Какие основные параметры устройства намотки проволоки ТТ-504. Для чего оно предназначено. Каковы его технические характеристики и особенности конструкции. Где применяется данное оборудование.
Назначение и область применения устройства намотки проволоки ТТ-504
Устройство намотки проволоки ТТ-504 предназначено для автоматизированной намотки сварочной проволоки на катушки, используемые в сварочных головках и автоматах. Основные области применения данного оборудования:
- Намотка проволоки на катушки для сварочных головок ОКА
- Подготовка катушек с проволокой для устройств автоматической сварки ОСА-ПА
- Перемотка сварочной проволоки с больших бухт на малые катушки
- Обеспечение равномерной и плотной намотки проволоки
Устройство позволяет существенно ускорить и автоматизировать процесс подготовки расходных материалов для сварочного оборудования.
Технические характеристики устройства намотки ТТ-504
Основные технические параметры устройства намотки проволоки ТТ-504:
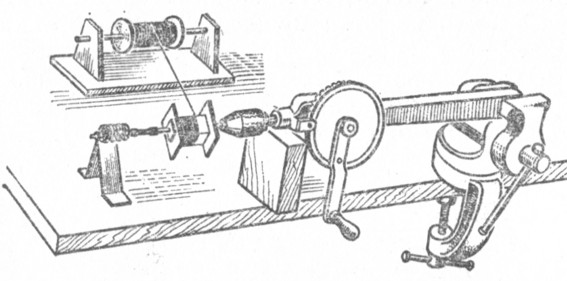
- Номинальное питающее напряжение: 220 В
- Диаметр сварочной проволоки: 0,8; 1,0; 1,2 мм
- Максимальная скорость намотки: 2 оборота/с
- Допустимые диаметры катушек: 200 и 300 мм
- Вес устройства: 25 кг
- Габаритные размеры: 485 × 450 × 385 мм
Устройство обеспечивает равномерную намотку проволоки различного диаметра на стандартные катушки, используемые в сварочном оборудовании.
Конструкция и принцип работы намоточного устройства
Устройство намотки проволоки ТТ-504 имеет следующую конструкцию:
- Основание с установленным на нем электроприводом
- Кронштейн для крепления катушкодержателя
- Блок привода с механизмом подачи проволоки
- Катушкодержатель для установки пустой катушки
- Каретка с направляющим роликом для укладки проволоки
- Прижимное устройство для фиксации катушки
Принцип работы заключается в следующем:
- На катушкодержатель устанавливается пустая катушка
- Проволока заправляется в механизм подачи
- При включении привода катушка начинает вращаться
- Каретка с направляющим роликом обеспечивает равномерную укладку витков
- Скорость намотки регулируется для обеспечения плотной намотки
Преимущества использования намоточного устройства ТТ-504
Применение устройства намотки проволоки ТТ-504 обеспечивает следующие преимущества:
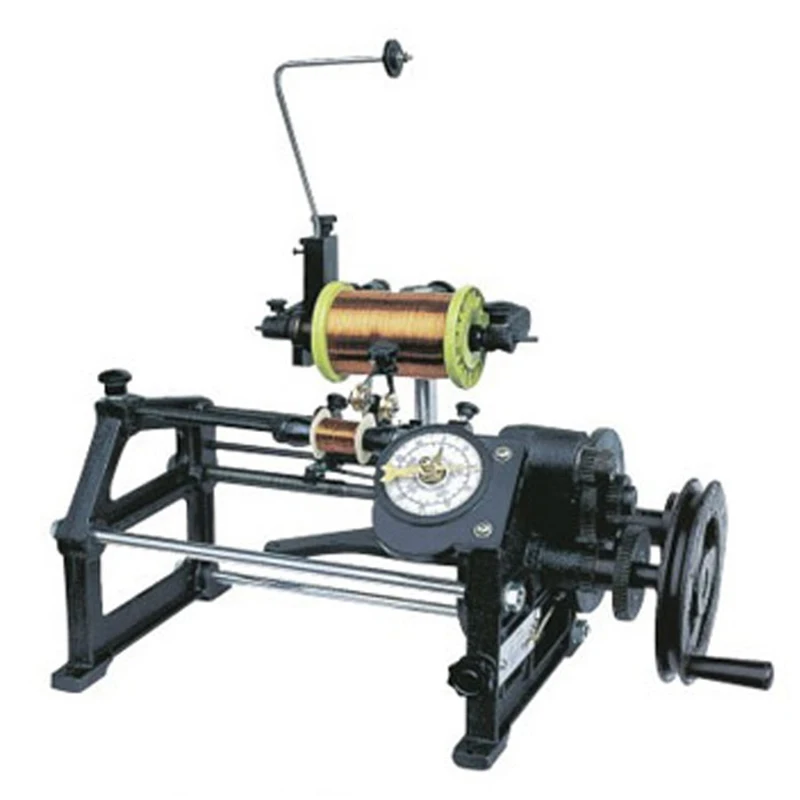
- Высокая скорость намотки проволоки — до 2 об/с
- Равномерная и плотная укладка витков
- Возможность намотки проволоки различного диаметра
- Совместимость с катушками диаметром 200 и 300 мм
- Простота эксплуатации и обслуживания
- Компактные размеры и небольшой вес
Это позволяет существенно повысить производительность подготовки расходных материалов для сварочного оборудования.
Условия эксплуатации намоточного устройства
Устройство намотки проволоки ТТ-504 предназначено для эксплуатации в следующих условиях:
- В закрытых помещениях с регулируемыми климатическими условиями
- При температуре окружающего воздуха от +1°C до +40°C
- При относительной влажности до 90% при температуре +20°C
- В условиях отсутствия прямого воздействия атмосферных осадков
Степень защиты устройства от внешних воздействий — IP22. Это обеспечивает защиту от проникновения твердых предметов размером более 12 мм и капель воды при наклоне корпуса до 15°.
Требования к обслуживанию и безопасности при работе
При эксплуатации устройства намотки проволоки ТТ-504 необходимо соблюдать следующие требования:
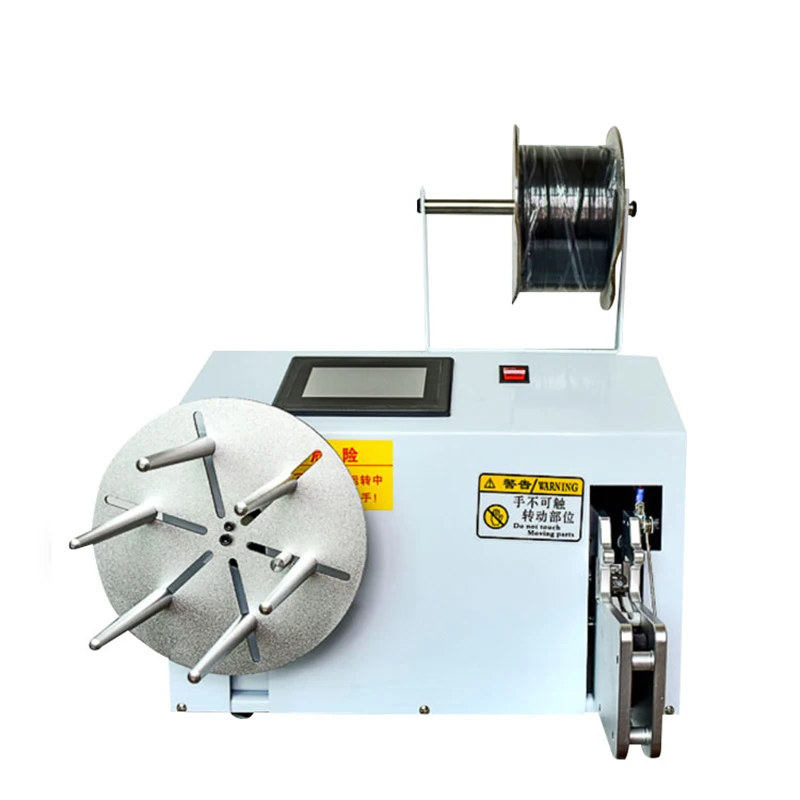
- Периодически проверять затяжку резьбовых соединений
- Очищать механизмы от пыли и грязи
- Смазывать подвижные части и подшипниковые узлы
- Не допускать попадания посторонних предметов в зону намотки
- Использовать средства индивидуальной защиты при работе
- Не касаться вращающихся частей во время работы
Соблюдение этих требований обеспечит долговременную и безопасную эксплуатацию намоточного устройства.
Сравнение с аналогичными устройствами других производителей
По сравнению с аналогичными устройствами других производителей, намоточное устройство ТТ-504 имеет следующие особенности:
- Более высокая скорость намотки — до 2 об/с
- Возможность работы с катушками диаметром 200 и 300 мм
- Меньшие габариты и вес при аналогичной функциональности
- Более простая конструкция, облегчающая обслуживание
- Невысокая стоимость по сравнению с импортными аналогами
Это делает устройство ТТ-504 оптимальным выбором для оснащения сварочных участков отечественных предприятий.
Перспективы развития и модернизации намоточного оборудования
Возможные направления дальнейшего совершенствования устройств намотки проволоки:
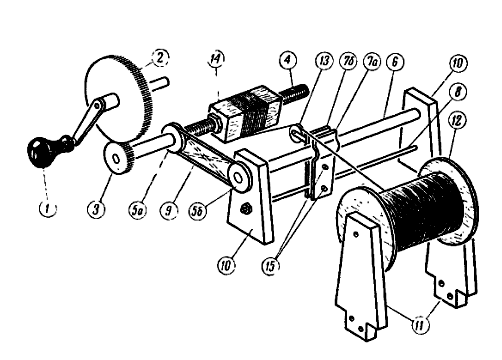
- Увеличение скорости намотки до 3-4 об/с
- Расширение диапазона диаметров наматываемой проволоки
- Автоматизация процесса заправки проволоки
- Внедрение электронных систем контроля намотки
- Разработка устройств для одновременной намотки нескольких катушек
Это позволит еще больше повысить производительность и качество намотки проволоки для сварочного оборудования.
от> |
Номинальное питающее напряжение, В | 220 |
Диаметр сварочной проволоки, мм | 0,8; 1,0; 1,2 |
Максимальная скорость намотки, оборот/с | 2 |
Допускается установка катушки диаметром, мм | 200; 300 |
Вес устройства, кг | 25 |
Габариты , мм | 485х450х385 |
1 – Основание; 2 – Кронштейн; 3 – Блок привода; 4 – Кронштейн; 5 – Катушкодержатель; 6 – Привод; 7 – Каретка; |
8 – Прижим; 9 – Табличка; 10 – Пустая катушка; 11 – Болт; 12 – Упор; 13 – Переходник под проволочную катушку диаметром 300мм; 14 – Компрессор; 15 – Подставка ТТ 376-01-1. |
xn--e1aqadalkdy.xn--p1ai
Технотрон устройство намотки проволоки тт 504
Федотов Алексей Геннадьевич (UA3VFS)
г. Гусь-Хрустальный
Технология намотки и способ изоляции на самом деле очень прост и не предполагает ни в коем случае ни какой обмотки, ни лакотканью, ни чем-либо другим. Дело в том, что при любой обмотки лакотканью или другими изоляторами внутреннее окно ТОРА мгновенно заполняются, так как, на внешней стороне получается один слой, а на внутренней 5-10 слоев, да еще неровных. Я давно собирался написать статью о способе качественной намотки торов. Это довольно долго объяснять и лучше показать на фото. Причем после намотки обмотки не превращаются в колесо, а сам трансформатор не становиться, яйцеобразным и расход провода минимален. Ввиду всего этого и КПД трансформатора максимален. А что из этого получается, Вы можете посмотреть в моем усилителе.
Сразу оговорюсь, речь идет о мощных тороидальных трансформаторах. Габаритная мощность, которых более 500Вт. Которые мотаются проводами от 1 до 3мм. естественно виток к витку. И, как правила, сетевая обмотка которых лежит в приделах от 100 до 400 витков, всего, то есть 0,5-2 витка на вольт. Мотать таким способом менее мощные трансформаторы хлопотно, но при желании можно.
Что нужно для намотки.
1) Необходимо сделать подставку для намотки тороида, делается это очень просто. Берем квадратный кусок ДСП или фанеры толщиной 10-15мм. Размерами 200Х200мм еще нам нужны два деревянных бруска длинной 200мм и с квадратом 20Х20мм. Эти два бруска нам нужно либо приклеить по центру нашей площадки, параллельно друг другу, на расстоянии между ними 100мм. А еще лучше привернуть к площадке эти бруски с помощью шурупов, но с потайными головками и головки утопить в фанеру иначе они будут царапать стол. Теперь если на эту подставку поставить тороид, он будет прочно и устойчиво стоять.
2) Нужен челнок, челнок я выпиливаю из оргстекла толщиной 5-6мм. Ширина обычно 30-40мм. длинна 300-400мм. Торцевые пропилы я делаю не углом, а полукругом и обрабатываю их напильником, что бы не портилась изоляция провода и даже проклеиваю одним двумя полосками изоленты опять же для защиты провода.
На челнок мы наматываем провод, не страшно, если провода не хватит, можно аккуратно спаять провод и мотать дальше. Но лучше все-таки рассчитать, так что бы провода хватило.
3) Теперь нам нужен материал для изоляции между слоями, это очень просто нужно найти
тонкий картон (упаковочный), я например, применяю коробки от динамиков для автомобилей. Главное что бы это был не толстый, но и не тонкий материал толщина картона, где-то 0,5мм. Если он будет с одной стороны глянцевый, то это тоже хорошо.
4) Еще нам потребуется нитки толстые 10-20 номер. Но на худой конец можно и 40 номер.
Сама намотка ведется от себя в правую сторону.
А теперь самое главное, это изготовление самих изоляционных прокладок между слоями.
Нам потребуется штангель-циркуль, с острыми концами .
Измеряем, внешний диаметр нашего тора , прибавляем 20мм. (для нахлеста) и делим пополам. Например, внешний диаметр тора 150мм.+ 20мм.= 170мм. 170мм./2 = 85мм.
Выставляем штангель на 85мм. и фиксируем винтом. Сам штангель мы будем использовать как циркуль для черчения кругов на картоне. Почему именно штангелем, а не обычным циркулем, которым и проще и удобнее? А все очень просто, когда мы будем острым и прочным концом штангеля чертить по картону, то на картоне останется продавленная борозда и именно она поможет нам. Эта борозда очень полезна для удобства сгибания внутренней рассеченной окружности наших прокладок. В общем, сами поймете, что штангелем лучше, чем удобным циркулем.
И так чертим, внешний круг на картоне и вырезаем его ножницами, в принципе внешний круг можно нарисовать и обычным циркулем.
Далее замеряем внутренний диаметр тора ничего не прибавляем, не убавляем, а просто делим пополам. Например, диаметр 60мм./2 = 30мм.
Выставляем, именно штангель-циркуль, на 30мм. фиксируем винтом и чертим внутренний диаметр на картоне.
Далее мы берем карандаш и линейку и работаем над внутренним кругом, сначала рисуем крест, то есть, делим круг на 4 части, потом на 8 частей, если внутренний диаметр ТОРА больше 60мм. то еще и на 16 частей.
>Далее мы рисуем обычным циркулем еще один круг, который меньше внутреннего в два раза, то есть, раздвигаем циркуль на 15мм.
А теперь нам потребуется ровный кусок, фанеры или ДСП на который, мы положим нашу картонную заготовку для прорезания концом острого скальпеля или ножа, нанесенных карандашом наших частей. Прорезать нужно по кругу от внешнего края окружности к центральной точке, не далее иначе картон будет задираться. Прорезать нужно насквозь картона. Далее ножницами вырезаем внутренний круг нарисованный нами обычным циркулем. Полученные дольки отгибаем перпендикулярно заготовки.
Понятно, что таких заготовок нужно на каждый слой по две штуки, каждый раз замеры диаметров делаются вновь, так как от слоя к слою их значение меняется.
Далее меряем высоту тора и вырезаем две полоски картона такой же ширины.
Одну полоску вставляем внутрь тора, так что бы нахлест был не более 10мм.
Вторую полоску накручиваем одним слоем на внешнюю сторону тора с таким же нахлестом.
Надеваем обе круглые заготовки на торцы тора, крепим ниткой в трех-четырех местах по кругу.
И далее начинаем мотать.
Самые опасные места для пробоя это углы окружностей ТОРА внешний и особенно внутренний. Поэтому если во время намотки мы увидим, что провод может соприкасаться с проводом внутреннего слоя, особенно по внутреннему углу окружности ТОРА. То необходимо подложить под провод полоски такого же картона шириной 10мм. и длинной по 20-30мм., там, где это необходимо. На внешней стороне, как правила этого делать не приходится, так как внешняя сторона заготовки наслаивается на край и хорошо предохраняет провод от замыкания.
Вся разметка и прорезка картонных заготовок делается с матовой стороны картона, применять картон с двух сторон глянцевый не желательно.
Перед тем как начать мотать тор, на пальцы рук нужно намотать два слоя изоленты на оба сгиба мизинца и на сгиб указательного пальца, иначе будут огромные водяные мозоли.
Многих интересует, как рассчитать ТОР.
Дело в том что количество витков будет зависеть от качества железа но приблизительный расчет делается просто, как и у обычного трансформатора только коэффициент берем 20-30.
Ну, например измеряем высоту, она = 10см.
Измеряем толщину стенки, она = 5 см.
10х5=50см.
25/50=0,5 витков на 1вольт.
220х0,5=110 витков сетевой обмотки.
Теперь начинаем мотать сетевую обмотку, намотав приблизительно 90 витков пробуем включить в сеть, меряя при этом ток холостого хода.
Совсем несложно подключить кончик провода прямо на челноке.
Постепенно доматывая провод, доводим ток холостого хода до 50-100ма. и на этом прекращаем мотать, полученное количество витков и будет реально. Теперь это реальное количество делим на 220 и получаем реальное значение количества витков на 1вольт.
И в соответствии с этой цифрой рассчитываем все выходные обмотки.
Имейте ввиду, что при включении трансформатора в сеть первичный мгновенный бросок тока очень большой. И для того, что бы не спалить тестер нужно делать так. Сетевой провод подключаем через замкнутый тумблер параллельно тумблеру включаем тестер, включаем вилку в розетку и только потом размыкаем тумблер, что бы посмотреть ток холостого хода.
Кстати именно из за мощного первичного броска тока трансформаторы мощностью более 1 КВт., обязательно нужно включать с помощью схемы мягкого включения. Тем более схема эта очень проста.
См.ц ены на станок (начинается распродажа! скидка 7 % на намоточные станки. Срок действия акции ограничен)
Намоточный станок СНПУ-2-01М предназначен для окрытой рядовой намотки электрических катушек.
1. Для намотки катушек сложных конструкций (много обмоток, выводов, прокладка изоляции между слоями и обмотками и т.д.) станок поставляется в одношпиндельном исполнении со следующими характеристиками:
-частота вращения шпинделя — 3000 об/мин;
-диметры наматываемых проводов -0,02-2,5мм;
-диаметры наматываемых катушек -120мм;
-длина раскладки -150мм;
-мощность привода -0,75кВт.
2. Для намотки катушек простых конструкций (одна многовитковая обмотка, отсутствие межслоевой изоляции) станок может поставляться с многошпиндельными приставками, обеспечивающими высокую скорость намотки.
При установке четырехшпиндельной приставки обеспечиваются следующие характеристики:
— число одновременно наматываемых катушек -4;
— частота вращения шпинделей -6000об/мин;
— диаметры наматываемых проводов -0,09-0,3мм;
— диаметры наматываемых катушек (по габаритам каркасов) — 60мм;
-длина раскладки -50мм.
3.При установке двухшпиндельной приставки обеспечиваются следующие характеристики:
-число одновременно наматываемых катушек -2;
-частота вращения шпинделей — 9000об/мин;
-диаметры наматываемых проводов 0,09 -0,3мм;
-диаметры наматываемых катушек -60мм;
-длина раскладки -50мм;
В зависимости от исполнения намоточные станки комплектуются необходимым количеством смоточных и натяжных устройств и роликов раскладки, а также задней бабкой.
Привод станка осуществляется асинхронным двигателем с частотным регулированием скорости. Управление — программируемым контроллером и двумя педалями. Для установки станка требуется стол с размерами в плане ≈ 1200х700мм. (стол поставляется по особому заказу).
Сменные части к станку
Устройство натяжное ПДА.417.09.00
Предназначено для обеспечения натяжения при сматывании проводов диаметром до 0,3 мм с неподвижных катушек.
Устройство натяжное ЫБМ.3.740.069
Предназначено для обеспечения натяжения при сматывании проводов диаметром от 0,3 мм до 2,5 мм с неподвижных катушек.
Устройство натяжное ПДА.417.027.00 и устройство смоточное ПДА.417.028.00
Предназначены для обеспечения натяжения при сматывании проводов диаметрами 0,02. 0,06 мм с неподвижных катушек диаметрами 32мм, 50 мм, 63 мм, установленных в смоточное устройство. Применяются совместно.
Смоточно-натяжное устройство ЫБМ.3.740.062
Предназначено для смотки и обеспечения натяжения проводов диаметром 0,3-2,5 мм с вращающихся катушек диаметрами до 250 мм, высотой до 200 мм. Сматываемые катушки устанавливаются на оправку, расположенную горизонтально.
Устройство смоточное ПДА.417.10.00
Предназначено для установки сматываемых катушек диаметром до 125 мм и высотой до 125 мм. Используется совместно с натяжными устройствами.
Устройство смоточное ПДА.417.11.00
Предназначено для установки сматываемых катушек диаметром до 250 мм и высотой до 200 мм. Используется совместно с натяжными устройствами.
Механизмы раскладки провода при намотке.
Механизм раскладки (ролики раскладки) предназначены для перемещения наматываемого провода вдоль оси вращающейся катушки. Выбор механизма раскладки зависит от диаметра проводов:
-механизм раскладки ЫБМ.3.773.055 — диаметры проводов — от 0,002 мм до 0,1 мм
-механизм раскладки ЫБМ.3.773.056 — диаметры проводов — до 0,5 мм
— механизм раскладки ЫБМ.3.773.057 — диаметры проводов — до 2,5 мм
Бабка задняя ПДА.417.02.00
Используется при намотке катушек, закрепляемых на съемных оправках, устанавливаемых в центрах.
Приставка намоточная ПДА.417.04.00 и механизм раскладки ПДА.417.06.00
Предназначены для одновременной намотки 4-х катушек проводами диаметрами 0,03. 0,3 мм. Максимальные диаметры наматываемых катушек 60 мм, длина раскладки 50 мм. Максимальная частота вращения шпинделей 6000 об/мин. Приставка соединяется со шпинделем намоточной головки, механизм раскладки устанавливается на каретку механизма раскладки станка.
Приставка намоточная ПДА.417.05.00
Предназначена для одновременной намотки 2-х катушек проводами диаметрами 0,03. 0,3 мм. Максимальные диаметры наматываемых катушек 60 мм, длина раскладки 50 мм. Максимальная частота вращения шпинделей 9000 об/мин. Приставка соединяется со шпинделем намоточной головки и работает совмемтно с механизмом раскладки ПДА.417.026.00, обеспечивающим подачу одновременно двух проводов.
Установка сменных частей на станке СНПУ-2-01
Возникла необходимость постоянной перемотки проволоки СВ 0,8Г2К с 15 кГ бухт на 5 кГ катушки.Для собственного применения(примерно 15 кГ бухта пару раз в месяц),поэтому вариант с намоточным станком отпадает. Господа сварщики, как Вы решаете подобную проблему?
дрель и штырь Вам в помощь
Если аппарат используется как стационар то можно не перематывать, проще сделать так » >
Точно. Катушку на ручную дрель и в тиски. Спасибо за мысль.
Kiria написал :
Точно. Катушку на ручную дрель и в тиски. Спасибо за мысль.
Можно и вручную.
Пробовали. Изрезали все руки. Нецензурно ругались и плевались на пол.
Опять-же, при ручной намотке на проволоке появляются заломы(потом двигается рывками) и на катушку мало влезает. Ну не наш метод.
Kiria написал :
Катушку на ручную дрель и в тиски
Можно и на родной катушкодержатель, ролики только ослабить
Выполним перемотку катушек сварочных аппаратов.
Сытый конному не пеший!
Tomkol ,
Наверное очень хороший вариант )) Но вот только доступа к этому блогу нет даже с регистрацией на драйве ))
P.S. Парни вы уж вообще всё выкладывайте под паролем и там куда гарантированно никто зайти не сможет , для гарантии чтобы никто не увидел ))
Tomkol ,
Наверное очень хороший вариант )) Но вот только доступа к этому блогу нет даже с регистрацией на драйве ))
P.S. Парни вы уж вообще всё выкладывайте под паролем и там куда гарантированно никто зайти не сможет , для гарантии чтобы никто не увидел ))
bellkin , виноват, не знал. Думал, там всё в свободном доступе. Просто там намного проще фотки вставлять. Но постараюсь реабилитироваться
Итак, дабы не создавать нечто громоздкое (бо в гараже и так барахла подобного хватает), решил максимально минимизировать эти приспособы.
Общий вид готового изделия
Ну а суть конструкции и процесса перемотки видно из остальных фоток
Большая катушка стоит на полу
а кронштейн с малой зажат в тисках на столе
Вид сверху. Большая катуха, стоящая на полу, из-за перспективных искажений на фото наоборот кажется маленькой
Ну и готовый результат. Не идеально рядная намотка, но зато быстро
Держалку для малой катушки сделал с подшипниками, чтоб её легче вращать дрелькой было.
А вот держалку для большой катухи сделал без подшипников потому, что предположил, что она трошки подтормаживаться будет и проволока с неё самопроизвольно не размотается. Но в процессе работы, а вернее — когда прекращал этот процесс, то всё-равно приходилось ногой гасить инерцию вращения большой катухи. Благо, что она на полу стоит.
Все размеры приспособ прикидывал на глаз по ходу их изготовления. Ну и исходя из того, какой металлолом в гараже был под руками. Запас разнокалиберных шпилек, гаек и шайб всегда есть. Единственное, что пришлось искать по соседним гаражам — убитые подшипники подходящего диаметра.
Держалку с большой 15 кг катухой можно использовать и с полуавтоматом, если он используется стационарно. Но мне приходится периодически на халтурки его брать. Поэтому удобнее всё ж, чтоб 5-килограммовая катушка была внутри аппарата.
ostwest.su
598 | НПП Технотрон, ООО
ТТ-598 — Установка предназначена для автоматической аргонодуговой сварки кольцевых швов неплавящимся электродом диаметром до 300 мм в вертикальном и горизонтальном положении.
Для закрепления деталей – заготовок используется токарный патрон, установленный на вращателе.
Установка предназначена для эксплуатации в помещениях (объемах) с искусственно регулируемыми климатическими условиями.
Тип атмосферы − II по ГОСТ 15150−69.
Климатическое исполнение установки соответствует категории УХЛ4 по ГОСТ 15150−69, но для работы при температурах от плюс 1 до плюс 40 °С.
В части стойкости к механическим внешним воздействующим факторам при эксплуатации установка относится к группе М20 со степенью жесткости 21а по ГОСТ 17516.1−90.
Установка устойчива к воздействию температуры окружающего воздуха от плюс 1 до плюс 40 °С и относительной влажности до 90 % при температуре плюс 20 °С.
Степень защиты установки − не ниже IР22 по ГОСТ 14254-96.
Технические требования и характеристики оборудования.
Диаметр свариваемых заготовок, мм | от 10 до 300 |
Длина свариваемой заготовки, мм, не более | от 10 до 600 |
Максимальная масса свариваемых деталей, кг | 50 |
Скорость сварки, мм/с | от 0,3 до 16 |
Диаметр присадочной проволоки, мм | 0,8; 1,0; 1,2 |
Скорость подачи присадочной проволоки, мм/с | от 5 до 40 |
Скорость перемещения горелки: — по вертикали, мм/с — по горизонтали, мм/с |
6 6 |
Допустимые отклонения скорости перемещения горелки, % | ±10 |
Величина перемещения горелки: — по вертикали, мм — по горизонтали, мм |
±40 ±40 |
Допустимые отклонения величины перемещения горелки. % | ±10 |
Регулировка величины колебаний горелки | бесступенчатая |
Скорость колебания горелки (дискретность 1 мм/с), мм/с | от 10 до 100 |
Охлаждение горелки | жидкостное |
Максимальное давление охлаждающей жидкости, МПа | 0,3 |
Напряжение питающей сети переменного тока, В | 380, ±10% |
Частота тока питающей сети, Гц | 50, +15Гц/-5Гц |
Предел регулирования сварочного тока (дискретность 1А), А | от 5 до 315 |
Потребляемая мощность установки, кВ∙А, не более | 15 |
Масса установки, кг, не более | 286 |
Масса блока приборов, кг, не более | 6 |
Масса пульта оператора, кг, не более | 3 |
Габаритные размеры установки, мм, не более | 1300×725×1800 |
Габаритные размеры блока приборов, мм, не более | 310×242×244 |
Габаритные размеры пульта оператора, мм, не более | 275×220×100 |
1 – источник питания; 2 – блок управления; 3 – блок приборов; 4 – блок принудительного охлаждения; 5 – пульт оператора; 6 – тележка; 7 – вращатель; |
8 – головка сварочная; 9 – механизм подающий; 10 – опора; 11 – задняя бабка; 12 – светильник; 13 – стол; 14 – фиксатор. |
Модификация установки ТТ598 длиной 6м с регулируемыми опорами
xn--e1aqadalkdy.xn--p1ai
Процесс сварки сплошной проволокой | НПП Технотрон, ООО
Процесс сварки сплошной проволокой в активных газах и смесях с управляемым комплексом (УПК)
Процесс УКП реализован НПП «Технотрон», ООО на базе источника ДС400.33УКП.
Традиционный процесс сварки в СО2 и смесях реализуется в настоящее время простейшим или инверторным выпрямителем с пологопадающей внешней характеристикой и включенным в сварочную цепь дросселем. Пологопадающая характеристика обуславливает саморегулирование дуги, дроссель ограничивает скорость нарастания тока КЗ, а накопленная во время КЗ энергия расходуется на плавление электрода и образование капли.
Основные недостатки традиционного процесса:
- в момент касания капли с ванной (точка 5 Рис.1) зона контакта минимальная и электродинамическая сила протекающего через перемычку препятствует переходу капли в ванну. Эта сила может вызвать отброс капли от поверхности ванны, а проходящий ток — перегрев и взрыв, образующейся перемычки. При этом капля, отрываясь от электрода, улетает в виде брызг, либо остается на торце электрода и переходит в ванну при следующем КЗ;
- после втекания капли в ванну за счет протекающего тока КЗ (пинг-эффект) происходит уменьшение диаметра перемычки между электродом и каплей. Далее происходит взрыв перемычки и капля полностью перетекает в ванну (точка 2 и 3 Рис.1). Происходит спад тока. Энергия накопленная в дросселе расходуется на зажигании дуги и образование новой капли. Из-за различного рода возмущений разрыв перемычки может произойти в точках 1,2,3 или 4.
Это приводит к тому, что энергия, идущая на образование следующей капли, будет разной, что в свою очередь ведет к нестабильности процесса.
Для устранения этих недостатков, начиная, примерно с 1970 года предприняты значительные усилия различными научными организациями. Большой вклад в это внесли И.И. Заруба, С.И. Пинчук, А.Г. Потаньявский, А.В. Лебедев, А.Ф. Князьков, Ю.Н. Сараев и др. Однако реализации идеи мешало отсутствие быстродействующей элементной базы. Только создание быстродействующих транзисторных инверторов позволило реализовать процесс сварки на основе высказанных идей практически.
В 1985 году компанией Lincoln Electric была создана сварочная система SST, способная управлять переносом электродного металла.
В НПП «Технотрон», ООО на базе транзисторного инвертора создан источник ДС400.33УКП, реализующий принцип управляемого каплепереноса (УКП). Данный источник позволяет успешно производить сварку тонкого металла и сварку по открытому зазору с формированием качественного обратного валика.
Процесс УКП организован следующим образом:
- капля касается ванны (точка 1). В этот момент ток по сигналу обратной связи сбрасывается почти до нуля на время 0,7-0,8 мс. За это время пятно контакта капли с ванной развивается, происходит «врастание» капли в сварочную ванну;
- в точке 2 токовая пауза заканчивается и начинается резкое нарастание тока КЗ до точки 3. Резкое нарастание ток в нашем случае возможно, так как капля уже надежно контактирует с ванной. Кроме того, это нужно для уменьшения времени КЗ за счет быстрого образования и сужения шейки между электродом и каплей. Ток КЗ возрастает до точки 3. Далее ток КЗ почти не меняется (плавно нарастает), так как для разрыва суженной перемычки между каплей и ванной большой ток не нужен.
- в момент 4 перемычка между электродом 4 и каплей разрушается. В это время по сигналу обратной связи включается ток импульса определенной (фиксированной) длительности и амплитуды 5 (регулируемой). В этот момент зажигается дуга и происходит образование новой капли. Дозированная амплитуда и длительность позволяют стабилизировать размер образовавшейся капли. Далее ток снижается до уровня базового — 6. Спад тока может пойти по кривым 7, 8 или 9 (параметр регулируется). Эта регулировка позволяет менять тепловложение в сварочную ванну. Ток поддерживается на уровне базового 6 до следующего короткого замыкания.
Основные регулируемые параметры при сварке корневого шва
Базовый ток — определяет общее тепловложение и форму обратного валика. Если базовый ток очень высокий, то будет хорошее проплавление, но недостаточная высота обратного валика. Низкое значение базового тока формирует высокий обратный валик, но возможно несплавление кромок.
Базовый ток устанавливается в пределах 30-150А.
Ток импульса — управляет длиной дуги и влияет на внешнюю поверхность корневого шва. Увеличение тока приводит к формированию более плоской внешней поверхности шва. Кроме того, ток импульса оказывает влияние на общее тепловложение.
Ток импульса устанавливается в пределах 200-500А.
Спад тока — регулирует тепловложение. Устанавливается в пределах 1-70 условных единиц.
Ток КЗ — регулирует амплитуду первоначального нарастания тока КЗ до точки 3 Рис.2. Устанавливается в зависимости от диаметра используемой проволоки и вида защитного газа.
Регулируется в пределах 110-300А. (21-40 в условных единицах).
Рекомендуемые режимы сварки корневого шва проволокой L-56 в СО2
Показатель | Ед. изм. | Значение |
---|---|---|
Базовый ток | А | 50-60 |
Ток импульса | А | 230-250 |
Спад | у.е. | 1-3 |
Скорость подачи проволоки | мм/с | 50-60 |
Скорость колебания электрода | мм/с | 10-15 |
Время задержки на кромках | с | 0-0.5 |
Амплитуда колебаний | мм | 0-4 |
Рекомендуемый зазор между кромками | мм | 3-4 |
xn--e1aqadalkdy.xn--p1ai
69 | НПП Технотрон, ООО
Установка контактной продольной роликовой сварки ТТ-69М предназначена для сварки продольных швов длиной до 200 мм. Сварка производится . Возможна сварка продольных швов цилиндрических деталей.
Установка комплектуется оснасткой для сварки конкретных деталей.
Установка может быть использована для выполнения продольных швов на изделиях из различных сплавов. Толщина одной из свариваемых деталей должна быть до 0,8 мм.
Свариваемое изделие устанавливается в специальную оснастку(оправку) или непосредственно на продольную подложку установки. При помощи специального рычага сварочный ролик опускается, прижимая детали с усилием, заданным преднатяжением пружины. После нажатия кнопки производится цикл сварки с заданными параметрами сварочных импульсов, скоростью и шагом сварки.
Установка ТТ-69М имеет заводскую гарантию 2 года.
Панель управления установки ТТ-69 На панели размещены цифровой индикатор параметров, энкодер задания длины сварочного шва, шага сварки, скорости сварки, индикатор питания, кнопка установки точечной прихватки, кнопки вращения шпинделя установки в наладочном режиме, тумблер включения сварочного источника, тумблер включения вращения шпинделя, тумблер переключения между наладочным режимом и автоматическим режимом, индикатор включения цикла сварки, кнопки запуска и остановки сварки. |
Источник тока контактной сварки инверторного типа «ИМПУЛЬС-3» — предназначен для контактной точечной сварки деталей малых толщин (до 1,2мм).
Поставляется с блоком выпрямительным ТТ-323 (с воздушным или жидкостным охлаждением).
Источник может быть использован для работы в составе точечных или шовных установок контактной сварки, а также с ручным инструментом.
Область применения источника — соединение прецизионных узлов и деталей в приборостроении и электронной технике методом контактной сварки. Максимальная толщина свариваемых материалов:
— малоуглеродистая сталь — до 1,0 мм;
— нержавеющая сталь — до 1,2 мм;
— латунь, бронза — до 0,4 мм;
Источник поставляется с выпрямительным блоком.
Источник «ИМПУЛЬС-3» имеет заводскую гарантию 2 года.
Технические характеристики источника
Напряжение питания, В | 380 |
Вид сварочного тока | постоянный |
Амплитуда сварочного тока (регулируемая), А | 300 — 7500 |
Длительность сварочного импульса, регулируемая, мс | 1 — 20 |
Длительность фронта импульса тока, регулируемая, мс (дискретность 1 мс) | 1 — 5 |
Максимальная производительность, сварок/с | 10 |
Точность поддержания установленного значения сварочного тока при изменении сопротивления нагрузки в 2 раза | + 10 % |
Точность поддержания установленного значения сварочного тока при колебаниях напряжения сети плюс 10 %, минус 15 % | + 2 % |
Количество записываемых в память режимов | 10 |
Габаритные размеры, мм источника блока выпрямительного | 545?232?425 345?246?296 |
Масса, кг источника блока выпрямительного | 22 13 |
Максимальная потребляемая мощность в режиме шовной сварки, кВт | 2 |
Панель управления источника «Импульс-3»
График регулируемого наклона фронта импульса.
Регулирование наклона фронта импульса необходимо для того, чтобы убрать возможные выплески металла из сварочной зоны. При сварке деталей из токопроводящих металлов и сплавов (медных, серебряных и т.д.) применяется более крутой фронт импульса, а при сварке малоуглеродистых и нержавеющих сталей применяется более пологий фронт импульса — с целью устранения выплесков из контактной зоны и более эффективного управления тепловложения в зону образования сварочного ядра.
xn--e1aqadalkdy.xn--p1ai
84 | НПП Технотрон, ООО
Установка шовной сварки сильфонов — ТТ-84 предназначена для сварки тонкостенных цилиндрических деталей. Толщина тонкой детали при этом не должна превышать 0,8 мм.
Установка комплектуется оснасткой для сварки конкретных деталей.
Находит широкое применение для сварки цилиндрических деталей к цилиндрическим корпусным (для выполнения сварки тонкостенная деталь должна быть предварительно напрессована на корпусную, желательно с натягом), сильфонов с арматурой. Установка может быть использована также для выполнения круговых швов на других изделиях.
Установкаимеет ТТ-84 заводскую гарантию 2 года.
Панель управления установки ТТ-84 На панели размещены цифровой индикатор параметров, энкодер задания диаметра сварочного шва, скорости сварки, шага сварки и перекрытия сварочного шва, индикатор питания, кнопка установки точечной прихватки, включения сварочного источника, кнопки вращения шпинделя установки в наладочном режиме, тумблер включения сварочного источника, тумблер включения вращения шпинделя, тумблер переключения между наладочным режимом и автоматическим режимом, индикатор включения цикла сварки, кнопки запуска и остановки сварки. Свариваемое изделие устанавливается в специальную оснастку(оправку) расположенную на оси шпинделя вращения. Специальным рычагом сварочный ролик и прижимной ролик подводятся к детали, сжимая ее с усилием, заданным преднатяжением пружин. После нажатия кнопки <Пуск> производится цикл сварки с заданными параметрами сварочных импульсов, скоростью и шагом сварки. Выполняется полный оборот с заданным перекрытием. |
Источник тока контактной сварки инверторного типа <ИМПУЛЬС-3> — предназначен для контактной точечной сварки деталей малых толщин (до 1,2мм).
Поставляется с блоком выпрямительным ТТ-323 (с воздушным или жидкостным охлаждением).
Источник может быть использован для работы в составе точечных или шовных установок контактной сварки, а также с ручным инструментом.
Область применения источника — соединение прецизионных узлов и деталей в приборостроении и электронной технике методом контактной сварки. Максимальная толщина свариваемых материалов:
— малоуглеродистая сталь — до 1,0 мм;
— нержавеющая сталь — до 1,2 мм;
— латунь, бронза — до 0,4 мм;
Источник поставляется с выпрямительным блоком.
Источник «ИМПУЛЬС-3» имеет заводскую гарантию 2 года.
Технические характеристики источника
Напряжение питания, В | 380 |
Вид сварочного тока | постоянный |
Амплитуда сварочного тока (регулируемая), А | 300 — 7500 |
Длительность сварочного импульса, регулируемая, мс | 1 — 20 |
Длительность фронта импульса тока, регулируемая, мс (дискретность 1 мс) | 1 — 5 |
Максимальная производительность, сварок/с | 10 |
Точность поддержания установленного значения сварочного тока при изменении сопротивления нагрузки в 2 раза | + 10 % |
Точность поддержания установленного значения сварочного тока при колебаниях напряжения сети плюс 10 %, минус 15 % | + 2 % |
Количество записываемых в память режимов | 10 |
Габаритные размеры, мм источника блока выпрямительного | 545?232?425 345?246?296 |
Масса, кг источника блока выпрямительного | 22 13 |
Максимальная потребляемая мощность в режиме шовной сварки, кВт | 2 |
Панель управления источника «Импульс-3»
График регулируемого наклона фронта импульса.
Регулирование наклона фронта импульса необходимо для того, чтобы убрать возможные выплески металла из сварочной зоны. При сварке деталей из токопроводящих металлов и сплавов (медных, серебряных и т.д.) применяется более крутой фронт импульса, а при сварке малоуглеродистых и нержавеющих сталей применяется более пологий фронт импульса — с целью устранения выплесков из контактной зоны и более эффективного управления тепловложения в зону образования сварочного ядра.
xn--e1aqadalkdy.xn--p1ai
ТТ-582 сварка трубных узлов | НПП Технотрон, ООО
Установка автоматической сварки трубных узлов ТТ-582 — предназначена для автоматической сварки в непрерывных и импульсных режимах поворотных стыков стальных труб:
— порошковыми проволоками в среде защитных, активных газов и их смесях;
— проволоками сплошного сечения в среде защитных, активных газов и их смесях, в том числе для односторонней сварки корневого слоя шва неповоротных и поворотных стыков труб по открытому зазору.
Сварка производится с наложением поперечных колебаний сварочной горелки.
Технические характеристики установки
Диапазон диаметров свариваемых труб, мм | 57 — 530 |
Общая длина свариваемых деталей, мм | до 5000 |
Грузоподъемность вращателя, кг | до 1000 |
Толщина стенки свариваемых изделий, мм | до 20 |
Диаметр электродной проволоки, мм | 0,8 — 2,0 |
Скорость вращения, мм/сек | 0 — 15 |
Скорость подачи электродной проволоки, мм/сек | 16 — 266 |
Размах колебаний сварочной головки, мм | 0 — 20 |
Охлаждение горелки | жидкостное |
Время «задержки на кромках», с | 0 — 1,2 |
Сварочный ток, А | до 500 |
Продолжительность нагрузки ПН, % | 100 |
Потребляемая мощность, кВ·А, не более | 27 |
Масса, кг | 730 |
Габаритные размеры, мм | 1220х420х1500 |
1 – источник питания ДС400.33М;
|
Источник питания ДC400.33М (1) — промышленный инверторный аппарат на ток до 500А предназначенный для механизированной сварки в режиме с короткими замыканиями, в струйном и импульсном режиме.
Головка сварочная (3) состоит из механизма колебания горелки, механизма корректировки вертикального положения горелки, рукоятки изменения вертикального положения горелки, рукоятки изменения горизонтального положения горелки.
Универсальный вращатель труб УВТ-2 (4) предназначен для вращения труб при сварке, имеет электропривод поднятия и опускания прижимных роликов и электропривод вращения приводных роликов.
Сварка трубы 325х16 в импульсном режиме |
Вид сварочного шва трубы 325х16 |
ДC400.33М — современный промышленный инверторный аппарат на ток до 500А предназначенный для механизированной сварки в режиме с короткими замыканиями, в струйном и импульсном режиме.
Аппарат обеспечивает точное поддержание режимов сварки (не зависимо от длины силовых кабелей и перепадов напряжения в сети питания), высокое качество сварочных швов со всеми видами сварочной проволоки, минимальное разбрызгивание, мягкое зажигание и плавное гашение дуги и устойчивое её горение в процессе сварки.
- сварка газозащитной проволокой сплошного сечения и порошковой проволокой.
- сварка самозащитной порошковой проволокой.
- Регулируемое время «горячего старта», от 0 до 2 секунд. Необходимо для улучшения зажигания сварочной дуги и формирования качественного начала шва.
- Цифровая индикация тока и напряжения сварки.
Технические характеристики аппарата ДC400.33М
Напряжение питания, В | 380 ,+10% -10% |
Потребляемая мощность, кВА, не более | 24 |
Напряжение источника MIG/MAG (плавнорегулируемое, дискретность 0,1), В | 16,5-34 |
Сварочный ток MIG/MAG, А | 50-500 |
Номинальный режим работы ПН, % | 100 |
Диапазон рабочих температур, С | От -40 до +40 |
Масса, кг | 50 |
Габаритные размеры, мм | 610270535 |
Блок импульсного режима позволяет производить сварку черных и нержавеющих сталей, алюминия и его сплавов в импульсном режиме с высокой производительностью и пониженным разбрызгиванием. Сварка ведется в аргоновых смесях. Наиболее распространены смеси Ar/CO2 (80%/20%).
Блок снабжен функцией синергетического управления сваркой. Сварщику необходимо задать только параметры сварочной проволоки и скорость ее подачи. Остальные параметры сварочного процесса источник выбирает автоматически.
Импульсный перенос металла.
Импульсный перенос металла является серьёзным усовершенствованием технологии сварки, т.к. он сочетает преимущества всех остальных методов переноса, будучи при этом практически полностью лишён характерных для этих методов недостатков. В отличие от переноса серией коротких замыканий, импульсный процесс не создаёт брызг и не склонен к образованию несплавлений. Положения, в которых может проводиться сварка по импульсному процессу, не ограничены, как в случае процесса струйного переноса, а использование сварочной проволоки гораздо более эффективно. Обладая меньшим тепловложением, по сравнению с методом переноса с помощью микрокапель, импульсный процесс позволяет сваривать более широкий диапазон деталей. Именно снижение тепловложения при импульсном процессе повышает качество сварки тонких материалов, исключая прожоги и снижая коробление, а также позволяя вести сварку при более низких скоростях подачи проволоки.При импульсной сварке происходит бесконтактный перенос металла с электрода в сварочную ванну. Иными словами, ни при каких условиях и ни в какой момент времени электрод не контактирует со сварочной ванной.
Характерная особенность импульсно-дуговой сварки плавящимся электродом — управляемый перенос электродного металла. Сварка осуществляется без замыканий дугового промежутка и обеспечивает перенос одной капли металла за каждый импульс тока. Во время импульса тока происходит резкое увеличение электродинамических сил, которые сбрасывают каплю строго в сварочную ванну.
Использование технологии импульсной сварки в аргоновых смесях позволяет получить:
|
Модуль индикации предназначен для индикации параметров шаблонных программ сварки – диаметра сварочной проволоки, материала сварочной проволоки или индикации номера специальной программы сварочных режимов. Также на индикаторе отображаются технологические параметры специальных режимов сварки. Энкодер предназначен для выбора или изменения параметров сварки. Резистор предназначен для управления длиной сварочной дуги.
Использование блока импульсного режима.
Блок импульсного режима имеет два режима работы:
Шаблонные программы – сварочные программы, жестко «зашитые» в память аппарата и описывающие работу со стандартными наборами материалов, проволок и газов.
Для работы в режиме шаблонных программ необходимо задать только:
— диаметр и материал сварочной проволоки,
— скорость подачи сварочной проволоки
Остальные параметры сварочного процесса источник определяет автоматически.
Специальный режим предназначен для задания индивидуальных программ сварки, не описанных шаблонными программами. Можно записать и вызвать из памяти до 20 специальных программ.
В этом режиме можно настроить работу источника с наименее распространенными комбинациями: защитный газ – сварочная проволока. Регулируются параметры импульса, частота следования импульсов и т.д.
xn--e1aqadalkdy.xn--p1ai