Что такое топливные элементы. Как работают топливные элементы. Какие бывают виды топливных элементов. Каковы преимущества и недостатки топливных элементов. Где применяются топливные элементы сегодня и в будущем.
Что такое топливные элементы и как они работают
Топливный элемент — это устройство, которое преобразует химическую энергию топлива напрямую в электрическую энергию без процесса горения. В отличие от обычных аккумуляторов, топливные элементы могут работать непрерывно, пока им подается топливо и окислитель.
Принцип работы топливного элемента заключается в следующем:
- На анод подается топливо (обычно водород).
- На катод подается окислитель (обычно кислород из воздуха).
- Топливо окисляется на аноде, в результате чего образуются электроны и ионы.
- Электроны идут во внешнюю цепь, создавая электрический ток.
- Ионы проходят через электролит к катоду, где соединяются с окислителем.
- В результате реакции образуется вода и выделяется тепло.
Таким образом, топливный элемент напрямую преобразует химическую энергию в электрическую, минуя малоэффективные процессы горения.

Основные виды топливных элементов
Существует несколько основных типов топливных элементов, которые различаются используемым электролитом и рабочей температурой:
- Щелочные топливные элементы (AFC)
- Топливные элементы с протонообменной мембраной (PEMFC)
- Топливные элементы на основе фосфорной кислоты (PAFC)
- Топливные элементы на расплавленных карбонатах (MCFC)
- Твердооксидные топливные элементы (SOFC)
Рассмотрим подробнее особенности и характеристики каждого типа.
Щелочные топливные элементы (AFC)
Щелочные топливные элементы используют в качестве электролита водный раствор гидроксида калия. Они имеют следующие характеристики:
- Рабочая температура: 60-220°C
- КПД: до 70%
- Мощность: до 20 кВт
- Преимущества: высокий КПД, низкая стоимость
- Недостатки: чувствительность к CO2, необходимость в чистых реагентах
Щелочные топливные элементы использовались в космических программах NASA, но сейчас применяются редко из-за высоких требований к чистоте топлива и окислителя.
Топливные элементы с протонообменной мембраной (PEMFC)
В топливных элементах этого типа используется полимерная мембрана в качестве электролита. Их основные характеристики:

- Рабочая температура: 50-100°C
- КПД: 40-60%
- Мощность: до 250 кВт
- Преимущества: компактность, быстрый запуск, низкая рабочая температура
- Недостатки: высокая стоимость катализаторов, чувствительность к примесям
PEMFC активно разрабатываются для применения в транспорте и портативных устройствах благодаря компактности и быстрому запуску.
Топливные элементы на основе фосфорной кислоты (PAFC)
Этот тип топливных элементов использует концентрированную фосфорную кислоту в качестве электролита. Их характеристики:
- Рабочая температура: 150-200°C
- КПД: 40-50%
- Мощность: до 200 кВт
- Преимущества: устойчивость к примесям, надежность
- Недостатки: большой вес, низкая удельная мощность
PAFC широко используются в стационарных энергетических установках средней мощности благодаря надежности и длительному сроку службы.
Топливные элементы на расплавленных карбонатах (MCFC)
В этих топливных элементах электролитом служит расплав карбонатов щелочных металлов. Их особенности:
- Рабочая температура: 600-700°C
- КПД: 50-60%
- Мощность: до 2 МВт
- Преимущества: высокий КПД, возможность внутренней конверсии топлива
- Недостатки: длительный запуск, коррозия компонентов
MCFC перспективны для использования в крупных стационарных энергетических установках, работающих на природном газе или биогазе.

Твердооксидные топливные элементы (SOFC)
Твердооксидные топливные элементы используют керамический электролит и работают при самых высоких температурах. Их характеристики:
- Рабочая температура: 800-1000°C
- КПД: 50-60%
- Мощность: до 2 МВт
- Преимущества: высокий КПД, топливная гибкость, отсутствие катализаторов из драгметаллов
- Недостатки: длительный запуск, проблемы с материалами из-за высоких температур
SOFC активно разрабатываются для применения в стационарной энергетике благодаря высокой эффективности и возможности работы на различных видах топлива.
Преимущества и недостатки топливных элементов
Топливные элементы имеют ряд важных преимуществ по сравнению с традиционными энергетическими установками:
- Высокий КПД преобразования энергии (до 60% и выше)
- Экологичность (отсутствие вредных выбросов при работе на водороде)
- Бесшумность работы
- Модульность конструкции
- Широкий диапазон мощностей (от ватт до мегаватт)
Однако у топливных элементов есть и недостатки:
- Высокая стоимость
- Ограниченный ресурс работы
- Чувствительность к примесям в топливе
- Необходимость в дорогих катализаторах
- Проблемы с хранением и транспортировкой водорода
Применение топливных элементов
Топливные элементы находят применение в различных областях:
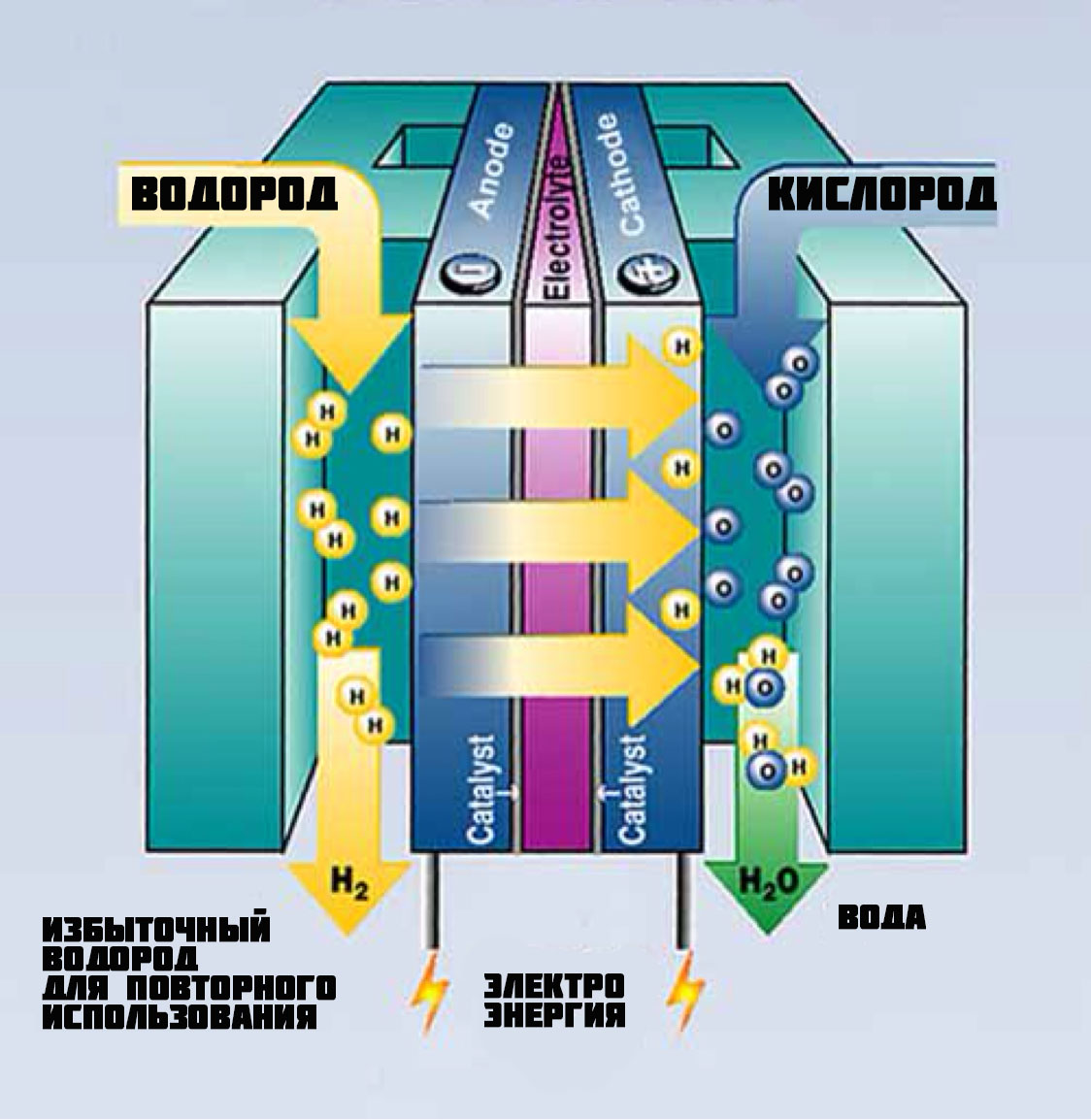
- Транспорт (автомобили, автобусы, погрузчики)
- Портативные источники питания
- Резервные источники питания
- Космическая техника
- Стационарные энергетические установки
- Военная техника
Наиболее активно развивается применение топливных элементов в транспорте и стационарной энергетике.
Перспективы развития технологии топливных элементов
Основные направления совершенствования топливных элементов включают:
- Снижение стоимости за счет новых материалов и технологий производства
- Повышение удельной мощности и энергоемкости
- Увеличение срока службы и надежности
- Разработка эффективных систем хранения и транспортировки водорода
- Создание инфраструктуры для широкого внедрения водородных технологий
По мере решения этих задач ожидается расширение сфер применения топливных элементов и постепенный переход к водородной энергетике.
Заключение
Топливные элементы представляют собой перспективную технологию для экологически чистого и эффективного производства электроэнергии. Несмотря на существующие проблемы, они имеют большой потенциал для применения в различных областях — от портативной электроники до крупных энергетических установок. Дальнейшее развитие технологии топливных элементов может внести значительный вклад в решение проблем энергетики и экологии.
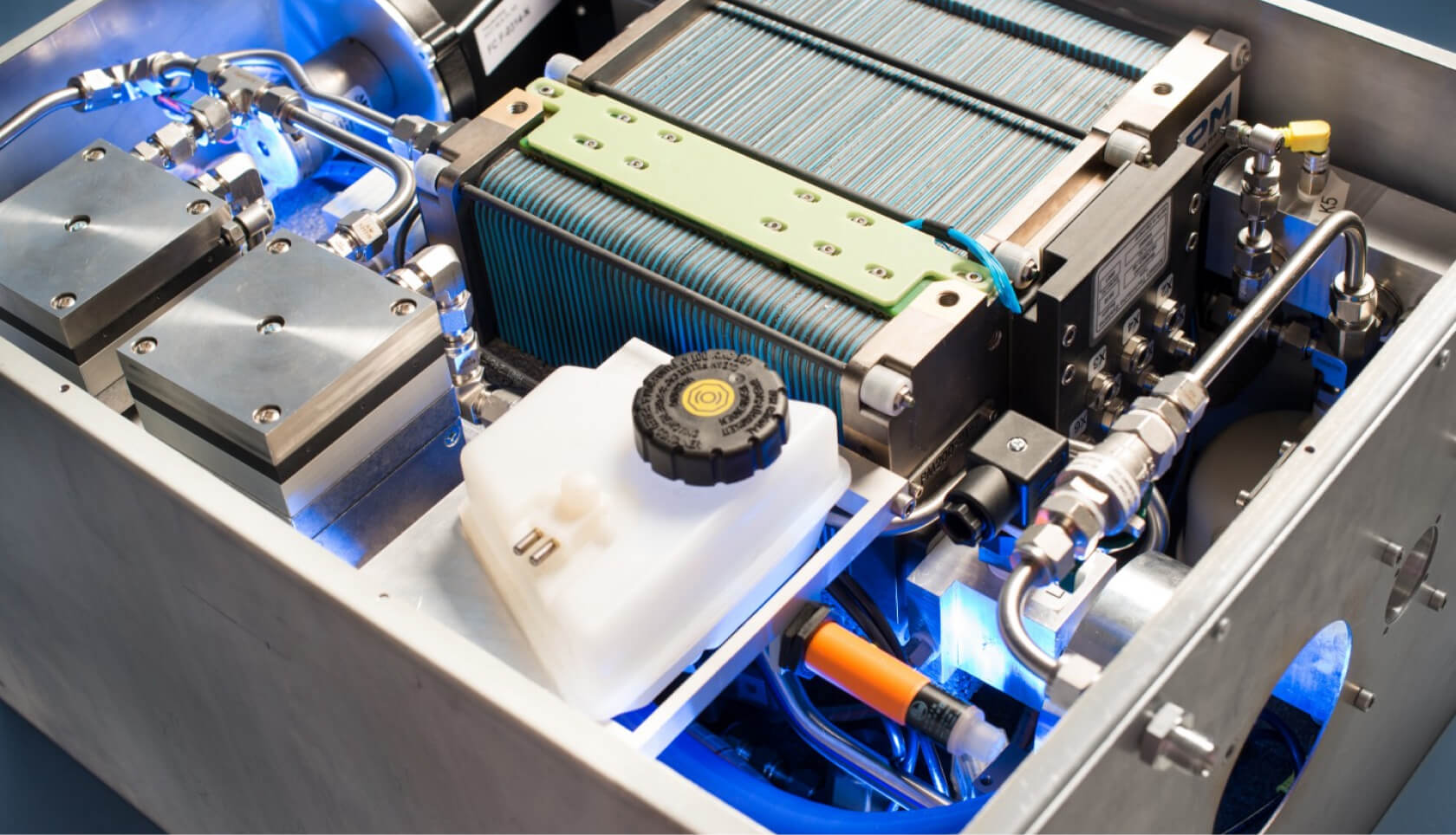
Топливные элементы (топливные ячейки)
Подобно существованию различных типов двигателей внутреннего сгорания, существуют различные типы топливных элементов – выбор подходящего типа топливной элементы зависит от его применения.
Топливные элементы делятся на высокотемпературные и низкотемпературные. Низкотемпературные топливные элементы требуют в качестве топлива относительно чистый водород. Это часто означает, что требуется обработка топлива для преобразования первичного топлива (такого как природный газ) в чистый водород. Этот процесс потребляет дополнительную энергию и требует специального оборудования. Высокотемпературные топливные элементы не нуждаются в данной дополнительной процедуре, так как они могут осуществлять «внутреннее преобразование» топлива при повышенных температурах, что означает отсутствие необходимости вкладывания денег в водородную инфраструктуру.
Топливные элементы на расплаве карбоната (РКТЭ)
Топливные элементы с расплавленным карбонатным электролитом являются высокотемпературными топливными элементами. Высокая рабочая температура позволяет непосредственно использовать природный газ без топливного процессора и топливного газа с низкой теплотворной способностью топлива производственных процессов и из других источников. Данный процесс был разработан в середине 1960-х гг. С того времени была улучшена технология производства, рабочие показатели и надежность.
Работа РКТЭ отличается от других топливных элементов. Данные элементы используют электролит из смеси расплавленных карбонатных солей. В настоящее время применяется два типа смесей: карбонат лития и карбонат калия или карбонат лития и карбонат натрия. Для расплавки карбонатных солей и достижения высокой степени подвижности ионов в электролите, работа топливных элементов с расплавленным карбонатным электролитом происходит при высоких температурах (650°C). КПД варьируется в пределах 60-80%.
При нагреве до температуры 650°C, соли становятся проводником для ионов карбоната (CO32-). Данные ионы проходят от катода на анод, где происходит объединение с водородом с образованием воды, диоксида углерода и свободных электронов. Данные электроны направляются по внешней электрической цепи обратно на катод, при этом генерируется электрический ток, а в качестве побочного продукта – тепло.
Реакция на аноде: CO32- + H2 => H2O + CO2 + 2e—
Реакция на катоде: CO2 + 1/2O2 + 2e— => CO3
Общая реакция элемента: H2(g) + 1/2O2(g) + CO2(катод) => H2O(g) + CO2(анод)
Высокие рабочие температуры топливных элементов с расплавленным карбонатным электролитом имеют определенные преимущества. При высоких температурах, происходит внутренний риформинг природного газа, что устраняет необходимость использования топливного процессора. Помимо этого, к числу преимуществ можно отнести возможность использования стандартных материалов конструкции, таких как листовая нержавеющая сталь и никелевого катализатора на электродах. Побочное тепло может быть использовано для генерации пара высокого давления для различных промышленных и коммерческих целей.
Высокие температуры реакции в электролите также имеют свои преимущества. Применение высоких температур требует значительного времени для достижения оптимальных рабочих условий, при этом система медленнее реагирует на изменение расхода энергии. Данные характеристики позволяют использовать установки на топливных элементах с расплавленным карбонатным электролитом в условиях постоянной мощности. Высокие температуры препятствуют повреждению топливного элемента окисью углерода, «отравлению», и пр.
Топливные элементы с расплавленным карбонатным электролитом подходят для использования в больших стационарных установках. Промышленно выпускаются теплоэнергетические установки с выходной электрической мощностью 2,8 МВт. Разрабатываются установки с выходной мощностью до 100 МВт.
Топливные элементы на основе фосфорной кислоты (ФКТЭ)
Топливные элементы на основе фосфорной (ортофосфорной) кислоты стали первыми топливными элементами для коммерческого использования. Данный процесс был разработан в середине 1960-х гг., испытания проводились с 1970-х гг. С того времени была увеличена стабильность, рабочие показатели и снижена стоимость.
Топливные элементы на основе фосфорной (ортофосфорной) кислоты используют электролит на основе ортофосфорной кислоты (H3PO4) с концентрацией до 100%. Ионная проводимость ортофосфорной кислоты является низкой при низких температурах, по этой причине эти топливные элементы используются при температурах до 150–220°C.
Носителем заряда в топливных элементах данного типа является водород (H+, протон). Схожий процесс происходит в топливных элементах с мембраной обмена протонов (МОПТЭ), в которых водород, подводимый к аноду, разделяется на протоны и электроны. Протоны проходят по электролиту и объединяются с кислородом, получаемым из воздуха, на катоде с образованием воды. Электроны направляются по внешней электрической цепи, при этом генерируется электрический ток. Ниже представлены реакции, в результате которых генерируется электрический ток и тепло.
Реакция на аноде: 2H2 => 4H+ + 4e—
Реакция на катоде: O2(g) + 4H+ + 4e— => 2H2O
Общая реакция элемента: 2H2 + O2 => 2H2O
КПД топливных элементов на основе фосфорной (ортофосфорной) кислоты составляет более 40% при генерации электрической энергии. При комбинированном производстве тепловой и электрической энергии, общий КПД составляет около 85%. Помимо этого, учитывая рабочие температуры, побочное тепло может быть использовано для нагрева воды и генерации пара атмосферного давления.
Высокая производительность теплоэнергетических установок на топливных элементах на основе фосфорной (ортофосфорной) кислоты при комбинированном производстве тепловой и электрической энергии является одним из преимуществ данного вида топливных элементов. В установках используется окись углерода с концентрацией около 1,5%, что значительно расширяет возможность выбора топлива. Помимо этого, СО2 не влияет на электролит и работу топливного элемента, данный тип элементов работает с риформированным природным топливом. Простая конструкция, низкая степень летучести электролита и повышенная стабильность также являются преимущества данного типа топливных элементов.
Промышленно выпускаются теплоэнергетические установки с выходной электрической мощностью до 400 кВт. Установки на 11 МВт прошли соответствующие испытания. Разрабатываются установки с выходной мощностью до 100 МВт.
Топливные элементы с мембраной обмена протонов (МОПТЭ)
Топливные элементы с мембраной обмена протонов считаются самым лучшим типом топливных элементов для генерации питания транспортных средств, которое способно заменить бензиновые и дизельные двигатели внутреннего сгорания. Эти топливные элементы были впервые использованы НАСА для программы «Джемини». Сегодня разрабатываются и демонстрируются установки на МОПТЭ мощностью от 1Вт до 2 кВт.
В качестве электролита в этих топливных элементах используется твердая полимерная мембрана (тонкая пластмассовая пленка). При пропитывании водой этот полимер пропускает протоны, но не проводит электроны.
Топливом является водород, а носителем заряда – ион водорода (протон). На аноде молекула водорода разделяется на ион водорода (протон) и электроны. Ионы водорода проходят сквозь электролит к катоду, а электроны перемещаются по внешнему кругу и производят электрическую энергию. Кислород, который берется из воздуха, подается к катоду и соединяется с электронами и ионами водорода, образуя воду. На электродах происходят следующие реакции:
Реакция на аноде: 2H2 + 4OH— => 4H2O + 4e—
Реакция на катоде: O2 + 2H2O + 4e— => 4OH—
Общая реакция элемента: 2H2 + O2 => 2H2O
По сравнению с другими типами топливных элементов, топливные элементы с мембраной обмена протонов производят больше энергии при заданном объеме или весе топливного элемента. Эта особенность позволяет им быть компактными и легкими. К тому же, рабочая температура – менее 100°C, что позволяет быстро начать эксплуатацию. Эти характеристики, а также возможность быстро изменить выход энергии – лишь некоторые черты, которые делают эти топливные элементы первым кандидатом для использования в транспортных средствах.
Другим преимуществом является то, что электролитом выступает твердое, а не жидкое, вещество. Удержать газы на катоде и аноде легче с использованием твердого электролита, и поэтому такие топливные элементы более дешевы для производства. По сравнению с другими электролитами, при применении твердого электролита не возникает таких трудностей, как ориентация, возникает меньше проблем из-за появления коррозии, что ведет к большей долговечности элемента и его компонентов.
Твердооксидные топливные элементы (ТОТЭ)
Твердооксидные топливные элементы являются топливными элементами с самой высокой рабочей температурой. Рабочая температура может варьироваться от 600°C до 1000°C, что позволяет использовать различные типы топлива без специальной предварительной обработки. Для работы с такими высокими температурами используемый электролит представляет собой тонкий твердый оксид металла на керамической основе, часто сплав иттрия и циркония, который является проводником ионов кислорода (О2—). Технология использования твердооксидных топливных элементов развивается с конца 1950-х гг. и имеет две конфигурации: плоскостную и трубчатую.
Твердый электролит обеспечивает герметичный переход газа от одного электрода к другому, в то время как жидкие электролиты расположены в пористой подложке. Носителем заряда в топливных элементах данного типа является ион кислорода (О2—). На катоде происходит разделение молекул кислорода из воздуха на ион кислорода и четыре электрона. Ионы кислорода проходят по электролиту и объединяются с водородом, при этом образуется четыре свободных электрона. Электроны направляются по внешней электрической цепи, при этом генерируется электрический ток и побочное тепло.
Реакция на аноде: 2H2 + 2O2— => 2H2O + 4e—
Реакция на катоде: O2 + 4e— => 2O2—
Общая реакция элемента: 2H2 + O2 => 2H2O
КПД производимой электрической энергии является самым высоким из всех топливных элементов – около 60%. Помимо этого, высокие рабочие температуры позволяют осуществлять комбинированное производство тепловой и электрической энергии для генерации пара высокого давления. Комбинирование высокотемпературного топливного элемента с турбиной позволяет создать гибридный топливный элемент для повышения КПД генерирования электрической энергии до 70%.
Твердооксидные топливные элементы работают при очень высоких температурах (600°C–1000°C), в результате чего требуется значительное время для достижения оптимальных рабочих условий, при этом система медленнее реагирует на изменение расхода энергии. При таких высоких рабочих температурах не требуется преобразователь для восстановления водорода из топлива, что позволяет теплоэнергетической установке работать с относительно нечистым топливом, полученным в результате газификации угля или отработанных газов и т.п. Также данный топливный элемент превосходно подходит для работы с высокой мощностью, включая промышленные и крупные центральные электростанции. Промышленно выпускаются модули с выходной электрической мощностью 100 кВт.
Топливные элементы с прямым окислением метанола (ПОМТЭ)
Технология использования топливных элементов с прямым окислением метанола переживает период активного развития. Она успешно зарекомендовала себя в области питания мобильных телефонов, ноутбуков, а также для создания переносных источников электроэнергии. на что и нацелено будущее применение данных элементов.
Устройство топливных элементов с прямым окислением метанола схоже с топливных элементах с мембраной обмена протонов (МОПТЭ), т.е. в качестве электролита используется полимер, а в качестве носителя заряда – ион водорода (протон). Однако, жидкий метанол (CH3OH) окисляется при наличии воды на аноде с выделением СО2, ионов водорода и электронов, которые направляются по внешней электрической цепи, при этом генерируется электрический ток. Ионы водорода проходят по электролиту и вступает в реакцию с кислородом из воздуха и электронами, поступающих с внешней цепи, с образованием воды на аноде.
Реакция на аноде: CH3OH + H2O => CO2 + 6H+ + 6e—
Реакция на катоде: 3/2O2 + 6H+ + 6e— => 3H2O
Общая реакция элемента: CH3OH + 3/2O2 => CO2 + 2H2O
Разработка данных топливных элементов была начата в начале 1990-х гг. После создания улучшенных катализаторов и, благодаря другим недавним нововведениям, была увеличена удельная мощность и КПД до 40%.
Были проведены испытания данных элементов в температурном диапазоне 50-120°C. Благодаря низким рабочим температурам и отсутствию необходимости использования преобразователя, топливные элементы с прямым окислением метанола являются лучшим кандидатом для применения как в мобильных телефонах и других товарах широкого потребления, так и в двигателях автомобилей. Достоинством данного типа топливных элементов являются небольшие габариты, благодаря использованию жидкого топлива, и отсутствие необходимости использования преобразователя.
Щелочные топливные элементы (ЩТЭ)
Щелочные топливные элементы (ЩТЭ) – одна из наиболее изученных технологий, используемая с середины 1960-х гг. агентством НАСА в программах «Аполлон» и «Спейс Шаттл». На борту этих космических кораблей топливные элементы производят электрическую энергию и питьевую воду. Щелочные топливные элементы – одни из самых эффективных элементов, используемых для генерации электричества, эффективность выработки электроэнергии доходит до 70%.
В щелочных топливных элементах используется электролит, то есть водный раствор гидроксида калия, содержащийся в пористой стабилизированной матрице. Концентрация гидроксида калия может меняться в зависимости от рабочей температуры топливного элемента, диапазон которой варьируется от 65°С до 220°С. Носителем заряда в ЩТЭ является гидроксильный ион (ОН—), движущийся от катода к аноду, где он вступает в реакцию с водородом, производя воду и электроны. Вода, полученная на аноде, движется обратно к катоду, снова генерируя там гидроксильные ионы. В результате этого ряда реакций, проходящих в топливном элементе, производится электричество и, как побочный продукт, тепло:
Реакция на аноде: 2H2 + 4OH— => 4H2O + 4e—
Реакция на катоде: O2 + 2H2O + 4e— => 4OH—
Общая реакция системы: 2H2 + O2 => 2H2O
Достоинством ЩТЭ является то, что эти топливные элементы — самые дешевые в производстве, поскольку катализатором, который необходим на электродах, может быть любое из веществ, более дешевых чем те, что используются в качестве катализаторов для других топливных элементов. Кроме того, ЩТЭ работают при относительно низкой температуре и являются одними из самых эффективных топливных элементов — такие характеристики могут соответственно способствовать ускорению генерации питания и высокой эффективности топлива.
Одна из характерных особенностей ЩТЭ – высокая чувствительность к CO2, который может содержаться в топливе или воздухе. CO2 вступает в реакцию с электролитом, быстро отравляет его, и сильно снижает эффективность топливного элемента. Поэтому использование ЩТЭ ограничено закрытыми пространствами, такими как космические и подводные аппараты, они должны работать на чистом водороде и кислороде. Более того, такие молекулы, как CO, H2O и CH4, которые безопасны для других топливных элементов, а для некоторых из них даже являются топливом, вредны для ЩТЭ.
Полимерные электролитные топливные элементы (ПЭТЭ)
В случае полимерных электролитных топливных элементов полимерная мембрана состоит из полимерных волокон с водными областями, в которых существует проводимость ионов воды H2O+ (протон, красный) присоединяется к молекуле воды. Молекулы воды представляют проблему из-за медленного ионного обмена. Поэтому требуется высокая концентрация воды как в топливе, так и на выпускных электродах, что ограничивает рабочую температуру 100°С.
Твердокислотные топливные элементы (ТКТЭ)
В твердокислотных топливных элементах электролит (CsHSO4) не содержит воды. Рабочая температура поэтому составляет 100-300°С. Вращение окси анионов SO42-позволяет протонам (красный) перемещаться так, как показано на рисунке. Как правило, твердокислотный топливный элемент представляет собой бутерброд, в котором очень тонкий слой твердокислотного компаунда располагается между двумя плотно сжатыми электродами, чтобы обеспечить хороший контакт. При нагреве органический компонент испаряется, выходя через поры в электродах, сохраняя способность многочисленных контактов между топливом (или кислородом на другом конце элементы), электролитом и электродами.
Новый материал для топливных элементов позволяет создавать долгосрочные «энергетические ячейки» / Хабр
Литиевые батареи — отличное решение для хранения энергии, генерируемой солнечными батареями или иными источниками «зеленого» электричества. Но они достаточно быстро разряжаются, так что это краткосрочное решение — накопить энергию «впрок» не получится. Кроме того, для хранения реально больших объемов энергии нужны очень массивные хранилища (одно такое построил Илон Маск в Австралии).
Специалисты ищут подходящее решение уже многие годы, но пока что ничего радикального создать не удалось. Правда, в последнее время становятся популярнее топливные элементы, которые вырабатывают энергию из, например, водорода. На днях стало известно о новом виде топливных ячеек, которые работают сразу в двух направлениях — они могут вырабатывать электричество из метана или водорода, или же потреблять энергию и производить метан или водород.
КПД ячейки довольно высокий: если потратить определенный объем энергии на выработку метана или водорода, а затем пустить все в обратном направлении, то получить можно 75% потраченного ранее электричества. В принципе, весьма неплохо.
Ограничения
Батареи, как уже говорилось выше, не слишком хороши для долгосрочных запасов электричества. Другие недостатки — медленная скорость подзарядки плюс дороговизна. Неплохим выходом могут служить проточные аккумуляторы, которые используются все шире.
Проточный (редокс) аккумулятор – это электрическое устройство хранения энергии, представляющее собой нечто среднее между обычной батареей и топливным элементом. Жидкий электролит, состоящий из раствора металлических солей, прокачивают через ядро, которое состоит из положительного и отрицательного электрода, разделенных мембраной. Возникающий между катодом и анодом ионный обмен приводит к выработке электричества.
Но проточные аккумуляторные не такие эффективные, как традиционные батареи, а электролит, который в них используется обычно токсичен или же вызывает коррозию (а иногда и то, и другое).
Альтернатива, позволяющая хранить энергию в течение долгого времени — превращать излишки электричества в топливо. Но здесь все не так просто, обычные схемы преобразования энергии в топливо достаточно энергозатратные, так что КПД системы никогда не будет высоким. Кроме того, катализаторы для проведения реакции обычно дорогие.
Способ сократить расходы — использовать обратимый (реверсивный) топливный элемент. В принципе, они не являются чем-то новым. При работе в прямом направлении топливные элементы берут водород или метан в качестве топлива и вырабатывают электричество. Работая в обратном направлении, они вырабатывают топливо, потребляя электричество.
Как раз реверсивные топливные элементы — идеальный вариант для долгосрочного хранения энергии, а также для получения метана или водорода там, где они нужны.
Почему же они еще не используются повсеместно? Потому, что в теории все выглядит отлично, но на практике возникают непреодолимые сложности. Во-первых, многие такие элементы нуждаются в высокой температуре для работы. Во-вторых, они производят смесь водорода и воды, а не чистый водород (в большинстве случаев). В-третьих, КПД цикла ну очень невелик. В-четвертых, катализатор в большинстве существующих элементов быстро разрушается.
Выход из положения
Его предложили исследователи из Колорадской горной школы. Они изучили возможности обратимых протонно-керамических электрохимических элементов. При выработке энергии они весьма эффективны, плюс они не нуждаются в очень уж высокой температуре — достаточно источников отработанного тепла от промышленных процессов или традиционного производства электроэнергии.
Ученые усовершенствовали технологию, предложив в качестве материала для электродов Ba/Ce/Zr/Y/Yb и Ba/Co/Zr/Y. Для их работы нужна температура в 500 градусов Цельсия, что не проблема, плюс в производство вовлекается около 97% энергии, которая была подведена к системе. При этом ячейки работают на воде или воде и углекислом газе. Вырабатывают они водород, в первом случае, или метан, во втором.
КПД системы составляет около 75%. Не так хорошо, как у батарей, но для большинства целей и этого вполне достаточно. При этом электроды не разрушаются. После 1200 часов испытаний оказалось, что материал практически не деградировал.
Правда, остается еще одна проблема — дороговизна исходных материалов, которые используются для создания электродов. Тот же иттербий стоит примерно $14 000 за килограмм, так что создание действительно значительных по размеру топливных элементов может оказаться весьма дорогим удовольствием.
Но, возможно, разработчики смогут решить и эту проблему — во всяком случае, работа в этом направлении уже ведется.
топливных элементов | Министерство энергетики
Отдел технологий водорода и топливных элементов
Топливный элемент использует химическую энергию водорода или другого топлива для чистого и эффективного производства электроэнергии. Если водород является топливом, единственными продуктами являются электричество, вода и тепло. Топливные элементы уникальны с точки зрения разнообразия их потенциального применения; они могут использовать широкий спектр видов топлива и сырья и могут обеспечивать питанием такие большие системы, как коммунальная электростанция, и такие маленькие, как портативный компьютер.
Зачем изучать топливные элементы
Топливные элементы могут использоваться в самых разных областях, обеспечивая электроэнергию для приложений в различных секторах, включая транспорт, промышленные/коммерческие/жилые здания и долговременное хранение энергии для сети в реверсивных системах. .
Топливные элементы имеют ряд преимуществ по сравнению с традиционными технологиями, основанными на сжигании, которые в настоящее время используются на многих электростанциях и транспортных средствах. Топливные элементы могут работать с более высокой эффективностью, чем двигатели внутреннего сгорания, и могут преобразовывать химическую энергию топлива непосредственно в электрическую энергию с эффективностью, превышающей 60%. Топливные элементы имеют более низкие или нулевые выбросы по сравнению с двигателями внутреннего сгорания. Водородные топливные элементы выделяют только воду, решая критические климатические проблемы, поскольку нет выбросов углекислого газа. Также отсутствуют загрязнители воздуха, создающие смог и вызывающие проблемы со здоровьем в месте эксплуатации. Топливные элементы работают бесшумно, так как в них мало движущихся частей.
Как работают топливные элементы
Топливные элементы работают как батареи, но они не разряжаются и не нуждаются в подзарядке. Они производят электричество и тепло до тех пор, пока подается топливо. Топливный элемент состоит из двух электродов — отрицательного электрода (или анода) и положительного электрода (или катода), зажатых вокруг электролита. К аноду подается топливо, например водород, а к катоду – воздух. В водородном топливном элементе катализатор на аноде разделяет молекулы водорода на протоны и электроны, которые идут разными путями к катоду. Электроны проходят через внешнюю цепь, создавая поток электричества. Протоны мигрируют через электролит к катоду, где они объединяются с кислородом и электронами с образованием воды и тепла. Узнать больше о:
- Части топливного элемента
- Системы топливных элементов
- Типы топливных элементов.
Посмотрите анимацию топливных элементов Управления водородных и топливных элементов, чтобы увидеть, как работают топливные элементы.
Цели исследований и разработок
Министерство энергетики США (DOE) тесно сотрудничает со своими национальными лабораториями, университетами и отраслевыми партнерами, чтобы преодолеть критические технические препятствия на пути разработки топливных элементов. Стоимость, производительность и долговечность по-прежнему являются ключевыми проблемами в отрасли топливных элементов. Просмотрите соответствующие ссылки, которые предоставляют подробную информацию о деятельности топливных элементов, финансируемой Министерством энергетики.
- Стоимость — Исследования, разработка и демонстрация (RD&D) сосредоточены на разработке недорогих блоков топливных элементов и баланса компонентов установки (BOP), а также передовых подходов к крупносерийному производству для снижения общей стоимости системы. Платина представляет собой один из самых больших компонентов стоимости топливного элемента с мембраной из полимерного электролита, работающего на водороде, поэтому особое внимание уделяется подходам, которые повысят активность и коэффициент использования, а также снизят содержание существующих катализаторов из металлов платиновой группы (МПГ) и сплавов МПГ, а также а также подходы катализатора без МПГ для долгосрочного применения.
- Производительность — Чтобы повысить эффективность и производительность топливных элементов, RD&D фокусируется на инновационных материалах и стратегиях интеграции. Усилия включают разработку электролитов для ионообменных мембран с повышенной эффективностью и долговечностью при сниженной стоимости; совершенствование мембранно-электродных узлов (МЭБ) с высокой удельной мощностью за счет интеграции современных компонентов МЭБ; моделирование для понимания конструкции системы и условий эксплуатации; и разработка стеков с высокой эффективностью при номинальной мощности и высокопроизводительных компонентов противовыбросового превентора, таких как компоненты управления воздухом с низкими паразитными потерями.
- Долговечность — Применения топливных элементов обычно требуют адекватной работы для поддержания в течение длительных периодов времени. Министерство энергетики установило конечные цели по сроку службы системы топливных элементов в реальных условиях эксплуатации: 8 000 часов для легковых автомобилей, 30 000 часов для большегрузных автомобилей и 80 000 часов для систем с распределенным питанием.
В наиболее требовательных приложениях требуется надежность и устойчивость системы в динамичных и суровых условиях эксплуатации. Реальные условия эксплуатации включают пуск и останов, замораживание и оттаивание, примеси в топливе и воздухе, а также влажность и циклы динамических нагрузок, которые приводят к нагрузкам на химическую и механическую стабильность материалов и компонентов системы топливных элементов. Исследования и разработки сосредоточены на выявлении и понимании механизмов деградации топливных элементов, а также на разработке материалов и стратегий для смягчения их последствий.
Технические задачи
Загрузите раздел «Топливные элементы» Многолетнего плана исследований, разработок и демонстраций Управления технологий производства водорода и топливных элементов, чтобы получить полную информацию о технических целях. Выполняется крупное обновление этого документа.
типов топливных элементов | Министерство энергетики
Отдел технологий водорода и топливных элементов
Топливные элементы классифицируются в первую очередь по типу используемого электролита. Эта классификация определяет тип электрохимических реакций, происходящих в ячейке, тип необходимых катализаторов, диапазон температур, в которых работает ячейка, необходимое топливо и другие факторы. Эти характеристики, в свою очередь, влияют на области применения, для которых эти элементы наиболее подходят. В настоящее время разрабатывается несколько типов топливных элементов, каждый из которых имеет свои преимущества, ограничения и потенциальные области применения. Узнайте больше о следующих типах топливных элементов.
Топливные элементы с мембраной из полимерного электролита
Топливные элементы с полимерно-электролитной мембраной (PEM), также называемые топливными элементами с протонообменной мембраной, обеспечивают высокую удельную мощность и обладают преимуществами малого веса и объема по сравнению с другими топливными элементами. Топливные элементы PEM используют твердый полимер в качестве электролита и пористые углеродные электроды, содержащие катализатор из платины или платинового сплава. Для работы им нужен только водород, кислород воздуха и вода. Как правило, они работают на чистом водороде, поступающем из резервуаров для хранения или установок риформинга.
Топливные элементы PEM работают при относительно низких температурах, около 80°C (176°F). Низкотемпературная работа позволяет им быстро запускаться (меньшее время прогрева) и приводит к меньшему износу компонентов системы, что увеличивает срок службы. Однако для разделения электронов и протонов водорода требуется катализатор из благородного металла (обычно платина), что увеличивает стоимость системы. Платиновый катализатор также чрезвычайно чувствителен к отравлению монооксидом углерода, что делает необходимым использование дополнительного реактора для уменьшения содержания монооксида углерода в топливном газе, если водород получают из углеводородного топлива. Этот реактор также увеличивает стоимость.
Топливные элементы PEM используются в основном для транспортных средств и некоторых стационарных приложений. Топливные элементы PEM особенно подходят для использования в транспортных средствах, таких как автомобили, автобусы и большегрузные грузовики.
Топливные элементы прямого действия на метаноле
Большинство топливных элементов работают на водороде, который может подаваться непосредственно в систему топливных элементов или может быть получен в системе топливных элементов путем риформинга богатого водородом топлива, такого как метанол, этанол и углеводородное топливо. Однако топливные элементы с прямым метанолом (DMFC) питаются от чистого метанола, который обычно смешивают с водой и подают непосредственно на анод топливного элемента.
Топливные элементы прямого действия на метаноле не имеют многих проблем с хранением топлива, типичных для некоторых систем топливных элементов, поскольку метанол имеет более высокую плотность энергии, чем водород, хотя и меньшую, чем бензин или дизельное топливо. Метанол также легче транспортировать и поставлять населению, используя нашу текущую инфраструктуру, потому что это жидкость, такая как бензин. DMFC часто используются для обеспечения питания портативных приложений на топливных элементах, таких как сотовые телефоны или портативные компьютеры.
Щелочные топливные элементы
Щелочные топливные элементы (AFC) были одной из первых разработанных технологий топливных элементов, и они были первым типом, широко используемым в космической программе США для производства электроэнергии и воды на борту космического корабля. Эти топливные элементы используют раствор гидроксида калия в воде в качестве электролита и могут использовать различные недрагоценные металлы в качестве катализатора на аноде и катоде. В последние годы были разработаны новые AFC, в которых в качестве электролита используется полимерная мембрана. Эти топливные элементы тесно связаны с обычными топливными элементами PEM, за исключением того, что в них используется щелочная мембрана вместо кислотной мембраны. Высокая производительность АФК обусловлена скоростью, с которой в клетке протекают электрохимические реакции. Они также продемонстрировали эффективность выше 60% в космических приложениях.
Основной проблемой топливных элементов этого типа является то, что они подвержены отравлению двуокисью углерода (CO2). На самом деле, даже небольшое количество CO2 в воздухе может существенно повлиять на производительность и долговечность клеток из-за образования карбонатов. Щелочные элементы с жидкими электролитами могут работать в режиме рециркуляции, что позволяет проводить регенерацию электролита, чтобы уменьшить влияние образования карбонатов в электролите, но режим рециркуляции создает проблемы с шунтирующими токами. Системы с жидким электролитом также страдают от дополнительных проблем, включая смачиваемость, повышенную коррозию и трудности при работе с перепадами давления. Топливные элементы с щелочной мембраной (AMFC) решают эти проблемы и менее восприимчивы к отравлению CO2, чем AFC с жидким электролитом. Тем не менее, CO2 по-прежнему влияет на производительность, а производительность и долговечность AMFC по-прежнему отстают от PEMFC. AMFC рассматриваются для приложений в масштабе от Вт до кВт. Проблемы для AMFC включают устойчивость к углекислому газу, проводимость и долговечность мембраны, работу при более высоких температурах, управление водой, удельную мощность и анодный электрокатализ.
Фосфорнокислотные топливные элементы
Топливные элементы на фосфорной кислоте (PAFC) используют жидкую фосфорную кислоту в качестве электролита — кислота содержится в матрице карбида кремния с тефлоновой связкой — и пористые угольные электроды, содержащие платиновый катализатор. Электрохимические реакции, происходящие в клетке, показаны на диаграмме справа.
PAFC считается «первым поколением» современных топливных элементов. Это один из наиболее зрелых типов клеток и первый, который будет использоваться в коммерческих целях. Этот тип топливных элементов обычно используется для стационарной выработки электроэнергии, но некоторые PAFC использовались для питания больших транспортных средств, таких как городские автобусы.
PAFC более устойчивы к примесям в ископаемом топливе, преобразованном в водород, чем элементы PEM, которые легко «отравляются» монооксидом углерода, поскольку монооксид углерода связывается с платиновым катализатором на аноде, снижая эффективность топливного элемента. PAFC имеют эффективность более 85% при совместном производстве электроэнергии и тепла, но они менее эффективны только при производстве электроэнергии (37–42%). Эффективность PAFC лишь немного выше, чем у электростанций, работающих на сжигании топлива, которые обычно работают с КПД около 33%. PAFC также менее мощны, чем другие топливные элементы, при том же весе и объеме. В результате эти топливные элементы обычно большие и тяжелые. PAFC также дороги. Они требуют гораздо более высоких загрузок дорогого платинового катализатора, чем другие типы топливных элементов, что повышает стоимость.
Топливные элементы с расплавленным карбонатом
Топливные элементы с расплавленным карбонатом (MCFC) в настоящее время разрабатываются для электростанций, работающих на природном газе и угле, для электроэнергетических, промышленных и военных применений. MCFC представляют собой высокотемпературные топливные элементы, в которых используется электролит, состоящий из расплавленной смеси карбонатных солей, взвешенных в пористой, химически инертной керамической матрице из оксида лития и алюминия. Поскольку они работают при высоких температурах 650 ° C (примерно 1200 ° F), недрагоценные металлы могут использоваться в качестве катализаторов на аноде и катоде, что снижает затраты.
Повышенная эффективность – еще одна причина, по которой MCFC обеспечивают значительное снижение затрат по сравнению с топливными элементами на основе фосфорной кислоты. Топливные элементы с расплавленным карбонатом в сочетании с турбиной могут достигать эффективности, приближающейся к 65%, что значительно выше, чем 37–42% эффективности установки на топливных элементах с фосфорной кислотой. Когда отработанное тепло улавливается и используется, общая эффективность использования топлива может превышать 85%.
В отличие от щелочных, фосфорнокислотных и PEM-топливных элементов, MCFC не требуют внешней установки риформинга для преобразования таких видов топлива, как природный газ и биогаз, в водород. При высоких температурах, при которых работают MCFC, метан и другие легкие углеводороды в этих видах топлива преобразуются в водород внутри самого топливного элемента в процессе, называемом внутренним риформингом, который также снижает стоимость.
Основным недостатком современной технологии MCFC является долговечность. Высокие температуры, при которых работают эти элементы, и используемый агрессивный электролит ускоряют разрушение компонентов и коррозию, сокращая срок службы элементов. В настоящее время ученые изучают коррозионно-стойкие материалы для компонентов, а также конструкции топливных элементов, которые удваивают срок службы элемента по сравнению с нынешними 40 000 часов (~ 5 лет) без снижения производительности.
Твердооксидные топливные элементы
Твердооксидные топливные элементы (ТОТЭ) используют твердый непористый керамический компаунд в качестве электролита. Эффективность ТОТЭ составляет около 60% при преобразовании топлива в электричество. В приложениях, предназначенных для улавливания и использования отработанного тепла системы (когенерация), общая эффективность использования топлива может превышать 85%.
ТОТЭ работают при очень высоких температурах — до 1000°C (1830°F). Работа при высоких температурах устраняет необходимость в катализаторе из драгоценных металлов, что снижает стоимость. Это также позволяет ТОТЭ проводить внутренний риформинг топлива, что позволяет использовать различные виды топлива и снижает затраты, связанные с добавлением в систему риформинг-установки.
ТОТЭ также являются наиболее устойчивыми к сере типами топливных элементов; они могут переносить на несколько порядков больше серы, чем другие типы клеток. Кроме того, они не отравляются угарным газом, который даже можно использовать в качестве топлива. Это свойство позволяет ТОТЭ использовать природный газ, биогаз и газы, полученные из угля. Работа при высоких температурах имеет недостатки. Это приводит к медленному запуску и требует значительной тепловой защиты для удержания тепла и защиты персонала, что может быть приемлемо для коммунальных приложений, но не для транспорта. Высокие рабочие температуры также предъявляют строгие требования к долговечности материалов. Разработка недорогих материалов с высокой прочностью при рабочих температурах ячейки является ключевой технической задачей, стоящей перед этой технологией.
В настоящее время ученые изучают возможность разработки низкотемпературных ТОТЭ, работающих при температуре 700°C или ниже, которые имеют меньше проблем с долговечностью и стоят меньше. Однако ТОТЭ с более низкой температурой еще не сравнимы по характеристикам с высокотемпературными системами, и материалы пакета, которые будут работать в этом более низкотемпературном диапазоне, все еще находятся в стадии разработки.
Реверсивные топливные элементы
Реверсивные топливные элементы производят электричество из водорода и кислорода, а в качестве побочных продуктов вырабатывают тепло и воду, как и другие топливные элементы. Однако обратимые системы топливных элементов также могут использовать электричество от солнечной энергии, энергии ветра или других источников для разделения воды на кислород и водородное топливо посредством процесса, называемого электролизом.