Как сделать микросхему своими руками. Какое оборудование необходимо для изготовления микросхем в домашних условиях. Какие этапы включает в себя процесс производства микросхем. Какие материалы используются при изготовлении микросхем в домашних условиях. Какие проблемы могут возникнуть при попытке создать микросхему дома.
Основные этапы производства микросхем в домашних условиях
Изготовление микросхем в домашних условиях — сложный многоступенчатый процесс, требующий специального оборудования и материалов. Рассмотрим основные этапы, которые необходимо пройти для создания простейшей микросхемы в домашней лаборатории:
- Подготовка кремниевой подложки
- Нанесение фоторезиста
- Экспонирование через фотошаблон
- Проявление фоторезиста
- Травление оксида кремния
- Легирование (диффузия или ионная имплантация)
- Нанесение металлизации
- Корпусирование микросхемы
Каждый из этих этапов требует тщательного контроля и соблюдения технологического процесса. Рассмотрим их подробнее.

Подготовка кремниевой подложки для изготовления микросхемы
Первый и один из важнейших этапов — подготовка кремниевой пластины, которая будет служить основой для будущей микросхемы. Какие шаги необходимо выполнить?
- Приобрести монокристаллическую кремниевую пластину нужного типа проводимости (p- или n-типа)
- Очистить поверхность пластины от загрязнений и жировых пятен
- Вырастить на поверхности тонкий слой диоксида кремния путем термического окисления
- Отполировать поверхность до зеркального блеска
Качество подготовки подложки во многом определяет характеристики будущей микросхемы. Важно использовать кремний высокой степени очистки и не допускать загрязнения поверхности в процессе обработки.
Нанесение и экспонирование фоторезиста
Следующий ключевой этап — формирование рисунка будущей микросхемы с помощью фотолитографии. Как это происходит?
- На поверхность кремниевой пластины наносится тонкий слой светочувствительного фоторезиста
- Поверх фоторезиста укладывается фотошаблон с рисунком микросхемы
- Производится экспонирование ультрафиолетовым светом
- Засвеченные участки фоторезиста изменяют свои свойства
- При проявлении удаляются либо засвеченные, либо незасвеченные области (в зависимости от типа фоторезиста)
В результате на поверхности пластины формируется рельефный рисунок из фоторезиста, повторяющий топологию микросхемы. Этот рисунок защищает нужные области при последующем травлении.
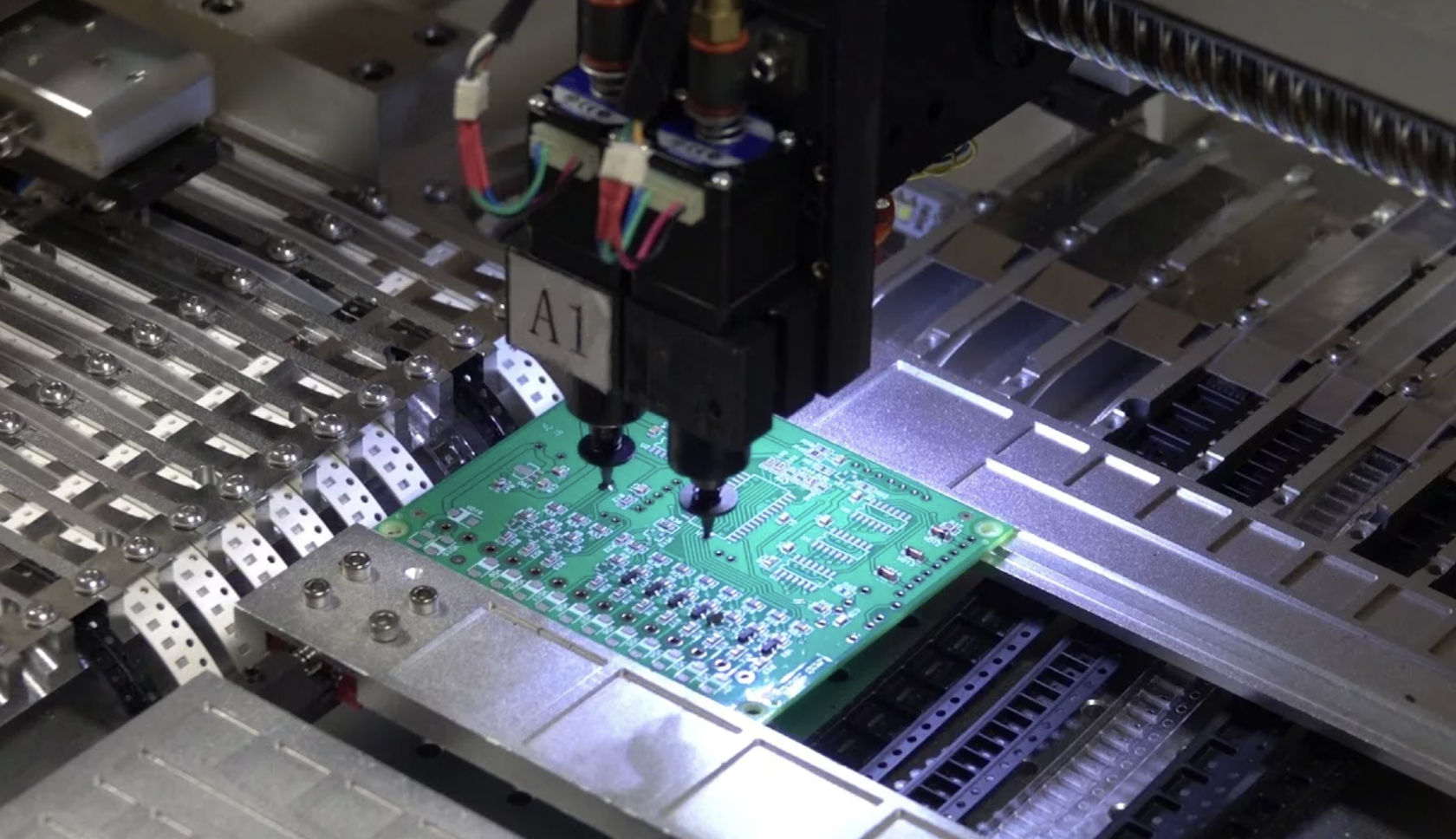
Травление и легирование кремниевой пластины
После формирования рисунка из фоторезиста производится травление незащищенных участков оксида кремния. Как происходит этот процесс?
- Пластина помещается в раствор плавиковой кислоты
- Оксид кремния растворяется в местах, не защищенных фоторезистом
- Образуются «окна» для последующего легирования
- Остатки фоторезиста удаляются с поверхности
Через полученные «окна» в оксиде производится легирование — внедрение примесных атомов для создания областей с нужным типом проводимости. В домашних условиях легирование обычно осуществляется методом диффузии при высокой температуре.
Нанесение металлизации и корпусирование микросхемы
Заключительные этапы изготовления микросхемы включают:
- Нанесение слоя металла (обычно алюминия) для создания электрических соединений
- Формирование рисунка металлизации с помощью фотолитографии
- Травление лишнего металла
- Разделение пластины на отдельные кристаллы
- Монтаж кристалла в корпус
- Присоединение выводов к контактным площадкам кристалла
- Герметизация корпуса микросхемы
На этом основные технологические операции завершаются. Далее производится тестирование и отбраковка готовых микросхем.
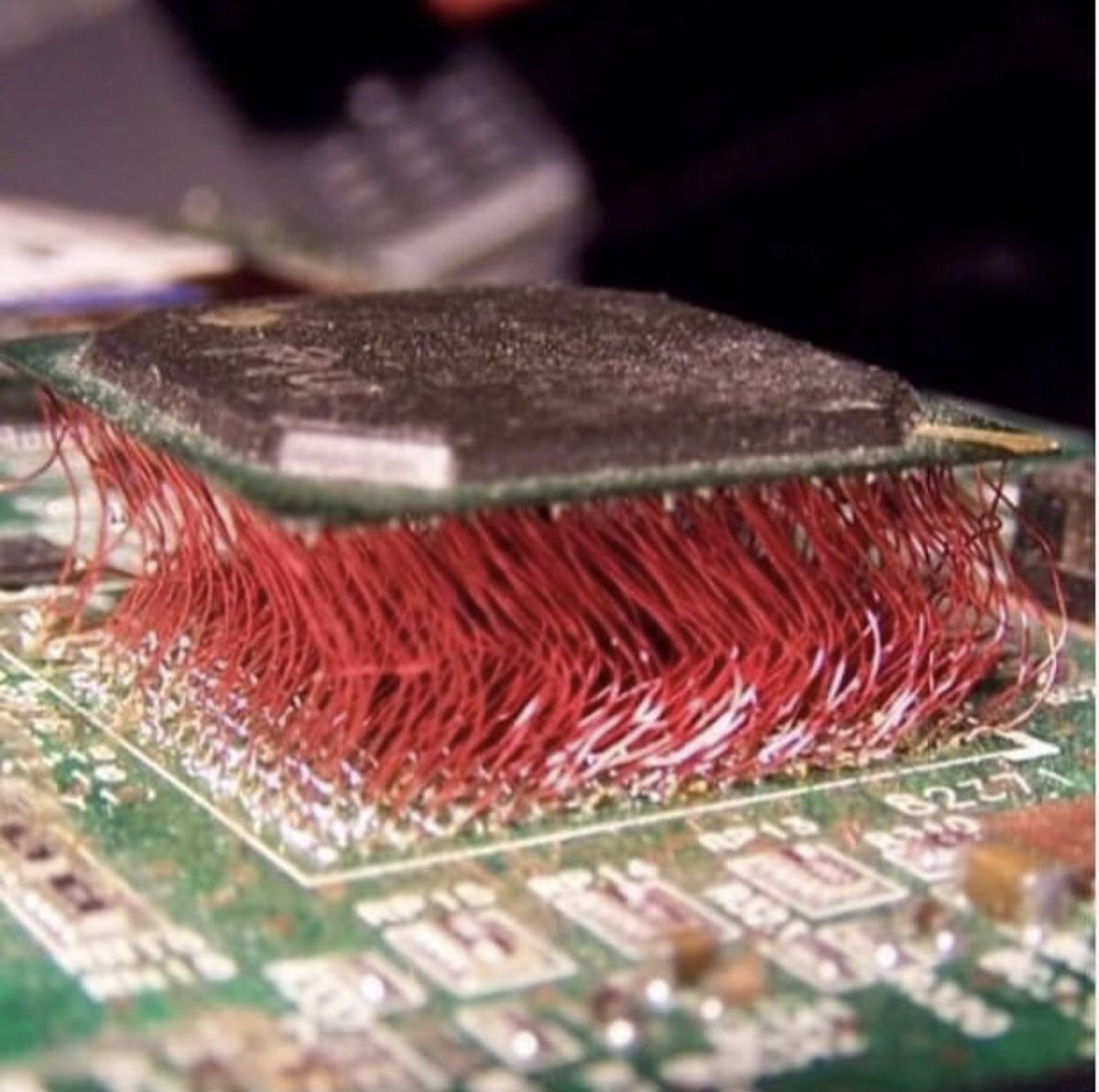
Необходимое оборудование для изготовления микросхем дома
Для производства микросхем в домашних условиях потребуется следующее основное оборудование:
- Вытяжной шкаф для работы с химикатами
- Центрифуга для нанесения фоторезиста
- Источник ультрафиолетового излучения
- Металлографический микроскоп
- Печь для термической обработки
- Химическая посуда для травления
- Измерительные приборы (мультиметр, осциллограф)
Кроме того, понадобятся расходные материалы — кремниевые пластины, химические реактивы, фоторезист, металлическая проволока для разварки и др. Многие приборы можно изготовить самостоятельно или приобрести бывшие в употреблении.
Проблемы и ограничения домашнего производства микросхем
При попытке изготовить микросхему в домашних условиях неизбежно возникает ряд сложностей:
- Низкая чистота помещений и материалов
- Невысокая точность совмещения слоев при фотолитографии
- Ограниченные возможности по миниатюризации элементов
- Сложность контроля технологических процессов
- Отсутствие специализированного оборудования
- Высокая стоимость расходных материалов
В результате в домашних условиях реально изготовить лишь простейшие микросхемы с размерами элементов в десятки микрон. Тем не менее, это позволяет освоить основные технологические процессы микроэлектроники на практике.
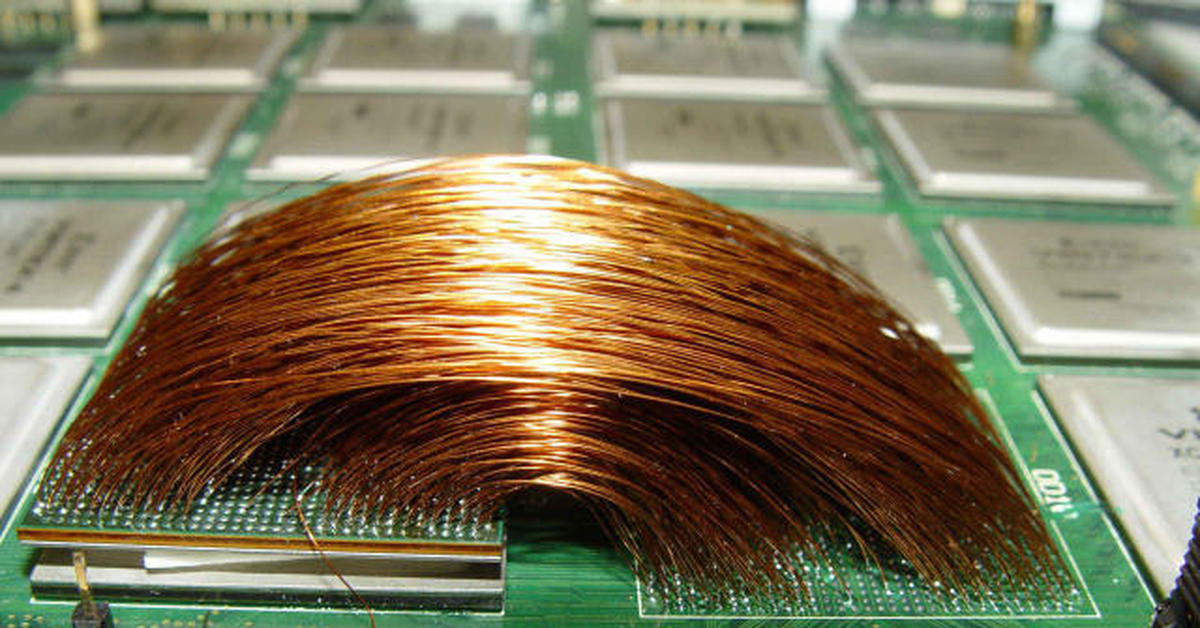
Перспективы домашнего производства микросхем
Какие возможности открывает освоение технологии изготовления микросхем в домашних условиях?
- Углубленное изучение основ микроэлектроники на практике
- Создание уникальных микросхем малыми партиями
- Разработка новых конструкций микросхем и их прототипирование
- Изготовление декоративных микросхем в качестве сувениров
- Использование в образовательных целях
Несмотря на ограничения, самостоятельное изготовление микросхем остается увлекательным хобби для энтузиастов электроники. В перспективе возможно появление доступных технологических комплексов для мелкосерийного производства заказных микросхем.
Как делают микросхемы
Как делают микросхемы
Поскольку микросхема создается на поверхности пластины, технология ее изготовления называется планарной (от англ.“planar” – “плоский”). Ее основу составляет литография. Наз-вание “литография” происходит от греческих слов “литос” камень и “графо” – пишу, что дословно означает “писать на камне”. Литография в микроэлектронике – это действительно способ формирования заданного рисунка (рельефа) в слое полупроводника.
Изготовление, или “выращивание”, интегральной микросхемы включает в себя несколько основных этапов:
1. Подготовка подложки
Подложкой обычно является пластина кристалла кремния (Si) _ самого распространенного полупроводника на Земле. Обычно пластина имеет форму диска диаметром 200 мм и толщиной менее миллиметра. Получают ее разрезанием цилиндрического монокристалла.
Так как свойства полупроводникового кристалла сильно зависят от направления (вдоль или поперек кристалла), то перед тем как нарезать кристалл на пластины, его свойства измеряют
во всех направлениях и ориентируют нужным образом.
Для резки монокристаллов на пластины применяются диски с режущей кромкой, покрытой алмазной крошкой размером 40-60 микрон, поэтому после резки пластины получаются шерохо-ватыми, на них остаются царапины, трещины и другие дефекты, нарушающие однородность структуры приповерхностного слоя и его физико_химические свойства. Чтобы восстановить поверхностный слой, пластину тщательно шлифуют и полируют.
Все процессы по обработке полупроводниковых пластин проводятся в условиях вакуумной гигиены в специальных помещениях со сверхчистой атмосферой. В противном случае пыль может осесть на пластину и нарушить элементы и соединения микросхемы (гораздо меньшие по размерам, чем сама пыль). Очищенная кремниевая пластина подвергается так называемому оксидированию (или окислению) _ воздействию на заготовку кислородом, которое происходит под высокой температурой (1000°C).
Таким образом на поверхности заготовки создается тончайший слой диоксида кремния SiO2. Регулируя время воздействия кислорода и температуру кремниевой подложки, можно легко сформировать слой оксида нужной толщины. Диоксидная пленка отличается очень высокой химической стойкостью, большой прочностью и обладает свойствами хорошего диэлектрика, что обеспечивает надежную изоляцию находящегося под ним кремния и защищает его от нежелательных воздействий в ходе дальнейшей обработки.
2. Нанесение фоторезиста
Если некоторые области кремния, лежащие под слоем оксида, необходимо подвергнуть обработке, то оксид надо предварительно удалить с соответствующих участков. Для этого на
диоксидную пленку наносится слой фоторезиста.
Рис 102 .Исходная полупроводниковая пластина с
проводимостью р_типа, покрытая слоями SiO2, и
фоторезиста: 1 _ слой фоторезиста, 2 _ слой SiO2,
3 _ полупроводниковая пластина
Фоторезист – это светочувствительный материал, который после облучения становится
растворимым в определенных химических веществах. Фотошаблон представляет собой пластинку, состоящую из прозрачных и непрозрачных участков, и играет роль трафарета.
3. Экспонирование
На следующем этапе-экспонировании-пластину с наложенным на нее фотошаблоном подвергают действию излучения. Фоторезист, расположенный под прозрачными участками
фотошаблона, засвечивается.
Рис 103. Облучение фоторезиста через фотошаблон:
1 _ засвеченный участок фоторезиста, 2 _ слой SiO2,
3 _ полупроводниковая пластина, 4 – фотошаблон
В результате засвеченный слой, чьи структура и химические свойства изменились под действием излучения, а также находящийся под ним слой диоксида кремния могут быть удалены с помощью химикатов (каждый слой-своим химикатом).
Делаем микросхемы дома — шаги 0 и 1 / Хабр
В этой статье я расскажу о начале своей работы над совершенно безбашенной задачей: конечная цель в том, чтобы получить рабочую микросхему по «толстым» нормам (5-10µm) дома. Это не первое апреля и я не сумасшедший, это просто моё хобби.Возникла эта идея не сейчас и неспроста. С детства я хотел быть газосварщиком, и… делать микросхемы. И если по первому пункту мне достаточно быстро удалось сделать дома сварочный аппарат (бутан-водород/кислород), то с микросхемами все никак не складывалось. Долгое время все мысли останавливались на том, что я не знал где можно взять собственно полупроводники необходимой чистоты (и мысли останавливались на ковырянии мощных транзисторов), пока на форуме не подсказали что в принципе, можно и купить пластины. Затем я даже наткнулся на человека, который 20 лет работал над похожей задачей, и в итоге сдался. Пожалуй, тут можно было опустить руки и перестать тратить время на глупые мечты. Но, однажды я увидел ролик чудовищно гениальной женщины – Jeri Ellsworth – она смогла сделать отдельные полевые транзисторы на основе заводских пластин – и тогда я решил, что настало время поплотнее заняться этой проблемой.
В этой статьях я расскажу о своём текущем прогрессе, но не ждите быстрого продолжения – весь процесс может легко занять пару лет.
Шаг 0:
Были скуплены все книги по теме из местных Интернет-магазинов (как раз на 1 полку), повыкачаны из торрентов все доступные сборники оцифрованных книг. Теоретической информации там конечно много, но с практической стороны – многое покрыто мраком. Даже старые техпроцессы в деталях не описаны нигде, и потому придется много пробовать. Также перерыл интернет в поисках местных поставщиков всех потенциально необходимых материалов (собственно кремний, фоторезисты, химия, газы). Пока найти не удалось местную компанию которая может изготавливать асферическую оптику из оптического/кварцевого стекла – но это в ближайший год не станет препятствием.
Шаг 1: Кремний
Монокристаллический кремний – сердце домашней микросхемы. Вырастить дома – хоть и реально (по моим безумным меркам), но чертовски дорого. Потому я стал гуглить местных производителей кремния – кто-то говорил что они свернули производство и занимаются только сдачей помещений в аренду, кто-то не отвечал, пока наконец я не дошел до компании Терасил – там я наконец смог купить все что мне нужно. Самое главное – разрезанные и отполированные пластины монокристаллического кремния легированного в P и N тип (справа на фото).
Далее – куча разбитых пластин для тренировки. Потренировался раскалывать пластину на кусочки (оказалось, что они все с ориентацией кристаллической решетки 111 – раскалываются треугольниками, а не квадратами). Т.к они еще не отполированы – я попробовал и отполировать – провал полный: паста гои кремний не берет, нужна алмазная паста. Если со временем получится полировать, можно будет пробовать делать солнечные батареи (а из монокристаллического кремния они получаются довольно эффективные).
И наконец – кусочки монокристаллического кремния. Те что толстые слева – погрязнее (но достаточно чистые для микросхем), 2 тоненьких справа – сверхчистые, намного выше требований чистоты кремния для обычных микросхем. Само собой, разрезать их дома не выйдет (если конечно не завалялась алмазная дисковая пила) – только разбить. Нужны для того чтобы пробовать осаждать пленки аморфного кремния химическим (PE CVD Sih5) или физическим (испарение в вакууме) путем.
Какие дальше стоят задачи
- В первую очередь – строительство печи на 1200 градусов для маленького образца. Промышленные печи под такую температуру в квартире не поставить, и стоят огого. Потому буду пробовать нагревать образец галогеновыми лампами с рефлекторами.
- Переезд в отдельную квартиру: меня сразу выгонят увидев бородатого мужика в противогазе и резиновых перчатках с кучей подозрительных баночек.
- Далее – необходимая химия и фоторезисты – и можно пробовать делать 1 транзистор по процессу Jeri.
Что я ищу и пока не нахожу
В первую очередь – это информация. Хотелось бы иметь контакты людей, которые работают на производстве – ведь я соберу все грабли, которые технологи собирали последние 50 лет Затем – информация о техпроцессах и главное – библиотеки под толстые техпроцессы – пока мне их не удалось достать, а из отдельных транзисторов особо не по-проектируешь. Ну и наконец, хочу найти разработчика ASIC, который показал бы мне основные шаги разработки (кое-что я думаю что знаю, но много пробелов и я могу ошибаться сильно). По всем этим вопросам приглашаю на форум по этому проекту (English only).
Комментарии / мнения — в студию.
Сколько стоит запуск производства микросхемы, и почему при наличии 22нм фабрик, бОльшая часть микросхем по всему миру до сих пор делается на «устаревшем» 180нм-500нм оборудовании?
Ответы на эти и многие другие вопросы под катом.
Транзисторы на кремниевой пластине рисуются с помощью фотолитографии, с помощью аппаратов называемых степперами или сканерами. Степпер — рисует кадр (до 26×33мм) целиком, затем переходит на новую позицию. Сканер — одновременно сдвигает маску и пластину таким образом, чтобы в каждый момент рисовать только одну узкую «строку» в центре кадра, таким образом аберрации оптической системы меньше влияют на изображение.Основные характеристики степперов/сканеров — длина волны света, на которой они работают (на ртутных лампах i-line — 365nm, затем на эксимерных лазерах — 248nm и 193nm), и численная апертура объектива. Чем короче длина волны, и чем больше апертура — тем меньшие детали могут быть нарисованы объективом в соответствии с дифракционным пределом:
Например, для одного из самых совершенных сканеров ASML NXT 1950i с длиной волны 193нм и численной апертурой 1.35, и k1=0.4(обычное значение для фотолитографии без «хитростей») получаем теоретическое разрешение 57нм. Применяя хитрости вроде фазовых масок, многократной экспозиции, оптической коррекции близости, off-axis illumination, поляризации света — получают минимальные элементы до 22нм.
Другие параметры степперов/сканеров — производительность (сколько пластин в час они могут обработать, до 220 пластин), и ошибка совмещения (на сколько нанометров в штуках промахивается позиционирование пластины относительно заданной позиции. На современных сканерах — до 3-5нм).
Степперы/сканеры печатают уменьшенное в 4–5 раз изображение вот такой маски (стеклянной пластинки с рисунком микросхемы, размер примерно 15×15см) в точно заданных местах.
Операцию печати рисунка (с разными масками) нужно повторить от ~10 (для самых простых и старых микросхем) до ~40 раз чтобы сформировать все нужные слои на микросхеме (начиная от самих транзисторов, и заканчивая 2–10 слоями металлических соединений). Между операциями фотолитографии пластины подвергаются различной обработке — их греют в печке до 1100 градусов, травят в растворах и плазме. На выходе остаётся пластину разрезать на отдельные кристаллы, протестировать и поместить в корпус.
«Крутость» технологии измеряют размером минимального рисуемого элемента (отдельные части транзистора, например затвор — могут быть как меньше так и больше этой цифры — т.е. это величина достаточно условная). Понятно что чем меньше транзисторы — тем быстрее работает микросхема, и больше кристаллов влезет на пластину (но не везде нужна максимальная скорость).
Сейчас начинается медленный и мучительный переход на EUV-литографию, с длиной волны 13.5nm и зеркальной оптикой. EUV сканеры пока дороже и медленнее обычных 193нм, и только-только начинают превосходить их по достижимому разрешению.
Цифры — грубые оценки, точных нигде не скажут без NDA.Лицензия софта на одно рабочее место разработчика микросхем — от 20’000 до 100’000$ в год и выше. Можно конечно и воровать, но за этим все вокруг следят.
Далее — изготовление масок. Они не должны иметь ни одного повреждения, и их изготовление обходится очень дорого: от ~7’000$ за комплект для микросхем на 1000нм, ~100’000$ для микросхем на 180нм и до ~5’000’000$ для микросхем на 32нм. А ведь микросхема с первого раза скорее всего не заработает — и после нахождения ошибки маски придётся переделывать. Частично с этой проблемой можно бороться размещая тестовые микросхемы от многих заказчиков на одном наборе масок — тогда все получат по чуть–чуть тестовых микросхем за 1/3–1/10 цены полного набора масок (это называют Shuttle или MPW — multi project wafer).
Каждая произведённая пластина стоит от 100–400$ для старых технологий на 1000нм, ~1000$ на 180нм и до ~5000$ для самых современных (помимо нанометров тут оказывает влияние и сложность технологии — простая логика дешевле, флеш память дороже, но не в разы). Тут также важно помнить и о размере пластин: самые современные производства сейчас работают с пластинами диаметром 300мм — они по площади примерно вдвое больше пластин на 200мм (которые сейчас используются в России на Микроне, Интеграле и в туманном будущем на Ангстрем-Т), а последние примерно вдвое больше ещё более старых 150мм. Пластины бОльшего размера позволяют получать микросхемы меньшей стоимости при большИх заказах т.к. количество телодвижений для изготовления 100 пластин примерно одинаковое, независимо от диаметра (это одна из причин планируемого перехода передовых производств на пластины диаметром 450мм в 2018 году по оптимистичным оценкам).
Допустим мы хотим разработать x86-совместимый процессор (или любую другую относительно сложную микросхему), по более-менее современной коммерчески доступной технологии 28/32нм (22нм хоть и существует, но коммерческие заказы пока не разместить — так что доступ к технологиям иногда как любовь: за деньги не продается). Вопрос со стоимостью патентов опустим, это вообще очень печальная тема. Предположим, для разработки нужно 200 мифических человеко-лет (это если мы делаем скромный процессор, не претендующий на первое место).
Лицензии на софт — 50k$*100 = 5 млн$ (грубая оценка, не всем нужны лицензии).
Зарплата разработчиков — допустим 3k$*1,5(налоги)*12*200 = 10.8 млн$
Тестовые запуски в MPW — 2*1.5 млн$
Изготовление масок для серийного производства 2*5млн$ = 10 млн$ (2 — потому что как ни старайся — с первого раза не выйдет)
Итого — 28.8 млн$
Это было то, что называется Non-recurring engineering (NRE) — единоразовые затраты, которые не зависят от объема производства, и успеха всего мероприятия.
Если процессор у нас получился площадью 200мм2, пластины по технологии 32нм диаметром 300мм стоят 5000$, то с пластины у нас получится 70690/200 = 350 кристаллов (оценка сверху), из которых работать допустим будет 300. Т.е. себестоимость кристалла — 16.6$, 20$ после корпусировки. За сколько теперь такой процессор можно будет продавать? 50$? 100$? Отнимем налоги и наценку магазинов…
И вот теперь вопрос — сколько же нужно продать таких процессоров, чтобы окупить наши NRE, проценты по кредитам, налоги и проч? Миллион? 5 миллионов? А главный вопрос — есть ли какие-то гарантии, что эти 5 миллионов процессоров удастся продать, учитывая что конкурентам ничего не стоит произвести на 5 миллионов больше их уже готового продукта?
Вот такой вот адский бизнес получается — огромные капитальные расходы, огромные риски и умеренная прибыль в лучшем случае.
Китай — решил проблему по своему, они решили во все школы поставить компьютеры со своими процессорами и Linux — и проблема с объёмами производства решена ((1) (2)).
Таким образом, главный вопрос при создании микросхем — это не как и где произвести, а как разработать и кому потом продать миллионы штук получившейся продукции?
Стоимость современного завода подбирается к отметке 5 млрд$ и выше. Такая сумма получается потому, что стоимость лицензий и некоторых других фиксированных расходов не сильно зависит от объёмов производства — и выгодно иметь большие производства, чтобы затраты «размазывались» по бОльшему объёму продукции. А каждый современный сканер (который собственно рисует эти 22–32нм детали) стоит 60–100млн $ (на большом заводе их может быть пара десятков). В принципе, 5млрд — не такие большие деньги в масштабах страны. Но естественно, никто не потратит 5 млрд без чёткого плана по возврату инвестиций. А ситуация там такая — несмотря на всю сложность индустрии, только монополисты работают с видимой прибылью (TSMC, Intel, Samsung и немногие другие), остальные еле сводят концы с концами.
Это просто не укладывалось у меня в голове — как же так, вкладывать миллиарды, и едва–едва их отбивать? Оказалось, все просто — по всему миру микроэлектроника жесточайше дотируемая отрасль — заводы постоянно выклянчивают освобождение от налогов, льготные кредиты и демпингуют (в Китае пошли ещё дальше — SMIC заводы строит за государственный счёт, и потом ими «управляет» — это у них называется Reverse Build-Operate-Transfer). После появления каждой новой технологии (45нм, 32нм…) — первые заводы-монополисты обладающие ей и рубят основную прибыль, а те, кто приходят на 2-5-10 лет позже старта — вынуждены работать практически по себестоимости. В результате денег тут заработать крайне сложно (без монополии и без дотаций).
Это похоже поняли и в России — и проекты больших микроэлектронных заводов пока отложили, и строят маленькие производства — чтобы если и терять деньги, то терять их мало. А даже 3000 пластин в месяц, производимых на Микроне — это с головой покрывает объёмы потребления билетов Метрополитена и оборонки (кристалл билета метро имеет размеры 0.6×0.6мм, на одной 200мм пластине получается 87’000 билетов в метро — но о грустной истории с билетами метро я расскажу в одной из следующих статей).
Вопреки расхожему мнению, особых ограничений на продажу оборудования для микроэлектроники в Россию нет — на поправку Джексона — Вэника в США ежегодно накладывается президентский мораторий, и нужно только получать обычное разрешение на экспорт. Сами производители оборудования кровно заинтересованы заработать побольше денег, и сами пинают со своей стороны выдачу разрешений. Но естественно, без денег никто ничего не делает. Так что за ваши деньги — любой каприз.
Но нужно помнить и о том, что свой завод не гарантирует полной независимости производства, и не дешевле производства за рубежом: основную стоимость составляют технологии/лицензии и стоимость закупаемого оборудования — а если своих технологий и оборудования нет, и все импортировать — то и дешевле получится не может. Многие расходные материалы также в любом случае придется импортировать. Отдельный больной вопрос — производство масок, только очень крупные фабрики могут иметь «своё» производство масок.
Многим кажется — вот, у Intel–а 22нм, а у нас 90нм — как мы безнадежно отстали, подайте трактор… Но есть и другая сторона медали: посмотрите например на ту же материнскую плату: там сотни полупроводниковых приборов — MOSFET–ы, драйверы, микросхемы питания, всякая вспомогательная мелочь — почти для всех из них хватает и 1000нм технологии. Вся промышленная электроника, и микросхемы для космоса и военных — это практически в 100% случаев технологии 180нм и толще. Таким образом, самые последние технологии нужны лишь для центральных процессоров (которые делать очень сложно/дорого из–за высоких рисков и высокого порога выхода на рынок), и различных «жопогреек» (айфонов и проч). Если вдруг случится война, и Россия лишится импорта — без «жопогреек» прожить можно будет, а вот без промышленной, космической и военной электроники — нет. Т.е. по факту мы видим, что критичные для страны вещи по возможности делают в России (или закупают впрок), а то, без чего можно будет прожить в крайнем случае — импортируем.Есть и другие факторы — та же стоимость масок. Если нам нужно сделать простую микросхему, то делать для её изготовления по 32нм маски стоимостью 5 млн $ — может быть выгодно если эту микросхему потом производить тиражом в десятки и сотни миллионов копий. А если нам нужно всего 100’000 микросхем — выгоднее экономить на масках, и выпускать микросхему по самой «толстой» технологии. Кроме этого, на микросхеме есть контактные площадки, к которым подсоединяются выводы микросхем — их уменьшать некуда, и следовательно, если площадь микросхемы сравнима с площадью контактных площадок — то делать микросхему по более тонкой технологии также нет смысла (если конечно «толстые нормы» удовлетворяют требованиям по скорости и энергопотреблению).
В результате — подавляющее большинство микросхем в мире делается по «толстым» технологиям (350–500нм и толще), и миллиарды микросхем уходящие на экспорт с Российских заводов (правда в основном в виде пластин) — вполне себе востребованы и продаются (так что в материнских платах и сотовых телефонах есть наши микросхемы и силовые транзисторы — но под зарубежными именами).
Ну и наконец, американский F–22 Raptor до недавнего времени летал на процессоре Intel 960mx, разработанном в 1984–м году, производство в США тогда было по нормам 1000–1500nm — никто особо не жужжал о том, что американцы ставят в самолеты отсталую электронику (хотя ладно, немного жужжали). Главное ведь не нанометры, а соответствие конечного продукта техзаданию.
Рыночная экономика эльфов и микроэлектронное производство — слабо совместимые вещи. Чем больше копаешься — тем меньше видно рынка, больше дотаций, картельных сговоров, патентных ограничений и прочих радостей «свободного рынка». Бизнес в этой отрасли — это одна большая головная боль, с огромными рисками, постоянными кризисами перепроизводства и прибылью только у монополистов.
Не удивительно, что в России стараются иметь маленькое, но своё производство, чтобы сохраняя независимость, терять меньше денег. Ни о какой прибыли на рыночных условиях говорить не приходится.
Ну и не для всех микросхем нужно 22-32нм производство, подавляющее большинство микросхем выгоднее производить на более старом 180-500нм оборудовании из-за стоимости масок и объемов производства.
В следующих статьях — расскажу об особенностях космической и военной микроэлектроники, и о текущем состоянии микроэлектроники в России.
Делаем микросхемы дома — часть 3 / Хабр
Прошло чуть больше года после предыдущих статей о моем проекте создания микросхем дома (1, 2), люди продолжают интересоваться результатами — а значит пора рассказать о прогрессе.Напомню цель проекта: научиться изготавливать несложные кремниевые цифровые микросхемы в «домашних» условиях. Это никоим образом не позволит конкурировать с серийным производством — помимо того, что оно на порядки более совершенное (~22нм против ~20мкм, каждый транзистор в миллион раз меньше по площади), так еще и чудовищно дешевое (этот пункт не сразу стал очевиден). Тем не менее, даже простейшие работающие микросхемы, изготовленные в домашних условиях будут иметь как минимум образовательную и конечно декоративную ценность.
Как я уже упоминал в комментариях к другому топику, попытка выйти с этим проектом на kickstarter провалилась — проект не прошел модерацию из-за отсутствия прототипа. Это заставило в очередной раз переосмыслить пути коммерциализации этой упрощенной технологии. Возможность релиза технологии домашних микросхем в виде RepRap-подобного opensource-кита покрыта туманом: очень уж много опасной, дорогой и нестойкой химии — так просто рассылать по почте не выйдет. Также по видимому отсутствует возможность делать мелкие партии микросхем дешевле серийных заводов: сейчас минимальные тестовые партии микросхем можно изготавливать примерно по 30-50$ штука (в партии ~25 штук), и существенно дешевле 30$ за микросхему сделать это на самодельной упрощенной установке не получится. Кроме того, не смотря на низкую цену на обычных заводах — любительские микросхемы практически никто не делает, задач где они имели бы преимущества перед FPGA/CPLD/микроконтроллерами практически нет, а стоимость и сложность разработки — остается очень высокой.Но как я уже упоминал выше — даже с этими недостатками проект остается для меня интересным.
Из того, что уже упоминалось в моих других статьях в последние месяцы — куплен кислородный концентратор, позволяет получить ~95% кислород без головной боли. Из вредных примесей — похоже только углекислый газ (35ppm), будем надеяться, этого будет достаточно. Также едет из Китая генератор озона (ему на входе нужен кислород) — есть результаты исследований, показывающих что им удобно растить тонкие подзатворные диэлектрики и использовать как один из этапов для очистки пластин.Уже достаточно давно куплен металлографический микроскоп, и исследованы кучи существующих микросхем. В целом, стало намного понятнее с чем придется иметь дело. И наконец, поскольку микроскоп — симметричный прибор, его можно использовать для проекции уменьшенного изображения при фотолитографии. Совмещение изображения — визуальное и ручное. Источник освещения для проецирования — даже не обязательно УФ диодом делать, белый свет также вполне подойдет — качество изображения позволяет (хотя мощные 405нм диоды у меня тоже есть). Достижимые таким образом нормы фотолитографии — микронные (если сильно постараться — то до ~350нм), но смысла сильно уменьшать транзисторы нет — т.к. пропорционально уменьшается и «размер кадра», контакты к которым придется приваривать выводы станут слишком мелкими. Так что придется первоначально ограничиться нормами 10-20мкм, как и планировалось.
Микроскоп несколько поколебал веру как в отечественных производителей, так и в китайских. Оказалось, некоторые «отечественные» микроскопы — перемаркированные китайцы за 200-300% цены. С другой стороны — один из объективов похоже немного кривоват и предметный столик имел небольшой дефект литья — пришлось дорабатывать напильником (в прямом смысле этого слова).
Один из важных химических элементов для производства микросхем — вода. Опять-же в Китае куплен кондуктометр — измеритель электропроводности воды. По электропроводности можно оценить количество растворенных солей (+-50%, если не известно что именно растворено). В воде обычно растворены соли калия, натрия, кальция и марганца — и все они очень опасны для микросхем (особенно натрий и калий), т.к. их ионы могут быстро двигаться в кремнии и оксиде кремния при обычных температурах и изменять электрические параметры транзисторов (для полевых транзисторов — пороговое напряжение, утечку).
Измерил имеющиеся образцы воды, и получил следующее:
Концентрация примесей | |
Водопроводная вода | 219ppm |
«Новый» бытовой фильтр | 118ppm |
«Старый» бытовой фильтр | 210ppm |
Кипяченая вода из нового фильтра | 140ppm (!!! 2 раза перепроверял) |
Бидистиллированная вода из Русхима (Не похоже на бидистиллированную) |
10ppm |
Деионизировнаная вода из института микробиологии | 0ppm |
Деионизированная после 6 часов на воздухе (Из-за растворения углекислого газа из воздуха) |
8ppm |
Также удалось купить и TMAH (тетраметиламмония гидроксид) — используется как проявитель для фоторезиста, не содержащий ионов щелочных металлов (которые как мы знаем — зло).
Для вакуумной системы — вместо покупки вакуумной резины (несколько раз пытался — но так и не осилил), нашелся в Китае вот такой вот gasket maker — паста, которую можно выдавить в нужную форму, она затвердевает — и становится резиновой.
По печке: для теплоизоляции — куплено вот такое базальтовое полотно, используется для теплоизоляции ядерных реакторов. Выдерживает 1000-1200 градусов.
Под микроскопом — видно отдельные нити расплавленного базальта, из которых сплетено полотно. Вот это настоящие нанотехнологии!!! В голове по началу не укладывается: как из камня можно сделать тончайшие нити, и соткать гибкий материал? (масштаб: 1 пиксель ~ 3 микрометра):
Найдены и порезаны кварцевые трубки для печки разного диаметра. Первый уровень теплоизоляции — воздушный зазор межу вставленными друг в друга трубками.
Изначально я думал питать печку прямо от 220 вольт — но все-же благоразумно решил перейти на питание постоянным напряжением 48 Вольт — это позволит как точнее регулировать и контролировать мощность, так и сделает конструкцию безопаснее. Куплены 2 блока питания на 400Вт. Как китайцы такой блок производят и доставляют за 19$ — загадка:
Для контроля температуры — изначально были куплены высокотемпературные термопары, рассчитанные на 1200 градусов (про них писал в прошлой серии — но фотографии не было). Размер конечно конский. Вероятно будет проще следить за уровнем инфракрасного излучения на длине волны 1мкм — кварц для него прозрачен.
И наконец — инертная среда для печки. В моем случае это Аргон. Из-за особенностей разделения газов — аргон получается чище, чем азот, хоть и несколько дороже. Я купил маленький 10л баллон, и регулятор. Регулятор внезапно не подошел — резьба не совпадает, нужно или переходник искать, или другой регулятор покупать.
Оказалось, сжатые газы продают рядом с домом (жизнь в промышленной зоне Москвы имеет свои преимущества) — и я приехал за ним с тележкой. Рабочий не оценил мой порыв — и настоятельно рекомендовал завернуть баллон в картон, чтобы прохожие не переживали. За 15 минут мы справились с камуфляжем. В общем, встреча с реальным миром вечно дарит сюрпризы 🙂
Генератор азота — это конечно удобно, работать с пластинами в инертной атмосфере и не возиться с баллонами, но также не критично.
Единственное, что серьёзно могло бы облегчить работу — это образцы spin-on dopants и spin-on glass. В России по различным причинам их не используют и не производят, за рубежем — производителей мало, продается большими партиями и стоит дорого (тысячи $). Компания Emulsitone, у которой покупала образцы Jeri Ellsworth когда делала свои транзисторы — похоже загнулась, с ними связаться так и не удалось. Но это также не обязательный пункт — работать можно и без них (с фосфорной и борной кислотами, POCl3 и BBr3), хоть и намного сложнее / несколько опаснее.
И наконец — конечно не хватает спонсора для моих проектов, иногда между дополнительными затратами времени и дополнительными затратами денег приходится выбирать первое. Если кто-то из компаний или частных лиц имеет желание спонсировать мои проекты (условия обсуждаемы) — вы знаете, где меня найти :-).
Update: Ориентировочная смета есть, высылаю по запросу — т.е. представление на что именно нужны деньги — есть.
Затем нужно думать, как в домашних условиях сделать ультразвуковую или термокомпрессионную сварку проволоки с кремниевой пластиной — это нужно для подключения выводов.
Надеюсь, в обозримом будущем домашние микросхемы мы все-же увидим 🙂
Эту завесу тайны мы сегодня и приподнимем, и поможет нам в этом — серная и азотная кислота.
Внимание! Любые операции с концентрированными (а тем более кипящими) кислотами крайне опасны, и работать с ними можно только используя соответствующие средства защиты (перчатки, очки, фартук, вытяжка). Помните, у нас всего 2 глаза, и каждому хватит одной капли: потому все что тут написано — повторять не стоит.
Берем интересующие нас микросхемы, добавляем концентрированной серной кислоты. Довести до кипения (~300 градусов), не помешивать 🙂 На дне насыпана сода — чтобы нейтрализовать пролитую кислоту и её пары.Через 30-40 минут от пластика остается углерод:
Достаем и выбираем, что пойдет еще на одну живительную кислотную ванну, а что уже готово:
Если куски углерода намертво прилипли к кристаллу, их можно удалить кипящей концентрированной азотной кислотой ( но температура тут уже намного ниже, ~110-120C). Разбавленная кислота съест металлизацию, потому нужна именно концентрированная:
Цвета традиционно «усилены» до максимума — в реальности буйство красок намного меньше.
PL2303HX — конвертор USB<>RS232, такие используются во всяких Arduino и иже с ними:
LM1117 — линейный регулятор питания:
74HC595 — 8-и битный сдвиговой регистр:
NXP 74AHC00
74AHC00 — 4 NAND (2И-НЕ) элемента. Глядя на гигантский размер кристалла (944×854 µm) — становится очевидно что и «старые» микронные технологии до сих пор используются. Интересно обилие «резервных» via для увеличения выхода годных.
Micron MT4C1024 — микросхема динамической памяти, 1 Мебибит (220 бит). Использовалась во времена 286 и 386. Размер кристалла — 8662×3969µm.
AMD Palce16V8h
Микросхемы GAL(Generic array logic) — предшественники FPGA и CPLD.
AMD Palce16V8h это 32×64 массив элементов AND.
Размер кристалла — 2434×2079µm, технология 1µm.
ATtiny13A — один из самых мелких микроконтроллеров Atmel: 1кб флеш-памяти и 32 байта SRAM. Размер кристалла — 1620×1640 µm. Технологические нормы — 500nm.
ATmega8 — один из наиболее популярных 8-и битных микроконтроллеров.
Размер кристалла — 2855×2795µm, технологические нормы 500nm.
КР580ИК80А (позже переименованный в КР580ВМ80А) — один из наиболее массовых советских процессоров.
Оказалось, что вопреки распространенному убеждению, он не является послойной копией Intel 8080/8080A (некоторые блоки похожи, но разводка и расположение контактных площадок существенно отличается).
Самые тонкие линии — 6µm.
STM32F100C4T6B — самый маленький микроконтроллер на ядре ARM Cortex-M3 производства STMicroelectronics. Размер кристалла — 2854×3123µm.
Altera EPM7032 — CPLD повидавшая многое, и одна из немногих работавших на 5В питании. Размер кристалла — 3446×2252µm, технологические нормы 1µm.
Черный ящик теперь открыт 🙂
PS. Если у вас есть микросхемы имеющие историческое значение (например Т34ВМ1, советский 286, зарубежные старые и уникальные для своего времени чипы), присылайте — посмотрим что у них внутри.
Фотографии распространяются под лицензией Creative Commons Attribution 3.0 Unported.
От песка до процессора / Блог компании Intel / Хабр
Сложно в это поверить, но современный процессор является самым сложным готовым продуктом на Земле – а ведь, казалось бы, чего сложного в этом куске железа?Как и обещал – подробный рассказ о том, как делают процессоры… начиная с песка. Все, что вы хотели знать, но боялись спросить )
Я уже рассказывал о том, «Где производят процессоры» и о том, какие «Трудности производства» на этом пути стоят. Сегодня речь пойдет непосредственно про само производство – «от и до».
Производство процессоров
Когда фабрика для производства процессоров по новой технологии построена, у нее есть 4 года на то, чтобы окупить вложенные средства (более $5млрд) и принести прибыль. Из несложных секретных расчетов получается, что фабрика должна производить не менее 100 работающих пластин в час.
Вкратце процесс изготовления процессора выглядит так: из расплавленного кремния на специальном оборудовании выращивают монокристалл цилиндрической формы. Получившийся слиток охлаждают и режут на «блины», поверхность которых тщательно выравнивают и полируют до зеркального блеска. Затем в «чистых комнатах» полупроводниковых заводов на кремниевых пластинах методами фотолитографии и травления создаются интегральные схемы. После повторной очистки пластин, специалисты лаборатории под микроскопом производят выборочное тестирование процессоров – если все «ОК», то готовые пластины разрезают на отдельные процессоры, которые позже заключают в корпуса.
Уроки химии
Давайте рассмотрим весь процесс более подробно. Содержание кремния в земной коре составляет порядка 25-30% по массе, благодаря чему по распространённости этот элемент занимает второе место после кислорода. Песок, особенно кварцевый, имеет высокий процент содержания кремния в виде диоксида кремния (SiO2) и в начале производственного процесса является базовым компонентом для создания полупроводников.
Первоначально берется SiO2 в виде песка, который в дуговых печах (при температуре около 1800°C) восстанавливают коксом:
SiO2 + 2C = Si + 2COТакой кремний носит название «технический» и имеет чистоту 98-99.9%. Для производства процессоров требуется гораздо более чистое сырье, называемое «электронным кремнием» — в таком должно быть не более одного чужеродного атома на миллиард атомов кремния. Для очистки до такого уровня, кремний буквально «рождается заново». Путем хлорирования технического кремния получают тетрахлорид кремния (SiCl4), который в дальнейшем преобразуется в трихлорсилан (SiHCl3):
3SiCl4 + 2H2 + Si 4SiHCl3Данные реакции с использованием рецикла образующихся побочных кремнийсодержащих веществ снижают себестоимость и устраняют экологические проблемы:
2SiHCl3 SiH2Cl2 + SiCl4Получившийся в результате водород можно много где использовать, но самое главное то, что был получен «электронный» кремний, чистый-пречистый (99,9999999%). Чуть позже в расплав такого кремния опускается затравка («точка роста»), которая постепенно вытягивается из тигля. В результате образуется так называемая «буля» — монокристалл высотой со взрослого человека. Вес соответствующий — на производстве такая дуля весит порядка 100 кг.
2SiH2Cl2 SiH3Cl + SiHCl3
2SiH3Cl SiH4 + SiH2Cl2
SiH4 Si + 2H2
Слиток шкурят «нулёвкой» 🙂 и режут алмазной пилой. На выходе – пластины (кодовое название «вафля») толщиной около 1 мм и диаметром 300 мм (~12 дюймов; именно такие используются для техпроцесса в 32нм с технологией HKMG, High-K/Metal Gate). Когда-то давно Intel использовала диски диаметром 50мм (2″), а в ближайшем будущем уже планируется переход на пластины с диаметром в 450мм – это оправдано как минимум с точки зрения снижения затрат на производство чипов. К слову об экономии — все эти кристаллы выращиваются вне Intel; для процессорного производства они закупаются в другом месте.
Каждую пластину полируют, делают идеально ровной, доводя ее поверхность до зеркального блеска.
Производство чипов состоит более чем из трёх сотен операций, в результате которых более 20 слоёв образуют сложную трёхмерную структуру – доступный на Хабре объем статьи не позволит рассказать вкратце даже о половине из этого списка 🙂 Поэтому совсем коротко и лишь о самых важных этапах.
Итак. В отшлифованные кремниевые пластины необходимо перенести структуру будущего процессора, то есть внедрить в определенные участки кремниевой пластины примеси, которые в итоге и образуют транзисторы. Как это сделать? Вообще, нанесение различных слоев на процессорную подложу это целая наука, ведь даже в теории такой процесс непрост (не говоря уже о практике, с учетом масштабов)… но ведь так приятно разобраться в сложном 😉 Ну или хотя бы попытаться разобраться.
Фотолитография
Проблема решается с помощью технологии фотолитографии — процесса избирательного травления поверхностного слоя с использованием защитного фотошаблона. Технология построена по принципу «свет-шаблон-фоторезист» и проходит следующим образом:
— На кремниевую подложку наносят слой материала, из которого нужно сформировать рисунок. На него наносится фоторезист — слой полимерного светочувствительного материала, меняющего свои физико-химические свойства при облучении светом.Нужная структура рисуется на фотошаблоне — как правило, это пластинка из оптического стекла, на которую фотографическим способом нанесены непрозрачные области. Каждый такой шаблон содержит один из слоев будущего процессора, поэтому он должен быть очень точным и практичным.
— Производится экспонирование (освещение фотослоя в течение точно установленного промежутка времени) через фотошаблон
— Удаление отработанного фоторезиста.
Иной раз осаждать те или иные материалы в нужных местах пластины просто невозможно, поэтому гораздо проще нанести материал сразу на всю поверхность, убрав лишнее из тех мест, где он не нужен — на изображении выше синим цветом показано нанесение фоторезиста.
Пластина облучается потоком ионов (положительно или отрицательно заряженных атомов), которые в заданных местах проникают под поверхность пластины и изменяют проводящие свойства кремния (зеленые участки — это внедренные чужеродные атомы).
Как изолировать области, не требующие последующей обработки? Перед литографией на поверхность кремниевой пластины (при высокой температуре в специальной камере) наносится защитная пленка диэлектрика – как я уже рассказывал, вместо традиционного диоксида кремния компания Intel стала использовать High-K-диэлектрик. Он толще диоксида кремния, но в то же время у него те же емкостные свойства. Более того, в связи с увеличением толщины уменьшен ток утечки через диэлектрик, а как следствие – стало возможным получать более энергоэффективные процессоры. В общем, тут гораздо сложнее обеспечить равномерность этой пленки по всей поверхности пластины — в связи с этим на производстве применяется высокоточный температурный контроль.
Так вот. В тех местах, которые будут обрабатываться примесями, защитная пленка не нужна – её аккуратно снимают при помощи травления (удаления областей слоя для формирования многослойной структуры с определенными свойствами). А как снять ее не везде, а только в нужных областях? Для этого поверх пленки необходимо нанести еще один слой фоторезиста – за счет центробежной силы вращающейся пластины, он наносится очень тонким слоем.
В фотографии свет проходил через негативную пленку, падал на поверхность фотобумаги и менял ее химические свойства. В фотолитографии принцип схожий: свет пропускается через фотошаблон на фоторезист, и в тех местах, где он прошел через маску, отдельные участки фоторезиста меняют свойства. Через маски пропускается световое излучение, которое фокусируется на подложке. Для точной фокусировки необходима специальная система линз или зеркал, способная не просто уменьшить, изображение, вырезанное на маске, до размеров чипа, но и точно спроецировать его на заготовке. Напечатанные пластины, как правило, в четыре раза меньше, чем сами маски.
Весь отработанный фоторезист (изменивший свою растворимость под действием облучения) удаляется специальным химическим раствором – вместе с ним растворяется и часть подложки под засвеченным фоторезистом. Часть подложки, которая была закрыта от света маской, не растворится. Она образует проводник или будущий активный элемент – результатом такого подхода становятся различные картины замыканий на каждом слое микропроцессора.
Собственно говоря, все предыдущие шаги были нужны для того, чтобы создать в необходимых местах полупроводниковые структуры путем внедрения донорной (n-типа) или акцепторной (p-типа) примеси. Допустим, нам нужно сделать в кремнии область концентрации носителей p-типа, то есть зону дырочной проводимости. Для этого пластину обрабатывают с помощью устройства, которое называется имплантер — ионы бора с огромной энергией выстреливаются из высоковольтного ускорителя и равномерно распределяются в незащищенных зонах, образованных при фотолитографии.
Там, где диэлектрик был убран, ионы проникают в слой незащищенного кремния – в противном случае они «застревают» в диэлектрике. После очередного процесса травления убираются остатки диэлектрика, а на пластине остаются зоны, в которых локально есть бор. Понятно, что у современных процессоров может быть несколько таких слоев — в таком случае на получившемся рисунке снова выращивается слой диэлектрика и далее все идет по протоптанной дорожке — еще один слой фоторезиста, процесс фотолитографии (уже по новой маске), травление, имплантация… ну вы поняли.
Характерный размер транзистора сейчас — 32 нм, а длина волны, которой обрабатывается кремний — это даже не обычный свет, а специальный ультрафиолетовый эксимерный лазер — 193 нм. Однако законы оптики не позволяют разрешить два объекта, находящиеся на расстоянии меньше, чем половина длины волны. Происходит это из-за дифракции света. Как быть? Применять различные ухищрения — например, кроме упомянутых эксимерных лазеров, светящих далеко в ультрафиолетовом спектре, в современной фотолитографии используется многослойная отражающая оптика с использованием специальных масок и специальный процесс иммерсионной (погружной) фотолитографии.
Логические элементы, которые образовались в процессе фотолитографии, должны быть соединены друг с другом. Для этого пластины помещают в раствор сульфата меди, в котором под действием электрического тока атомы металла «оседают» в оставшихся «проходах» — в результате этого гальванического процесса образуются проводящие области, создающие соединения между отдельными частями процессорной «логики». Излишки проводящего покрытия убираются полировкой.
Финишная прямая
Ура – самое сложное позади. Осталось хитрым способом соединить «остатки» транзисторов — принцип и последовательность всех этих соединений (шин) и называется процессорной архитектурой. Для каждого процессора эти соединения различны – хоть схемы и кажутся абсолютно плоскими, в некоторых случаях может использоваться до 30 уровней таких «проводов». Отдаленно (при очень большом увеличении) все это похоже на футуристическую дорожную развязку – и ведь кто-то же эти клубки проектирует!
Когда обработка пластин завершена, пластины передаются из производства в монтажно-испытательный цех. Там кристаллы проходят первые испытания, и те, которые проходят тест (а это подавляющее большинство), вырезаются из подложки специальным устройством.
На следующем этапе процессор упаковывается в подложку (на рисунке – процессор Intel Core i5, состоящий из CPU и чипа HD-графики).
Привет, сокет!
Подложка, кристалл и теплораспределительная крышка соединяются вместе – именно этот продукт мы будем иметь ввиду, говоря слово «процессор». Зеленая подложка создает электрический и механический интерфейс (для электрического соединения кремниевой микросхемы с корпусом используется золото), благодаря которому станет возможным установка процессора в сокет материнской платы – по сути, это просто площадка, на которой разведены контакты от маленького чипа. Теплораспределительная крышка является термоинтерфейсом, охлаждающим процессор во время работы – именно к этой крышке будут примыкать система охлаждения, будь то радиатор кулера или здоровый водоблок.
Сокет (разъём центрального процессора) — гнездовой или щелевой разъём, предназначенный для установки центрального процессора. Использование разъёма вместо прямого распаивания процессора на материнской плате упрощает замену процессора для модернизации или ремонта компьютера. Разъём может быть предназначен для установки собственно процессора или CPU-карты (например, в Pegasos). Каждый разъём допускает установку только определённого типа процессора или CPU-карты.
На завершающем этапе производства готовые процессоры проходят финальные испытания на предмет соответствия основным характеристикам – если все в порядке, то процессоры сортируются в нужном порядке в специальные лотки – в таком виде процессоры уйдут производителям или поступят в OEM-продажу. Еще какая-то партия пойдет на продажу в виде BOX-версий – в красивой коробке вместе со стоковой системой охлаждения.
The end
Теперь представьте себе, что компания анонсирует, например, 20 новых процессоров. Все они различны между собой – количество ядер, объемы кэша, поддерживаемые технологии… В каждой модели процессора используется определенное количество транзисторов (исчисляемое миллионами и даже миллиардами), свой принцип соединения элементов… И все это надо спроектировать и создать/автоматизировать – шаблоны, линзы, литографии, сотни параметров для каждого процесса, тестирование… И все это должно работать круглосуточно, сразу на нескольких фабриках… В результате чего должны появляться устройства, не имеющие права на ошибку в работе… А стоимость этих технологических шедевров должна быть в рамках приличия… Почти уверен в том, что вы, как и я, тоже не можете представить себе всего объема проделываемой работы, о которой я и постарался сегодня рассказать.
Ну и еще кое-что более удивительное. Представьте, что вы без пяти минут великий ученый — аккуратно сняли теплораспределительную крышку процессора и в огромный микроскоп смогли увидеть структуру процессора – все эти соединения, транзисторы… даже что-то на бумажке зарисовали, чтобы не забыть. Как думаете, легко ли изучить принципы работы процессора, располагая только этими данными и данными о том, какие задачи с помощью этого процессора можно решать? Мне кажется, примерно такая картина сейчас видна ученым, которые пытаются на подобном уровне изучить работу человеческого мозга. Только если верить стэнфордским микробиологам, в одном человеческом мозге находится больше «транзисторов», чем во всей мировой IT-инфраструктуре. Интересно, правда?
BONUS
Хватило сил дочитать до этого абзаца? ) Поздравляю – приятно, что я постарался не зря. Тогда предлагаю откинуться на спинку кресла и посмотреть всё описанное выше, но в виде более наглядного видеоролика – без него статья была бы не полной.
Эту статью я писал сам, пытаясь вникнуть в тонкости процесса процессоростроения. Я к тому, что в статье могут быть какие-то неточности или ошибки — если найдете что-то, дайте знать. А вообще, чтобы окончательно закрепить весь прочитанный материал и наглядно понять то, что было недопонято в моей статье, пройдите по этой ссылке. Теперь точно всё.
Успехов!
Как на самом деле производят процессоры
Песок. В наших компьютерах в буквальном смысле песок, вернее — составляющий его кремний. Это основной элемент, благодаря которому в компьютерах всё работает. А вот как из песка получаются компьютеры.
Что такое процессор
Процессор — это небольшой чип внутри вашего компьютера или телефона, который производит все вычисления. Об основе вычислений мы уже писали — это транзисторы, которые собраны в сумматоры и другие функциональные блоки.
Если очень упрощённо — это сложная система кранов и труб, только вместо воды по ним течёт ток. Если правильным образом соединить эти трубы и краны, ток будет течь полезным для человека образом и получатся вычисления: сначала суммы, потом из сумм можно получить более сложные математические операции, потом числами можно закодировать текст, цвет, пиксели, графику, звук, 3D, игры, нейросети и что угодно ещё.
Кремний
Почти все процессоры, которые производятся в мире, делаются на кремниевой основе. Это связано с тем, что у кремния подходящая внутренняя атомная структура, которая позволяет делать микросхемы и процессоры практически любой конфигурации.
Самый доступный источник кремния — песок. Но кремний, который получается из песка, на самом первом этапе недостаточно чистый: в нём есть 0,5% примесей. Может показаться, что чистота 99,5% — это круто, но для процессоров нужна чистота уровня 99,9999999%. Такой кремний называется электронным, и его можно получить после цепочки определённых химических реакций.
Когда цепочка заканчивается и остаётся только чистый кремний, можно начинать выращивать кристалл.
Кристалл и подложка
Кристаллы — это такие твёрдые тела, в которых атомы и молекулы вещества находятся в строгом порядке. Проще говоря, атомы в кристалле расположены предсказуемым образом в любой точке. Это позволяет точно понимать, как будет вести себя это вещество при любом воздействии на него. Именно это свойство кристаллической решётки используют на производстве процессоров.
Самые распространённые кристаллы — соль, драгоценные камни, лёд и графит в карандаше.
Большой кристалл можно получить, если кремний расплавить, а затем опустить туда заранее подготовленный маленький кристалл. Он сформирует вокруг себя новый слой кристаллической решётки, получившийся слой сделает то же самое, и в результате мы получим один большой кристалл. На производстве он весит под сотню килограмм, но при этом очень хрупкий.
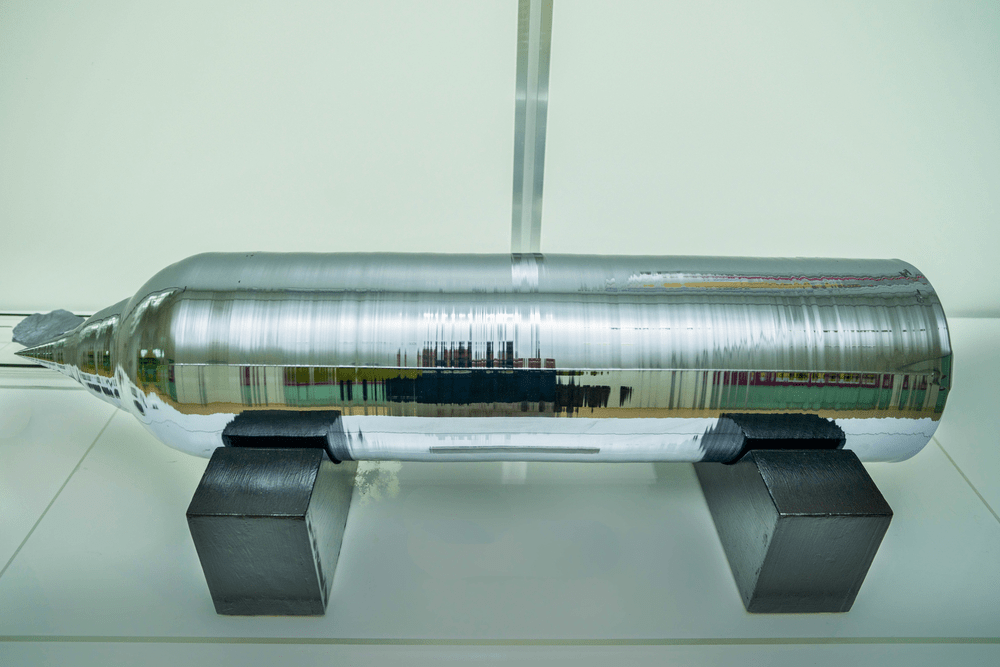
Готовый кристалл кремния.
После того, как кристалл готов, его нарезают специальной пилой на диски толщиной в миллиметр. При этом диаметр такого диска получается около 30 сантиметров — на нём будет создаваться сразу несколько десятков процессоров.
Каждую такую пластинку тщательно шлифуют, чтобы поверхность получилась идеально ровной. Если будут зазубрины или шероховатости, то на следующих этапах диск забракуют.
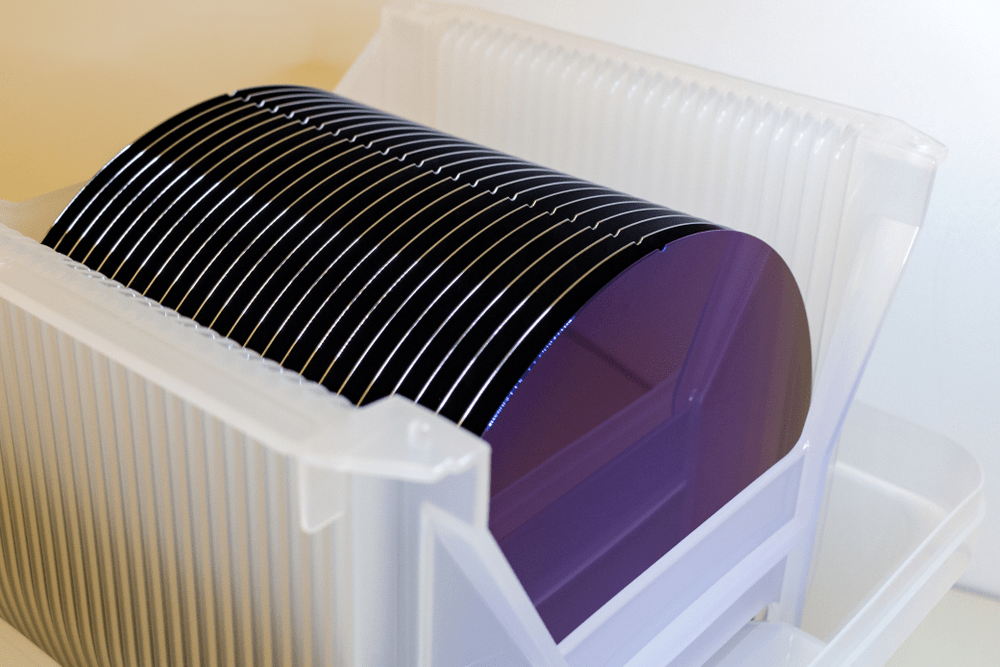
Готовые отполированные пластины кремния.
Печатаем транзисторы
Когда диски отполированы, на них можно формировать процессоры. Процесс очень похож на то, как раньше печатали чёрно-белые фотографии: брали плёнку, светили сверху лампой, а снизу клали фотобумагу. Там, куда попадал свет, бумага становилось тёмной, а те места, которые закрыло чёрное изображение на плёнке, оставались белыми.
С транзисторами всё то же самое: на диск наносят специальный слой, который при попадании света реагирует с молекулами диска и изменяет его свойства. После такого облучения в этих местах диск начинает проводить ток чуть иначе — сильнее или слабее.
Чтобы так поменять только нужные участки, на пути света помещают фильтр — прямо как плёнку в фотопечати, — который закрывает те места, где менять ничего не надо.
Потом получившийся слой покрывают тонким слоем диэлектрика — это вещество, которое не проводит ток, типа изоленты. Это нужно, чтобы слои процессора не взаимодействовали друг с другом. Процесс повторяется несколько десятков раз. В результате получаются миллионы мельчайших транзисторов, которые теперь нужно соединить между собой.
Соединяем всё вместе
То, как соединяются между собой транзисторы в процессоре, называется процессорной архитектурой. У каждого поколения и модификации процессоров своя архитектура. Все производители держат в секрете тонкости архитектуры, потому что от этого может зависеть скорость работы или стоимость производства.
Так как транзисторов много, а связей между ними нужно сделать немало, то поступают так: наносят токопроводящий слой, ставят фильтр и закрепляют проводники в нужном месте. Потом слой диэлектрика и снова токопроводящий слой. В результате выходит бутерброд из проводников, которые друг другу не мешают, а транзисторы получают нужные соединения.
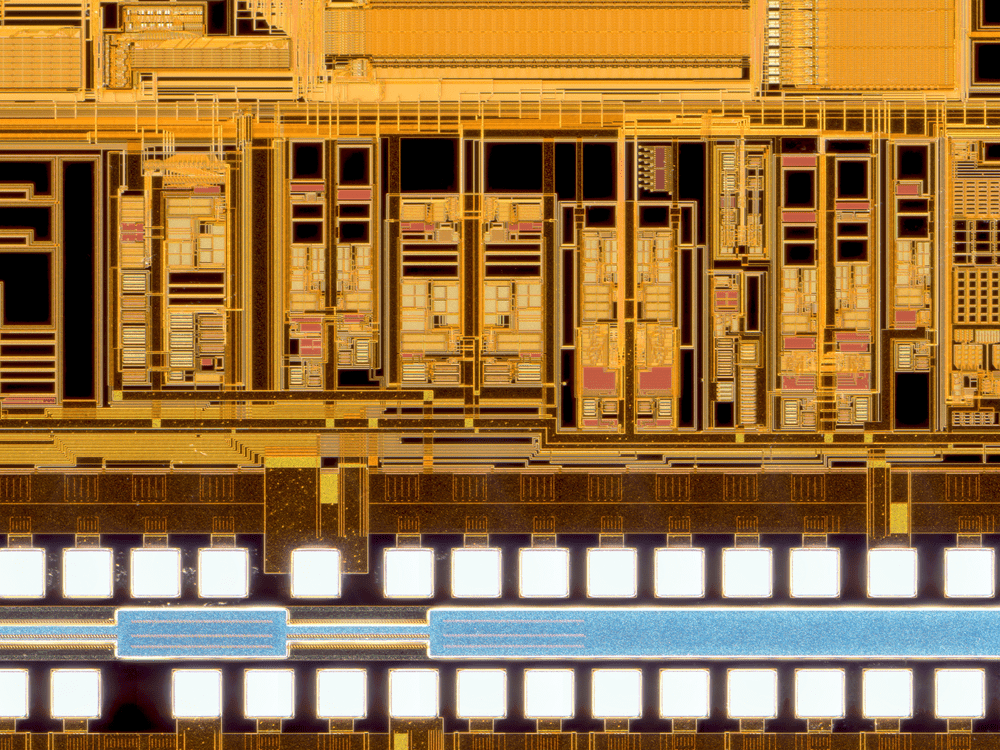
Токопроводящие дорожки крупным планом. На фото они уже в несколько слоёв и не мешают друг другу.
В чём сложность
Современные процессоры производятся на нанометровом уровне, то есть размеры элементов измеряются нанометрами, это очень мало.
Если, например, во время печати очень толстый мальчик упадёт на пол в соседнем цехе, еле заметная ударная волна прокатится по перекрытиям завода и печатная форма немного сдвинется, а напечатанные таким образом транзисторы окажутся бракованными. Пылинка, попавшая на пластину во время печати — это, считай, загубленное ядро процессора.
Поэтому на заводах, где делают процессоры, соблюдаются жёсткие стандарты чистоты, все ходят в масках и костюмах, на всех воздуховодах стоят фильтры, а сами заводы находятся на сейсмических подушках, чтобы толчки земной коры не мешали производить процессоры.
Крышка и упаковка
Когда дорожки готовы, диск отправляют на тесты. Там смотрят на то, как работает каждый процессор, как он греется и сколько ему нужно энергии, заодно проверяют на брак.
В зависимости от результатов процессоры с одной пластины могут получить разную маркировку и продаваться по разной стоимости. Те процессоры, которые получились более удачными, становятся дорогими серверными продуктами. Те, где кто-то рядом чихнул или вздохнул, имеют некоторые несовершенства и дефекты, их могут отправить на потребительскую линию.
После тестов диск разрезают на готовые процессорные ядра.
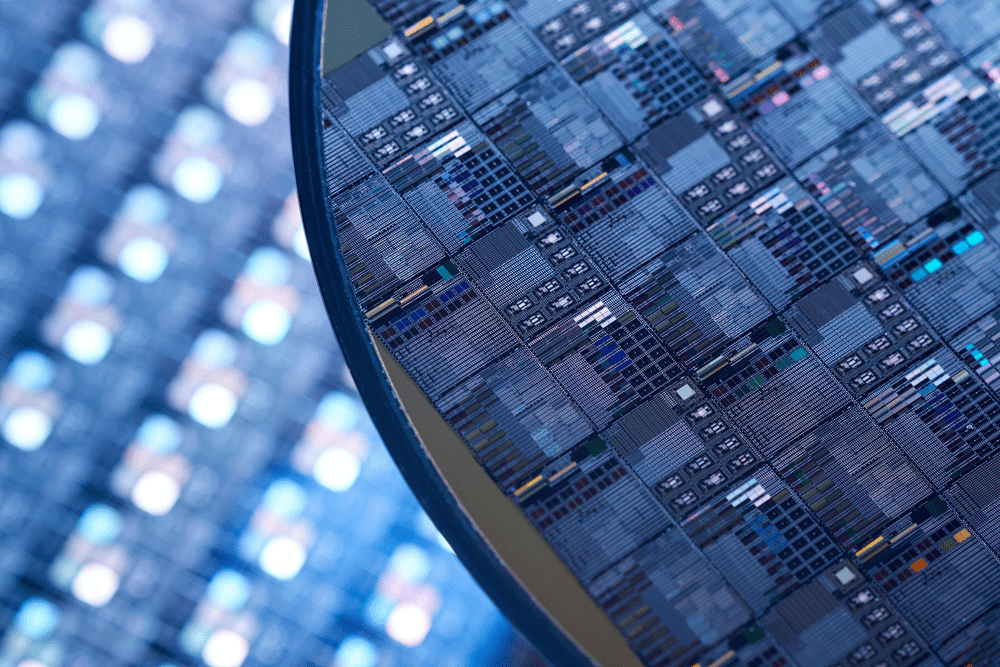
Пластина со множеством одинаковых процессорных ядер.
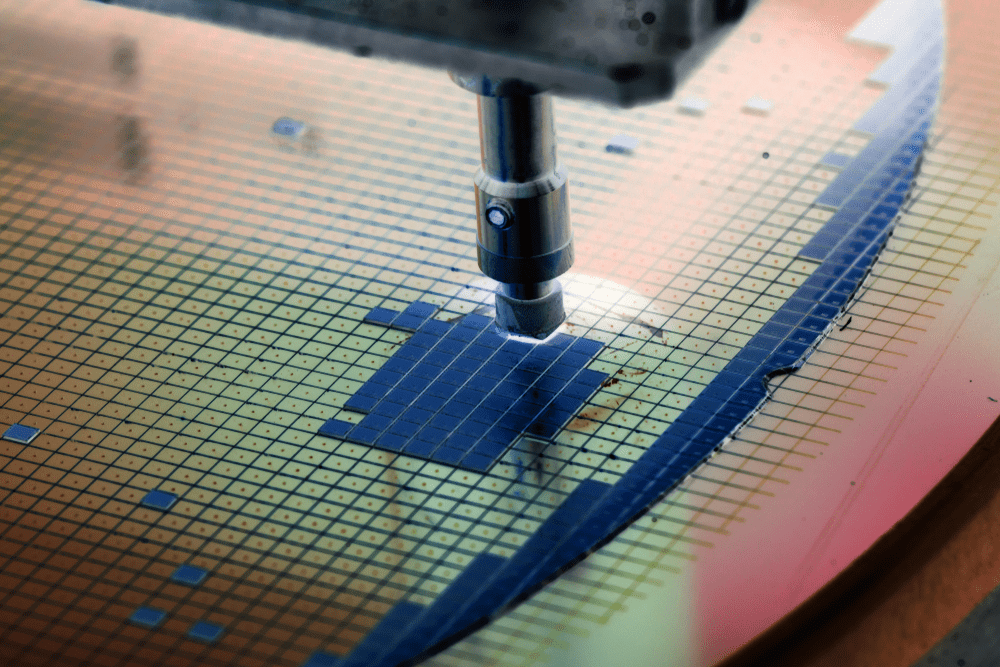
Робот вырезает ядра из готовой пластины.
После этого к ядру процессора добавляют контакты, чтобы можно было вставить его в материнскую плату, и накрывают крышкой. Чёрный или металлический прямоугольник, из которого торчат ножки, — это как раз крышка.
Крышка выполняет две функции: защищает сам кристалл от повреждений и отводит от него тепло во время работы. Дело в том, что миллионы транзисторов при работе нагреваются, и если процессор не остужать, то он перегреется и кристалл может испортиться. Чтобы такого не произошло, на крышку процессора ставят воздушные кулеры или делают водяное охлаждение.
Система на чипе
Чипы процессоров уже настолько маленькие, что под одной крышкой можно поместить какое-нибудь ещё устройство. Например, видеосистему — то, что обсчитывает картинку перед выводом на экран. Или устройство радиосвязи с антенной.
В какой-то момент на маленьком чипе площадью около 1 см2 уже можно было поместить процессор, видео, модем и блютус, сделать всё нужное для поддержки памяти и периферии — в общем, система на чипе. Подключаете к этому хозяйству экран, нужное количество антенн, портов и кнопок, а главное — здоровенную батарею, и у вас готовый смартфон. По сути, все «мозги» вашего смартфона находятся на одном маленьком чипе, а 80% пространства за экраном занимает батарея.
Статья о микросхемах от Free Dictionary
* PCU3344133344131, Производство полупроводников и связанных с ними устройств: встроенные микросхемы, в том числе сертификация процессов и распознавание дефектов: гибриды, микросхемы и модули RF / MMIC — эта сертификация процессов необходима для качества, процессов, инженеров-производителей, дизайнеров и старших техников и идеально подходит для инспекторы и линейные операторы, стремящиеся расширить свою базу знаний и понимание критериев визуального контроля, а также материалов и процессов, используемых для сборки гибридов, микросхем и модулей RFMIC для высоконадежных военных и аэрокосмических применений.Исследователи показывают, что слабая связь обеспечивает основу для пресинаптической пластичности, отличительной черты синаптической передачи сигналов в микросхемах гиппокампа. Передача информации в синапсе между нейронами является очень сложной, но в то же время очень быстрой серией событий. Он сказал, что доля Армении на мировом рынке микросхем и дизайна составляет 5%. Требование DLA предусматривает, что Агентство будет только закупить FSC 5962 (микросхемы), в которых используется маркировка ДНК SigNature. Обсуждаемые темы включают в себя биологические вдохновленные универсальные когнитивные микросхемы, визуальные паттерны при сканировании человека, эволюционные подходы к построению искусственных умов, моделирование человеческой памяти, эмоциональную основу для обучения, подобного человеку, и дисциплину когнитивной агенты.Микросхемы гиппокампа; справочник по компьютерному моделированию. Собранные данные послужили основой для очень подробного моделирования групп нервных клеток, а также микросхем нейронов, которые распределены по более крупным структурам, таким как зрительная кора. Пьезокерамика необходима для создания напряжения от вибраций. которые полезны в микросхемах. И Хендерсон, и Армстронг подчеркивают важность конденсатора, который хранит механическую энергию, создаваемую окружающими колебаниями.Газ, используемый при изготовлении жидкокристаллических плоскопанельных дисплеев, микросхем и тонкопленочных фотоэлектрических элементов, в 17000 раз более мощный парниковый газ, чем углекислый газ. Он внес выдающийся вклад в пересмотр спецификации военных характеристик для микросхем. В пересмотренном документе рассматриваются текущие инженерные и технические потребности космического сообщества, военных ведомств и производителей оборудования DoD для создания надежных военных и космических микросхем. Поскольку количество модулей на микросхему в следующем десятилетии будет увеличиваться, ожидается поток данных. Юрий А. говорит, что он опережает возможности обработки информации в электронных микросхемах, которые переносят и направляют трафик.,Как произносится MICROCIRCUIT, язык: Английский
Ваш браузер не поддерживает аудио HTML5
Великобритания
Как произносится microcircuit существительное в британском английскомВаш браузер не поддерживает аудио HTML5
нас
Как произносится microcircuit существительное в американском английском,
микросхема 들 들
микросхема
Система контроля позволила пользователю сканировать поверхность гибридных микросхем.,