Что такое акустический датчик. Как работает акустический датчик. Какие бывают виды акустических датчиков. Где применяются акустические датчики. Каковы преимущества использования акустических датчиков.
Что такое акустический датчик и как он работает
Акустический датчик (микрофон) — это устройство, которое преобразует звуковые колебания в электрический сигнал. Принцип работы большинства современных акустических датчиков основан на изменении емкости конденсатора при колебаниях звуковой мембраны.
Основные элементы конструкции акустического датчика:
- Тонкая гибкая мембрана (диафрагма)
- Неподвижная пластина с отверстиями (задняя пластина)
- Воздушный зазор между мембраной и задней пластиной
- Электроды на мембране и задней пластине
Когда звуковая волна воздействует на мембрану, она начинает колебаться относительно неподвижной задней пластины. Это приводит к изменению емкости конденсатора, образованного мембраной и задней пластиной. Изменение емкости преобразуется в электрический сигнал с помощью специальной электронной схемы.
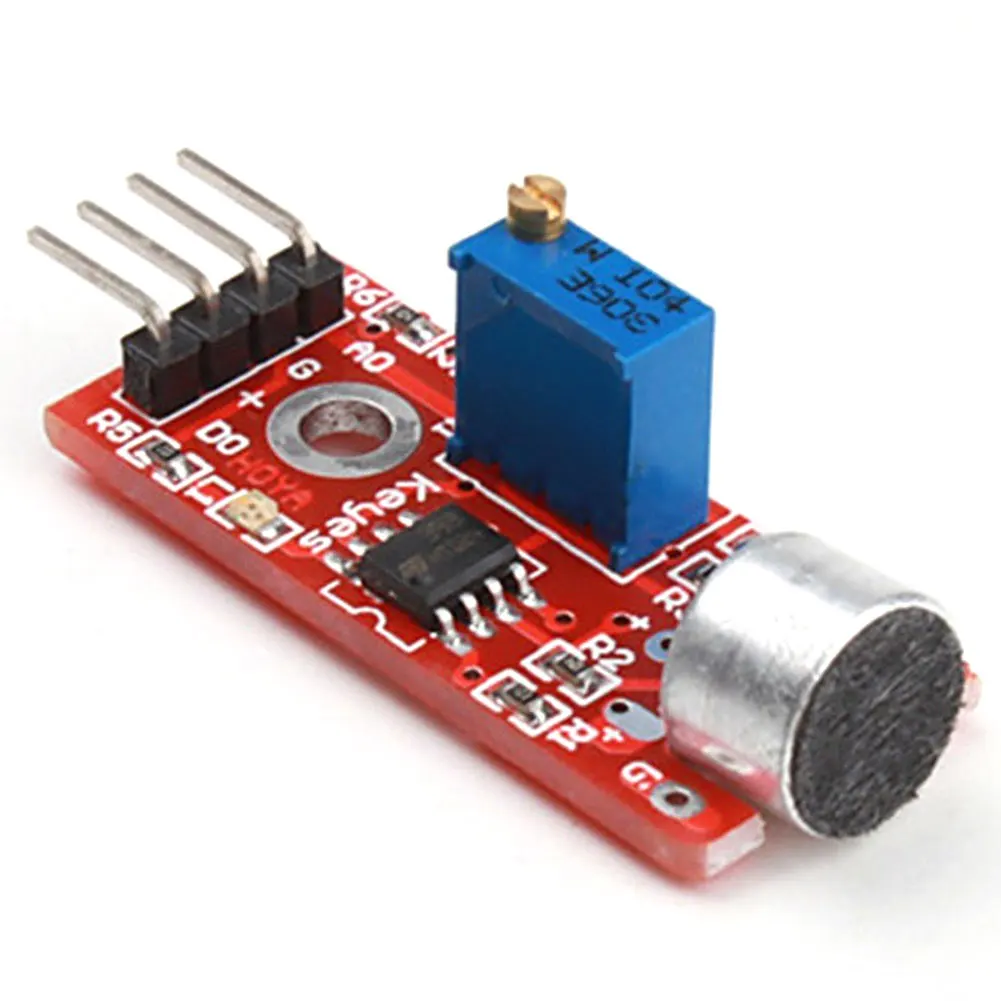
Основные виды акустических датчиков
Существует несколько основных типов акустических датчиков:
1. Конденсаторные (емкостные) микрофоны
Это наиболее распространенный тип акустических датчиков. Принцип их работы описан выше. Отличаются высокой чувствительностью и качеством звука.
2. Электретные микрофоны
Разновидность конденсаторных микрофонов, в которых используется электретный материал, сохраняющий постоянный электрический заряд. Не требуют внешнего источника питания для поляризации.
3. Динамические микрофоны
В них используется подвижная катушка, прикрепленная к мембране и расположенная в магнитном поле постоянного магнита. При колебаниях мембраны в катушке индуцируется электрический ток.
4. Пьезоэлектрические микрофоны
Работают на основе пьезоэлектрического эффекта — возникновения электрического заряда при деформации некоторых кристаллов. Отличаются простотой конструкции.
Применение акустических датчиков в современных системах
Акустические датчики нашли широкое применение в различных областях техники и технологий:
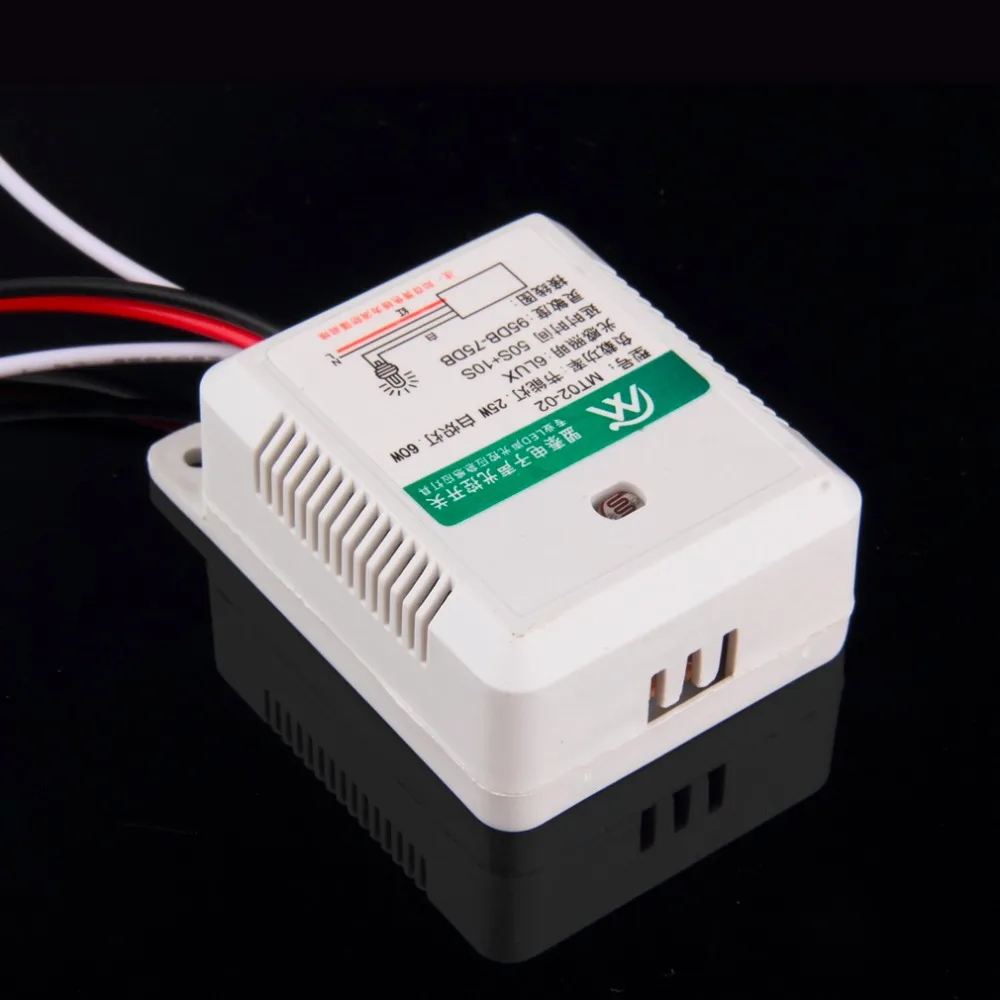
1. Системы распознавания речи и голосового управления
Акустические датчики используются в смартфонах, умных колонках и других устройствах для записи голосовых команд пользователя. Это позволяет реализовать функции голосовых помощников и голосового управления техникой.
2. Системы шумоподавления
В наушниках с активным шумоподавлением акустические датчики регистрируют внешний шум, который затем компенсируется с помощью специальных алгоритмов.
3. Охранные системы
Акустические датчики способны обнаруживать звук разбивающегося стекла или другие подозрительные шумы, что позволяет использовать их в системах охраны помещений.
4. Промышленный контроль
В промышленности акустические датчики применяются для мониторинга состояния оборудования, обнаружения утечек в трубопроводах и других задач неразрушающего контроля.
5. Медицинская диагностика
Акустические датчики используются в электронных стетоскопах для прослушивания звуков сердца и легких, а также в ультразвуковых диагностических системах.
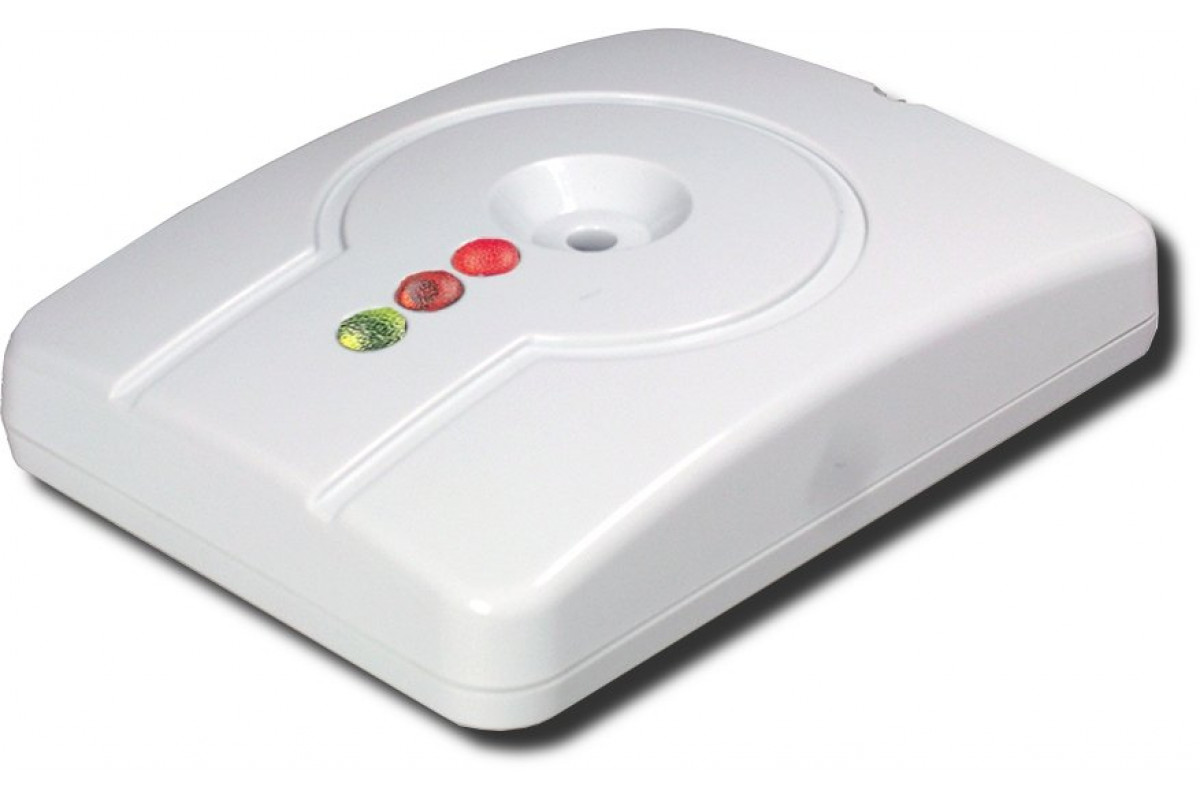
Преимущества использования акустических датчиков MEMS
Современные акустические датчики часто изготавливаются по технологии MEMS (микроэлектромеханические системы). Это обеспечивает ряд преимуществ:
- Миниатюрные размеры (менее 1 мм)
- Низкое энергопотребление
- Возможность интеграции с электронными схемами на одном кристалле
- Высокая стабильность характеристик
- Низкая стоимость при массовом производстве
Благодаря этим преимуществам акустические датчики MEMS широко используются в мобильных устройствах, носимой электронике и IoT-устройствах.
Проблемы и задачи при разработке акустических датчиков
При создании современных акустических датчиков инженерам приходится решать ряд сложных задач:
Снижение собственного шума датчика
Уменьшение размеров датчика приводит к увеличению влияния тепловых шумов и других источников помех. Для борьбы с этим применяются специальные конструктивные решения, например:
- Использование щелевой конструкции диафрагмы для снижения демпфирования
- Оптимизация расположения и размеров отверстий в задней пластине
- Применение специальных материалов с низкими внутренними потерями
Повышение чувствительности
Для увеличения чувствительности датчика при сохранении малых размеров используются следующие подходы:

- Уменьшение толщины и увеличение площади диафрагмы
- Оптимизация формы диафрагмы для увеличения ее подвижности
- Применение новых материалов с улучшенными механическими свойствами
Расширение частотного диапазона
Для работы в широком диапазоне частот применяются следующие методы:
- Использование нескольких резонансных частот диафрагмы
- Применение специальных демпфирующих покрытий
- Оптимизация акустических свойств корпуса датчика
Перспективы развития акустических датчиков
Основные направления совершенствования акустических датчиков в ближайшем будущем:
1. Дальнейшая миниатюризация
Уменьшение размеров датчиков позволит интегрировать их в еще более компактные устройства, например, в миниатюрные слуховые аппараты или имплантируемые медицинские устройства.
2. Повышение энергоэффективности
Снижение энергопотребления акустических датчиков критически важно для носимых устройств и автономных сенсорных систем с длительным сроком работы.
3. Интеграция с системами искусственного интеллекта
Объединение акустических датчиков с нейронными сетями позволит создавать более совершенные системы распознавания речи, эмоций и окружающих звуков.
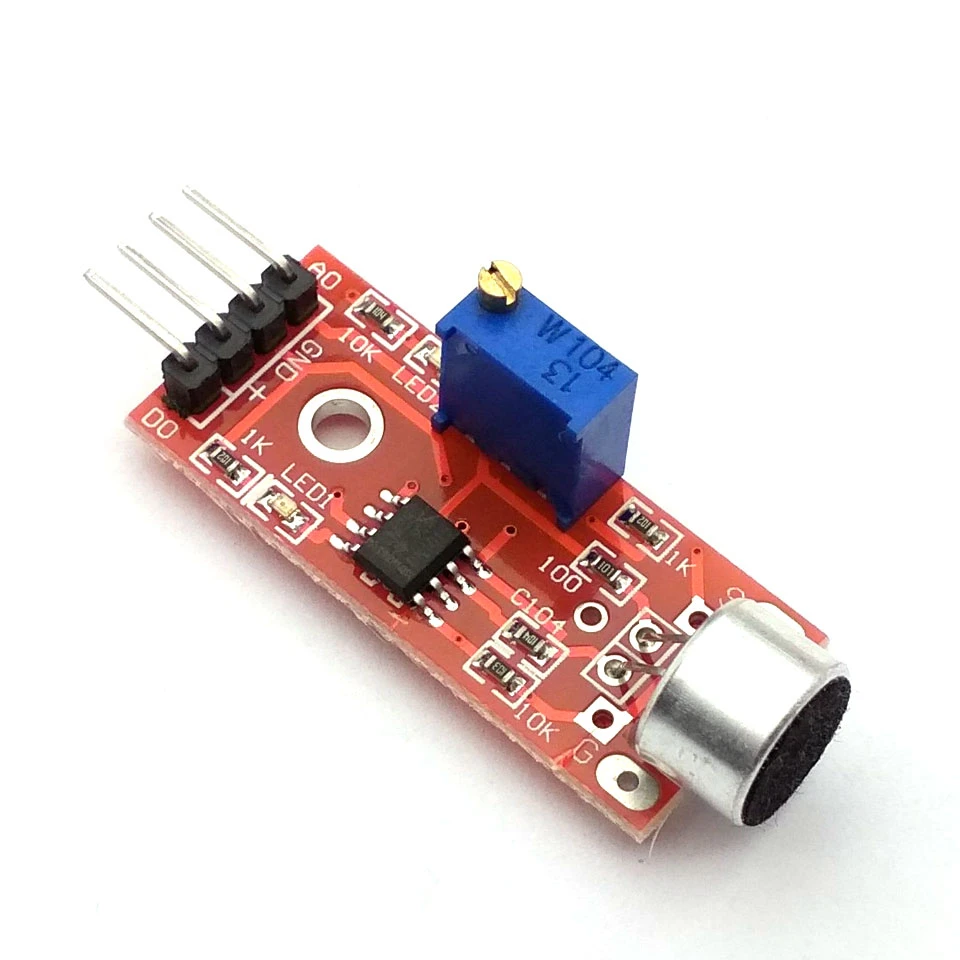
4. Развитие многофункциональных датчиков
Создание датчиков, способных одновременно регистрировать звук, вибрацию и другие физические параметры, расширит возможности их применения в различных областях.
Заключение
Акустические датчики играют важную роль в современных технологиях, обеспечивая взаимодействие между человеком и машиной, контроль окружающей среды и диагностику различных систем. Развитие технологий MEMS и новых материалов открывает широкие перспективы для создания еще более совершенных и миниатюрных акустических датчиков, которые найдут применение в самых разнообразных областях — от бытовой электроники до космических аппаратов.
Акустический датчик разбития стекла
Включите в вашем браузере JavaScript!
- Главная
Охранно-пожарная сигнализация- Датчики разбития, наклона, вибро
- Акустический датчик разбития стекла
Сортировкапо возрастанию ценыпо убыванию ценысначала новыепо названию
В наличии
6 м
Предзаказ
Извещатель охранный поверхностный звуковой Звон-1 (ИО 329-8)
В наличии6 м
120°
Предзаказ
Звуковой извещатель разбития стекла Астра-531 АК
В наличии
6 м
Предзаказ
Извещатель охранный акустический Астра-С
В наличии
9 м
Предзаказ
Извещатель охранный поверхностный звуковой Стекло-3 (ИО 329-4)
В наличии
SALE
Предзаказ
Детектор разбития стекла Pironix BG16DF
В наличии
120°
9 м
Предзаказ
Извещатель охранный поверхностный звуковой адресный Rubezh ИО 32920-2 прот. R3
В наличии
90°
18 м
Предзаказ
Извещатель совмещенный Crow SWAN PGB (ИК + акустический)
В наличии
RF 433 Мгц
6 м
120°
Предзаказ
Радиоканальный звуковой извещатель разбития стекла Астра-6131
В наличии
Предзаказ
PIR датчик с детекцией разбития стекла Hikvision DS-PDPG12P-EG2
Нет в наличии
6 м
Предзаказ
Извещатель совмещенный Астра-531 СМ (ИК + акустический)
Нет в наличии
10 м
Предзаказ
Извещатель охранный поверхностный совмещенный ИК+разбитие Орлан-Д (ИО 315-1/2)
9 м
Предзаказ
Извещатель потолочный совмещенный Орлан-2 (ИО 315-7) (ИК + акустический)
Online заказ 24 / 7
Быстрая доставка по России
Любые способы оплаты
Специальные условия для монтажных организаций
Прогрессивные и накопительные скидки
Гарантия на всё оборудование
Каталог
Обратный звонок
Запрос успешно отправлен!
Телефон *
Настоящим подтверждаю, что я ознакомлен и согласен с условиями оферты и политики конфиденциальности *
Предзаказ
Предзаказ успешно отправлен!
Телефон *
Настоящим подтверждаю, что я ознакомлен и согласен с условиями оферты и политики конфиденциальности *
Добавить в корзину
Перейти в корзину
Распределенный акустический датчик — Инно технолоджи
Распределенный акустический датчик
(Distributed Acoustic Sensor, DAS)
Позволяет обнаруживать вибрационные воздействия (акустические колебания) действующие на оптическое волокно. В зависимости от места установки оптического кабеля технологию можно использовать как для охраны периметров, так и для проведения акустических исследований скважин. В качестве чувствительного элемента используется стандартное телекоммуникационное одномодовое волокно.
Преимущества технологии
- Определение нехарактерных для нормальной работы скважины событий на основе акустических шаблонов
- Проведение вертикального сейсмопрофилирования
- Измерение акустического воздействия по всей длине кабеля
- Определяет места локальных возмущений и превышение допустимых значений вибро-акустического фона вблизи кабеля
- Возможность одновременного использования данной технологии в комплексе с геофизическим прибором
Принцип работы распределенного акустического датчика (DAS)
После обработки
Обработка акустических данных
Начнем работу
Ответим на любые вопросы. Просто оставьте заявку на сайте.
+7 (342) 294-41-23
+7 (342) 294-41-24
614068, Пермский край, г. Пермь, ул. Решетникова, дом 4
Политика конфиденциальности
- Главная
- Контакты
- Продукты и услуги
- Системы постоянного мониторинга (CMS)
- Многорычажная профилеметрия (MFC)
- Метод многочастотной диэлектрической интроскопии (MFDI)
- Распределенный датчик температуры (DTS)
- Распределенный акустический датчик (DAS)
- Волоконно-оптический датчик на брэгговских решетках (FBG)
- Высокотемпературные исследования скважин (HTS)
- Высокотемпературный гироскопический инклинометр (HTGI)
Акустические датчики MARPOSS
ОПИСАНИЕ
Системы мониторинга, основанные на акустической технологии, контролируют шум, издаваемый при касании шлифовальным кругом детали или правящего инструмента. Шум возникает во время резания и передается через шлифование в виде ультразвуковых волн. Когда эти волны проходят через различные компоненты машины, их частота и амплитуда меняются. Отслеживая эти волны, можно проверить любые изменения во время обработки и, следовательно, можно выполнить корректирующие действия на станке. Эффективность датчиков определяется их расположением как можно ближе к зоне обработки.
Мониторинг с помощью акустических датчиков используется для определения контакта шлифовального круга с деталью или инструментом для правки, сокращая время воздушного зазора. Изменения в акустической эмиссии могут указывать на изменения силы из-за условий резания шлифовального круга и позволяют адаптировать цикл, тем самым оптимизируя производственный процесс.
Существует две серии акустических датчиков:
- Стационарные акустические датчики: датчики состоят из одной детали, сигнал может передаваться в воздухе или через жидкость. Доступны различные размеры для удовлетворения любых требований применения.
- Бесконтактные акустические датчики: датчики состоят из неподвижной части (статора) и вращающейся части (ротора), но имеют различные формы и размеры для соответствия требованиям любого применения. Сигнал передается без прямого контакта между ротором и статором.
Датчики могут быть подключены к следующим системам:
BLÚ P1D AE P3SE P7SE Sensitron6 DS5000 DS6000 DS7000
ЛЬГОТЫ
- Мониторинг производственного процесса
- Проверка воздушного зазора и сокращение времени цикла
- Проверка на столкновение и снижение риска серьезного повреждения шлифовального круга и станка
- Снижение затрат на техническое обслуживание и общих затрат
- Увеличение срока службы деталей машины
ТЕХНИЧЕСКИЕ ХАРАКТЕРИСТИКИ
- Частотная характеристика: до 1000 кГц
- Скорость вращения: до 120 000 об/мин
ВЕРСИИ
Доступны различные версии акустических датчиков, которые позволяют размещать их как можно ближе к зоне обработки, где достигается наилучшее соотношение сигнал/шум.
Стационарный акустический датчик: ультразвуковой датчик акустической эмиссии с поверхностным распространением и передачей сигнала по кабелю. Датчик располагается на детали или на приспособлении для правки толкателя.
Акустический датчик жидкости: 9Датчик ультразвуковой акустической эмиссии 0048 с поверхностным распространением и передачей сигнала по кабелю. Сигнал передается от детали или опоры детали или инструмента через машинную смазку/охлаждающую жидкость.
Поворотный акустический датчик: ультразвуковой акустико-эмиссионный датчик с бесконтактной передачей сигнала. Датчик располагается на шпинделе, на опорном фланце шлифовального круга или на правящем диске.
Внутренний акустический датчик шпинделя: ультразвуковой акустико-эмиссионный датчик с бесконтактной передачей сигнала. Поворотная часть разделена и состоит из пьезоэлектрического датчика и части передачи электронного сигнала. Размеры датчика могут быть адаптированы к конкретным требованиям применения. Датчик располагается на шлифовальном круге или шпинделе правки.
Кольцевой акустический датчик: ультразвуковой акустико-эмиссионный датчик с бесконтактной передачей сигнала. Неподвижная и вращающаяся части имеют форму кольца и доступны в различных размерах и формах, чтобы их можно было устанавливать снаружи на различные модели шлифовальных станков. Датчик располагается на фланце шлифовального круга, на шпинделе или на опорной головке детали.
Скачать
Брошюра | |
---|---|
Английский | ДАТЧИКИ АКУСТИЧЕСКОЙ ЭМИССИИ: (5.19MB) |
Немецкий | ДАТЧИКИ АКУСТИЧЕСКОЙ ЭМИССИИ: (5.![]() |
Исследование и разработка малошумящих акустических датчиков МЭМС | ОМРОН ТЕХНИКС | Технология
Важные соображения по воздушному демпфированию и стабильности процесса
- Инновационная технология
- Акустический датчик МЭМС
- Конструкция с щелевой диафрагмой
- Снижение собственного шума
- Расположение узких проемов
- Технология стабилизации процесса травления
2019/12/13
В последнее время большое внимание привлекают технологии акустического восприятия, такие как распознавание речи или шумоподавление. Эти новые приложения стимулируют спрос на акустические датчики MEMS (микроэлектромеханическая система) меньшего размера и с меньшим уровнем шума. Датчики микромасштаба чувствительны к собственному шуму, вызванному воздушным демпфированием. Поэтому понимание и управление воздушным демпфированием имеет решающее значение для разработки датчиков с низким уровнем шума.
В этой статье мы сообщаем о новой конструкции акустических датчиков MEMS, которая обеспечивает SNR (отношение сигнал/шум) более 68 дБ. Мы смоделировали доминирующие источники шума на основе анализа эквивалентных схем и представили оригинальные структуры, которые значительно уменьшают демпфирование сжатой воздушной пленки. Этот новый дизайн был успешно коммерциализирован благодаря отработанным методам стабильности процесса тонкопленочных. Разработанные нами акустические датчики могут широко использоваться в приложениях, требующих мелкомасштабных и точных акустических измерений.
1. Введение
Тенденция к установке различных датчиков на различные приборы или живые организмы для сбора данных и использования полученных данных для жизнеобеспечения и промышленности растет день ото дня. В таких условиях возлагаются большие надежды на малые и высокоточные сенсорные устройства. Микроэлектромеханическая система (МЭМС), представляющая собой технологию микрообработки, к которой применяется полупроводниковая технология, представляет собой эффективный метод, позволяющий уменьшить размеры, повысить точность и снизить энергопотребление. Компания Omron практически реализовала датчики давления и датчики расхода на основе технологии MEMS.
Как правило, уменьшение размера датчика снижает его чувствительность и облегчает его заглушение шумом, создаваемым самим датчиком. В случае MEMS, миниатюризированного до микрометрового масштаба, поскольку на него существенно влияют тепловые флуктуации, влияние шума представляет собой более серьезную проблему 1) . Таким образом, метод проектирования малошумящих МЭМС-датчиков является важной темой.
Вышеупомянутое обстоятельство относится и к микрофонам (далее – «акустические датчики»). С расширением потребностей в использовании акустического восприятия в новых приложениях, таких как распознавание речи и шумоподавление, ожидается, что акустические датчики будут более точными, то есть с меньшим шумом 2) .
В этом исследовании мы систематически работали над реализацией малошумящего МЭМС-датчика, используя в качестве объекта акустические датчики. В результате удалось добиться значительно меньшего шума, чем на момент начала серийного производства, за счет выявления основных источников шума и перепроектирования соответствующих конструкций. В этой статье мы сообщаем о моделировании, направленном на снижение шума, о результатах проверки эффекта снижения шума посредством прототипирования и оценки реальных устройств, а также о технологии стабилизации процесса.
2. Состав МЭМС акустического датчика
2.1 Модуль акустического датчика
На рис. 1 показан состав модуля акустического датчика МЭМС. Микросхема датчика MEMS для обнаружения звуков и интегральная микросхема для считывания сигнала установлены на подложке, которая закрыта крышкой. На рис. 1 (а) представлена фотография внешнего вида модуля акустического датчика МЭМС с открытой крышкой, а на рис. 1 (б) — схематический вид в разрезе. В случае акустического датчика звуковое отверстие на подложке и внутренний объем крышки являются важными составляющими элементами, оказывающими решающее влияние на акустические характеристики. На этом рисунке модуль оценки (2.95 × 3,76 × 1,25 мм).
2.2 Микросхема акустического датчика MEMS
На рис. 2 (a) показана структура нашего обычного чипа акустического датчика МЭМС емкостного типа 3) . В этой конструкции тыльная пластина с множеством отверстий (из нитрида кремния, толщиной 3,5 мкм и стороной 750 мкм) и квадратная тонкая диафрагма (из поликремния, толщиной 0,8 мкм) обращены друг к другу с воздушным зазором 3–4 мкм между ними для образования конденсатора. Вибрация диафрагмы, вызванная звуковым давлением, обнаруживается как незначительное изменение емкости. Как показывает изображение, полученное с помощью сканирующего электронного микроскопа (СЭМ) на рис. 2 (б), использование технологии МЭМС позволило уменьшить размер датчика с точностью до одного миллиметра, что меньше, чем у механических акустических датчиков.
В микросхеме акустического датчика, показанной на рис. 2 (а), имеются небольшие участки, обозначенные буквой «L» на рисунке, между периметром диафрагмы и кремниевой подложкой, где они перекрываются (далее — «перекрытие»). ”, что составляет 2,2 мкм в высоту и 60 мкм в ширину). Эти области представляют собой вентиляционные отверстия, соединяющие переднюю сторону диафрагмы с ее задней стороной, которые важны для предотвращения изменения характеристики из-за изменения внешнего атмосферного давления. Однако, если эти области слишком велики, возникает дифракция звука и снижается чувствительность. Следовательно, акустическое сопротивление должно быть достаточно высоким, когда воздух проходит через эти пространства.
3.
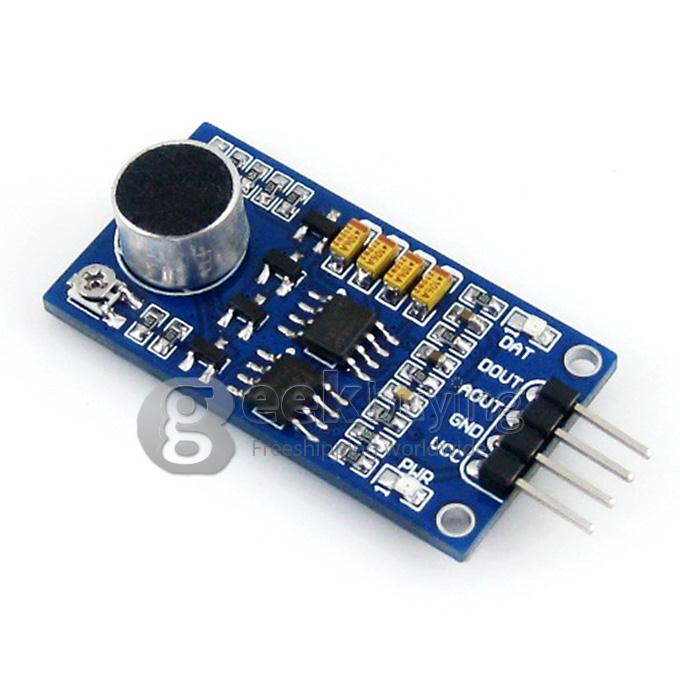
3.1 Проблема шума с компактными датчиками
Не ограничиваясь акустическими датчиками, сигнал, который генерируется внутри активированного сенсорного модуля, даже если все внешние входы заблокированы, называется «собственным шумом». Предпочтительно, чтобы собственный шум был низким, поскольку он определяет минимальный предел обнаружения. Для компактных датчиков собственный шум более проблематичен по следующим трем причинам:
- (1)
- Наличие механизма генерации шума, специфичного для микрометрической шкалы: см. следующий раздел.
- (2)
- Ухудшение баланса из-за шума ИС из-за низкой чувствительности: если область считывания мала, чувствительность снижается и, как правило, скрывается за электрическими шумами, вызванными ИС (такими как шум Джонсона и мерцающий шум).
- (3)
- Шум из-за малого объема: В случае акустического датчика низкочастотный шум увеличивается по мере уменьшения объема упаковки.
Поэтому при разработке датчика необходимо учитывать влияние соответствующих шумов. Объем изделия № 3 зависит от требований заказчика, а для изделия № 2 ключевой задачей является разработка микросхемы с низким уровнем шума для датчика. В этом исследовании мы работали над снижением собственного шума, создаваемого микросхемой MEMS, описанной в пункте № 1.
3.2 Источник шума, характерный для устройств с микрометровой шкалой
Конструкции в микрометровом масштабе становятся трудно перемещаемыми из-за влияния вязкости 4) . На пластину, расположенную на расстоянии нескольких микрометров от неподвижной пластины и совершающую вертикальные колебания, действует сила сопротивления, препятствующая свободным движениям. Это явление называется «затухание сжатой пленки» и связано с вязкостью жидкости, возникающей, когда тонкий слой жидкости между пластинами проталкивается внутрь и наружу пластин вдоль поверхности стенки, как показано на рис. 3 (а). Поскольку эта сила сопротивления обратно пропорциональна кубу расстояния между пластинами, она становится очень большой в микрометровом масштабе 9.0124 5) . Это демпфирующее сопротивление может быть значительным источником шума для устройств MEMS, потому что сила сопротивления, описанная выше, вызывает тепловые флуктуации, и эти флуктуации сотрясают диафрагму, превращаясь в собственный шум. Тепловой шум вызван тепловыми колебаниями воздуха или конструкции, и амплитуда колебаний пропорциональна квадратному корню из силы сопротивления 1) . Акустический датчик MEMS, показанный на рис. 2, также имеет область, где вышеупомянутое демпфирование сжатой пленкой происходит на перекрытии и в воздушном зазоре.
Для уменьшения демпфирующего сопротивления, описанного выше, обычно используется неподвижная пластина или подвижная пластина с отверстиями, как показано на рис. 3 (b) 5) . Однако следует отметить, что чрезмерное открытие отверстий приводит к снижению чувствительности.
3.3 Анализ шума на основе модели эквивалентной схемы
Известно, что анализ на основе модели эквивалентной схемы эффективен для проектирования свойств датчика 6) . На рис. 4 показан модуль акустического датчика, показанный на рис. 1, в модели эквивалентной электроакустической схемы, которая показывает поток звукового давления, поступающего из звукового отверстия, а затем преобразуемого в электрический сигнал через элементы, соответствующие соответствующие структуры МЭМС и ИС. Перекрытие, описанное в разделе 2.2, выражается двумя резистивными элементами,
и
.
Из этой модели эквивалентной схемы можно спрогнозировать собственный шум всего модуля с помощью симулятора схемы путем добавления как шума, вызванного ИС, так и шума, вызванного МЭМС и структурой корпуса. Подробнее о том, как его рассчитать, см. в предыдущем отчете 7) .
На рис. 5 (а) показаны спектры плотности шума нашего обычного акустического датчика, полученные в результате моделирования и экспериментального результата. Результат расчета хорошо воспроизводит реально измеренную форму спектра. Кроме того, в среднем диапазоне (100 Гц – 10 кГц), который важен для слухового восприятия человека, определено, что шум, вызванный MEMS, преобладает над шумом, вызванным IC. На рис. 5 (b) показан шум МЭМС, разбитый на резистивные составляющие в эквивалентной схеме. На рис. 5 (б) показаны спектры мощности шума, взвешенные (А-вес) в отражении слухового ощущения человека. Площадь каждого графика соответствует мощности шума. Из этого рисунка видно, что шум, вызванный МЭМС, состоит в основном из шума, генерируемого во всем модуле (9).2% всего шума). Доля шума МЭМС, вызванная вкладом демпфирующего сопротивления Rd на перекрытии, чрезвычайно высока (80 % от общего числа), за ним следует вклад демпфирующего сопротивления Rag на воздушном зазоре (11 % от общего числа) и другие вклады могут быть почти проигнорированы.
3.4 Подход к снижению шума
Разбивка факторов шума прояснила, какой части мы должны уделить первоочередное внимание работе над снижением шума. Сопротивление демпфирования в узком пространстве является основной причиной собственного шума, генерируемого акустическими датчиками MEMS, и ниже мы опишем уменьшение демпфирования. Сначала работаем над уменьшением демпфирования в перекрытии, затем в воздушном зазоре.
4. Предложение новой малошумной конструкции
4.1 Конструкция с щелевой диафрагмой
Как описано в разделе 3.3, перекрытие считается основным источником шума. Однако это перекрытие необходимо для уменьшения влияния изменения давления. Поэтому мы предлагаем новую конструкцию диафрагмы, как показано на рис. 6 (а) 7) . В конструкции периметр диафрагмы разделен узкой щелью, и только внутренняя диафрагма, окруженная щелью, вибрирует под действием звукового давления. Преимущество этой конструкции состоит в том, что демпфирование между диафрагмой и подложкой может быть полностью устранено, поскольку ни одна кремниевая подложка не расположена нигде, обращенной к вибрирующей диафрагме (т.
равен нулю). Кроме того, поскольку щель играет роль вентиляционного отверстия, соединяющего переднюю сторону диафрагмы с ее задней стороной, конструкция щели с малой шириной позволяет поддерживать высокое акустическое сопротивление.
(б) – (г) СЭМ-изображения прототипа МЭМС-чипа
На рисунках 6 (б) – (г) показаны СЭМ-изображения разработанной нами конструкции щелевой диафрагмы 7) . На изображении поперечного сечения видно, что диафрагма отделена щелью шириной 0,5 мкм. Чтобы использовать эту щелевую структуру на практике, важна стабильность коробления диафрагмы. Это связано с тем, что при смещении щели по вертикали на 1 мкм и более вентиляционное отверстие увеличивается, и чувствительность в низкочастотном диапазоне снижается. Следовательно, требуется точный контроль напряжений в тонкой поликремниевой пленке, образующей диафрагму. Управляя ключевыми параметрами, такими как формирование поликремниевой пленки, ионная имплантация и температуры отжига 8) удалось стабильно поддерживать коробление диафрагмы в пределах +/- 0,5 мкм по всей поверхности 8-дюймовой пластины.
4.2 Расположение узких отверстий
Если перекрытие, которое является наибольшим источником шума, удалено, демпфирующее сопротивление в воздушном зазоре становится следующей доминантой. В последние годы демпфирующее сопротивление между перфорированной пластиной с регулярной сотовой структурой отверстий и неподвижной пластиной, как показано на рис. 3 (b), было хорошо исследовано, и было предложено несколько формул анализа 9) 10) . В этом исследовании мы рассчитали сопротивление демпфированию на основе различных комбинаций диаметра
и шаг
используя теоретическую формулу, полученную Veijola 10) . Сопротивление демпфированию уменьшается по мере увеличения коэффициента раскрытия задней пластины. Однако при чрезмерном увеличении коэффициента раскрытия уменьшение площади считывания приводит к снижению чувствительности и ухудшению отношения сигнал-шум (отношение сигнал/шум). Поэтому мы рассчитали модуль SNR для соответствующих диаметров и шагов с учетом как изменения чувствительности, так и изменения сопротивления демпфирования, как показано на рис.0124 11) . Для нашего обычного продукта диаметром 17 мкм и шагом 24 мкм было определено, что SNR может быть дополнительно улучшено, если шаг и диаметр отверстий находятся в пределах диапазона, обведенного белой пунктирной линией.
Поэтому мы разработали сенсорные микросхемы, оснащенные задней пластиной, для которой диаметр и шаг отверстий находятся в пределах диапазона, ограниченного белой пунктирной линией, показанной на рис. 7. В таблице 1 приведен список схем расположения отверстий. . Структура щелевой диафрагмы, описанная в предыдущем разделе, была применена ко всем макетам, и мы изменили только расположение отверстий в задней пластине. В таблице 1 также показаны виды сверху на разработанные нами задние пластины 11) . По сравнению с обычным продуктом ширина
,
которая показывает ширину оставшейся задней пластины между соседними отверстиями, мала. Для реализации подобных раскладок с узким шагом ключевым моментом является стабилизация процесса травления, в котором образуются отверстия. Управление фотолитографией и условиями травления таким образом, чтобы угол наклона поверхности стенки приближался к вертикальному углу, позволило свести к минимуму изменение поверхности 8-дюймовой пластины даже в случае узкого шага, когда оставшаяся ширина составляла 3 мкм или меньше.
и микроскопические и СЭМ изображения
5.

5.1 Метод измерения
Мы установили МЭМС-микросхему, в которую были введены новые структуры, описанные в главе 4, а также микросхему производства Omron на оценочный модуль, аналогичный показанному на рис. 1. Кроме того, мы измерили чувствительность к звуковому давлению. 1 Па и шума с использованием звуконепроницаемой коробки. При оценке отверстий с узким шагом мы использовали упаковку с внешними размерами 2,65×3,50×0,9.8 мм, что было более компактно, чем показанное на рис. 1 (а). Для измерения мы использовали аудиоанализатор (Audio Precision, SYS2722). Кроме того, чтобы отделить шум, вызванный МЭМС, от шума, вызванного ИС, мы также измерили шум, когда МЭМС был заменен чип-конденсатором эквивалентного конденсатора.
5.2 Результаты оценки
На рис. 8 показаны результаты измерения спектра шума, проведенного для изучения влияния конструкции щелевой диафрагмы 7) . По сравнению с обычным продуктом (длина перекрытия составляет 60 мкм) минимальный уровень шума в диапазоне от 1 кГц до 10 кГц уменьшался по мере уменьшения длины перекрытия, а минимальный уровень шума стал еще ниже при применении щелевой структуры. Это согласуется с предсказанием, описанным в разделе 3.3, о том, что основным источником шума в среднем диапазоне является сопротивление перекрытия. В результате применения щелевой структуры мы подтвердили, что собственный шум значительно уменьшился, а отношение сигнал-шум модуля увеличилось до более чем 66 дБ, в то время как у обычного модуля оно составляло 62 дБ. Описывая только результат, выбор узкой ширины щели позволил расширить полосу пропускания без снижения чувствительности до более низкого диапазона (< 20 Гц), чем у обычного продукта. Было подтверждено, что использование щелевой структуры эффективно для расширения диапазона частотных характеристик 7) .
Далее на рис. 9 показаны спектры шума акустических датчиков с измененным расположением отверстий на задней пластине, как описано в разделе 4.211). Во всех модулях от A до C было установлено, что минимальный уровень шума в диапазоне от 1 кГц до 10 кГц был ниже, чем у обычной компоновки, и шум уменьшался по мере увеличения коэффициента раскрытия. Это согласуется с результатом расчета уровня шума, описанным в разделе 3.3, согласно которому основным источником шума после удаления перекрытия был воздушный зазор. Как вставка на рис. 9Как видно, существует хорошая корреляция между измеренным демпфирующим сопротивлением воздушного зазора и теоретическим расчетным значением. В таблице 2 приведены результаты измерения чувствительности, шума и отношения сигнал-шум разработанного нами модуля. Во всех модулях от A до C отношение сигнал-шум составляло около 68,5 дБ, что было лучше на 1,0 дБ или более, чем у обычной раскладной компоновки. Можно сказать, что хотя увеличение степени раскрытия задней пластины снижает чувствительность, в модулях A–C преобладает эффект шумоподавления, что привело к улучшению SNR 11) .
Принимая во внимание баланс с механической прочностью задней панели, мы, наконец, выбрали схему открывания модуля B.
(вставка) Сравнение сопротивления в воздушном зазоре между расчетным значением и фактическим значением измерения
Таблица 2 Чувствительность, шум и ОСШ модулей с измененной схемой раскрытия
5.3 Краткое описание эффекта шумоподавления
Как мы описали в предыдущем разделе, внедрение структуры щелевой диафрагмы, а также оптимизация расположения отверстий на задней панели позволили снизить собственный шум акустического датчика на одну четверть (эквивалентно -6 дБ).
6. Выводы
Мы представили новые структуры для подавления основных источников шума в акустическом датчике MEMS, чтобы создать компактный и высокопроизводительный акустический датчик. Нам удалось снизить собственный шум датчика на 6 дБ по сравнению с обычными датчиками и достичь SNR 68 дБ, что было самым высоким уровнем в мире для акустического датчика MEMS по состоянию на 2018 год. Тот факт, что шум был снижен на 6 дБ означает, что качество сигнала может быть сохранено, если расстояние между датчиком и источником звука было удвоено, что выгодно для получения четких акустических данных. Ожидается, что акустический датчик, который мы разработали на этот раз, будет использоваться в новых приложениях акустического зондирования, таких как обнаружение аномалий оборудования или обнаружение биологических звуков, за счет использования его характеристик, таких как небольшой размер, низкий уровень шума и широкий диапазон частот.
Кроме того, метод количественного разделения источников шума с использованием модели эквивалентной схемы может применяться в самых разных приложениях, помимо акустических датчиков, для систематического снижения уровня шума. В частности, можно сказать, что управление воздушным демпфированием является общей проблемой при разработке МЭМС-устройств, оснащенных приводными частями микрометрового порядка, и этот метод можно эффективно использовать.
Наконец, практическая реализация новых структур, которые мы представили на этот раз (структура с щелевой диафрагмой и расположение отверстий с узким шагом), является результатом совершенствования производственных технологий, таких как контроль напряжения тонкой пленки поликремния и стабильность травления в плоскости. Можно сказать, что усилия, которые мы предприняли в этой разработке, являются примером передового опыта, показывающего, насколько важно сотрудничество между технологиями проектирования и технологическими процессами для устройств MEMS.
Благодарности
Эта разработка проводилась при поддержке г-на Такафуми Ота, г-на Кента Кадзикава и сотрудников завода Ясу, которые сотрудничали в производстве прототипов пластин и улучшении процесса. Мы также хотели бы поблагодарить г-на Такаши Фучимото и г-на Такуя Катагири, которые принадлежат к отделу развития III и сотрудничали в установке пакетов, сотрудников отдела обеспечения качества, которые сотрудничали в наблюдении за SEM и разработке микрофона. участников, которые дали много ценных советов. Мы хотели бы воспользоваться этой возможностью, чтобы выразить нашу искреннюю благодарность.
Каталожные номера
- 1)
- Т. Б. Габриэльсон: «Механическо-тепловой шум в микромеханических акустических и вибрационных датчиках», IEEE Transactions on Electron Devices, 1993, Vol. 40, с. 903-909.
- 2)
- М. Бустани и Ж. Бушо: «Внедрение высококачественных микрофонов обещает рост доходов», отчет IHS technology, 2014 г.
- 3)
- T. Kasai, Y. Tsurukame, T. Takahashi, F. Sato и S. Horiike: «Маленький кремниевый конденсаторный микрофон, улучшенный задней камерой с вогнутыми боковыми сторонами», в Digest Tech. Доклады Transducers 2007 Conference, 2007, с. 2613-2616.
- 4)
- С. Д. Сентурия.
; Дизайн микросистем, Kluwer Academic Publishers, 2001, 689 стр.
- 5)
- З. Шквор: «Об акустическом сопротивлении вследствие вязких потерь в воздушном зазоре электростатических преобразователей», Акустика, 1967, т. 1, с. 19, стр. 295-299.
- 6)
- С. К. Томпсон, Дж. Л. ЛоПрести, Э. М. Ринг, Х. Г. Непомусено, Дж. Дж. Берд, В. Дж. Баллад и Э.В. Карлсон: «Шум в миниатюрных микрофонах», J. Acoust. соц. Ам., 2002, Том. 111, стр. 861-866.
- 7)
- Т. Иноуэ, А. Мураками, Ю. Хоримото, Ю. Учида и Т. Касаи: «Проектирование усовершенствованного микрофона с высоким отношением сигнал-шум и плоской частотной характеристикой с использованием модели эквивалентной схемы», Материалы 8-го симпозиума JSAP по интегрированным МЭМС, 26:001-Д-1, 2016.
- 8)
- Томохиро Йошимура: «Упреждающее управление с помощью модели PLS всего процесса в производстве МЭМС», AEC/APC Symposium Asia 2015, MC-O-23, 2015.