Что такое пайка твердыми припоями. Какие бывают виды твердых припоев. Как выполняется технология пайки твердыми припоями. Где применяется пайка твердыми припоями в промышленности и быту. Какие преимущества и недостатки у этого метода соединения металлов.
Что такое пайка твердыми припоями
Пайка твердыми припоями — это метод неразъемного соединения металлических деталей с помощью расплавленного металлического припоя, имеющего температуру плавления выше 450°C. Данный способ позволяет получать прочные соединения, способные работать при высоких температурах.
Основные особенности пайки твердыми припоями:
- Температура плавления припоев — от 450°C до 1100°C
- Высокая прочность паяного соединения
- Хорошая термостойкость шва
- Возможность пайки разнородных металлов
- Необходимость нагрева деталей до высоких температур
Виды твердых припоев
Твердые припои можно разделить на несколько основных групп:
1. Медно-цинковые припои
Состоят из меди (40-60%) и цинка (40-60%). Температура плавления 820-980°C. Применяются для пайки стали, чугуна, меди и ее сплавов.
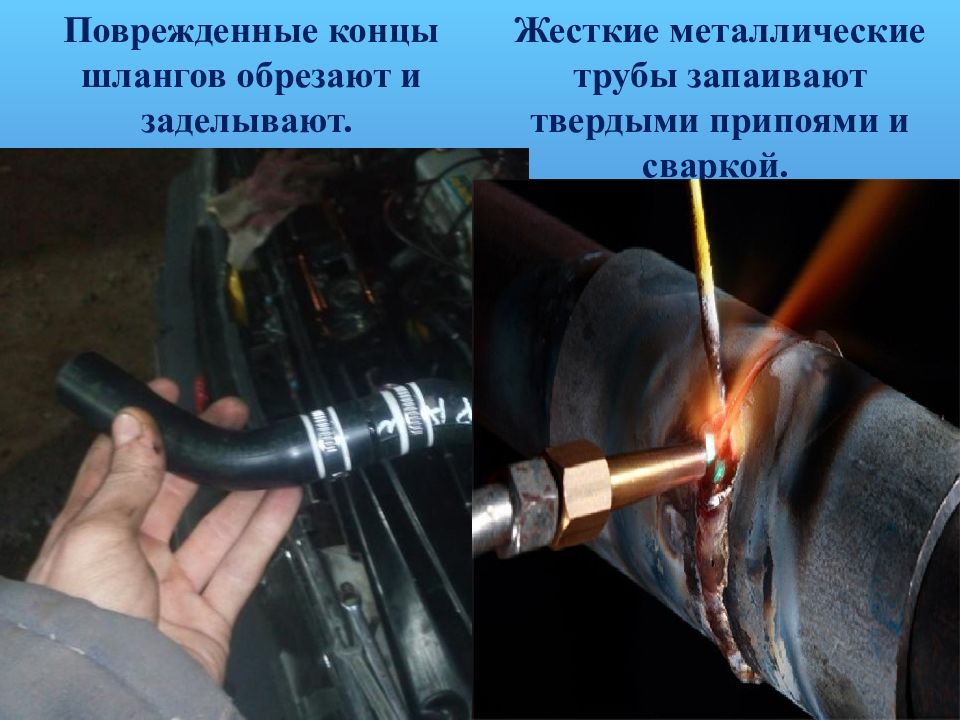
2. Медно-фосфорные припои
Содержат 80-95% меди и 5-8% фосфора. Температура плавления 710-820°C. Используются для пайки меди и ее сплавов без применения флюса.
3. Серебряные припои
Содержат 15-90% серебра, а также медь, цинк, кадмий. Температура плавления 620-780°C. Применяются для пайки черных и цветных металлов, твердых сплавов.
Технология пайки твердыми припоями
Процесс высокотемпературной пайки включает следующие основные этапы:
- Подготовка поверхностей под пайку (очистка, обезжиривание)
- Нанесение флюса на место пайки
- Фиксация деталей в требуемом положении
- Нагрев места пайки до температуры плавления припоя
- Введение припоя в зазор между деталями
- Выдержка при температуре пайки для заполнения зазора припоем
- Охлаждение паяного соединения
Способы нагрева при пайке твердыми припоями
Для нагрева деталей при высокотемпературной пайке используются следующие способы:
- Газопламенный нагрев горелками
- Индукционный нагрев токами высокой частоты
- Нагрев в печах (муфельных, вакуумных)
- Нагрев погружением в расплавленные соли
- Электроконтактный нагрев
Выбор способа нагрева зависит от материала, размеров деталей и серийности производства.
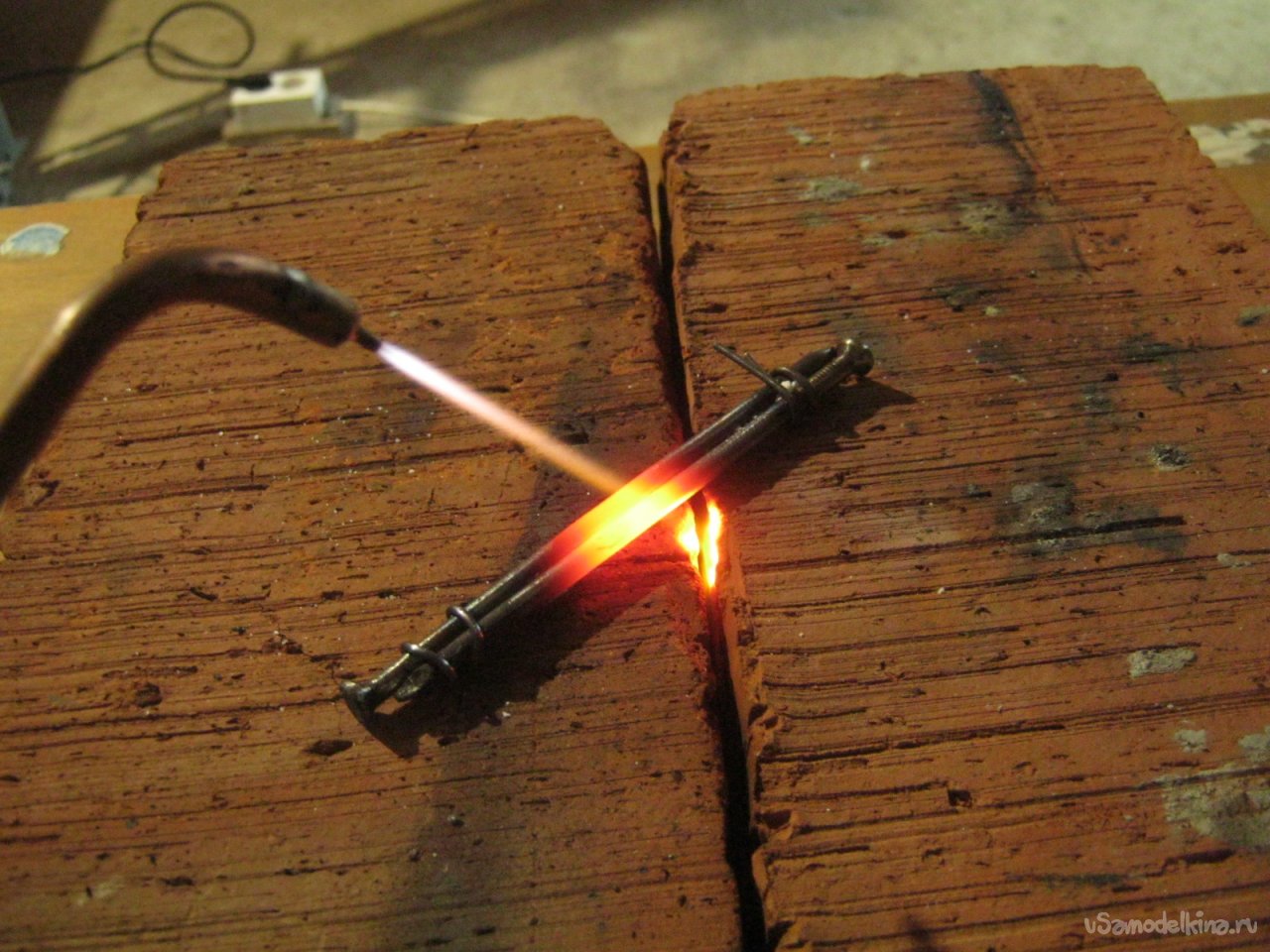
Преимущества пайки твердыми припоями
Данный метод соединения имеет ряд важных достоинств:
- Высокая прочность соединения, близкая к прочности основного металла
- Возможность пайки разнородных металлов
- Хорошая герметичность шва
- Способность паяных соединений работать при высоких температурах
- Отсутствие значительных деформаций деталей
- Возможность автоматизации процесса
Недостатки пайки твердыми припоями
К основным недостаткам метода можно отнести:
- Необходимость нагрева деталей до высоких температур
- Возможность структурных изменений в металле при нагреве
- Сложность пайки массивных деталей
- Необходимость тщательной подготовки поверхностей
- Токсичность паров некоторых флюсов
Применение пайки твердыми припоями
Высокотемпературная пайка широко используется в различных отраслях промышленности:
- Машиностроение (пайка твердосплавных пластин к державкам инструмента)
- Приборостроение (герметизация корпусов приборов)
- Авиастроение (пайка деталей из жаропрочных сплавов)
- Электротехника (пайка контактов, обмоток электродвигателей)
- Производство теплообменной аппаратуры
- Ювелирная промышленность
В быту пайка твердыми припоями применяется при ремонте радиаторов, трубопроводов, кухонной утвари из меди и латуни.

Флюсы для пайки твердыми припоями
При высокотемпературной пайке используются специальные флюсы, выполняющие следующие функции:
- Защита поверхности металла от окисления при нагреве
- Растворение оксидных пленок
- Улучшение смачивания поверхности металла припоем
Основные типы флюсов для твердой пайки:
- Борная кислота и бура
- Хлориды и фториды щелочных металлов
- Борфтористоводородная кислота и ее соли
- Канифоль (для низкотемпературных припоев)
Формы паяных соединений
При пайке твердыми припоями используют следующие основные типы соединений:
- Нахлесточное — детали соединяются внахлестку
- Стыковое — детали соединяются торцами
- Телескопическое — одна деталь входит в отверстие другой
- Тавровое — одна деталь припаивается перпендикулярно другой
Выбор типа соединения зависит от конструкции изделия и действующих нагрузок.
Пайка твердыми припоями — Пайка
Пайка твердыми припоями
Категория:
Пайка
Пайка твердыми припоями
Пайку твердыми припоями применяют для получения прочных и термостойких швов.
Пайку твердыми припоями осуществляют, соблюдая следующие основные правила:
— как и при пайке мягкими припоями, повеохности подгоняют друг к другу припили-ванием, тщательно очищают от грязи, окислов и жиров механическим или химическим способом;
— подогнанные детали в месте спая покрывают флюсом, на место спая накладывают кусочки- припоя (медные пластинки) и закрепляют мягкой вязальной проволокой;
— подготовленные детали (заготовки) нагревают паяльной лампой, в кузнечном горне или электропечи;
— когда припой расплавится, деталь снимают с огня и держаг в таком положении, чтобы припой не мог стекать со шва;
— затем деталь медленно охлаждают. Охлаждать детали с напаянной пластинкой в воде нельзя, так как это ослабит прочность соединения.
Применяют другой способ пайки: подготовленную деталь (изделие) нагревают и обсыпают бурой, затем нагревают и к месту соединения подводят конец медной или латунной проволоки, которая, расплавляясь, заливает место спая. По мере охлаждения спаянные детали промывают в воде, протирают сухими тряпками и просушивают; шов зачищают наждачной бумагой или опиливают напильником.
Дефекты при пайке, их причины и меры предотвращения следующие:
припой не смачивает поверхность паяемого металла вследствие недостаточной активности флюса, наличия окисной пленки, жира и других загрязнений. Для предотвращения несмачивания в состав флюса добавляют фтористые соли или увеличивают его количество, улучшают обработку деталей, удаляя следы коррозии, жира; наплывы или натеки припоя вследствие недостаточного прогрева детали, припой не расплавился.
Рис. 1. Лужение деталей: а — погружением в ванну с оловом, б — нагрев деталей для облуживания, в — обслуживание растиранием олова
Безопасность труда при выполнении паяльных работ и лужении. Рабочие места, предназначенные для выполнения работ по пайке мелких деталей, должны оборудоваться местными вытяжными устройствами, обеспечивающими скорость движения воздуха непосредственно на месте пайки не менее 0,6 м/с.
В помещениях, где выполнялись паяльные работы, должно производиться мытье полов, сухая уборка пола не разрешается. Хранение одежды в помещениях, где производится пайка, запрещается.
В непосредственной близости от рабочих мест, предназначенных для выполнения работ по пайке мелких деталей мягкими припоями, должны устанавливаться: умывальник, бачок с 1%-ным раствором уксусной кислоты для предварительного обмывания рук и легкообмы-ваемые переносные емкости для сбора бумажных или хлопчатобумажных салфеток и ветоши. Около умывальника постоянно должны быть мыло, щетки, салфетки для вытирания рук. Применение полотенец общего пользования не разрешается.
Подготовка металлов и процесс пайки связаны с выделением пыли, вредных паров цветных металлов и солей, которые, попадая в организм человека через дыхательные органы, пищевод или кожу, вызывают раздражение слизистой оболочки глаз, поражение кожи и отравление.
Поэтому при пайке, и лужении необходимо соблюдать следующие правила;
рабочее место паяльщика должно быть оборудовано местной вентиляцией;
не допускается работа в загазованных помещениях;
после окончания работы и перед принятием пищи тщательно мыть руки мылом;
химикаты засыпать осторожно малыми порциями, не допуская брызг.
Попадание кислоты в глаза может вызвать слепоту, испарения кислот очень вредны;
серную кислоту хранить в стеклянных бутылях с притертыми пробками в плетеных корзинах с мягкой прокладкой;
пользоваться только разведенной кислотой. При разведении кислоту следует вливать в воду тонкой струей, непрерывно помешивая раствор. Запрещается лить воду в кислоту, так как при соединении воды с кислотой происходит сильная химическая реакция с выделением большого количества теплоты. Даже при небольшом количестве воды, попадающей в кислоту, вода быстро нагревается и превращается в пар, что может привести к взрыву;
— при нагреве паяльника соблюдать общие правила безопасного обращения с источником нагрева;
— при работе с паяльными лампами: проверить исправность лампы, горючее наливать в лампу не более 75% емкости; недопустимо доливать или наливать горючее в не-остывшую лампу; керосиновую лампу заправлять только керосином; работать электрическим паяльником, ручка которого должна быть сухой и не проводящей тока.
Рис. 2. Пайка твердыми припоями: а — подгонка поверхностей деталей, б — смазывание поверхностей деталей флюсом, в — вставка медной пластины, г — фиксирование соединяемых деталей направляющей прокладкой, д — нагрев деталей
—-
Имеется несколько способов пайки твердыми припоями. Эти способы могут быть классифицированы по способу нагрева металла в процессе пайки. Обычно твердые припои разделяются на медные, медно-цинковые, медно-никелевые и серебряные. Отдельную группу составляют алюминиевые припои. Наиболее важные твердые припои стандартизованы.
Припой ПМЦЗб из-за низкой прочности и хрупкости в машиностроении не применяется. Припои ПМЦ48 и ПМЦ54 ввиду недостаточной пластичности и низкой вибростойкости паянных ими соединений применяются мало. Наибольшее распространение получили припои JI62 и JIOK 62-06-04, дающие прочные паяные соединения. Предел прочности припоя JI62 составляет 30 кГ/мм2 при относительном удлинении 35 %.
Основой большинства флюсов для твердой пайки является бура Na2B407, кристаллизующаяся с десятью частями воды в крупные прозрачные бесцветные кристаллы Na2B407 • ЮН20. Кристаллическая бура начинает плавиться при 75 °С; по мере
усиления нагрева она постепенно теряет воду, сильно вспучиваясь и разбрызгиваясь, и переходит в безводную соль — плавленую или жженую буру, плавящуюся при температуре 783 °С. Бура в расплавленном состоянии может быть нагрета до высоких температур без заметного испарения; она весьма жидкотекуча и энергично растворяет окислы многих металлов, в особенности окислы меди.
Для пайки нержавеющей стали применяется смесь из равных частей буры и борной кислоты, замешанных на насыщенном водном растворе хлористого цинка до пастообразного состояния. При пайке серого ковкого чугуна для выжигания графита и увеличения чистой металлической поверхности, смачиваемой припоем, во флюсы часто вводят сильные окислители (хлорат калия, перекись марганца, окись железа и т. д.).
Флюсы могут иметь форму порошка или пасты. Применяются также флюсы и в виде жидких растворов, например раствор буры в горячей воде. Иногда целесообразно применять прутки припоя, покрытые флюсом. Флюсующее действие могут оказывать составные части самого припоя. Например, фосфор, окисляясь в фосфорный ангидрид, является хорошим флюсом для меди и медных сплавов, восстанавливая окислы и переводя их в легкоплавкие фосфорнокислые соединения. Поэтому фосфористые медные ири-пои не требуют флюсов для пайки медных сплавов, что очень удобно на практике.
Рис. 1. Классификация способов пайки твердыми припоями
Порошкообразные флюсы можно посыпать тонким слоем на кромки, причем часто применяется предварительный подогрев кромок, с тем чтобы частицы флюса плавились, прилипая к металлу, и не сдувались пламенем горелки при пайке. В порошкообразный флюс можно также обмакивать конец прутка припоя, нагретый выше температуры плавления флюса, который прочно пристает к прутку. Пасты и жидкие растворы наносят кистью или в них обмакивают припой. Можно изготовлять пасту из флюса с порошкообразным припоем и наносить ее на кромку перед пайкой.
Для пайки имеют важное значение подготовительные работы, часто определяющие качество соединения. Широко применяются три основные формы паяных соединений: нахлесточное, стыковое и соединение «в ус» (рис. 239). Наиболее распространенным является нахлесточное соединение, удобное для выполнения и весьма прочное. Увеличивая перекрытие нахлесточного соединения, можно повышать его прочность и в большинстве случаев достигнуть равнопрочности с основным металлом. Стыковое соединение имеет лучший внешний вид и при хороших припоях и правильном выполнении часто может обеспечить достаточную прочность (предел прочности может доходить до 40— 45 кГ/мм2). Стыковое соединение применяется в тех случаях, когда удвоение толщины металла нежелательно. Соединение в ус, требующее усложненной подготовки кромок, совмещает преимущества стыкового и нахлесточного соединений и обеспечивает хороший внешний вид и отсутствие выступающих кромок. Соединение в ус дает возможность достичь равнопрочности с целым сечением за счет увеличения рабочей площади соединения.
Существенное значение имеет величина зазора между соединяемыми кромками, которая должна быть малой как для улучшения всасывания жидкого припоя действием капиллярных сил, так и для увеличения прочности соединения. Для серебряных припоев рекомендуется зазор 0,05—0,15 мм; для пайки медью в защитном газе рекомендуются зазоры 0,1—0,2 мм. Строгие требования в отношении величины зазора заставляют производить достаточно чистую механическую обработку поверхностей, так как грубая обработка, например опиловка напильником или опескоструивание, может быть причиной чрезмерного расхода припоя в соединении и резкого падения его прочности.
Для хорошего смачивания припоем поверхность, подлежащая пайке, должна быть безукоризненно чистой. Обезжиривать можно горячей щелочью, трихлорэтиленом или четыреххлористым углеродом. Окислы удаляют травлением в кислотах с последующей тщательной промывкой и сушкой.
Рис. 2. Формы паяных соединений: 1 — нахлесточное; 2 — стыковое; з — «в ус»
Механическую очистку производят протиркой ветошью, тонкой наждачной бумагой, шлифованием мелкозернистыми шлифовальными кругами, щетками и т. д. При сборке часто предварительно наносят флюс на кромки и размещают припой между кромками; в этом случае применяют припой в форме фольги или тонкого порошка, или же припой в виде проволоки или ленты, помещаемой около места пайки.
Собранные детали перед пайкой должны быть достаточно прочно скреплены проволочными связками, шпильками, точечной сваркой и т. д., с тем чтобы устранить возможность смещения деталей при нагреве и в процессе пайки. Поверхность изделий, которая не должна облуживаться, покрывают перед пайкой пастой из мела, глины, графита или их смесей, или смачивают раствором хромовой кислоты и тому подобными веществами, устраняющими прилипание припоя к поверхности изделия.
—
Пайку изделий твердыми припоями применяют в том случае, если неразъемные соединения должны обладать достаточной прочностью (временное сопротивление 15—20 кгс/мм2).
Твердые припои имеют температуру плавления выше 450 °С.
Для нагрева изделий при пайке твердыми припоями используют различные методы: газовым пламенем (горелкой), в печах, в соляных ваннах, токами высокой частоты, на электрических контактных машинах.
Реклама:
Читать далее:
Клеевые соединения
Статьи по теме:
ПАЙКА ТВЕРДЫМИ ПРИПОЯМИ
СВАРКА, РЕЗКА И ПАЙКА МЕТАЛЛОВ
Имеется несколько способов пайки твёрдыми припоями. Эти способы могут быть классифицированы (фиг. 212) по способу нагрева металла в процессе пайки. Твёрдые припои иногда разделяются на тугоплавкие с температурой плавления 875—1100° и легкоплавкие с температурой плавления ниже 875°. Отдельную группу составляют алюминиевые припои. Обычные твёрдые припои раз
деляются на медные, медноцинковые, медноникелевые и серебряные. Наиболее важные твёрдые припои стандартизованы.
Фиг. 212. Способы пайки твёрдыми припоями. |
Состав и примерное назначение медноцннко — вых припоев по ГОСТ 1534-42 даны в табл. 24. Состав и примерное назначение серебряных припоев по ОСТ 2982 даны в табл. 25.
Кроме указанных стандартных припоев, представляют известный интерес и могут находить промышленное применение припои, указанные в табл. 26. В ряде случаев в качестве припоя используется технически чистая медь в температурой плавления 1083°.
Стандартные медноцинковые припои (состав в процентах) Таблица 24
|
Основой большинства флюсов для твёрдой пайки является бура Na2B407, кристаллизующаяся с 10 частями воды с образованием крупных прозрачных бесцветных кристаллов Na2B407 • 10Н2О. Кристаллическая десятиводная бура начинает плавиться при 75°, по мере усиления нагрева постепенно теряет воду, сильно вспучиваясь и разбрызгиваясь, и переходит в безводную соль — плавленую или жжёную буру, плавящуюся при 783°. Бура в расплавленном состоянии может быть нагрета до высоких температур без заметного испарения, весьма жидкотекуча и энергично растворяет окислы многих металлов, в особенности окислы меди.
Для усиления действия флюса к буре часто добавляется борная кислота В (ОН)3, благодаря которой флюс становится более густым и вязким, требующим повышения рабочей температуры. Для пони
жения рабочей температуры флюса, что особенно важно для легкоплавких припоев, вводят хлористый цинк ZnCb, фтористый калий K. F и другие галоидные соли щелочных металлов.
Таблица 25
Стандартные серебряные припон (состав в процентах)
Марка | Ag | Си | Zn | Прі не РЬ | 1МЄСИ более Всего | Темпера — j тура плав — і леяия в °С | Примерное назначение |
ПСр-10 | 9,7—10,3 | 52-54 | 0,5 | 1,0 | 830 | Пайка латуни, | |
содержащей не | |||||||
ПСр-12 | 11,7—12,3 | Со СП ) Со -V) | 0,3 | 1,0 | 785 | менее 58% медн | |
ПСр-25 | 24,7-2-5,3 | 39—41 | о | 0,5 | 1,0 | 765 | Пайка меди, брон |
W | зы, латуни, стали | ||||||
ПСр-45 | 44,5—45,5 | 29,5-30,5 | С5 с-3 | 0,3 | 0,5 | 720 | Пайка меди и |
О о | бронзы | ||||||
ПСр-65 | 64,5-65,5 | 19,5-20,5 | 0,3 | 0,5 | 740 | Пайка ленточ | |
ных пил | |||||||
ПСр-70 | 69,5—70,5 | 25,5—26,5 | 0,3 | 0,5 | 780 | Пайка проводов |
Для пайки нержавеющей стали применяется смесь из равных частей буры и борной кислоты, замешанных до густоты пасты на насыщенном водном растворе хлористого цинка.
Для пайки серого ковкого чугуна в флюсы часто вводятся сильные окислители, например хлорат калия, перекись марганца, окись железа и т. д., для выжигания графита и увеличения чистой металлической поверхности, смачиваемой припоем.
Таблица 26
Разные твёрдые припои (состав в процентах) А. Медные
|
Б. Серебряные
|
Флюсы могут иметь форму порошка или пасты. Применяются также флюсы и в виде жидких растворов, например раствор буры в горячей воде. Иногда целесообразно применять прутки припоя, покрытые с поверхности флюсом. Флюсующее действие могут производить составные части самого припоя. Например, фосфор, окисляясь в фосфорный ангидрид, является хорошим флюсом для меди и медных сплавов, восстанавливая окислы и переводя их в легкоплавкие фосфорно-кислые соединения. Поэтому фосфористые медные припои не требуют флюсов для пайки медных сплавов, что очень удобно на практике.
Порошкообразные флюсы можно посыпать тонким слоем на кромки, причём часто применяется предварительный подогрев кромок, с тем, чтобы частицы флюса плавились, прилипая к металлу, и не сдувались пламенем горелки при пайке. В порошкообразный флюс можно также обмакивать конец прутка припоя, нагретый выше температуры плавления флюса, который прочно пристаёт к прутку.
Пасты и жидкие растворы наносятся кистью или в них обмакивается припой. Можно изготовлять пасту из флюса с порошкообразным припоем и наносить её на кромку перед пайкой.
Для пайки имеют важное значение подготовительные работы, часто определяющие качество соединения. Широко применяются три основные формы паяных соединений: нахлёсточное, стыковое и соединение в ус (фиг. 213). Наиболее распространённым является нахлёсточное соединение, удобное для выполнения и весьма. прочное. Увеличивая перекрытие нахлёсточного соединения, можно повышать его прочность и в большинстве случаев достигнуть равно-
прочности с основным металлом. Стыковое соединение обладает лучшим внешним видом и при хороших припоях и правильном выполнении часто может обеспечить достаточную прочность (предел прочности может доходить до 40—45 кг! мм1). Стыковое соединение применяется в тех случаях, когда удвоение толщины металла нежелательно. Соединение в ус, требующее усложнённой подготовки кромок, совмещает преимущества стыкового и нахлёсточного соединений и обеспечивает хороший внешний вид и отсутствие выступающих кромок и удвоения толщины. Соединение в ус даёт возможность достичь равнопрочности с целым сечением за счёт увеличения рабочей площади соединения.
Фиг. 213. Формы паяных соединений: / — нахлёсточное; 2—стыковое; S — в ус. |
Существенное значение имеет величина зазора между соединяемыми кромками, которая должна быть малой как для улучшения всасывания жидкого припоя действием капиллярных сил, так и для увеличения прочности соединения. Для серебряных припоев рекомендуется зазор 0,05—
0,08 мм, для пайки медью в защитном газе рекомендуются зазоры не более 0,012 мм. Строгие требования к величине зазора предписывают достаточно чистую механическую обработку поверхностей, гак как грубая обработка, например опиловка напильником или опескоструивание, может быть причиной чрезмерного расхода припоя в соединении и резкого падения его прочности.
Для получения хорошего смачивания припоем, поверхность, подлежащая пайке, должна быть безукоризненно чистой.
Обезжиривание может производиться горячей щёлочью, три — хлорэтиленом или четырёххлористым углеродом. Окислы удаляются травлением в кислотах с последующей тщательной промывкой и сушкой.
Механическая чистка производится протиркой концами, тонкой наждачной шкуркой, шлифованием тонкими номерами шлифовальных кругов, щётками и т. д. При сборке часто применяется предварительное нанесение флюса на кромки с размещением припоя между кромками; в этом случае применяется припой в форме фольги или тонкого порошка, или же припой в виде проволоки или ленты, помещаемой около места пайки.
Собранные детали перед пайкой должны быть достаточно прочно скреплены сжимами, проволочными связками, шпильками, точечной сваркой и т. д. с тем, чтобы устранить возможность смещения деталей при нагреве и в процессе пайки. Поверхность изделий, которая не должна облуживаться, покрывается перед пайкой пастой из мела, глины, графита или их смесей, или смачивается раствором хромовой кислоты и т. п. веществами, устраняющими прилипание припоя к поверхности изделия.
В соответствии с приведённой выше классификацией приведём краткое описание основных способов выполнения процесса твёрдой пайки.
Газовая пайка. При этом способе нагрев места пайки осуществляется газовыми горелками. Для пайки мелких деталей пользуются горелками, работающими на воздухе с природным (метаном) или другим горючим газом или же ацетиленом. Для крупных деталей применяются горелки, работающие на кислороде с метаном или другими горючими газами, в особенности ацетиленом. Кислородно-ацетиленовые горелки применяются как специального типа для пайки, дающие широкий факел, так и нормальные, сварочные. Специальные горелки для пайки дают менее концентрированный нагрев и охватывают пламенем сразу значительную поверхность; пламя поддерживается с небольшим избытком ацетилена.
Пайка погружением. При этом способе пайка производится погружением изделия в ванну с расплавленным припоем или в ванну с расплавленными солями. Для металлических ванн обычно используются медноцинковые припои. Расплавленный припой в ванне покрывается слоем флюса. Поверхность изделия, которая должна остаться чистой от припоя, смазывается пастами и растворами, препятствующими её смачиванию.
Соляные ванны для твёрдой пайки устраиваются по типу соляных ванн для термообработки стали. Особенно удобны ванны с электрическим нагревом. Соляная смесь обычно составляется из хлоридов калия и бария КС1 + ВаС12. Состав ванны для любого температурного интервала можно подобрать, меняя соотношения составных частей соляной смеси.
Детали собираются с нанесеним флюса на поверхность, подлежащую пайке, и с размещение
Пайка твердыми припоями в домашних условиях
И все же, несмотря на то, что низкотемпературная и высокотемпературная пайки представляют собой явления одной сущности, их технология, используемые материалы и оборудование, характеристики получаемого соединения существенно различаются. Что, собственно, и явилось основанием для разделения этих способов. За граничную температуру, разделяющую их, приняты 450°C.
Отличия высокотемпературной пайки от низкотемпературной
Важным отличием высокотемпературной пайки от низкотемпературной является повышенная термоустойчивость соединения. Поскольку температура плавления твердых припоев значительно выше температуры плавления мягких, соединение, выполненное высокотемпературной пайкой, способно работать при более высоких температурах, сохраняя все свои свойства. Во многих случаях при выборе способа пайки, эта особенность является определяющей.
Но есть и то, в чем пайка твердыми припоями уступает пайке мягкими припоями. Относительно высокая температура может вызывать структурные изменения в некоторых металлах. Такое, в частности, наблюдается в чугуне, в котором при пайке могут возникать закалочные структуры, приводящие к повышенной хрупкости металла в зоне шва.
Высокая температура плавления твердых припоев предъявляет свои требования к источникам нагрева. Они должны обеспечивать расплавление припоев, температура плавления которых достигает иногда 1000°C. Это исключает использование при высокотемпературной пайке удобных паяльников, являющихся основным инструментом при пайке мягкими припоями.
Резюмируя вышесказанное, можно подвести итог сравнения высокотемпературной и низкотемпературной паек. К достоинствам первой относится высокая прочность и термоустойчивость соединения, к недостаткам – сложность технологического процесса, обусловленная необходимостью прогрева паяемых деталей до относительно высоких температур.
Применение пайки твердыми припоями
Пайка твердыми припоями является основным способом при изготовлении металлорежущего инструмента с твердосплавными пластинами. Припаивание последних обеспечивает достаточную прочность соединения и не оказывает отрицательного воздействия на твердость и геометрию режущих пластин.
Изготовление всевозможных сосудов из цветных металлов и нержавеющих сталей, соединение стальных и медных трубопроводов, работающих под высоким давлением или повышенной температуре в различных системах – холодильных, теплообменных и пр. – также не может обойтись без пайки твердыми припоями.
Широко используется высокотемпературная пайка при ремонте автомобилей – радиаторов, трубопроводных систем двигателя и трансмиссии, кузовов, различных деталей – везде, где нельзя или нежелательно применять сварку.
Целесообразно использование высокотемпературной пайки для соединения между собой тонкостенных деталей, работающих при значительных нагрузках и упругих деформациях.
Для ремонта медных и латунных бытовых изделий, подвергающихся в процессе эксплуатации высоким температурам, высокотемпературная пайка является способом ремонта не имеющим альтернативы. Таких, например, как старинный самовар, растапливаемый дровами. В этом случае мягкие припои не могут применяться из-за неспособности выдерживать высокую температуру нагрева.
Источники нагрева при высокотемпературной пайке
Основными источниками нагрева при высокотемпературной пайке являются газовые горелки различных типов, индукторы и печи. Применяется также нагрев электросопротивлением. В быту чаще всего твердыми припоями паяют с помощью горелок.
Припои
Иногда используют в качестве припоя и технически чистую медь. Однако гораздо чаще используют пайку медными припоями, представляющими собой соединения меди с другими металлами – цинком, серебром, кремнием, оловом и пр. Каждый из этих элементов вносит свою лепту в технологические свойства припоев. Почти все они снижают температуру плавления (у чистой меди она составляет 1083°C).
При высокотемпературной пайке используются медно-цинковые, медно-фосфорные, серебряные припои и латуни.
Медно-цинковые припои. Существует большое количество медно-цинковых припоев (ПМЦ-35, ПМЦ-39, ПМЦ-50, ПМЦ-54, ПМЦ-57 и пр.). Цифры указывают процентное содержание меди. Их используют для пайки бронзы, меди, стали. Недостатком чисто медно-цинковых материалов является плохая работа в условиях ударных, вибрационных и изгибающих нагрузок. Чтобы убрать или снизить этот недостаток используют легирование их другими металлами (например, латуни можно рассматривать как легированные медно-цинковые припои). Легированные медно-цинковые припои используются, в частности, при пайке твердосплавных резцов.
Медно-фосфорные припои. Медно-фосфорные припои (ПМФ-7, ПМФ-9, ПМФОЦр-6-4-0,03) представляют собой сплав меди с фосфором. Следующая за буквами цифра указывает на процентное содержание фосфора. Припой ПМФОЦр-6-4-0.03, кроме меди и фосфора, содержит олово и цирконий.
Медно-фосфорные припои относятся к среднеплавким (700-850°C), обладают высокой текучестью и хорошей коррозионной устойчивостью к агрессивным средам. Используются для пайки меди и ее сплавов (бронзы, латуни, мельхиора). Можно их использовать и в качестве заменителя серебряных припоев при ремонте ювелирных изделий.
Пайка сталей и чугуна медными припоями, содержащими фосфор, не применяется из-за повышенной хрупкости соединения и его неспособности переносить ударные, вибрационные и изгибающие нагрузки. Это вызвано образованием по границе шва пленки фосфитов.
Отличительную особенность медно-фосфорных припоев является то, что они являются самофлюсующимися. При пайке ими медных изделий, применение флюса не обязательно.
Латуни. Широкое распространение в качестве припоев получили латуни, которые являются сплавом меди с цинком. Латуни Л62 и ЛОК-62-06-04 дают прочные паяные соединения. ЛОК-62-06-04 отличается от Л62 наличием олова и кремния, обеспечивающих более высокие технологические свойства припоя. Олово увеличивает жидкотекучесть и снижает температуру плавления, а соединения кремния предохраняют цинк от окисления и испарения. Латуни применяются при пайке меди, стали, чугуна.
Серебряные припои. Серебро является отличным материалом для пайки. Серебряным припоям, которые представляют собой в основном сплав серебра с медью и цинком, принадлежит первое место по растеканию, смачиваемости, прочности и антикоррозионности. Не будь они такими дорогими, можно было бы отказаться от всех остальных припоев, используя только серебряные. Благо они обладают универсальностью и способны паять практически любой металл.
Припои на основе серебра обозначаются буквами ПСр (ПСр-15, ПСр-25, ПСр-45, ПСр-65, ПСр-70). Марки ПСр-15 и ПСр-25 используются для пайки не очень ответственных деталей. Если требуется получить особо качественное соединение, используют припой ПСр-45, имеющий 45% серебра, 30% меди и 25% цинка. ПСр-45 обладает отличными качествами – вязкостью, ковкостью, жидкотекучестью, устойчивостью против коррозии, способностью выдерживать вибрацию и удары. Припой ПСр-65 не уступает ПСр-45, но слишком дорог.
Серебряными припоями можно паять практически любой металл – медь и ее сплавы, серебро, стали и пр. Однако в силу их дороговизны пайку серебряными припоями применяют только там, где это экономически целесообразно, в частности, для соединения нержавеющих сталей, относящихся к разряду труднопаяемых и требующих припоев, обладающих хорошей смачиваемостью и позволяющих избежать коррозии, ко
ПАЙКА ТВЕРДЫМИ ПРИПОЯМИ | Инструмент, проверенный временем
Имеется несколько способов пайки твёрдыми припоями. Эти способы могут быть классифицированы (фиг. 212) по способу нагрева металла в процессе пайки. Твёрдые припои иногда разделяются на тугоплавкие с температурой плавления 875—1100° и легкоплавкие с температурой плавления ниже 875°. Отдельную группу составляют алюминиевые припои. Обычные твёрдые припои раз
деляются на медные, медноцинковые, медноникелевые и серебряные. Наиболее важные твёрдые припои стандартизованы.
Состав и примерное назначение медноцннко — вых припоев по ГОСТ 1534-42 даны в табл. 24. Состав и примерное назначение серебряных припоев по ОСТ 2982 даны в табл. 25.
Кроме указанных стандартных припоев, представляют известный интерес и могут находить промышленное применение припои, указанные в табл. 26. В ряде случаев в качестве припоя используется технически чистая медь в температурой плавления 1083°.
жения рабочей температуры флюса, что особенно важно для легкоплавких припоев, вводят хлористый цинк ZnCЬ, фтористый калий K. F и другие галоидные соли щелочных металлов.
Таблица 25
Стандартные серебряные припои (состав в процентах)
Марка | Ag | Си | Zn | Прі не РЬ | 1МЄСИ более Всего | Темпера — j тура плав — і ления в °С | Примерное назначение |
ПСр-10 | 9,7—10,3 | 52-54 | 0,5 | 1,0 | 830 | Пайка латуни, содержащей не | |
ПСр-12 | 11,7—12,3 | Со СП ) Со -V) | 0,5 | 1,0 | 785 | менее 58% меди | |
ПСр-25 | 24,7-25,3 | 39—41 | О О W | 0,5 | 1,0 | 765 | Пайка меди, бронзы, латуни, стали |
ПСр-45 | 44,5—45,5 | 29,5-30,5 | КЗ еЗ н о о | 0,3 | 0,5 | 720 | Пайка меди и бронзы |
ПСр-65 | 64,5-65,5 | 19,5-20,5 | 0,3 | 0,5 | 740 | Пайка ленточных пил | |
ПСр-70 | 69,5—70,5 | 25,5—26,5 | 0,3 | 0,5 | 780 | Пайка проводов |
Для пайки нержавеющей стали применяется смесь из равных частей буры и борной кислоты, замешанных до густоты пасты на насыщенном водном растворе хлористого цинка.
Для пайки серого ковкого чугуна в флюсы часто вводятся сильные окислители, например хлорат калия, перекись марганца, окись железа и т. д., для выжигания графита и увеличения чистой металлической поверхности, смачиваемой припоем.
Таблица 26
Разные твёрдые припои (состав в процентах) А. Медные
|
Б. Серебряные
|
Флюсы могут иметь форму порошка или пасты. Применяются также флюсы и в виде жидких растворов, например раствор буры в горячей воде. Иногда целесообразно применять прутки припоя, покрытые с поверхности флюсом. Флюсующее действие могут производить составные части самого припоя. Например, фосфор, окисляясь в фосфорный ангидрид, является хорошим флюсом для меди и медных сплавов, восстанавливая окислы и переводя их в легкоплавкие фосфорно-кислые соединения. Поэтому фосфористые медные припои не требуют флюсов для пайки медных сплавов, что очень удобно на практике.
Порошкообразные флюсы можно посыпать тонким слоем на кромки, причём часто применяется предварительный подогрев кромок, с тем, чтобы частицы флюса плавились, прилипая к металлу, и не сдувались пламенем горелки при пайке. В порошкообразный флюс можно также обмакивать конец прутка припоя, нагретый выше температуры плавления флюса, который прочно пристаёт к прутку.
Пасты и жидкие растворы наносятся кистью или в них обмакивается припой. Можно изготовлять пасту из флюса с порошкообразным припоем и наносить её на кромку перед пайкой.
Для пайки имеют важное значение подготовительные работы, часто определяющие качество соединения. Широко применяются три основные формы паяных соединений: нахлёсточное, стыковое и соединение в ус (фиг. 213). Наиболее распространённым является нахлёсточное соединение, удобное для выполнения и весьма. прочное. Увеличивая перекрытие нахлёсточного соединения, можно повышать его прочность и в большинстве случаев достигнуть равно-
прочности с основным металлом. Стыковое соединение обладает лучшим внешним видом и при хороших припоях и правильном выполнении часто может обеспечить достаточную прочность (предел прочности может доходить до 40—45 кг! мм1). Стыковое соединение применяется в тех случаях, когда удвоение толщины металла нежелательно. Соединение в ус, требующее усложнённой подготовки кромок, совмещает преимущества стыкового и нахлёсточного соединений и обеспечивает хороший внешний вид и отсутствие выступающих кромок и удвоения толщины. Соединение в ус даёт возможность достичь равнопрочности с целым сечением за счёт увеличения рабочей площади соединения.
Существенное значение имеет величина зазора между соединяемыми кромками, которая должна быть малой как для улучшения всасывания жидкого припоя действием капиллярных сил, так и для увеличения прочности соединения. Для серебряных припоев рекомендуется зазор 0,05—
0,08 мм, для пайки медью в защитном газе рекомендуются зазоры не более 0,012 мм. Строгие требования к величине зазора предписывают достаточно чистую механическую обработку поверхностей, гак как грубая обработка, например опиловка напильником или опескоструивание, может быть причиной чрезмерного расхода припоя в соединении и резкого падения его прочности.
Для получения хорошего смачивания припоем, поверхность, подлежащая пайке, должна быть безукоризненно чистой.
Обезжиривание может производиться горячей щёлочью, трихлорэтиленом или четырёххлористым углеродом. Окислы удаляются травлением в кислотах с последующей тщательной промывкой и сушкой.
Механическая чистка производится протиркой концами, тонкой наждачной шкуркой, шлифованием тонкими номерами шлифовальных кругов, щётками и т. д. При сборке часто применяется предварительное нанесение флюса на кромки с размещением припоя между кромками; в этом случае применяется припой в форме фольги или тонкого порошка, или же припой в виде проволоки или ленты, помещаемой около места пайки.
Собранные детали перед пайкой должны быть достаточно прочно скреплены сжимами, проволочными связками, шпильками, точечной сваркой и т. д. с тем, чтобы устранить возможность смещения деталей при нагреве и в процессе пайки. Поверхность изделий, которая не должна облуживаться, покрывается перед пайкой пастой из мела, глины, графита или их смесей, или смачивается раствором хромовой кислоты и т. п. веществами, устраняющими прилипание припоя к поверхности изделия.
В соответствии с приведённой выше классификацией приведём краткое описание основных способов выполнения процесса твёрдой пайки.
Газовая пайка. При этом способе нагрев места пайки осуществляется газовыми горелками. Для пайки мелких деталей пользуются горелками, работающими на воздухе с природным (метаном) или другим горючим газом или же ацетиленом. Для крупных деталей применяются горелки, работающие на кислороде с метаном или другими горючими газами, в особенности ацетиленом. Кислородно-ацетиленовые горелки применяются как специального типа для пайки, дающие широкий факел, так и нормальные, сварочные. Специальные горелки для пайки дают менее концентрированный нагрев и охватывают пламенем сразу значительную поверхность; пламя поддерживается с небольшим избытком ацетилена.
Пайка погружением. При этом способе пайка производится погружением изделия в ванну с расплавленным припоем или в ванну с расплавленными солями. Для металлических ванн обычно используются медноцинковые припои. Расплавленный припой в ванне покрывается слоем флюса. Поверхность изделия, которая должна остаться чистой от припоя, смазывается пастами и растворами, препятствующими её смачиванию.
Соляные ванны для твёрдой пайки устраиваются по типу соляных ванн для термообработки стали. Особенно удобны ванны с электрическим нагревом. Соляная смесь обычно составляется из хлоридов калия и бария КС1 + ВаС12. Состав ванны для любого температурного интервала можно подобрать, меняя соотношения составных частей соляной смеси.
Детали собираются с нанесеним флюса на поверхность, подлежащую пайке, и с размещением припоя между кромками или около места соединения, после чего скрепляются и обмакиваются в ванну. Соляная ванна обеспечивает постоянный температурный режим с точностью ± 5° и защищает место пайки от окисления. Когда деталь вынута из ванны, её защищает от окисления при охлаждении плёнка расплавленных солей, которая по охлаждении может быть удалена промывкой в горячей воде. Применение соляных ванн для твёрдой пайки заслуживает большого внимания. Весьма вероятно широкое распространение этого метода в нашей промышленности в ближайшие годы.
Пайка погружением в ванны отличается высокой производительностью, однородностью качества пайки и может быть механизирована.
Электрическая пайка. Электрический нагрев места пайки может быть осуществлён различными методами: электрической дугой прямого или косвенного действия, пропусканием тока через место сварки, вихревыми токами, которые индуктируются в металле изделия
переменными магнитными полями, за счёт разогрева контакта между поверхностью изделия и токоподводящим электродом и т. д.
Для пайки дугой прямого действия медноцинковые припои мало пригодны, ввиду летучести цинка и сильного его испарения и выгорания под действием высокой температуры дуги. Наиболее пригодны тугоплавкие медные припои с содержанием фосфора или кремния. Для пайки используется угольная дуга, которая направляется преимущественно на конец стержня припоя, касающегося основного металла, и не должна расплавлять кромок изделия.
Угольная дуга косвенного действия (дуговая горелка) заменяет газовую горелку и даёт возможность выполнять процесс пайки всеми типами твёрдых припоев, как медноцинковых, так и серебряных. Технологически дуговая горелка менее удобна, чем газовая, и применяется обычно лишь при небольшом объёме работ по пайке.
Электрическая пайка сопротивлением может выполняться на нормальных сварочных контактных машинах или на специальных электрических аппаратах для пайки. Нагрев места пайки производится пропусканием через него тока большой силы. Ток получается от низковольтного трансформатора, встроенного в корпус аппарата для пайки и составляющего с ним одно целое.
Более универсальными электрическими аппаратами для пайки являются аппараты, работающие по способу горячего контакта между угольным или графитным электродом и изделием. Такой аппарат состоит из двух основных частей: понижающего трансформатора, подвижного или стационарного, и клещей для пайки, соединяемых с зажимами трансформатора гибкими проводами, которые могут иметь значительную длину, что придаёт установке гибкость и универсальность применения.
Понижающий трансформатор изготовляется по типу трансформаторов для электрических контактных сварочных машин. Первичная обмотка трансформатора делается секционированной, что даёт возможность регулировать напряжение вторичной обмотки и рабочую силу тока путём переключения витков первичной обмотки, как это делается в контактных машинах. Первичная обмотка трансформатора включается в электрическую цепь контактором с кнопочным управлением. Кнопка включения помещается на ручке паяльных клещей (фиг. 214) или выносится в форме отдельной переносной педали. Рабочие токоподводящие контакты паяльных клещей выполнены в форме сменных призматических блоков — брусков из электродного угля или графита. Зажатие детали производится зажимным винтом, включение нагревающего тока — кнопкой на ручке клещей. Рабочие токи для пайки обычно находятся в пределах 500—1000 а.
Паяльные клещи присоединяются ко вторичной обмотке трансформатора гибкими проводами достаточного сечения и требующейся длины (обычно до 2—3 м). Для пайки меди обычно пользуются фосфористыми медными припоями и для пайки стали серебряными
припоями. Фосфорно-медные припои для пайки чёрных металлов непригодны.
Пайка токами высокой частоты. В последнее время быстро развивается и начинает находить широкое промышленное применение новый весьма эффективный способ пайки токами высокой частоты. Метод основан на нагреве металла у места пайки вихревыми токами, которые создаются переменным магнитным полем высокой частоты. Переменное магнитное поле, в свою очередь, создаётся намагничивающими обмотками — индукторами. При приближении индуктора к поверхности изделия возникают вихревые токи в зоне металла, подвергающейся магнитному воздействию индуктора. Действие индуктора тем сильнее, чем меньше расстояние между индуктором и нагреваемым металлом. Для возможного уменьшения расстояния применяют индукторы с изоляцией из тугоплавкой эмали; в этом случае расстояние между индуктором и нагреваемым металлом может быть снижено до 0,3—0,5 мм.
Нагревание токами высокой частоты сосредоточивается в очень тонком поверхностном слое металла, в котором возникают вихревые токи. Нижележащие слои нагреваются вследствие теплопроводности. Малый объём разогреваемого металла позволяет вести нагрев весьма быстро с высоким к. п. д.
Процесс пайки отличается чистотой, удобством выполнения, легко поддаётся механизации и может быть хорошо приспособлен к условиям массового производства однотипных деталей. Все эти преимущества обеспечивают нагреву токами высокой частоты возможность широкого промышленного использования при пайке. Препятствием к применению токов высокой частоты пока служит довольно высокая стоимость и некоторая сложность установок для получения этих токов. По мере упрощения и удешевления установки найдут широкое применение для процесса пайки.
Пайка в печах. Нагрев под пайку может производиться также в различных печах, по устройству аналогичных печам для термообработки стали. Применяются, например, очковые печи с нефтяным отоплением, широко применяются муфельные печи, в особенности удобны электрические муфельные печи. Пайка ведётся посредством нагрева деталей с заранее нанесёнными флюсом и припоем, который закладывается между соединяемыми кромками или
помещается рядом с местом пайки. Пайка в печах с применением флюса трудоёмка, требует достаточно квалифицированной рабочей силы и не имеет перспектив на особенно широкое промышленное применение. Значительно важнее пайка в печах в восстановительной атмосфере; этот вид пайки имеет перспективы на широкое применение в массовом производстве.
Применение пайки твердыми припоями — Студопедия
Область применения пайки твердыми припоями определяется ее промежуточным положением между низкотемпературной пайкой и сваркой. Везде, где требуется получить более прочное соединение, чем это можно сделать с использованием мягких припоев, способное к тому же работать в условиях высоких температур, и в то же время сохранить структуру соединяемых металлов, не допустить их разупрочнения и деформации (как это имеет место при сварке), применяют высокотемпературную пайку.
Пайка твердыми припоями является основным способом при изготовлении металлорежущего инструмента с твердосплавными пластинами. Припаивание последних обеспечивает достаточную прочность соединения и не оказывает отрицательного воздействия на твердость и геометрию режущих пластин.
Резцы
Изготовление всевозможных сосудов из цветных металлов и нержавеющих сталей, соединение стальных и медных трубопроводов, работающих под высоким давлением или повышенной температуре в различных системах — холодильных, теплообменных и пр. — также не может обойтись без пайки твердыми припоями.
Широко используется высокотемпературная пайка при ремонте автомобилей — радиаторов, трубопроводных систем двигателя и трансмиссии, кузовов, различных деталей — везде, где нельзя или нежелательно применять сварку.
Целесообразно использование высокотемпературной пайки для соединения между собой тонкостенных деталей, работающих при значительных нагрузках и упругих деформациях.
Для ремонта медных и латунных бытовых изделий, подвергающихся в процессе эксплуатации высоким температурам, высокотемпературная пайка является способом ремонта не имеющим альтернативы. Таких, например, как старинный самовар, растапливаемый дровами. В этом случае мягкие припои не могут применяться из-за неспособности выдерживать высокую температуру нагрева.
Источники нагрева при высокотемпературной пайке
В качестве источников нагрева при высокотемпературной пайке может использоваться любое оборудование, которое позволяет нагревать паяемые детали несколько выше температуры плавления используемых припоев. Эта температура может колебаться в пределах 450-1200°C. При использовании тугоплавких материалов, таких как латунь или технически чистая медь, требуется нагрев, превышающий 1000°C, при использовании среднеплавких припоев требуется температура нагрева в 700-800°C.
Основными источниками нагрева при высокотемпературной пайке являются газовые горелки различных типов, индукторы и печи. Применяется также нагрев электросопротивлением. В быту чаще всего твердыми припоями паяют с помощью горелок.
Припои
Основная заслуга в образовании прочных и термоустойчивых соединений при высокотемпературной пайке принадлежит меди. Она не только входит практически во все твердые припои, но в большинстве из них выполняет главную роль, являясь основой припоев.
Иногда используют в качестве припоя и технически чистую медь. Однако гораздо чаще используют пайку медными припоями, представляющими собой соединения меди с другими металлами — цинком, серебром, кремнием, оловом и пр. Каждый из этих элементов вносит свою лепту в технологические свойства припоев. Почти все они снижают температуру плавления (у чистой меди она составляет 1083°C).
При высокотемпературной пайке используются медно-цинковые, медно-фосфорные, серебряные припои и латуни.
Твердый припой
Твердый припой покрытый флюсом
Медно-цинковые припои. Существует большое количество медно-цинковых припоев (ПМЦ-35, ПМЦ-39, ПМЦ-50, ПМЦ-54, ПМЦ-57 и пр.). Цифры указывают процентное содержание меди. Их используют для пайки бронзы, меди, стали. Недостатком чисто медно-цинковых материалов является плохая работа в условиях ударных, вибрационных и изгибающих нагрузок. Чтобы убрать или снизить этот недостаток используют легирование их другими металлами (например, латуни можно рассматривать как легированные медно-цинковые припои). Легированные медно-цинковые припои используются, в частности, при пайке твердосплавных резцов.
Медно-фосфорные припои. Медно-фосфорные припои (ПМФ-7, ПМФ-9, ПМФОЦр-6-4-0,03) представляют собой сплав меди с фосфором. Следующая за буквами цифра указывает на процентное содержание фосфора. Припой ПМФОЦр-6-4-0.03, кроме меди и фосфора, содержит олово и цирконий.
Медно-фосфорные припои относятся к среднеплавким (700-850°C), обладают высокой текучестью и хорошей коррозионной устойчивостью к агрессивным средам. Используются для пайки меди и ее сплавов (бронзы, латуни, мельхиора). Можно их использовать и в качестве заменителя серебряных припоев при ремонте ювелирных изделий.
Пайка сталей и чугуна медными припоями, содержащими фосфор, не применяется из-за повышенной хрупкости соединения и его неспособности переносить ударные, вибрационные и изгибающие нагрузки. Это вызвано образованием по границе шва пленки фосфитов.
Отличительную особенность медно-фосфорных припоев является то, что они являются самофлюсующимися. При пайке ими медных изделий, применение флюса не обязательно.
Латуни. Широкое распространение в качестве припоев получили латуни, которые являются сплавом меди с цинком. Латуни Л62 и ЛОК-62-06-04 дают прочные паяные соединения. ЛОК-62-06-04 отличается от Л62 наличием олова и кремния, обеспечивающих более высокие технологические свойства припоя. Олово увеличивает жидкотекучесть и снижает температуру плавления, а соединения кремния предохраняют цинк от окисления и испарения. Латуни применяются при пайке меди, стали, чугуна.
Серебряные припои. Серебро является отличным материалом для пайки. Серебряным припоям, которые представляют собой в основном сплав серебра с медью и цинком, принадлежит первое место по растеканию, смачиваемости, прочности и антикоррозионности. Не будь они такими дорогими, можно было бы отказаться от всех остальных припоев, используя только серебряные. Благо они обладают универсальностью и способны паять практически любой металл.
Припои на основе серебра обозначаются буквами ПСр (ПСр-15, ПСр-25, ПСр-45, ПСр-65, ПСр-70). Марки ПСр-15 и ПСр-25 используются для пайки не очень ответственных деталей. Если требуется получить особо качественное соединение, используют припой ПСр-45, имеющий 45% серебра, 30% меди и 25% цинка. ПСр-45 обладает отличными качествами — вязкостью, ковкостью, жидкотекучестью, устойчивостью против коррозии, способностью выдерживать вибрацию и удары. Припой ПСр-65 не уступает ПСр-45, но слишком дорог.
Серебряными припоями можно паять практически любой металл — медь и ее сплавы, серебро, стали и пр. Однако в силу их дороговизны пайку серебряными припоями применяют только там, где это экономически целесообразно, в частности, для соединения нержавеющих сталей, относящихся к разряду труднопаяемых и требующих припоев, обладающих хорошей смачиваемостью и позволяющих избежать коррозии, которая может возникнуть в спае.
Флюсы
Основным компонентом флюсов для пайки твердыми припоями являются борные соединения — бура (Na2B4O7), борная кислота (H3BO3), борный ангидрид (B2O3). Для усиления активности борных флюсов, например при пайке нержавеющих и жаростойких сталей, в них добавляются соединения фтора — фтористый кальций, фтористый калий. Применяются специальные флюсы, регламентированные ГОСТ 23178-78 — под марками ПВ200, ПВ201, ПВ209, ПВ209Х, ПВ284Х. В первые два входят борная кислота, бура и фтористый кальций. Они используются для пайки нержавеющих и конструкционных сталей и жаропрочных сплавов. Флюс ПВ209 состоит из фтористого калия, борного ангидрида, калия тетрафторбората. Флюсы ПВ209Х, ПВ284Х состоят из борной кислоты, гидроксида калия, плавиковой кислоты. Флюсы ПВ209, ПВ209Х, ПВ284Х можно использовать для пайки меди и ее сплавов, нержавеющих и конструкционных сталей.
Пайка меди и ее сплавов может производиться с помощью чистой буры, которая является универсальным флюсом для высокотемпературной пайки.
Бура
Используются различные формы выпуска флюсов — жидкости, порошок, кусочки (кристаллы буры, например). Чтобы облегчить их дозирование (избыток флюса так же нежелателен, как и недостаток), используют объединение их с припоем. Делается это разными способами — добавлением в виде порошка в сыпучие формы припоев, обмазкой прутков припоя или помещением внутрь трубочки из припоя, совместным прессованием таблетированных форм.
Пайка меди твердым припоем ПМФ-7 (harris). (добавлены фото) / Мастерские / В помощь стим-мастеру / Коллективные блоги / Steampunker.ru
Здравствуйте дамы и господа.В последнее время возникало много вопросов по пайке твердым припоем. Я решил привести пример пайки припоем ПМФ7(harris — импортный аналог ПМФ7) (припой меднофосфорный с содержанием фосфора 7%).
Для работы вам потребуются: газовая горелка, припой, кислота, приспособления для закрепления заготовки (тиски, пинцет, проволока).
собственно сам припой.
Горелка которой я пользуюсь. Фирма Topex.
Приведу пример, вам нужно спаять кольцо из медной проволоки определенного сечения, вы изначально должны очистить медь от окисла либо акалины(если обжигали лак). Очищать проще всего азотной либо соляной кислотой. Если нет возможности купить/хранить кислоты дома, пойдет обычная лимонная кислота(можно купить в магазине, в отделе специй). Лимонная растворяется в кипятке, столовая ложка на стакан кипятка(единственный нюанс — снимает ненужное с металла в течении часа). И так, когда ваше кольцо будет очищено, необходимо зафиксировать его так, что бы зазор, который вы хотите спаять не превышал 0.4мм.
Делаем из проволоки кольцо.
Можно больше зазор сделать, можно меньше, но 0.4мм (я паяю на глаз обычно, делаю зазор максимально маленьким, но главное что бы зазор был) оптимальный зазор для заполнения его припоем.
После этого, как все у вас закреплено, вы горелкой раскаляете заготовку до бела, и подносите к зазору пруток припоя. Пруток начнет плавиться от температуры заготовки, припой стечет и заполнит зазор.
Нагреваем
Дотрагиваемся припоем до зазора
Убираем припой
Результат
Очищаем в азотной кислоте
Промываем от азотной кислоты (лучше это делать под краном, но я ленюсь)
Слегка полируем шов
Отбиваем до ровного состояния
Получаем результат
Затраченное время работы — примерно 5 минут.
Видео не снимал, ибо после работы очень хотелось кушать, но если по фото не понятен процесс, по просьбе обязательно сделаю видео.
*P.s.* Есть еще такой нюанс как теплопроводность. Если вы зажмете данное кольцо в тиски, скорее всего вы не сможете разогреть его обычной горелкой с температурой 1300с, так как тепло будет уходить на тиски. в данном случае лучше закрепить кольцо на медную проволку (можно ее для устойчивости слегка расплющить — отбить молотком), а прволку с закрепленным на нее кольцом закрепить в тиски. В данном случае основное тепло будет именно на кольце, минимум будет уходить на крепежную проволку, а на тиски уже почти не будет уходить тепла — это облегчит работу.
Если вы делаете что либо большое, то скорее всего температуры 1300с будет недостаточно. В данном случаем могу посоветовать только газ МАРР(метил ацетилен пропадоин пропан), у него температура горения на ~30% выше. Либо искать оборудование посерьезнее.
Есть несколько небольших нюансов:
1 — если вы долго будете греть заготовку, она покроется акалиной, температура заготовки заметно снизится, этой температуры вполне может не хватить для плавления припоя. (желательно делать все быстро, ибо если изделие покроется акалиной, его придется снова очищать)
2 — Если долго будете держать пруток на раскаленном изделии, то на него может стечь очень много припоя, по мимо заполнения зазора образуется капля, которую придется долго и кропотливо убирать напильником.
3 — Если вы попадете прутком под пламя горелки, высока вероятность того, что пруток расплавится и образует каплю прямо на себе, а не стечет на деталь, по этому желательно касаться припоем именно раскаленной детали минуя активное пламя. Делать это можно путем нагрева изделия снизу, а пруток припоя подавать сверху.
4 — Если вы дадите детали на мгновение остыть, когда коснулись к ней припоем, то припой может заполнить зазор и застыть. У вас останется деталь с припаянным к ней прутком, и при попытке его оторвать — деформируете изделие. Решение данной данной проблемы просто — если греете деталь руками, точно прогревайте деталь, не отводя пламя. Коснулись припоем, он стек на изделие, сразу же убрали припой. Для верности можно закрепить горелку на какой нибудь штатив, что бы пламя было постоянным и направлено ровно в одну точку.
Есть еще нюансы пайки. Например кусать припой на мелкие крошки, помещать его в зазоры и греть уже его. Но так высока вероятность того что припой будет просто скатываться в шарики.
Кстати, если на зазоре все же образовался небольшой излишек припоя, убрать его можно путем прогрева детали по сторонам от зазора. Просто водите горелкой раскаляя металл слева и справа от зазора, излишки тонкой пленкой растекутся и покроют раскаленную часть. Хочу так же заметить что медь покрытая припоем имеет немного шероховатую структуру и иной цвет. Это будет заметно даже под патиной. Так что излишки все же снимать наждачной бумагой и полировать после этого поверхность. Изменение цвета обусловлено тем, что после расплавления припоя — фосфора там уже не будет, останется только медь, а медная проволока обычно имеет в себе примеси, по этому и отличается по цвету.
Надеюсь что данная информация будет для вас полезной.
Пайка мягкими и твердыми припоями
Полуавтоматы для дуговой сварки и их основные узлы
Пайкой называется технологический процесс получения неразъемных соединений, выполняемый с применением припоя — проволоки из сплава, имеющего температуру плавления более низкую, чем температура плавления основного металла. В результате взаимодействия расплавленного при определенной температуре припоя с кромками основного металла и последующего остывания образуется спай. Кромки основного металла соединяются (спаиваются) вследствие эффекта смачивания их поверхностей, взаимного растворения и диффузии (проникновения) припоя и основного металла в зоне шва (спая). В связи с развитием современных ресурсосберегающих технологий процесс пайки находит широкое применение при изготовлении продукции машиностроения, приборостроения,
электротехнической и электронной промышленности. По сравнению с другими методами получения неразъемных соединений (в том числе и по сравнению со сваркой) пайка имеет ряд преимуществ: простота
выполнения операции, сохранение размеров и формы соединяемых деталей, сохранение неизменного химического состава и физикомеханических свойств паяемых материалов. Кроме того, при пайке отпадает необходимость в последующей механической и термической
обработке, легче получаются соединения в труднодоступных местах и есть возможности для механизации и автоматизации процесса пайки. Процесс получения паяного соединения газопламенной горелкой состоит из нескольких стадий. Подготовка деталей перед пайкой аналогична подготовке под сварку. Перед предварительным нагревом для защиты металла от окисления на детали наносят флюс. При пайке применяют горелку, как правило, малой мощности. Состав пламени, присадочную проволоку и флюсы подбирают в зависимости от паяемого металла. Восстановительным пламенем производят пайку меди, бронз, латуни и различных сталей. Нейтральным пламенем паяют, как правило, сплавы цветных металлов специального назначения. Пламенем горелки осуществляют общий или местный нагрев до температуры пайки. Обычно температура пайки превышает температуру плавления припоя на 30—50 °С. Затем расплавляют припой, который смачивает соединяемые поверхности и заполняет зазор соединения. Исходя из условий образования соединения, припои должны удовлетворять следующим основным требованиям: иметь температуру плавления ниже температуры плавления паяемых материалов; хорошо смачивать поверхность соединяемых материалов, хорошо растекаться по ним и заполнять капиллярные зазоры; не вызывать в последующем химическую эрозию, не подвергаться старению; не изменять свои физико-механические свойства в процессе эксплуатации изделия. Припои классифицируют по следующим основным признакам: температуре плавления —
особолегкоплавкие до 145 °С, легкоплавкие до 450 °С, среднеплавкие до 1100 °С, высокоплавкие до 1850 °С, тугоплавкие свыше 1850 °С; способу образования — готовые, образующиеся в процессе пайки; химическому составу (основному компоненту) — оловянные, медные, никелевые, марганцевые, железные, титановые, серебряные, золотые и т. д.; способности к флюсованию — флюсуемые и самофлюсующиеся; виду полуфабриката — листовые, ленточные, проволочные, порошковые и др. Выбор марки припоя и метода нанесения определяется конструкцией и требованиями, предъявляемыми к соединению. В настоящее время разработано большое количество всевозможных припоев и флюсов. Различают два основных вида пайки: мягкими и твердыми припоями. Мягкие припои имеют невысокую механическую прочность и их плавление осуществляется при температуре до 400 °С. Прочность твердых припоев значительно выше, а температура плавления — свыше 550 °С. Пайку мягкими припоями применяют главным образом для получения плотного соединения деталей, не подверженных значительным нагрузкам. Широко известны припои оловянно-свинцовые (ПОС). Химический состав, температура плавления и примерное назначение некоторых мягких припоев приведены в табл. 82.
Таблица 82
Химический состав, температура плавления и примерное назначение некоторых мягких припоев
Марка | Химический ссстаз. %. псмассе | Темпера тура гиаз- ления. ;С | Примерное назначение | ||||
Sii | Sb | РЪ | Bi | Cd | |||
ПОС90 | S9-90 | Не более 0.15 | Осталь ное | Не более 0.1 | — | 222 | Для пищевой промышленности и внутренних швов хозяйственной посулы |
ПОС40 | 39-40 | 1,5-2;0 | Осталь ное | Не более 0.1 | — | 235 | Для радиаторов, элек — тро — н радиоаппаратуры. физико-технических приборов |
nocis | 17—IS | 2.0-75 | Осталь ное | Не более 0.1 | — | 277 | Для изделий из цинка. оцинкованного железа. меди и ее сплавов, луження подтип Н ИЪ-ОБ |
Легко плав кий став | 13 | — | 27 | 50 | 10 | 70 | Для пайки изделий нз легкоплавких металлов сплавов |
При пайке железа мягким припоем применяют в качестве флюсов хлористый цинк ZnCI3 или хлористый аммоний Nh5C1 (нашатырь). Эти флюсы, как все хлориды, ускоряют последующее ржавление и поэтому после пайки поверхность необходимо тщательно промыть. Для пайки меди и латуни часто применяют канифоль, а для пайки легкоплавких сплавов и металлов — стеарин; они хорошо растворяют оксидные пленки. Пайка твердыми припоями дает возможность получить соединение, приближающееся по прочности к сварным, и поэтому широко применяется в производстве. Соединения могут быть внахлестку, встык или в «ус». Наиболее прочное соединение получается при пайке внахлестку. Подготовка кромок состоит в их точной подгонке, в обезжиривании горячей щелочью и в фиксации деталей, чтобы обеспечить заданный зазор. Чем меньше зазор, тем прочнее спай. Наиболее приемлемый и широко применяемый на практике зазор составляет 0,01—0,02 мм. Стальные детали обычно паяют электролитической медью. Кроме меди для пайки различных сталей и особенно сплавов цветных металлов применяют различные припои: медно-цинковые, медно-никелевые, серебряные, палладиевые, марганцевые, марганцово-никелевые, никелевые, германиевые, титановые, алюминиевые. Наиболее широко применяемые припои стандартизованы. Можно применять в качестве припоев латунь Л62 иЛ68, силумины и др. Наиболее известные в практике припои приведены в табл. 83.
Таблица 83
Химический состав, температура плавления и назначение некоторых твердых припоев
Маржа | Химический состав. иг массе | Температура плавления. :С | Примерное назначение | ||||
Си | Zu | As | Si | AI | |||
ПМЦЗб[11] | 34—3S | Опаль ное | — | — | — | S25 | Для панки изделий из латуни с содержанием ыедн не более 63% |
ПМЦ48 | 46-50 | Опаль ное | — | — | — | S65 | Дія панки медных сплавов, содержащих более 6S % мели |
ПСр45** | 30(0.5) | Опаль ное | 45(0.5) | — | — | 720 | То же. нто и ПМЦ4В, но прн более тонких работах, когда требуется высокая лнстоіа места спая |
ПСр72 | 23(0.5) | Опаль ное | 72(0.5) | — | — | 7S0 | Для панки проводников. когда место спая не должно резко уменьшать электропроводность |
AJI2 (силу мин) | — | — | — | 10-13 | S0-S7 | 577 | Для панки алюминиевых изделий |
В качестве флюса при пайке твердыми припоями используют традиционную обезвоженную буру (Na2B207). Широко известны флюсы ПВ200, ПВ201, ПВ209, ПВ284; для пайки алюминия применяется флюс типа 34А на основе щелочных и щелочноземельных металлов.
Методы контроля качества сварных соединений могут быть разделены на две основные группы: методы контроля без разрушения образцов или изделий — неразрушающий контроль; методы контроля с разрушением образцов или производственных стыков …
Надежность эксплуатации сварных соединений зависит от их соответствия нормативно-технической документации, которая регламентирует конструктивные размеры и форму готовых сварных швов, прочность, пластичность, коррозионную стойкость и свойства сварных соединений. Сварные соединения, выполненные …
Для предупреждения пожаров необходимо соблюдать следующие противопожарные мероприятия. Постоянно следить за наличием и исправным состоянием противопожарных средств (огнетушителей, ящиков с сухим песком, лопат, пожарных рукавов, асбестовых покрывал и т. д.). …
Пайка— Повторная публикация в Википедии // WIKI 2
Высокотемпературная пайка; технология соединения металлов заливкой высокотемпературным расплавом
Эта статья о процессе соединения металлов. О технике приготовления см. Тушение.
Пайка
Пайка — это процесс соединения металлов, в котором два или более металлических предмета соединяются вместе путем плавления и протекания присадочного металла в соединение, при этом присадочный металл имеет более низкую температуру плавления, чем прилегающий металл.
Пайка отличается от сварки тем, что она не включает плавление деталей, а от пайки для аналогичного процесса используются более высокие температуры, а также требуются более плотно подогнанные детали, чем при пайке. Присадочный металл капиллярно перетекает в зазор между прилегающими деталями. Присадочный металл нагревается немного выше температуры плавления (ликвидуса), в то время как он защищен подходящей атмосферой, обычно флюсом. Затем он течет по основному металлу (в процессе, известном как смачивание), а затем охлаждается, чтобы соединить детали вместе. [1] Основным преимуществом пайки является способность соединять один и тот же или разные металлы со значительной прочностью.
Энциклопедия YouTube
1/5
Просмотры:261156
166766
44144
11837
462652
✪ Обучение HVAC — Базовая пайка
✪ Базовая кислородно-ацетиленовая пайка
✪ Холодильная пайка и пайка
✪ Процедура пайки — Часть 1
✪ Пайка сломанного чугуна: ремонт самолета Stanley 55
Содержание
Основы
Высококачественные паяные соединения требуют, чтобы детали были плотно подогнаны, а основные металлы были исключительно чистыми и не содержали оксидов.В большинстве случаев для наилучшего капиллярного действия и прочности суставов рекомендуются зазоры в швах от 0,03 до 0,08 мм (от 0,0012 до 0,0031 дюйма). [2] Однако при некоторых операциях пайки нередки зазоры между стыками около 0,6 мм (0,024 дюйма). Чистота паяемых поверхностей также важна, так как любое загрязнение может вызвать плохое смачивание (текучесть). Два основных метода очистки деталей перед пайкой — это химическая очистка и абразивная или механическая очистка. В случае механической очистки важно поддерживать надлежащую шероховатость поверхности, так как смачивание на шероховатой поверхности происходит намного легче, чем на гладкой поверхности той же геометрии. [2]
Еще одним соображением является влияние температуры и времени на качество паяных соединений. При повышении температуры припоя усиливается легирующее и смачивающее действие присадочного металла. Как правило, выбираемая температура пайки должна быть выше точки плавления присадочного металла. Однако на выбор температуры, выбранной конструктором стыка, влияет несколько факторов. Лучшая температура обычно выбирается для:
- Минимально возможная температура пайки
- Свести к минимуму тепловое воздействие на сборку
- Минимизация взаимодействия присадочный металл / основной металл
- Увеличьте срок службы любых используемых приспособлений или приспособлений [2]
В некоторых случаях рабочий может выбрать более высокую температуру, чтобы учесть другие факторы в конструкции (например.g., чтобы можно было использовать другой присадочный металл, или для контроля металлургических эффектов, или для достаточного удаления поверхностного загрязнения). Влияние времени на паяное соединение в первую очередь влияет на степень, в которой эти эффекты присутствуют. В целом, однако, большинство производственных процессов выбираются так, чтобы минимизировать время пайки и связанные с этим затраты. Однако это не всегда так, поскольку в некоторых непроизводственных условиях время и стоимость вторичны по отношению к другим характеристикам соединения (например, прочности, внешнему виду).
Флюс
Если операции пайки не проводятся в инертной среде или среде с восстановительной атмосферой (например, в вакуумной печи), для предотвращения образования оксидов при нагревании металла требуется флюс, например бура. Флюс также служит для очистки любых загрязнений, оставшихся на поверхностях пайки. Флюс можно наносить в любом количестве форм, включая пасту для флюса, жидкость, порошок или готовые паяльные пасты, в которых флюс сочетается с порошком присадочного металла. Флюс также можно наносить с помощью прутков для пайки с покрытием из флюса или сердечника из флюса.В любом случае флюс течет в соединение при нанесении на нагретое соединение и вытесняется расплавленным присадочным металлом, поступающим в соединение. Избыточный флюс следует удалить по завершении цикла, поскольку флюс, оставшийся в стыке, может привести к коррозии, затруднить проверку стыка и предотвратить дальнейшие операции по чистовой обработке поверхности. Фосфорсодержащие припои могут самофлюсоваться при соединении меди с медью. [3] Флюсы обычно выбираются в зависимости от их характеристик на конкретных цветных металлах.Чтобы флюс был эффективным, он должен быть химически совместим как с основным металлом, так и с используемым присадочным металлом. Самофлюсующиеся фосфорные присадочные сплавы образуют хрупкие фосфиды при использовании с железом или никелем. [3] Как правило, при более длительных циклах пайки следует использовать менее активные флюсы, чем при коротких пайках. [4]
Присадочные материалы
В качестве присадочного металла для пайки используются различные сплавы в зависимости от предполагаемого использования или метода нанесения. Как правило, припои состоят из 3 или более металлов для образования сплава с желаемыми свойствами.Присадочный металл для конкретного применения выбирается на основе его способности: смачивать основные металлы, выдерживать требуемые условия эксплуатации и плавиться при более низкой температуре, чем основные металлы, или при очень определенной температуре.
Сплав припоя обычно доступен в виде прутка, ленты, порошка, пасты, крема, проволоки и преформ (таких как штампованные шайбы). [5] В зависимости от области применения, наполнитель может быть предварительно размещен в желаемом месте или нанесен во время цикла нагрева.Для ручной пайки обычно используются проволочные и прутковые формы, поскольку их легче всего наносить при нагревании. В случае пайки в печи сплав обычно наносится заранее, так как процесс обычно сильно автоматизирован. [5] Некоторые из наиболее распространенных типов используемых присадочных металлов:
Атмосфера
Поскольку пайка требует высоких температур, окисление поверхности металла происходит в кислородсодержащей атмосфере. Это может потребовать использования других атмосферных условий, кроме воздуха.Обычно используемые атмосферы: [7] [8]
- Air : Просто и экономично. Многие материалы подвержены окислению и образованию накипи. Для удаления окисления после работы можно использовать кислотную очистительную ванну или механическую очистку. Флюс противодействует окислению, но может ослабить соединение.
- Сгоревший топливный газ (с низким содержанием водорода, AWS тип 1, «экзотермические генерируемые атмосферы»): 87% N 2 , 11–12% CO 2 , 5–1% CO, 5–1% H 2 .Для серебряных, медно-фосфорных и медно-цинковых присадочных металлов. Для пайки меди и латуни.
- Сгоревший топливный газ (обезуглероживание, AWS тип 2, «эндотермические генерируемые атмосферы»): 70–71% N 2 , 5–6% CO 2 , 9–10% CO, 14–15% H 2 . Для медных, серебряных, медно-фосфорных и медно-цинковых присадочных металлов. Для пайки меди, латуни, никелевых сплавов, монеля, среднеуглеродистых сталей.
- Сгоревший топливный газ (осушенный, тип AWS 3, «эндотермические генерируемые атмосферы»): 73–75% N 2 , 10–11% CO, 15–16% H 2 .Для медных, серебряных, медно-фосфорных и медно-цинковых присадочных металлов. Для пайки меди, латуни, сплавов с низким содержанием никеля, монеля, средне- и высокоуглеродистых сталей.
- Сгоревший топливный газ (осушенный, обезуглероживающий, AWS тип 4): 41–45% N 2 , 17–19% CO, 38–40% H 2 . Для медных, серебряных, медно-фосфорных и медно-цинковых присадочных металлов. Для пайки меди, латуни, низко-никелевых сплавов, средне- и высокоуглеродистых сталей.
- Аммиак (AWS тип 5, также называемый формирующим газом ): диссоциированный аммиак (75% водорода, 25% азота) можно использовать для многих типов пайки и отжига.Недорого. Для меди, серебра, никеля, медно-фосфорных и медно-цинковых присадочных металлов. Для пайки меди, латуни, никелевых сплавов, монеля, средне- и высокоуглеродистых сталей и хромовых сплавов.
- Азот + водород , криогенный или очищенный (AWS тип 6A): 70–99% N 2 , 1–30% H 2 . Для меди, серебра, никеля, медно-фосфорных и медно-цинковых присадочных металлов.
- Азот + водород + окись углерода , криогенный или очищенный (AWS тип 6B): 70–99% N 2 , 2–20% H 2 , 1–10% CO.Для меди, серебра, никеля, медно-фосфорных и медно-цинковых присадочных металлов. Для пайки меди, латуни, низко-никелевых сплавов, средне- и высокоуглеродистых сталей.
- Азот , криогенный или очищенный (AWS тип 6C): неокисляющий, экономичный. При высоких температурах может реагировать с некоторыми металлами, например. некоторые стали, образующие нитриды. Для меди, серебра, никеля, медно-фосфорных и медно-цинковых присадочных металлов. Для пайки меди, латуни, сплавов с низким содержанием никеля, монеля, средне- и высокоуглеродистых сталей.
- Водород (AWS тип 7): сильный раскислитель, обладающий высокой теплопроводностью. Может использоваться для пайки меди и отжига стали. Может вызвать водородную хрупкость некоторых сплавов. Для меди, серебра, никеля, медно-фосфорных и медно-цинковых присадочных металлов. Для пайки меди, латуни, никелевых сплавов, монеля, средне- и высокоуглеродистых сталей и хромовых сплавов, кобальтовых сплавов, вольфрамовых сплавов и карбидов.
- Пары неорганические (различные летучие фториды, AWS тип 8): специального назначения.Может смешиваться с атмосферой AWS 1–5 для замены флюса. Используется для пайки серебром латуни.
- Благородный газ (обычно аргон, AWS тип 9): неокисляющий, более дорогой, чем азот. Инертный. Детали должны быть очень чистыми, газ должен быть чистым. Для меди, серебра, никеля, медно-фосфорных и медно-цинковых присадочных металлов. Для пайки меди, латуни, никелевых сплавов, монеля, средне- и высокоуглеродистых сталей, хромовых сплавов, титана, циркония, гафния.
- Благородный газ + водород (AWS тип 9A)
- Вакуум : требуется вакуумирование рабочей камеры.Дорого. Непригоден (или требует особого ухода) для металлов с высоким давлением пара, например серебро, цинк, фосфор, кадмий и марганец. Используется для высококачественных соединений, например аэрокосмические приложения.
Общие методы
![Brazing and soldering processes classification chart[9]](/800/600/https/wiki2.org/wikipedia/commons/thumb/7/77/Brazing_and_soldering_processes_-_AWS_A3.0_2001.svg/im324-393px-Brazing_and_soldering_processes_-_AWS_A3.0_2001.svg.png)
Горелка для пайки
Пайка горелкой — это, безусловно, самый распространенный метод механизированной пайки. Его лучше всего использовать в небольших объемах производства или на специализированных предприятиях, а в некоторых странах на его долю приходится большая часть пайки.Существует три основных используемых типа пайки горелкой: [10] ручная пайка, машинная пайка и автоматическая пайка горелкой.
Пайка с ручной горелкой — это процедура, при которой нагревание осуществляется с помощью газового пламени, помещенного на или рядом с паяемым соединением. Горелку можно держать в руке или удерживать в фиксированном положении в зависимости от того, выполняется ли операция полностью вручную или имеется некоторый уровень автоматизации. Ручная пайка чаще всего используется при небольших объемах производства или в приложениях, где размер или конфигурация детали делает другие методы пайки невозможными. [10] Основным недостатком этого метода является высокая стоимость рабочей силы, а также навыки оператора, необходимые для получения качественных паяных соединений. Для предотвращения окисления требуется использование флюса или самофлюса. Паять медь горелкой можно без использования флюса, если она паяется горелкой с использованием кислорода и газообразного водорода, а не кислорода и других горючих газов.
Пайка с механической горелкой обычно используется там, где выполняется повторяющаяся пайка.Этот метод представляет собой сочетание как автоматизированных, так и ручных операций, при этом оператор часто размещает припой, флюс и детали для отсадки, в то время как механизм машины выполняет фактическую пайку. [10] Преимущество этого метода в том, что он снижает трудозатраты и навыки ручной пайки. Для этого метода также требуется использование флюса, так как нет защитной атмосферы, и он лучше всего подходит для малых и средних объемов производства.
Автоматическая пайка горелкой — это метод, который практически исключает необходимость ручного труда при пайке, за исключением загрузки и разгрузки машины.Основными преимуществами этого метода являются: высокая производительность, равномерное качество пайки и низкие эксплуатационные расходы. Используемое оборудование практически такое же, как и оборудование, используемое для пайки с резаком, с основным отличием в том, что оборудование заменяет оператора при подготовке деталей. [10]
Печь для пайки
Схема печи для пайки
Пайка в печи — это полуавтоматический процесс, широко используемый в промышленных процессах пайки благодаря его приспособляемости к массовому производству и использованию неквалифицированной рабочей силы.Пайка в печи имеет множество преимуществ перед другими методами нагрева, которые делают ее идеальной для массового производства. Одним из основных преимуществ является легкость, с которой он может производить большое количество мелких деталей, которые легко закрепляются или устанавливаются самостоятельно. [11] Этот процесс также предлагает преимущества контролируемого теплового цикла (позволяющего использовать детали, которые могут деформироваться при локальном нагреве) и отсутствие необходимости в очистке после пайки. Обычно используются следующие атмосферы: инертная, восстановительная или вакуумная, каждая из которых защищает деталь от окисления.Некоторые другие преимущества включают: низкую стоимость единицы при использовании в массовом производстве, точный контроль температуры и возможность паять несколько стыков одновременно. Печи обычно нагреваются с помощью электричества, газа или масла в зависимости от типа печи и области применения. Однако некоторые из недостатков этого метода включают в себя высокую стоимость капитального оборудования, более сложные конструктивные особенности и высокое энергопотребление. [11]
Существует четыре основных типа печей, используемых для операций пайки: периодического действия; непрерывный; реторта с контролируемой атмосферой; и вакуум.
Печь периодического действия типа имеет относительно низкие начальные затраты на оборудование и может нагревать каждую частичную загрузку отдельно. Его можно включать и выключать по желанию, что сокращает эксплуатационные расходы, когда он не используется. Эти печи подходят для производства средних и крупных партий и предлагают большую степень гибкости в выборе типов деталей, которые можно паять. [11] Для контроля окисления и чистоты деталей можно использовать либо контролируемую атмосферу, либо флюс.
Печи непрерывного действия лучше всего подходят для постоянного потока деталей аналогичного размера через печь. [11] Эти печи часто питаются конвейером, движущиеся части проходят через горячую зону с контролируемой скоростью. Обычно в печах непрерывного действия используют либо контролируемую атмосферу, либо предварительно нанесенный флюс. В частности, эти печи предлагают очень низкие требования к ручному труду и поэтому лучше всего подходят для крупномасштабных производственных операций.
Ретортные печи отличаются от других печей периодического действия тем, что в них используется герметичная футеровка, называемая «реторта».Реторта обычно закрывается либо прокладкой, либо приваривается и полностью заполняется желаемой атмосферой, а затем нагревается снаружи обычными нагревательными элементами. [11] Из-за высоких температур реторта обычно изготавливается из жаропрочных сплавов, устойчивых к окислению. Ретортные печи часто используются в периодическом или полунепрерывном вариантах.
Вакуумные печи — это относительно экономичный метод предотвращения образования оксидов, который чаще всего используется для пайки материалов с очень стабильными оксидами (алюминий, титан и цирконий), которые нельзя паять в атмосферных печах.Вакуумная пайка также широко используется для огнеупорных материалов и других экзотических комбинаций сплавов, не подходящих для атмосферных печей. Из-за отсутствия флюса или восстановительной атмосферы чистота детали имеет решающее значение при пайке в вакууме. Существуют три основных типа вакуумных печей: реторта с одинарными стенками, реторта с двойными стенками и реторта с холодными стенками. Типичные уровни вакуума для пайки находятся в диапазоне от давлений от 1,3 до 0,13 Па (от 10 −2 до 10 −3 Торр) до 0,00013 Па (10 −6 Торр) или ниже. [11] Вакуумные печи чаще всего бывают периодического действия и подходят для средних и больших объемов производства.
Серебряная пайка
Серебряный припой , иногда известный как твердый припой , представляет собой пайку с использованием наполнителя на основе сплава серебра. Эти серебряные сплавы состоят из серебра и других металлов, таких как медь, цинк и кадмий, с различным процентным содержанием.

Трещина в металлической пластине 90–10 Cu – Ni из-за напряжений при серебряной пайке
Пайка широко используется в инструментальной промышленности для крепления наконечников из твердого металла (карбид, керамика, металлокерамика и т.п.) к таким инструментам, как пильные полотна.Часто проводится «предварительное лужение»: припой расплавляется на твердый металлический наконечник, который помещается рядом со сталью и переплавляется. Предварительное лужение решает проблему трудностей смачивания твердых металлов.
Паяные твердосплавные соединения обычно имеют толщину от двух до семи мил. Припой соединяет материалы и компенсирует разницу в степени их расширения. Он также обеспечивает амортизацию между твердосплавным наконечником и твердой сталью, которая смягчает удары и предотвращает потерю и повреждение наконечника — так же, как подвеска автомобиля помогает предотвратить повреждение шин и транспортного средства.Наконец, припой соединяет два других материала, создавая композитную структуру, так же как слои дерева и клея создают фанеру. Стандарт прочности паяных соединений во многих отраслях промышленности — это соединение, которое прочнее любого основного материала, так что под нагрузкой один или другой основной материал выходит из строя раньше, чем соединение. Серебряная пайка может вызвать дефекты в некоторых сплавах, например. межкристаллитное растрескивание медно-никелевого сплава под действием напряжений.
Один специальный метод серебряной пайки называется пайкой штифтом или пайкой штифтом .Он был разработан специально для подключения кабелей к железнодорожным путям или для установок катодной защиты. В этом методе используется припой, содержащий серебро и флюс, который оплавляется в проушине кабельного наконечника. Оборудование обычно питается от батарей.
Пайка сварочная
Сварка припоем — это использование присадочного стержня из бронзы или латуни, покрытого флюсом, для соединения стальных деталей. Оборудование, необходимое для сварки припоем, в основном идентично оборудованию, используемому при пайке.Поскольку для пайки твердым припоем обычно требуется больше тепла, чем для пайки, обычно используется газообразное топливо ацетилен или метилацетилен-пропадиен (MAP). Название происходит от того, что не используется капиллярное действие.
Сварка пайкой имеет много преимуществ перед сваркой плавлением. Это позволяет соединять разнородные металлы, сводить к минимуму тепловую деформацию и может снизить потребность в обширном предварительном нагреве. Кроме того, поскольку соединенные металлы в процессе не плавятся, компоненты сохраняют свою первоначальную форму; края и контуры не стираются и не изменяются в результате образования галтеля.Еще один эффект сварки припоем — устранение накопленных напряжений, которые часто присутствуют при сварке плавлением. Это крайне важно при ремонте больших отливок. Недостатки — потеря прочности при воздействии высоких температур и неспособность выдерживать высокие нагрузки.
Наконечники из карбида, металлокерамики и керамики покрываются гальваническим покрытием, а затем соединяются со сталью для изготовления ленточных пил с напайками. Покрытие действует как припой.
Чугун «Сварка»
«Сварка» чугуна обычно представляет собой операцию пайки с использованием присадочного прутка, сделанного в основном из никеля, хотя также доступна настоящая сварка чугунными прутками.Труба из чугуна с шаровидным графитом также может быть «сварена вручную» — процесс, при котором соединения соединяются с помощью небольшой медной проволоки, вплавленной в железо при предварительном заземлении до голого металла, параллельно чугунным соединениям, формируемым согласно ступичной трубе с неопреновой прокладкой. морские котики. Цель этой операции — использовать электричество по медной кабине для поддержания тепла в подземных трубах в холодном климате.
Вакуумная пайка
Вакуумная пайка — это метод соединения материалов, который дает значительные преимущества: чрезвычайно чистые, превосходные, не содержащие флюса паяные соединения с высокой целостностью и прочностью.Этот процесс может быть дорогостоящим, потому что он должен выполняться внутри сосуда с вакуумной камерой. При нагреве в вакууме на заготовке поддерживается однородность температуры, что значительно снижает остаточные напряжения из-за медленных циклов нагрева и охлаждения. Это, в свою очередь, может значительно улучшить термические и механические свойства материала, тем самым обеспечивая уникальные возможности термообработки. Одной из таких возможностей является термообработка или упрочнение заготовки при выполнении процесса соединения металлов в одном термическом цикле печи.
Продукты, которые чаще всего паяют под вакуумом, включают алюминиевые холодные пластины, пластинчато-ребристые теплообменники и плоские трубчатые теплообменники. [12]
Вакуумная пайка часто проводится в печи; это означает, что можно выполнить сразу несколько соединений, поскольку вся заготовка достигает температуры пайки. Тепло передается с помощью излучения, так как многие другие методы нельзя использовать в вакууме.
Пайка погружением
Пайка погружением особенно хорошо подходит для пайки алюминия, так как воздух исключен, что предотвращает образование оксидов.Соединяемые детали закрепляются, и на сопрягаемые поверхности наносится припой, обычно в виде суспензии. Затем сборки погружаются в ванну с расплавом соли (обычно NaCl, KCl и другие соединения), которая действует как теплоноситель и флюс. Многие паяные погружением детали используются в системах теплопередачи в аэрокосмической промышленности. [13]
Способы нагрева
Горелком для технического персонала ВМС США паяет стальную трубу
Существует множество методов нагрева для пайки.Наиболее важным фактором при выборе метода нагрева является достижение эффективной передачи тепла по всему соединению и при этом в пределах теплоемкости отдельных используемых основных металлов. Геометрия паяного соединения также является решающим фактором, который необходимо учитывать, как и скорость и объем требуемого производства. Самый простой способ классифицировать методы пайки — сгруппировать их по способу нагрева. Вот некоторые из наиболее распространенных: [1] [14]
- Горелка для пайки
- Печь для пайки
- Индукционная пайка
- Пайка погружением
- Пайка сопротивлением
- Инфракрасная пайка
- Пайка полотна
- Электронно-лучевая и лазерная пайка
- Сварка припоем
Эти методы нагрева подразделяются на методы локализованного и диффузного нагрева и имеют преимущества в зависимости от их различных применений. [15]
Безопасность
Пайка может повлечь за собой воздействие опасных химических паров. Национальный институт безопасности и гигиены труда в США рекомендует контролировать воздействие этих паров до уровней ниже допустимого предела воздействия. [16]
Достоинства и недостатки
Пайка имеет много преимуществ по сравнению с другими методами соединения металлов, такими как сварка. Поскольку пайка не плавит основной металл соединения, она позволяет более строго контролировать допуски и обеспечивает чистое соединение без необходимости вторичной чистовой обработки.Кроме того, можно паять разнородные металлы и неметаллы (например, металлизированная керамика). [17] В общем, пайка также вызывает меньшую тепловую деформацию, чем сварка, из-за равномерного нагрева паяной детали. Сложные и состоящие из нескольких частей узлы можно экономично спаять. Сварные соединения иногда необходимо шлифовать заподлицо, что является дорогостоящей вторичной операцией, при которой пайка не требует, так как она дает чистое соединение. Еще одно преимущество состоит в том, что пайка может быть покрыта или плакирована в защитных целях.Наконец, пайка легко адаптируется к массовому производству и легко автоматизируется, поскольку отдельные параметры процесса менее чувствительны к изменениям. [18] [19]
Одним из основных недостатков является недостаточная прочность соединения по сравнению со сварным соединением из-за использования более мягких присадочных металлов. [1] Прочность паяного соединения, вероятно, будет меньше, чем у основного металла (ов), но больше, чем у присадочного металла. [20] Другим недостатком является то, что паяные соединения могут быть повреждены при высоких рабочих температурах. [1] Паяные соединения требуют высокой степени чистоты основного металла при выполнении в промышленных условиях. В некоторых случаях пайки требуется использование соответствующих флюсов для контроля чистоты. Цвет шва часто отличается от цвета основного металла, что создает эстетический недостаток.
Присадочные материалы
Некоторые припои представлены в виде трилистников , многослойной фольги из несущего металла, плакированной слоем припоя с каждой стороны. Центральный металл часто — медь; его роль заключается в том, чтобы действовать как носитель для сплава, поглощать механические напряжения из-за e.грамм. дифференциальное тепловое расширение разнородных материалов (например, карбидного наконечника и стального держателя) и действовать как диффузионный барьер (например, чтобы остановить диффузию алюминия из алюминиевой бронзы в сталь при пайке этих двух материалов).
Семейства пайки
Паяльные сплавы образуют несколько отдельных групп; Сплавы одной группы имеют схожие свойства и применение. [21]
- нелегированные. Часто благородные металлы — серебро, золото, палладий.
- Серебро-медь.Хорошие плавильные свойства. Серебро усиливает текучесть. Эвтектический сплав, используемый для пайки в печи. Сплавы с высоким содержанием меди, склонные к растрескиванию под действием аммиака.
- Серебро-цинк. Подобно Cu-Zn, используется в ювелирных изделиях из-за высокого содержания серебра, поэтому продукт соответствует требованиям к пробам. Цвет соответствует серебристому, и он устойчив к чистящим средствам, содержащим аммиак.
- Медь-цинк. Общего назначения, применяется для соединения стали и чугуна. Коррозионная стойкость обычно недостаточна для меди, кремнистой бронзы, медно-никелевой меди и нержавеющей стали.Достаточно пластичный. Высокое давление пара из-за летучего цинка, не подходит для пайки в печи. Сплавы с высоким содержанием меди, склонные к растрескиванию под действием аммиака.
- Серебро-медь-цинк. Более низкая температура плавления, чем у Ag-Cu, при таком же содержании Ag. Сочетает в себе преимущества Ag-Cu и Cu-Zn. При содержании цинка выше 40% пластичность и прочность падают, поэтому используются только сплавы этого типа с низким содержанием цинка. При содержании цинка выше 25% появляются менее пластичные медно-цинковые и серебряно-цинковые фазы. Содержание меди выше 60% приводит к снижению прочности и ликвидуса при температуре выше 900 ° C.Содержание серебра выше 85% приводит к снижению прочности, высокой ликвидности и высокой стоимости. Сплавы с высоким содержанием меди, склонные к растрескиванию под действием аммиака. Припои с высоким содержанием серебра (более 67,5% Ag) являются отличительными чертами и используются в ювелирных изделиях; Сплавы с пониженным содержанием серебра используются в инженерных целях. Сплавы с соотношением меди и цинка около 60:40 содержат те же фазы, что и латунь, и соответствуют ее цвету; они используются для соединения латуни. Небольшое количество никеля улучшает прочность и коррозионную стойкость, а также способствует смачиванию карбидов.Добавление марганца вместе с никелем увеличивает вязкость разрушения. Добавление кадмия дает сплавов Ag-Cu-Zn-Cd с улучшенной текучестью и смачиванием и более низкой температурой плавления; однако кадмий токсичен. Добавление олова может играть в основном ту же роль.
- Медь-фосфорная. Широко применяется для меди и медных сплавов. Не требует флюса для меди. Может также использоваться с серебром, вольфрамом и молибденом. Сплавы с высоким содержанием меди, склонные к растрескиванию под действием аммиака.
- Как Cu-P, с улучшенным потоком.Лучше для больших зазоров. Более пластичный, лучшая электропроводность. Сплавы с высоким содержанием меди, склонные к растрескиванию под действием аммиака.
- Золото-серебро. Благородные металлы. Используется в ювелирном деле.
- Золото-медь. Непрерывный ряд твердых растворов. Легко смачивает многие металлы, в том числе тугоплавкие. Узкие диапазоны плавления, хорошая текучесть. [22] Часто используется в ювелирных изделиях. Сплавы с 40–90% золота твердеют при охлаждении, но остаются пластичными. Никель улучшает пластичность.Серебро снижает температуру плавления, но ухудшает коррозионную стойкость. Для поддержания коррозионной стойкости содержание золота должно составлять более 60%. Высокотемпературную прочность и коррозионную стойкость можно улучшить за счет дальнейшего легирования, например, хромом, палладием, марганцем и молибденом. Добавленный ванадий позволяет смачивать керамику. Золото-медь имеет низкое давление пара.
- Золото-никель. Непрерывный ряд твердых растворов. Более широкий диапазон плавления, чем у сплавов Au-Cu, но лучшая коррозионная стойкость и улучшенное смачивание.Часто легируется другими металлами для уменьшения доли золота при сохранении свойств. Медь может быть добавлена для уменьшения доли золота, хром для компенсации потери коррозионной стойкости и бор для улучшения смачивания, нарушенного хромом. Обычно используется не более 35% Ni, поскольку более высокие отношения Ni / Au имеют слишком широкий диапазон плавления. Низкое давление пара.
- Золото-палладий. Повышенная коррозионная стойкость по сравнению с сплавами Au-Cu и Au-Ni. Используется для соединения жаропрочных сплавов и тугоплавких металлов при высоких температурах, например.грамм. реактивные двигатели. Дорого. Может быть заменен припоями на основе кобальта. Низкое давление пара.
- Палладий. Хорошие высокотемпературные характеристики, высокая коррозионная стойкость (меньше золота), высокая прочность (больше золота). обычно легированы никелем, медью или серебром. Образует твердые растворы с большинством металлов, не образует хрупких интерметаллидов. Низкое давление пара.
- Никелевые сплавы, даже более многочисленные, чем сплавы серебра. Высокая сила. Более низкая стоимость, чем у серебряных сплавов.Хорошие высокотемпературные характеристики, хорошая коррозионная стойкость в умеренно агрессивных средах. Часто применяется для нержавеющих сталей и жаропрочных сплавов. Хрупкие серой и некоторыми металлами с более низкой температурой плавления, например цинк. Бор, фосфор, кремний и углерод понижают температуру плавления и быстро диффундируют к основным металлам. Это позволяет выполнять диффузионную пайку и использовать соединение при температуре выше температуры пайки. Бориды и фосфиды образуют хрупкие фазы. Аморфные преформы можно изготавливать путем быстрого затвердевания.
- Кобальтовые сплавы. Хорошая стойкость к высокотемпературной коррозии, возможная альтернатива припоям Au-Pd. Низкая обрабатываемость при низких температурах, преформы, полученные методом быстрого затвердевания.
- Алюминий-кремний. Для пайки алюминия.
- Содержит активные металлы, например титан или ванадий. Используется для пайки неметаллических материалов, например графит или керамика.
Роль элементов
элемент | роль | волатильность | коррозионная стойкость | стоимость | несовместимость | описание |
---|---|---|---|---|---|---|
Статья о пайке по Свободному словарю
Пайка
Метод соединения металлов и других материалов с применением тепла и припоя. Используемые присадочные металлы имеют температуру плавления выше 840 ° F (450 ° C), но ниже температуры плавления соединяемых металлов или материалов. Они текут капиллярно в зазор между основными металлами или материалами и соединяются между собой, создавая между ними металлургическую связь на молекулярном уровне. Процесс похож на пайку, но отличается тем, что присадочный металл более прочен и имеет более высокую температуру плавления.
При правильной конструкции паяное соединение обеспечивает очень высокую степень эксплуатационной надежности при сосредоточенных напряжениях, вибрации и температурных нагрузках. Можно сказать, что при правильно спроектированной пайке любой отказ будет происходить в основном металле, а не в соединении. Следует учитывать множество переменных дизайна. Первым из них является механическая конфигурация соединяемых деталей и сама область соединения. Все пайки можно разделить на две категории: соединение внахлест или стык.Другие являются адаптациями этих двух.
При проектировании следует учитывать обоснованный выбор основного и присадочного металлов. В дополнение к основным механическим требованиям, основные металлы, используемые в пайке, должны сохранять целостность своих физических свойств в течение всего нагрева цикла пайки. Невозможно найти универсальный присадочный металл, удовлетворяющий всем конструктивным требованиям, но доступно множество типов: от чистых металлов, таких как медь, золото или серебро, до сложных сплавов алюминия, золота, никеля, магния, кобальта, серебра и палладия. .
Существует 11 основных процессов пайки. При пайке горелкой тепло передается пламенем от горелки определенного типа непосредственно к основному металлу. Обычно используется минеральный флюс. Паяльный присадочный металл может быть предварительно помещен в соединение или подан в соединение торцевой стороной. При индукционной пайке температура припоя достигается в частях, подлежащих пайке, путем помещения их в источник высокочастотного переменного тока или рядом с ним. Обычно используются флюс и наплавленный металл. При контактной пайке используются электроды, которые расположены так, что соединение образует часть электрической цепи.Тепло вырабатывается сопротивлением деталей прохождению электрического тока. При пайке погружением припой присадочный металл предварительно помещается в стык или в нем, а сборка погружается в ванну с расплавом соли или флюса до достижения температуры пайки. В одном из вариантов этого процесса сборку подвергают предварительному флюсу и погружают в ванну с расплавленным припоем. Инфракрасная пайка — это процесс, при котором кварцевые лампы высокой интенсивности направляются на соединяемые металлы.
Пайка в печи — широко используемый метод, особенно полезный, когда детали, подлежащие пайке, подвергаются механической обработке или формованию до их окончательных размеров или представляют собой сложную сборку, которая уже была слегка соединена или закреплена.Атмосфера в паяльной печи обычно регулируется, что обеспечивает большую гибкость. Важным преимуществом является то, что потенциальное искажение металла, создаваемое нагреванием и охлаждением, можно прогнозировать и контролировать, тем самым минимизируя или устраняя его. Кроме того, в процессе пайки печи упрощается автоматизация.
Диффузионная пайка, в отличие от пайки в печи, определяется не методом нагрева, а степенью взаимного растворения присадочного металла и диффузии с основным металлом в результате используемой температуры и временного интервала нагрева.При диффузионной пайке температура, время, в некоторых случаях давление и выбор основных и присадочных материалов регулируются таким образом, что присадочный металл частично или полностью диффундирует в основной металл. В этом случае свойства соединения очень близки к свойствам основного металла.
Другие, менее используемые процессы включают дуговую пайку, блочную пайку, пайку потоком и двойную углеродную дуговую пайку.
.Страница не найдена «Oerlikon Corporate
\ uf1ad
- Компания
- Профиль компании
- Обзор компании
- Организация
- Факты и цифры
- Сегменты рынка
- Глобальный охват
- Соответствие
- Налоговая стратегия
- Спонсорство
История Портал с поставщиками - Инновации
- Наши компетенции
- Наши рынки
- Исследования и разработки
- Отзывы клиентов
- Качество и сертификаты
- Знаете ли вы
- Круглосуточная поездка
- Круглосуточно по всему миру
000000 9000000 9000 9000 9000 9000 90000009000 9000 - 32 000
- Блог Oerlikon 9 Пресс-релизы
- События и повестка дня
- Медиа-галерея
- Новости
- Подписка RSS-канал новостей
- Контакты
- Информационный бюллетень
- Информационный бюллетень
- Корпоративное управление 9000 Публикации
- Вакансии
- Зачем к нам
- Как к нам присоединиться
- Ваша карьера Найдите то, что вам подходит
- Наши сотрудники
- Контакты
- Головной офис
- Форма запроса
- По всему миру
- Группа
- Корпоративный
Сегмент поверхностных решений
- Бальцерс
- Metco
- Аддитивное производство
Сегмент искусственных волокон
- Бармаг
- Neumag
- Область
- Китай
- Индия
- Россия
- Язык:
Как спаять металл вместе | Паяльный металл
Пайка — это процесс соединения двух независимых металлических частей для образования одного прочного несущего соединения.
- Пайка аналогична пайке, но при более высоких температурах.
- Используйте пруток, подходящий для металла, используемого в вашем проекте.
- Пруток для припоя должен расплавляться за счет тепла соединяемых металлических деталей, а не за счет прямого контакта с пламенем горелки.
- Используйте горелку, излучающую пламя высокой интенсивности.
Рекомендуемые стержни по типу металла
Медь, латунь, бронза:
Медно-фосфорные прутки для пайки и сварки
Сталь, нержавеющая сталь, никелевые сплавы, медные сплавы, чугун, карбид вольфрама:
Прутки для пайки и сварки нейзильбера
Чугун, оцинкованный, никель, сталь, ковкий чугун:
Бронзовые прутки для пайки и сварки
Алюминий:
Bernzomatic AL3 Алюминиевые прутки для пайки и сварки
Ступени
- Используйте проволочную щетку или наждачную бумагу, чтобы потереть поверхность металла.Затем очистите поверхности мыльной водой или обезжиривателем.
- Расположите металл по желанию. В большинстве случаев соединение внахлест прочнее и легче спаивается, чем соединение с зазором. При необходимости используйте зажимы, чтобы закрепить детали на месте.
- Нагрейте стык в месте соприкосновения двух металлических частей, пока стык не станет светиться.
- Приложите пруток к стыку, продолжая нагревать металлические поверхности. Для больших площадей нагрейте участки стыка до температуры, а затем переходите к следующему прилегающему участку.
- После пайки используйте проволочную щетку для очистки паяной поверхности от окисления или остатков.
Советы
- Прочтите наши Общие меры безопасности перед тем, как начать свой проект.
- Прочтите инструкции, прилагаемые к горелке и пайке, прежде чем приступить к проекту.
- Всегда снимайте резак с топливного цилиндра и храните топливо в вертикальном положении после завершения проекта.