если этого не делать, могут появляться неметаллизированные отверстия.
электролиз
Раствор:
10 гр. медного купороса растворяется
в 100 мл. воды
туда доливаем 1см3 (=1мл) серной кислоты (электролит для свинцовых автомобильных аккумуляторов) = раствор серной кислоты
Блескообразующую добавку RV-T по возможности.
Электроды надо закрывать полностью
Емкость:
посередине катод — МИНУС(наша плата), двигается влево / вправо (ардуина + серво двигатель на пластмассовых внутренностях CD ROMа)
по бокам анод — это ПЛЮС .
Даем ток 2А из расчета на 1дм2 платы. Моя первая установка для электролиза выглядела так:
Электролит живет долго, главное следить за его чистотой (фильтровать, через ватные диски или марлю).
Электролит у меня хранится в обычной пластмассовом пищевом контейнере (хранить можно где угодно).
Использовать печку для приготовления пищи понятно нельзя. Пробовал нагревать плату на плите и по неопытности пережарил плату вплоть до размягчения текстолита — вонь была ужасная. Пришлось купить обычную печку 25$ (до 250С) и сразу процесс пошел в правильном направлении. Результат после 10мин электролиза. К сожалению МИНУС был подан только на одну сторону платы (вторая была без потенциала), но надо признаться все очень даже обнадеживающе :
дырки 1мм
дырки 0.4мм
Фоткал подсвечивая снизу фонариком.
В результате надо сделать вывод, что медь в дырках осаждается, хотя и не достаточно равномерно (есть заметные проплешины).
Не нужным эффектом является также осаждение меди на всей плоской поверхности платы, увеличивая и без того достаточную толщину меди 0.35мм.
Дело в том , что медь расходуется довольно интенсивно и Анод на глазах исчезает.
Может быть имеет смысл все закрывать маской из чего нибудь и оставлять только дырки?
Хлоррид паладия , метод подороже
Альтернативный вариант
Серебрение , Активатор — нитрат серебра (ляпис AgNO3)
Купорос медный 2 и натр едкий 4 (в г) + глицерин 3,5 + 25% спирт нашатырный 1+ 10% формалин 11±4 (в мл).
Не хранится долго
Графитирование
ручная металлизация без химии
LPKF рекламирует чудо пасту для металлизации отверстий без химии, т.е. без электролиза.
Просто втираем пасту в отверстия и греем плату.
Но найти в интернете в открытом доступе нельзя , на али тоже естественно нет.
По запросу прислали цены для России такие:
Полный набор:
115790 Базовый набор для металлизации ProConduct € 970,00.
Или его компоненты:
116110 Паста полимерная для ProConduct 20х2,9гр. € 222,00
116159 ProConduct foil consumable set (Пленки) € 109,36
115891 LPKF — Cleaner for ProConduct(Очиститель) € 37,38
Какие ключевые слова ищем в интернете
Pcb plating foil
protection film
hot air convection oven
pcb plating paste plumber
conductive copper paste
electrically conductive paste
Carbon Conductive Assembly Paste
Through-Hole Plating With Rivets
Chemical-Free Through-Hole Plating
Through-Hole Electroplating
Galvanization
liquid tin
Immerse tin plating
No-clean, lead-free solder paste is a modified rosin based paste, which allows repeatability and consistency. The Patented Nihon Superior nickel stabilized tin/copper eutectic alloy has a melting point of 227°C. Size: 250 gram jar
AFAIK — металлорезист
Химическое лужение
20 г хлористого олова SnCl2 • 2h3O;
40 г концентрированной серной кислоты h3SO4;
80 г тиомочевины;
5 г препарата ОС-20;
до 1 л дистиллированной воды
Варианты исполнения печатных плат с глухими и скрытыми отверстиями
Рано или поздно любой инженер-разработчик многослойных печатных плат (МПП) сталкивается с необходимостью применения несквозных переходных отверстий. Это может быть связано с увеличением плотности монтажа, использованием BGA с маленьким шагом выводов, необходимостью иметь переходное отверстие в SMT-площадке, невозможностью организовать площадки для переходных отверстий на обратной стороне платы или с другими факторами. К сожалению, в промышленности нет единого стандарта на проектирование и выполнение таких отверстий. Как правило, все определяется технологическими возможностями конкретного производства МПП. Однако можно обобщить некоторые принципы, следование которым позволит инженеру спроектировать многослойную плату наиболее технологичным образом, так, чтобы ее можно было заказать практически на любом современном производстве.
Рассмотрим поперечное сечение печатной платы («микрошлиф», или microsection) на рис. 1. Мы можем увидеть шесть слоев меди, причем второй, третий, четвертый и пятый соединены переходным отверстием, не выходящим на наружные слои. Кроме того, первый слой соединен со вторым при помощи микроотверстия. Это наиболее типичный вариант использования несквозных отверстий. Далее мы рассмотрим, какие бывают виды несквозных отверстий, методы их формирования и основные параметры.
Терминология
В мире сложилась определенная терминология обозначения видов несквозных отверстий. К сожалению, в русском языке один и тот же вид имеет несколько обозначений, и иногда они применяются некорректно или неоднозначно. Мы будем пользоваться следующей терминологией:
Blind via — «глухие» или «слепые». Имеются в виду отверстия, соединяющие наружный слой с одним или несколькими внутренними.
Buried via — «скрытые», «погребенные», «встроенные». Это переходные отверстия, не выходящие наружу и соединяющие между собой сигналы на внутренних слоях.
Micro-via, или uVia — «микроотверстия». Подразумеваются отверстия малого диаметра и малой глубины, выполненные лазером или сверлением с контролем глубины и соединяющие внешний слой с внутренними.
HDI (High Density Interconnection) — «соединения высокой плотности». Общее название класса МПП высокой плотности с глухими и скрытыми отверстиями.
Выбор конструкции МПП
Наше глубокое убеждение, основанное на многолетнем опыте проектирования и приема заказов МПП с глухими и скрытыми отверстиями, состоит в следующем: Выбор конструкции должен производиться в самом начале проектирования МПП, и перед началом проектирования эта конструкция должна быть согласована с заводом-изготовителем!
Нередко разработчик печатной платы закладывает структуру отверстий HDI исходя из собственных представлений, никак не связанных с возможностями конкретного производства, или же добавляет их «на ходу», исходя из потребностей уже «почти страссированного» проекта, в котором немножко не хватило места. Последствия могут быть самыми печальными, как для разработчика (в дальнейшем приходится переразводить плату под другие требования), так и для компании в целом (неизбежные потери времени и денег, связанные с поиском подходящего производителя и увеличением срока и стоимости заказа). Случается, что спроектированная вот так, необдуманно, конструкция МПП с HDI нереализуема в принципе, ни на одном из существующих в мире производств, или же стоимость реализации на порядок превышает бюджет проекта.
Рассмотрим, какие основные факторы следует принимать во внимание при начальном формировании конструкции печатной платы.
Факторы, связанные с выбором конструкции МПП
1. Размещение слоев МПП (питающие, земляные, сигнальные, теплоотводящие) — требования инженера-схемотехника, рекомендации от производителей сложных BGA-корпусов.
2. Расположение в слоях, а также параметры сигналов с контролируемым импедансом (по требованию схемотехника) и расчет волнового сопротивления.
3. Виды и размещение глухих и скрытых переходных отверстий — технологические возможности поставщика, типовые конструкции.
4. Выбор материалов (диэлектрические и медные слои, теплоотводящие слои) — требования схемотехника и возможности поставщика ПП.
Таким образом, при формировании конструкции печатной платы задача инженераконструктора — оптимальным образом совместить требования от разработчика схемы с возможностями производителя плат.
Не будем подробно останавливаться на выборе материалов и толщины слоев — это тема отдельной статьи. Наша задача — понять, как выбрать конструкцию платы, пригодную для производства. Для этого рассмотрим основные методы формирования несквозных переходных отверстий.
Формирование скрытых отверстий
Методы формирования скрытых отверстий на внутреннем ядре (или на «частичном пакете») схожи по технологии с тем, как выполняются сквозные металлизированные отверстия. При проектировании МПП следует учитывать, что при металлизации таких отверстий на медной поверхности соответствующих слоев платы (например, слой 2 и 5 на рис. 1) происходит осаждение меди, дополнительно от 25 до 45 мкм. Поэтому при расчете, например, минимально допустимой ширины проводников в таких слоях их толщину надо брать с учетом металлизации.
Таким образом, для варианта, представленного на рис. 1, сначала прессуется пакет из слоев 2–5, например:
====== ядро FR4 0,36 мм, фольга с двух сторон 35 мкм;
~~~~~~ препрег, несколько слоев;
====== ядро FR4 0,36 мм, фольга с двух сторон 35 мкм.
В этом пакете, как в готовой плате, сверлятся и металлизируются сквозные отверстия. Затем они заполняются смолой, и пакет прессуется в составе печатной платы:
––––––– фольга 18 мкм + металлизация, итого 45–55 мкм;
~~~~~~ препрег, несколько слоев, общая толщина 0,2 мм;
====== ядро FR4 0,36 мм, фольга 35 мкм + металлизация;
~~~~~~ препрег, несколько слоев;
====== ядро FR4 0,36 мм, фольга 35 мкм + металлизация;
~~~~~~ препрег, несколько слоев, общая толщина 0,2 мм;
––––––– фольга 18 мкм + металлизация.
Так как происходит два этапа прессования и металлизации отверстий, стоимость изделия увеличивается примерно в полтора–два раза.
Пример из реальной практики
Неопытный разработчик прислал проект МПП 6 со скрытыми отверстиями между слоями: 2–3, 2–4, 2–5, 3–4, 3–5, 4–5. Разработчик обосновывает такой набор скрытых отверстий упрощением и ускорением автоматической трассировки платы, так как готовые платы ему нужно получить срочно.
Результат:
Такой проект очень сложен в реализации. Невозможно разбить комбинации слоев на частичные пакеты, так как номера слоев в них пересекаются. В итоге разработчик потерял несколько недель на поиск производителя и был вынужден переразводить плату вручную, изменив структуру на следующую: 2–3, 2–5, 4–5. Для реализации такой конструкции выполняются металлизированные отверстия в ядре 2–3 и ядре 4–5, затем прессуется пакет 2–5 и выполняется металлизация отверстий в нем. Дальнейший анализ показал, что плату можно было страссировать, обойдясь только скрытыми отверстиями 2–5 и микроотверстиями 1–2 и 5–6.
Методы формирования микроотверстий
Один из популярных видов несквозных отверстий — так называемые микроотверстия.
Они формируются на уже спрессованном пакете МПП путем лазерного сверления или механическим сверлением с контролем глубины. Затем эти отверстия металлизируются одновременно с металлизацией сквозных отверстий и проводников на поверхности платы.
На рис. 2 приведены фотографии микроотверстий, сформированных различными методами. Общее свойство микроотверстий — их глубина не должна превышать диаметр, в противном случае невозможно обеспечить качественную металлизацию стенок.
Материалы внешних слоев для микроотверстий
Как известно, наиболее популярная структура слоев МПП подразумевает выполнение наружных слоев из фольги со слоями препрега (смолистых прокладок). В том случае, если требуется выполнение микроотверстий, также используется эта структура, и микроотверстие выполняется в слое препрега. Кроме того, часто в качестве наружного слоя применяется специальный материал — RCC (resin coated copper, «фольга со смолистым слоем»). RCC — это материал, созданный специально для плат с микроотверстиями, его отличие от обычных материалов в том, что в нем отсутствуют нити стекловолокна. Это делает стенки микроотверстий более качественными.
Пример
Типичная ошибка инженеров-конструкторов — применение микроотверстий с глубиной, превышающей их диаметр.
Предположим, что мы проектируем МПП, количество слоев — 6, общая толщина — 1,6 мм, толщина диэлектрика между слоями 1–2 задана как 0,2 мм (исходя из соображений обеспечения импеданса 50 Ом для линий шириной 0,35 мм на слое Top относительно земляного слоя Int1).
Структура МПП может быть следующей:
––––––– фольга 18 мкм + металлизация, итого 45–55 мкм;
~~~~~~ препрег, несколько слоев, общая толщина 0,2 мм;
====== ядро FR4 0,36 мм, фольга с двух сторон 35 мкм;
~~~~~~ препрег, несколько слоев;
====== ядро FR4 0,36 мм, фольга с двух сторон 35 мкм;
~~~~~~ препрег, несколько слоев, общая толщина 0,2 мм;
––––––– фольга 18 мкм + металлизация.
Предположим, мы решили, что для удобства трассировки нам нужны микроотверстия с 1-го на 2-й слой (GND) и с 1-го на 3-й слой (сигнальный). Будет ошибкой делать эти микроотверстия с одинаковым диаметром, например, 0,2 мм с площадкой 0,5 мм. Однако такие некорректные проекты — не редкость в нашей практике. К сожалению, они нереализуемы и нуждаются в переделке.
В самом деле, мы видим, что первый вид микроотверстий должен быть выполнен на глубину 0,2 мм, а второй вид — на глубину 0,2 + 0,035 + 0,36, итого 0,6 мм. Таким образом, исходя из условия «1:1», диаметр для первого вида микроотверстий составит 0,2 мм, с площадкой 0,5–0,6 мм, а диаметр для второго вида — не менее чем 0,6 мм, с площадкой 1 мм. Такой довольно большой размер площадки может свести на нет все преимущества от применения микроотверстий.
Заметим, что (с нашей точки зрения) не очень технологично выполнять микроотверстия в ядре FR4. Можно использовать другую структуру, с последовательным наращиванием слоев препрега и фольги, например:
––––––– фольга 18 мкм + металлизация;
~~~~~~ препрег, несколько слоев, общая толщина 0,2 мм;
––––––– фольга 35 мкм;
~~~~~~ препрег, общая толщина 0,1 мм;
====== ядро FR4 0,8 мм, фольга с двух сторон 35 мкм;
~~~~~~ препрег, общая толщина 0,1 мм;
––––––– фольга 35 мкм;
~~~~~~ препрег, несколько слоев, общая толщина 0,2 мм;
––––––– фольга 18 мкм + металлизация.
В этом случае диаметр отверстия между слоями 1–3 может составлять всего 0.34 мм, с площадкой 0,65–0,75 мм, что существенно упростит трассировку МПП.
Разумеется, мы рассмотрели некий гипотетический пример, но он отражает общую схему рассуждений при выборе конструкции печатной платы.
Параметры микроотверстий
На рис. 3 и в таблице показаны минимально допустимые параметры лазерных микроотверстий. Мы рекомендуем при разработке конструкции МПП запросить подобную таблицу у поставщика печатных плат.
Типовые конструкции МПП 4
Давайте посмотрим, какие могут быть основные варианты конструкции ПП. На рис. 4 показан вариант с ядром внутри и микроотверстиями снаружи.
Тип материала и толщина ±30% |
Отверстие, мкм |
Внешняя площадка, мкм |
Внутренняя площадка, мкм |
1 x RCC 60 мкм | 100 | 300 | 330 |
1 x 106 p/p 50 мкм | 100 | 300 | 330 |
и минимум | 90 | 250 | 300 |
1 x 1080 p/p 65 мкм | 120 | 330 | 380 |
и минимум | 100 | 300 | 350 |
2 x 106 p/p 100 мкм | 150 | 360 | 400 |
Материал внешнего слоя, варианты:
1. Материал RCC толщиной 60 мкм, отверстие 90 мкм.
2. Препрег «106» толщиной 45 мкм, отверстие 90 мкм.
3. Препрег «1080» толщиной 65 мкм, отверстие 100 мкм.
4. Препрег 2 х «106», толщина 100 мкм, отверстие 150 мкм.
Тип материала
Может быть использован материал типа FR4, FR4 без галогена, FR4 High Tg (высокотемпературный), FR4 Low CTE (высоковольтный). Однако не может быть использован СВЧ-материал типа Ro4003 и др.
Мы рекомендуем закладывать в стоимость МПП с HDI-структурами высокотемпературный материал типа FR4 High Tg. Он менее подвержен деградации при термоударе, возникающем при нанесении покрытия HAL, а также при монтаже компонентов. Таким образом, применение High Tg материала повышает надежность и долговечность МПП с глухими и скрытыми отверстиями.
Скрытое отверстие
Обратите внимание, что в приведенной выше структуре во внутренних слоях выполнено «скрытое» отверстие со слоя 2 на слой 3. Технология исполнения таких отверстий, как мы видели ранее, схожа с технологий изготовления обычных сквозных металлизированных отверстий, с последующим заполнением смолой и прессованием в составе пакета МПП. Заметим, что выполнение микроотверстий непосредственно над «скрытым» отверстием невозможно, так как в этом месте во внутреннем слое находится не сплошная площадка, а медное кольцо с отверстием в центре.
На рис. 5 показана другая структура — в этом случае внешние слои выполнены из «ядер» FR4, склеенных слоями препрега.
Способ изготовления такой структуры: сначала выполняется сквозная сверловка и металлизация отверстий отдельно в каждом из ядер, затем формируется рисунок проводников на внутренних поверхностях ядер и производится прессование пакета МПП. С точки зрения производства такая последовательность операций является менее технологичной, так как требует выполнения дополнительных этапов металлизации отверстий. Однако при отсутствии оборудования для сверления микроотверстий это единственно возможный вариант.
Заметим, что в данной структуре, в отличие от предыдущей, в слоях с глухими отверстиями возможно применение СВЧ-материала.
На основании приведенных выше 4-слойных структур можно строить комбинации с большей слойностью, однако не следует злоупотреблять сложностью и многообразием видов глухих и скрытых отверстий. Опыт показывает, что при выборе между добавлением в проект еще одного вида несквозных отверстий и добавлением еще одной пары слоев правильнее будет добавить пару слоев. В частности, для микросхем BGA с шагом 1 мм и даже 0,8 мм нет необходимости в применении несквозных отверстий. Для BGA с шагом 0,65 мм и 0,5 мм без несквозных отверстий, пожалуй, не обойтись. В любом случае, конструкция МПП должна быть спроектирована с учетом того, как именно она будет реализована в производстве.
Пример из практики
Один из наших заказчиков прислал проект МПП 12 слоев со структурой глухих отверстий 1–2, 1–4, 1–6, 12–11, 12–9, 12–7. Предполагается, что она реализуется в три этапа прессования, путем металлизации частичных пакетов 1–2 и 12–11, затем 1–4 и 12–9, потом 1–6 и 12–7. После этого выполняется последнее прессование и металлизация сквозных отверстий. Однако заметим два слабых места такой конструкции:
А) На каждом этапе металлизации на проводниках на слое Top формируется дополнительный медный слой от 25 до 40 мкм. Таким образом, после четвертого цикла к толщине фольги добавится от 100 до 160 мкм меди, что делает невозможным обеспечение проводников и зазоров шириной менее чем 0,4 мм. Имеется специальный метод, позволяющий частично снять этот дополнительный слой меди, однако это не вполне технологичная операция, снижающая выход годных и повышающая стоимость плат.
Б) Кроме того, мы выполняем три итерации прессования. На каждой из них взаимное смещение слоев может достичь 0,05–0,075 мм, в результате чего после трех прессований мы получаем пакет, в котором все проводниковые слои могут быть смещены в произвольных направлениях на величину до 0,15–0,2 мм. Если мы просветим такую плату рентгеном в месте расположения площадок переходного отверстия, то увидим так называемую «ромашку» (рис. 6) — рассовмещенные площадки в слоях. Чтобы учесть такое смещение, надо предусматривать в проекте гарантийный поясок не менее 0,25 мм. Это означает, что для переходных отверстий 0,2мм применяются площадки не менее чем 0,7 мм.
Типовые конструкции многослойных плат HDI
На рис. 7 приведены примеры типовых конструкций МПП, в порядке увеличения сложности. Мы рекомендуем придерживаться этих структур, это позволит вам без особых проблем разместить заказ на изготовление МПП. Коэффициент увеличения стоимости показан на рисунке для различных структур условно, в среднем он составляет от 50% до 200% от стоимости заказа, в зависимости от его сложности и объема. Заметим, что применение глухих отверстий иногда может привести к удешевлению проекта в целом, за счет экономии на общем количестве слоев, лучшей трассируемости, уменьшения размера печатной платы, а также возможности применить компоненты с более мелким шагом. Однако в каждом конкретном случае решение об их применении следует принимать индивидуально и обоснованно.
Приведены только основные, наиболее технологичные и наименее дорогостоящие варианты выполнения несквозных отверстий и их комбинаций. Разумеется, есть множество более сложных технологий, позволяющих, например, разместить микроотверстие непосредственно над скрытым отверстием или сделать «стек» из нескольких микроотверстий, или заполнить микроотверстие медью для формирования ровной площадки. Но это, пожалуй, тема для отдельной большой публикации.
Рекомендации
Мы настоятельно советуем: не усложняйте конструкцию печатной платы и обеспечивайте полностью симметричную структуру слоев и отверстий. Если не обойтись без более сложной структуры отверстий, обязательно обратитесь к поставщику печатных плат перед началом проектирования. В частности, инженеры компании PCB technology могут проконсультировать вас по вопросам проектирования таких печатных плат и дать примеры реализации и оформления подобных проектов.
Металлизация отверстий печатной платы
В процессе изготовления печатной платы обычно необходимо пройти через отверстие, чтобы реализовать передачу схемы и герметизацию. Металлизация отверстий является одним из наиболее важных процессов в технологии производства печатных плат, чтобы реализовать металлизацию отверстий, обычно используют химическую медь (PTH), черную дыру (Black Hole) и метод проводящей полимерной пленки на подложке из проводящей смолы.
Химическая медь
Электрохимическое меднение — это принцип восстановления меди до меди в условиях восстановителя. Процесс можно разделить на три этапа: предварительная обработка, активация и осаждение меди.
Основной состав раствора для химического меднения включает соль меди, комплексообразователь, восстановитель, регулятор pH и добавку.Одним из наиболее распространенных восстановителей является формальдегид, два метиламиноборана, гипофосфит, гидразингидрат, соль с низким содержанием металлов, редуцирующий сахар. Среди них цена формальдегида низкая, а относительное содержание меди в покрытии выше, поэтому он является наиболее широко используемым и наиболее широко используемым. Однако формальдегид является летучим, нестабильным и имеет другие недостатки, в последние годы вопрос о том, как заменить формальдегид, также находится в центре внимания исследования. Комплексообразующий агент является одним из ключевых компонентов химического меднения, которое может увеличить поляризацию ионов меди для достижения кристаллического тонкого и яркого покрытия.Винная кислота обыкновенная, ЭДТА, триэтаноламин, три изопропиламин и др.
Черная дыра
Черная дыра представляет собой мелкие капли графита или порошка сажи, диспергированных в деионизированной воде, с использованием поверхностно-активных веществ или графитопроводящей суспензии сажи, остающейся стабильной и обладающей хорошими смачивающими свойствами, графит или технический углерод могут полностью абсорбироваться на поверхности стенки непроводящего отверстия. , образуя сочетание равномерного и тщательного проводящего слоя, сплошного.
Пленка полимерная проводящая
Непроводящая поверхностная химическая реакция в щелочном водном растворе перманганата калия, генерирующая слой диоксида марганца, затем в кислотном растворе, гетероциклические соединения или ряд пиррол-пиррольных мономеров на непроводящей поверхности и потеря полимеризации протонпроводящего полимера, нерастворимое образование тесно связано с файл. Затем печатная плата покрывается проводящим полимером для завершения металлизации.
Процесс в основном делится на три части: предварительная обработка; образование проводящего полимера; покрытие из сульфата меди.
[PDF] Прямая металлизация Процесс металлизации сквозных отверстий с низким уровнем микрочастиц
Скачать процесс металлизации сквозных отверстий методом прямой металлизации с низким …
Гальваническое медное заполнение сквозных отверстий на подложке различной толщины Кешенг Фенга, Билл Десариа, Майк Юб, Дон ДеСалвок, Джим Ватковски а МакДермид, 227 Freight Street, Waterbury, CT 06702 b Макдермид Тайваньский технический центр c Макдермид Статья в Техническом центре Сучжоу Аннотация Процесс заполнения сквозных отверстий медью для применения в конструкциях межсоединений высокой плотности и подложках ИС.Процесс состоит из двух циклов кислотного меднения. Первый цикл использует периодическое импульсное обратное гальваническое покрытие, чтобы сформировать мост в середине отверстия, с последующим гальваническим покрытием постоянным током, чтобы заполнить результирующие переходные отверстия, образованные во время цикла моста. Этот процесс может обеспечить бездефектные заполненные отверстия с общей плакированной медью на поверхности менее 25 мкм, с углублением менее 5 мкм для плат с толщиной сердцевины 0,2 мм и 0,25 мм. Этот процесс был разработан для использования в специально сконструированных вертикальных гальванических установках непрерывного действия (VCP), что позволяет сократить объем капитального оборудования по сравнению с горизонтальными конвейерными гальваническими установками.Химические компоненты, медь, кислота и добавка, для периодического импульсного цикла обратного гальванического покрытия оптимизированы с помощью экспериментальных условий, выбранных из программного обеспечения DOE (планирование экспериментов). Определяются критические параметры и количественно оценивается влияние на образование полости на этапе перекрытия. Концентрации добавки и меди играют ключевую роль в уменьшении дефектов во время образования мостиков и в результате образования. Высокоэффективный процесс заполнения сквозных отверстий используется для заполнения образовавшихся сквозных отверстий с глубиной углублений менее 5 микрон с нанесением на поверхность приблизительно 12 микрон.Тонкая поверхность меди обеспечивает четкое разрешение линий без необходимости выравнивания или шлифования. Механические свойства гальванического покрытия соответствуют или превосходят все стандарты IPC. Этот процесс применим как к просверленным лазером сквозным отверстиям X-образной формы, так и к механически просверленным прямым отверстиям. Просверленные лазером сквозные отверстия перекрываются быстрее, чем отверстия, просверленные механическим способом. Однако отверстия, просверленные механическим способом, имеют меньшую тенденцию к образованию дефектов, вызванных сверлением, особенно при меньшем диаметре отверстия 0.1мм. Этот процесс показал возможность заполнения сквозных отверстий в более толстых кернах от 0,4 мм до 0,8 мм, и дальнейшие исследования продолжаются. 1. Введение Заглушка смолой или пастой сквозных отверстий в сердечниках уже много лет является частью технологии наращивания, особенно в подложках ИС. Тем не менее, увеличение плотности схем и укладка сквозных конструкций в сочетании с устройствами большей мощности добавили дополнительный аспект управления температурным режимом. Заполнение этих сквозных отверстий сплошной медью дает множество преимуществ, таких как уменьшение несоответствия CTE, обеспечение стабильной платформы для укладки микропереходов и обеспечение свойств управления температурой для устройств высокой мощности.Начали развиваться новые технологии, позволяющие полностью заполнить сквозные отверстия и переходные отверстия в нарастающих слоях сердечника в HDI и IC сплошной медью. Один из подходов к заполнению сквозных отверстий медью — это технология покрытия постоянным током для тонкой основной платы с просверленными лазером X-отверстиями, как показано ниже (Рисунок 1). Сквозное отверстие перед процессом заливки медьюСквозное отверстие во время меднения, стадия «перемычки»
Сквозное отверстие, заполненное медью, через стадию заполнения
РИСУНОК 1. ЭТАПЫ ЗАПОЛНЕНИЯ МЕДИ С ПОМОЩЬЮ ТЕХНОЛОГИИ ПОСТОЯННОГО ТОКА
Покрытая медью поверхность может быть контролируется менее 25 мкм, с толщиной сердцевины около 100 мкм и диаметром около 100 мкм (50-70 мкм в середине).Процесс розлива состоит из двух этапов. На начальном этапе медь предпочтительно осаждается в середине сквозных отверстий до тех пор, пока стенка отверстия в центре отверстия не встретится, что приведет к образованию двух глухих микропереходов. Этот этап называется «мостик». Второй этап состоит из заполнения, в результате чего происходит двойное слепое переходное отверстие. Единый химический состав и одноэтапный процесс нанесения покрытия идеально подходят для заполнения сквозных отверстий сплошной медью. Однако покрытие постоянного тока ограничено толщиной подложки.Когда толщина подложки превышает 200 мкм, склонность к появлению включений / полостей возрастает (рис. 2), а толщина плакированной поверхности меди увеличивается за пределы 25 мкм. Более частое появление полостей может снизить надежность, в то время как увеличенная толщина поверхностной меди снижает способность разрешать тонкие линии и требования к пространству. Эти ограничения усугубляются для досок с механически просверленными сквозными отверстиями.
РИСУНОК 2. ДЕФЕКТЫ ПОЛОСТИ В ПРОЦЕССЕ ОСНОВАНИЯ ПОСТОЯННОГО ТОКА, КОГДА ТОЛЩИНА ПЛАТЫ ПРЕВЫШАЕТ 200 мкм.2. Двухэтапная технология заполнения сквозных отверстий Двухступенчатая концепция используется в двухступенчатом гальваническом покрытии, первый этап состоит из «перемычки» с периодическим импульсным обратным гальваническим покрытием, а затем заполнения образовавшегося двойного глухого сквозного отверстия с помощью процесса гальванизации сквозного заполнения. Комбинированные процессы предлагают бездефектную технологию заполнения сплошной медью для плат со сквозными отверстиями, просверленными как лазерным, так и механическим способом. Сквозные отверстия обрабатывались с помощью стандартных процессов первичной металлизации, в том числе перманганатной очистки или плазменной очистки, химического меднения или процесса прямой металлизации, такого как Blackhole, чтобы отверстия стали проводящими.Чтобы получить проводящий медный слой внутри сквозного отверстия, можно использовать импульсное покрытие, чтобы убедиться, что сквозные отверстия имеют хорошую проводимость по всей стене. Химический состав перед пластиной и технологические циклы не были изменены с учетом процесса кислотного меднения. 2.1 Постепенное перекрытие путем нанесения покрытия с периодическим обратным импульсом, формирование переходного отверстия Периодическое нанесение покрытия с обратным направлением импульсов — широко используемый процесс электролитического меднения. За последнее десятилетие эта технология получила широкое распространение при конформном покрытии сквозных отверстий с высоким соотношением сторон.Продолжает развиваться практика периодического импульсного обратного гальванического покрытия. Новые выпрямители и программное обеспечение теперь предлагают большую гибкость для форм волны, включая формирование асинхронных пульсовых волн для увеличения скорости металлизации в центре сквозных отверстий, то есть до 5 раз быстрее по сравнению с обычными пульсовыми волнами. Гальваническая медь слилась в середине отверстия, образуя два противоположных переходных отверстия, как показано на рисунке 3. Этот процесс называется этапом «перемычки». Стандартизированная вертикальная гальваническая ячейка была разработана для достижения этого нового типа гальванической способности внутри сквозных отверстий.Вертикальная гальваническая ячейка, установленная с нерастворимыми анодами из IrO-сетки, обеспечивает самый широкий рабочий диапазон гальваники по плотности тока для перекрытия сквозных отверстий. Дополнительные соображения для вертикальной гальванической ячейки включают экранирование анода, расстояние между анодом и катодом, соотношение площадей, перемешивание панели, движение раствора, скорость потока и систему зажима панели. После этапа перемычки два противоположных переходных отверстия заполняются эффективным раствором кислотного медного покрытия путем заливки, чтобы завершить процесс заливки медью, как показано на рисунке 4
РИСУНОК 3.РАЗРЕЗ ПОСЛЕ СТУПЕНИ МОСТА.
РИСУНОК 4. ПОПЕРЕЧНЫЙ РАЗРЕЗ ПОСЛЕ ЭТАПА МОСТИКА И ЧЕРЕЗ ЭТАП ЗАПОЛНЕНИЯ
2.2 Химический состав на этапе перемычки Химический состав для процесса периодического импульсного обратного кислотного меднения, используемого на этапе моста, является производственным химическим материалом. Этот процесс содержит специально разработанную систему органических добавок для импульсных покрытий. Компоненты электролита, сульфат меди, серная кислота и хлорид-ион, типичны для стандартных растворов для кислотного меднения.Для изучения взаимодействия между химическими компонентами концентрации сульфата меди, серной кислоты и добавки оптимизируются с экспериментальными условиями, выбранными из программного обеспечения DOE (дизайн экспериментов) для достижения хороших характеристик перекрытия / заполнения отверстий и отсутствия полостей в середине сквозные отверстия. В качестве ограничения Министерства энергетики США, объединенные концентрации сульфата меди и серной кислоты поддерживались ниже 350 г / л, чтобы предотвратить образование кристаллов сульфата меди в растворе для нанесения покрытия. Платы со сквозными отверстиями, используемые для DOE, представляли собой просверленные лазером платы с толщиной сердцевины 200 мкм и диаметром отверстий 100 мкм.После этапа перемычки были проверены 10 сквозных отверстий для каждого тестируемого состояния по поперечному сечению, чтобы определить, присутствовали ли какие-либо полости в медных заполненных сквозных отверстиях, как показано на Рисунке 3 выше. 2.3. ТАБЛИЦА оптимизации химического состава 1. ПОЛУЧАЮТ РЕЗУЛЬТАТЫ КОНЦЕНТРАЦИИ ДОБАВОК, ВЛИЯЮЩЕЙ НА ПОЛОСТЬ ВО ВРЕМЯ ЭТАПА МОСТОВОГО МОНТАЖА Кодирование программного фактора Design-Expert®: фактическая мостиковая полость
Однофакторное предупреждение! Фактор, участвующий во множественных взаимодействиях.
30
Диапазоны CI X1 = C: Фактические коэффициенты аддитивного A: Сульфат меди = 240.00 B: Серная кислота = 109,46
Мостиковая полость
20
10
0
-10
0,50
1,80
3,10
4,40
2. ПРИНИМАЮТСЯ ЛИ РЕЗУЛЬТАТЫ НА ПОЛОСТИ, ВЛИЯЮЩИЕ НА ВЛИЯНИЕ КОНЦЕНТРАЦИЙ СУЛЬФАТА МЕДИ И СЕРНОЙ КИСЛОТЫ ПРИ ДОБАВКЕ 0,5 МЛ / Л иметь более низкую добавку и более высокую концентрацию сульфата меди, как показано на диаграммах 1 и 2.Одной из лучших комбинаций каждого компонента является сульфат меди 240 г / л, серная кислота 110 г / л и добавка 0,5 мл / л. 2.4 Шаг заполнения переходных отверстий путем нанесения покрытия постоянным током Технология заполнения микропереходных отверстий электролитической медью широко используется при производстве HDI и упаковочных материалов. Новый производственный процесс меднения используется для заполнения глухих переходных отверстий после этапа перемычки. Это обеспечивает покрытие из тонкой меди на поверхности панели с минимальной глубиной углублений, как показано на Рисунке 5 ниже.
РИСУНОК 5.ПРОЦЕСС ПОКРЫТИЯ МЕДИ С ПОМОЩЬЮ ЗАПОЛНЕНИЯ (ЕДИНИЦА В µM)
Комбинированные процессы нанесения покрытия на этапах соединения и заполнения обеспечивают технологию заполнения медью более толстых плат со сквозными отверстиями разного диаметра. 3. Платы с заполнением из сплошной меди с различной толщиной сердцевины. Эта технология заполнения отверстий сплошной медью может применяться к платам с различной толщиной сердцевины и геометрией отверстий. 3.1 Платы с толщиной сердцевины 200 мкм, содержащие просверленные лазером сквозные отверстия с диаметром 100 мкм на поверхности и диаметром 50-70 мкм в середине отверстия. Просверленные лазером сквозные отверстия требуют меньшего времени на покрытие перемычки, чем механически просверленные прямые отверстия.Полное перекрытие просверленных лазером сквозных X-отверстий достигается примерно за 30 минут при толщине сердцевины 200 мкм. Когда просверленные лазером отверстия показали несоответствие диаметра середины отверстий, как показано на рисунке 3, все еще можно получить заполненные сквозные отверстия медью без полостей. Время нанесения покрытия для заполнения переходного отверстия составляло около 50 минут. Общая толщина медного покрытия на поверхности составляла приблизительно 20 мкм, как показано на Рисунке 3. 3.2 Платы с толщиной сердцевины 200 и 250 мкм, содержащие механически просверленные отверстия диаметром 100 мкм Время нанесения покрытия на механически просверленное сквозное отверстие составляет приблизительно 60 минут для перемычки. шаг, и приблизительно 50 минут для шага заполнения.Гальваническая поверхность меди составляет около 25 мкм, как показано на Рисунке 6.
РИСУНОК 6. МЕХАНИЧЕСКОЕ ПРОСВЕРЛЕНИЕ ПРОХОДНОГО ОТВЕРСТИЯ, ТОЛЩИНА СЕРДЦА 200 мкм 3.3 Платы с толщиной сердечника 400 мкм, содержащие механически просверленные отверстия диаметром 100 мкм Более длительное время нанесения покрытия требуется для более толстых панелей с толщиной сердцевины 400 мкм, механически просверленных отверстий диаметром 100 мкм. Время нанесения покрытия на этапе перекрытия составляло приблизительно 120 минут, в то время как время заполнения переходного отверстия оставалось равным 50 минутам. Общая толщина плакированной поверхности меди составляет около 35 мкм.
РИСУНОК 7. M ЭХАНИЧЕСКОЕ ПРОСВЕРЛЕНИЕ СКВОЗНОГО ОТВЕРСТИЯ, ТОЛЩИНА СЕРДЕЧНИКА 400 мкм, ДИАМЕТР 100 мкм 3.4 Плата с толщиной сердцевины 800 мкм, механически просверленные сквозные отверстия
Становится сложной задачей перекрытие панелей с толщиной сердцевины 800 мкм. В отверстиях диаметром менее 250 мкм наблюдались полости.
РИСУНОК 8. M ЭХАНИЧЕСКИ ПРОСЛУШЕНО СКВОЗНОЕ ОТВЕРСТИЕ, ТОЛЩИНА СЕРДЕЧНИКА 800 мкм, ДИАМЕТР 250 И 300 мкм, ПОСЛЕ ШАГА СОЕДИНЕНИЯ, 240 МИНУТ. Для сквозных отверстий большего диаметра требуется больше времени для заполнения образовавшихся переходных отверстий, что приводит к более толстому покрытию меди на поверхности панели.4. Рентгеновский контроль. Большая часть оценки была сделана под микроскопом с поперечными сечениями. Рентгеновский контроль использовался для проверки плат с толщиной сердцевины 200 мкм, как с механическим просверливанием сквозного отверстия, так и с лазерным просверливанием сквозного отверстия. Рентгеновский контроль после двухэтапного процесса нанесения гальванического покрытия показал, что заполненная медь в сквозных отверстиях не имела дефектов, как показано на рис. 9.
ЗАПОЛНЕННАЯ ЛАЗЕРОМ МЕДЬ ПРОСЛУШИЛАСЬ ЧЕРЕЗ ОТВЕРСТИЕ МЕДЬ ЗАПОЛНЕНА МЕХАНИЧЕСКИ ПРОСРЕЛИ ЧЕРЕЗ ОТВЕРСТИЕ РИС. 9. РЕНТГЕНОВСКИЙ ИЗОБРАЖЕНИЕ НА ПЛАТЕ С ТОЛЩИНОЙ СЕРДЕЧНИКА 200 мкм
5.Физические свойства. Физические свойства покрытия имеют решающее значение для обеспечения приемлемого качества готовой плиты. Предел прочности на разрыв и относительное удлинение в процентах измеряли с помощью производственного прибора для испытания на растяжение с медным покрытием в перемычке и ванне для заполнения переходных отверстий. Результаты приведены в Таблице 1. ТАБЛИЦА 1. РЕЗУЛЬТАТЫ ОТНОСИТЕЛЬНО УДЛИНЕНИЯ И ПРОЧНОСТИ НА РАЗРЫВ Цикл покрытия Медное покрытие с перемычкой плюс через процесс заполнения
Образец №
1 2 3 4 5 Среднее значение
Толщина усилия на разрыв медного покрытия (мил) ( фунт-сила)
2.82 3,23 2,71 2,87 3,05 3,94
62,75 72,83 60,21 62,89 68,12 65,36
Масса (г) Относительное удлинение (%)
0,9726 1,1146 0,9348 0,9901 1,0510 1,0126
21,92 21,19 20,79 Прочность 19,4000 PSI
21,92 21,19 47699,5 47018,9 46368,8 47314,6 47100,0
Плата с толщиной сердцевины 250 мкм и диаметром отверстий от 100 до 300 мкм была замкнута и заполнена медью. Эти панели были подвергнуты оценке термического напряжения в соответствии с IPC TM-650 2.6.8 Припой 6X плавает в течение 10 секунд при 288 ºC. Целостность отложений была превосходной, так как ни трещины, ни отслоения не наблюдались ни в одном из испытанных сквозных отверстий, как показано на Рисунке 10.
РИСУНОК 10 ПОПЕРЕЧНЫЙ РАЗРЕЗ ПОСЛЕ 6-кратного УДАРА ПАЙКОЙ 6. Выводы Технология заполнения сквозных отверстий медью для продемонстрировано применение к конструкциям межсоединений высокой плотности и подложкам ИС. Процесс состоит из двух циклов кислотного меднения. Первый цикл — это периодическое импульсное обратное гальваническое покрытие, чтобы сформировать перемычку в середине отверстия, за которым следует гальваническое покрытие постоянным током, чтобы заполнить результирующие двойные переходные отверстия, образованные во время перемычки.Этот процесс может обеспечить бездефектное заполнение сквозного отверстия сплошной медью. Механические свойства гальванического покрытия соответствуют или превосходят все стандарты IPC.
Гальваническое заполнение сквозных отверстий медью при различной толщине субстрата Jim Watkowski Electronics Solutions, MacDermid
ОБЗОР 1 2 3 4 5
ВВЕДЕНИЕ ТЕХНОЛОГИЯ ДВУХЭТАПНЫХ ТЕХНОЛОГИЙ ЗАПОЛНЕНИЯ ПРОХОДНЫХ ОТВЕРСТИЙ (THF) • Химическая оптимизация заполнения сквозных отверстий • Формирование перемычек в сквозных отверстиях химия
ПРИМЕНЕНИЕ К РАЗЛИЧНЫМ ПЛАТАМ ФИЗИЧЕСКИЕ СВОЙСТВА МЕДИ ЗАКЛЮЧЕНИЕ
Введение Тенденция в отрасли, повышенная плотность схемы / миниатюризация • Заполненные переходные отверстия позволяют штабелировать • Частично заполненные переходные отверстия • Сквозные отверстия, заполненные медью, как более надежный процесс
Сквозные отверстияВставить
Сквозное отверстие, заполненное медью Источник фото: Prismark / Binghamton University
Процесс заполнения медью — Повышенная надежность — Улучшенное управление температурным режимом — Меньшее количество этапов процесса — Повышенная производительность при сокращении затрат
Двухэтапный процесс • Перекрыть отверстия — закрыть отверстие в центре , образуя два переходных отверстия по одному по обе стороны от Электронная плата
Мост
1.0 мм
0,35 мм
0,15 мм
Толщина 0,4 мм
• Заполните два переходных отверстия гальванической медью (технология Via Fill) Заполните
Почему двухэтапный процесс? • • • •
Обеспечивает заполнение отверстий более широкого диапазона диаметров Хорошо заполняет просверленные механически отверстия Позволяет использовать более толстые подложки (0,2-0,6 мм), а проявление более толстых PPR уменьшает поверхность меди
DC только
(0,2 мм толщина)
Мост PPR + VF (DC)
Технология заполнения сквозных отверстий посредством меднения постоянного тока Ограничено толщиной платы для получения бездефектного покрытия,> 200 мкм
Технология двухступенчатого заполнения сквозных отверстий 1.Покрытие с периодическим обратным импульсом (PPR) 2. Покрытие сквозного заполнения Сквозное отверстие перед процессом заполнения медью
Этап перемычки PPR, медное покрытие в середине сквозного отверстия
Через этап заполнения сформированные переходные отверстия были заполнены до завершения процесса заполнения сквозного отверстия
Bridging Step
Acid Cleaner Rinse Etch (если промелькнул) Acid Dip PPR
• Вертикальный процесс с использованием нерастворимых анодов • Специальные выпрямители, создающие уникальные формы волны • Конструкция оборудования с высокой степенью воздействия раствора • Возможность адаптации к VCP
Фазовый сдвиг
град.сдвиг
180 град. сдвиг
Станд. 0 град. shift
Оптимизация мостов в программном обеспечении Design-Expert® Факторное кодирование: фактическая полость моста
Однофакторное предупреждение! Фактор, участвующий во множественных взаимодействиях.
30
Диапазоны CI
DOE на • Сульфат меди • Серная кислота • Добавка
X1 = C: Фактические факторы добавки A: Сульфат меди = 240,00 B: Серная кислота = 109,46
Полость перекрытия
20 9 мм Отверстие
10
0
-10
0.50
1,80
3,10
4,40
C: Добавка
5,70
7,00
Оптимизация моста Кодирование программного фактора Design-Expert®: Фактические точки проектирования межмолекулярной полости 10
000000000 9000
Фактический коэффициент C: Добавка = 0,50
Одно из лучших условий • Сульфат меди 240 г / л • Серная кислота 110 г / л • Добавка 0,5 мл / л
B: Серная кислота
X1 = A : Сульфат меди X2 = B: Серная кислота
150.00
0
6
4
2
8
125.00
100.00 100.00
135.00
170.00
A: Медный сульфат
205.00
для однородности заполнения снизу вверх, тонкой поверхности меди и устранения пустот
Кислотноочистительная пластина
Rinse Etch 9 мкм
Активатор AVF Обозначения, необходимые для сухих панелей
100 мкм 100 мкм
Варианты толщины платы и геометрии отверстий Лазерная просверленная форма X сквозное отверстие, толщина 200 мкм, диаметр 100 мкм.• Перемычка PPR 30 мин., Через заливку 50 мин. • Толщина меди менее 20 мкм. • Ямка менее 5 мкм
Различия в толщине платы и геометрии отверстий Механическое просверливание сквозного отверстия, толщиной 200 и 250 мкм, диаметром 100 мкм. • Перемычка PPR 60 мин, через заливку 50 мин. • Толщина меди менее 25 мкм. • Ямка менее 5 мкм
0,15 мм (отверстия) толщиной 2 мм Шаблонная пластина Ямка = 0 мкм Поверхностная медь = 21 мкм Время цикла = 75 минут
Результаты перемычки и заполнения 0,25 мм t
0.35 мм
0,25 мм
0,30 мм
0,20 мм
0,15 мм
0,10 мм
0,20 мм
0,15 мм
0,10 мм
0,40 мм t
0,35 мм
мм
0,80 мм t
0,4 мм
0,35 мм
0,3 мм
0,25 мм
0,20 мм
Рентгеновский контроль сквозных отверстий, заполненных медью, как лазерных, так и механических. 100 мкм.
Свойства наполненной меди • •
Покрытие медью с перемычкой плюс через процесс заполнения Измерено производственным испытательным устройством на растяжение
Цикл покрытия Медное покрытие с перемычкой плюс через процесс наполнения
Образец № 1
Медь с покрытием Толщина разрыва (мил) (фунт-сила) 2,82 62,75
Вес (г) 0,9726
Предел прочности на растяжение (%) (PSI) 21,92 47098,0
2 3
3,23 2,71
72,83 60,21
1,1146 0.9348
21,19 20,79
47699,5 47018,9
4 5
2,87 3,05
62,89 68,12
0,9901 1,0510
19,46 22,47
463681004000
19,46 22,47
463681004000
19,46 22,47
463681004000 9124000
9142000
4636810040009 Среднее значение
Свойства наполненной меди • •
Толщина сердцевины при 250 мкм, диаметр варьировался от 100 до 300 мкм. 6 раз всплытие припоя в течение 10 с при 288 ° C. В меди, заполненной сквозными отверстиями, не наблюдалось ни трещин, ни расслоения.
Заключение • Технология заполнения сквозных отверстий медью может быть применена к конструкциям межсоединений высокой плотности и подложкам ИС.• Комбинация PPR-перемычек и высокоэффективного заполнения отверстий обеспечивает бездефектную заполненную медь в различных платах с различной геометрией сквозных отверстий. • Механические свойства металлического покрытия соответствуют или превосходят все стандарты IPC.
Спасибо Вопросы? Электронная почта: [адрес электронной почты защищен]
Металлизация палладия, через заливное покрытие
Джордж Милад
Uyemura International Corporation
Southington CT
печатных плат вчерашнего дня даже близко не соответствуют технологиям и требованиям сегодняшних печатных плат и корпусов, а постоянный переход к новым технологиям означает, что платы завтрашнего дня поставят перед собой еще более захватывающие задачи.Поскольку электронная промышленность продолжает свое постоянное развитие в сторону более быстрых, компактных и дешевых, а также постоянно возникающих проблем с соблюдением нормативных требований, поставщики технологической химии и оборудования должны постоянно стремиться соответствовать этим конструкциям печатных плат и корпусов следующего поколения.
Движущей силой этой эволюции является потребность в более быстрых машинах с большим упором на форм-фактор и все более сложную конструкцию. Соответствие RoHS и экологическая осведомленность WEEE также сказываются на сложности конструкции.Возьмем, к примеру, множество возможностей форм-фактора и решений гибких и жестко-гибких плат — это всего лишь одна область нашей отрасли — и вы можете начать видеть обширную матрицу возможностей для всех видов печатных плат и корпусов.
Проблемы, связанные с выполнением этих требований, открывают множество возможностей для следующего поколения химикатов гальваники и обработки поверхности или даже для новых применений старых надежных компонентов. В эпицентре этого жонглирования оказываются поставщики химикатов, которые имеют в своем распоряжении любую комбинацию гальванического покрытия и химического состава переходного наполнения для удовлетворения этих требований.
Например, кислотное меднение сталкивается с новыми проблемами, связанными с нанесением плат с более высоким соотношением сторон и неровным рисунком дорожек, не говоря уже о проблемах заполнения переходных отверстий для HDI. Обработка поверхности требует лучшего понимания и новых продуктов для удовлетворения новых условий высокотемпературной сборки бессвинцовой электроники и обеспечения надежности этих паяных соединений.
Что с металлизацией? Крайне важно, чтобы системы металлизации / удаления смазки переходили к жестким условиям высокотемпературной обработки бессвинцовых продуктов и должны сосуществовать с высокотемпературными ламинатами и бессвинцовыми припоями.Каковы идеальные системы металлизации для гибких полиимидных и жестко-гибких плит? Адекватны ли существующие системы? Есть необходимость в чем-то новом?
В этой статье представлен анализ доступных химических процессов, которые соответствуют требованиям самых сложных на сегодняшний день печатных плат и корпусов. Потому что когда вы входите в этот дивный новый мир, вы должны понимать доступные химические процессы и решения, а также то, как они будут соответствовать потребностям вашего конечного потребителя.
Покрытие
Чтобы соответствовать новым требованиям рынка, производители печатных плат вынуждены искать новые и передовые процессы на каждом этапе производственного процесса.Металлизация сквозного отверстия и кислотное меднение подвергаются тщательному изучению, так как они представляют собой процессы, формирующие следы и соединения сквозных отверстий, передающие сигнал от конца к концу конечного устройства.
Металлизация палладия
Внедряется новая система металлизации, основанная на адсорбции палладия, вызванная недостатками существующих процессов, таких как химическая медь или углеродная металлизация. Металлизация палладия не нова, но новое поколение отличается, поскольку оно устраняет все недостатки предыдущих поколений, а также альтернативные процессы.
Новая система разработана для удовлетворения потребностей гибких и жестко-гибких плит, при укладке которых всегда используются клеевые слои. Эти слои подвержены воздействию высокой щелочности, используемой при химическом осаждении меди.
Это новое поколение обеспечивает значительно сокращенное время процесса, сводя к минимуму воздействие щелочности. Он также имеет уникальную систему кондиционирования, благодаря которой палладий прилипает только к полиимидному диэлектрику, а не к меди. Процессы углеродной металлизации требуют удаления углерода с поверхности меди перед нанесением покрытия, но эта новая система не требует травления поверхности меди перед нанесением электролитического покрытия.Микротравление поверхности меди привело к образованию клиновидных пустот, что снизило надежность межсоединений внутреннего слоя в многослойных платах.
Кислая медь
Задача кислотного гальванического покрытия меди состоит в том, чтобы добиться хорошего распределения толщины и однородности поверхности без ухудшения металлургических свойств (прочности на разрыв и относительного удлинения) покрытия. Эти свойства становятся особенно важными, поскольку медь с гальваническим покрытием подвергается более высокой термической нагрузке во время сборки бессвинцового припоя.
Производители обычно сталкиваются с проблемами распределения кислой меди по толщине в двух основных областях: на поверхности и в металлическом сквозном отверстии. На поверхности кислотная медь может вызвать чрезмерное покрытие изолированных дорожек (участков с высокой плотностью тока) по сравнению с более крупными участками заземления (низкая плотность тока). В отверстии задача состоит в том, чтобы выполнить требования к минимальной толщине меди в центре отверстия с высоким соотношением сторон, также известные как метательная сила.
Однородность поверхности иногда мешает появлению конкреций, которые происходят из самых разных источников. При склеивании золотой проволокой нет толерантности к любому уровню нодуляции.
Новые разработки помогают решить эти задачи:
- Новые пакеты химических добавок для улучшенного распределения
- Улучшения массопереноса для дополнительных присадок
- Устранение конкреций с помощью нерастворимого анода
- «Через заполнение», специальное приложение
Покрытие постоянного тока большой дальности
В последние годы на рынке появилось новое поколение кислотно-медных систем с высокой производительностью.Эти ванны рассчитаны на современные токи гальваники, которые ниже, чем традиционные 25–30 ASF, которые были распространены во времена двухсторонних и более простых изделий.
Ванны с большим радиусом действия разработаны для обеспечения желаемых физических свойств при плотностях тока от 5 до 20 ASF со стандартным выпрямлением постоянного тока. Они образуют яркие пластичные отложения.
Эти типы ванн характеризуются особой комбинацией пакетов органических добавок, включающих уникальный выравнивающий агент.Выравниватель играет ключевую роль в улучшении заброса, особенно в сочетании с эдукторным (безвоздушным) перемешиванием.
Рисунок 1:
На рис. 1 показан ПТГ с соотношением сторон 10: 1, нанесенный при 10 ASF в течение 120 минут с использованием системы кислотного меднения постоянного тока.
Некоторые из этих ванн могут дать метательную силу> 80% для отверстия с соотношением сторон 10: 1, гальванизация при 15 ASF в течение 90 минут с использованием выпрямления постоянного тока в баке с вертикальным погружением.
Покрытие заполнения переходного отверстия
Чтобы удовлетворить требования HDI, сквозное покрытие быстро становится очевидным выбором для соединения различных слоев в технологии наращивания (многослойные переходные отверстия и переходные отверстия в контактной площадке). Это обеспечивает общее повышение долговременной надежности как печатных плат, так и корпусов микросхем.
Импульсное и постоянное гальваническое покрытие через химические системы заполнения, многие из которых с новыми электролитами, предлагают ряд преимуществ, поскольку они не требуют выпрямления импульсов и позволяют избежать сложности управления импульсной волной.Кроме того, системы гальваники постоянного тока стабильны и не требуют постоянной регенерации электролитов, используемых при импульсном выпрямлении.
Заполнение переходных отверстий основано на высокой концентрации осаждающих ионов в сочетании с низкой концентрацией выравнивающего агента, а также добавок носителя и осветлителя. Для большинства этих систем требуется оптимизированный поток раствора, позволяющий выравнивателю накапливаться на поверхности, что препятствует нанесению металлизации, в то время как нижняя часть переходного отверстия продолжает покрывать пластину. Динамика покрытия в нижней части отверстия сильно отличается от динамики покрытия на поверхности платы, так как отверстие заполняется, а динамика покрытия выравнивается.
Новое поколение кислотно-медных переходных отверстий для заполнения переходных отверстий разработано для работы в режиме постоянного тока при 10–30 ASF, заполняя переходные отверстия менее чем за час с использованием стандартной гальванической ячейки с выпрямлением постоянного тока. Эти системы также способны покрывать отверстия во время процесса металлизации переходных отверстий и нашли применение при заполнении каналов и переходных отверстий в корпусах. На рисунке 2 показано последовательное наращивание многослойных переходных отверстий.
Рисунок 2:
Кислотное меднение прошло долгий путь с момента появления двусторонних и односторонних печатных плат, и само собой разумеется, что проблемы с нанесением покрытия будут продолжать расти по мере появления на рынке требований к новым продуктам (более легким, компактным и надежным). По мере того, как покоряется одна передовая веха, устанавливается новая.
Финиш — это только начало
Эволюция отделки поверхности опережает все химические процессы, потому что сложность конструкции и экологические ограничения электроники, не содержащей свинца и галогенов, вынуждают промышленность внимательнее присматриваться к тому, как существующие покрытия соответствуют этим требованиям, а также к постоянному созданию новых систем.
Поверхностная обработка — это все, что связано с возможностью соединения, будь то паяное соединение, соединение проводов или даже соприкасающаяся поверхность.Обработка поверхности делится на две категории в зависимости от типа паяного соединения IMC: Ni / Sn IMC и Cu / Sn IMC. Иммерсионное золото без химического никеля (ENIG) и иммерсионное золото с палладием (ENEPIG), не содержащее химического никеля, образуют Ni / Sn IMC, в то время как OSP, иммерсионное серебро, иммерсионное олово и золото для прямого погружения (DIG) образуют Cu / Sn IMC. На рисунке 3 показаны компоненты IMC для обеих этих категорий.
Рисунок 3:
Ni / Sn IMC требует более высокой температуры сборки, чем Cu / Sn IMC, а также имеет обогащенный фосфором слой на границе раздела.Это естественный компонент любого ИМК NI / Sn, образующегося на никелево-фосфорном осадке.
ENIG
ENIG образуется путем осаждения никель-фосфора химическим способом на катализированную поверхность меди с последующим нанесением тонкого слоя иммерсионного золота. Спецификация IPC ENIG, IPC-4552, определяет 120–240 микродюймов (мкдюймов) никеля и 2–4 микродюйма (мкдюймов) иммерсионного золота.
ENIG — универсальная отделка поверхности. Это паяемая поверхность, соединяемая алюминиевым проводом и превосходная поверхность электрического контакта.Его срок годности превышает 12 месяцев, его легко проверить (визуально), а его толщину легко проверить с помощью неразрушающего измерения XRF. ENIG продолжает увеличивать долю рынка, особенно после понимания и фактического устранения проблемы «Black Pad». «Черная накладка» возникает, когда скомпрометированная поверхность никеля подвергается коррозии в результате длительного воздействия на этапе осаждения золота иммерсией.
В настоящее время доступен новый химический состав золота, разработанный в Японии для устранения чрезмерной коррозии никеля во время осаждения золота.Механизм осаждения является как иммерсионным, так и автокаталитическим — автокаталитическое осаждение не вызывает коррозии.
ENEPIG
ENEPIG формируется путем осаждения никеля без химического воздействия (120–240 мкдюймов) с последующим нанесением 4–8 мкдюймов палладия без химического воздействия с иммерсионной вспышкой золота (1–2 мкдюймов). ENEPIG — это отделка с широчайшими возможностями для применения в самых разных областях. Иногда ее называют «универсальной» отделкой, она была представлена в середине 90-х годов, а ENEPIG стала известна как «универсальная отделка» из-за универсальности использования.
- пайка
- золотая проволока для склеивания
- алюминиевая проволока с возможностью соединения
- связаться с
Несмотря на то, что ENEPIG был представлен в середине 90-х, он не стал популярным, как ожидалось, особенно в области пайки эвтектическим припоем, который использовался в то время. Несовместимость свинца с палладием препятствовала образованию однородной ИМС Ni / Sn.
Перенесемся в 2006 год, и ENEPIG снова подверглась тщательной проверке, поскольку промышленность оценивает ее возможности в условиях бессвинцовой сборки.ENEPIG показал себя с честью, поскольку образовал одно из самых прочных паяных соединений с бессвинцовыми сплавами типа SAC. Испытание на увеличенный срок службы паяного соединения (см. Рисунок 4) Было проведено моделирование с использованием обжига при 150 ° C в течение до 1000 часов, и испытания на сдвиг шариком не показали потери прочности паяного соединения. Исследования SEM и элементный анализ показывают, что присутствие палладия в стыке стыка резко снижает распространение интерметаллидов (IMC), что делает ENEPIG лучшим выбором для отделки корпусов, требующих пайки и соединения проводов с бессвинцовыми сплавами типа SAC.
Рисунок 4:
DIG
Золото с прямым погружением (DIG) на медь — это относительно новая отделка поверхности, которая имеет многообещающие перспективы для бессвинцовых применений. Эта отделка состоит из покрытия 2 микродюймов (0,05 микрон) золота непосредственно на медной поверхности в качестве консерванта паяемости. Механизм представляет собой комбинацию погружения, а также химического (автокаталитического) осаждения, что приводит к очень плотной решетке, которая значительно ограничивает диффузию меди на поверхность.
График (любезно предоставлен Photocircuits) на Рисунке 5 показывает кривые баланса смачивания в течение 877 дней после нанесения. Образцы хранили в лабораторных условиях.
Рисунок 5:
Одно из ключевых применений этой отделки — печатные платы, предназначенные для распространения радиочастотных сигналов. Из-за «скин-эффекта» целостность сигнала может быть нарушена, если толстый слой никеля нанесен ниже поверхности золота, как в случае ENIG.
DIG образует соединение Cu / Sn IMC как с эвтектическими припоями, так и с бессвинцовыми припоями из сплава SAC. DIG подает большие надежды, поскольку устраняет недостатки, присущие другим поверхностям. Он выдерживает множественные тепловые колебания, сформированное паяное соединение не имеет межфазных пустот, не образует никаких IMC во время хранения перед сборкой и не образует усов.
DIG также допускает нанесение покрытия из мягкого золота без химического восстановления, и толщиной всего 15 микродюймов (0.6 микрон) поверхность идеально подходит для склеивания золотой проволокой. DIG в основном используется в Японии и в основном для упаковки, но он получает признание на рынке по мере того, как дизайнеры и производители все больше знакомятся с его возможностями.
Иммерсионное серебро
Хотя эта отделка хорошо зарекомендовала себя в отрасли, кривая обучения обращению, упаковке и хранению была самой большой проблемой при выводе на рынок иммерсионного серебра.Дополнительные исследования продолжаются, чтобы установить его жизнеспособность при использовании бессвинцовых припоев и пайки. По мере того, как эта обработка поверхности укрепляется на рынке, ее преимущества и недостатки становятся более понятными. В последнее время сообщалось о некоторых случаях чрезмерного межфазного мочеиспускания, но это явление было хорошо изучено и были установлены его первопричины. Незначительные модификации процесса были внесены, чтобы гарантировать, что производитель может избежать любых условий, которые могут вызвать дефект.
Иммерсионное олово
Иммерсионное олово также является хорошо зарекомендовавшей себя отделкой поверхности, которая претерпела изменения в течение многих поколений. Благодаря своим смазывающим свойствам и однородности толщины иммерсионное олово является идеальным выбором для совместимых со штифтом и запрессовкой соединителей. Каким бы привлекательным ни выглядело иммерсионное олово для обработки поверхности, не содержащее свинца, более высокие температурные требования, присущие бессвинцовой сборке, создали новые проблемы, требующие изменения технических характеристик толщины иммерсионного олова.
Иммерсионное олово не нашло широкого распространения в отрасли, два основных ограничения иммерсионного олова — это образование IMC между оловом и лежащей под ним медью и склонность к росту нитевидных кристаллов, когда олово наносится на медь. Исследования продолжаются по обоим направлениям, чтобы определить наилучшие условия эксплуатации. Также были обнаружены добавки, которые практически исключают образование усов.
В быстро развивающемся технологическом мире, в котором мы живем, решение сегодняшних отраслевых задач и требований завтрашнего дня открывает двери к возможностям, в которых инновационные компании имеют возможность вносить свой вклад и расти за счет инвестиций в исследования и разработки, чтобы предоставлять решения для постоянно меняющихся требований рынка. для меньших, более дешевых, легких и быстрых пакетов.
Правила, связанные с RoHS и WEEE, требуют новых технологий, которые выводят отрасль в неизведанные области, требующие новых продуктов для решения неожиданных проблем, связанных с требованиями к более высоким температурам.
Это захватывающие времена для нашей отрасли с множеством сложных задач и возможностей. По мере того, как достигается одна передовая веха, устанавливается новая.PCB (Печатная плата) Процесс металлизации отверстий и меднения
Металлизация и покрытие
Процесс металлизации отверстий и меднения на печатной плате
Меднение печатной платы (PCB) включает гальваническое покрытие меди, гальваническое покрытие олова, гальваническое покрытие никелем и золотом и т. Д.Среди них гальваника меди занимает важное место в производстве печатных плат.
1 Погрузите печатную плату в кислотную жидкость
Целью погружения печатной платы в кислотную жидкость является удаление оксидов с поверхности пластины, активация платы, обычно концентрация составляет 5%, а некоторые — 10%, в основном для предотвращения попадания воды в контейнер с жидкостью, что приводит к нестабильности серной кислоты.
2 Подпиточная жидкость для гальваники
Кислотная электронная жидкость состоит из CuSO 4 , H 2 SO 4 , HCl и органических добавок.CuSO 4 жидкость является основным ингредиентом, который является основным источником Cu +, концентрация CuSO 4 важна во время производства. Обычно CuSO 4 5H 2 O составляет 60 г / л-100 г / л. Количество H 2 SO 4 составляет около 180 г / л-220 г / л. Содержание Cl — в жидкости ниже, примерно 30-80 мг / л. Органические добавки — это транспортный агент, осветлитель, выравнивающий агент и другие.
3 гальванический
3.1 Полный пансион гальванический медь
Он также известен как только медь, его основная функция — защита тонкой химически чистой меди, которая только что откладывается.Процесс заключается в использовании всей платы в качестве катода путем увеличения толщины меди до определенной степени после металлизации отверстий; затем формируют линию цепи путем травления, которая может предотвратить отходы из-за тонкого слоя меди, нанесенного химическим способом, который травится в следующем процессе.
3.2 Вторичная гальваническая медь
Она также известна как вторичная медь или медь для контуров. Для соответствия номинальной токовой нагрузке толщина каждой линии цепи и металлизации отверстий должна соответствовать требованиям.Графическая гальваника предназначена для увеличения толщины.
4 Кислотное обезжиривание
Обезжиривание используется для удаления оксидов, чернил, клея или пленки с поверхности медной платы для обеспечения силы связывания между медью и графической медью или никелем. Жидкость бывает двух видов: кислая и щелочная, лучше щелочное средство, но почему бы его не использовать? Поскольку графические изображения и чернила не являются щелочью, щелочное средство повредит эту линию, обратите внимание на использование кислотного обезжиривающего средства во время работы.Концентрация жидкости около 10%, время менее 6 мин. Замена составляет около 15 м2 / л, добавление предметов — 0,5–0,8 л / 100 м2.
5 Офорт
Травление в основном используется для очистки поверхности медной платы, чтобы обеспечить сцепление между графической медной платой и медью. Обычно травильная жидкость — это Na 2 S 2 O 8 , концентрация около 60 г / л, время около 20 секунд, добавление элементов составляет 3–4 кг каждые 100 м2; содержание меди менее 20 г / л.
Традиционная металлизация отверстий печатной платы дополняется слоем химического меднения; все более и более популярным становится процесс прямого нанесения гальванического покрытия, он не только упрощает процесс, прост в эксплуатации, но и защищает окружающую среду; Он заменит процесс химического восстановления меди и станет неизбежным трендом.Китай FPC металлизация отверстий и процесс очистки поверхности медной фольги производители и поставщики
Металлизация отверстий — двухсторонний производственный процесс FPC
Металлизация отверстий гибких печатных плат в основном такая же, как у жестких печатных плат.
В последние годы появился процесс прямого гальванического покрытия, который заменяет покрытие без химического восстановления и использует технологию формирования углеродного проводящего слоя. Металлизация отверстий гибкой печатной платы также вводит эту технологию.
Гибкие печатные платы из-за своей мягкости требуют специальных креплений. Крепления могут не только фиксировать гибкие печатные платы, но также должны быть устойчивы в растворе для покрытия, иначе толщина медного покрытия будет неравномерной, что также приведет к отсоединению во время процесса травления. И важная причина для перемычки. Чтобы получить равномерный слой медного покрытия, гибкую печатную плату необходимо закрепить в зажимном приспособлении и поработать над положением и формой электрода.
При аутсорсинге обработки металлизации отверстий необходимо избегать передачи на аутсорсинг фабрик, не имеющих опыта работы с отверстиями на гибких печатных платах. При отсутствии специальной линии нанесения покрытия на гибкие печатные платы качество отверстий не может быть гарантировано.
Очистка поверхности медной фольги производственный процесс
Чтобы улучшить адгезию резистной маски, поверхность медной фольги должна быть очищена перед нанесением покрытия на резистную маску.Даже такой простой процесс требует особого внимания к гибким печатным платам.
Как правило, для очистки есть процесс химической очистки и процесс механической полировки. При изготовлении точной графики в большинстве случаев используются два типа очистки поверхности. При механической полировке используется метод полировки. Если полировальный материал слишком твердый, он повредит медную фольгу, а если он слишком мягкий, он будет недостаточно отполирован.Обычно используются нейлоновые щетки, длина и твердость которых должны быть тщательно изучены. Используйте два полировальных ролика, размещенных на конвейерной ленте, направление вращения противоположно направлению транспортировки ленты, но в это время, если давление полировальных роликов слишком велико, подложка будет растягиваться под большим натяжением, что вызовет размерные изменения. Одна из важных причин.
Если обработка поверхности медной фольги не является чистой, адгезия к резистной маске будет плохой, что снизит скорость прохождения процесса травления.В последнее время из-за улучшения качества плат из медной фольги процесс очистки поверхности также может быть исключен в случае односторонних схем. Однако очистка поверхности — незаменимый процесс для точных рисунков размером менее 100 мкм.
Кратко описана технология металлизации отверстий печатной платы — Знание
1. Кратко опишите технологию химического осаждения меди
Химическое осаждение меди относится к процессу, в котором ионы меди восстанавливаются до меди из раствора с помощью восстановителей с образованием металлических покрытий.Химическое меднение — это своего рода каталитическая РЕДОКС-реакция собственного типа, она не зависит от того, вызывает ли металлический объект покрытие, полное использование восстановителя вызывает химическую реакцию в катализаторе под действием осаждения металла из раствора, а затем использовать Новые экологически активные атомы металла в качестве каталитического ядра продолжают каталитическую реакцию восстановления металла, другой до достижения желаемой толщины осаждения металлического слоя.
Чтобы получить хорошее осаждение меди, мы должны понимать технологические характеристики химического меднения, чтобы эффективно управлять им.Химическое меднение не ограничено природой основного материала, применимо к металлической, неметаллической поверхности: не ограничено формой поверхности, которую можно покрыть, можно ли получить канавку, полость, глубокие отверстия, глухие отверстия и т. Д. части, контактирующие с раствором равномерного покрытия, не нуждаются в протекании тока, оборудование простое и имеет широкий спектр применений. Технология металлизации отверстий в процессе печатной платы использует эти характеристики процесса химического меднения для нанесите проводящий слой меди на поверхность подложки и стенку отверстия.
2. Ключевые моменты процесса химического осаждения меди
Комбинация между слоем химического меднения и неметаллической матрицей стенки отверстия является физической и подвержена тепловому удару или изменению температуры. Процесс должен строго контролироваться, чтобы улучшить силу связывания, чтобы получить надежный проводящий слой меди. Следовательно, следующий технологический процесс должен выполняться строго для обеспечения силы связывания между слоем стока и матрицей.
(1) Предварительная обработка покрытия
Для стола из неметаллических материалов и нанесения покрытия методом химического восстановления покрытие включает два аспекта: первый — очистка поверхности, роль — удаление масла с поверхности стенки отверстия подложки и других органических или неорганических загрязнений, так что гальванический раствор и непроводящая поверхность надежно контактируют; Другой — обработка модификации поверхности, ее функция для улучшения смачивающей способности раствора химического гальванического покрытия к материалу матрицы, покрытие и непроводящая поверхность прочно, компактно комбинация.Правильный состав и строгая эксплуатация и техническое обслуживание — это две основные контрольные точки для контроля качества предварительной обработки.
(2) Строгий контроль условий процесса
Особенности, основанные на их каталитическом окислительно-восстановительном процессе химического нанесения покрытия, должны строго контролировать условия рабочего процесса, химический баланс, ключевым моментом является сохранение стабильности раствора для нанесения покрытия, если раствор Стабильность, неблагоприятна для опускания меди качество трудно гарантировать непрерывное производство: если слишком стабильный раствор для нанесения покрытия, скорость осаждения слишком низкая, появляются даже покрытия, покрывающие неполное «пустое»: раствор для нанесения покрытия слишком близко к точке рефлекса, химическая реакция после нанесения покрытия методом погружения слишком сильная, осадочная структура рыхлая, покрытие неудовлетворительное, не может удовлетворить требованиям металлизации отверстий печатной платы, серьезное самопроизвольное разложение приведет к ненужному расходу и нанесению покрытия.Таким образом, строгий контроль технологических условий является одним из основных факторов обеспечения качества слоя химического меднения.
(3) Хорошая мойка из меди
Устройство и метод химического меднения имеют важное влияние на качество меднения. Прежде всего, ванна, подвесные инструменты и нагреватели раствора для химического нанесения покрытия, система охлаждения, система циркуляционной фильтрации и т. д., все части, контактирующие с гальваническим раствором, должны быть изготовлены из инертных неметаллических материалов, чтобы избежать инициирования химических реакций в этих частях, приводящих к бесполезному расходу гальванического раствора и самопроизвольному разложению.Оборудование должно иметь хорошую систему контроля температуры, современное оборудование и автоматические добавки и систему контроля pH, чтобы поддерживать химическую реакцию в наилучшем состоянии.
(4) Строгое техническое обслуживание и управление процессом
При использовании раствора для химического нанесения покрытия необходимо поддерживать чистоту и стабильность ванны, вовремя корректировать и дополнять химический состав, а также предотвращать проникновение посторонних примесей и влияние продуктов автокаталитического восстановления.После каждого использования температура раствора должна быть снижена до комнатной температуры или ниже температуры химической реакции во времени, значение pH должно быть снижено, чтобы замедлить или остановить химическую реакцию, и должна быть проведена фильтрующая обработка.
(5) Строгая постобработка
Последующая обработка процесса химического осаждения меди относится к обработке покрытия после осаждения меди. Обычно используется химическая опускная медь — процесс «опускания тонкой меди», осаждение из покрытия очень тонкий, но также очень легко окисляется, поэтому медное покрытие раковины следует проводить сразу после обработки утолщением покрытия или обработки антиокислительной пропиткой, чтобы избежать окисления покрытия и микроэрозии.
(6) Строго предотвращать загрязнение примесями
Строго запрещается вносить примеси в гальванический раствор и раствор для обработки в процессе химического меднения, чтобы предотвратить блокирование отверстия посторонними предметами, которые напрямую повлияют на эффект химического меднения. Предотвратить попадание обрабатывающего раствора из предыдущего процесса в гальванический раствор или другой обрабатывающий раствор следующего процесса во время обработки подложки; после каждого этапа обработки подложка должна быть очищена, а очищающая вода следует избегать в лечебный раствор.
(7) Своевременно регулировать раствор для химического покрытия и различные растворы для обработки
Строго контролировать состав раствора для нанесения покрытия и различных растворов для обработки, своевременный анализ, регулировку, добавление и обработку, чтобы гарантировать, что состав различных растворов находится в нормальном диапазоне , который должен улучшить качество покрытия и предотвратить «черную дыру» (отсутствие медной дыры) в фундаменте.
Металлизация отверстий жестко-гибкой платы — Диссертация
Используя процесс химического осаждения меди или гальванического покрытия на двухсторонних печатных платах или многослойных жестко-гибких печатных платах, можно нанести некоторый металл на диэлектрическую поверхность материалов PI или EP.Слой металла может осуществить соединение двухсторонней цепи. Металлизация отверстий в жестко-гибких печатных платах, включая сверление, удаление смазки, химическое нанесение покрытия, гальваническое покрытие, является ключевым процессом в производстве жестко-гибких печатных плат. Сквозное отверстие в пластине (PTH) требует превосходных механических и электрических характеристик, отличной однородности и целостности медного слоя, отсутствия поднятой площадки, отсутствия отрыва металлической стенки от отверстия, отсутствия пустот из смолы и пузырьков воздуха. Из-за требований к электронным продуктам (меньше, легче, тоньше) и высокой плотности сборки, разработка и производство печатных плат получили быстрый прогресс, а требования к металлизации отверстий на печатных платах также стали более строгими.Поскольку диаметр отверстия становится все меньше и меньше, процесс металлизации отверстия становится все труднее. Теперь это стало узким местом производства печатных плат (особенно жестко-гибких печатных плат). В статье представлены разработка и перспективы жестко-гибких FPC, принцип процесса металлизации отверстий, влияние различных технологических факторов на качество продукции. Эта бумага. Основные процессы очистки и нанесения покрытия на медь химическим способом, которые являются ключевыми, изучены и представлены в деталях.Потому что материал жестко-гибких печатных плат отличается от жесткой печатной платы (RPCB) и гибкой печатной платы (FPCB). Основными материалами RPCB являются эпоксидная смола, стеклоткань, PTFE (политетрафторэтилен) и т. Д. Основными материалами FPCB являются полиимидная смола, кристаллический клей и т. Д. Из-за низкой температуры Tg этих диэлектрических материалов и высокой температуры, выделяемой высокой -скоростной бурильщик, на поверхности отверстия может образоваться некоторый мазок, который может вызвать поражение металлического сквозного отверстия.В RPCB мазок, вызванный этими материалами, можно устранить с помощью перманганата калия. В то время как жестко-гибкие печатные платы в основном основаны на таких материалах, как PI (полиимид), эпоксидная смола, полиакрилаты, этот процесс может привести к отрыву слоев, поэтому От мазка, нанесенного этим материалом, нельзя избавиться перманганатом калия.