Какие бывают припои для пайки. Из чего состоят припои. Для чего применяются разные виды припоев. Как выбрать подходящий припой. Какие флюсы используются при пайке.
Основные виды припоев и их характеристики
Припои являются ключевым материалом, используемым при пайке для соединения металлических деталей. От выбора правильного припоя во многом зависит качество и надежность паяного соединения. Рассмотрим основные виды припоев и их особенности:
Мягкие припои
К мягким относятся легкоплавкие припои с температурой плавления до 450°C. Основу большинства мягких припоев составляют олово и свинец в различных пропорциях. Наиболее распространенные марки:
- ПОС-61 (61% олова, 39% свинца) — универсальный припой для пайки меди, латуни, бронзы.
- ПОС-40 (40% олова, 60% свинца) — более дешевый аналог ПОС-61.
- ПОС-90 (90% олова, 10% свинца) — для пайки деталей, подвергающихся гальванической обработке.
Мягкие припои обеспечивают хорошую смачиваемость и растекаемость, но уступают по прочности твердым припоям.
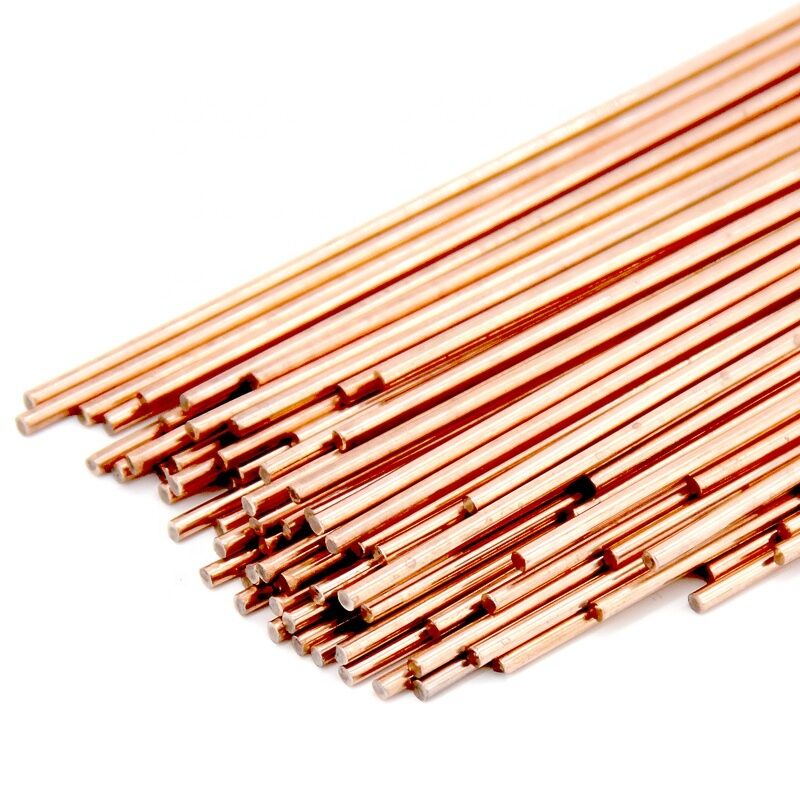
Твердые припои
Твердые припои имеют температуру плавления выше 450°C и обеспечивают более прочное соединение. Основные виды:
- Медно-цинковые (латунные) — для пайки стали, чугуна, меди. Температура плавления 880-950°C.
- Серебряные — высокопрочные припои для ответственных соединений. Содержат 15-90% серебра.
- Медно-фосфорные — для пайки меди и ее сплавов без применения флюса. Температура плавления 710-820°C.
Твердые припои обеспечивают более прочное и коррозионностойкое соединение по сравнению с мягкими.
Состав и свойства основных марок припоев
Выбор припоя зависит от материала соединяемых деталей и требований к паяному соединению. Рассмотрим состав и характеристики наиболее распространенных марок припоев:
Оловянно-свинцовые припои
Марка | Состав | Температура плавления, °C | Применение |
---|---|---|---|
ПОС-61 | 61% Sn, 39% Pb | 190 | Универсальный припой для радиомонтажа |
ПОС-40 | 40% Sn, 60% Pb | 235 | Пайка крупных деталей из меди и ее сплавов |
ПОС-30 | 30% Sn, 70% Pb | 256 | Лужение и пайка стали, чугуна |
Серебряные припои
Марка | Состав | Температура плавления, °C | Применение |
---|---|---|---|
ПСр-45 | 45% Ag, Cu, Zn | 660-730 | Пайка нержавеющих сталей, твердых сплавов |
ПСр-72 | 72% Ag, Cu | 780 | Высокотемпературная пайка ответственных соединений |
Правильный выбор припоя для различных металлов
Для получения качественного паяного соединения важно правильно подобрать припой в зависимости от материала соединяемых деталей:
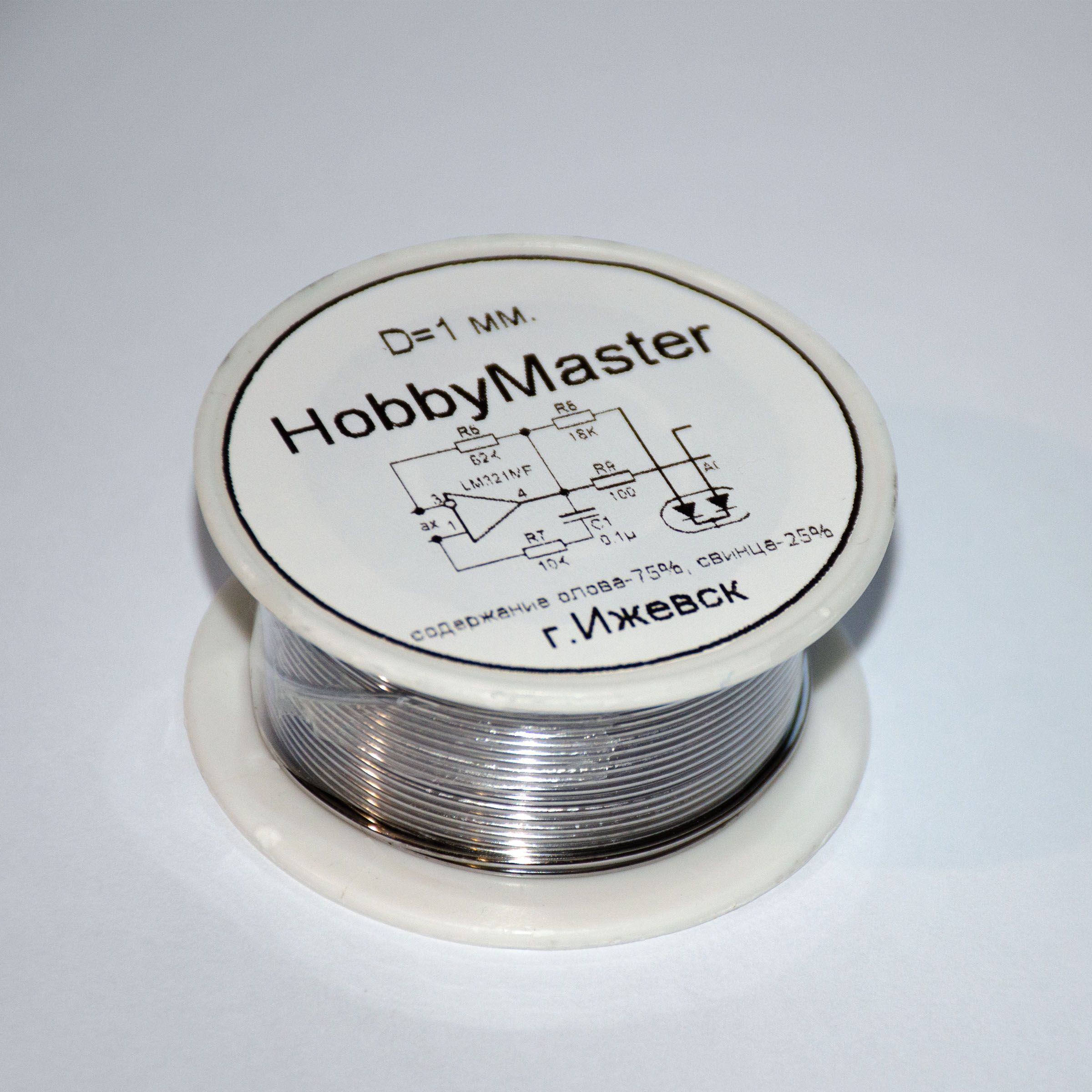
Пайка меди и ее сплавов
Для пайки меди, латуни и бронзы оптимально подходят оловянно-свинцовые припои марок ПОС-61 и ПОС-40. При необходимости повышенной прочности применяют медно-фосфорные припои типа ПМФ-7.
Пайка алюминия и его сплавов
Для пайки алюминия используют специальные алюминиевые припои, например, А34 (34% цинка, 66% алюминия). Температура пайки составляет 380-420°C. Также возможна пайка припоями ПОС с применением специальных флюсов.
Пайка нержавеющей стали
Наилучшие результаты при пайке нержавейки дают серебряные припои с содержанием серебра 25-72%. Они обеспечивают прочное и коррозионностойкое соединение. Температура пайки 700-780°C.
Флюсы для пайки и их назначение
Флюсы играют важную роль в процессе пайки, выполняя следующие функции:
- Очищают поверхности от оксидов
- Защищают от окисления при нагреве
- Улучшают растекание припоя
- Способствуют лучшему смачиванию поверхностей
Основные виды флюсов:
Канифольные флюсы
Состоят из канифоли, растворенной в спирте или другом растворителе. Применяются при пайке меди и ее сплавов. Преимущества — отсутствие коррозионного воздействия.

Кислотные флюсы
Содержат соляную или ортофосфорную кислоту. Обладают высокой активностью, применяются для пайки стали, нержавейки. После пайки требуют тщательного удаления остатков во избежание коррозии.
Безкислотные активированные флюсы
Содержат хлориды цинка и аммония. Занимают промежуточное положение между канифольными и кислотными по активности. Применяются для пайки меди, латуни, оцинкованной стали.
Технология пайки различных металлов
Процесс пайки включает следующие основные этапы:
- Подготовка поверхностей (очистка, обезжиривание)
- Нанесение флюса
- Нагрев места пайки
- Нанесение расплавленного припоя
- Охлаждение
- Очистка от остатков флюса
Рассмотрим особенности пайки некоторых металлов:
Пайка меди и латуни
Медь и латунь хорошо поддаются пайке оловянно-свинцовыми припоями. Важно тщательно зачистить и обезжирить поверхности. В качестве флюса используют канифоль или активированные флюсы. Температура пайки 240-280°C.
Пайка алюминия
Алюминий сложнее поддается пайке из-за оксидной пленки. Применяют специальные алюминиевые припои и активные флюсы на основе хлоридов. Место пайки необходимо тщательно зачистить непосредственно перед нанесением флюса. Температура пайки 380-420°C.

Пайка нержавеющей стали
Для пайки нержавейки используют серебряные или медно-цинковые припои. Необходимо применение активных флюсов. Температура пайки зависит от марки припоя и составляет 700-900°C. После пайки важно тщательно удалить остатки флюса во избежание коррозии.
Современные бессвинцовые припои
В связи с ужесточением экологических требований все большее распространение получают бессвинцовые припои:
- SAC305 (96,5% Sn, 3% Ag, 0,5% Cu) — наиболее распространенный бессвинцовый припой
- SN100C (99,3% Sn, 0,7% Cu, микродобавки Ni и Ge)
- SnBi58 (58% Bi, 42% Sn) — низкотемпературный припой
Основные преимущества бессвинцовых припоев:
- Экологическая безопасность
- Повышенная прочность и надежность соединений
- Лучшая смачиваемость поверхностей
Недостатки — более высокая стоимость и температура плавления по сравнению с оловянно-свинцовыми припоями.
Техника безопасности при пайке
При выполнении паяльных работ необходимо соблюдать следующие правила безопасности:
- Работать в хорошо проветриваемом помещении
- Использовать защитные очки
- Не допускать попадания флюса и припоя на кожу
- Не вдыхать пары флюса и припоя
- Соблюдать осторожность при работе с нагретым паяльником
- Не оставлять включенный паяльник без присмотра
При соблюдении этих простых правил пайка будет безопасным процессом.

Сплав для пайки, 6 (шесть) букв
Большая Советская Энциклопедия Значение слова в словаре Большая Советская Энциклопедия
металл или сплав, вводимый в зазор между соединяемыми деталями или образующийся между ними в результате диффузии в процессе пайки . П. имеет более низкую температуру плавления, чем паяемые материалы. Одной из важнейших характеристик П., от которой зависят…
Новый толково-словообразовательный словарь русского языка, Т. Ф. Ефремова. Значение слова в словаре Новый толково-словообразовательный словарь русского языка, Т. Ф. Ефремова.
Толковый словарь русского языка. С.И.Ожегов, Н.Ю.Шведова. Значение слова в словаре Толковый словарь русского языка. С.И.Ожегов, Н.Ю.Шведова.
-я, м, (спец.). Металл или сплав для заполнения зазоров при пайке. прил. припойный, -ая, -ое.
Энциклопедический словарь, 1998 г. Значение слова в словаре Энциклопедический словарь, 1998 г.
обычно металл или сплав, заполняющий зазор между соединяемыми деталями при пайке. Распространены припои на основе Sn, Pb, Cu, Ag, Ni, Zn. Иногда в качестве припоя используют материалы на основе оксидов и др.
Толковый словарь русского языка. Д.Н. Ушаков Значение слова в словаре Толковый словарь русского языка. Д.Н. Ушаков
припоя, мн. нет, м. (тех.). Металл, сплав для паяния. При паянии посуды в качестве припоя употребляют олово со свинцом.
Основные материалы применяемые для пайки * Алмазное сверление бетона
Удельный вес при температуре 20°С | 7,31 |
Температура плавления | 231,9°С |
Олово — мягкий, ковкий металл серебристо-белого цвета. Хорошо растворяется в концентрированной соляной или серной кислоте. Сероводород на него почти не влияет. Ценным свойством олова является его устойчивость во многих органических кислотах. При комнатной температуре мало поддается окислению, но при воздействии температуры ниже 18°С способен переходить в серую модификацию («оловянная чума»). В местах появления частиц серого олова происходит разрушение металла. Переход белого олова в серое резко ускоряется при понижении температуры до —50°С. Для пайки может применяться как в чистом виде, так и в виде сплавов с другими металлами.
Удельный вес при температуре 20°С | 11,34 |
Температура плавления | 327°С |
Свинец — синевато-серый металл, мягкий, легко поддается обработке, режется ножом. На воздухе окисляется только с поверхности. В щелочах, а также в азотной и органических кислотах растворяется легко. Стоек против воздействий серной кислоты и сернокислых соединений. Применяется для изготовления припоев.
Удельный вес при температуре 20°С | 8,6 |
Температура плавления | 321°С |
Кадмий — серебристо-белый металл, мягкий, пластичный, механически непрочный. Применяется как для антикоррозийных покрытий, так и в сплавах со свинцом, оловом, висмутом для легкоплавких припоев.
Удельный вес при температуре 20°С | 6,68 |
Температура плавления | 630,5°С |
Сурьма — хрупкий серебристо-белый металл. На воздухе не окисляется. Применяется в сплавах со свинцом, оловом, висмутом, кадмием для легкоплавких припоев.
Удельный вес при температуре 20°С | 9,82 |
Температура плавления | 271°С |
Висмут — хрупкий серебристо-серый металл. Растворяется в азотной и горячей серной кислотах. Применяется в сплавах с оловом, свинцом, кадмием для получения легкоплавких припоев.
Удельный вес при температуре 20°С | 7,1 |
Температура плавления | 419°С |
Цинк — синевато-серый металл. В холодном состоянии хрупок. В сухом воздухе окисляется, во влажном воздухе покрывается пленкой окиси, которая предохраняет его от разрушения. В соединении с медью дает ряд прочных сплавов. Легко растворяется в слабых кислотах. Применяется для изготовления твердых припоев и кислотных флюсов.
Удельный вес при температуре 20°С | 8,6 — 8,9 |
Температура плавления | 1083°С |
Медь — красноватый металл, тягучий и мягкий. Растворяется в серной и азотной кислотах и в аммиаке. В сухом воздухе почти не поддается окислению, в сыром воздухе покрывается окисью зеленого цвета. Применяется для изготовления тугоплавких припоев и сплавов.
Припой | Удельный вес при температуре 20°С | Температура плавления |
---|---|---|
Олово | 7,31 | 231,9°С |
Висмут | 9,82 | 271°С |
Кадмий | 8,6 | 321°С |
Свинец | 11,34 | 327°С |
Цинк | 7,1 | 419°С |
Сурьма | 6,68 | 630,5°С |
Медь | 8,6 — 8,9 | 1083°С |
Температура размягчения | от 55°C до 83°С |
Канифоль —продукт переработки смолы хвойных деревьев Более светлые сорта канифоли (более тщательно очищенные) считаются лучшими. Применяется как флюс для пайки мягкими припоями.
Выбор припоя зависит от соединяемых металлов или сплавов, от способа пайки, температурных ограничений, размеров деталей, требуемой механической прочности, коррозионной стойкости и др. Наиболее широко применяются в любительской практике легкоплавкие припои. Рекомендации по их применению, на основании которых можно выбрать припой, приведены в таблице 1. Буквы ПОС в марке припоя означают припой оловянно-свинцовый, цифры — содержание олова в процентах (ПОС-61, ПОС-40). Для получения специальных свойств в состав оловянно-свинцовых припоев вводят сурьму, кадмий, висмут и другие металлы. Состав некоторых таких припоев приведён в таблице 2.
Легкоплавкие припои
Таблица 1. Легкоплавкие припои.
Марка припоя | Темпе- ратура | Область применения |
---|---|---|
Сплав Вуда | 60 °С | Пайка, когда требуется особо низкая температура плавления припоя. |
Cплав д’Арсенваля | 79 °С | Пайка, когда требуется особо низкая температура плавления припоя. |
Сплав «Розе» | 92-95 °С | Пайка, когда требуется особо низкая температура плавления припоя. |
ПОСВ-33 | 130 °С | Пайка плавких предохранителей. |
ПОСК-50 | 145 °С | Пайка деталей из меди и её сплавов, не допускающих местного перегрева. Пайка полупроводниковых приборов. |
ПОСК-47-17 | 180 °С | Пайка проводов и выводов элементов к слою серебра, нанесённого на керамику методом вжигания. |
ПОС-61 | 190 °C | Лужение и пайка тонких спиральных пружин в измерительных приборах и других ответственных деталей из стали, меди, латуни, бронзы, когда не допустим или нежелателен высокий нагрев в зоне пайки. Пайка тонких (диаметром 0,05 — 0,08 мм) обмоточных проводов, в том числе высоко — частотных (лицендрата), выводов обмоток, радиоэлементов и микросхем, монтажных проводов в полихлорвиниловой изоляции, а также пайка в тех случаях, когда требуется повышенная механическая прочность и электропроводность. |
П-200 | 200 °С | Пайка тонкостенных деталей из алюминия и его сплавов. |
ПОС-90 | 222 °C | Пайка деталей и узлов, подвергающихся в дальнейшем гальванической обработке (серебрение, золочение) |
ПОС-50 | 222 °C | То же, но когда допускается более высокий нагрев, чем при ПОС-61 |
ПОС-40 | 235 °С | Лужение и пайка токопроводящих деталей неответственного назначения, наконечников, соединение проводов с лепестками, когда допускается более высокий нагрев, чем при ПОС-50 или ПОС-61. |
ПОС-30 | 256 °С | Лужение и пайка механических деталей не ответственного назначения из меди и её сплавов, стали и железа. |
ПОССу-4-6 | 265 °С | Лужение и пайка деталей из меди и железа погружением в ванну с расплавленным припоем. |
ПОС-18 | 277 °С | Лужение и пайка при пониженных требованиях к прочности шва, деталей не ответственного назначения из меди и её сплавов, оцинкованного железа. |
П-250 | 280 °С | Пайка тонкостенных деталей из алюминия и его сплавов. |
Выпускают легкоплавкие припои в виде литых чушек, прутков, проволоки, лент фольги, порошков, трубок диаметром от 1 до 5 мм, заполненных канифолью, а также в виде паст, составленных из порошка припоя и жидкого флюса.
Флюсы растворяют и удаляют оксиды и загрязнения с поверхности паяемого соединения. Кроме того, во время пайки они защищают от окисления поверхность нагреваемого металла и расплавленный припой. Всё это способствует увеличению растекаемости припоя, а следовательно, улучшению качества пайки. Флюс выбирают в зависимости от свойств соединяемых пайкой металлов или сплавов и применяемого припоя, а также от способа пайки. Остатки флюса, особенно активного, т продукты его разложения нужно удалять сразу после пайки, так как они загрязняют места соединений и являются очагами коррозии. При монтаже электро и радиоаппаратуры наиболее широко применяются канифоль и флюсы, приготовленные на её основе с добавлением неактивных веществ — спирта, глицерина и даже скипидара. Канифоль не гигроскопична, является хорошим диэлектриком, поэтому не удаленный остаток её не представляет опасности для паяного соединения. Данные о флюсах, наиболее часто применяемых в любительской практике, приведены в таблице 2 и таблице 3.
Неактивные флюсы
Таблица 2. Неактивные (безкислотные) флюсы.
Состав в % | Область применения | Способ удаления остатков |
---|---|---|
Канифоль светлая | Пайка меди, латуни, бронзы легкоплавкими припоями. | Промывка кистью или тампоном, смоченным в спирте или ацетоне. |
Канифоль — 15-18; спирт этиловый — остальное (флюс спиртоканифольный) | То же, и пайка в труднодоступных местах | Тоже |
Канифоль — 6; глицерин -14; спирт этиловый или денатурированный — остальное (флюс глицерино-конифольный) | То же, при повышенных требованиях к герметичности паяного соединения. | То же |
Активные флюсы
Таблица 3. Активные (кислотные) флюсы.
Состав % | Область применения | Способ удаления остатков |
---|---|---|
Хлористый цинк — 25-30; концентрированная соляная кислота — 06-07; остальное вода | Пайка деталей из чёрных и цветных металлов. | Тщательная промывка водой. |
Хлористый цинк (насыщенный раствор) 3,7: вазелин технический 85; вода дистиллированная -остальное (флюс паста) | То же, когда по роду работы удобнее пользоваться пастой. | Тщательная промывка водой. |
Хлористый цинк — 1,4; глицерин — 3; спирт этиловый -40; остальное вода дистиллированная. | Пайка никеля, платины и её сплавов. | Тщательная промывка водой. |
Канифоль — 24; хлористый цинк — 1; остальное этиловый спирт. | Пайка цветных и драгоценных металлов (в том числе золото), ответственных деталей из чёрных металлов. | Промывка ацетоном. |
Канифоль — 16; хлористый цинк — 4; вазелин технический — 80; (флюс паста) | То же, для получения соединений повышенной прочности, но только деталей простой конфигурации, не затрудняющей промывки. | Тщательная промывка водой. |
Пайка сталей с гальваническим покрытием
Пайка сталей с гальваническим покрытием цинком или кадмием возможна оловяно-свинцовами припоями паяльником с применением флюса хлористого цинка. Пайка с канифольными флюсами не даёт качественного соединения.
Пайка алюминия припоями ПОС
Пайка алюминия припоями ПОС затруднительна, но всё же возможна, если оловянно-свинцовый припой содержит не менее 50% олова (ПОС-50, ПОС-61, ПОС-90). В качестве флюса применяют минеральное масло. Лучшие результаты получаются при использовании щелочного масла (для очистки оружия после стрельбы). Удовлетворительное качество пайки обеспечивает минеральное масло для швейных машин и точных механизмов. На место пайки наносят флюс и поверхность алюминия под слоем масла зачищают скребком или лезвием ножа, чтобы удалить имеющуюся всегда на поверхности алюминия оксидную плёнку. Паяют хорошо нагретым паяльником. Для пайки тонкого алюминия достаточна мощность паяльника 50 Вт, для алюминия толщиной 1 мм и более желательна мощность 90 Вт. При пайке алюминия толщиной более 2 мм место пайки нужно предварительно прогреть паяльником и только после этого наносить флюс.
Пайка алюминия припоями
П-200 и П-250Коррозийная стойкость паяльных швов, выполненных этими припоями, несколько ниже, чем выполненных оловяно-свинцовыми припоями. Флюс представляет собой смесь олеиновой кислоты йодида лития. Йодид лития (2-3 г) помещают в пробирку или колбу и добавляют 20 мл (около 20 г) олеиновой кислоты. В состав флюса может входить от 5 до 17% йодида лития. Смесь слегка прогревают, опустив пробирку в горячую воду, и перемешивают до полного растворения соли. Готовый флюс сливают в чистую стеклянную посуду и охлаждают. Если используется водная соль лития, то при её растворении на дно пробирки опускается слой водной смеси, а флюс всплывает и его осторожно сливают. Перед пайкой жало хорошо прогретого паяльника (температура жала должна быть около 270 — 350 °C) зачищают и лудят припоем, пользуясь чистой канифолью. Соединяемые поверхности деталей смачивают флюсом, лудят и паяют. После охлаждения остатки флюса удаляют тампоном из ткани, смоченным в спирте, ацетоне или бензине, и покрывают шов защитным лаком. Флюс в процессе пайки не выделяет токсичных и обладающих резким запахом веществ. С ткани и кожи рук он легко смывается водой с мылом.
Пайка нихрома
Пайка нихрома (нихром с нихромом, нихром с медью и её сплавами, нихром со сталью) может быть осуществлена припоем ПОС-61, ПОС-50 (хуже — ПОС-40) с применением флюса следующего состава в граммах: Вазелин — 100, хлористый цинк в порошке — 7, глицерин — 5. Флюс приготовляют в фарфоровой ступке, в которую кладут вазелин, а затем добавляют, хорошо перемешивая до получения однородной массы, последовательно хлористый цинк т глицерин. Соединяемые поверхности тщательно зачищают шлифовальной шкуркой и протирают ваткой, смоченной в 10%-ном спиртовом растворе хлористой меди, наносят флюс, лудят и только после этого паяют.
При пайке в домашних условиях припой обычно набирают и наносят паяльником. Контролировать количество расплавленного припоя, переносимое паяльником, крайне затруднительно: оно зависит от температуры плавления припоя, температуры и чистоты жала и от других факторов. Не исключено при этом попадание капель расплавленного припоя на проводники, корпуса элементов, изоляцию, что приводит иногда к нежелательным последствиям. Приходится работать крайне осторожно и аккуратно, и всё же бывает трудно добиться хорошего качества пайки. Облегчить пайку и улучшить её можно с помощью паяльной пасты. Для приготовления пасты измельчают припой напильником с крупной насечкой (мелкая забивается припоем) и смешивают опилки со спирто-канифольным флюсом. Количество припоя в пасте подбирают опытным путём. Если паста получилась слишком густой, в неё добавляют спирт. Хранить пасту нужно в плотно закрывающейся посуде. На место пайки пасту наносят нужными дозами металлической лопаточкой. Применение паяльной пасты, кроме того, позволяет избежать перегрева малогабаритных деталей и полупроводниковых приборов.
«Паяльная лента» незаменима при сращивании проводников, трубок, стержней, когда нет возможности воспользоваться электрическим паяльником. Чтобы изготовить «паяльную ленту», необходимо сначала приготовить пасту из опилок припоя, канифоли и вазелина. Пасту наносят тонким ровным слоем на миткалевую ленту. Место пайки обматывают в один слой «паяльной лентой», смачивают бензином или керосином и поджигают. Предварительно соединяемые поверхности желательно залудить.
Лужение проводов в эмалевой изоляции.
При зачистке выводных концов обмоточного провода ЛЭШО, ПЭЛШО, ПЭЛ и ПЭВ при помощи наждачной бумаги или лезвия нередки надрезы и обрывы тонких жил провода. Зачистка путём обжига также не всегда даёт удовлетворительные результаты из-за возможного оплавления проводов малого сечения. Кроме того, в месте обжига провод теряет прочность и легко обрывается. Для зачистки проводов малого сечения в эмалевой изоляции можно использовать полихлорвиниловую трубку. Отрезок трубки кладут на дощечку и, прижимая провод к трубке плоскостью жала хорошо разогретого паяльника, лёгким усилием 2 — 3 раза протягивают провод. При этом одновременно происходит разрушение эмалевого покрытия и лужение провода. Применение канифоли при этом необязательно. Вместо полихлорвиниловой трубки можно воспользоваться обрезками монтажного провода или кабеля в плихлорвиниловой изоляции. Провод в эмалевой изоляции любого диаметра можно лудить с помощью аспирино-канифольной пасты. Аспирин и канифоль нужно растолочь в порошок и смешать (в массовом соотношении 2:1). Полученную смесь развести этиловым спиртом до пастообразного состояния. Конец провода погружают в пасту и жалом горячего паяльника с небольшим усилием проводят по проводу или перемещают провод под жалом. При этом эмаль разрушается и провод лудится. Для удаления остатков ацетилсалециловой кислоты (аспирина) провод ещё раз лудят, используя чистую канифоль.
Вместо припоя — клей.
Часто приходится припаивать провод к детали из металла, трудно поддающегося пайке: нержавеющей стали, хрома, никеля, сплавов алюминия и др. Деталь в месте присоединения провода тщательно очищают от грязи и оксидов и обезжиривают. Луженый конец провода обмакивают в клей БФ-2 и жалом нагретого паяльника прижимают к месту соединения в течении 5 — 6 секунд. После остывания на место контакта наносят 1 — 2 капли эпоксидного клея и сушат до полного затвердевания.
Сварка вместо пайки.
Электросварка значительно сокращает время, затрачиваемое на монтажные работы, даёт соединения, выдерживающие высокотемпературный нагрев, не требует припоев, флюсов, предварительного лужения, позволяет соединять проводники из металлов и сплавов, трудно поддающихся пайке, например провода электронагревательных приборов. Для сварки необходимо иметь источник постоянного или переменного тока напряжением 6 — 30 вольт, обеспечивающий ток не менее 1 ампер. Электродом для сварки служит графитовый стержень от использованных батарей КБС или других, заточенный под угол 30° — 40°. В качестве держателя электрода можно использовать щуп от ампервольтметра с наконечником «крокодил». В местах будущей сварки предварительно зачищенные проводники скручивают жгутом и соединяют с одним из полюсов источника тока, разогревают место, подлежащее сварке. Расплавленный металл образует соединение каплевидной формы. По мере выгорания графита в процессе работы электрод следует затачивать. С приобретением навыков сварка получается чистой, без окалины. Работать необходимо в светозащитных очках.
Как паять алюминий.
Покрываете место пайки тонким слоем канифоли и сразу же натираете таблеткой анальгина. Далее облуживаете поверхность припоем ПОС-50, прижимая к ней с небольшим усилием жало сильно нагретого паяльника. Ацетоном смываете остатки флюса. Снова осторожно прогреваете поверхность и смываете флюс. Теперь можете начать пайку обычным образом.
Чтобы жало паяльника не подгорало.
Чтобы защитить стержень от обгорания, его нужно обмазать тонким слоем смеси силикатного клея и сухой минеральной краски (окись железа, цинка и магния). Перед включением паяльника покрытие нужно хорошо просушить, иначе клей вспенится и покрытие будет осыпаться.
Как зачистить проводники печатной платы.
Кроме уже известных способов зачистки проводников печатной платы перед пайкой или лужением, хорошо себя зарекомендовал способ, описанный ниже. На ватный тампон наносят несколько капель технической соляной кислоты и протирают им поверхность фольги. Кислота хорошо удаляет слой окиси меди, практически не затрагивая металл. После этого плату надо промыть под проточной водой, сначала в горячей, а потом в холодной. Отверстия под выводы деталей лучше просверлить после этой обработки. При работе с кислотой необходимо соблюдать меры безопасности.
Качество паяного соединения не зависит от количества припоя и флюса, скорее наоборот: излишки припоя могут скрыть дефекты соединения, а обилие флюса приводит к загрязнению места пайки. Хорошее паяное соединение характеризуется такими признаками: паяная поверхность должна быть светлой блестящей или светло-матовой, без тёмных пятен и посторонних включений, форма паяных соединений должна иметь вогнутые галтели припоя (без избытка припоя). Через припой должны проявляться контуры входящих в соединение выводов элементов и проводников.
«Паяльную кислоту» (хлористый цинк) получают путём растворения металлического цинка в концентрированной соляной кислоте из расчёта 412 г/л. Кислоту осторожно вливают в посуду с кусочками цинка, причём уровень не должен превышать 3/4 глубины посуды. При окончательном растворении цинка прекращается выделение пузырьков водорода. Полученному раствору хлористого цинка дают отстояться до прозрачности и оккуратно сливают в пузырёк.
Вместо «паяльной кислоты» можно использовать флюс, приготовленный из равных по массе долей хлористого амония и глицерина. При этом место пайки не окисляется. Флюс пригоден и для пайки нержавеющей стали.
Вместо флюса при лужении стальных деталей (в том числе из нержавеющих сталей) перед пайкой можно воспользоваться отрезком полихлорвиниловой трубки. Место пайки зачищают и обезжиривают. Жалом хорошо прогретого паяльника с каплей припоя растирают на месте пайки отрезок этой трубки до получения равномерного слоя полуды. Затем ведут пайку как обычно.
Заржавевшие детали из чёрных металлов перед пайкой следует опустить на 10 — 12 ч в хлористый цинк, разведённый наполовину дистиллированной водой.
Ацетоно-канифольный флюс не уступает по качеству пайки спирто-канифольному. Он хорошо смачивает поверхность и легко затекает в зазор между паяемыми деталями. Поэтому при отсутствии спирта можно приготовить флюс и на ацетоне, взяв его в таком же соотношении, которое указано в таблице 3. Однако необходимо помнить, что ацетон токсичен и обладает резким неприятным запахом, поэтому работать с таким флюсом можно только при хорошей вентиляции помещения.Хранить жидкий и полужидкий флюс (спирто-канифольный, «паяльную кислоту» и др) удобно в полиэтиленовой маслёнке, хоботок которой закрывается специальной пробкой. С помощью такой маслёнки можно легко и быстро наносить требуемое количество флюса на место пайки. При этом флюс расходуется экономно, уменьшается испарение его растворителя, пайка получается более чистой и аккуратной.
Припаять обойму шарикоподшипника к фланцу можно с помощью припоя ПОС-61 и флюса следующего состава: спирт этиловый — 5 г, триэтаноломин — 2 г. Перед пайкой детали следует обезжирить, после пайки — промыть узел в бензине и подшипник смазать.
Для сращивания проводов из сплавов с высоким сопротивлением (нихром, константан, манганин и др.) можно использовать простой способ, не требующий какого-либо специального инструмента. Провода в месте соединения зачищают и скручивают. Затем пропускают высокий ток, чтобы место соединения накалилось докрасна. На это место пинцетом кладут кусочек ляписа, который при нагревании расплавляется, в результате чего образуется хороший электрический контакт.
Тонкие медные провода можно сваривать в пламени спиртовки или спички. Для этого их зачищают на 20 мм, складывают, аккуратно скручивают, и нагревают до тех пор, пока не образуется шарик расплавленного металла, дающий надёжный контакт.
Лудить алюминий легче, если его предварительно покрыть медью. Нужное место зачищают и аккуратно наносят на него две-три капли насыщенного раствора медного купороса. Далее к алюминиевой детали подключают отрицательный полюс источника постоянного тока, а к положительному полюсу присоединяют кусок медного провода, конец которого опускают в каплю купороса, так чтобы провод не касался алюминия. Через некоторое время на поверхности детали осядет слой красной меди, который после промывки и сушки лудят обычным способом. В качестве источника тока можно использовать батарейку от карманного фонаря.
Обнавлено:
Серебряные припои / ГОСТы / Завод припоев Новосибирск, олово, припой, припои, свинец, сплав, сплавы, цинк, баббиты
Припои на основе серебра – оптимальное решение для создания прочного, надежного и обладающего хорошей электропроводностью шва. В чистом виде благородный металл использовать для пайки невозможно. Он слишком пластичен и имеет очень высокую температуру плавления. Поэтому в припои добавляют другие металлы, чаще всего медь или цинк. Благодаря добавкам температура плавления понижается, а, следовательно, уменьшается расход энергии и времени на пайку.
Среди достоинств серебряных припоев следует выделить отличные прочностные качества получаемых швов, устойчивость к окислению, механическим и вибрационным воздействиям.
Количество марок серебряных припоев настолько велико, что подобрать состав можно практически для любых задач по пайке различных металлов.
Содержание серебра в припое
Количество серебра в припое регламентируется требованиями ГОСТ. В маркировке продукции присутствует цифровое обозначение, указывающее на процент благородного металла в сплаве. Припои с большим содержанием серебра (50-70%) применяют для создания швов с большой электропроводностью, сплавы с меньшим количеством серебра рекомендуются для соединения деталей, которые не подвергаются значительному нагреву при эксплуатации. Сплавы с низким содержанием Ag наиболее востребованы в машиностроении для создания швов высокой твердости. Радиолюбители в основном пользуются славами с пониженным содержанием серебра (всего около 2%).
Бюджетные марки серебряных припоев
Припой ПСр-10 содержит всего 10% серебра. Такой припой применяют для создания твердых швов, выдерживающих температуру до 800 градусов. В качестве спаиваемых материалов могут выступать сталь и сплавы цветных металлов, в том числе латунь с высоким содержанием меди.
Припои с содержанием серебра 12% применяют для спайки латуни (с содержанием меди до 58%) и меди.
Продукция с содержанием серебра 25% позволяет получить чистый шов, однако, с не самыми высокими прочностными качествами.
Припои со средним количеством серебра
Серебряный припой, содержащий 40% серебра, позволяет получить прочный и пластичный шов. Чаще всего такой состав применяют для соединения подвижных деталей, поскольку шов может подвергаться деформации после застывания, не теряя целостности.
Припой ПСр-45 рекомендован для спайки стыков значительной толщины (до 3 мм). Швы получаются прочными, устойчивыми к ударным и вибрационным нагрузкам, не трескаются и не окисляются
Припои с большим процентным содержанием серебра
Припой, содержащий 65% благородного металла, используют для соединения пильных полотен. Сплав с содержанием серебра 70% часто используют для пайки узлов в электронике. Благодаря высокой электропроводности металла такой припой не нарушает проводимость проводов при пайке.
В ювелирном деле нашли применение припои с содержанием серебра 70-80%.
Выбор флюса для пайки
Чтобы шов получился максимально чистым и прочным, перед пайкой поверхность обрабатывают флюсами. Назначение флюса:
- очистка поверхности;
- уменьшение окисления состава;
- снижение поверхностного напряжения металла;
- увеличение прочности соединения.
ГОСТ 19738-74
Постановлением Государственного комитета стандартов Совета Министров СССР от 26.04.74 №1015 дата введения установлена 01.01.75
Ограничение срока действия снято Постановлением Госстандарта от 31.01.85 №241
1. Настоящий стандарт распространяется на серебряные припои общего назначения и устанавливает марки припоев.
Коды ОКП марок серебряных припоев приведены в приложении 3. (Измененная редакция, Изм. №1).
2. Марки и химический состав серебряных припоев должны соответствовать указанным в таблице.
3. Примерное назначение серебряных припоев указано в приложении 1
4. Данные по температурам плавления, плотности и удельном электрическому сопротивлению серебряных припоев приведены в приложении 2.
Марка припоя | Химический состав, % | |||||||||||||
Серебро | Медь | Цинк | Олово | Марганец | Сурьма | Фосфор | Кадмий | Никель | Свинец | Примеси не более | ||||
Железа | Сумма определяемых примесей | |||||||||||||
ПСр 72 | 72+0,5 | Остальное | — | — | — | — | — | — | — | — | 0,005 | 0,10 | 0,005 | 0,10 |
ПСр 71 | 71+0,5 | Остальное | — | — | — | — | 1,0+0,2 | — | — | — | 0,005 | 0,15 | 0,005 | 0,15 |
ПСр 70 | 70+0,5 | 26,0+0,5 | Остальное | — | — | — | — | — | — | — | 0,050 | 0,10 | 0,005 | 0,15 |
ПСрМО 68-27-5 | 68+0,5 | Остальное | — | 5,0+0,5 | — | — | — | — | — | — | 0,005 | 0,15 | 0,005 | 0,15 |
ПСр 65 | 65+0,5 | 20,0+0,5 | Остальное | — | — | — | — | — | — | — | 0,100 | 0,10 | 0,005 | 0,15 |
ПСр 62 | 62+0,5 | 28,0+1,0 | — | Остальное | — | — | — | — | — | — | 0,005 | 0,15 | 0,005 | 0,15 |
ПСр 50 | 50,0+0,5 | Остальное | — | — | — | — | — | — | — | — | 0,005 | 0,15 | 0,005 | 0,15 |
ПСр 50 Кд | 50,0+0,5 | 16,0+1,0 | 16,0+1,0 | — | — | — | — | Остальное | — | — | 0,100 | 0,10 | 0,005 | 0,15 |
ПСрКдМ 50-34-16 | 50,0+0,5 | Остальное | — | — | — | — | — | 31,0+1,0 | — | — | 0,05 | 0,15 | 0,005 | 0,15 |
ПСр 45 | 45,0+0,5 | 30,0+0,5 | Остальное | — | — | — | — | — | — | — | 0,050 | 0,10 | 0,005 | 0,15 |
ПСрМЦКд 45-15-16-24 | 45+0,5 | Остальное | 16,0+1,0 | — | — | — | — | 24,0+1,0 | — | — | 0,150 | 0,15 | 0,005 | 0,15 |
ПСр 40 | 40,0+1,0 | 16,7+0,7 | 17,0+0,8 | — | — | — | — | Остальное | 0,3+0,2 | — | 0,050 | 0,10 | 0,005 | 0,15 |
ПСр 37,5 | 37,5+0,3 | Остальное | 5,5+0,5 | — | 8,2+0,3 | — | — |
— | — | — | 0,050 | 0,10 | 0,005 | 0,15 |
ПСр 25 | 25,0+0,3 | 40,0+1,0 | Остальное | — | — | — | — | — | — | — | 0,050 | 0,10 | 0,005 | 0,15 |
ПСр 25Ф | 25,+0,3 | Остальное | — | — | — | — | 5,0+0,5 | — | — | — | 0,010 | 0,15 | 0,010 | 0,15 |
ПСр 15 | 15,0+0,5 | Остальное | — | — | — | — | 4,8+0,3 | — | — | — | 0,100 | 0,05 | 0,010 | 0,15 |
ПСр 12М | 12,0+0,3 | 52,0+1,0 | Остальное | — | — | — | — | — | — | — | 0,050 | 0,10 | 0,05 | 0,15 |
ПСр 10 | 10,0+0,3 | 53,0+1,0 | Остальное | — | — | — | — | — | — | — | 0,050 | 0,10 | 0,05 | 0,15 |
ПСрО 10-90 | 10,0+0,5 | — | — | Остальное | — | — | — | — | — | — | 0,200 | 0,15 | 0,010 | 0,30 |
ПСрОСу 8 (ВПр-6) | 8,0+0,5 | — | — | Остальное | — | 7,5+0,5 | — | — | — | — | 0,200 | 0,20 | 0,015 | 0,40 |
ПСрМО 5(ВПр-9) | 5,0+0,5 | 2,0+0,5 | — | То же | — | 1,0+0,2 | — | — | — | — | 0,200 | 0,20 | 0,015 | 0,40 |
ПСрОС 3,5-95 | 3,5+0,4 | — | — | « | — | — | — | — | — | 1,0+0,3 | — | 0,15 | 0,010 | 0,15 |
ПСр 3 | 3,0+0,3 | — | — | — | — | — | — | — | — | Остальное | — | 0,15 | 0,010 | 0,15 |
ПСрО 3-97 | 3,0+0,3 | — | — | Остальное | — | — | — | — | — | — | 0,200 | 0,15 | 0,010 | 0,30 |
ПСрОС 3-58 | 3,0+0,4 | — | — | 57,8+1,0 | — | 0,5+0,3 | — | — | — | Остальное | — | 0,15 | 0,010 | 0,15 |
ПСр 3Кд | 3,0+0,5 | — | 1,0+0,5 | — | — | — | — | Остальное | — | — | 0,200 | 0,10 | 0,010 | 0,30 |
ПСр 2,5 | 2,5+0,3 | — | — | 5,5+0,5 | — | — | — | — | — | Остальное | — | 0,15 | 0,010 | 0,15 |
ПСр 2,5С | 2,5+0,2 | — | — | — | — | — | — | — | — | То же | — | 0,15 | 0,010 | 0,15 |
ПСр 2 | 2,0+0,3 | — | — | 30,0+1,0 | — | — | — | 5,0+0,5 | — | « | — | 0,15 | 0,010 | 0,15 |
ПСрОС 2-58 | 2+0,3 | — | — | 58,8+1,0 | — | 0,5+0,3 | — | — | — | « | — | 0,15 | 0,010 | 0,15 |
ПСр 1,5 | 1,5+0,3 | — | — | 15,0+1,0 | — | — | — | — | — | « | — | 0,15 | 0,010 | 0,15 |
ПСр 1 | 1,0+0,2 | — | — | 35,0+1,0 | — | 0,9+0,4 | — | 2,5+0,5 | — | « | — | 0,15 | 0,010 | 0,15 |
Примечания:
1. В обозначении марок припоев буквы означают: П — припой, Ср – серебро, Кд – кадмий, Ц – цинк, Су – сурьма, М – медь, Ф – фосфор, О – олово, С – свинец. Цифра после буквы означает содержание серебра в процентах.
2. Содержание цинка в сплавах ПСр 72 и ПСр 50 должно быть не более 0,007%.
Приложение 1
Рекомендуемое
Марка припоя | Область применения |
ПСр 72; ПСр 71; ПСр 62; ПСр 50Кд; ПСр 50; ПСр 40; ПСр 37,5; ПСр 25; ПСр 15; ПСр 10; ПСр 2,5 | Лужение и пайка меди, медно-никелевых сплавов, никеля, ковара, нейзильберта, латуней и бронз. |
ПСр 72 | Пайка железониклевого сплава с посеребренными деталями из стали. |
ПСр 72; ПСр 62; ПСр 40; ПСр 25; ПСр 12М | Пайка стали с медью, никелем, медными и медно-никелевыми сплавами. |
ПСр 72; ПСр 62 | Пайка меди с никелированным вольфрамом. |
Пайка титана и титановых сплавов с нержавеющей сталью | |
ПСр 37,5 | Пайка меди и медных сплавов с жаропрочными сплавами и нержавеющими сталями. |
ПСр 40 | Пайка меди и латуни с коваром, никелем, с нержавеющими сталями и жаропрочными сплавами, пайка свинцово-оловянистых бронз. |
ПСрО 10-90; ПСрОСу 8; ПСрМО 5; ПСрОС 3,5-95; ПСрО 3-97; ПСрОС 3-58; ПСрОС 2-58; ПСр2; ПСр 1,5. | Пайка и лужение меди, никеля, медных и медно-никлевых сплавов с посеребренной керамикой, пайка посеребренных деталей. |
ПСр 3; ПСр 2; ПСр 1,5 | Пайка меди и никеля со стеклоэмалью и керамикой. |
ПСр 72; ПСр 70; ПСр 65; ПСр 45; ПСр 25; ПСр 15; ПСр 2 | Пайка и лужение ювелирных изделий. |
ПСр 71; ПСр 25Ф; ПСр 15 | Самофлюсующийся припой для пайки меди с бронзой, меи с медью, бронзы с бронзой. |
ПСр 3Кд | Пайка меди, медных сплавов и сталей по свеженанесенному медному гальваническому покрытию не менее 10 мкм. |
ПСрМо 68-27-5; ПСрКдМ 50-34-16; ПСрМЦКд 45-15-16-24; ПСр 3; ПСр 2,5 | Пайка и лужение цветных металлов и сталей. |
ПСр 1 | Пайка и лужение серебряных деталей |
Приложение 2
Справочное
Данные по температуре плавления, плотности и удельному электрическому сопротивлению серебряных припоев
Марка припоя | Плотность кг/м3 | Температура плавления, К(оС) | Удельное электрическое сопротивление 10-3 Ом м | |
Верхняя критическая точка | Нижняя критическая точка | |||
ПСр 72 | 10000 | 1052 (779) | 1052 (779) | 2,1 |
ПСр71 | 9800 | 1068 (795) | 918 (654) | 4,3 |
ПСр70 | 9800 | 1043 (770) | 988 (715) | 4,1 |
ПСрМО 68-27-5 | 9900 | 1038 (765) | 928 (655) | 14,0 |
ПСр 65 | 9450 | 995 (722) | 968 (695) | 8,6 |
ПСр 62 | 9600 | 996 (723) | 923 (650) | 25,5 |
ПСр 50 | 9300 | 1133 (860) | 1052 (779) | 2,5 |
ПСр 50 Кд | 9250 | 913 (640) | 898 (625) | 7,8 |
ПСрМЦКд 45-15-16-24 | 9400 | 888 (615) | 888 (615) | 6,5 |
ПСрКдМ 50-34-16 | 9600 | 958 (685) | 903 (630) | 5,8 |
ПСр 45 | 9100 | 1003 (730) | 938 (665) | 10,0 |
ПСр 40 | 9250 | 883 (610) | 863 (590) | 7,0 |
ПСр 37,5 | 8900 | 1083 (810) | 998 (725) | 37,2 |
ПСр 25 | 8700 | 1048 (775) | 1013 (740) | 7,7 |
ПСр 25Ф | 8300 | 998 (725) | 918 (645) | 18,6 |
ПСр 15 | 8500 | 1083 (810) | 913 (640) | 20,7 |
ПСр 12М | 8300 | 1103 (830) | 1066 (793) | 7,4 |
ПСр 10 | 8400 | 1123 (850) | 1095 (822) | 7,1 |
ПСрО 10-90 | 7600 | 553 (280) | 494 (221) | 12,9 |
ПСрОСу 8 (ВПР-6) | 7400 | 523 (250) | 508 (235) | 19,7 |
ПСрМО 5(ВПР-9) | 7400 | 513 (240) | 488 (215) | 15,3 |
ПСрОС 3,5-95 | 7400 | 497 (224) | 493 (220) | 12,3 |
ПСр 3 | 11400 | 588 (315) | 577 (304) | 20,4 |
ПСр 3-97 | 7400 | 498 (225) | 494 (221) | 12,5 |
ПСрОС 3-58 | 8600 | 463 (190) | 453 (180) | 14,5 |
ПСр 3Кд | 8700 | 615 (342) | 587 (314) | 8,0 |
ПСр 2,5 | 11000 | 573 (300) | 568 (295) | 21,4 |
ПСр 2,5С | 11300 | 579 (306) | 577 (304) | 20,7 |
ПСр 2 | 9500 | 511 (238) | 508 (235) | 16,7 |
ПСрОС 2-58 | 8500 | 456 (183) | 456 (183) | 14,1 |
ПСр 1,5 | 10400 | 553 (280) | 546 (273) | 19,1 |
ПСр 1 | 9400 | 508 (235) | 498 (225) | 26,0 |
Приложение 3
Справочное
Марка припоя | Код ОКП | Марка припоя | Код ОКП |
ПСр 72 | 17 5232 0006 | ПСр 12М | 17 5232 0004 |
ПСр 71 | 17 5232 0007 | ПСр 10 | 17 5232 0005 |
ПСр 70 | 17 5232 0001 | ПСрО 10-90 | 17 5232 0020 |
ПСрМО 68-27-5 | 17 5232 0008 | ПСрОСу 8 (ВПР-6) | 17 5232 0021 |
ПСр 65 | 17 5232 0002 | ПСрМО 5(ВПР-9) | 17 5232 0022 |
ПСр 62 | 17 5232 0010 | ПСрОС 3,5-95 | 17 5232 0023 |
ПСр 50 | 17 5232 0011 | ПСр 3 |
|
ПСр 50 Кд | 17 5232 0012 | ПСр 3-97 | 17 5232 0024 |
ПСрКдМ 50-34-16 | 17 5232 0013 | ПСрОС 3-58 | 17 5232 0025 |
ПСр 45 | 17 5232 0014 | ПСр 3Кд | 17 5232 0009 |
ПСрМЦКд 45-15-16-24 | 17 5232 0015 | ПСр 2,5 | 17 5232 0026 |
ПСр 40 | 17 5232 0016 | ПСр 2,5С | 17 5232 0027 |
ПСр 37,5 | 17 5232 0017 | ПСр 2 | 17 5232 0028 |
ПСр 25 | 17 5232 0003 | ПСрОС 2-58 | 17 5232 0029 |
ПСр 25Ф | 175232 0018 | ПСр 1,5 | 17 5232 0030 |
ПСр 15 | 17 5232 0019 | ПСр 1 | 17 5232 0031 |
Как называется сплав олова со свинцом (4 буквы)?
Возможно, это припой. Используется при пайке изделий в условиях повышенной влажности или неустойчивой температуры.
Ингас- есть такой город в Аргентине.
Также ингас или галинстан является торговой маркой справа.
В этот справ входит:
- галий — 68,5%
- индий — 21,5%
- олово — 10%.
Справ малотоксичен.
Температура плавления -19 градусов Цельсия.
Французское золото ещё называют орайде. Это имитирующий драгоценные металлы бронзовый сплав.
Он состоит из 58,3 % красной меди, 16,7 % олова и 25 % цинка.
По внешнему виду оно и правда похоже на золото, имеет такой же цвет, а также блеск золота.
Используют его в основном на выделку художественных, галантерейный изделий. Правда встречаются и ювелирные изделия, которые изготовлены именно из него.
Со временем эти изделия теряют свой блеск, но зато пока они новые, то прямо радуют глаз, да и цена на них обычно дешевле.
Припой – это сплав нескольких металлов, используемый для соединения металлических деталей методом пайки.
Поскольку для проведения пайки припой необходимо расплавить, температура его плавления должна быть ниже, чем температура плавления соединяемых деталей (иначе они будут повреждены).
Температура плавления припоя зависит от его состава, от того, какие металлы в него входят и в каком количестве.
Sn60 Pb40 имеет температуру плавления 183-190 º C.
Sn63 Pb37 плавится при 183º C.
Sn62 Pb 36 Ag2 плавится при 179 º C.
Sn96.5 Ag3 Cu0.5 плавится при 217-220 º C.
Sn96.5 Ag3.5 плавится при 221 º C.
Sn99.3 Cu0.7 плавится при 227 º C.
Sn – обозначает олово, Pb – свинец, Ag – серебро, Cu — медь.
Цифры показывают процентное содержание металла в припое.
Сплав Вуда- тяжелый, легкоплавкий сплав.Олово-12.5%,свинец 25%,висмут 50%,кадмий 12.5%.Применяется в прецизионном литье,в датчиках пожарной безопасности и т.д.
Урок 13. сплавы металлов — Химия — 11 класс
Химия, 11 класс
Урок № 13. Сплавы металлов
Перечень вопросов, рассматриваемых в теме: урок посвящён изучению сплавов чёрных и цветных металлов, роли легирующих добавок, зависимости свойств сплавов от состава.
Глоссарий
Бронза – сплав на основе меди; оловянная бронза содержит до 8,5% олова. Может содержать также алюминий, кремний, свинец. Используется для изготовления деталей машин, инструментов, при ударе не образующих искр.
Баббиты – сплавы на основе олова и свинца. Применяются для изготовления подшипников, так как отличаются высокой устойчивостью к истиранию.
Дюралюминий – высокопрочные сплавы на основе алюминия с добавками меди, магния и марганца. Основной конструкционный материал в авиа- и ракетостроении.
Константан – сплав на основе меди, никеля и марганца, используется для изготовления электроизмерительных приборов.
Латунь – сплав меди и цинка, с небольшими добавками никеля, олова, свинца, марганца. Используется для изготовления деталей машин и запорной аппаратуры.
Легированная сталь – сталь, в состав которой включены легирующие добавки, повышающие прочность, коррозионную устойчивость, жаропрочность и другие свойства сплава.
Легирующие добавки – вещества, вводимые в сплав в определённых количествах, для придания сплаву необходимых свойств.
Мельхиор – медно-никелевый сплав с добавлением железа, используется для изготовления монет, инструментов, столовых приборов.
Нейзильбер – трёхкомпонентный сплав на основе меди, цинка и никеля.
Силумин – сплав алюминия с кремнием. Применяется для литья деталей в авто- моторостроении.
Сплав — материал с металлическими свойствами, состоящий из двух или более компонентов, один из которых обязательно металл.
Сплав Вуда – легкоплавкий сплав на основе висмута, свинца, олова и кадмия. Используется для изготовления металлических моделей, заливки образцов, пайки некоторых сплавов.
Сталь – сплав железа с углеродом, причем доля углерода не превышает 2,14%.
Цветные металлы – алюминий, медь, никель, цинк, олово, свинец и другие металлы, не относящиеся к чёрным.
Цементит – карбид железа Fe3C, образуется в виде отдельной фазы в чугуне с высоким содержанием углерода.
Чёрные металлы – железо, марганец, иногда к чёрным металлам относят хром.
Чугун – сплав железа с углеродом, содержание углерода в пределах от 2,14 до 4,3%.
Электрон – сплав на основе магния и алюминия с добавлением цинка, и марганца. Используется в авиа- и ракетостроении.
Основная литература: Рудзитис, Г. Е., Фельдман, Ф. Г. Химия. 10 класс. Базовый уровень; учебник/ Г. Е. Рудзитис, Ф. Г, Фельдман – М.: Просвещение, 2018. – 224 с.
Дополнительная литература:
1. Рябов, М.А. Сборник задач, упражнений и тестов по химии. К учебникам Г.Е. Рудзитис, Ф.Г. Фельдман «Химия. 10 класс» и «Химия. 11 класс»: учебное пособие / М.А. Рябов. – М.: Экзамен. – 2013. – 256 с.
2. Рудзитис, Г.Е. Химия. 10 класс: учебное пособие для общеобразовательных организаций. Углублённый уровень / Г.Е. Рудзитис, Ф.Г. Фельдман. – М.: Просвещение. – 2018. – 352 с.
Открытые электронные ресурсы:
- Единое окно доступа к информационным ресурсам [Электронный ресурс]. М. 2005 – 2018. URL: http://window.edu.ru/ (дата обращения: 01.06.2018).
ТЕОРЕТИЧЕСКИЙ МАТЕРИАЛ ДЛЯ САМОСТОЯТЕЛЬНОГО ИЗУЧЕНИЯ
Сплавы металлов и их классификация
Одним из первых металлов, который человек стал применять для своих нужд, была медь. Но ещё в III тысячелетии люди обнаружили, что медь, сплавленная с оловом, позволяет делать более прочное оружие, долговечную посуду. Материал, полученный при сплавлении меди с оловом, получил название «бронза». Это был первый сплав, изготовленный человеком.
Сплавом называют искусственный материал с металлическими свойствами, состоящий из двух или более компонентов, из которых, по крайней мере, один является металлом.
В зависимости от количества компонентов различают двойные (бинарные), тройные и многокомпонентные сплавы. Сплавы могут иметь однородную структуру (гомогенные сплавы), а также состоять из нескольких фаз (гетерогенные сплавы). В зависимости от своих свойств сплавы подразделяются на легкоплавкие, тугоплавкие, жаропрочные, высокопрочные, твердые, коррозионно-устойчивые. По предполагаемой технологии обработки различают литейные (изделия производят путём литья) и деформируемые (обрабатывают путём ковки, проката, штамповки, прессования) сплавы.
Чёрные металлы и сплавы на их основе
В зависимости от природы металла, составляющего основу сплава, различают чёрные и цветные сплавы. В чёрных сплавах основным металлом является железо. Самыми распространенными из чёрных сплавов являются сталь и чугун. К чёрным металлам относятся железо, а также марганец и хром, которые входят в состав чёрных сплавов.
Чугун
Чугун – сплав на основе железа, содержание углерода в котором превышает точку предельной растворимости углерода в расплаве железа (2,14%). При остывании сплава, углерод кристаллизуется в виде отдельных включений цементита и графита. Углерод придает чугуну твердость, но снижает пластичность сплава, поэтому чугун хрупкий. Чугун применяют для изготовления литых деталей (коленчатых валов, колёс, труб, радиаторов отопления, ванн, решеток ограждения), кухонной посуды (сковородок, чугунков, казанов).
Сталь
В стали содержание углерода значительно меньше. В низкоуглеродистых сталях количество углерода не превышает 0,25%, в высокоуглеродистой стали содержание углерода может достигать 2%. Самые первые стальные изделия появились 4000 лет назад. В настоящее время выплавляют стальные сплавы с различными свойствами. Это конструкционные, нержавеющие, инструментальные, жаропрочные стали.
Легирующие добавки
Для придания стали особых свойств в процессе её изготовления, вводят легирующие добавки. Легирующими добавками называют вещества, которые добавляют в сплав в определенном количестве для изменения механических и физических свойств материала.
Легированные стали
В зависимости от количества легирующих добавок различают низколегированную, среднелегированную и высоколегированную сталь. Марка стали обозначается с помощью букв и цифр. Буква указывает на химическую природу легирующей добавки, а цифра, стоящая после буквы – на примерное содержание этой добавки в сплаве. Если содержание добавки меньше 1%, то цифру не ставят. Цифры впереди букв показывают содержание углерода в сотых долях процента. Например, в стали марки 18ХГТ содержится 0,18 % С, 1 % Сr, 1 % Мn, около 0,1 % Тi.
Стали применяют для изготовления армирующих железнодорожных рельсов, дробильных установок, конструкций, турбин электростанций и двигателей самолётов, инструментов (пилы, сверла, резцы, зубила, фрезы), химической аппаратуры, деталей автомобилей, тракторов, дорожных машин, труб и много другого.
Цветные металлы и сплавы на их основе
К цветным металлам относят алюминий, цинк, медь, никель, олово, свинец и др. Сплавы на основе цветных металлов называют цветными. Это бронза, латунь, силумин, дюралюминий, баббиты и многие другие. В авиации широкое применение нашли легкие и прочные сплавы на основе алюминия и титана. Изделия из медных сплавов: бронзы и латуни, применяются в химической промышленности, для изготовления запорной аппаратуры: кранов, вентилей. Сплавы на основе олова и свинца используют для изготовления подшипников. Из мельхиора и нейзильбера – сплавов меди и никеля, изготовляют столовые наборы, монеты.
ПРИМЕРЫ И РАЗБОР РЕШЕНИЙ ЗАДАЧ ТРЕНИРОВОЧНОГО МОДУЛЯ
1. Расчет массовой доли металла в сплаве
Условие задачи: Кусочек нейзильбера массой 2,00 г поместили в раствор гидроксида натрия. В ходе реакции выделилось 0,14 л водорода (н.у.). Вычислите массовую долю цинка в сплаве. Ответ запишите в процентах с точностью до десятых долей.
Шаг первый: запишем уравнение реакции цинка с раствором гидроксида натрия:
Zn + 2NaOH → Na2ZnO2 + H2↑.
Один моль цинка вытесняет из щёлочи один моль водорода.
Шаг второй: найдём количество цинка, которое вытеснило 0,14 л водорода.
Для этого найдём в периодической таблице элементов Д.И. Менделеева молярную массу цинка: М(Zn) = 65 г/моль. При нормальных условиях 1 моль любого газа занимает объём, равный 22,4 л. Составим пропорцию:
65 г цинка вытесняет 22,4 л водорода;
х г цинка вытесняет 0,14 л водорода.
65 : х = 22,4 : 0,14, откуда х = (65·0,14) : 22,4 = 0,41 (г) – масса цинка в сплаве.
Шаг третий: найдём массовую долю цинка в сплаве:
ω = (0,41 : 2,00)*100 = 20,5 (%).
Ответ: 20,5
2. Расчёт массы легирующей добавки
Условие задачи: Для придания стали противокоррозионных свойств в сплав добавляют хром. Сталь марки С1 должна содержать 12% хрома, 1% кремния, 1,5% марганца и 0,2% углерода. Сколько хрома необходимо добавить к железному лому (посторонними примесями пренебрегаем) массой 500 кг, чтобы получить нержавеющую сталь требуемой марки? Ответ записать в килограммах с точностью до десятых долей.
Шаг первый: найдём массовую долю железа в стали марки С1:
Для этого от 100% отнимем массовые доли остальных элементов:
100 – 12 – 1 – 1,5 – 0,2 = 85,3 (%).
Шаг второй: найдём массу одного процента сплава.
Для этого массу железного лома разделим на массовую долю железа:
500 : 85,3 = 5,9 (кг).
Шаг третий: найдём необходимую массу хрома. Для этого массу одного процента сплава умножим на массовую долю хрома в сплаве:
5,9*12 = 70,8 (кг).
Ответ: 70,8
Металл Стоматология-Стоматологические Сплавы Нержавеющие
Сплавы в стоматологии ортопедической
Металл в стоматологии занимает центральное место среди материалов. Из стоматологических сплавов отливают (или штампуют) большинство несъёмных протезов, каркасы съемных протезов. Сплавы в стоматологии используют как вспомогательные материалы, для пайки и штамповки. Из них делают стоматологические инструменты.
План статьи:
- Классификация металлов и сплавов в стоматологии
- Конструкционные сплавы металлов в ортопедической стоматологии
- Благородные сплавы металлов в стоматологии
- Неблагородные сплавы в ортопедической стоматологии
- Вспомогательные сплавы металлов в стоматологии
Металлы и сплавы в стоматологии Классификация
Все металлы и сплавы делят на черные и цветные.
Черные металлы – это железо и сплавы на его основе. Стали и чугун. Чугун содержит более 2,14% углерода. В стоматологии не применяется.
Поверхность у чугуна матовая и неблестящая. Он плохо поддается полировке.Сталь в стоматологии
сплав на основе железа, содержащий менее 2,14% углерода. Кроме железа и углерода в стали присутствуют и другие металлы. Они придают сплаву новые свойства (легированная сталь), в том числе делают её нержавеющей.
Стальные колпачки для штамповки коронокЛегированная сталь – сплав железа и углерода, с добавлением любых других металлов. Они меняют свойства сплава (температуру плавления, твердость, пластичность, ковкость и т.д.).
Легированная стальНержавеющая сталь – сталь устойчивая к коррозии. В качестве антикарозионного агента чаще всего применяют хром (21%), а также другие металлы.
Цветные металлы — это соответственно все остальные металлы.
Металлы в ортопедической стоматологии делят на благородные и не благородные.
Благородные металлы (или драгоценные металлы) – металлы устойчивые к коррозии и химически инертные. Основные благородные металлы – это золото, серебро, и металлы платиновой группы (платина, палладий, иридий, осмий и др.).
Неблагородные металлы – металлы, легко подвергающиеся коррозии, и не встречающиеся в природе в чистом виде. Их всегда добывают из руд.
В зависимости от плотности
металлы применяемые в стоматологии бывают легкие и тяжелые.
В этом вопросе нет единой точки зрения. Наиболее общий критерий – плотность металла больше плотности железа (8г/см³) или атомный вес больше 50 а.е.м. Если хотя бы одно условие выполняется – металл тяжелый.
Для экологии и медицины тяжелые металлы — это металлы, которые обладают высокой токсичностью и экологической значимостью. Что создает ещё большую путаницу. Например золото с плотностью 19,32 г/см³ и атомным весом 197 а.е.м. не относят к тяжелым металлам, из-за его инертности и отличной биосовместимости.
Стоматологические сплавы металлов классификация
По назначению сплавы металлов в ортопедической стоматологии делят на:
- А. Конструкционные – из них делают зубные протезы.
- Б. Сплавы для пломбирования – амальгамы.
- В. Сплавы, для изготовления стоматологических инструментов.
- Г. Вспомогательные. Металлы, применяемые для других целей (Например, легкоплавкие металлы для штамповки или припои).
По химическому составу сплавы применяемые в стоматологии бывают:
- Сплавы благородных металлов
- Сплавы неблагородных металлов
Благородные металлы в стоматологии и сплавы
Благородные металлы в стоматологии стоят дорого. Но, несмотря на это, их продолжают применять из-за отличной биосовместимости. Они не подвержены коррозии, не реагируют со слюной, не вызывают аллергию и интоксикацию.
Золотой сплав часто может стать единственным вариантом для пациентов с полиэтиологической контактной аллергией.
Благородные сплавы долговечны. Единственный их недостаток (кроме цены) – это мягкость и подверженность истиранию.
Сплавы золота в стоматологии.
- Сплав золота 900-й пробы. ( ЗлСрМ-900-40).
СОСТАВ: 90% золота, 4% серебра, 6% меди.
СВОЙСТВА: температура плавления 1063°С.
Сплав отличается пластичностью, легко поддается механической обработке под давлением (штамповке, вальцеванию, ковке).
Из-за низкой твердости сплав легко стирается. Поэтому, при изготовлении штампованных коронок изнутри, на жевательную поверхность или режущий край, заливают припой.
Выпускают: в виде дисков диаметром 18, 20, 23, 25мм и блоков по 5г.
Применение: для штампованных коронок и мостовидных протезов из
сплава благородных металлов в ортопедической стоматологии
- Сплав золота 750-й пробы (ЗлСрПлМ-750-80)
Состоит из Золота – 75%, Серебра и меди по 8%, и платины – 9%
Платина придает этому сплаву упругость и уменьшает усадку при литье.
Применяют для изготовления литых золотых частей бюгельных протезов, кламмеров и вкладок
- Сплав золота стоматологический 750-й пробы (ЗлСрКдМ)
В состав добавлен кадмий – 5-12%.
За счет кадмия снижается температура плавления сплава до 800 С. (Средняя температура плавления золотых сплавов 950-1050 С.) Что позволяет применять этот сплав в качестве припоя.
Серебряно палладиевый сплав в стоматологии
Серебряно-палладиевые сплавы отличаются большей Т.пл = 1100-1200 С. Их физико-механические свойства похожи на золотые сплавы. Но устойчивость к коррозии ниже. (Серебро темнеет при контакте с соединениями серы) Сплавы пластичные и ковкие. Паяются золотым припоем (ЗлСрКдМ).
СОСТАВ: 75,1% серебра, 24,5% палладия, немного легирующих металлов (цинк, медь, золото).
Применяют для штампованных коронок. Выпускают соответственно в виде дисков различного диаметра (18, 20, 23, 25 мм) и толщиной 0,3 мм.
Состав: 78% серебра, 18,5% палладия, другие металлы.
Применяют как сплав для литья в стоматологии.Уменьшено кол-во палладия до 14,5%, увеличено серебра.
Применяют для вкладок.
Неблагородные сплавы металлов применяемые в ортопедической стоматологии
Для уменьшения стоимости протезов разрабатывались сплавы, на основе более дешевых металлов, чтобы заменить дорогое золото.
В СССР наиболее широко использовалась дешевая нержавеющая сталь.
Сегодня основную массу ранка занимают кобальто-хромовые и никель-хромовые сплавы.
Сплав нержавеющий стоматологический-сталь стоматологическая
Сталь – самый распространенный сплав в мире. Его свойства отлично известны. А за счет легирующих агентов ей можно придать какие угодно свойства.
Сталь стоматологическая очень дешевая.
Из недостатков: сталь тяжелая (плотность около 8 г/см3) и химически активная. Может вызвать аллергию, гальванозы.
Нержавеющая сталь в стоматологии ортопедической — марки:
- СТАЛЬ МАРКИ 1X18H9Т (ЭЯ-1)
Стоматологический сплав для коронок
СОСТАВ:1,1% углерода; 9% никеля ;18% хрома; 2% марганца, 0,35% титана, 1,0% кремния, остальное — железо.
Применяют для несъемных протезов: индивидуальных коронок, литых зубов, фасеток.
- СТАЛЬ МАРКИ 20Х18Н9Т
СОСТАВ: 0,20% углерода, 9% никеля, 18%хрома, 2,0% марганца, 1,0% титана, 1,0% кремния, остальное — железо.
Из этого типа стали в заводских условиях изготавливают:
- стандартные гильзы, идущие на производство штампованных коронок;
- заготовки кламмеров (для ЧСПП)
- эластичные металлические матрицы для пломбирования, а также сепарационные полоски
- СТАЛЬ для стоматологии МАРКИ 25Х18Н102С
СОСТАВ: 0,25% углерода, 10,0% никеля, 18,0% хрома, 2,0% марганца, 1,8% кремния, остальное — железо.
ПРИМЕНЕНИЕ: в заводских условиях изготавливают:
- зубы (боковые верхние и нижние) для штампованнопаяных мостовидных протезов;
- каркасы для метало-пластмассовых мостовидных протезов, для облицовки;
- проволоку ортодонтическую диаметром от 0,6 до 2,0 мм (шаг 0,2мм)
.
В качестве припоя для неблагородных сплавов используется серебряный припой ПСР-37 или припой Цетрина.
Содержит серебро-37%, медь – 50%, Марганец – 8-9%, Цинк – 5-6%
Температура плавления – 725-810 С
Кобальт хромовый сплав в стоматологии
(кобальто-хромовый сплав, хромокобальтовый сплав)
СОСТАВ:
- кобальт 66-67%, основа сплава, твердый, прочный и лёгкий металл.
- хром 26-30%, вводимый в основном(как и в стали) для повышения устойчивости коррозии.
- никель 3-5%, повышает пластичность, ковкость, вязкость сплава, улучшает технологические свойства сплава.
- молибден 4-5,5%,повышает прочность сплава.
- марганец 0,5%, увеличивающий прочность, качество литья, понижающий температуру плавления, способствующий удалению токсических соединений серы из сплава.
- углерод 0,2%, снижает температуру плавления и улучшает жидкотекучесть сплава.
- кремний 0,5%, улучшает качество отливок, повышает жидкотекучесть сплава.
- железо 0,5%, повышает жидкотекучесть, улучшает качество литья.
СВОЙСТВА КХС-сплава стоматологического:
Отличается хорошими физико-механическими свойствами, малой плотностью (и соответственно весом реставраций) и отличной жидкотекучестью, позволяющей отливать ажурные изделия высокой прочности.
Температура плавления составляет 1458 С
Сплав устойчив к истиранию и долго сохраняет зеркальный блеск.
Кобальтохромовый сплав в стоматологии
Используется в для литых коронок, мостовидных протезов, цельнолитых бюгельных протезов, каркасов металлокерамических протезов, съемных протезов с литыми базисами, шинирующих аппаратов, литых кламмеров.
Металлокерамика состав металла в стоматологииЦеллит-К – кобальто-хромовый
сплав входящий в состав металла
металлокерамики в стоматологии.
Никель хромовые сплавы в стоматологии
Сплавы, в которых основной элемент Ni. Элементы этого сплава кроме никеля — Сг (не менее 20%), Со и молибден (Мо) (4%).
По свойствам сплав никеля близок к сплаву кобальта.
Применяется: для литья несъемных протезов и каркасов съемных протезов.
Сегодня ограничено применение сплавов никеля из-за их высокой аллергенности.
Сплавы титана в стоматологии ортопедическойВ стоматологии применяют как чистый титан (99,5%), так и его сплавы.
Чистый титанДля литья и фрезерования применяют сплавы титана, алюминия и ванадия (90-6-4% соответственно). И сплав титана с алюминием и ниобием (87-6-7%).
Сплавы титана лёгкие и удивительно прочные. Но тугоплавкие и тяжелые в обработке.
В ортодонтии, для изготавления дуг применяют сплавы титана, ванадия и алюминия (75-15-10%).
Металлы используемые в ортопедической стоматологии
Сплав никеля и титана – никелид титана – никель 55%, титан 45%.
Сплав обладает памятью формы. Деформированные охлажденные изделия из этого сплава при нагревании приобретают исходную форму.
Сплав применяется в ортодонтии, где при действии температуры тела он принима
ет нужную форму.
Также из него делают эндодонтические инструменты с памятью формы.
Вспомогательные сплавы применяемые в ортопедической стоматологии
Бронза – сплав меди с оловом. В стоматологии применяется алюминиевая бронза (алюминий вместо олова). Из нее делают лигатуры для шинирования переломов челюстей.
Латунь – сплав меди с цинком – из нее делают штифты для разборных моделей.
Магналий – сплав алюминия и магния – из него делают детали самолетов (сплав очень легкий и прочный). В стоматологии из него делают артикуляторы и некоторые кюветы.
Амальгамы – сплав металла с ртутью. Применяются для пломбирования.
Тема слишком обширная, о амальгаме в стоматологии будет отдельная статья.
Легкоплавкие сплавы в стоматологии ортопедическойСплавы легкоплавкие (Меллота, Вуда, Розе) – содержат Висьмут, Олово, Свинец
– их температура плавления около 70 С.
Применяются для штампов при штамповки коронок, контр штампов, изготовления разборных моделей.
Легкоплавкие металлы в стоматологии
Сплав Вуда.
Температура плавления 68 С.
Состав: Висмут – 50%, Свинец – 25%, Олово – 12,5%, Кадмий – 12,5%.
Токсичен, так как содержит кадмий.
Сплав Меллота.
Температура плавления 63 С
Состав: Висмут – 50%, Свинец – 20%, Олово – 30%.
Сплав Розе для стоматологии.
Температура плавления 94 С.
Состав: Висмут – 50%, Свинец и Олово по 25%.
Сталь для стоматологических инструментов
Инструментальная сталь – содержит углерод от 0,7% и более.
Отличается высокой прочностью и твердостью (после специальной температурной обработки).
Добавление к стали вольфрама, молибдена, ванадия и хрома делает сталь способной хорошо резать при высокой скорости. Такую сталь используют для боров и фрез.
Карбид вольфрама – не сплав. Химическое соединение вольфрама с углеродом (химическая формула WC). Сопостовим по твердости с алмазом. Применяют для производства бронебойных танковых снарядов. А ещё для твердосплавных стоматологических боров.
Металл цирконий в стоматологииДиоксид циркония – тоже не сплав. Химическое соединение металла циркония с кислородом. По химической природе близок к керамике, но твёрже и прочнее. В стоматологии применяют для изготовления фрезерованных протезов.
Сплавы металлов применяемых в стоматологии (заключение)
Представить современную стоматологию без металлов невозможно. Они в основе всего. И нет материала, который мог бы заменить металл.
Применение металлов в стоматологии
Металлы в стоматологии применяют для:
- Коронок и мостовидных протезов
- Каркасов бюгельных протезов
- Металлических базисов чспп и пспп
- Дентальных имплантатов
- Для инструментов и приспособлений
- Как вспомогательный материал для различных технологических процессов
- Для пломбирования
Видео: Металл с памятью формы в медицине
Припой серебряный | ООО “Урал-Олово”
Припой серебряный
ГОСТ 19746-2015 (19739-2015)
Серебряные припои имеют температуру плавления от 183°С до 1133°С и представляют собой сплавы серебро-свинец-олово, серебро-свинец, серебро-медь, серебро-медь-цинк, серебро-медь-цинк-кадмий, и другие.
Наименование |
ГОСТ |
Проволока, мм |
Полоса (150х400), мм |
|||
0,5-1 |
1,2-3 |
3,6-5 |
0,8 |
0,3 |
||
ПСр 72 |
ГОСТ 19746-2015 (19739-2015) |
0,5-1 |
1,2-3 |
3,6-5 |
0,8 |
0,3 |
ПСр 71 |
ГОСТ 19746-2015 (19739-2015) |
0,5-1 |
1,2-3 |
3,6-5 |
0,8 |
0,3 |
ПСр 70 |
ГОСТ 19746-2015 (19739-2015) |
0,5-1 |
1,2-3 |
3,6-5 |
0,8 |
0,3 |
ПСрМО 68-27-5 |
ГОСТ 19746-2015 (19739-2015) |
0,5-1 |
1,2-3 |
3,6-5 |
0,8 |
0,3 |
ПСр 65 |
ГОСТ 19746-2015 (19739-2015) |
0,5-1 |
1,2-3 |
3,6-5 |
0,8 |
0,3 |
ПСр 62 |
ГОСТ 19746-2015 (19739-2015) |
0,5-1 |
1,2-3 |
3,6-5 |
0,8 |
0,3 |
ПСр 50 |
ГОСТ 19746-2015 (19739-2015) |
0,5-1 |
1,2-3 |
3,6-5 |
0,8 |
0,3 |
ПСр 50 Кд |
ГОСТ 19746-2015 (19739-2015) |
0,5-1 |
1,2-3 |
3,6-5 |
0,8 |
0,3 |
ПСрКдМ 50-34-16 |
ГОСТ 19746-2015 (19739-2015) |
0,5-1 |
1,2-3 |
3,6-5 |
0,8 |
0,3 |
ПСр 45 |
ГОСТ 19746-2015 (19739-2015) |
0,5-1 |
1,2-3 |
3,6-5 |
0,8 |
0,3 |
ПСрМЦКд 45-15-16-24 |
ГОСТ 19746-2015 (19739-2015) |
0,5-1 |
1,2-3 |
3,6-5 |
0,8 |
0,3 |
ПСр 40 |
ГОСТ 19746-2015 (19739-2015) |
0,5-1 |
1,2-3 |
3,6-5 |
0,8 |
0,3 |
ПСр 37,5 |
ГОСТ 19746-2015 (19739-2015) |
0,5-1 |
1,2-3 |
3,6-5 |
0,8 |
0,3 |
ПСр 25 |
ГОСТ 19746-2015 (19739-2015) |
0,5-1 |
1,2-3 |
3,6-5 |
0,8 |
0,3 |
ПСр 25Ф |
ГОСТ 19746-2015 (19739-2015) |
0,5-1 |
1,2-3 |
3,6-5 |
0,8 |
0,3 |
ПСр 15 |
ГОСТ 19746-2015 (19739-2015) |
0,5-1 |
1,2-3 |
3,6-5 |
0,8 |
0,3 |
ПСр12М |
ГОСТ 19746-2015 (19739-2015) |
0,5-1 |
1,2-3 |
3,6-5 |
0,8 |
0,3 |
ПСр 10 |
ГОСТ 19746-2015 (19739-2015) |
0,5-1 |
1,2-3 |
3,6-5 |
0,8 |
0,3 |
ПСрО 10-90 |
ГОСТ 19746-2015 (19739-2015) |
0,5-1 |
1,2-3 |
3,6-5 |
0,8 |
0,3 |
ПСрОСу 8 (ВПр-6) |
ГОСТ 19746-2015 (19739-2015) |
0,5-1 |
1,2-3 |
3,6-5; |
0,8 |
0,3 |
ПСрМО 5 (ВПр-9) |
ГОСТ 19746-2015 (19739-2015) |
0,5-1 |
1,2-3 |
3,6-5 |
0,8 |
0,3 |
ПСрОС 3,5-95 |
ГОСТ 19746-2015 (19739-2015) |
0,5-1 |
1,2-3 |
3,6-5 |
0,8 |
0,3 |
ПСр 3 |
ГОСТ 19746-2015 (19739-2015) |
0,5-1 |
1,2-3 |
3,6-5 |
0,8 |
0,3 |
ПСрО 3-97 |
ГОСТ 19746-2015 (19739-2015) |
0,5-1 |
1,2-3 |
3,6-5 |
0,8 |
0,3 |
ПСрОС 3-58 |
ГОСТ 19746-2015 (19739-2015) |
0,5-1 |
1,2-3 |
3,6-5 |
0,8 |
0,3 |
ПСр 3Кд |
ГОСТ 19746-2015 (19739-2015) |
0,5-1 |
1,2-3 |
3,6-5 |
0,8 |
0,3 |
ПСр 2,5 |
ГОСТ 19746-2015 (19739-2015) |
0,5-1 |
1,2-3 |
3,6-5 |
0,8 |
0,3 |
ПСр 2,5С |
ГОСТ 19746-2015 (19739-2015) |
0,5-1 |
1,2-3 |
3,6-5 |
0,8 |
0,3 |
ПСр 2 |
ГОСТ 19746-2015 (19739-2015) |
0,5-1 |
1,2-3 |
3,6-5 |
0,8 |
0,3 |
ПСрОС 2-58 |
ГОСТ 19746-2015 (19739-2015) |
0,5-1 |
1,2-3 |
3,6-5 |
0,8 |
0,3 |
ПСр 1,5 |
ГОСТ 19746-2015 (19739-2015) |
0,5-1 |
1,2-3 |
3,6-5 |
0,8 |
0,3 |
ПСр 1 |
ГОСТ 19746-2015 (19739-2015) |
0,5-1 |
1,2-3 |
3,6-5 |
0,8 |
0,3 |
ПСрФ 1-7,5 ПТ 9х11х300-320 |
ТУ 48-1-205-84 |
0,5-1 |
1,2-3 |
3,6-5 |
0,8 |
0,3 |
ПСрФ 1,7-7,5 ПТ 5х9х260 |
ТУ 48-1-205-84 |
0,5-1 |
1,2-3 |
3,6-5 |
0,8 |
0,3 |
ПСрОСИн 3-56 |
ТУ 48-1-338-85 |
0,5-1 |
1,2-3 |
3,6-5 |
0,8 |
0,3 |
Серебряные припои имеют достаточно широкую область применения:
— лужение и пайка меди, медно-никелевых сплавов, никеля, ковара, нейзильбера, латуней и бронз
— пайка железоникелевых сплавов с посеребренными деталями из стали
— пайка стали с медью, никелем, медными и медно-никелевыми сплавами
— пайка меди с никелированным вольфрамом
— пайка титана и титановых сплавов с нержавеющей сталью
— пайка меди и медных сплавов с жаропрочными сплавами и нержавеющими сталями
— пайка меди и латуни с коваром, никелем, с нержавеющими сталями и жаропрочными сплавами, пайка свинцово-оловянистых бронз
— пайка и лужение меди, никеля, медных и медно-никелевых сплавов с посеребренной керамикой, пайка посеребренных деталей
— пайка меди и никеля со стеклоэмалью и керамикой
— пайка и лужение ювелирных изделий
— пайка меди с бронзой, меди с медью, бронзы с бронзой
— пайка меди, медных сплавов и сталей по свежеосаждённому медному гальваническому покрытию толщиной не менее 10 мкм
— пайка и лужение цветных металлов и сталей
— пайка и лужение серебряных деталей.
Химический состав серебряных припоев ПСр:
Марка припоя |
Химический состав, % | |||||||||||||
Серебро | Медь | Цинк | Олово | Марганец | Сурьма | Фосфор | Кадмий | Никель | Свинец | Примеси не более | ||||
Свинца | Железа | Висмута | Сумма определяемых примесей | |||||||||||
ПСр 72 |
72 ± 0,5 | Остальное | - | - | - | - | - | - | - | - | 0,005 | 0,1 | 0,005 | 0,1 |
ПСр 71 |
71±0,5 | Остальное | - | - | - | - | 1,0±0,2 | - | - | - | 0,005 | 0,15 | 0,005 | 0,15 |
ПСр 70 |
70±0,5 | 26,0±0,5 | Остальное | - | - | - | - | - | - | - | 0,05 | 0,1 | 0,005 | 0,15 |
ПСрМО 68-27-5 |
68±0,5 | Остальное | - | 5,0±0,5 | - | - | - | - | - | - | 0,005 | 0,15 | 0,005 | 0,15 |
ПСр 65 |
65±0,5 | 20,0±0,5 | Остальное | - | - | - | - | - | - | - | 0,1 | 0,1 | 0,005 | 0,15 |
ПСр 62 |
62±0,5 | 28,0±1,0 | - | Остальное | - | - | - | - | - | - | 0,005 | 0,15 | 0,005 | 0,15 |
ПСр 50 |
50,0±0,5 | Остальное | - | - | - | - | - | - | - | - | 0,005 | 0,15 | 0,005 | 0,15 |
ПСр 50Кд |
50,0±0,5 | 16,0±1,0 | - | - | - | - | Остальное | - | - | 0,1 | 0,1 | 0,005 | 0,15 | |
ПСрКдМ 50-34-16 |
50,0±0,5 | Остальное | - | - | - | - | - | 31,0±1,0 | - | - | 0,05 | 0,15 | 0,005 | 0,15 |
ПСр 45 | 45,0±0,5 | 30,0±0,5 | Остальное | - | - | - | - | - | - | - | 0,05 | 0,1 | 0,005 | 0,15 |
ПСрМЦКд 45-15-16-24 |
45,0±0,5 | Остальное | - | - | - | - | 24,0±1,0 | - | - | 0,15 | 0,15 | 0,005 | 0,15 | |
ПСр 40 |
40,0±1,0 | 16,7±0,7 | - | - | - | - | Остальное | 0,3±0,2 | - | 0,05 | 0,1 | 0,005 | 0,15 | |
ПСр 37,5 |
37,5±0,3 | Остальное | - | 8,2±0,3 | - | - | - | - | - | 0,05 | 0,1 | 0,005 | 0,15 | |
ПСр 25 |
25,0±0,3 | 40,0±1,0 | Остальное | - | - | - | - | - | - | - | 0,05 | 0,1 | 0,005 | 0,15 |
ПСр 25Ф |
25,0±0,3 | Остальное | - | - | - | - | - | - | - | 0,01 | 0,15 | 0,01 | 0,15 | |
ПСр 15 |
15,0±0,5 | Остальное | - | - | - | - | - | - | - | 0,1 | 0,05 | 0,01 | 0,15 | |
ПСр 12М |
12,0±0,3 | 52,0±1,0 | Остальное | - | - | - | - | - | - | - | 0,05 | 0,1 | 0,005 | 0,15 |
ПСр 10 |
10,0±0,3 | 53,0±1,0 | Остальное | - | - | - | - | - | - | - | 0,05 | 0,1 | 0,005 | 0,15 |
ПСрО 10-90 |
10,0±0,5 | - | - | Остальное | - | - | - | - | - | - | 0,2 | 0,15 | 0,01 | 0,3 |
ПСрОСу 8 (ВПр-6) |
0,8±0,5 | - | - | Остальное | - | - | - | - | - | 0,2 | 0,2 | 0,015 | 0,4 | |
ПСрМО 5 (ВПр-9) |
5,0±0,5 | 2,0±0,5 | - | То же | - | - | - | - | - | 0,2 | 0,2 | 0,015 | 0,4 | |
ПСрОС 3,5-95 |
3,5±0,4 | - | - | « | - | - | - | - | - | 1,0±0,3 | - | 0,15 | 0,01 | 0,15 |
ПСр 3 |
3,0±0,3 | - | - | - | - | - | - | - | - | Остальное | - | 0,15 | 0,01 | 0,15 |
ПСрО 3-97 |
3,0±0,3 | - | - | Остальное | - | - | - | - | - | - | 0,2 | 0,15 | 0,01 | 0,3 |
ПСрОС 3-58 |
3,0±0,4 | - | - | 57,8±1,0 | - | - | - | - | Остальное | - | 0,1 | 0,01 | 0,15 | |
ПСр 3Кд |
3,0±0,5 | - | 1,0±0,5 | - | - | - | - | Остальное | - | - | 0,2 | 0,15 | 0,01 | 0,3 |
ПСр 2,5 |
2,5±0,3 | - | - | 5,5±0,5 | - | - | - | - | - | Остальное | 0,15 | 0,01 | 0,15 | |
ПСр 2,5С |
2,5±0,2 | - | - | - | - | - | - | - | - | То же | - | 0,15 | 0,01 | 0,15 |
ПСр 2 |
2,0±0,3 | - | - | 30,0±1,0 | - | - | - | 5,0± 0,5 | - | « | - | 0,15 | 0,01 | 0,15 |
ПСр ОС 2-58 |
2±0,3 | - | - | 58,8±1,0 | - | - | - | - | « | - | 0,15 | 0,01 | 0,15 | |
ПСр 1,5 |
1,5±0,3 | - | - | 15,0±1,0 | - | - | - | - | - | « | - | 0,15 | 0,01 | 0,15 |
ПСр 1 | 1,0±0,2 | - | - | 35,0±1,0 | - | - | 2,5 ± 0,5 | - | « | - | 0,15 | 0,01 | 0,15 | |
Примечания: |
Примерное назначение серебряных припоев ПСр:
Марка припоя |
Область применения |
ПСр 72; ПСр 71; ПСр 62; ПСр50 Кд; ПСр 50; ПСр 40; ПСр 37,5; ПСр 25; ПСр 15; ПСр 10; ПСр 2,5 | Лужение и пайка меди, медно-никелевых сплавов, никеля, ковара, нейзильберта, латуней и бронз. |
ПСр 72 | Пайка железо-никелевого сплава с посеребренными деталями из стали |
ПСр 72; ПСр 62; ПСр 40; ПСр 25; ПСр 12 М | Пайка стали с медью, никелем, медными и медно-никелевыми сплавами. |
ПСр 72; ПСр 62 | Пайка меди с никелированным вольфрамом. |
ПСрМО 68-27-5; ПСр 70; ПСр 50 | Пайка титана и титановых сплавов с нержавеющей сталью |
ПСр 37,5 | Пайка меди и медных сплавов с жаропрочными сплавами и нержавеющими сталями. |
ПСр 40 | Пайка меди и латуни с коваром, никелем, с нержавеющими сталями и жаропрочными сплавами, пайка свинцово-оловянистых бронз |
ПСрО 10-90; ПСрОСу 8; ПСрМО 5; ПСрОС 3,5-95; ПСрО 3-97; ПСрОС 3-58; ПСрОС 2-58; ПСр2; ПСр 1,5 | Пайка и лужение меди, никеля, медных и медно-никелевых сплавов с посеребренной керамикой, пайка посеребренных деталей. |
ПСр 3; ПСр 2; ПСр 1,5 | Пайка меди и никеля со стеклоэмалью и керамикой. |
ПСр 72; ПСр 70; ПСр 65; ПСр 45; ПСр 25; ПСр 15; ПСр 2 | Пайка и лужение ювелирных изделий |
ПСр 71; ПСр 25Ф; ПСр 15 | Самофлюсующийся припой для пайки меди с бронзой, меи с медью, бронзы с бронзой. |
ПСр 3Кд | Пайка меди, медных сплавов и сталей по свеженанесенному медному гальваническому покрытию не менее 10 мкм |
ПСрМо 68-27-5; ПСрКдМ 50-34-16; ПСрМЦКд 45-15-16-24; ПСр 3; ПСр 2,5 | Пайка и лужение цветных металлов и сталей. |
ПСр 1 | Пайка и лужение серебряных деталей. |
Температуры плавления основных марок серебряных припоев ПСр:
ПСр-10 — 830 °С.
ПСр-12 — 785 °С.
ПСр-25 — 765 °С.
ПСр-45 — 720 °С.
ПСр-65 — 740 °С.
ПСр-70 — 780 °С.
Урал Олово
, припаянные сплавом — ответы на кроссворды
Кроссворд , припаянный сплавом с 6 буквами, последний раз видели 01 января 1970 года . Мы думаем, что вероятным ответом на эту подсказку будет BRAZED . Ниже приведены все возможные ответы на эту подсказку, отсортированные по ее рангу. Вы можете легко улучшить свой поиск, указав количество букв в ответе.Рейтинг | Слово | Подсказка |
---|---|---|
95% | ПЛОТНАЯ | Паял сплавом |
3% | СТАЛЬ | Сплав; щипать |
3% | ЛАТУНЬ | Медный сплав |
2% | HALLE | Берри с Оскаром и Эмми |
2% | МИНДАЛЬНОЕ ДЕРЕВО | Твердая древесина со съедобным семенем |
2% | DUO | В паре с воздухом |
2% | КАРАНДАШ | Реализовать ластиком |
2% | MONA | Лиза с маслянистым лицом? |
2% | OLE | Восклицание с ударением |
2% | HEW | Резать топором |
2% | БРОНЗА | Сплав меди и олова |
2% | АЛЕКСА | Голос с эхом |
2% | ИНПЕН | Чернильным орудием |
2% | ПАЙКИ | Соединяется со сплавом |
2% | ПАЙКА | Предохранитель со сплавом |
2% | BRAZE | Припой со сплавом |
2% | ТЕРН | Покрытие сплавом |
2% | ТЕРНЕД | С покрытием из сплава |
2% | ТАБЛИЦА | Покрытие сплавом. |
2% | ТЕРН | Покрытия сплавом. |
Уточните результаты поиска, указав количество букв. Если определенные буквы уже известны, вы можете указать их в виде шаблона: «CA ????».
Каковы лучшие решения для
, припаянного сплавом ?Мы нашли 1 решений для , припаянных сплавом .Лучшие решения определяются по популярности, рейтингам и частоте запросов. Наиболее вероятный ответ на разгадку — BRAZED .
Сколько решений у Soldered With Alloy?
С crossword-solver.io вы найдете 1 решение. Мы используем исторические головоломки, чтобы найти наиболее подходящие ответы на ваш вопрос. Мы добавляем много новых подсказок ежедневно.
Как я могу найти решение для пайки сплавом?
С нашей поисковой системой для решения кроссвордов у вас есть доступ к более чем 7 миллионам подсказок.Вы можете сузить круг возможных ответов, указав количество содержащихся в нем букв. Мы нашли более 1 ответов для Паяные со сплавом.
Поделитесь своими мыслями
У вас есть предложения или вы хотите сообщить о пропущенном слове?Обратная связь
© 2020 Авторские права: кроссворд-решатель.io
Припой— Определение припоя
Поддержка: Помогите сделать словарь Word Game сайтом без рекламы. Нажмите, чтобы принять слово припойДа, припой
есть в словаре скрэбла… и стоит
8 очков.найдите больше слов, которые вы можете составить ниже
существительное
1. Любой из различных легкоплавких сплавов, обычно олова и свинца, используемых для соединения металлических деталей.
2. То, что соединяет или цементирует.
3. Металл или металлический сплав, используемый при плавлении для соединения металлических поверхностей.
4. Используемый таким образом сплав свинца и олова.
5. То, что объединяет.
глагол
1. Для соединения или соединения припоем.
2. Ввести или восстановить в твердый союз.
3. Для использования припоя.
4. Соединяться или ремонтироваться припоем или как бы припоем.
непереходный глагол
1. Для соединения или объединения.
2. Для соединения или ремонта припоя.
глагол-переходный
1. Присоединиться или объединиться: Соглашение объединило фракции в альянс.
2. Для соединения или ремонта (например, деталей) припоем.
Вот еще несколько слов, которые можно составить из букв
припойЛучшие слова по баллам | Очки | Игра в слова |
---|---|---|
дорсель | 7 | Эрудит |
дорсель | 8 | Слова с друзьями |
2 буквы | Scrabble® | WWF® | ||
---|---|---|---|---|
do | 3 | 3 | ||
lo | 3 | |||
от | 3 | 3 | ||
oe | 2 | 2 | ||
или | 2 | |||
2 | 9022 900 | os | 2 | 2 |
es | 2 | 2 | ||
er | 2 | 2 | ||
el 2 | 3 | |||
ред | 3 | 9 0261 3 | ||
де | 3 | 3 | ||
т. |
6 букв | Scrabble® | WWF® |
---|---|---|
дорсель | 7 | 81 | 8 |
припой | 7 | 8 |
Найдено 93 слов в 0.22405 секунд
Примеры предложений припоя
Соединение их вместе с помощью выдувной трубы без помощи припоя (который быстро разрушается кислотой) .0 | 0 |
Микроскопическая точность должна быть достигнута при вырезании пространства для вставки конструкции, и хотя последняя должна быть надежно припаяна на своем месте, ни малейшие следы припоя или малейшие признаки соединения не должны быть различимы между ними. металл вставленного изображения и металл поля, в которое он вставлен.0 | 0 |
Ни один человек не может спаять миллиард транзисторов в процессоре компьютера, поэтому для сборки вашему компьютеру нужен робот.0 | 0 |
Его использование при пайке зависит от того факта, что припой прилипает только к поверхности незапятнанного металла, и, следовательно, немного буры помещается на поверхность металла и нагревается паяльником, чтобы удалить любую поверхностную пленку. оксид.0 | 0 |
При «автогенной пайке» два куска металла объединяются путем плавления противоположных поверхностей без использования отдельного легкоплавкого сплава или припоя в качестве связующего материала.0 | 0 |
* Следующие примеры предложений были собраны из разных источников, чтобы идти в ногу со временем, ни один из них не отражает мнение Словаря игр в словаНапишите свой собственный пример предложения для Solder и проявите творческий подход, может быть, даже смешно.
Прикладные науки | Бесплатный полнотекстовый | Надежный метод обнаружения трещин при пайке сплавов при ускоренном испытании на долговечность
7.1. Обсуждение
Результаты статистического анализа определили мощность теста, который показывает, что размер выборки адекватен с уровнем значимости 95%.Для определения нормальности данных был проведен анализ Шапиро Уилка, где было получено значение p 0,1349, указывающее, что данные в норме. Также были измерены значения тока, и ток ± 2 мкА был признан неисправным. На рис. 5 показан график ненадежности каждого уровня припоя, где сплавы SnPb показали более низкую надежность в зависимости от времени. В распределении Вейбулла наблюдается, что данные не образуют кривизны и что они близки к прямой линии; также значения β больше 1.0 указывает на отсутствие износа. Полученные результаты показывают, что со временем частота отказов увеличивается, а надежность снижается.Основное внимание в тестах уделяется быстрому получению данных, которые при правильном моделировании и анализе дают желаемую информацию о сроке службы продукта при нормальных условиях использования. Этот процесс был разработан, чтобы продемонстрировать, что можно найти незначительные неисправности в электронных платах и резисторах диодно-светодиодных ламп. Химический состав не изменился, о чем свидетельствуют микрофотографии.Был механический износ, трещины и разрывы. Из-за термического удара температуры и вибрации пористость сварного шва увеличилась из-за отслоения сварного шва. Другие применяемые методы требуют дополнительных испытаний.
Метод показывает удовлетворительную производительность при оценке надежности системы на основе надежности компонентов. Более того, использование ALT дает оценки с меньшим смещением и дисперсией, чем использование проверки условий для этого случая.
В обзоре литературы можно проверить результаты, полученные разными исследователями.Благодаря этим работам, полученные результаты могли быть подтверждены и проверены, и они позволили нам подтвердить, что предложенный метод в их исследовательских работах предлагал эффективное решение для прогнозирования неисправностей подшипников. Используемые в настоящее время припои с высоким содержанием свинца (Snpb) применяются для различных применений независимо от рабочих температур (150–200 ° C), и это в первую очередь потому, что их химическая структура не состоит из каких-либо интерметаллических соединений. Таким образом, рабочие температуры не имеют большого влияния на их микроструктуру [32,33].Этот аспект мог повлиять на достигнутые результаты, поскольку припой из свинца SnPb мог выйти из строя из-за качества химического производственного состава. ALT заключается в вводе в эксплуатацию образца некоторых представляющих интерес продуктов в течение определенного времени под контролируемым среды для получения быстрой информации о продолжительности жизни. Испытуемые блоки подвергаются высоким уровням напряжений и выходят из строя раньше, чем в расчетных условиях. Информация, полученная в ускоренных условиях, анализируется в рамках модели, а затем экстраполируется в расчетных условиях для оценки распределения срока службы и вероятности отказа.Следовательно, металлы, пластмассы, батареи, клеи, полупроводники, изоляторы, подшипники, химикаты, краски, асфальт, солнечное излучение, лекарства, одноразовые устройства, планирование технического обслуживания и даже жизненные ситуации могут потребовать подходов к деградации. Теория была описана Микерандом и Нельсоном [34] и Баем, Чангом и Чуном [35], и в этих источниках использовались простые примеры, соответствующие теории.Когда размер выборки невелик, а измерения показывают изменчивость, простую теорию может быть трудно применить.Для одиночного напряжения на постоянном уровне возможность измерить деградацию в присутствии «шума» может быть проблемой. Хорошая основа в области физики отказов (POF) может помочь определить режимы и причины отказов при мониторинге деградации. В документах есть ограничения на применение тестов ускоренной деградации и, по крайней мере, семь допущений для успешного использования методов деградации. Более широкий список включает:
Наблюдаемое ухудшение (изменение) необратимо при снятии напряжения.
Существует уникальный или доминирующий процесс разложения, который можно изучить (POF).
Любое ухудшение до начала ускоренного теста.
Когда ускоренные ресурсные испытания используются в промышленных условиях, эффективность процессов или активов становится проблемой как для производителей, так и для конечных пользователей. Надежность систем — это фундаментальный вопрос. Оценка надежности обычно основана на сборе полевых данных во время повседневной работы.Распространенной проблемой будет считывание данных и их компиляция, поскольку это деятельность, которая во многих случаях требует времени, и это связано с периодами, необходимыми для сопоставления с данными, которые оказываются надежными.
Важно отметить, что ALT — это метод оценки компонентов и надежности систем за короткий период, обычно недели или месяцы, с использованием стратегии тестирования с чрезмерными усилиями. В этой работе обсуждается пример сварки электронных компонентов. Модель для ALT, изучаемая здесь, соответствующим образом адаптируется к данным случая, позволяя получить хорошую оценку вероятности отказа, как показали тесты, проведенные для такой корректировки, с показанным уровнем достоверности, хотя в целом они могут меняться в зависимости от уровень, который требуется, но они не стали бы делать это радикально.Был проведен обзор ALT, необходимых для моделирования срока службы блоков, прошедших ускоренное испытание. Оптимальные планы для математической модели были изучены с различных соображений. Первоначально предполагалось, что испытание будет заканчиваться до тех пор, пока не произойдет отказ компонентов, но был рассмотрен случай, когда испытание имеет заранее определенную продолжительность. Для модели Вейбулла разработан оптимальный план ускоренного теста со ступенчатыми усилиями. Для нашего случая было получено оптимальное время применения вероятности отказа при этом испытании, и что испытание имеет заранее заданную продолжительность T.Из теста ALT была получена необходимая информация для определения оптимального плана ускоренного теста с двумя ступенчатыми усилиями, следуя процедуре, разработанной в этой работе. Для нашего случая мы получили оптимальное время применения вероятности отказа в этом тесте, и что тест имеет заранее определенную продолжительность T. Разработан и проведен комплекс экспериментальных испытаний в стрессовых условиях на 17 образцах.
Результаты моделирования ALT были сопоставлены с моделированием Вейбулла на основе реальных данных и проанализированы.Фактически, модель ALT и модель реальных данных согласуются: разница между двумя средними значениями времени и оценками отказов составляла минимальный процент, количественные тесты ускоренного срока службы, в отличие от качественных методов тестирования, состоят из тестов, предназначенных для количественно оценить жизненные характеристики продукта, компонента или системы в нормальных условиях. Условия использования, а значит, обеспечивают «достоверность информации». Информация о надежности может включать:
Определение вероятности отказа продукта в условиях использования означает низкий срок службы.
Условия использования, предполагаемый возврат и гарантии.
Затраты также могут использоваться для помощи в обнаружении ошибок и улучшении процесса.
Проведение оценки рисков, проектирование, сравнения и т. Д.
Однако новый импульс в ALT теперь требует разработки, создания процедур ALT, которые могут быть более подробными. Оценки срока службы, применимые к новым разработкам и новым технологиям в результате этого исследования, определили некоторые области как потенциальные для дальнейшего развития:
Применение запланированных статистических методов для расширения возможностей проектировщика делать выводы на основе ALT;
Изучение сильных и слабых сторон каждой представленной модели ALT и сравнение этого исследования с существующей практикой для определения лучших стратегий тестирования;
Практики управления надежностью с определением последовательности, важности, распределения ресурсов и влияния процедур ALT в цикле разработки продукта.
Межфазная реакция бессвинцового припоя Sn-Ag-Cu на Cu: обзор
В данной статье рассматриваются функции и важность припоев Sn-Ag-Cu в электронной промышленности и межфазная реакция Sn-Ag -Паяное соединение Cu / Cu при различных формах припоя и условиях оплавления припоя. Сплавы припоев Sn-Ag-Cu исследуются в больших объемах и в тонких пленках. Затем исследуется влияние условий пайки на образование интерметаллических соединений, таких как выбор подложки Cu, структурные фазы, эволюция морфологии, кинетика роста, температура и время, а также обсуждаются.Бессвинцовые припои Sn-Ag-Cu являются наиболее многообещающим кандидатом на замену припоям Sn-Pb в современной микроэлектронной технологии. Припои Sn-Ag-Cu могут быть рассмотрены и адаптированы в технологиях миниатюризации. Таким образом, эта статья должна представлять большой интерес для большого количества материалов, связанных с электроникой, надежности, процессов и сборочного сообщества.
1. Введение
Среди различных систем сплавов, которые рассматриваются в качестве кандидатов в бессвинцовые припои, сплавы Sn-Ag-Cu были признаны наиболее перспективными из-за их относительно низкой температуры плавления (по сравнению с бинарной эвтектикой Sn-Ag. бессвинцовый припой), превосходными механическими свойствами и хорошей совместимостью с другими компонентами [1–3].Сплавы Sn-Ag-Cu широко используются в качестве бессвинцовых решений для межсоединений шариковых решеток (BGA) в производстве микроэлектронной упаковки в виде шариков припоя и паст [4].
Среди ударных материалов семейство припоев на основе тройного эвтектического состава Sn-Ag-Cu (217 ° C) имеет наибольший потенциал для широкого использования в промышленности [5]. Выбор эвтектического состава является благоприятным, поскольку он ведет себя как независимая гомогенная фаза, имеет уникальную металлографическую структуру и отчетливую температуру плавления [6].Припои Sn-Ag-Cu могут способствовать повышению прочности соединений, а также сопротивлению ползучести и термической усталости, а также позволяют повышать рабочие температуры для изготовления современных электронных систем и устройств [7, 8]. Международная ассоциация печатных схем предположила, что 96,5Sn-3,0Ag-0,5Cu (SAC305) и Sn-3,9Ag-0,6Cu (два почти эвтектических сплава) будут наиболее широко используемыми сплавами в будущем [7]. Это предсказание объясняется их хорошими механическими свойствами, приемлемыми смачивающими свойствами и подходящими температурами плавления [2, 3, 9–11].
Сообщалось о том, что бессвинцовые паяные соединения имеют тонкую и стабильную микроструктуру из-за образования мелкодисперсных частиц. Таким образом, эти соединения имеют более высокую прочность на сдвиг [12, 13]. Припои Sn-Ag-Cu требуют более высокой температуры оплавления из-за более высокой температуры плавления. Например, температура плавления Sn-3.8Ag-0.7Cu составляет 219 ° C, а SAC305 — 217 ° C. Высокая температура плавления не только требует нового профиля оплавления, но также увеличивает проблемы стабильности компонентов, связанные с более высокой температурой.Некоторые компоненты могут не выдержать высокой температуры оплавления.
2. Бессвинцовый припой и его применение
Пайка — это хорошо известный металлургический метод соединения припоя с основным материалом (обычно металлом) при температуре плавления ниже 425 ° C [14]. Возьмем для примера рисунок 1. В процессе пайки припой SAC305 (рис. 1 (а)) плавится и контактирует с основным металлом медной подложки (рис. 1 (b)). Более того, Sn в расплавленном припое реагирует с Cu с образованием интерметаллического соединения (IMC) на границе раздела.Именно этот слой IMC связывает между собой припой и Cu [15–20].
Как правило, процесс пайки изображен на рисунке 2. Процесс пайки можно разделить на три стадии [21]: (а) растекание; (б) растворение основного металла; (в) формирование слоя IMC.
Подложка из меди не плавилась и не изменяла свою микроструктуру во время пайки. Затем жидкая фаза превращалась в различные твердые фазы, когда соединения охлаждались. Различные виды и относительные количества твердых фаз, образующихся во время затвердевания, важны для свойств паяного соединения.
Припои обычно являются сплавами с низкой температурой плавления, поскольку пайка проводится, когда припои полностью расплавлены [22]. Продукты используются в твердой фазе при относительно высоких рабочих температурах. Следовательно, диффузионная способность является важным свойством для большинства припоев. Кроме того, для хороших припоев требуется хорошее смачивание; таким образом, межфазные реакции с подложками обычно важны не только на контактах жидкость / твердое тело, но также и на контактах твердое тело / твердое тело при высоких рабочих температурах [22].
Прочность паяного соединения контролируется конструкцией контактных площадок и хорошей металлургической связью между компонентом и платой. Надежное паяное соединение должно иметь паяемую поверхность для образования хорошей металлургической связи между припоем и соединяемыми компонентами. Межфазные реакции в паяных соединениях являются ключевыми факторами при производстве электронных продуктов.
3. IMC припоев Sn-Ag-Cu с Cu-подложкой
В электронных продуктах все обычные базовые материалы, покрытия и металлизации, такие как Cu, Ni, Ag, Ag-Pd и Au, образуют IMC с Sn .Следовательно, химические реакции происходят между припоями и металлами проводника во время пайки (то есть металлизация компонентов, обработка поверхности платы и нижележащие проводники), а IMC зарождаются и растут на границах раздела припой / проводник.
Наличие IMC между припоями и металлами проводника желательно, поскольку это приводит к хорошему металлургическому соединению. Тонкий, непрерывный и однородный слой IMC является важным требованием для хорошего склеивания. Без IMC соединение припоя и проводника будет слабым, потому что в соединении не происходит металлургического взаимодействия, что губительно для электронной упаковки.Однако толстый слой IMC на границе раздела припой / металл проводника может снизить надежность паяных соединений из-за присущей им хрупкой природы и их тенденции к возникновению структурных дефектов, вызванных несоответствием физических свойств (таких как модуль упругости и коэффициент термической стойкости). разложение) [23]. Во время процесса следует избегать толстого слоя IMC. Таким образом, знание взаимодействий припоя и металла с проводником и фазовой эволюции в соединениях припоя важно для понимания надежности соединений припоя с металлургической точки зрения и для оптимизации процесса пайки [17].
Интерметаллические реакционные слои образуются в три последовательные стадии [17]: (а) растворение; (б) химическая реакция; (в) затвердевание.
Во время пайки припоя Sn-Ag-Cu на Cu-подложку Cu начинает мгновенно растворяться в расплавленном припое после того, как флюс удаляет оксиды и разрешает металлургический контакт между припоем и контактировавшей Cu. Начальная скорость растворения очень высока. Растворение является неравновесным процессом, и очень высокая концентрация Cu может быть локально обнаружена на границе раздела Cu / жидкость.Через короткий промежуток времени слой расплавленного припоя, прилегающий к контактировавшей Cu, становится перенасыщенным растворенной Cu по всей поверхности раздела.
С точки зрения термодинамики, твердый ИМС начинает формироваться в слое припоя, примыкающем к контактирующему металлу, при локальной равновесной растворимости. Cu 6 Sn 5 кристаллитов образуются, потому что в метастабильном составе существует большая движущая сила для химической реакции между атомами Cu и Sn.Cu 6 Sn 5 гребешкового типа сначала образуется на границе Sn / Cu во время пайки, и скорость его образования очень высока. Cu 6 Sn 5 образовался в результате растворения Cu с последующей химической реакцией. Если контакт с расплавленным припоем достаточно длительный, Cu 3 Sn образуется между Cu 6 Sn 5 и Cu. Cu 3 Sn образовался в результате диффузии и роста по реакционному типу [24].
На рисунке 3 кратко показана межфазная реакция SAC305 / Cu во время оплавления припоя.При нагревании твердый припой SAC305 плавится, и контактирующая медная подложка начинает растворяться в расплавленном припое SAC305 (рис. 3 (а)). Слой расплавленного припоя SAC305 рядом с границей раздела SAC305 / Cu становится перенасыщенным растворенной Cu (рис. 3 (b)). Твердый ИМС начинает формироваться в межфазной зоне. Сначала был сформирован Cu 6 Sn 5 со структурой гребешка (рис. 3 (c)), за которым последовал тонкий слой Cu 3 Sn (рис. 3 (d)).
4.Структурные фазы IMC в Sn-Ag-Cu / Cu
Cu — наиболее часто используемый металл-проводник, и он используется в контакте с припоями из-за его хорошей паяемости и отличной теплопроводности [25]. Лю и др. [26] исследовали межфазные реакции между паяльной пастой SAC305 и поликристаллической медной подложкой при 250 ° C и 300 ° C в период от 30 с до 1800 с. Они обнаружили, что некоторые наноразмерные частицы Ag 3 Sn адсорбировались на границе раздела SAC305 / Cu после пайки.Авторы объяснили, что атомы Ag сначала прореагировали с Sn с образованием фазы Ag 3 Sn в жидком припое. Во время затвердевания фаза Ag 3 Sn выделялась вблизи ИМС и была склонна «захватываться» ИМС. Более того, Wang et al. [27] выполнили рентгеноструктурный анализ поверхности раздела SAC305 / Cu, чтобы изучить фазовую структуру IMC во время пайки при 260 ° C в течение 20 с. Диаграмма XRD показывает, что кристаллическая структура IMC для SAC305 / Cu представляет собой Cu 6 Sn 5 .Однако фаза Ag 3 Sn в этом случае обнаружена не была.
Диаграммы XRD SAC305 в различных формах припоя показаны на рисунке 4. Общая интенсивность припоя SAC305 была намного ниже, чем у тонкой пленки SAC305 после осаждения и SAC305 / Cu после оплавления. После осаждения тонкая пленка SAC305 показала отражение β -Sn, -Cu 6 Sn 5 и Ag 3 Sn. Нагревание припоя SAC305 не привело к изменениям фазы, за исключением его относительной интенсивности.Пики Cu 6 Sn 5 и Ag 3 Sn были слишком низкими, чтобы их можно было увидеть на рентгенограмме припоя SAC305 (рис. 4 (а)), которая имела более низкую интенсивность, чем у припоя. нанесена тонкая пленка SAC305 (рис. 4 (б)). После оплавления припоя при 230 ° C большинство фаз β -Sn уменьшилось (рисунок 4 (c)). Напротив, дифракционные пики -Cu 6 Sn 5 и Ag 3 Sn стали более очевидными. Новые фазы ИМС образовались и были подтверждены как -Cu 6 Sn 5 , ɛ -Cu 3 Sn и SnO.
5. Эволюция микроструктуры IMC в Sn-Ag-Cu / Cu
Kar et al. [28] оценили микроструктуру переходного соединения, состоящего из припоя Sn-Ag-Cu и медной подложки в оплавленном состоянии при 230 ° C в течение 120 с. Они подтвердили присутствие интерметаллических фаз Cu 6 Sn 5 , Cu 3 Sn и Ag 3 Sn в межфазном реакционном слое (IRL). Присутствие Ag в ИРЛ было минимальным и не участвовало в образовании ИМС на границе раздела.Gao et al. [29] предположили, что значительное количество Ag было связано с Sn с образованием Ag 3 Sn в припое. Таким образом, степень диффузии Sn по направлению к IRL была уменьшена.
Одной из характеристик ИМС является формирование морфологии гребешкового типа. Гребешок Cu 6 Sn 5 IMC были сформированы на границах раздела SAC305 / Cu, тогда как припой находился в расплавленном состоянии во время оплавления при 270 ° C в течение 120 с [30]. Этот результат также соответствует исследованию, проведенному Kim et al.[1] о влиянии IMC на припой SAC305 (в виде паст и шариков) с соединением Cu-подложки после обработки оплавлением при 260 ° C. Юн и Юнг [31] также исследовали межфазную реакцию многослойных паяных соединений Cu / Sn-3.5Ag-0.7Cu / Cu. Типичный гребешковый слой Cu 6 Sn 5 IMC-слои были сформированы на обеих границах раздела Sn-3.5Ag-0.7Cu / Cu после оплавления. Слои имели состав приблизительно 54,8 ат.% Cu и 45,2 ат.% Sn.
На рисунке 5 представлена микрофотография поперечного сечения FESEM образца SAC305 / Cu после оплавления.Реакционный слой на медной подложке представляет собой фазу гребешка Cu 6 Sn 5 , которая образовалась во время обработки оплавлением. Длинные Cu 6 Sn 5 IMC наблюдались в верхней части межфазной границы Cu 6 Sn 5 гребешков, и рост приписывается потоку Cu от подложки Cu к гребешкам [32]. Однако относительно большие КИМ Cu 6 Sn 5 образовывались в матрице припоя из-за растворения медной площадки.Некоторые площадки Cu растворялись в расплавленном припое SAC305 во время оплавления, и растворенная Cu осаждалась в виде больших Cu 6 Sn 5 IMC в матрице припоя. Другими словами, при затвердевании эвтектического припоя SAC305 образовалась смесь матрицы β -Sn, мелкодисперсного Ag 3 Sn и Cu 6 Sn 5 частиц IMC.
Более того, Ag 3 Sn IMC был равномерно диспергирован в припое после оплавления [33]. Микроструктурный анализ припоев Sn-Ag-Cu с различным содержанием Ag был проведен для понимания деталей микроструктуры и оценки образования интерметаллических соединений.Удлиненные пластины фазы ɛ -Ag 3 Sn наблюдались в эвтектической матрице припоев Sn-1.0Ag-0.5Cu (SAC105), Sn-2.0Ag-0.5Cu (SAC205) и SAC305. С другой стороны, в припойном сплаве Sn-4.0Ag-0.5Cu (SAC405) были четко видны большие интерметаллические пластины ε -Ag 3 Sn и удлиненные пластины фазы ε -Ag 3 Sn. На рисунке 6 показана морфология IMC Ag 3 Sn в матрице припоя, которая может быть изменена путем изменения содержания Ag.Ag 3 Sn IMC удлиненной пластинчатой структуры существуют, когда содержание Ag составляет от 1,0 до 3,0 мас.% (Рис. 6 (а)). Более высокий состав Ag, равный 4,0 мас.%, Приводит к образованию крупных IMC Ag 3 Sn, как показано на Рисунке 6 (b).
На общую надежность может сильно повлиять количество и размер ε -Ag 3 Sn IMC в микроструктуре. Большие ε -Ag 3 Sn IMC обычно считаются вредными как для зарождения, так и для распространения трещин, и многочисленные исследования связывают отказ припоев SAC305 с крупными пластинчатыми ε -Ag 3 Sn IMC ниже ударные и термоциклические раздражители [1, 34, 35].Кроме того, образование больших пластинчатых ИМС ε -Ag 3 Sn вызывает растворение твердых частиц и дисперсионное твердение, что, в свою очередь, снижает прочность матрицы [36, 37].
На рис. 7 показана межфазная реакция тонкой пленки SAC305, нанесенной методом термического напыления. Затем тонкую пленку оплавляли при 230 ° C в течение 30 с. Верхний белый слой — это твердый слой SAC305, который состоит из рыхлых частиц SAC305, которые физически адсорбируются на медной подложке (рис. 7 (а)).После оплавления припоя произошла межфазная реакция. Как показано на рисунке 7 (b), были сформированы два слоя IMC. Верхняя область — это Cu 6 Sn 5 , а нижний слой — Cu 3 Sn. Cu 6 Sn 5 был толстым и неравномерным по толщине, тогда как Cu 3 Sn был очень тонким и имел более однородную толщину и слоистую морфологию. Однако тонкий слой в определенной степени повторял топографию соседнего фазового слоя Cu 6 Sn 5 .Не наблюдалось отслаивания или отслаивания IMC, что указывает на низкую концентрацию Sn в тонкой пленке. Тонкопленочный припой SAC305 полностью прореагировал с избытком Cu-подложки с образованием Cu 6 Sn 5 во время оплавления. Интерметаллический слой Cu 3 Sn последовательно увеличивался с повышением температуры, тогда как Cu 6 Sn 5 постепенно уменьшался с повышением температуры оплавления.
6. Кинетика образования и роста межфазных ИМС
Образование гребешка Cu 6 Sn 5 наблюдалось в реакциях смачивания между эвтектикой Sn-Pb и Cu [38-40], эвтектикой Sn-Ag и Cu. [39], эвтектики Sn-Bi и Cu [39].Морской гребешок — это распространенный способ роста, который со временем становится больше, но меньше. Такое поведение указывает на то, что среди зерен типа гребешка происходит неконсервативная реакция созревания. Кроме того, морфология гребешка стабильна до тех пор, пока присутствует непрореагировавшая Cu.
В системе Cu-Sn Cu 6 Sn 5 и Cu 3 Sn IMC образуются на границах раздела припой / подложка [1, 39, 41–47]. Фактическая последовательность образования этих фаз определяется локальными термодинамическими условиями на границе раздела Cu / Sn.Фаза Cu 6 Sn 5 выделяется на самых ранних стадиях взаимодействия припой / подложка, что соответствует более высокой движущей силе для выделения, чем у фазы Cu 3 Sn [48, 49]. Экспериментально подтверждено, что фаза Cu 6 Sn 5 выделяется случайным образом вдоль границы раздела припой / подложка.
Формирование и рост межфазных ИМС Cu-Sn проиллюстрировано на Рисунке 8. На начальном этапе (Рисунок 8 (a)) отдельные зерна Cu 6 Sn 5 появляются в случайных местах вдоль границы раздела твердое / жидкое. в течение нескольких миллисекунд.После появления зерен Cu 6 Sn 5 они начали распространяться вдоль границы раздела без значительного роста перпендикулярно границе раздела припой / подложка, пока не встретили другие растекающиеся зерна, что привело к образованию относительно однородного слоя IMC Cu. 6 Sn 5 (Рисунок 8 (б)).
После первоначального формирования слоя ИМС его толщина увеличивается за счет подстилающей подложки. Отдельные зерна приобретают морфологию гребешка [50], которая продолжает расти перпендикулярно границе раздела (рис. 8 (c)).Процесс созревания способствует формированию структуры гребешков IMCs, что приводит к укрупнению гребешков по мере уменьшения их количества (рис. 8 (d)). Эта реакция вызвана эффектом Гиббса-Томсона в процессе созревания. Таким образом, более мелкие зерна IMC растворяются в жидком припое, и рост соседних зерен дополнительно ускоряется [39, 51, 52].
После осаждения фазы Cu 6 Sn 5 , осаждение фазы Cu 3 Sn на границе раздела Cu 6 Sn 5 / подложка становится термодинамически возможным.Это явление обычно наблюдается на более поздних стадиях реакций пайки. Ожидается, что толщина Cu 3 Sn будет намного меньше, чем толщина Cu 6 Sn 5 , потому что Cu 3 Sn был выращен методом твердотельной диффузии.
Развитие ИМС Cu-Sn для пар Sn-Ag-Cu / Cu основано на непрерывном росте Cu 6 Sn 5 путем пайки и на образовании и росте Cu 3 Sn между Cu 6 Sn 5 и Cu.Образование Cu 3 Sn регулируется фазовой стабильностью согласно следующей реакции [29]:
Вианко [53] обнаружил образование Cu 6 Sn 5 и Cu 3 Sn на границе раздела между Cu и 95,5Sn-3,9Ag-0,6Cu. Автор пришел к выводу, что слой Cu 6 Sn 5 образовался во время пайки, а Cu 3 Sn образуется во время твердофазного старения между Cu 6 Sn 5 и медной подложкой.Рост слоя ограничен диффузией и чувствителен к концентрации CU в припое.
Оставшееся количество компонентов, участвующих в межфазной реакции, принимает участие в фазовой эволюции после образования первой фазы. В системе Sn-Pb / Cu слой Cu 6 Sn 5 , который сформировался первым, трансформируется в Cu 3 Sn, если объем припоя очень мал по сравнению с объемом припоя [54, 55]. И наоборот, Cu 3 Sn преобразуется обратно в Cu 6 Sn 5 , если тонкая пленка представляет собой Cu [56].Cu 3 Sn может растворяться с образованием Cu 6 Sn 5 , а также может реагировать с атомами Sn с образованием Cu 6 Sn 5 [3, 57]. Уравнения преобразования Cu 3 Sn в Cu 6 Sn 5 показаны следующим образом:
Во время охлаждения внешний слой Cu 3 Sn, который находится в контакте с расплавленным припоем, превращается обратно в Cu 6 Sn 5 за счет перитектической реакции
Существует множество моделей для прогнозирования образования первой фазы твердофазных межфазных реакций в тонких пленках.Кинетика роста каждого слоя может контролироваться диффузией или межфазной реакцией. Самый большой продукт изменения свободной энергии Гиббса и скорости роста определяет образование первой фазы. Другими словами, фаза, которая имеет наибольший поток взаимной диффузии, становится первой фазой, которая образуется.
Разница в скорости роста ИМС объясняется различной кинетикой роста [58]. Скорость диффузии контролирует скорость роста IMC, в то время как различные энергии границы раздела припой / IMC контролируют укрупнение зерен IMC и кинетику зародышеобразования.Рост КИМ в паяных соединениях считается обычным диффузионным ростом и должен контролироваться взаимной диффузией элементов подложки и припоя. Межфазные слои IMC продолжают расти даже при комнатной температуре после завершения затвердевания паяных соединений из-за его низкой энергии активации [59, 60].
Если рост слоя IMC является процессом с преобладанием диффузии, изотермический рост слоя IMC должен следовать закону извлечения квадратного корня из времени. Толщина () слоя IMC непосредственно измеряется с помощью FESEM вместе с системой обработки изображений и может быть выражена параболическим уравнением [61] где — начальная толщина (см), — время старения (с), — константа скорости роста, которая сильно связана с коэффициентом диффузии атомных элементов ИМС (см 2 / с) и может быть получена из линия линейной регрессии.
Перепишем (5) для экспериментальных целей и построения графиков как Значение для конкретной температуры может быть получено из наклона линейной регрессии средней измеренной толщины интерметаллида в зависимости от графика.
Между тем, энергии активации роста интерметаллида могут быть рассчитаны с использованием соотношения Аррениуса [43]: Записываем (7) для построения графика в виде где — постоянная роста слоя (см 2 / с), — энергия активации роста слоя (кДж / моль), — постоянная идеального газа (8.314 Дж / моль K), а — абсолютная температура (K). Рост для слоя будет получен из наклона графика зависимости, умноженного на.
7. Влияние температуры и времени оплавления на межфазные IMC
Толщина слоев IMC измеряется в нескольких выбранных областях, а затем делится на количество выбранных точек для получения среднего значения, как показано на рисунке 9. Толщина Количество слоев IMC, сформированных на границе раздела SAC305 / Cu, увеличивается с увеличением температуры и времени пайки.ИМС Cu-Sn были сформированы на границе раздела Sn-0.3Ag-0.7Cu и Cu-подложки путем пайки погружением при различной температуре и времени пайки [62]. В межфазной зоне обнаружена интерметаллическая фаза Cu 3 Sn или Cu 6 Sn 5 в зависимости от условий пайки. Авторы пришли к выводу, что увеличение толщины интерметаллического слоя в обоих случаях объясняется диффузионным ростом этих интерметаллических фаз в процессе пайки.
Кроме того, Yu et al.[61] исследовали формирование и рост слоя IMC на границе между бессвинцовым припоем Sn-3.5Ag и медной подложкой во время пайки и старения. Пайка проводилась при 250 ° C методом окунания. Сплошной слой IMC был сформирован за короткое время, и растворение IMC сыграло важную роль в росте IMC. С увеличением времени пайки скорость роста и растворения уменьшались. При старении при 70, 125 и 170 ° C до 1000 ч исходная морфология гребешка слоя ИМС изменилась на более планарную.
Об увеличении толщины IMC в результате увеличения времени пайки также сообщили Yu и Wang [3]. Авторы спаяли бессвинцовые припои Sn-3.5Ag, Sn-3.5Ag-0.7Cu, Sn-3.5Ag-1.7Cu и Sn-0.5Ag-4.0Cu с медной подложкой при 250 ° C. Рост слоев IMC происходит быстро при коротком времени пайки. Толщина слоя IMC постепенно увеличивается с увеличением времени пайки. Однако скорость увеличения толщины IMC замедляется, когда время пайки превышает 60 с.Таким образом, авторы пришли к выводу, что образование ИМС изначально контролируется реакционной диффузией и высокой скоростью роста. После достижения определенной толщины рост контролируется механизмом диффузии по границам зерен. Следовательно, рост слоя IMC становится медленным, как показано на рисунке 10.
Авторы также пришли к выводу, что Sn-0.5Ag-4.0Cu имеет самый тонкий слой IMC, когда время пайки меньше 90 с. После пайки в течение 600 с порядок толщины КМС в паяных соединениях — Sn-3.5Ag
После длительной пайки в течение 180 с между слоем Cu 6 Sn 5 и Cu образовался тонкий слой Cu 3 Sn. Более того, слои IMC стали толще, а количество зерен IMC уменьшилось при пайке образцов в течение 600 с, что привело к морфологии гребешка.
Рисунок 11 демонстрирует рост ИМС Cu-Sn при различных временах оплавления. На рисунке 11 (а) показано формирование структуры типа гребешка на межфазном слое SAC305 / Cu, когда время оплавления составляло 30 с.Ag 3 Sn присутствуют в матрице припоя. Кроме того, наблюдалось скалывание сфероидов Cu 6 Sn 5 из-за высокой концентрации Sn в SAC305. Образованию сфероидов способствовала реакция созревания между зернами соединения. При пайке в течение 180 с тонкая полоса Cu 3 Sn наблюдалась на границе раздела Cu 6 Sn 5 / Cu (рисунок 11 (b)). При пайке в течение 600 с слои ИМС стали толще, а количество гребешков Cu 6 Sn 5 уменьшилось.Cu 3 Sn сохранял свою сплошную слоистую морфологию с увеличением толщины и времени оплавления (рис. 11 (c)).
,Ли и Чен [63] также провели эксперимент с коммерческими бессвинцовыми припоями, а именно Sn-3.5Ag и Sn-3.5Ag-0.7Cu, с использованием стандартной инфракрасной печи оплавления при 250 ° C в течение 2, 6, 15, 30, 60, 120, 240 и 360 с. В паяном соединении были обнаружены Cu 6 Sn 5 и Ag 3 Sn. Фаза Ag 3 Sn была обнаружена, поскольку она образовалась поверх слоя во время процесса оплавления.Однако гребешковый слой Cu 6 Sn 5 IMC был расположен на границе раздела припой-медь-подложка. Авторы добавили, что фаза Cu 3 Sn не наблюдалась в затвердевшем паяном соединении, хотя она может существовать между Cu и фазой Cu 6 Sn 5 .
На Рисунке 12 сравнивается толщина слоев IMC, сформированных в межфазной области, в зависимости от температуры оплавления. Интерметаллический слой Cu 3 Sn постоянно увеличивается с повышением температуры (Рисунок 12 (a)), тогда как Cu 6 Sn 5 постепенно уменьшается с увеличением температуры оплавления (Рисунок 12 (b)).На рисунке 13 показана зависимость между толщиной слоя IMC и временем оплавления. Аналогичным образом, при определенной температуре пайки толщина слоев IMC в межфазной зоне увеличивалась с увеличением времени пайки. Основываясь на исследовании, проведенном Yu и Wang [3], увеличение времени пайки позволяет слою IMC быстро расти из-за эффекта осаждения Cu 6 Sn 5 . Cu 6 Sn 5 может быть отозван, чтобы превратиться в Cu 3 Sn, когда подача Sn ограничена.Следовательно, толщина Cu 3 Sn увеличивается с уменьшением толщины Cu 6 Sn 5 , несмотря на то, что Cu 6 Sn 5 обычно увеличивается с увеличением времени пайки. Эти результаты свидетельствуют о том, что межфазный слой Cu 3 Sn растет за счет Cu 6 Sn 5 в соответствии с реакцией Cu 6 Sn 5 + 9Cu → 5Cu 3 Sn [29]. Более того, рост толщины Cu 3 Sn подчиняется линейному уравнению.Согласно кинетике материала, линейный рост указывает на то, что формирование межфазного слоя Cu-Sn IMC является процессом, контролируемым межфазной реакцией [64].
Увеличение слоя IMC Cu 3 Sn является результатом роста диффузионного и реакционного типа в процессе пайки [17]. Рост Cu 3 Sn состоит из нескольких этапов: растворение Cu из слоя Cu, диффузия Cu и Sn через существующий слой Cu 3 Sn и преобразование Cu 6 Sn 5 в Cu 3 Sn на границе Cu 6 Sn 5 / Cu 3 Sn и реакцию Sn с Cu на границе Cu / Cu 3 Sn [65].И наоборот, Cu 6 Sn 5 образуется в результате растворения Cu с последующей химической реакцией [17], и его рост ограничен слоем Cu 3 Sn, поскольку количество свободных атомов Cu, которые могут диффундировать к Cu 6 Sn 5 очень мала. Следовательно, Cu 3 Sn быстро растет с температурой, потребляя Cu 6 Sn 5 на границе раздела Cu 3 Sn / Cu 6 Sn 5 .
8. Выводы
Sn-Ag-Cu — ведущий кандидат для производства экологически чистых продуктов.Два интерметаллических слоя обычно находятся в межфазной зоне Sn-Ag-Cu и подложки Cu, то есть Cu 6 Sn 5 и Cu 3 Sn. Cu 6 Sn 5 образуется первым и обладает структурой, подобной гребешку, тогда как Cu 3 Sn выходит на границе раздела Cu 6 Sn 5 / Cu и имеет слоистую структуру. Однако толщина Cu 3 Sn намного меньше, чем толщина Cu 6 Sn 5 , и для его образования требуется более длительное время контакта.Морфологические превращения могут происходить в зависимости от фазовой стабильности. Обе ИМС Cu-Sn растут с увеличением температуры и времени оплавления.
Благодарности
Л. М. Ли хотел бы поблагодарить MyBrain15 и Программу стипендий USM за финансовую помощь. А. А. Мохамад благодарит USM за финансовую поддержку (грант RUI № 814112).
Зачем переходить с «хороших» свинцовых припоев на бессвинцовые при пайке вручную?
С 2006 года, после введения в действие Директивы ЕС 2002/95 / EC в Законе об электрическом оборудовании, большинство производителей промышленной электроники установили, что они должны использовать бессвинцовые припои для изготовления своих сборок.Согласно этому закону, «бессвинцовый» означает припои, которые содержат не более 0,1% свинца и, следовательно, ниже указанных предельных значений. Эта директива ЕС была заменена директивой 2011/65 / EU в 2013 году. Ничего не изменилось в допустимых предельных значениях для припоев для мягкой пайки; были также добавлены несколько антипиренов, которые использовались в области производства печатных плат. В июне 2018 года свинец был добавлен в список веществ, вызывающих очень серьезную озабоченность, в соответствии с Европейским законом о химических веществах (SVHC — «Вещества, вызывающие очень серьезную озабоченность»).Это приводит к изменению требований к маркировке для всех содержащих свинец припоев (например, припоев) с более чем 0,3% свинца в твердой форме, поскольку с этой даты свинец справедливо классифицируется как токсичный для воспроизводства. Это не шикана, но отражает необходимость того, чтобы обращение со свинцовыми припоями было адаптировано к современным знаниям об их опасности.
Эта классификация как токсичная для воспроизводства означала, что припой, содержащий свинец, можно было продавать только специально обученным людям.Различные юридические требования объединились, так что сегодня многие частные любители электроники также сталкиваются с темой преобразования сплавов. Конечно, есть исключения, RoHS относится к «размещению на рынке» электронных сборок. Это частный пользователь, который сам разрабатывает свои хобби-проекты, паяет, а затем использует их — и который не «выставляет их на рынок»? Наверное, нет, но это не меняет того, что мы знаем об опасностях обращения со свинцом.
Переключатель на бессвинцовые припои
Переход от свинцовых припоев к бессвинцовым хорошо зарекомендовал себя в промышленности.Конечно, были необходимы корректировки технологии системы и, конечно же, корректировка производственных параметров. Тот или иной компонент, а также печатные платы должны были быть оптимизированы с точки зрения термостойкости. Но в области ручной пайки с помощью паяльной станции необходимые настройки сохраняются в узких пределах. Некоторые из первых бессвинцовых сборок эксплуатируются до 15 лет — и нет никаких причин отказа, которые можно было бы объяснить только использованием бессвинцовых сплавов.
Каковы основные различия между сплавами, используемыми в секторе сплавов? Содержит свинец Sn63Pb37 в виде эвтектического сплава с температурой плавления 183 ° C или вариаций с большим количеством свинца или небольшим количеством меди / серебра в качестве добавки с диапазоном плавления около 179–190 ° C. Они были стандартом на протяжении многих лет. Эти сплавы можно было хорошо обрабатывать с помощью паяльной станции мощностью 30-50 Вт с установленной температурой жала паяльника 300-320 ° C. Припой становился жидким, флюс удалял оксиды с поверхностей, подлежащих пайке, олово из припоя растворялось. медь (или другие виды металлизации) на компоненте или печатной плате и интерметаллическая фаза была создана.Это сделало паяное соединение хорошо сформированным, упругим и прочным.
В бессвинцовых сплавах обычно гораздо больше олова. Вместо 63% это больше похоже на 95-99% Sn. В результате температура плавления сплава повышается до 217–227 ° C, но олово всегда было компонентом припоя, который образует интерметаллическую фазу и может «ослабить» все паяемые металлические поверхности. Свинец всегда был только «инертным» (неактивным) компонентом сплава, с тем преимуществом, что он удешевлял и снижал температуру плавления олова с 232 до 183 ° C.Однако теперь больше олова в припое в сочетании с более высокой температурой пайки означает, что вам нужно уделять больше внимания своим инструментам и металлизации компонентов. Припой не только быстрее растворяет медные поверхности, но и растворяется быстрее. Прежде чем вы это узнаете, паяльная петля на печатной плате растворилась.
Стандартные бессвинцовые сплавы
Но давайте более подробно рассмотрим некоторые стандартные сплавы, не содержащие свинца: если вы хотите достичь вышеупомянутых 217 ° C как одной из самых низких возможных температур в диапазоне SnAgCu, используйте состав с Sn95.5%, можно использовать Ag3,8% Cu0,7%. Преимущество — относительно низкая температура плавления, недостаток — почти 4% серебра в припое, что может почти вдвое дороже припоя. В принципе, этот серебросодержащий сплав можно немного удешевить, снизив содержание серебра до 3%. Тогда сплав имеет интервал плавления 217 — 223 ° С, но это не особо заметно ни при обработке, ни с учетом долговечности паяного соединения. Как самый дешевый сплав оловянно-медный сплав (Sn99.3% Cu0,7%) может использоваться в качестве эвтектического сплава с определенной температурой плавления 227 ° C без серебра. При использовании этого сплава также необязательно повышать температуру на паяльном наконечнике на 10 ° C по сравнению со сплавом, содержащим серебро.
Для всех бессвинцовых припоев применяется то же эмпирическое правило для определения требуемой температуры паяльного жала, что и для свинцовых припоев:
Ликвидус (точка разжижения) сплава + 120 ° C = рабочая температура на жало паяльника
Итак, арифметически, свинецсодержащий припой с диапазоном плавления 183–190 ° C дает температуру жала паяльника 310 ° C в качестве начального значения с Sn99.3 Cu0,7 при температуре 227 ° C, 350 ° C — хорошая отправная точка для начала пайки. Если для ввода определенного количества тепла за короткое время требуется на 10-20 ° C больше, это определенно может быть вариантом. Температура выше 380 ° C обычно больше повреждает печатные платы и компоненты, чем помогает. Флюс в проволоке также горит намного быстрее, поэтому он может выполнять свою работу только определенное время при определенной температуре. Каждые 10 ° C повышения температуры вдвое сокращают активную продолжительность флюса. Время, необходимое для удаления оксидов, становится меньше — в какой-то момент оно оказывается слишком коротким.В конечном счете, речь идет не об абсолютных температурах. Мягкая пайка — это всегда подвод необходимого количества энергии и достижение определенных минимальных температур. Припой должен быть жидким, его температура должна быть выше температуры ликвидуса, чтобы позволить металлизации раствориться и, таким образом, образовать интерметаллические фазы и, таким образом, упругую точку пайки.
Все перечисленные выше бессвинцовые сплавы обладают достаточной долговременной стойкостью: можно грубо определить серебросодержащие припои как более подходящие для применений с более высокими перепадами температуры, часто связанными с постоянным механическим напряжением (вибрацией).В качестве примера можно привести использование в автомобилях. Припои с низким содержанием серебра или без серебра часто, но не исключительно, используются в бытовой электронике. Отсутствие резких перепадов температуры, меньшая механическая нагрузка. Это те области, где можно обойтись без серебра. Кроме того, такие факторы, как количество припоя, расположение геометрии пайки и металлизация, используемая на компоненте и печатной плате, также имеют значительное влияние на оценку долговременной надежности паяного соединения.Так что вопрос не только в том, какой припой используется для разрушения, и на него ответить.
Entwicklungen der Lotlegierungen
Кроме того, в последние годы в области припоев было много разработок, которые могут оптимизировать долговременную надежность и другие свойства стандартных припоев. Эти микролегированные припои основаны на вышеупомянутых припоях на основе олово-медь или олово-серебро-медь, но добавлено около 500 ppm контролируемых микрокомпонентов. Часто это никель, кобальт или другие металлы и полуметаллы.Это снижает способность к растворению и улучшает микроструктуру паяного соединения. Что означает улучшение микроструктуры? Более мелкие границы зерен в припое позволяют паяльному соединению поглощать значительно больше механической энергии до того, как оно будет механически разрушено при испытаниях на термический удар — долговременная надежность выше. Жала паяльника снова живут дольше, потому что смачиваемый слой железа на жале растворяется намного медленнее. Медь также будет растворяться в припое намного медленнее, припой на печатной плате останется дольше, и процесс ремонта будет более надежным.Известной серией лотов являются лоты серии FLOWTIN. Более длительный срок службы жала паяльника по сравнению со стандартным припоем, составляющий 30-50%, может быть достигнут при аккуратном обращении с параметрами пайки и инструментами.
Поскольку паяльная проволока состоит не только из сплава, но и флюс, который она содержит, является важным компонентом, здесь мы сделаем краткий экскурс в разницу во флюсах, которые используются в бессвинцовых / содержащих свинец припоях. Задача флюса — удалить оксиды с задействованных компонентов: компонента, печатной платы и, конечно же, жидкого припоя.Делать это нужно как можно дольше, чтобы при пайке было большое технологическое окно. В зависимости от типа и количества оксида на паяемом элементе активность должна быть адаптирована. Есть флюсы без галогенов, а также несколько более сильные галогенсодержащие флюсы. Обе группы удаляют оксиды посредством реакции кислота-оксид металла. Однако флюс для бессвинцовых припоев должен выполнять этот механизм реакции при более высокой температуре и, таким образом, оставаться активным дольше даже при более высокой температуре пайки.Флюс должен иметь возможность течь в достаточном количестве перед припоем, удалять оксиды, отводить образующиеся соли перед припоем и оставлять жидкий припой с хорошо чистой, чистой металлической поверхностью. Затем может происходить процесс диффузии и образуется паяное соединение. При повышенных температурах пайки необходимо также отрегулировать флюс, чтобы оптимизировать распыление флюса и смачивание. Здесь вступают в игру два по-разному активированных флюса Kristall 600 и 611.Они были разработаны в сочетании с бессвинцовыми и микролегированными припоями и, таким образом, могут полностью раскрыть свой потенциал на различных окисленных поверхностях.
При выборе флюса всегда следует использовать более слабый. Все, что не остается на сборке в качестве активаторов и продуктов их реакции в остатке, не может вызвать никаких проблем с долговременной надежностью. Всегда настолько сильно и настолько, насколько вам нужно для достижения хорошей реакции смачивания.
Еще одним преимуществом этих припоев является то, что они сделаны только из олова из линейки Stannol Fairtin.Здесь играет роль не только качество сырья, но и другие факторы, такие как условия труда при добыче олова, применяемые экологические стандарты и многое другое.
Работа с бессвинцовым припоем
Рассмотрим теперь процесс работы с бессвинцовым припоем. Паяное соединение без свинца требует больше энергии, чем соединение, содержащее свинец, при тех же условиях. Это относится ко всем процессам пайки, независимо от того, используете ли вы припой или паяльную пасту.
Поскольку требуется больше энергии, передача тепла к точке пайки также должна рассматриваться как наиболее важный аспект при пайке. Здесь важно создать оптимальную контактную поверхность для теплопередачи. В этом контексте оптимальное — это как можно больше! Сделать это довольно просто: просто используйте жало паяльника с наибольшей площадью контакта и не оставляйте тонкий кончик иглы прикрепленным весь день. Таким образом, для каждой задачи по пайке необходимо найти оптимальное паяльное жало.Из-за большей переходной площади это одновременно обеспечивает большее количество энергии, так что более высокие затраты энергии на плавление бессвинцового припоя не нужно компенсировать повышением рабочей температуры. Это снова привело бы к более быстрому износу жала паяльника.
Исследования показали, что повышение температуры с 360 ° C до 410 ° C увеличивает износ жала паяльника почти экспоненциально при использовании бессвинцовых сплавов. Срок службы жала не только сокращается вдвое, но и значительно сокращается.Поэтому, как правило, следует учитывать несколько более длительное время пайки или контакта точки пайки, чтобы не увеличивать рабочую температуру без необходимости.
Еще один важный фактор — это правильный выбор инструмента. Важную роль играет технология теплопередачи. Быстрое время реакции паяльника на повышенную потребность в тепле является основополагающим фактором в поддержании максимально низкой рабочей температуры.
Технологии активных паяльных жало, в которых паяльное жало образует «блок» из нагревательного элемента, датчика и смачиваемой области, имеют очень быстрое время нагрева (прибл.3 секунды) и может быть быстро отрегулирован соответственно. Это преимущество насадок с прямым нагревом идет рука об руку с гораздо более высокой ценой. Но благодаря быстрому нагреву эти паяльные жала могут быстрее автоматически переходить в режим ожидания, что снижает износ и потребление энергии.
Технологии пассивного паяльника отделяют управляющую электронику в паяльнике (нагревательный элемент / датчик) от паяльного жала, которое затем можно заменить как изнашиваемую деталь — и это дешевле.Чтобы иметь возможность оптимально использовать эффективность пассивной технологии, важна хорошая поверхность контакта между паяльником и паяльником, а также необходим мощный паяльный инструмент с мощностью не менее 80 Вт или более (например, Weller WSP 80, WTP 90, WXP 120).
Если вы затем выбрали паяльную проволоку с оптимальным флюсом, который может удалить присутствующие оксиды, вы сможете добиться хорошей реакции смачивания.
Внешний вид бессвинцовых паяных соединений немного отличается от свинцовых паяных соединений.Хотя «правило 3G» (ровный, гладкий и блестящий) все еще применяется к паяным соединениям, содержащим свинец, эти критерии применимы лишь в ограниченной степени к бессвинцовым паяным соединениям. Самый важный критерий бессвинцовой пайки — чисто сформированный «мениск». Этот видимый угол смачивания можно увидеть на поверхности паяного соединения. Поскольку состав бессвинцовых и серебросодержащих сплавов означает, что поверхности становятся более шероховатыми, они не могут так хорошо блестеть и не могут соответствовать правилу «3G».Но и здесь есть припои без серебра с компонентами из микролегированных сплавов, которые могут создавать блестящие паяные соединения с припоем на основе SnCu. Flowtin TC или SN100c упомянуты здесь в качестве примеров.
Заключение
Бессвинцовая пайка не сложна — она просто отличается от пайки свинцовыми припоями.
Критерии качества изменятся, и, возможно, придется адаптировать используемые паяльные инструменты. Но электробезопасность бессвинцового паяного соединения ничем не уступает свинцовому пайке! Если вы ознакомились с изменившимися характеристиками растекания и смачивания бессвинцового сплава и согласны с немного более длительным временем пайки, чтобы без необходимости не повышать температуру, вы быстро обнаружите, что пайка фактически не изменилась.
Испытайте различные бессвинцовые сплавы в качестве недорогих тестовых упаковочных карт без больших финансовых затрат, чтобы найти подходящий припой для вашего применения:
Проволока для припоя станнола Kristall 600 FLOWTIN TC FAIRTIN Sn99 Cu1 диаметром 1,00 мм на карте обмотки (6g)
Проволока для припоя станнола Kristall 511 TC Sn99 Cu1 диаметром 1,00 мм на карте обмотки (6g)
Проволока для припоя станнола HS 10 TC Sn99 Cu1 диаметром 1,00 мм на упаковочной карте (6 г)
Проволока для припоя станнола HS 10 FAIR FLOWTIN TC + Sn99 Cu1 + ML в 1.Ø 00 мм на упаковочной карте (5г)
Этот взнос предоставлен компанией STANNOL GMBH & Co. KG
(PDF) Экспериментальные исследования влияния добавления Ag в тройной бессвинцовый припой Sn-1Cu-1Ni
240
Jayesh et al. / Letters on Materials 9 (2), 2019 pp. 239-242
1. Введение
За последние два десятилетия в припоях произошли революционные изменения
из-за запрета на свинец в сплаве со ссылкой на его присущую ему токсичность
и вопросы окружающей среды.Строгие государственные правила
и спрос со стороны клиентов вынудили передовые отрасли производства электронных корпусов
постепенно увеличивать использование бессвинцовых припоев. [1, 2,12].
e обычно используемый сплав Sn-Pb заменяется
большим количеством групп бессвинцовых сплавов. В качестве замены сплава
Sn-Pb в основном используются следующие сплавы: Sn-Zn, Sn-Cu,
,Sn-Bi, Sn-Bi-Ag, Sn-Ag-Cu, Sn-Zn-Bi и т. Д. .[3–11]. Температура плавления
, точка, твердость, смачиваемость и микротвердость — вот важные свойства
, которые следует учитывать при выборе варианта
сплава Sn-Pb [13–16]. Sn-Cu
привлек большое внимание как выбор сплава для бессвинцового припоя, когда стоимость
рассматривается как переменная. Но сплав Sn-Cu имеет
худшие характеристики смачивания и механические свойства.
[16–19]. Микроструктурные и механические свойства
,бессвинцовых припоев могут быть существенно улучшены за счет добавления посторонних материалов.Добавление Ni в Sn-Cu
улучшает свойства припоя [20, 21].
В данном исследовании анализируется возможность добавления
Ag в тройной сплав Sn-1Cu-1Ni. E Ag
добавляется в количестве 0,25, 0,5, 0,75 и 1 мас.% В матрицу припоя
из Sn-1Cu-1Ni. Были проанализированы твердость, температура плавления, угол смачивания
и микроструктура этих пяти сплавов (один образец
Sn-Cu-Ni и четыре образца Sn-Cu-Ni-xAg)
.Количество серебра должно быть очень тщательно определено
, поскольку серебро значительно увеличит стоимость припоя
.
2. Методика эксперимента
2.1. Подготовка образца
Наиболее распространенным методом приготовления припоев
является порошковая металлургия. Элементы в составе
будут в виде порошка. Этот порошок
будет спрессован в виде сырого тела.Затем is
спекают в требуемую форму при повышенных температурах. Sn, Cu,
Ni и Ag были сделаны доступными в форме порошка, и
позволили плавиться при повышенной температуре около 900 ° C
в течение 45 минут. Затем этот расплавленный материал переносят в
специально разработанные цилиндрические формы. Все эти ve сплавы с вариацией
по составу Ag подвергали закалке, а
выдерживали при комнатной температуре в течение 2 суток.Визуальный анализ
этих сплавов был проведен при первичной приемке. Проведен анализ химического состава
этих сплавов.
2.2. Анализ температуры плавления
Более высокая температура плавления припоя
считается плохим свойством, ссылаясь на тот факт, что электронный блок
выйдет из строя при более высоких температурах. Температура плавления
всех пяти образцов был проведен с использованием ermo
гравиметрического и дифференциального термального анализа (TG-DTA).
Термогравиметрический анализ (TGA) измерял вес
потери или увеличения как функцию температуры, график TGA
отображается в виде ступенек, это может быть связано с производной TGA
по времени или температуре. Дифференциальный термический анализ
(ДТА) — это метод регистрации разницы в температуре
между веществом и эталонным материалом
в зависимости от времени или температуры, поскольку два образца
,подвергаются одинаковой температуре. режимах в среде
, нагретой или охлаждаемой с контролируемой скоростью.
2.3. Измерение микротвердости и анализ смачивания
Характеристики абразивного износа и износа материала можно оценить
с помощью анализа твердости. Испытания на твердость проводили на твердомере
. Каждое значение HV было средним из
точек различных показаний, которые были записаны случайным образом в
точках на поверхности образца. Подготовка образца
проводилась шлифованием с использованием различных марок бумаги SiC.
Затем образцы были отполированы. Поверхности сплавов
,анализировали на металлургическом микроскопе Axio Vertical A1
до и после испытания на микротвердость.
Смачивание можно определить как способность расплавленного припоя
сплававступать в реакцию с нижней подложкой. Формируются интерметаллические соединения
(IMC), которые действуют как адгезионный слой
для соединения припоя и подложки. Расплавленный образец
пяти сплавов был распределен по медной подложке.Затем измеряется угол контакта
. Обычно, если угол смачивания или контакта
,лежит между 0 ° и 90 °, система считается влажной.
Если смачивание или угол контакта составляет от 90 ° до 180 °, система
считается несмачивающей.
2.4. Анализ микроструктуры
Для шлифовки образцов сплава ve
использовались четыре сорта бумаги SiC, после чего следовала механическая полировка
алмазной суспензией.95% раствор этанола / 5%
HCl используется для химического травления. Детали поверхности образцов
,анализировали с помощью сканирующей электронной микроскопии с полевой эмиссией
(FE-SEM, Carl Zeiss Sigma). Все изображения
,были сделаны при увеличении 5,00 KX, масштаб = 1 мкм,
Электронное высокое напряжение (EHT) = 5,00Kv, рабочее расстояние
(WD) = 3,2 мкм
3. Результат и обсуждение
3.1. Химический состав
Было изготовлено пять образцов сплавов разного состава.
Химический состав сплавов анализировали с помощью
ICP-OES. Результаты анализа представлены в таблице №1.
3.2. Температура плавления
° С. Температуры плавления всех пяти образцов
были протестированы с использованием анализа ТГА. Результаты были записаны, и
, сравнение показано на рисунке 1. Видно, что
температура плавления сплава Sn-Cu-Ni составляет 232,2 ° C.
e Температура плавления Sn-Cu-Ni-xAg (x = 0.25, 0,5,
0,75, 1 мас.%) Равны 231,2, 230,1, 229,4, 228,7 соответственно. Таким образом,
можно сделать вывод, что с добавлением Ag в Sn-Cu-Ni,
температура плавления несколько снижается. Расстояние
,между соседними атомами и средняя амплитуда колебаний
определяет свойство температуры плавления.
SOLDER a Scrabble Word | Слова, составленные из букв SOLDER
Определения и значение припоя
припой
Этимология
со среднеанглийского souder , soudere , soudur (существительное), со старофранцузского soldure , soudeure (существительное), со старофранцузского souder , solder («припаять», глагол ) (> Среднеанглийский souden («паять»)), от латинского solidāre , присутствует активный инфинитив solidō («делать твердый»).
Произношение
- (Великобритания) enPR: sŏlʹdə (r), sōlʹdə (r); IPA (ключ) : /ˈsɒl.də(ɹ)/, /ˈsəʊl.də(ɹ)/
- Рифм: -ldə (ɹ), -ldə (ɹ)
- (Канада, General American) enPR: sŏdʹər, sōʹdər; IPA (ключ) : /ˈsɑd.ɚ/, /ˈsoʊ.dəɹ/
- Стихотворения: -də (ɹ), -əʊdə (ɹ)
- LanguageHat обсуждение множества вариантов произношения слова «solder»
Существительное
припой ( счетные и несчетные , множественные припои )
- Любой из различных легкоплавких сплавов, обычно из олова и свинца, которые используются для ремонта, покрытия или соединения металлических предметов, обычно небольших размеров.
- Образно говоря, обстоятельства или эмоции, которые прочно связывают вещи или людей вместе по аналогии с припоем, соединяющим металлы.
Переводы
Глагол
припой ( третье лицо единственное простое настоящее припои , причастие настоящего пайка , простое причастие прошедшего и прошедшего времени спаянное )
- для соединения элементов или покрытия их припоем
- (образно) соединять вещи как бы припоем.
Антонимы
Производные термины
Переводы
См. Также
Анаграммы
- Elrods, Loders, dorsel, перепродано
Африкаанс
Этимология
из голландского zolder , из среднего голландского solre , из старого голландского * solari , * soleri , из латинского sōlārium .
Произношение
Существительное
припой ( множественный припой припой , уменьшенный припой )
- чердак
Производные условия
Французский
Этимология
из solde + -er
Произношение
Глагол
припой
- на закрытие (сделка)
- (финансы) на расчет, погашение (долг)
- продать на продажу, продать
- (рефлексивный, ~ пар. ), чтобы закончить (in), чтобы закончить (in)
Спряжение
Связанные термины
Дополнительная литература
- «припаять» в Trésor de la langue française informatisé ( Оцифрованное казначейство французского языка ).
Анаграммы
индонезийский
Этимология
От голландского soldeer , от старофранцузского soldure , soudeure (существительное), от старофранцузского souder , solder («припаять», глагол) (> среднеанглийский souden («припаять») ”)), От латинского solidāre , представляет собой активный инфинитив solidō (« сделать твердый »).
Произношение
- IPA (ключ) : [ˈsɔldɛr]
- Расстановка переносов: sol‧dèr
Существительное
припой-припой
- припой: любой из различных легкоплавких сплавов, обычно из олова и свинца, которые используются для ремонта, покрытия или соединения металлических предметов, обычно небольших размеров.