Как переделать сварочный инвертор в полуавтомат в домашних условиях. Какие способы существуют для самостоятельной сборки сварочного полуавтомата из инвертора. Что потребуется для переделки и как правильно это сделать. Какие преимущества дает самодельный сварочный полуавтомат.
Устройство и принцип работы сварочного полуавтомата
Сварочный полуавтомат состоит из двух основных блоков:
- Силовой блок (инвертор) — источник сварочного тока
- Подающий механизм — устройство для автоматической подачи сварочной проволоки
Принцип работы полуавтомата заключается в следующем:
- Сварщик подводит горелку к месту сварки
- Из сопла горелки одновременно подаются защитный газ и сварочная проволока
- Между проволокой и металлом возникает электрическая дуга
- Проволока и основной металл плавятся, образуя сварочную ванну
- Сварщик перемещает горелку, формируя сварной шов
Преимущества полуавтоматической сварки:
- Высокая производительность
- Хорошее качество сварного соединения
- Возможность сварки тонких материалов
- Низкое разбрызгивание металла
Способы переделки инвертора в полуавтомат своими руками
Существует несколько основных способов самостоятельной переделки сварочного инвертора в полуавтомат:

1. Изменение вольт-амперной характеристики с помощью дросселя
Для этого способа потребуется:
- Рабочий инвертор для ММА сварки
- Дроссель от лампы дневного света
- Провода и разъемы для подключения
Последовательность действий:
- Подключить дроссель к выходу инвертора
- Взять напряжение обратной связи после дросселя
- Подключить подающий механизм к инвертору
2. Использование инвертора с переключением характеристик
Для этого варианта необходимо:
- Инвертор с возможностью переключения в режим жесткой ВАХ
- Внешний подающий механизм с комплектом кабелей
Порядок действий:
- Переключить инвертор в режим с жесткой ВАХ
- Подключить подающий механизм к разъемам инвертора
3. Модификация схемы инвертора
Для реализации потребуется:
- Инвертор с компоновкой ZX-7
- Дополнительные электронные компоненты
- Навыки работы с электроникой
Основные этапы:
- Изменение схемы управления инвертором
- Установка регулировки нарастания тока
- Подключение механизма подачи проволоки
Как выбрать инвертор-донор для переделки в полуавтомат
При выборе инвертора для переделки следует обратить внимание на следующие параметры:
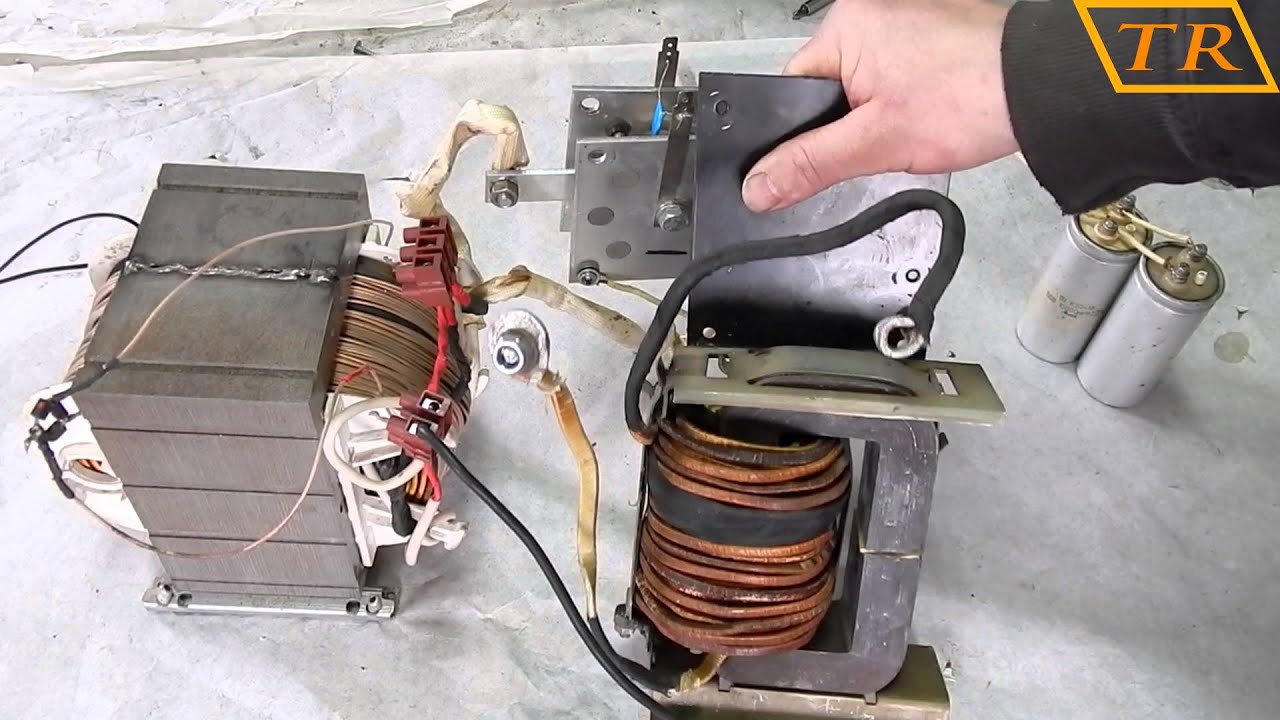
- Мощность — не менее 160-180 А
- Продолжительность включения — не менее 60%
- Наличие шунта на выходе
- Отсутствие сложных дополнительных функций
- Простая схема управления
Желательно использовать недорогие бытовые модели инверторов без избыточного функционала. Это упростит процесс модификации и снизит вероятность повреждения дорогостоящих компонентов.
Преимущества самодельного сварочного полуавтомата
Самостоятельная переделка инвертора в полуавтомат дает ряд преимуществ:
- Существенная экономия средств по сравнению с покупкой готового полуавтомата
- Возможность настройки параметров под конкретные задачи
- Развитие навыков работы с электроникой
- Понимание принципов работы сварочного оборудования
- Возможность дальнейшей модернизации аппарата
Меры безопасности при самостоятельной сборке сварочного полуавтомата
При переделке инвертора в полуавтомат необходимо соблюдать следующие меры предосторожности:
- Отключать аппарат от сети перед любыми работами
- Использовать качественные комплектующие
- Тщательно изолировать все соединения
- Проверять работоспособность всех систем безопасности
- Не превышать номинальные параметры компонентов
- Проводить пробную сварку на низкой мощности
Соблюдение этих правил позволит безопасно собрать и эксплуатировать самодельный сварочный полуавтомат.
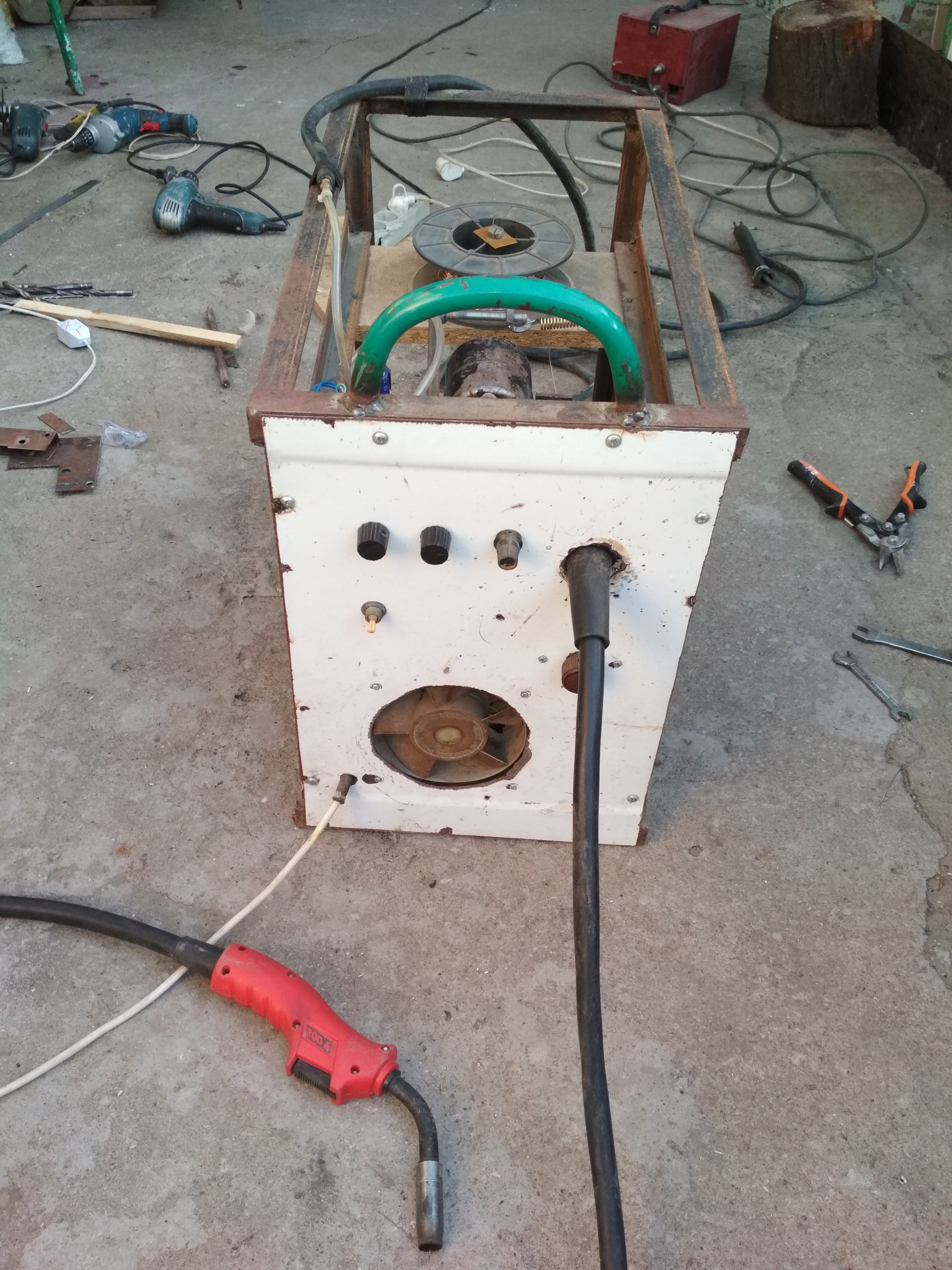
Особенности эксплуатации самодельного сварочного полуавтомата
При использовании самостоятельно собранного полуавтомата следует учитывать некоторые нюансы:
- Необходимость более частого технического обслуживания
- Возможные отклонения параметров от заводских значений
- Отсутствие гарантийного обслуживания
- Потребность в самостоятельной настройке режимов сварки
- Ограниченный ресурс работы некоторых компонентов
При правильной сборке и эксплуатации самодельный полуавтомат может прослужить долгие годы, обеспечивая высокое качество сварных соединений.
Схема простого сварочного полуавтомата
Сварочные полуавтоматы (СПА) находят все большее распространение в народном хозяйстве нашей страны. Их использование дает возможность многим мелким предприятиям эффективно сваривать металлические конструкции любой сложности. В этой статье рассмотрена конструкция наиболее простого сварочного полуавтомата, а также основные принципы работы и требования, предъявляемые к сварочным не нажатом положении). В других подающих механизмах двигатели имеют обмотку реверса движения.
В основном используют двигатели постоянного тока. В некоторых современных портативных СПА механизм подачи как бы вращается вокруг проволоки, тем самым, заставляя двигаться ее, благодаря нарезанию резьбы вокруг проволоки. Существуют подающие механизмы, находящиеся на рукаве у самого наконечника, они выполнены в виде цанги, которая является сердечником соленоидной катушки. При воздействии импульса цанга захватывает проволоку и оттягивает ее на небольшое расстояние, отпуская проволоку только в конце движения. При поступлении серии импульсов проволока потихоньку двигается.
В данной статье остановимся на самом простом варианте. Для любого простого СПА необходим в первую очередь сварочный трансформатор. Так как СПА обязан проваривать металл толщиной до 3 мм, то с учетом [1, 2] его мощность должна быть 1,8-3 кВт при напряжении холостого хода 40-60 В и крутопадающей характеристике (можно с низким КПД, т.е. собранном в любительских условиях). Для соблюдения мер безопасности в холостом режиме СПА не должен выдавать напряжение на наконечник рукава. Логика управления должна соответствовать диаграмме на рис.3, где имк — напряжение включения СПА, снимаемое с микровыключателя; идв -напряжение, подаваемое на двигатель; ирев — напряжение, подаваемое на реверсивную обмотку двигателя; Ucna -напряжение, подаваемое на рукав и на отсекатель газа.
Схема на рис.4 является наиболее распространенной, хотя имеет ряд недостатков. В некоторые СПА устанавливают трансформаторы с многовыводной первичной обмоткой. Это делается для возможности регулировки тока. Но, как показали многолетние испытания, регулировка таким способом отрицательно сказывается на качестве свариваемого шва. Поэтому автор использовал сварочный реостат R2 (рис.4), который также применяется при сварке электродами.
Изменение тока сварки с помощью реостата является наиболее простым и очень эффективным средством при регулировке сварочной дуги с разной толщиной металла. Автору удавалось сваривать изделия для швейной промышленности (оверлоков), имеющие размеры 5×5 мм с толщиной 0,5 мм, а также пруты для оконных решеток толщиной 1 см, и при этом никаких конструктивных изменений в СПА не вводилось.
При нажатии SA1 (рис.4) вольтметр РА1 показывает напряжение Х.Х., на наконечнике рукава напряжение отсутствует. При нажатии SA2 включается подача проволоки, контакты SA2.2 замыкаются, а SA2.1 размыкаются. Срабатывает реле К1, замыкаются контакты К1.1 — К1.3. Включается отсекатель тока КЗ, отсекатель газа К4, а К1.3 замыкает цепь питания двигателя М.
В данной схеме рассматривается двигатель с реверсивной обмоткой. Для двигателя подачи с электротормозом схема включения показана на рис.5 (где 1 — двигатель; 2 — электротормоз). Через К1.2 заряжается С11. По окончании режима сварки (SA2 не нажата) цепь питания К1 разрывается, а к К2 через замкнутые контакты SA2.1 от С11 подводится напряжение питания. В результате K2.1 и К2.2 замыкаются. Включается обмотка реверса двигателя М. А так как отсекатель тока КЗ и отсекатель газа К4 остаются включены, благодаря контактам К2.1, то на наконечнике рукава присутствует напряжение питания и подается углекислота.
Это необходимо для того, чтобы подающая проволока отгорела в месте окончания сварки без ухудшения качества свариваемого шва. Одновременно реверсивный режим работы двигателя демпфирует инерционность редуктора и якоря двигателя. По окончании разряда конденсатора С11 реле К2 отключается и СПА переходит в начальное положение.
Элементы.
Подающий механизм взят от сварочного полуавтомата типа А547УмПДГ-309. Реле K1, K2 типа ТКЕ-54ПД1 или аналогичные с максимальным током на контактах до 2 А. Реле КЗ КМ200Д-В, реле К4 — отсекатель газа (идет в комплекте с подающим). Трансформатор TV1 любой сварочный с габаритной мощностью 3 кВт. Выключатель SA1 — пакетный на 380 В, 15 А или два спаренных типа ВДС 6320-75 на 15 А. Предохранитель РА1 на 15 А. Силовой дроссель L1: сердечник из низкочастотного железа от трансформатора на габаритную мощность 1,5-3 кВт. Обмотка имеет 40-80 витков сечением 20 мм . Автор использовал стандартный дроссель от сварочного полуавтомата типа А547УмПДГ-309. L2 — ДФ2 или любой другой на ток 2 А. В зазор установлена полоска из текстолита толщиной 7 мм (рис.6). Диоды VD1-VD4 типа ВЛ-200-90 или другие низкочастотные с током пропускания не менее 100 А. Радиатор стандартный 7x8x10 см. VD9 — Д816Д на радиаторе с площадью рассеивания 100 см , VD5-VD8 — Д226 с любым буквенным индексом; C1,
C2 — 0,1 на 400 В, любые металлобумажные; СЗ-С8 -10000 на100 В типа К50-32, можно К50-18,К50-19; С9-С11 — 100 на 100 В К50-27, можно другие; R1 — шунт типа 75ШС ММЗ-500; R2 — реостат сварочный, можно от регулятора аргонно-дуговой сварки; R3 — 20 Ом ПЭВ-5-77; R4 — 47 Ом, реостат переменный 22 Вт; R5- 12 Ом ПЗ-75; R6- 100 Ом ПЗ-75; РА1 — вольтметр с пределом шкалы 75-100 В типа М43300, М43100; РА2 — амперметр с пределом шкалы 300500 А типа М43300, М43100.
Провода, указанные на схеме утолщенной линией, должны иметь площадь сечения не менее 20 мм.
Конструкция. На рис. 7 (а — вид сбоку; б — вид сверху) показана конструкция сварочного полуавтомата в сборе: 1 — трансформатор; 2 — диодный мост; 3 — дроссель L1; 4 — реостат R2; 5 — баллон углекислоты; 6 — «масса»; 7 -редуктор; 8 — подающий механизм; 9 — рукав; 10 — предохранитель; 11 — пакетный выключатель SA1; 12 -вольтметр, амперметр РА1 и РА2; 13 — регулятор скорости подачи R4.
Наладка СПА. От качества настройки СПА сильно зависит удобство пользования аппаратом, поэтому необходимо как можно внимательней отнестись к следующим рекомендациям. В данном простейшем варианте СПА «узким местом» является настройка подачи проволоки и настройка качества шва.
Настройка подачи проволоки
Подающий механизм следует включить без затяжки проволоки в рукав и без подсоединения углекислоты. Если углекислота подключена тумблером SA3 (он необходим для отключения отсекателя газа при затяжке проволоки в целях экономии С02), отключить отсекатель газа. При нажатии SA2 должны сработать отсекатель тока, отсекатель газа (при включенном SA3) и двигатель подающего механизма М. Через 5 с отпустить SA2 , при этом двигатель должен включиться в обратном направлении.
Заправить проволоку от барабана 1 через подающий механизм в рукав и затянуть ролик подачи, чтобы проволока 5 прижималась роликом 3 к подшипнику 4 и входила в рукав 2 (рис.8).
Включить SA2 на 20 с, после чего выключить. Механика очень инерционна, поэтому проволока сначала движется медленно, а со временем ускоряется. При отпускании SA2 ток в двигателе через реверсивную обмотку должен быть достаточен для полного торможения проволоки. Ток регулируют подстроечным реостатом R5. Для торможения проволоки необходимо время.
Обмотка реверса включена в цепь питания на время, определяемое временем разряда С11 через К2 и R6. Для нормального торможения проволоки, чтобы проволоку не затягивало обратно в рукав или не выводило дольше наконечника более чем на 1 см, необходимо очень точно и терпеливо отрегулировать R5 и R6, режим торможения зависит на 20% также от реостата R2. К сожалению, описать все подробности регулировки не позволяет объем статьи и, кроме того, невозможно учесть все нюансы разных серий подающих механизмов. Процесс сварки чаще всего будет прерывистым, т.е. с интервалом включения подачи проволоки примерно в 0,5-1 с. Настройка качества шва для проволоки диаметром 0,8-1 мм
Отрегулировать в процессе сварки подачу углекислоты в пределах 0,5-1 атм по манометру на редукторе. Установить в среднее положение реостат R2.
На чистом листе металла 0,7-0,8 мм при подсоединенной массе включить режим подачи проволоки. Если лист металла будет прожигаться, уменьшить подачу проволоки реостатом R4. При дальнейшем прожигании листа увеличить сопротивление реостата R2. Если проволока не расплавляется, а краснеет и ложится на лист небольшими кучками, увеличить реостатом R4 подачу проволоки или уменьшить сопротивление реостата R2.
Эти все процессы необходимо наблюдать через маску для электросварки. Как только шов будет ложиться нормально на лист металла, необходимо отрегулировать зазор в дросселе. Для этого измеряют вольтметром переменную составляющую в режиме сварки непосредственно между плюсом на рукаве и «массой». Регулируя зазор в дросселе, а также количество витков, добиваются переменной составляющей напряжения в пределах 1,2-3 В.
Надо учитывать слишком большую индуктивность дросселя. При этом ток, необходимый для нормальной сварки, будет нарастать через определенный промежуток времени, а в начальный момент подаваемая проволока не будет даже расправляться. В этом случае необходимо уменьшить количество витков на дросселе.
Для безопасности автор рекомендует все операции настройки проводить в резиновых перчатках на резиновом коврике в сухом помещении. Все детали, находящиеся под напряжением, следует изолировать. Для сварщика лучше использовать специальный сварочный костюм, так как при работе образуется большое количество окалины (брызг раскаленного металла).
Литература:
1. Пронский И.Н. Секреты сварочного трансформатора//Радюаматор.- 1998.-№1 .-С..21-22
2. Пронский И.Н. Секреты сварочного трансформатора//Радюаматор.- 1998.-№3.- С.43-45.К
Ответы на вопросы тех, кто хочет самостоятельно изготовить сварочный агрегат
1. Почему именно крутопадающая характеристика?
Большинство радиолюбителей при сборке СПА пользуются самодельными сварочными трансформаторами. Трансформаторы ручной сборки (не профессиональной) имеют низкий КПД и вследствие этого крутопадающую характеристику (рис.1, кривая А) [1]. Это выгодно сказывается при конструировании СПА, так как основная масса сварщиков имеет невысокие профессиональные навыки, а именно, умение правильно держать «рукав» (под правильным углом по отношению к свариваемой конструкции), правильно зажигать дугу и поддерживать ее горение. Как видим из рис.1, дуга имеет разные характеристики при различной ее длине 11, 12 где 11 и 12 ~ расстояние между электродами. При этом изменение тока незначительное, что выгодно влияет на фильтрацию переменной составляющей, а также на однородность свариваемого шва.
2. Как собрать трансформатор для СПА?
Этот вопрос является наиболее трудным, так как количество витков в трансформаторе напрямую зависит от свойств магнитного железа, применяемого в сердечнике трансформатора.
При расчете сварочного трансформатора в первую очередь необходимо учитывать габаритную мощность трансформатора, которая для нормального провара металла глубиной до 4 мм составляет примерно 3 кВт. Рассмотрим подробнее устройство трансформаторов [2].
Трансформатор состоит из следующих частей: сердечника, обмоток, каркаса и деталей, стягивающих сердечник. Сердечник трансформатора является магнитопроводом, который изготовляют из стальных листов толщиной 0,35…0,5 мм [3]. В настоящее время применяют два вида специальной электротехнической стали: горячекатаную с высоким содержанием кремния и холоднокатаную. Последняя имеет лучшие магнитные характеристики в направлении прокатки.
Стальные листы изолированы друг от друга бумажной, лаковой изоляцией (толщиной 0,04-0,6 мм) или окалиной, что позволяет уменьшить потери мощности в магнитопроводе за счет того, что вихревые токи замыкаются в плоскости поперечного сечения отдельного листа (рис.2). Чем меньше толщина листа, тем меньше сечение проводника, по которому протекает вихревой ток 1 В, и тем больше его сопротивление.
В результате вихревой ток и потери мощности на нагрев магнитопровода уменьшаются (по этой причине автор не советует использовать сердечники от электродвигателей).
По типу или конфигурации магнитопровода трансформаторы подразделяют на стержневые и броневые.
В стержневых трансформаторах обмотки, насаженные на стержень магнитопровода, охватывают его (рис.3,а) В броневых трансформаторах магнитопровод частично охватывает обмотки и как бы «бронирует» их (рис.3,6). Горизонтальные части магнитопровода, не охваченные обмотками, называются нижним и верхним ярмом. Трансформаторы большой и средней мощностей обычно изготовляют стержневыми, так как они проще по конструкции, имеют лучшие условия для охлаждения обмоток, что особенно важно в мощных трансформаторах, имеющих большие габариты. Магнитопровод таких трансформаторов набирают из отдельных пластин прямоугольной формы (рис.4,а, автор применил именно такую сборку трансформатора).
Для уменьшения магнитного сопротивления их набирают так, чтобы стыки пластин в двух соседних слоях были в разных местах. Аналогично выполняют магнитопроводы с двумя стержнями. Магнитопроводы броневого типа применяют для сухих трансформаторов средней мощности и используют в электросварке. Наружные броневые стержни этого магнитопровода частично защищают обмотки трансформатора от механических повреждений.
Трансформаторы малой мощности могут иметь магнитопровод, собранный из пластин, выполненных в форме буквы «Ш», и прямоугольных полос (рис.4,6) Магнитопроводы стержневых и броневых трансформаторов малой мощности можно навивать из узкой ленты электротехнической стали (рис.5). Это позволяет уменьшить воздушные зазоры в магнитопроводе и снизить магнитное сопротивление, а следовательно, и ток холостого хода. В большинстве случаев ленточные магнитопроводы разрезают, чтобы на них легче посадить заранее намотанные обмотки. Затем половинки магнитопроводов соединяют. Из ленточных магнитопроводов чаще всего для электросварки применяют кольцевые тороидальные (рис.5,в). КПД таких тороидальных трансформаторов очень высок. Поэтому количество наматываемых витков на сердечник меньше, чем в стержневых и броневых трансформаторах.
При изготовлении трансформаторов используют каркасы для намотки обмоток (рис.6). Как правило, их изготовляют из листовых электроизоляционных материалов (гетинакс или электроизоляционный картон). Размеры каркаса зависят от размера сердечника. У тороидальных трансформаторов каркас отсутствует, сердечник обматывают специальной лакотканью (стеклоткань или искусственная высоковольтная электротехническая ткань, пропитанная электротехническим лаком). Сердечник обматывают в два-три слоя тканью в натяжку и фиксируют нитками или пропитывают лаком. После высыхания лака наматывают обмотку.
Для изготовления обмоток трансформаторов и дросселей применяют круглые медные провода с эмалевой изоляцией (в первичной обмотке можно использовать указанные провода, при этом провода укладывают как можно ближе друг к другу, одновременно провод изолируют лакотканью (можно стеклотканью с пропиткой лаком), в случае намотки первичной обмотки двумя проводами каждый провод изолируют отдельно). Начало намотки фиксируют ниткой (рис.7). При этом провод должен выходить сбоку трансформатора, а не внутри его. Вторичную обмотку (силовую) наматывают прямоугольным проводом (изоляция провода аналогична рассмотренной выше).
Рассмотрим наиболее простой метод расчета сварочного трансформатора. Начальные данные: Ргаб=3 кВт; Uxx=45 В при Ih=0; Uh=30 В при 1н=100 А; исети=220 В; Рсети=50 Гц; допустимый КПД=0,85.
Автор использовал табличные данные из разных источников, поэтому они приближенные.
Воспользуемся методикой, предложенной в [4]. Имеем формулу
Как видим, полученное значение Км меньше табличного (табл.2). В этом случае полезно на 10% увеличить диаметр провода первичной обмотки, поскольку она расположена внутри и хуже охлаждается. В большинстве случаев конструирования сварочных трансформаторов число витков на 1 В достигает 0,7. Прежде чем наматывать вторичную обмотку, желательно собрать трансформатор и проверить ток холостого хода по методике, рассмотренной в [2].
Остановимся немного на технологии сборки трансформатора. Каркас изготовляем с внутренним окном (рис.6,б) не 10-20% больше размеров сечения сердечника. После сборки трансформатора в оставшиеся промежутки между каркасом и сердечником забиваем расклинивающие деревянные клинья для снижения уровня шума. При намотке на каркас обмотки (особенно вторичной) в окно каркаса вставляем деревянный брусок, а обмотку прибиваем к каркасу деревянным молотком (лучше через текстолитовую пластину, чтобы не повредить изоляцию проводов). Обмотки изолируем друг от друга специальным изоляционным материалом (табл.4)
Диэлектрическая проницаемость Епр не должна быть менее (в межобмоточной изоляции) 10 кВ/мм. Как правило, первичную обмотку наматываем первой, а вторичную -сверху первичной, изоляция между обмотками должна быть двойной. Если необходимого провода нет, то обмотку можно наматывая двойным проводом (одновременно), причем суммарная площадь сечения проводов должна быть на 10-20% больше расчетной.
Сердечник трансформатора стягиваем шпильками через отверстия (рис.4), при этом саму шпильку изолируем от сердечника электроизоляционной бумагой (табл.4). Для стяжки сердечника используем также бандаж или брусья (стальная лента шириной 40 мм, толщиной 1-3 мм) из маломагнитной стали. Как правило, верхнюю ярмовую балку стягиваем с обеих сторон пластинами, а нижнюю — уголками, которые играют роль шасси. От активной стали магнитопровода эти пластины изолируем с помощью полосы электротехнического картона толщиной 23 мм. Активную сталь магнитопровода и ярмовых балок заземляем в одной точке с помощью медной луженой ленты.
Автор: И.Н. Пронский, г. Киев
Литература:
1. Пронский И.Н. Секреты сварочного трансформатора //Радюаматор. — 1998.- №1.
2. Зызюк А.Г. О трансформаторах //Радюаматор.- 1998.- №2.
3. Иванов И.И., Равдоник B.C. Электротехника — М.: Высш. шк., 1984.
4.Мезель К.Б. Трансформаторы электропитания — М.: Энергоиздат, 1982.
Сварочный полуавтомат своими руками из инвертора: как сделать?
Время чтения: 7 минут
Полуавтомат для многих мастеров не просто инструмент. Это полноценный помощник в хозяйстве и на работе. Он может понадобиться каждому умельцу: от дачника до автолюбителя. Ведь полуавтомат отлично подходит для сварки всех типов металлов практически без ограничений по толщине и составу. При этом сварка может быть и профессиональной, и любительской.
Полуавтоматы появились не так давно в массовой продаже. Сварщики старой закалки помнят, как раньше варили металл с помощью больших громоздких трансформаторов. Однако, с развитием технического прогресса инженерам удалось сконструировать компактный и удобный полуавтомат. В начале 20 века он вытеснил аппараты прошлого поколения и завоевал уважения большинства сварщиков по всему миру.
Современный полуавтомат способен выполнять различные типы сварочных работ. Это может быть MMA сварка, MIG/MAG сварка, а также TIG сварка. Все это возможно благодаря «начинке» полуавтомата. В основе аппарата лежит стандартный инвертор. Это значит, что в теории полуавтомат можно собрать самому. Конечно, используя инвертор в качестве «донора». В этой статье будет все: и основы работы полуавтомата, и переделка сварочного инвертора в полуавтомат.
Содержание статьи
Устройство полуавтомата
Устройство полуавтомата — это первое, что вам нужно изучить, если вы хотите собрать свой аппарат.
Стандартный полуавтомат состоит из двух частей (или двух блоков): силовой и подающей. Подающая часть — это просто подающее устройство для полуавтоматической сварки. Но, давайте подробнее рассмотрим устройство полуавтомата.
Силовая часть, он же силовой блок — это, по сути, инвертор. Инвертор выполняет роль источника тока. Здесь все просто. А вот подающая часть представляет собой отдельно стоящий, подключаемый подающий механизм. Подающий механизм используется для подачи проволоки. Проволока продается в бобинах и бобина вставляется прямо в подающий механизм. Ее конец выходит через сопло горелки.
Конечно, вам необязательно использовать подающий механизм, чтобы выполнить полуавтоматическую сварку. Проволоку можно подавать и вручную. Но это крайне неудобно, и в таком случае теряется вся суть полуавтоматической технологии.
Вот и все компоненты. Этого, конечно, недостаточно, чтобы сделать сварочный полуавтомат своими силами. Еще вам придется докупить детали, но они зависят от типа вашего инвертора и способа, с помощью которого вы будете переделывать его в полуавтомат. Не забудьте про комплектующие (горелка, рукав, правильно подобранное сопло и т.д.).
Принцип работы
Принцип работы полуавтомата прост. Он будет понятен даже новичку, так что внимательно изучите эту информацию. Она пригодится для сборки самодельного аппарата.
Итак, все начинается с подачи горелки в зону сварки. Горелка совмещает в себе два устройства: из своего сопла она подает защитный газ и проволоку одновременно. Количество газа сварщик регулирует вручную, а вот проволока подается в полуавтоматическом режиме (отсюда и название «полуавтомат»). Именно поэтому в процессе у сварщика всегда занята лишь одна рука. Та, что держит горелку.
Как мы уже сказали, одновременно с проволокой в сварочную зону подается газ. В смеси газов между концом проволоки и поверхностью металл образовывается электрический разряд, благодаря которому плавится заготовка и сама проволока. Расплавленный металл смешивается с расплавленной проволокой. Далее можно формировать шов.
В данном случае проволока необходима и без нее сварка просто невозможна. Газ так же нужен, он защищает сварочную ванну от кислорода, поступающего извне. Но если у вас нет возможности использовать газ, вы можете взять специальную порошковую проволоку и варить только ею.
Полуавтомат из инвертора
Существует несколько способов, как можно из инвертора сделать рабочий полуавтомат. Мы перечислим самые интересные, на наш взгляд. Вы сможете воплотить их в домашних условиях, обладая базовыми знаниями в области электротехники.
Способ №1
Чтобы сделать инверторный сварочный полуавтомат своими руками, вам понадобится «донор». Без него сделать полуавтомат просто не получится. В качестве «донора» возьмите не самый слабый инвертор для ММА сварки. Он обязательно должен быть рабочим, и без проблем выполнять обычные сварочные операции.
Вам необходимо изменить вольт-амперные характеристики выбранного вами инвертора, чтобы он мог работать в режиме полуавтоматической сварки. Для этого можно использовать ШИМ-контроллер. Однако, этот вариант очень трудоемкий и не подойдет для тех, кто не силен в электротехнике.
Поэтому, чтобы собрать сварочный полуавтомат из инвертора своими руками, мы рекомендуем сделать дроссель. Для этого подойдет дроссель от лампы дневного света. И после дросселя нужно взять напряжение на обратную связь. Посмотрите ролик ниже, где подробно рассказывается суть этого способа. Там же в ролике есть понятная схема.
Способ №2
Второй способ крайне прост и подойдет для тех, кто обладает определенной инверторнойсваркой.Дело в том, что в продаже существуют инверторы, способные переключаться в режим с жестким изменением вольт-амперной характеристики.Если вы обладатель именно такого инвертора, то можете только порадоваться за себя.Чтобы превратить такой аппарат в полуавтомат, вам достаточно докупить внешний подающий механизм.
В комплекте с механизмом должны быть все необходимые кабели и разъемы. Вам достаточно без проблем подключить подающий механизм подачи сварочной проволоки к сварочному инвертору и можно варить. Можно считать, что в данном случае подающий механизм работает как приставка к инвертору для полуавтоматической сварки. Посмотрите видео ниже, где автор рассказывает про свой инвертор, к которому он подключил подающий механизм.
Способ №3
Последний способ превращения из сварочного инвертора в полуавтомат своими руками потребует некоторых знаний и навыков. В этом случае вам так же понадобится инвертор-донор. Учтите, что подойдет не любой аппарат. Вам нужен инвертор с компоновкой ZX-7. На выходе у него должен быть шунт, а на «первичке» должен быть трансформатор тока. Еще лучше, если у аппарата не будет никаких дополнительных функций вроде горячего старта или форсажа дуги.
Вам так же необходимо изменить вольт-амперные характеристики, а еще установить настройку нарастания тока. Дальнейшие действия напрямую зависят от схемы вашего инвертора. Так что не ленитесь найти темы на различных форумах, посвященных переделке инвертора в полуавтомат. Посмотрите видео ниже с тестом такого самодельного аппарата.
Читайте также: Как собрать сварочный аппарат своими руками?
Вместо заключения
Теперь вы знаете, как переделать сварочный инвертор в полуавтомат в домашних условиях. Такой аппарат станет отличной заменой полуавтомату заводского изготовления. Переделка обойдется недорого, и вы сможете развить свои навыки в сборке электроприборов. Самодельный полуавтомат хорошо переносит неаккуратное хранение и в целом неприхотлив к условиях работы. Еще одно преимущество самодельного аппарата — это его «начинка». Вы с точность до детали знаете, из чего он собран. Поэтому смоете быстро и недорого его починить в случае необходимости.
Но учтите, что не всегда самодельный полуавтомат из сварочного инвертора может решить все ваши трудности. Мы не рекомендуем переделывать инвертор под полуавтомат, если вы планируете использовать его как постоянный рабочий инструмент. Вы должны понимать, что самодельный аппарат может быть не таким надежным и продуманным, как заводской. И если вы будете выполнять сварку на выезде, то рискуете попасть в неприятную ситуацию. Для выполнения полупрофессиональной сварки лучше все-таки купить аппарат в магазине.
Конечно, в этой статье мы не затронули множество нюансов сборки самодельного полуавтомата. Но мы рассказали о самом главном. Инвертор можно переделать в полуавтомат, но это довольно трудоемко и самодельный аппарат будет работать немного хуже заводского. Вы должны понимать это, прежде чем примете верное решение. Желаем удачи в работе!
[Всего: 0 Средний: 0/5]схема самодельных аппаратов для сварки. Как сделать его из инвертора по чертежам?
Сварка уже давно является одним из довольно востребованных процессов при работе с такой структурой, как металлы. Её использование позволяет обеспечить создание и ремонт разнообразных поверхностей, выполненных из различного рода металлов и сплавов. Но сам по себе сварочный аппарат – сравнительно недешёвое удовольствие.
Хотя, в принципе, сделать сварочный полуавтомат своими руками в домашних условиях можно. Попытаемся разобраться, как самостоятельно сконструировать простое полуавтоматическое устройство для сварки и какие для этого понадобятся запчасти.
Особенности изготовления
Для понимания того, как собрать сварочный полуавтомат, требуется обладать кое-какими познаниями в области электротехники, ведь создание подобного прибора – не самая простая задача. Проще всего переделать устройство из инвертора. Чтобы это стало возможным, его мощность должна составлять не менее 150 ампер.
Также важным моментом будет наличие пусковой схемы сварочного полуавтомата.
В данном случае потребуется иметь под рукой трансформатор на 150 ампер, бобину, блок управления, механизм проволокоподачи, шланг газоподачи.
Лучше всего будет разместить все вышеупомянутые элементы в специальном корпусе. Например, корпусе от персонального компьютера или микроволновки.
Инструменты и материалы
Выше была уже упомянута часть материалов, которые потребуются для сборки рассматриваемого устройства. Но полный список элементов выглядит так:
- 150-амперный инвертор;
- механизм подачи проволоки;
- газовая горелка;
- шланг подачи, что выполняет роль направляющего рукава;
- газовый шланг;
- катушка с проволокой присадки;
- электронный блок управления.
Как можно убедиться, большинство указанных компонентов применяется без каких-либо изменений. Единственное, что нужно будет немного поработать с механизмом проволокоподачи, чтобы процесс шёл с такой же скоростью, как и плавка. Кроме того, следует предусмотреть регулятор, ведь скорость может изменяться. На это повлияют:
- диаметр проволоки;
- тип;
- категория материалов, что свариваются.
Пошаговая инструкция
Теперь приведем пошаговую инструкцию создания полуавтомата для сварки из китайских деталей:
- немного будет сказано о схеме;
- разберёмся, как произвести подготовку трансформатора;
- произведём подбор корпуса;
- разберёмся с блоком управления и катушками;
- создадим охладительный механизм.
Схема
Схему самодельного полуавтоматического устройства для сваривания можно найти на просторах Всемирной паутины. Различные варианты почти не отличаются. Главные их компоненты – чертежи, а также описание конкретной модели рассматриваемого устройства. Учитывая малое количество отличий, целесообразно будет рассмотреть некую общую модель.
Обычно подача проволоки производится благодаря применению небольшого электрического двигателя. Лучше всего в данном случае использовать стеклоподъёмник, которым оснащается любой автомобиль.
Но работу этой части устройства следует регулировать. Для этого можно применить ШИМ-регулировку. Качество сварной работы будет полностью зависеть от верности подачи проволоки. Она должна идти ровно и чётко, без каких-либо прерываний.
Если говорить о подаче газа, то следует произвести регулировку соответствующим образом. Лучше всего будет, если клапан газоподачи будет открываться на пару мгновений ранее, чем начнется подача электрода. Если регулировку настроить неверно, это может стать причиной преждевременного оплавления и вместо ванны будет происходить возгорание электрода. Естественно, что в этой ситуации о получении хорошего и крепкого шва можно забыть.
Реализация необходимой задержки проволоки к месту подачи сварки может быть осуществлена при помощи реле. Если говорить о клапане подавания, его можно снять с автомобиля, применив автомобильный воздушный клапан. В качестве альтернативы может быть использован и электроклапан от баллонного редуктора.
Подобная схема полуавтомата будет приблизительной, где описаны основные части устройства. Конечно, другие модели могут иметь модификации, но принцип работы устройства везде остаётся одинаковым.
Подготовка трансформатора
Трансформатор – главный элемент самодельного сварочного аппарата из инвертора. Следует знать, что чаще всего при самостоятельном конструировании его берут из обычной СВЧ-печи, попросту переделав его. Это основной узел, который обеспечит питание процесса сварки. Обычно принцип его действия являются снижающим. Причина этого состоит в том, что сетевое напряжение довольно большое, из-за чего его необходимо снизить до требуемого показателя.
Переделка данной части будет состоять в создании определённого количества витков на обмотке первичного и вторичного типа, ведь в микроволновке установлен трансформатор повышающего типа, а в данном случае требуется противоположный.
Основа работы рассматриваемого устройства будет следующей: когда осуществится подключение к сети по контуру первичного типа, по нему начнёт идти ток переменного характера, что будет формировать магнитный поток. В обмотках начнёт индуцироваться ЭДС, что будет зависеть от наличия некоторого количества витков кабеля.
Если максимально упростить, то намотав на первичную обмотку 100 витков, а на вторую, предположим, 5, получим трансформационный коэффициент, равный 20. А в результате он даст где-то 11 вольт, то есть почти в 20 раз меньшее значение, чем в электросети.
То есть, делаем мы переделку, чтобы изменить количество витков на обмотке вторичного типа, ведь их существенно больше, чем потребуется. Но в этом вопросе лучше сильно не спешить. Если сила тока будет очень велика, то может случиться возгорание проводки, и трансформатор просто сгорит. А слабый ток не позволит устройству работать нормально.
Найти идеальное значение можно лишь исходя из расчётов. Сначала требуется понять, сколько напряжения будет на намотках, каким будет ток и иные показатели.
Именно на основе этих характеристик и должен производиться расчёт сердечника, намоток и подбор проводов с соответствующим сечением.
При проведении расчётов следует принимать во внимание большое количество характеристик. В данном случае лучше воспользоваться онлайн-калькуляторами.
Подбор корпуса
Если смотреть на схему сварочного аппарата, то можно увидеть, что тут присутствует немалое количество различных частей. Естественно, что они должны быть правильно размещены в корпусе устройства. Требований к нему не очень много, ведь он никак не влияет на работоспособность нашего полуавтомата. Но правильный подбор корпуса может существенно повысить комфорт работы с устройством.
Лучше всего будет использовать в данном случае короб, выполненный из тонколистового металла. Все размеры тут следует продумать заранее. Чтобы получить действительно удобный и практичный корпус, стоит предварительно сделать чертеж, где нужно отметить места расположения всех частей агрегата.
Когда короб будет изготовлен, в него следует поставить трансформатор, регулятор подачи проволоки и другие элементы, согласно схеме. Важным моментом, которым не следует пренебрегать, является механизм охлаждения. Он нужен, чтобы трёхфазный инвертор работал стабильно, ведь именно этот элемент нагревается больше всего. За охлаждение в данной конструкции будут отвечать вентиляторы, которые лучше всего будет расположить по бокам корпуса внутри.
Экономить на вентиляции нет нужды, и нагнетаемый воздух должен максимально быстро выводиться наружу.
Неплохим решением в этом вопросе будет корпус от компьютера. Его сильными сторонами будет наличие требуемых отверстий и места для вентиляторов.
Плата управления
Одним из важнейших элементов рассматриваемого устройства является блок управления. Он состоит из таких частей:
- реле;
- генератора задающего типа;
- защиты от перегрузок температурного характера;
- обратной связи.
Нелишним будет оборудовать наш полуавтомат регулятором тока, который вполне можно сделать самому. После окончания всех работ управляющую плату следует присоединить к силовому блоку устройства перед подключением в электросеть. После этого остаётся проверить работоспособность блока при помощи осциллографа через его присоединение к выходам.
Катушки
Как уже говорилось, в корпус полуавтомата из аккумулятора или любого другого приспособления, сделанного собственноручно, монтируются трансформаторы. После этого их следует совместить. Точнее, совместить первичные катушки со вторичными. Сделать это можно так: первичные намотки соединяем параллельно, а вот вторичные будут соединяться последовательно.
Благодаря этому появится возможность получить на выходе большую силу тока, которой будет вполне достаточно для бесперебойной работы устройства. То есть получится полуавтомат с вольтодобавкой.
Система охлаждения
Как уже стало ясно, во время постоянной работы трансформаторный импульсный инвертор может сильно перегреваться. Поэтому тут требуется хорошая система охлаждения.
Простейшим методом, который позволит осуществлять охлаждение элементов полуавтомата, будет монтаж вентиляторов, которые можно установить по бокам корпуса.
Их следует установить так, чтобы они могли работать исключительно на выдув. Кулеры можно вытащить из отработанного блока питания от компьютера. Кстати, не забудьте проделать отверстия для вывода воздушных масс в корпусе механизма. Их размер должен быть не меньше 5 миллиметров.
Использование самодельного аппарата
Чтобы нормально использовать самодельный сварочный полуавтомат, требуется чётко понимать, что его долговечность и надёжность зависят от того, насколько будет соблюдаться температурный режим. Нормальными будут считаться значения на радиаторах около 75 градусов по Цельсию.
При перегреве, поломке либо замыкании пользователь будет оповещён сигналом звукового характера. Кроме того, электронный блок управления автоматически снизит ток для работы до 20 ампер, а звуковое оповещение будет сохраняться до нормализации ситуации.
Необходимо точно знать, что именно вы делаете и для чего. Кроме того, следует использовать самодельный прибор исключительно по его прямому назначению и не пытаться применять его для чего-то ещё. Следует помнить и о том, что перед началом эксплуатации не будет лишним проверить его работоспособность.
О том, как сделать сварочный полуавтомат своими руками, смотрите далее.
Сварочный полуавтомат своими руками: схема и устройство
Сварочный полуавтомат предназначен для сварки металлоконструкций различного типа и проведения кузовного ремонта. Устройство позволяет накладывать соединительные швы на тонком металле точно и аккуратно. Может отличаться по типу и конструкции, но в любом случае, должно отвечать критериям качества, безопасности и многофункциональности. Можно сделать сварочный полуавтомат своими руками из инвертора. Тем более, что схема сборки достаточно простая.
Как работает сварочный полуавтомат
Нагрев и деформация соединяемых поверхностей происходит под действием электрического разряда, формируемого металлом и электродом, которые находятся под напряжением. Инертный газ предотвращает появление окислов, что благоприятно сказывается на качестве шва.
Полярности сварочного полуавтоматаПолуавтомат имеет выходы обратной полярности: «плюс» и «минус». Один из них подключается к детали, а второй — к подвижному контакту сварочной горелки. Полярность подключения определяется по типу свариваемого материала.
Инвертор необходим для обеспечения и контроля сварочного процесса, а также для перемещения и регулировки горелки. Сварочный аппарат работает от постоянного тока, поэтому необходимо устройство преобразования переменного тока электрической сети. В него входит высокочастотный трансформатор, выпрямители и модуль с электронной схемой, включающей микроконтроллер для управления рабочим током.
Аппарат должен обеспечивать заданную скорость перемещения проволоки, напряжение и силу тока. Равновесие характеристик обеспечивает источник питания дуги с необходимыми вольтамперными показаниями. Длина дуги зависит от напряжения, а скорость подачи стержня — от величины сварочного тока.
Работа установки начинается с предварительной продувки системы, необходимой для последующего поступления газа. После этого подключается источник питания дуги и подается катанка.
Основное преимущество автоматической сварки в том, что сварочная проволока подается в рабочую зону автоматически, и нет необходимости менять электроды.
Что необходимо приготовить из инструментов и материалов
Для изготовления самодельного полуавтомата необходимы следующие базовые элементы:
Из чего состоит сварочный полуавтомат своими руками- Источник питания и стабилизатор напряжения;
- Блок управления сварочным током;
- Специальные сварочные горелки;
- Рукава и зажимы;
- Тележка для перемещения;
- Устройство равномерной подачи проволоки;
- Гибкий шланг с газопроводом, гнездом для проволоки, силовым и управляющим кабелем;
- Клапан отсекания газа с электромагнитным управлением;
- Бобина с намотанной проволокой;
- Модуль управления.
Последовательность сборки
Сборочные работы начинаются с выбора необходимого корпуса. Подойдет короб или ящик подходящего размера из пластика, текстолита или фанеры толщиной 6 мм, либо листового металла.
В него встраиваются трансформаторы, связанные первичными и вторичными обмотками. Для первичной обмотки применяется параллельная схема подключения, а для вторичной – последовательная. Такое исполнение обеспечивает поступление тока до 60 А. Максимальное сварочное напряжение на выходе будет 40 В. Полученные рабочие характеристики позволяют сваривать маленькие металлоконструкции бытового назначения.
Непрерывная работа инверторного устройства вызывает перегрев. Чтобы этого не произошло, в конструктивную схему встраивается система охлаждения. Самым простым способом снижения нагрева является установка по бокам корпуса вентиляторов. Они размещаются напротив трансформаторов так, чтобы работать на вытяжку.
Для сварочного полуавтомата используют блок охлаждения от устаревших моделей компьютеров. Обеспечить отвод теплого воздуха и поступление свежего поможет ряд отверстий в корпусе диаметром не меньше 5 мм. Количество отверстий — 20-50 штук.
Доработка инвертора
Полуавтомат из сварочного инвертора может получится, если его трансформатор несколько модернизировать. Инвертор для этих целей выбирают такой, чтобы он мог выдавать ток для сварки не меньше 150 А. В готовом виде устройство использовать не получится по причине несоответствия вольт-амперных характеристик условиям сваривания электродной проволокой в защитном газе.
Функциональная схема инверторного полуавтоматаЧтобы получить необходимые выходные параметры, достаточно обмотать трансформатор полосой из меди с изоляцией из термобумаги. Толстый провод использовать не получится, потому что он сильно греется. У вторичной обмотки должно быть три слоя из жести, изолированных между собой фторопластовой лентой. Концы соединяются между собой методом пайки с целью повышения токопроводности.
В процессе работы установка будет сильно греться. Особенно в зоне радиатора, куда нужно установить термодатчик, чтобы обеспечить автоматическое отключение устройства в случае перегрева.
После включения полуавтомата индикатор должен показать ток 120 А, что подтвердит правильность выполненной доработки и подключения. Случается, что на табло светятся восьмерки. Так бывает при низком напряжении в сварочном контуре.
Про дроссель и сварочную горелку
Дроссель для сварочного полуавтомата своими руками сделать вполне по силам. Для этого потребуется трансформатор и эмальпровод, диаметр которого не превышает 1,5 мм. При наматывании после каждого слоя укладывается изоляция. С помощью шины размером 2,5х5,4 мм нужно плотно намотать 24 витка. Концы шины оставляют по 30 см.
Дроссель для сварочного полуавтоматаСердечник прокладывается кусочками текстолита с зазором как минимум 1 мм. Для наматывания дросселя еще используют металл от цветного телевизора лампового типа. Однако в этом случае удастся установить лишь одну катушку. Полученное устройство способно стабилизировать ток сварки и выдавать свыше 24 В при токе 6 А.
Сварочная горелка является конечным рабочим органом, обеспечивающим подачу углекислого газа, дуги напряжения и электродной катанки в зону сваривания. Рекомендуется пользоваться готовым пистолетом, где есть пусковое устройство, рукав для подключения газа и подачи сварочного металла.
Как обеспечить работу устройства подачи сварочной проволоки
Несмотря на надежность инвертора, поломки все же случаются. Чаще всего в ремонте нуждается регулятор, подающий металл от специальной катушки по гибкому шлангу. Для сварки полуавтоматом применяется проволока разного диаметра (от 0,8 мм до 1,6 мм), потому и возникает необходимость в регулировании подачи. Равномерный и качественный шов получается, когда скорость плавления и скорость поступления катанки совпадают.
В устройство входит прижимной ролик с регулятором усилия прижима проволоки. Ролик подачи с двумя неглубокими выемками подает сварочную проволоку. В качестве роликов можно использовать подшипники подходящего диаметра. По наружному кольцу достаточно проточить небольшую канавку для направления стержня.
Штанги, с установленными роликами, подпружиниваются. Усилие регулируется болтом, к которому и закреплена пружина.
Неполадки с регулятором связаны с ненадежным креплением для достаточно большого узла. Перекос способен привести к сбою в работе сварочного полуавтомата.
Располагать устройство в основном корпусе при создании сварочного полуавтомата необходимо так, чтобы разъем был в удобном для работы месте. Сборочные единицы должны закрепляться четко одна напротив другой для равномерного продвижения проволоки. Центрирование роликов осуществляется относительно отверстия входного штуцера.
Следует учесть, что самодельное устройство не сможет работать при низкой температуре. Установка рассчитана только на летний период и эксплуатацию внутри помещений. «Сварочник» успешно справится с небольшими бытовыми задачами, а для производственных нужд лучше приобрести готовый инвертор.
Видео: Сварочный полуавтомат своими руками
устройство, принцип работы, схема сборки и регулировка
В настоящее время многие владельцы машин или те, у кого есть частный дом, сталкиваются с проблемой небольшого ремонта. В этом случае помогает сварочный полуавтомат — устройство для сварки различных видов сталей. С его помощью легко починить деталь машины, изготовить необходимую металлическую конструкцию. Скорость работы напрямую зависит от подающего механизма для полуавтомата. Его несложно изготовить самостоятельно.
Общие сведения
Сварочный полуавтомат — это прибор, предназначенный для соединения металлов методом электродуговой сварки. Отличие от классического сварочного аппарата в том, что вместо привычных вольфрамовых электродов применяется плавящаяся проволока. Она намотана на специальную бобину и по мере выполнения рабочего процесса автоматически разматывается. Так же при такой сварке используют электроды Э42.
Таким образом, происходит постоянная подача электрода в сварочную ванную. Саму сварку вручную проводит сварщик, который может регулировать скорость размотки катушки с проволокой.
Полуавтоматические устройства разделяются в зависимости от степени защиты сварочной зоны, а именно:
- Приборы, предназначенные для сварки с флюсом. В этом случае флюс входит как добавка в саму проволоку. Это достаточно дорогой способ и в самодельных устройствах используется редко.
- Аппараты, использующие газовую среду. Самый популярный и массовый способ среди сварщиков.
- Полуавтоматы, работающие со специальной порошковой проволокой. Этот вариант обычно используется совместно с газовой защитой.
Лучше всего полуавтомат раскрывает свои преимущества, когда нужно аккуратно, красиво и точно соединить стальные тонкие детали. Соединение будет надежным при самых разных марках стали, таких как легированные, низкоуглеродистые, нержавеющие.
Принцип работы
Самым распространенным видом сварочного прибора являются устройства, работающие в защитной газовой среде. Устройство сварочных полуавтоматов этого типа принципиально одинаково.
Основными узлами являются:
- Источник питания. Разные модели рассчитаны на разное напряжение. Оно может быть как однофазным, так и трехфазным. С помощью переключателя можно переходить с 380 вольт на привычные 220 вольт, что позволяет использовать агрегаты не только на производстве, но и в обычных бытовых условиях. Ток передаётся или через самодельный трансформатор, или через инвертор. Инвертор понижает напряжение и повышает силу тока.
- Электродная горелка вместе с трубкой для подвода газа.
- Баллон с газом для защиты зоны плавления.
- Специальный механизм движения проволоки.
- Блок управления и настройки.
Подача проволоки бывает в основном двух типов: толкающего или тянущего. Иногда применяются оба способа одновременно.
В моделях с толкающим механизмом проволока для сварки движется внутри направляющей трубки, когда специальный узел толкает наружу. В случае если применяется тянущий тип, то узел подачи расположен в глубине горелки и вытаскивает на себя электродную проволоку с бобины.
Принцип работы полуавтоматической сварки предусматривает управление и регулирование важнейших параметров: величину напряжения, силу тока и скорость разматывания катушек. Регулирование может быть переменным, с плавным изменением значений или ступенчатым. Некоторые устройства самостоятельно выбирают скорость подачи проволоки в зависимости от установленных сварочных значений.
Порядок действий при работе с аппаратом:
- Кнопкой «Пуск» включается источник питания.
- Выпускается на горелку защитный газ и подается напряжение.
- Узел подачи разматывает катушку.
- Между проволокой и поверхностью металла возникает электрическая дуга, и проволока начинает плавиться.
- Газ защищает зону плавления.
- Происходит сваривание металлических частей.
Сборка устройства
Если есть основные знания по базовым понятиям в электронике, при наличии некоторых инструментов и желания можно собрать сварочное полуавтоматическое устройство самостоятельно.
Для успешного проведения сварки важно, чтобы основные значения напряжения, силы тока и скорости движения электрода находились в оптимальном равновесии. Для этого нужен источник питания, имеющий стабильное вольт-амперное значение. Неизменяемое напряжение поддерживает постоянную длину дуги. Сварочный ток регулирует величину скорости движения проволоки и величину импульса, необходимого для розжига и поддержания ровного горения.
Конструирование трансформатора
Мощность трансформатора в сварочном устройстве зависит от величины сечения проволоки. Например, в стандартном варианте, при толщине проволоки до одного миллиметра, величина силы тока может составлять 160 ампер. Для получения такой величины необходим трансформатор с мощностью не менее трех киловатт. Сердечником трансформатора служит ферритовая металлическая конструкция кольцеобразной формы.
Сердечник должен иметь диаметр в 40 квадратных сантиметров. Первичная обмотка состоит из провода ПЭВ, у которого толщина около двух миллиметров. Провод вплотную наматывается на сердечник, и количество витков должно быть равно 220. Нужно следить за плотностью прилегания витков — свободного пространства не должно быть. После создания первого слоя создается еще один слой из бумажной или тканевой ленты, который закрепляется тесемкой.
На вторую часть наматывается вторичная обмотка. Для неё требуется медный провод с диаметром не менее 60 квадратных миллиметров. Наматывается 56 витков. Как и в первом случае, после этого создается второй защитный слой.
Полученный трансформатор с мощностью в три киловатта и силой тока до 200 ампер способен обеспечить правильную скорость движения гибкого электрода.
Механизм автоподачи
Проволокоподающий механизм, отвечающий за самостоятельную подачу электродной проволоки в ванную сварки, — один из самых ответственных узлов прибора. Механизм подачи проволоки для полуавтомата своими руками можно собрать из узла обычных дворников автомашины. Вполне подойдет стеклоочиститель от ГАЗ-69. Сварочная горелка соединена с протяжкой для полуавтомата. Своими руками чертежи делать уже не надо, они есть в свободном доступе:
Схема податчика включает в себя:
- Основание (1).
- Проволоку (7).
- Направляющий рукав (6).
- Ведущий ролик подачи и ведомый (2, 10).
- Ось ролика ведомого (14).
- Кронштейны (5, 12).
- Пружинку прижимную (11).
- Подшипник втулочный и стопор в виде гайки (3).
- Катушечный стержень (8).
- Планку прижимную (9).
- Штуцер дистанционный (16).
- Вал выходной редуктора (4).
- Обойму ролика ведомого (13).
- Шайбу (15).
Часть горелки связана одновременно с протяжным механизмом для полуавтомата, с узлом подачи защитного газа и блоком проводки электротока. Сама проволока пропускает электрический ток, а по шлангу подается газ. Проволока вставляется в один конец направляющей трубы с резьбой диаметром 4 миллиметра и протягивается через длинную трубку в направляющую сварочной горелки. В качестве направляющей можно использовать оболочку от спидометра автомобиля сечением 1,2 миллиметра.
Кнопка запуска на кронштейне прикрепляется к каналу внутри горелки, где подключается к кабелю. Там же монтируют трубку подвода газа. Горелка состоит из двух идентичных половинок, а провода и шланги собираются в один жгут и скрепляются специальными прищепками или металлическими полосками.
В конструкцию сварочной горелки входят:
- Кнопка запуска (7).
- Кронштейн (8).
- Направляющая (1).
- Защитная обшивка (13).
- Рукав для проволоки (2).
- Канал-основа (3).
- Инжекторная трубка (4).
- Газовый шланг (5).
- Провод (6).
- Винт стопора (9).
- Гайка из латуни (10).
- Шайбочка (11).
- Втулка с наконечником (12, 14).
Лентопротяжный механизм может быть организован с помощью электромотора с редуктором от автомобильных дворников. Например, от ГАЗ-69.
Перед началом обработки двигателя надо убедиться, что его вал вращается в одном направлении, а не «влево-вправо».
Необходимо выходной вал сточить до 25 миллиметров и нарезать на нём левую резьбу сечением в 5 миллиметров.
Впереди на роликах вырезают зубья шириной в 5 миллиметров и создают зубчатое соединение. Сзади на роликах делаются сечения шириной до 10 миллиметров для лучшего сцепления с проволокой. На ось, которая пересекает проволоку и втулку, насаживается один конец рамки ведомого ролика. Второй конец скрепляется с пружиной, которая зажимает электродную проволоку между роликами.
Весь узел подачи вместе с газовым клапаном, выключателем и резисторами располагают на текстолитовой плате. Она же закрывает щиток управления. Подающая бобина с проволокой устанавливается в 20 сантиметрах от узла подачи.
Во время подготовки к работе направляющие приближают к роликам и закрепляют при помощи гаек. Проволоку через направляющие протягивают в горелку. Наконечник прикручивают к горелке и надевают защитную обшивку, который закрепляется винтами. Газовый шланг соединяется с клапаном, и в редукторе создают давление около полутора атмосфер.
Электрическая схема протяжки
На скорость протягивания проволоки влияет не только механическая, но и электрическая часть устройства.
Электрическое управление происходит по такому сценарию. Когда включен переключатель SB1, то при замыкании кнопки SA1 начинает срабатывать реле K2. Его работа задействует реле К1 и К3. Один из контактов К1.1 отвечает за газовую подачу, при этом К1.2 соединяет цепь и включает подачу электрического тока к электродвигателю. Двигательный тормоз выключается через К1.3. Время обратных действий задается резистором R2, и через этот промежуток времени срабатывают контакты реле К3. Результатом этих действий является подача газа в горелку, но процесс сварки еще не начат.
Сварочный процесс начинается после того, как зарядится конденсатор С2 и выключится реле К3. Тогда электродвигатель запускается, срабатывает реле К5, начинается подача проволоки и сварка. О сварочной проволоке св08г2с можно узнать здесь.
Главным элементом узла управления, который отвечает за стабилизацию тока, является микроконтроллер. Параметры и возможность регулировки силы тока зависят от этого электрического элемента.
Когда размыкаются контакты кнопки SA1, в свою очередь, размыкается реле К2, тем самым выключая реле К1. Подача тока прекращается с помощью контакта К1.1, и тогда сварка прекращается.
Окончательный монтаж
Сначала в каркас монтируется преобразующий трансформатор с узлом управления. К трансформатору присоединяется сетевой кабель. Отдельным узлом собирается блок управления. Его блок при помощи кабеля подключается к трансформатору и горелке. Затем баллон с газом соединяется с горелкой.
Для изготовления и сборки нужен такой набор инструментов:
- Сварочный аппарат.
- Тиски с зубилами.
- Паяльник.
- Молоток.
- Плоскогубцы.
- Болгарка.
- Острый нож с линейкой.
- Комплект метчиков.
- Ножовка и дрель.
Правила безопасности
Сварочный полуавтомат замечательно подходит для выполнения ряда работ в домашних условиях. С его помощью даже новичок может получить чистый и красивый шов при сваривании различных материалов.
Чтобы работа была комфортной и производительной, нужно соблюдать ряд важных правил и особенно требования техники безопасности, а именно:
- К сварочному аппарату должен быть свободный доступ со всех сторон.
- Перед началом работ необходимо проверить заземление прибора и исправность всех соединений.
- Смотреть на световую дугу нужно через специальные средства защиты глаз.
- Сварочные работы в помещении нужно проводить при постоянном проветривании.
- Любые ремонтные работы надо проводить во время полного обесточивания устройства.
Соблюдение несложных правил сведет к минимуму риск травматизма, ожогов и обеспечит производительную сварку.
Полуавтомат сварочный 547Д1 типа ПДГ-101
Полуавтомат сварочный 547Д1 типа ПДГ-101
- Подробности
- Категория: Электродуговая сварка
Полуавтомат предназначен для электродуговой сварки малоуглеродистых сталей стальной электродной проволокой сплошною сечения в защитной среде двуокиси углерода.
Применение проволоки малых диаметров при сварке в двуокиси углерода в сочетании с жесткой или пологопадающей характеристикой сварочного тока обеспечивает:
1) безотказное возбуждение дуги при подаче электрода к изделию (за счет мгновенного расплавления) без предварительного реверсирования электрода;
2) высокую устойчивость процесса, стабильность режима сварки и незначительное разбрызгивание электродного металла;
3) высокое качество сварного шва на всем протяжении благодаря подаче газа в зону сварки до зажигания дуги и после обрыва ее;
4) хорошее формирование шва и простоту заделки кратера;
5) выполнение сварочных швов в любых пространственных положениях.
В связи с тем, что сварка производится малыми токами, удается без подкладки варить стыковые швы металла толщиной 1—2 мм даже при наличии относительно больших зазоров.
Скачать документацию
Устройство и работа
1. Подающий механизм.
1.1. Подающий механизм (рис. 2) предназначен для подачи электродной проволоки в зону дуги. Механизм приводится в движение от двигателя 2. Редуктор 6 передает вращение ролику подающему 10.
Проволока, поступающая из кассеты 8, проходит через трубку 13 между роликом подающим 10 и шарикоподшипником 11. Шарикоподшипник насажен на эксцентрик 12, с помощью которого можно поднимать и опускать шарикоподшипник при наладке полуавтомата.
В корпусе механизма помещен электромагнитный отсекатель газа 5 предназначенный для включения подачи газа перед началом сварки и отключения подачи газа после окончания сварки. Отсекатель газа срабатывает от кнопки включения 7 (см. рис. 1) или от кнопки на держателе горелки 9. Подающий механизм вместе с кассетой для электродной проволоки и отсекателем газа смонтирован в компактном корпусе 7 (рис. 2), имеющем форму небольшой) чемодана размером 355X235X130 мм.
Кассета крепится винтом 9 с левой резьбой.
Подающий механизм устанавливается у рабочего места и переносится сварщиком за ручку 1. При работе в стационарных условиях подающий механизм крепится на рабочем столе, для чего и дне корпуса имеются два отверстия. В этом случае целесообразно пользоваться проволокой из бухты, уложенной на вертушку.
1.2. Масса подающего механизма без электродной проволоки не более 6,0 кг.
1.3. Кассета вмещает до 5.5 кг электродной проволоки. В комплект подающего механизма полуавтомата входят три сменных подающих ролика диаметром 18, 32 н 47 мм, обеспечивающих ступенчатое изменение скорости подачи электродной проволоки.
1.4. Плавное изменение скорости подачи внутри диапазона обеспечивается изменением числа оборотов электродвигателя 2 с помощью резистора 4.
1.5. Электромонтажный чертеж подающего механизма приведен на рис. 3.
2. Электродвигатель
2.2. Электродвигатель (рис. 4) состоит из следующих основных узлов:
1) корпуса с полюсами и катушками возбуждения;
2) якоря с коллектором и крыльчаткой;
3) переднего (со стороны привода) и заднего (со стороны коллектора) щитов: последний — с суппортом и щеткодержателями.
2.3. Корпус 2 электродвигателя, являющийся магнитопроводом, изготовлен из стали 10. К внутренней поверхности корпуса крепятся два полюса 4.
Полюсы изготовлены из стали 10. На полюсах расположены катушки возбуждения 3.
Якорь электродвигателя состоит из стального вала 19, пакета железа 14. обмотки 15. коллектора 9 и крыльчатки 1, предназначенной для охлаждения электродвигателя.
Коллектор выполнен на пластмассовой основе и состоит из медных ламелей, изолированных одна от другой прокладками из коллекторного миканита.
Якорь монтируется в двух шарикоподшипниках 18 с одной защитной шайбой.
Па внутренней торцовой стороне шита 10 расположен суппорт с двумя щеткодержателями 5. Щеткодержатели снабжены ленточными спиральными пружинами 6, прижимающими щетки к коллектору.
Для подхода к щеткам и коллектору в щите сделаны окна, которые закрываются колпаком 11.
2.4. Электрическая схема электродвигателя приведена на рис. 5.
3. Отсекатель газа.
3.1. Отсекатель газа (рис. 6) состоит из следующих основных частей:
1) корпуса 1, состоящего из стоики, гильзы и конического полюса;
2) крышки 2 с входным и выходным штуцером;
3) якоря 3 с уплотняющими резиновыми прокладками;
4) пружины 5;
5) катушки 4;
6) корпуса 6.
3.3. Отсекатель газа представляет собой электроклапан, открывающийся при подаче на него напряжения 16 — 32 В
Материал магнитопроводящих деталей — сталь 10.
Катушка намотана проводом ПЭТВ-1*0,250, число витков 3150±50, сопротивление (77±7) Ом.
Трущиеся поверхности якоря и пружины смазаны тонким’слоем теплостойкой смазки.
На якоре установлены две резиновые прокладки толщиной по 2 мм, что позволяет производить ремонт уплотнения сменой рабочей поверхности прокладок.
4. Горелки.
4.1. Горелка предназначена для подвода сварочного тока к электроду, направления движения электродной проволоки и подачи двуокиси углерода непосредственно в зону сварки.
Полуавтомат комплектуется двумя типами горелок со шлангами:
1) горелкой для электродной проволоки диаметром 0,8—1,0 мм (рис. 7) для сварки токами до 200 А. Длина шланга 1,5 м;
2) горелкой для электродной проволоки диаметром 1,0— 1,2 мм (рис. 8) для сварки токами свыше 200 А. Длина шланга 2,5 м. Горелка имеет поворотный мундштук с углом поворота на ±360° и фиксирующую гайку.
4.2. Обе горелки состоят из мундштука и гибкого шланга.
На мундштуке расположено сопло 2 (рис. 7 и 8), изолированное от токоведущих частей втулкой 5. Свеча 3 и наконечник 1 обеспечивают подвод тока к электродной проволоке.
Конструкция мундштуков обеспечивает быструю и легкую смену сопла и наконечника или снятие их для очистки от брызг
Гибкий шланг, состоящий из двух стальных спиралей, заключенных в плетенку и резиновую трубку, предназначен для подвода сварочного тока и электродной проволоки от подающего механизма к мундштуку.
4.3. В шланге для проволоки диаметром 1,0—1,2 мм, кроме того, имеется трубка для подвода двуокиси углерода к мундштуку.
Конструкция обеих горелок обеспечивает возможность извлечения и чистки внутренней спирали.
5. Кнопка включения.
5.1. Кнопка включении 7 (рис. 1) предназначена для включения полуавтомата при работе горелкой для проволоки диаметром 0,8—1,0 мм.
Кнопка включения может устанавливаться на ручке защитного щитка и включается большим пальнем руки. Вилка Х5 кнопки включения подсоединяется к розетке Х5 подающего механизма.
5.2. При работе горелкой для проволоки диаметром 1,0—1,2 мм кнопка включения встроена непосредственно в ручку горелки. Её провода вмонтированы и шланг и также подключаются к розетке Х5 подающего механизма.
6. Регулятор У-ЗОП-2.
6.1. Регулятор расхода газа с указателем расхода и подогревателем предназначен для подачи газа к сварочному посту с постоянным расходом.
Регулятор обеспечивает понижение давления с 5390—4900 кПа (55—50 кгс/см2) до 294—98 кПа (3—1 кгс/см2).
6.2. Подогреватель предназначен для подогрева газа, поступающего из баллона в редуктор, с целью предотвращения замерзания редуктора. Напряжение питания подогревателя Umax =36 В.
7. Выпрямитель.
7.1. Устройство выпрямителя показано на рис. 9.
Па каркасе 1 установлены основные узлы и летали выпрямителя: силовой трансформатор 13. вспомогательный трансформатор 3. дроссель 4, рама 16, панели передняя 5 и задняя 12, стенки правая 18 и левая 20, панель 2 с выводами для подсоединения сварочных проводов и термовыключатели 14.
Кроме того, на каркасе установлены выключатель, переключатель напряжения холостого хода силового трансформатора, держатели плавких вставок и разъемы подключения выпрямителя. Сверху на каркас устанавливается крышка б и ручки 1. Под задней панелью на каркасе находится болт заземления 15.
На магнитопроводе силового трансформатора размещены: выпрямительный блок 10 и блок зажимов 11. На раме 16 установлены блок конденсаторов 17, блоки диодов 21 и 22, пускатель 23, реле 8 с конденсатором 9 и вентиляторы 19.
На передней панели выпрямителя размещены (рис. 10): выключатель с кнопкой включения 1 и кнопкой выключения 2, автомат защиты двигателя 3, сигнальная лампа 4 «Сеть», вольтметр 5, переключатель 6 напряжения холостого хода силового трансформатора, переключатель 7 скорости подачи электродной проволоки, переключатель 8 места включения, разъем 9 подключения механизма подачи, вывод 10 «+» подключения сварочного провода, идущего к механизму подачи и вывод II с —» подключения провода заземления, идущего к свариваемому изделию.
На задней панели размещены держатель 12 плавкой вставки защиты цепи вентиляторов, держатель 13 плавкой вставки защиты цепи встроенного источника питания подающего механизма, разъем 14 подключения подогревателя газа и разъем 15 подключения выпрямителя к питающей сети.
7.2. Трехфазный силовой трансформатор Т2 (рис. 11) стержневого типа имеет развитое магнитное рассеивание.
Изменение напряжения холостого хода трансформатора осуществляется за счет постепенного изменения схемы соединения первичных обмоток от к Δ при помощи переключателя S5. Вторичные обмотки соединены в Δ. На первичных обмотках намотаны дополнительные вторичные обмотки для питания через выпрямительный мост V12 — V17 якоря электродвигателя М3 подающего механизма.
В цепи силовых вторичных обмоток включен диодный мост V6 — V11, в минусовой цепи которого находится дроссель L1, за-шунтированный диодом V23, в обратном направлении. Шунтирование дросселя диодом V23 автоматически уменьшает индуктивность дросселя при работе выпрямителя на малых режимах, обеспечивая стабильный процесс сварки.
Силовые диоды V6 — V11 и диод V23 расположены на охладителях, которые совместно с трансформатором Т2 и дросселем L1 обдуваются вентиляторами M1 и М2.
Для питания вспомогательных цепей и обмотки возбуждения электродвигателя М3 предназначен трансформатор Т1. Одна из его вторичных обмоток используется для питания сигнальной лампы HL1, а после выпрямления напряжения диодным мостом V1—V4 — для питания реле К2. Обмотка этого реле зашунтирована конденсатором С4 для обеспечения задержки на отключение сварочного напряжения и защитного газа. В цепи обмотки реле К2 включен контакт S2 термовыключателя, отключающий выпрямитель при перегреве вторичных катушек силового трансформатора.
В цепи второй вторичной обмотки трансформатора Т1 включен диодный мост V18 — V21, для питания обмотки возбуждения электродвигателя М3.
Для обеспечения возможности дистанционного включения сварочного напряжения имеется магнитный пускатель КМ1, в цепи которого включен замыкающийся контакт К2.1 реле К2. Такой же контакт К2.2 включен в цепи обмотки возбуждения электродвигателя, зашунтированной диодом V22 в обратном направлении.
Подогреватель газа подключается к выходным клеммам выпрямителя через разъем ХЗ.
Переключатель S7 предназначен для грубой регулировки скорости подачи электродной проволоки путем отключения одной из трех обмоток трансформатора Т2, соединенных Δ.
8. Электрическая схема
8.1. Работает полуавтомат следующим образом: при включении автоматического выключателя S1 трехфазное напряжение питающей сети подается на вентиляторы M1, М2, первичную обмотку трансформатора Т1. При этом на передней панели загорается сигнальная лампа HL1. Выпрямитель готов к работе. Переключатель S4 разомкнут (в положении «Дистанционное»).
Включение сварочного напряжения производится нажатием кнопки S8 на держателе горелки сварочного полуавтомата (или нажатием кнопки на щитке сварщика), которая включает реле К2. Контакт K2.I включит магнитный пускатель КМ1. а контакт К2.2 подаст напряжение на обмотку возбуждения двигателя полуавтомата М3.
Магнитный пускатель КМ1 своими контактами подаст напряжение на силовой трансформатор Т2.
На выходных клеммах выпрямителя (на сварочной горелке и изделии), подогревателе газа, а также на якоре электродвигателя М3 появится напряжение, величина которого определяется положением переключателя S5 (и переключателя S7 для якоря) и контролируется по вольтметру PV 1 па лицевой панели (кроме напряжения якоря).
По окончании процесса сварки кнопка S8 отпускается. При этом реле К2 отключается с задержкой не менее 1 с, определяемой конденсатором С4. обеспечивая тем самым защиту расплавленного металла шва углекислым газом до его затвердевания. Контакт K2.I отключит магнитный пускатель KM1. а контакт К2.2 — обмотку возбуждения электродвигателя М3. Это приводит к отключению выходного напряжения сварочного выпрямителя и электродвигателя.
При перегреве в процессе сварки наиболее нагреваемых элементов (вторичных обмоток силового трансформатора) срабатывает термовыключатель S2 и отключает реле К2, которое отключает магнитный пускатель КМ1 и цени силового трансформатора Т2. Вентиляторы M1, М2 продолжают работать.
Возобновление процесса сварки возможно только после снижения температуры вторичных обмоток силового трансформатора до уровня ниже порога срабатывания термовыключателя.
Скачать документацию
Типы сварочных процессов (ручная, полуавтоматическая, машинная, автоматизированная, роботизированная сварка) — Общие технические знания
Определено в Американском национальном стандарте: стандартные термины и определения для сварки, AWS A3.0: 2001:
1. Ручная сварка (MMA, TIG…)
Сварка, при которой вся сварочная операция выполняется и контролируется вручную. Поскольку сварщик выполняет всю работу вручную, это требует больших физических усилий и может привести к травмам.
При ручной сварке как «сварка с помощью горелки, пистолета или электрододержателя, удерживаемая и управляемая вручную», сварщик выполняет функцию сварки и постоянно контролирует сварочные операции вручную.
2. Полуавтоматическая сварка (FCAW, MIG, MAG…)
При полуавтоматической сварке, определяемой как «ручная сварка с использованием оборудования, которое автоматически контролирует один или несколько условий сварки», сварщик манипулирует сварочным пистолетом для создания сварного шва, в то время как электрод автоматически подается на дугу.
3. Сварка машинная (механизированная)
Сварка с помощью оборудования, требующего манипуляций со стороны оператора или регулировки в ответ на изменения условий сварки. Резак, пистолет или электрододержатель удерживается механическим устройством, а механическое устройство, которое удерживает пистолет, горелку или электрод, может быть роботом.
В механизированной сварке определяется как «сварка с использованием оборудования, которое требует ручной регулировки органов управления оборудованием в ответ на визуальное наблюдение за сваркой, с горелкой, пистолетом или электрододержателем, удерживаемым механическим устройством», вмешательство сварщика заключается в настройки органов управления оборудованием в ответ на визуальное наблюдение за операциями.
4. Автоматическая сварка (SAW…)
Сварка с использованием оборудования, которое требует лишь периодического наблюдения за сварным швом или его отсутствия, а также без ручной регулировки органов управления оборудованием. При этом типе сварки сварщик запускает машину и отслеживает дефекты или проблемы, требующие исправления.
В автоматизированной сварке определяется как «сварка с использованием оборудования, которое требует только периодического наблюдения или отсутствия наблюдения за сварным швом и без ручной регулировки органов управления оборудованием», участие сварщика ограничивается активацией аппарата для запуска цикла сварки и наблюдением сварка на прерывистой основе, если вообще.
5. Роботизированная сварка
Сварка выполняется и контролируется роботизированным оборудованием, которое не требует участия сварщика. Основная функция сварщика в роботизированной сварке — поддерживать контроль качества и устранять любые отклонения или проблемы.
Роботизированная сварка, , определяемая как «сварка, которая выполняется и управляется роботизированным оборудованием», не влечет за собой участия оператора сварки в выполнении сварки, поскольку сварочные операции выполняются и контролируются сварочными роботами.
В чем разница между механизированной, автоматической и роботизированной сваркой?
Определения каждого термина в соответствии с Британским стандартом BS 499: Часть 1: 1991 следующие:
Механизированная сварка — Сварка, при которой параметры сварки регулируются механически или электронно и могут быть изменены вручную во время сварки для поддержания требуемого положения при сварке.
Автоматическая сварка — Сварка, при которой все параметры сварки регулируются.Ручная регулировка может выполняться между сварочными операциями, но не во время сварки.
Роботизированная сварка — Автоматическая сварка с использованием робота, который можно предварительно запрограммировать на различные пути сварки и геометрию изготовления.
Успешное применение механизированных / автоматизированных систем может дать ряд преимуществ. К ним относятся повышение производительности, стабильное качество сварки, прогнозируемая производительность сварки, снижение переменных затрат на сварку и снижение стоимости деталей. Ограничения включают более высокие капитальные вложения, чем для ручного сварочного оборудования, потребность в более точном расположении и ориентации деталей, а также более сложных устройствах перемещения дуги и управления.Таким образом, производственные требования должны быть достаточно большими, чтобы оправдывать затраты на оборудование и установку, техническое обслуживание оборудования и обучение операторов / программистов для автоматизированного / роботизированного оборудования.
Справочный документ:
+ TWI
+ AWS A3.0
+ BS 499
Нравится:
Нравится Загрузка …
Связанные
Полуавтоматический переносной аппарат для точечной сварки, малошумный стандарт безопасности
Аппарат для точечной сварки / Полуавтомат, Переносной сварочный аппарат Цена
ОПИСАНИЕ
1.Эта машина подходит для двух выводов нагревательной трубки с двойной конструкцией электрода
.2. Машина предназначена для использования японского «NIPPON CHEMI CON» (NCC225UF / 475V) для хранения и выпуска. электричество . На следующем рисунке показан принцип работы сварочного аппарата
для конденсаторно-разрядной сварки.СПЕЦИФИКАЦИЯ
Модель | Напряжение | Мощность | Выходное тепло | Емкость | Герметизация | Электрод Ход | Закрытие | Платформа Расстояние | Электрод Расстояние | Охлаждающая вода |
В | кВА | Дж | мкФ | кг | мм | мм | мм | мм | Лит / мин | |
WL-CD-3K | 220/1Ф | 3.5 | 1500 | 13500 | 350 | 80 | 145-225 | 250 | 320-420 | Мин. 2 |
380/1 Φ |
КОНФИГУРАЦИЯ МАТЕРИАЛОВ
С.Н. | Имя | Спецификация | Марка | Происхождение |
1 | Контролируемый заряд кремния | КП-150 | MCC | U.S.A |
2 | Контролируемый разряд кремния | SKKT1000-12E | MCC | США |
3 | Выпрямительный диод | ЗП-150А | MCC | США |
4 | Токоограничивающее сопротивление | 100 Вт / 100 Ом | NANFA | Гонконг |
5 | Емкость | 225 мкФ / 475 В | Nitponchemi.con | Япония |
6 | Разрядный контактор | JMC-75 | LG | Южная Корея |
7 | Зарядный контактор | JMC-18 | LG | Южная Корея |
8 | Панель управления зарядкой | WD-20DC-1 | HWASHI | Самодельное |
9 | Панель управления выгрузкой | WD-20DC-2 | HWASHI | Самодельное |
10 | Выключатель зарядки | 15A | MITSUBISHI | Япония |
11 | Задний переключатель | DS-231 | IDEC | Япония |
12 | Главный магнитный клапан | 3000 # | SANWO | Корея |
13 | Прижимной магнитный клапан | 4 # | SANWO | Корея |
14 | Авиагруппа | 4000 # | SANWO | Корея |
КОНКУРЕНТНОЕ ПРЕИМУЩЕСТВО
1.HWASHI — ведущий бренд в области контактной сварки в Китае уже 20 лет; Прямая продажа с фабрики, конкурентоспособная цена.
2. Индивидуальное обслуживание: мы можем помочь спроектировать и разработать сварочный аппарат в соответствии с вашими требованиями. Мы гибкий и способный поставщик.
3. Оригинальный продукт с отличным качеством: гарантия 12 месяцев. Наши машины строго соответствуют требованиям ISO9001: 2000 и обязательной сертификации Китая. Срок службы большинства наших машин составляет 8-10 лет.100% гарантийный тест перед доставкой.
4. Послепродажное обслуживание и техническая поддержка: круглосуточная техническая поддержка по электронной почте. Наша профессиональная команда всегда готова стать вашим техническим консультантом.
5. Быстрая доставка: Наша компания обеспечивает доставку точно в срок.
6. Оперативное реагирование на клиентов: наша цель — это ваше удовлетворение.
Типы электрических чертежей и схем
Различные типы электрических схем и чертежей
В области электротехники и электроники мы используем различные типы чертежей или схем для представления определенной электрической системы или цепи.Эти электрические цепи представлены линиями для обозначения проводов и символов или значков для обозначения электрических и электронных компонентов. Это помогает лучше понять связь между различными компонентами. Электрики полагаются на электрическую схему этажа (которая также является электрической схемой) при выполнении любой проводки в здании.
Инженеры используют различные типы электрических чертежей, чтобы выделить определенные аспекты системы, но физическая схема и ее функции остаются прежними. Некоторые из этих электрических чертежей или схем описаны ниже.
Блок-схема
Блок-схема — это тип электрического чертежа, который представляет основные компоненты сложной системы в виде блоков, соединенных линиями, которые представляют их взаимосвязь. Это простейшая форма электрического чертежа, поскольку она только подчеркивает функцию каждого компонента и обеспечивает последовательность процессов в системе.
Блок-схема проще в разработке и является первым этапом проектирования сложной схемы для любого проекта.В нем отсутствует информация о разводке и размещении отдельных компонентов. Он представляет только основные компоненты системы и игнорирует любые мелкие компоненты. Вот почему; электрики не полагаются на блок-схему.
Пример:
В следующих двух примерах блок-схемы показаны FM-передатчик и частотно-регулируемый преобразователь частоты.
На этой схеме показан процесс преобразования аудиосигнала в сигнал с частотной модуляцией. Это довольно просто и понятно.Каждый блок обрабатывает сигнал и передает его следующему. Практически FM-передатчик не выглядит так, потому что на блок-схеме отсутствуют отдельные компоненты.
На этой блок-схеме показано преобразование трехфазного источника питания переменного тока в постоянный, который снова преобразуется в управляемый источник переменного тока. Это довольно сложный процесс, но эта диаграмма упрощает процесс на блоки для лучшего понимания.
Блок-схема дает представление о том, как выполняется процесс, не вникая слишком глубоко в электрические термины, но этого недостаточно для реализации схемы.Каждый блок представляет собой сложную схему, которую можно объяснить с помощью других методов рисования, описанных ниже.
Принципиальная схема Принципиальная схема
Принципиальная схема электрической цепи показывает полные электрические соединения между компонентами с использованием их символов и линий. В отличие от схемы подключения, в ней не указывается реальное расположение компонентов, линия между компонентами не отображает реальное расстояние между ними.
помогает показать последовательное и параллельное соединение между компонентами и точное контактное соединение между ними.Можно легко устранить неполадки в определенной схеме, применив теорию электронных схем.
Это наиболее распространенный тип электрических чертежей, который в основном используется техниками при реализации электрических схем. Большинство студентов-инженеров полагаются на принципиальную схему при разработке различных электрических проектов.
Пример:
Это принципиальная схема усилителя напряжения. Он использует различные символы для обозначения электрических компонентов и линий для обозначения электрического соединения между их выводами.Практическая схема может отличаться по внешнему виду, но электрическое соединение и ее функции останутся прежними.
Однолинейная схема или однолинейная схема
Однолинейная схема ( SLD ) или однолинейная схема — это представление электрической цепи с использованием одной линии. Как следует из названия, одна линия используется для обозначения нескольких линий питания, например, в трехфазной системе.
Однолинейная схема не показывает электрические соединения компонента, но может отображать размер и номинальные характеристики используемых компонентов.он упрощает сложные трехфазные силовые цепи, показывая все электрические компоненты и их взаимосвязь.
Они используются для определения и изоляции любого неисправного оборудования в любой энергосистеме во время поиска и устранения неисправностей.
На схеме SLD используются специальные электрические символы и значки для различных компонентов.
Пример:
Распространенным примером трехфазной силовой цепи для представления с использованием однолинейной схемы может быть передача и распределение электроэнергии потребителям.
На этой схеме четко показана трехфазная электростанция, которая передает электроэнергию потребителям, указанным ниже. Он проходит через несколько станций, функции и характеристики которых также упоминаются, но их электрические соединения не выделяются.
Связанные сообщения:
Схема подключения
Схема подключения используется для представления электрических компонентов в их приблизительном физическом расположении с использованием их специальных символов и их соединений с помощью линий.Вертикальные и горизонтальные линии используются для обозначения проводов, а каждая линия представляет собой один провод, соединяющий электрические компоненты.
Схема электрических соединений показывает графическое изображение компонентов, напоминающее их электрическое соединение, расположение и положение в реальной цепи. Это действительно помогает показать соединения в различном оборудовании, таком как электрические панели, распределительные коробки и т. Д., Они в основном используются для монтажа электропроводки в доме и на производстве.
Пример:
Схема установки трехфазной электропроводкиЭто схема установки трехфазной электропроводки в доме.На нем четко показаны компоненты с правильным электрическим подключением. Каждая отдельная линия (с цветовым кодом) представляет определенный фазовый провод и его соединение с каждым компонентом. Такой тип схем используется для электромонтажа дома электриками.
Графическая диаграмма
Графическая диаграмма не обязательно отображает реальную схему. Фактически он показывает внешний вид схемы в реальном времени. его нельзя использовать для понимания или устранения неисправностей в реальной цепи, и только по этой причине он обычно не используется.Для человека с меньшими познаниями в области электрики невозможно понять, как работает схема, и диагностировать ее.
Пример:
Как видите, графическая диаграмма не дает достаточной информации относительно электрического соединения компонентов.
Связанные сообщения:
Лестничная диаграмма или линейная диаграмма
Лестничная диаграмма — это электрические схемы, которые представляют электрические цепи в отраслях для документирования логических систем управления.Она похожа на лестницу, поэтому называется лестничной диаграммой. Есть две вертикальные линии; левая вертикальная линия представляет шину питания (источник напряжения), а правая вертикальная линия представляет землю или нейтраль. Каждая горизонтальная строка представляет собой параллельную цепь, называемую звеном.
Релейная диаграмма проста, легче для понимания и помогает быстро устранять неисправности в цепи.
Пример:
Логическая диаграмма
Логическая диаграмма представляет собой логическую схему, показывая сложную схему и процесс с использованием различных блоков или символов.Логические функции представлены их логическими символами, тогда как блоки используются для представления сложной логической схемы. Эти блоки помечены своей логической функцией для лучшего понимания без знания внутренней структуры.
Блоки соединены линиями, которые представляют входные и выходные линии для сигналов.
Логическая схема не показывает электрические характеристики цепи, такие как ток, напряжение, мощность и т. Д., Она представляет только логическую функцию схемы или устройства, в которых сигнал рассматривается в двоичном формате i.е. 1 или 0. Логические схемы обычно используются при проектировании цифровой логики.
Пример:
Это логическая схема однобитового полного сумматора, состоящего из цифровых логических вентилей. Каждая входная линия A и B передает один бит в сумматор, в то время как c in представляет бит переноса из предыдущих сумматоров. Строки вывода обеспечивают сумму и вывод в виде битов.
Связанный пост: Различные типы датчиков с приложениями
Схема стояка
Схема стояка — это иллюстрация физической схемы распределения электроэнергии в многоуровневом здании с использованием одной линии.Он показывает размер кабелепровода, размер провода, номинал автоматического выключателя и других электрических устройств (номинал переключателей, вилок, розеток и т. Д.) От точки входа до небольших ответвлений цепи на каждом уровне. Он разделяет планировку с системой сигнализации, а также телекоммуникационными и интернет-кабелями.
Диаграмма стояка получила свое название, потому что показывает перетекание мощности с одного уровня на другой. В нем не указывается физическое местонахождение оборудования и не содержится лишней информации.
Он в основном фокусируется на распределении электроэнергии между различными приборами в здании на каждом уровне.Он предоставляет информацию о том, как работает освещение, отопление, вентиляция и т. Д. В здании, и если есть какая-либо опасность, ее можно легко устранить.
Инженеры-электрики полагаются на схему стояков здания, чтобы избежать любых потенциальных электрических опасностей.
Похожие сообщения:
Электрический план этажа
Это вертикальное представление различных приборов, таких как свет, выключатель, вентиляторы и т. Д. В здании. В нем указывается их точное местоположение с указанием их размера и расстояния от каждой стены и потолка.Он показывает увеличенную версию каждой комнаты сверху. Обычно он содержит легенду, которая дает наглядное объяснение используемых в ней символов.
Индивидуальный план этажа разработан для каждого этажа в многоуровневом здании и используется в электрике для электромонтажа во вновь построенном здании или при перетяжке электропроводки в здании. это помогает определить расположение кабелей внутри стен.
Связанные сообщения:
Схема расположения ИС
Схема расположения ИС или макет ИС (маска) относится к внутренней конструкции полупроводникового компонента.Он состоит из нескольких слоев или масок из металла, оксида и полупроводника, образующих интегральную схему (ИС). Он представляет геометрию, а также размер различных полупроводниковых слоев и их соединения. Он описывает внутреннюю структуру и используется при производстве и проектировании интегральных схем.