Что такое оптоволокно и как оно работает. Как производят оптическое волокно. Преимущества и недостатки оптоволоконной связи. Процесс сварки оптоволокна и распространенные ошибки при работе с ним. Перспективы развития оптоволоконных технологий.
Что такое оптоволокно и как оно передает информацию
Оптоволокно — это тонкая нить из прозрачного материала (обычно кварцевого стекла), по которой передаются световые сигналы. Принцип его работы основан на явлении полного внутреннего отражения света. Оптоволокно состоит из сердцевины с высоким показателем преломления и оболочки с более низким показателем. Благодаря разнице показателей преломления свет отражается от границы сердцевины и оболочки, распространяясь внутри волокна на большие расстояния с минимальными потерями.
Технология производства оптического волокна
Процесс изготовления оптоволокна включает два основных этапа:
- Создание заготовки — стеклянного стержня с заданным профилем показателя преломления. Для этого используют различные методы, например, осаждение германия внутри кварцевой трубки.
- Вытяжка волокна из заготовки в специальной башне. Нижнюю часть заготовки нагревают до 1500°C и вытягивают тонкую нить, которая охлаждается и покрывается защитным полимером.
Из одной заготовки можно получить до 100 км оптоволокна толщиной всего 9 мкм (тоньше человеческого волоса). Затем волокна собирают в пучки и помещают в защитную оболочку, формируя оптический кабель.
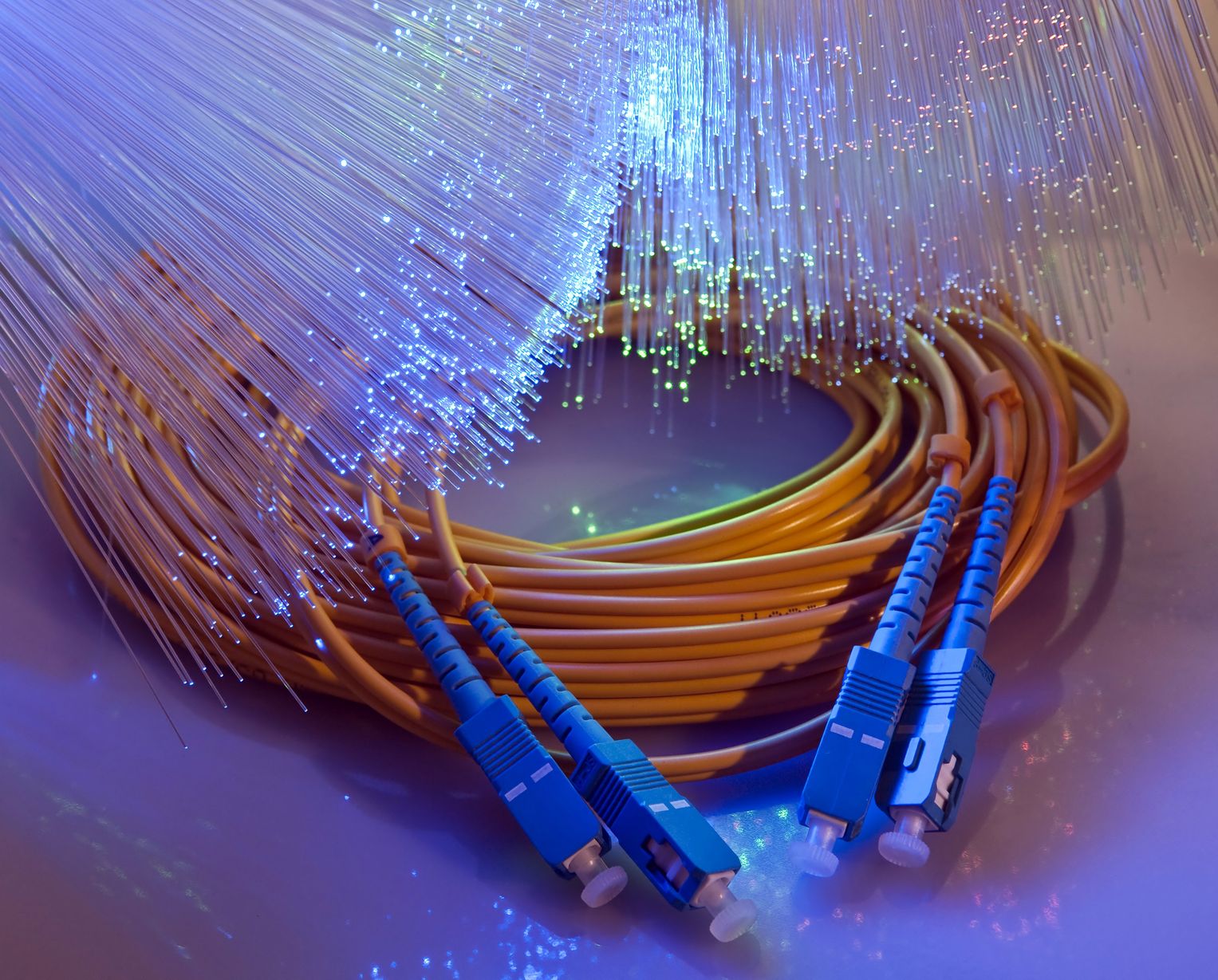
Преимущества оптоволоконной связи перед другими технологиями
Основные преимущества оптоволокна:
- Высокая пропускная способность — до 3000 Мбит/с по одному волокну
- Низкое затухание сигнала — до 100-200 км без регенерации
- Нечувствительность к электромагнитным помехам
- Малый вес и габариты кабеля
- Высокая защищенность от несанкционированного доступа
Благодаря этим свойствам оптоволокно широко используется для построения магистральных линий связи, в том числе трансокеанских.
Типы оптических волокон и их характеристики
Оптические волокна делятся на два основных типа:
- Одномодовые (SM) — с диаметром сердцевины 8-10 мкм, передают один луч света
- Многомодовые (MM) — с диаметром 50-62,5 мкм, передают несколько лучей
Одномодовые волокна обеспечивают передачу на большие расстояния с меньшим затуханием. Многомодовые проще в монтаже, но имеют более высокое затухание. Также волокна различаются по профилю показателя преломления (ступенчатый или градиентный) и другим параметрам.
Процесс сварки оптоволокна и необходимое оборудование
Сварка оптоволокна выполняется в следующей последовательности:
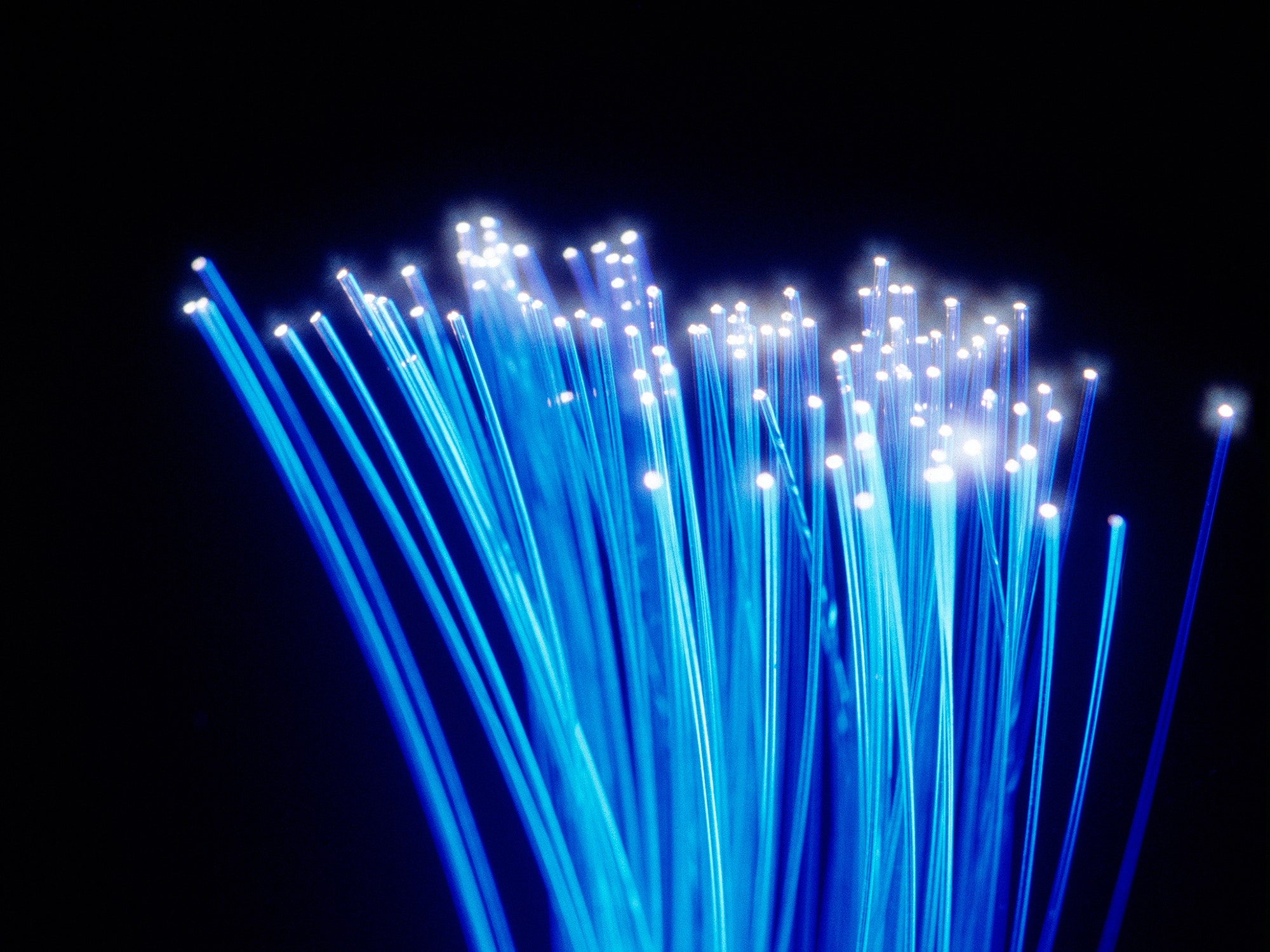
- Подготовка концов волокон — снятие внешних оболочек, очистка от гидрофобного заполнителя
- Скалывание волокон под прямым углом специальным скалывателем
- Установка волокон в сварочный аппарат и юстировка
- Сварка волокон при помощи электрической дуги
- Проверка качества сварного соединения
- Защита места сварки термоусаживаемой гильзой
Для сварки используются специальные сварочные аппараты, которые автоматизируют большую часть процесса. Также необходимы стриппер для снятия изоляции, скалыватель, расходные материалы.
Распространенные ошибки при работе с оптоволокном
Основные ошибки при монтаже оптоволокна:
- Недостаточная очистка волокон от загрязнений
- Неправильный выбор типа волокна для сварки
- Некачественное скалывание концов
- Неправильная юстировка в сварочном аппарате
- Недостаточная защита места сварки
- Превышение допустимого радиуса изгиба волокна
Эти ошибки могут привести к высоким потерям в месте соединения или повреждению волокна. Поэтому важно строго соблюдать технологию монтажа и использовать качественные инструменты.
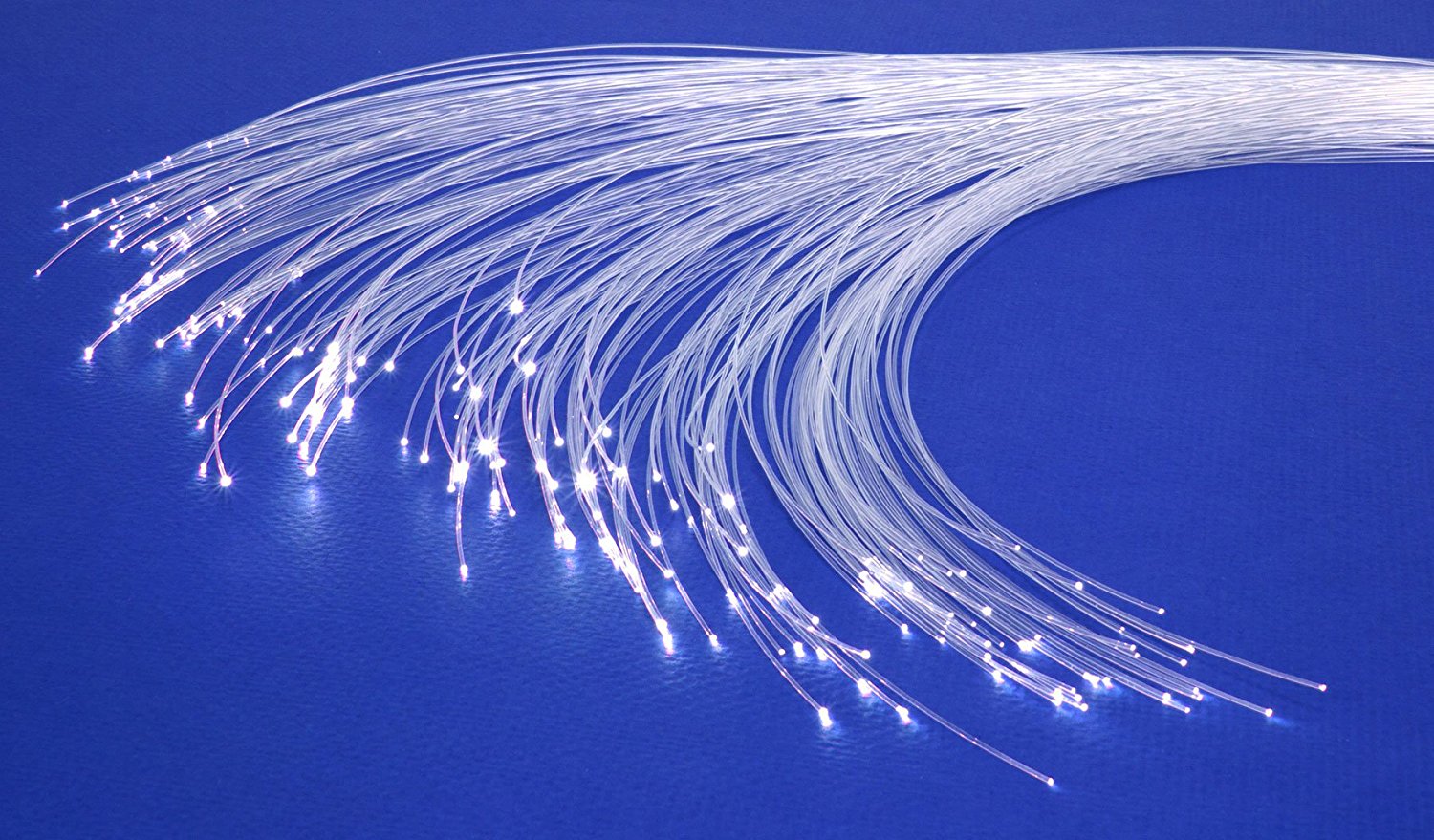
Перспективы развития оптоволоконных технологий
Основные направления совершенствования оптоволоконной связи:
- Увеличение пропускной способности волокон (технологии WDM, SDM)
- Снижение затухания сигнала (волокна с полой сердцевиной)
- Упрощение монтажа и эксплуатации
- Создание полностью оптических сетей без преобразования в электрический сигнал
- Применение в квантовых коммуникациях и вычислениях
Оптоволоконные технологии продолжат играть ключевую роль в развитии телекоммуникаций, обеспечивая растущие потребности в скорости и объемах передачи данных.
Оптическое волокно (оптоволокно)
Волоконно-оптические линии связи (ВОЛС) давно занимают одну из лидирующих позиций на рынке телекоммуникаций. Имея ряд преимуществ перед другими способами передачи информации (витая пара, коаксиальный кабель, беспроводная связь…), ВОЛС широко используются в телекоммуникационных сетях разных уровней, а также в промышленности, энергетике, медицине, системах безопасности, высокопроизводительных вычислительных системах и во многих других областях.
Передача информации в ВОЛС осуществляется по оптическому волокну (optical fiber). Для того чтобы грамотно подойти к вопросу использования ВОЛС, важно хорошо понимать, что из себя представляет оптическое волокно как среда передачи данных, каковы его основные свойства и характеристики, какие бывают разновидности оптических волокон. Именно этим базовым вопросам теории волоконно-оптической связи и посвящена данная статья.
Структура оптического волокна
Оптическое волокно (оптоволокно) – это волновод с круглым поперечным сечением очень малого диаметра (сравним с толщиной человеческого волоса), по которому передается электромагнитное излучение оптического диапазона. Длины волн оптического излучения занимают область электромагнитного спектра от 100 нм до 1 мм, однако в ВОЛС обычно используется ближний инфракрасный (ИК) диапазон (760-1600 нм) и реже – видимый (380-760 нм). Оптическое волокно состоит из сердцевины (ядра) и оптической оболочки, изготовленных из материалов, прозрачных для оптического излучения (рис. 1).
Рис. 1. Конструкция оптического волокна
Свет распространяется по оптоволокну благодаря явлению полного внутреннего отражения. Показатель преломления сердцевины, обычно имеющий величину от 1,4 до 1,5, всегда немного больше, чем показатель преломления оптической оболочки (разница порядка 1%). Поэтому световые волны, распространяющиеся в сердцевине под углом, не превышающим некоторое критическое значение, претерпевают полное внутреннее отражение от оптической оболочки (рис. 2). Это следует из закона преломления Снеллиуса. Путем многократных переотражений от оболочки эти волны распространяются по оптическому волокну.
Рис. 2. Полное внутреннее отражение в оптическом волокне
На первых метрах оптической линии связи часть световых волн гасят друг друга вследствие явления интерференции. Световые волны, которые продолжают распространяться в оптоволокне на значительные расстояния, называются пространственными модами оптического излучения. Понятие моды описывается математически при помощи уравнений Максвелла для электромагнитных волн, однако в случае оптического излучения под модами удобно понимать траектории распространения разрешенных световых волн (обозначены черными линиями на рис. 2). Понятие моды является одним из основных в теории волоконно-оптической связи.
Основные характеристики оптического волокна
Способность оптического волокна передавать информационный сигнал описывается при помощи ряда геометрических и оптических параметров и характеристик, из которых наиболее важными являются затухание и дисперсия.
1.

Помимо соотношения диаметров сердцевины и оболочки, большое значение для процесса передачи сигнала имеют и другие геометрические параметры оптоволокна, например:
- некруглость (эллиптичность) сердцевины и оболочки, определяемая как разность максимального и минимального диаметров сердцевины (оболочки), деленная на номинальный радиус, выражается в процентах;
- неконцентричность сердцевины и оболочки – расстояние между центрами сердцевины и оболочки (рис. 3).
Рис 3. Некруглость и неконцентричность сердцевины и оболочки
Геометрические параметры стандартизированы для разных типов оптического волокна. Благодаря совершенствованию технологии производства значения некруглости и неконцентричности удается свести к минимуму, так что влияние неточности геометрии оптоволокна на его оптические свойства оказывается несущественным.
2. Числовая апертура.

Числовая апертура (NA) – это синус максимального угла падения луча света на торец волокна, при котором выполняется условие полного внутреннего отражения (рис. 4). Этот параметр определяет количество мод, распространяющихся в оптическом волокне. Также величина числовой апертуры влияет на точность, с которой должна производиться стыковка оптических волокон друг с другом и с другими компонентами линии.
Рис 4. Числовая апертура
3. Профиль показателя преломления.
Профиль показателя преломления – это зависимость показателя преломления сердцевины от ее поперечного радиуса. Если показатель преломления остается одинаковым во всех точках поперечного сечения сердцевины, такой профиль называется ступенчатым. Среди других профилей наибольшее распространение получил градиентный профиль, при котором показатель преломления плавно увеличивается от оболочки к оси (рис. 5). Помимо этих двух основных, встречаются и более сложные профили.
Рис. 5. Профили показателя преломления
4. Затухание (потери).
Затухание – это уменьшение мощности оптического излучения по мере распространения по оптическому волокну (измеряется в дБ/км). Затухание возникает вследствие различных физических процессов, происходящих в материале, из которого изготавливается оптоволокно. Основными механизмами возникновения потерь в оптическом волокне являются поглощение и рассеяние.
а) Поглощение. В результате взаимодействия оптического излучения с частицами (атомами, ионами…) материала сердцевины часть оптической мощности выделяется в виде тепла. Различают собственное поглощение, связанное со свойствами самого материала, и примесное поглощение, возникающее из-за взаимодействия световой волны с различными включениями, содержащимися в материале сердцевины (гидроксильные группы OH—, ионы металлов…).
б) Рассеяние света, то есть отклонение от исходной траектории распространения, происходит на различных неоднородностях показателя преломления, геометрические размеры которых меньше или сравнимы с длиной волны излучения. Такие неоднородности являются следствием как наличия дефектов структуры волокна (рассеяние Ми), так и свойствами аморфного (некристаллического) вещества, из которого изготавливается волокно (рэлеевское рассеяние). Рэлеевское рассеяние является фундаментальным свойством материала и определяет нижний предел затухания оптического волокна. Существуют и другие виды рассеяния (Бриллюэна-Мандельштама, Рамана), которые проявляются при уровнях мощности излучения, превышающих те, которые обычно используются в телекоммуникациях.
Величина коэффициента затухания имеют сложную зависимость от длины волны излучения. Пример такой спектральной зависимости приведен на рис. 6. Область длин волн с низким затуханием называется окном прозрачности оптического волокна. Таких окон может быть несколько, и именно на этих длинах волн обычно осуществляется передача информационного сигнала.
Рис. 6. Спектральная зависимость коэффициента затухания
Потери мощности в волокне обуславливаются также различными внешними факторами. Так, механические воздействия (изгибы, растяжения, поперечные нагрузки) могут приводить к нарушению условия полного внутреннего отражения на границе сердцевины и оболочки и выходу части излучения из сердцевины. Определенное влияние на величину затухания оказывают условия окружающей среды (температура, влажность, радиационный фон…).
Поскольку приемник оптического излучения имеет некоторый порог чувствительности (минимальную мощность, которую должен иметь сигнал для корректного приема данных), затухание служит ограничивающим фактором для дальности передачи информации по оптическому волокну.
5.Дисперсионные свойства.
Помимо расстояния, на которое передается излучение по оптическому волокну, важным параметром является скорость передачи информации. Распространяясь по волокну, оптические импульсы уширяются во времени. При высокой частоте следования импульсов на определенном расстоянии от источника излучения может возникнуть ситуация, когда импульсы начнут перекрываться во времени (то есть следующий импульс придет на выход оптического волокна раньше, чем закончится предыдущий). Это явление носит название межсимвольной интерференции (англ. ISI – InterSymbol Interference, см. рис. 7). Приемник обработает полученный сигнал с ошибками.
Рис. 7. Перекрывание импульсов, вызывающее межсимвольную интерференцию: а) входной сигнал; б) сигнал, прошедший некоторое расстояние L1 по оптическому волокну; в) сигнал, прошедший расстояние L2>L1.
Уширение импульса, или дисперсия, обуславливается зависимостью фазовой скорости распространения света от длины волны излучения, а также другими механизмами (табл. 1).
Таблица 1. Виды дисперсии в оптическом волокне.
Название | Краткое описание | Параметр |
1. Хроматическая дисперсия | Любой источник излучает не одну длину волны, а спектр незначительно отличающихся длин волн, которые распространяются с разной скоростью. |
Коэффициент хроматической дисперсии, пс/(нм*км). Может быть положительным (спектральные составляющие с большей длиной волны двигаются быстрее) и отрицательным (наоборот). Существует длина волны с нулевой дисперсией. |
а) Материальная хроматическая дисперсия | Связана со свойствами материала (зависимость показателя преломления от длины волны излучения) | |
б) Волноводная хроматическая дисперсия | Связана с наличием волноводной структуры (профиль показателя преломления) | |
2. Межмодовая дисперсия | Моды распространяются по разным траекториям, поэтому возникает задержка во времени их распространения. |
Ширина полосы пропускания (bandwidth), МГц*км. Эта величина определяет максимальную частоту следования импульсов, при которой не происходит межсимвольной интерференции (сигнал передается без существенных искажений). Пропускная способность канала (Мбит/с) может численно отличаться от ширины полосы пропускания (МГц*км) в зависимости от способа кодирования информации. |
3. Поляризационная модовая дисперсия, PMD | Мода имеет две взаимно перпендикулярные составляющие (поляризационные моды), которые могут распространяться с различными скоростями. |
Коэффициент PMD, пс/√км. Временная задержка из-за PMD, нормируемая на 1 км. |
Таким образом, дисперсия в оптическом волокне отрицательно сказывается как на дальности, так и на скорости передачи информации.
Разновидности и классификация оптических волокон
Рассмотренные свойства являются общими для всех оптических волокон. Однако описанные параметры и характеристики могут существенно отличаться и оказывать различное влияние на процесс передачи информации в зависимости от особенностей производства оптоволокна.
Фундаментальным является деление оптическим волокон по следующим критериям.
- Материал. Основным материалом для изготовления сердцевины и оболочки оптического волокна является кварцевое стекло различного состава. Однако используется большое количество других прозрачных материалов, в частности, полимерные соединения.
- Количество распространяющихся мод. В зависимости от геометрических размеров сердцевины и оболочки и величины показателя преломления в оптическом волокне может распространяться только одна (основная) или же большое количество пространственных мод. Поэтому все оптические волокна делят на два больших класса: одномодовые и многомодовые (рис. 8).
Рис. 8. Многомодовое и одномодовое волокно
На основании этих факторов можно выделить четыре основных класса оптических волокон, получивших распространение в телекоммуникациях:
- Кварцевое многомодовое волокно.
- Кварцевое одномодовое волокно.
- Пластиковое, или полимерное, оптическое волокно (POF).
- Кварцевое волокно с полимерной оболочкой (HCS).
Каждому из этих классов посвящена отдельная статья на нашем сайте. Внутри каждого из этих классов также существует своя классификация.
Производство оптических волокон
Процесс изготовления оптического волокна крайне сложен и требует большой точности. Технологический процесс проходит в два этапа: 1) создание заготовки, представляющей собой стержень из выбранного материала со сформированным профилем показателя преломления, и 2) вытягивание волокна в вытяжной башне, сопровождающееся покрытием защитной оболочкой. Существует большое количество различных технологий создания заготовки оптического волокна, разработка и совершенствование которых происходит постоянно.
Волоконно-оптические кабели
Практическое использование оптического волокна в качестве среды передачи информации невозможно без дополнительного упрочнения и защиты. Волоконно-оптическим кабелем называется конструкция, включающая в себя одно или множество оптических волокон, а также различные защитные покрытия, несущие и упрочняющие элементы, влагозащитные материалы. По причине большого разнообразия областей применения оптоволокна производители выпускают огромное количество самых разных волоконно-оптических кабелей, отличающихся конструкцией, размерами, используемыми материалами и стоимостью (рис. 9).
Рис.9. Волоконно-оптические кабели
Что такое и как работает оптоволокно
Скоростной интернет, цифровое телевидение, мобильная связь возможны благодаря тонким стеклянным нитям, тянущимся по морскому дну между континентами. Если бы не оптоволокно, вы бы вряд ли читали эти строки. Принципиальные основы этой технологии описаны еще в середине XIX века. Тогда в роли проводника сигнала безуспешно пытались использовать воду. Подходящие для реализации смелой идеи материалы были разработаны только через сто с лишним лет.
Проводник для света
В обычном проводе сигнал передается по медной жиле. Информацию переносит поток электронов – электрический ток. Данные передаются зашифрованными в двоичном коде. Если импульс проходит – это обозначает единицу, не проходит – ноль. В оптоволоконной линии связи принцип кодировки тот же, но информацию переносят фотоны или световые волны, точнее, и то, и другое одновременно. Ученые так долго спорили о природе света, что в конце концов объединили несовместимые теории. Но не нужно понимать квантово-волновой дуализм, чтобы разобраться, как свет используют для передачи информации в телекоммуникационных сетях. Достаточно понять, как заставить свет течь по проводам на протяжении километров. Первое, что приходит в голову, – зеркала.
Сделайте металлическую трубку и покройте изнутри гладким слоем, например, из серебра. Свет, попав внутрь с одной стороны, будет отражаться от стенок, пока не достигнет выхода с другой стороны. Неплохая идея, но она не будет работать. Во-первых, изготовление такой трубки нужной длины – чрезвычайно сложная, а значит и дорогая задача. Во-вторых, коэффициент отражения серебра – 99%, то есть попавший в трубку свет будет терять энергию и уже через 100 отражений совершенно погаснет. Гораздо лучше обойтись и без зеркал. Как это сделать, подскажут основы геометрической оптики, заложенные в XIX веке. Основную идею легко продемонстрировать на примере аквариума. Луч света от источника под водой проходит через границу воды и воздуха – двух сред с разными оптическими свойствами – и частично меняет направление движения, а частично отражается от границы двух сред как от зеркала.
Если угол падения луча уменьшать, в определенный момент свет перестанет выходить из воды вовсе и будет отражаться полностью, на 100%. Граница двух сред работает лучше всякого зеркала.
Как выяснилось, чтобы создать такую границу, вода не нужна. Подойдут любые два материала, по-разному пропускающие свет – имеющие разные коэффициенты преломления. Даже разницы в 1% достаточно для создания световода.
Стеклянные провода
В светильниках и игрушках световоды делают из пластмасс, но, чтобы получить пригодное для связи оптоволокно, необходимы более дорогие и более прозрачные материалы. Ученые приспособили для этой цели кварцевое стекло. Сердцевину заготовки для оптоволокна чаще всего делают из чистого диоксида кремния. Внешний слой также создают из кварца, но с примесью бора или германия для снижения коэффициента преломления.
Раньше, чтобы получить такую заготовку, просто вставляли две стеклянные трубки друг в друга, но сегодня чаще поступают иначе. Полые трубки из чистого кварца наполняют смесью газов с высоким содержанием германия и медленно нагревают до тех пор, пока германий не осядет равномерным слоем на внутреннюю поверхность. После того как на кварцевом стекле нарастет достаточно толстый слой оксида германия, трубу нагревают до размягчения и вытягивают до тех пор, пока полость внутри не схлопывается. Так получается стержень диаметром от 1 до 10 сантиметров и длиной приблизительно 1 метр, уже содержащий в сердцевине кварц с добавкой германия, имеющий повышенный показатель преломления и оболочку из чистого кварца вокруг. Такую заготовку доставляют на вершину башни высотой до нескольких десятков метров. Там нижнюю часть заготовки вновь нагревают до полутора тысяч градусов — почти что до точки плавления, и вытягивают из нее тончайшую нить. По пути вниз стекло остывает и окунается в ванну с полимером, который формирует на поверхности кварца защитный слой. Таким методом из одной заготовки получается до 100 км стекловолокна. У основания башни остывшее волокно наматывается на бобину. Да, именно наматывается: как ни странно, кварцевое волокно легко гнется. Получившиеся волокна собираются в пучки по несколько штук и запаиваются в полиэтилен. Затем из этих пучков сплетаются кабели.
В каждом кабеле может быть от двух-трех и до нескольких сотен световодов. Снаружи они для прочности оплетаются полимерной нитью и получают еще одну защитную оболочку из полиэтилена.
Преимущества и недостатки оптоволокна
Все эти сложности оправданы потому, что свет – самое быстрое, что есть во Вселенной. Благодаря этому свойству света оптоволокно обладает непревзойденной информационной емкостью. Витая пара, подобная телефонной линии, или коаксиальный кабель, проводник с экраном, пропускают 100 мегабит в секунду. Самый распространенный для компьютерных сетей восьмижильный кабель из 4 скрученных пар пропускает до 1000 мегабит в секунду. Оптоволокно по одной жиле — в три раза больше, до 3000 мегабит в секунду, а при помощи различных экспериментальных ухищрений можно преодолеть и этот порог. К тому же оптоволокно значительно легче меди. При толщине 9 микрон – тоньше человеческого волоса – нить из кварца длиной 100 км весит около 15 г.
Практически все современные магистральные линии передачи данных проложены из оптоволоконных кабелей. Они связывают континенты, страны и дата-центры. В крупных городах «оптика» используется и при подключении многоквартирных домов к мировой сети, но волокно прокладывается между провайдером и домом, а по квартирам разводится обычная витая пара. При такой схеме подключения максимальная скорость доступа к сети для абонента по-прежнему не превышает 100 Мбит/с. Для сравнения, проведя оптический кабель прямо в квартиру, можно получить канал в 1 Гбит/с, и все же потребитель редко сталкивается с оптоволоконным Интернетом.
Дело не только в том, что оптоволокно дорого в производстве. Проложить кабель – это лишь начало. Сигналы, идущие по линии связи, с расстоянием накапливают ошибки и в конце концов вовсе затухают. У витой пары это происходит через 1 км, у коаксиального кабеля примерно через 5 км. После сигнал приходится восстанавливать и усиливать – регенерировать. У оптоволокна дистанция регенерации в разы больше, но, каким бы чистым ни было кварцевое стекло, в нем остаются примеси, например, миллионные доли процентов воды. Длина волокна может составлять сотни тысяч километров, но через 100–200 км затухание оптического сигнала все же себя проявляет. Поэтому на линиях оптоволоконной связи устанавливаются промежуточные усилители, которые восстанавливают амплитуду оптического сигнала, и регенераторы, удаляющие помехи. Такое оборудование значительно более дорогое, чем усилители на традиционных линиях связи, и требует квалифицированного обслуживания. Но главное, на данный момент гигабитные каналы связи мало востребованы обычными людьми.
Возможно, с появлением умных домов, носимых компьютеров, распространением стриминга видео в сверхвысоком разрешении потребность в них возрастет, но пока скорости, предоставляемой витой парой, среднему потребителю вполне достаточно. Даже не соприкасаясь с этой технологией напрямую, каждый из нас пользуется ее преимуществами. Стабильность подключения, малая задержка прохождения сигнала до самых удаленных серверов и высокая скорость получения ответа от них, возможность снять деньги в любом банкомате и совершить звонок в любую страну мира – все это заслуга оптоволокна, и конкурентов у него нет и в проекте.
Сварка оптоволокна — 15 глупых ошибок. Как правильно паять оптоволоконный кабель.
Оптоволоконный кабель уже давно и прочно вошел в нашу жизнь, постепенно заменяя все остальные марки проводов, широко применяемые ранее в слаботочных сетях и сетях телекоммуникаций.
При этом у всех почему-то крепко засело в головах, что для работы с оптикой требуются какие-то суперпрофессионалы и обучаться той же сварке оптоволокна нужно очень долго и усердно.
Достаточно придерживаться определенных инструкций, не совершать элементарных ошибок и чудо аппарат сделает за вас большую часть работы самостоятельно.
Так ли это на самом деле или нет? Чтобы объективно ответить на данный вопрос, следует сделать важную ремарку – сама сварка это всего лишь 5% от общей работы кабельщика ВОЛС.
Изучив только процесс сварки, без соответствующих знаний чтения схем, постройки магистралей, навыков разделки и укладки кабеля в кассету и кросс, измерения затухания рефлектометром, вы никогда не будете считаться профессионалом своего дела.
Но давайте все-таки подробнее рассмотрим именно процесс сварочных работ, подготовки кабеля к нему и отметим наиболее распространенные ошибки, которые печальным образом сказываются на месте соединения, уровне сигнала и дальнейшей работе ВОЛС.
Типы оптоволоконного кабеля
Сварочные аппараты для оптики работают примерно по одному принципу. Поэтому не будем заострять внимание на какой-то одной модели, старый добрый Фуджикура (Fujikura) или Ilsintech, изучим саму последовательность процесса.
У вас может быть даже модель с управлением от смартфона. Но это в корне не меняет технологию работ. Она везде одинакова.
Итак, изначально мы имеем два отрезка кабеля ВОЛС, с которых нужно снять внешнюю изоляцию.
Снимая внешнюю оболочку, делайте это с таким прицелом, чтобы в дальнейшем у вас не возникло проблем с укладкой волокон и модулей в сплайс-кассете, кроссе или муфте.
Ошибка №1
Если кабель при этом долго лежал под открытым небом (без защитной капы), перед разделкой обязательно отрезается около 1м с каждого конца.
Дело в том, что нити в кабеле как губка всасывают всю окружающую влагу. В итоге оптоволокно мутнеет.
И даже если вы идеально сделаете соединение, это все равно в дальнейшем не спасет вас от больших потерь сигнала.
Включаете аппарат и выставляете на нем тип кабеля, который будет соединяться.
Различают одномодовые (SM) и многомодовые (MM) оптические кабеля.
На одномодовых волокнах в основном используется три длины волны (три окна прозрачности):
Все зависит от общей длины трассы и используемого оборудования. Кроме того, волокна подразделяют на:
- со смещенной дисперизацией — DS
- с ненулевой смещенной дисперизацией — NZ
Внешне их никак не отличить. При сварке чаще всего работают с простыми и со смещенкой. Соединять смещенку и простые волокна не рекомендуется.
Стриппер для снятия изоляции с оптического кабеля
Далее требуется удалить изоляцию с модулей и с отдельных жил. Чаще всего для этого используют специальный ручной инструмент — оптический стриппер.
Хотя в отдельных моделях сварочников можно встретить и встроенный термостриппер. Однако механическим работать гораздо удобнее и быстрее.
Тем более, когда варишь не за удобным столиком, а где-нибудь на высоте или в колодце.
Ошибка №2
Запомните, такой инструмент, по-хорошему, должен иметь заводскую юстировку.
Иначе весь процесс может превратиться не в аккуратное срезание, а в царапанье или грубое сдирание оболочки.
Если лаковое покрытие с волокн не снимается с первого раза и приходится юлозить стриппером туда-сюда, это многое говорит о качестве инструмента.
Сначала изоляция снимается с модулей. Перед этим, салфеткой смоченной в спирте, с них счищается гидрофобное покрытие.
Рекомендуется проделывать это в перчатках. Гидрофоб очень неприятная штука, которая в дальнейшем плохо смывается.
А вам после этого еще работать с тонким оптоволокном и сварочником!
Ошибка №3
Удаляя оболочку с жил, не делайте это так, как показано ниже.
Оптоволокно крепкий материал на разрыв, но не на излом! При разделке в минусовую температуру жила при таком способе запросто может сломаться.
Поэтому изоляцию лучше снимать стриппером, поочередно вытягивая ее с каждой жилки, и только после этого переходить к следующей, избегая резких изгибов и заломов.
После снятия внешней изоляции, с волокна удаляется лаковое покрытие. Оно придает ему одновременно гибкость и жесткость.
Без него волокно становится очень хрупким. Можете без лака на такую жилку положить мобильник и она сломается. А вот с лаком совсем другое дело.
Бывает, что кабель неделями висит только на этих нитках в лаке, когда вся внешняя оболочка уже повреждена. А оптоволокну хоть бы что, держит и ветровые и растягивающие нагрузки.
Ошибка №4
Когда зачищаете волокно от лака, часть его остаётся на стриппере.
Из-за этого можно случайно сломать или поцарапать следующее волокно, что скажется на качестве сварки. Поэтому переходя к зачистке очередной жилы, каждый раз убирайте с лезвий все лишнее.
Ошибка №5
Оптическим стриппером запрещено перекусывать что-либо другое, кроме жил ВОЛС.
Он рассчитан именно на оптоволоконные жилы в 125мкм. Откусите им пластиковую стяжку и можете идти покупать другой инструмент.
Ошибка №6
Также при зачистке следите, чтобы сварочный аппарат был закрыт и туда не попало посторонних обрезков или мусора.
Испытание сварочника Фуджикура в пыльных и влажных условияхКстати, многие сварочники при запылении даже запрещено продувать сжатым воздухом.
В них установлена очень уж чувствительная механика и сильный поток воздуха может нарушить заводские настройки.
Скалыватель оптических волокон
После снятия лакового слоя с волокна, его требуется протереть безворсовой салфеткой, смоченной в спирте.
Ошибка №7
При чистке следующего волокна рекомендуется использовать другую салфетку, ну или по крайней мере ту ее часть, которая не участвовала в предыдущей очистке, либо не контактировала с вашими пальцами.
Если жила идеально чистая, протирая ее салфеткой, вы должны услышать характерный скрипящий звук.
Ошибка №8
С этого момента дотрагиваться до волокна руками или чем-либо другим ни в коем случае нельзя.
Более того, пока вы ее не поместили в сварочный аппарат, на нее даже пылинки не должно осесть. Это все влияет на качество сварки и уровень потерь.
После этого волокно нужно идеально ровно отрезать.
Ошибка №9
Нельзя это делать каким-либо другим инструментом, кроме специального скалывателя.
Хотя в СССР на ранних порах развития оптики, применялся даже вот такой универсальный набор кабельщика ВОЛС.
Срез должен быть очень четким, иметь строго цилиндрическую форму, без каких-либо углов и сколов.
Скалыватель может быть как встроен в сварочный аппарат, так и идти отдельным инструментом. Второй вариант предпочтительнее.
Просто помещаете проводок в скалыватель и закрываете крышечки до щелчка.
Ошибка №10
Внимание – остатки и отрезанные кусочки оптоволокна должны обязательно собираться в отдельный контейнер.
Нельзя чтобы они упали на пол, на стол или попали еще куда-либо. Толщина этих жилок настолько мала, что попав вам под кожу, этот кусочек может проникнуть в вену и начнет свое путешествие по всему организму. Также его можно случайно вдохнуть в легкие.
Все это в конечном итоге приведет к печальным последствиям.
Многие решают проблему сбора обрезков при помощи обычных кусочков изоленты. Дешево и сердито.
Ошибка №11
После скалывания волокно больше нельзя протирать спиртом или касаться им чего-либо.
Даже находиться с ним в пыльных или антисанитарных условиях запрещено. Создайте для этого подходящее рабочее место (палатка, затащите и спрячьте кабель в машину и т.п).
Сварка оптоволокна и уровень затухания сигнала
Подготовленная и зачищенная жила аккуратно вкладывается в посадочное место для сварки, чуть-чуть не доставая своим кончиком середины электрода.
Все те же операции проделываются со вторым концом кабеля.
Ошибка №12
Не забудьте перед этим одеть на второй конец муфточку КДЗС (комплект динамической защиты сварочного соединения), иначе потом будет поздно.
КДЗС — это две термоусадочные трубочки, между которыми располагается стальной штифт.
Волокна должны попасть именно в центральную трубочку, а не между ними.
В противном случае после пайки стальной штифт может его поломать.
Подготовленный второй конец закладывается в сварочник с обратной стороны от первого.
В итоге идеально чистые и ровно срезанные два конца волокна, должны оказаться между двух электродов, которые и будут выполнять сварку.
Если один из концов оказался слишком далеко от электродов и заданного положения, прибор известит вас об этом.
Также высветится ошибка, если волокна будут пересекать друг дружку.
Как только вы закрываете крышку происходит процесс самодиагностики, калибровки и выравнивания двух концов. Все это выводится на экран.
Если все нормально, нажимаете кнопку сварки и она запускается автоматически. Если вдруг один из кончиков оказался срезан недостаточно ровно, система известит вас об этом, не только просигналив об ошибке, но и известив какой конец кабеля виноват.
В данной ситуации процесс зачистки и скалывания повторяется. Со вторым, нормально зачищенным концом ничего делать не нужно.
При успешном завершении сварочного процесса (длится пару секунд), на экран выводятся потери или затухание сигнала в децибелах. Очень хорошим результатом считается 0,01-0,02дб.
Идеал – это соединение вообще без потерь. Бывает и такое.
Хотя даже на заводских пигтейлах (от английского pig tail – поросячий хвостик) встречаются не такие уж идеальные пайки.
При неудовлетворительных результатах сварки, монитор качественных аппаратов проинформирует вас об этом.
Допустимыми значениями затухания считаются следующие параметры:
Ошибка №13
Однако никогда не полагайтесь только на результат показаний сварочного аппарата.
Для конечной проверки результата обязательно требуется рефлектометр. Иначе после окончания всех работ будете задаваться вот такими вот вопросами:
Объясняется это тем, что камера микроскопа сварочника не способна увидеть всю картинку в 360 градусов вокруг волокна. Отсюда и погрешность.
После сварки и открытия крышки аппарат с расчётным усилием пытается развести жилки, как бы растягивая их. Тем самым проводится тест на прочность контакта.
Если сварка выдержала и не порвалась – все ОК. Однако некоторые кабельщики отключают программно такой тест, предполагая, что такое «растягивание» может повредить еще не до конца остывший контакт.
Комплект защиты сварки
После этого оптоволокно аккуратно достается из сварочника. На место сварки надвигается муфточка КДЗС.
Ошибка №14
КДЗС должна полностью покрывать всю длину зачищенного волокна, иначе никакой жесткости не обеспечить.
Остался последний этап работ. Оптоволокно с муфтой помещается в печку, которая обычно расположена в верхней части сварочного прибора.
Выравниваете жилу в этой печке и закрываете крышку. Нажимаете на табло значок печки и ждете некоторое время до появления сигнала.
Далее открыв крышку, достаете ваше оптоволокно. При этом внутри прозрачной муфты не должно быть пузырьков, которые свидетельствуют о наличии воздуха или отдельных деформированных участков (локальный перегрев).
С каждого конца муфты должно показаться и вытечь наружу немного клеящего состава. Все это говорит о хорошей сварке и надежном соединении и изоляции проводов.
При сварке многожильного кабеля все готовые муфты КДЗС обычно укладываются в специальный охлаждающий лоток. Его смысл не просто удобно расположить жилы, дабы они не путались и не мешались, а в равномерном охлаждении гильз.
Некоторые кабельщики делают такие лотки самостоятельно, например из алюминиевых уголков.
При последовательной сварке нескольких жил, не оставляйте надолго муфту в данном отсеке, иначе ее стенки расплавятся и прилипнут к стенкам направляющих элементов.
Ошибка №15
Еще одна ошибка – так называемый “горячий пирожок”.
Это когда еще не совсем остывшую муфту, сразу же из печки перекладывают в ложемент сплайс кассеты оптического кросса. С одной стороны очень удобно, сплавил – вставил, сплавил – вставил. Ничего не запутается и не переплетется с другими жилами.
Однако в этом случае стенки ложемента не дают толком остыть муфточке, мягкие стенки гильзы изгибает, что в итоге деформирует волокно и приводит к потерям.
Как видите, даже при использовании профессионального сварочного оборудования в этом деле имеется огромное количество своих нюансов и тонкостей.
Укладка кабеля в оптический кросс и сплайс кассету
Но на этом процесс вовсе не заканчивается. Когда вы заправляете оптоволоконный кабель в кросс или муфту, учтите еще несколько моментов.
Концы кабеля с необходимым запасом должны быть уложены в кассету. Именно эта работа, а не сама сварка считаются у монтажников более ответственным этапом и требует определенной сноровки и навыков.
Запас модуля в кроссе должен составлять порядка 90см, а запас волокна в кассете 2,5-3 оборота.
Поэтому изначально все вымеряйте и не экономьте на разделке.
Место крепления модуля хомутиками, кабельщики рекомендуют обматывать изолентой. Это снижает нагрузку на модуль и не повредит его острыми стенками хомута. Но и перебарщивать с изолентой не стоит.
При укладке волокон в кассете и самого кабеля в кроссе, нигде не должно образоваться острых углов. Любой острый угол превышающий допустимый радиус изгиба кабеля – это потери и ухудшение сигнала.
Критичный изгиб кабеля может случиться и при его монтаже. Поэтому когда монтажники, заводя оптику в ваш дом или проводя по подъезду, не укладывают ее, а именно “пихают”, ждите беды.
При этом, изгиба в дальнейшем может и не остаться, трасса будет идеально ровной. Однако заломленный кабель при монтаже приводит к трещинам на волокнах.
Со временем затухания будут увеличиваться. Активное оборудование поначалу будет вытягивать полезный сигнал из шумов. Но это до тех пор, пока чувствительность приемника и FEC позволяют.
Кассету после укладки жил закрывают крышкой.
Перед этим обязательно проверьте, не торчат ли где какие проводки. Иначе можете попросту перерубить их этой самой крышкой и весь процесс начнете заново.
Проверка затухания оптическим рефлектометром
Ну и на финальном этапе остается проверить уровень сигнала непосредственно на самом коннекторе. Оптический рефлектометр не только покажет значение в виде цифры, но и проинформирует на каком расстоянии и в какой точке кабеля происходит падение.
Это не обязательно окажется место пайки, вполне возможно, что сигнал будет теряться на каком-нибудь из поворотов трассы.
Подобными сварочными аппаратами легко и удобно варить кабель GPON для подключения одного или нескольких абонентов. А вот если дело коснется 64-х или 96-ти жильной оптики, то конечно данный процесс с поэтапной заправкой каждой жилки будет сплошным мучением.
При этом нужно иметь очень зоркий глаз, дабы не перепутать цветные оттенки многочисленных жилок.
Для опытного кабельщика на фуджике с отдельным скалывателем, технологический процесс сварки 24-х волокон занимает чуть более 40 минут (1,5минуты на жилу). А сборка кросса, со всеми сопутствующими операциями (разделка, укладка, маркировка) – до полутора часов.
Какой вывод можно сделать из всего вышеизложенного? Конечно, сварить оптику на исправном и настроенном оборудовании, стоимостью в несколько сотен тысяч может каждый, у кого руки растут из нужного места.
А вот настроить этот самый сварочник, скалыватель, плюс поддерживать все это в исправном и работоспособном состоянии годами – для этого уже надо быть профессионалом своего дела и любить данную работу.
Статьи по теме
Как делают оптоволокно: фоторепортаж из Саранска | ServerNews
Оригинал | Краткая версия
Поводом для экскурсии по заводу стал выпуск четырёхмиллионного километра оптического волокна. Ускорение производства произошло благодаря обновлению оборудования, средства на которое были получены в том числе от Фонда развития промышленности (ФРП), организовавшего это мероприятие.
История завода
Попытки организовать массовое производство оптоволокна на территории страны предпринимались неоднократно: на рубеже веков дошло даже до закупок оборудования, но дальше дело не двинулось. Саранский завод тоже не сразу строился. Компания «Оптиковолоконные системы» была основана в 2008 году, ещё несколько лет ушло на переговоры относительно инвестиций с Газпромбанком, Роснано и Республикой Мордовия. В 2011 году был подписан договор с финской Nextrom (когда-то бывшей частью Nokia) о поставках оборудования, но только через два года началось строительство завода, который заработал в 2015 году. А первая продукция попала на рынок только в 2016 году. Впоследствии ФРП выдало предприятию заём на модернизацию производства — обновлённые линии как раз и были продемонстрированы в ходе экскурсии.
АО «Оптиковолоконные системы»АО «Оптиковолоконные системы»
Выход первой капли как символ начала работы заводаВыход первой капли как символ начала работы завода
Сейчас на заводе работают около 130 человек. Практически все они местные, за исключением некоторых руководителей. В основном на работу берут выпускников локальных университетов, обучавшихся по техническим специальностям в области физики и химии, — и потом их ещё два месяца доучивают. У многих из них научными руководителями были сотрудники НЦВО РАН и ИХВВ РАН. Впрочем, так было не всегда. Первый состав местных специалистов нужной квалификации пришлось искать с трудом, так как мало кто из них работал по специальности: кто-то занимался починкой компьютеров, кто-то продавал мобильные телефоны в одном из известных салонов связи.
Как бы то ни было, производство работает. Сейчас оно состоит из двух частей: собственно вытяжки волокна и небольшого цеха по изготовлению преформ.
Изготовление преформ
На преформу или, говоря по-русски, заготовку, приходится более половины себестоимости продукции. Именно от неё во многом зависят качество и характеристики будущего оптоволокна. Сейчас заготовки закупаются у японской компании Sumitomo Electric — на данном этапе это экономически выгодно. Переход на полный цикл производства с собственным изготовлением преформ имеет смысл только при отгрузке более 10 млн км волокна ежегодно, тогда как сейчас спрос в России и Белоруссии (они рассматриваются как единый рынок) составляет только 9 млн км в год. Впрочем, про экономику мы ещё поговорим. Сейчас собственное опытное производство заготовок на заводе тоже имеется. Оно нужно для отработки технологического процесса и для изготовления преформ под особые нужды некоторых заказчиков.
Сама преформа — это большой массивный цилиндр из кварцевого стекла. Конусообразный на одном конце и с тонкой «ручкой» на другом. Заготовка состоит из чистого — примесей не более одной частицы на миллиард — кварца с небольшим легированием германием в сердцевине. Это не единственный материал для создания оптоволокна, но самый распространённый. Конкретных способов изготовления тоже несколько. Это, например, спекание кварцевой крупки внутри полой стеклянной тубы или же парофазное осаждение. В последнем случае газовая смесь из тетрахлоридов кремния и германия вкупе с кислородом нагревается, реагирует и осаждается в виде оксидов на небольшую заготовку или на стенки полой трубы. На последнем этапе преформа спекается.
Изготовление преформы методом парофазного осажденияИзготовление преформы методом парофазного осаждения
Тетрахлориды нужной чистоты производятся в Дзержинске и Нижнем Новгороде, но пока в малых объёмах. Для маленьких преформ под спецзаказы на волокна с особыми характеристиками хватает. Другие газы, используемые в производстве — аргон, гелий, азот, углекислый, дейтерий, — закупаются в России. Защитное покрытие заказывается в Голландии, но пробуют и продукцию отечественных заводов. Вся прочая мелочёвка переведена на местное производство. Также на заводе есть опытный участок изготовления тестовых преформ для многомодового оптоволокна методом FCVD.
Под все эти задачи есть отдельная небольшая линия производства, седьмая по счёту. Остальные шесть линий работают с обычными покупными заготовками. На заводе после модернизации используются типовые преформы диаметром 150 мм (возможна модернизация до Ø230 мм) и длиной чуть больше полутора метров, которые позволяют получить около 2000 км волокна. Ранее использовался стандарт 115 мм на 1000 км волокна.
Производство оптоволокна
Если описывать процесс производства совсем уж упрощённо, то он сводится к плавлению заготовки и вытягиванию из неё ниточки. Кажется, что всё довольно просто, но на практике есть масса нюансов.
Общая схема линииОбщая схема линии
ПреформаПреформа
Каждая производственная линия вытянута по вертикали и занимает восемь этажей. На последнем этаже находятся печи. В них и помещается преформа, которая подвешивается за «ручку» и аккуратно центруется, а в процессе её положение дополнительно корректируется. По мере расхода материала заготовка постепенно опускается всё глубже и глубже в печь, хотя заметить это невооружённым глазом затруднительно, так как скорость погружения на полной мощности составляет около одного миллиметра в минуту.
Печь нагрева заготовкиПечь нагрева заготовки
Внутри печи находятся графитовые элементы, повторяющие форму заготовки. Они нагреваются от высокочастотного индуктора и передают тепло преформе в нужных местах, а она, в свою очередь, постепенно плавится. Температура держится около 2000 °C, и лишь во время смены преформы «на горячую» — то есть без полного цикла охлаждения и последующего разогрева длительностью несколько часов — опускается примерно до 1200 °C. Под внешней обшивкой печи проходят трубы охлаждения, по которым постоянно циркулирует вода. Однако находиться около работающей установки даже на расстоянии пары метров уже не очень комфортно — от неё буквально пышет жаром.
Преформа медленно опускается внутрь печиПреформа медленно опускается внутрь печи
Расплавленный кварц тянется вниз и постепенно охлаждаетсяРасплавленный кварц тянется вниз и постепенно охлаждается
Верхняя часть печи закрыта кварцевыми створками, а снизу из неё выходит стеклянная труба, которая заканчивается в дли-и-инном шкафу высотой в несколько этажей. Сделано это не просто так — до определённого момента весь рабочий материал находится в изолированной среде. Внутри печи циркулирует аргон, который защищает нагретый графит от контакта с кислородом воздуха. В самой башне воздух соответствует классу чистоты ИСО 7, а внутри вышеупомянутого шкафа классу ИСО 6.
Герметичный «шкаф» тянется сквозь этажиГерметичный «шкаф» тянется сквозь этажи
На первом этапе после начального разогрева заготовки формируется довольно крупная капля, которая отрезается на уровне 7-го этажа, а оставшийся кончик толщиной 3-4 мм уходит вниз и стягивается, постепенно утончаясь. Больше половины пути будущее волокно, по сути, равномерно остывает. Попутно несколько раз лазерными датчиками измеряется его положение в пространстве, уровень натяжения (по длине стоячей волны) и диаметр. На уровне третьего этажа его температура падает с почти 2000 °C до примерно 350 °C и оно попадает в трубу охлаждения. Труба омывается водой из чиллера, а внутри неё находится гелий, изолированный азотными затворами. На выходе из трубы температура волокна равна примерно 60 °C.
Измерение параметров волокна, таких датчиков на линии несколькоИзмерение параметров волокна, таких датчиков на линии несколько
Полимеризация защитного покрытияПолимеризация защитного покрытия
Последний этап — нанесение полимерного слоя. Волокно проходит через блок цилиндров с фильерами, куда подаётся акрилатное покрытие, предварительно очищенное и разогретое до температуры 55-57 °C: первичное, а сразу за ним и вторичное. Далее оно проходит в азотной среде мимо пяти УФ-ламп для полимеризации покрытия, которое в итоге значительно улучшает механические свойства оптоволокна. «Голое» волокно не получится согнуть с диаметром изгиба менее 10-15 сантиметров, а с покрытием его можно свернуть в колечко радиусом несколько миллиметров.
Протяжный механизмПротяжный механизм
Заправка волокнаЗаправка волокна
В конце концов уже на первом этаже волокно попадает в протяжный механизм, который автоматически регулирует натяжение для сохранения толщины и формы нити в соответствии с данными измерений вышестоящих лазерных датчиков. После этого оно наматывается на катушки, способные вместить до 250 км волокна. Рабочая скорость намотки составляет 1700-1800 метров в минуту. В тестовом режиме одна из линий работает на скорости 2100 м/мин. Её можно разогнать до 2500 м/мин. А вообще это не предел — на зарубежных заводах скорость приближаются к порогу в 3000 м/мин., но там и объёмы другие. Ускорение процесса зависит в первую очередь от эффективности охлаждения и числа УФ-ламп, а также приёмников волокна.
Перетяжка волокна и пруф-тестПеретяжка волокна и пруф-тест
На этом путь оптоволокна вовсе не заканчивается. Впереди ещё перемотка с большой катушки на малые (обычно на них умещается 25-50 км волокна) с дополнительным натяжением и тестированием на дефекты порядка одного микрона. Далее идут тесты, связанные с оптическими и механическими параметрами продукции: длиной волокна в катушке; коэффициентом затухания; диаметром/некруглостью/концентричностью сердцевины, оболочки и обоих слоёв защитного покрытия; длиной волны отсечки; диаметром модового поля; хроматической дисперсией и так далее. Всего тестируется полтора десятка различных параметров.
Тестовые стендыТестовые стенды
Но и это ещё не всё! После всех тестов катушки с волокном на четверо суток отправляются принимать азотно-дейтериевые ванны. Дейтерий образует OD-группы, препятствуя появлению OH-групп. Так что волокно, проще говоря, не мутнеет со временем и сохраняет свои свойства на протяжении 25 лет — именно такую гарантию даёт завод на свою продукцию. Правда, производители кабелей, которые и закупают волокно, дают уже существенно меньший гарантийный срок на изделия — это могут быть и 5 лет.
Дейтерирование волокнаДейтерирование волокна
Продукция
Готовое одномодовое оптоволокно состоит из нескольких частей. В центре находится кварцевая сердцевина диаметром 8-10 мкм, именно она легирована германием. Вокруг неё — кварцевая же оболочка на 125 мкм. Всё это покрыто защитным слоем, так что итоговая толщина составляет 242 мкм. Опционально внешняя оболочка может быть окрашена в разные цвета: предлагается 8 вариантов, в том числе с рисунком. Окрашивание нужно лишь для удобства — при последующей сварке так гораздо проще отличить одно волокно от другого.
Образцы продукции: обычные, окрашенные и тонкие волокнаОбразцы продукции: обычные, окрашенные и тонкие волокна
Сейчас основная продукция завода — это волокна стандарта G.652D и его изгибостойкого варианта G.657A1. Помимо упомянутых выше многомодовых версий и вариантов специального назначения, есть и опытные образцы волокон толщиной 200 мкм (требования к ним те же, что и для 242-мкм). Они актуальны для европейских заказчиков — в Европе в канализации уже просто не хватает места, поэтому большее число волокон при том же сечении кабеля крайне важно.
Основными потребителями оптоволокна являются кабельные заводы, реже — очень крупные телеком-операторы. Сейчас продукция поставляется трём заводам в ЕАЭС и ещё с семью налаживаются отношения, а около четверти продукции экспортируется в Италию, Великобританию, Австрию, Чехию, Польшу, Нидерланды — для европейских стран важна логистика и быстрая доставка, в течение недели. Экспорт идёт и в США, Китай, Пакистан, Индию.
Быть или не быть?
Правда, структура сбыта поменялась — в первые годы упор был на экспорт (98%), сейчас же осваивается отечественный рынок. Связано это с непростой экономикой рынка. Общая мощность производства оптоволокна в мире составляет около 300 млн км в год. Но потребление его неравномерно. В частности, приводятся данные о том, что в России протяжённость оптоволоконных линий связи на душу населения в 4-5 раз меньше, чем в США, Южной Корее и Японии. Ещё один крупный, но непростой регион — Китай. Там, с одной стороны, правительство ещё 15 лет назад ввело заградительные пошлины, а с другой — были масштабные программы по развитию FTTx и 4G-сетей, которые привели к строительству новых заводов и резкому увеличению объёмов производства волокна.
Прямо сейчас наступило затишье перед внедрением 5G, поэтому китайские вендоры готовы продавать волокно даже себе в убыток — по $5/км, тогда как среднерыночная цена составляет $7/км, а в 2017 году она была на уровне $10/км. Такая ситуация, к слову, стала поводом для обращения в ФАС, так как есть опасения, что Corning, крупнейший производитель волокна в мире (60-70% рынка), вынудил кабельные заводы подписать долгосрочные контракты, и поэтому даже сейчас они не берут дешёвое, но достаточно качественное китайское волокно, не говоря уж об российском.
Ситуация осложняется ещё и тем, что, в отличие от кабелей, оптоволокно не является конечным продуктом, а потому под различные льготы и преференции в области импортозамещения не подпадает. К тому же любая перенастройка или обновление линий и материалов приводит к необходимости дополнительных тестов и прохождения сертификации у заказчиков, чего, кстати, с зарубежными поставщиками почему-то не происходит. Есть и другие аспекты.
В целом же руководство завода считает, что выбранный путь развития — постепенное освоение различных этапов полного цикла производства, которое продолжается до сих пор, и (пере)ориентация на нужные рынки — оказался верным. Попутно происходит и постепенная локализация, которая сейчас составляет около 50 %: если уж оборудование нужного класса в России не создаётся, то хотя бы материалы и вспомогательные компоненты вроде тех же катушек уже можно частично получать не у иностранных компаний. И всё же очень странно, конечно, осознавать, что такое предприятие — единственное в России. Хотя, казалось бы…
Понравилась статья? Ставь лайк и подписывайся на наш канал 🙂
Работа с оптоволокном: не так страшно, как кажется
В рубрику «Видеонаблюдение (CCTV)» | К списку рубрик | К списку авторов | К списку публикаций
В прошлом году мы проводили ряд семинаров, посвященных системам передачи информации по оптоволоконному кабелю. Общаясь со слушателями, часто сталкивались с ситуацией, когда люди готовы применять данные системы: у них есть проекты, преимущества решения превалируют над стоимостью — ставь и сдавай проект, получай деньги и уверенность в том, что у заказчика не будет претензий к качеству выполненных работ. Но тот факт, что у специалистов нет никакого опыта работы с подобным оборудованием, их останавливал. Все неоднократно слышали о сложностях, о необходимости высокой квалификации специалистов. Многие считают, что сварка оптоволокна и монтаж оборудования с использованием оптоволоконного кабеля — рискованный процесс, требующий дорогих материалов и высокооплачиваемых сотрудников, что это не для них.
С.А. Карачунский
Руководитель отдела маркетинга компании «В1 электроникс»
На самом деле, работа с оптоволокном хоть и требует определенного опыта и навыков, но их наработать — не такая сложная задача. Тем более что сейчас рынок предлагает большое количество инструментов и оборудования для разделки и монтажа кабеля. Этому вопросу и посвящена данная статья.
Вводная информация
Одно из главных требований при работе с оптоволоконными кабелями — внимательное отношение ко всем этапам процесса монтажа кабельной системы: укладке, разделке, соединению и оконцовке. Ошибка дорогого стоит — это затраты на поиск места повреждения и замена участка кабеля. Замена поврежденного участка не только увеличивает трудозатраты, но и снижает качество всей системы: каждый соединительный элемент, каждая спайка вносит свои искажения в передаваемый сигнал, уменьшает расстояние передачи сигнала, требует увеличения оптического бюджета системы. Для специалистов, которые только начинают свою работу по монтажу оптоволокна, рекомендуется приобрести готовый комплект основных инструментов и материалов, необходимых для проведения работ: тара, дозаторы, распределители, расходные материалы и защитные средства. Спустя некоторое время, когда вы получите начальные навыки работы с оптоволоконным кабелем и сформируете предпочтения в разнообразии используемых инструментов и материалов, вы сможете комбинировать набор «под себя».
Разделка волоконно-оптического кабеля
Волоконно-оптический кабель представляет собой несколько оптических волокон, которые вместе с армирующими нитями заключены в защитную полимерную оболочку. Для защиты от агрессивных внешних воздействий кабель помещают в броневую защиту из гофрированной алюминиевой или стальной защитной ленты либо из стальной проволоки. Из-за того, что оптическое волокно в достаточной степени чувствительно к осевым и радиальным деформациям, для его разрезания непригодны недорогие кабелерезы, которые используются для работы с медными кабелями. Рекомендуется использовать инструмент, лезвия которого рассчитаны на резку стали.
Начальный этап разделки волоконно-оптических кабелей — удаление верхнего слоя защитных и броневых покровов, выполняется теми же инструментами, что и разделка обычных кабелей. Полимерная изоляция и фольга вскрываются резаками, а стальная проволока выкусывается бокорезами. Рекомендуется применять кабельные ножи: они позволяют снимать полимерное покрытия с кабеля диаметром от 4 до 35 мм, и при этом кабельный нож имеет специальную насадку, ограничивающую глубину разреза оболочки, что исключает повреждение оптоволоконных жил.
Но в дальнейшей работе без специальных инструментов все равно не обойтись:
- ножницы или кусачки с керамическими лезвиями — используются для удаления армирующих нитей из кевлара. Обычные ножницы эти тонкие, гибкие и прочные волокна не режут, а выдавливают или гнут;
- стрипперы — предназначены для снятия буферного слоя. Их применение снижает риск повреждения оптического волокна: в первую очередь из-за того, что его рабочие поверхности имеют фиксированную настройку;
- скалыватель оптических волокон — применяется для отсекания лишнего отрезка волокна под углом 90 град. Скалыватели бывают ручные и автоматические. При подготовке оптоволокна для последующей сварки или соединения волокон при помощи сплайса рекомендуется использовать автоматические скалыватели, которые позволяют получить чистый и ровный скол без дефектов под углом 90±0,5 град. Например, скол с углом более 2 град. может привести к увеличению потерь в соединении до 1 дБ, что при оптическом общем бюджете системы в 15-25 дБ — зачастую непозволительная роскошь;
- микроскопы позволяют диагностировать разъемы оптических волокон на качество полировки жилы, наличие трещин, царапин;
- кримперы предназначены для обжимки наконечников, разъемов и контактов.
Способы соединения волоконно-оптического кабеля
Широко применяются три способа монтажа оптоволокна:
- сварка оптических волокон;
- соединение при помощи механических разъемов;
- соединение при помощи сплайса.
Сварка оптических волокон
Осуществляется с помощью специальных сварочных аппаратов и обычно выполняется в три этапа:
- подготовка и зачистка кабеля, получение качественного торца;
- сваривание сварочным аппаратом;
- тестирование и оценка качества соединения. Сварочный аппарат осуществляет соединение оптоволокна с хорошими параметрами места соединения просто и быстро. Современные сварочные аппараты позволяют снизить потери в месте соединения до 0,04 дБ и менее. Аппарат автоматически выполняет все необходимые операции: юстирует оптоволокна, расплавляет концы оптоволокон, сваривает их. Наиболее функциональные (но и, к сожалению, более дорогие) модели также проверяют качество соединения. После чего место сварки защищают, обычно при помощи термоусаживающей трубки.
Соединение при помощи механических разъемов
Сварка оптического волокна также используется при оконцовке волокна коннекторами. Для этих целей используются готовые волоконно-оптические перемычки -пигтейлы (англ. pigtail — гибкий проводник). Пигтейл обычно изготавливается в заводских условиях, он представляет собой отрезок оптоволоконного кабеля, который имеет с одной стороны оптический коннектор. Волокно оптического кабеля сваривается с волокном пигтейла, а уже при помощи коннектора его подключают к оборудованию.
Соединение при помощи сплайса
Сплайс — устройство для сращивания волоконно-оптического кабеля без применения сварки. В сплайс через специальные направляющие навстречу друг другу вводятся подготовленные концы оптических волокон и фиксируются в нем. Для уменьшения вносимых потерь стык между волокнами помещают в специальный (иммерсионный) гель, который зачастую находится внутри сплайса.
Технология соединения при помощи сплайса включает в себя несколько этапов:
- разделка волоконно-оптического кабеля;
- обработка торцов;
- выполнение соединения;
- тестирование и оценка качества соединения;
- нанесение защитных покрытий, восстановление защитной оболочки и брони.
Применение сплайсов облегчает процесс сращивания оптоволокна, но работа с ними требует практических навыков. Вносимые потери при этом методе соединения волокон меньше, чем при использовании пары волоконно-оптических вилок и адаптера, но все же могут составлять 0,1 дБ и выше. Согласно требованиям стандартов на СКС IS0 11801, TIA EIA 568B вносимые потери в сплайсе не должны превышать 0,3 дБ. Для этого в ходе монтажа проводится корректировка положения волокон относительно друг друга, в процессе работ также необходимо проводить постоянный замер потерь на месте соединения.
Кроме того, следует принимать во внимание тот факт, что со временем потери в месте соединения при помощи сплайса могут увеличиться из-за смещения волокон в пространстве или высыхания иммерсионного геля.
Выводы
Материал, который здесь представлен, кому-то может показаться неполным, кому-то поверхностным. Я и не ставил себе задачу изложить всю информацию об инструментах и оборудовании, применяющихся при работе с оптоволокном — да и не уверен, что для этого хватит всего журнала: информации много, она разнообразна.
Но, для того чтобы приступить к работе, вполне достаточно начальных знаний и навыков. Читайте, спрашивайте, приходите на семинары и тренинги — поставщики оборудования должны быть сами заинтересованы в повышении вашей грамотности. Не боги горшки обжигали — и у нас все получится.
Опубликовано: Журнал «Системы безопасности» #2, 2010
Посещений: 36324
В рубрику «Видеонаблюдение (CCTV)» | К списку рубрик | К списку авторов | К списку публикаций
Оптоволоконные кабели связи. Как это делается / Хабр
В нескольких своих
постах, опубликованных более года назад, я поднял такую интересную для многих и чем-то захватывающую тему, как магистральные оптоволоконные кабели связи, в частности, тему «подводной» оптики. Информация в данных публикациях была неполной, торопливой и разрозненной, так как статьи писались «на коленке» во время обеденного перерыва. Сейчас я бы хотел поделиться структурированным и, насколько это возможно, полным материалом по теме оптики, с максимумом вкусных подробностей и гик-порно, от которых на душе любого технаря станет тепло.
Внутри схемы, гифки, таблицы и много интересного текста.
Вы готовы?
Условная классификация
В отличие от всем нам знакомой витой пары, которая вне зависимости от места применения имеет примерно одну и ту же конструкцию, оптоволоконные кабели связи могут иметь значительные отличия исходя из сферы применения и места укладки.
Можно выделить следующие основные виды оптоволоконных кабелей для передачи данных исходя из области применения:
- Для прокладки внутри зданий;
- для кабельной канализации небронированный;
- для кабельной канализации бронированный;
- для укладки в грунт;
- подвесной самонесущий;
- с тросом;
- подводный.
Наиболее простой конструкцией обладают кабели для прокладки внутри зданий и канализационный небронированный, а самыми сложными — для прокладки в землю и подводные.
Кабель для прокладки внутри зданий
Оптические кабели для прокладки внутри зданий разделяют на распределительные, из которых формируется сеть в целом, и абонентские, которые используются непосредственно для прокладки по помещению к конечному потребителю. Как и витую пару, прокладывают оптику в кабельных лотках, кабель-каналах, а некоторые марки могут быть протянуты и по внешним фасадам зданий. Обычно такой кабель заводят до межэтажной распределительной коробки или непосредственно до места подключения абонента.
Конструкция оптоволоконных кабелей для прокладки в зданиях включает в себя оптическое волокно, защитное покрытие и центральный силовой элемент, например, пучок арамидных нитей. К оптике, прокладываемой в помещениях, есть особые требования по противопожарной безопасности, такие как нераспространение горения и низкое дымовыделение, поэтому в качестве оболочки для них используется не полиэтилен, а полиуретан. Другие требования — это низкая масса кабеля, гибкость и небольшой размер. По этой причине многие модели имеют облегченную конструкцию, иногда с дополнительной защитой от влаги. Так как протяженность оптики внутри зданий обычно невелика, то и затухание сигнала незначительно и влияние на передачу данных оно не оказывает. Число оптических волокон в таких кабелях не превышает двенадцати.
Также существует и своеобразная помесь «бульдога с носорогом» — оптоволоконный кабель, который содержит в себе, дополнительно, еще и витую пару.
Небронированный канализационный кабель
Небронированная оптика используется для укладки в канализации, при условии, что на нее не будет внешних механических воздействий. Также подобный кабель прокладывается в тоннелях, коллекторах и зданиях. Но даже в случаях отсутствия внешнего воздействия на кабель в канализации, его могут укладывать в защитные полиэтиленовые трубы, а монтаж производится либо вручную, либо при помощи специальной лебедки. Характерной особенностью данного типа оптоволоконного кабеля можно назвать наличие гидрофобного наполнителя (компаунда), который гарантирует возможность эксплуатации в условиях канализации и дает некоторую защиту от влаги.
Бронированный канализационный кабель
Бронированные оптоволоконные кабели используются при наличии больших внешних нагрузок, в особенности, на растяжение. Бронирование может быть различным, ленточным или проволочным, последнее подразделяется на одно- и двухповивное. Кабели с ленточным бронированием используются в менее агрессивных условиях, например, при прокладке в кабельной канализации, трубах, тоннелях, на мостах. Ленточное бронирование представляет собой стальную гладкую или гофрированную трубку толщиной в 0,15-0,25 мм. Гофрирование, при условии, что это единственный слой защиты кабеля, является предпочтительным, так как оберегает оптоволокно от грызунов и в целом повышает гибкость кабеля. При более суровых условиях эксплуатации, например, при закладке в грунт или на дно рек используются кабели с проволочной броней.
Кабель для укладки в грунт
Для прокладки в грунт используют оптические кабели с проволочной одноповивной или двухповивиной броней. Также применяются и усиленные кабели с ленточным бронированием, но значительно реже. Прокладка оптического кабеля осуществляется в траншею или с помощью кабелеукладчиков. Более подробно этот процесс расписан в моей второй статье по этой теме, где приводятся примеры наиболее распространенных видов кабелеукладчиков. Если температура окружающей среды ниже отметки в -10 оС, кабель предварительно прогревают.
В условиях влажного грунта используется модель кабеля, оптоволоконная часть которого заключена в герметичную металлическую трубку, а бронеповивы проволоки пропитаны специальным водоотталкивающим компаундом. Тут же в дело вступают расчеты: инженеры, работающие на укладке кабеля, не должны допускать превышения растягивающих и сдавливающих нагрузок сверх допустимых. В противном случае, сразу или со временем, могут быть повреждены оптические волокна, что приведет кабель в негодность.
Броня влияет и на значение допустимого усилия на растяжение. Оптоволоконные кабели с двухповивной броней могут выдержать усилие от 80 кН, одноповивные — от 7 до 20 кН, а ленточная броня гарантирует «выживание» кабеля при нагрузке не менее 2,7 кН.
Подвесной самонесущий кабель
Подвесные самонесущие кабели монтируются на уже существующих опорах воздушных линий связи и высоковольтных ЛЭП. Это технологически проще, чем прокладка кабеля в грунт, но при монтаже существует серьезное ограничение — температура окружающей среды во время работ не должна быть ниже — 15 оС. Подвесные самонесущие кабели имеют стандартную круглую форму, благодаря которой снижаются ветровые нагрузки на конструкцию, а расстояние пролета между опорами может достигать ста и более метров. В конструкции самонесущих подвесных оптических кабелей обязательно присутствует ЦСЭ — центральный силовой элемент, изготовленный из стеклопластика или арамидных нитей. Благодаря последним оптоволоконный кабель выдерживает высокие продольные нагрузки. Подвесные самонесущие кабели с арамидным нитями используют в пролетах до одного километра. Еще одно преимущество арамидных нитей, кроме их прочности и малом весе, заключается в том, что арамид по природе своей является диэлектриком, то есть кабели, изготовленные на его основе безопасны, например, при попадании молнии.
В зависимости от строения сердечника различают несколько типов подвесного кабеля:
- Кабель с профилированным сердечником — содержит оптические волокна или модули с этими волокнами – кабель устойчив к растяжению и сдавливанию;
- Кабель со скрученными модулями — содержит оптические волокна, свободно уложенные, кабель устойчив к растяжениям;
- Кабель с одним оптическим модулем – сердечник данного типа кабеля не имеет силовых элементов, поскольку они находятся в оболочке. Такие кабели обладают недостатком, связанным с неудобством идентификации волокон. Тем не менее, они обладают меньшим диаметром и более доступной ценой.
Оптический кабель с тросом
Оптические кабеля с тросом — это разновидность самонесущих кабелей, которые также используются для воздушной прокладки. В таком изделии трос может быть несущим и навивным. Еще существуют модели, в которых оптика встроена в грозозащитный трос.
Усиление оптического кабеля тросом (профилированным сердечником) считается достаточно эффективным методом. Сам трос представляет собой стальную проволоку, заключенную в отдельную оболочку, которая в свою очередь соединяется с оболочкой кабеля. Свободное пространство между ними заполняется гидрофобным заполнителем. Часто такую конструкцию оптического кабеля с тросом называют «восьмеркой» из-за внешнего сходства, хотя лично у меня возникают ассоциации с перекормленной «лапшой». «Восьмерки» применяют для прокладки воздушных линий связи с пролетом не более 50-70 метров. В эксплуатации подобных кабелей есть некоторые ограничения, например, «восьмерку» со стальным тросом нельзя подвешивать на ЛЭП. Надеюсь, объяснять, почему именно, не нужно.
Но кабели с навивным грозозащитным тросом (грозотросом) спокойно монтируются на высоковольтных ЛЭП, крепясь при этом к проводу заземления. Грозотросный кабель используется в местах, где есть риски повреждения оптики дикими животными или охотниками. Также его можно использовать на больших по дистанции пролетах, чем обычную «восьмерку».
Подводный оптический кабель
Данный тип оптических кабелей стоит в сторонке от всех остальных, так как прокладывается в принципиально иных условиях. Почти все типы подводных кабелей, так или иначе, бронированы, а степень бронирования уже зависит от рельефа дна и глубины залегания.
Различают следующие основные типы подводных кабелей (по типу бронирования):
- Не бронирован;
- Одинарное (одноповивное) бронирование;
- Усиленное (одноповивное) бронирование;
- Усиленное скальное (двухповивное) бронирование;
Подробно конструкцию подводного кабеля я рассматривал больше года назад вот в этой статье, поэтому тут приведу только краткую информацию с рисунком:
Как не парадоксально, прямой корреляции бронирования кабеля с глубиной залегания нет, так как армирование защищает оптику не от высоких давлений на глубине, а от деятельности морских обитателей, а также сетей, тралов и якорей рыболовецких судов. Корреляция эта, скорее, обратная — чем ближе к поверхности, тем больше тревог, что явно видно по таблице ниже:
Таблица типов и характеристик подводных кабелей в зависимости от глубины укладки
Производство
Теперь, когда мы познакомились с наиболее распространенными видами оптоволоконных кабелей, можно проговорить и о производственном процессе всего этого зоопарка. Все мы знаем об оптоволоконных кабелях, многие из нас имели с ними дело лично (как абоненты и как монтажники), но как становится ясно из информации выше, оптоволоконные, в особенности магистральные, кабели могут серьезно отличаться от того, с чем вы имели дело в помещении.
Так как для прокладки оптоволоконной магистрали требуются тысячи километров кабеля, их производством занимаются целые заводы.
Изготовление оптоволоконной нити
Все начинается с производства главного элемента — оптоволоконной нити. Производят это чудо на специализированных предприятиях. Одной из технологий производства оптической нити является ее вертикальная вытяжка. А происходит это следующим образом:
- На высоте в несколько десятков метров в специальной шахте устанавливается два резервуара: один со стеклом, второй, ниже по шахте, со специальным полимерным материалом первичного покрытия.
- Из узла прецизионной подачи заготовки или, проще говоря, первого резервуара с жидким стеклом, вытягивается стеклянная нить.
- Ниже нить проходит через датчик диаметра волоконного световода, который отвечает за контроль диаметра изделия.
- После контроля качества нить обволакивается первичным полимерным покрытием из второго резервуара.
- Пройдя процедуру покрытия, нить отправляется в еще одну печь, в которой полимер закрепляется.
- Нить оптоволокна протягивается еще N-метров, в зависимости от технологии, охлаждается и поступает на прецизионный намотчик, проще говоря, наматывается на бобину, которая уже и транспортируется как заготовка к месту производства кабеля.
Наиболее распространены следующие размеры оптоволоконного кабеля:
- C сердечником 8,3 мк и оболочкой 125 мкм;
- C сердечником 62,5 мк и оболочкой 125 мкм;
- C сердечником 50 мк и оболочкой 125 мкм;
- C сердечником 100 мк и оболочкой 145 мкм.
Оптику с диаметром сердечника в 8,3 мк качественно спаять в полевых условиях, без высокоточного оборудования или установки концентраторов, непросто или практически невозможно.
Огромное значение имеет контроль диаметра световода. Именно эта часть установки отвечает за один из главных параметров на всех этапах производства нити — неизменность диаметра конечного изделия (стандарт — 125 мкм). Из-за сложностей при сварке нитей любых диаметров, их стремятся сделать настолько длинными, насколько это возможно. Погонный метраж оптоволоконной «заготовки» на бобине может достигать десятков километров (да, именно километров) и более, в зависимости от требований заказчика.
Уже на самом предприятии, хотя это можно сделать и на стекольном заводе, все зависит от производственного цикла, бесцветную нить с полимерным покрытием для удобства могут перемотать на другую бобину, в процессе окрашивая ее в собственный яркий цвет, по аналогии со всем знакомой витой парой. Зачем? Во славу сата.. для быстрого различения каналов при, например, ремонте или сварке кабеля.
Изготовление кабеля
Теперь мы получили сердце нашего изделия — оптоволоконную нить. Что дальше? Дальше давайте посмотрим на схему такого себе среднестатистического подводного (да, мне они нравятся больше всего) кабеля в разрезе:
На заводе полученные оптические нити запускаются в станки, в совокупности своей образующие целый конвейер по производству какого-то одного типа кабеля. На первом этапе производства небронированных моделей, нити сплетаются в пучки, которые и составляют, в итоге, «оптический сердечник». Количество нитей в кабеле может быть различным, в зависимости от заявленной пропускной способности. Пучки, в свою очередь, сматывают в «тросс» на специальном оборудовании, которое, в зависимости от своей конструкции и назначения. Это оборудование может еще и покрывать полученный «тросс» гидроизолирующим материалом, чтобы предотвратить попадание влаги и потускнения оптики в будущем (на схеме обозван «внутримодульным гидрофобным заполнителем»).
Вот так проходит процесс скрутки собранных вместе пучков в трос на пермском заводе оптоволоконных кабелей:
После того, как в «тросс» было собрано необходимое количество пучков оптоволокна, их заливают полимером или укладывают в металлическую или медную трубку. Тут, на первый взгляд, кажется, что подводных камней нет и быть не может, но так как производитель стремится минимизировать количество соединений и швов, то все получается не совсем просто. Рассмотрим один конкретный пример.
Для создания трубки-корпуса, представленной на схеме выше как «центральная трубка», может использоваться огромная по длине лента из необходимого нам материала (сталь, либо же медь). Лента используется, чтобы не маяться со всем знакомым нам и очевидным прокатом, и сваркой по всей окружности стыка. Согласитесь, тогда у кабеля было бы слишком много «слабых» мест в конструкции.
Так вот. Металлическая ленточная заготовка проходит через специальный станок, натягивающий ее и имеющий с десяток-другой валиков, которые идеально ее выравнивают. После того, как лента выровнена, она подается на другой станок, где встречается с нашим пучком оптоволоконных нитей. Автомат на конвейере загибает ленту вокруг натянутого оптоволокна, создавая идеальную по форме трубку.
Вся эта, пока еще хрупкая, конструкция протягивается по конвейеру дальше, к электросварочному аппарату высокой точности, который на огромной скорости проводит сварку краев ленты, превращая ее в монолитную трубку, в которую уже заложен оптоволоконный кабель. В зависимости от тех. процесса, все это дело может заливаться гидрофобным заполнителем. Или не заливаться, тут уже все зависит от модели кабеля.
В целом, с производством все стало более-менее понятно. Различные марки оптоволоконного, в первую очередь, магистрального кабеля, могут иметь некоторые конструкционные отличия, например, по количеству жил. Тут инженеры не стали выдумывать велосипед и просто объединяют несколько кабелей поменьше в один большой, то есть такой магистральный кабель будет иметь не один, а, например, пять трубок с оптоволокном внутри, которые, в свою очередь, все также заливаются полиэтиленовой изоляцией и, при необходимости, армируются. Такие кабели называют многомодульными.
Одна из моделей многомодульного кабеля в разрезе
Многомодульные кабели, которые, в основной своей массе, и используются для протяженных магистралей, имеют еще одну обязательную конструктивную особенность в виде сердечника, или как его еще называют — центрального силового элемента. ЦСЭ используется как «каркас», вокруг которого группируют трубки с жилами оптоволокна.
К слову, пермский завод «Инкаб», производственный процесс которого представлен на гифках выше, со своими объемами до 4,5 тыс. километров кабеля в год — карлик, по сравнению с заводом того же инфраструктурного гиганта Alcatel, который может выдавать несколько тысяч километров оптоволоконного кабеля одним куском, который сразу же грузится на судно-кабелеукладчик.
Стальная трубка — это наименее радикальный вариант бронирования оптики. Для неагрессивных условий эксплуатации и монтажа часто применяют обычный изолирующий полиэтилен. Однако, это не отменяет того факта, что после изготовления такого кабеля его могут «обернуть» в бронирующую намотку из алюминиевой или стальной проволоки или тросов.
Бронирование кабеля с полиэтиленовой изоляцией на том же пермском заводе
Вывод
Как можно понять из материала выше, основным отличие различных видов оптоволоконного кабеля является их «обмотка», то есть то, во что упаковываются хрупкие стеклянные нити в зависимости от области применения и среды, в которой будет проводиться кабелеукладка.
Если вам понравился данный материал, то можете смело задавать вопросы в комментариях, опираясь на которые я постараюсь подготовить еще статью по этой теме.
Спасибо за внимание.
возможные проблемы и способы их решения
- Главная
- Соединение оптоволокна: возможные проблемы и способы их решения
Оптоволоконные линии связи являются основой современных коммуникаций и широко используются, как на объектах критической инфраструктуры, так и в обычных локальных вычислительных сетях. Постоянно возникает необходимость подключения или соединения двух оптических кабелей. Это кропотливая работа, требующая опыта и строгого соблюдения процедур. Ошибки на определенном этапе соединения оптоволокна приводят к подавляющему большинству неисправностей в линиях оптической передачи данных.
Микроскопическая причина больших проблем
Статистические исследования из разных источников показывают, что около 85% локальных неисправностей оптоволоконных кабелей связаны с тем, что при соединении оптоволокно не было качественно очищено. Частицы мусора, царапины, сколы и полости приводят к изменению показателя преломления, обратному рассеянию или «утечке» фотонов в воздух. Это три самые распространенные причины, вызывающие ухудшение качества сигнала. Всего лишь микронная частица мусора приводит к потере 1% света, или 0,05 Дб. Крохотное пятнышко в 10 микрон способно полностью блокировать сердцевину оптоволоконной нити.
Поврежденное, чистое, грязное и восстановленное оптоволокно
Вне зависимости от того, производится соединение коннектором, сваркой, склеиванием или механическим способом, необходимо ответственно подходить к очистке оптоволокна. Нужно не только следовать процедурам, описанным в руководствах, но и учесть ряд неочевидных факторов.
Эксперты одного из ведущих мировых производителей инструментов Hobbes считают, что необходимо всегда проверять чистоту волоконно-оптических соединений. Они подготовили несколько рекомендаций для специалистов, работающих с оптическим кабелем.
Подготовка к соединению оптоволокна
На первый взгляд кажется, что перед соединением оптоволокна необходимо всегда проводить очистку волокна и каждого коннектора. Это является самым распространенным заблуждением. Качественные коннекторы имеют идеально чистую поверхность, и лишняя чистка, наоборот, повышает вероятность того, что они будут загрязнены.
Поэтому важно помнить, что чистоту оптоволокна необходимо всегда проверять, но не всегда нужно проводить очистку. Кроме того, оптические контакты имеют закругленную форму, которая помогает вытолкнуть крупные частицы. Они вряд ли останутся в центре соединения, а по краям будут задерживать лишь незначительную часть света.
Соединение слева чистое, справа — загрязненное водой, отпечатками пальцев и пылью
В центральных участках оптоволокна загрязнение недопустимо. Есть несколько зон, у которых разные требования к степени чистоты.
Схематическое изображение среза оптоволокна
В зоне А не должно быть никаких царапин и выемок — эта зона требует особо тщательной проверки. В зонах В и С допустимы небольшие царапины и каверны, но грязи быть не должно. В зоне D незначительное загрязнение не приведет к неисправности соединения, но проверять ее все равно необходимо, так как это зона напряжения в месте соединения.
Таким образом, несмотря на проверку оптоволокна интерферометром на производстве, все равно перед соединением оптоволокна необходимо проводить визуальный осмотр непосредственно на месте установки и при необходимости чистить оптоволокно. Для этого применяются специальные инструменты и наборы.
Контроль чистоты поверхности в оптическом кабеле
Одним из наиболее удобных и надежных инструментов для осмотра торца волокна или коннекторов — это специальные микроскопы, которые позволяют осмотреть срез оптоволокна и выявить проблему. Современные видеомикроскопы, такие как Greenlee GVIS300C-PM-02-V, имеют функцию автоматического анализа и могут выполнять несколько задач, например, измерять мощность и затухание сигнала, выявлять повреждения оптоволокна, анализировать качество оптических соединений. Собранные сведения можно немедленно отправить в базу данных через Wi-Fi.
Прибор Greenlee GVIS300C-PM-02-V и примеры визуализации проблем на оптоволоконных коннекторах
Для быстрой оценки чистоты оптоволокна есть более простые узкофункциональные ручные микроскопы, например Fluke Networks FiberViewer с увеличением 200 или 400 крат.
Микроскоп для контроля чистоты коннектора Fluke Networks FiberViewer FT120 (200x)
Приборы для проверки оптоволокна являются частью качественных наборов для монтажа и обслуживания оптоволоконных сетей. Необходимый набор выбирается в зависимости от сложности решаемых задач, но преимущество наборов в любом случае — это наличие приспособлений для чистки и исправления дефектов. Набор позволяет выявить и сразу решить проблему.
Инструменты для монтажа и обслуживания волоконно-оптического кабеля. Слева — набор Jensen GoKit Deluxe с микроскопом 100x. Справа — полный профессиональный набор SK-PON-KIT с видеомикроскопом и сварочным аппаратом для оптоволокна
Очистка оптических компонентов
Все поставщики качественных оптических компонентов и систем предоставляют соответствующие инструкции по чистке своих изделий. Эти рекомендации являются оптимальными, поскольку учитывают свойства материалов и конструктивные особенности.
В большинстве наборов для монтажа волоконно-оптических кабелей, соединителей и коннекторов есть приспособления и материалы для чистки.
Существует два основных компонента для качественной очистки: специальные салфетки и прочие материалы для протирания, а также специальные растворы для удаления загрязнений.
Раствор смывает пятна и микрочастицы, при этом он не оставляет пятен после высыхания и играет роль смазки, предотвращая появление царапин при чистке салфетками. Следует иметь в виду, что в случае сильного загрязнения очистку следует повторить.
Чистота — залог надежности
Качественно выполненная процедура очистки значительно повышает надежность работы оптоволоконных сетей. Использование эффективных приборов для визуализации и приспособлений для очистки может окупиться мгновенно — за счет первого же предотвращенного незапланированного простоя дорогостоящего оборудования.
Смотрите также:
Как производятся оптические волокна? — Как работает волоконная оптика
Теперь, когда мы знаем, как работают волоконно-оптические системы и почему они полезны — как они их делают? Оптические волокна изготовлены из особо чистого оптического стекла . Мы думаем о стеклянном окне как о прозрачном, но чем толще становится стекло, тем менее прозрачным оно становится из-за примесей в стекле. Однако стекло в оптическом волокне содержит гораздо меньше примесей, чем оконное стекло. Одна компания описывает качество стекла следующим образом: если бы вы были на вершине океана, покрытого стекловолокном с твердой сердцевиной, вы могли бы ясно видеть дно.
Изготовление оптических волокон требует следующих шагов:
- Изготовление стеклянного цилиндра преформы
- Вытягивание волокон из преформы
- Тестирование волокон
Изготовление заготовки преформы
Стекло для Преформа изготавливается с помощью процесса, называемого модифицированным химическим осаждением из паровой фазы (MCVD).
В MCVD кислород барботируется через растворы хлорида кремния (SiCl4), хлорида германия (GeCl4) и / или других химикатов.От точной смеси зависят различные физические и оптические свойства (показатель преломления, коэффициент расширения, температура плавления и т. Д.). Затем пары газа направляются внутрь трубы из синтетического диоксида кремния или из кварца (оболочка) в специальном токарном станке . Когда токарный станок вращается, резак перемещается вверх и вниз по внешней стороне трубы. Сильный жар от горелки вызывает две вещи:
- Кремний и германий вступают в реакцию с кислородом, образуя диоксид кремния (SiO2) и диоксид германия (GeO2).
- Диоксид кремния и диоксид германия осаждаются на внутренней части трубки и сливаются вместе, образуя стекло.
Токарный станок непрерывно вращается, обеспечивая равномерное покрытие и однородную заготовку. Чистота стекла поддерживается за счет использования коррозионно-стойкого пластика в системе подачи газа (клапанные блоки, трубы, уплотнения) и за счет точного контроля потока и состава смеси. Процесс изготовления заготовки преформы автоматизирован и занимает несколько часов.После охлаждения заготовки преформы ее проверяют на качество (показатель преломления).
Вытяжка волокон из заготовки преформы
После тестирования заготовки преформы ее загружают в башню для вытягивания волокна .
Заготовку опускают в графитовую печь (от 3452 до 3992 градусов по Фаренгейту или от 1900 до 2200 градусов по Цельсию), и наконечник расплавляется до тех пор, пока расплавленный шарик не падает под действием силы тяжести. При падении охлаждается и образует нить.
Оператор продевает прядь через серию стаканов для нанесения покрытий (буферных покрытий) и печи для отверждения в ультрафиолетовом свете на катушку, управляемую трактором.Механизм трактора медленно вытягивает волокно из нагретой заготовки преформы и точно контролируется с помощью лазерного микрометра для измерения диаметра волокна и передачи информации обратно в механизм трактора. Волокна вытягиваются из заготовки со скоростью от 33 до 66 футов / с (от 10 до 20 м / с), и готовый продукт наматывается на катушку. Катушки нередко содержат оптоволокно длиной более 1,4 мили (2,2 км).
Испытание готового оптического волокна
Готовое оптическое волокно испытывают на следующие характеристики:
- Предел прочности на разрыв — Должен выдерживать 100000 фунтов / дюйм 2 или более
- Профиль показателя преломления — Определите числовую апертуру как а также экран для оптических дефектов
- Геометрия волокна — Диаметр сердцевины, размеры оболочки и диаметр покрытия одинаковы
- Затухание — Определить степень ухудшения световых сигналов с различной длиной волны на расстоянии
- Пропускная способность информации (полоса пропускания) — Количество сигналов, которые могут передаваться за один раз (многомодовые волокна)
- Хроматическая дисперсия — Распространение различных длин волн света через сердцевину (важно для полосы пропускания)
- Диапазон рабочих температур / влажности
- Температура зависимость затухания
- Способность к проводить свет под водой — Важно для подводных кабелей
После того, как волокна прошли контроль качества, они продаются телефонным компаниям, компаниям кабельного телевидения и поставщикам сетей.Многие компании в настоящее время заменяют свои старые системы на основе медных проводов новыми системами на основе оптоволокна, чтобы повысить скорость, емкость и четкость.
Блог: Как делают оптоволокно
Многие люди спрашивают, как делают оптоволокно. Нельзя просто использовать «обычное» стекло. Если бы вы сделали оптическое волокно из обычного оконного стекла, свету, который вы через него светите, было бы трудно преодолеть расстояние более нескольких километров, не говоря уже о расстояниях, необходимых для передачи на большие расстояния.Это потому, что обычное стекло содержит искажения, обесцвечивание и другие загрязнения, которые быстро поглощают, отражают или иным образом рассеивают свет задолго до того, как оно сможет пройти какое-либо большое расстояние.
Ознакомьтесь с преимуществами процесса Corning от компании Corning
Напротив, поскольку оптическое волокно на самом деле сделано из очень чистого стекла, свет проходит на большие расстояния, в основном без примесей и искажений.
Волоконно-оптический кабель — свет Как это работаетДля эффективной передачи света оптоволоконный кабель должен содержать стекло высшей степени чистоты.Процесс изготовления стекла такого уровня чистоты очень сложен и требует тщательного контроля материалов и процессов. Тем не менее, основная концепция проста. По сути, оптическое волокно изготавливается путем вытягивания расплавленного волокна из нагретой стеклянной заготовки или «заготовки». Ниже приводится более подробное объяснение трех основных этапов изготовления оптического волокна.
Шаг № 2
Вытяжка оптического волокна из преформы На этом шаге готовая стеклянная преформа устанавливается наверху башни, которая поддерживает различные устройства, используемые в процессе вытяжки волокна.
Процесс начинается с опускания одного конца преформы в поточную печь, которая производит тепло в диапазоне от 3400 до 4000 градусов по Фаренгейту. Когда нижний конец преформы начинает плавиться, он образует расплавленный шарик, который под действием силы тяжести тянется вниз. За шаром тянется тонкая полоска стекла, которая быстро остывает и затвердевает.
Оператор оборудования продевает эту стеклянную нить через остальные устройства на башне, в том числе несколько аппликаторов для нанесения буферного покрытия и ультрафиолетовые печи для отверждения.Наконец, оператор подключает волокно к тракторному механизму.
Устройство трактора вытягивает стеклянную нить из преформы со скоростью от 33 до 66 футов в секунду. Фактическая скорость, с которой трактор тянет нить, зависит от информации обратной связи, которую устройство получает от лазерного микрометра, который постоянно измеряет диаметр волокна.
В конце цикла готовое волокно наматывается на катушку.
Step # 3
Тестирование волоконной оптики
Готовое оптическое волокно должно пройти ряд тестов для определения качества готового продукта.Ниже приведены некоторые из использованных оценок:
• Профиль показателя преломления
• Проверка геометрии волокна, включая сердцевину, оболочку и покрытие
• Предел прочности
• Пропускная способность
• Затухание при различные длины волн
• Хроматическая дисперсия
• Диапазон рабочих температур и влажности
Контроль качества при производстве оптического волокна
На качество и чистоту производимого оптического волокна влияют различные факторы.К ним относятся:
Химический состав — Достижение оптимального соотношения различных химикатов, используемых для создания преформы, важно для достижения чистоты стекла. Эта смесь химикатов также определяет оптические свойства волокна, которое будет изготовлено из преформы, включая коэффициент расширения, показатель преломления и так далее.
Мониторинг газа — Очень важно, чтобы состав газа и скорость потока контролировались на протяжении всего процесса создания преформы.Также важно, чтобы все клапаны, трубки и трубопроводы, контактирующие с газом, были изготовлены из коррозионно-стойких материалов.
Нагрев и вращение — Полый цилиндр, который используется для создания преформы, необходимо нагревать до нужной температуры и постоянно вращать, чтобы химикаты распределялись равномерно.
Основы POF: как это сделано
Из чего сделаны оптические волокна?
Кремнеземное стекло (SiO 2 ) является наиболее распространенным материалом, используемым в стекловолоконной оптике из-за его простого производственного процесса и надежности в установках.С другими типами стекла экспериментировали или использовали, особенно в первые дни существования волоконной оптики.
В пластиковой волоконной оптике используются такие материалы, как полиметилметакрилат (ПММА), полистирол (ПС) и поликарбонат (ПК). У каждого из них есть свои преимущества и недостатки, но PMMA является наиболее распространенным материалом, используемым для сердечников POF.
При выборе материала для волокна его показатель преломления (отношение скорости света в вакууме к скорости света в материале), оптическое затухание (какая часть светового сигнала поглощается в оптической среде) учитываются температура стеклования (которая отражает диапазон температур, которые может выдерживать волокно), а также прочность и подверженность потерям из-за изгиба.
Как делается оптоволоконный кабель?
При производстве POF или GOF из преформы оптоволоконный кабель начинается с большого цилиндра преформы из материала сердечника. Заготовку подают через печь, где она нагревается, и одно волокно желаемого диаметра непрерывно вытягивается, охлаждается и наматывается. Другие методы производства POF включают нагрев компонентов материала сердцевины до их точки плавления и их экструзию вместе с оболочкой.
Как изготавливаются полимерные волокна?
Синтетические волокна производятся в процессе прядения, при котором полимерная жидкость выдавливается через мелкие отверстия, называемые фильерами.После этого полученные волокна вытягиваются на определенную длину для увеличения кристалличности и, следовательно, прочности волокон.
В зависимости от типа производимого полимерного волокна могут использоваться разные методы прядения. Влажное прядение — это метод, используемый для таких материалов, как акрил, поливинилхлорид (ПВХ) и полиметилметакрилат (ПММА), полимер, наиболее часто используемый в качестве пластиковой сердцевины оптического волокна.
Что такое полимер, армированный волокном?
Армированный волокном полимер — это композитный материал, состоящий из полимерного материала, в котором используется армирование волокнами для придания ему прочности в направлении волокон.
Углеродное волокно является типичным примером этого. Жгуты углеродного волокна, состоящие из тысяч отдельных волокон, могут быть сотканы в прочную ткань. Затем эта ткань армируется смолой для создания жесткого материала с очень высоким отношением прочности к весу.
Пластиковый оптоволоконный кабель Mitsubishi ESKA® серии GHTT усилен элементами из арамидного волокна в его оболочке. Благодаря этой конструкции оптические каналы передачи данных с высокой пропускной способностью могут работать в сложных механических средах, таких как робототехника для автоматизации производства.
Ссылки
O. Ziemann et al., Справочник POF . Берлин, Германия: Springer-Verlag Berlin Heidelberg, 2008.
A. Weinert., Пластиковые оптические волокна . Мюнхен, Германия: Publicis MCD Verbeagentur GmbH, 1999.
ПОЛИМЕР, АРМИРОВАННЫЙ ВОЛОКНОМ [Онлайн]. Доступно: https://theconstructor.org/concrete/fibre-reinforced-polymer/1583/
Что такое углеродное волокно? Технология углеродного волокна, [Интернет]. Доступно: https: // dragonplate.ru / разделы / technology.asp
Искусственные волокна — Полимерные волокна, Другие синтетические волокна [Online]. Доступно: http://science.jrank.org/pages/532/Artificial-Fibers.html
FOA Tech Topics: Производство оптического волокна
FOA Tech Topics: Производство оптического волокнаВолоконно-оптическая ассоциация — Технические темы
Изготовление Оптическое волокно
Студенты
часто спрашивают, как есть клетчатка
сделал.Это, конечно, не очевидно, как что-то всего лишь 1/8 мм
— 0,005 дюйма — в диаметре может быть изготовлено с такой точностью.
Некоторые основные факты о том, как производится оптическое волокно, могут помочь
чтобы лучше понять, как работает оптическое волокно.
При Ядро
Как известно, существует два основных типа оптического волокна: одномодовое
и многомодовый. Оба типа волокна состоят только из двух основных
концентрические стеклянные конструкции: ядро, несущее свет
сигналов, а также оболочка, задерживающая свет в сердцевине (рис.1).
одномодовый
волокно имеет меньший
ядро — всего 9 микрон в диаметре — и всего в 6 раз больше длины волны
света, который он пропускает. Небольшой размер ядра ограничивает передаваемую
свет в волокне только к одной основной моде, что сводит к минимуму
рассеивание световых импульсов, увеличение дальности сигнала
можно отправить.
многомодовый
волокно имеет большую сердцевину
диаметр по сравнению с длиной волны проходящего света 50
или 62.5 мкм. Следовательно, многомодовое волокно распространяется более чем на
один режим света. Благодаря относительно большой сердцевине многомодовое волокно
страдает большей дисперсией, чем одномодовый. Использование градуированного индекса
core, где слои света имеют более низкий показатель преломления, чем
вы идете дальше от центра ядра, сводит к минимуму дисперсию
но усложняет процесс изготовления.
Есть два
основные шаги в
процесс преобразования сырья в оптическое волокно, готовое к
быть отправлено:
1.изготовление преформы из чистого стекла и 2. чертеж
преформа
Производство
Преформа
Первая
шаг в производстве
стеклянные оптические волокна предназначены для изготовления твердого стеклянного стержня, известного как
преформа. Сверхчистые химические вещества — в первую очередь тетрахлорид кремния.
(SiCl4) и тетрахлорид германия (GeCl4) — превращаются в
стекло при изготовлении преформ. Эти химические вещества используются в
различные пропорции для изготовления основных областей для различных
виды преформ.
Базовый
химическая реакция
изготовление оптического стекла:
SiCl4 (газ) +
O2> SiO2 (твердый)
+ 2Cl2 (при нагревании)
GeCl4 (газ) +
O2> GeO2 (твердый)
+ 2Cl2 (при наличии тепла)
Сердечник состав всех стандартных Коммуникационные волокна состоят в основном из кремнезема, с различными количество германия, добавленное для увеличения показателя преломления волокна до желаемого уровня.Одномодовые волокна обычно имеют только небольшие размеры. количества германии и имеют однородный состав в пределах основной. Многомодовые волокна обычно имеют гораздо более высокий коэффициент преломления. индекс, и, следовательно, гораздо более высокое содержание германии. Также ядро состав и показатель преломления многомодового градиентного волокна изменяются по сердцевине волокна, чтобы дать преломляющую индекс параболической формы.
Есть использовалось несколько методов для изготовления преформ.В модифицированном химическом осаждении из паровой фазы (MCVD) процесс, тщательно контролируемая смесь описанных химикатов выше проходит через внутреннюю часть вращающейся стеклянной трубки, выполненной чистого синтетического SiO2.
Трубка из чистого кремнезема монтируется на токарном станке, оснащенном специальным
нагревательная горелка. Когда газы протекают внутри трубки, они реагируют на
тепло за счет образования твердых субмикронных частиц, называемых «сажей»,
в непосредственной близости от зоны нагрева.Как только сажа образовалась, она
оседает на внутренней стенке трубки. Когда горелка проходит
поверх осажденной сажи тепло превращает эти твердые белые
частицы в чистое прозрачное стекло в процессе, называемом
остекловывание.
Осажденный материал будет составлять сердцевину оптического
волокно (см. схему процесса на рис. 2)
Процесс
повторяется для многих
часов по мере формирования каждого последующего внутреннего слоя.На каждый взмах
горелки производитель может изменять состав, вязкость
и толщину наплавленного слоя для получения конкретных
конструкции волокна. Это в сочетании с возможностью изменять
скорость, с которой движется горелка, и температура
пламя, дает нам возможность производить широкий спектр сверхчистых
типы оптического волокна.
Точный
доставка химикатов
обеспечивается за счет конструкции производственного оборудования, которое
работает точно и стабильно.Например, массовый расход
контроллеры
используются для дозирования химикатов в реакции. Весь критический процесс
параметры контролируются и контролируются в реальном времени с помощью on-line
компьютеры, которые также запрограммированы для сбора всех соответствующих процессов
данные.
После
желаемое количество ядра
материал осаждается, химический поток устраняется, скорость
факела уменьшается, а температура пламени
увеличился так, что трубка сжалась в сплошной стержень.На
В конце этого процесса оператор отделяет преформу от
остальную часть сборки стекла и перемещает ее к следующему шагу. В
весь процесс производства преформ в высшей степени автоматизирован с
минимальное участие человека.
The
показатель преломления изготовленных
преформа измеряется с помощью анализатора преформ. Этот инструмент
измеряет критические основные параметры и сравнивает их с внутренними
технические характеристики. Все соответствующие параметры отображаются автоматически.
на диаграммах статистического контроля, которые операторы просматривают для каждого
измерение.
Чистый кварцевое стекло пусковое трубка стала частью области покрытия преформы. В область облицовки дополнительно увеличена за счет «рукава» или процесс «чрезмерного коллапса». Вот еще один чистый кремнезем трубка сжимается снаружи исходной преформы, в результате чего геометрические размеры преформы в соответствии с окончательными спецификациями.
Другой
используемый процесс — Внешний
Осаждение из паровой фазы (OVD), при котором сажа оседает на поверхности
«удочки» из чистого кремнезема.Первые слои
являются сердцевиной, то добавляется оболочка. После всех слоев
откладываются, стержень для приманки удаляется, и преформа направляется
и рухнул аналогично процессу MCVD.
Чертеж
Волокно
Следующий шаг в процессе производство оптических волокон заключается в преобразовании изготовленной преформы в тонкое волокно. Это делается в операции, называемой волокном. рисовать (рис.3). Наконечник преформы опускается в высокочистый графитовая печь. Чистые газы вводятся в топку для обеспечить чистую и проводящую атмосферу. В топке плотно контролируемые температуры, приближающиеся к 1900 ° C, смягчают наконечник преформы. Как только температура размягчения наконечника преформы станет достигнута, сила тяжести берет верх и позволяет расплавленной капле «освободить падают », пока не растянутся в тонкую прядь.
Оператор
нити эту прядь
волокна через серию штампов для нанесения покрытия, а процесс вытяжки
начинается.Волокно натягивается тракторной лентой, расположенной на
нижняя часть вытяжной башни, а затем намотана на намоточные барабаны. В течение
при вытяжке преформа нагревается при оптимальной температуре до
добиться идеального натяжения рисунка. Скорость прорисовки 10-20 метров
в секунду не редкость в отрасли.
Во время
нарисовать процесс диаметра
вытянутого волокна контролируется до 125 микрон в пределах допуска
всего 1 микрон. Лазерный измеритель диаметра используется для контроля
диаметр волокна.Датчик может измерять диаметр
волокно со скоростью более 750 раз в секунду. Настоящий
значение диаметра сравнивается с мишенью 125 микрон. Незначительный
отклонения от цели преобразуются в изменения скорости вытяжки
и подается в механизм трактора для коррекции. Если диаметр
волокна увеличивается выше его цели, скорость вытягивания составляет
повысился; если диаметр волокна начинает падать ниже цели,
скорость вытяжки снижена.Как правило, контроль диаметром 125 микрон
достигается в пределах интервала шесть сигм с допуском в 1 микрон.
Двухслойный
защитное покрытие
затем наносится на волокно — мягкое внутреннее покрытие и твердое
внешнее покрытие. Эта двухкомпонентная защитная куртка обеспечивает механическое
защита при обращении, а также защита нетронутой поверхности
волокна из суровых условий окружающей среды. Эти покрытия отверждаются
ультрафиолетовыми лампами. Процесс рисования хорошо автоматизирован и
практически не требует взаимодействия с оператором после распараллеливания
шаг.
Тест
и измерение
Нарисованный
следующее испытание волокна,
где проверяются все оптические и геометрические параметры для обеспечения
что они соответствуют строгим требованиям.
Во-первых,
прочность на разрыв
волокно тестируется. Каждая катушка вытянутого волокна намотана
ряд кабестанов и подвергался нагрузкам, чтобы гарантировать, что
волокно имеет минимальную заданную прочность на разрыв.Волокно
затем намотали на транспортировочные бобины и отрезали до заданной длины.
Волокно
проверено на точку
дефекты с помощью оптического рефлектометра во временной области (OTDR), который
использует рассеянный свет, чтобы указать местоположение любых аномалий
по длине волокна.
Спулированный
волокно автоматически
протестировано на параметры трансмиссии, в том числе:
- затухание: уменьшение мощности сигнала на расстоянии
- пропускная способность: информационная емкость; важное измерение для многомодового волокно
- числовой апертура: измерение угла приема света волокна
- отрезной длина волны: в одномодовом волокне длина волны, выше которой только одномодовое распространение
- режим диаметр поля: в одномодовом волокне радиальная ширина светового пульс в волокне; важно для соединения
- хроматический дисперсия: распространение импульсов света за счет лучей разных длины волн, проходящие через сердечник с разной скоростью; в одномодовое волокно это ограничивающий фактор для передачи информации вместимость
Кроме того,
как многомодовые, так и
одномодовые волокна измеряются по многим геометрическим параметрам
в том числе:
- облицовка диаметр
- облицовка некруглость
- покрытие внешний диаметр
- покрытие внешняя некруглость
- покрытие ошибка концентричности
- с сердечником ошибка концентричности
- ядро некруглость
- ядро
диаметр
Окружающая среда и механические испытания также выполняется периодически, чтобы гарантировать, что продукт поддерживает его оптическая и механическая целостность и соответствие требованиям заказчика требования.Эти тесты включают:
- покрытие сила полосы
- действующих диапазон температур
- температура зависимость затухания
- температура-влажность Велоспорт
- ускоряется старение
- вода
иммерсионный
Наконец, протестированное волокно готово для прокладки кабеля для защиты волокна и последующей установки.
Спасибо для информации и фотографии к O F S, ранее Lucent Technologies, которая производит и продает высокопроизводительные многомодовые оптические волокна для приложений передачи данных по всему миру. Посетите веб-сайт O F S по адресу http://www.ofsinnovations.com/
Вернуться в FOA Домашняя страница
Вернуться в FOA Технические темы
Волокно жестче, чем вы думаете
Оптоволоконный кабель обычно классифицируется как хрупкий, как стекло, каковым, конечно же, является настоящее волокно.Но в отличие от стаканов, которые разбиваются при падении, или окон, которые проигрывают каждую битву с детским бейсбольным мячом, стекловолокно невероятно прочное и гибкое. Помните, что материал, обеспечивающий прочность стеклопластиковых лодок, лестниц и т. Д., — это стекловолокно.
СилаFiber восходит к процессу производства. Чаще всего стекло изготавливается путем плавления диоксида кремния (SiO2, который в основном представляет собой песок) в большом горшке, заливки его в форму и охлаждения достаточно быстро, чтобы предотвратить кристаллизацию, в результате чего остается аморфное твердое вещество.Хотя этот процесс дешев и быстр, производимое стекло не является чистым, что ограничивает его прочность и способность пропускать свет. Примеси поглощают в 1000 раз больше света, чем оптическое волокно, и концентрируют напряжения, которые снижают его прочность и могут вызвать трещины.
Оптическое волокно производится совершенно другим способом. Он начинается с стержня или трубки из чистого кремнезема, а остальная часть материала осаждается при высокой температуре с использованием сверхчистых газов для создания преформы. Преформа затвердевает, затем помещается в вытяжную башню, где волокно вытягивается в длинные пряди.Тщательный контроль процесса делает стекло невероятно чистым, прозрачным и прочным.
Насколько сильно? Теоретическая максимальная прочность (на разрыв) стекловолокна составляет около 2 миллионов фунтов на квадратный дюйм, но практический предел составляет от 10 до 20 процентов от этого. Площадь поперечного сечения настолько мала, около 20 миллионных долей дюйма, что фактическая максимальная прочность волокна составляет от пяти до 10 фунтов натяжения.
Но каким бы прочным ни было волокно толщиной с волос, его небольшой размер требует защиты от влаги и царапин.Влага может увеличить затухание и сделать волокно хрупким. Царапины на поверхности вызывают неисправности, из-за которых волокно выходит из строя. Первый уровень защиты — это герметичное пластиковое покрытие, наносимое на волокно сразу после его выхода из вытяжной башни.
Затем оптическое волокно превращается в кабель. Кабель обеспечивает защиту от окружающей среды, а не только от влаги или грязи, но и от других жидкостей, от сдавливающих или изгибающих сил и, конечно же, от растягивающего напряжения, возникающего при установке.
Все волоконно-оптические кабели включают в себя силовые элементы, обычно арамидные волокна, такие как кевлар DuPont.Кевлар прочен, но его самая важная характеристика — он не растягивается при растяжении. При вытягивании он не растягивается, а затем расслабляется, когда напряжение снимается, что может вызвать перекручивание кабеля и создать нагрузку на волокно. Количество арамидного волокна внутри типичного внутреннего кабеля позволяет растягивать до 200 фунтов, в то время как наружные кабели рассчитаны на напряжение от 600 до 800 фунтов. Дополнительный усиливающий элемент используется в качестве элемента жесткости для поддержания допустимого радиуса изгиба кабеля и предотвращения перекручивания при прохождении углов.
Вы всегда должны помнить, что никогда не тяните оптоволоконный кабель за куртку, если он специально не предназначен для этого. Некоторые кабели, у которых есть броня или силовые элементы, встроенные в куртку, можно натянуть с помощью захвата Келлума на куртке, но необходимо также привязать тяговое ушко к кабелю с силовыми элементами, чтобы распределить растягивающее натяжение вокруг.
Волокнотакже гибкое из-за своего крошечного диаметра и высокой прочности. Вы можете взять симплексный кабель или трос с застежкой-молнией и завязать его узлами.Плотные изгибы вызовут потери в волокне, но мягкие арамидные прочностные элементы, окружающие волокно и мягкую оболочку, будут защищать волокно и предотвращать его разрушение. Удалите узел, и трос вернется в исходное состояние. Вы можете попробовать это самостоятельно, используя оптоволоконный измеритель мощности и источник, чтобы увидеть, сколько потерь вызвано узлом и как они исчезают, когда кабель развязан. Со многими кабелями вы можете использовать визуальный локатор повреждений (видимый лазерный источник) и фактически видеть свет, потерянный через оптоволоконную оболочку.
Волоконно-оптические кабели спроектированы таким образом, чтобы выдерживать силу сжатия. Мягкая куртка и набивка, обеспечиваемые силовыми элементами, защищают волокна. Волоконно-оптические кабели используются под коврами в казино, где по ним регулярно толкают тележки с деньгами. Специальные тактические тросы используются на поле боя, где они выдерживают вес танков.
В целом, оптоволоконные кабели были спроектированы так, чтобы быть более прочными, чем это возможно. Но это страховка от неуклюжей установки.Успешная установка оптоволокна обеспечивается следующими двумя рекомендациями:
¥ Не превышайте максимальное тяговое усилие.
¥ Допускается минимальный радиус изгиба, в 20 раз превышающий диаметр кабеля при растягивании. EC
HAYES — писатель и инструктор VDV, а также президент Ассоциации волоконной оптики. Найдите его на сайте www.JimHayes.com.
Как это сделано: оптоволоконные кабели
Приглашаем вас на экскурсию по нашим производственным предприятиям в Кэрроллтоне, Джорджия, США.Ознакомьтесь с высокоавтоматизированным производственным процессом OFS, позволяющим производить широкий спектр волоконно-оптических продуктов для телекоммуникационных приложений. Здесь производятся свободная трубка, микрокабели, плоская лента, ADSS, катящиеся ленточные кабели сверхвысокой плотности и кабели для помещений.
OFS Волокно
Завод в Кэрроллтоне вертикально интегрирован, и оптоволокно ежедневно доставляется с завода OFS Norcross, расположенного примерно в часе езды.
Качество
Предприятие зарегистрировано в соответствии со стандартами ISO 9001, ISO 14000 и TL 9000.Прослеживаемость сохраняется на каждом этапе процесса и, в конечном итоге, до входящего волокна. На предприятии также есть полнофункциональная лаборатория аттестации продукции и испытательная площадка для прокладки кабелей.
OFS использует волокна 200 и 250 микрон
OFS производит несколько различных волоконных структур на заводе в Кэрроллтоне, в том числе структуры со свободной трубкой, плоской лентой и скручивающейся лентой. Эти конструкции используются в различных типах кабелей и приложениях.
Методы статистического управления процессами
Каждый этап производственного процесса строго контролируется с соблюдением соответствующих заданных размеров и допусков.
Цветные чернила нанесены на Fiber
Цветовой код промышленного стандарта используется для четкой идентификации волокон в течение их срока службы. Цветные чернила наносятся до определенной толщины, отверждаются и повторно охлаждаются для следующего этапа процесса.
Процесс производства буферной трубки
Для изготовления незакрепленных трубок волокна или ленты снимаются с катушек, а вокруг них выдавливается буферная трубка. Завод в Кэрроллтоне производит гелевые и заполненные гелем буферные пробирки из различных материалов, включая полипропилен и PBT.Буферные пробирки разного размера используются для разных типов продуктов. Буферные пробирки, используемые вне растений, включают либо водоблокирующие материалы, пропитанные супервпитывающим полимером, либо гелем.
Процесс производства ленты
Матричный материал наносится на волокна, чтобы связать их вместе, чтобы их можно было сращивать как группу. Наиболее распространены плоские ленты из 12 и 24 волокон. Выравнивание цветового кода волокна и геометрические характеристики очень важны, поэтому ленты можно сращивать и соединять в полевых условиях.
Рулонная лента
Скручиваемые ленты только частично связаны друг с другом, что позволяет скручивать их в цилиндрическую упаковку. Скручиваемые ленты только частично связаны друг с другом, что позволяет сворачивать их в цилиндрическую упаковку. Поскольку круги занимают больше места, чем прямоугольники, кабели с роликовыми лентами могут удерживать вдвое больше волокон, чем плоские ленточные кабели сопоставимого размера. Поскольку эти волокна частично связаны, их можно легко сращивать как отдельные волокна, так и в виде ленты, что дает оператору сети большую гибкость развертывания.
Кабельная проводка
OFS производит два основных типа кабелей — многожильные кабели и кабели с центральной трубкой.
Многожильный кабель
Скрученные кабели изготавливаются путем скручивания трубок из волокон, плоских лент или скручиваемых лент вокруг центрального элемента. Многожильные кабели часто используются в приложениях, требующих частого доступа к волокнам.
Кабели центральной трубки
Кабели с центральной трубкой изготавливаются путем выдавливания центральной трубки вокруг волоконной структуры.Кабели с центральной трубкой могут обеспечивать более высокую плотность волокна.
Прочность
Силовые элементы, включая стекловолокно и арамидную пряжу, используются для ограничения нагрузки на кабели и волокна при приложении к ним натяжения.
Гидроизоляционные материалы
Пряжа и ленты добавляются для защиты от воды за пределами сердечника кабеля.
Броня
Для проложенных прямо под землей кабелей может быть добавлен один или несколько слоев стальной брони для обеспечения устойчивости к грызунам и тонизирующей способности.
Наружная куртка
Полиэтилен различных версий используется для большинства внешних кабелей. Для кабелей внутри помещений или внутри / вне помещений выбираются материалы, обеспечивающие соответствующую огнестойкость и дымостойкость.
Информационная печать
Напечатан тип кабеля, дата изготовления, длина и уникальный серийный номер, позволяющий проследить весь производственный процесс.
Заключительное испытание
По завершении производства готовый кабель проходит окончательные испытания на длину и оптические свойства.
Доставка
Затем кабели упаковываются для отправки и загружаются на грузовики до конечного пункта назначения.
Теги: оптоволоконные кабели, оптоволокно
Последние сообщения
Категории:
Взгляд изнутри на производство оптоволоконного стекла
Оптоволоконный кабельпомог донести эту статью до любого устройства, на котором вы ее читаете. Крошечные нитки сверхпрозрачного стекла играют решающую роль практически во всем, что происходит в Интернете — от подключения огромных центров обработки данных до доставки The Mandalorian на ваш телевизор.А поскольку использование широкополосной связи в некоторых районах во время пандемии увеличилось более чем на 40 процентов, эти быстрые трубы стали важнее, чем когда-либо.
В этом году открытию, сделавшему возможным быстрый обмен данными, исполняется 50 лет. В 1970 году группа ученых, работающих на стекольном заводе Corning, разработала метод изготовления чистого кварцевого стекла, позволяющий получать сигналы — электронные письма, веб-сайты, Fortnite сеанса — пройти по нитям толщиной 125 микрон в виде импульсов лазерного света с беспрецедентной эффективностью.Сообщения передаются на большие расстояния намного быстрее и с меньшими затратами, чем аналогичные эхо-запросы по медным проводам, которые лежат в основе обычных стационарных телефонов и кабельных соединений.
В течение десятилетий волокно производилось на той же фабрике в Уилмингтоне, штат Северная Каролина. Нити, которые они производят, объединяются в провода, из которых состоит все, от трансатлантических подводных кабелей до интернет-шнура, идущего в ваш дом.
Укладка частиц
Форсунки пламени направляют частицы на вращающиеся стержни.Из простого плавления песка, который в основном состоит из диоксида кремния, будет стекло, но из этого песчанистого материала не будет такой оптической чистоты, которая необходима для распространения света по всему земному шару. Поэтому Corning производит собственный чистый диоксид кремния. Чтобы сформировать так называемый «бланк», то есть стержень, который в конечном итоге превратится в волокнистую нить, струи пламени выдувают элементы сердцевины волокна из резервуаров. Образовавшиеся частицы, известные как сажа, попадают на вращающиеся керамические стержни и накапливаются, как снежный ком. Второй слой с несколько другим химическим составом создает отражающий барьер, который не дает фотонам улетучиваться, когда они отскакивают от трубы, которая действует как волновод.Corning называет эту часть производственного процесса «укладкой».
Запекание заготовок
Печь связывает частицы в единое целое.Пустой стержень (подвешенный слева) больше похож на огромную палку мела, чем на чистый кусок стекла. Сажа прилипла слоями, но общая структура очень пористая, и молекулы не полностью связаны друг с другом. Отсюда роботизированный механизм опускает каждый цилиндр в раскаленную печь на несколько часов, чтобы приготовить и осветлить.
Объединение частиц
[Слева] Незавершенная заготовка идет в печь. [Справа] Заготовки выходят из печи чистыми.Corning называет процесс приготовления консолидацией. Заготовка, входящая в печь слева, кажется мутной, а выходящая справа — сплошной прозрачной массой. Тепло связывает молекулы кремнезема плотно друг с другом, делая стекло плотным и свободным от примесей, которые могут препятствовать его способности пропускать свет.Corning удаляет керамический стержень, который изначально использовался для сбора сажи, и оставшееся после него отверстие закрывается по мере плавления материала. Конечный результат имеет те же оптические свойства, что и тонкая прядь волокна, но в гораздо большем масштабе.
Растяжка стекла
Фаза вытяжки плавит заготовки, которые удлиняются в длинные пряди [справа] по мере прохождения через оборудование [слева].Чтобы растянуть толстые стеклянные трубки в ультратонкие пряди, оборудование справа нагревает цилиндры примерно до 2000 градусов Цельсия.(Для сравнения, обычное оконное стекло плавится при ничтожных 600 градусах Цельсия.) Толстая капля образуется, когда вещество плавится, и сила тяжести тянет субстрат вниз на несколько этажей по трубке, пока датчики контролируют его температуру. Внизу машина — а иногда и человек — отрезает каплю, чтобы подготовить волокно для раскручивания на барабанах.
Намотка волокна
Для удобства каждый тип волокна имеет цветовую кодировку.Готовый продукт покрывается цветными полимерами перед тем, как машины наматывают его на бухты.Поскольку оптоволоконный кабель состоит из десятков или даже тысяч жил с слегка различающимися свойствами — и, следовательно, с разными допусками, например, на изгиб под углом 90 градусов, — оттенки дают техническим специалистам и производителям кабеля простой и визуальный метод идентификации каждого типа. . Например, провод в вашем доме может включать 72 нити, в то время как один провод, переправляющий данные через Атлантику, может иметь более 5000.
.