Какие бывают виды припоя для пайки. Чем отличаются мягкие и твердые припои. Как выбрать припой для меди, алюминия и других металлов. Какие характеристики припоя важно учитывать при выборе.
Основные виды и классификация припоев
Припои для пайки классифицируются по нескольким основным признакам:
- По температуре плавления:
- Мягкие (до 300°C)
- Твердые (выше 300°C)
- По основному металлу в составе:
- Оловянные
- Свинцовые
- Медные
- Серебряные
- Алюминиевые
- По форме выпуска:
- Проволока
- Прутки
- Паста
- Лента
Выбор конкретного вида припоя зависит от материала соединяемых деталей, требуемой прочности соединения, условий эксплуатации и других факторов.
Мягкие и твердые припои: в чем разница?
Мягкие и твердые припои отличаются температурой плавления и прочностью получаемого соединения:
Мягкие припои:
- Температура плавления до 300°C
- Прочность на растяжение 16-100 МПа
- Основа — олово, свинец, висмут, кадмий
- Используются для пайки тонких деталей и электроники
Твердые припои:
- Температура плавления выше 300°C
- Прочность на растяжение 100-500 МПа
- Основа — медь, серебро, никель, цинк
- Применяются для прочных соединений, работающих при высоких температурах
Какой тип выбрать? Мягкие припои подходят для бытовых задач, электроники, радиотехники. Твердые — для силовых конструкций, труб под давлением, высокотемпературных узлов.
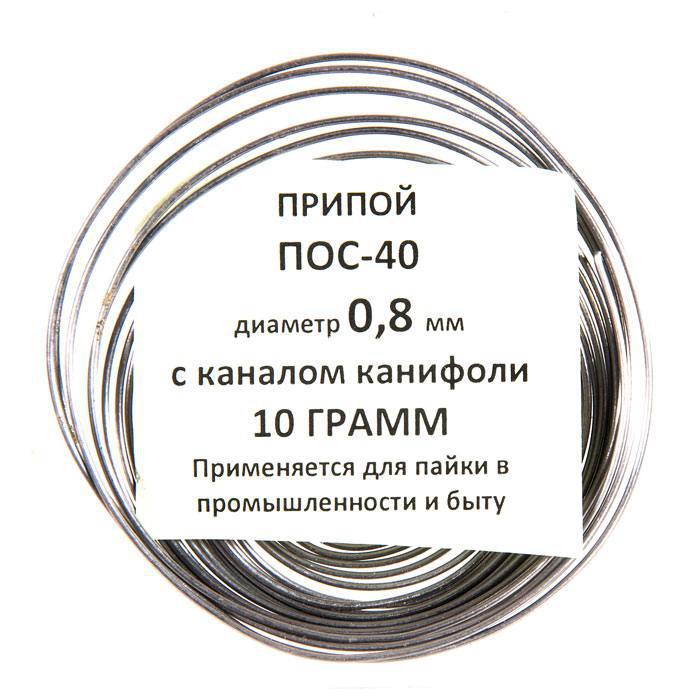
Припои для пайки меди: особенности и популярные марки
Для пайки медных изделий и труб чаще всего используются следующие виды припоев:
ПОС-61
- Состав: 61% олова, 39% свинца
- Температура плавления: 190°C
- Применение: электротехника, радиотехника
ПОССр
- Состав: олово, свинец, 2-3% серебра
- Температура плавления: 180-230°C
- Применение: ответственные соединения в электронике
ПМЦ-36
- Состав: медь, цинк
- Температура плавления: 825°C
- Применение: пайка медных труб в сантехнике
Для пайки меди важно подобрать припой с хорошей адгезией к меди и коррозионной стойкостью. Добавки серебра повышают прочность и пластичность соединения.
Какой припой выбрать для пайки алюминия?
Пайка алюминия имеет свои особенности из-за образования оксидной пленки. Для этого металла рекомендуются специальные припои:
AL-Cu-Si
- Состав: алюминий, медь, кремний
- Температура плавления: 525-585°C
- Особенности: высокая прочность соединения
ZnAl
- Состав: цинк, алюминий
- Температура плавления: 380-450°C
- Особенности: хорошая коррозионная стойкость
Силумин
- Состав: алюминий, кремний
- Температура плавления: 575-630°C
- Особенности: высокая жидкотекучесть
При пайке алюминия крайне важно тщательно очистить поверхность от оксидной пленки и использовать специальные флюсы.

Бессвинцовые припои: экологичная альтернатива
В связи с ужесточением экологических требований все большее распространение получают бессвинцовые припои. Каковы их особенности?
- Основные компоненты: олово, медь, серебро, висмут, индий
- Более высокая температура плавления (около 220-230°C)
- Меньшая пластичность по сравнению со свинцовыми
- Более высокая стоимость
- Экологическая безопасность
Популярные марки бессвинцовых припоев: SAC305 (Sn-Ag-Cu), SN100C (Sn-Cu-Ni), Innolot (Sn-Ag-Cu-Bi-Sb-Ni). Они активно применяются в электронике и производстве бытовой техники.
Как правильно выбрать припой для пайки?
При выборе припоя следует учитывать несколько ключевых факторов:- Материал соединяемых деталей
- Требуемая прочность соединения
- Рабочая температура узла
- Условия эксплуатации (влажность, вибрации и т.д.)
- Метод пайки (паяльник, газовая горелка, печь)
Важно помнить, что температура плавления припоя должна быть ниже температуры плавления соединяемых материалов. Для ответственных соединений рекомендуется использовать припои с добавками серебра или других легирующих элементов.
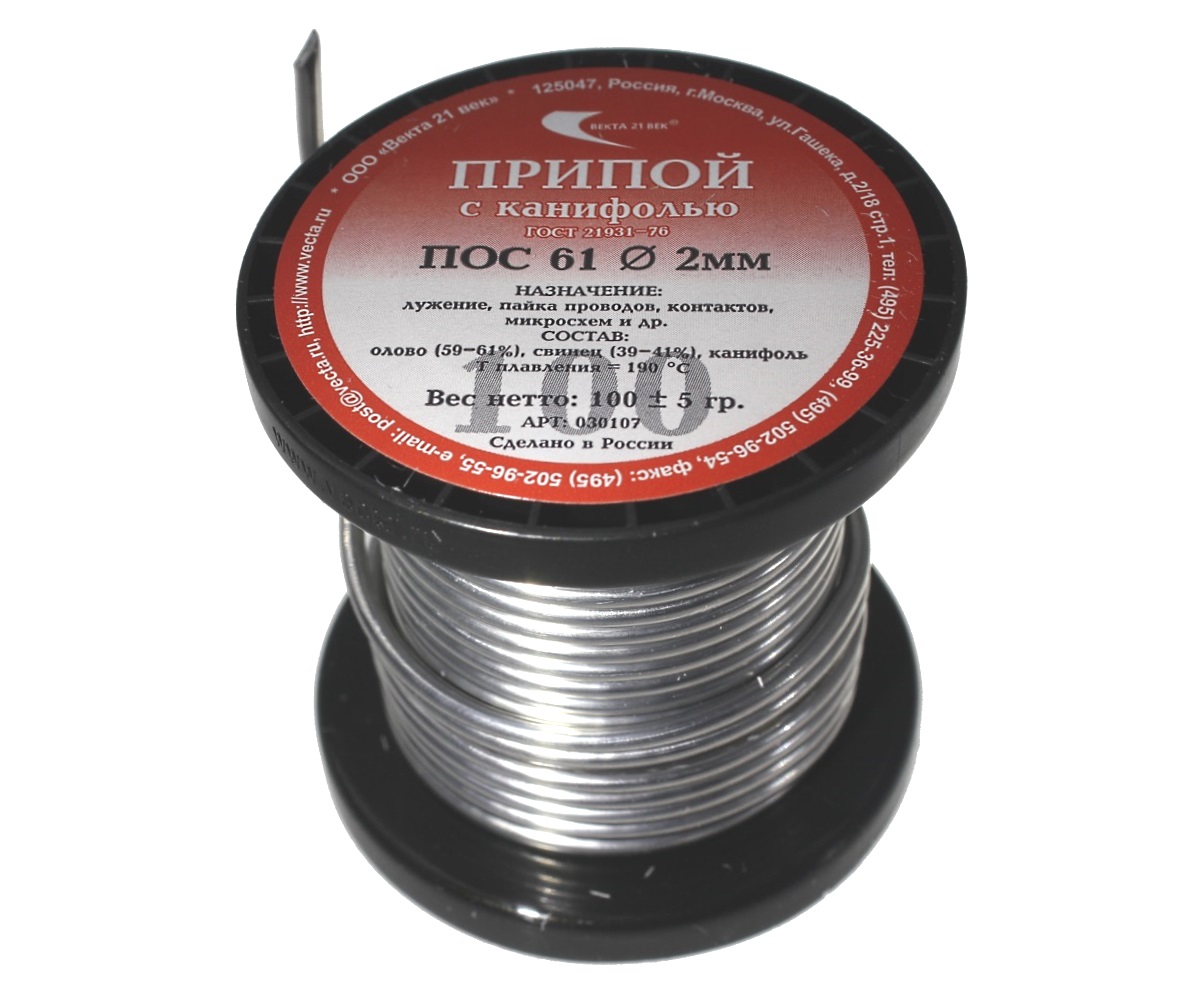
Флюсы для пайки: назначение и виды
Флюсы играют важную роль в процессе пайки. Каковы их основные функции?
- Очистка поверхности металла от оксидов
- Снижение поверхностного натяжения припоя
- Защита от окисления в процессе пайки
- Улучшение растекания припоя
Основные виды флюсов:
- Канифольные (для электроники)
- Кислотные (для пайки стали, меди)
- Безотмывочные (не требуют удаления после пайки)
- Активированные (для трудно паяемых металлов)
Выбор флюса зависит от материала деталей и типа припоя. Неправильно подобранный флюс может привести к коррозии или некачественному соединению.
Техника безопасности при работе с припоями
При работе с припоями необходимо соблюдать следующие меры безопасности:
- Использовать средства индивидуальной защиты (перчатки, очки, респиратор)
- Обеспечить хорошую вентиляцию рабочего места
- Не допускать контакта припоя и флюса с кожей и глазами
- Не вдыхать пары, образующиеся при пайке
- Соблюдать правила пожарной безопасности
- Хранить припои и флюсы в недоступном для детей месте
Особую осторожность следует проявлять при работе со свинецсодержащими припоями из-за их токсичности. После работы необходимо тщательно вымыть руки.
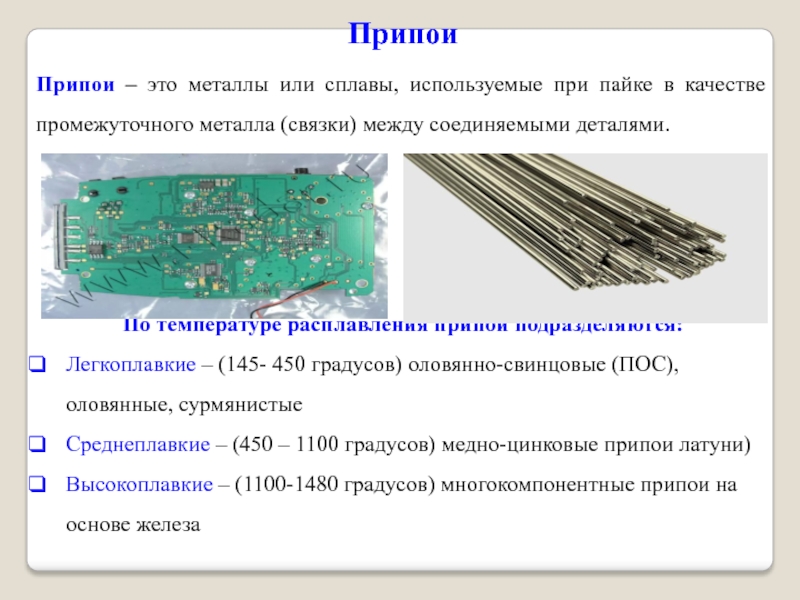
Заключение
Выбор правильного припоя — ключевой фактор успешной пайки. Современный рынок предлагает широкий ассортимент припоев для различных задач и материалов. Понимание особенностей разных видов припоев позволяет подобрать оптимальный вариант для конкретной задачи, обеспечив надежное и долговечное соединение.
Оловянно-свинцовые припои: виды и характеристики
Оловянно-свинцовые припои: виды и характеристикиЧто такое припой знает каждый, кто хоть единожды пытался соединить металлические детали с помощью пайки. Но о том, что припои бывают разные и самый популярный из них известен под маркировкой «ПОС», известно далеко не всем.
Рассмотрим, какие бывают припои для пайки меди, алюминия и других металлов, на сайте svarkapajka.ru
ПОС — легкоплавкий оловянно-свинцовый припой. Сплав из олова и свинца образует эвтектическую смесь, отличающуюся более низкой температурой плавления, нежели каждый металл по отдельности. Именно это качество позволяет сплаву соединять различные металлы.
В настоящее время существует множество разных марок ПОС: бессурьмянистые, малосурьмянистые, сурьмянистые, сплавы с кадмием, медью или висмутом. Разное соотношение компонентов в сплавах обусловливает их различные характерные особенности.
Разнообразие марок
Припойная продукция выпускается в различных формах, это могут быть литые чушки, проволока, порошок, паста, ленты из фольги или трубки с флюсом внутри. Все припои ПОС производятся в соответствии с ГОСТом и имеют различные характеристики в зависимости от процентного соотношения компонентов.
Цифры в маркировке припойных смесей говорят о количестве в их составе олова. Поскольку температура плавления и прочность припоя напрямую зависят именно от него. Так, например, ПОС-90 состоит из 9 частей олова и 1 части свинца.
Плавится состав при 220°C и используется для пайки металлических деталей перед гальванизацией золотом или серебром. А ПОС-40, где оловянная составляющая представлена 40%, плавится при температуре 222°C.
Чаще всего специалисты применяют припой с маркировкой 61. Его популярность обусловлена более низкой температурой плавления (около 190 градусов) и достаточной прочностью.
Сплавы с сурьмой
Маркировка «ПОСсу» говорит о том, что в оловянно-свинцовую композицию введено небольшое количество сурьмы. Чем больше её в сплаве, тем выше температура его плавления. Добавление сурьмы делает припой дешевле, но паять таким сплавом труднее, поэтому обычно с этим расходным материалом работают только профессионалы.
Сотые доли процента сурьмы имеют малосурьмянистые марки, они начинают плавиться при 189 градусах и используются при производстве холодильников, авиа- и автоприборов, посуды для приготовления еды.
Сурьмянистые припои для пайки содержат 1,5 — 6,0 % сурьмы. Их применяют в трубчатых радиаторах, электрических лампах, а так же для пайки белой жести.
Маркировка ПОСК
Большую прочность шва при низкой температуре плавления (145°C) могут обеспечить припои с маркировкой ПОСК.
В составе такого сплава присутствует кадмий. Обычно ПОСК используют в работе с металлизированными и керамическими изделиями.
Именные припои
В числе оловянно-свинцовых припоев можно встретить композиции, названные в честь учёных, их разработавших. Так, эвтектический сплав Розе состоит из 50% висмута и равных частей олова и свинца и плавится при 94°C. Такой припой используют для пайки медных деталей и при изготовлении изделий с постоянной эксплуатационной температурой.
Припой Вуда имеет температуру плавления 68,5 градусов Цельсия. В его составе половину занимает висмут, четверть — свинец, остаток — в равных долях олово и кадмий. Используется припой Вуда в изготовлении прецизионных (высокоточных) инструментов и чувствительных датчиков.
Для паяния легкоплавких металлов используют сплав Д’Арсе, расплавляющийся при 79 градусах и содержащий всего 1 часть олова, остальные 9 состоят из равного количества свинца и висмута.
что это такое, температура плавления, с канифолью, бессвинцовый, ПОС, сплав, оловянный, РОЗЕ – Оборудование для пайки на Svarka.guru
При изготовлении и ремонте электротехники постоянно требуются навыки обращения с паяльником, а для спайки используют припой и канифоль, в середине прошлого века для этих целей использовалось олово, но не в чистом виде, т. к. это весьма дорогое удовольствие, а сплавы с другими легкоплавкими металлами.
Какие встречаются?
Что же такое припой и как надо правильно его выбирать — на практике они могут быть мягкими или твёрдыми.
Компоненты неизвестного происхождения отличается по следующим признакам:
- Насыщенный блеск среза говорит о высоком присутствии олова.
- Преобладание свинца гарантирует субстанции тускло-серый цвет и матовую поверхность.
- При повышенном содержании свинца изделие становится пластичным, например, проволока сечением в 6 мм без видимого услия сгибается руками.
Иногда для качественной пайки применяется уже готовая смесь — это припой в виде проволоки, а флюс запаян внутри. Производители изготавливают аналогичные субстанции с допуском флюса в пределах 1—3% от общего веса, что благоприятно сказывается на процессе пайки и увеличивает производительность труда, т. к. отпадает необходимость постоянно макать жало паяльника в баночку с флюсом.
По консистенции выпускаются двух видов: мягкий или твердый припой, а по температуре плавления различают обыкновенные и тугоплавкие типы.
Основные свойства
Смачиваемость пайки
Такой термин означает сцепление молекул жидкого расплава с твёрдой поверхностью, от степени которой зависит текучесть пайки. Для хорошей пайки жидкий припой качественно смачивает поверхность, где происходит пайка, а граница его образует острый угол.
Высохший флюс удаляется только при помощи механической зачистки, потому что появился дополнительный сплав. Если капля расплавленного вещества образует тупой угол с поверхностью, то это указывает на неудовлетворительное качество смачивания, которому противодействуют загрязнения, жировые пятна или оксидная плёнка металла.
Варианты смачиваемости поверхности пайки расплавленным флюсом.Температура плавления
Основной критерий выбора качественных сплавов заключается в том, что они должны приходить в жидкое состояние раньше, чем соединяемые структуры, при этом температура плавления припоя существенно отличается от аналогичного показателя другого вида, например, имеющего в составе примеси свинца.
Наличие разных примесей влияет на способность плавиться при одинаковой температуре, например, ПОС-40 расплавляется при достижении 238 0С, но встречаются тугоплавкие припои и для их плавления применяются специальные приспособления.
Низкотемпературные варианты
На первом месте находится сплав ВУДА с составом: по 10% Sn и Cd, по 40% Pb и Bi, начало расплава — 65—72 0C. Вторую позицию занимает припой под названием РОЗЕ, которых начинает плавиться при 90—94 0C. Состоит: по 25% олова и свинца, а остальные 50% занимает висмут. Вышеперечисленные сплавы относятся к дорогим припоям.
Третье место среди низкотемпературных изделий занимает ПОСК-50-18, с температурой 142—145 0С. В состав этого припоя входит 50% олова, 32% свинца и 18% кадмия, что усиливает сопротивляемость коррозии, но добавляет ему токсичность.
Большую популярность у радиолюбителей имеет второй номинант (под названием РОЗЕ), но в отечественной радиоэлектронике его маркировка — ПОСВ-50, где цифры — это процент висмута. Применяется для монтажа/демонтажа и лужения чувствительных к перегреву дорожек из меди на печатных платах.
Марки мягкого вида
Припой для пайки из этой категории применяется с уже готовым флюсом, находящимся внутри проволоки, поэтому расплавление происходит одновременно. Большое распространение получило изделие с названием Третник, потому что в нём содержится треть свинца от общей величины состава. Олово, входящее в состав сплава для пайки, отличается чистой в плане экологии, поэтому разрешается применение этого вида в пищевой промышленности.
Мягкие виды припоев применяются для пайки деталей, боящихся перегрева, например: транзисторов или предохранителей. Сплав ВУДА из-за токсичности применяется в ограниченных сферах человеческой деятельности.
Отечественные сплавы маркируются аббревиатурой ПОС, но при наличии других веществ в конце добавляется буква, соответствующая названию, например, ПОСВ-33 — этот припой содержит равные части олова, свинца и висмута.
Основные технические параметры
Материалы для пайки разделяют по таким параметрам:
- Проводимость, например, припои с содержанием алюминия обладают лучшими аналогичными значениями, нежели с маркировкой ПОС.
- Прочность на усилие растяжения, единица измерения кг/мм. Этот параметр напрямую зависит от процентного содержания олова.
- Температура плавления, которая зависит химического состава.
Флюс
В продаже распространён припой с канифолью в виде полой проволоки, свитой кольцами. Аналогичного состава флюс производится из хвойных деревьев, такая субстанция приходит в мягкое состояние при нагревании до 50 °С, а при 250 °C — начинает кипеть с частичным испарением. Канифоль нужно обязательно удалять после окончания работ, иначе произойдёт окисление, а субстанция, впитывая влагу из воздуха, начнёт препятствовать исправной работе приборов.
Популярные составы
Существуют три основных категории:
- Светлого цвета канифоль применяют при соединении меди и других мягких цветных металлов; спиртовой раствор с концентрацией один к пяти применяют в труднодоступном месте спайки; а смесь глицерина и канифоли применяют для герметичной пайки.
- Флюсы, включающие спирт, вазелин или хлористый цинк, используются для прочного соединения цветных и драгоценных металлов. Применение пасты оправдано тем, что её удобнее наносить в требуемом количестве на изделие.
- Кислотно активные вещества производятся в жидком виде, например, ортофосфорная кислота, имеющая плотность 1,7.
[stextbox id=’alert’]Хранить жидкие флюсы надо в герметически закрывающихся ёмкостях, для исключения испарения.[/stextbox]
Пастообразные
Большое распространение получила паста Тиноль, которая применяется для пайки разных изделий в труднодоступных местах. Наносится лопаткой, с последующим активным нагреванием паяльником или другим, более мощным электрическим инструментом.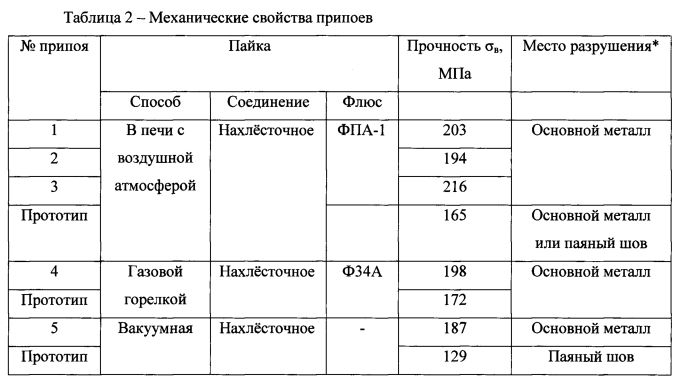
Использование ПОС
Первооткрыватели этого сплава были приятно удивлены, что он превращается в расплавленное состояние при меньшей температуре, а эвтектическая смесь способна играть роль растворителя для добавленного металла. Так и были разработаны самые первые марки припоев ПОС.
Свинцовые варианты
Такие смеси с содержанием свинца, отличаются мягкостью, быстрым расплавлением и лёгкой обработкой, поэтому получили название свинецсодержащие припои. Они вредны, поэтому были запрещены для использования во время спайки элементов электрических приборов по всему миру. Процент содержание кадмия, ртути, а также аналогичных вредоносных компонентов в оборудовании строго регламентировано и проверяется соответствующими организациями.
Без содержания свинца
Бессвинцовый припой не должен содержать вредного металла и считается экологически чистым, не причиняющим вреда окружающей среде и исполнителям работ по пайке. Простейшим примером служит припой оловянный, который содержит чистое олово, имеет повышенную смачиваемость и высокую электропроводность. Для борьбы с недостатками, в них добавляют медь, серебро и золото, что помогает сделать субстанцию более твёрдой.
У такого изделия повышается температура расплавления, но найти полную альтернативу стандартным видам припоя пока что не удаётся, но основным показателем является безвредность. Олово занимает главное место в химическом составе, поэтому присущие ему свойства оказывают большое влияние на припой, из-за этого температура плавления у бессвинцового припоя ниже, а материал получается более мягким.
[stextbox id=’info’]В. И. Блинов, образование ПТУ, специальность сварщик шестого разряда, допуск от НАКС к НГДО и ГО, опыт работы с 2004 года: «При отсутствии подходящего по всем параметрам варианта, во время пайки используйте марку ПСР-45, в которой содержание вредного свинца минимальное и составляет не более 0,5% от общего веса». [/stextbox]
Колофонская смола
Именно так называется общеизвестная канифоль — аморфное вещество с характерным изломом и стеклянным блеском сколов. Кроме того, что она обладает природным свойством диэлектрика, известны и такие особенности:
- хорошо растворяется в бензине, спирте, эфире и ацетоне, но остаётся безразличной к воздействию воды;
- температура плавления варьируется в пределах 50—70 градусов, но иногда повышается до 130 0C;
- в химическом составе присутствует до 90% смоляных кислот, основой является абиетиновая кислота;
- легко разрушается при незначительном механическом воздействии.
Цвет изменяется от светло-жёлтого до тёмно-бурого оттенков, что зависит от степени очистки и указывает на количество посторонних примесей. Отличные электроизоляционные свойства принадлежат смоле с лимонным окрасом.
Секреты выбора
Задача любого исполнителя состоит в создании крепкого и надёжного закрепления на плате радиодеталей, поэтому подбор припоя выполняется согласно следующим параметрам:
- Состав материалов, подвергающихся пайке — здесь надо учитывать характеристики материала, его способность к перегреву и многое другое.
- При пайке проводов или других крупных предметов применяются тугоплавкие припои.
- Иногда нужно применить припой, обладающий высокой способностью к проведению электрического тока, надо учитывать, что сопротивление олова намного меньше, чем у свинца, поэтому для спайки высокочастотных плат применяют дорогостоящие марки припоя.
В каждой конкретной ситуации исполнитель должен чётко знать соответствие припоя и соединяемого изделия, чтобы выбрать оптимальный вариант для качественной пайки.
Выводы
Сегодня в продаже встречается изобилие разных припоев, как говорится, на все случаи жизни, но выбирать следует проверенные образцы, которые помогут спаять изделие качественно и с высокой надёжностью при эксплуатации.
Классификация, виды и марки припоев для пайки медных труб, проводов
При операциях по соединению металла используются различные способы. Если нет возможности применить сварку, то в качестве альтернативы используют пайку, если речь идет об относительно тонких изделиях и не крупных поломках. Несмотря на то, что в обоих случаях в качестве основного присадочного материала используется металлические сплавы, в пайке основной металл не расплавляется. Тем не менее, для качественного проведения процесса следует использовать различные виды припоев, причем для каждой разновидности металла нужно подбирать отдельную марку материала наплавки.
Виды припоев для пайки
Их классификация происходит по тому, для пайки чего они предназначаются. Ведь в промышленности и в частной сфере встречается масса сплавов со своими особенностями. Также здесь учитывается температура, в которой будет эксплуатироваться изделие, какие механические и вибрационные нагрузки на него возлагаются, будет ли контакт с человеком и так далее. Все эти и многие другие факторы создают большое количество марок для каждого металла. Различные виды припоев для пайки используются для заделки трещин в трубах, для чего нужно сопротивление коррозии, соединения проводов, тут требуется высокая электропроводимость, соединения металла подобно сварке, где нужна высокая прочность и так далее. Различные виды припоев для пайки производятся по ГОСТ 21931-76.
Классификация
Классификация припоев происходит по нескольким основным признакам. В первую очередь они делятся на мягкие и твердые. К мягким относятся те марки к которых температура плавления достигает 300 градусов Цельсия. Максимальный предел прочности на растяжения в таком случае составляет 100 Мпа, тогда как минимальный только 16 МПа. К ним причисляются сплавы из свинца, олова, кадмия цинка, сурьмы и прочих легкоплавных металлов, в том числе и бессвинцовые припои.
К твердым относятся те марки, у которых температура плавления выше 300 градусов Цельсия. Это повышает и предел прочности на растяжение, так как минимальное значение тут составляет около 100 МПа, а максимальное значение может достигать 500 Мпа. Это сплавы меди, цинка, никеля, серебра и прочих металлов, у которых высокая температура плавления.
Твердый припой для пайки
Помимо этого есть разделение на то, какой именно основной металл содержится в составе присадочного материала. Это может быть:
Также стоит выделить в отдельный класс флюсованные марки, внутри которых содержится флюс, соответственно, им не требуется его дополнительное применение.
По вариантам поставки выделяются:
- Стержни – небольшие плотные элементы, которые расплавляются паяльником;
- Проволока – хорошо подходит как для газовой пайки, так и для паяльника;
- Трубчатые – выполняется в виде трубки, внутри которой зачастую располагается флюс;
- Листы – тонкие листы сплава, которые подходят как для пайки плоских поверхностей, так и для других целей.
Существуют различные технологии производства, которые также создают разные марки припоев для пайки. Среди них выделяются тянутые, измельченные, литые, прессованные, спеченные, штампованные, аморфные и катанные.
Виды припоев для пайки медных труб и проводов
Виды припоев для пайки медных жил и труб выглядят следующим образом:
Марка | Характеристика |
1S | Мягкий сплав в состав сплава которого входит серебро.![]() |
Rosol 3 | Мягкий сплав для соединения которым нужно использовать флюс. Температура плавления такого материала составляет 240 градусов Цельсия. Они применяют для сварки труб и проводов из меди. Также хорошо взаимодействует с тонкими металлами. |
Rolot 94 | Твердый припой. Материал высокого качества пайки, что предназначен для капиллярной и щелевой пайки труб, у которых нет фитинга. Помимо меди хорошо соединяется с красной бронзой и латунью. Температура плавления составляет от 730 градусов Цельсия, что предполагает использование только с толстыми заготовками. У него достаточно большой интервал между температурой плавления и кипения. |
Rolot 2 | Твердый припой.![]() |
Виды припоев для пайки алюминия
Марка | Характеристики |
Авиа 1 | Используется практически для всех сплавов из алюминия и является универсальным расходным материалом. Благодаря низкой температуре плавления подходит для соединения проводов. Это мягкий сплав, температура плавления которого до 200 градусов Цельсия. Основой является олово (55%), а также в него входит цинк (25%) и кадмий (20%). |
Castolin 190 | Флюсованный твердый сплав, температура плавления которого составляет 580 градусов Цельсия. Используется как для соединения алюминиево-медных сплавов, так и для чистого алюминия. Состав обладает высокой текучестью и адгезией. Применяется для таких видов как капиллярное спаивания, так и с зазором. Марку часто используют для ремонта электроники и бытовой техники.![]() |
Вилы припоев для пайки нержавейки
Марка | Характеристика |
HTS528 | Универсальный присадочный материал, подходящий для всех процедур по спаиванию нержавеющей стали различных сортов. Это твердый припой, температура плавления которого составляет 760 градусов Цельсия. Материал имеет флюсовое покрытие, которое придает ему красный цвет. Размер одного прутка составляет 45 см при весе в 20 грамм. |
П-81 | Это твердый припой, температура плавления которого составляет 650 градусов Цельсия. Припой часто используется профессионалами для ремонта. В составе встречается нержавеющая сталь, чугун, никель, серебро и прочее. Предел прочности наплавленного материала составляет 170 МПа. Поставляется в прутках по 59 см и диаметром около до 3 мм. |
Выбор припоя
При подборке припоя нужно обращать внимание на температуру плавления материала. Она должна быть ниже, чем этот же показатель у основного материала, иначе он будет расплавляться, что приведет к изменению структуры. Но тут стоит учитывать и особенности эксплуатации, так как при низкой температуре плавления состав не сможет выдержать высокотемпературные режимы использования. Здесь уже больше подойдут твердые марки.
Также важен основной материал. Но здесь не всегда идет полное соответствие, как в сварке. К примеру, виды припоев для пайки медных проводов будут содержать медь в своем составе, но для пайки алюминия могут использоваться припои, в которых нет алюминия.
«Важно!
При работе с алюминием нужно осуществлять дополнительную обработку.»
Для длительных операций, когда нужно много паять, лучше подбирать материал в длинных прутках, чтобы лишний раз не прерывать температурную обработку. Для домашней сферы лучше всего подходят проволочные припои и аморфные, так как их применение происходит периодически и в малых количествах.
Виды припоя для пайки
При выполнении пайки металла неизменно возникает необходимость использования специальных припоев, которые позволяют надежно и качественно соединять металлические элементы. Следует сказать, что выбор тех или иных видов припоя зависит от технологии пайки и разновидности соединяемых металлов. Расскажем поподробнее о видах таких припоев и дадим рекомендации по их выбору.
Припой принято классифицировать в зависимости от вида материала, для работы с которым они предназначаются. В зависимости от рабочего металла различается температура пайки, а, следственно, и эксплуатационные характеристики такого вида припоя. При условии правильного выбора можно будет гарантировать качественное и долговечное соединение металлических элементов, а также отсутствие коррозии на месте соединения. Разнообразные виды припоев могут применяться для заделки имеющихся трещин в трубах, соединения проводов, сварки металла и так далее. Требования к таким соединительным элементам устанавливает ГОСТ, что и позволяет с легкостью выбирать те или иные припои для пайки.
Существующая классификация
На сегодняшний день имеется несколько основных характеристик, по которым принято различать припой. Их разделяют на твердые разновидности и мягкие. Так, например мягкий припой может применяться для соединения металлических элементов, температура пайки которых не превышает 300 градусов. Показатели предела прочности в данном случае составляют порядка 100 МПа. К такому мягкому припою относятся сплавы из сурьмы, цинка, олова, других легкосплавных металлов.
Твердая разновидность выполняется из металлических сплавов, с температурой плавления более 300 градусов. В данном случае обеспечивается максимально возможное значение предела прочности.
Имеется также классификация такого присадочного материала, который содержится в металле. Принято различать в соответствии с данной классификации следующий припой:
- Алюминиевый.
- Медные сплавы.
- Оловянный.
- Серебряный.
Отметим, что принято выделять отдельный класс плюсовых припоев, которым не требуется присадочный материал.
В зависимости от варианта поставки принято классифицировать на:
- Листы, которые выполнены в виде тонких листов сплава. Такие присадки подходят для спаивания тонких плоских поверхностей.
- Трубчатые обычно изготавливаются из флюса, имеют вид трубки с расположенным внутри основным материалом.
- Проволочные отлично подходят для паяльника или газовой пайки.
- Стержни представляют собой небольшие плотные элементы, которые в процессе работы расплавляются паяльником.
Существуют также катаные, аморфные, штампованные, прессованные и измельченные марки, однако они не получили должного распространения, что объясняется сложностью работы с ними и их узкой специализацией.
Припой для спаивания медных труб
Для соединения элементов из меди можно использовать следующий припой:
- Марка 1S. Мягкий сплав, содержащий небольшое количество серебра. Возможно использование такой марки с медными трубами, бронзовыми изделиями и другими высокотемпературными сплавами.
Из отличительных особенностей таких припоев можем отметить их великолепную коррозийную стойкость и способность выдерживать высокую температуру. Для повышения показателей прочности соединения можно использовать дополнительно порошковый или обыкновенный флюс.
- Rosol 3. Это мягкая марка, которая подразумевает обязательное дополнительное использование флюса. Применяется такой припой для меди. Отлично взаимодействует с тонкими металлическими сплавами и обеспечивает прочное соединение.
- Rolot 94. Твердый сплав, применяемый для капиллярной пайки. Повышенная прочность таких сплавов позволяет использовать их для соединения труб без применения фитингов. Rolot 94 может использоваться для работы с медью, сплавами латуни и бронзы. Максимальный показатель температуры плавления равняется 730 градусам. Отметим также большой интервал у Rolot 94 между плавлением припоя и кипением. Подобное необходимо учитывать при выполнении пайки.
- Rolot 2. Твердая разновидность припоя относится к узкоспециализированному типу.
В качестве дополнительного элемента используется серебро, что позволяет обеспечить максимальную прочность и качество соединения.
Разновидности для алюминия
- Castolin 190. Качественный флюсованный сплав, с температурой плавления в 580 градусов. Этот припой применяется с алюминиевыми сплавами или же чистым алюминием. Castolin 190 обладает отличной адгезией и текучестью. Этот припой применяется в ремонте техники. Изготавливается он в прутках с длиной в 50 сантиметров.
- Авиа 1. Это универсальный тип припоя для алюминия, поэтому он получил наиболее широкое распространение. Показатели температуры плавления у этого мягкого сплава не превышают двухсот градусов. Этот сплав содержит25% цинка, 55% олова, 20% кадмия.
Припой для работы с нержавейкой
- HTS528. Универсальный тип присадочного материала, который используется для работы с многочисленными сортами стали. Относятся к категории твердых марок, и имеет показатель температуры плавления в 760 градусов.
Отметим наличие флюсового покрытия, придающего припою красный цвет.
- П-81. Твердый сплав с температурой плавления около 650 градусов. Данная разновидность присадочного материала применяется профессионалами при выполнении ремонтных работ. В составе этого сплава можно найти дополнительные включения из никеля, чугуна и нержавеющей стали. Показатель предела прочности наплавляемого материала — 170 Мпа.
Как правильно выбрать припой
При выборе такого присадочного материала необходимо в первую очередь обратить внимание на показатели температуры плавления металла. У припоя этот показатель должен быть ниже, нежели чем у соединяемых элементов. Также вам следует учитывать особенности металлических сплавов и требования к выполненному соединению. Так, например если требуется обеспечить в последующем максимально возможную прочность шва, следует применять твердые марки.
Отметим, что при использовании припоя не всегда выдерживается соответствие основного материала в присадке и соединяемых металлических элементах. Так, например, для сварки меди используется припой, в основе которого содержится медь. А вот для соединения алюминия применяют легкие марки, в составе которых отсутствует алюминий.
Также при выборе припоя необходимо учитывать особенности сварки. Если необходимо соединить металлические элементы длинным швом, то лучше всего использовать припой с максимально возможной длиной. Тем самым вы избегайте прерывания температурной обработки, что в свою очередь повышает качество соединения. Если же вы выбираете припой для использования в домашних условиях, то отлично подойдет аморфная проволока, которая продается в небольших количествах.
что это такое, как и где используется, характеристики и особенности
Как профессионалы, так и любители часто в своей практике используют припои и флюсы для паяния. Добротные красивые швы – одно из главных преимуществ такой пайки.
Существует много видов этих материалов для качественной сварки дома и на производстве. В специализированных местах можно даже найти припой со встроенным внутрь флюсом.
Поэтому тем кто первый раз встречается с подобным видом пайки, бывает сложно выбрать нужные материалы. Чтобы вам помочь, мы расскажем о некоторых видах и как их использовать.
Какие отличия существуют у легкоплавких и тугоплавких припоев? Что мы знаем про слабоактивные и активные флюсы? Как работать с такими материалами? Ответы вы найдёте чуть ниже.
Содержание статьиПоказать
Какие бывают припои
Припой необходим, чтобы заполнить границы между заготовками. Представляет собой прут с содержанием металла. При работе с ним происходит соединение с главным металлом, а в некоторых случаях он сам выступает как ключевой.
Имеет разный диаметр. Основной элемент – олово, но другие элементы также присутствуют в составе. Плюмбум и купрум, к примеру. Два основных вида – это легкоплавкий и тугоплавкий.
Легкоплавкий
Этот вид применяется в основном для работы с мелкими деталями, такими как радиоаппаратура. Если необходимо припаять радиоэлектронные частицы, легкоплавкому припою замены не найти.
В состав, помимо олова, входят такие элементы как кадмий, свинец, висмут, цинк.
Если судить по названию, то сразу приходит понимание, что этот материал лёгок в плавлении. Один паяльник небольшого размера легко может справиться.
Если ваша деятельность связана с радиоэлектронными деталями, вам подойдут прутки, которые плавятся при температуре до ста сорока градусов.
Также есть специальные виды для металлообработки плат. Они плавятся при температуре сто градусов. Лужение с такими материалами может происходить гораздо проще и за меньшее время.
Также припои имеют свои модели, только это довольно большая тема, которая заслуживает своей статьи.
Для нынешнего оборудования подойдёт припой, который не содержит свинец, а температура плавления составляет двести градусов. Это зависит от особенностей оборудования.
Большинство техники производится опираясь на жесткие экологические нормы, которые запрещают применение свинца, из-за выделения им вредных паров.
Тугоплавкий
Тугоплавкий вид припоев – противоположность легкоплавкому. Они плавятся при нагревании в четыреста градусов и более. Этот вид используют профессионалы на производстве, где нужно взаимодействовать с более крупными деталями.
Основа – это медь, серебро, магний, никель. Эти материалы обладают прочностью и толщиной, поэтому с ними не работают в домашних условиях.
С этим видом можно браться за работу с такими тугоплавкими материалами, как латунь или чугун.
Припой с флюсом
Припои с встроенным флюсом представляют свой отдельный вид. Также его называют трубчатым. Выглядит он как пустой прут, внутри которого встроен химикат для защиты.
При плавлении прут плавится, а флюс применяется для защитных функций. Одни из часто используемых моделей – это Brazetec Comet 3476U и Castolin 192 FBK.
Этот тип флюса практичен в использовании, так как вы выполняете паяние и защиту одновременно. Время, которое вы потратили бы на выбор флюса и покрытие им припоя, остаётся свободным.
Но такие типы не всегда защищают максимально хорошо. Если вы гонитесь за качеством, то лучше будет выбрать эти материалы отдельно. А зачем всё-таки нужен флюс, мы поведаем далее.
Какие бывают флюсы
Флюс — это вещества, используемые для удаления оксидов с поверхностей пайки и повышающие уровень качества шва. Флюс работает на эстетику.
Он может сильно изменить вид шва, но помимо этого улучшает качество и гладкость. Он очень важен. Поэтому необходимо выбирать внимательно.
Припой напрямую влияет на флюс. Если припой растапливается с легкостью, то и свойства флюса раскроются хорошо. У защитного материала должна быть маленькая температура при которой он плавится, относительно припоя.
Только в этом случае вы выполните работу качественно. Существует два вида флюсов: активные и слабоактивные.
Активные
В структуру химически активных флюсов входят множество кислотосодержащих веществ. Они необходимы для того, чтобы уничтожать налёт и коррозию.
После работы с флюсом, нужно отчистить зону паяния от остатка, чтобы металл не испортился, и не появилась новая ржавчина.
Активность таких видов это плюс и минус в одно время. Если химикат использовать не правильно, он может разъесть материалы, при работе с радиоаппаратурой.
Также химикат оставляет ожоги на поверхности кожи, поэтому нужно помнить о технике безопасности. Но когда вы выполняете работу правильно, этот вид может послужить вам хорошую службу: удалить налёт и ржавчину, повысит уровень качества.
Химически активные флюсы не для домашней работы. Работа с ними требует большого опыта и внимательности. А при плавлении радиоэлементов лучше не брать этот вид. Так как есть большая вероятность, что он повредит текстолит, а изменить этого вы не сможете.
Слабоактивные
С химикатами подобного типа работать гораздо проще. Окислительные свойства такого флюса не так ярко выражены, поэтому и используют их чаще. Они защищают от жира и засорения, но со ржавчиной уже не справляются.
В структуре такого флюса материалов содержатся органика, поэтому с ними можно паять радиоэлементы.
Пассивные, так же как и активные, производят защиту области паяния от окисления, поднимают уровень качества.
Применение
Материалы предназначены для разных работ, поэтому и техники по эксплуатации будут отличаться. Например, припои приспособлены для заполнения границ между заготовками.
А флюсы необходимы для того, чтобы улучшить шов и сберечь от разъедания покрытия кислотами.
Для того, чтобы эксплуатировать припой, его нужно довести до определённой температуры. При работе с небольшими деталями, нужно приложить его к зоне пайки, а к прутку поднести паяльный аппарат, чтобы он нагрелся и заполнил границы.
Если вы занимаетесь сваркой, вместе паяльника нужно взять газовую горелку.
Работа с отдельным видом припоя со встроенным флюсом, никак не отличается от работы с основными типами, легкоплавкими и тугоплавкими. Припой расплавится, а пары флюса выделятся поверх зоны паяния.
Для эксплуатации флюсов, вы должны разбираться в их консистенции. Если материал жидкий или пастообразный, то его наносят кистью, если сухой, то для этого понадобится специальный аппарат.
Подведем итог
Флюсы и припои эксплуатируют для множества направлений при пайке. Одни необходимы для работы на дому, другие хорошо подходят для производства.
Выбор правильного припоя и флюса важный момент, отталкивайтесь всегда от того, что нужно вам. Если взять правильный вид материалов, это сделает вашу работу легче.
А вы работали с такими материалами раньше? Каким был ваш опыт? Расскажите об этом в комментариях. Продуктивности в работе!
Какие виды припоев используются при изготовлении ювелирных изделий?
- АВТОРИЗОВАТЬСЯ
- ЧЛЕНСТВО
- Сообщество
- Около
- Рекламировать
- Связаться с нами
- Обучающий центр
- Геммология
- Ювелирные изделия и гранильные изделия
- Энциклопедия драгоценных камней
- Курсы
- Членство в IGS для профессионалов и энтузиастов
- Мини-курсы
- Сертификация профессионального геммолога
- Сертификация алмазного специалиста
- Цены
&
Руководства по покупке
- Руководство по ценам на драгоценные камни
- Руководства по покупке драгоценных камней
- Консультации по покупке бриллиантов
- Руководство для начинающих
- Ясность
- цвет
- Караты
- Порез
- 5-й C — Сертификация
- Алмазные формы
- Выбор стиля, настройки и металла кольца
- Источники алмазов
- Факторы затрат, сбережения и финансирование
- Решение, где купить бриллиант
- Бизнес, связанный с драгоценными камнями
- Просмотреть все компании
- Оценки
- Аукционы
- Огранка драгоценных камней
- Обработка драгоценных камней
- Геммологические лаборатории
Эволюция бессвинцовых припоев | IntechOpen
1.
Введение
Принятие в 2003 г. Директивы об ограничении использования опасных веществ 2002/95 / EC (RoHS 1) стало одной из движущих сил, заставивших электронную промышленность искать альтернативы для замены эвтектического сплава олово-свинец (SnPb-6337). которые использовались десятилетиями. RoHS 1 ограничивает содержание Pb менее 1000 частей на миллион по весу в каждом гомогенном материале, включая материал для пайки. SnPb-6337 содержит 37% Pb, элемента с известным вредным воздействием на здоровье человека и окружающую среду.Таким образом, SnPb-6337 необходимо заменить, чтобы соответствовать требованиям RoHS. Pb — лишь одно из шести запрещенных веществ согласно RoHS 1 [1]. Запрещенный список RoHS расширился до 10 в соответствии с Директивой (ЕС) 2015/863 (RoHS 2), которая была опубликована в 2015 году. Полный список запрещенных веществ в RoHS 2 приведен в таблице 1. ПБД и ПБДЭ в основном используются в качестве каркасный замедлитель в пластмассах и шестивалентном хроме используется в хромировании, хромовых покрытиях и грунтовках, а также в хромовой кислоте. DEHP, BBP, DBP и DIBP — это фталаты, которые используются в качестве пластификаторов.Эти вещества редко встречаются в припоях. Из 10 веществ, перечисленных в RoHS 2, только Pb является наиболее опасным веществом для паяльной промышленности. Это объясняет, почему некоторые из нас называют припой, соответствующий требованиям RoHS, бессвинцовым припоем. Хотя соблюдение требований RoHS не может помочь в сокращении отходов электроники, количество которых за последние годы резко возросло, оно помогает минимизировать опасность такого мусора для окружающей среды.
Вещество | Ограничение RoHS |
---|---|
Свинец (Pb) | 1000 ppm / 0.1% |
Ртуть (Hg) | 1000 частей на миллион / 0,1% |
Кадмий (Cd) | 100 частей на миллион / 0,01% |
Шестивалентный хром (Cr 6+ ) | 0,1%|
Полибромированные бифенилы (PBB) | 1000 ppm / 0,1% |
Полибромированный дифениловый эфир (PBDE) | 1000 ppm / 0,1% |
Bis (2-этилгексил) | 1000 ppm / 0,1% |
Бутилбензилфталат (BBP) | 1000 ppm / 0.![]() |
Дибутилфталат (DBP) | 1000 ppm / 0,1% |
Диизобутилфталат (DIBP) | 1000 ppm / 0,1% |
10 Таблица 1.
Директива об ограничении использования опасных веществ 2015/863 (RoHS 2).С 2006 года бессвинцовая пайка является основным направлением в промышленности, поскольку с 1 июля 2006 года вступил в силу RoHS 1. Внесены многие изменения в состав сплава, чтобы соответствовать требованиям паяного соединения с определением бессвинцовой пайки.Олово-медь (SnCu), олово-серебро (SnAg) и олово-серебро-медь (SnAgCu или SAC) являются преобладающими бессвинцовыми припоями, применяемыми в промышленности.
Сплав SAC получил наибольшую известность на начальном этапе перехода от SnPb-6337 к бессвинцовому припою. Одна из причин заключалась в том, что сплав SAC с 3,0% серебра (Ag) и 0,5% меди (Cu), SAC305 был одобрен IPC Solder Value Product Council в качестве предпочтительного варианта для сборки SMT. Помимо SAC305, промышленность также приняла другие сплавы SAC с более высоким содержанием серебра, такие как Sn3.8Ag0.7Cu (SAC387) и Sn4.0Ag0.5Cu (SAC405), которые, как полагают, являются истинно эвтектическими тройными припоями, имеющими единственную точку плавления при 217 ° C. SAC305 — это трехкомпонентный доэвтектический сплав с интервалом плавления 217–219 ° C. Однако высокая стоимость серебра вынуждает промышленность рассматривать другие альтернативы, такие как раствор с низким содержанием серебра, SAC0307, или отсутствие растворов серебра, например SnCuNi (SN100C ® ). Более подробное обсуждение этой темы будет рассмотрено в Разделе 2 этой главы.
Требования к характеристикам паяных соединений ужесточаются для поддержки современной электронизации.Особенно это касается автомобильной промышленности. В современной автомобильной системе все чаще используются передовые электронные компоненты, например, в логическом управлении, переключателях и датчиках. Внедрение электронных компонентов значительно повысило скорость и точность этих систем. Электронизация автомобильных систем, таких как усовершенствованные системы помощи водителю (ADAS), дала потребителю новый уровень опыта вождения. С другой стороны, включение мультимедийной системы в автомобильную систему, которая должна повысить уровень комфорта водителя, еще больше увеличило использование электронных компонентов в автомобиле.Это объясняет, что рост автомобильной электроники в последние годы превысил рост других отраслей [2]. Из-за суровых условий эксплуатации, когда температура под капотом намного выше, чем в других приложениях, требования к характеристикам паяного соединения выше. Более того, эти системы считаются жизненно важными, что усложняет выбор подходящего припоя. В связи с такими новыми требованиями производители припоев и исследователи стремятся изобрести новый сплав, который может поддерживать эту платформу.Это также означает, что обычные бессвинцовые припои, такие как SnCu, SAC и низкий SAC, демонстрируют ограничения в удовлетворении требований таких приложений.
Различные механизмы упрочнения припоев на основе олова, применяемые в промышленности, будут рассмотрены в разделе 3 этой главы.
Помимо автомобильных систем, популяризация электромобилей способствовала дальнейшему использованию электронных компонентов в автомобильной промышленности. Принимая во внимание тот факт, что этот тип системы включает в себя сильноточные и высокотемпературные, обычные бессвинцовые сплавы SAC не могут удовлетворить основные требования.Это причина, по которой освобождение от соблюдения требований RoHS было продлено до 2021 года для использования Pb в припоях с высокой температурой плавления (то есть в припоях на основе Pb, содержащих 85% по массе или более Pb, Категория 7a). В настоящее время в большинстве электронных устройств для такого применения все еще используется припой с высоким содержанием свинца в качестве материала крепления кристалла. Существуют различные варианты замены припоя с высоким содержанием свинца в процессе присоединения матрицы. Но есть еще пробелы, которые необходимо заполнить, прежде чем такие новые материалы смогут быть полностью коммерциализированы и массовое внедрение таких новых материалов в текущее производство.
Интернет вещей (IoT) привлек большое внимание промышленности. Многие игроки отрасли считают, что Интернет вещей приведет к переходу электронных компонентов на новый уровень — в эпоху Интернета вещей. Интернет вещей изменил бизнес-процессы многих крупных организаций, подготовив их к работе на этой волне. Чтобы упростить интерпретацию Интернета вещей, это приложение, которое позволяет широко использовать сенсоры в нашей повседневной жизни. В IoT также есть платформа, которая может подключать все соответствующие датчики для анализа данных и активации.Цель Интернета вещей — сделать мир умнее. По данным Business Insider , в 2014 году было 1,9 миллиарда взаимосвязанных устройств, а к 2018 году ожидается 9 миллиардов. К тому времени количество устройств Интернета вещей превысит сумму мобильных телефонов, планшетов и ПК, которые в настоящее время являются основными. потребительский рынок. При таком большом количестве устройств IoT использование припоя в качестве межсоединения также является перспективным. При выборе припоя для удовлетворения требований этого сектора основное внимание будет уделяться соблюдению конкретных критериев производства, надежности, токсичности, стоимости и доступности.
Ввиду перспективного роста количества электронных компонентов и новых требований к паяным соединениям производители припоев и исследователи совместно работают над разработкой нового сплава или изменением существующих сплавов, чтобы сократить разрыв между пользователем и поставщиком припоя. В следующих главах обсуждается эволюция бессвинцового сплава и методы, используемые для повышения прочности припоя.
2. Эволюция припоя с высоким содержанием серебра к припою с низким содержанием серебра
В 2000-х годах система SAC была определена как замена эвтектических припоев Sn-Pb в соответствии с требованиями RoHS.Разные страны или организации выбрали разный состав SAC в качестве предпочтительного состава припоя. Это Sn3.0Ag0.5Cu, SAC305 (Япония), Sn3.5Ag0.9Cu, SAC3509 (Европейский Союз) и Sn3. 9Ag0.6Cu, SAC3906 (США) [3].
В 2000 году это была эра потребительских товаров, которые включали в себя многие электронные компоненты в свои системы, такие как персональный компьютер, телевизор, радио, рисоварку и кондиционер на окнах. В этих продуктах в основном использовались компоненты для сквозных отверстий и / или компоненты для поверхностного монтажа (SMT).Это означает, что расход припоя на единицу устройства в тот период времени был огромным. Это объясняет причину массового внедрения SAC305 вместо других бессвинцовых решений. Это связано с более низким содержанием серебра в SAC305 по сравнению с другими сплавами SAC, упомянутыми в предыдущем абзаце. Серебро — драгоценный металл, и его включение в припой значительно увеличивает стоимость припоя. Например, для производства 1 кг SAC305 необходимо добавить 1 унцию серебра. Это зависит от рыночной цены серебра, при условии, что 20 долларов США за унцию, стоимость серебра в 1 кг SAC305 составляет почти 50% от продажной цены 1 кг прутка SAC305. Когда цена серебра резко возрастает, например, в апреле 2011 года, когда цена серебра составляла 40 долларов США за унцию, стоимость серебра в прутке припоя SAC305 составляла более 50% от его продажной цены. Для композиций с более высоким содержанием серебра соотношение цены серебра к отпускной цене прутка припоя обычно составляет более 50% в зависимости от цены олова. Это становится большим бременем для паятелей. Припой в основном используется в процессе пайки волной припоя. Это был очень распространенный процесс сборки печатных плат (PCBA) для упомянутых выше потребительских товаров.Во время пика этой эпохи потребление прутков припоя могло превышать 2000 кг в месяц для одного клиента, у которого в производстве более 10 линий пайки волной припоя. Другая причина массового внедрения SAC305 вместо другого сплава SAC с более высоким содержанием серебра — это скорее политическая причина. В то время японские потребительские товары были очень популярны и распространены. Электрическая рисоварка марки National должна быть одним из обязательных электроприборов в каждом доме.
SAC305 был признан Японской ассоциацией производителей электроники и информационных технологий, JEITA также рекомендовала бессвинцовый сплав.
Тем не менее, промышленность очень быстро искала альтернативы для SAC305 после его внедрения в промышленность, даже несмотря на то, что он был принят в качестве бессвинцового сплава вместо припоя SnPb-6337. В целом, есть две основные причины в оправдание этого направления: стоимость и ударопрочность сплава SAC305. Пользователи искали альтернативу, чтобы снизить высокую стоимость SAC305, как упоминалось выше. Это было время, когда сплавы с низким содержанием SAC начали присоединяться к цепочке поставок припоя.В таблице 2 перечислены некоторые доступные на рынке сплавы с низким содержанием ПАВ, предлагаемые различными поставщиками припоев. Внедрение этих сплавов с низким содержанием SAC произошло всего через 2 года после массового внедрения сплава SAC305 в качестве бессвинцового припоя в промышленности. Тем не менее, SAC305 по-прежнему является основным сплавом, принятым в промышленности после 10 лет принятия RoHS. Стоит отметить, что Nihon Superior представила раствор без содержания серебра и свинца с 1999 года. Он стал основным решением при пайке, особенно при пайке волной и бессвинцовой пайке горячим воздухом (HASL).
Производитель припоя | Состав сплава | Солидус (° C) | Ликвидус (° C) | Дебют (год) |
---|---|---|---|---|
A Решения для сборки Alpha .7Cu | 216 | 225 | 2007–2010 | |
Sn0.3Ag0.7Cu | 217 | 228 | 2007–2010 | |
Senju Metal Industry![]() | 217 | 227 | 2007–2010 | |
Sn1.0Ag0.7Cu | 217 | 224 | 2007–2010 | |
Indium201 | ||||
Indium Corporation | 225 | 2007–2010 | ||
Sn0.3Ag0.7Cu | 217 | 227 | 2007–2010 | |
Nippon Micrometal Corporation | Sn1.20N20N0.5 | 2000-е годы | ||
Nihon Superior | Sn0.7Cu0.05Ni0.01Ge | 227 | 227 | 1999 |
Таблица 2.
Список припоев с низким содержанием SAC и припоев без серебра в качестве альтернативы SAC305.
При более низком содержании серебра в сплаве SAC некоторые пользователи надеялись уменьшить полость горячего разрыва или усадки. Это явление, которое сначала считалось дефектом процесса, было обнаружено при переходе пользователей с SnPb-6337 на SAC305. На сегодняшний день это явление вызывает недоумение у многих пользователей, хотя IPC классифицирует его как приемлемое.На рис. 1 показано сравнение нескольких сплавов с низким содержанием ПАВ и эвтектического сплава олово-медь-никель.
Рис. 1.
Сравнение внешнего вида различных сплавов SAC и эвтектического сплава SnCuNi.
Помимо внешнего вида припоя, разница в котором легко заметна, пользователей также беспокоила надежность низкого SAC, особенно интерметаллического соединения (IMC), образующегося между припоем и паяльной площадкой. На рисунках 2 и 3 показаны IMC SAC 305, low SAC, SAC1205 и бессвинцовый припой (SnCuNi) на медной (Cu) и никелево-золотой (NiAu) площадке, соответственно. Оба сплава SAC независимо от содержания Ag демонстрировали столбчатый рост IMC, и IMC продолжал расти во время термообработки при 125 ° C в течение 500 часов. SnCuNi IMC оказался плоским и стабильным даже после термообработки. Помимо столбчатого IMC, трещина наблюдалась на подушке из Cu после термообработки в IMC сплава SAC305, но не в сплавах SAC1205 и SnCuNi. Это наблюдение соответствовало объяснению, предложенному Nogita et al. в своем дневнике [4]. Добавление Ni в бессвинцовый сплав успешно подавило полиморфное превращение Cu 6 Sn 5 , которое является виновником этой трещины IMC.Происходит превращение гексагональной в моноклинную Cu 6 Sn 5 и наоборот при температуре 186 ° C из-за аллотропного свойства Cu 6 Sn 5 . Это преобразование включает изменение объема Cu 6 Sn 5 IMC, что вызывает высокие напряжения в этом слое. Напряжение превысило прочность этого IMC и вызвало трещину в этом слое.
Микротрещины могли образоваться внутри SAC305 IMC в процессе затвердевания соединения, и трещины распространялись во время термообработки из-за роста IMC.Это объясняет, почему трещина все еще образовывалась, даже несмотря на то, что температура термообработки составляла всего 125 ° C, что было намного ниже температуры полиморфного превращения.
Рис. 2.
IMC, сформированный на медной подушке с припоем SnCuNi (SN100C®), SAC305 и SAC1205 (LF35).
Рис. 3.
IMC, сформированный на контактной площадке NiAu с припоем из сплава SnCuNi (SN100C®), SAC305 и SAC1205 (LF35).
Помимо упомянутой выше проблемы стоимости, еще одной движущей силой, которая побудила промышленность рассматривать сплав с низким содержанием SAC, была устойчивость к ударам при падении.Широко признано, что добавление серебра может эффективно снижать ликвидус и увеличивать предел текучести и модуль упругости сплава SAC; также из-за высокой прочности и высокого модуля упругости, благодаря которым сплав легко передает напряжение на поверхность стыка припоя, которая является областью IMC [5]. Из-за этого механизма большинство отказов, обнаруженных при испытании на ударопрочность при падении с обычными сплавами SAC, в основном происходит в области IMC, и большинство этих отказов являются ранними отказами. При уменьшении содержания Ag в сплаве SAC модуль сплава уменьшается.Это значительно повысило устойчивость к ударам при падении. Стремление к поиску сплава с высокой ударопрочностью при падении еще больше возросло из-за популярности портативных устройств в середине 2000-х до конца 2000-х. В то время портативные музыкальные плееры, такие как MP3-плееры и iPod, а также портативные игровые консоли были очень распространены. Устойчивость к ударам при падении имела решающее значение для сохранения разумной надежности таких устройств. Например, во время первоначальной реализации бессвинцовой пайки большая часть шариков припоя использовалась в массиве шариковой сетки, корпус BGA — это композиция SAC305.Многие мобильные интегральные схемы и ИС были переведены на шарик припоя BGA LF35 или SAC1205, чтобы повысить производительность ИС при испытании на падение.
Однако только снижение содержания Ag в сплаве SAC не дало полного решения, которое оправдало бы ожидания пользователей. Производители припоев применили множество других видов микролегирования, чтобы повысить характеристики сплава с низким содержанием SAC, например, добавляя никель, Ni, цинк, Zn и марганец, Mn в систему сплава. Как показано на Фигуре 2, добавление Ni в композицию LF35 подавило полиморфное превращение Cu 6 Sn 5 во время затвердевания.Этого нельзя добиться только за счет снижения содержания Ag в сплаве SAC.
Принятие решений с низким содержанием SAC или SnCuNi в качестве бессвинцовых растворов также поощряется готовностью других материалов к процессу бессвинцовой пайки. Одной из основных проблем при использовании сплава с низким содержанием SAC или SnCuNi является высокая температура плавления этого сплава. Он имеет температуру плавления примерно на 44 и 10 ° C выше, чем у эвтектического сплава SnPb и сплава SAC соответственно. Однако сейчас рынок более готов к бессвинцовой пайке. Машины для пайки оплавлением и волной припоя обладают более высокой теплоемкостью, чтобы соответствовать высокой температуре плавления бессвинцового припоя, печатных плат и электронных компонентов используются материалы с более высокой температурой стеклования (Tg), а паяльный флюс может дольше выдерживать высокотемпературное оплавление. Все эти усовершенствования позволили использовать при пайке сплав SnCuNi с низким содержанием SAC. Этим также объясняется рост доли рынка сплавов с низким содержанием SAC и SnCuNi в последние годы. SN100C ® стал одним из предпочтительных вариантов для бессвинцовой пайки волной припоя.
Короче говоря, есть две движущие силы, которые вызвали распространение сплавов с низким содержанием SAC и SnCuNi для электронной промышленности. Кто-то назвал низкий SAC вторым поколением бессвинцовых сплавов. На рисунке 4 показана эволюция этого бессвинцового сплава от обычного SAC к сплаву с низким SAC для электронной промышленности. Этот переход очень важен для поддержки эпохи Интернета вещей. Одна из характеристик Интернета вещей — огромное количество. Широкое использование электронных компонентов в эпоху Интернета вещей также требует использования припоя.Тип припоя для этой эпохи должен соответствовать конкретным требованиям в отношении технологичности, надежности, токсичности, стоимости и доступности. Бессвинцовый сплав второго поколения должен быть лучшим выбором для эпохи Интернета вещей.
Рис. 4.
Эволюция SAC-сплавов в бессвинцовых растворах от первого до второго поколения.
В следующем разделе обсуждается превращение бессвинцового сплава в сплав третьего поколения для обеспечения высокой надежности.
3.Требуется сплав высокой надежности
Как обсуждалось в разделе 2, из-за стоимости и устойчивости к ударам при падении происходит эволюция бессвинцового припоя от обычного сплава SAC с высоким содержанием серебра к сплавам с низким содержанием SAC. Это переход от SAC-сплавов первого поколения к SAC-сплавам второго поколения. Однако более низкое содержание Ag ухудшает характеристики термической усталости. Это связано с тем, что повышение прочности сплава SAC происходит за счет диспергирования очень небольшого количества Ag 3 Sn IMC внутри оловянной матрицы.Этот мелкозернистый ИМС Ag 3 Sn препятствует перемещению дислокаций оловянной матрицы. Благодаря этому механизму сплав SAC имеет более высокий модуль упругости по сравнению с SnPb-6337. Более высокое содержание Ag увеличивает количество мелкодисперсного Ag 3 Sn IMC, но также увеличивает возможность роста тромбоцитов большого размера Ag 3 Sn. Эта большая пластинка Ag 3 Sn может быть точкой концентрации напряжения, и с этой точки будет возникать трещина. В крайнем случае, большая пластина из Ag 3 Sn может даже выступать за поверхность припоя и деформировать небольшое паяное соединение [5].Следовательно, крупная пластина Ag 3 Sn не является желательной морфологией в паяном соединении. Однако более низкое содержание Ag в сплавах с низким содержанием SAC приводит к огромному снижению количества Ag 3 Sn IMC.
Хотя существует другой IMC, который представляет собой Cu 6 Sn 5 в объемном припое, этот IMC намного меньше по сравнению с IMC Ag 3 Sn обычных сплавов SAC. Более того, часть Cu из объемного припоя будет извлечена при формировании IMC на площадке из Cu. Это дополнительно снижает количество Cu 6 Sn 5 в объеме припоя.Таким образом, основной силой сплава SAC по-прежнему является дисперсия мелкодисперсного Ag 3 Sn в оловянной матрице.
Компромисс в характеристиках термической усталости сплава SAC был дополнительно усложнен явлением укрупнения Ag 3 Sn IMC. Укрупнение Ag 3 Sn — это процесс созревания Оствальда. Это эволюционный процесс неоднородной структуры, в которой маленькая частица растет и притягивает соседнюю частицу с течением времени, образуя более крупную частицу.Это спонтанный процесс, потому что большая частица более энергетически стабильна, чем малая частица. Это потому, что внутреннее давление обратно пропорционально радиусу частицы. Следовательно, мелкие частицы имеют более высокую поверхностную энергию. Маленькие частицы будут пытаться достичь более высокой энергетической стабильности, увеличиваясь до большего размера. Это грубо. Кроме того, созревание Оствальда — это термодинамический процесс. При высокой температуре окружающей среды процесс огрубления усилится.Это укрупнение Ag 3 Sn оказывает значительное влияние на прочность сплава SAC. Как обсуждалось ранее, прочность сплава SAC заключается в дисперсии мелкодисперсного Ag 3 Sn IMC. На рисунке 5 показан пример укрупнения Ag 3 Sn в сплаве SAC305 после воздействия высокой температуры 125 ° C в течение 6 месяцев.
Рис. 5.
Ag3Sn укрупняется при испытании на хранение при высокой температуре.
В процессе укрупнения будут наблюдаться два изменения: 1. Количество Ag 3 Sn в оловянной матрице и 2.Расстояние между ИМС Ag 3 Sn. Когда количество Ag 3 Sn сокращается и расстояние между Ag 3 Sn увеличивается, его способность препятствовать перемещению дислокаций уменьшается. Это процесс деградации сплавов SAC. Фактически, мы можем легко продемонстрировать этот механизм, подвергая сплав SAC воздействию высокой температуры окружающей среды в течение определенного периода времени. Предел прочности на разрыв сплава SAC снижается после термического старения. На рисунке 6 показан пример такого разрушения сплава SAC305.Это экспериментальные данные сравнения прочности образца для испытаний на растяжение из сплава SAC305 с выдержкой и без изотермического старения (150 ° С в течение 500 ч).
Рис. 6.
Прочность на растяжение SAC305 до и после изотермического старения при 150 ° C в течение 500 часов.
3.1. Высоконадежный припой для PCBA
Деградация сплавов SAC с течением времени вызывает беспокойство, потому что инженеру по надежности сложно спрогнозировать срок службы паяного соединения.Это особенно важно для таких жизненно важных систем, как электронная система в автомобиле или самолете. Как упоминалось в разделе 1, в последнее время автомобильная электроника растет очень агрессивно. Эта отрасль требует высокой надежности и отсутствия дефектов электронных компонентов. Есть запчасти от производителей оригинального оборудования (OEM), которые имеют длительный гарантированный срок службы от 10 до 15 лет. По этой причине в некоторых автомобильных приложениях до сих пор используется SnPb-6337.Поскольку бессвинцовая пайка становится все более распространенной даже в таких высокотехнологичных приложениях, а SAC305 по-прежнему является наиболее распространенным бессвинцовым сплавом, который, очевидно, не может удовлетворить требования высокой надежности таких приложений, возникает большая движущая сила, побуждающая производителей припоев и исследователям найти новый раствор бессвинцового сплава.
Помимо укрупнения Ag 3 Sn, гомологическая температура паяльной системы становится выше из-за более высокой температуры окружающей среды.Чтобы сохранить прочность, особенно при усталости, необходим припой с более низкой гомологической температурой. Электронные компоненты, расположенные под капотом, — хороший тому пример. Это еще раз подтвердило необходимость в новом сплаве для удовлетворения будущих потребностей в надежности электроники.
Существуют консорциумы и некоммерческие организации, такие как Консорциум передовых исследований в области сборки электроники (AREA) и Международная инициатива по производству электроники (iNEMI), которые собирают экспертов по припоям, чтобы совместно определить новый бессвинцовый сплав для решения проблем, упомянутых выше [6] .Эти новые сплавы названы третьим поколением бессвинцовых сплавов, которые обладают превосходными характеристиками как по сопротивлению термической усталости, так и по сопротивлению ударам при падении, что соответствует высоким требованиям надежности паяных соединений. На рисунке 7 показана эволюция бессвинцовых сплавов от первого к третьему поколению.
Рис. 7.
Эволюция бессвинцовых сплавов от первого поколения к третьему поколению, высоконадежный сплав для тяжелых условий эксплуатации.
По-видимому, для повышения прочности требуется большее упрочнение бессвинцовых сплавов. Как обсуждалось ранее, в сплавах SAC используется метод упрочнения частицами для повышения прочности сплава. Основное улучшение происходит за счет диспергирования ИМК Ag 3 Sn в оловянной матрице. Определенно, можно добавить больше Ag, чтобы повысить модуль упругости сплава, но это увеличит возможность образования пластинок Ag 3 Sn. Кроме того, бессвинцовый сплав с высоким содержанием серебра имеет более низкую стойкость к ударам при падении. Высокое содержание Ag в системе сплава также увеличивает стоимость материала.Следовательно, нужен другой подход.
Упрочнение твердым раствором — один из вариантов упрочнения бессвинцового сплава. Фактически, упрочнение твердым раствором широко применялось в эпоху пайки SnPb, когда Pb добавлялся в Sn для улучшения характеристик сплава. Почему-то этот метод не применялся при переходе с SnPb на бессвинцовую пайку. В бессвинцовых сплавах Cu и Ag добавляются к олову по отдельности или вместе, чтобы получить наиболее широко используемые сплавы SAC, которые почти не растворяются в матрице β-олова. Cu и Ag появляются в микроструктуре только в виде интерметаллических соединений: Ag 3 Sn и Cu 6 Sn 5 , как обсуждалось ранее. Конечно, Pb нельзя снова рассматривать как растворенное вещество в твердом растворе, упрочняющем из-за соответствия RoHS. Для достижения этой цели следует рассмотреть другие растворенные вещества, например висмут, Bi; Индий, В; и Сурьма, Сб. Эти три вещества являются наиболее распространенными и возможными кандидатами, выбранными производителями припоев и исследователями для повышения прочности бессвинцового сплава на основе Sn.Bi и In могут уменьшить ликвидус сплава на основе Sn, но Sb может увеличить ликвидус. Это зависит от требований конечного приложения. Если требуется припой с более низкой гомологической температурой, микролегирование с Bi или In может быть нецелесообразным. Тем не менее, Sb является запрещенным или ограниченным используемым веществом в некоторых приложениях, таких как мобильная и потребительская промышленность.
Это ограничило использование этого вещества для микролегирования с целью повышения прочности припоя.
На начальном этапе внедрения бессвинцовой пайки, примерно в 2006 году, была сформирована рабочая группа по разработке более прочного бессвинцового сплава для автомобильной промышленности.С тех пор промышленность понимает необходимость более прочного сплава для будущих требований к автомобильной электронике. В эту рабочую группу входят Siemens, Bosch, Heraeus, Alpha Metals, Infineon, Институт Фраунгофера и т. Д. 90iSC стал результатом усилий этой группы. 90iSC — это сплав SAC с высоким содержанием серебра и добавками Bi, Sb и Ni. Это очень сложная система, в которой невозможно полностью понять и оценить характеристики и надежность. Производители припоев, такие как Nihon Superior, приняли более простой подход, просто микролегируя Bi в систему SnCuNi, чтобы получить более прочный сплав.Это SN100CV ® . Без добавления Ag в SN100CV ® можно снять беспокойство по поводу разрушения сплава из-за укрупнения Ag 3 Sn. Многие пользователи все еще могут скептически относиться к бессвинцовому сплаву без добавления Ag. Их беспокоит прочность этого бессвинцового припоя, не содержащего серебра. Фактически, упрочнение твердого раствора с добавлением Bi даже более эффективно для повышения прочности сплава на растяжение. Например, в SN100CV ® микролегирование 1,5% Bi может значительно повысить предел прочности сплава SnCuNi и сделать его еще более прочным по сравнению с SAC305, который содержит 3% Ag.На рисунке 8 показано сравнение прочности на разрыв трех сплавов: SnCuNi (SN100C ® ), SnCuNiBi (SN100CV ® ) и SnAgCu (SAC305).
Рис. 8.
Сравнение прочности на растяжение трех сплавов в литом состоянии.
Помимо сравнения в состоянии литья, три различных сплава, показанные на рисунке 8, были подвергнуты термическому старению при 150 ° C в течение 500 часов. После термического старения были собраны данные о прочности на разрыв. Как и ожидалось, существует значительная деградация прочности образца SAC305 из-за укрупнения Ag 3 Sn. Падение прочности на разрыв как для SnCuNi, так и для SnCuNiBi минимально. На рисунке 9 приведены сравнительные данные после термического старения.
Рис. 9.
Сравнение прочности на разрыв для трех сплавов в литом состоянии и после термического старения.
Однако выбор правильного соотношения Bi в системе SnCuNi является сложной задачей. Если добавлено слишком мало Bi, эффект упрочнения твердого раствора незначителен. Но если добавить слишком много Bi, произойдет осаждение Bi из β-олова. На рис. 10 показана прочность на разрыв различных сплавов до и после термического старения при 150 ° C в течение 500 ч.
Рис. 10.
Прочность на растяжение исследуемых сплавов в литом состоянии и после термического старения при 150 ° C в течение 500 часов.
3.2. Высоконадежный припой для прикрепления матрицы
Использование припоя не ограничивается межсоединениями между электронными компонентами и печатной платой в процессе печатной платы. В электронных компонентах, таких как интегральная схема (IC), припой использовался в качестве материала для крепления кристалла, особенно в устройстве, где требуется высокая тепловая и электрическая связь между задней стороной кристалла и выводной рамкой или подложкой. Этот тип ИС включает высокомощные устройства и высокоскоростные переключатели, такие как силовой полевой МОП-транзистор, биполярный транзистор с изолированным затвором (IGBT), мощные диод и транзистор, выпрямитель и инвертор. Из-за высокой рабочей температуры такой ИС, которая обычно превышает 260 ° C, промышленность по-прежнему освобождена от соблюдения требований RoHS, и они по-прежнему используют припои с высоким содержанием свинца, такие как Pb5Sn и Pb5Sn2.5Ag, в процессе прикрепления кристаллов. Это связано с тем, что обычные бессвинцовые сплавы на основе Sn имеют температуру плавления ниже 260 ° C.Комитет RoHS разрешает еще 5 лет продления этого исключения в 2016 году из-за технических ограничений, связанных с существующими технологиями. До сих пор нет простого решения по замене припоя с высоким содержанием свинца для такого применения.
Поскольку большинство бессвинцовых сплавов на основе Sn имеют солидус ниже 260 ° C, другие бессвинцовые сплавы, такие как золото-олово (AuSn), висмут-серебро (BiAg) и цинк-алюминий (ZnAl), считаются кандидаты на замену припоя с высоким содержанием свинца, который в настоящее время является материалом для крепления высокотемпературных кристаллов. Однако у этих сплавов есть некоторые ограничения, которые производителям необходимо преодолеть, прежде чем станет возможным массовое внедрение. К ограничениям относятся высокая стоимость (AuSn), низкая теплопроводность, плохая смачиваемость (BiAg) и низкая обрабатываемость из-за хрупкости (ZnAl). Indium Corporation инновационно улучшила характеристики BiAg, чтобы сделать его более удобным для пользователя процессом присоединения штампа. Чтобы улучшить смачиваемость BiAg, эта компания представила паяльную пасту, состоящую из двух типов припоя.Первый тип — это основной порошок, который представляет собой BiAg, и второстепенный порошок, который представляет собой порошок добавки. Порошок добавки имеет более низкую температуру плавления, чем BiAg, и лучшую смачиваемость на обычной паяльной площадке. Порошок добавки может быть известной эвтектикой SnBi, сплавом SAC или сплавом SnAg. В процессе оплавления порошок добавки сначала плавится и реагирует с паяльной площадкой, затем следует плавление большей части порошка, которым является BiAg.
Это необратимый процесс, потому что второстепенный порошок будет полностью израсходован или вступит в реакцию с основным порошком во время процесса оплавления.Соединение, сформированное с использованием этой паяльной пасты, будет иметь такие же свойства, что и BiAg, который составляет большую часть этой паяльной пасты. Требуются дополнительные исследования для оценки пригодности этой паяльной пасты для замены сплава с высоким содержанием свинца. Солидус BiAg все еще ниже, чем у припоя с высоким содержанием свинца. Следовательно, гомологичная температура для этих двух припоев разная.
Помимо припоев, промышленность также активно работает над разработкой спекаемого материала для замены припоя с высоким содержанием свинца.Движущей силой разработки спекаемого материала является не только замена существующего припоя с высоким содержанием свинца, но и подготовка решения для будущего применения. Согласно плану развития ИС, рабочая температура ИС может достигать 600 ° C, особенно для кристалла из карбида кремния (SiC). При такой высокой рабочей температуре это будет проблемой для обычного припоя. Спекание — это процесс атомной диффузии. Для ускорения этого процесса диффузии могут применяться тепло и давление. Атомы в частицах порошка диффундируют через границы частиц, сплавляя частицы вместе и создавая одну твердую деталь (объемный материал).Другими словами, для завершения процесса спекания требуется более низкая температура процесса, чем точка плавления материала. В процессе спекания не происходит плавления. Соединение, образованное после спекания, будет иметь характеристики, аналогичные сыпучему материалу. Поскольку Ag является наиболее распространенным основным ингредиентом для спекания, соединение, образованное спекаемым материалом Ag, будет повторно плавиться только тогда, когда температура превысит точку плавления Ag, которая составляет 961 ° C. Это главная привлекательность агломерационного материала Ag, используемого в этом приложении.Фактически, агломерационные материалы из серебра были изучены в промышленности еще в 1980-х годах.
Но для завершения процесса в течение этого периода по-прежнему требовались высокие температура и давление спекания. Это сделало прием этого материала низким. Благодаря недавней разработке наночастиц Ag, процесс спекания может быть завершен в приемлемом диапазоне температур спекания. Компания Nihon Superior разработала пасту для спекания Ag Alconano ® , которая продемонстрировала хорошее качество соединения серебра на стыковочном слое штампа при температуре спекания до 200 ° C.Это возможно только благодаря наноразмерным частицам Ag, которые обладают высокой поверхностной энергией. Задача производства агломерирующей пасты из серебра состоит не только в получении частиц серебра, но и в разработке правильной системы пассивации для поддержания частиц в хорошем состоянии до начала процесса спекания. Alconano ® использует спирт в качестве пассивирующей системы, которая образует алкоксиды с атомами серебра на поверхности наночастиц. Преимущество этих химикатов в этом применении состоит в том, что связь кислород-серебро, которая достаточно прочна для стабилизации наночастиц во время производственных процессов и последующего хранения и обращения, достаточно слабая, чтобы ее можно было разорвать при относительно низкой температуре, чтобы обнажить активный элемент.
поверхность наночастицы, чтобы она могла связываться с соседними частицами.Еще одно преимущество использования спирта в качестве пассивирующей системы заключается в том, что он не оставляет вредных остатков после процесса спекания. Остаток не содержит соединений серы и азота, которые могут влиять на характеристики спеченного серебра и способствовать возникновению проблем коррозии при эксплуатации. Проблема массового внедрения пасты для спекания Ag не ограничивается только ее производством. Применение этой пасты при прикреплении штампа также является сложной задачей. Для разработки соответствующего набора параметров процесса требуется много инженерных работ.Соединение из спеченного серебра представляет собой пористый слой. Фактически, эта пористость необходима для того, чтобы Ag стал подходящим соединением для крепления штампа. Объемное соединение Ag без какой-либо пористости может быть слишком жестким, чтобы поддерживать архитектуру IC. В таком случае трещина в штампе будет наиболее заметным дефектом в данной области.
Получение правильных свойств этого соединения Ag должно быть совместным усилием между пользователем и поставщиком. Одним из преимуществ этой пасты для спекания Ag является то, что ее пористость можно регулировать с помощью процесса спекания. Изменяя давление и температуру во время спекания, можно достичь различного диапазона пористости.На рисунке 11 показан пример соединения Alconano ® , спеченного из серебра, с пористостью менее 10%. Эти соединения были сформированы с параметрами спекания под давлением: 10 МПа, 300 ° C и время спекания 5 мин. Стабильность процентной пористости удовлетворительна. Помимо удовлетворительной технологичности, надежность соединения, выполненного из этого агломерационного материала Ag, должна быть на уровне или даже лучше, чем характеристики припоя с высоким содержанием свинца. У такого материала для крепления штампа есть две основные характеристики, на которые обращают внимание пользователи.Это теплопроводность и электрическая проводимость стыка.
На основании недавнего отраслевого обзора бессвинцовых высокотемпературных крепежных материалов для штампов, теплопроводность является наиболее необходимым свойством для этого материала [7]. Очень важно поддерживать высокую теплопроводность на протяжении всего срока службы изделия. В некоторых случаях соединение теряет теплопроводность из-за трещины от термической усталости внутри соединения, особенно в горячей и циклической атмосфере. Поэтому при разработке Alconano ® компания Nihon Superior сравнила характеристики Alconano ® с припоем с высоким содержанием свинца и обычным припоем SAC после испытаний на надежность термоциклирования, −40 ° C / + 200 ° C со временем выдержки. 30 мин.Результаты сравнения показаны на рисунке 12.
Рисунок 11.
Проверка пористости после спекания под давлением на спекаемом соединении из серебра.
Рис. 12.
Изменение термического сопротивления высокотемпературного материала крепления матрицы в зависимости от термоциклирования. В качестве испытательной машины использовалась силиконовая матрица 10 × 10 мм на подложке из Al2O3 с пластинчатым теплоотводом из меди. Условия спекания составляли 300 ° C, поддерживаемое давление 40 МПа и продолжительность спекания 3 мин.
Бессвинцовый жидкофазный диффузионный материал (LPDB) — еще один новый материал, который потенциально может быть использован в качестве высокотемпературного бессвинцового материала для крепления кристаллов.Процесс связывания этого LPDB очень похож на процесс склеивания модифицированной пасты BiAg, упомянутой выше. Подобно модифицированной пасте BiAg, паста LPDB состоит из двух типов порошка: с высокой температурой плавления и низкой температурой плавления. В отличие от модифицированной пасты BiAg, в которой оба типа порошка будут плавиться во время процесса склеивания, порошок LPDB с высокой температурой плавления никогда не будет плавиться во время процесса склеивания, а только порошок с низкой температурой плавления будет плавиться и вступать в реакцию с площадками для пайки и одновременно реагировать с высокоплавкий порошок для образования нового IMC. В процессе склеивания происходит гомогенизация расплава. IMC будет образовываться из-за реакции между расплавленным порошком с низкой температурой плавления и порошком с высокой температурой плавления. И этот вновь образованный IMC имеет гораздо более высокую температуру плавления, чем порошок с низкой температурой плавления. Следовательно, расплав начнет затвердевать еще до начала охлаждения из-за изменения температуры плавления. После процесса склеивания соединение будет переплавляться только при температуре выше, чем температура склеивания. Вот почему этот материал также называют переходным жидкофазным диффузионным связывающим материалом.Компания Nihon Superior Co., Ltd. приняла участие в проекте лаборатории Эймса из Университета штата Айова в разработке этого материала LPDB. Лаборатория Эймса смешивает порошок Cu-10Ni с высокой температурой плавления с коммерческим мелкодисперсным порошком SN100C ® , чтобы получить этот материал LPDB. В процессе связывания весь порошок SN100C ® преобразуется в высокотемпературный (Cu, Ni) 6 Sn 5 IMC, который будет плавиться только при 525 ° C [8].
Это очень важная характеристика, позволяющая сделать его потенциально высокотемпературным бессвинцовым материалом для крепления кристаллов.Кроме того, добавка Ni в Cu 6 Sn 5 значительно улучшила свойства этого IMC. Это сделало его более прочным соединением, поскольку Ni препятствовал полиморфному превращению аллотропной Cu 6 Sn 5 , как обсуждалось ранее в этой главе. Согласно Choquette и Iver [8], добавка Ni в Cu 6 Sn 5 также должна улучшить пластичность и прочность соединения. Этот материал LPDB может быть потенциальным решением для замены припоя с высоким содержанием свинца, поскольку он может завершить соединение при обычной температуре оплавления (240–260 ° C), но он будет повторно плавиться только при 525 ° C.
4. Заключение
Из-за соответствия директиве RoHS, электронная промышленность перестала принимать стабильный и знакомый припой SnPb-6337, который десятилетиями использовался в качестве межсоединения, и перешла на бессвинцовый припой. Существует множество разработок бессвинцового припоя с целью удовлетворить ожидания пользователей в отношении технологичности и надежности. Такого рода разработки наводнили рынок множеством составов сплавов и усложнили пользователю выбор правильного бессвинцового сплава, который может оправдать их ожидания.Как правило, с 2006 года на рынок выводится три поколения бессвинцовых припоев. Бессвинцовый припой первого поколения — это обычный сплав SAC с содержанием серебра в подшипниках от 3,0 до 4,0%. Затем рынок переходит на сплавы с низким содержанием SAC из-за резкого роста цен на Ag в начале 2010-х годов и плохой стойкости к ударам при падении этих традиционных сплавов с SAC. В последнее время, в связи с агрессивным ростом автомобильной электроники и авионики, к бессвинцовому припою предъявлены новые требования в отношении надежности паяных соединений.Это третье поколение бессвинцовых сплавов, которые представляют собой систему сплавов, обеспечивающую длительный срок службы при термической усталости и стойкость к ударам при падении.
С другой стороны, многие ИС и электронные компоненты все еще используют припой с высоким содержанием свинца (мягкий припой) в качестве материала для крепления кристаллов. Промышленности активно ищут альтернативы, не содержащие свинца. Системы сплавов, такие как AuSn, BiAg, ZnAl, агломерационный материал Ag и материал LPDB, являются потенциальными кандидатами в списке.
Благодарности
Эта публикация полностью финансируется Nihon Superior Co., Ltd. Автор благодарит отдел исследований и разработок Nihon Superior за поддержку в сборе и анализе данных. Автор также хотел бы выразить особую благодарность доктору Тетсуро Нишимура, господину Такатоши Нишимура и господину Кейту Свитману за их помощь и руководство в этой публикации.
Свойства и микроструктура бессвинцовых припоев Sn-Ag-Cu-X в электронных корпусах
Припой SnAgCu считался одним из самых популярных бессвинцовых припоев из-за их хорошей надежности и механических свойств.Однако есть также много проблем, которые необходимо решить для припоев SnAgCu, таких как высокая температура плавления и плохая смачиваемость. Чтобы преодолеть эти недостатки и еще больше улучшить свойства припоев SnAgCu, многие исследователи предпочитают добавлять ряд легирующих элементов (In, Ti, Fe, Zn, Bi, Ni, Sb, Ga, Al и редкоземельные элементы) и наночастиц к припоям SnAgCu. В этой статье рассмотрена работа бессвинцовых припоев SnAgCu, содержащих легирующие элементы и наночастицы, и обсуждено влияние легирующих элементов и наночастиц на температуру плавления, смачиваемость, механические свойства, свойства твердости, микроструктуры, интерметаллиды и усы. .
1. Введение
Олово-свинцовые припои (SnPb) широко используются в электронных упаковках. Однако из-за растущей озабоченности по поводу токсичности свинца для окружающей среды и здоровья человека правительства многих стран приняли законы, запрещающие использование Pb из электронных приложений. Таким образом, исследование бессвинцового припоя стало важной темой исследований в области электронной упаковки.
В последние годы, чтобы заменить обычные припои Sn-Pb, были разработаны несколько типов бессвинцовых припоев на основе Sn, таких как SnAg, SnCu, SnZn, SnBi, SnIn и SnAgCu.Среди серий бессвинцовых припоев SnAgCu был предложен как наиболее многообещающий бессвинцовый припой для замены традиционного оловянно-свинцового припоя благодаря его хорошей надежности, превосходному сопротивлению ползучести и характеристикам термической усталости [1–3]. Однако остается еще много нерешенных вопросов. Например, припой SnAgCu имеет высокую температуру плавления, плохую смачиваемость, более грубую микроструктуру и так далее. Для дальнейшего улучшения свойств бессвинцового припоя используются два метода. Первый метод заключается в добавлении в припой SnAgCu легирующих элементов, таких как элемент Ga, который может улучшить смачиваемость.А добавление редкоземельных элементов может улучшить общие характеристики. Другой метод — добавление микро- или наночастиц. Он в основном состоит из металлических частиц, составных частиц, керамических частиц, углеродных нанотрубок и полимерных частиц. С изменением типа и размера добавляемых частиц свойства припоя SnAgCu становятся другими. Добавление металлических частиц может не только изменить микроструктуру припоя, но также появится новая фаза в матрице припоя, в то время как добавление частиц соединения или керамических частиц не может сформировать новую фазу.
В этом обзоре мы подводим итоги разработки припоев SnAgCu и анализируем влияние добавления четвертых элементов на температуру плавления, смачиваемость, механические свойства, свойства твердости, микроструктуру и интерметаллические соединения (IMC). В то же время мы также обсудим усы Sn, и были выдвинуты некоторые предложения, которые могут решить эту проблему.
2. Температура плавления
Температура плавления является важным фактором при разработке новых бессвинцовых припоев.Перспективный припойный сплав должен иметь низкую температуру плавления и узкий интервал плавления [4]. Как мы все знаем, эвтектический SnPb имеет температуру плавления 183 ° C, а температура плавления припоя SnAgCu составляет 217 ° C, что на 34 ° C выше, чем у эвтектического SnPb. Такая высокая температура плавления увеличит температуру оплавления и приведет к термическому повреждению полимерной подложки [5]. Между тем, он также увеличивает скорость растворения и растворимость Cu в расплавленном припое, тем самым улучшая скорость образования IMC.Это причина того, что IMCs слой SnAgCu толще, чем Sn-Pb. Следовательно, некоторые исследователи ожидают добавления четвертых элементов для снижения температуры плавления припоев SnAgCu.
Следы индия (In), добавленные в бессвинцовый припой SnAgCu, могут явно изменить характер плавления. В литературе [6] показано, что добавление 3,0 мас.% In при температурах солидуса и ликвидуса снизилось на 21,7 и 11,5 ° C соответственно по сравнению с 219,4 и 241,7 ° C для припоя Sn0,3Ag0,7Cu.Но In очень дорогой, добавление In может увеличить стоимость бессвинцовых припоев. Chuang et al. [7] предположили влияние Ti на температуру плавления припоя Sn3.5Ag0.5Cu (SAC). При добавлении элемента Ti температуры плавления меняются незначительно. Температуры ликвидуса составляют 220,95, 220,86 и 219,47 ° C для припоев SAC- x Ti с содержанием Ti 0,25, 0,5 и 1,0 мас.% Соответственно. Причем интервал плавления снижен с 4,66 до 2,88 ° С. Вообще говоря, узкий диапазон плавления припоя означает отличные термические свойства.В основном это связано с узким диапазоном плавления, объясняющим, что припои существуют в виде жидкой части в течение очень короткого времени во время затвердевания и могут образовывать надежные соединения в процессе оплавления. На рис. 1 представлена кривая дифференциальной сканирующей калориметрии (ДСК) SnAgCu, содержащего различные марганец (Mn) и титан (Ti). Показано, что припой Sn3.0Ag0.5Cu имеет только один эндотермический пик, а у припоя Sn1.0Ag0.5Cu (SAC) — два пика. Между тем, стоит отметить, что на степень переохлаждения проэвтектического Sn существенно повлияло добавление в припой SAC примесных легирующих элементов (Mn и Ti).Образец SAC-0.5Ti показал чрезвычайно подавленное переохлаждение всего на 4 ° C [8]. Добавление Fe в припой SnAgCu не сильно изменило температуру плавления [9]. Результаты ДСК продемонстрировали единственный пик припоя Sn3.6Ag0.9Cu. Однако есть два очевидных эндотермических пика (220 ° C и 235 ° C), которые появляются для припоя SnAgCu-0.2Fe. Это показывает, что плавление происходило в широком диапазоне температур. Это может быть связано с перекрытием пиков; первый пик может указывать на то, что припой частично расплавился.Добавление Fe, скорее всего, привело к смещению точки плавления от точки эвтектики к точке, близкой к точке эвтектики, а температура плавления припоя находится в диапазоне от 222,87 до 230 ° C, что выше, чем точка плавления припоя SnAgCu. (217 ° С). При добавлении 0,6 мас.% Fe был обнаружен только один эндотермический пик при 221,35 ° C, что свидетельствует о его эвтектическом составе. Эль-Дали и др. В [10] изучались ДСК-профили припоя Sn1.0Ag0.3Cu. ДСК показала два эндотермических пика между 220.1 ° С и 227,2 ° С. Два пика указывают на две стадии процесса плавления припоя SnAgCu. Согласно фазовой диаграмме тройного SnAgCu [11], две стадии были связаны с плавлением тройной эвтектики β -Sn + Ag 3 Sn + η Cu 6 Sn 5 фазы и первичной β -Sn. Однако для припоя SnAgCu, содержащего Zn, на кривой ДСК появляется только один эндотермический пик, а температуры плавления составляют 222,8 и 220,8 ° C для SAC-2.0Zn и SAC-3.0Zn соответственно. Добавление Bi снижает температуру плавления припоя Sn3.8Ag0.7Cu (SAC) [12]. Установлено, что температуры солидуса SAC-2.0Bi и SAC-4.0Bi составили 213,08 и 206,40 ° C соответственно. Однако при добавлении слишком большого количества Bi появится отслоение паяного соединения. Сканирование методом ДСК припоя с низким содержанием Ag Sn0,5Ag0,7Cu (SAC), содержащего Ni, и результаты показали, что добавление Ni мало влияет на температуру плавления [13]. Пиковая температура припоев SAC, SAC-0,05Ni и SAC-0,1Ni составила 221 ° C.1, 222,9 и 223,4 ° С. Более того, значения диапазона плавления составляли 12,6, 11,9 и 12,8 ° C для SAC, SAC-0,05Ni и SAC-0,1Ni соответственно. Для припоя SnPb она очень близка к 11,5 ° C [14]. Об этом также сообщалось в литературе [15].
Хорошо известно, что добавление небольшого количества РЗЭ в металлы может значительно улучшить их свойства [16]. Однако это существенно не меняет температуру плавления. Кривые ДСК припоев Sn3.9Ag0.7Cu и Sn3.9Ag0.7Cu0.5RE исследовали Дудек и Чавла [17]; все припои демонстрируют единственный эндотермический пик между 217 ° C и 219 ° C, показывая начало плавления припоя SnAgCu.Выявлено, что добавление РЗЭ в припой Sn3.9Ag0.7Cu не влияет на характеристики плавления. Более того, также обнаружено, что добавление La оказывает минимальное воздействие, в то время как добавление Ce и Y увеличивает начальную температуру примерно на 2 ° C.
В последнее время многие исследователи также исследуют добавление наночастиц в припои SnAgCu для улучшения свойств и микроструктуры. Xiang et al. [18] сообщили, что добавление наночастиц Mn существенно не изменило температуру плавления Sn3.Припой 8Ag0.7Cu (SAC). Результаты показали, что начальные температуры плавления композитных припоев SAC-0,12Mn, SAC-0,18Mn и SAC-0,47Mn составляли 217 ° C, 217,3 ° C и 217,5 ° C соответственно. Небольшие количества наночастиц SiC, добавленные в припой Sn3.8Ag0.7Cu, не сильно изменяют температуру плавления. Четко выраженный эндотермический пик сдвигается от 219,9 ° C до 218,9 ° C при добавлении 0,2 мас.% SiC [19]. Al 2 O 3 наночастиц были добавлены в припой Sn3,5Ag0,5Cu.Во время процесса нагрева при анализе ДСК припой Sn3,5Ag0,5Cu показал эвтектический сплав с температурой плавления 221,2 ° C, которая несколько повысилась с увеличением количества нано-Al 2 O 3 частиц [20]. Чтобы определить влияние различных методов изготовления соединений и количества добавленного TiO 2 на припой Sn3.0Ag0.5Cu (SAC), был использован анализ DSC. Использовали DSC-анализ. Результаты показали, что температура плавления припоя SAC и припоя, несущего 1 мас.% TiO 2 наночастиц находились в диапазоне от 217 ° C до 217,64 ° C, с только эвтектическим пиком [21]. Аналогичное явление наблюдалось и в других исследованиях композитных припоев SAC [22]. Анализ методом ДСК был проведен, чтобы понять влияние добавления наночастиц ZnO к припою Sn3,5Ag0,5Cu (SAC) на его температуру плавления. Результаты ДСК показывают, что температуры плавления простого припоя SAC и композитного припоя SAC-0.5ZnO составляли около 221,18 ° C и 222,16 ° C, соответственно, с только эвтектическим пиком [23].Поведение плавления припоя Sn3.0Ag0.5Cu, армированного наноразмерными частицами ZrO 2 , было исследовано Гейном и Чаном [24]. Температура плавления повышалась менее чем на 1 ° C, когда количество наночастиц ZrO 2 составляло 1 мас.%.
Таким образом, добавление легирующих элементов и наночастиц на температуру плавления мало влияет. Однако была разработана новая печь для бессвинцовой пайки волной и оплавлением, которая может выполнять пайку при температуре ниже 250 ° C. Следовательно, указанные выше элементы, добавленные к припою SnAgCu, могут соответствовать требованиям настоящего процесса пайки, и нет необходимости вносить изменения в текущий процесс оплавления.Кроме того, в будущих исследованиях нам может потребоваться только убедиться, что добавление элементов может незначительно повлиять на плавление припоев SnAgCu.
3. Смачиваемость
Смачиваемость припоя можно определить как способность расплавленного припоя растекаться по подложке во время процесса оплавления [25]. Для процесса оплавления, температура нагрева при определенных условиях, только хорошая смачиваемость поверхности основного материала для образования хороших влажных стыков, а именно для образования паяных соединений.Паяные соединения несут все электронное устройство как механическую опору и электрические соединения; таким образом, паяные соединения напрямую определяют рабочие характеристики электронных продуктов. Для традиционного припоя SnPb из-за наличия Pb припой имеет лучшую смачиваемость. Но для бессвинцовых припоев смачиваемость, очевидно, может снизиться из-за замены Pb. Чтобы улучшить смачиваемость припоя, добавление легирующего элемента является горячим исследователем.Как правило, существует множество методов измерения смачиваемости, но метод баланса смачивания и метод распределения считаются относительно универсальными методами.
Добавление небольшого количества In в припой SnAgCu было исследовано Moser et al. [26]. Угол смачивания был уменьшен с 37 ° до 22 ° при добавлении 75 ат.% In. Испытания баланса смачивания были проведены на воздухе, чтобы показать смачиваемость Sn3.6Ag0.9Cu- x Fe, Fallahi et al. [9]. Обнаружено, что добавление 0.2 мас.% Fe увеличивают силу смачивания и уменьшают угол смачивания. Однако Fe было добавлено в количестве более 0,6 мас.%, Что привело к более низкой смачиваемости. Элемент Zn был включен в припои Sn3.8Ag0.7Cu Zhang et al. [27]. Смачиваемость припоев SnAgCu можно улучшить добавлением Zn. При содержании Zn до 0,8% припой Sn3.8Ag0.7Cu имел наименьший угол. Однако при добавлении 3% Zn угол смачивания был наибольшим. Это можно отнести к тому, что Zn легко окисляется; образование остатков оксида во время пайки может ухудшить смачиваемость припоя SnAgCu.Добавление небольшого количества Bi в припои SnAgCu может изменить характеристики смачивания. Ризви и др. [28] экспериментально продемонстрировали влияние 1,0 мас.% Bi на смачиваемость припоя Sn2,8Ag0,5Cu по сравнению со сплавом Sn-37Pb. Показано, что смачиваемость припоя Sn2.8Ag0.5Cu1.0Bi ниже, чем у традиционного припоя SnPb для всех типов флюсов и температур ванны припоя. Однако из-за высокой температуры пайки способствует процессу диффузии, тем самым уменьшая угол смачивания и улучшая характеристики смачивания.Более того, смачиваемость припоя Sn2.8Ag0.5Cu1.0Bi на Ni-подложке была ниже, чем у Cu-подложки. Исследователи объясняют, что атомы Ni диффундировали в припой через интерметаллические соединения (ИМС) намного медленнее, чем атомы Cu. Moser et al. [29] также исследовали влияние Bi на припой SnAgCu в защитной атмосфере Ar-H 2 и обнаружили, что атмосфера Ar-H 2 может лучше снизить поверхностное натяжение и улучшить смачиваемость. Это из-за того, что инертный газ может защитить припой, снижает вероятность контакта жидкого припоя с кислородом.Элемент Ga, содержащий припой Sn0.5Ag0.7Cu, был исследован Луо и др. [30]. Результаты показывают, что время смачивания и силы смачивания меняются в зависимости от Ga, когда Ga был добавлен в припой Sn0,5Ag0,7Cu до 0,5%, что приводит к уменьшению значений среднего времени смачивания (сила смачивания показывает тенденция к увеличению). При дальнейшем увеличении добавления Ga можно обнаружить увеличение времени смачивания. Из-за поверхностно-активных свойств Ga, Ga будет накапливаться на границе раздела припоя в состоянии плавления; затем поверхностное натяжение жидкого припоя было уменьшено [31].Следовательно, новые композитные припои показали лучшую смачиваемость. Лу и др. [32] подтвердили, что добавление элемента Mg в припой SnAgCu ухудшает характеристики смачивания, поскольку Mg очень склонен к окислению, а образование оксидной пленки увеличивает поверхностное натяжение жидкого припоя, что препятствует растеканию припоя по подложке из Cu. .
Редкоземельные элементы (РЗЭ) называют «витамином» металлов, что означает, что небольшое количество РЗЭ, очевидно, может улучшить свойства металлов [33].В ряду характеристик бессвинцового припоя смачиваемость при добавлении редкоземельных элементов является наиболее очевидным улучшением. Yu et al. [34] исследовали влияние РЗЭ (Ce и La) на припой SnAgCu, где температура пайки составляла 250 ° C и использовался флюс RMA. Установлено, что угол смачивания Sn2,5Ag0,7Cu выше, чем у Sn3,5Ag0,5Cu из-за более высокой температуры плавления Sn2,5Ag0,7Cu. А когда RE составляет менее 0,1 мас.%, Угол смачивания Sn3,5Ag0,7Cu уменьшается с увеличением RE.Поскольку содержание выше 0,1 мас.%, Угол смачивания увеличивается. Аналогичный результат был получен Law et al. [35]. На рис. 2 показано, что угол смачивания был уменьшен при добавлении РЭ элементов. Однако при добавлении чрезмерного количества RE-элемента угол смачивания увеличится. Тяжелый редкоземельный элемент Y может улучшить смачиваемость припоя Sn3,8Ag0,7Cu, при этом площади растекания увеличиваются, а углы смачивания уменьшаются по мере увеличения содержания Y. При добавлении 0,15 мас.% Y площади растекания и углы смачивания достигают пика, но когда Y превышает 0.На 15 мас.% Смачиваемость композиционного припоя заметно снизилась [36]. Редкоземельный элемент Er был включен в припой Sn3.8Ag0.7Cu, что может изменить характеристики смачивания [37]. Когда содержание Er составляет менее 0,25 мас.%, Площади растекания увеличиваются при добавлении элемента Er. Однако по мере того, как содержание элемента Er продолжает увеличиваться до 1,0 мас.%, Площади растекания будут уменьшаться. Смачиваемость припоя SnAgCu улучшается за счет добавления элемента Pr. Gao et al.[38, 39] обнаружили, что добавление следовых количеств Pr и Nd может значительно улучшить смачиваемость припоя Sn3,8Ag0,7Cu, где оптимальное смачивающее поведение было достигнуто, поскольку содержание RE составляет около 0,05 мас.% Из-за более низкой поверхности. напряжение, вызванное РЭ элементами. Добавление Yb в SnAgCu исследовали Zhang et al. [40]. В результате краевые углы уменьшались по мере увеличения содержания Yb. Когда добавка Yb составляла 0,05%, контактный угол может уменьшиться до максимального значения, но когда содержание Yb превышает 0.05%, заметно увеличились углы смачивания. Из-за более высокого сродства Sn к редкоземельным элементам в припоях. Во-первых, Sn имеет тенденцию реагировать с Yb с образованием частиц Sn-Yb, и реакция легко протекает, когда частицы Sn-Yb прилипают к подложке для образования зародышей, особенно для зарождения частиц в тройной точке на рисунке 3. ; когда частицы существуют в тройной точке, баланс между газом, твердым телом и жидкостью будет нарушен. Влияние добавления редкоземельного элемента Се, атмосферы и температуры на характеристики смачивания припоев SnAgCu- x Ce было изучено Ван и др.[41]. Результаты показывают, что с добавлением Ce заметно улучшается смачиваемость припоев Sn3,8Ag0,7Cu. При добавлении от 0,03% до 0,05% время смачивания составляет около 0,7 с при 250 ° C, что очень близко к припою Sn-Pb. Более того, в атмосфере N 2 характеристики смачивания припоя SnAgCu значительно улучшаются. Из-за окисления расплавленного припоя и подложки ингибируется атмосфера N 2 . Кроме того, Zhao et al. [42] также обнаружили, что площадь распространения увеличивалась с увеличением содержания Ce.Когда добавка Ce составляет 0,1%, Sn3.0Ag2.8Cu-Ce имеет максимальную площадь растекания 242,80 мм 2 . Однако, если содержание Ce превышает 0,1%, площадь укрытия будет уменьшаться.
Одним словом, добавление редкоземельных элементов может изменить характеристики смачивания; есть две причины, приводящие к этому результату: с одной стороны, редкоземельный элемент является поверхностно-активным элементом, который может снизить поверхностное натяжение жидкого припоя. В другом аспекте редкоземельный элемент подвержен окислению; таким образом, образование чрезмерного количества оксидного остатка во время пайки может ухудшить смачиваемость припоя, тем самым влияя на растекающиеся свойства [43].
В настоящее время, с развитием нанотехнологий на протяжении многих лет, все больше и больше исследователей пытаются добавлять наночастицы для улучшения комплексных характеристик бессвинцовых припоев Sn-Ag-Cu.
Добавление наночастиц Mn в припой SnAgCu ухудшает характеристики смачивания. При добавлении 0,47 мас.% Наночастиц Mn угол смачивания припоя SnAgCu был увеличен с 10,71 ° до 25,6 °, а скорость растекания припоя также снизилась с 88,9% до 77,4%. Это вызвано повышенной вязкостью для добавления наночастиц во время пайки [18].Tay et al. [44] обнаружили, что добавление наночастиц Ni изменяет смачиваемость припоя Sn3.8Ag0.7Cu. Результаты показали, что добавление наночастиц Ni в припой SnAgCu приводит к увеличению угла смачивания с 19,3 ° до 29,9 °. Для припоя Sn3.8Ag0.7Cu, содержащего наночастицы Co, влияние наночастиц Co на смачиваемость было обнаружено Yoon et al. [45]. С увеличением концентрации добавленных наночастиц Co угол смачивания увеличивался, а скорость растекания уменьшалась. О подобных эффектах сообщили Haseeb et al.[46, 47]. Наночастицы Al 2 O 3 могут значительно изменить характеристики смачивания припоя Sn3,5Ag0,5Cu. Угол смачивания припоя SnAgCu был уменьшен за счет добавления наночастиц Al 2 O 3 ; минимальный угол 28,9 ° может быть найден при добавлении 0,5% частиц нано-Al 2 O 3 [20]. Ли и др. [48] производили припои Sn3.0Ag0.5Cu путем механического перемешивания наночастиц TiO 2 и указали, что следовые количества наночастиц TiO 2 могут эффективно влиять на смачиваемость Sn3.Припой 0Ag0,5Cu. Понятно, что время смачивания может быть уменьшено на 53,7%, а сила смачивания может быть увеличена на 37,6% при добавлении 0,25% частиц TiO 2 . Лю и др. [49] исследовали добавление графеновых нанолистов (ГНС) в припои Sn3.0Ag0.5Cu с помощью порошковой металлургии. Результаты показывают, что для припоя SAC- x GNS с увеличением содержания добавок GNS угол смачивания уменьшался. При содержании ГНС 0,1% краевой угол смачивания можно уменьшить на 15.5%. Nai et al. [50] исследовали влияние инородных и негрубых посторонних добавок на смачиваемость припоя SnAgCu. Обнаружено, что углы смачивания уменьшились на 15,7% и 19,8% при добавлении 0,04% и 0,07% углеродных нанотрубок (УНТ). Han et al. [51] также обнаружили, что добавление следовых количеств углеродных нанотрубок с никелевым покрытием (Ni-CNT) значительно улучшило смачиваемость припоя SnAgCu.
В заключение, добавление наночастиц не оказало значительного влияния на смачиваемость припоев SnAgCu и может даже ухудшить углы смачивания.Однако, согласно Kripesh et al. [52], качество смачивания считается «очень хорошим», когда значение составляет 0 ° <<20 °. Значение 20 ° <<40 ° считается «хорошим и приемлемым». Смачиваемость считается «плохой» при температуре> 40 °. Следовательно, с добавлением наночастиц угол смачивания композитного припоя SnAgCu находится в приемлемом диапазоне. Более того, разные исследователи получили разный результат. Это может быть связано с составом припоя, температурой пайки, рабочей средой, типом флюса, металлургией подложки и т. Д.
4. Механические свойства
Механические свойства — важный показатель для оценки свойств припоя. Он играет жизненно важную роль в надежности паяных соединений.
Влияние элемента In на предел прочности при растяжении припоя Sn0,3Ag0,7Cu с низким содержанием серебра было изучено Kanlayasiri et al. [6]. При добавлении 3,0 мас.% In прочность на разрыв SnAgCu увеличивается примерно на 79%. Добавление Ti может значительно улучшить механические свойства припоя SnAgCu. Однако с добавлением Ti более 1.0 мас.%, Механические свойства Sn3.5Ag0.5Cu снизились из-за появления в эвтектических колониях крупного Ti 2 Sn 3 [7]. Элемент Fe может увеличить прочность припоя SnAgCu на сдвиг. Fallahi et al. [9] обнаружили, что прочность на сдвиг припоя Sn3.6Ag0.9Cu составляет 29 МПа; при добавлении 0,2 мас.% и 0,6 мас.% Fe прочность на сдвиг была увеличена до 40 МПа и 53 МПа. При добавлении 0,8 мас.% Zn к припою Sn3,8Ag0,7Cu растягивающая сила паяного соединения SnAgCu может быть улучшена на 10%.При дальнейшем увеличении содержания Zn растягивающее усилие заметно уменьшается. Это связано с тем, что Zn имеет более сильное сродство к кислороду, а добавление избыточного количества Zn приведет к образованию избыточных оксидов Zn. Поэтому механические свойства паяных соединений SnAgCu- x Zn были снижены [27]. Подобный упрочняющий эффект Zn на предел прочности SnAgCu был также обнаружен Song et al. [53]. Элемент Bi также может улучшить механические свойства припоя SnAgCu. Когда добавление Bi было 2.0 мас.%, Было достигнуто улучшение предела прочности на разрыв (UTS) на 47%. Когда добавка Bi составляла 4,0 мас.%, UTS была почти в 2 раза выше, чем у припоя SnAgCu [12]. Ni может улучшать механические свойства припоя Sn2.0Ag0.5Cu, что было исследовано Эль-Дали и Эль-Тахером [54]. Установлено, что предел прочности при растяжении (UTS) и предел текучести (YS) увеличиваются с увеличением количества Ni. Прочность на разрыв паяного соединения SnAgCu с подшипником Sb была исследована Ли и др. [55], как показано в таблице 1.Результаты показали, что добавление Sb, очевидно, может улучшить прочность на разрыв припоев и соединений SnAgCu во время старения. Причина может быть связана с упрочнением твердого раствора и твердыми частицами. Луо и др. [30] сообщили, что прочность на сдвиг паяного соединения Sn0,5Ag0,7Cu может быть улучшена путем добавления Ga. Когда добавка Ga составляла до 0,5 мас.%, Прочность на сдвиг увеличивалась на 17,9%.