Что такое металлизация отверстий в печатных платах. Какие бывают виды металлизированных отверстий. Как выполняется процесс металлизации. Какие технологии применяются для металлизации микроотверстий.
Что такое металлизация отверстий печатных плат
Металлизация отверстий — это технологический процесс нанесения проводящего металлического покрытия на стенки отверстий в печатных платах. Основная цель металлизации — обеспечить электрическое соединение между проводящими слоями многослойной печатной платы.
Металлизация отверстий решает следующие важные задачи:
- Создание электрических межслойных соединений в многослойных печатных платах
- Обеспечение надежного электрического контакта при монтаже выводных компонентов
- Повышение механической прочности крепления компонентов к плате
- Увеличение теплоотвода от электронных компонентов
Таким образом, качественная металлизация отверстий критически важна для нормального функционирования печатных узлов и электронных устройств в целом.
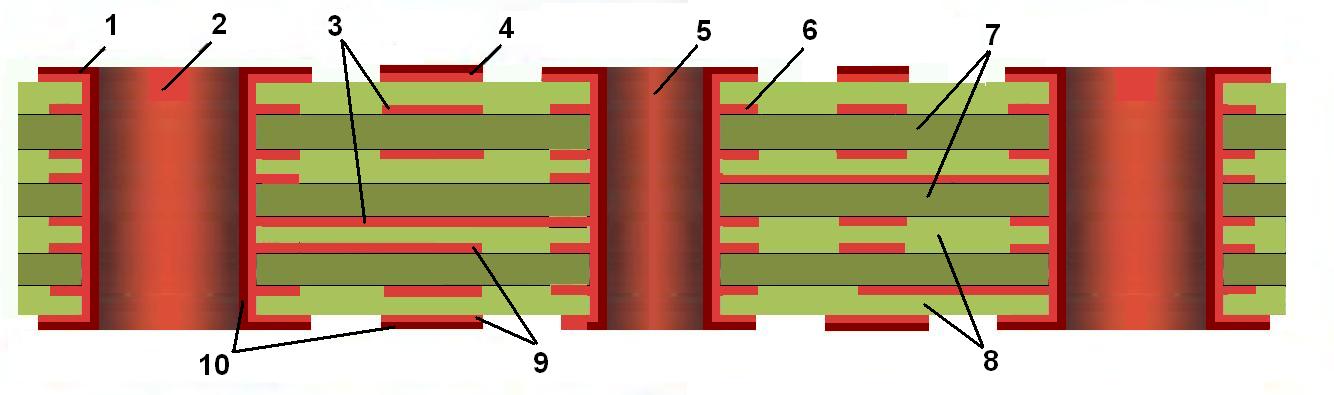
Основные виды металлизированных отверстий
В современных печатных платах используются следующие основные виды металлизированных отверстий:
Сквозные металлизированные отверстия
Это отверстия, проходящие через все слои многослойной печатной платы. Используются для соединения проводящих слоев и монтажа компонентов. Являются наиболее распространенным и простым в изготовлении видом.
Глухие отверстия (blind vias)
Соединяют один из внешних слоев с одним или несколькими внутренними слоями платы. Не проходят насквозь через всю толщину платы.
Скрытые отверстия (buried vias)
Располагаются между внутренними слоями платы и не выходят на внешние поверхности. Используются для создания межслойных соединений.
Микроотверстия (micro vias)
Отверстия малого диаметра (менее 0.15 мм), обычно соединяющие 2-3 соседних слоя. Формируются лазером или прецизионным сверлением.
Технология металлизации сквозных отверстий
Процесс металлизации сквозных отверстий многослойных печатных плат обычно включает следующие основные этапы:
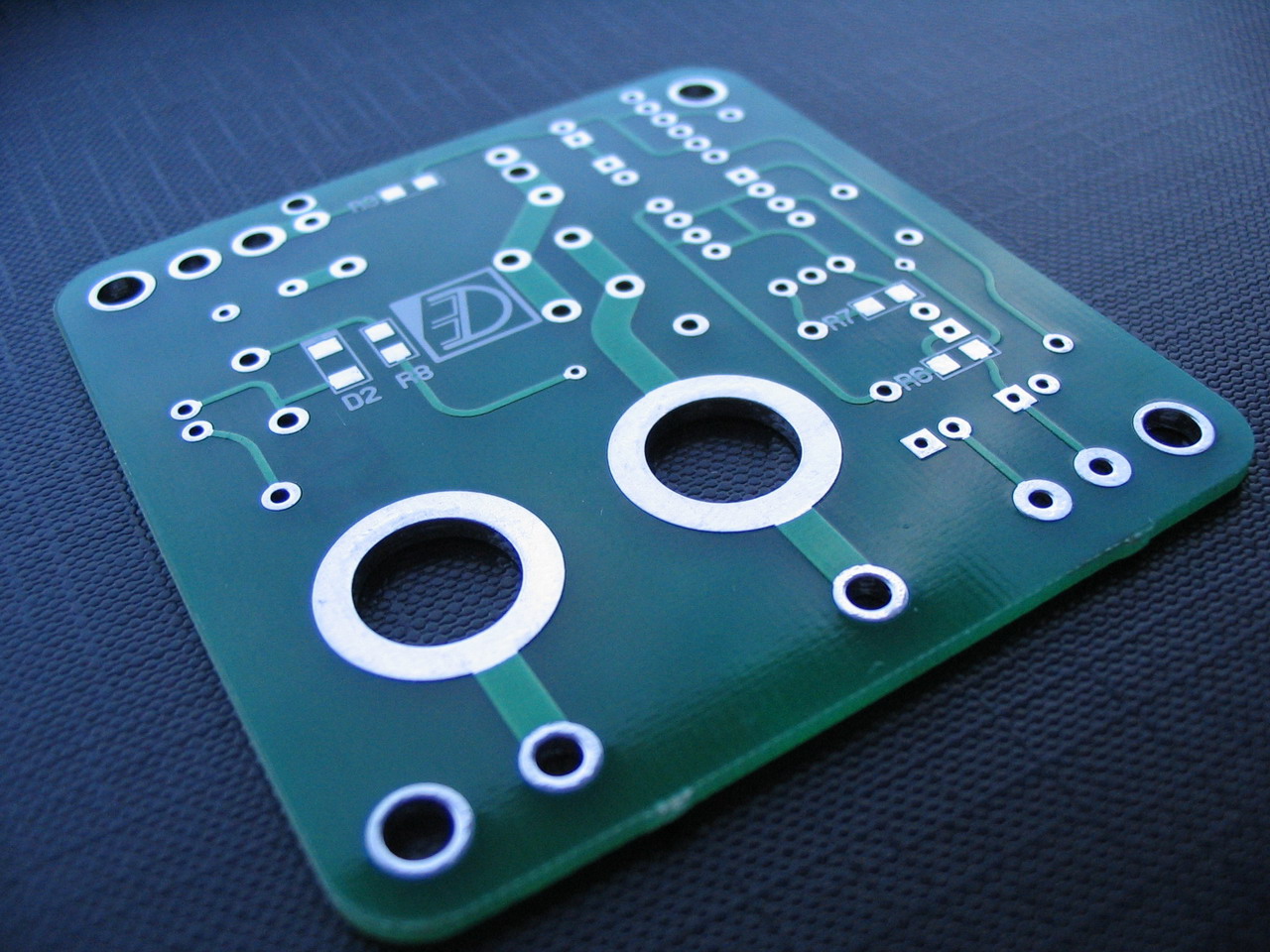
- Сверление отверстий в заготовке печатной платы
- Очистка и подготовка поверхности отверстий
- Химическое меднение для создания тонкого проводящего слоя
- Гальваническое наращивание слоя меди до требуемой толщины
- Нанесение финишных покрытий (олово-свинец, иммерсионное золото и др.)
Ключевым этапом является химическое меднение, обеспечивающее начальную металлизацию диэлектрических поверхностей отверстий. Оно позволяет создать тонкий проводящий слой, на который затем наращивается основной слой меди.
Особенности металлизации микроотверстий
Металлизация микроотверстий имеет ряд специфических особенностей:
- Требуется прецизионное формирование отверстий лазером или сверлением с контролем глубины
- Необходимо обеспечить высокую равномерность металлизации по всей глубине отверстия
- Используются специальные химические составы для металлизации с улучшенной проникающей способностью
- Применяется гальваническое наращивание меди в импульсном режиме для лучшего заполнения
Качественная металлизация микроотверстий — одна из самых сложных задач в производстве современных печатных плат высокой плотности.
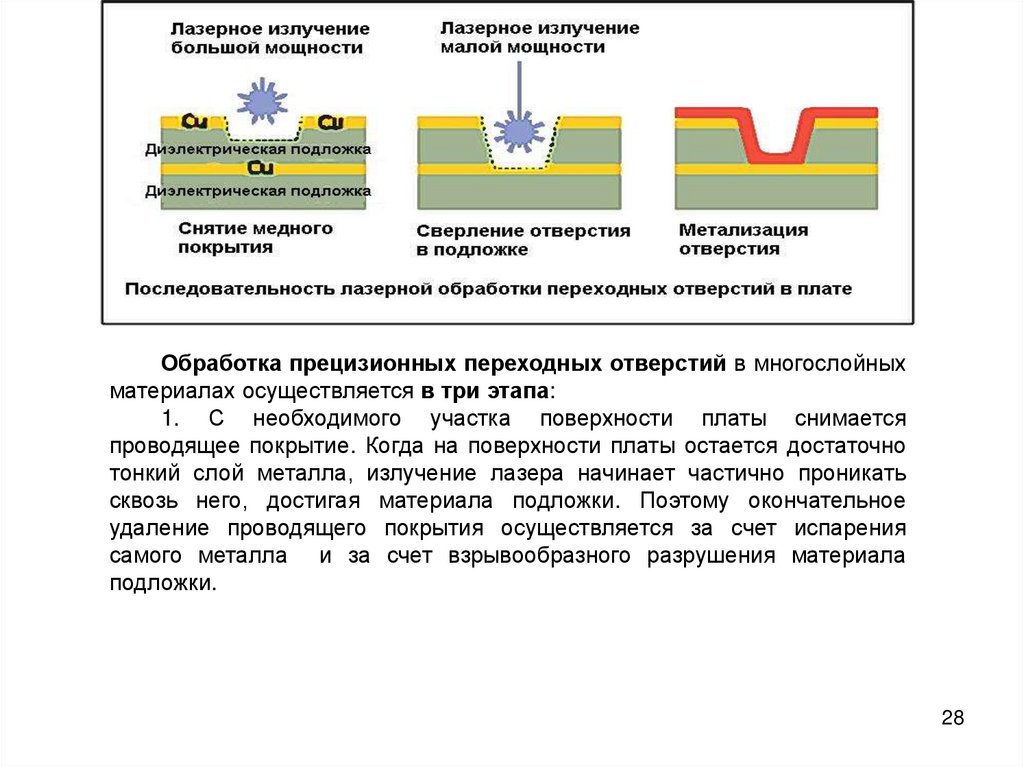
Современные технологии прямой металлизации
В последние годы активно развиваются технологии прямой металлизации отверстий, позволяющие исключить этап химического меднения. Основные преимущества прямой металлизации:
- Сокращение количества технологических операций
- Снижение расхода химикатов и объема сточных вод
- Улучшение адгезии и качества металлизации
- Возможность металлизации высокоаспектных отверстий
Наиболее распространенные методы прямой металлизации:
- Палладиевая активация поверхности
- Графитовые технологии
- Технологии на основе проводящих полимеров
Выбор конкретной технологии зависит от требований к печатным платам и возможностей производства.
Ключевые параметры качества металлизации отверстий
При оценке качества металлизации отверстий печатных плат учитываются следующие основные параметры:
- Толщина металлизации (обычно 20-35 мкм для сквозных отверстий)
- Равномерность металлизации по глубине отверстия
- Адгезия металлизации к диэлектрику
- Отсутствие пустот и непрометаллизированных участков
- Качество соединения с контактными площадками слоев
Контроль этих параметров осуществляется методами микрошлифов, рентгеновского анализа, измерения сопротивления и другими.
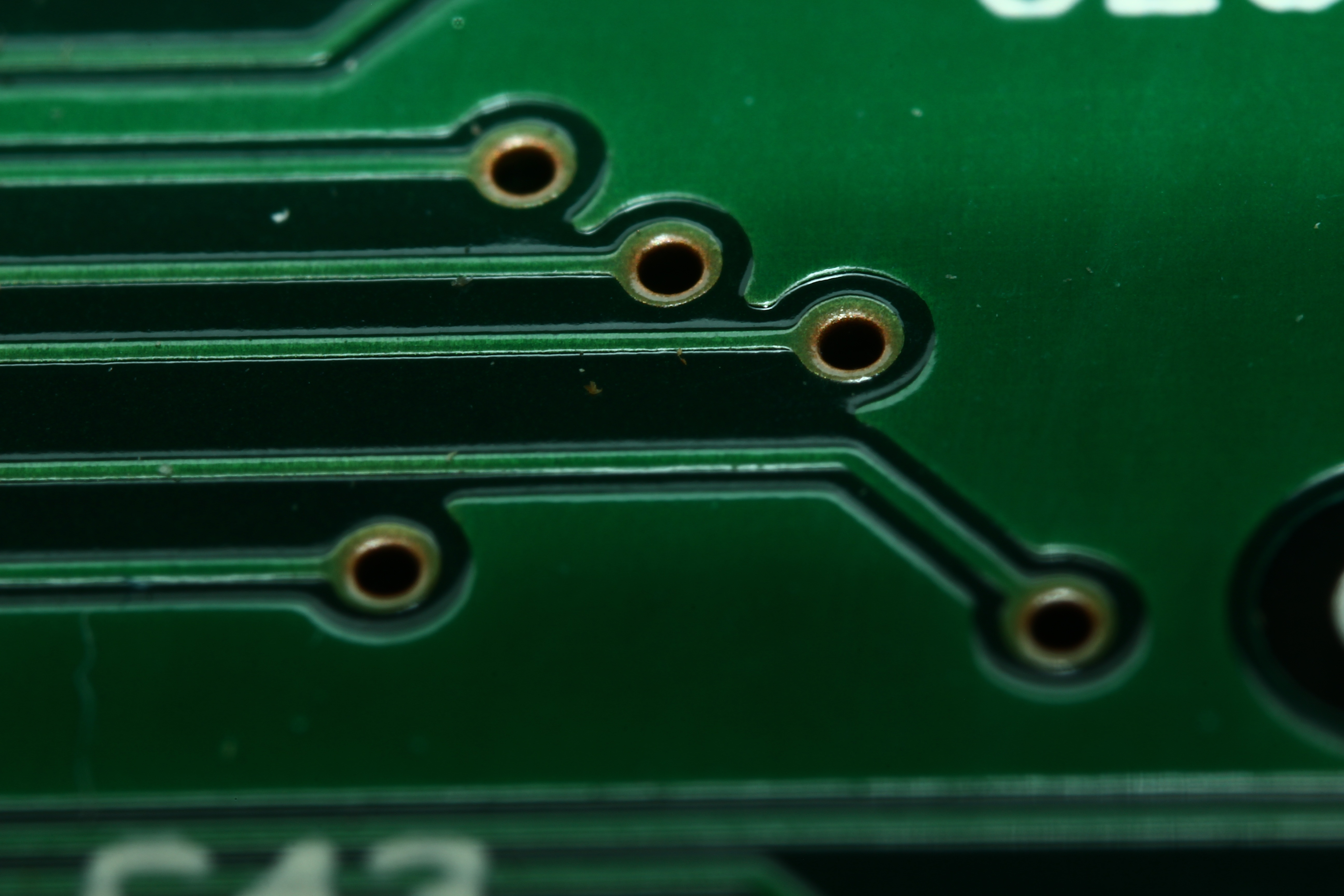
Проблемы при металлизации отверстий и их решение
При металлизации отверстий печатных плат могут возникать различные дефекты и проблемы. Наиболее распространенные из них:
Неравномерная металлизация
Проявляется в виде утонения слоя металлизации в центре отверстия. Причины: неоптимальные режимы гальванического осаждения, загрязнение электролита. Решение: корректировка состава и режимов электролита, применение импульсных режимов осаждения.
Плохая адгезия металлизации
Выражается в отслаивании металлизации от стенок отверстия. Причины: некачественная подготовка поверхности, загрязнения. Решение: оптимизация процессов очистки и активации поверхности перед металлизацией.
Пустоты в металлизации
Образование пустот и каверн в слое металлизации. Причины: захват пузырьков воздуха, неоптимальные режимы осаждения. Решение: применение вакуумной пропитки, корректировка режимов металлизации.
Своевременное выявление и устранение подобных дефектов позволяет обеспечить высокое качество и надежность металлизации отверстий печатных плат.

Выбор технологии металлизации отверстий
При выборе технологии металлизации отверстий печатных плат необходимо учитывать следующие основные факторы:
- Тип печатной платы (односторонняя, двусторонняя, многослойная)
- Требуемые параметры отверстий (диаметр, глубина, аспектное отношение)
- Материал основания платы
- Требования к качеству и надежности металлизации
- Производительность и экономические показатели
- Экологические аспекты процесса
Для большинства стандартных многослойных печатных плат оптимальным выбором является классическая технология металлизации с химическим меднением. Для плат высокой плотности с микроотверстиями более предпочтительны современные методы прямой металлизации.
В любом случае, выбор конкретной технологии должен осуществляться на основе тщательного анализа всех требований к изделию и возможностей производства.
Alex_EXE » Псевдо металлизация отверстий
Одна из самых сложных операций при изготовление двухсторонних плат в домашних условиях – это металлизация отверстий, которая требует кучи хим. реактивов и множество операций.
Самым простым способом прокинуть контакт с одной стороны платы на другую – является отверстие с проводником запаянных с обеих сторон. В качестве такого проводника может выступать вывод детали, если к нему есть доступ паяльника. Но на платах с плотным монтажом бывает достаточно сложно найти место под пару отверстий, а простые планарные детали вытесняются безвыводными. Что делать, если нужно будет на плате разместить панельку под многовыводную микросхему, где доступ к её выводам нужен с обеих сторон платы? Об альтернативном способе проложить контакт сквозь отверстие с деталью будет рассказано в статье.
Ответ прост: нужно заранее прокинуть в том же отверстие, где должен будет проходить контакт, проволочку, а лучше многожильный тонкий провод без изоляции, например зачищенный МГТФ.
Для того, что бы такую проволочку было удобно прокинуть – нужно на этапе проектирования печатной плате заложить отверстие большего диаметра и удлинённые площадки для запаивания проволочки с обеих сторон платы, или хотя бы под корпусом детали.
Дорожки с обратной стороны платы и под деталью
На подготовленной плате с обратной стороны платы, относительно корпуса детали, вставляем перемычку в отверстие.
Готовая к запайке перемычке двухсторонняя плата
С противоположной стороны, которая будет закрыта корпусом детали, пригибаем перемычку к контактной площадке и аккуратно припаиваем, не заливая отверстие оловом.
Запайка проволочки
Припаянная перемычка
Затем с противоположной стороны платы, откуда вводили перемычку, откусываем лишнее, оставив небольшой хвостик.
Откусываем лишнее от перемычки
оставив небольшой хвостик
Когда все перемычки будут прокинуты, вставляем деталь и запаиваем её выводы вместе с перемычками.
Все проволочки прокинуты
Деталь установлена
и запаяна
Запаянная деталь
К сожалению, такой способ псвевдо металлизации, не очень удобен и муторный, но на этапе прототипирования и при изготовление единичных конструкций может очень выручить.
Современные способы металлизации
Сегодня отрасль печатных плат переживает период значительных перемен. После нескольких лет расцвета, рынок вошел в стадию рецессии, отмеченную закрытием предприятий, сокращением издержек и общей нестабильностью. Ясным остается одно – выход из кризиса будет зависеть от способности отрасли эффективно внедрить технологии, позволяющие снизить затраты без ущерба качеству. Возможность добиться подобного результата есть у каждого предприятия.
В большинстве случаев наиболее эффективными оказываются вложения в автоматизацию производства, снижение объемов выбросов и запуск экономичных процессов, повышающих производительность. Что касается сквозной металлизации отверстий печатных плат, наиболее результативным способом оптимизации данного процесса является использование автоматических горизонтальных установок.
Согласно тенденции, прослеживаемой на мировом рынке, прямое меднение (химическое меднение) как способ металлизации отверстия печатной платы постепенно отходит на второй план. Это особенно заметно в азиатском и тихоокеанском регионах, а также ряде европейских стран. Основные причины этого явления перечислены ниже.
В Европе действует масса законов и предписаний, ограничивающих или запрещающих использование таких токсичных и канцерогенных веществ, как формальдегид и цианид. Кроме того, не стоит забывать о том, что в большинстве европейских стран значительно ужесточилось законодательство в отношении применения таких традиционных хелаторов, доказавших свою эффективность и стабильность в растворах химического меднения, как EDTA и «Qualdrol».
Характерной особенностью процесса химического меднения является последовательная цепочка реакций в газовой среде.
Успешное выполнение процесса химического меднения требует тщательного трудоемкого контроля. Это связано как с многочисленностью этапов данного процесса, так и с тем фактом, что используемый раствор с течением времени претерпевает значительные изменения.
По количеству образующихся выбросов, объему используемой воды и стоимости процессов очистки химическое меднение значительно превосходит прямую металлизацию.
Стоимость автоматизации горизонтальной установки химического меднения гораздо выше стоимости автоматизации подобного оборудования для прямой металлизации. При химическом меднении используется более дорогостоящее оборудование, требуется больше рабочего пространства и потребляется больше энергии.
Обзор рынка
В течение последних пяти лет в отрасли наблюдается активное внедрение процесса прямой металлизации. По началу этот метод, разработанный в начале 80-х годов, принимался рынком довольно настороженно. Первые процессы этого типа накладывали гораздо больше ограничений, чем химическое меднение. В середине 90-х годов большинство имеющихся процессов выпускались в усовершенствованном варианте.
Постоянная работа в этой области привела к созданию технологии, которая позволяет добиться результата, по многим параметрам превосходящего химическое меднение. В результате, начиная с 2000 года, прямая металлизация нашла широкое применение на рынке печатных плат.
Исследования
С момента создания первых процессов прямой металлизации различные исследовательские организации, отраслевые ассоциации, производители и поставщики занялись исследованиями с целью сравнения различных технологий и выявления лучшей. Наиболее всесторонним является обзор, выполненный Агентством по охране окружающей среды в 1998 году,
«Оценка альтернативных технологий изготовления печатных плат: проводимость отверстий». Эта работа совместно с «Анализом результатов испытаний технологий, предотвращающих загрязнение окружающей среды при производстве печатных плат» представляет собой сравнительную характеристику всех технологий прямой металлизации, имеющихся на отраслевом рынке. Кроме того, в них приведены различные способы водоочистки, организации бессточного производства, снижения риска для здоровья человека и состояния окружающей среды, рекомендуемые к использованию при производстве печатных плат.
С этими документами будет крайне полезно ознакомиться всякому, кто рассматривает возможность отказа от химического меднения и внедрения прямой металлизации.
Прямая металлизация: выбор технологии
Запатентованные процессы прямой металлизации отличаются еще большим разнообразием, чем технологии химического меднения. Каждый поставщик разрабатывает свой способ обработки сквозных отверстий. Чтобы выбрать подходящий Вам процесс металлизации, необходимо понять основный принцип действия этого способа, а, значит, и его химические и механические особенности.
Все существующие технологии металлизации условно делятся на три группы: с использованием палладия или других драгоценных металлов, с использованием угля или графита и с использованием проводящих полимеров.
Всем трем группам присущи преимущества, связанные с автоматизацией процесса и снижением объемов потребляемой и очищаемой воды. Однако только одна группа процессов обеспечивает селективное осаждение проводящего слоя при высокой проводимости финишного покрытия. Это свойство, типичное только для процессов металлизации, требующих образования проводящего слоя, зависит от типа используемого мономера и достигается в результате специфических реакций, происходящих в сквозных отверстиях.
Одной из таких систем металлизации, основанных на проводящих свойствах полимеров, является Envision® DMS-E. Ее использование обеспечивает селективное осаждение проводящей полимерной пленки на диэлектрической и стеклянной поверхности печатных плат (сквозных отверстий), без осаждения медного слоя. Основной принцип действия данной технологии заключается в том, что только каучуковые и стеклянные поверхности способны вступать в реакцию с окислителем, входящим в состав системы. Образующаяся в результате реакции оксидная пленка сообщает поверхности окислительную способность, необходимую для трансформации мономерного раствора в тонкий проводящий слой, в то время, как поверхность меди, не подвергшаяся воздействию окислителя, в реакцию не вступила.
Данная технология обладает целым рядом преимуществ. В отличие от других систем прямой металлизации этот процесс не создает нежелательного слоя на меди.
В случае применения некоторых палладиевых и всех угольных технологий после осаждения проводящего слоя требуется обработка медных участков сильным раствором травления и тщательная очистка. Травление необходимо для удаления с поверхности меди всех нежелательных примесей.
Это усложняет как сам процесс металлизации, так и последующую обработку сточных вод. Кроме того, сама процедура травления представляет собой техническую проблему. Чрезмерная интенсивность может привести к повреждению слоя палладия, угля или графита на диэлектрике в области, прилегающей к межслойным проводникам. Это, в свою очередь, негативно скажется на результате гальванической обработки сквозных отверстий. Наиболее типичным последствием подобного дефекта является пустоты в местах межсоединений (рис.1). Оно чаще всего называется среди недостатков большинства процессов прямой металлизации, требующих травления медного слоя, и исключено в случае с технологией образования проводящего слоя.
Технология прямой металлизации с образованием проводящего слоя оставляет медное покрытие в первоначальном состоянии, предусматривая лишь предварительную подготовку с помощью щетки в случае обработки двусторонних плат или дисмеринга в случае обработки двусторонних и многослойных печатных плат. Медь просто не от чего очищать перед нанесением сухой пленки или любого гальванического покрытия.
Данная технология не допускает возможности образования нежелательных пленок на межслойной поверхности многослойных плат вне зависимости от количества соединений. Исключается сам источник возможного дефекта межсоединений. Конечный результат использования этого процесса металлизации – исключительная сила сцепления слоя гальванической меди со стенками отверстия, а также всеми медными поверхностями, включая межслойные и поверхности микроотверстий.
Эти свойства крайне важны при производстве плат большой толщины, многослойных плат и плат с большим количеством микроотверстий.
Прямая металлизация микроотверстий
Несмотря на тот факт, что в течение последних 10 лет прямая металлизация получила широкое распространение, которое постоянно растет, остались и сторонники химического меднения, которые настаивают на преимуществах использования этого процесса, в особенности при изготовлении высокотехнологичной продукции, например, для обработки микроотверстий и отверстий с большим отношением длины к толщине покрытия. Однако капитальные и текущие расходы, связанные с применением химического меднения, значительно превышают сумму, требующуюся для внедрения альтернативной технологии.
Значительная экономия затрат возможна уже благодаря одному только снижению водопотребления и сокращению объемов выбросов (таб. 1). Кроме того, к неблагоприятной смете химической металлизации следует добавить стоимость палладия, который за последние несколько лет невероятно поднялся в цене. Палладий – необходимый компонент ряда процессов прямой металлизации и всех без исключения процессов химического меднения. В результате роста стоимости этого металла расходы, связанные с выполнением процесса химического меднения, увеличились на 50%.
Для многих предприятий немаловажным фактором является экологическая безопасность процесса. В подобном случае производитель печатных плат полностью переходит на использование прямой металлизации, включая обработку микроотверстий. Прямая металлизация считается менее опасной для окружающей среды, поскольку при ее выполнении используется меньшее количество токсичных веществ. В случае с металлизацией через нанесение проводящего слоя исключается использование металлов, сильных комплексообразователей или высокотоксичных материалов. Переработка отработанного электролита не требует больших расходов. По сравнению с химическим меднением прямая металлизация отличается пониженным расходом воды для промывки – менее одного м3 в час.
Технологический процесс прямой металлизации с нанесением токопроводящего слоя исключительно короток. Размеры установки, стоимость оборудования, рабочая площадь и длительность обработки — в несколько раз меньше, чем при химическом меднении. Что касается использования технологии прямой металлизации для обработки микроотверстий, следует уделить особое внимание не только составу раствора, но механическим особенностям процесса (горизонтальное нанесение). Было установлено, что наиболее значительными факторами при горизонтальной обработке являются контроль и оптимизация процесса нанесения покрытия.
Кондиционирование
Для кондиционирования используется водный раствор веществ, активирующих диэлектрические и стеклянные поверхности.
Обработка в перманганате
Это основной этап образования проводящей пленки. На данной стадии происходит химическая реакция, в результате которой исключительно на каучуковых и активированных стеклянных поверхностях образуется оксидный слой, который представляет собой пленку двуокиси марганца. Эта пленка является непременным условием последующей реакции полимеризации.
Количество двуокиси марганца на поверхности отверстия имеет довольно большое значение.
Толщина слоя образуемой пленки контролируется химическим и механическим способами. Возможность влиять на процесс нанесения покрытия механическим способом является одним из наиболее ценных достижений разработчиков для производителей многослойных печатных плат.
Воздействие катализатором
Этот этап положен в основу технологии. Катализатор содержит мономер и органическую кислоту. Реакция происходит мгновенно Под воздействием кислоты слой двуокиси марганца вступает в реакцию с мономером, образуя проводящую полимерную пленку, а марганец восстанавливается до Mn+2. Вступая в реакцию с мономером, двуокись марганца никогда не оставляет никаких следов марганца на стенках отверстия.
После завершения реакции на диэлектрических и стеклянных поверхностях печатной платы остается сплошная тонкая (околот0,2 микрон) проводящая пленка.
Скорость реакции, при обычных условиях занимающей не более 60 секунд, может быть увеличена с помощью использования ультразвука. В случае обработки сверх микроскопических отверстий или отверстий с чрезвычайно высоким отношением длины к толщине слоя (>10:1) применение ультразвука обязательно.
Промывка
Обработка в соли марганцевой кислоты сопровождается рядом операций промывки, которые требуют менее тщательного контроля. После традиционной промывки в воде, печатная плата обрабатывается кислотой и ополаскивается. Промывки в данном случае выполняют двойную функцию: обработка в кислоте поддерживает в необходимом для дальнейших операций состоянии пленку двуокиси марганца, а также восстанавливает поверхность меди, сохраняя ее первоначальное состояние.
Свойства электропроводящих полимеров
В результате углубленного изучения свойств электропроводящих полимеров, а также процесса осаждения меди на полимерную поверхность, было установлено, что меднение происходит в результате формирования скоплений кристаллов меди небольшого размера, формирующихся на определенных расстояниях друг от друга.
Эти кристаллы быстро увеличиваются в размерах и сливаются друг с другом, покрывая поверхность отверстия. В результате на поверхности образуется плотная поликристаллическая пленка. Скорость образования медного слоя зависит как от качества проводящего полимера, так и от типа и количества органических добавок, введенных в электролит электролитического меднения.
Результаты экспериментов
Первоначально для изучения воздействия незначительных изменений оборудования, интенсивности нанесения раствора, вращательного движения и времени воздействия были использованы уже имеющиеся на предприятии горизонтальные линии обработки. На начальных этапах исследования горизонтальные процессы ограничивались нанесением проводящей пленки. Электролитическое меднение выполнялось на стандартной вертикальной установке.
При обработке микроотверстий размером более 100 микрон (отношение длины к толщине слоя 1:0,5) высокие результаты были получены на всех видах испытуемого оборудования (рис. 2).
При обработке микроотверстий размером около 80 микрон (отношение длины к толщине слоя 1:0,625) сократилась кроющая способность, однако результаты были относительно высокими (рис. 3).
При обработке микроотверстий размером менее 80 микрон различные модификации оборудования приводили к улучшению результатов. Предпринятые меры включали увеличение количества подвесок при снижении напора подачи электролита и использование ультразвука.
При обработке микроотверстий размером 50 микрон (отношение длины к толщине слоя 1:1,20) требуется нанесение меди электрохимическим способом только с использованием горизонтальной установки (или вертикальной модели, работающей с возвратно-поступательным движением) (рис. 4).
Вывод
Сегодня, более, чем когда-либо, мы должны обращать особое внимание на то, какой подход мы выбираем к ведению своего бизнеса.
Чтобы выжить в условиях жесткой конкуренции, уже недостаточно использовать тот или иной процесс только потому, что он с успехом применялся Вами в прошлом.
Основное внимание по-прежнему уделяется надежности и качеству продукции. Оценивая технологию, мы должны опираться на критерии оценки качества собственного производства. Без сомнения, прямая металлизация – процесс, который способен обеспечить качественную обработку изделия, отличаясь при этом простотой в применении, экономичностью, возможностью автоматизации, экологической безопасностью, пониженным потреблением воды и энергоресурсов и целым рядом других преимуществ.
Варианты исполнения печатных плат с глухими и скрытыми отверстиями
Рано или поздно любой инженер-разработчик многослойных печатных плат (МПП) сталкивается с необходимостью применения несквозных переходных отверстий. Это может быть связано с увеличением плотности монтажа, использованием BGA с маленьким шагом выводов, необходимостью иметь переходное отверстие в SMT-площадке, невозможностью организовать площадки для переходных отверстий на обратной стороне платы или с другими факторами. К сожалению, в промышленности нет единого стандарта на проектирование и выполнение таких отверстий. Как правило, все определяется технологическими возможностями конкретного производства МПП. Однако можно обобщить некоторые принципы, следование которым позволит инженеру спроектировать многослойную плату наиболее технологичным образом, так, чтобы ее можно было заказать практически на любом современном производстве.
Рассмотрим поперечное сечение печатной платы («микрошлиф», или microsection) на рис. 1. Мы можем увидеть шесть слоев меди, причем второй, третий, четвертый и пятый соединены переходным отверстием, не выходящим на наружные слои. Кроме того, первый слой соединен со вторым при помощи микроотверстия. Это наиболее типичный вариант использования несквозных отверстий. Далее мы рассмотрим, какие бывают виды несквозных отверстий, методы их формирования и основные параметры.
Терминология
В мире сложилась определенная терминология обозначения видов несквозных отверстий. К сожалению, в русском языке один и тот же вид имеет несколько обозначений, и иногда они применяются некорректно или неоднозначно. Мы будем пользоваться следующей терминологией:
Blind via — «глухие» или «слепые». Имеются в виду отверстия, соединяющие наружный слой с одним или несколькими внутренними.
Buried via — «скрытые», «погребенные», «встроенные». Это переходные отверстия, не выходящие наружу и соединяющие между собой сигналы на внутренних слоях.
Micro-via, или uVia — «микроотверстия». Подразумеваются отверстия малого диаметра и малой глубины, выполненные лазером или сверлением с контролем глубины и соединяющие внешний слой с внутренними.
HDI (High Density Interconnection) — «соединения высокой плотности». Общее название класса МПП высокой плотности с глухими и скрытыми отверстиями.
Выбор конструкции МПП
Наше глубокое убеждение, основанное на многолетнем опыте проектирования и приема заказов МПП с глухими и скрытыми отверстиями, состоит в следующем: Выбор конструкции должен производиться в самом начале проектирования МПП, и перед началом проектирования эта конструкция должна быть согласована с заводом-изготовителем!
Нередко разработчик печатной платы закладывает структуру отверстий HDI исходя из собственных представлений, никак не связанных с возможностями конкретного производства, или же добавляет их «на ходу», исходя из потребностей уже «почти страссированного» проекта, в котором немножко не хватило места. Последствия могут быть самыми печальными, как для разработчика (в дальнейшем приходится переразводить плату под другие требования), так и для компании в целом (неизбежные потери времени и денег, связанные с поиском подходящего производителя и увеличением срока и стоимости заказа). Случается, что спроектированная вот так, необдуманно, конструкция МПП с HDI нереализуема в принципе, ни на одном из существующих в мире производств, или же стоимость реализации на порядок превышает бюджет проекта.
Рассмотрим, какие основные факторы следует принимать во внимание при начальном формировании конструкции печатной платы.
Факторы, связанные с выбором конструкции МПП
1. Размещение слоев МПП (питающие, земляные, сигнальные, теплоотводящие) — требования инженера-схемотехника, рекомендации от производителей сложных BGA-корпусов.
2. Расположение в слоях, а также параметры сигналов с контролируемым импедансом (по требованию схемотехника) и расчет волнового сопротивления.
3. Виды и размещение глухих и скрытых переходных отверстий — технологические возможности поставщика, типовые конструкции.
4. Выбор материалов (диэлектрические и медные слои, теплоотводящие слои) — требования схемотехника и возможности поставщика ПП.
Таким образом, при формировании конструкции печатной платы задача инженераконструктора — оптимальным образом совместить требования от разработчика схемы с возможностями производителя плат.
Не будем подробно останавливаться на выборе материалов и толщины слоев — это тема отдельной статьи. Наша задача — понять, как выбрать конструкцию платы, пригодную для производства. Для этого рассмотрим основные методы формирования несквозных переходных отверстий.
Формирование скрытых отверстий
Методы формирования скрытых отверстий на внутреннем ядре (или на «частичном пакете») схожи по технологии с тем, как выполняются сквозные металлизированные отверстия. При проектировании МПП следует учитывать, что при металлизации таких отверстий на медной поверхности соответствующих слоев платы (например, слой 2 и 5 на рис. 1) происходит осаждение меди, дополнительно от 25 до 45 мкм. Поэтому при расчете, например, минимально допустимой ширины проводников в таких слоях их толщину надо брать с учетом металлизации.
Таким образом, для варианта, представленного на рис. 1, сначала прессуется пакет из слоев 2–5, например:
====== ядро FR4 0,36 мм, фольга с двух сторон 35 мкм;
~~~~~~ препрег, несколько слоев;
====== ядро FR4 0,36 мм, фольга с двух сторон 35 мкм.
В этом пакете, как в готовой плате, сверлятся и металлизируются сквозные отверстия. Затем они заполняются смолой, и пакет прессуется в составе печатной платы:
––––––– фольга 18 мкм + металлизация, итого 45–55 мкм;
~~~~~~ препрег, несколько слоев, общая толщина 0,2 мм;
====== ядро FR4 0,36 мм, фольга 35 мкм + металлизация;
~~~~~~ препрег, несколько слоев;
====== ядро FR4 0,36 мм, фольга 35 мкм + металлизация;
~~~~~~ препрег, несколько слоев, общая толщина 0,2 мм;
––––––– фольга 18 мкм + металлизация.
Так как происходит два этапа прессования и металлизации отверстий, стоимость изделия увеличивается примерно в полтора–два раза.
Пример из реальной практики
Неопытный разработчик прислал проект МПП 6 со скрытыми отверстиями между слоями: 2–3, 2–4, 2–5, 3–4, 3–5, 4–5. Разработчик обосновывает такой набор скрытых отверстий упрощением и ускорением автоматической трассировки платы, так как готовые платы ему нужно получить срочно.
Результат:
Такой проект очень сложен в реализации. Невозможно разбить комбинации слоев на частичные пакеты, так как номера слоев в них пересекаются. В итоге разработчик потерял несколько недель на поиск производителя и был вынужден переразводить плату вручную, изменив структуру на следующую: 2–3, 2–5, 4–5. Для реализации такой конструкции выполняются металлизированные отверстия в ядре 2–3 и ядре 4–5, затем прессуется пакет 2–5 и выполняется металлизация отверстий в нем. Дальнейший анализ показал, что плату можно было страссировать, обойдясь только скрытыми отверстиями 2–5 и микроотверстиями 1–2 и 5–6.
Методы формирования микроотверстий
Один из популярных видов несквозных отверстий — так называемые микроотверстия.
Они формируются на уже спрессованном пакете МПП путем лазерного сверления или механическим сверлением с контролем глубины. Затем эти отверстия металлизируются одновременно с металлизацией сквозных отверстий и проводников на поверхности платы.
На рис. 2 приведены фотографии микроотверстий, сформированных различными методами. Общее свойство микроотверстий — их глубина не должна превышать диаметр, в противном случае невозможно обеспечить качественную металлизацию стенок.
Материалы внешних слоев для микроотверстий
Как известно, наиболее популярная структура слоев МПП подразумевает выполнение наружных слоев из фольги со слоями препрега (смолистых прокладок). В том случае, если требуется выполнение микроотверстий, также используется эта структура, и микроотверстие выполняется в слое препрега. Кроме того, часто в качестве наружного слоя применяется специальный материал — RCC (resin coated copper, «фольга со смолистым слоем»). RCC — это материал, созданный специально для плат с микроотверстиями, его отличие от обычных материалов в том, что в нем отсутствуют нити стекловолокна. Это делает стенки микроотверстий более качественными.
Пример
Типичная ошибка инженеров-конструкторов — применение микроотверстий с глубиной, превышающей их диаметр.
Предположим, что мы проектируем МПП, количество слоев — 6, общая толщина — 1,6 мм, толщина диэлектрика между слоями 1–2 задана как 0,2 мм (исходя из соображений обеспечения импеданса 50 Ом для линий шириной 0,35 мм на слое Top относительно земляного слоя Int1).
Структура МПП может быть следующей:
––––––– фольга 18 мкм + металлизация, итого 45–55 мкм;
~~~~~~ препрег, несколько слоев, общая толщина 0,2 мм;
====== ядро FR4 0,36 мм, фольга с двух сторон 35 мкм;
~~~~~~ препрег, несколько слоев;
====== ядро FR4 0,36 мм, фольга с двух сторон 35 мкм;
~~~~~~ препрег, несколько слоев, общая толщина 0,2 мм;
––––––– фольга 18 мкм + металлизация.
Предположим, мы решили, что для удобства трассировки нам нужны микроотверстия с 1-го на 2-й слой (GND) и с 1-го на 3-й слой (сигнальный). Будет ошибкой делать эти микроотверстия с одинаковым диаметром, например, 0,2 мм с площадкой 0,5 мм. Однако такие некорректные проекты — не редкость в нашей практике. К сожалению, они нереализуемы и нуждаются в переделке.
В самом деле, мы видим, что первый вид микроотверстий должен быть выполнен на глубину 0,2 мм, а второй вид — на глубину 0,2 + 0,035 + 0,36, итого 0,6 мм. Таким образом, исходя из условия «1:1», диаметр для первого вида микроотверстий составит 0,2 мм, с площадкой 0,5–0,6 мм, а диаметр для второго вида — не менее чем 0,6 мм, с площадкой 1 мм. Такой довольно большой размер площадки может свести на нет все преимущества от применения микроотверстий.
Заметим, что (с нашей точки зрения) не очень технологично выполнять микроотверстия в ядре FR4. Можно использовать другую структуру, с последовательным наращиванием слоев препрега и фольги, например:
––––––– фольга 18 мкм + металлизация;
~~~~~~ препрег, несколько слоев, общая толщина 0,2 мм;
––––––– фольга 35 мкм;
~~~~~~ препрег, общая толщина 0,1 мм;
====== ядро FR4 0,8 мм, фольга с двух сторон 35 мкм;
~~~~~~ препрег, общая толщина 0,1 мм;
––––––– фольга 35 мкм;
~~~~~~ препрег, несколько слоев, общая толщина 0,2 мм;
––––––– фольга 18 мкм + металлизация.
В этом случае диаметр отверстия между слоями 1–3 может составлять всего 0.34 мм, с площадкой 0,65–0,75 мм, что существенно упростит трассировку МПП.
Разумеется, мы рассмотрели некий гипотетический пример, но он отражает общую схему рассуждений при выборе конструкции печатной платы.
Параметры микроотверстий
На рис. 3 и в таблице показаны минимально допустимые параметры лазерных микроотверстий. Мы рекомендуем при разработке конструкции МПП запросить подобную таблицу у поставщика печатных плат.
Типовые конструкции МПП 4
Давайте посмотрим, какие могут быть основные варианты конструкции ПП. На рис. 4 показан вариант с ядром внутри и микроотверстиями снаружи.
Тип материала и толщина ±30% |
Отверстие, мкм |
Внешняя площадка, мкм |
Внутренняя площадка, мкм |
1 x RCC 60 мкм | 100 | 300 | 330 |
1 x 106 p/p 50 мкм | 100 | 300 | 330 |
и минимум | 90 | 250 | 300 |
1 x 1080 p/p 65 мкм | 120 | 330 | 380 |
и минимум | 100 | 300 | 350 |
2 x 106 p/p 100 мкм | 150 | 360 | 400 |
Материал внешнего слоя, варианты:
1. Материал RCC толщиной 60 мкм, отверстие 90 мкм.
2. Препрег «106» толщиной 45 мкм, отверстие 90 мкм.
3. Препрег «1080» толщиной 65 мкм, отверстие 100 мкм.
4. Препрег 2 х «106», толщина 100 мкм, отверстие 150 мкм.
Тип материала
Может быть использован материал типа FR4, FR4 без галогена, FR4 High Tg (высокотемпературный), FR4 Low CTE (высоковольтный). Однако не может быть использован СВЧ-материал типа Ro4003 и др.
Мы рекомендуем закладывать в стоимость МПП с HDI-структурами высокотемпературный материал типа FR4 High Tg. Он менее подвержен деградации при термоударе, возникающем при нанесении покрытия HAL, а также при монтаже компонентов. Таким образом, применение High Tg материала повышает надежность и долговечность МПП с глухими и скрытыми отверстиями.
Скрытое отверстие
Обратите внимание, что в приведенной выше структуре во внутренних слоях выполнено «скрытое» отверстие со слоя 2 на слой 3. Технология исполнения таких отверстий, как мы видели ранее, схожа с технологий изготовления обычных сквозных металлизированных отверстий, с последующим заполнением смолой и прессованием в составе пакета МПП. Заметим, что выполнение микроотверстий непосредственно над «скрытым» отверстием невозможно, так как в этом месте во внутреннем слое находится не сплошная площадка, а медное кольцо с отверстием в центре.
На рис. 5 показана другая структура — в этом случае внешние слои выполнены из «ядер» FR4, склеенных слоями препрега.
Способ изготовления такой структуры: сначала выполняется сквозная сверловка и металлизация отверстий отдельно в каждом из ядер, затем формируется рисунок проводников на внутренних поверхностях ядер и производится прессование пакета МПП. С точки зрения производства такая последовательность операций является менее технологичной, так как требует выполнения дополнительных этапов металлизации отверстий. Однако при отсутствии оборудования для сверления микроотверстий это единственно возможный вариант.
Заметим, что в данной структуре, в отличие от предыдущей, в слоях с глухими отверстиями возможно применение СВЧ-материала.
На основании приведенных выше 4-слойных структур можно строить комбинации с большей слойностью, однако не следует злоупотреблять сложностью и многообразием видов глухих и скрытых отверстий. Опыт показывает, что при выборе между добавлением в проект еще одного вида несквозных отверстий и добавлением еще одной пары слоев правильнее будет добавить пару слоев. В частности, для микросхем BGA с шагом 1 мм и даже 0,8 мм нет необходимости в применении несквозных отверстий. Для BGA с шагом 0,65 мм и 0,5 мм без несквозных отверстий, пожалуй, не обойтись. В любом случае, конструкция МПП должна быть спроектирована с учетом того, как именно она будет реализована в производстве.
Пример из практики
Один из наших заказчиков прислал проект МПП 12 слоев со структурой глухих отверстий 1–2, 1–4, 1–6, 12–11, 12–9, 12–7. Предполагается, что она реализуется в три этапа прессования, путем металлизации частичных пакетов 1–2 и 12–11, затем 1–4 и 12–9, потом 1–6 и 12–7. После этого выполняется последнее прессование и металлизация сквозных отверстий. Однако заметим два слабых места такой конструкции:
А) На каждом этапе металлизации на проводниках на слое Top формируется дополнительный медный слой от 25 до 40 мкм. Таким образом, после четвертого цикла к толщине фольги добавится от 100 до 160 мкм меди, что делает невозможным обеспечение проводников и зазоров шириной менее чем 0,4 мм. Имеется специальный метод, позволяющий частично снять этот дополнительный слой меди, однако это не вполне технологичная операция, снижающая выход годных и повышающая стоимость плат.
Б) Кроме того, мы выполняем три итерации прессования. На каждой из них взаимное смещение слоев может достичь 0,05–0,075 мм, в результате чего после трех прессований мы получаем пакет, в котором все проводниковые слои могут быть смещены в произвольных направлениях на величину до 0,15–0,2 мм. Если мы просветим такую плату рентгеном в месте расположения площадок переходного отверстия, то увидим так называемую «ромашку» (рис. 6) — рассовмещенные площадки в слоях. Чтобы учесть такое смещение, надо предусматривать в проекте гарантийный поясок не менее 0,25 мм. Это означает, что для переходных отверстий 0,2мм применяются площадки не менее чем 0,7 мм.
Типовые конструкции многослойных плат HDI
На рис. 7 приведены примеры типовых конструкций МПП, в порядке увеличения сложности. Мы рекомендуем придерживаться этих структур, это позволит вам без особых проблем разместить заказ на изготовление МПП. Коэффициент увеличения стоимости показан на рисунке для различных структур условно, в среднем он составляет от 50% до 200% от стоимости заказа, в зависимости от его сложности и объема. Заметим, что применение глухих отверстий иногда может привести к удешевлению проекта в целом, за счет экономии на общем количестве слоев, лучшей трассируемости, уменьшения размера печатной платы, а также возможности применить компоненты с более мелким шагом. Однако в каждом конкретном случае решение об их применении следует принимать индивидуально и обоснованно.
Приведены только основные, наиболее технологичные и наименее дорогостоящие варианты выполнения несквозных отверстий и их комбинаций. Разумеется, есть множество более сложных технологий, позволяющих, например, разместить микроотверстие непосредственно над скрытым отверстием или сделать «стек» из нескольких микроотверстий, или заполнить микроотверстие медью для формирования ровной площадки. Но это, пожалуй, тема для отдельной большой публикации.
Рекомендации
Мы настоятельно советуем: не усложняйте конструкцию печатной платы и обеспечивайте полностью симметричную структуру слоев и отверстий. Если не обойтись без более сложной структуры отверстий, обязательно обратитесь к поставщику печатных плат перед началом проектирования. В частности, инженеры компании PCB technology могут проконсультировать вас по вопросам проектирования таких печатных плат и дать примеры реализации и оформления подобных проектов.
Печатные платы – Завод ЭЛЕКТРОКОННЕКТ
На сегодняшний момент на всех производствах печатных плат, в том числе и у нас, существуют входные требования к крепёжным отверстиям, обусловленные технологией производства печатных плат и общей технологичностью применения печатных плат при монтаже и изделия в целом. Крепёжные отверстия можно разделить на два вида: первый – крепёжные отверстия для крепления печатной платы к несущим элементам конструкции РЭА; второй – крепёжные отверстия для крепления навесных елементов, в т.ч. разъёмов, к печатной плате. Исходя из этого, требования к изготовлению этих отверстий разные:
- для крепёжных отверстий для крепления печатной платы к несущим элементам необходима точность совмещения крепёжного отверстия и контура печатной платы; для крепёжного отверстия разъёма необходимо точное совмещение с отверстиями выводов разъёма, т.е. с топологией рисунка.
При серийном производстве печатных плат по умолчанию все отверстия диаметром до 4,5 мм, включая крепёжные, сверлятся за одну операцию на станках с ЧПУ и являются отверстиями с металлизацие. Это обусловлено стандартной технологией химобработки печатных плат. Такие отверстия полностью удоблетворяют требованиям к точному совмещению с отверстиями выводов разъёма, а точность совмещения с контуром платы может составлять ± 200 мкм, что в большинстве случае некритично. С конструктивной точки зрения металлизация таких крепёжных отверстий не влияет на качественные параметры печатной платы, кроме того, в некоторых случаях эти отверстия служат дополнительным соединеним слоя (или цепей) «земля» с элементами несущих конструкций. Но так же следует иметь в виду и мнение технологов по сборке – они категорически возражают против металлизации любых крепёжных отверстий: при вкручивании винта/шурупа на стенках металлизированного отверстия может получиться металлическая стружка, она попадёт на плату и вызовет короткое замыкание. Но зачастую это происходит только из-за того, что отверстия заложены впритык под винт, а при сборке в блоке отверстия «гуляют». Здесь решение простое – заранее зная все погрешности отверстий, можно определить необходимый размер крепёжного отверстия и/или подобрать винты с нужным соотношением длины резьбы и «голой шейкой», при котором таких стружек не будет. Если в каких-то отверстиях металлизация недопустима, такие отверстия при производстве печатных плат сверлятся на конечном этапе фрезеровки контура платы, и эти отверстия полностью удовлетворяют требованию к точному совмещению с контуром платы, а точность совмещения с металлизированными отверстиями составит ± 200 мкм, что может быть критично для некоторых элементов и разъёмов со специфичным креплением к печатной плате (встраиваемые в контур, с пластиковыми фиксаторами Fit-Contact и т.п.). Поэтому при разработке проекта печатной платы конструктор должен учитывать все эти факторы и требования, взвешенно указывая наличие/отсутствие металлизации крепёжных отверстий, при размещении заказа на производство и закладывать крепёжные отверстия, удовлетворяющие требованиям как технологов по сборке, так и технологов производства печатных плат – этим достигается технологичность и низкая себестоимость печатной платы. В противном случае при предъявлении противоречивых требований к металлизации крепёжных отверстий и точности их совмещения как с контуром платы, так и с монтажными металлизированными отверстиями, производитель вынужден идти на технологические ухищрения. В нашем случае, из-за требования заказчика при отсутствии металлизации в крепёжных отверстиях разъёма и высокой точности совмещения с монтажными металлизированными отверстиями под контакты, мы вынуждены применять технологию тентирования крепёжных отверстий, отсверленных на этапе сверловки до меднения. Эта технология не гарантирует отсутствия остатков металлизации в отверстиях диаметром более 2 мм из-за несовершенства струйных процессов при травлении фоторезиста: под струями агрессивных травильных растворов рвётся тонкая плёнка, закрывающая отверстия.
В результате и у производителя и у заказчика растёт объём отбракованных печатных плат, не проходящих ОТК по причине наличия остатков металлизации в отверстиях. Чтобы как-то справиться с этой ситуацией, мы вынуждены либо увеличивать объём дозапуска печатных плат для компенсации брака и сроков, либо доабатывать отверстия, удаляя вручную металлизацию со стенок отверстий, из-за шероховатости стенок отверстий эта операция становится весьма трудоёмкой, металлизаций до конца не всегда удаляется, и в значительной степени «страдает» геометрия отверстий. Эти мероприятия приводят к значительному повышению себестоимости печатных плат, что приводит к повышению цены заказа и не выгодно ни заказчику, ни производителю. В такой ситуации видятся следующие решения: [numlist] Если для заказчика на первом месте стоит «технологичность + низкая себестоимость» печатной платы, то выбрать соответствующий тип металлизации крепёжных отверстий, с внесением изменений в КД с учётом допусков на металлизацию. Если для заказчика на первом месте точность совмещения отверстий и нежелательность металлизации + низкая себестоимость печатной платы, то снизить требования к остаткам металлизации в отвертиях (из-за причин отмеченных выше). Если компромисс невозможен, то ожидать от производителя значительного увеличения стоимости заказов, либо отказа от производства. [/numlist]
Самодельная печатная плата и переходные отверстия
Занимаясь разработкой печатных плат в домашних условиях часто сталкиваешься с проблемой «рельефных» переходных отверстий. Обычно на самодельных двухслойных платах переходный контакт паяется с обеих сторон тонким залуженным проволокой, результат устраивает но не тогда когда нужно сделать переходный контакт под микросхемой с корпусом TQFP48, SOIC16 если контакт очень рельефный то будет просто невозможно аккуратно припаять микросхему так как ее ножки будут висеть в воздухе.Предлагаю вам свой вариант создания плоских переходных отверстий.

Создание качественной платы начинается с разработки качественного трафарета для засветки фоторезиста. Плату я создаю в программе EAGLE она очень удобна и в сети достаточно библиотек элементов для нее и примеров использования.
1. Плату вырезаем с запасом по 12 мм с каждой стороны от результирующего размера платы.
2. Перед нанесением фоторезиста плату тщательно шлифуем нулевкой (особенно края от заусенцев) моем губкой с порошковым моющим средством типа «Гала»
Поверхность платы обычно грязная и жирная том моем и прополаскивают до тех пор пока порошок на губке перестанет становиться грязного цвета.
3. Тщательно сушим плату, если надо быстро можно использовать фен для пайки SMD.
4. Фоторезист Pozitiv 20 наносим за один раз и на всю поверхность платы.
5. Даем фоторезисту высохнуть в течение 1 часа разместив ее в горизонтальном положении в темном месте.
6. Пора трафарета. Испытав различные методы самостоятельно печатать трафареты, я остановился на варианте промышленного пленочного трафарета.
Заказываю его на фирме производящей визитные карточки и полиграфию, услуга называется «Фотовывод на пленку». Плату печатаю из Eagle через Bullzip pdf printer и импортирует CorelDraw этот файл и отдаю на печать в фирму. Трафарет получается идеальный, у меня получается делать с ним дорожки 0.2 мм. Заказывают обычно пленку формата А4 на нее помещается много платок моих и моих друзей.
7. Трафарет накладываем на плату с фоторезиста и засвечиваем УФ лампой в течение 3 минут.
8. После засветки даем фоторезиста полимеризоваться потом оставляем его в темном месте на 40 минут.
9. Проявляем плату в растворе NAOH (можно также использовать средство для прочистки труб «Крот» это тот же самый NAOH и он доступен в хозяйственных магазинах) в пропорциях указанных на баллоне с фоторезиста.
10. Даем плате высохнуть.
11. Нижнюю часть заклеиваем скотчем.
12. Травим плату в хлорной железе.
13. После того как плата вытравилась для точного позиционирования нижнего слоя сверлим 2-3 контрольные отверстия через них мы выставим нижний трафарет на просвет отверстий. Здесь важно высверлить отверстия перпендикулярно для поверхности платы. Для этого я сделал простой станочек из моторчика от струйного принтера и каретки от CD привода в качестве обратной пружины сейчас используются денежные резинки))))).
14. Для нижней части платы повторяем пункты 2 -12
Получаем такую штуку.
это именно та плата с дорожками 0.2мм. Обратите внимание на отступы по бокам платы они нам еще понадобятся
15. Сверлим остальные отверстия.
16. Лудим плату.
17. Переходим именно к переходным контактов.
17.1 Отрезаем медный проводок 0.2мм диаметром.
17.2 Лудим его.
17.3 Расплющиваем его на расстояние равное радиусу VIA.
17.4 Загибаем расплюснутый кончик на 90 градусов.
17.5 Вставляем в отверстие и запаиваем его с лицевой стороны.
17.6 Запаиваем его с задней стороны (расплюснутый кончик не даст выпасть проволочке).
17.7 Повторяем со всеми отверстиями.
18. Финальный аккорд. Шлифуем рельефные переходные контакты с обеих сторон, с помощью вот такого устройства
сделанного из алюминиевого уголка с наклеенной на него наждачной бумагой (клеится с помощью двойного скотча)
Шлифуем до желаемой высоты переходных контактов.
Вот тут нам и пригодились отступы на плате они берут удар на себя и не дают «Шкурнику» повредить границы результирующей платы.
Вуаля опрятные платы без ляпов и подгибки ножек!
TQFP48
SOIC16
Оригинал статьи на украинском языке
Прямая металлизация печатных плат… — Ормикс Инжиниринг
Доброго Дня! Не следует думать, что печатные платы при всем своем подобии изготавливаются одинаково, Многие десятки лет технологии их производства развивались, исправлялись ошибки, расширялись возможности, разрабатывались новые реагенты и оборудование. Это закономерный процесс. А все профильные институты, производственные лаборатории и заводы служили огромной испытательной площадкой. Множество технологий развивалось параллельно. Каждая со своими преимуществами и недостатками. Наш «Ормикс Инжиниринг», как и любая другая компания, решившая заняться производством печатных плат, взвешивала «за» и «против».
Историческая справка. Уже 50 лет для сквозной металлизации отверстий использовался палладий в качестве катализатора, создавая центры активации для последующего химического меднения. Только в последние 15 лет все зарубежье мощно двинулась к процессам прямой металлизации в которых создается неразрывная проводящая пленка по диэлектрику, исключающую необходимость химического меднения, Прямая металлизация позволила сразу наращивать плотную, пластичную гальваническую медь без всяких промежуточных слоев.
В 2005 году мы решились на современную технологию Прямой Металлизации. На базе реагентов Шведского концерна J-Кем. Сейчас с полной ответственностью говорим — это единственно правильное решение для нас. Внедрение, адаптация и всестороннее изучение позволило достичь высокого качества и воспроизводимости процесса. Правда, последнее, что нам окончательно помогло – это использование анодов из меди, производства Германии. Отличная равномерность, большая эффективность эрозии и оптимальные режимы осаждения.
Достоинств у прямой металлизации множество. И прямых, и сопутствующих. Это и отсутствие рыхлого слоя из химической меди и отличная адгезия гальванической меди к любым материалам. Дополнительно, высокая пластичность и практически справочная электропроводность. А чего стоит сама идея, что медь устилает единым сплошным покрывалом одну сторону печатной платы через отверстия на другую. Это значит, что нет границы между материнской медью на диэлектрике и медью гальванической. Отличное покрытие тонких отверстий с соотношением глубины к диаметру вплоть до 20. Так же уверенное покрытие глухих полостей и отверстий. Результатом прямой металлизации являются весьма надежные переходы, способные выдержать жесткие условия сборки и эксплуатации. Расслаиваться нечему – покрывало одно. Нет нужды делать его толстым и рыхлым из-за технологических ограничений. Достаточно сделать его качественным и однородным с исходной медью диэлектрика.
Естественным нашим желание было самим проверить, а так ли хороша прямая металлизация? Правда, подобное тестирование мы делали спустя несколько лет. Когда освоили ее должным образом. В подтверждение описываем несколько показательных тестов.
Тест электропроводности. Тест №1_А,В,С. Мы создали структуры меандров шириной в 1 mm и длинной 1M на фольге из материнской меди толщиной в 18um (А). И такие же меандры из нашей гальваномеди (В), осажденной с рассеивающей добавкой J-Kem J-plate_Cu400. Толщина выращенного слоя 18 um по двухмикронной материнской фольге (стравленной специальным полирующим травителем, Яп.). И контрольный меандр 18+18 um (С). Удельное сопротивления тестов: А = 0,0169 Ohm х M/mm2, B = 0,0170, C = 0,0170. Сами видите, Это практически одна и таже медь. Очень близко к теоретическому значению — 0,0168. Гальваномедь подтверждает свои характеристики и дальше по процессу. В противостоянии окислению и неизменности скорости травления. К сожалению, не сохранилась сама тестовая заготовка с 2009 года, а только результаты. Технологии в которых использованы процессы химического осаждения меди, с их рыхлой структурой, делают осадок более хрупким, что ухудшает электропроводность до 0,02 — 0,024 Ohm х M/mm2. Это делает переходы менее надежными. Так что Прямая Металлизация нас убедила.
Тест термоэлектроустойчивости. Тестовая плата с семейством стандартных проводников шириной 1 — 2 mm и переходными отверстиями по 0,7-1,5 mm. Пропускание запредельного тока, например в 30-50 Ампер, почти мгновенно приводило к выгоранию самого слабого участка на пути тока.
Обратите внимание, что перегорают только проводники на поверхности платы. Тест показателен тем, что мгновенно выявляет даже минимальные дефекты. В них лавинообразно развивается зона перегрева из-за местного роста удельного сопротивления. Даже однопроцентное ослабление металлизации определится безусловно. Как видите, все металлизированные отверстия выдержали. И не только. При рассмотрении в микроскоп, мы не увидели в них каких-либо изменений. При всем этом толщина тестовой металлизации составляла 18 um, а не 25 или 35, как принято для технологий прошлого. Отличный результат и подтверждение высокого качества металлизации отверстий по технологии от J-Кем.
Статистический анализ дефектов металлизации. Правильно разделять два понятия. Дефекты прямой металлизации ДПМ и дефекты металлизации последующих операций ДПО. Для анализа берем три последних года нашей работы. Это наиболее напряженный и насыщенный период с постоянной загрузкой собственного производства. Ориентировочное количество металлизированных отверстий Nme = 21 х 12 х 3 х 5000 х 8 х 2 = 60 480 000. Количество выявленных случаев нарушения металлизации в производстве и их процент, в том числе и в годной продукции, приведен в таблице. Но не все так гладко было на этапе отработки в 2006 г. Любую технологию надо изучить и осознать в деталях. Итак, данные по годам.
№ | Параметр, описание |
Кол-во |
Кол-во |
Деф. |
Кол-во |
Деф. |
Деф. в |
Деф. в |
1 | Nme_2011, кол-во метал. отв. | 17 600 000 | 1400 | 0,008 | 16400 | 0,09 | 0,00008 | 0,00008 |
2 | Nme_2012, кол-во метал.![]() |
21 000 000 | 200 | 0,001 | 10000 | 0,05 | 0,00001 | 0,00001 |
3 | Nme_2013, кол-во метал. отв. | 21 880 000 | 0 | 0 | 4000 | 0,02 | 0 | 0,000004 |
Иными словами, мы исключили дефекты отверстий благодаря системе прямой металлизации. Эта статистика справедлива для серийных стеклонаполненых материалов типа FR4, которые составляют 99% от общего объема заказов.
Значительно труднее происходит активация неармированных стекловолокном пластиков, DUROID-ов, ROGERS-ов и фторопластов. Правильными технологическими режимами или повторной активацией всегда достигается неизменно высокий результат. Общий объем таких материалов не превышает 1%.
Вы так же можете убедиться в возможностях Прямой Металлизации. Всегда высокое качество печатных плат от нашей производственной лабораторией в г, Минске.
Технический директор «Ормикс Инжиниринг»
способ электрохимической металлизации отверстий печатных плат — патент РФ 2019925
Область использования: технология беспалладиевой металлизации отверстий двусторонних и многослойных печатных плат. Сущность изобретения: очистку поверхности фольги после термообработки заготовок, активированных в растворе беспалладиевой металлизации, осуществляют путем анодного растворения продуктов термического разложения гипофосфита меди в течение 2 — 5 мин при начальной анодной плотности тока 4-5 A/дм2 , после чего заготовку дополнительно выдерживают 1 — 2 мин в электролите без тока и промывают водой. Способ обеспечивает упрощение процесса и его интенсификацию. 1 з.п. ф-лы, 1 табл. Рисунок 1Формула изобретения
1.
Описание изобретения к патенту
Изобретение относится к технологии изготовления печатных плат и предназначено для использования при металлизации отверстий печатных плат, изготавливаемых из фольгированного диэлектрического материала. Известен способ металлизации отверстий печатных плат, включающий сенсибилизацию и активацию поверхности заготовок в растворах хлористого олова и хлористого палладия с последующим химическим осаждением меди и гальваническим наращиванием слоя предварительной химической металлизации до требуемой толщины. Указанный способ длителен, трудоемок и связан с высоким расходом дорогостоящих и дефицитных реагентов, в частности соли драгметалла палладия. Наиболее близким по технической сущности и достигаемому результату является способ беспалладиевой металлизации отверстий печатных плат, включающий активацию заготовки в растворе на основе гипофосфита меди, термообработку активированных заготовок при 100-135оС в течение 7-15 мин и последующее гальваническое наращивание слоя предварительной металлизации. Слой предварительной металлизации, представляющий собой смесь продуктов термического разложения гипофосфита меди, образуется на всей активированной раствором поверхности — как на диэлектрике в отверстиях печатной платы, так и на медной фольге.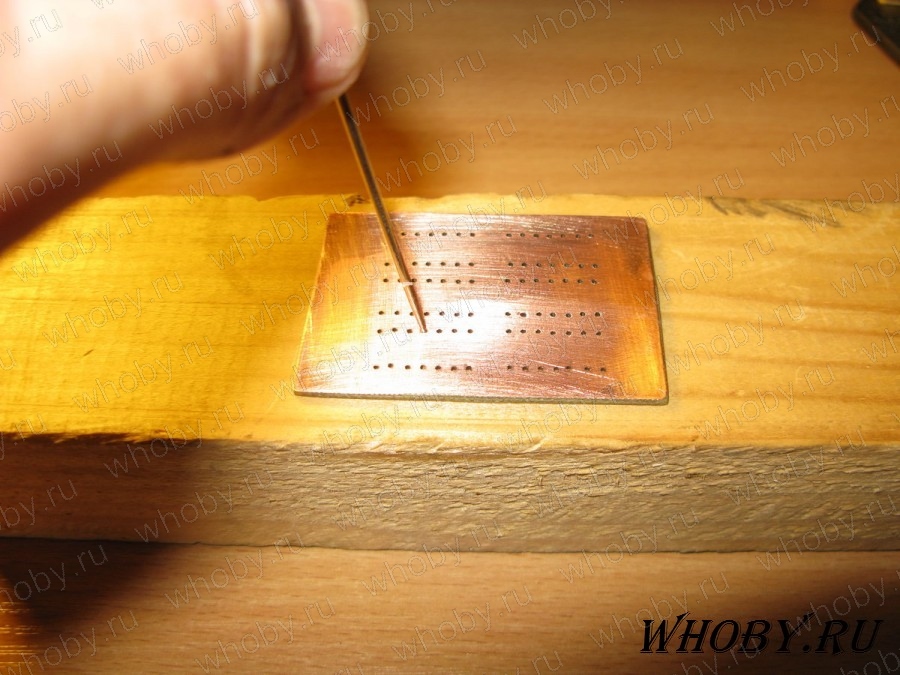
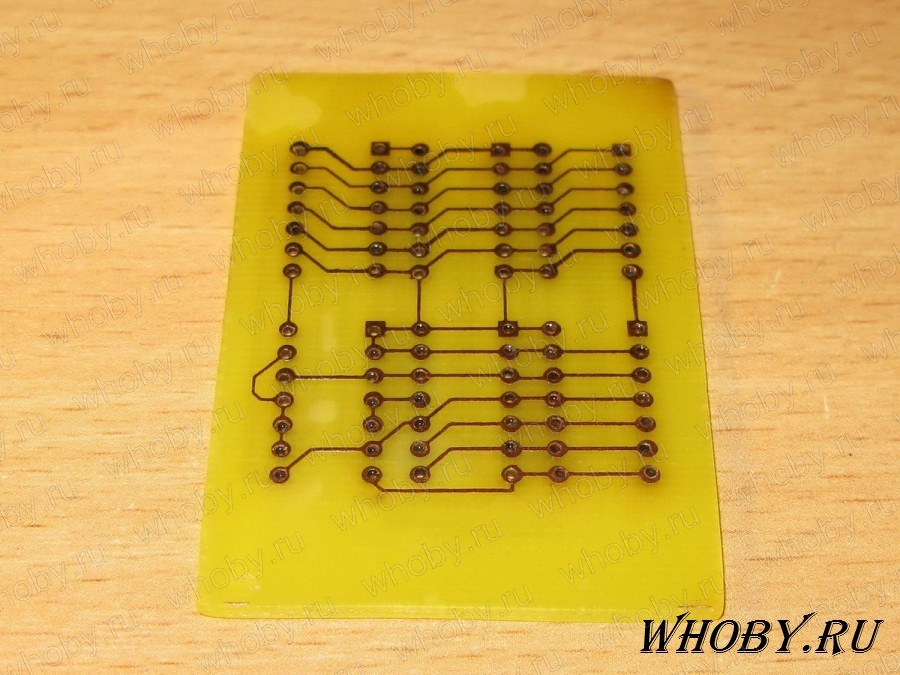

Время активирования 0,5-1 мин при комнатной температуре. После активирования заготовку с заполненными раствором отверстиями помещают во встроенный в линию блок термолиза и подвергают термообработке при 125 + 10оС в течение 10-15 мин. Заготовку извлекают из блока термолиза, охлаждают до комнатной температуры и помещают в электролит, содержащий, г/л: Ортофосфорная кислота 1250-1530 Этиленгликоль 60-90 Медь (в пересчете на металлическую) 10-20
Заготовку подвешивают между двумя медными катодами, площадь каждого из которых вдвое больше площади заготовки, включают источник питания постоянного тока и устанавливают протекающий через электролит ток таким образом, чтобы начальное значение тока соответствовало анодной плотности тока 0,4-5,0 А/дм2. Анодное растворение продуктов термического разложения гипофосфита меди ведут при комнатной температуре в течение 2-5 мин., затем отключают ток и выдерживают заготовку в электролите еще в течение 1-2 мин без тока. Извлекают заготовку из электролита, после стекания которого поверхность заготовки промывают водой. Промытую заготовку с фольгой блестящего розового цвета, не содержащую следов продуктов термического разложения гипофосфита меди, переносят в ванну гальванического меднения состава: Сернокислая медь, 5-водная 220 г/л Серная кислота 60 г/л Этиловый спирт 10 мл/л
Гальваническое наращивание меди ведут в ванне с медными анодами при 22 + 2оС и катодной плотности тока 3 А/дм2 в течение 20-30 мин до толщины гальванически осажденного слоя меди 15 5 мкм.
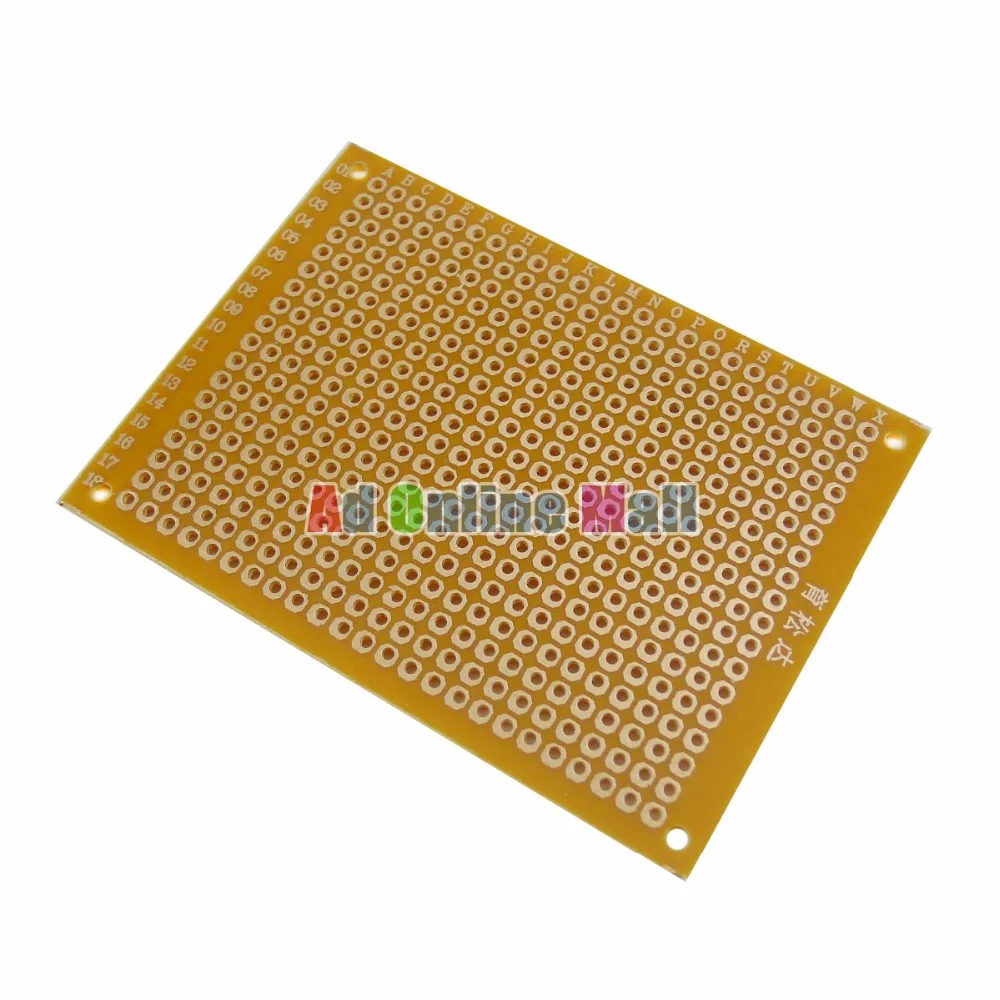
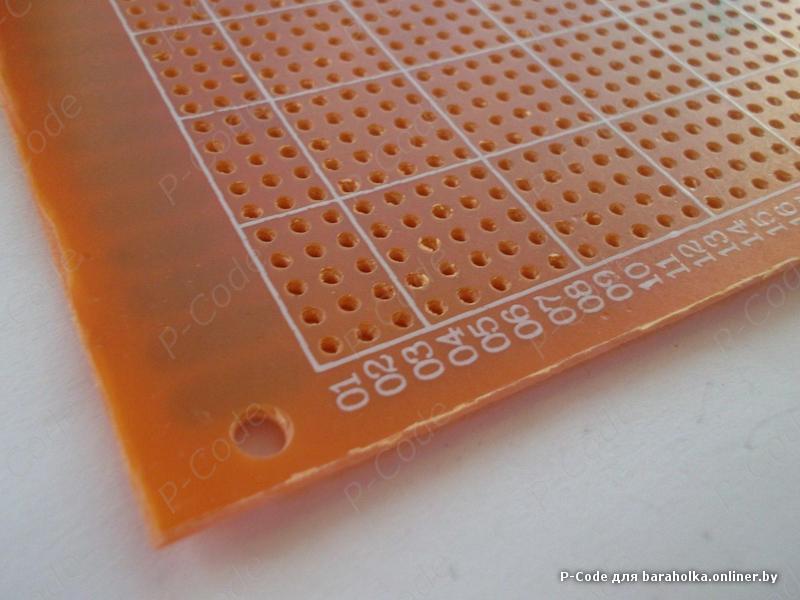
Металлизация отверстий печатной платы
В процессе изготовления печатной платы обычно необходимо пройти через отверстие, чтобы реализовать передачу схемы и герметизацию. Металлизация отверстий является одним из наиболее важных процессов в технологии производства печатных плат, для реализации металлизации отверстий обычно используются химическая медь (PTH), черная дыра (Black Hole) и метод проводящей полимерной пленки на подложке из проводящей смолы.
Химическая медь
Электрохимическое меднение — это принцип восстановления меди до меди в условиях восстановителя. Процесс можно разделить на три этапа: предварительная обработка, активация и осаждение меди.
Основной состав раствора для химического меднения включает соль меди, комплексообразователь, восстановитель, регулятор pH и добавку.Одним из наиболее распространенных восстановителей является формальдегид, два метиламиноборана, гипофосфит, гидразингидрат, соль с низким содержанием металлов, редуцирующий сахар. Среди них цена формальдегида низкая, а относительное содержание меди в покрытии выше, поэтому он является наиболее широко используемым и наиболее широко используемым. Однако формальдегид является летучим, нестабильным и имеет другие недостатки, в последние годы вопрос о том, как заменить формальдегид, также находится в центре внимания исследования. Комплексообразующий агент является одним из ключевых компонентов химического меднения, которое может увеличить поляризацию ионов меди для достижения кристаллического тонкого и яркого покрытия.Винная кислота обыкновенная, ЭДТА, триэтаноламин, три изопропиламин и др.
Черная дыра
Черная дыра представляет собой мелкие капли графита или порошка сажи, диспергированные в деионизированной воде, с использованием поверхностно-активных веществ или графитопроводящей суспензии сажи, остающейся стабильной и обладающей хорошими смачивающими свойствами, графит или сажа могут полностью абсорбироваться на поверхности стенки непроводящего отверстия. , образуя сочетание равномерного и тщательного проводящего слоя, сплошного.
Пленка полимерная проводящая
Непроводящая поверхностная химическая реакция в щелочном водном растворе перманганата калия, генерирующая слой диоксида марганца, затем в кислотном растворе, гетероциклические соединения или ряд пиррол-пиррольных мономеров на непроводящей поверхности и потеря полимеризации протонпроводящего полимера, нерастворимое образование тесно связано файл. Затем печатная плата покрывается проводящим полимером для завершения металлизации.
Процесс в основном делится на три части: предварительная обработка; образование проводящего полимера; покрытие из сульфата меди.
Лазерная металлизация отверстий в материалах печатных плат
О. Миура, К. Миядзаки, А. Такахаши, Р. Ватанабе и Т. Мива, IEEE Trans. на Компоненты, Гибриды и Производство. Technol. 16, 817 (1993).
Артикул CAS Google Scholar
F. Kuchenmeister, M. Frank, V. Beyer, S. Thierbach, E. Meusel, M. Agater, J. Kickelhain и D. Meier, IEEE 48th Electron. Compon.s & Technol. Конф. Piscataway, NJ: IEEE, 1998), стр. 320.
Google Scholar
М. Гринштейн и М. Фарид, IEEE Trans. на Компоненты, Гибриды и Производство. Technol. 14, 445 (1991).
Артикул Google Scholar
Т.Ф. Редмонд, Ч. Прасад и Г.А. Уокер, IEEE 41th Electron. Компон. & Technol. Конф. (Пискатауэй, Нью-Джерси: IEEE, 1991), стр. 689.
Google Scholar
J.K. Лампп и С. Аллен, IEEE Trans. на Компоненты, Гибриды и Производство. Technol. В 20, 241 (1997).
Артикул CAS Google Scholar

В. Сринивасан, М.А. Смртич, С.V. Babu, J. Appl. Phys. 59 3861 (1986).
Артикул CAS Google Scholar
B. Hopp, Zs. Бор, Э. Хомоля и Э. Михалик, SPIE Proc. , 3423, 389 (1998).
Артикул CAS Google Scholar
P. Simon and J. Ihlemann, Appl. Прибой. Sci. 109/110, 25 (1997).
Артикул CAS Google Scholar
A.G. Schrott, B. Braren, E.J.M. О’Салливан, Р.Ф. Сараф, П. Бейли и Дж. Ролдан, J. Electrochem. Soc. 142, 944 (1995).
Артикул CAS Google Scholar
К. Кордас, Я. Бекеши, К. Бали, Р. Вайтаи, Л. Нанай, Т.Ф. Джордж и С. Леппавуори, J. Mater. Res. 14, 3690 (1999).
Артикул Google Scholar
К.Кордас, К. Бали, С. Леппавуори, А. Уусимаки и Л. Нанай, Appl. Прибой. Sci. 152, 149 (1999).
Артикул Google Scholar
К. Кордас, С. Леппавуори, А. Уусимяки, Т.Ф. Джордж, Л. Нанай, Р. Вайтай, К. Бали и Дж. Бекеши, Тонкие твердые пленки 384, 185 (2001).
Артикул Google Scholar
T.J. Хирш, Р.Ф. Мираки, К.Линь, заявл. Phys. Lett. 57, 1357 (1990).
Артикул CAS Google Scholar
A. Gupta, R. Jagannathan, Appl. Phys. Lett. 51, 2254 (1987).
Артикул CAS Google Scholar
S. Szatmari, G. Almasi, M. Feuerhhake, P. Simon, Appl. Phys. В 63, 463 (1996).
Артикул CAS Google Scholar
Процесс металлизации отверстий и меднения на печатной плате
Металлизация и покрытие
Процесс металлизации отверстий и меднения на печатной плате
Меднение печатной платы (PCB) включает гальваническое покрытие меди, гальваническое покрытие оловом, гальваническое покрытие никелем и золотом и т. Д.Среди них гальваника меди занимает важное место в производстве печатных плат.
1 Погрузите печатную плату в кислотную жидкость
Целью погружения печатной платы в кислотную жидкость является удаление оксидов с поверхности пластины, активация платы, обычно концентрация составляет 5%, а некоторые — 10%, в основном для предотвращения попадания воды в емкость с жидкостью, что приводит к нестабильности серной кислоты.
2 Подпиточная жидкость для гальваники
Кислотная электронная жидкость состоит из CuSO 4 , H 2 SO 4 , HCl и органических добавок.CuSO 4 жидкость является основным ингредиентом, который является основным источником Cu +, концентрация CuSO 4 важна во время производства. Обычно CuSO 4 5H 2 O составляет 60 г / л-100 г / л. Количество H 2 SO 4 составляет около 180 г / л-220 г / л. Содержание Cl — в жидкости ниже, примерно 30-80 мг / л. Органические добавки — это транспортный агент, осветлитель, выравнивающий агент и другие.
3 гальванический
3.1 Полный пансион гальванический медь
Он также известен как только медь, основная функция — защита тонкой химически чистой меди, которая только что откладывается.Процесс заключается в использовании всей платы в качестве катода путем увеличения толщины меди до определенной степени после металлизации отверстий; затем формируют линию цепи путем травления, которая может предотвратить отходы из-за тонкого слоя меди, нанесенного химическим способом, который травится в следующем процессе.
3.2 Вторичная гальваническая медь
Она также известна как вторичная медь или медь для контуров. Для соответствия номинальной токовой нагрузке толщина каждой линии цепи и металлизации отверстий должна соответствовать требованиям.Графическая гальваника предназначена для увеличения толщины.
4 Кислотное обезжиривание
Обезжиривание используется для удаления оксидов, чернил, клея или пленки с поверхности медной платы для обеспечения силы связывания между медью и графической медью или никелем. Жидкость бывает двух видов: кислая и щелочная, лучше щелочное средство, но почему бы его не использовать? Поскольку графические изображения и чернила не являются щелочью, щелочное средство повредит эту линию, обратите внимание на использование кислотного обезжиривающего средства во время работы.Концентрация жидкости около 10%, время менее 6 мин. Замена составляет около 15 м2 / л, добавление предметов — 0,5–0,8 л / 100 м2.
5 Офорт
Травление в основном используется для очистки поверхности медной платы для обеспечения силы связи между графической медной платой и медью. Обычно травильная жидкость — это Na 2 S 2 O 8 , концентрация около 60 г / л, время около 20 секунд, добавление элементов составляет 3–4 кг на каждые 100 м2; содержание меди менее 20 г / л.
Традиционная металлизация отверстий печатной платы дополняется слоем химического меднения; все более и более популярным является процесс прямого нанесения гальванического покрытия, он не только упрощает процесс, простота эксплуатации, но и экологичность; Он заменит процесс химического восстановления меди и станет неизбежным трендом.(PDF) ПОКРЫТИЕ ПРОХОДНЫХ ОТВЕРСТИЙ ПОЛИПИРРОЛОМ В ПЕЧАТНЫХ ПЛАТАХ
Сушка полипиррола сразу после его осаждения на стенках отверстий FR4 критична для достижения хорошего уровня адгезии
.
Слой меди, полученный с помощью нашего метода, является когерентным и имеет достаточную адгезию к FR4.
Полипиррол, нанесенный на промежуточные слои многослойных печатных плат, не создает проблем когезии
между медью внутреннего слоя и медью, осажденной на стенках отверстий, поскольку
нанесенная медь встроена в структуру полипиррола.
При отсутствии перемешивания медь осаждается на пленке PPy по
путям с высокой проводимостью, что приводит к образованию дендритных структур. При перемешивании медь осаждается посредством более гомогенного механизма 3-D зародышеобразования
.
БИБЛИОГРАФИЯ
[1] Ангелопулос М., Проводящие полимеры в микроэлектонике (IBM J. Res. & Dev. 2001; 45 (1): 57-
75)
[2] Д. Йфантис, Н. Вурдас , А. Ифантис, С. Какос, А.Кацори, Н. Йфантис, Д. Шмайссер, Металлизация
изоляторов (пластиков) с использованием полипиррола в качестве предварительного покрытия, 55-е ежегодное собрание Международного общества электрохимии
ISE 2004, Книга тезисов I, стр.558
[3] Г. Аппель, А. Ифантис, В. Гёпель, Д. Шмайссер, Высококондуктивные полипиррольные пленки на непроводящих подложках
, Synthetic Metals, Vol. 83, 1996, pp. 197-200
[4] Д. К. Ифантис, А. Д. Ифантис, С. Лампракопулос, С.Depountis, CD Yfantis, D. Schmeisser,
Новые экологически безопасные методы — композитные покрытия на основе полипирролов, WSEAS
ОПЕРАЦИИ ПО ОКРУЖАЮЩЕЙ СРЕДЕ и РАЗВИТИЮ, Выпуск 3, Том 2, март 2006 г.
с.167-172
[5 ] A. Yfantis, G. Appel, D. Schmeisser, D. Yfantis, Полипиррол, допированный комплексами фтор-металл
: термическая стабильность и структурные свойства, Синтетические металлы, Vol. 106, 1999, стр. 187 —
195
[6] R.П. Микало, Г. Аппель, П. Хоффманн, Д. Шмайссер, Изгиб ленты в легированной проводимости
полипиррол: взаимодействие с серебром, Синтетические металлы, Vol. 122, 2001, pp. 249 — 261
[7] С. Лампракопулос, Д. Ифантис, А. Ифантис, Д. Шмайссер, Дж. Анастассопулу, Т. Теофанидес,
Исследование роли H
методом FTIR. 2
O и D
2
O в механизме старения проводящих
Полипирролы, Synthetic Metals, Vol 144, 2004, p.229-234
[8] Ифантис А. Разработка и характеристика коррозионно-стойких слоев проводящих полимеров
на алюминиевых сплавах, докторская диссертация, BTU-Cottbus, Германия, 2000
[9] Michael Carano Electrochemicals Inc., Performance and Проблемы надежности процесса прямой металлизации на основе графита
(Maple Plain, США)
[10] Хюн К. Чанг, Бьюнг-Хак Чо, Джонг К. Ли, Влияние пленок оксида титана на зародышеобразование меди
во время электроосаждения. Материаловедение и инженерия A 409 (2005) 317–328
[11] Уассим Годбейн, Лайонел Роу, Даниэль Беланжер, Электроосаждение меди на пиролитических графитовых электродах
: влияние соли меди на процесс электроосаждения, Electrochimica
Acta 52 (2007) 5843–5855
[12] C.Д. Ифантис, С. И. Какос, Д. К. Ифантис, «Металлизация изоляторов на основе полипиррола — приложение
к печатным платам (PCB)», 1-я Международная конференция WSEAS по материалам
Science, Бухарест, 2008.
[13] Х. Мейер, RJ Николс, Д. Шроер, Л. Штамп, Использование проводящих полимеров и коллоидов в покрытии печатных плат через сквозные отверстия
, Electrochemica Acta, Vol. 39, 1994.
[14] Александр Мильчев, Теодора Запрянова, Зарождение и рост меди при комбинированных ограничениях переноса заряда и диффузии
: Часть I, Electrochimica Acta 51 (2006) 2926–2933.
Подробные процедуры покрытия медью для обработки печатных плат
——Технический анализ медного покрытия для обработки печатных плат
Электролитическое нанесение покрытия широко используется в производстве и обработке печатных плат (ПП), в которых есть отверстия, и его также можно назвать PTH (Plate Through Hole), основная цель состоит в том, чтобы нанести слой меди с помощью ряда методов химической обработки на проводящую подложку, а затем увеличить толщину слоя меди с помощью последующих методов гальваники до определенной толщины конструкции, которая обычно составляет 1 мил (25.4 мкм) или более толще, а иногда даже напрямую увеличивая толщину меди всей печатной платы с помощью специальных химических методов.
Значения PTH включают по крайней мере одно или оба двух из следующих:
1. Стать частью цепей между компонентами и проводниками
2. Стать взаимосвязанными цепями или печатными схемами между слоями
Как правило, a Печатная плата представляет собой тонкую плату из стекловолокна, композитного эпоксидного материала или другого ламината. Проводящие пути протравливаются или «печатаются» на плате, соединяя различные компоненты на печатной плате, такие как транзисторы, резисторы и интегральные схемы.
Классификация материалов подложки:
Полиакриламидная смола PI Основной материал: он используется для гибких пластин (FPC) и подходит для требований высоких температур;
Подложка из фенольной бумаги (сорт MENA): ее можно перфорировать, распространенными типами являются FR-2, XXX-PC и т. Д .;
Основа из эпоксидной бумаги (сорт MENA): свойства основы из эпоксидной бумаги лучше, чем у основы из фенольной бумаги, и распространенными типами являются CEM-1, FR-3;
Эпоксидно-стекловолоконная плита (марка MENA): она армирована стекловолоконной тканью и имеет отличные механические свойства. Распространенными типами являются FR-4, FR-5, G-10, G-11;
Нетканая основа из стекловолокна и полиэстера (сорт MENA): подходит для некоторых специальных применений, обычно это FR-6.
Медное покрытие:
Отверстия на непроводящей подложке могут обеспечивать взаимное соединение между слоями или иметь гораздо лучшую способность к пайке или получать оба из них после окончательной металлизации. Внутри непроводящей подложки могут быть некоторые внутренние схемы — схемы травлением были там до ламинирования, и эти платы в этом процессе также известны как многослойная плата (MLB). В многослойной плате отверстие для металлизации не только играет роль соединения двух внешних цепей, но также играет роль межсоединения между внутренними слоями, когда оно предназначено для прохождения через непроводящую подложку (концепция глухого отверстия на тот момент еще не сформирован).
В настоящее время на многих печатных платах в процессе производства используется заглушка из ламината. Другими словами, поверхность непроводящей подложки представляет собой слой медной фольги определенной толщины, нанесенный методом химического восстановления. Толщина медной фольги выражается в весе (унциях) медной фольги на квадратный фут.
Метод с хромовой кислотой:
Наличие шестивалентного хрома в отверстиях может вызвать множество проблем, которые могут привести к проколу, который является частым результатом этого препятствия, например, влияние на покрытие медной фольги, разрушение олова-палладия. коллоид, препятствующий реакции восстановления меди и т. д.Эту ситуацию можно решить путем вторичной активации, но стоимость доработки или вторичной активации слишком высока, особенно в автоматической линии. Кроме того, вторичный процесс активации пока еще не очень развит.
Всегда есть нейтрализованные процессы после криминального айкда. Например, раствор гидросульфита натрия всегда используется для восстановления шестивалентного хрома до трехвалентного хрома, а температура раствора гидросульфита натрия обычно составляет около 100 ° F. Температура стирки обычно составляет 120-150 ° F после нейтрализации.Чистый раствор сульфитов можно использовать для промывки, избегая других растворов, которые вносятся в процесс и мешают активации.
Существуют также другие химические методы, используемые для удаления пятен клея и других пятен, образующихся в процессе травления или нанесения покрытия, такие как нанесение органических растворителей, раствора перманганата калия, а также концентрированного раствора серной кислоты. Кроме того, можно использовать плазменный метод, но в настоящее время он все еще находится на стадии экспериментального применения, который трудно использовать для крупномасштабного производства из-за больших вложений в оборудование.
Процесс химического нанесения покрытия на медь:
I . Основная цель этапа предварительной обработки:
1. Обеспечение непрерывной целостности химически осажденных слоев меди;
2. Обеспечьте силу сцепления между химической медью и медной фольгой подложки;
3. Обеспечьте силу сцепления между химической медью и внутренней медной фольгой;
4. Обеспечьте силу связи между слоями меди, нанесенными химическим способом, и непроводящими субстратами.
(Выше представлено краткое описание предварительной обработки меди химическим способом.)
II . Типичные процедуры предварительной обработки меди для химического нанесения покрытий описаны ниже:
Удаление масла:
i . Цель удаления масла :
① Удалить масло и жир с медной фольги и отверстий;
② Удалите загрязнения с медной фольги и отверстий;
③ Удаляет загрязнения с поверхности медной фольги и пригоден для последующей термообработки;
④ Легко справляется с пятнами полимерной смолы, образующимися при сверлении отверстий;
⑤ Удаление заусенцев в дефектных отверстиях;
ii .Некоторые ключевые элементы в процессе удаления масла:
① Как выбрать подходящий тип средства для удаления масла;
② Рабочая температура маслосъемника;
③ Концентрация маслоудаления;
④ Время пропитки маслоудаления;
⑤ Механическое перемешивание в емкости для снятия жира;
⑥ Точка очистки, где снижается обезжиривающий эффект;
⑦ Моющий эффект после удаления масла.
(В вышеупомянутой операции очистки температура является ключевым фактором, который следует учитывать.У многих маслосъемников установлен минимальный температурный предел.)
iii . Некоторые элементы могут повлиять на стирку:
① Температура стирки должна быть выше 60F;
② Перемешивание воздуха;
③ Распыление может быть лучше;
④ Для всего процесса мойки достаточно пресной воды, чтобы ее можно было вовремя заменить
Промывка после удаления масла в определенном смысле так же важна, как и само удаление масла, и оставшееся маслоудаление на поверхности доски и стенке отверстия будет сам по себе становится загрязнителем на печатной плате, который затем загрязняет следующие основные решения для обработки, такие как микрокоррозия и активация.
Регулировка заряда:
Типичный процесс регулировки заряда используется после удаления масла. Как правило, при производстве некоторых специальных пластин / пролета> многослойных плат процесс регулировки заряда необходим в процессе удаления смазывания / пролета> травления из-за фактора заряда самой смолы. Важная роль регулировки заряда заключается в проведении «суперпропитки» на непроводящих подложках, другими словами, в преобразовании поверхности смолы со слабо отрицательными зарядами в поверхность со слегка положительными зарядами после обработки корректирующим раствором.В некоторых случаях обеспечение однородной непрерывной полярной поверхности с положительным зарядом может гарантировать, что активаторы могут быть эффективно и адекватно прикреплены к стенке отверстия в последующем процессе. Иногда в маслоудаление добавляется отрегулированный препарат, поэтому его также называют регулирующей жидкостью для удаления масла. Хотя раздельное маслоудаление и регулирующая жидкость будут более эффективными, чем комбинированная регулирующая жидкость для удаления масла, отраслевая тенденция объединила их, и модифицирующим агентом на самом деле являются лишь некоторые поверхностно-активные вещества.После завершения регулировки заряда очень важна стирка. Если промывка не выполнена должным образом, поверхностно-активное вещество останется на медном слое платы, что может загрязнить последующее микротравление и активированный раствор, что может повлиять на конечную силу связывания между медью и медью. В результате сила связи между медью с химическим покрытием и медью подложки будет уменьшена. Следует обращать внимание на температуру очищающей воды и эффективный поток очищающей воды, и особое внимание следует уделять концентрации адъюванта, при этом следует избегать использования слишком высокой концентрации адъюванта как правильного количество адъюванта будет иметь более очевидный эффект.
Микротравление:
Следующим этапом предварительной обработки меди, нанесенной химическим способом, является микротравление, микротравление, микро-укрупнение или укрупнение. Цель этого шага — обеспечить слегка грубую структуру активной поверхности меди для последующего химического нанесения покрытия на медь. Если микротравление отсутствует, сила связи между медью с химическим покрытием и медью подложки будет значительно уменьшена. Функции шероховатой поверхности следующие:
① Площадь поверхности медной фольги значительно увеличена, а также значительно увеличена поверхностная энергия, обеспечивая большую площадь контакта между медью с химическим покрытием и медной подложкой;
② Если некоторые поверхностно-активные вещества не были промыты в воде, ингибиторы микротравления могут протравить медную фольгу на дне подложки, чтобы удалить поверхностно-активное вещество с поверхности подложки, но полностью зависят от микротравильного агента для удаления поверхностно-активного вещества не слишком реалистично и эффективно.Например, когда площадь поверхностно-активного вещества, оставшегося на медном слое, больше, функция ингибиторов микротравления очень мала, и они даже не могут воздействовать на поверхностно-активное вещество на медном слое.
Покрытие сквозных отверстий на печатной плате промышленного уровня: 5 ступеней
ВНИМАНИЕ! НЕ РАБОТАЙТЕ С ХИМИЧЕСКИМИ ВЕЩЕСТВАМИ БЕЗ ПЕРЧАТК!
Хотя в целом все ингредиенты не опасны, они все же представляют опасность для вашей кожи.
Также рекомендуется проводить заключительные этапы приготовления раствора на открытом воздухе или при очень хорошей вентиляции (открытого окна может быть недостаточно). См. Ниже почему.
Для приготовления раствора активатора нам понадобятся:
1. Дистиллированная вода
2. Сульфат меди
3. Гипофосфит кальция (Ca (h3PO2) 2)
4. Гидроксид аммония (25%)
5. Жидкое мыло
Все ингредиенты требуются в небольших количествах (см. Ниже), и большинство из них широко доступны.Единственный менее доступный компонент — это гипофосфит кальция, но на самом деле он не редкость и не дорогой, просто его нельзя купить в ближайшей аптеке или Home Depot. Вероятно, самый простой способ получить его — просто купить в Интернете в качестве аналитического реагента. Минимальные количества обычно около 1 кг, этого хватит, чтобы открыть собственный небольшой магазин печатных плат 🙂
Раствор активатора готовится следующим образом.
1. Возьмите 140 мл воды и растворите в ней 30 г сульфата меди. Перемешивайте, пока весь сульфат меди не растворится.В этот момент раствор приобретет голубой цвет. №
2. Влить в раствор 22 г гипофосфита кальция и тщательно перемешивать 3-4 минуты. Если влить в раствор гипофосфит кальция, появится осадок, который меняет цвет раствора на бело-голубой. Осадок состоит в основном из гипса (фосфата кальция). Учтите, что осадок достаточно велик, поэтому для приготовления раствора используйте банки объемом не менее 0,5 л.
3. Отфильтровать раствор через воронку с помещенной в нее фильтровальной бумагой.Опять же, используйте большую воронку. Кроме того, в конце скорость фильтрации может быть довольно низкой, так что наберитесь терпения. Раствор должен иметь светло-голубой (возможно, немного тусклый) цвет.
4. Вылейте через осадок еще 100 мл воды.
5. Снимите воронку и добавьте 40 мл 25% гидроксида аммония. ПРЕДУПРЕЖДЕНИЕ! Этот реагент воняет! Итак, пока вы будете это делать, старайтесь держать нос как можно дальше от раствора. Как только гидроксид аммония растворяется в растворе, он значительно меньше воняет, поэтому активирующий раствор можно использовать в помещении, хотя он все еще воняет, поэтому емкость с раствором не следует оставлять открытой на долгое время.Раствор в течение некоторого времени быстро загустевает, появляются белые хлопья, но они довольно быстро исчезают, и раствор приобретает темно-синий цвет. Вы можете ускорить этот процесс, помешивая раствор.
6. Добавьте около 5-6 мл жидкого мыла и перемешивайте несколько секунд.
7. Добавьте около 8-10 г гипофосфита кальция. Часть его растворится, но часть останется в растворе в виде осадка. Перемешивайте раствор в течение нескольких секунд, чтобы ускорить процесс.
Решение готово. Он достаточно стабилен и может храниться длительное время, не теряя своих свойств.Используйте плотно закрытый контейнер и храните в сухом, защищенном от прямых солнечных лучей и недоступном для детей и домашних животных месте. Поскольку раствор содержит соединения меди, он может быть токсичным, если вы его выпьете, поэтому делать это не рекомендуется 🙂
Раствор требует ухода, особенно при интенсивном использовании. Обслуживание довольно простое — просто проверяйте время от времени, есть ли еще осадок гипофосфита кальция на дне емкости, в которой хранится раствор, и при необходимости добавьте несколько граммов гипофосфита кальция.
После того, как вы подготовили решение, вы готовы к следующему шагу.
На приведенных ниже изображениях показан раствор активатора на разных стадиях приготовления.
Метод металлизации отверстий печатных плат
(57) Реферат:
Изобретение относится к технологии изготовления печатных плат и предназначено для использования при металлизации отверстий печатных плат из фольгированного диэлектрического материала. Технический результат — предотвратить травление медной поверхности печатной платы в процессе химической металлизации отверстий и тем самым существенно снизить потери рабочего раствора в процессе (активации) заготовок печатных плат, а также расширителя. особенности респальдадос металлизации.Способ металлизации отверстий печатных плат включает предварительную подготовку печатных плат в водном растворе основы и ее химическую металлизацию в водном растворе фосфорных солей меди и подложки, термообработку, очистку и гальванику емкостей. металла. Новым является то, что в процессе химической металлизации проводят обработку катодной медью поверхности заготовки печатной платы плотностью тока 0,8 — 1,0 А / дм 2 .Таблица 1. Изобретение относится к технологии изготовления печатных плат и предназначено для использования с металлизацией отверстий печатных плат, включает подготовку поверхности (обезжиривание и ополаскивание в проточной воде), нанесение раствора фосфата.
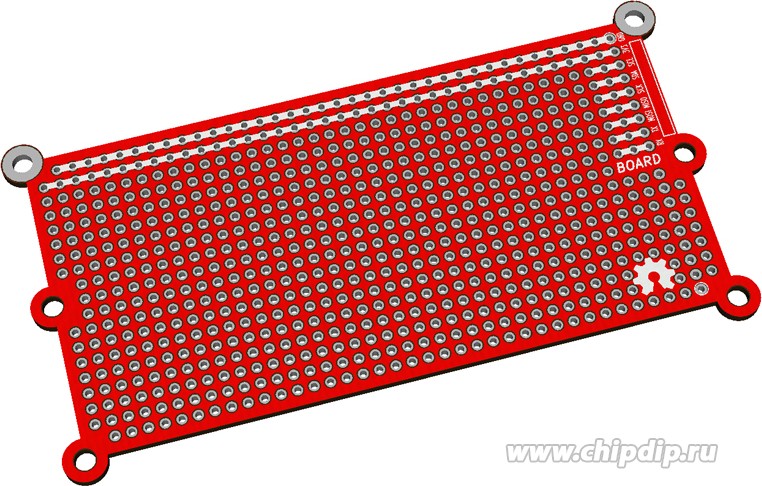
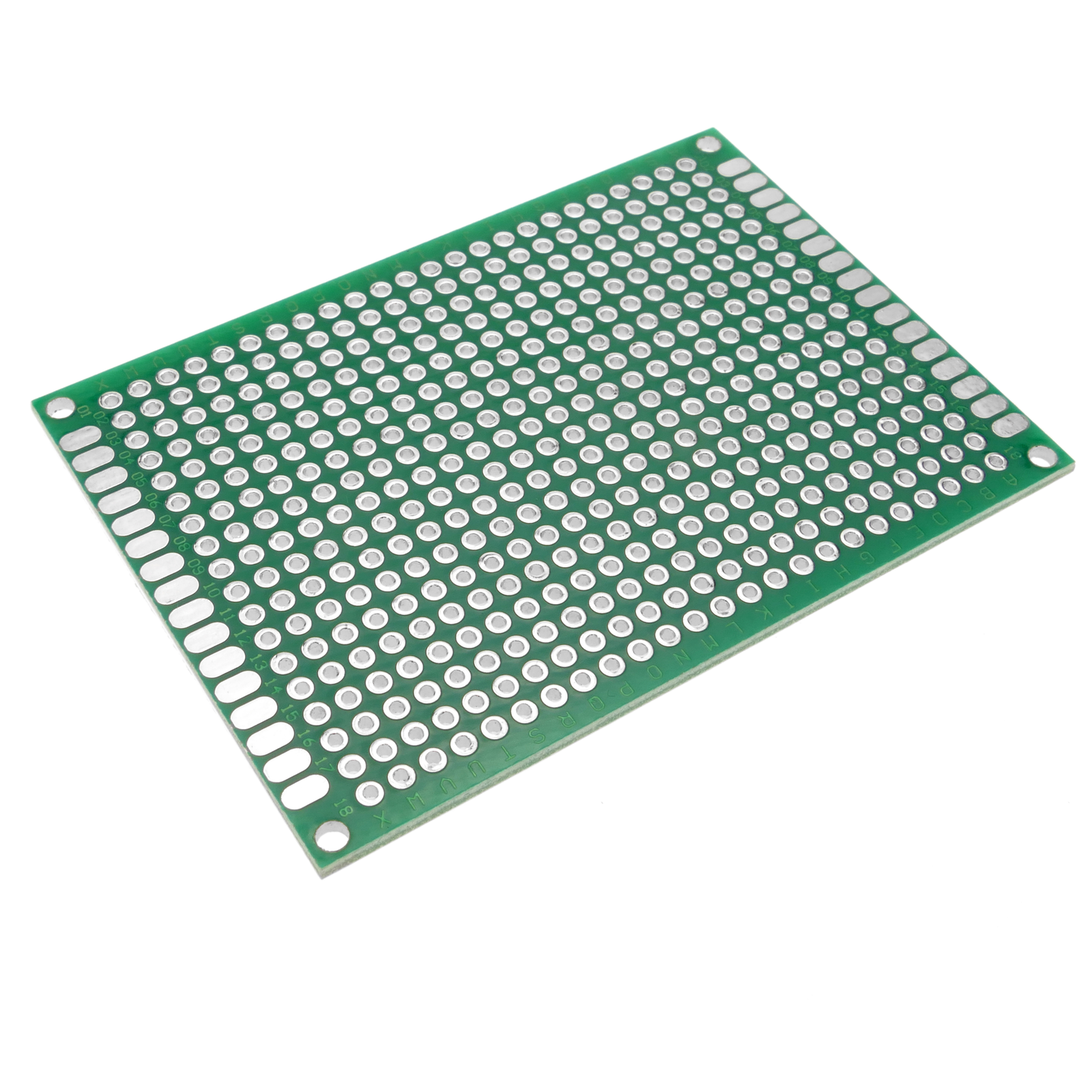