ΠΠ°ΠΊ ΡΠΎΠ±ΡΠ°ΡΡ ΠΊΠΎΠ½ΡΡΠΎΠ»Π»Π΅Ρ Π§ΠΠ£ ΡΠ°ΠΌΠΎΡΡΠΎΡΡΠ΅Π»ΡΠ½ΠΎ. ΠΠ°ΠΊΠΈΠ΅ ΠΊΠΎΠΌΠΏΠΎΠ½Π΅Π½ΡΡ ΠΏΠΎΡΡΠ΅Π±ΡΡΡΡΡ Π΄Π»Ρ ΡΠ±ΠΎΡΠΊΠΈ ΠΊΠΎΠ½ΡΡΠΎΠ»Π»Π΅ΡΠ°. ΠΠ°ΠΊ ΠΏΡΠ°Π²ΠΈΠ»ΡΠ½ΠΎ ΠΏΠΎΠ΄ΠΊΠ»ΡΡΠΈΡΡ ΠΈ Π½Π°ΡΡΡΠΎΠΈΡΡ ΠΊΠΎΠ½ΡΡΠΎΠ»Π»Π΅Ρ Π§ΠΠ£. ΠΠ°ΠΊΠΎΠ΅ ΠΏΡΠΎΠ³ΡΠ°ΠΌΠΌΠ½ΠΎΠ΅ ΠΎΠ±Π΅ΡΠΏΠ΅ΡΠ΅Π½ΠΈΠ΅ ΠΈΡΠΏΠΎΠ»ΡΠ·ΠΎΠ²Π°ΡΡ Π΄Π»Ρ ΡΠΏΡΠ°Π²Π»Π΅Π½ΠΈΡ ΡΠ°ΠΌΠΎΠ΄Π΅Π»ΡΠ½ΡΠΌ ΠΊΠΎΠ½ΡΡΠΎΠ»Π»Π΅ΡΠΎΠΌ Π§ΠΠ£.
Π§ΡΠΎ ΡΠ°ΠΊΠΎΠ΅ ΠΊΠΎΠ½ΡΡΠΎΠ»Π»Π΅Ρ Π§ΠΠ£ ΠΈ Π·Π°ΡΠ΅ΠΌ ΠΎΠ½ Π½ΡΠΆΠ΅Π½
ΠΠΎΠ½ΡΡΠΎΠ»Π»Π΅Ρ Π§ΠΠ£ (ΡΠΈΡΠ»ΠΎΠ²ΠΎΠ³ΠΎ ΠΏΡΠΎΠ³ΡΠ°ΠΌΠΌΠ½ΠΎΠ³ΠΎ ΡΠΏΡΠ°Π²Π»Π΅Π½ΠΈΡ) — ΡΡΠΎ ΡΡΡΡΠΎΠΉΡΡΠ²ΠΎ, ΠΊΠΎΡΠΎΡΠΎΠ΅ ΡΠΏΡΠ°Π²Π»ΡΠ΅Ρ ΡΠ°Π±ΠΎΡΠΎΠΉ ΡΡΠ°Π½ΠΊΠ° Ρ Π§ΠΠ£. ΠΡΠ½ΠΎΠ²Π½ΡΠ΅ ΡΡΠ½ΠΊΡΠΈΠΈ ΠΊΠΎΠ½ΡΡΠΎΠ»Π»Π΅ΡΠ°:
- ΠΠ½ΡΠ΅ΡΠΏΡΠ΅ΡΠ°ΡΠΈΡ G-ΠΊΠΎΠ΄Π° ΠΈ ΠΏΡΠ΅ΠΎΠ±ΡΠ°Π·ΠΎΠ²Π°Π½ΠΈΠ΅ Π΅Π³ΠΎ Π² ΠΊΠΎΠΌΠ°Π½Π΄Ρ Π΄Π»Ρ Π΄Π²ΠΈΠ³Π°ΡΠ΅Π»Π΅ΠΉ ΡΡΠ°Π½ΠΊΠ°
- Π£ΠΏΡΠ°Π²Π»Π΅Π½ΠΈΠ΅ ΡΠ°Π³ΠΎΠ²ΡΠΌΠΈ Π΄Π²ΠΈΠ³Π°ΡΠ΅Π»ΡΠΌΠΈ ΠΈΠ»ΠΈ ΡΠ΅ΡΠ²ΠΎΠΏΡΠΈΠ²ΠΎΠ΄Π°ΠΌΠΈ ΠΎΡΠ΅ΠΉ ΡΡΠ°Π½ΠΊΠ°
- ΠΠΎΠ½ΡΡΠΎΠ»Ρ ΡΠΊΠΎΡΠΎΡΡΠΈ ΠΈ ΡΡΠΊΠΎΡΠ΅Π½ΠΈΡ ΠΏΠ΅ΡΠ΅ΠΌΠ΅ΡΠ΅Π½ΠΈΡ ΠΎΡΠ΅ΠΉ
- Π£ΠΏΡΠ°Π²Π»Π΅Π½ΠΈΠ΅ ΡΠΏΠΈΠ½Π΄Π΅Π»Π΅ΠΌ
- ΠΠ±ΡΠ°Π±ΠΎΡΠΊΠ° ΡΠΈΠ³Π½Π°Π»ΠΎΠ² Ρ Π΄Π°ΡΡΠΈΠΊΠΎΠ² ΡΡΠ°Π½ΠΊΠ°
ΠΠ΅Π· ΠΊΠΎΠ½ΡΡΠΎΠ»Π»Π΅ΡΠ° Π§ΠΠ£ Π½Π΅Π²ΠΎΠ·ΠΌΠΎΠΆΠ½Π° Π°Π²ΡΠΎΠΌΠ°ΡΠΈΠ·ΠΈΡΠΎΠ²Π°Π½Π½Π°Ρ ΡΠ°Π±ΠΎΡΠ° ΡΡΠ°Π½ΠΊΠ° ΠΏΠΎ Π·Π°Π΄Π°Π½Π½ΠΎΠΉ ΠΏΡΠΎΠ³ΡΠ°ΠΌΠΌΠ΅. ΠΠΎΡΡΠΎΠΌΡ ΡΠ±ΠΎΡΠΊΠ° ΠΊΠΎΠ½ΡΡΠΎΠ»Π»Π΅ΡΠ° — Π²Π°ΠΆΠ½ΡΠΉ ΡΡΠ°ΠΏ Π² ΡΠΎΠ·Π΄Π°Π½ΠΈΠΈ ΡΠ°ΠΌΠΎΠ΄Π΅Π»ΡΠ½ΠΎΠ³ΠΎ ΡΡΠ°Π½ΠΊΠ° Ρ Π§ΠΠ£.
ΠΡΠ±ΠΎΡ ΠΊΠΎΠΌΠΏΠΎΠ½Π΅Π½ΡΠΎΠ² Π΄Π»Ρ ΡΠ±ΠΎΡΠΊΠΈ ΠΊΠΎΠ½ΡΡΠΎΠ»Π»Π΅ΡΠ° Π§ΠΠ£
ΠΠ»Ρ ΡΠ±ΠΎΡΠΊΠΈ ΠΏΡΠΎΡΡΠΎΠ³ΠΎ ΠΊΠΎΠ½ΡΡΠΎΠ»Π»Π΅ΡΠ° Π§ΠΠ£ ΡΠ²ΠΎΠΈΠΌΠΈ ΡΡΠΊΠ°ΠΌΠΈ ΠΏΠΎΡΡΠ΅Π±ΡΡΡΡΡ ΡΠ»Π΅Π΄ΡΡΡΠΈΠ΅ ΠΎΡΠ½ΠΎΠ²Π½ΡΠ΅ ΠΊΠΎΠΌΠΏΠΎΠ½Π΅Π½ΡΡ:
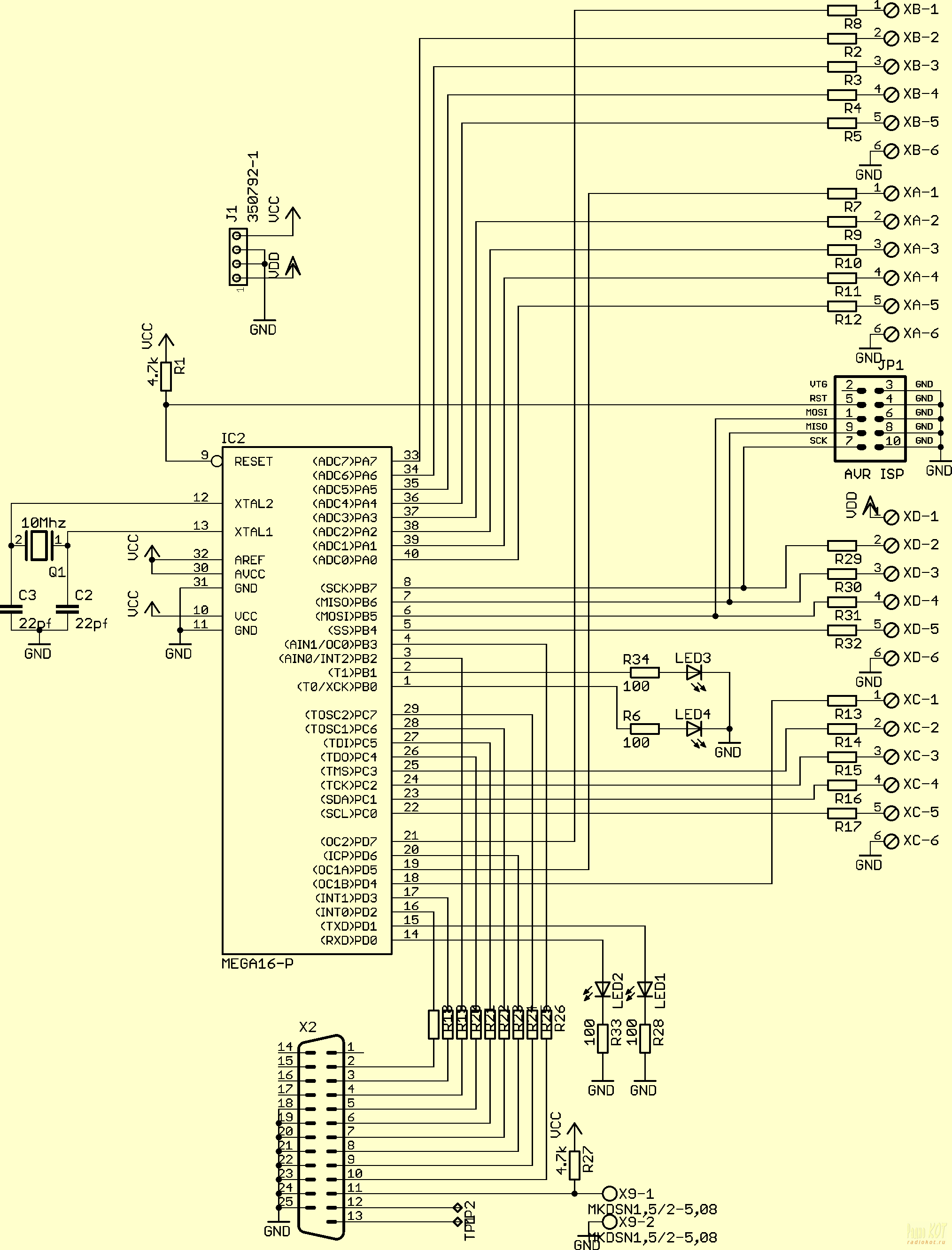
- ΠΠΈΠΊΡΠΎΠΊΠΎΠ½ΡΡΠΎΠ»Π»Π΅Ρ (Π½Π°ΠΏΡΠΈΠΌΠ΅Ρ, ATmega328P ΠΈΠ»ΠΈ STM32)
- ΠΡΠ°ΠΉΠ²Π΅ΡΡ ΡΠ°Π³ΠΎΠ²ΡΡ Π΄Π²ΠΈΠ³Π°ΡΠ΅Π»Π΅ΠΉ
- ΠΡΡΠΎΡΠ½ΠΈΠΊ ΠΏΠΈΡΠ°Π½ΠΈΡ
- ΠΠ»Π°ΡΠ° Π΄Π»Ρ ΠΌΠΎΠ½ΡΠ°ΠΆΠ° ΠΊΠΎΠΌΠΏΠΎΠ½Π΅Π½ΡΠΎΠ²
- Π Π°Π·ΡΠ΅ΠΌΡ Π΄Π»Ρ ΠΏΠΎΠ΄ΠΊΠ»ΡΡΠ΅Π½ΠΈΡ Π΄Π²ΠΈΠ³Π°ΡΠ΅Π»Π΅ΠΉ ΠΈ Π΄Π°ΡΡΠΈΠΊΠΎΠ²
ΠΡΠ±ΠΎΡ ΠΊΠΎΠ½ΠΊΡΠ΅ΡΠ½ΡΡ ΠΊΠΎΠΌΠΏΠΎΠ½Π΅Π½ΡΠΎΠ² Π·Π°Π²ΠΈΡΠΈΡ ΠΎΡ ΡΡΠ΅Π±ΡΠ΅ΠΌΠΎΠΉ ΡΡΠ½ΠΊΡΠΈΠΎΠ½Π°Π»ΡΠ½ΠΎΡΡΠΈ ΠΈ Π±ΡΠ΄ΠΆΠ΅ΡΠ°. ΠΠ»Ρ Π½Π°ΡΠΈΠ½Π°ΡΡΠΈΡ ΠΎΠΏΡΠΈΠΌΠ°Π»ΡΠ½ΠΎ ΠΈΡΠΏΠΎΠ»ΡΠ·ΠΎΠ²Π°ΡΡ Π³ΠΎΡΠΎΠ²ΡΠ΅ Π½Π°Π±ΠΎΡΡ Π΄Π»Ρ ΡΠ±ΠΎΡΠΊΠΈ ΠΊΠΎΠ½ΡΡΠΎΠ»Π»Π΅ΡΠΎΠ² Π§ΠΠ£ Π½Π° ΠΎΡΠ½ΠΎΠ²Π΅ Arduino ΠΈΠ»ΠΈ Π΄ΡΡΠ³ΠΈΡ ΠΏΠΎΠΏΡΠ»ΡΡΠ½ΡΡ ΠΏΠ»Π°ΡΡΠΎΡΠΌ.
ΠΠΎΡΠ°Π³ΠΎΠ²Π°Ρ ΠΈΠ½ΡΡΡΡΠΊΡΠΈΡ ΠΏΠΎ ΡΠ±ΠΎΡΠΊΠ΅ ΠΊΠΎΠ½ΡΡΠΎΠ»Π»Π΅ΡΠ° Π§ΠΠ£
Π Π°ΡΡΠΌΠΎΡΡΠΈΠΌ ΠΎΡΠ½ΠΎΠ²Π½ΡΠ΅ ΡΡΠ°ΠΏΡ ΡΠ±ΠΎΡΠΊΠΈ ΠΏΡΠΎΡΡΠΎΠ³ΠΎ ΠΊΠΎΠ½ΡΡΠΎΠ»Π»Π΅ΡΠ° Π§ΠΠ£ Π½Π° Π±Π°Π·Π΅ Arduino:
- ΠΠΎΠ΄Π³ΠΎΡΠΎΠ²ΡΡΠ΅ Π²ΡΠ΅ Π½Π΅ΠΎΠ±Ρ ΠΎΠ΄ΠΈΠΌΡΠ΅ ΠΊΠΎΠΌΠΏΠΎΠ½Π΅Π½ΡΡ ΠΈ ΠΈΠ½ΡΡΡΡΠΌΠ΅Π½ΡΡ
- Π£ΡΡΠ°Π½ΠΎΠ²ΠΈΡΠ΅ ΠΌΠΈΠΊΡΠΎΠΊΠΎΠ½ΡΡΠΎΠ»Π»Π΅Ρ Arduino Π½Π° ΠΌΠΎΠ½ΡΠ°ΠΆΠ½ΡΡ ΠΏΠ»Π°ΡΡ
- ΠΠΎΠ΄ΠΊΠ»ΡΡΠΈΡΠ΅ Π΄ΡΠ°ΠΉΠ²Π΅ΡΡ ΡΠ°Π³ΠΎΠ²ΡΡ Π΄Π²ΠΈΠ³Π°ΡΠ΅Π»Π΅ΠΉ ΠΊ Arduino ΡΠΎΠ³Π»Π°ΡΠ½ΠΎ ΡΡ Π΅ΠΌΠ΅
- ΠΠΎΠ΄ΠΊΠ»ΡΡΠΈΡΠ΅ ΡΠ°Π·ΡΠ΅ΠΌΡ Π΄Π»Ρ Π΄Π²ΠΈΠ³Π°ΡΠ΅Π»Π΅ΠΉ ΠΈ ΠΊΠΎΠ½ΡΠ΅Π²ΡΡ Π΄Π°ΡΡΠΈΠΊΠΎΠ²
- ΠΠΎΠ΄ΠΊΠ»ΡΡΠΈΡΠ΅ ΠΈΡΡΠΎΡΠ½ΠΈΠΊ ΠΏΠΈΡΠ°Π½ΠΈΡ ΠΊ Π΄ΡΠ°ΠΉΠ²Π΅ΡΠ°ΠΌ ΠΈ Arduino
- ΠΡΠΎΠ²Π΅ΡΡΡΠ΅ Π²ΡΠ΅ ΡΠΎΠ΅Π΄ΠΈΠ½Π΅Π½ΠΈΡ Π½Π° ΠΎΡΡΡΡΡΡΠ²ΠΈΠ΅ Π·Π°ΠΌΡΠΊΠ°Π½ΠΈΠΉ
- ΠΠ°Π³ΡΡΠ·ΠΈΡΠ΅ ΠΏΡΠΎΡΠΈΠ²ΠΊΡ Π² Arduino (Π½Π°ΠΏΡΠΈΠΌΠ΅Ρ, GRBL)
- ΠΠ°ΡΡΡΠΎΠΉΡΠ΅ ΠΏΠ°ΡΠ°ΠΌΠ΅ΡΡΡ ΠΏΡΠΎΡΠΈΠ²ΠΊΠΈ ΠΏΠΎΠ΄ Π²Π°Ρ ΡΡΠ°Π½ΠΎΠΊ
ΠΠΎΡΠ»Π΅ ΡΠ±ΠΎΡΠΊΠΈ Π½Π΅ΠΎΠ±Ρ ΠΎΠ΄ΠΈΠΌΠΎ ΡΡΠ°ΡΠ΅Π»ΡΠ½ΠΎ ΠΏΡΠΎΠ²Π΅ΡΠΈΡΡ ΡΠ°Π±ΠΎΡΡ ΠΊΠΎΠ½ΡΡΠΎΠ»Π»Π΅ΡΠ° ΠΏΠ΅ΡΠ΅Π΄ ΠΏΠΎΠ΄ΠΊΠ»ΡΡΠ΅Π½ΠΈΠ΅ΠΌ ΠΊ ΡΡΠ°Π½ΠΊΡ.

ΠΠ°ΡΡΡΠΎΠΉΠΊΠ° ΠΏΡΠΎΠ³ΡΠ°ΠΌΠΌΠ½ΠΎΠ³ΠΎ ΠΎΠ±Π΅ΡΠΏΠ΅ΡΠ΅Π½ΠΈΡ Π΄Π»Ρ ΡΠΏΡΠ°Π²Π»Π΅Π½ΠΈΡ ΠΊΠΎΠ½ΡΡΠΎΠ»Π»Π΅ΡΠΎΠΌ
ΠΠ»Ρ ΡΠΏΡΠ°Π²Π»Π΅Π½ΠΈΡ ΡΠ°ΠΌΠΎΠ΄Π΅Π»ΡΠ½ΡΠΌ ΠΊΠΎΠ½ΡΡΠΎΠ»Π»Π΅ΡΠΎΠΌ Π§ΠΠ£ ΠΌΠΎΠΆΠ½ΠΎ ΠΈΡΠΏΠΎΠ»ΡΠ·ΠΎΠ²Π°ΡΡ ΡΠ°Π·Π»ΠΈΡΠ½ΠΎΠ΅ ΠΏΡΠΎΠ³ΡΠ°ΠΌΠΌΠ½ΠΎΠ΅ ΠΎΠ±Π΅ΡΠΏΠ΅ΡΠ΅Π½ΠΈΠ΅:
- Universal G-code Sender — ΠΏΡΠΎΡΡΠ°Ρ Π±Π΅ΡΠΏΠ»Π°ΡΠ½Π°Ρ ΠΏΡΠΎΠ³ΡΠ°ΠΌΠΌΠ° Π΄Π»Ρ ΠΎΡΠΏΡΠ°Π²ΠΊΠΈ G-ΠΊΠΎΠ΄Π°
- bCNC — ΠΏΡΠΎΠ΄Π²ΠΈΠ½ΡΡΠ°Ρ ΠΏΡΠΎΠ³ΡΠ°ΠΌΠΌΠ° Ρ Π²ΠΈΠ·ΡΠ°Π»ΠΈΠ·Π°ΡΠΈΠ΅ΠΉ ΠΎΠ±ΡΠ°Π±ΠΎΡΠΊΠΈ
- Mach3/Mach4 — ΠΏΡΠΎΡΠ΅ΡΡΠΈΠΎΠ½Π°Π»ΡΠ½ΠΎΠ΅ ΠΠ Π΄Π»Ρ ΡΠΏΡΠ°Π²Π»Π΅Π½ΠΈΡ ΡΡΠ°Π½ΠΊΠ°ΠΌΠΈ Ρ Π§ΠΠ£
ΠΡΠ±ΠΎΡ ΠΠ Π·Π°Π²ΠΈΡΠΈΡ ΠΎΡ ΡΠ»ΠΎΠΆΠ½ΠΎΡΡΠΈ ΡΡΠ°Π½ΠΊΠ° ΠΈ ΡΡΠ΅Π±ΠΎΠ²Π°Π½ΠΈΠΉ ΠΊ ΡΡΠ½ΠΊΡΠΈΠΎΠ½Π°Π»ΡΠ½ΠΎΡΡΠΈ. ΠΠ»Ρ Π½Π°ΡΠ°Π»Π° ΡΠ΅ΠΊΠΎΠΌΠ΅Π½Π΄ΡΠ΅ΡΡΡ ΠΈΡΠΏΠΎΠ»ΡΠ·ΠΎΠ²Π°ΡΡ Universal G-code Sender ΠΈΠ·-Π·Π° ΠΏΡΠΎΡΡΠΎΡΡ Π½Π°ΡΡΡΠΎΠΉΠΊΠΈ.
ΠΠΎΠ΄ΠΊΠ»ΡΡΠ΅Π½ΠΈΠ΅ ΠΈ ΡΠ΅ΡΡΠΈΡΠΎΠ²Π°Π½ΠΈΠ΅ ΠΊΠΎΠ½ΡΡΠΎΠ»Π»Π΅ΡΠ° Π§ΠΠ£
ΠΠΎΡΠ»Π΅ ΡΠ±ΠΎΡΠΊΠΈ ΠΈ Π½Π°ΡΡΡΠΎΠΉΠΊΠΈ ΠΠ Π½Π΅ΠΎΠ±Ρ ΠΎΠ΄ΠΈΠΌΠΎ ΠΏΠΎΠ΄ΠΊΠ»ΡΡΠΈΡΡ ΠΊΠΎΠ½ΡΡΠΎΠ»Π»Π΅Ρ ΠΊ ΡΡΠ°Π½ΠΊΡ ΠΈ Π²ΡΠΏΠΎΠ»Π½ΠΈΡΡ ΡΠ΅ΡΡΠΈΡΠΎΠ²Π°Π½ΠΈΠ΅:
- ΠΠΎΠ΄ΠΊΠ»ΡΡΠΈΡΠ΅ Π΄Π²ΠΈΠ³Π°ΡΠ΅Π»ΠΈ ΠΎΡΠ΅ΠΉ ΠΊ ΡΠΎΠΎΡΠ²Π΅ΡΡΡΠ²ΡΡΡΠΈΠΌ ΡΠ°Π·ΡΠ΅ΠΌΠ°ΠΌ ΠΊΠΎΠ½ΡΡΠΎΠ»Π»Π΅ΡΠ°
- ΠΠΎΠ΄ΠΊΠ»ΡΡΠΈΡΠ΅ ΠΊΠΎΠ½ΡΠ΅Π²ΡΠ΅ Π΄Π°ΡΡΠΈΠΊΠΈ (Π΅ΡΠ»ΠΈ ΠΈΡΠΏΠΎΠ»ΡΠ·ΡΡΡΡΡ)
- Π‘ΠΎΠ΅Π΄ΠΈΠ½ΠΈΡΠ΅ ΠΊΠΎΠ½ΡΡΠΎΠ»Π»Π΅Ρ Ρ ΠΊΠΎΠΌΠΏΡΡΡΠ΅ΡΠΎΠΌ ΡΠ΅ΡΠ΅Π· USB
- ΠΠ°ΠΏΡΡΡΠΈΡΠ΅ ΠΏΡΠΎΠ³ΡΠ°ΠΌΠΌΡ ΡΠΏΡΠ°Π²Π»Π΅Π½ΠΈΡ ΠΈ ΡΡΡΠ°Π½ΠΎΠ²ΠΈΡΠ΅ ΡΠΎΠ΅Π΄ΠΈΠ½Π΅Π½ΠΈΠ΅ Ρ ΠΊΠΎΠ½ΡΡΠΎΠ»Π»Π΅ΡΠΎΠΌ
- ΠΡΠΏΠΎΠ»Π½ΠΈΡΠ΅ Π±Π°Π·ΠΎΠ²ΡΠ΅ ΠΊΠΎΠΌΠ°Π½Π΄Ρ ΠΏΠ΅ΡΠ΅ΠΌΠ΅ΡΠ΅Π½ΠΈΡ ΠΎΡΠ΅ΠΉ Π΄Π»Ρ ΠΏΡΠΎΠ²Π΅ΡΠΊΠΈ ΡΠ°Π±ΠΎΡΡ
- ΠΠ°ΡΡΡΠΎΠΉΡΠ΅ ΠΎΠ³ΡΠ°Π½ΠΈΡΠ΅Π½ΠΈΡ ΠΏΠ΅ΡΠ΅ΠΌΠ΅ΡΠ΅Π½ΠΈΠΉ ΠΈ Π΄ΡΡΠ³ΠΈΠ΅ ΠΏΠ°ΡΠ°ΠΌΠ΅ΡΡΡ ΡΡΠ°Π½ΠΊΠ°
ΠΠ½ΠΈΠΌΠ°ΡΠ΅Π»ΡΠ½ΠΎ ΡΠ»Π΅Π΄ΠΈΡΠ΅ Π·Π° ΡΠ°Π±ΠΎΡΠΎΠΉ ΡΡΠ°Π½ΠΊΠ° Π²ΠΎ Π²ΡΠ΅ΠΌΡ ΠΏΠ΅ΡΠ²ΡΡ ΡΠ΅ΡΡΠΎΠ². ΠΡΠΈ ΠΏΠΎΡΠ²Π»Π΅Π½ΠΈΠΈ Π½Π΅ΡΡΠ°ΡΠ½ΡΡ ΡΠΈΡΡΠ°ΡΠΈΠΉ Π½Π΅ΠΌΠ΅Π΄Π»Π΅Π½Π½ΠΎ ΠΎΡΡΠ°Π½ΠΎΠ²ΠΈΡΠ΅ ΡΠ΅ΡΡΠΈΡΠΎΠ²Π°Π½ΠΈΠ΅.
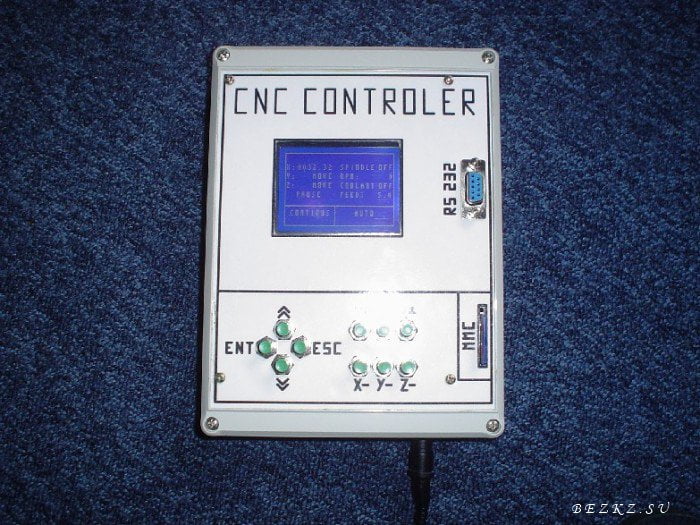
Π’ΠΈΠΏΠΈΡΠ½ΡΠ΅ ΠΏΡΠΎΠ±Π»Π΅ΠΌΡ ΠΏΡΠΈ ΡΠ±ΠΎΡΠΊΠ΅ ΠΊΠΎΠ½ΡΡΠΎΠ»Π»Π΅ΡΠ° Π§ΠΠ£ ΠΈ ΠΈΡ ΡΠ΅ΡΠ΅Π½ΠΈΠ΅
ΠΡΠΈ ΡΠ°ΠΌΠΎΡΡΠΎΡΡΠ΅Π»ΡΠ½ΠΎΠΉ ΡΠ±ΠΎΡΠΊΠ΅ ΠΊΠΎΠ½ΡΡΠΎΠ»Π»Π΅ΡΠ° Π§ΠΠ£ ΠΌΠΎΠ³ΡΡ Π²ΠΎΠ·Π½ΠΈΠΊΠ½ΡΡΡ ΡΠ»Π΅Π΄ΡΡΡΠΈΠ΅ ΠΏΡΠΎΠ±Π»Π΅ΠΌΡ:
- ΠΠ²ΠΈΠ³Π°ΡΠ΅Π»ΠΈ Π½Π΅ Π²ΡΠ°ΡΠ°ΡΡΡΡ ΠΈΠ»ΠΈ Π²ΡΠ°ΡΠ°ΡΡΡΡ ΡΡΠ²ΠΊΠ°ΠΌΠΈ — ΠΏΡΠΎΠ²Π΅ΡΡΡΠ΅ ΠΏΠΎΠ΄ΠΊΠ»ΡΡΠ΅Π½ΠΈΠ΅ ΠΈ Π½Π°ΡΡΡΠΎΠΉΠΊΠΈ Π΄ΡΠ°ΠΉΠ²Π΅ΡΠΎΠ²
- ΠΡΠΈΠ±ΠΊΠΈ ΠΏΠΎΠ·ΠΈΡΠΈΠΎΠ½ΠΈΡΠΎΠ²Π°Π½ΠΈΡ — ΠΎΡΠΊΠ°Π»ΠΈΠ±ΡΡΠΉΡΠ΅ ΡΠ°Π³ΠΈ Π½Π° ΠΌΠΈΠ»Π»ΠΈΠΌΠ΅ΡΡ Π΄Π»Ρ ΠΊΠ°ΠΆΠ΄ΠΎΠΉ ΠΎΡΠΈ
- ΠΠΎΡΠ΅ΡΡ ΡΠ²ΡΠ·ΠΈ Ρ ΠΊΠΎΠΌΠΏΡΡΡΠ΅ΡΠΎΠΌ — ΠΏΡΠΎΠ²Π΅ΡΡΡΠ΅ USB-ΠΊΠ°Π±Π΅Π»Ρ ΠΈ Π½Π°ΡΡΡΠΎΠΉΠΊΠΈ ΠΏΠΎΡΡΠ°
- ΠΠ΅ΡΠ΅Π³ΡΠ΅Π² ΠΊΠΎΠΌΠΏΠΎΠ½Π΅Π½ΡΠΎΠ² — ΠΎΠ±Π΅ΡΠΏΠ΅ΡΡΡΠ΅ Π΄ΠΎΡΡΠ°ΡΠΎΡΠ½ΠΎΠ΅ ΠΎΡ Π»Π°ΠΆΠ΄Π΅Π½ΠΈΠ΅ ΠΊΠΎΠ½ΡΡΠΎΠ»Π»Π΅ΡΠ°
ΠΠΎΠ»ΡΡΠΈΠ½ΡΡΠ²ΠΎ ΠΏΡΠΎΠ±Π»Π΅ΠΌ ΡΠ΅ΡΠ°Π΅ΡΡΡ ΠΏΡΠΎΠ²Π΅ΡΠΊΠΎΠΉ ΡΠΎΠ΅Π΄ΠΈΠ½Π΅Π½ΠΈΠΉ ΠΈ ΠΊΠΎΡΡΠ΅ΠΊΡΠΈΡΠΎΠ²ΠΊΠΎΠΉ Π½Π°ΡΡΡΠΎΠ΅ΠΊ ΠΏΡΠΎΠ³ΡΠ°ΠΌΠΌΠ½ΠΎΠ³ΠΎ ΠΎΠ±Π΅ΡΠΏΠ΅ΡΠ΅Π½ΠΈΡ. ΠΡΠΈ Π²ΠΎΠ·Π½ΠΈΠΊΠ½ΠΎΠ²Π΅Π½ΠΈΠΈ ΡΠ»ΠΎΠΆΠ½ΠΎΡΡΠ΅ΠΉ ΠΎΠ±ΡΠ°ΡΠΈΡΠ΅ΡΡ Π·Π° ΠΏΠΎΠΌΠΎΡΡΡ Π½Π° ΡΠΎΡΡΠΌΡ ΠΏΠΎ Π§ΠΠ£.
ΠΠΎΠΏΠΎΠ»Π½ΠΈΡΠ΅Π»ΡΠ½ΡΠ΅ Π²ΠΎΠ·ΠΌΠΎΠΆΠ½ΠΎΡΡΠΈ ΡΠ°ΠΌΠΎΠ΄Π΅Π»ΡΠ½ΠΎΠ³ΠΎ ΠΊΠΎΠ½ΡΡΠΎΠ»Π»Π΅ΡΠ° Π§ΠΠ£
ΠΠ°Π·ΠΎΠ²ΡΠΉ ΠΊΠΎΠ½ΡΡΠΎΠ»Π»Π΅Ρ Π§ΠΠ£ ΠΌΠΎΠΆΠ½ΠΎ Π΄ΠΎΠΏΠΎΠ»Π½ΠΈΡΡ ΡΠ°Π·Π»ΠΈΡΠ½ΡΠΌΠΈ ΡΡΠ½ΠΊΡΠΈΡΠΌΠΈ:
- ΠΠΎΠ΄ΠΊΠ»ΡΡΠ΅Π½ΠΈΠ΅ ΠΏΡΠ»ΡΡΠ° ΡΠΏΡΠ°Π²Π»Π΅Π½ΠΈΡ Ρ LCD Π΄ΠΈΡΠΏΠ»Π΅Π΅ΠΌ
- ΠΠΎΠ±Π°Π²Π»Π΅Π½ΠΈΠ΅ Π΄Π°ΡΡΠΈΠΊΠ° Π²ΡΡΠΎΡΡ ΠΈΠ½ΡΡΡΡΠΌΠ΅Π½ΡΠ°
- Π£ΠΏΡΠ°Π²Π»Π΅Π½ΠΈΠ΅ ΡΠ°ΡΡΠΎΡΠΎΠΉ Π²ΡΠ°ΡΠ΅Π½ΠΈΡ ΡΠΏΠΈΠ½Π΄Π΅Π»Ρ
- ΠΠΎΠ΄ΠΊΠ»ΡΡΠ΅Π½ΠΈΠ΅ ΡΠΈΡΡΠ΅ΠΌΡ ΠΎΡ Π»Π°ΠΆΠ΄Π΅Π½ΠΈΡ
- ΠΠ½ΡΠ΅Π³ΡΠ°ΡΠΈΡ Ρ ΡΠΈΡΡΠ΅ΠΌΠΎΠΉ ΡΠ΅Ρ Π½ΠΈΡΠ΅ΡΠΊΠΎΠ³ΠΎ Π·ΡΠ΅Π½ΠΈΡ
Π Π°ΡΡΠΈΡΠ΅Π½ΠΈΠ΅ ΡΡΠ½ΠΊΡΠΈΠΎΠ½Π°Π»ΡΠ½ΠΎΡΡΠΈ ΠΏΠΎΠ·Π²ΠΎΠ»ΠΈΡ ΡΠΎΠ·Π΄Π°ΡΡ Π±ΠΎΠ»Π΅Π΅ ΡΠ½ΠΈΠ²Π΅ΡΡΠ°Π»ΡΠ½ΡΠΉ ΠΈ ΡΠ΄ΠΎΠ±Π½ΡΠΉ Π² ΡΠ°Π±ΠΎΡΠ΅ ΡΡΠ°Π½ΠΎΠΊ Ρ Π§ΠΠ£. ΠΠ΄Π½Π°ΠΊΠΎ ΡΡΠ»ΠΎΠΆΠ½Π΅Π½ΠΈΠ΅ ΠΊΠΎΠ½ΡΡΡΡΠΊΡΠΈΠΈ ΠΏΠΎΡΡΠ΅Π±ΡΠ΅Ρ Π±ΠΎΠ»Π΅Π΅ Π³Π»ΡΠ±ΠΎΠΊΠΈΡ Π·Π½Π°Π½ΠΈΠΉ ΡΠ»Π΅ΠΊΡΡΠΎΠ½ΠΈΠΊΠΈ ΠΈ ΠΏΡΠΎΠ³ΡΠ°ΠΌΠΌΠΈΡΠΎΠ²Π°Π½ΠΈΡ.
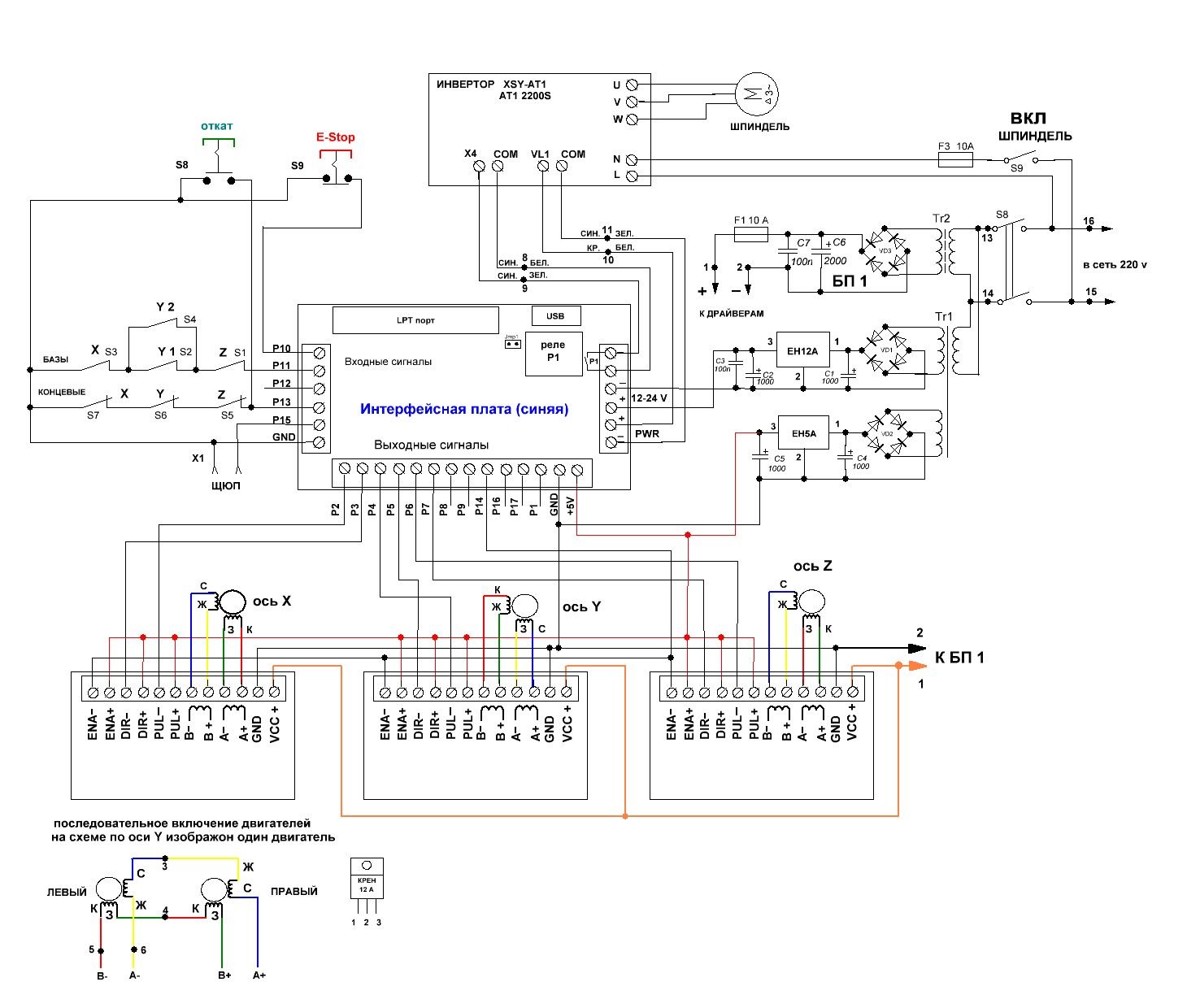
ΡΡ Π΅ΠΌΠ°, ΡΠ±ΠΎΡΠΊΠ° ΡΠ²ΠΎΠΈΠΌΠΈ ΡΡΠΊΠ°ΠΌΠΈ, Π²ΠΈΠ΄Ρ
ΠΠΎΠΏΡΠΎΡ-ΠΡΠ²Π΅ΡΠ£ ΡΠΌΠ΅Π»ΡΡΠ΅Π², ΠΊΠΎΡΠΎΡΡΠ΅ ΠΏΡΡΠ°ΡΡΡΡ ΡΠ°ΠΌΠΈ ΡΠΎΠ±ΡΠ°ΡΡ ΠΏΡΠΎΠ³ΡΠ°ΠΌΠΌΠΈΡΡΠ΅ΠΌΡΠΉ ΡΡΠ°Π½ΠΎΠΊ, ΡΠ°ΡΡΠΎ Π²ΠΎΠ·Π½ΠΈΠΊΠ°Π΅Ρ ΠΏΡΠΎΠ±Π»Π΅ΠΌΠ°: ΠΊΠ°ΠΊ Π²ΡΠ±ΡΠ°ΡΡ Π΄Π»Ρ Π½Π΅Π³ΠΎ ΠΊΠΎΠ½ΡΡΠΎΠ»Π»Π΅Ρ ΡΠΏΡΠ°Π²Π»Π΅Π½ΠΈΡ ΡΠ°Π³ΠΎΠ²ΡΠΌΠΈ Π΄Π²ΠΈΠ³Π°ΡΠ΅Π»ΡΠΌΠΈ. ΠΠΎΠ½ΡΡΠ½ΠΎ, ΡΡΠΎ ΠΈΡ ΠΈΠ½ΡΠ΅ΡΠ΅ΡΡΠ΅Ρ ΡΡ Π΅ΠΌΠ° ΡΡΠΎΠ³ΠΎ ΡΡΡΡΠΎΠΉΡΡΠ²Π°.
Π‘ΡΠ΅Π΄ΠΈ Π±ΠΎΠ»ΡΡΠΎΠ³ΠΎ ΡΠ°Π·Π½ΠΎΠΎΠ±ΡΠ°Π·ΠΈΡ ΠΊΠΎΠ½ΡΡΠΎΠ»Π»Π΅ΡΠΎΠ², ΠΏΠΎΠ»ΡΠ·ΠΎΠ²Π°ΡΠ΅Π»ΠΈ ΠΈΡΡΡ Π΄Π»Ρ ΡΠ°ΠΌΠΎΡΡΠΎΡΡΠ΅Π»ΡΠ½ΠΎΠΉ ΡΠ±ΠΎΡΠΊΠΈ ΡΠ΅ ΡΡ Π΅ΠΌΡ, ΠΊΠΎΡΠΎΡΡΠ΅ Π±ΡΠ΄ΡΡ ΠΏΡΠΈΠ΅ΠΌΠ»Π΅ΠΌΡ ΠΈ Π½Π°ΠΈΠ±ΠΎΠ»Π΅Π΅ ΡΡΡΠ΅ΠΊΡΠΈΠ²Π½Ρ. ΠΡΠΈΠΌΠ΅Π½ΡΡΡΡΡ ΠΈ ΠΎΠ΄Π½ΠΎΠΊΠ°Π½Π°Π»ΡΠ½ΡΠ΅ ΡΡΡΡΠΎΠΉΡΡΠ²Π° ΠΈ ΠΌΠ½ΠΎΠ³ΠΎΠΊΠ°Π½Π°Π»ΡΠ½ΡΠ΅: 3-Ρ ΠΈ 4-Ρ ΠΎΡΠ΅Π²ΠΎΠΉ ΠΊΠΎΠ½ΡΡΠΎΠ»Π»Π΅ΡΡ.
ΠΠ°ΡΠΈΠ°Π½ΡΡ ΡΡΡΡΠΎΠΉΡΡΠ²
ΠΠ½ΠΎΠ³ΠΎΠΊΠ°Π½Π°Π»ΡΠ½ΡΠ΅ ΠΊΠΎΠ½ΡΡΠΎΠ»Π»Π΅ΡΡ Π¨Π (ΡΠ°Π³ΠΎΠ²ΡΡ Π΄Π²ΠΈΠ³Π°ΡΠ΅Π»Π΅ΠΉ) ΠΏΡΠΈ ΡΠΈΠΏΠΎΡΠ°Π·ΠΌΠ΅ΡΠ°Ρ 42 ΠΈΠ»ΠΈ 57 ΠΌΠΌ ΠΈΡΠΏΠΎΠ»ΡΠ·ΡΠ΅ΡΡΡ Π² ΡΠ»ΡΡΠ°Π΅ Π½Π΅Π±ΠΎΠ»ΡΡΠΎΠ³ΠΎ ΡΠ°Π±ΠΎΡΠ΅Π³ΠΎ ΠΏΠΎΠ»Ρ ΡΡΠ°Π½ΠΊΠ° β Π΄ΠΎ 1 ΠΌ. ΠΠΎΠ³Π΄Π° ΡΠΎΠ±ΠΈΡΠ°ΡΡ ΡΡΠ°Π½ΠΎΠΊ Π±ΠΎΠ»ΡΡΠ΅Π³ΠΎ ΡΠ°Π±ΠΎΡΠ΅Π³ΠΎ ΠΏΠΎΠ»Ρ β ΡΠ²ΡΡΠ΅ 1ΠΌ, Π½ΡΠΆΠ΅Π½ ΡΠΈΠΏΠΎΡΠ°Π·ΠΌΠ΅Ρ 86 ΠΌΠΌ. Π£ΠΏΡΠ°Π²Π»ΡΡΡ Π½ΠΈΠΌ ΠΌΠΎΠΆΠ½ΠΎ, ΠΏΠΎΠ»ΡΠ·ΡΡΡΡ ΠΎΠ΄Π½ΠΎΠΊΠ°Π½Π°Π»ΡΠ½ΡΠΌ Π΄ΡΠ°ΠΉΠ²Π΅ΡΠΎΠΌ (ΡΠΎΠΊ ΡΠΏΡΠ°Π²Π»Π΅Π½ΠΈΡ, ΠΏΡΠ΅Π²ΡΡΠ°ΡΡΠΈΠΉ 4,2 Π).
Π£ΠΏΡΠ°Π²Π»ΡΡΡ ΡΡΠ°Π½ΠΊΠΎΠΌ Ρ ΡΠΈΡΠ»ΠΎΠ²ΡΠΌ ΠΏΡΠΎΠ³ΡΠ°ΠΌΠΌΠ½ΡΠΌ ΡΠΏΡΠ°Π²Π»Π΅Π½ΠΈΠ΅ΠΌ, Π² ΡΠ°ΡΡΠ½ΠΎΡΡΠΈ, ΡΡΠ΅Π·Π΅ΡΠ½ΡΠΌ Π½Π°ΡΡΠΎΠ»ΡΠ½ΡΠΌ ΠΌΠΎΠΆΠ½ΠΎ ΠΊΠΎΠ½ΡΡΠΎΠ»Π»Π΅ΡΠΎΠΌ, ΡΠΎΠ·Π΄Π°Π½Π½ΡΠΌ Π½Π° Π±Π°Π·Π΅ ΡΠΏΠ΅ΡΠΈΠ°Π»ΠΈΠ·ΠΈΡΠΎΠ²Π°Π½Π½ΡΡ ΠΌΠΈΠΊΡΠΎΡΡ Π΅ΠΌ βΠ΄ΡΠ°ΠΉΠ²Π΅ΡΠΎΠ², ΠΏΡΠ΅Π΄Π½Π°Π·Π½Π°ΡΠ΅Π½Π½ΡΡ ΠΊ ΠΏΡΠΈΠΌΠ΅Π½Π΅Π½ΠΈΡ Π΄Π»Ρ Π¨Π Π΄ΠΎ 3Π. ΠΠΎΠ½ΡΡΠΎΠ»Π»Π΅Ρ Π§ΠΠ£ ΡΡΠ°Π½ΠΊΠ° ΡΠΏΡΠ°Π²Π»ΡΠ΅ΡΡΡ ΡΠΏΠ΅ΡΠΏΡΠΎΠ³ΡΠ°ΠΌΠΌΠΎΠΉ. ΠΠ΅ ΡΡΡΠ°Π½Π°Π²Π»ΠΈΠ²Π°ΡΡ Π½Π° ΠΠ, ΠΈΠΌΠ΅ΡΡΠΈΠΉ ΡΠ°ΡΡΠΎΡΡ ΠΏΡΠΎΡΠ΅ΡΡΠΎΡΠ° ΡΠ²ΡΡΠ΅ 1GHz, Π° ΠΎΠ±ΡΠ΅ΠΌ ΠΏΠ°ΠΌΡΡΠΈ 1 ΠΠ±). ΠΡΠΈ ΠΌΠ΅Π½ΡΡΠ΅ΠΌ ΠΎΠ±ΡΠ΅ΠΌΠ΅, ΡΠΈΡΡΠ΅ΠΌΡ ΠΎΠΏΡΠΈΠΌΠΈΠ·ΠΈΡΡΡΡ.
ΠΠΠ ΠΠ’ΠΠ’Π ΠΠΠΠΠΠΠΠ! ΠΡΠ»ΠΈ ΡΡΠ°Π²Π½ΠΈΠ²Π°ΡΡ Ρ Π½ΠΎΡΡΠ±ΡΠΊΠΎΠΌ, ΡΠΎ Π² ΡΠ»ΡΡΠ°Π΅ ΠΏΠΎΠ΄ΠΊΠ»ΡΡΠ΅Π½ΠΈΡ ΡΡΠ°ΡΠΈΠΎΠ½Π°ΡΠ½ΠΎΠ³ΠΎ ΠΊΠΎΠΌΠΏΡΡΡΠ΅ΡΠ° β Π»ΡΡΡΠΈΠ΅ ΡΠ΅Π·ΡΠ»ΡΡΠ°ΡΡ, Π΄Π° ΠΈ ΠΎΠ±Ρ ΠΎΠ΄ΠΈΡΡΡ ΠΎΠ½ Π΄Π΅ΡΠ΅Π²Π»Π΅.
ΠΠΎΠ΄ΠΊΠ»ΡΡΠ°Ρ ΠΊΠΎΠ½ΡΡΠΎΠ»Π»Π΅Ρ ΠΊ ΠΊΠΎΠΌΠΏΡΡΡΠ΅ΡΡ, ΠΈΡΠΏΠΎΠ»ΡΠ·ΡΡΡ USB ΠΈΠ»ΠΈ ΡΠ°Π·ΡΠ΅ΠΌ ΠΏΠ°ΡΠ°Π»Π»Π΅Π»ΡΠ½ΠΎΠ³ΠΎ ΠΏΠΎΡΡΠ° LPT. ΠΡΠ»ΠΈ ΡΡΠΈΡ ΠΏΠΎΡΡΠΎΠ² Π½Π΅Ρ, ΡΠΎ ΠΏΠΎΠ»ΡΠ·ΡΡΡΡΡ ΠΏΠ»Π°ΡΠ°ΠΌΠΈ-ΡΠ°ΡΡΠΈΡΠΈΡΠ΅Π»ΡΠΌΠΈ ΠΈΠ»ΠΈ ΠΊΠΎΠ½ΡΡΠΎΠ»Π»Π΅ΡΠ°ΠΌΠΈ-ΠΏΡΠ΅ΠΎΠ±ΡΠ°Π·ΠΎΠ²Π°ΡΠ΅Π»ΡΠΌΠΈ.
ΠΠΊΡΠΊΡΡΡ Π² ΠΈΡΡΠΎΡΠΈΡ
ΠΠ΅Ρ ΠΈ ΡΠ΅Ρ ΠΏΡΠΎΠ³ΡΠ΅ΡΡΠ° ΡΡ Π΅ΠΌΠ°ΡΠΈΡΠ΅ΡΠΊΠΈ ΠΌΠΎΠΆΠ½ΠΎ ΠΎΠ±ΠΎΠ·Π½Π°ΡΠΈΡΡ ΡΠ°ΠΊ:
- Π£ ΠΏΠ΅ΡΠ²ΠΎΠ³ΠΎ ΠΊΠΎΠ½ΡΡΠΎΠ»Π»Π΅ΡΠ° Π½Π° ΠΌΠΈΠΊΡΠΎΡΡ Π΅ΠΌΠ΅ Π±ΡΠ» ΡΡΠ»ΠΎΠ²Π½ΠΎ Π½Π°Π·Π²Π°Π½ Β«ΡΠΈΠ½Π΅ΠΉ ΠΏΠ»Π°ΡΠΎΠΉΒ». Π£ ΡΡΠΎΠ³ΠΎ Π²Π°ΡΠΈΠ°Π½ΡΠ° Π΅ΡΡΡ Π½Π΅Π΄ΠΎΡΡΠ°ΡΠΊΠΈ ΠΈ ΡΡ Π΅ΠΌΠ° ΡΡΠ΅Π±ΠΎΠ²Π°Π»Π° Π΄ΠΎΡΠ°Π±ΠΎΡΠΊΠΈ. ΠΠ»Π°Π²Π½ΠΎΠ΅ Π΄ΠΎΡΡΠΎΠΈΠ½ΡΡΠ²ΠΎ β Π΅ΡΡΡ ΡΠ°Π·ΡΠ΅ΠΌ, ΠΊ Π½Π΅ΠΌΡ ΠΈ ΠΏΠΎΠ΄ΠΊΠ»ΡΡΠ°Π»ΠΈ ΠΏΡΠ»ΡΡ ΡΠΏΡΠ°Π²Π»Π΅Π½ΠΈΡ.
- ΠΡΠ»Π΅Π΄ Π·Π° ΡΠΈΠ½ΠΈΠΌ, ΠΏΠΎΡΠ²ΠΈΠ»ΡΡ ΠΊΠΎΠ½ΡΡΠΎΠ»Π»Π΅Ρ, Π½Π°Π·ΡΠ²Π°Π΅ΠΌΡΠΉ Β«ΠΊΡΠ°ΡΠ½ΠΎΠΉ ΠΏΠ»Π°ΡΠΎΠΉΒ». Π Π½ΡΠΌ ΡΠΆΠ΅ ΠΈΡΠΏΠΎΠ»ΡΠ·ΠΎΠ²Π°Π»ΠΈΡΡ Π±ΡΡΡΡΡΠ΅ (Π²ΡΡΠΎΠΊΠΎΡΠ°ΡΡΠΎΡΠ½ΡΠ΅) ΠΎΠΏΡΡΠΎΠ½Ρ, ΡΠ΅Π»Π΅ ΡΠΏΠΈΠ½Π΄Π΅Π»Ρ Π½Π° 10Π, ΡΠ°Π·Π²ΡΠ·ΠΊΠ° ΠΏΠΎ ΠΏΠΈΡΠ°Π½ΠΈΡ (Π³Π°Π»ΡΠ²Π°Π½ΠΈΡΠ΅ΡΠΊΠ°Ρ) ΠΈ ΡΠ°Π·ΡΠ΅ΠΌ, ΠΊΡΠ΄Π° Π±Ρ ΠΏΠΎΠ΄ΠΊΠ»ΡΡΠ°Π»ΠΈΡΡ Π΄ΡΠ°ΠΉΠ²Π΅ΡΡ ΡΠ΅ΡΠ²Π΅ΡΡΠΎΠΉ ΠΎΡΠΈ.
- ΠΡΠΈΠΌΠ΅Π½ΡΠ»ΠΎΡΡ ΡΠ°ΠΊΠΆΠ΅ Π΅ΡΠ΅ ΠΎΠ΄Π½ΠΎ ΠΏΠΎΠ΄ΠΎΠ±Π½ΠΎΠ΅ ΡΡΡΡΠΎΠΉΡΡΠ²ΠΎ Ρ ΠΊΡΠ°ΡΠ½ΠΎΠΉ ΠΌΠ°ΡΠΊΠΈΡΠΎΠ²ΠΊΠΎΠΉ, Π½ΠΎ Π±ΠΎΠ»Π΅Π΅ ΡΠΏΡΠΎΡΠ΅Π½Π½ΠΎΠ΅. ΠΡΠΈ Π΅Π³ΠΎ ΠΏΠΎΠΌΠΎΡΠΈ ΠΌΠΎΠΆΠ½ΠΎ Π±ΡΠ»ΠΎ ΡΠΏΡΠ°Π²Π»ΡΡΡ Π½Π΅Π±ΠΎΠ»ΡΡΠΈΠΌ ΡΡΠ°Π½ΠΊΠΎΠΌ Π½Π°ΡΡΠΎΠ»ΡΠ½ΠΎΠ³ΠΎ ΡΠΈΠΏΠ° β ΠΈΠ· ΡΠΈΡΠ»Π° 3-ΠΎΡΠ΅Π²ΡΡ .
- Π‘Π»Π΅Π΄ΡΡΡΠΈΠΌ Π² Π»ΠΈΠ½Π΅ΠΉΠΊΠ΅ ΡΠ΅Ρ ΠΏΡΠΎΠ³ΡΠ΅ΡΡΠ° ΡΡΠ°Π» ΠΊΠΎΠ½ΡΡΠΎΠ»Π»Π΅Ρ Ρ Π³Π°Π»ΡΠ²Π°Π½ΠΈΡΠ΅ΡΠΊΠΎΠΉ ΡΠ°Π·Π²ΡΠ·ΠΊΠΎΠΉ ΠΏΠΎ ΠΏΠΈΡΠ°Π½ΠΈΡ, Π±ΡΡΡΡΡΠΌΠΈ ΠΎΠΏΡΡΠΎΠ½Π°ΠΌΠΈ ΠΈ ΠΎΡΠΎΠ±ΡΠΌΠΈ ΠΊΠΎΠ½Π΄Π΅Π½ΡΠ°ΡΠΎΡΠ°ΠΌΠΈ, ΠΈΠΌΠ΅ΡΡΠΈΠΉ Π°Π»ΡΠΌΠΈΠ½ΠΈΠ΅Π²ΡΠΉ ΠΊΠΎΡΠΏΡΡ, ΠΊΠΎΡΠΎΡΡΠΉ ΠΎΠ±Π΅ΡΠΏΠ΅ΡΠΈΠ²Π°Π» Π·Π°ΡΠΈΡΡ ΠΎΡ ΠΏΡΠ»ΠΈ. ΠΠΌΠ΅ΡΡΠΎ ΡΠ΅Π»Π΅ ΡΠΏΡΠ°Π²Π»Π΅Π½ΠΈΡ, ΠΊΠΎΡΠΎΡΠΎΠ΅ Π²ΠΊΠ»ΡΡΠ°Π»ΠΎ Π±Ρ ΡΠΏΠΈΠ½Π΄Π΅Π»Ρ, Π² ΠΊΠΎΠ½ΡΡΡΡΠΊΡΠΈΠΈ Π±ΡΠ»ΠΎ Π΄Π²Π° Π²ΡΡ ΠΎΠ΄Π° ΠΈ Π²ΠΎΠ·ΠΌΠΎΠΆΠ½ΠΎΡΡΡ, ΡΡΠΎΠ±Ρ ΠΏΠΎΠ΄ΠΊΠ»ΡΡΠΈΡΡ ΡΠ΅Π»Π΅ ΠΈΠ»ΠΈ Π¨ΠΠ (ΡΠΈΡΠΎΡΠ½ΠΎ-ΠΈΠΌΠΏΡΠ»ΡΡΠ½Π°Ρ ΠΌΠΎΠ΄ΡΠ»ΡΡΠΈΡ) ΡΠΏΡΠ°Π²Π»Π΅Π½ΠΈΠ΅ ΡΠΊΠΎΡΠΎΡΡΡΡ Π²ΡΠ°ΡΠ΅Π½ΠΈΡ.
- Π‘Π΅ΠΉΡΠ°Ρ ΠΆΠ΅ Π΄Π»Ρ ΠΈΠ·Π³ΠΎΡΠΎΠ²Π»Π΅Π½ΠΈΡ ΡΠ°ΠΌΠΎΠ΄Π΅Π»ΡΠ½ΠΎΠ³ΠΎ ΡΡΠ΅Π·Π΅ΡΠ½ΠΎ-Π³ΡΠ°Π²ΠΈΡΠΎΠ²Π°Π»ΡΠ½ΠΎΠ³ΠΎ ΡΡΠ°Π½ΠΊΠ°, ΠΈΠΌΠ΅ΡΡΠ΅Π³ΠΎ Π¨Π, Π΅ΡΡΡ Π²Π°ΡΠΈΠ°Π½ΡΡ β 4-Ρ ΠΎΡΠ΅Π²ΠΎΠΉ ΠΊΠΎΠ½ΡΡΠΎΠ»Π»Π΅Ρ, Π΄ΡΠ°ΠΉΠ²Π΅Ρ Π¨Π ΠΎΡ Allegro, ΠΎΠ΄Π½ΠΎΠΊΠ°Π½Π°Π»ΡΠ½ΡΠΉ Π΄ΡΠ°ΠΉΠ²Π΅Ρ Π΄Π»Ρ ΡΡΠ°Π½ΠΊΠ°, ΠΈΠΌΠ΅ΡΡΠ΅Π³ΠΎ Π±ΠΎΠ»ΡΡΠΎΠ΅ ΡΠ°Π±ΠΎΡΠ΅Π΅ ΠΏΠΎΠ»Π΅.
ΠΠΠΠΠ! ΠΠ΅ ΡΡΠΎΠΈΡ ΠΏΠ΅ΡΠ΅Π³ΡΡΠΆΠ°ΡΡ Π¨Π, ΠΏΡΠΈΠΌΠ΅Π½ΡΡ ΠΊΡΡΠΏΠ½ΡΡ ΡΡΠ΅Π·Ρ Π°Π³ΡΠ΅Π³Π°ΡΠ° ΠΈ Π±ΠΎΠ»ΡΡΡΡ ΡΠΊΠΎΡΠΎΡΡΡ.
ΠΠΎΠ½ΡΡΠΎΠ»Π»Π΅Ρ ΠΈΠ· ΠΏΠΎΠ΄ΡΡΡΠ½ΡΡ ΠΌΠ°ΡΠ΅ΡΠΈΠ°Π»ΠΎΠ²
ΠΠΎΠ»ΡΡΠΈΠ½ΡΡΠ²ΠΎ ΡΠΌΠ΅Π»ΡΡΠ΅Π² ΠΏΡΠ΅Π΄ΠΏΠΎΡΠΈΡΠ°ΡΡ ΡΠΏΡΠ°Π²Π»Π΅Π½ΠΈΠ΅ ΡΠ΅ΡΠ΅Π· LPT ΠΏΠΎΡΡ Π΄Π»Ρ Π±ΠΎΠ»ΡΡΠΈΠ½ΡΡΠ²Π° ΠΏΡΠΎΠ³ΡΠ°ΠΌΠΌ ΡΠΏΡΠ°Π²Π»Π΅Π½ΠΈΡ Π»ΡΠ±ΠΈΡΠ΅Π»ΡΡΠΊΠΎΠ³ΠΎ ΡΡΠΎΠ²Π½Ρ. ΠΠΌΠ΅ΡΡΠΎ ΠΏΡΠΈΠΌΠ΅Π½Π΅Π½ΠΈΡ ΠΊΠΎΠΌΠΏΠ»Π΅ΠΊΡΠ° ΡΠΏΠ΅ΡΠΌΠΈΠΊΡΠΎΡΡ Π΅ΠΌ Π΄Π»Ρ ΡΡΠΎΠΉ ΡΠ΅Π»ΠΈ, ΠΊΠΎΠ΅-ΠΊΡΠΎ ΡΡΡΠΎΠΈΡ ΠΊΠΎΠ½ΡΡΠΎΠ»Π»Π΅Ρ ΠΈΠ· ΠΏΠΎΠ΄ΡΡΡΠ½ΡΡ ΠΌΠ°ΡΠ΅ΡΠΈΠ°Π»ΠΎΠ² βΒ ΠΏΠΎΠ»Π΅Π²ΡΡ ΡΡΠ°Π½Π·ΠΈΡΡΠΎΡΠΎΠ² ΠΈΠ· ΡΠ³ΠΎΡΠ΅Π²ΡΠΈΡ ΠΌΠ°ΡΠ΅ΡΠΈΠ½ΡΠΊΠΈΡ ΠΏΠ»Π°Ρ (ΠΏΡΠΈ Π½Π°ΠΏΡΡΠΆΠ΅Π½ΠΈΠΈ ΡΠ²ΡΡΠ΅ 30 Π²ΠΎΠ»ΡΡ ΠΈ ΡΠΎΠΊΠΎΠΌ Π±ΠΎΠ»ΡΡΠ΅ 2 Π°ΠΌΠΏΠ΅Ρ).
Π ΠΏΠΎΡΠΊΠΎΠ»ΡΠΊΡ ΡΠΎΠ·Π΄Π°Π²Π°Π»ΡΡ ΡΡΠ°Π½ΠΎΠΊ Π΄Π»Ρ Π½Π°ΡΠ΅Π·Π°Π½ΠΈΡ ΠΏΠ΅Π½ΠΎΠΏΠ»Π°ΡΡΠ°, Π² ΠΊΠ°ΡΠ΅ΡΡΠ²Π΅ ΠΎΠ³ΡΠ°Π½ΠΈΡΠΈΡΠ΅Π»Ρ ΡΠΎΠΊΠ° ΠΈΠ·ΠΎΠ±ΡΠ΅ΡΠ°ΡΠ΅Π»Ρ ΠΈΡΠΏΠΎΠ»ΡΠ·ΠΎΠ²Π°Π» Π°Π²ΡΠΎΠΌΠΎΠ±ΠΈΠ»ΡΠ½ΡΠ΅ Π»Π°ΠΌΠΏΡ Π½Π°ΠΊΠ°Π»ΠΈΠ²Π°Π½ΠΈΡ, Π° Π¨Π ΡΠ½ΠΈΠΌΠ°Π»ΠΈ ΡΠΎ ΡΡΠ°ΡΡΡ ΠΏΡΠΈΠ½ΡΠ΅ΡΠΎΠ² ΠΈΠ»ΠΈ ΡΠΊΠ°Π½Π΅ΡΠΎΠ². Π’Π°ΠΊΠΎΠΉ ΠΊΠΎΠ½ΡΡΠΎΠ»Π»Π΅Ρ ΡΡΡΠ°Π½Π°Π²Π»ΠΈΠ²Π°Π»ΠΈ Π±Π΅Π· ΠΈΠ·ΠΌΠ΅Π½Π΅Π½ΠΈΠΉ Π² ΡΡ Π΅ΠΌΠ΅.
Π§ΡΠΎΠ±Ρ ΡΠ΄Π΅Π»Π°ΡΡ ΠΏΡΠΎΡΡΠ΅ΠΉΡΠΈΠΉ ΡΡΠ°Π½ΠΎΠΊ Π§ΠΠ£ ΡΠ²ΠΎΠΈΠΌΠΈ ΡΡΠΊΠ°ΠΌΠΈ, ΡΠ°Π·Π±ΠΈΡΠ°Ρ ΡΠΊΠ°Π½Π΅Ρ, ΠΏΠΎΠΌΠΈΠΌΠΎ Π¨Π, ΠΈΠ·Π²Π»Π΅ΠΊΠ°Π΅ΡΡΡ ΠΈ ΠΌΠΈΠΊΡΠΎΡΡ Π΅ΠΌΠ° ULN2003, ΠΈ Π΄Π²Π° ΡΡΠ°Π»ΡΠ½ΡΠ΅ ΠΏΡΡΡΠΊΠΈ, ΠΎΠ½ΠΈ ΠΏΠΎΠΉΠ΄ΡΡ Π½Π° ΡΠ΅ΡΡΠΎΠ²ΡΠΉ ΠΏΠΎΡΡΠ°Π». Π ΡΠΎΠΌΡ ΠΆΠ΅ ΠΏΠΎΠ½Π°Π΄ΠΎΠ±ΡΡΡΡ:
- ΠΠΎΡΠΎΠ±ΠΊΠ° ΠΈΠ· ΠΊΠ°ΡΡΠΎΠ½Π° (ΠΈΠ· Π½Π΅Π΅ ΡΠΌΠΎΠ½ΡΠΈΡΡΡΡ ΠΊΠΎΡΠΏΡΡ ΡΡΡΡΠΎΠΉΡΡΠ²Π°). ΠΠΎΠ·ΠΌΠΎΠΆΠ΅Π½ Π²Π°ΡΠΈΠ°Π½Ρ Ρ ΡΠ΅ΠΊΡΡΠΎΠ»ΠΈΡΠΎΠΌ ΠΈΠ»ΠΈ ΡΠ°Π½Π΅ΡΠ½ΡΠΌ Π»ΠΈΡΡΠΎΠΌ, Π½ΠΎ ΠΊΠ°ΡΡΠΎΠ½ ΡΠ΅Π·Π°ΡΡ Π»Π΅Π³ΡΠ΅; ΠΊΡΡΠΊΠΈ Π΄ΡΠ΅Π²Π΅ΡΠΈΠ½Ρ;
- ΠΈΠ½ΡΡΡΡΠΌΠ΅Π½ΡΡ β Π² Π²ΠΈΠ΄Π΅ ΠΊΡΡΠ°ΡΠ΅ΠΊ, Π½ΠΎΠΆΠ½ΠΈΡ, ΠΎΡΠ²Π΅ΡΡΠΎΠΊ; ΠΊΠ»Π΅Π΅Π²ΠΎΠΉ ΠΏΠΈΡΡΠΎΠ»Π΅Ρ ΠΈ ΠΏΠ°ΡΠ»ΡΠ½ΡΠ΅ ΠΏΡΠΈΠ½Π°Π΄Π»Π΅ΠΆΠ½ΠΎΡΡΠΈ;
- Π²Π°ΡΠΈΠ°Π½Ρ ΠΏΠ»Π°ΡΡ, ΠΊΠΎΡΠΎΡΠ°Ρ ΠΏΠΎΠ΄Ρ ΠΎΠ΄ΠΈΡ Π½Π° ΡΠ°ΠΌΠΎΠ΄Π΅Π»ΡΠ½ΡΠΉ Π§ΠΠ£ ΡΡΠ°Π½ΠΎΠΊ;
- ΡΠ°Π·ΡΠ΅ΠΌ Π΄Π»Ρ LPT ΠΏΠΎΡΡΠ°;
- Π³Π½Π΅Π·Π΄ΠΎ Π² ΡΠΎΡΠΌΠ΅ ΡΠΈΠ»ΠΈΠ½Π΄ΡΠ° Π΄Π»Ρ ΠΎΠ±ΡΡΡΡΠΎΠΉΡΡΠ²Π° Π±Π»ΠΎΠΊΠ° ΠΏΠΈΡΠ°Π½ΠΈΡ;
- ΡΠ»Π΅ΠΌΠ΅Π½ΡΡ ΡΠΎΠ΅Π΄ΠΈΠ½Π΅Π½ΠΈΡ β ΡΡΠ΅ΡΠΆΠ½ΠΈ Ρ ΡΠ΅Π·ΡΠ±ΠΎΠΉ, Π³Π°ΠΉΠΊΠΈ, ΡΠ°ΠΉΠ±Ρ ΠΈ ΡΡΡΡΠΏΡ;
- ΠΏΡΠΎΠ³ΡΠ°ΠΌΠΌΠ° Π΄Π»Ρ TurboCNC.
Π‘Π±ΠΎΡΠΊΠ° ΡΠ°ΠΌΠΎΠ΄Π΅Π»ΡΠ½ΠΎΠ³ΠΎ ΡΡΡΡΠΎΠΉΡΡΠ²Π°
ΠΡΠΈΡΡΡΠΏΠΈΠ² ΠΊ ΡΠ°Π±ΠΎΡΠ΅ Π½Π°Π΄ ΡΠ°ΠΌΠΎΠ΄Π΅Π»ΡΠ½ΡΠΌ ΠΊΠΎΠ½ΡΡΠΎΠ»Π»Π΅ΡΠΎΠΌ Π΄Π»Ρ ΡΠΏΡ, ΠΏΠ΅ΡΠ²ΡΠΉ ΡΠ°Π³ β Π°ΠΊΠΊΡΡΠ°ΡΠ½ΠΎ ΠΏΡΠΈΠΏΠ°ΡΡΡ ΠΌΠΈΠΊΡΠΎΡΡ Π΅ΠΌΡ Π½Π° ΠΌΠ°ΠΊΠ΅ΡΠ½ΡΡ ΠΏΠ»Π°ΡΡ Ρ Π΄Π²ΡΠΌΡ ΡΠΈΠ½Π°ΠΌΠΈ ΡΠ»Π΅ΠΊΡΡΠΎΠΏΠΈΡΠ°Π½ΠΈΡ. ΠΠ°Π»ΡΡΠ΅ ΠΏΠΎΡΠ»Π΅Π΄ΡΠ΅Ρ ΡΠΎΠ΅Π΄ΠΈΠ½Π΅Π½ΠΈΠ΅ Π²ΡΠ²ΠΎΠ΄Π° ULN2003 ΠΈ ΠΊΠΎΠ½Π½Π΅ΠΊΡΠΎΡΠ° LPT. ΠΠ°Π»Π΅Π΅ ΠΎΡΡΠ°Π²ΡΠΈΠ΅ΡΡ Π²ΡΠ²ΠΎΠ΄Ρ ΠΏΠΎΠ΄ΠΊΠ»ΡΡΠ°Π΅ΠΌ ΠΏΠΎ ΡΡ Π΅ΠΌΠ΅. ΠΡΠ»Π΅Π²ΠΎΠΉ Π²ΡΠ²ΠΎΠ΄ (25-ΡΠΉ ΠΏΠ°ΡΠ°Π»Π»Π΅Π»ΡΠ½ΠΎΠ³ΠΎ ΠΏΠΎΡΡΠ°) ΡΠΎΠ΅Π΄ΠΈΠ½ΡΠ΅ΡΡΡ Ρ ΠΎΡΡΠΈΡΠ°ΡΠ΅Π»ΡΠ½ΡΠΌ Π½Π° ΡΠΈΠ½Π΅ ΠΏΠΈΡΠ°Π½ΠΈΡ ΠΏΠ»Π°ΡΡ.
ΠΠ°ΡΠ΅ΠΌ Π¨Π ΡΠΎΠ΅Π΄ΠΈΠ½ΡΡΡ Ρ ΡΡΡΡΠΎΠΉΡΡΠ²ΠΎΠΌ ΡΠΏΡΠ°Π²Π»Π΅Π½ΠΈΡ, Π° Π³Π½Π΅Π·Π΄ΠΎ Π΄Π»Ρ ΡΠ»Π΅ΠΊΡΡΠΎΠΏΠΈΡΠ°Π½ΠΈΡ β Ρ ΡΠΎΠΎΡΠ²Π΅ΡΡΡΠ²ΡΡΡΠ΅ΠΉ ΡΠΈΠ½ΠΎΠΉ. ΠΠ»Ρ Π½Π°Π΄ΡΠΆΠ½ΠΎΡΡΠΈ ΡΠΎΠ΅Π΄ΠΈΠ½Π΅Π½ΠΈΠΉ ΠΏΡΠΎΠ²ΠΎΠ΄ΠΎΠ² Π²ΡΠΏΠΎΠ»Π½ΡΡΡ ΠΈΡ ΡΠΈΠΊΡΠ°ΡΠΈΡ ΡΠ΅ΡΠΌΠΎΠΊΠ»Π΅Π΅ΠΌ.
ΠΠ΅ ΡΠΎΡΡΠ°Π²ΠΈΡ ΡΡΡΠ΄Π° ΠΏΠΎΠ΄ΠΊΠ»ΡΡΠ΅Π½ΠΈΠ΅ Turbo CNC. ΠΡΠΎΠ³ΡΠ°ΠΌΠΌΠ° ΡΡΡΠ΅ΠΊΡΠΈΠ²Π½Π° Ρ MS-DOS, ΡΠΎΠ²ΠΌΠ΅ΡΡΠΈΠΌΠ° ΠΈ ΡΒ Windows, Π½ΠΎ Π² ΡΡΠΎΠΌ ΡΠ»ΡΡΠ°Π΅ Π²ΠΎΠ·ΠΌΠΎΠΆΠ½Ρ Π½Π΅ΠΊΠΎΡΠΎΡΡΠ΅ ΠΎΡΠΈΠ±ΠΊΠΈ ΠΈ ΡΠ±ΠΎΠΈ.
ΠΠ°ΡΡΡΠΎΠΈΠ² ΠΏΡΠΎΠ³ΡΠ°ΠΌΠΌΡ Π½Π° ΡΠ°Π±ΠΎΡΡ Ρ ΠΊΠΎΠ½ΡΡΠΎΠ»Π»Π΅ΡΠΎΠΌ, ΠΌΠΎΠΆΠ½ΠΎ ΠΈΠ·Π³ΠΎΡΠΎΠ²ΠΈΡΡ ΡΠ΅ΡΡΠΎΠ²ΡΡ ΠΎΡΡ. ΠΠΎΡΠ»Π΅Π΄ΠΎΠ²Π°ΡΠ΅Π»ΡΠ½ΠΎΡΡΡ Π΄Π΅ΠΉΡΡΠ²ΠΈΠΉ ΠΏΠΎ ΠΏΠΎΠ΄ΠΊΠ»ΡΡΠ΅Π½ΠΈΡ ΡΡΠ°Π½ΠΊΠΎΠ² ΡΠ°ΠΊΠΎΠ²Π°:
- Π ΠΎΡΠ²Π΅ΡΡΡΠΈΡ, ΠΏΡΠΎΡΠ²Π΅ΡΠ»Π΅Π½Π½ΡΠ΅ Π½Π° ΠΎΠ΄Π½ΠΎΠΌ ΡΡΠΎΠ²Π½Π΅ Π² ΡΡΠ΅Ρ Π΄Π΅ΡΠ΅Π²ΡΠ½Π½ΡΡ Π±ΡΡΡΠΊΠ°Ρ , Π²ΡΡΠ°Π²Π»ΡΡΡ ΠΏΡΡΡΠΊΠΈ ΠΈΠ· ΡΡΠ°Π»ΠΈ ΠΈ Π·Π°ΠΊΡΠ΅ΠΏΠ»ΡΡΡ ΡΡΡΡΠΏΠ°ΠΌΠΈ Π½Π΅Π±ΠΎΠ»ΡΡΠΎΠ³ΠΎ ΡΠ°Π·ΠΌΠ΅ΡΠ°.
- Π¨Π ΡΠΎΠ΅Π΄ΠΈΠ½ΡΡΡ ΡΠΎ Π²ΡΠΎΡΡΠΌ Π±ΡΡΡΠΊΠΎΠΌ, Π½Π°Π΄Π΅Π²Π°Ρ Π΅Π³ΠΎ Π½Π° ΡΠ²ΠΎΠ±ΠΎΠ΄Π½ΡΠ΅ ΠΊΠΎΠ½ΡΡ ΠΏΡΡΡΠΎΠ² ΠΈ ΠΏΡΠΈΠΊΡΡΡΠΈΠ²Π°ΡΡ, ΠΏΡΠΈΠΌΠ΅Π½ΡΡ ΡΡΡΡΠΏΡ.
- Π§Π΅ΡΠ΅Π· ΡΡΠ΅ΡΡΠ΅ ΠΎΡΠ²Π΅ΡΡΡΠΈΠ΅ ΠΏΡΠΎΠ΄Π΅Π²Π°Π΅ΡΡΡ Ρ ΠΎΠ΄ΠΎΠ²ΠΎΠΉ Π²ΠΈΠ½Ρ ΠΈ ΡΡΠ°Π²ΠΈΡΡΡ Π³Π°ΠΉΠΊΠ°. ΠΠΈΠ½Ρ, Π²ΡΡΠ°Π²Π»Π΅Π½Π½ΡΠΉ Π² ΠΎΡΠ²Π΅ΡΡΡΠΈΠ΅ Π²ΡΠΎΡΠΎΠ³ΠΎ Π±ΡΡΡΠΊΠ°, Π·Π°Π²ΠΈΠ½ΡΠΈΠ²Π°ΡΡ Π΄ΠΎ ΡΠΏΠΎΡΠ°, ΡΡΠΎΠ±Ρ ΠΎΠ½, ΠΏΡΠΎΠΉΠ΄Ρ ΡΠ΅ΡΠ΅Π· ΡΡΠΈ ΠΎΡΠ²Π΅ΡΡΡΠΈΡ, Π²ΡΡΠ΅Π» Π½Π° Π²Π°Π» Π΄Π²ΠΈΠ³Π°ΡΠ΅Π»Ρ.
- ΠΠ°Π»Π΅Π΅ ΠΏΡΠ΅Π΄ΡΡΠΎΠΈΡ ΡΠΎΠ΅Π΄ΠΈΠ½Π΅Π½ΠΈΠ΅ ΡΡΠ΅ΡΠΆΠ½Ρ Ρ Π²Π°Π»ΠΎΠΌ Π΄Π²ΠΈΠ³Π°ΡΠ΅Π»Ρ ΠΎΡΡΠ΅Π·ΠΊΠΎΠΌ ΡΠ»Π°Π½Π³Π° ΠΈΠ· ΡΠ΅Π·ΠΈΠ½Ρ ΠΈ ΠΏΡΠΎΠ²ΠΎΠ»ΠΎΡΠ½ΡΠΌ Π·Π°ΠΆΠΈΠΌΠΎΠΌ.
- ΠΠ»Ρ ΠΊΡΠ΅ΠΏΠ»Π΅Π½ΠΈΡ Ρ ΠΎΠ΄ΠΎΠ²ΠΎΠΉ Π³Π°ΠΉΠΊΠΈ Π½ΡΠΆΠ½Ρ Π΄ΠΎΠΏΠΎΠ»Π½ΠΈΡΠ΅Π»ΡΠ½ΡΠ΅ Π²ΠΈΠ½ΡΡ.
- Π‘Π΄Π΅Π»Π°Π½Π½Π°Ρ ΠΏΠΎΠ΄ΡΡΠ°Π²ΠΊΠ° ΡΠ°ΠΊΠΆΠ΅ ΠΊΡΠ΅ΠΏΠΈΡΡΡ ΠΊ Π²ΡΠΎΡΠΎΠΌΡ Π±ΡΡΡΠΊΡ ΠΏΡΠΈ ΠΏΠΎΠΌΠΎΡΠΈ ΡΡΡΡΠΏΠΎΠ². ΠΠΎΡΠΈΠ·ΠΎΠ½ΡΠ°Π»ΡΠ½ΡΠΉ ΡΡΠΎΠ²Π΅Π½Ρ ΡΠ΅Π³ΡΠ»ΠΈΡΡΠ΅ΡΡΡ Π΄ΠΎΠΏΠΎΠ»Π½ΠΈΡΠ΅Π»ΡΠ½ΡΠΌΠΈ Π²ΠΈΠ½ΡΠ°ΠΌΠΈ ΠΈ Π³Π°ΠΉΠΊΠ°ΠΌΠΈ.
- ΠΠ±ΡΡΠ½ΠΎ Π²ΠΌΠ΅ΡΡΠ΅ Ρ ΠΊΠΎΠ½ΡΡΠΎΠ»Π»Π΅ΡΠ°ΠΌΠΈ ΠΏΠΎΠ΄ΠΊΠ»ΡΡΠ°ΡΡΡΡ ΠΈ Π΄Π²ΠΈΠ³Π°ΡΠ΅Π»ΠΈ ΠΈ ΡΠ΅ΡΡΠΈΡΡΡΡΡΡ Π½Π° ΠΏΡΠ΅Π΄ΠΌΠ΅Ρ ΠΏΡΠ°Π²ΠΈΠ»ΡΠ½ΠΎΠ³ΠΎ ΡΠΎΠ΅Π΄ΠΈΠ½Π΅Π½ΠΈΡ. ΠΠ°Π»Π΅Π΅ ΡΠ»Π΅Π΄ΡΠ΅Ρ ΠΏΡΠΎΠ²Π΅ΡΠΊΠ° ΠΌΠ°ΡΡΡΠ°Π±ΠΈΡΠΎΠ²Π°Π½ΠΈΡ Π§ΠΠ£, ΠΏΡΠΎΠ³ΠΎΠ½ΠΊΠ° ΡΠ΅ΡΡΠΎΠ²ΠΎΠΉ ΠΏΡΠΎΠ³ΡΠ°ΠΌΠΌΡ.
- ΠΡΡΠ°Π΅ΡΡΡ ΡΠ΄Π΅Π»Π°ΡΡ ΠΊΠΎΡΠΏΡΡ ΡΡΡΡΠΎΠΉΡΡΠ²Π° ΠΈ ΡΡΠΎ Π±ΡΠ΄Π΅Ρ Π·Π°Π²Π΅ΡΡΠ°ΡΡΠΈΠΌ ΡΡΠ°ΠΏΠΎΠΌ ΡΠ°Π±ΠΎΡΡ ΡΠ΅Ρ , ΠΊΡΠΎ ΡΠΎΠ·ΠΈΠ΄Π°Π΅Ρ ΡΠ°ΠΌΠΎΠ΄Π΅Π»ΡΠ½ΡΠ΅ ΡΡΠ°Π½ΠΊΠΈ.
ΠΡΠΎΠ³ΡΠ°ΠΌΠΌΠΈΡΡΡ ΡΠ°Π±ΠΎΡΡ 3-ΠΎΡΠ΅Π²ΠΎΠ³ΠΎ ΡΡΠ°Π½ΠΊΠ°, Π² Π½Π°ΡΡΡΠΎΠΉΠΊΠ°Ρ ΠΏΠΎ ΠΏΠ΅ΡΠ²ΡΠΌ Π΄Π²ΡΠΌ ΠΎΡΡΠΌ β Π±Π΅Π· ΠΏΠ΅ΡΠ΅ΠΌΠ΅Π½. Π Π²ΠΎΡ ΠΏΡΠΈ ΠΏΡΠΎΠ³ΡΠ°ΠΌΠΌΠΈΡΠΎΠ²Π°Π½ΠΈΠΈ ΠΏΠ΅ΡΠ²ΡΡ 4-Ρ ΡΠ°Π· ΡΡΠ΅ΡΡΠ΅ΠΉ β Π²Π²ΠΎΠ΄ΡΡΡΡ ΠΈΠ·ΠΌΠ΅Π½Π΅Π½ΠΈΡ.
ΠΠ½ΠΈΠΌΠ°Π½ΠΈΠ΅!Β ΠΡΠΏΠΎΠ»ΡΠ·ΡΡ ΡΠΏΡΠΎΡΠ΅Π½Π½ΡΡ ΡΡ Π΅ΠΌΡ ΠΊΠΎΠ½ΡΡΠΎΠ»Π»Π΅ΡΠ° ATMega32 (ΠΡΠΈΠ»ΠΎΠΆΠ΅Π½ΠΈΠ΅ 1),Β Π² ΠΎΡΠ΄Π΅Π»ΡΠ½ΡΡ ΡΠ»ΡΡΠ°ΡΡ ΠΌΠΎΠΆΠ½ΠΎ ΡΡΠΎΠ»ΠΊΠ½ΡΡΡΡΡ Ρ Π½Π΅ΠΊΠΎΡΡΠ΅ΠΊΡΠ½ΠΎΠΉ ΠΎΠ±ΡΠ°Π±ΠΎΡΠΊΠΎΠΉ ΠΎΡΠΈΒ ZΒ β ΡΠ΅ΠΆΠΈΠΌ ΠΏΠΎΠ»ΡΡΠ°Π³Π°. Π Π²ΠΎΡ Π² ΠΏΠΎΠ»Π½ΠΎΠΉ Π²Π΅ΡΡΠΈΠΈ Π΅Π³ΠΎ ΠΏΠ»Π°ΡΡ (ΠΡΠΈΠ»ΠΎΠΆΠ΅Π½ΠΈΠ΅ 2), ΡΠΎΠΊΠΈ ΠΎΡΠ΅ΠΉ ΡΠ΅Π³ΡΠ»ΠΈΡΡΡΡΡΡ Π²Π½Π΅ΡΠ½ΠΈΠΌ Π°ΠΏΠΏΠ°ΡΠ°ΡΠ½ΡΠΌ Π¨ΠΠΠΎΠΌ.
ΠΠ°ΠΊΠ»ΡΡΠ΅Π½ΠΈΠ΅
Π ΠΊΠΎΠ½ΡΡΠΎΠ»Π»Π΅ΡΠ°Ρ , ΡΠΎΠ±ΡΠ°Π½Π½ΡΡ Π§ΠΠ£ ΡΡΠ°Π½ΠΊΠΎΠ² β ΡΠΈΡΠΎΠΊΠΈΠΉ ΡΠΏΠ΅ΠΊΡΡ ΠΈΡΠΏΠΎΠ»ΡΠ·ΠΎΠ²Π°Π½ΠΈΡ: Π² ΠΏΠ»ΠΎΡΡΠ΅ΡΠ°Ρ , Π½Π΅Π±ΠΎΠ»ΡΡΠΈΡ ΡΡΠ΅Π·Π΅ΡΠ°Ρ , ΡΠ°Π±ΠΎΡΠ°ΡΡΠΈΡ Ρ Π΄ΡΠ΅Π²Π΅ΡΠΈΠ½ΠΎΠΉ ΠΈ ΠΏΠ»Π°ΡΡΠΈΠΊΠΎΠ²ΡΠΌΠΈ Π΄Π΅ΡΠ°Π»ΡΠΌΠΈ, Π³ΡΠ°Π²Π΅ΡΠ°Ρ ΠΏΠΎ ΡΡΠ°Π»ΠΈ, ΠΌΠΈΠ½ΠΈΠ°ΡΡΡΠ½ΡΡ ΡΠ²Π΅ΡΠ»ΠΈΠ»ΡΠ½ΡΡ ΡΡΠ°Π½ΠΊΠ°Ρ .
Π£ΡΡΡΠΎΠΉΡΡΠ²Π° Ρ ΠΎΡΠ΅Π²ΡΠΌ ΡΡΠ½ΠΊΡΠΈΠΎΠ½Π°Π»ΠΎΠΌ ΠΈΡΠΏΠΎΠ»ΡΠ·ΡΡΡ ΡΠ°ΠΊΠΆΠ΅ Π² Π³ΡΠ°ΡΠΎΠΏΠΎΡΡΡΠΎΠΈΡΠ΅Π»ΡΡ , Π½Π° Π½ΠΈΡ ΠΌΠΎΠΆΠ½ΠΎ ΡΠΈΡΠΎΠ²Π°ΡΡ ΠΈ ΠΈΠ·Π³ΠΎΡΠΎΠ²Π»ΡΡΡ ΠΏΠ΅ΡΠ°ΡΠ½ΡΠ΅ ΠΏΠ»Π°ΡΡ. Π’Π°ΠΊ ΡΡΠΎ ΡΡΠΈΠ»ΠΈΡ, Π·Π°ΡΡΠ°ΡΠ΅Π½Π½ΡΠ΅ Π½Π° ΡΠ±ΠΎΡΠΊΡ ΠΌΠ°ΡΡΠ΅ΡΠ°ΠΌΠΈ-ΡΠΌΠ΅Π»ΡΡΠ°ΠΌΠΈ, Π² Π±ΡΠ΄ΡΡΠ΅ΠΌ ΠΊΠΎΠ½ΡΡΠΎΠ»Π»Π΅ΡΠ΅ ΠΎΠ±ΡΠ·Π°ΡΠ΅Π»ΡΠ½ΠΎ ΠΎΠΊΡΠΏΡΡΡΡ.
ΠΠΎΠ½ΡΡΠΎΠ»Π»Π΅Ρ Π΄Π»Ρ ΡΡΠ°Π½ΠΊΠ° Π»Π΅Π³ΠΊΠΎ ΡΠΌΠΎΠΆΠ΅Ρ ΡΠΎΠ±ΡΠ°ΡΡ ΠΈ Π΄ΠΎΠΌΠ°ΡΠ½ΠΈΠΉ ΠΌΠ°ΡΡΠ΅Ρ. ΠΠ°Π΄Π°ΡΡ Π½ΡΠΆΠ½ΡΠ΅ ΠΏΠ°ΡΠ°ΠΌΠ΅ΡΡΡ Π½Π΅ ΡΠ»ΠΎΠΆΠ½ΠΎ, Π΄ΠΎΡΡΠ°ΡΠΎΡΠ½ΠΎ ΡΡΠ΅ΡΡΡ Π½Π΅ΡΠΊΠΎΠ»ΡΠΊΠΎ Π½ΡΠ°Π½ΡΠΎΠ².
Π‘ΠΎΠ²Π΅ΡΡ ΠΏΠΎ ΡΠ±ΠΎΡΠΊΠ΅ ΠΊΠΎΠ½ΡΡΠΎΠ»Π»Π΅ΡΠΎΠ² Π΄Π»Ρ Π§ΠΠ£ ΡΡΠ°Π½ΠΊΠΎΠ²
ΠΠ΅Π· ΠΏΡΠ°Π²ΠΈΠ»ΡΠ½ΠΎΠ³ΠΎ Π²ΡΠ±ΠΎΡΠ° ΠΊΠΎΠ½ΡΡΠΎΠ»Π»Π΅ΡΠ° Π΄Π»Ρ ΡΡΠ°Π½ΠΊΠ° Π½Π΅ ΡΠ΄Π°ΡΡΡΡ ΡΠΎΠ±ΡΠ°ΡΡ ΡΠ°ΠΌ ΠΊΠΎΠ½ΡΡΠΎΠ»Π»Π΅Ρ Π΄Π»Ρ Π§ΠΠ£ Π½Π° Atmega8 16au ΡΠ²ΠΎΠΈΠΌΠΈ ΡΡΠΊΠ°ΠΌΠΈ. ΠΡΠΈ ΡΡΡΡΠΎΠΉΡΡΠ²Π° Π΄Π΅Π»ΡΡΡΡ Π½Π° Π΄Π²Π΅ ΡΠ°Π·Π½ΠΎΠ²ΠΈΠ΄Π½ΠΎΡΡΠΈ:
- ΠΠ½ΠΎΠ³ΠΎΠΊΠ°Π½Π°Π»ΡΠ½ΡΠ΅. Π‘ΡΠ΄Π° Π²Ρ ΠΎΠ΄ΡΡ 3 ΠΈ 4-ΠΎΡΠ΅Π²ΡΠ΅ ΠΊΠΎΠ½ΡΡΠΎΠ»Π»Π΅ΡΡ Π΄Π»Ρ ΡΠ°Π³ΠΎΠ²ΡΡ Π΄Π²ΠΈΠ³Π°ΡΠ΅Π»Π΅ΠΉ.
- ΠΠ΄Π½ΠΎΠΊΠ°Π½Π°Π»ΡΠ½ΡΠ΅.
ΠΠ΅Π±ΠΎΠ»ΡΡΠΈΠ΅ ΡΠ°ΡΠΎΠ²ΡΠ΅ Π΄Π²ΠΈΠ³Π°ΡΠ΅Π»ΠΈ Π½Π°ΠΈΠ±ΠΎΠ»Π΅Π΅ ΡΡΡΠ΅ΠΊΡΠΈΠ²Π½ΠΎ ΡΠΏΡΠ°Π²Π»ΡΡΡΡΡ ΠΌΠ½ΠΎΠ³ΠΎΠΊΠ°Π½Π°Π»ΡΠ½ΡΠΌΠΈ ΠΊΠΎΠ½ΡΡΠΎΠ»Π»Π΅ΡΠ°ΠΌΠΈ. Π‘ΡΠ°Π½Π΄Π°ΡΡΠ½ΡΠ΅ ΡΠΈΠΏΠΎΡΠ°Π·ΠΌΠ΅ΡΡ Π² Π΄Π°Π½Π½ΠΎΠΌ ΡΠ»ΡΡΠ°Π΅ β 42, Π»ΠΈΠ±ΠΎ 57 ΠΌΠΈΠ»Π»ΠΈΠΌΠ΅ΡΡΠΎΠ². ΠΡΠΎ ΠΎΡΠ»ΠΈΡΠ½ΡΠΉ Π²Π°ΡΠΈΠ°Π½Ρ Π΄Π»Ρ ΡΠ°ΠΌΠΎΡΡΠΎΡΡΠ΅Π»ΡΠ½ΠΎΠΉ ΡΠ±ΠΎΡΠΊΠΈ Π§ΠΠ£ ΡΡΠ°Π½ΠΊΠΎΠ², Ρ ΠΊΠΎΡΠΎΡΡΡ ΡΠ°Π±ΠΎΡΠ΅Π΅ ΠΏΠΎΠ»Π΅ ΠΈΠΌΠ΅Π΅Ρ ΡΠ°Π·ΠΌΠ΅Ρ Π΄ΠΎ 1 ΠΌΠ΅ΡΡΠ°.
ΠΡΠ»ΠΈ ΠΆΠ΅ ΡΠ°ΠΌΠΎΡΡΠΎΡΡΠ΅Π»ΡΠ½ΠΎ ΡΠΎΠ±ΠΈΡΠ°Π΅ΡΡΡ ΡΡΠ°Π½ΠΎΠΊ Β Π½Π° ΠΌΠΈΠΊΡΠΎΠΊΠΎΠ½ΡΡΠΎΠ»Π»Π΅ΡΠ΅ Ρ ΠΏΠΎΠ»Π΅ΠΌ Π±ΠΎΠ»Π΅Π΅ ΡΠ΅ΠΌ Π² 1 ΠΌΠ΅ΡΡ β Π½Π°Π΄ΠΎ ΠΈΡΠΏΠΎΠ»ΡΠ·ΠΎΠ²Π°ΡΡ Π΄Π²ΠΈΠ³Π°ΡΠ΅Π»ΠΈ, Π²ΡΠΏΡΡΠΊΠ°ΡΡΠΈΠ΅ΡΡ Π² ΡΠΈΠΏΠΎΡΠ°Π·ΠΌΠ΅ΡΠ°Ρ Π΄ΠΎ 86 ΠΌΠΈΠ»Π»ΠΈΠΌΠ΅ΡΡΠΎΠ². Π Π΄Π°Π½Π½ΠΎΠΌ ΡΠ»ΡΡΠ°Π΅ ΡΠ΅ΠΊΠΎΠΌΠ΅Π½Π΄ΡΠ΅ΡΡΡ ΠΎΡΠ³Π°Π½ΠΈΠ·ΠΎΠ²ΡΠ²Π°ΡΡ ΡΠΏΡΠ°Π²Π»Π΅Π½ΠΈΠ΅ ΠΌΠΎΡΠ½ΡΠΌΠΈ ΠΎΠ΄Π½ΠΎΠΊΠ°Π½Π°Π»ΡΠ½ΡΠΌΠΈ Π΄ΡΠ°ΠΉΠ²Π΅ΡΠ°ΠΌΠΈ, Ρ ΡΠΎΠΊΠΎΠΌ ΡΠΏΡΠ°Π²Π»Π΅Π½ΠΈΡ ΠΎΡ 4,2 Π ΠΈ Π²ΡΡΠ΅.
ΠΠΎΠ½ΡΡΠΎΠ»Π»Π΅ΡΡ ΡΠΎ ΡΠΏΠ΅ΡΠΈΠ°Π»ΡΠ½ΡΠΌΠΈ ΠΌΠΈΠΊΡΠΎΡΡ Π΅ΠΌΠ°ΠΌΠΈ-Π΄ΡΠ°ΠΉΠ²Π΅ΡΠ°ΠΌΠΈ ΠΏΠΎΠ»ΡΡΠΈΠ»ΠΈ ΡΠΈΡΠΎΠΊΠΎΠ΅ ΡΠ°ΡΠΏΡΠΎΡΡΡΠ°Π½Π΅Π½ΠΈΠ΅ Π² ΡΠ»ΡΡΠ°Π΅ Π½Π΅ΠΎΠ±Ρ ΠΎΠ΄ΠΈΠΌΠΎΡΡΠΈ ΠΎΡΠ³Π°Π½ΠΈΠ·ΠΎΠ²Π°ΡΡ ΠΊΠΎΠ½ΡΡΠΎΠ»Ρ ΡΠ°Π±ΠΎΡΡ ΡΡΠ°Π½ΠΊΠΎΠ² Ρ ΡΡΠ΅Π·Π΅ΡΠ°ΠΌΠΈ Π½Π°ΡΡΠΎΠ»ΡΠ½ΠΎΠ³ΠΎ ΡΠΈΠΏΠ°. ΠΠΏΡΠΈΠΌΠ°Π»ΡΠ½ΡΠΌ Π²Π°ΡΠΈΠ°Π½ΡΠΎΠΌ Π±ΡΠ΄Π΅Ρ ΠΌΠΈΠΊΡΠΎΡΡ Π΅ΠΌΠ°, ΠΎΠ±ΠΎΠ·Π½Π°ΡΠ°Π΅ΠΌΠ°Ρ ΠΊΠ°ΠΊ TB6560 ΠΈΠ»ΠΈ A3977. Π£ ΡΡΠΎΠ³ΠΎ ΠΈΠ·Π΄Π΅Π»ΠΈΡ Π²Π½ΡΡΡΠΈ Π΅ΡΡΡ ΠΊΠΎΠ½ΡΡΠΎΠ»Π»Π΅Ρ, ΡΠΏΠΎΡΠΎΠ±ΡΡΠ²ΡΡΡΠΈΠΉ ΡΠΎΡΠΌΠΈΡΠΎΠ²Π°Π½ΠΈΡ ΠΏΡΠ°Π²ΠΈΠ»ΡΠ½ΠΎΠΉ ΡΠΈΠ½ΡΡΠΎΠΈΠ΄Ρ Π΄Π»Ρ ΡΠ΅ΠΆΠΈΠΌΠΎΠ², ΠΏΠΎΠ΄Π΄Π΅ΡΠΆΠΈΠ²Π°ΡΡΠΈΡ ΡΠ°Π·Π½ΡΠ΅ ΠΏΠΎΠ»ΡΡΠ°Π³ΠΈ. Π’ΠΎΠΊΠΈ ΠΎΠ±ΠΌΠΎΡΠΊΠΈ ΠΌΠΎΠ³ΡΡ Π±ΡΡΡ ΡΡΡΠ°Π½ΠΎΠ²Π»Π΅Π½Ρ ΠΏΡΠΎΠ³ΡΠ°ΠΌΠΌΠ½ΡΠΌ ΡΠΏΠΎΡΠΎΠ±ΠΎΠΌ. ΠΡΠΈ ΠΌΠΈΠΊΡΠΎΠΊΠΎΠ½ΡΡΠΎΠ»Π»Π΅ΡΠ°Ρ Π΄ΠΎΠ±ΠΈΡΡΡΡ ΡΠ΅Π·ΡΠ»ΡΡΠ°ΡΠ° ΠΏΡΠΎΡΡΠΎ.
Π£ΠΏΡΠ°Π²Π»Π΅Π½ΠΈΠ΅
ΠΠΎΠ½ΡΡΠΎΠ»Π»Π΅ΡΠΎΠΌ Π»Π΅Π³ΠΊΠΎ ΡΠΏΡΠ°Π²Π»ΡΡΡ, ΠΈΡΠΏΠΎΠ»ΡΠ·ΡΡ ΡΠΏΠ΅ΡΠΈΠ°Π»ΠΈΠ·ΠΈΡΠΎΠ²Π°Π½Π½ΠΎΠ΅ ΠΏΡΠΎΠ³ΡΠ°ΠΌΠΌΠ½ΠΎΠ΅ ΠΎΠ±ΠΎΡΡΠ΄ΠΎΠ²Π°Π½ΠΈΠ΅, ΡΡΡΠ°Π½ΠΎΠ²Π»Π΅Π½Π½ΠΎΠ΅ Π½Π° ΠΠ. ΠΠ»Π°Π²Π½ΠΎΠ΅, ΡΡΠΎΠ±Ρ Ρ ΡΠ°ΠΌΠΎΠ³ΠΎ ΠΊΠΎΠΌΠΏΡΡΡΠ΅ΡΠ° ΠΏΠ°ΠΌΡΡΡ Π±ΡΠ»Π° ΠΌΠΈΠ½ΠΈΠΌΡΠΌ 1 ΠΠ, Π° ΠΏΡΠΎΡΠ΅ΡΡΠΎΡ β Π½Π΅ ΠΌΠ΅Π½Π΅Π΅ 1 GHz.
ΠΠΎΠΆΠ½ΠΎ ΠΈΡΠΏΠΎΠ»ΡΠ·ΠΎΠ²Π°ΡΡ Π½ΠΎΡΡΠ±ΡΠΊΠΈ, Π½ΠΎ ΡΡΠ°ΡΠΈΠΎΠ½Π°ΡΠ½ΡΠ΅ ΠΊΠΎΠΌΠΏΡΡΡΠ΅ΡΡ Π² ΡΡΠΎΠΌ ΠΏΠ»Π°Π½Π΅ Π΄Π°ΡΡ Π»ΡΡΡΠΈΠ΅ ΡΠ΅Π·ΡΠ»ΡΡΠ°ΡΡ. Π ΠΎΠ±Ρ ΠΎΠ΄ΡΡΡΡ Π³ΠΎΡΠ°Π·Π΄ΠΎ Π΄Π΅ΡΠ΅Π²Π»Π΅. ΠΠΎΠΌΠΏΡΡΡΠ΅Ρ ΠΌΠΎΠΆΠ½ΠΎ ΠΈΡΠΏΠΎΠ»ΡΠ·ΠΎΠ²Π°ΡΡ Π΄Π»Ρ ΡΠ΅ΡΠ΅Π½ΠΈΡ Π΄ΡΡΠ³ΠΈΡ Π·Π°Π΄Π°Ρ, ΠΊΠΎΠ³Π΄Π° ΡΡΠ°Π½ΠΊΠΈ Π½Π΅ ΡΡΠ΅Π±ΡΡΡ ΡΠΏΡΠ°Π²Π»Π΅Π½ΠΈΡ. Π₯ΠΎΡΠΎΡΠΎ, Π΅ΡΠ»ΠΈ Π΅ΡΡΡ Π²ΠΎΠ·ΠΌΠΎΠΆΠ½ΠΎΡΡΡ ΠΎΠΏΡΠΈΠΌΠΈΠ·ΠΈΡΠΎΠ²Π°ΡΡ ΡΠΈΡΡΠ΅ΠΌΡ ΠΏΠ΅ΡΠ΅Π΄ Π½Π°ΡΠ°Π»ΠΎΠΌ ΡΠ°Π±ΠΎΡΡ.
ΠΠ°ΡΠ°Π»Π»Π΅Π»ΡΠ½ΡΠΉ ΠΏΠΎΡΡ LPT β Π²ΠΎΡ ΠΊΠ°ΠΊΠ°Ρ Π΄Π΅ΡΠ°Π»Ρ ΠΏΠΎΠΌΠΎΠ³Π°Π΅Ρ ΠΎΡΠ³Π°Π½ΠΈΠ·ΠΎΠ²Π°ΡΡ ΠΏΠΎΠ΄ΠΊΠ»ΡΡΠ΅Π½ΠΈΠ΅. ΠΡΠ»ΠΈ ΠΊΠΎΠ½ΡΡΠΎΠ»Π»Π΅Ρ ΠΈΠΌΠ΅Π΅Ρ ΠΏΠΎΡΡ USB, ΡΠΎ ΠΈΡΠΏΠΎΠ»ΡΠ·ΡΠ΅ΡΡΡ ΡΠ°Π·ΡΠ΅ΠΌ ΡΠΎΠΎΡΠ²Π΅ΡΡΡΠ²ΡΡΡΠ΅ΠΉ ΡΠΎΡΠΌΡ. ΠΡΠΈ ΡΡΠΎΠΌ Π²ΡΠΏΡΡΠΊΠ°Π΅ΡΡΡ Π²ΡΠ΅ Π±ΠΎΠ»ΡΡΠ΅ ΠΈ Π±ΠΎΠ»ΡΡΠ΅ ΠΊΠΎΠΌΠΏΡΡΡΠ΅ΡΠΎΠ², Ρ ΠΊΠΎΡΠΎΡΡΡ ΠΏΠ°ΡΠ°Π»Π»Π΅Π»ΡΠ½ΡΠΉ ΠΏΠΎΡΡ ΠΎΡΡΡΡΡΡΠ²ΡΠ΅Ρ.
ΠΠ·Π³ΠΎΡΠΎΠ²Π»Π΅Π½ΠΈΠ΅ ΡΠ°ΠΌΠΎΠ³ΠΎ ΠΏΡΠΎΡΡΠΎΠ³ΠΎ Π²Π°ΡΠΈΠ°Π½ΡΠ° ΡΠΊΠ°Π½Π΅ΡΠ°
ΠΠ΄Π½ΠΎ ΠΈΠ· ΡΠ°ΠΌΡΡ ΠΏΡΠΎΡΡΡΡ ΡΠ΅ΡΠ΅Π½ΠΈΠΉ Π΄Π»Ρ ΡΠ°ΠΌΠΎΠ΄Π΅Π»ΡΠ½ΠΎΠ³ΠΎ ΡΠΎΠ·Π΄Π°Π½ΠΈΡ Π§ΠΠ£ ΡΡΠ°Π½ΠΊΠ° β ΠΈΡΠΏΠΎΠ»ΡΠ·ΠΎΠ²Π°Π½ΠΈΠ΅ Π΄Π΅ΡΠ°Π»Π΅ΠΉ ΠΎΡ Π΄ΡΡΠ³ΠΎΠ³ΠΎ ΠΎΠ±ΠΎΡΡΠ΄ΠΎΠ²Π°Π½ΠΈΡ, ΡΠ½Π°Π±ΠΆΠ΅Π½Π½ΠΎΠ³ΠΎ ΡΠ°ΡΠΎΠ²ΡΠΌΠΈ Π΄Π²ΠΈΠ³Π°ΡΠ΅Π»ΡΠΌΠΈ. Π€ΡΠ½ΠΊΡΠΈΡ ΠΎΡΠ»ΠΈΡΠ½ΠΎ Π²ΡΠΏΠΎΠ»Π½ΡΡΡ ΡΡΠ°ΡΡΠ΅ ΠΏΡΠΈΠ½ΡΠ΅ΡΡ.
ΠΠ΅ΡΠ΅ΠΌ ΡΠ»Π΅Π΄ΡΡΡΠΈΠ΅ Π΄Π΅ΡΠ°Π»ΠΈ, ΠΈΠ·Π²Π»Π΅ΡΠ΅Π½Π½ΡΠ΅ ΠΈΠ· ΠΏΡΠ΅ΠΆΠ½ΠΈΡ ΠΏΡΠΈΠ±ΠΎΡΠΎΠ²:
- Π‘Π°ΠΌΠ° ΠΌΠΈΠΊΡΠΎΡΡ Π΅ΠΌΠ°.
- Π¨Π°Π³ΠΎΠ²ΡΠΉ Π΄Π²ΠΈΠ³Π°ΡΠ΅Π»Ρ.
- ΠΠ°ΡΠ° ΡΡΠ°Π»ΡΠ½ΡΡ ΠΏΡΡΡΠΊΠΎΠ².
ΠΡΠΈ ΡΠΎΠ·Π΄Π°Π½ΠΈΠΈ ΠΊΠΎΡΠΏΡΡΠ° ΠΊΠΎΠ½ΡΡΠΎΠ»Π»Π΅ΡΠ° Π½Π°Π΄ΠΎ Π²Π·ΡΡΡ ΠΈ ΡΡΠ°ΡΡΡ ΠΊΠ°ΡΡΠΎΠ½Π½ΡΡ ΠΊΠΎΡΠΎΠ±ΠΊΡ. ΠΠΎΠΏΡΡΡΠΈΠΌΠΎ ΠΈΡΠΏΠΎΠ»ΡΠ·ΠΎΠ²Π°ΡΡ ΠΊΠΎΡΠΎΠ±ΠΊΠΈ ΠΈΠ· ΡΠ°Π½Π΅ΡΡ ΠΈΠ»ΠΈ ΡΠ΅ΠΊΡΡΠΎΠ»ΠΈΡΠ°, ΠΈΡΡ ΠΎΠ΄Π½ΡΠΉ ΠΌΠ°ΡΠ΅ΡΠΈΠ°Π» Π½Π΅ ΠΈΠΌΠ΅Π΅Ρ Π·Π½Π°ΡΠ΅Π½ΠΈΡ. ΠΠΎ ΠΊΠ°ΡΡΠΎΠ½ ΠΏΡΠΎΡΠ΅ Π²ΡΠ΅Π³ΠΎ ΠΎΠ±ΡΠ°Π±ΠΎΡΠ°ΡΡ, ΠΈΡΠΏΠΎΠ»ΡΠ·ΡΡ ΠΎΠ±ΡΡΠ½ΡΠ΅ Π½ΠΎΠΆΠ½ΠΈΡΡ.
Π‘ΠΏΠΈΡΠΎΠΊ ΠΈΠ½ΡΡΡΡΠΌΠ΅Π½ΡΠΎΠ² Π±ΡΠ΄Π΅Ρ Π²ΡΠ³Π»ΡΠ΄Π΅ΡΡ ΡΠ»Π΅Π΄ΡΡΡΠΈΠΌ ΠΎΠ±ΡΠ°Π·ΠΎΠΌ:
- ΠΠ°ΡΠ»ΡΠ½ΠΈΠΊ Π²ΠΌΠ΅ΡΡΠ΅, Π΄ΠΎΠΏΠΎΠ»Π½Π΅Π½Π½ΡΠΉ ΠΏΡΠΈΠ½Π°Π΄Π»Π΅ΠΆΠ½ΠΎΡΡΡΠΌΠΈ.
- ΠΠΈΡΡΠΎΠ»Π΅Ρ Ρ ΠΊΠ»Π΅Π΅ΠΌ.
- ΠΠΎΠΆΠ½ΠΈΡΠ½ΡΠΉ ΠΈΠ½ΡΡΡΡΠΌΠ΅Π½Ρ.
- ΠΡΡΠ°ΡΠΊΠΈ.
ΠΠ°ΠΊΠΎΠ½Π΅Ρ, ΠΈΠ·Π³ΠΎΡΠΎΠ²Π»Π΅Π½ΠΈΠ΅ ΠΊΠΎΠ½ΡΡΠΎΠ»Π»Π΅ΡΠ° ΠΏΠΎΡΡΠ΅Π±ΡΠ΅Ρ ΡΠ»Π΅Π΄ΡΡΡΠΈΡ Π΄ΠΎΠΏΠΎΠ»Π½ΠΈΡΠ΅Π»ΡΠ½ΡΡ Π΄Π΅ΡΠ°Π»Π΅ΠΉ:
- Π Π°Π·ΡΠ΅ΠΌ Ρ ΠΏΡΠΎΠ²ΠΎΠ΄ΠΎΠΌ, Π΄Π»Ρ ΠΎΡΠ³Π°Π½ΠΈΠ·Π°ΡΠΈΠΈ ΡΠ΄ΠΎΠ±Π½ΠΎΠ³ΠΎ ΠΏΠΎΠ΄ΠΊΠ»ΡΡΠ΅Π½ΠΈΡ.
- Π¦ΠΈΠ»ΠΈΠ½Π΄ΡΠΈΡΠ΅ΡΠΊΠΎΠ΅ Π³Π½Π΅Π·Π΄ΠΎ. Π’Π°ΠΊΠΈΠ΅ ΠΊΠΎΠ½ΡΡΡΡΠΊΡΠΈΠΈ ΠΎΡΠ²Π΅ΡΠ°ΡΡ Π·Π° ΠΏΠΈΡΠ°Π½ΠΈΠ΅ ΡΡΡΡΠΎΠΉΡΡΠ²Π°.
- Π₯ΠΎΠ΄ΠΎΠ²ΡΠΌΠΈ Π²ΠΈΠ½ΡΠ°ΠΌΠΈ ΡΠ»ΡΠΆΠ°Ρ ΡΡΠ΅ΡΠΆΠ½ΠΈ, ΠΈΠΌΠ΅ΡΡΠΈΠ΅ ΠΎΠΏΡΠ΅Π΄Π΅Π»Π΅Π½Π½ΡΡ ΡΠ΅Π·ΡΠ±Ρ.
- ΠΠ°ΠΉΠΊΠ° Ρ ΠΏΠΎΠ΄Ρ ΠΎΠ΄ΡΡΠΈΠΌΠΈ Π΄Π»Ρ Ρ ΠΎΠ΄ΠΎΠ²ΠΎΠ³ΠΎ Π²ΠΈΠ½ΡΠ° ΡΠ°Π·ΠΌΠ΅ΡΠ°ΠΌΠΈ.
- Π¨ΡΡΡΠΏΡ, ΡΠ°ΠΉΠ±Ρ, Π΄ΡΠ΅Π²Π΅ΡΠΈΠ½Π° Π² ΡΠΎΡΠΌΠ΅ ΠΊΡΡΠΊΠΎΠ².
ΠΠ°ΡΠΈΠ½Π°Π΅ΠΌ ΡΠ°Π±ΠΎΡΡ ΠΏΠΎ ΡΠΎΠ·Π΄Π°Π½ΠΈΡ ΡΠ°ΠΌΠΎΠ΄Π΅Π»ΡΠ½ΠΎΠ³ΠΎ ΡΡΠ°Π½ΠΊΠ°
Π¨Π°Π³ΠΎΠ²ΡΠΉ Π΄Π²ΠΈΠ³Π°ΡΠ΅Π»Ρ Π²ΠΌΠ΅ΡΡΠ΅ Ρ ΠΏΠ»Π°ΡΠΎΠΉ Π΄ΠΎΠ»ΠΆΠ½Ρ Π±ΡΡΡ ΠΈΠ·Π²Π»Π΅ΡΠ΅Π½Ρ ΠΈΠ· ΡΡΠ°ΡΡΡ ΡΡΡΡΠΎΠΉΡΡΠ². Π£ ΡΠΊΠ°Π½Π΅ΡΠ° Π΄ΠΎΡΡΠ°ΡΠΎΡΠ½ΠΎ ΡΠ½ΡΡΡ ΡΡΠ΅ΠΊΠ»ΠΎ, Π° Π·Π°ΡΠ΅ΠΌ β Π²ΡΠ²Π΅ΡΠ½ΡΡΡ Π½Π΅ΡΠΊΠΎΠ»ΡΠΊΠΎ Π±ΠΎΠ»ΡΠΎΠ². Π‘Π½ΠΈΠΌΠ°ΡΡ ΠΏΠΎΡΡΠ΅Π±ΡΠ΅ΡΡΡ ΠΈ ΡΡΠ°Π»ΡΠ½ΡΠ΅ ΡΡΠ΅ΡΠΆΠ½ΠΈ, ΠΈΡΠΏΠΎΠ»ΡΠ·ΡΠ΅ΠΌΡΠ΅ Π² Π΄Π°Π»ΡΠ½Π΅ΠΉΡΠ΅ΠΌ, ΡΠΎΠ·Π΄Π°Π²Π°Ρ ΡΠ΅ΡΡΠΎΠ²ΡΠΉ ΠΏΠΎΡΡΠ°Π».
ΠΠΈΠΊΡΠΎΡΡ Π΅ΠΌΠ° ΡΠΏΡΠ°Π²Π»Π΅Π½ΠΈΡ ULN2003 ΡΡΠ°Π½Π΅Ρ ΠΎΠ΄Π½ΠΈΠΌ ΠΈΠ· Π³Π»Π°Π²Π½ΡΡ ΡΠ»Π΅ΠΌΠ΅Π½ΡΠΎΠ². ΠΠΎΠ·ΠΌΠΎΠΆΠ½ΠΎ ΠΎΡΠ΄Π΅Π»ΡΠ½ΠΎΠ΅ ΠΏΡΠΈΠΎΠ±ΡΠ΅ΡΠ΅Π½ΠΈΠ΅ Π΄Π΅ΡΠ°Π»Π΅ΠΉ, Π΅ΡΠ»ΠΈ Π² ΡΠΊΠ°Π½Π΅ΡΠ΅ ΠΈΡΠΏΠΎΠ»ΡΠ·ΡΡΡΡΡ Π΄ΡΡΠ³ΠΈΠ΅ ΡΠ°Π·Π½ΠΎΠ²ΠΈΠ΄Π½ΠΎΡΡΠΈ ΠΌΠΈΠΊΡΠΎΡΡ Π΅ΠΌ. Π ΡΠ»ΡΡΠ°Π΅ Π½Π°Π»ΠΈΡΠΈΡ Π½ΡΠΆΠ½ΠΎΠ³ΠΎ ΡΡΡΡΠΎΠΉΡΡΠ²Π° Π½Π° ΠΏΠ»Π°ΡΠ΅ Π΅Π³ΠΎ Π°ΠΊΠΊΡΡΠ°ΡΠ½ΠΎ Π²ΡΠΏΠ°ΠΈΠ²Π°Π΅ΠΌ. ΠΠΎΡΡΠ΄ΠΎΠΊ Π΄Π΅ΠΉΡΡΠ²ΠΈΠΉ ΠΏΡΠΈ ΡΠ±ΠΎΡΠΊΠ΅ ΠΊΠΎΠ½ΡΡΠΎΠ»Π»Π΅ΡΠ° Π΄Π»Ρ Π§ΠΠ£ Π½Π° Atmega8 16au ΡΠ²ΠΎΠΈΠΌΠΈ ΡΡΠΊΠ°ΠΌΠΈ Π²ΡΠ³Π»ΡΠ΄ΠΈΡ ΡΠ»Π΅Π΄ΡΡΡΠΈΠΌ ΠΎΠ±ΡΠ°Π·ΠΎΠΌ:
- Π‘Π½Π°ΡΠ°Π»Π° ΡΠ°Π·ΠΎΠ³ΡΠ΅Π²Π°Π΅ΠΌ ΠΎΠ»ΠΎΠ²ΠΎ, ΠΈΡΠΏΠΎΠ»ΡΠ·ΡΡ ΠΏΠ°ΡΠ»ΡΠ½ΠΈΠΊ.
- Π£Π΄Π°Π»Π΅Π½ΠΈΠ΅ Π²Π΅ΡΡ Π½Π΅Π³ΠΎ ΡΠ»ΠΎΡ ΠΏΠΎΡΡΠ΅Π±ΡΠ΅Ρ ΠΈΡΠΏΠΎΠ»ΡΠ·ΠΎΠ²Π°Π½ΠΈΡ ΠΎΡΡΠΎΡΠ°.
- ΠΠ΄Π½ΠΈΠΌ ΠΊΠΎΠ½ΡΠΎΠΌ ΠΎΡΠ²Π΅ΡΡΠΊΡ ΡΡΡΠ°Π½Π°Π²Π»ΠΈΠ²Π°Π΅ΠΌ ΠΏΠΎΠ΄ ΠΌΠΈΠΊΡΠΎΡΡ Π΅ΠΌΡ.
- ΠΠ°Π»ΠΎ ΠΏΠ°ΡΠ»ΡΠ½ΠΈΠΊΠ° Π΄ΠΎΠ»ΠΆΠ½ΠΎ ΠΊΠ°ΡΠ°ΡΡΡΡ ΠΊΠ°ΠΆΠ΄ΠΎΠ³ΠΎ Π²ΡΠ²ΠΎΠ΄Π° ΠΌΠΈΠΊΡΠΎΡΡ Π΅ΠΌΡ. ΠΡΠ»ΠΈ ΡΡΠΎ ΡΡΠ»ΠΎΠ²ΠΈΠ΅ ΡΠΎΠ±Π»ΡΠ΄Π°Π΅ΡΡΡ, Π½Π° ΠΈΠ½ΡΡΡΡΠΌΠ΅Π½Ρ ΠΌΠΎΠΆΠ½ΠΎ Π½Π°ΠΆΠΈΠΌΠ°ΡΡ.
ΠΠ°Π»Π΅Π΅ ΠΌΠΈΠΊΡΠΎΡΡ Π΅ΠΌΠ° ΠΏΡΠΈΠΏΠ°ΠΈΠ²Π°Π΅ΡΡΡ Π½Π° ΠΏΠ»Π°ΡΡ, ΡΠΎΠΆΠ΅ Ρ ΠΌΠ°ΠΊΡΠΈΠΌΠ°Π»ΡΠ½ΠΎΠΉ Π°ΠΊΠΊΡΡΠ°ΡΠ½ΠΎΡΡΡΡ. ΠΠ»Ρ ΠΏΠ΅ΡΠ²ΡΡ ΠΏΡΠΎΠ±Π½ΡΡ ΡΠ°Π³ΠΎΠ² ΠΌΠΎΠΆΠ½ΠΎ ΠΈΡΠΏΠΎΠ»ΡΠ·ΠΎΠ²Π°ΡΡ ΠΌΠ°ΠΊΠ΅ΡΡ. ΠΡΠΏΠΎΠ»ΡΠ·ΡΠ΅ΠΌ Π²Π°ΡΠΈΠ°Π½Ρ Ρ Π΄Π²ΡΠΌΡ ΡΠΈΠ½Π°ΠΌΠΈ ΡΠ»Π΅ΠΊΡΡΠΎΠΏΠΈΡΠ°Π½ΠΈΡ. ΠΠ΄Π½Π° ΠΈΠ· Π½ΠΈΡ ΡΠΎΠ΅Π΄ΠΈΠ½ΡΠ΅ΡΡΡ Ρ ΠΏΠΎΠ»ΠΎΠΆΠΈΡΠ΅Π»ΡΠ½ΡΠΌ Π²ΡΠ²ΠΎΠ΄ΠΎΠΌ, Π° Π΄ΡΡΠ³Π°Ρ β Ρ ΠΎΡΡΠΈΡΠ°ΡΠ΅Π»ΡΠ½ΡΠΌ.
ΠΠ° ΡΠ»Π΅Π΄ΡΡΡΠ΅ΠΌ ΡΡΠ°ΠΏΠ΅ ΠΈΠ΄Π΅Ρ ΡΠΎΠ΅Π΄ΠΈΠ½Π΅Π½ΠΈΠ΅ Π²ΡΠ²ΠΎΠ΄Π° Ρ Π²ΡΠΎΡΠΎΠ³ΠΎ ΠΊΠΎΠ½Π½Π΅ΠΊΡΠΎΡΠ° ΠΏΠ°ΡΠ°Π»Π»Π΅Π»ΡΠ½ΠΎΠ³ΠΎ ΠΏΠΎΡΡΠ° Ρ Π²ΡΠ²ΠΎΠ΄ΠΎΠΌ Π² ΡΠ°ΠΌΠΎΠΉ ΠΌΠΈΠΊΡΠΎΡΡ Π΅ΠΌΠ΅. ΠΡΠ²ΠΎΠ΄Ρ Ρ ΠΊΠΎΠ½Π½Π΅ΠΊΡΠΎΡΠ° ΠΈ ΠΌΠΈΠΊΡΠΎΡΡ Π΅ΠΌΡ Π΄ΠΎΠ»ΠΆΠ½Ρ Π±ΡΡΡ ΡΠΎΠ΅Π΄ΠΈΠ½Π΅Π½Ρ ΡΠΎΠΎΡΠ²Π΅ΡΡΡΠ²ΡΡΡΠΈΠΌ ΠΎΠ±ΡΠ°Π·ΠΎΠΌ.
ΠΡΠ»Π΅Π²ΠΎΠΉ Π²ΡΠ²ΠΎΠ΄ ΠΏΡΠΈΡΠΎΠ΅Π΄ΠΈΠ½ΡΠ΅ΡΡΡ ΠΊ ΠΎΡΡΠΈΡΠ°ΡΠ΅Π»ΡΠ½ΠΎΠΉ ΡΠΈΠ½Π΅.
ΠΠ΄ΠΈΠ½ ΠΈΠ· ΠΏΠΎΡΠ»Π΅Π΄Π½ΠΈΡ ΡΡΠ°ΠΏΠΎΠ² β ΠΏΡΠΈΠΏΠ°ΠΉΠΊΠ° ΡΠ°Π³ΠΎΠ²ΠΎΠ³ΠΎ Π΄Π²ΠΈΠ³Π°ΡΠ΅Π»Ρ ΠΊ ΡΡΡΡΠΎΠΉΡΡΠ²Ρ ΡΠΏΡΠ°Π²Π»Π΅Π½ΠΈΡ.
Π₯ΠΎΡΠΎΡΠΎ, Π΅ΡΠ»ΠΈ Π΅ΡΡΡ Π²ΠΎΠ·ΠΌΠΎΠΆΠ½ΠΎΡΡΡ ΠΈΠ·ΡΡΠΈΡΡ Π΄ΠΎΠΊΡΠΌΠ΅Π½ΡΠ°ΡΠΈΡ ΠΎΡ ΠΏΡΠΎΠΈΠ·Π²ΠΎΠ΄ΠΈΡΠ΅Π»Ρ ΡΡΡΡΠΎΠΉΡΡΠ². ΠΡΠ»ΠΈ Π½Π΅Ρ, ΡΠΎ ΠΏΡΠΈΠ΄Π΅ΡΡΡ ΡΠ°ΠΌΠΎΡΡΠΎΡΡΠ΅Π»ΡΠ½ΠΎ ΠΈΡΠΊΠ°ΡΡ ΠΏΠΎΠ΄Ρ ΠΎΠ΄ΡΡΠ΅Π΅ ΡΠ΅ΡΠ΅Π½ΠΈΠ΅.
ΠΡΠΎΠ²ΠΎΠ΄Π° ΡΠ΅ΠΊΠΎΠΌΠ΅Π½Π΄ΡΠ΅ΡΡΡ ΠΏΡΠΈΠΏΠ°ΠΈΠ²Π°ΡΡ ΡΠ°ΠΊ, ΡΡΠΎΠ±Ρ ΠΏΠΎΡΠΎΠΌ ΠΈΡ ΠΌΠΎΠΆΠ½ΠΎ Π±ΡΠ»ΠΎ Π»Π΅Π³ΠΊΠΎ ΡΠΎΠ΅Π΄ΠΈΠ½ΠΈΡΡ Ρ Π·Π°ΠΆΠΈΠΌΠ°ΠΌΠΈ-ΠΊΡΠΎΠΊΠΎΠ΄ΠΈΠ»Π°ΠΌΠΈ. ΠΠ»Π΅ΠΌΠΌΡ Ρ Π²ΠΈΠ½ΡΠΎΠ²ΡΠΌΠΈ ΡΠΎΠ΅Π΄ΠΈΠ½Π΅Π½ΠΈΡΠΌΠΈ β ΠΏΠΎΠ΄Ρ ΠΎΠ΄ΡΡΠΈΠ΅ Π΄Π»Ρ ΡΠ΅ΡΠ΅Π½ΠΈΡ Π·Π°Π΄Π°ΡΠΈ ΡΠ΅ΡΠ΅Π½ΠΈΡ. ΠΠ°ΠΊ ΠΈ Π»ΡΠ±ΡΠ΅ Π΄ΡΡΠ³ΠΈΠ΅ ΠΏΠΎΠ΄ΠΎΠ±Π½ΡΠ΅ Π΄Π΅ΡΠ°Π»ΠΈ.
ΠΡΠΎΠ²ΠΎΠ΄Π° ΡΠΎΠ΅Π΄ΠΈΠ½ΡΡΡΡΡ Ρ Π²ΡΠ²ΠΎΠ΄Π°ΠΌΠΈ. ΠΠ°ΠΊΠΎΠ½Π΅Ρ, ΠΎΠ΄ΠΈΠ½ ΠΈΠ· Π½ΠΈΡ ΡΠΎΠ΅Π΄ΠΈΠ½ΡΠ΅ΡΡΡ Ρ ΠΏΠΎΠ»ΠΎΠΆΠΈΡΠ΅Π»ΡΠ½ΠΎΠΉ ΡΠΈΠ½ΠΎΠΉ.
Π¨ΠΈΠ½Ρ ΠΈ Π³Π½Π΅Π·Π΄Π° ΡΠ»Π΅ΠΊΡΡΠΎΠΏΠΈΡΠ°Π½ΠΈΡ Π½ΡΠΆΠ½ΠΎ ΡΠΎΠ΅Π΄ΠΈΠ½ΠΈΡΡ.
Π’Π΅ΡΠΌΠΎΠΊΠ»Π΅ΠΉ ΠΈΠ· ΠΏΠΈΡΡΠΎΠ»Π΅ΡΠ° ΠΏΠΎΠΌΠΎΠΆΠ΅Ρ Π·Π°ΠΊΡΠ΅ΠΏΠΈΡΡ Π΄Π΅ΡΠ°Π»ΠΈ, ΡΡΠΎΠ±Ρ ΠΎΠ½ΠΈ Π½Π΅ ΠΎΡΠΊΠ°Π»ΡΠ²Π°Π»ΠΈΡΡ.
ΠΡΠΏΠΎΠ»ΡΠ·ΡΠ΅ΠΌ Turbo CNC β ΠΏΡΠΎΠ³ΡΠ°ΠΌΠΌΡ Π΄Π»Ρ ΡΠΏΡΠ°Π²Π»Π΅Π½ΠΈΡ
ΠΠ Turbo CNC ΡΠΎΡΠ½ΠΎ Π±ΡΠ΄Π΅Ρ ΡΠ°Π±ΠΎΡΠ°ΡΡ Ρ ΠΌΠΈΠΊΡΠΎΠΊΠΎΠ½ΡΡΠΎΠ»Π»Π΅ΡΠΎΠΌ, ΠΊΠΎΡΠΎΡΡΠΉ ΠΈΡΠΏΠΎΠ»ΡΠ·ΡΠ΅Ρ ΠΌΠΈΠΊΡΠΎΡΡ Π΅ΠΌΡ ULN2003.
- ΠΡΠΏΠΎΠ»ΡΠ·ΡΠ΅ΠΌ ΡΠΏΠ΅ΡΠΈΠ°Π»ΠΈΠ·ΠΈΡΠΎΠ²Π°Π½Π½ΡΠΉ ΡΠ°ΠΉΡ, ΠΎΡΠΊΡΠ΄Π° ΠΌΠΎΠΆΠ½ΠΎ ΡΠΊΠ°ΡΠ°ΡΡ ΠΏΡΠΎΠ³ΡΠ°ΠΌΠΌΠ½ΠΎΠ΅ ΠΎΠ±ΠΎΡΡΠ΄ΠΎΠ²Π°Π½ΠΈΠ΅.
- ΠΡΠ±ΠΎΠΉ ΠΏΠΎΠ»ΡΠ·ΠΎΠ²Π°ΡΠ΅Π»Ρ ΡΠ°Π·Π±Π΅ΡΠ΅ΡΡΡ Π² ΡΠΎΠΌ, ΠΊΠ°ΠΊ ΠΏΡΠΎΠ²Π΅ΡΡΠΈ ΡΡΡΠ°Π½ΠΎΠ²ΠΊΡ.
- ΠΠΌΠ΅Π½Π½ΠΎ Π΄Π°Π½Π½Π°Ρ ΠΏΡΠΎΠ³ΡΠ°ΠΌΠΌΠ° Π»ΡΡΡΠ΅ Π²ΡΠ΅Π³ΠΎ ΡΠ°Π±ΠΎΡΠ°Π΅Ρ ΠΏΠΎΠ΄ MS-DOS. Π ΡΠ΅ΠΆΠΈΠΌΠ΅ ΡΠΎΠ²ΠΌΠ΅ΡΡΠΈΠΌΠΎΡΡΠΈ Π½Π° Windows ΠΌΠΎΠ³ΡΡ ΠΏΠΎΡΠ²Π»ΡΡΡΡΡ Π½Π΅ΠΊΠΎΡΠΎΡΡΠ΅ ΠΎΡΠΈΠ±ΠΊΠΈ.
- ΠΠΎ, Ρ Π΄ΡΡΠ³ΠΎΠΉ ΡΡΠΎΡΠΎΠ½Ρ, ΡΡΠΎ ΠΏΠΎΠ·Π²ΠΎΠ»ΠΈΡ ΡΠΎΠ±ΡΠ°ΡΡ ΠΊΠΎΠΌΠΏΡΡΡΠ΅Ρ Ρ ΠΎΠΏΡΠ΅Π΄Π΅Π»Π΅Π½Π½ΡΠΌΠΈ Ρ Π°ΡΠ°ΠΊΡΠ΅ΡΠΈΡΡΠΈΠΊΠ°ΠΌΠΈ, ΡΠΎΠ²ΠΌΠ΅ΡΡΠΈΠΌΡΠΌΠΈ ΠΈΠΌΠ΅Π½Π½ΠΎ Ρ Π΄Π°Π½Π½ΡΠΌ ΠΏΡΠΎΠ³ΡΠ°ΠΌΠΌΠ½ΡΠΌ ΠΎΠ±Π΅ΡΠΏΠ΅ΡΠ΅Π½ΠΈΠ΅ΠΌ.
Π Π΅ΠΊΠΎΠΌΠ΅Π½Π΄Π°ΡΠΈΠΈ ΠΏΠΎ Π½Π°ΡΡΡΠΎΠΉΠΊΠ°ΠΌ
- ΠΠΎΡΠ»Π΅ ΠΏΠ΅ΡΠ²ΠΎΠ³ΠΎ Π·Π°ΠΏΡΡΠΊΠ° ΠΏΡΠΎΠ³ΡΠ°ΠΌΠΌΡ ΠΏΠΎΡΠ²ΠΈΡΡΡ ΡΠΏΠ΅ΡΠΈΠ°Π»ΡΠ½ΡΠΉ ΡΠΊΡΠ°Π½.
- ΠΠ°Π΄ΠΎ Π½Π°ΠΆΠ°ΡΡ ΠΏΡΠΎΠ±Π΅Π». Π’Π°ΠΊ ΠΏΠΎΠ»ΡΠ·ΠΎΠ²Π°ΡΠ΅Π»Ρ ΠΎΠΊΠ°Π·ΡΠ²Π°Π΅ΡΡΡ Π² Π³Π»Π°Π²Π½ΠΎΠΌ ΠΌΠ΅Π½Ρ.
- ΠΠ°ΠΆΠΈΠΌΠ°Π΅ΠΌ F1, Π° ΠΏΠΎΡΠΎΠΌ Π²ΡΠ±ΠΈΡΠ°Π΅ΠΌ ΠΏΡΠ½ΠΊΡ Configure.
- ΠΠ°Π»Π΅Π΅ Π½Π°Π΄ΠΎ Π½Π°ΠΆΠ°ΡΡ ΠΏΡΠ½ΠΊΡ Β«number of AxisΒ». ΠΡΠΏΠΎΠ»ΡΠ·ΡΠ΅ΠΌ ΠΊΠ»Π°Π²ΠΈΡΡ Enter.
- ΠΡΡΠ°Π΅ΡΡΡ ΡΠΎΠ»ΡΠΊΠΎ Π²Π²Π΅ΡΡΠΈ ΠΊΠΎΠ»ΠΈΡΠ΅ΡΡΠ²ΠΎ ΡΠΎΠ΅ΠΉ, ΠΊΠΎΡΠΎΡΡΠ΅ ΠΏΠ»Π°Π½ΠΈΡΡΠ΅ΡΡΡ ΠΈΡΠΏΠΎΠ»ΡΠ·ΠΎΠ²Π°ΡΡ. Π Π΄Π°Π½Π½ΠΎΠΌ ΡΠ»ΡΡΠ°Π΅ Ρ Π½Π°Ρ ΠΎΠ΄ΠΈΠ½ ΠΌΠΎΡΠΎΡ, ΠΏΠΎΡΠΎΠΌΡ ΠΈ Π½Π°ΠΆΠΈΠΌΠ°Π΅ΠΌ Π½Π° ΡΠΈΡΡΡ 1.
- ΠΠ»Ρ ΠΏΡΠΎΠ΄ΠΎΠ»ΠΆΠ΅Π½ΠΈΡ ΠΈΡΠΏΠΎΠ»ΡΠ·ΡΠ΅ΠΌ Enter. ΠΠ°ΠΌ ΡΠ½ΠΎΠ²Π° ΠΏΠΎΠ½Π°Π΄ΠΎΠ±ΠΈΡΡΡ ΠΊΠ»Π°Π²ΠΈΡΠ° F1, ΠΏΠΎΡΠ»Π΅ Π΅Π΅ ΠΏΡΠΈΠΌΠ΅Π½Π΅Π½ΠΈΡ Π² ΠΌΠ΅Π½Ρ Configure Π²ΡΠ±ΠΈΡΠ°Π΅ΠΌ Configure Axis. ΠΠ°ΡΠ΅ΠΌ β Π΄Π²Π° ΡΠ°Π·Π° Π½Π°ΠΆΠΈΠΌΠ°Π΅ΠΌ ΠΏΡΠΎΠ±Π΅Π».
Drive Type β Π²ΠΎΡ ΠΊΠ°ΠΊΠ°Ρ Π²ΠΊΠ»Π°Π΄ΠΊΠ° Π½Π°ΠΌ Π½ΡΠΆΠ½Π°, Π΄ΠΎ Π½Π΅Π΅ Π΄ΠΎΡ ΠΎΠ΄ΠΈΠΌ ΠΌΠ½ΠΎΠ³ΠΎΡΠΈΡΠ»Π΅Π½Π½ΡΠΌΠΈ Π½Π°ΠΆΠΈΠΌΠ°Π½ΠΈΡΠΌΠΈ Tab. Π‘ΡΡΠ΅Π»ΠΊΠ° Π²Π½ΠΈΠ· ΠΏΠΎΠΌΠΎΠ³Π°Π΅Ρ Π΄ΠΎΠΉΡΠΈ Π΄ΠΎ ΠΏΡΠ½ΠΊΡΠ° Type. ΠΠ°ΠΌ Π½ΡΠΆΠ½Π° ΡΡΠ΅ΠΉΠΊΠ°, ΠΊΠΎΡΠΎΡΠ°Ρ Π½ΠΎΡΠΈΡ Π½Π°Π·Π²Π°Π½ΠΈΠ΅ Scale. ΠΠ°Π»Π΅Π΅ ΠΎΠΏΡΠ΅Π΄Π΅Π»ΡΠ΅ΠΌ, ΡΠΊΠΎΠ»ΡΠΊΠΎ ΡΠ°Π³ΠΎΠ² Π΄Π²ΠΈΠ³Π°ΡΠ΅Π»Ρ ΡΠΎΠ²Π΅ΡΡΠ°Π΅Ρ ΡΠΎΠ»ΡΠΊΠΎ Π·Π° Π²ΡΠ΅ΠΌΡ ΠΎΠ΄Π½ΠΎΠ³ΠΎ ΠΎΠ±ΠΎΡΠΎΡΠ°. ΠΠ»Ρ ΡΡΠΎΠ³ΠΎ Π΄ΠΎΡΡΠ°ΡΠΎΡΠ½ΠΎ Π·Π½Π°ΡΡ Π½ΠΎΠΌΠ΅Ρ Π΄Π΅ΡΠ°Π»ΠΈ. Π’ΠΎΠ³Π΄Π° Π»Π΅Π³ΠΊΠΎ Π±ΡΠ΄Π΅Ρ ΠΏΠΎΠ½ΡΡΡ, Π½Π° ΡΠΊΠΎΠ»ΡΠΊΠΎ Π³ΡΠ°Π΄ΡΡΠΎΠ² ΠΎΠ½ ΠΏΠΎΠ²ΠΎΡΠ°ΡΠΈΠ²Π°Π΅ΡΡΡ Π²ΡΠ΅Π³ΠΎ Π·Π° ΠΎΠ΄ΠΈΠ½ ΡΠ°Π³. ΠΠ°Π»Π΅Π΅ ΡΠΈΡΠ»ΠΎ Π³ΡΠ°Π΄ΡΡΠΎΠ² Π΄Π΅Π»ΠΈΡΡΡ Π½Π° ΠΎΠ΄ΠΈΠ½ ΡΠ°Π³. Π’Π°ΠΊ ΠΌΡ Π²ΡΡΠΈΡΠ»ΡΠ΅ΠΌ ΠΊΠΎΠ»ΠΈΡΠ΅ΡΡΠ²ΠΎ ΡΠ°Π³ΠΎΠ².
ΠΡΡΠ°Π»ΡΠ½ΡΠ΅ Π½Π°ΡΡΡΠΎΠΉΠΊΠΈ ΠΌΠΎΠΆΠ½ΠΎ ΠΎΡΡΠ°Π²ΠΈΡΡ Π² ΠΏΠ΅ΡΠ²ΠΎΠ½Π°ΡΠ°Π»ΡΠ½ΠΎΠΌ Π²ΠΈΠ΄Π΅. Π§ΠΈΡΠ»ΠΎ, ΠΏΠΎΠ»ΡΡΠΈΠ²ΡΠ΅Π΅ΡΡ Π² ΡΡΠ΅ΠΉΠΊΠ΅ Scale, ΠΏΡΠΎΡΡΠΎ ΠΊΠΎΠΏΠΈΡΡΠ΅ΡΡΡ Π² ΡΠ°ΠΊΡΡ ΠΆΠ΅ ΡΡΠ΅ΠΉΠΊΡ, Π½ΠΎ Π½Π° Π΄ΡΡΠ³ΠΎΠΌ ΠΊΠΎΠΌΠΏΡΡΡΠ΅ΡΠ΅. ΠΠ½Π°ΡΠ΅Π½ΠΈΠ΅ 20 Π΄ΠΎΠ»ΠΆΠ½ΠΎ Π±ΡΡΡ ΠΏΡΠΈΡΠ²ΠΎΠ΅Π½ΠΎ ΡΡΠ΅ΠΉΠΊΠ΅ Acceleration. ΠΠΎ ΡΠΌΠΎΠ»ΡΠ°Π½ΠΈΡ Π² ΡΡΠΎΠΉ ΠΎΠ±Π»Π°ΡΡΠΈ ΡΡΠΎΠΈΡ Π·Π½Π°ΡΠ΅Π½ΠΈΠ΅ 2000, Π½ΠΎ ΠΎΠ½ΠΎ ΡΠ»ΠΈΡΠΊΠΎΠΌ Π±ΠΎΠ»ΡΡΠΎΠ΅ Π΄Π»Ρ ΡΠΎΠ±ΠΈΡΠ°Π΅ΠΌΠΎΠΉ ΡΠΈΡΡΠ΅ΠΌΡ. ΠΠ°ΡΠ°Π»ΡΠ½ΡΠΉ ΡΡΠΎΠ²Π΅Π½Ρ β 20, Π° ΠΌΠ°ΠΊΡΠΈΠΌΠ°Π»ΡΠ½ΡΠΉ β 175. ΠΠ°Π»Π΅Π΅ ΠΎΡΡΠ°Π΅ΡΡΡ Π½Π°ΠΆΠΈΠΌΠ°ΡΡ TAB, ΠΏΠΎΠΊΠ° ΠΏΠΎΠ»ΡΠ·ΠΎΠ²Π°ΡΠ΅Π»Ρ Π½Π΅ Π΄ΠΎΡ ΠΎΠ΄ΠΈΡ Π΄ΠΎ ΠΏΡΠ½ΠΊΡΠ° Last Phase. ΠΠ΄Π΅ΡΡ Π½ΡΠΆΠ½ΠΎ ΠΏΠΎΡΡΠ°Π²ΠΈΡΡ ΡΠΈΡΡΡ 4. ΠΠ°Π»Π΅Π΅ ΠΆΠΌΠ΅ΠΌ Tab, ΠΏΠΎΠΊΠ° Π½Π΅ Π΄ΠΎΠΉΠ΄Π΅ΠΌ Π΄ΠΎ ΡΡΠ΄Π° ΠΈΠ· ΠΈΠΊΡΠΎΠ², ΠΏΠ΅ΡΠ²ΠΎΠ³ΠΎ Π² ΡΠΏΠΈΡΠΊΠ΅. ΠΠ΅ΡΠ²ΡΠ΅ ΡΠ΅ΡΡΡΠ΅ ΡΡΡΠΎΡΠΊΠΈ Π΄ΠΎΠ»ΠΆΠ½Ρ ΡΠΎΠ΄Π΅ΡΠΆΠ°ΡΡ ΡΠ»Π΅Π΄ΡΡΡΠΈΠ΅ ΠΏΠΎΠ·ΠΈΡΠΈΠΈ:
1000XXXXXXXX
0100XXXXXXXX
0010XXXXXXXX
0001XXXXXXXX
Π ΠΎΡΡΠ°Π»ΡΠ½ΡΡ ΡΡΠ΅ΠΉΠΊΠ°Ρ Π½Π΅ Π½ΡΠΆΠ½ΠΎ ΠΏΡΠΎΠ²ΠΎΠ΄ΠΈΡΡ Π½ΠΈΠΊΠ°ΠΊΠΈΡ ΠΈΠ·ΠΌΠ΅Π½Π΅Π½ΠΈΠΉ. ΠΡΠΎΡΡΠΎ Π²ΡΠ±ΠΈΡΠ°Π΅ΠΌ ΠΠ. ΠΡΠ΅, ΠΏΡΠΎΠ³ΡΠ°ΠΌΠΌΠ° Π½Π°ΡΡΡΠΎΠ΅Π½Π° Π΄Π»Ρ ΡΠ°Π±ΠΎΡΡ Ρ ΠΊΠΎΠΌΠΏΡΡΡΠ΅ΡΠΎΠΌ, ΡΠ°ΠΌΠΈΠΌΠΈ ΠΈΡΠΏΠΎΠ»Π½ΠΈΡΠ΅Π»ΡΠ½ΡΠΌΠΈ ΡΡΡΡΠΎΠΉΡΡΠ²Π°ΠΌΠΈ.
ΠΠΎΡΡΠ°ΡΠ°Π»ΡΡ Π½Π°ΠΏΠΈΡΠ°ΡΡ ΡΠΎΠ»ΡΠΊΠΎ ΡΠ΅ ΠΌΠΎΠΌΠ΅Π½ΡΡ, ΠΊΠΎΡΠΎΡΡΠ΅ Π»ΠΈΡΠ½ΠΎ ΠΌΠ½Π΅ ΠΏΠΎΠΊΠ°Π·Π°Π»ΠΈΡΡ Π²Π°ΠΆΠ½ΡΠΌΠΈ.
Π‘ΡΡΠ»ΠΊΠ° Π½Π° ΠΈΡΡ ΠΎΠ΄Π½ΠΈΠΊΠΈ ΠΊΠΎΠ½ΡΡΠΎΠ»Π»Π΅ΡΠ° ΠΈ Π½Π°ΡΡΡΠΎΠ΅Π½Π½ΡΡ ΠΎΠ±ΠΎΠ»ΠΎΡΠΊΡ Eclipse+gcc ΠΈ ΠΏΡ. Π»Π΅ΠΆΠ°Ρ ΡΠ°ΠΌ ΠΆΠ΅, Π³Π΄Π΅ ΡΠΎΠ»ΠΈΠΊ:
Π Π΅Π³ΡΠ»ΡΡΠ½ΠΎ ΡΡΠ°Π»ΠΊΠΈΠ²Π°ΡΡΡ, Ρ Π½Π΅ΠΎΠ±Ρ ΠΎΠ΄ΠΈΠΌΠΎΡΡΡΡ ΡΠ΄Π΅Π»Π°ΡΡ ΡΡ ΠΈΠ»ΠΈ ΠΈΠ½ΡΡ ΠΌΠ΅Π»ΠΊΡΡ Β«ΡΡΡΡΠΊΡΒ» ΡΠ»ΠΎΠΆΠ½ΠΎΠΉ ΡΠΎΡΠΌΡ, ΠΏΠ΅ΡΠ²ΠΎΠ½Π°ΡΠ°Π»ΡΠ½ΠΎ Π·Π°Π΄ΡΠΌΠ°Π»ΡΡ ΠΎ 3D ΠΏΡΠΈΠ½ΡΠ΅ΡΠ΅. Π Π΄Π°ΠΆΠ΅ Π½Π°ΡΠ°Π» Π΅Π³ΠΎ Π΄Π΅Π»Π°ΡΡ. ΠΠΎ ΠΏΠΎΡΠΈΡΠ°Π» ΡΠΎΡΡΠΌΡ ΠΈ ΠΎΡΠ΅Π½ΠΈΠ² ΡΠΊΠΎΡΠΎΡΡΡ ΡΠ°Π±ΠΎΡΡ 3D ΠΏΡΠΈΠ½ΡΠ΅ΡΠ°, ΠΊΠ°ΡΠ΅ΡΡΠ²ΠΎ ΠΈ ΡΠΎΡΠ½ΠΎΡΡΡ ΡΠ΅Π·ΡΠ»ΡΡΠ°ΡΠ°, ΠΏΡΠΎΡΠ΅Π½Ρ Π±ΡΠ°ΠΊΠ° ΠΈ ΠΊΠΎΠ½ΡΡΡΡΠΊΡΠΈΠΎΠ½Π½ΡΠ΅ ΡΠ²ΠΎΠΉΡΡΠ²Π° ΡΠ΅ΡΠΌΠΎΠΏΠ»Π°ΡΡΠΌΠ°ΡΡΡ, ΠΏΠΎΠ½ΡΠ», ΡΠΎ ΡΡΠΎ Π½Π΅ Π±ΠΎΠ»Π΅Π΅ ΡΠ΅ΠΌ ΠΈΠ³ΡΡΡΠΊΠ°.
ΠΠ°ΠΊΠ°Π· Π½Π° ΠΊΠΎΠΌΠΏΠ»Π΅ΠΊΡΡΡΡΠΈΠ΅ ΠΈΠ· ΠΠΈΡΠ°Ρ ΠΏΡΠΈΡΠ΅Π» Π·Π° ΠΌΠ΅ΡΡΡ. Π ΡΠΆΠ΅ ΡΠ΅ΡΠ΅Π· 2 Π½Π΅Π΄Π΅Π»ΠΈ ΡΡΠ°Π½ΠΎΠΊ ΡΠ°Π±ΠΎΡΠ°Π» Ρ ΡΠΏΡΠ°Π²Π»Π΅Π½ΠΈΠ΅ΠΌ ΠΎΡ LinuxCNC. Π‘ΠΎΠ±ΠΈΡΠ°Π» ΠΈΠ· Π²ΡΡΠΊΠΎΠΉ ΡΠΈΠ³Π½ΠΈ, ΡΡΠΎ Π±ΡΠ»Π° ΠΏΠΎΠ΄ ΡΡΠΊΠΎΠΉ, ΠΏΠΎΡΠΊΠΎΠ»ΡΠΊΡ Ρ ΠΎΡΠ΅Π»ΠΎΡΡ ΠΏΠΎΠ±ΡΡΡΡΠ΅Π΅ (ΠΏΡΠΎΡΠΈΠ»Ρ + ΡΠΏΠΈΠ»ΡΠΊΠΈ). Π‘ΠΎΠ±ΠΈΡΠ°Π»ΡΡ ΠΏΠΎΡΠΎΠΌ ΠΏΠ΅ΡΠ΅Π΄Π΅Π»Π°ΡΡ, Π½ΠΎ, ΠΊΠ°ΠΊ ΠΎΠΊΠ°Π·Π°Π»ΠΎΡΡ, ΡΡΠ°Π½ΠΎΠΊ ΠΏΠΎΠ»ΡΡΠΈΠ»ΡΡ Π΄ΠΎΡΡΠ°ΡΠΎΡΠ½ΠΎ ΠΆΠ΅ΡΡΠΊΠΈΠΉ, ΠΈ Π³Π°ΠΉΠΊΠΈ Π½Π° ΡΠΏΠΈΠ»ΡΠΊΠ°Ρ Π½Π΅ ΠΏΡΠΈΡΠ»ΠΎΡΡ ΠΏΠΎΠ΄ΡΡΠ³ΠΈΠ²Π°ΡΡ Π½ΠΈ ΡΠ°Π·Ρ. Π’Π°ΠΊ ΡΡΠΎ ΠΊΠΎΠ½ΡΡΡΡΠΊΡΠΈΡ ΠΎΡΡΠ°Π»Π°ΡΡ Π±Π΅Π· ΠΈΠ·ΠΌΠ΅Π½Π΅Π½ΠΈΠΉ.
ΠΠ°ΡΠ°Π»ΡΠ½Π°Ρ ΡΠΊΡΠΏΠ»ΡΠ°ΡΠ°ΡΠΈΡ ΡΡΠ°Π½ΠΊΠ° ΠΏΠΎΠΊΠ°Π·Π°Π»Π° ΡΡΠΎ:
- ΠΡΠΏΠΎΠ»ΡΠ·ΠΎΠ²Π°ΡΡ Π² ΠΊΠ°ΡΠ΅ΡΡΠ²Π΅ ΡΠΏΠΈΠ½Π΄Π΅Π»Ρ Π±ΠΎΡΠΌΠ°ΡΠΈΠ½ΠΊΡ βchina nonameβ Π½Π° 220V Π½Π΅ Π»ΡΡΡΠ°Ρ ΠΈΠ΄Π΅Ρ. ΠΠ΅ΡΠ΅Π³ΡΠ΅Π²Π°Π΅ΡΡΡ ΠΈ ΠΆΡΡΠΊΠΎ Π³ΡΠΎΠΌΠΊΠΎ ΡΠ°Π±ΠΎΡΠ°Π΅Ρ. ΠΠΎΠΊΠΎΠ²ΠΎΠΉ Π»ΡΡΡ ΡΡΠ΅Π·Ρ (ΠΏΠΎΠ΄ΡΠΈΠΏΠ½ΠΈΠΊΠΎΠ²?) ΠΎΡΡΡΠ°Π΅ΡΡΡ ΡΡΠΊΠ°ΠΌΠΈ.
- ΠΠΎΡΠΌΠ°ΡΠΈΠ½ΠΊΠ° Proxon ΡΠ°Π±ΠΎΡΠ°Π΅Ρ ΡΠΈΡ ΠΎ. ΠΡΡΡ Π½Π΅ ΠΎΡΡΡΠΈΠΌ. ΠΠΎ ΠΏΠ΅ΡΠ΅Π³ΡΠ΅Π²Π°Π΅ΡΡΡ ΠΈ Π²ΡΠΊΠ»ΡΡΠ°ΡΡΡ ΡΠ΅ΡΠ΅Π· 5 ΠΌΠΈΠ½ΡΡ.
- ΠΠΎΠΌΠΏΡΡΡΠ΅Ρ, Π²Π·ΡΡΡΠΉ Π½Π° Π²ΡΠ΅ΠΌΡ, Ρ LPT Π΄Π²ΡΠ½Π°ΠΏΡΠ°Π²Π»Π΅Π½Π½ΡΠΌ ΠΏΠΎΡΡΠΎΠΌ β Π½Π΅ ΡΠ΄ΠΎΠ±Π΅Π½. ΠΠ·ΡΡ Π½Π° Π²ΡΠ΅ΠΌΡ (Π½Π°ΠΉΡΠΈ PCI-LPT ΠΎΠΊΠ°Π·Π°Π»ΠΎΡΡ ΠΏΡΠΎΠ±Π»Π΅ΠΌΠΎΠΉ). ΠΠ°Π½ΠΈΠΌΠ°Π΅Ρ ΠΌΠ΅ΡΡΠΎ. Π Π²ΠΎΠΎΠ±ΡΠ΅..
ΠΠΎΡΠ»Π΅ ΠΏΠ΅ΡΠ²ΠΎΠ½Π°ΡΠ°Π»ΡΠ½ΠΎΠΉ ΡΠΊΡΠΏΠ»ΡΠ°ΡΠ°ΡΠΈΠΈ Π·Π°ΠΊΠ°Π·Π°Π» ΡΠΏΠΈΠ½Π΄Π΅Π»Ρ Ρ Π²ΠΎΠ΄ΡΠ½ΡΠΌ ΠΎΡ Π»Π°ΠΆΠ΄Π΅Π½ΠΈΠ΅ΠΌ ΠΈ ΡΠ΅ΡΠΈΠ» ΡΠ΄Π΅Π»Π°ΡΡ ΠΊΠΎΠ½ΡΡΠΎΠ»Π»Π΅Ρ Π΄Π»Ρ Π°Π²ΡΠΎΠ½ΠΎΠΌΠ½ΠΎΠΉ ΡΠ°Π±ΠΎΡΡ Π½Π° ΡΠ°ΠΌΠΎΠΌ Π΄Π΅ΡΠ΅Π²ΠΎΠΌ Π²Π°ΡΠΈΠ°Π½ΡΠ΅ STM32F103, ΠΏΡΠΎΠ΄Π°Π²Π°Π΅ΠΌΠΎΠΌ Π² ΠΊΠΎΠΌΠΏΠ»Π΅ΠΊΡΠ΅ Ρ 320×240 LCD ΡΠΊΡΠ°Π½ΠΎΠΌ.
ΠΠΎΡΠ΅ΠΌΡ Π½Π°ΡΠΎΠ΄ Π΄ΠΎ ΡΠΈΡ ΠΏΠΎΡ ΡΠΏΠΎΡΠ½ΠΎ ΠΌΡΡΠ°Π΅Ρ 8-ΠΈ ΡΠ°Π·ΡΡΠ΄Π½ΡΠ΅ ATMega Π΄Π»Ρ ΠΎΡΠ½ΠΎΡΠΈΡΠ΅Π»ΡΠ½ΠΎ ΡΠ»ΠΎΠΆΠ½ΡΡ Π·Π°Π΄Π°Ρ, Π΄Π° Π΅ΡΠ΅ ΡΠ΅ΡΠ΅Π· Arduino Π΄Π»Ρ ΠΌΠ΅Π½Ρ Π·Π°Π³Π°Π΄ΠΊΠ°. ΠΠ°Π²Π΅ΡΠ½ΠΎΠ΅ Π»ΡΠ±ΡΡ ΡΡΡΠ΄Π½ΠΎΡΡΠΈ.
Π Π°Π·ΡΠ°Π±ΠΎΡΠΊΠ° ΠΊΠΎΠ½ΡΡΠΎΠ»Π»Π΅ΡΠ°
ΠΡΠΎΠ³ΡΠ°ΠΌΠΌΡ ΡΠΎΠ·Π΄Π°Π²Π°Π» ΠΏΠΎΡΠ»Π΅ Π²Π΄ΡΠΌΡΠΈΠ²ΠΎΠ³ΠΎ ΠΏΡΠΎΡΠΌΠΎΡΡΠ° ΠΈΡΡ ΠΎΠ΄Π½ΠΈΠΊΠΎΠ² LinuxCNC ΠΈ gbrl. ΠΠ΄Π½Π°ΠΊΠΎ Π½ΠΈ ΡΠ΅, Π½ΠΈ ΡΠ΅ ΠΈΡΡ ΠΎΠ΄Π½ΠΈΠΊΠΈ ΡΠ°ΡΡΠ΅ΡΠ° ΡΡΠ°Π΅ΠΊΡΠΎΡΠΈΠΈ Π½Π΅ Π²Π·ΡΠ». ΠΠ°Ρ ΠΎΡΠ΅Π»ΠΎΡΡ ΠΏΠΎΠΏΡΠΎΠ±ΠΎΠ²Π°ΡΡ Π½Π°ΠΏΠΈΡΠ°ΡΡ ΠΌΠΎΠ΄ΡΠ»Ρ ΡΠ°ΡΡΠ΅ΡΠ° Π±Π΅Π· ΠΈΡΠΏΠΎΠ»ΡΠ·ΠΎΠ²Π°Π½ΠΈΡ float. ΠΡΠΊΠ»ΡΡΠΈΡΠ΅Π»ΡΠ½ΠΎ Π½Π° 32-Ρ ΡΠ°Π·ΡΡΠ΄Π½ΠΎΠΉ Π°ΡΠΈΡΠΌΠ΅ΡΠΈΠΊΠ΅.
Π Π΅Π·ΡΠ»ΡΡΠ°Ρ ΠΌΠ΅Π½Ρ ΡΡΡΡΠ°ΠΈΠ²Π°Π΅Ρ Π΄Π»Ρ Π²ΡΠ΅Ρ ΡΠ΅ΠΆΠΈΠΌΠΎΠ² ΡΠΊΡΠΏΠ»ΡΠ°ΡΠ°ΡΠΈΠΈ ΠΈ ΠΏΡΠΎΡΠΈΠ²ΠΊΡ Π½Π΅ ΡΡΠΎΠ³Π°Π» ΡΠΆΠ΅ Π΄Π°Π²Π½ΠΎ.
Π‘ΠΊΠΎΡΠΎΡΡΡ ΠΌΠ°ΠΊΡΠΈΠΌΠ°Π»ΡΠ½Π°Ρ, ΠΏΠΎΠ΄ΠΎΠ±ΡΠ°Π½Π½Π°Ρ ΡΠΊΡΠΏΠ΅ΡΠΈΠΌΠ΅Π½ΡΠ°Π»ΡΠ½ΠΎ: X:2000ΠΌΠΌ/ΠΌΠΈΠ½ Y:1600 Z:700 (1600 step/mm. ΡΠ΅ΠΆΠΈΠΌ 1/8).
ΠΠΎ ΠΎΠ³ΡΠ°Π½ΠΈΡΠ΅Π½Π° Π½Π΅ ΡΠ΅ΡΡΡΡΠ°ΠΌΠΈ ΠΊΠΎΠ½ΡΡΠΎΠ»Π»Π΅ΡΠ°. ΠΡΠΎΡΡΠΎ Π²ΡΡΠ΅ ΡΠΆΠ΅ ΠΌΠ΅ΡΠ·ΠΊΠΈΠΉ Π·Π²ΡΠΊ ΠΏΡΠΎΠΏΡΡΠΊΠ° ΡΠ°Π³ΠΎΠ² Π΄Π°ΠΆΠ΅ ΠΏΡΡΠΌΡΡ ΡΡΠ°ΡΡΠΊΠ°Ρ ΠΏΠΎ Π²ΠΎΠ·Π΄ΡΡ Ρ. ΠΡΠ΄ΠΆΠ΅ΡΠ½Π°Ρ ΠΊΠΈΡΠ°ΠΉΡΠΊΠ°Ρ ΠΏΠ»Π°ΡΠ° ΡΠΏΡΠ°Π²Π»Π΅Π½ΠΈΡ ΡΠ°Π³ΠΎΠ²ΠΈΠΊΠ°ΠΌΠΈ Π½Π° TB6560 Π½Π΅ ΡΠ°ΠΌΡΠΉ Π»ΡΡΡΠΈΠΉ Π²Π°ΡΠΈΠ°Π½Ρ.
Π€Π°ΠΊΡΠΈΡΠ΅ΡΠΊΠΈ ΡΠΊΠΎΡΠΎΡΡΡ ΠΏΠΎ Π΄Π΅ΡΠ΅Π²Ρ (Π±ΡΠΊ, 5ΠΌΠΌ Π·Π°Π³Π»ΡΠ±Π»Π΅Π½ΠΈΡ,d=1ΠΌΠΌ ΡΡΠ΅Π·Π°, ΡΠ°Π³ 0.15ΠΌΠΌ) Π±ΠΎΠ»ΡΡΠ΅ 1200 ΠΌΠΌ Π½Π΅ ΡΡΠ°Π²Π»Ρ. ΠΠΎΠ·ΡΠ°ΡΡΠ°Π΅Ρ Π²Π΅ΡΠΎΡΡΠ½ΠΎΡΡΡ ΠΏΠΎΠ»ΠΎΠΌΠΊΠΈ ΡΡΠ΅Π·Ρ.
Π ΡΠ΅Π·ΡΠ»ΡΡΠ°ΡΠ΅ ΠΏΠΎΠ»ΡΡΠΈΠ»ΡΡ ΠΊΠΎΠ½ΡΡΠΎΠ»Π»Π΅Ρ ΡΠΎ ΡΠ»Π΅Π΄ΡΡΡΠΈΠΌ ΡΡΠ½ΠΊΡΠΈΠΎΠ½Π°Π»ΠΎΠΌ:
- ΠΠΎΠ΄ΠΊΠ»ΡΡΠ΅Π½ΠΈΠ΅ ΠΊ Π²Π½Π΅ΡΠ½Π΅ΠΌΡ ΠΊΠΎΠΌΠΏΡ ΠΊΠ°ΠΊ ΡΡΠ°Π½Π΄Π°ΡΡΠ½ΠΎΠ΅ usb mass storage device (FAT16 Π½Π° SD ΠΊΠ°ΡΡΠ΅). Π Π°Π±ΠΎΡΠ° Ρ ΡΠ°ΠΉΠ»Π°ΠΌΠΈ ΡΡΠ°Π½Π΄Π°ΡΡΠ½ΠΎΠ³ΠΎ ΡΠΎΡΠΌΠ°ΡΠ° G-code
- Π£Π΄Π°Π»Π΅Π½ΠΈΠ΅ ΡΠ°ΠΉΠ»ΠΎΠ² ΡΠ΅ΡΠ΅Π· ΠΏΠΎΠ»ΡΠ·ΠΎΠ²Π°ΡΠ΅Π»ΡΡΠΊΠΈΠΉ ΠΈΠ½ΡΠ΅ΡΡΠ΅ΠΉΡ ΠΊΠΎΠ½ΡΡΠΎΠ»Π»Π΅ΡΠ°.
- ΠΡΠΎΡΠΌΠΎΡΡ ΡΡΠ°Π΅ΠΊΡΠΎΡΠΈΠΈ ΠΏΠΎ Π²ΡΠ±ΡΠ°Π½Π½ΠΎΠΌΡ ΡΠ°ΠΉΠ»Ρ (Π½Π°ΡΠΊΠΎΠ»ΡΠΊΠΎ ΠΏΠΎΠ·Π²ΠΎΠ»ΡΠ΅Ρ ΡΠΊΡΠ°Π½ 640×320) ΠΈ ΡΠ°ΡΡΠ΅Ρ Π²ΡΠ΅ΠΌΠ΅Π½ΠΈ Π²ΡΠΏΠΎΠ»Π½Π΅Π½ΠΈΡ. Π€Π°ΠΊΡΠΈΡΠ΅ΡΠΊΠΈ ΡΠΌΡΠ»ΡΡΠΈΡ Π²ΡΠΏΠΎΠ»Π½Π΅Π½ΠΈΡ Ρ ΡΡΠΌΠΌΠΈΡΠΎΠ²Π°Π½ΠΈΠ΅ΠΌ Π²ΡΠ΅ΠΌΠ΅Π½ΠΈ.
- ΠΡΠΎΡΠΌΠΎΡΡ ΡΠΎΠ΄Π΅ΡΠΆΠΈΠΌΠΎΠ³ΠΎ ΡΠ°ΠΉΠ»ΠΎΠ² Π² ΡΠ΅ΡΡΠΎΠ²ΠΎΠΌ Π²ΠΈΠ΄Π΅.
- Π Π΅ΠΆΠΈΠΌ ΡΡΡΠ½ΠΎΠ³ΠΎ ΡΠΏΡΠ°Π²Π»Π΅Π½ΠΈΡ Ρ ΠΊΠ»Π°Π²ΠΈΠ°ΡΡΡΡ (ΠΏΠ΅ΡΠ΅ΠΌΠ΅ΡΠ΅Π½ΠΈΠ΅ ΠΈ Π²ΡΡΡΠ°Π²Π»Π΅Π½ΠΈΡ Β«0Β»).
- ΠΠ°ΠΏΡΡΠΊ Π²ΡΠΏΠΎΠ»Π½Π΅Π½ΠΈΡ Π·Π°Π΄Π°Π½ΠΈΡ ΠΏΠΎ Π²ΡΠ±ΡΠ°Π½Π½ΠΎΠΌΡ ΡΠ°ΠΉΠ»Ρ (G-code).
- ΠΡΠΈΠΎΡΡΠ°Π½ΠΎΠ²/ΠΏΡΠΎΠ΄ΠΎΠ»ΠΆΠΈΡΡ Π²ΡΠΏΠΎΠ»Π½Π΅Π½ΠΈΠ΅. (ΠΈΠ½ΠΎΠ³Π΄Π° ΠΏΠΎΠ»Π΅Π·Π½ΠΎ).
- ΠΠ²Π°ΡΠΈΠΉΠ½ΡΠΉ ΠΏΡΠΎΠ³ΡΠ°ΠΌΠΌΠ½ΡΠΉ ΡΡΠΎΠΏ.
ΠΠΎΠ½ΡΡΠΎΠ»Π»Π΅Ρ ΠΏΠΎΠ΄ΠΊΠ»ΡΡΠ°ΡΡΡ ΠΊ ΠΏΠ»Π°ΡΠ΅ ΡΠΏΡΠ°Π²Π»Π΅Π½ΠΈΡ ΡΠ°Π³ΠΎΠ²ΠΈΠΊΠ°ΠΌΠΈ ΡΠ΅ΡΠ΅Π· ΡΠΎΡ ΠΆΠ΅ ΡΠ°Π·ΡΠ΅ΠΌ LPT. Π’.Π΅. ΠΎΠ½ Π²ΡΠΏΠΎΠ»Π½ΡΠ΅Ρ ΡΠΎΠ»Ρ ΡΠΏΡΠ°Π²Π»ΡΡΡΠ΅Π³ΠΎ ΠΊΠΎΠΌΠΏΡΡΡΠ΅ΡΠ° Ρ LinuxCNC/Mach4 ΠΈ Π²Π·Π°ΠΈΠΌΠΎΠ·Π°ΠΌΠ΅Π½ΡΠ΅ΠΌ Ρ Π½ΠΈΠΌ.
ΠΠΎΡΠ»Π΅ ΡΠ²ΠΎΡΡΠ΅ΡΠΊΠΈΡ
ΡΠΊΡΠΏΠ΅ΡΠΈΠΌΠ΅Π½ΡΠΎΠ² ΠΏΠΎ Π²ΡΡΠ΅Π·Π°Π½ΠΈΡ ΡΠΎΠ±ΡΡΠ²Π΅Π½Π½ΠΎΡΡΡΠ½ΠΎ Π½Π°ΡΠΈΡΠΎΠ²Π°Π½Π½ΡΡ
ΡΠ΅Π»ΡΠ΅ΡΠΎΠ² Π½Π° Π΄Π΅ΡΠ΅Π²Π΅, ΠΈ ΡΠΊΡΠΏΠ΅ΡΠΈΠΌΠ΅Π½ΡΠΎΠ² Ρ Π½Π°ΡΡΡΠΎΠΉΠΊΠ°ΠΌΠΈ ΡΡΠΊΠΎΡΠ΅Π½ΠΈΠΉ Π² ΠΏΡΠΎΠ³ΡΠ°ΠΌΠΌΠ΅, Π·Π°Ρ
ΠΎΡΠ΅Π» Π΄ΠΎΠΏΠΎΠ»Π½ΠΈΡΠ΅Π»ΡΠ½ΠΎ Π΅ΡΠ΅ ΠΈ ΡΠ½ΠΊΠΎΠ΄Π΅ΡΡ Π½Π° ΠΎΡΡΡ
. ΠΠ°ΠΊ ΡΠ°Π· Π½Π° e-bay Π½Π°ΡΠ΅Π» ΠΎΡΠ½ΠΎΡΠΈΡΠ΅Π»ΡΠ½ΠΎ Π΄Π΅ΡΠ΅Π²ΡΠ΅ ΠΎΠΏΡΠΈΡΠ΅ΡΠΊΠΈ ΡΠΊΠΎΠ΄Π΅ΡΡ (1/512), ΡΠ°Π³ Π΄Π΅Π»Π΅Π½ΠΈΡ ΠΊΠΎΡΠΎΡΡΡ
Π΄Π»Ρ ΠΌΠΎΠΈΡ
Π¨ΠΠ Π±ΡΠ» 5/512= 0.0098ΠΌΠΌ.
ΠΡΡΠ°ΡΠΈ, ΠΈΡΠΏΠΎΠ»ΡΠ·ΠΎΠ²Π°Π½ΠΈΠ΅ ΠΎΠΏΡΠΈΡΠ΅ΡΠΊΠΈΡ
ΡΠ½ΠΊΠΎΠ΄Π΅ΡΠΎΠ² Π²ΡΡΠΎΠΊΠΎΠ³ΠΎ ΡΠ°Π·ΡΠ΅ΡΠ΅Π½ΠΈΡ, Π±Π΅Π· Π°ΠΏΠΏΠ°ΡΠ°ΡΠ½ΠΎΠΉ ΡΡ
Π΅ΠΌΡ ΡΠ°Π±ΠΎΡΡ Ρ Π½ΠΈΠΌΠΈ (Π² STM32 ΠΎΠ½Π° Π΅ΡΡΡ) β Π±Π΅ΡΡΠΌΡΡΠ»Π΅Π½Π½ΠΎ. ΠΠΈ ΠΎΠ±ΡΠ°Π±ΠΎΡΠΊΠ° ΠΏΠΎ ΠΏΡΠ΅ΡΡΠ²Π°Π½ΠΈΡ, Π½ΠΈ, ΡΠ΅ΠΌ Π±ΠΎΠ»Π΅Π΅, ΠΏΡΠΎΠ³ΡΠ°ΠΌΠΌΠ½ΡΠΉ ΠΎΠΏΡΠΎΡ Π½ΠΈΠΊΠΎΠ³Π΄Π° Π½Π΅ ΡΠΏΡΠ°Π²ΡΡΡΡ Ρ Β«Π΄ΡΠ΅Π±Π΅Π·Π³ΠΎΠΌΒ» (ΡΡΠΎ Π³ΠΎΠ²ΠΎΡΡ Π΄Π»Ρ Π»ΡΠ±ΠΈΡΠ΅Π»Π΅ΠΉ ATMega).
Π ΠΏΠ΅ΡΠ²ΡΡ ΠΎΡΠ΅ΡΠ΅Π΄Ρ, Ρ Ρ
ΠΎΡΠ΅Π» Π΄Π»Ρ ΡΠ»Π΅Π΄ΡΡΡΠΈΡ
Π·Π°Π΄Π°Ρ:
- Π ΡΡΠ½ΠΎΠ΅ ΠΏΠΎΠ·ΠΈΡΠΈΠΎΠ½ΠΈΡΠΎΠ²Π°Π½ΠΈΠ΅ Π½Π° ΡΡΠΎΠ»Π΅ Ρ Π²ΡΡΠΎΠΊΠΎΠΉ ΡΠΎΡΠ½ΠΎΡΡΡΡ.
- ΠΠΎΠ½ΡΡΠΎΠ»Ρ ΠΏΡΠΎΠΏΡΡΠΊΠ° ΡΠ°Π³ΠΎΠ² Ρ ΠΊΠΎΠ½ΡΡΠΎΠ»Π΅ΠΌ ΠΎΡΠΊΠ»ΠΎΠ½Π΅Π½ΠΈΠ΅ ΡΡΠ°Π΅ΠΊΡΠΎΡΠΈΠΈ ΠΎΡ ΡΠ°ΡΡΠ΅ΡΠ½ΠΎΠΉ.
ΠΠ΄Π½Π°ΠΊΠΎ, Π½Π°ΡΠ΅Π» ΠΈΠΌ Π΅ΡΠ΅ ΠΎΠ΄Π½ΠΎ ΠΏΡΠΈΠΌΠ΅Π½Π΅Π½ΠΈΠ΅, ΠΏΡΡΡΡ ΠΈ Π² Π΄ΠΎΠ²ΠΎΠ»ΡΠ½ΠΎ ΡΠ·ΠΊΠΎΠΉ Π·Π°Π΄Π°ΡΠ΅.
ΠΠ°ΠΌΠ΅ΡΠΈΠ», ΡΡΠΎ ΠΏΡΠΈ Π²ΡΡΠ΅Π·Π°Π½ΠΈΠΈ ΡΠ΅Π»ΡΠ΅ΡΠ°, ΠΏΡΠΈ Π·Π°Π΄Π°Π½ΠΈΠΈ ΡΡΠΊΠΎΡΠ΅Π½ΠΈΡ ΠΏΠΎ Z Π±ΠΎΠ»ΡΡΠ΅ ΠΎΠΏΡΠ΅Π΄Π΅Π»Π΅Π½Π½ΠΎΠΉ Π²Π΅Π»ΠΈΡΠΈΠ½Ρ, ΠΎΡΡ Z Π½Π°ΡΠΈΠ½Π°Π΅Ρ ΠΌΠ΅Π΄Π»Π΅Π½Π½ΠΎ, Π½ΠΎ ΡΠ²Π΅ΡΠ΅Π½Π½ΠΎ ΠΏΠΎΠ»Π·ΡΠΈ Π²Π½ΠΈΠ·. ΠΠΎ, Π²ΡΠ΅ΠΌΡ Π²ΡΡΠ΅Π·Π°Π½ΠΈΡ ΡΠ΅Π»ΡΠ΅ΡΠ° ΠΏΡΠΈ ΡΡΠΎΠΌ ΡΡΠΊΠΎΡΠ΅Π½ΠΈΠΈ Π½Π° 20% ΠΌΠ΅Π½ΡΡΠ΅. ΠΠΎ ΠΎΠΊΠΎΠ½ΡΠ°Π½ΠΈΡ Π²ΡΡΠ΅Π·Π°Π½ΠΈΡ ΡΠ΅Π»ΡΠ΅ΡΠ° 17×20 ΡΠΌ Ρ ΡΠ°Π³ΠΎΠΌ 0.1ΠΌΠΌ ΡΡΠ΅Π·Π° ΠΌΠΎΠΆΠ΅Ρ ΡΠΉΡΠΈ Π²Π½ΠΈΠ· Π½Π° 1-2 ΠΌΠΌ ΠΎΡ ΡΠ°ΡΡΠ΅ΡΠ½ΠΎΠΉ ΡΡΠ°Π΅ΠΊΡΠΎΡΠΈΠΈ.
ΠΠ½Π°Π»ΠΈΠ· ΡΠΈΡΡΠ°ΡΠΈΠΈ Π² Π΄ΠΈΠ½Π°ΠΌΠΈΠΊΠ΅ ΠΏΠΎ ΡΠ½ΠΊΠΎΠ΄Π΅ΡΠ°ΠΌ, ΠΏΠΎΠΊΠ°Π·Π°Π», ΡΡΠΎ ΠΏΡΠΈ ΠΏΠΎΠ΄ΡΠ΅ΠΌΠ΅ ΡΡΠ΅Π·Ρ ΠΈΠ½ΠΎΠ³Π΄Π° ΡΠ΅ΡΡΠ΅ΡΡΡ 1-2 ΡΠ°Π³Π°.
ΠΡΠΎΡΡΠΎΠΉ Π°Π»Π³ΠΎΡΠΈΡΠΌ ΠΊΠΎΡΡΠ΅ΠΊΡΠΈΠΈ ΡΠ°Π³ΠΎΠ² Ρ ΠΈΡΠΏΠΎΠ»ΡΠ·ΠΎΠ²Π°Π½ΠΈΠ΅ΠΌ ΡΠ½ΠΊΠΎΠ΄Π΅ΡΠ° Π΄Π°Π΅Ρ ΠΎΡΠΊΠ»ΠΎΠ½Π΅Π½ΠΈΠ΅ Π½Π΅ Π±ΠΎΠ»Π΅Π΅ 0.03 ΠΌΠΌ ΠΈ ΠΏΠΎΠ·Π²ΠΎΠ»ΡΠ΅Ρ ΡΠΌΠ΅Π½ΡΡΠΈΡΡ Π²ΡΠ΅ΠΌΡ ΠΎΠ±ΡΠ°Π±ΠΎΡΠΊΠΈ Π½Π° 20%. Π Π΄Π°ΠΆΠ΅ 0.1 ΠΌΠΌ Π²ΡΡΡΡΠΏ Π½Π° Π΄Π΅ΡΠ΅Π²Π΅ Π·Π°ΠΌΠ΅ΡΠΈΡΡ ΡΠ»ΠΎΠΆΠ½ΠΎ.
ΠΠ΄Π΅Π°Π»ΡΠ½ΡΠΌ Π²Π°ΡΠΈΠ°Π½ΡΠΎΠΌ Π΄Π»Ρ Ρ ΠΎΠ±Π±ΠΈΠΉΠ½ΡΡ ΡΠ΅Π»Π΅ΠΉ ΠΏΠΎΡΡΠΈΡΠ°Π» Π½Π°ΡΡΠΎΠ»ΡΠ½ΡΠΉ Π²Π°ΡΠΈΠ°Π½Ρ Ρ ΠΏΠΎΠ»Π΅ΠΌ ΡΡΡΡ Π±ΠΎΠ»ΡΡΠ΅ ΡΠ΅ΠΌ A4. Π Π΄ΠΎ ΡΠΈΡ ΠΏΠΎΡ ΠΌΠ½Π΅ ΡΡΠΎΠ³ΠΎ Ρ Π²Π°ΡΠ°Π΅Ρ.
ΠΠΎΠ΄Π²ΠΈΠΆΠ½ΡΠΉ ΡΡΠΎΠ»
ΠΠ»Ρ ΠΌΠ΅Π½Ρ Π΄ΠΎ ΡΠΈΡ ΠΏΠΎΡ ΠΎΡΡΠ°Π΅ΡΡΡ Π·Π°Π³Π°Π΄ΠΊΠΎΠΉ, ΠΏΠΎΡΠ΅ΠΌΡ Π²ΡΠ΅ Π²ΡΠ±ΠΈΡΠ°ΡΡ Π΄Π»Ρ Π½Π°ΡΡΠΎΠ»ΡΠ½ΡΡ ΡΡΠ°Π½ΠΊΠΎΠ² ΠΊΠΎΠ½ΡΡΡΡΠΊΡΠΈΡ Ρ ΠΏΠΎΠ΄Π²ΠΈΠΆΠ½ΡΠΌ ΠΏΠΎΡΡΠ°Π»ΠΎΠΌ. ΠΠ΄ΠΈΠ½ΡΡΠ²Π΅Π½Π½ΠΎΠ΅ Π΅Ρ ΠΏΡΠ΅ΠΈΠΌΡΡΠ΅ΡΡΠ²ΠΎ β Π²ΠΎΠ·ΠΌΠΎΠΆΠ½ΠΎΡΡΡ ΠΎΠ±ΡΠ°Π±ΠΎΡΠ°ΡΡ ΠΏΠΎ ΡΠ°ΡΡΡΠΌ ΠΎΡΠ΅Π½Ρ Π΄Π»ΠΈΠ½Π½ΡΡ Π΄ΠΎΡΠΊΡ ΠΈΠ»ΠΈ, Π΅ΡΠ»ΠΈ ΠΏΡΠΈΡ ΠΎΠ΄ΠΈΡΡΡ ΡΠ΅Π³ΡΠ»ΡΡΠ½ΠΎ ΠΎΠ±ΡΠ°Π±Π°ΡΡΠ²Π°ΡΡ ΠΌΠ°ΡΠ΅ΡΠΈΠ°Π» Π²Π΅Ρ ΠΊΠΎΡΠΎΡΠΎΠ³ΠΎ Π±ΠΎΠ»ΡΡΠ΅ Π²Π΅ΡΠ° ΠΏΠΎΡΡΠ°Π»Π°.
ΠΠ° Π²ΡΠ΅ Π²ΡΠ΅ΠΌΡ ΡΠΊΡΠΏΠ»ΡΠ°ΡΠ°ΡΠΈΠΈ Π½ΠΈ ΡΠ°Π·Ρ Π½Π΅ Π±ΡΠ»ΠΎ Π½Π΅ΠΎΠ±Ρ ΠΎΠ΄ΠΈΠΌΠΎΡΡΡ Π²ΡΠΏΠΈΠ»ΠΈΡΡ ΠΏΠΎ ΡΠ°ΡΡΡΠΌ ΡΠ΅Π»ΡΠ΅Ρ Π½Π° 3-Ρ ΠΌΠ΅ΡΡΠΎΠ²ΠΎΠΉ Π΄ΠΎΡΠΊΠ΅ ΠΈΠ»ΠΈ ΡΠ΄Π΅Π»Π°ΡΡ Π³ΡΠ°Π²ΠΈΡΠΎΠ²ΠΊΡ Π½Π° ΠΊΠ°ΠΌΠ΅Π½Π½ΠΎΠΉ ΠΏΠ»ΠΈΡΠ΅.
ΠΠΎΠ΄Π²ΠΈΠΆΠ½ΡΠΉ ΡΡΠΎΠ» ΠΎΠ±Π»Π°Π΄Π°Π΅Ρ ΡΠ»Π΅Π΄ΡΡΡΠΈΠΌΠΈ ΠΏΡΠ΅ΠΈΠΌΡΡΠ΅ΡΡΠ²Π°ΠΌΠΈ Π΄Π»Ρ Π½Π°ΡΡΠΎΠ»ΡΠ½ΡΡ ΡΡΠ°Π½ΠΊΠΎΠ²:
- ΠΠΎΠ½ΡΡΡΡΠΊΡΠΈΡ ΠΏΡΠΎΡΠ΅ ΠΈ, Π² ΠΎΠ±ΡΠ΅ΠΌ ΡΠ»ΡΡΠ°Π΅, ΠΊΠΎΠ½ΡΡΡΡΠΊΡΠΈΡ Π±ΠΎΠ»Π΅Π΅ ΠΆΠ΅ΡΡΠΊΠ°Ρ.
- ΠΠ° Π½Π΅ΠΏΠΎΠ΄Π²ΠΈΠΆΠ½ΡΠΉ ΠΏΠΎΡΡΠ°Π» Π½Π°Π²Π΅ΡΠΈΠ²Π°ΡΡΡΡ Π²ΡΠ΅ ΠΏΠΎΡΡΠΎΡ Π° (Π±Π»ΠΎΠΊΠΈ ΠΏΠΈΡΠ°Π½ΠΈΡ, ΠΏΠ»Π°ΡΡ ΠΈ ΠΏΡ.) ΠΈ ΡΡΠ°Π½ΠΎΠΊ ΠΏΠΎΠ»ΡΡΠ°Π΅ΡΡΡ ΠΊΠΎΠΌΠΏΠ°ΠΊΡΠ½Π΅Π΅ ΠΈ ΡΠ΄ΠΎΠ±Π½Π΅Π΅ Π΄Π»Ρ ΠΏΠ΅ΡΠ΅Π½ΠΎΡΠΊΠΈ.
- ΠΠ°ΡΡΠ° ΡΡΠΎΠ»Π° ΠΈ ΠΊΡΡΠΊΠ° ΡΠΈΠΏΠΈΡΠ½ΠΎΠ³ΠΎ ΠΌΠ°ΡΠ΅ΡΠΈΠ°Π»Π° Π΄Π»Ρ ΠΎΠ±ΡΠ°Π±ΠΎΡΠΊΠΈ ΡΡΡΠ΅ΡΡΠ²Π΅Π½Π½ΠΎ Π½ΠΈΠΆΠ΅ ΡΠ΅ΠΌ ΠΌΠ°ΡΡΠ° ΠΏΠΎΡΡΠ°Π»Π° ΠΈ ΡΠΏΠΈΠ½Π΄Π΅Π»Ρ.
- ΠΡΠ°ΠΊΡΠΈΡΠ΅ΡΠΊΠΈ ΠΈΡΡΠ΅Π·Π°Π΅Ρ ΠΏΡΠΎΠ±Π»Π΅ΠΌΠ° Ρ ΠΊΠ°Π±Π΅Π»ΡΠΌΠΈ ΠΈ ΡΠ»Π°Π½Π³Π°ΠΌΠΈ Π²ΠΎΠ΄ΡΠ½ΠΎΠ³ΠΎ ΠΎΡ Π»Π°ΠΆΠ΄Π΅Π½ΠΈΡ ΡΠΏΠΈΠ½Π΄Π΅Π»Ρ.
Π¨ΠΏΠΈΠ½Π΄Π΅Π»Ρ
Π₯ΠΎΡΠ΅Π» Π±Ρ Π·Π°ΠΌΠ΅ΡΠΈΡΡ, ΡΡΠΎ Π΄Π°Π½Π½ΡΠΉ ΡΡΠ°Π½ΠΎΠΊ Π½Π΅ Π΄Π»Ρ ΡΠΈΠ»ΠΎΠ²ΠΎΠΉ ΠΎΠ±ΡΠ°Π±ΠΎΡΠΊΠΈ. Π§ΠΠ£ ΡΡΠ°Π½ΠΎΠΊ Π΄Π»Ρ ΡΠΈΠ»ΠΎΠ²ΠΎΠΉ ΠΎΠ±ΡΠ°Π±ΠΎΡΠΊΠΈ ΠΏΡΠΎΡΠ΅ Π²ΡΠ΅Π³ΠΎ ΡΠ΄Π΅Π»Π°ΡΡ Π½Π° Π±Π°Π·Π΅ ΠΎΠ±ΡΡΠ½ΠΎΠ³ΠΎ ΡΡΠ΅Π·Π΅ΡΠ½ΠΎΠ³ΠΎ ΡΡΠ°Π½ΠΊΠ°.
ΠΠ° ΠΌΠΎΠΉ Π²Π·Π³Π»ΡΠ΄, ΡΡΠ°Π½ΠΎΠΊ Π΄Π»Ρ ΡΠΈΠ»ΠΎΠ²ΠΎΠΉ ΠΎΠ±ΡΠ°Π±ΠΎΡΠΊΠΈ ΠΌΠ΅ΡΠ°Π»Π»Π° ΠΈ ΡΡΠ°Π½ΠΎΠΊ Ρ Π²ΡΡΠΎΠΊΠΎ ΠΎΠ±ΠΎΡΠΎΡΠΈΡΡΡΠΌ ΡΠΏΠΈΠ½Π΄Π΅Π»Π΅ΠΌ Π΄Π»Ρ ΠΎΠ±ΡΠ°Π±ΠΎΡΠΊΠΈ Π΄Π΅ΡΠ΅Π²Π°/ΠΏΠ»Π°ΡΡΠΌΠ°ΡΡ β ΡΡΠΎ ΡΠΎΠ²Π΅ΡΡΠ΅Π½Π½ΠΎ ΡΠ°Π·Π½ΡΠ΅ ΡΠΈΠΏΡ ΠΎΠ±ΠΎΡΡΠ΄ΠΎΠ²Π°Π½ΠΈΡ.
Π‘ΠΎΠ·Π΄Π°ΡΡ Π² Π΄ΠΎΠΌΠ°ΡΠ½ΠΈΡ ΡΡΠ»ΠΎΠ²ΠΈΡ ΡΠ½ΠΈΠ²Π΅ΡΡΠ°Π»ΡΠ½ΡΠΉ ΡΡΠ°Π½ΠΎΠΊ ΠΊΠ°ΠΊ ΠΌΠΈΠ½ΠΈΠΌΡΠΌ Π½Π΅ ΠΈΠΌΠ΅Π΅Ρ ΡΠΌΡΡΠ»Π°.
ΠΡΠ±ΠΎΡ ΡΠΏΠΈΠ½Π΄Π΅Π»Ρ Π΄Π»Ρ ΡΡΠ°Π½ΠΊΠ° Ρ Π΄Π°Π½Π½ΡΠΌ ΡΠΈΠΏΠΎΠΌ Π¨ΠΠ ΠΈ Π½Π°ΠΏΡΠ°Π²Π»ΡΡΡΠΈΠΌΠΈ Ρ Π»ΠΈΠ½Π΅ΠΉΠ½ΡΠΌΠΈ ΠΏΠΎΠ΄ΡΠΈΠΏΠ½ΠΈΠΊΠ°ΠΌΠΈ ΠΎΠ΄Π½ΠΎΠ·Π½Π°ΡΠ΅Π½. ΠΡΠΎ Π²ΡΡΠΎΠΊΠΎ ΠΎΠ±ΠΎΡΠΎΡΠΈΡΡΡΠΉ ΡΠΏΠΈΠ½Π΄Π΅Π»Ρ.
ΠΠ»Ρ ΡΠΈΠΏΠΈΡΠ½ΠΎΠ³ΠΎ Π²ΡΡΠΎΠΊΠΎ ΠΎΠ±ΠΎΡΠΎΡΠΈΡΡΠΎΠ³ΠΎ ΡΠΏΠΈΠ½Π΄Π΅Π»Ρ (20000 ΠΎΠ±/ΠΌΠΈΠ½) ΡΡΠ΅Π·Π΅ΡΠΎΠ²ΠΊΠ° ΡΠ²Π΅ΡΠ½ΡΡ
ΠΌΠ΅ΡΠ°Π»Π»ΠΎΠ² (ΠΏΡΠΎ ΡΡΠ°Π»Ρ Π΄Π°ΠΆΠ΅ ΡΠ΅ΡΠΈ Π½Π΅ ΠΈΠ΄Π΅Ρ) β ΡΡΠΎ ΡΠΊΡΡΡΠ΅ΠΌΠ°Π»ΡΠ½ΡΠΉ ΡΠ΅ΠΆΠΈΠΌ Π΄Π»Ρ ΡΠΏΠΈΠ½Π΄Π΅Π»Ρ. ΠΡ, ΡΠ°Π·Π²Π΅ ΡΡΠΎ ΠΎΡΠ΅Π½Ρ Π½Π°Π΄ΠΎ ΠΈ ΡΠΎΠ³Π΄Π° ΡΡΠ΅ΠΌ ΠΏΠΎ 0.3 ΠΌΠΌ Π·Π° ΠΏΡΠΎΡ
ΠΎΠ΄ Ρ ΠΏΠΎΠ»ΠΈΠ²ΠΎΠΌ ΠΠ.
Π¨ΠΏΠΈΠ½Π΄Π΅Π»Ρ Π΄Π»Ρ ΡΡΠ°Π½ΠΊΠ° ΡΠ΅ΠΊΠΎΠΌΠ΅Π½Π΄ΠΎΠ²Π°Π» Π±Ρ Ρ Π²ΠΎΠ΄ΡΠ½ΡΠΌ ΠΎΡ
Π»Π°ΠΆΠ΄Π΅Π½ΠΈΠ΅ΠΌ. Π‘ Π½ΠΈΠΌ ΡΠ»ΡΡΠ½ΠΎ Π²ΠΎ Π²ΡΠ΅ΠΌΡ ΡΠ°Π±ΠΎΡΡ ΡΠΎΠ»ΡΠΊΠΎ Β«ΠΏΠ΅Π½ΠΈΠ΅Β» ΡΠ°Π³ΠΎΠ²ΡΡ
Π΄Π²ΠΈΠ³Π°ΡΠ΅Π»Π΅ΠΉ ΠΈ Π±ΡΠ»ΡΠΊΠ°Π½ΡΠ΅ Π°ΠΊΠ²Π°ΡΠΈΡΠΌΠ½ΠΎΠ³ΠΎ Π½Π°ΡΠΎΡΠ° Π² ΠΊΠΎΠ½ΡΡΡΠ΅ ΠΎΡ
Π»Π°ΠΆΠ΄Π΅Π½ΠΈΡ.
Π ΠΏΠ΅ΡΠ²ΡΡ ΠΎΡΠ΅ΡΠ΅Π΄Ρ Ρ ΠΌΠ΅Π½Ρ ΡΡΠ»Π° ΠΏΡΠΎΠ±Π»Π΅ΠΌΠ° ΠΊΠΎΡΠΏΡΡΠΎΠ². ΠΡΠ±ΠΎΠΉ ΡΠΎΡΠΌΡ ΠΊΠΎΡΠΏΡΡ ΡΡΠ΅Π·Π΅ΡΡΠ΅ΡΡΡ ΠΈΠ· Β«ΠΎΡΠ³ΡΡΠ΅ΠΊΠ»Π°Β» ΠΈ ΠΏΠΎ ΠΈΠ΄Π΅Π°Π»ΡΠ½ΠΎ ΠΏΠΎ Π³Π»Π°Π΄ΠΊΠΈΠΌ ΡΡΠ΅Π·Π°ΠΌ ΡΠΊΠ»Π΅ΠΈΠ²Π°Π΅ΡΡΡ ΡΠ°ΡΡΠ²ΠΎΡΠΈΡΠ΅Π»Π΅ΠΌ.
Π‘ΡΠ΅ΠΊΠ»ΠΎΡΠ΅ΠΊΡΡΠΎΠ»ΠΈΡ ΠΎΡΠΊΠ°Π·Π°Π»ΡΡ ΡΠ½ΠΈΠ²Π΅ΡΡΠ°Π»ΡΠ½ΡΠΌ ΠΌΠ°ΡΠ΅ΡΠΈΠ°Π»ΠΎΠΌ. Π’ΠΎΡΠ½ΠΎΡΡΡ ΡΡΠ°Π½ΠΊΠ° ΠΏΠΎΠ·Π²ΠΎΠ»ΡΠ΅Ρ Π²ΡΡΠ΅Π·Π°ΡΡ ΠΏΠΎΡΠ°Π΄ΠΎΡΠ½ΠΎΠ΅ ΠΌΠ΅ΡΡΠΎ ΠΏΠΎΠ΄ ΠΏΠΎΠ΄ΡΠΈΠΏΠ½ΠΈΠΊ, Π² ΠΊΠΎΡΠΎΡΠΎΠ΅ ΠΎΠ½ Ρ ΠΎΠ»ΠΎΠ΄Π½ΡΠΉ Π·Π°ΠΉΠ΄Π΅Ρ, ΠΊΠ°ΠΊ ΠΏΠΎΠ»ΠΎΠΆΠ΅Π½ΠΎ Ρ Π»Π΅Π³ΠΊΠΈΠΌ Π½Π°ΡΡΠ³ΠΎΠΌ, Π° ΠΏΠΎΡΠ»Π΅ ΡΠΆΠ΅ Π½Π΅ Π²ΡΡΠ°ΡΠΈΡΡ. Π¨Π΅ΡΡΠ΅ΡΠ½ΠΈ ΠΈΠ· ΡΠ΅ΠΊΡΡΠΎΠ»ΠΈΡΠ° ΠΎΡΠ»ΠΈΡΠ½ΠΎ Π²ΡΡΠ΅Π·Π°ΡΡΡΡ Ρ ΡΠ΅ΡΡΠ½ΡΠΌ ΡΠ²ΠΎΠ»ΡΠ²Π΅Π½ΡΠ½ΡΠΌ ΠΏΡΠΎΡΠΈΠ»Π΅ΠΌ.
ΠΠ±ΡΠ°Π±ΠΎΡΠΊΠ° Π΄Π΅ΡΠ΅Π²Π° (ΡΠ΅Π»ΡΠ΅ΡΡ ΠΈ ΠΏΡ.) β ΡΠΈΡΠΎΠΊΠΈΠΉ ΠΏΡΠΎΡΡΠΎΡ Π΄Π»Ρ ΡΠ΅Π°Π»ΠΈΠ·Π°ΡΠΈΠΈ ΡΠ²ΠΎΠΈΡ ΡΠ²ΠΎΡΡΠ΅ΡΠΊΠΈΡ ΠΏΠΎΡΡΠ²ΠΎΠ² ΠΈΠ»ΠΈ, ΠΊΠ°ΠΊ ΠΌΠΈΠ½ΠΈΠΌΡΠΌ, Π΄Π»Ρ ΡΠ΅Π°Π»ΠΈΠ·Π°ΡΠΈΠΈ ΡΡΠΆΠΈΡ ΠΏΠΎΡΡΠ²ΠΎΠ² (Π³ΠΎΡΠΎΠ²ΡΠ΅ ΠΌΠΎΠ΄Π΅Π»ΠΈ).
ΠΠΎΡ ΡΠΎΠ»ΡΠΊΠΎ ΡΠ²Π΅Π»ΠΈΡΠΊΡ Π½Π΅ ΠΏΡΠΎΠ±ΠΎΠ²Π°Π». ΠΠ΅Π³Π΄Π΅ ΠΎΠΏΠΎΠΊΠΈ ΠΏΡΠΎΠΊΠ°Π»ΠΈΠ²Π°ΡΡ/ΠΏΠ»Π°Π²ΠΈΡΡ/Π»ΠΈΡΡ. Π₯ΠΎΡΡ Π±ΡΡΡΠΎΠΊ ΡΠ²Π΅Π»ΠΈΡΠ½ΠΎΠ³ΠΎ Π²ΠΎΡΠΊΠ° ΠΆΠ΄Π΅Ρ ΡΠ²ΠΎΠ΅Π³ΠΎ ΡΠ°ΡΠ°.
ΠΠΎΠ½ΡΡΠΎΠ»Π»Π΅Ρ Π΄Π»Ρ ΡΡΠ°Π½ΠΊΠ° Π»Π΅Π³ΠΊΠΎ ΡΠΌΠΎΠΆΠ΅Ρ ΡΠΎΠ±ΡΠ°ΡΡ ΠΈ Π΄ΠΎΠΌΠ°ΡΠ½ΠΈΠΉ ΠΌΠ°ΡΡΠ΅Ρ. ΠΠ°Π΄Π°ΡΡ Π½ΡΠΆΠ½ΡΠ΅ ΠΏΠ°ΡΠ°ΠΌΠ΅ΡΡΡ Π½Π΅ ΡΠ»ΠΎΠΆΠ½ΠΎ, Π΄ΠΎΡΡΠ°ΡΠΎΡΠ½ΠΎ ΡΡΠ΅ΡΡΡ Π½Π΅ΡΠΊΠΎΠ»ΡΠΊΠΎ Π½ΡΠ°Π½ΡΠΎΠ².
Π‘ΠΎΠ²Π΅ΡΡ ΠΏΠΎ ΡΠ±ΠΎΡΠΊΠ΅ ΠΊΠΎΠ½ΡΡΠΎΠ»Π»Π΅ΡΠΎΠ² Π΄Π»Ρ Π§ΠΠ£ ΡΡΠ°Π½ΠΊΠΎΠ²
ΠΠ΅Π· ΠΏΡΠ°Π²ΠΈΠ»ΡΠ½ΠΎΠ³ΠΎ Π²ΡΠ±ΠΎΡΠ° ΠΊΠΎΠ½ΡΡΠΎΠ»Π»Π΅ΡΠ° Π΄Π»Ρ ΡΡΠ°Π½ΠΊΠ° Π½Π΅ ΡΠ΄Π°ΡΡΡΡ ΡΠΎΠ±ΡΠ°ΡΡ ΡΠ°ΠΌ ΠΊΠΎΠ½ΡΡΠΎΠ»Π»Π΅Ρ Π΄Π»Ρ Π§ΠΠ£ Π½Π° Atmega8 16au ΡΠ²ΠΎΠΈΠΌΠΈ ΡΡΠΊΠ°ΠΌΠΈ. ΠΡΠΈ ΡΡΡΡΠΎΠΉΡΡΠ²Π° Π΄Π΅Π»ΡΡΡΡ Π½Π° Π΄Π²Π΅ ΡΠ°Π·Π½ΠΎΠ²ΠΈΠ΄Π½ΠΎΡΡΠΈ:
- ΠΠ½ΠΎΠ³ΠΎΠΊΠ°Π½Π°Π»ΡΠ½ΡΠ΅. Π‘ΡΠ΄Π° Π²Ρ ΠΎΠ΄ΡΡ 3 ΠΈ 4-ΠΎΡΠ΅Π²ΡΠ΅ ΠΊΠΎΠ½ΡΡΠΎΠ»Π»Π΅ΡΡ Π΄Π»Ρ ΡΠ°Π³ΠΎΠ²ΡΡ Π΄Π²ΠΈΠ³Π°ΡΠ΅Π»Π΅ΠΉ.
- ΠΠ΄Π½ΠΎΠΊΠ°Π½Π°Π»ΡΠ½ΡΠ΅.
ΠΠ΅Π±ΠΎΠ»ΡΡΠΈΠ΅ ΡΠ°ΡΠΎΠ²ΡΠ΅ Π΄Π²ΠΈΠ³Π°ΡΠ΅Π»ΠΈ Π½Π°ΠΈΠ±ΠΎΠ»Π΅Π΅ ΡΡΡΠ΅ΠΊΡΠΈΠ²Π½ΠΎ ΡΠΏΡΠ°Π²Π»ΡΡΡΡΡ ΠΌΠ½ΠΎΠ³ΠΎΠΊΠ°Π½Π°Π»ΡΠ½ΡΠΌΠΈ ΠΊΠΎΠ½ΡΡΠΎΠ»Π»Π΅ΡΠ°ΠΌΠΈ. Π‘ΡΠ°Π½Π΄Π°ΡΡΠ½ΡΠ΅ ΡΠΈΠΏΠΎΡΠ°Π·ΠΌΠ΅ΡΡ Π² Π΄Π°Π½Π½ΠΎΠΌ ΡΠ»ΡΡΠ°Π΅ β 42, Π»ΠΈΠ±ΠΎ 57 ΠΌΠΈΠ»Π»ΠΈΠΌΠ΅ΡΡΠΎΠ². ΠΡΠΎ ΠΎΡΠ»ΠΈΡΠ½ΡΠΉ Π²Π°ΡΠΈΠ°Π½Ρ Π΄Π»Ρ ΡΠ°ΠΌΠΎΡΡΠΎΡΡΠ΅Π»ΡΠ½ΠΎΠΉ ΡΠ±ΠΎΡΠΊΠΈ Π§ΠΠ£ ΡΡΠ°Π½ΠΊΠΎΠ², Ρ ΠΊΠΎΡΠΎΡΡΡ ΡΠ°Π±ΠΎΡΠ΅Π΅ ΠΏΠΎΠ»Π΅ ΠΈΠΌΠ΅Π΅Ρ ΡΠ°Π·ΠΌΠ΅Ρ Π΄ΠΎ 1 ΠΌΠ΅ΡΡΠ°.
ΠΡΠ»ΠΈ ΠΆΠ΅ ΡΠ°ΠΌΠΎΡΡΠΎΡΡΠ΅Π»ΡΠ½ΠΎ ΡΠΎΠ±ΠΈΡΠ°Π΅ΡΡΡ ΡΡΠ°Π½ΠΎΠΊ Β Π½Π° ΠΌΠΈΠΊΡΠΎΠΊΠΎΠ½ΡΡΠΎΠ»Π»Π΅ΡΠ΅ Ρ ΠΏΠΎΠ»Π΅ΠΌ Π±ΠΎΠ»Π΅Π΅ ΡΠ΅ΠΌ Π² 1 ΠΌΠ΅ΡΡ β Π½Π°Π΄ΠΎ ΠΈΡΠΏΠΎΠ»ΡΠ·ΠΎΠ²Π°ΡΡ Π΄Π²ΠΈΠ³Π°ΡΠ΅Π»ΠΈ, Π²ΡΠΏΡΡΠΊΠ°ΡΡΠΈΠ΅ΡΡ Π² ΡΠΈΠΏΠΎΡΠ°Π·ΠΌΠ΅ΡΠ°Ρ Π΄ΠΎ 86 ΠΌΠΈΠ»Π»ΠΈΠΌΠ΅ΡΡΠΎΠ². Π Π΄Π°Π½Π½ΠΎΠΌ ΡΠ»ΡΡΠ°Π΅ ΡΠ΅ΠΊΠΎΠΌΠ΅Π½Π΄ΡΠ΅ΡΡΡ ΠΎΡΠ³Π°Π½ΠΈΠ·ΠΎΠ²ΡΠ²Π°ΡΡ ΡΠΏΡΠ°Π²Π»Π΅Π½ΠΈΠ΅ ΠΌΠΎΡΠ½ΡΠΌΠΈ ΠΎΠ΄Π½ΠΎΠΊΠ°Π½Π°Π»ΡΠ½ΡΠΌΠΈ Π΄ΡΠ°ΠΉΠ²Π΅ΡΠ°ΠΌΠΈ, Ρ ΡΠΎΠΊΠΎΠΌ ΡΠΏΡΠ°Π²Π»Π΅Π½ΠΈΡ ΠΎΡ 4,2 Π ΠΈ Π²ΡΡΠ΅.
ΠΠΎΠ½ΡΡΠΎΠ»Π»Π΅ΡΡ ΡΠΎ ΡΠΏΠ΅ΡΠΈΠ°Π»ΡΠ½ΡΠΌΠΈ ΠΌΠΈΠΊΡΠΎΡΡ Π΅ΠΌΠ°ΠΌΠΈ-Π΄ΡΠ°ΠΉΠ²Π΅ΡΠ°ΠΌΠΈ ΠΏΠΎΠ»ΡΡΠΈΠ»ΠΈ ΡΠΈΡΠΎΠΊΠΎΠ΅ ΡΠ°ΡΠΏΡΠΎΡΡΡΠ°Π½Π΅Π½ΠΈΠ΅ Π² ΡΠ»ΡΡΠ°Π΅ Π½Π΅ΠΎΠ±Ρ ΠΎΠ΄ΠΈΠΌΠΎΡΡΠΈ ΠΎΡΠ³Π°Π½ΠΈΠ·ΠΎΠ²Π°ΡΡ ΠΊΠΎΠ½ΡΡΠΎΠ»Ρ ΡΠ°Π±ΠΎΡΡ ΡΡΠ°Π½ΠΊΠΎΠ² Ρ ΡΡΠ΅Π·Π΅ΡΠ°ΠΌΠΈ Π½Π°ΡΡΠΎΠ»ΡΠ½ΠΎΠ³ΠΎ ΡΠΈΠΏΠ°. ΠΠΏΡΠΈΠΌΠ°Π»ΡΠ½ΡΠΌ Π²Π°ΡΠΈΠ°Π½ΡΠΎΠΌ Π±ΡΠ΄Π΅Ρ ΠΌΠΈΠΊΡΠΎΡΡ Π΅ΠΌΠ°, ΠΎΠ±ΠΎΠ·Π½Π°ΡΠ°Π΅ΠΌΠ°Ρ ΠΊΠ°ΠΊ TB6560 ΠΈΠ»ΠΈ A3977. Π£ ΡΡΠΎΠ³ΠΎ ΠΈΠ·Π΄Π΅Π»ΠΈΡ Π²Π½ΡΡΡΠΈ Π΅ΡΡΡ ΠΊΠΎΠ½ΡΡΠΎΠ»Π»Π΅Ρ, ΡΠΏΠΎΡΠΎΠ±ΡΡΠ²ΡΡΡΠΈΠΉ ΡΠΎΡΠΌΠΈΡΠΎΠ²Π°Π½ΠΈΡ ΠΏΡΠ°Π²ΠΈΠ»ΡΠ½ΠΎΠΉ ΡΠΈΠ½ΡΡΠΎΠΈΠ΄Ρ Π΄Π»Ρ ΡΠ΅ΠΆΠΈΠΌΠΎΠ², ΠΏΠΎΠ΄Π΄Π΅ΡΠΆΠΈΠ²Π°ΡΡΠΈΡ ΡΠ°Π·Π½ΡΠ΅ ΠΏΠΎΠ»ΡΡΠ°Π³ΠΈ. Π’ΠΎΠΊΠΈ ΠΎΠ±ΠΌΠΎΡΠΊΠΈ ΠΌΠΎΠ³ΡΡ Π±ΡΡΡ ΡΡΡΠ°Π½ΠΎΠ²Π»Π΅Π½Ρ ΠΏΡΠΎΠ³ΡΠ°ΠΌΠΌΠ½ΡΠΌ ΡΠΏΠΎΡΠΎΠ±ΠΎΠΌ. ΠΡΠΈ ΠΌΠΈΠΊΡΠΎΠΊΠΎΠ½ΡΡΠΎΠ»Π»Π΅ΡΠ°Ρ Π΄ΠΎΠ±ΠΈΡΡΡΡ ΡΠ΅Π·ΡΠ»ΡΡΠ°ΡΠ° ΠΏΡΠΎΡΡΠΎ.
Π£ΠΏΡΠ°Π²Π»Π΅Π½ΠΈΠ΅
ΠΠΎΠ½ΡΡΠΎΠ»Π»Π΅ΡΠΎΠΌ Π»Π΅Π³ΠΊΠΎ ΡΠΏΡΠ°Π²Π»ΡΡΡ, ΠΈΡΠΏΠΎΠ»ΡΠ·ΡΡ ΡΠΏΠ΅ΡΠΈΠ°Π»ΠΈΠ·ΠΈΡΠΎΠ²Π°Π½Π½ΠΎΠ΅ ΠΏΡΠΎΠ³ΡΠ°ΠΌΠΌΠ½ΠΎΠ΅ ΠΎΠ±ΠΎΡΡΠ΄ΠΎΠ²Π°Π½ΠΈΠ΅, ΡΡΡΠ°Π½ΠΎΠ²Π»Π΅Π½Π½ΠΎΠ΅ Π½Π° ΠΠ. ΠΠ»Π°Π²Π½ΠΎΠ΅, ΡΡΠΎΠ±Ρ Ρ ΡΠ°ΠΌΠΎΠ³ΠΎ ΠΊΠΎΠΌΠΏΡΡΡΠ΅ΡΠ° ΠΏΠ°ΠΌΡΡΡ Π±ΡΠ»Π° ΠΌΠΈΠ½ΠΈΠΌΡΠΌ 1 ΠΠ, Π° ΠΏΡΠΎΡΠ΅ΡΡΠΎΡ β Π½Π΅ ΠΌΠ΅Π½Π΅Π΅ 1 GHz.
ΠΠΎΠΆΠ½ΠΎ ΠΈΡΠΏΠΎΠ»ΡΠ·ΠΎΠ²Π°ΡΡ Π½ΠΎΡΡΠ±ΡΠΊΠΈ, Π½ΠΎ ΡΡΠ°ΡΠΈΠΎΠ½Π°ΡΠ½ΡΠ΅ ΠΊΠΎΠΌΠΏΡΡΡΠ΅ΡΡ Π² ΡΡΠΎΠΌ ΠΏΠ»Π°Π½Π΅ Π΄Π°ΡΡ Π»ΡΡΡΠΈΠ΅ ΡΠ΅Π·ΡΠ»ΡΡΠ°ΡΡ. Π ΠΎΠ±Ρ ΠΎΠ΄ΡΡΡΡ Π³ΠΎΡΠ°Π·Π΄ΠΎ Π΄Π΅ΡΠ΅Π²Π»Π΅. ΠΠΎΠΌΠΏΡΡΡΠ΅Ρ ΠΌΠΎΠΆΠ½ΠΎ ΠΈΡΠΏΠΎΠ»ΡΠ·ΠΎΠ²Π°ΡΡ Π΄Π»Ρ ΡΠ΅ΡΠ΅Π½ΠΈΡ Π΄ΡΡΠ³ΠΈΡ Π·Π°Π΄Π°Ρ, ΠΊΠΎΠ³Π΄Π° ΡΡΠ°Π½ΠΊΠΈ Π½Π΅ ΡΡΠ΅Π±ΡΡΡ ΡΠΏΡΠ°Π²Π»Π΅Π½ΠΈΡ. Π₯ΠΎΡΠΎΡΠΎ, Π΅ΡΠ»ΠΈ Π΅ΡΡΡ Π²ΠΎΠ·ΠΌΠΎΠΆΠ½ΠΎΡΡΡ ΠΎΠΏΡΠΈΠΌΠΈΠ·ΠΈΡΠΎΠ²Π°ΡΡ ΡΠΈΡΡΠ΅ΠΌΡ ΠΏΠ΅ΡΠ΅Π΄ Π½Π°ΡΠ°Π»ΠΎΠΌ ΡΠ°Π±ΠΎΡΡ.
ΠΠ°ΡΠ°Π»Π»Π΅Π»ΡΠ½ΡΠΉ ΠΏΠΎΡΡ LPT β Π²ΠΎΡ ΠΊΠ°ΠΊΠ°Ρ Π΄Π΅ΡΠ°Π»Ρ ΠΏΠΎΠΌΠΎΠ³Π°Π΅Ρ ΠΎΡΠ³Π°Π½ΠΈΠ·ΠΎΠ²Π°ΡΡ ΠΏΠΎΠ΄ΠΊΠ»ΡΡΠ΅Π½ΠΈΠ΅. ΠΡΠ»ΠΈ ΠΊΠΎΠ½ΡΡΠΎΠ»Π»Π΅Ρ ΠΈΠΌΠ΅Π΅Ρ ΠΏΠΎΡΡ USB, ΡΠΎ ΠΈΡΠΏΠΎΠ»ΡΠ·ΡΠ΅ΡΡΡ ΡΠ°Π·ΡΠ΅ΠΌ ΡΠΎΠΎΡΠ²Π΅ΡΡΡΠ²ΡΡΡΠ΅ΠΉ ΡΠΎΡΠΌΡ. ΠΡΠΈ ΡΡΠΎΠΌ Π²ΡΠΏΡΡΠΊΠ°Π΅ΡΡΡ Π²ΡΠ΅ Π±ΠΎΠ»ΡΡΠ΅ ΠΈ Π±ΠΎΠ»ΡΡΠ΅ ΠΊΠΎΠΌΠΏΡΡΡΠ΅ΡΠΎΠ², Ρ ΠΊΠΎΡΠΎΡΡΡ ΠΏΠ°ΡΠ°Π»Π»Π΅Π»ΡΠ½ΡΠΉ ΠΏΠΎΡΡ ΠΎΡΡΡΡΡΡΠ²ΡΠ΅Ρ.
ΠΠ·Π³ΠΎΡΠΎΠ²Π»Π΅Π½ΠΈΠ΅ ΡΠ°ΠΌΠΎΠ³ΠΎ ΠΏΡΠΎΡΡΠΎΠ³ΠΎ Π²Π°ΡΠΈΠ°Π½ΡΠ° ΡΠΊΠ°Π½Π΅ΡΠ°
ΠΠ΄Π½ΠΎ ΠΈΠ· ΡΠ°ΠΌΡΡ ΠΏΡΠΎΡΡΡΡ ΡΠ΅ΡΠ΅Π½ΠΈΠΉ Π΄Π»Ρ ΡΠ°ΠΌΠΎΠ΄Π΅Π»ΡΠ½ΠΎΠ³ΠΎ ΡΠΎΠ·Π΄Π°Π½ΠΈΡ Π§ΠΠ£ ΡΡΠ°Π½ΠΊΠ° β ΠΈΡΠΏΠΎΠ»ΡΠ·ΠΎΠ²Π°Π½ΠΈΠ΅ Π΄Π΅ΡΠ°Π»Π΅ΠΉ ΠΎΡ Π΄ΡΡΠ³ΠΎΠ³ΠΎ ΠΎΠ±ΠΎΡΡΠ΄ΠΎΠ²Π°Π½ΠΈΡ, ΡΠ½Π°Π±ΠΆΠ΅Π½Π½ΠΎΠ³ΠΎ ΡΠ°ΡΠΎΠ²ΡΠΌΠΈ Π΄Π²ΠΈΠ³Π°ΡΠ΅Π»ΡΠΌΠΈ. Π€ΡΠ½ΠΊΡΠΈΡ ΠΎΡΠ»ΠΈΡΠ½ΠΎ Π²ΡΠΏΠΎΠ»Π½ΡΡΡ ΡΡΠ°ΡΡΠ΅ ΠΏΡΠΈΠ½ΡΠ΅ΡΡ.
ΠΠ΅ΡΠ΅ΠΌ ΡΠ»Π΅Π΄ΡΡΡΠΈΠ΅ Π΄Π΅ΡΠ°Π»ΠΈ, ΠΈΠ·Π²Π»Π΅ΡΠ΅Π½Π½ΡΠ΅ ΠΈΠ· ΠΏΡΠ΅ΠΆΠ½ΠΈΡ ΠΏΡΠΈΠ±ΠΎΡΠΎΠ²:
- Π‘Π°ΠΌΠ° ΠΌΠΈΠΊΡΠΎΡΡ Π΅ΠΌΠ°.
- Π¨Π°Π³ΠΎΠ²ΡΠΉ Π΄Π²ΠΈΠ³Π°ΡΠ΅Π»Ρ.
- ΠΠ°ΡΠ° ΡΡΠ°Π»ΡΠ½ΡΡ ΠΏΡΡΡΠΊΠΎΠ².
ΠΡΠΈ ΡΠΎΠ·Π΄Π°Π½ΠΈΠΈ ΠΊΠΎΡΠΏΡΡΠ° ΠΊΠΎΠ½ΡΡΠΎΠ»Π»Π΅ΡΠ° Π½Π°Π΄ΠΎ Π²Π·ΡΡΡ ΠΈ ΡΡΠ°ΡΡΡ ΠΊΠ°ΡΡΠΎΠ½Π½ΡΡ ΠΊΠΎΡΠΎΠ±ΠΊΡ. ΠΠΎΠΏΡΡΡΠΈΠΌΠΎ ΠΈΡΠΏΠΎΠ»ΡΠ·ΠΎΠ²Π°ΡΡ ΠΊΠΎΡΠΎΠ±ΠΊΠΈ ΠΈΠ· ΡΠ°Π½Π΅ΡΡ ΠΈΠ»ΠΈ ΡΠ΅ΠΊΡΡΠΎΠ»ΠΈΡΠ°, ΠΈΡΡ ΠΎΠ΄Π½ΡΠΉ ΠΌΠ°ΡΠ΅ΡΠΈΠ°Π» Π½Π΅ ΠΈΠΌΠ΅Π΅Ρ Π·Π½Π°ΡΠ΅Π½ΠΈΡ. ΠΠΎ ΠΊΠ°ΡΡΠΎΠ½ ΠΏΡΠΎΡΠ΅ Π²ΡΠ΅Π³ΠΎ ΠΎΠ±ΡΠ°Π±ΠΎΡΠ°ΡΡ, ΠΈΡΠΏΠΎΠ»ΡΠ·ΡΡ ΠΎΠ±ΡΡΠ½ΡΠ΅ Π½ΠΎΠΆΠ½ΠΈΡΡ.
Π‘ΠΏΠΈΡΠΎΠΊ ΠΈΠ½ΡΡΡΡΠΌΠ΅Π½ΡΠΎΠ² Π±ΡΠ΄Π΅Ρ Π²ΡΠ³Π»ΡΠ΄Π΅ΡΡ ΡΠ»Π΅Π΄ΡΡΡΠΈΠΌ ΠΎΠ±ΡΠ°Π·ΠΎΠΌ:
- ΠΠ°ΡΠ»ΡΠ½ΠΈΠΊ Π²ΠΌΠ΅ΡΡΠ΅, Π΄ΠΎΠΏΠΎΠ»Π½Π΅Π½Π½ΡΠΉ ΠΏΡΠΈΠ½Π°Π΄Π»Π΅ΠΆΠ½ΠΎΡΡΡΠΌΠΈ.
- ΠΠΈΡΡΠΎΠ»Π΅Ρ Ρ ΠΊΠ»Π΅Π΅ΠΌ.
- ΠΠΎΠΆΠ½ΠΈΡΠ½ΡΠΉ ΠΈΠ½ΡΡΡΡΠΌΠ΅Π½Ρ.
- ΠΡΡΠ°ΡΠΊΠΈ.
ΠΠ°ΠΊΠΎΠ½Π΅Ρ, ΠΈΠ·Π³ΠΎΡΠΎΠ²Π»Π΅Π½ΠΈΠ΅ ΠΊΠΎΠ½ΡΡΠΎΠ»Π»Π΅ΡΠ° ΠΏΠΎΡΡΠ΅Π±ΡΠ΅Ρ ΡΠ»Π΅Π΄ΡΡΡΠΈΡ Π΄ΠΎΠΏΠΎΠ»Π½ΠΈΡΠ΅Π»ΡΠ½ΡΡ Π΄Π΅ΡΠ°Π»Π΅ΠΉ:
- Π Π°Π·ΡΠ΅ΠΌ Ρ ΠΏΡΠΎΠ²ΠΎΠ΄ΠΎΠΌ, Π΄Π»Ρ ΠΎΡΠ³Π°Π½ΠΈΠ·Π°ΡΠΈΠΈ ΡΠ΄ΠΎΠ±Π½ΠΎΠ³ΠΎ ΠΏΠΎΠ΄ΠΊΠ»ΡΡΠ΅Π½ΠΈΡ.
- Π¦ΠΈΠ»ΠΈΠ½Π΄ΡΠΈΡΠ΅ΡΠΊΠΎΠ΅ Π³Π½Π΅Π·Π΄ΠΎ. Π’Π°ΠΊΠΈΠ΅ ΠΊΠΎΠ½ΡΡΡΡΠΊΡΠΈΠΈ ΠΎΡΠ²Π΅ΡΠ°ΡΡ Π·Π° ΠΏΠΈΡΠ°Π½ΠΈΠ΅ ΡΡΡΡΠΎΠΉΡΡΠ²Π°.
- Π₯ΠΎΠ΄ΠΎΠ²ΡΠΌΠΈ Π²ΠΈΠ½ΡΠ°ΠΌΠΈ ΡΠ»ΡΠΆΠ°Ρ ΡΡΠ΅ΡΠΆΠ½ΠΈ, ΠΈΠΌΠ΅ΡΡΠΈΠ΅ ΠΎΠΏΡΠ΅Π΄Π΅Π»Π΅Π½Π½ΡΡ ΡΠ΅Π·ΡΠ±Ρ.
- ΠΠ°ΠΉΠΊΠ° Ρ ΠΏΠΎΠ΄Ρ ΠΎΠ΄ΡΡΠΈΠΌΠΈ Π΄Π»Ρ Ρ ΠΎΠ΄ΠΎΠ²ΠΎΠ³ΠΎ Π²ΠΈΠ½ΡΠ° ΡΠ°Π·ΠΌΠ΅ΡΠ°ΠΌΠΈ.
- Π¨ΡΡΡΠΏΡ, ΡΠ°ΠΉΠ±Ρ, Π΄ΡΠ΅Π²Π΅ΡΠΈΠ½Π° Π² ΡΠΎΡΠΌΠ΅ ΠΊΡΡΠΊΠΎΠ².
ΠΠ°ΡΠΈΠ½Π°Π΅ΠΌ ΡΠ°Π±ΠΎΡΡ ΠΏΠΎ ΡΠΎΠ·Π΄Π°Π½ΠΈΡ ΡΠ°ΠΌΠΎΠ΄Π΅Π»ΡΠ½ΠΎΠ³ΠΎ ΡΡΠ°Π½ΠΊΠ°
Π¨Π°Π³ΠΎΠ²ΡΠΉ Π΄Π²ΠΈΠ³Π°ΡΠ΅Π»Ρ Π²ΠΌΠ΅ΡΡΠ΅ Ρ ΠΏΠ»Π°ΡΠΎΠΉ Π΄ΠΎΠ»ΠΆΠ½Ρ Π±ΡΡΡ ΠΈΠ·Π²Π»Π΅ΡΠ΅Π½Ρ ΠΈΠ· ΡΡΠ°ΡΡΡ ΡΡΡΡΠΎΠΉΡΡΠ². Π£ ΡΠΊΠ°Π½Π΅ΡΠ° Π΄ΠΎΡΡΠ°ΡΠΎΡΠ½ΠΎ ΡΠ½ΡΡΡ ΡΡΠ΅ΠΊΠ»ΠΎ, Π° Π·Π°ΡΠ΅ΠΌ β Π²ΡΠ²Π΅ΡΠ½ΡΡΡ Π½Π΅ΡΠΊΠΎΠ»ΡΠΊΠΎ Π±ΠΎΠ»ΡΠΎΠ². Π‘Π½ΠΈΠΌΠ°ΡΡ ΠΏΠΎΡΡΠ΅Π±ΡΠ΅ΡΡΡ ΠΈ ΡΡΠ°Π»ΡΠ½ΡΠ΅ ΡΡΠ΅ΡΠΆΠ½ΠΈ, ΠΈΡΠΏΠΎΠ»ΡΠ·ΡΠ΅ΠΌΡΠ΅ Π² Π΄Π°Π»ΡΠ½Π΅ΠΉΡΠ΅ΠΌ, ΡΠΎΠ·Π΄Π°Π²Π°Ρ ΡΠ΅ΡΡΠΎΠ²ΡΠΉ ΠΏΠΎΡΡΠ°Π».
ΠΠΈΠΊΡΠΎΡΡ Π΅ΠΌΠ° ΡΠΏΡΠ°Π²Π»Π΅Π½ΠΈΡ ULN2003 ΡΡΠ°Π½Π΅Ρ ΠΎΠ΄Π½ΠΈΠΌ ΠΈΠ· Π³Π»Π°Π²Π½ΡΡ ΡΠ»Π΅ΠΌΠ΅Π½ΡΠΎΠ². ΠΠΎΠ·ΠΌΠΎΠΆΠ½ΠΎ ΠΎΡΠ΄Π΅Π»ΡΠ½ΠΎΠ΅ ΠΏΡΠΈΠΎΠ±ΡΠ΅ΡΠ΅Π½ΠΈΠ΅ Π΄Π΅ΡΠ°Π»Π΅ΠΉ, Π΅ΡΠ»ΠΈ Π² ΡΠΊΠ°Π½Π΅ΡΠ΅ ΠΈΡΠΏΠΎΠ»ΡΠ·ΡΡΡΡΡ Π΄ΡΡΠ³ΠΈΠ΅ ΡΠ°Π·Π½ΠΎΠ²ΠΈΠ΄Π½ΠΎΡΡΠΈ ΠΌΠΈΠΊΡΠΎΡΡ Π΅ΠΌ. Π ΡΠ»ΡΡΠ°Π΅ Π½Π°Π»ΠΈΡΠΈΡ Π½ΡΠΆΠ½ΠΎΠ³ΠΎ ΡΡΡΡΠΎΠΉΡΡΠ²Π° Π½Π° ΠΏΠ»Π°ΡΠ΅ Π΅Π³ΠΎ Π°ΠΊΠΊΡΡΠ°ΡΠ½ΠΎ Π²ΡΠΏΠ°ΠΈΠ²Π°Π΅ΠΌ. ΠΠΎΡΡΠ΄ΠΎΠΊ Π΄Π΅ΠΉΡΡΠ²ΠΈΠΉ ΠΏΡΠΈ ΡΠ±ΠΎΡΠΊΠ΅ ΠΊΠΎΠ½ΡΡΠΎΠ»Π»Π΅ΡΠ° Π΄Π»Ρ Π§ΠΠ£ Π½Π° Atmega8 16au ΡΠ²ΠΎΠΈΠΌΠΈ ΡΡΠΊΠ°ΠΌΠΈ Π²ΡΠ³Π»ΡΠ΄ΠΈΡ ΡΠ»Π΅Π΄ΡΡΡΠΈΠΌ ΠΎΠ±ΡΠ°Π·ΠΎΠΌ:
- Π‘Π½Π°ΡΠ°Π»Π° ΡΠ°Π·ΠΎΠ³ΡΠ΅Π²Π°Π΅ΠΌ ΠΎΠ»ΠΎΠ²ΠΎ, ΠΈΡΠΏΠΎΠ»ΡΠ·ΡΡ ΠΏΠ°ΡΠ»ΡΠ½ΠΈΠΊ.
- Π£Π΄Π°Π»Π΅Π½ΠΈΠ΅ Π²Π΅ΡΡ Π½Π΅Π³ΠΎ ΡΠ»ΠΎΡ ΠΏΠΎΡΡΠ΅Π±ΡΠ΅Ρ ΠΈΡΠΏΠΎΠ»ΡΠ·ΠΎΠ²Π°Π½ΠΈΡ ΠΎΡΡΠΎΡΠ°.
- ΠΠ΄Π½ΠΈΠΌ ΠΊΠΎΠ½ΡΠΎΠΌ ΠΎΡΠ²Π΅ΡΡΠΊΡ ΡΡΡΠ°Π½Π°Π²Π»ΠΈΠ²Π°Π΅ΠΌ ΠΏΠΎΠ΄ ΠΌΠΈΠΊΡΠΎΡΡ Π΅ΠΌΡ.
- ΠΠ°Π»ΠΎ ΠΏΠ°ΡΠ»ΡΠ½ΠΈΠΊΠ° Π΄ΠΎΠ»ΠΆΠ½ΠΎ ΠΊΠ°ΡΠ°ΡΡΡΡ ΠΊΠ°ΠΆΠ΄ΠΎΠ³ΠΎ Π²ΡΠ²ΠΎΠ΄Π° ΠΌΠΈΠΊΡΠΎΡΡ Π΅ΠΌΡ. ΠΡΠ»ΠΈ ΡΡΠΎ ΡΡΠ»ΠΎΠ²ΠΈΠ΅ ΡΠΎΠ±Π»ΡΠ΄Π°Π΅ΡΡΡ, Π½Π° ΠΈΠ½ΡΡΡΡΠΌΠ΅Π½Ρ ΠΌΠΎΠΆΠ½ΠΎ Π½Π°ΠΆΠΈΠΌΠ°ΡΡ.
ΠΠ°Π»Π΅Π΅ ΠΌΠΈΠΊΡΠΎΡΡ Π΅ΠΌΠ° ΠΏΡΠΈΠΏΠ°ΠΈΠ²Π°Π΅ΡΡΡ Π½Π° ΠΏΠ»Π°ΡΡ, ΡΠΎΠΆΠ΅ Ρ ΠΌΠ°ΠΊΡΠΈΠΌΠ°Π»ΡΠ½ΠΎΠΉ Π°ΠΊΠΊΡΡΠ°ΡΠ½ΠΎΡΡΡΡ. ΠΠ»Ρ ΠΏΠ΅ΡΠ²ΡΡ ΠΏΡΠΎΠ±Π½ΡΡ ΡΠ°Π³ΠΎΠ² ΠΌΠΎΠΆΠ½ΠΎ ΠΈΡΠΏΠΎΠ»ΡΠ·ΠΎΠ²Π°ΡΡ ΠΌΠ°ΠΊΠ΅ΡΡ. ΠΡΠΏΠΎΠ»ΡΠ·ΡΠ΅ΠΌ Π²Π°ΡΠΈΠ°Π½Ρ Ρ Π΄Π²ΡΠΌΡ ΡΠΈΠ½Π°ΠΌΠΈ ΡΠ»Π΅ΠΊΡΡΠΎΠΏΠΈΡΠ°Π½ΠΈΡ. ΠΠ΄Π½Π° ΠΈΠ· Π½ΠΈΡ ΡΠΎΠ΅Π΄ΠΈΠ½ΡΠ΅ΡΡΡ Ρ ΠΏΠΎΠ»ΠΎΠΆΠΈΡΠ΅Π»ΡΠ½ΡΠΌ Π²ΡΠ²ΠΎΠ΄ΠΎΠΌ, Π° Π΄ΡΡΠ³Π°Ρ β Ρ ΠΎΡΡΠΈΡΠ°ΡΠ΅Π»ΡΠ½ΡΠΌ.
ΠΠ° ΡΠ»Π΅Π΄ΡΡΡΠ΅ΠΌ ΡΡΠ°ΠΏΠ΅ ΠΈΠ΄Π΅Ρ ΡΠΎΠ΅Π΄ΠΈΠ½Π΅Π½ΠΈΠ΅ Π²ΡΠ²ΠΎΠ΄Π° Ρ Π²ΡΠΎΡΠΎΠ³ΠΎ ΠΊΠΎΠ½Π½Π΅ΠΊΡΠΎΡΠ° ΠΏΠ°ΡΠ°Π»Π»Π΅Π»ΡΠ½ΠΎΠ³ΠΎ ΠΏΠΎΡΡΠ° Ρ Π²ΡΠ²ΠΎΠ΄ΠΎΠΌ Π² ΡΠ°ΠΌΠΎΠΉ ΠΌΠΈΠΊΡΠΎΡΡ Π΅ΠΌΠ΅. ΠΡΠ²ΠΎΠ΄Ρ Ρ ΠΊΠΎΠ½Π½Π΅ΠΊΡΠΎΡΠ° ΠΈ ΠΌΠΈΠΊΡΠΎΡΡ Π΅ΠΌΡ Π΄ΠΎΠ»ΠΆΠ½Ρ Π±ΡΡΡ ΡΠΎΠ΅Π΄ΠΈΠ½Π΅Π½Ρ ΡΠΎΠΎΡΠ²Π΅ΡΡΡΠ²ΡΡΡΠΈΠΌ ΠΎΠ±ΡΠ°Π·ΠΎΠΌ.
ΠΡΠ»Π΅Π²ΠΎΠΉ Π²ΡΠ²ΠΎΠ΄ ΠΏΡΠΈΡΠΎΠ΅Π΄ΠΈΠ½ΡΠ΅ΡΡΡ ΠΊ ΠΎΡΡΠΈΡΠ°ΡΠ΅Π»ΡΠ½ΠΎΠΉ ΡΠΈΠ½Π΅.
ΠΠ΄ΠΈΠ½ ΠΈΠ· ΠΏΠΎΡΠ»Π΅Π΄Π½ΠΈΡ ΡΡΠ°ΠΏΠΎΠ² β ΠΏΡΠΈΠΏΠ°ΠΉΠΊΠ° ΡΠ°Π³ΠΎΠ²ΠΎΠ³ΠΎ Π΄Π²ΠΈΠ³Π°ΡΠ΅Π»Ρ ΠΊ ΡΡΡΡΠΎΠΉΡΡΠ²Ρ ΡΠΏΡΠ°Π²Π»Π΅Π½ΠΈΡ.
Π₯ΠΎΡΠΎΡΠΎ, Π΅ΡΠ»ΠΈ Π΅ΡΡΡ Π²ΠΎΠ·ΠΌΠΎΠΆΠ½ΠΎΡΡΡ ΠΈΠ·ΡΡΠΈΡΡ Π΄ΠΎΠΊΡΠΌΠ΅Π½ΡΠ°ΡΠΈΡ ΠΎΡ ΠΏΡΠΎΠΈΠ·Π²ΠΎΠ΄ΠΈΡΠ΅Π»Ρ ΡΡΡΡΠΎΠΉΡΡΠ². ΠΡΠ»ΠΈ Π½Π΅Ρ, ΡΠΎ ΠΏΡΠΈΠ΄Π΅ΡΡΡ ΡΠ°ΠΌΠΎΡΡΠΎΡΡΠ΅Π»ΡΠ½ΠΎ ΠΈΡΠΊΠ°ΡΡ ΠΏΠΎΠ΄Ρ ΠΎΠ΄ΡΡΠ΅Π΅ ΡΠ΅ΡΠ΅Π½ΠΈΠ΅.
ΠΡΠΎΠ²ΠΎΠ΄Π° ΡΠ΅ΠΊΠΎΠΌΠ΅Π½Π΄ΡΠ΅ΡΡΡ ΠΏΡΠΈΠΏΠ°ΠΈΠ²Π°ΡΡ ΡΠ°ΠΊ, ΡΡΠΎΠ±Ρ ΠΏΠΎΡΠΎΠΌ ΠΈΡ ΠΌΠΎΠΆΠ½ΠΎ Π±ΡΠ»ΠΎ Π»Π΅Π³ΠΊΠΎ ΡΠΎΠ΅Π΄ΠΈΠ½ΠΈΡΡ Ρ Π·Π°ΠΆΠΈΠΌΠ°ΠΌΠΈ-ΠΊΡΠΎΠΊΠΎΠ΄ΠΈΠ»Π°ΠΌΠΈ. ΠΠ»Π΅ΠΌΠΌΡ Ρ Π²ΠΈΠ½ΡΠΎΠ²ΡΠΌΠΈ ΡΠΎΠ΅Π΄ΠΈΠ½Π΅Π½ΠΈΡΠΌΠΈ β ΠΏΠΎΠ΄Ρ ΠΎΠ΄ΡΡΠΈΠ΅ Π΄Π»Ρ ΡΠ΅ΡΠ΅Π½ΠΈΡ Π·Π°Π΄Π°ΡΠΈ ΡΠ΅ΡΠ΅Π½ΠΈΡ. ΠΠ°ΠΊ ΠΈ Π»ΡΠ±ΡΠ΅ Π΄ΡΡΠ³ΠΈΠ΅ ΠΏΠΎΠ΄ΠΎΠ±Π½ΡΠ΅ Π΄Π΅ΡΠ°Π»ΠΈ.
ΠΡΠΎΠ²ΠΎΠ΄Π° ΡΠΎΠ΅Π΄ΠΈΠ½ΡΡΡΡΡ Ρ Π²ΡΠ²ΠΎΠ΄Π°ΠΌΠΈ. ΠΠ°ΠΊΠΎΠ½Π΅Ρ, ΠΎΠ΄ΠΈΠ½ ΠΈΠ· Π½ΠΈΡ ΡΠΎΠ΅Π΄ΠΈΠ½ΡΠ΅ΡΡΡ Ρ ΠΏΠΎΠ»ΠΎΠΆΠΈΡΠ΅Π»ΡΠ½ΠΎΠΉ ΡΠΈΠ½ΠΎΠΉ.
Π¨ΠΈΠ½Ρ ΠΈ Π³Π½Π΅Π·Π΄Π° ΡΠ»Π΅ΠΊΡΡΠΎΠΏΠΈΡΠ°Π½ΠΈΡ Π½ΡΠΆΠ½ΠΎ ΡΠΎΠ΅Π΄ΠΈΠ½ΠΈΡΡ.
Π’Π΅ΡΠΌΠΎΠΊΠ»Π΅ΠΉ ΠΈΠ· ΠΏΠΈΡΡΠΎΠ»Π΅ΡΠ° ΠΏΠΎΠΌΠΎΠΆΠ΅Ρ Π·Π°ΠΊΡΠ΅ΠΏΠΈΡΡ Π΄Π΅ΡΠ°Π»ΠΈ, ΡΡΠΎΠ±Ρ ΠΎΠ½ΠΈ Π½Π΅ ΠΎΡΠΊΠ°Π»ΡΠ²Π°Π»ΠΈΡΡ.
ΠΡΠΏΠΎΠ»ΡΠ·ΡΠ΅ΠΌ Turbo CNC β ΠΏΡΠΎΠ³ΡΠ°ΠΌΠΌΡ Π΄Π»Ρ ΡΠΏΡΠ°Π²Π»Π΅Π½ΠΈΡ
ΠΠ Turbo CNC ΡΠΎΡΠ½ΠΎ Π±ΡΠ΄Π΅Ρ ΡΠ°Π±ΠΎΡΠ°ΡΡ Ρ ΠΌΠΈΠΊΡΠΎΠΊΠΎΠ½ΡΡΠΎΠ»Π»Π΅ΡΠΎΠΌ, ΠΊΠΎΡΠΎΡΡΠΉ ΠΈΡΠΏΠΎΠ»ΡΠ·ΡΠ΅Ρ ΠΌΠΈΠΊΡΠΎΡΡ Π΅ΠΌΡ ULN2003.
- ΠΡΠΏΠΎΠ»ΡΠ·ΡΠ΅ΠΌ ΡΠΏΠ΅ΡΠΈΠ°Π»ΠΈΠ·ΠΈΡΠΎΠ²Π°Π½Π½ΡΠΉ ΡΠ°ΠΉΡ, ΠΎΡΠΊΡΠ΄Π° ΠΌΠΎΠΆΠ½ΠΎ ΡΠΊΠ°ΡΠ°ΡΡ ΠΏΡΠΎΠ³ΡΠ°ΠΌΠΌΠ½ΠΎΠ΅ ΠΎΠ±ΠΎΡΡΠ΄ΠΎΠ²Π°Π½ΠΈΠ΅.
- ΠΡΠ±ΠΎΠΉ ΠΏΠΎΠ»ΡΠ·ΠΎΠ²Π°ΡΠ΅Π»Ρ ΡΠ°Π·Π±Π΅ΡΠ΅ΡΡΡ Π² ΡΠΎΠΌ, ΠΊΠ°ΠΊ ΠΏΡΠΎΠ²Π΅ΡΡΠΈ ΡΡΡΠ°Π½ΠΎΠ²ΠΊΡ.
- ΠΠΌΠ΅Π½Π½ΠΎ Π΄Π°Π½Π½Π°Ρ ΠΏΡΠΎΠ³ΡΠ°ΠΌΠΌΠ° Π»ΡΡΡΠ΅ Π²ΡΠ΅Π³ΠΎ ΡΠ°Π±ΠΎΡΠ°Π΅Ρ ΠΏΠΎΠ΄ MS-DOS. Π ΡΠ΅ΠΆΠΈΠΌΠ΅ ΡΠΎΠ²ΠΌΠ΅ΡΡΠΈΠΌΠΎΡΡΠΈ Π½Π° Windows ΠΌΠΎΠ³ΡΡ ΠΏΠΎΡΠ²Π»ΡΡΡΡΡ Π½Π΅ΠΊΠΎΡΠΎΡΡΠ΅ ΠΎΡΠΈΠ±ΠΊΠΈ.
- ΠΠΎ, Ρ Π΄ΡΡΠ³ΠΎΠΉ ΡΡΠΎΡΠΎΠ½Ρ, ΡΡΠΎ ΠΏΠΎΠ·Π²ΠΎΠ»ΠΈΡ ΡΠΎΠ±ΡΠ°ΡΡ ΠΊΠΎΠΌΠΏΡΡΡΠ΅Ρ Ρ ΠΎΠΏΡΠ΅Π΄Π΅Π»Π΅Π½Π½ΡΠΌΠΈ Ρ Π°ΡΠ°ΠΊΡΠ΅ΡΠΈΡΡΠΈΠΊΠ°ΠΌΠΈ, ΡΠΎΠ²ΠΌΠ΅ΡΡΠΈΠΌΡΠΌΠΈ ΠΈΠΌΠ΅Π½Π½ΠΎ Ρ Π΄Π°Π½Π½ΡΠΌ ΠΏΡΠΎΠ³ΡΠ°ΠΌΠΌΠ½ΡΠΌ ΠΎΠ±Π΅ΡΠΏΠ΅ΡΠ΅Π½ΠΈΠ΅ΠΌ.
Π Π΅ΠΊΠΎΠΌΠ΅Π½Π΄Π°ΡΠΈΠΈ ΠΏΠΎ Π½Π°ΡΡΡΠΎΠΉΠΊΠ°ΠΌ
- ΠΠΎΡΠ»Π΅ ΠΏΠ΅ΡΠ²ΠΎΠ³ΠΎ Π·Π°ΠΏΡΡΠΊΠ° ΠΏΡΠΎΠ³ΡΠ°ΠΌΠΌΡ ΠΏΠΎΡΠ²ΠΈΡΡΡ ΡΠΏΠ΅ΡΠΈΠ°Π»ΡΠ½ΡΠΉ ΡΠΊΡΠ°Π½.
- ΠΠ°Π΄ΠΎ Π½Π°ΠΆΠ°ΡΡ ΠΏΡΠΎΠ±Π΅Π». Π’Π°ΠΊ ΠΏΠΎΠ»ΡΠ·ΠΎΠ²Π°ΡΠ΅Π»Ρ ΠΎΠΊΠ°Π·ΡΠ²Π°Π΅ΡΡΡ Π² Π³Π»Π°Π²Π½ΠΎΠΌ ΠΌΠ΅Π½Ρ.
- ΠΠ°ΠΆΠΈΠΌΠ°Π΅ΠΌ F1, Π° ΠΏΠΎΡΠΎΠΌ Π²ΡΠ±ΠΈΡΠ°Π΅ΠΌ ΠΏΡΠ½ΠΊΡ Configure.
- ΠΠ°Π»Π΅Π΅ Π½Π°Π΄ΠΎ Π½Π°ΠΆΠ°ΡΡ ΠΏΡΠ½ΠΊΡ Β«number of AxisΒ». ΠΡΠΏΠΎΠ»ΡΠ·ΡΠ΅ΠΌ ΠΊΠ»Π°Π²ΠΈΡΡ Enter.
- ΠΡΡΠ°Π΅ΡΡΡ ΡΠΎΠ»ΡΠΊΠΎ Π²Π²Π΅ΡΡΠΈ ΠΊΠΎΠ»ΠΈΡΠ΅ΡΡΠ²ΠΎ ΡΠΎΠ΅ΠΉ, ΠΊΠΎΡΠΎΡΡΠ΅ ΠΏΠ»Π°Π½ΠΈΡΡΠ΅ΡΡΡ ΠΈΡΠΏΠΎΠ»ΡΠ·ΠΎΠ²Π°ΡΡ. Π Π΄Π°Π½Π½ΠΎΠΌ ΡΠ»ΡΡΠ°Π΅ Ρ Π½Π°Ρ ΠΎΠ΄ΠΈΠ½ ΠΌΠΎΡΠΎΡ, ΠΏΠΎΡΠΎΠΌΡ ΠΈ Π½Π°ΠΆΠΈΠΌΠ°Π΅ΠΌ Π½Π° ΡΠΈΡΡΡ 1.
- ΠΠ»Ρ ΠΏΡΠΎΠ΄ΠΎΠ»ΠΆΠ΅Π½ΠΈΡ ΠΈΡΠΏΠΎΠ»ΡΠ·ΡΠ΅ΠΌ Enter. ΠΠ°ΠΌ ΡΠ½ΠΎΠ²Π° ΠΏΠΎΠ½Π°Π΄ΠΎΠ±ΠΈΡΡΡ ΠΊΠ»Π°Π²ΠΈΡΠ° F1, ΠΏΠΎΡΠ»Π΅ Π΅Π΅ ΠΏΡΠΈΠΌΠ΅Π½Π΅Π½ΠΈΡ Π² ΠΌΠ΅Π½Ρ Configure Π²ΡΠ±ΠΈΡΠ°Π΅ΠΌ Configure Axis. ΠΠ°ΡΠ΅ΠΌ β Π΄Π²Π° ΡΠ°Π·Π° Π½Π°ΠΆΠΈΠΌΠ°Π΅ΠΌ ΠΏΡΠΎΠ±Π΅Π».
Drive Type β Π²ΠΎΡ ΠΊΠ°ΠΊΠ°Ρ Π²ΠΊΠ»Π°Π΄ΠΊΠ° Π½Π°ΠΌ Π½ΡΠΆΠ½Π°, Π΄ΠΎ Π½Π΅Π΅ Π΄ΠΎΡ ΠΎΠ΄ΠΈΠΌ ΠΌΠ½ΠΎΠ³ΠΎΡΠΈΡΠ»Π΅Π½Π½ΡΠΌΠΈ Π½Π°ΠΆΠΈΠΌΠ°Π½ΠΈΡΠΌΠΈ Tab. Π‘ΡΡΠ΅Π»ΠΊΠ° Π²Π½ΠΈΠ· ΠΏΠΎΠΌΠΎΠ³Π°Π΅Ρ Π΄ΠΎΠΉΡΠΈ Π΄ΠΎ ΠΏΡΠ½ΠΊΡΠ° Type. ΠΠ°ΠΌ Π½ΡΠΆΠ½Π° ΡΡΠ΅ΠΉΠΊΠ°, ΠΊΠΎΡΠΎΡΠ°Ρ Π½ΠΎΡΠΈΡ Π½Π°Π·Π²Π°Π½ΠΈΠ΅ Scale. ΠΠ°Π»Π΅Π΅ ΠΎΠΏΡΠ΅Π΄Π΅Π»ΡΠ΅ΠΌ, ΡΠΊΠΎΠ»ΡΠΊΠΎ ΡΠ°Π³ΠΎΠ² Π΄Π²ΠΈΠ³Π°ΡΠ΅Π»Ρ ΡΠΎΠ²Π΅ΡΡΠ°Π΅Ρ ΡΠΎΠ»ΡΠΊΠΎ Π·Π° Π²ΡΠ΅ΠΌΡ ΠΎΠ΄Π½ΠΎΠ³ΠΎ ΠΎΠ±ΠΎΡΠΎΡΠ°. ΠΠ»Ρ ΡΡΠΎΠ³ΠΎ Π΄ΠΎΡΡΠ°ΡΠΎΡΠ½ΠΎ Π·Π½Π°ΡΡ Π½ΠΎΠΌΠ΅Ρ Π΄Π΅ΡΠ°Π»ΠΈ. Π’ΠΎΠ³Π΄Π° Π»Π΅Π³ΠΊΠΎ Π±ΡΠ΄Π΅Ρ ΠΏΠΎΠ½ΡΡΡ, Π½Π° ΡΠΊΠΎΠ»ΡΠΊΠΎ Π³ΡΠ°Π΄ΡΡΠΎΠ² ΠΎΠ½ ΠΏΠΎΠ²ΠΎΡΠ°ΡΠΈΠ²Π°Π΅ΡΡΡ Π²ΡΠ΅Π³ΠΎ Π·Π° ΠΎΠ΄ΠΈΠ½ ΡΠ°Π³. ΠΠ°Π»Π΅Π΅ ΡΠΈΡΠ»ΠΎ Π³ΡΠ°Π΄ΡΡΠΎΠ² Π΄Π΅Π»ΠΈΡΡΡ Π½Π° ΠΎΠ΄ΠΈΠ½ ΡΠ°Π³. Π’Π°ΠΊ ΠΌΡ Π²ΡΡΠΈΡΠ»ΡΠ΅ΠΌ ΠΊΠΎΠ»ΠΈΡΠ΅ΡΡΠ²ΠΎ ΡΠ°Π³ΠΎΠ².
ΠΡΡΠ°Π»ΡΠ½ΡΠ΅ Π½Π°ΡΡΡΠΎΠΉΠΊΠΈ ΠΌΠΎΠΆΠ½ΠΎ ΠΎΡΡΠ°Π²ΠΈΡΡ Π² ΠΏΠ΅ΡΠ²ΠΎΠ½Π°ΡΠ°Π»ΡΠ½ΠΎΠΌ Π²ΠΈΠ΄Π΅. Π§ΠΈΡΠ»ΠΎ, ΠΏΠΎΠ»ΡΡΠΈΠ²ΡΠ΅Π΅ΡΡ Π² ΡΡΠ΅ΠΉΠΊΠ΅ Scale, ΠΏΡΠΎΡΡΠΎ ΠΊΠΎΠΏΠΈΡΡΠ΅ΡΡΡ Π² ΡΠ°ΠΊΡΡ ΠΆΠ΅ ΡΡΠ΅ΠΉΠΊΡ, Π½ΠΎ Π½Π° Π΄ΡΡΠ³ΠΎΠΌ ΠΊΠΎΠΌΠΏΡΡΡΠ΅ΡΠ΅. ΠΠ½Π°ΡΠ΅Π½ΠΈΠ΅ 20 Π΄ΠΎΠ»ΠΆΠ½ΠΎ Π±ΡΡΡ ΠΏΡΠΈΡΠ²ΠΎΠ΅Π½ΠΎ ΡΡΠ΅ΠΉΠΊΠ΅ Acceleration. ΠΠΎ ΡΠΌΠΎΠ»ΡΠ°Π½ΠΈΡ Π² ΡΡΠΎΠΉ ΠΎΠ±Π»Π°ΡΡΠΈ ΡΡΠΎΠΈΡ Π·Π½Π°ΡΠ΅Π½ΠΈΠ΅ 2000, Π½ΠΎ ΠΎΠ½ΠΎ ΡΠ»ΠΈΡΠΊΠΎΠΌ Π±ΠΎΠ»ΡΡΠΎΠ΅ Π΄Π»Ρ ΡΠΎΠ±ΠΈΡΠ°Π΅ΠΌΠΎΠΉ ΡΠΈΡΡΠ΅ΠΌΡ. ΠΠ°ΡΠ°Π»ΡΠ½ΡΠΉ ΡΡΠΎΠ²Π΅Π½Ρ β 20, Π° ΠΌΠ°ΠΊΡΠΈΠΌΠ°Π»ΡΠ½ΡΠΉ β 175. ΠΠ°Π»Π΅Π΅ ΠΎΡΡΠ°Π΅ΡΡΡ Π½Π°ΠΆΠΈΠΌΠ°ΡΡ TAB, ΠΏΠΎΠΊΠ° ΠΏΠΎΠ»ΡΠ·ΠΎΠ²Π°ΡΠ΅Π»Ρ Π½Π΅ Π΄ΠΎΡ ΠΎΠ΄ΠΈΡ Π΄ΠΎ ΠΏΡΠ½ΠΊΡΠ° Last Phase. ΠΠ΄Π΅ΡΡ Π½ΡΠΆΠ½ΠΎ ΠΏΠΎΡΡΠ°Π²ΠΈΡΡ ΡΠΈΡΡΡ 4. ΠΠ°Π»Π΅Π΅ ΠΆΠΌΠ΅ΠΌ Tab, ΠΏΠΎΠΊΠ° Π½Π΅ Π΄ΠΎΠΉΠ΄Π΅ΠΌ Π΄ΠΎ ΡΡΠ΄Π° ΠΈΠ· ΠΈΠΊΡΠΎΠ², ΠΏΠ΅ΡΠ²ΠΎΠ³ΠΎ Π² ΡΠΏΠΈΡΠΊΠ΅. ΠΠ΅ΡΠ²ΡΠ΅ ΡΠ΅ΡΡΡΠ΅ ΡΡΡΠΎΡΠΊΠΈ Π΄ΠΎΠ»ΠΆΠ½Ρ ΡΠΎΠ΄Π΅ΡΠΆΠ°ΡΡ ΡΠ»Π΅Π΄ΡΡΡΠΈΠ΅ ΠΏΠΎΠ·ΠΈΡΠΈΠΈ:
1000XXXXXXXX
0100XXXXXXXX
0010XXXXXXXX
0001XXXXXXXX
Π ΠΎΡΡΠ°Π»ΡΠ½ΡΡ ΡΡΠ΅ΠΉΠΊΠ°Ρ Π½Π΅ Π½ΡΠΆΠ½ΠΎ ΠΏΡΠΎΠ²ΠΎΠ΄ΠΈΡΡ Π½ΠΈΠΊΠ°ΠΊΠΈΡ ΠΈΠ·ΠΌΠ΅Π½Π΅Π½ΠΈΠΉ. ΠΡΠΎΡΡΠΎ Π²ΡΠ±ΠΈΡΠ°Π΅ΠΌ ΠΠ. ΠΡΠ΅, ΠΏΡΠΎΠ³ΡΠ°ΠΌΠΌΠ° Π½Π°ΡΡΡΠΎΠ΅Π½Π° Π΄Π»Ρ ΡΠ°Π±ΠΎΡΡ Ρ ΠΊΠΎΠΌΠΏΡΡΡΠ΅ΡΠΎΠΌ, ΡΠ°ΠΌΠΈΠΌΠΈ ΠΈΡΠΏΠΎΠ»Π½ΠΈΡΠ΅Π»ΡΠ½ΡΠΌΠΈ ΡΡΡΡΠΎΠΉΡΡΠ²Π°ΠΌΠΈ.

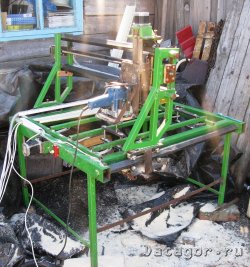
ΠΡΠ΅ΠΌ Π΄ΠΎΠ±ΡΠΎΠ³ΠΎ Π²ΡΠ΅ΠΌΠ΅Π½ΠΈ ΡΡΡΠΎΠΊ! Π Π²ΠΎΡ ΠΈ Ρ Ρ Π½ΠΎΠ²ΠΎΠΉ ΡΠ°ΡΡΡΡ ΡΠ²ΠΎΠ΅Π³ΠΎ ΡΠ°ΡΡΠΊΠ°Π·Π° ΠΎ Π§ΠΠ£ — ΡΡΠ°Π½ΠΊΠ΅. ΠΠΎΠ³Π΄Π° Π½Π°ΡΠΈΠ½Π°Π» ΠΏΠΈΡΠ°ΡΡ ΡΡΠ°ΡΡΡ Π΄Π°ΠΆΠ΅ Π½Π΅ Π΄ΡΠΌΠ°Π», ΡΡΠΎ ΠΎΠ½Π° ΠΏΠΎΠ»ΡΡΠΈΡΡΡ Π½Π°ΡΡΠΎΠ»ΡΠΊΠΎ ΠΎΠ±ΡΠ΅ΠΌΠ½ΠΎΠΉ. ΠΠΎΠ³Π΄Π° Π½Π°ΠΏΠΈΡΠ°Π» ΠΏΡΠΎ ΡΠ»Π΅ΠΊΡΡΠΎΠ½ΠΈΠΊΡ ΡΡΠ°Π½ΠΊΠ° ΠΏΠΎΡΠΌΠΎΡΡΠ΅Π» ΠΈ ΠΈΡΠΏΡΠ³Π°Π»ΡΡ β Π»ΠΈΡΡ Π4 ΠΈΡΠΏΠΈΡΠ°Π½ Ρ Π΄Π²ΡΡ ΡΡΠΎΡΠΎΠ½, Π° Π΅ΡΡ ΠΎΡΠ΅Π½Ρ ΠΈ ΠΎΡΠ΅Π½Ρ ΠΌΠ½ΠΎΠ³ΠΎ ΡΠ΅Π³ΠΎ Π½ΡΠΆΠ½ΠΎ ΡΠ°ΡΡΠΊΠ°Π·Π°ΡΡ.
Π ΠΈΡΠΎΠ³Π΅ ΠΏΠΎΠ»ΡΡΠΈΠ»ΠΎΡΡ ΡΡΠ°ΠΊΠΎΠ΅ ΡΡΠΊΠΎΠ²ΠΎΠ΄ΡΡΠ²ΠΎ ΠΏΠΎ ΡΠΎΠ·Π΄Π°Π½ΠΈΡ ΡΡΠ°Π½ΠΊΠ° Π§ΠΠ£, ΡΠ°Π±ΠΎΡΠ΅Π³ΠΎ ΡΡΠ°Π½ΠΊΠ°, Ρ Π½ΠΎΠ»Ρ. ΠΡΠ΄Π΅Ρ ΡΡΠΈ ΡΠ°ΡΡΠΈ ΡΡΠ°ΡΡΠΈ ΠΎΠ± ΠΎΠ΄Π½ΠΎΠΌ ΡΡΠ°Π½ΠΊΠ΅: 1-ΡΠ»Π΅ΠΊΡΡΠΎΠ½Π½Π°Ρ Π½Π°ΡΠΈΠ½ΠΊΠ°, 2-ΠΌΠ΅Ρ
Π°Π½ΠΈΠΊΠ° ΡΡΠ°Π½ΠΊΠ°, 3-Π²ΡΠ΅ ΡΠΎΠ½ΠΊΠΎΡΡΠΈ Π½Π°ΡΡΡΠΎΠΉΠΊΠΈ ΡΠ»Π΅ΠΊΡΡΠΎΠ½ΠΈΠΊΠΈ, ΡΠ°ΠΌΠΎΠ³ΠΎ ΡΡΠ°Π½ΠΊΠ°, ΠΈ ΠΏΡΠΎΠ³ΡΠ°ΠΌΠΌΡ ΡΠΏΡΠ°Π²Π»Π΅Π½ΠΈΡ ΡΡΠ°Π½ΠΊΠΎΠΌ.
Π ΠΎΠ±ΡΠ΅ΠΌ ΠΏΠΎΠΏΡΡΠ°ΡΡΡ ΠΎΠ±ΡΠ΅Π΄ΠΈΠ½ΠΈΡΡ Π² ΠΎΠ΄Π½ΠΎΠΌ ΠΌΠ°ΡΠ΅ΡΠΈΠ°Π»Π΅ Π²ΡΡ ΠΏΠΎΠ»Π΅Π·Π½ΠΎΠ΅ ΠΈ Π½Π΅ΠΎΠ±Ρ
ΠΎΠ΄ΠΈΠΌΠΎΠ΅ ΠΊΠ°ΠΆΠ΄ΠΎΠΌΡ Π½Π°ΡΠΈΠ½Π°ΡΡΠ΅ΠΌΡ Π² ΡΡΠΎΠΌ ΠΈΠ½ΡΠ΅ΡΠ΅ΡΠ½ΠΎΠΌ Π΄Π΅Π»Π΅, ΡΠΎ ΡΡΠΎ ΡΠ°ΠΌ ΠΏΡΠΎΡΠ΅Π» Π½Π° ΡΠ°Π·Π½ΡΡ
ΠΈΠ½ΡΠ΅ΡΠ½Π΅Ρ-ΡΠ΅ΡΡΡΡΠ°Ρ
ΠΈ ΠΏΡΠΎΠΏΡΡΡΠΈΠ» ΡΠ΅ΡΠ΅Π· ΡΠ΅Π±Ρ.
Π‘ΠΎΠ΄Π΅ΡΠΆΠ°Π½ΠΈΠ΅ / Contents
ΠΡΡΠ°ΡΠΈ, Π² ΡΠΎΠΉ ΡΡΠ°ΡΡΠ΅ Ρ Π·Π°Π±ΡΠ» ΠΏΠΎΠΊΠ°Π·Π°ΡΡ ΡΠΎΡΠΎΠ³ΡΠ°ΡΠΈΠΈ ΠΈΠ·Π³ΠΎΡΠΎΠ²Π»Π΅Π½Π½ΡΡ ΠΏΠΎΠ΄Π΅Π»ΠΎΠΊ. ΠΡΠΏΡΠ°Π²Π»ΡΡ ΡΡΠΎ. ΠΠ΅Π½ΠΎΠΏΠ»Π°ΡΡΠΎΠ²ΡΠΉ ΠΌΠ΅Π΄Π²Π΅Π΄Ρ ΠΈ ΡΠ°Π½Π΅ΡΠ½ΠΎΠ΅ ΡΠ°ΡΡΠ΅Π½ΠΈΠ΅.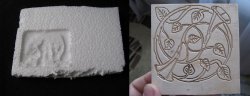
ΠΠ΅ Π·Π½Π°Π» Ρ ΡΠ΅Π³ΠΎ Π½Π°ΡΠ°ΡΡ. ΠΠ΅ΡΠ²ΡΠΌ Π΄Π΅Π»ΠΎΠΌ Π·Π°ΠΊΠ°Π·Π°Π» Π½ΠΎΡΠΌΠ°Π»ΡΠ½ΡΠΉ ΡΠ°Π³ΠΎΠ²ΡΠΉ Π΄Π²ΠΈΠ³Π°ΡΠ΅Π»Ρ Vexta Π½Π° 12 ΠΊΠ³/ΡΠΌ, ΠΌΠ΅ΠΆΠ΄Ρ ΠΏΡΠΎΡΠΈΠΌ Ρ Π³ΠΎΡΠ΄ΠΎΠΉ Π½Π°Π΄ΠΏΠΈΡΡΡ Β«made in JapanΒ».
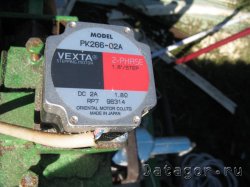
ΠΠΎΠΊΠ° ΡΠΎΡ Π΅Ρ Π°Π» ΡΠ΅ΡΠ΅Π· Π²ΡΡ Π ΠΎΡΡΠΈΡ, ΡΠΈΠ΄Π΅Π» Π²Π΅ΡΠ΅ΡΠ°ΠΌΠΈ Π½Π° ΡΠ°Π·Π½ΡΡ Π§ΠΠ£-ΡΠ½ΡΡ ΡΠΎΡΡΠΌΠ°Ρ ΠΈ ΠΏΡΡΠ°Π»ΡΡ ΠΎΠΏΡΠ΅Π΄Π΅Π»ΠΈΡΡΡΡ Π² Π²ΡΠ±ΠΎΡΠ΅ ΠΊΠΎΠ½ΡΡΠΎΠ»Π»Π΅ΡΠ° STEP/DIR ΠΈ Π΄ΡΠ°ΠΉΠ²Π΅ΡΠ° ΡΠ°Π³ΠΎΠ²ΡΡ Π΄Π²ΠΈΠ³Π°ΡΠ΅Π»Π΅ΠΉ. Π Π°ΡΡΠΌΠ°ΡΡΠΈΠ²Π°Π» ΡΡΠΈ Π²Π°ΡΠΈΠ°Π½ΡΠ°: Π½Π° ΠΌΠΈΠΊΡΠΎΡΡ Π΅ΠΌΠ΅ L298, Π½Π° ΠΏΠΎΠ»Π΅Π²ΠΈΠΊΠ°Ρ , Π»ΠΈΠ±ΠΎ ΠΆΠ΅ ΠΊΡΠΏΠΈΡΡ Π³ΠΎΡΠΎΠ²ΡΠΉ ΠΊΠΈΡΠ°ΠΉΡΠΊΠΈΠΉ TB6560 ΠΎ ΠΊΠΎΡΠΎΡΠΎΠΌ Π±ΡΠ»ΠΈ ΠΎΡΠ΅Π½Ρ ΠΏΡΠΎΡΠΈΠ²ΠΎΡΠ΅ΡΠΈΠ²ΡΠ΅ ΠΎΡΠ·ΡΠ²Ρ.
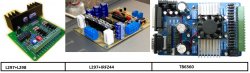
Π£ ΠΎΠ΄Π½ΠΈΡ ΠΎΠ½ ΡΠ°Π±ΠΎΡΠ°Π» Π±Π΅Π· ΠΏΡΠΎΠ±Π»Π΅ΠΌ ΠΏΡΠΎΠ΄ΠΎΠ»ΠΆΠΈΡΠ΅Π»ΡΠ½ΠΎΠ΅ Π²ΡΠ΅ΠΌΡ, Ρ Π΄ΡΡΠ³ΠΈΡ ΡΠ³ΠΎΡΠ°Π» ΠΏΡΠΈ ΠΌΠ°Π»Π΅ΠΉΡΠ΅ΠΉ ΠΎΡΠΈΠ±ΠΊΠΈ ΠΏΠΎΠ»ΡΠ·ΠΎΠ²Π°ΡΠ΅Π»Ρ. ΠΡΠΎ-ΡΠΎ Π΄Π°ΠΆΠ΅ ΠΏΠΈΡΠ°Π», ΡΡΠΎ Ρ Π½Π΅Π³ΠΎ ΡΠ³ΠΎΡΠ΅Π», ΠΊΠΎΠ³Π΄Π° ΡΠΎΡ Π½Π΅ΠΌΠ½ΠΎΠΆΠΊΠΎ ΠΏΡΠΎΠ²Π΅ΡΠ½ΡΠ» Π²Π°Π» Π΄Π²ΠΈΠ³Π°ΡΠ΅Π»Ρ, ΠΏΠΎΠ΄ΠΊΠ»ΡΡΠ΅Π½Π½ΠΎΠ³ΠΎ Π² ΡΡΠΎ Π²ΡΠ΅ΠΌΡ ΠΊ ΠΊΠΎΠ½ΡΡΠΎΠ»Π»Π΅ΡΡ. ΠΠ°Π²Π΅ΡΠ½ΠΎΠ΅ ΡΠ°ΠΊΡ Π½Π΅Π½Π°Π΄Π΅ΠΆΠ½ΠΎΡΡΠΈ ΠΊΠΈΡΠ°ΠΉΡΠ° ΠΈ ΡΡΠ³ΡΠ°Π» Π² ΠΏΠΎΠ»ΡΠ·Ρ Π²ΡΠ±ΠΎΡΠ° ΡΡ Π΅ΠΌΡ L297+IRFZ44 Π°ΠΊΡΠΈΠ²Π½ΠΎ ΠΎΠ±ΡΡΠΆΠ΄Π°Π΅ΠΌΠΎΠΉ Π½Π° ΡΠΎΡΡΠΌΠ΅. Π‘Ρ Π΅ΠΌΠ° Π½Π°Π²Π΅ΡΠ½ΠΎΠ΅ ΠΈ Π² ΡΠ°ΠΌΠΎΠΌ Π΄Π΅Π»Π΅ Π½Π΅ΡΠ±ΠΈΠ²Π°Π΅ΠΌΠ°Ρ Ρ.ΠΊ. ΠΏΠΎΠ»Π΅Π²ΠΈΠΊΠΈ Π΄ΡΠ°ΠΉΠ²Π΅ΡΠ° ΠΏΠΎ Π°ΠΌΠΏΠ΅ΡΠ°ΠΌ Π² Π½Π΅ΡΠΊΠΎΠ»ΡΠΊΠΎ ΡΠ°Π· ΠΏΡΠ΅Π²ΡΡΠ°ΡΡ ΡΠΎ, ΡΡΠΎ Π½ΡΠΆΠ½ΠΎ ΠΏΠΎΠ΄Π°Π²Π°ΡΡ Π½Π° ΠΌΠΎΡΠΎΡΡ. ΠΡΡΡΡ ΠΈ ΡΠ°ΠΌΠΎΠΌΡ ΠΏΠ°ΡΡΡ Π½Π°Π΄ΠΎ (ΡΡΠΎ ΠΆΠ΅ ΡΠΎΠ»ΡΠΊΠΎ Π² ΠΏΠ»ΡΡ), ΠΈ ΠΏΠΎ ΡΡΠΎΠΈΠΌΠΎΡΡΠΈ Π΄Π΅ΡΠ°Π»Π΅ΠΉ Π²ΡΡ ΠΎΠ΄ΠΈΠ»ΠΎ ΡΡΡΡ Π±ΠΎΠ»ΡΡΠ΅, ΡΠ΅ΠΌ ΠΊΠΈΡΠ°ΠΉΡΠΊΠΈΠΉ ΠΊΠΎΠ½ΡΡΠΎΠ»Π»Π΅Ρ, Π·Π°ΡΠΎ Π½Π°Π΄Π΅ΠΆΠ½ΠΎ, ΡΡΠΎ Π²Π°ΠΆΠ½Π΅Π΅.
ΠΠ΅ΠΌΠ½ΠΎΠ³ΠΎ ΠΎΡΡΡΡΠΏΠ»Ρ ΠΎΡ ΡΠ΅ΠΌΡ. ΠΠΎΠ³Π΄Π° Π²ΡΡ ΡΡΠΎ Π΄Π΅Π»Π°Π»ΠΎΡΡ, Π΄Π°ΠΆΠ΅ Π½Π΅ Π²ΠΎΠ·Π½ΠΈΠΊΠ»ΠΎ ΠΌΡΡΠ»ΠΈ, ΡΡΠΎ ΠΊΠΎΠ³Π΄Π°-Π½ΠΈΠ±ΡΠ΄Ρ Π±ΡΠ΄Ρ ΠΎΠ± ΡΡΠΎΠΌ ΠΏΠΈΡΠ°ΡΡ. ΠΠΎΡΡΠΎΠΌΡ Π½Π΅Ρ ΡΠΎΡΠΎΠ³ΡΠ°ΡΠΈΠΉ ΠΏΡΠΎΡΠ΅ΡΡΠ° ΡΠ±ΠΎΡΠΊΠΈ ΠΌΠ΅Ρ Π°Π½ΠΈΠΊΠΈ ΠΈ ΡΠ»Π΅ΠΊΡΡΠΎΠ½ΠΈΠΊΠΈ, ΡΠΎΠ»ΡΠΊΠΎ Π½Π΅ΡΠΊΠΎΠ»ΡΠΊΠΎ ΡΠΎΡΠΎΠΊ, ΡΠ΄Π΅Π»Π°Π½Π½ΡΡ Π½Π° ΠΊΠ°ΠΌΠ΅ΡΡ ΠΌΠΎΠ±ΠΈΠ»ΡΠ½ΠΈΠΊΠ°. ΠΡΡ ΠΎΡΡΠ°Π»ΡΠ½ΠΎΠ΅ ΡΠ΅Π»ΠΊΠ°Π» ΡΠΏΠ΅ΡΠΈΠ°Π»ΡΠ½ΠΎ Π΄Π»Ρ ΡΡΠ°ΡΡΠΈ, Π² ΡΠΆΠ΅ ΡΠΎΠ±ΡΠ°Π½Π½ΠΎΠΌ Π²ΠΈΠ΄Π΅.
ΠΠ°ΡΠ½Ρ Ρ Π±Π»ΠΎΠΊΠ° ΠΏΠΈΡΠ°Π½ΠΈΡ. ΠΠ»Π°Π½ΠΈΡΠΎΠ²Π°Π» ΡΠ΄Π΅Π»Π°ΡΡ ΠΈΠΌΠΏΡΠ»ΡΡΠ½ΡΠΉ, ΠΏΡΠΎΠ²ΠΎΠ·ΠΈΠ»ΡΡ Ρ Π½ΠΈΠΌ Π½Π°Π²Π΅ΡΠ½ΠΎΠ΅ Π½Π΅Π΄Π΅Π»Ρ, Π½ΠΎ ΡΠ°ΠΊ ΠΈ Π½Π΅ ΡΠΌΠΎΠ³ ΠΏΠΎΠ±Π΅Π΄ΠΈΡΡ Π²ΠΎΠ·Π±ΡΠ΄, ΠΊΠΎΡΠΎΡΡΠΉ ΡΠ΅Π» Π½Π΅ΠΏΠΎΠ½ΡΡΠ½ΠΎ ΠΎΡΠΊΡΠ΄Π°. ΠΠΎΡΠ°Ρ ΡΡΠ°Π½Ρ Π½Π° 12Π² β Π²ΡΡ ΠΠ, ΠΌΠΎΡΠ°Ρ Π½Π° 30-ΠΏΠΎΠ»Π½Π°Ρ Π½Π΅ΡΠ°Π·Π±Π΅ΡΠΈΡ Π°. ΠΡΠΈΡΠ΅Π» ΠΊ Π²ΡΠ²ΠΎΠ΄Ρ, ΡΡΠΎ ΠΊΠ°ΠΊΠ°Ρ-ΡΠΎ Π±ΡΠΊΠ° Π»Π΅Π·Π΅Ρ ΠΏΠΎ ΠΎΠ±ΡΠ°ΡΠ½ΠΎΠΉ ΡΠ²ΡΠ·ΠΈ Ρ 30Π² Π½Π° TL494 ΠΈ ΡΠ½ΠΎΡΠΈΡ Π΅ΠΉ Π±Π°ΡΠ½Ρ. Π’Π°ΠΊ ΠΈ Π·Π°Π±ΡΠΎΡΠΈΠ» ΡΡΠΎΡ ΠΈΠΌΠΏΡΠ»ΡΡΠ½ΠΈΠΊ, Π±Π»Π°Π³ΠΎ Π±ΡΠ»ΠΎ Π½Π΅ΡΠΊΠΎΠ»ΡΠΊΠΎ Π’Π‘-180 ΠΎΠ΄ΠΈΠ½ ΠΈΠ· ΠΊΠΎΡΠΎΡΡΡ ΠΏΠΎΡΠ΅Π» ΡΠ»ΡΠΆΠΈΡΡ ΡΠΎΠ΄ΠΈΠ½Π΅ Π² ΠΊΠ°ΡΠ΅ΡΡΠ²Π΅ ΡΡΠ°Π½ΡΠ° ΠΏΠΈΡΠ°Π½ΠΈΡ. ΠΠ° ΠΈ ΡΡΠΎ Π½ΠΈ Π³ΠΎΠ²ΠΎΡΠΈ, Π° ΠΊΡΡΠΎΠΊ ΠΆΠ΅Π»Π΅Π·Π° ΠΈ ΠΌΠ΅Π΄ΠΈ Π±ΡΠ΄Π΅Ρ Π½Π°Π΄Π΅ΠΆΠ½Π΅Π΅ ΠΊΡΡΠΊΠΈ ΡΠ°ΡΡΡΠΏΡΡ ΠΈ. Π’ΡΠ°Π½ΡΡΠΎΡΠΌΠ°ΡΠΎΡ ΠΏΠ΅ΡΠ΅ΠΌΠΎΡΠ°Π» Π½Π° Π½ΡΠΆΠ½ΡΠ΅ Π½Π°ΠΏΡΡΠΆΠ΅Π½ΠΈΡ, Π° Π½ΡΠΆΠ½ΠΎ Π±ΡΠ»ΠΎ +30Π² Π½Π° ΠΏΠΈΡΠ°Π½ΠΈΠ΅ ΠΌΠΎΡΠΎΡΡΠΈΠΊΠΎΠ², +15Π² Π½Π° ΠΏΠΈΡΠ°Π½ΠΈΠ΅ IR2104, +5Π² Π½Π° L297, ΠΈ Π²Π΅Π½ΡΠΈΠ»ΡΡΠΎΡ. ΠΠ° Π΄Π²ΠΈΠ³Π°ΡΠ΅Π»ΠΈ ΠΌΠΎΠΆΠ½ΠΎ ΠΏΠΎΠ΄Π°Π²Π°ΡΡ 10, Π° ΠΌΠΎΠΆΠ½ΠΎ ΠΈ 70, Π³Π»Π°Π²Π½ΠΎΠ΅ Π½Π΅ ΠΏΡΠ΅Π²ΡΡΠ°ΡΡ ΠΏΠΎ ΡΠΎΠΊΡ, Π½ΠΎ, Π΅ΡΠ»ΠΈ ΡΠ΄Π΅Π»Π°ΡΡ ΠΌΠ΅Π½ΡΡΠ΅ β ΡΠ½ΠΈΠΆΠ°ΡΡΡΡ ΠΌΠ°ΠΊΡΠΈΠΌΠ°Π»ΡΠ½ΡΠ΅ ΠΎΠ±ΠΎΡΠΎΡΡ ΠΈ ΡΠΈΠ»Π°, Π° Π²ΠΎΡ Π±ΠΎΠ»ΡΡΠ΅ Π½Π΅ ΠΏΠΎΠ·Π²ΠΎΠ»ΡΠ» ΡΡΠ°Π½ΡΡΠΎΡΠΌΠ°ΡΠΎΡ Ρ.ΠΊ. Π½ΡΠΆΠ½ΠΎ Π±ΡΠ»ΠΎ 6-7Π. ΠΠ°ΠΏΡΡΠΆΠ΅Π½ΠΈΡ 5 ΠΈ 15Π² Π·Π°ΡΡΠ°Π±ΠΈΠ»ΠΈΠ·ΠΈΡΠΎΠ²Π°Π», 30 ΠΎΡΡΠ°Π²ΠΈΠ» Β«ΠΏΠ»Π°Π²Π°ΡΡΠΈΠΌΠΈΒ» Π½Π° ΡΡΠΌΠΎΡΡΠ΅Π½ΠΈΠ΅ Π½Π°ΡΠ΅ΠΉ ΡΠ»Π΅ΠΊΡΡΠΎΡΠ΅ΡΠΈ.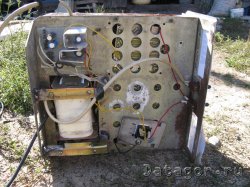
ΠΡΡ ΡΡΠΎ Π²ΡΠ΅ΠΌΡ Π΅ΠΆΠ΅Π²Π΅ΡΠ΅ΡΠ½Π΅Π΅ ΡΠΈΠ΄Π΅Π» Π·Π° ΠΊΠΎΠΌΠΏΡΡΡΠ΅ΡΠΎΠΌ ΠΈ ΡΠΈΡΠ°Π», ΡΠΈΡΠ°Π», ΡΠΈΡΠ°Π». ΠΠ°ΡΡΡΠΎΠΉΠΊΠ° ΠΊΠΎΠ½ΡΡΠΎΠ»Π»Π΅ΡΠ°, Π²ΡΠ±ΠΎΡ ΠΏΡΠΎΠ³ΡΠ°ΠΌΠΌ: ΠΊΠ°ΠΊΠΎΠΉ ΡΠΈΡΠΎΠ²Π°ΡΡ, ΠΊΠ°ΠΊΠΎΠΉ ΡΠΏΡΠ°Π²Π»ΡΡΡ ΡΡΠ°Π½ΠΊΠΎΠΌ, ΠΊΠ°ΠΊ ΠΈΠ·Π³ΠΎΡΠΎΠ²ΠΈΡΡ ΠΌΠ΅Ρ Π°Π½ΠΈΠΊΡ ΠΈ ΡΠ΄. ΠΈ ΡΠΏ. Π ΠΎΠ±ΡΠ΅ΠΌ, ΡΠ΅ΠΌ Π±ΠΎΠ»ΡΡΠ΅ ΡΠΈΡΠ°Π», ΡΠ΅ΠΌ ΡΡΡΠ°ΡΠ½Π΅Π΅ ΡΡΠ°Π½ΠΎΠ²ΠΈΠ»ΠΎΡΡ, ΠΈ Π²ΡΡ ΡΠ°ΡΠ΅ Π²ΠΎΠ·Π½ΠΈΠΊΠ°Π» Π²ΠΎΠΏΡΠΎΡ Β«Π½Π°ΡΠΈΠ³Π° ΠΌΠ½Π΅ ΡΡΠΎ Π½Π°Π΄ΠΎ?!Β». ΠΠΎ ΠΎΡΡΡΡΠΏΠ°ΡΡ Π±ΡΠ»ΠΎ ΠΏΠΎΠ·Π΄Π½ΠΎ, Π΄Π²ΠΈΠ³Π°ΡΠ΅Π»Ρ Π½Π° ΡΡΠΎΠ»Π΅, Π΄Π΅ΡΠ°Π»ΠΈ Π³Π΄Π΅-ΡΠΎ Π² ΠΏΡΡΠΈ β Π½Π°Π΄ΠΎ ΠΏΡΠΎΠ΄ΠΎΠ»ΠΆΠ°ΡΡ.
ΠΡΠΈΡΠ»ΠΎ Π²ΡΠ΅ΠΌΡ ΠΏΠ°ΡΡΡ ΠΏΠ»Π°ΡΡ. ΠΠΌΠ΅ΡΡΠΈΠ΅ΡΡ Π² ΠΈΠ½ΡΠ΅ΡΠ½Π΅ΡΠ΅ ΠΌΠ½Π΅ Π½Π΅ ΠΏΠΎΠ΄ΠΎΡΠ»ΠΈ ΠΏΠΎ ΡΡΠ΅ΠΌ ΠΏΡΠΈΡΠΈΠ½Π°ΠΌ:
1 — Π ΠΌΠ°Π³Π°Π·ΠΈΠ½Π΅, ΠΊΠΎΡΠΎΡΠΎΠΌ Π·Π°ΠΊΠ°Π·ΡΠ²Π°Π» Π΄Π΅ΡΠ°Π»ΠΈ Π½Π΅ ΠΎΠΊΠ°Π·Π°Π»ΠΎΡΡ IR2104 Π² DIP ΠΊΠΎΡΠΏΡΡΠ°Ρ
, ΠΈ ΠΌΠ½Π΅ ΠΏΡΠΈΡΠ»Π°Π»ΠΈ 8-SOICN. ΠΠ° ΠΏΠ»Π°ΡΡ ΠΎΠ½ΠΈ ΠΏΡΠΈΠΏΠ°ΠΈΠ²Π°ΡΡΡΡ Ρ Π΄ΡΡΠ³ΠΎΠΉ ΡΡΠΎΡΠΎΠ½Ρ, ΠΏΠ΅ΡΠ΅Π²Π΅ΡΠ½ΡΡΡΠ΅, ΠΈ ΡΠΎΠΎΡΠ²Π΅ΡΡΡΠ²Π΅Π½Π½ΠΎ Π½ΡΠΆΠ½ΠΎ Π±ΡΠ»ΠΎ Π·Π΅ΡΠΊΠ°Π»ΠΈΡΡ Π΄ΠΎΡΠΎΠΆΠΊΠΈ, Π° ΠΈΡ
(IR2104) 12 ΡΡΡΠΊ.
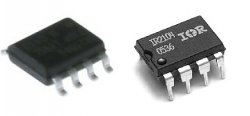
2 — Π Π΅Π·ΠΈΡΡΠΎΡΡ ΠΈ ΠΊΠΎΠ½Π΄Π΅Π½ΡΠ°ΡΠΎΡΡ ΡΠ°ΠΊΠΆΠ΅ Π²Π·ΡΠ» Π² SMD ΠΊΠΎΡΠΏΡΡΠ°Ρ Π΄Π»Ρ ΡΠΌΠ΅Π½ΡΡΠ΅Π½ΠΈΡ ΠΊΠΎΠ»ΠΈΡΠ΅ΡΡΠ²Π° ΠΎΡΠ²Π΅ΡΡΡΠΈΠΉ, ΠΊΠΎΡΠΎΡΡΠ΅ Π½ΡΠΆΠ½ΠΎ Π±ΡΠ»ΠΎ ΡΠ²Π΅ΡΠ»ΠΈΡΡ.
3 — ΠΠΌΠ΅ΡΡΠΈΠΉΡΡ Ρ ΠΌΠ΅Π½Ρ ΡΠ°Π΄ΠΈΠ°ΡΠΎΡ Π±ΡΠ» ΠΌΠ΅Π½ΡΡΠ΅Π³ΠΎ ΡΠ°Π·ΠΌΠ΅ΡΠ° ΠΈ ΠΊΡΠ°ΠΉΠ½ΠΈΠ΅ ΡΡΠ°Π½Π·ΠΈΡΡΠΎΡΡ Π±ΡΠ»ΠΈ Π²Π½Π΅ Π΅Π³ΠΎ ΠΏΠ»ΠΎΡΠ°Π΄ΠΈ. ΠΡΠΆΠ½ΠΎ Π±ΡΠ»ΠΎ ΡΠΌΠ΅ΡΠ°ΡΡ ΠΏΠΎΠ»Π΅Π²ΠΈΠΊΠΈ Π½Π° ΠΎΠ΄Π½ΠΎΠΉ ΠΏΠ»Π°ΡΠ΅ Π²ΠΏΡΠ°Π²ΠΎ, Π° Π½Π° Π΄ΡΡΠ³ΠΎΠΉ Π²Π»Π΅Π²ΠΎ, ΠΏΠΎΡΡΠΎΠΌΡ ΠΈΠ·Π³ΠΎΡΠΎΠ²ΠΈΠ» Π΄Π²Π° Π²ΠΈΠ΄Π° ΠΏΠ»Π°ΡΡ.
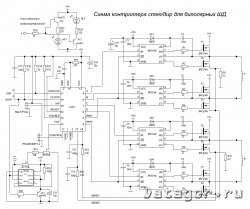
ΠΠ»Ρ Π±Π΅Π·ΠΎΠΏΠ°ΡΠ½ΠΎΡΡΠΈ LPT ΠΏΠΎΡΡΠ°, ΠΊΠΎΠ½ΡΡΠΎΠ»Π»Π΅Ρ ΠΈ ΠΊΠΎΠΌΠΏΡΡΡΠ΅Ρ ΡΠΎΠ΅Π΄ΠΈΠ½ΠΈΠ» ΡΠ΅ΡΠ΅Π· ΠΏΠ»Π°ΡΡ ΠΎΠΏΡΠΎΡΠ°Π·Π²ΡΠ·ΠΊΠΈ. Π‘Ρ Π΅ΠΌΡ ΠΈ ΠΏΠ΅ΡΠ°ΡΠΊΡ Π²Π·ΡΠ» Π½Π° ΠΎΠ΄Π½ΠΎΠΌ ΠΈΠ·Π²Π΅ΡΡΠ½ΠΎΠΌ ΡΠ°ΠΉΡΠ΅, Π½ΠΎ ΠΎΠΏΡΡΡ ΠΆΠ΅ ΠΏΡΠΈΡΠ»ΠΎΡΡ Π½Π΅ΠΌΠ½ΠΎΠ³ΠΎ ΠΏΠ΅ΡΠ΅Π΄Π΅Π»Π°ΡΡ Π΅Ρ ΠΏΠΎΠ΄ ΡΠ΅Π±Ρ ΠΈ ΡΠ±ΡΠ°ΡΡ Π»ΠΈΡΠ½ΠΈΠ΅ Π΄Π΅ΡΠ°Π»ΠΈ.

ΠΠ΄Π½Π° ΡΡΠΎΡΠΎΠ½Π° ΠΏΠ»Π°ΡΡ ΠΏΠΈΡΠ°Π΅ΡΡΡ ΡΠ΅ΡΠ΅Π· USB ΠΏΠΎΡΡ, Π΄ΡΡΠ³Π°Ρ, ΠΏΠΎΠ΄ΠΊΠ»ΡΡΠ΅Π½Π½Π°Ρ ΠΊ ΠΊΠΎΠ½ΡΡΠΎΠ»Π»Π΅ΡΡ — ΠΎΡ ΠΈΡΡΠΎΡΠ½ΠΈΠΊΠ° +5Π². Π‘ΠΈΠ³Π½Π°Π»Ρ ΠΏΠ΅ΡΠ΅Π΄Π°ΡΡΡΡ ΡΠ΅ΡΠ΅Π· ΠΎΠΏΡΡΠΎΠ½Ρ. ΠΡΠ΅ ΠΏΠΎΠ΄ΡΠΎΠ±Π½ΠΎΡΡΠΈ ΠΎ Π½Π°ΡΡΡΠΎΠΉΠΊΠ΅ ΠΊΠΎΠ½ΡΡΠΎΠ»Π»Π΅ΡΠ° ΠΈ ΡΠ°Π·Π²ΡΠ·ΠΊΠΈ Π½Π°ΠΏΠΈΡΡ Π² ΡΡΠ΅ΡΡΠ΅ΠΉ Π³Π»Π°Π²Π΅, Π·Π΄Π΅ΡΡ ΠΆΠ΅ ΡΠΏΠΎΠΌΡΠ½Ρ ΡΠΎΠ»ΡΠΊΠΎ ΠΎΡΠ½ΠΎΠ²Π½ΡΠ΅ ΠΌΠΎΠΌΠ΅Π½ΡΡ. ΠΠ°Π½Π½Π°Ρ ΠΏΠ»Π°ΡΠ° ΡΠ°Π·Π²ΡΠ·ΠΊΠΈ ΠΏΡΠ΅Π΄Π½Π°Π·Π½Π°ΡΠ΅Π½Π° Π΄Π»Ρ Π±Π΅Π·ΠΎΠΏΠ°ΡΠ½ΠΎΠ³ΠΎ ΠΏΠΎΠ΄ΠΊΠ»ΡΡΠ΅Π½ΠΈΡ ΠΊΠΎΠ½ΡΡΠΎΠ»Π»Π΅ΡΠ° ΡΠ°Π³ΠΎΠ²ΠΎΠ³ΠΎ Π΄Π²ΠΈΠ³Π°ΡΠ΅Π»Ρ ΠΊ LPT ΠΏΠΎΡΡΡ ΠΊΠΎΠΌΠΏΡΡΡΠ΅ΡΠ°. ΠΠΎΠ»Π½ΠΎΡΡΡΡ ΡΠ»Π΅ΠΊΡΡΠΈΡΠ΅ΡΠΊΠΈ ΠΈΠ·ΠΎΠ»ΠΈΡΡΠ΅Ρ ΠΏΠΎΡΡ ΠΊΠΎΠΌΠΏΡΡΡΠ΅ΡΠ° ΠΎΡ ΡΠ»Π΅ΠΊΡΡΠΎΠ½ΠΈΠΊΠΈ ΡΡΠ°Π½ΠΊΠ°, ΠΈ ΠΏΠΎΠ·Π²ΠΎΠ»ΡΠ΅Ρ ΡΠΏΡΠ°Π²Π»ΡΡΡ 4-Ρ ΠΎΡΠ΅Π²ΡΠΌ Π§ΠΠ£ ΡΡΠ°Π½ΠΊΠΎΠΌ. ΠΡΠ»ΠΈ ΡΡΠ°Π½ΠΎΠΊ ΠΈΠΌΠ΅Π΅Ρ ΡΠΎΠ»ΡΠΊΠΎ ΡΡΠΈ ΠΎΡΠΈ, ΠΊΠ°ΠΊ Π² Π½Π°ΡΠ΅ΠΌ ΡΠ»ΡΡΠ°Π΅, Π½Π΅Π½ΡΠΆΠ½ΡΠ΅ Π΄Π΅ΡΠ°Π»ΠΈ ΠΌΠΎΠΆΠ½ΠΎ ΠΎΡΡΠ°Π²ΠΈΡΡ Π²ΠΈΡΠ΅ΡΡ Π² Π²ΠΎΠ·Π΄ΡΡ Π΅, Π»ΠΈΠ±ΠΎ Π²ΠΎΠΎΠ±ΡΠ΅ ΠΈΡ Π½Π΅ Π²ΠΏΠ°ΠΈΠ²Π°ΡΡ. ΠΠΌΠ΅Π΅ΡΡΡ Π²ΠΎΠ·ΠΌΠΎΠΆΠ½ΠΎΡΡΡ ΠΏΠΎΠ΄ΠΊΠ»ΡΡΠ΅Π½ΠΈΡ ΠΊΠΎΠ½ΡΠ΅Π²ΡΡ Π΄Π°ΡΡΠΈΠΊΠΎΠ², ΠΊΠ½ΠΎΠΏΠΊΠΈ ΠΏΡΠΈΠ½ΡΠ΄ΠΈΡΠ΅Π»ΡΠ½ΠΎΠΉ ΠΎΡΡΠ°Π½ΠΎΠ²ΠΊΠΈ, ΡΠ΅Π»Π΅ Π²ΠΊΠ»ΡΡΠ΅Π½ΠΈΡ ΡΠΏΠΈΠ½Π΄Π΅Π»Ρ ΠΈ Π΄ΡΡΠ³ΠΎΠ³ΠΎ ΡΡΡΡΠΎΠΉΡΡΠ²Π°, Π½Π°ΠΏΡΠΈΠΌΠ΅Ρ ΠΏΡΠ»Π΅ΡΠΎΡΠ°.
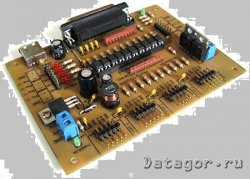
ΠΡΠΎ Π±ΡΠ»ΠΎ ΡΠΎΡΠΎ ΠΏΠ»Π°ΡΡ ΠΎΠΏΡΠΎΡΠ°Π·Π²ΡΠ·ΠΊΠΈ Π²Π·ΡΡΠΎΠ΅ ΠΈΠ· ΠΈΠ½ΡΠ΅ΡΠ½Π΅ΡΠ°, Π° Π²ΠΎΡ ΡΠ°ΠΊ Π²ΡΠ³Π»ΡΠ΄ΠΈΡ ΠΌΠΎΠΉ ΠΎΠ³ΠΎΡΠΎΠ΄ ΠΏΠΎΡΠ»Π΅ ΡΡΡΠ°Π½ΠΎΠ²ΠΊΠΈ Π² ΠΊΠΎΡΠΏΡΡ. ΠΠ²Π΅ ΠΏΠ»Π°ΡΡ ΠΈ ΠΊΡΡΠ° ΠΏΡΠΎΠ²ΠΎΠ΄ΠΎΠ². ΠΠΎ Π²ΡΠΎΠ΄Π΅ Π±Ρ Π½Π°Π²ΠΎΠ΄ΠΎΠΊ Π½ΠΈΠΊΠ°ΠΊΠΈΡ Π½Π΅Ρ, ΠΈ Π²ΡΡ ΡΠ°Π±ΠΎΡΠ°Π΅Ρ Π±Π΅Π· ΠΎΡΠΈΠ±ΠΎΠΊ.
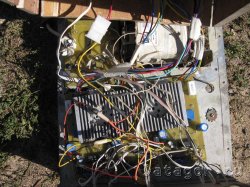
ΠΠ΅ΡΠ²Π°Ρ ΠΏΠ»Π°ΡΠ° ΠΊΠΎΠ½ΡΡΠΎΠ»Π»Π΅ΡΠ° Π³ΠΎΡΠΎΠ²Π°, Π²ΡΡ ΠΏΡΠΎΠ²Π΅ΡΠΈΠ» ΠΈ ΠΏΠΎΡΠ°Π³ΠΎΠ²ΠΎ ΠΏΡΠΎΡΠ΅ΡΡΠΈΡΠΎΠ²Π°Π», ΠΊΠ°ΠΊ Π² ΠΈΠ½ΡΡΡΡΠΊΡΠΈΠΈ. ΠΠΎΠ΄ΡΡΡΠΎΠ΅ΡΠ½ΠΈΠΊΠΎΠΌ Π²ΡΡΡΠ°Π²ΠΈΠ» Π½Π΅Π±ΠΎΠ»ΡΡΠΎΠΉ ΡΠΎΠΊ (ΡΡΠΎ Π²ΠΎΠ·ΠΌΠΎΠΆΠ½ΠΎ Π±Π»Π°Π³ΠΎΠ΄Π°ΡΡ Π½Π°Π»ΠΈΡΠΈΡ Π¨ΠΠ), ΠΈ ΠΏΠΎΠ΄ΠΊΠ»ΡΡΠΈΠ» ΠΏΠΈΡΠ°Π½ΠΈΠ΅ (Π΄Π²ΠΈΠ³Π°ΡΠ΅Π»Π΅ΠΉ) ΡΠ΅ΡΠ΅Π· ΡΠ΅ΠΏΠΎΡΠΊΡ Π»Π°ΠΌΠΏΠΎΡΠ΅ΠΊ 12+24Π², ΡΡΠΎΠ±Ρ Π±ΡΠ»ΠΎ Β«Π½ΠΈΡΡ, Π΅ΡΠ»ΠΈ ΡΡΒ». Π£ ΠΌΠ΅Π½Ρ ΠΆΠ΅ ΠΏΠΎΠ»Π΅Π²ΠΈΠΊΠΈ ΡΡΠΎΡΡ Π±Π΅Π· ΡΠ°Π΄ΠΈΠ°ΡΠΎΡΠ°.
ΠΠ²ΠΈΠ³Π°ΡΠ΅Π»Ρ Π·Π°ΡΠΈΠΏΠ΅Π». Π₯ΠΎΡΠΎΡΠ°Ρ Π½ΠΎΠ²ΠΎΡΡΡ, Π·Π½Π°ΡΠΈΡ Π¨ΠΠ ΡΠ°Π±ΠΎΡΠ°Π΅Ρ ΠΊΠ°ΠΊ Π½Π°Π΄ΠΎ. ΠΠ°ΠΆΠΈΠΌΠ°Ρ ΠΊΠ»Π°Π²ΠΈΡΡ ΠΈ ΠΎΠ½ ΠΊΡΡΡΠΈΡΡΡ! ΠΠ°Π±ΡΠ» ΡΠΏΠΎΠΌΡΠ½ΡΡΡ, ΡΡΠΎ ΡΡΠΎΡ ΠΊΠΎΠ½ΡΡΠΎΠ»Π»Π΅Ρ ΠΏΡΠ΅Π΄Π½Π°Π·Π½Π°ΡΠ΅Π½ Π΄Π»Ρ ΡΠΏΡΠ°Π²Π»Π΅Π½ΠΈΡ Π±ΠΈΠΏΠΎΠ»ΡΡΠ½ΡΠΌ ΡΠ°Π³ΠΎΠ²ΡΠΌ Π΄Π²ΠΈΠ³Π°ΡΠ΅Π»Π΅ΠΌ Ρ.Π΅. ΡΠ΅ΠΌ, Ρ ΠΊΠΎΡΠΎΡΠΎΠ³ΠΎ ΠΏΠΎΠ΄ΠΊΠ»ΡΡΠ°ΡΡΡΡ 4 ΠΏΡΠΎΠ²ΠΎΠ΄Π°. ΠΠ³ΡΠ°Π»ΡΡ Ρ ΡΠ΅ΠΆΠΈΠΌΠ°ΠΌΠΈ ΡΠ°Π³/ΠΏΠΎΠ»ΡΡΠ°Π³, ΡΠΎΠΊΠΎΠΌ. Π ΡΠ΅ΠΆΠΈΠΌΠ΅ ΠΏΠΎΠ»ΡΡΠ°Π³ Π΄Π²ΠΈΠ³Π°ΡΠ΅Π»Ρ Π²Π΅Π΄ΡΡ ΡΠ΅Π±Ρ ΡΡΠ°Π±ΠΈΠ»ΡΠ½Π΅Π΅ ΠΈ ΡΠ°Π·Π²ΠΈΠ²Π°Π΅Ρ Π±ΠΎΠ»ΡΡΠΈΠ΅ ΠΎΠ±ΠΎΡΠΎΡΡ + ΡΠ²Π΅Π»ΠΈΡΠΈΠ²Π°Π΅ΡΡΡ ΡΠΎΡΠ½ΠΎΡΡΡ. Π’Π°ΠΊ ΠΈ ΠΎΡΡΠ°Π²ΠΈΠ» ΠΏΠ΅ΡΠ΅ΠΌΡΡΠΊΡ Π² Β«ΠΏΠΎΠ»ΡΡΠ°Π³Π΅Β». Π‘ ΠΌΠ°ΠΊΡΠΈΠΌΠ°Π»ΡΠ½ΡΠΌ Π±Π΅Π·ΠΎΠΏΠ°ΡΠ½ΡΠΌ Π΄Π»Ρ Π΄Π²ΠΈΠ³Π°ΡΠ΅Π»Ρ ΡΠΎΠΊΠΎΠΌ ΠΏΡΠΈ Π½Π°ΠΏΡΡΠΆΠ΅Π½ΠΈΠΈ ΠΏΡΠΈΠΌΠ΅ΡΠ½ΠΎ 30Π² ΠΏΠΎΠ»ΡΡΠΈΠ»ΠΎΡΡ ΡΠ°ΡΠΊΡΡΡΠΈΡΡ Π΄Π²ΠΈΠ³Π°ΡΠ΅Π»Ρ Π΄ΠΎ 2500 ΠΎΠ±/ΠΌΠΈΠ½! ΠΠΎΠ΅ΠΌΡ ΠΏΠ΅ΡΠ²ΠΎΠΌΡ ΡΡΠ°Π½ΠΊΡ Π±Π΅Π· Π¨ΠΠ ΡΠ°ΠΊΠΎΠ΅ ΠΈ Π½Π΅ ΡΠ½ΠΈΠ»ΠΎΡΡ. ))
Π‘Π»Π΅Π΄ΡΡΡΠΈΠ΅ Π΄Π²Π° ΠΌΠΎΡΠΎΡΠ° Π·Π°ΠΊΠ°Π·Π°Π» ΠΏΠΎΠΌΠΎΡΠ½Π΅Π΅, Nema Π½Π° 18ΠΊΠ³/Ρ, Π½ΠΎ ΡΠΆΠ΅ Β«made in ChinaΒ».
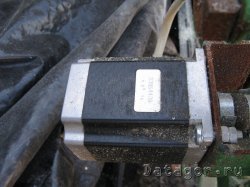
ΠΠΎ ΠΊΠ°ΡΠ΅ΡΡΠ²Ρ ΠΎΠ½ΠΈ ΡΡΡΡΠΏΠ°ΡΡ Vexta, Π²ΡΡ-ΡΠ°ΠΊΠΈ ΠΠΈΡΠ°ΠΉ ΠΈ Π―ΠΏΠΎΠ½ΠΈΡ ΡΠ°Π·Π½ΡΠ΅ Π²Π΅ΡΠΈ. ΠΠΎΠ³Π΄Π° Π²ΡΠ°ΡΠ°Π΅ΡΡ Π²Π°Π» ΡΡΠΊΠΎΠΉ Ρ ΡΠΏΠΎΠ½ΡΠ° ΡΡΠΎ ΠΏΡΠΎΠΈΡΡ ΠΎΠ΄ΠΈΡ ΠΊΠ°ΠΊ-ΡΠΎ ΠΌΡΠ³ΠΊΠΎ, Π° ΠΎΡ ΠΊΠΈΡΠ°ΠΉΡΠ΅Π² ΠΎΡΡΡΠ΅Π½ΠΈΠ΅ Π΄ΡΡΠ³ΠΎΠ΅, Π½ΠΎ Π½Π° ΡΠ°Π±ΠΎΡΠ΅ ΡΡΠΎ ΠΏΠΎΠΊΠ° ΡΡΠΎ Π½ΠΈΠΊΠ°ΠΊ Π½Π΅ ΡΠΊΠ°Π·Π°Π»ΠΎΡΡ. ΠΠ°ΠΌΠ΅ΡΠ°Π½ΠΈΠΉ ΠΊ Π½ΠΈΠΌ Π½Π΅Ρ.
Π‘ΠΏΠ°ΡΠ» Π΄Π²Π΅ ΠΎΡΡΠ°Π²ΡΠΈΠ΅ΡΡ ΠΏΠ»Π°ΡΡ, ΠΏΡΠΎΠ²Π΅ΡΠΈΠ» ΡΠ΅ΡΠ΅Π· Β«ΡΠ²Π΅ΡΠΎΠ΄ΠΈΠΎΠ΄Π½ΡΠΉ ΡΠΈΠΌΡΠ»ΡΡΠΎΡ ΡΠ°Π³ΠΎΠ²ΠΎΠ³ΠΎ Π΄Π²ΠΈΠ³Π°ΡΠ΅Π»ΡΒ», Π²ΡΠΎΠ΄Π΅ Π±Ρ Π²ΡΡ Ρ ΠΎΡΠΎΡΠΎ. ΠΠΎΠ΄ΠΊΠ»ΡΡΠ°Ρ ΠΎΠ΄ΠΈΠ½ ΠΌΠΎΡΠΎΡ β ΡΠ°Π±ΠΎΡΠ°Π΅Ρ ΠΎΡΠ»ΠΈΡΠ½ΠΎ, Π½ΠΎ ΡΠΆΠ΅ Π½Π΅ 2500 ΠΎΠ±ΠΎΡΠΎΡΠΎΠ², Π° ΠΎΠΊΠΎΠ»ΠΎ 3000! ΠΠΎ ΡΠΆΠ΅ ΠΎΡΡΠ°Π±ΠΎΡΠ°Π½Π½ΠΎΠΉ ΡΡ Π΅ΠΌΠ΅ ΠΏΠΎΠ΄ΠΊΠ»ΡΡΠ°Ρ ΡΡΠ΅ΡΠΈΠΉ ΠΌΠΎΡΠΎΡ ΠΊ ΡΡΠ΅ΡΠ΅ΠΉ ΠΏΠ»Π°ΡΠ΅, ΠΊΡΡΡΠΈΡΡΡ ΠΏΠ°ΡΡ ΡΠ΅ΠΊΡΠ½Π΄ ΠΈ Π²ΡΡΠ°Π»β¦ Π‘ΠΌΠΎΡΡΡ ΠΎΡΡΠΈΠ»Π»ΠΎΠΌ β Π½Π° ΠΎΠ΄Π½ΠΎΠΌ Π²ΡΠ²ΠΎΠ΄Π΅ ΠΈΠΌΠΏΡΠ»ΡΡΠΎΠ² Π½Π΅Ρ. ΠΡΠΎΠ·Π²Π°Π½ΠΈΠ²Π°Ρ ΠΏΠ»Π°ΡΡ β ΠΎΠ΄Π½Π° ΠΈΠ· IR2104 ΠΏΡΠΎΠ±ΠΈΡΠ°.
ΠΡ Π»Π°Π΄Π½ΠΎ, ΠΌΠΎΠΆΠ΅Ρ Π±ΡΠ°ΠΊΠΎΠ²Π°Π½Π½Π°Ρ ΠΏΠΎΠΏΠ°Π»Π°ΡΡ, ΡΠΈΡΠ°Π» ΡΡΠΎ ΡΠ°ΡΡΠΎ ΡΠ°ΠΊΠΎΠ΅ Π±ΡΠ²Π°Π΅Ρ Ρ ΡΡΠΎΠΉ ΠΌΠΈΠΊΡΡΡ
ΠΎΠΉ. ΠΠΏΠ°ΠΈΠ²Π°Ρ Π½ΠΎΠ²ΡΡ (Π±ΡΠ°Π» Ρ Π·Π°ΠΏΠ°ΡΠΎΠΌ 2 ΡΡΡΠΊΠΈ), ΡΠ° ΠΆΠ΅ Π΅ΡΡΠ½Π΄Π° β ΠΏΠ°ΡΡ ΡΠ΅ΠΊΡΠ½Π΄ ΠΊΡΡΡΠΈΡ ΠΈ STOP! Π’ΡΡ Ρ ΠΏΠΎΠ΄Π½Π°ΠΏΡΡΠ³ΡΡ, ΠΈ Π΄Π°Π²Π°ΠΉ ΠΏΡΠΎΠ²Π΅ΡΡΡΡ ΠΏΠΎΠ»Π΅Π²ΠΈΠΊΠΈ. ΠΡΡΠ°ΡΠΈ, Π² ΠΌΠΎΠ΅ΠΉ ΠΏΠ»Π°ΡΠ΅ ΡΡΡΠ°Π½ΠΎΠ²Π»Π΅Π½Ρ IRF530 (100Π/17Π) ΠΏΡΠΎΡΠΈΠ² IRFZ44 (50Π/49Π), ΠΊΠ°ΠΊ Π² ΠΎΡΠΈΠ³ΠΈΠ½Π°Π»Π΅. ΠΠ° ΠΌΠΎΡΠΎΡ Π±ΡΠ΄Π΅Ρ ΠΈΠ΄ΡΠΈ ΠΌΠ°ΠΊΡΠΈΠΌΡΠΌ 3Π, ΡΠ°ΠΊ ΡΡΠΎ Π·Π°ΠΏΠ°ΡΠ° Π² 14Π Ρ
Π²Π°ΡΠΈΡ Ρ ΠΈΠ·Π±ΡΡΠΊΠΎΠΌ, Π° Π²ΠΎΡ ΡΠ°Π·Π½ΠΈΡΠ° Π² ΡΠ΅Π½Π΅ ΠΏΠΎΡΡΠΈ Π² 2 ΡΠ°Π·Π° Π² ΠΏΠΎΠ»ΡΠ·Ρ 530-ΡΡ
.
Π’Π°ΠΊ Π²ΠΎΡ, ΠΏΡΠΎΠ²Π΅ΡΡΡ ΠΏΠΎΠ»Π΅Π²ΠΈΠΊΠΈ ΠΈ ΡΡΠΎ Ρ Π²ΠΈΠΆΡβ¦Π½Π΅ ΠΏΡΠΈΠΏΠ°ΡΠ» ΠΎΠ΄Π½Ρ Π½ΠΎΠΆΠΊΡ! Π Π½Π° Π²ΡΡ
ΠΎΠ΄ ΡΡΠΎΠΉ «ΠΈΡΠΊΠΈ» ΠΏΠΎΠ»Π΅ΡΠ΅Π»ΠΈ Π²ΡΠ΅ 30Π Ρ ΠΏΠΎΠ»Π΅Π²ΠΈΠΊΠ°. ΠΡΠΈΠΏΠ°ΡΠ» Π½ΠΎΠΆΠΊΡ, Π΅ΡΡ ΡΠ°Π· Π²Π½ΠΈΠΌΠ°ΡΠ΅Π»ΡΠ½ΠΎ Π²ΡΡ ΠΎΡΠΌΠΎΡΡΠ΅Π», ΡΡΠ°Π²Π»Ρ Π΅ΡΡ ΠΎΠ΄Π½Ρ IR2104, ΡΠ°ΠΌ Π²ΠΎΠ»Π½ΡΡΡΡ β ΡΡΠΎ ΠΆΠ΅ ΠΏΠΎΡΠ»Π΅Π΄Π½ΡΡ. ΠΠΊΠ»ΡΡΠΈΠ» ΠΈ Π±ΡΠ» ΠΎΡΠ΅Π½Ρ ΡΡΠ°ΡΡΠ»ΠΈΠ², ΠΊΠΎΠ³Π΄Π° Π΄Π²ΠΈΠ³Π°ΡΠ΅Π»Ρ Π½Π΅ ΠΎΡΡΠ°Π½ΠΎΠ²ΠΈΡΡΡ ΠΏΠΎΡΠ»Π΅ Π΄Π²ΡΡ
ΡΠ΅ΠΊΡΠ½Π΄ ΡΠ°Π±ΠΎΡΡ. Π Π΅ΠΆΠΈΠΌΡ ΠΎΡΡΠ°Π²ΠΈΠ» ΡΠ°ΠΊΠΈΠ΅: Π΄Π²ΠΈΠ³Π°ΡΠ΅Π»Ρ Vexta β 1,5Π, Π΄Π²ΠΈΠ³Π°ΡΠ΅Π»Ρ NEMA 2,5Π. ΠΡΠΈ ΡΠ°ΠΊΠΎΠΌ ΡΠΎΠΊΠ΅ Π΄ΠΎΡΡΠΈΠ³Π°ΡΡΡΡ ΠΎΠ±ΠΎΡΠΎΡΡ ΠΏΡΠΈΠΌΠ΅ΡΠ½ΠΎ 2000, Π½ΠΎ Π»ΡΡΡΠ΅ ΠΎΠ³ΡΠ°Π½ΠΈΡΠΈΡΡ ΠΈΡ
ΠΏΡΠΎΠ³ΡΠ°ΠΌΠΌΠ½ΠΎ Π²ΠΎ ΠΈΠ·Π±Π΅ΠΆΠ°Π½ΠΈΠΈ ΠΏΡΠΎΠΏΡΡΠΊΠ° ΡΠ°Π³ΠΎΠ², ΠΈ ΡΠ΅ΠΌΠΏΠ΅ΡΠ°ΡΡΡΠ° Π΄Π²ΠΈΠ³Π°ΡΠ΅Π»Π΅ΠΉ ΠΏΡΠΈ Π΄Π»ΠΈΡΠ΅Π»ΡΠ½ΠΎΠΉ ΡΠ°Π±ΠΎΡΠ΅ Π½Π΅ ΠΏΡΠ΅Π²ΡΡΠ°Π΅Ρ Π±Π΅Π·ΠΎΠΏΠ°ΡΠ½ΡΡ Π΄Π»Ρ ΠΌΠΎΡΠΎΡΠΎΠ². Π’ΡΠ°Π½ΡΡΠΎΡΠΌΠ°ΡΠΎΡ ΠΏΠΈΡΠ°Π½ΠΈΡ ΡΠΏΡΠ°Π²Π»ΡΠ΅ΡΡΡ Π±Π΅Π· ΠΏΡΠΎΠ±Π»Π΅ΠΌ, Π²Π΅Π΄Ρ ΠΎΠ±ΡΡΠ½ΠΎ ΠΎΠ΄Π½ΠΎΠ²ΡΠ΅ΠΌΠ΅Π½Π½ΠΎ ΠΊΡΡΡΡΡΡΡ ΡΠΎΠ»ΡΠΊΠΎ 2 ΠΌΠΎΡΠΎΡΠ°, Π½ΠΎ ΡΠ°Π΄ΠΈΠ°ΡΠΎΡΡ ΠΆΠ΅Π»Π°ΡΠ΅Π»ΡΠ½ΠΎ Π΄ΠΎΠΏΠΎΠ»Π½ΠΈΡΠ΅Π»ΡΠ½ΠΎΠ΅ Π²ΠΎΠ·Π΄ΡΡΠ½ΠΎΠ΅ ΠΎΡ
Π»Π°ΠΆΠ΄Π΅Π½ΠΈΠ΅.
Π’Π΅ΠΏΠ΅ΡΡ ΠΏΡΠΎ ΡΡΡΠ°Π½ΠΎΠ²ΠΊΡ ΠΏΠΎΠ»Π΅Π²ΠΈΠΊΠΎΠ² Π½Π° ΡΠ°Π΄ΠΈΠ°ΡΠΎΡ, Π° ΠΈΡ
24 ΡΡΡΠΊΠΈ, Π΅ΡΠ»ΠΈ ΠΊΡΠΎ Π½Π΅ Π·Π°ΠΌΠ΅ΡΠΈΠ». Π ΡΡΠΎΠΌ Π²Π°ΡΠΈΠ°Π½ΡΠ΅ ΠΏΠ»Π°ΡΡ ΠΎΠ½ΠΈ ΡΠ°ΡΠΏΠΎΠ»ΠΎΠΆΠ΅Π½Ρ Π»Π΅ΠΆΠ°, Ρ.Π΅. ΡΠ°Π΄ΠΈΠ°ΡΠΎΡ ΠΏΡΠΎΡΡΠΎ Π½Π° Π½ΠΈΡ
Π»ΠΎΠΆΠΈΡΡΡ ΠΈ ΡΠ΅ΠΌ-Π»ΠΈΠ±ΠΎ ΠΏΡΠΈΡΡΠ³ΠΈΠ²Π°Π΅ΡΡΡ.
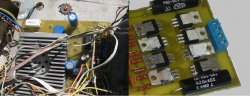
ΠΠΎΠ½Π΅ΡΠ½ΠΎ, ΠΆΠ΅Π»Π°ΡΠ΅Π»ΡΠ½ΠΎ ΠΏΠΎΠ»ΠΎΠΆΠΈΡΡ ΡΠΏΠ»ΠΎΡΠ½ΠΎΠΉ ΠΊΡΡΠΎΠΊ ΡΠ»ΡΠ΄Ρ Π΄Π»Ρ ΠΈΠ·ΠΎΠ»ΡΡΠΈΠΈ ΡΠ°Π΄ΠΈΠ°ΡΠΎΡΠ° ΠΎΡ ΡΡΠ°Π½Π·ΠΈΡΡΠΎΡΠΎΠ², Π½ΠΎ Ρ ΠΌΠ΅Π½Ρ Π΅Π³ΠΎ Π½Π΅ Π±ΡΠ»ΠΎ. ΠΡΡ ΠΎΠ΄ Π½Π°ΡΠ΅Π» ΡΠ°ΠΊΠΎΠΉ. Π’.ΠΊ. Ρ ΠΏΠΎΠ»ΠΎΠ²ΠΈΠ½Ρ ΡΡΠ°Π½Π·ΠΈΡΡΠΎΡΠΎΠ² ΠΊΠΎΡΠΏΡΡ ΠΈΠ΄ΡΡ Π½Π° ΠΏΠ»ΡΡ ΠΏΠΈΡΠ°Π½ΠΈΡ ΠΈΡ ΠΌΠΎΠΆΠ½ΠΎ ΠΊΡΠ΅ΠΏΠΈΡΡ Π±Π΅Π· ΠΈΠ·ΠΎΠ»ΡΡΠΈΠΈ, ΠΏΡΠΎΡΡΠΎ Π½Π° ΡΠ΅ΡΠΌΠΎΠΏΠ°ΡΡΡ. Π ΠΏΠΎΠ΄ ΠΎΡΡΠ°Π²ΡΠΈΠ΅ΡΡ Ρ ΠΏΠΎΠ»ΠΎΠΆΠΈΠ» ΠΊΡΡΠΎΡΠΊΠΈ ΡΠ»ΡΠ΄Ρ, ΠΎΡΡΠ°Π²ΡΠΈΠ΅ΡΡ ΠΎΡ ΡΠΎΠ²Π΅ΡΡΠΊΠΈΡ ΡΡΠ°Π½Π·ΠΈΡΡΠΎΡΠΎΠ². Π Π°Π΄ΠΈΠ°ΡΠΎΡ ΠΈ ΠΏΠ»Π°ΡΡ ΠΏΡΠΎΡΠ²Π΅ΡΠ»ΠΈΠ» Π² ΡΡΠ΅Ρ ΠΌΠ΅ΡΡΠ°Ρ Π½Π°ΡΠΊΠ²ΠΎΠ·Ρ ΠΈ ΡΡΡΠ½ΡΠ» Π±ΠΎΠ»ΡΠΈΠΊΠ°ΠΌΠΈ. ΠΠ΄Π½Ρ Π±ΠΎΠ»ΡΡΡΡ ΠΏΠ»Π°ΡΡ Ρ ΠΏΠΎΠ»ΡΡΠΈΠ» ΠΏΡΡΠ΅ΠΌ ΡΠΏΠ°ΠΈΠ²Π°Π½ΠΈΡ ΡΡΠ΅Ρ ΠΎΡΠ΄Π΅Π»ΡΠ½ΡΡ ΠΏΠ»Π°Ρ ΠΏΠΎ ΠΊΡΠ°ΡΠΌ, ΠΏΡΠΈ ΡΡΠΎΠΌ Π΄Π»Ρ ΠΏΡΠΎΡΠ½ΠΎΡΡΠΈ Π²ΠΏΠ°ΡΠ» ΠΏΠΎ ΠΏΠ΅ΡΠΈΠΌΠ΅ΡΡΡ ΠΌΠ΅Π΄Π½ΡΠΉ ΠΏΡΠΎΠ²ΠΎΠ΄ 1ΠΌΠΌ. ΠΡΡ ΡΠ»Π΅ΠΊΡΡΠΎΠ½Π½ΡΡ Π½Π°ΡΠΈΠ½ΠΊΡ ΠΈ Π±Π»ΠΎΠΊ ΠΏΠΈΡΠ°Π½ΠΈΡ ΡΠ°Π·ΠΌΠ΅ΡΡΠΈΠ» Π½Π° ΠΊΠ°ΠΊΠΎΠΌβΡΠΎ ΠΆΠ΅Π»Π΅Π·Π½ΠΎΠΌ ΡΠ°ΡΡΠΈ, Π΄Π°ΠΆΠ΅ Π½Π΅ Π·Π½Π°Ρ ΠΎΡ ΡΠ΅Π³ΠΎ.
ΠΠΎΠΊΠΎΠ²ΡΠ΅ ΠΈ Π²Π΅ΡΡ
Π½ΡΡ ΠΊΡΡΡΠΊΡ Π²ΡΡΠ΅Π·Π°Π» ΠΈΠ· ΡΠ°Π½Π΅ΡΡ, ΠΈ ΡΠ²Π΅ΡΡ
Ρ ΠΏΠΎΡΡΠ°Π²ΠΈΠ» Π²Π΅Π½ΡΠΈΠ»ΡΡΠΎΡ.
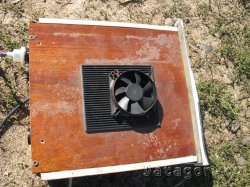
Π Π»ΠΈΡΠ΅Π²ΠΎΠΉ ΠΏΠ°Π½Π΅Π»ΠΈ ΠΏΡΠΎΡΠ²Π΅ΡΠ»ΠΈΠ» ΠΎΡΠ²Π΅ΡΡΡΠΈΡ ΠΏΠΎΠ΄ ΠΌΠ½ΠΎΠ³ΠΎΡΠΈΡΠ»Π΅Π½Π½ΡΠ΅ ΡΠ²Π΅ΡΠΎΠ΄ΠΈΠΎΠ΄Ρ ΠΈΠ½Π΄ΠΈΠΊΠ°ΡΠΈΠΈ ΡΠ΅ΠΆΠΈΠΌΠΎΠ² ΡΠ°Π±ΠΎΡΡ.
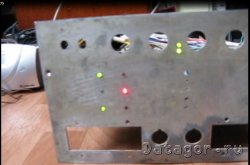
ΠΠ»Ρ Π±ΡΡΡΡΠΎ ΠΏΠΎΠ΄ΠΊΠ»ΡΡΠ΅Π½ΠΈΡ/ΠΎΡΠΊΠ»ΡΡΠ΅Π½ΠΈΡ Π΄Π²ΠΈΠ³Π°ΡΠ΅Π»Π΅ΠΉ ΠΈ Π±Π»ΠΎΠΊΠ° ΡΠΏΡΠ°Π²Π»Π΅Π½ΠΈΡ ΠΈΡΠΏΠΎΠ»ΡΠ·ΠΎΠ²Π°Π» ΡΠ°Π·ΡΡΠΌΡ ΠΈΠ· ΠΏΡΠΎΡΠ»ΠΎΠ³ΠΎ ΡΡΡΡΡΠ΅Π»Π΅ΡΠΈΡ. Π ΠΊΠΎΠ½ΡΠ°ΠΊΡ Ρ ΠΎΡΠΎΡΠΈΠΉ ΠΈ Π½ΡΠΆΠ½ΡΠΉ ΡΠΎΠΊ Π΄Π΅ΡΠΆΠ°Ρ Π±Π΅Π· ΠΊΠ°ΠΊΠΈΡ -Π»ΠΈΠ±ΠΎ ΠΏΠΎΡΠ»Π΅Π΄ΡΡΠ²ΠΈΠΉ Π΄Π»Ρ ΡΠ΅Π±Ρ.
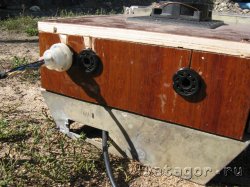
ΠΠ»Ρ ΡΠΎΠ³ΠΎ, ΡΡΠΎΠ±Ρ Π½Π΅ Π·Π°ΠΏΡΡΠ°ΡΡΡΡ Π³Π΄Π΅ ΠΊΠ°ΠΊΠΎΠΉ ΠΈΠ½Π΄ΠΈΠΊΠ°ΡΠΎΡ ΠΈ ΡΡΠΌΠ±Π»Π΅Ρ, Π½Π°ΡΠΈΡΠΎΠ²Π°Π», ΠΏΡΠΈΠΊΠ»Π΅ΠΈΠ» ΡΠ°ΠΊΡΡ Π±ΡΠΌΠ°ΠΆΠΊΡ, ΠΏΡΠΎΠΏΡΡΠ΅Π½Π½ΡΡ ΡΠ΅ΡΠ΅Π· Π»Π°ΠΌΠΈΠ½Π°ΡΠΎΡ.
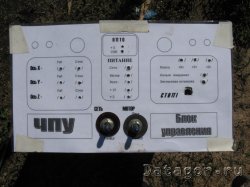
ΠΠ»Π΅ΠΊΡΡΠΎΠ½Π½Π°Ρ ΡΠ°ΡΡΡ Π·Π°ΠΊΠΎΠ½ΡΠΈΠ»Π°ΡΡ. Π‘Π»Π΅Π΄ΡΡΡΠ°Ρ Π³Π»Π°Π²Π° ΠΏΠΎΠ»Π½ΠΎΡΡΡΡ ΠΏΠΎΡΠ²ΡΡΠ΅Π½Π° ΠΆΠ΅Π»Π΅Π·ΡΠΊΠ°ΠΌ. ΠΠΎ Π²ΡΡΡΠ΅ΡΠΈ!
ΠΡΠ΅ ΠΌΠ°ΡΠ΅ΡΠΈΠ°Π»Ρ Π½Π°ΠΉΠ΄Π΅Π½Ρ Π² ΡΠ²ΠΎΠ±ΠΎΠ΄Π½ΠΎΠΌ Π΄ΠΎΡΡΡΠΏΠ΅ Π½Π° ΠΏΡΠΎΡΡΠΎΡΠ°Ρ Π‘Π΅ΡΠΈ. Π£ ΠΊΠ°ΠΆΠ΄ΠΎΠΉ ΡΡ Π΅ΠΌΡ Π΅ΡΡΡ Π°Π²ΡΠΎΡ ΠΈ Π½Π΅ Ρ ΠΎΡΠ΅ΡΡΡ Π½ΠΈΠΊΠΎΠ³ΠΎ ΠΎΠ±ΠΈΠ΄Π΅ΡΡ — Π½Π° Π°Π²ΡΠΎΡΡΡΠ²ΠΎ Π½ΠΈΠΊΠ°ΠΊ Π½Π΅ ΠΏΡΠ΅ΡΠ΅Π½Π΄ΡΡ.
ΠΠΈΠΆΠ΅ ΡΠ΅ΡΡΠ΅ΠΆΠΈ ΠΏΠ»Π°ΡΡ ΡΠ°Π·Π²ΡΠ·ΠΊΠΈ ΠΈ ΡΠ°ΠΌΠΎΠ³ΠΎ ΠΊΠΎΠ½ΡΡΠΎΠ»Π»Π΅ΡΠ°, ΠΏΠΎΠ΄ΡΡΡΠΎΠ΅Π½Π½ΡΠ΅ ΠΏΠΎΠ΄ ΡΠ΅Π±Ρ.
βΌ Π€Π°ΠΉΠ»ΠΎΠ²ΡΠΉ ΡΠ΅ΡΠ²ΠΈΡ Π½Π΅Π΄ΠΎΡΡΡΠΏΠ΅Π½. ΠΠ°ΡΠ΅Π³ΠΈΡΡΡΠΈΡΡΠΉΡΠ΅ΡΡ ΠΈΠ»ΠΈ Π°Π²ΡΠΎΡΠΈΠ·ΡΠΉΡΠ΅ΡΡ Π½Π° ΡΠ°ΠΉΡΠ΅.
Π‘ΠΏΠ°ΡΠΈΠ±ΠΎ Π·Π° Π²Π½ΠΈΠΌΠ°Π½ΠΈΠ΅! ΠΡΠΎΠ΄ΠΎΠ»ΠΆΠ΅Π½ΠΈΠ΅ ΡΠ»Π΅Π΄ΡΠ΅Ρ.
ΠΠ°ΠΌΡΠ°Π΄, ΡΠ°ΡΡΠΌΠΎΡΡΠΈ Π΄Π°ΡΠ°Π³ΠΎΡΡΠΊΠΈΠ΅ ΡΠ΅ΠΊΠΎΠΌΠ΅Π½Π΄Π°ΡΠΈΠΈ
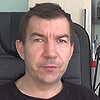
ΠΠΈΠΊΡΠΎΡ (alchedat)
Ρ. ΠΠ»ΡΠ΅Π΄Π°Ρ, ΠΠ΅ΠΌΠ΅ΡΠΎΠ²ΡΠΊΠ°Ρ ΠΎΠ±Π».
Π ΡΠ΅Π±Π΅ Π°Π²ΡΠΎΡ Π½ΠΈΡΠ΅Π³ΠΎ Π½Π΅ ΡΠΎΠΎΠ±ΡΠΈΠ».
Β
Π₯ΠΎΡΡ Π½Π°ΡΠ°ΡΡ Ρ ΠΈΡΡΠΎΡΠΈΠΈ, ΠΊΠΎΡΠΎΡΠ°Ρ Π½Π°ΡΠ°Π»Π°ΡΡ Π² ΠΊΠΎΠ½ΡΠ΅ 2015 Π³ΠΎΠ΄Π°. ΠΡΡΡΠ΅ΡΠΈΠ²ΡΠΈΡΡ ΡΠΎΠ³Π΄Π° Ρ Π΄ΡΡΠ³ΠΎΠΌ, ΠΎΠ½ ΠΏΡΠ΅Π΄Π»ΠΎΠΆΠΈΠ» ΠΌΠ½Π΅ ΡΠ΄Π΅Π»Π°ΡΡ ΡΡΠ΅Π·Π΅ΡΠ½ΡΠΉ ΡΠΏΡ-ΡΡΠ°Π½ΠΎΠΊ Π΄Π»Ρ ΡΠ°ΡΠΊΡΠΎΠΉΠΊΠΈ ΡΠ°Π½Π΅ΡΡ ΠΈ ΠΏΠ»Π°ΡΡΠΈΠΊΠ°. ΠΠ΅Π΄ΠΎΠ»Π³ΠΎ ΠΏΠΎΠ΄ΡΠΌΠ°Π², Ρ ΡΠΊΠ°Π·Π°Π» Π΅ΠΌΡ, ΡΡΠΎ Π΄Π»Ρ Π²ΡΡΠ΅Π·Π°Π½ΠΈΡ ΡΠ°Π·Π»ΠΈΡΠ½ΡΡ
ΡΠ»ΠΎΠ², ΡΠ°ΠΌΠΎΡΠ΅ΠΊ ΠΈ ΠΏΡΠΎΡΠ΅Π³ΠΎ ΡΡΠ°Π½ΠΎΠΊ Π½Π΅ ΠΎΠΊΡΠΏΠΈΡ ΡΠ΅Π±Ρ ΠΈ ΡΡΠ°Π½Π΅Ρ ΡΠ±ΡΡΠΎΡΠ½ΡΠΌ, Π½Π° ΡΡΠΎ ΠΎΠ½ ΠΌΠ½Π΅ ΠΎΡΠ²Π΅ΡΠΈΠ» Β«ΠΏΡΠΈΠ΄ΡΠΌΠ°ΠΉ ΡΡΠΎ-Π½ΠΈΠ±ΡΠ΄ΡΒ»β¦
Π’Π°ΠΊ ΠΊΠ°ΠΊ Π² ΠΎΡΠ½ΠΎΠ²Π΅ ΠΏΡΠΎΠ΅ΠΊΡΠ° Π±ΡΠ» ΠΏΠΎΠ»ΠΎΠΆΠ΅Π½ ΠΈΠ½ΡΠ΅ΡΠ΅Ρ Ρ, ΠΊΠΎΠ½Π΅ΡΠ½ΠΎ ΠΆΠ΅, Π²Π·ΡΠ»ΡΡ Π·Π° Π½Π΅Π³ΠΎ. ΠΠΎ Π²ΡΠ΅ Π±Ρ Π½ΠΈΡΠ΅Π³ΠΎ, Π½ΠΎ Π½Π° ΠΏΡΠ΅Π΄Π»ΠΎΠΆΠ΅Π½Π½ΡΠΉ ΠΏΡΠΎΠ΅ΠΊΡ Π½Π΅ Π±ΡΠ»ΠΎ Π΄Π΅Π½Π΅Π³, Π΄Π° ΠΈ ΡΠ²ΠΎΠ±ΠΎΠ΄Π½ΠΎΠ³ΠΎ Π²ΡΠ΅ΠΌΠ΅Π½ΠΈ ΡΠΎΠΆΠ΅. Π’ΠΎΠ³Π΄Π°, ΠΈΡΡ ΠΎΠ΄Ρ ΠΈΠ· Π·Π°Π΄Π°Ρ, Π²ΠΎΠ·Π»ΠΎΠΆΠ΅Π½Π½ΡΡ Π½Π° ΡΡΠ°Π½ΠΎΠΊ, Π±ΡΠ»ΠΎ ΡΠΏΡΠΎΠ΅ΠΊΡΠΈΡΠΎΠ²Π°Π½ΠΎ ΡΠ»Π΅Π΄ΡΡΡΠ΅Π΅:
Π ΠΈΡΠΎΠ³Π΅ Π½Π° Π²Π΅ΡΡ ΡΡΠ°Π½ΠΎΠΊ Π²ΡΠ΄Π΅Π»ΠΈΠ»ΠΈ 20 Ρ.Ρ. Π Π°Π±ΠΎΡΠ΅Π΅ ΠΏΠΎΠ»Π΅ β 550Ρ 950 ΠΌΠΌ. Π ΠΊΠ°ΡΠ΅ΡΡΠ²Π΅ ΡΠΏΡΠ°Π²Π»Π΅Π½ΠΈΡ Π²ΡΠ±ΡΠ°Π» ΠΊΠΈΡΠ°ΠΉΡΠΊΡΡ ΡΠΈΠ½ΡΡ ΠΏΠ»Π°ΡΡ Π½Π° Π΄ΡΠ°ΠΉΠ²Π΅ΡΠ°Ρ TB6560 Π½Π° 4 ΠΎΡΠΈ, Π² ΠΊΠΎΠΌΠΏΠ»Π΅ΠΊΡ Π΅ΡΠ΅ Π²Ρ ΠΎΠ΄ΠΈΡ 4 Π΄Π²ΠΈΠ³Π°ΡΠ΅Π»Ρ, Π±Π»ΠΎΠΊ ΠΏΠΈΡΠ°Π½ΠΈΡ, Π΄ΠΈΡΠΊ Ρ ΠΠ ΠΈ ΠΏΡΠΎΠ²ΠΎΠ΄ Π΄Π»Ρ ΠΏΠΎΠ΄ΠΊΠ»ΡΡΠ΅Π½ΠΈΡ ΠΊ ΠΠ, Π½Π° ΡΠΎΡ ΠΌΠΎΠΌΠ΅Π½Ρ ΠΎΠ½Π° ΠΎΠ±ΠΎΡΠ»Π°ΡΡ ΠΌΠ½Π΅ Π² 14 Ρ ΠΊΠΎΠΏΠ΅ΠΉΠΊΠ°ΠΌΠΈ Ρ.Ρ.
Π’Π°ΠΊ ΠΊΠ°ΠΊ ΠΏΠ»Π°Π½ΠΈΡΠΎΠ²Π°Π»ΠΎΡΡ ΡΠ΄Π΅Π»Π°ΡΡ ΡΡΠΎ-ΡΠΎ Π²ΡΠΎΠ΄Π΅ ΠΊΠΎΠ½ΡΡΡΡΠΊΡΠΎΡΠ°, ΠΈ Π½Π΅ ΠΏΡΠΈΠ±Π΅Π³Π°Ρ ΠΊ ΡΡΠ΅Π·Π΅ΡΠ½ΡΠΌ, ΡΠ°ΡΡΠΎΡΠ½ΡΠΌ, ΡΠ»ΠΈΡΠΎΠ²Π°Π»ΡΠ½ΡΠΌ ΡΠ°Π±ΠΎΡΠ°ΠΌ, Π²ΡΡ ΠΊΠΎΠ½ΡΡΡΡΠΊΡΠΈΡ ΠΈΠ·Π³ΠΎΡΠΎΠ²Π»ΡΠ»Π°ΡΡ ΠΈΠ· ΠΊΠΎΠ½ΡΡΡΡΠΊΡΠΈΠΎΠ½Π½ΠΎΠΉ Π»ΠΈΡΡΠΎΠ²ΠΎΠΉ ΡΡΠ°Π»ΠΈ ΡΠΎΠ»ΡΠΈΠ½ΠΎΠΉ 8ΠΌΠΌ, ΡΠ°ΡΠΊΡΠΎΠ΅Π½Π½ΠΎΠΉ Π½Π° Π»Π°Π·Π΅ΡΠ½ΡΠΌ Π§ΠΠ£ ΡΡΠ°Π½ΠΊΠ΅. ΠΠΎ Π±Π΅Π· ΡΠΎΠΊΠ°ΡΠ½ΠΎΠΉ ΠΎΠ±ΡΠ°Π±ΠΎΡΠΊΠΈ Π½Π΅ ΠΎΠ±ΠΎΡΠ»ΠΎΡΡ, ΡΠ°ΠΊ ΠΊΠ°ΠΊ Π½Π°Π΄ΠΎ ΡΠΎΡΠΈΡΡ ΠΏΠΎΠ΄ΡΠΈΠΏΠ½ΠΈΠΊΠΎΠ²ΡΠ΅ ΠΎΠΏΠΎΡΡ, Π²ΡΡΠ»ΠΊΠΈ ΡΠΊΠΎΠ»ΡΠΆΠ΅Π½ΠΈΡ, ΠΎΠ±ΡΠ°ΡΠΈΠ²Π°ΡΡ ΠΊΠΎΠ½ΡΡ Π²ΠΈΠ½ΡΠΎΠ² ΠΈ Π² ΡΡΠΎΠΌ ΠΏΠΎΠΌΠΎΠ³Π»Π° Π½Π°ΡΠ° Π΄ΠΎΡΠ΅ΡΠ½ΡΡ ΡΠΈΡΠΌΠ°. Π Π²ΠΎΠΎΠ±ΡΠ΅ ΡΠΎ, ΡΡΠΎ ΠΊΠ°ΡΠ°Π΅ΡΡΡ ΠΌΠ΅ΡΠ°Π»Π»ΠΎΠΎΠ±ΡΠ°Π±ΠΎΡΠΊΠΈ Π² Π ΠΎΡΡΠΈΠΈ, Ρ ΠΏΠΎΡΡΠ°ΡΠ°Π»ΡΡ, Π²ΡΡΠΊΠ°Π·Π°ΡΡ ΡΠ²ΠΎΠΈ ΠΌΡΡΠ»ΠΈ Π² Π±Π»ΠΎΠ³Π΅, ΡΡΠΎΠ±Ρ Π·Π΄Π΅ΡΡ Π½Π΅ ΡΠ»ΡΠ΄ΠΈΡΡ.
ΠΠΎΠ΄ΡΠΈΠΏΠ½ΠΈΠΊΠΎΠ²Π°Ρ ΠΎΠΏΠΎΡΠ°.
Π ΠΈΡΠΎΠ³Π΅ ΡΠ°ΡΠΊΡΠΎΠΉ Π²ΡΠ΅Ρ Π΄Π΅ΡΠ°Π»Π΅ΠΉ ΠΊ ΡΡΠ°Π½ΠΊΡ ΠΈΠ· ΠΌΠ΅ΡΠ°Π»Π»ΠΈΡΠ΅ΡΠΊΠΎΠ³ΠΎ Π»ΠΈΡΡΠ° Π²ΡΡΠ»ΠΎ Π² 1,5Ρ.Ρ., Π΅ΡΠ΅ 2Ρ.Ρ. ΠΎΡΠ΄Π°Π» Π·Π° ΡΠΎΠΊΠ°ΡΠ½ΡΡ ΠΎΠ±ΡΠ°Π±ΠΎΡΠΊΡ, ΠΎΡΡΠ°Π»ΡΠ½ΠΎΠ΅ ΠΏΠΎΡΡΠ°ΡΠΈΠ»ΠΎΡΡ Π½Π° ΠΊΡΠ΅ΠΏΠ΅ΠΆ, ΠΏΠΎΠ΄ΡΠΈΠΏΠ½ΠΈΠΊΠΈ ΠΈ ΠΏΡΠΎΡΠΈΠ΅ Π½Π΅Π²ΡΠΏΠΎΠΌΠ½Π΅Π½Π½ΡΠ΅ ΠΌΠ½ΠΎΠΉ ΠΌΠΎΠΌΠ΅Π½ΡΡ.
ΠΠ°Π»Π΅Π΅ Ρ ΠΎΡΠ΅Π»ΠΎΡΡ Π±Ρ ΠΏΡΠΎΠ΄Π΅ΠΌΠΎΠ½ΡΡΡΠΈΡΠΎΠ²Π°ΡΡ Π½Π΅ΡΠΊΠΎΠ»ΡΠΊΠΎ Π²ΠΈΠ΄Π΅ΠΎ ΠΎ ΠΏΡΠΎΡΠ΅ΡΡΠ΅ ΡΠ±ΠΎΡΠΊΠΈ ΠΈ ΡΠ°Π±ΠΎΡΡ ΡΡΠ°Π½ΠΊΠ°, Π° ΡΠ°ΠΊΠΆΠ΅ ΡΠΎΡΠΎ ΡΠΎΠ³ΠΎ, ΡΡΠΎ ΠΏΡΠΎΠ±ΠΎΠ²Π°Π» Π²ΡΡΠ΅Π·Π°ΡΡ Ρ.
Π Π΅ΡΠ΅ ΠΎΠ΄ΠΈΠ½ ΠΌΠΎΠΌΠ΅Π½Ρ: Π² ΠΊΠ°ΡΠ΅ΡΡΠ²Π΅ ΡΠΏΠΈΠ½Π΄Π΅Π»Ρ ΡΠ΅ΡΠΈΠ» ΠΈΡΠΏΠΎΠ»ΡΠ·ΠΎΠ²Π°ΡΡ ΠΎΠ±ΡΠΊΠ½ΠΎΠ²Π΅Π½Π½ΡΡ Π΄ΡΠ΅Π»Ρ, Π²Π²ΠΈΠ΄Ρ Π½Π΅Π²ΡΡΠΎΠΊΠΎΠΉ ΡΠΊΠΎΡΠΎΡΡΠΈ ΡΠ°Π±ΠΎΡΡ ΡΡΠ°Π½ΠΊΠ°.
ΠΠΎΠΏΡΠΎΠ±ΠΎΠ²Π°Π»ΠΈ Π²ΡΠΆΠΈΠ³Π°ΡΡ
ΠΠΎ ΠΈΡΠΎΠ³Π°ΠΌ ΡΠ±ΠΎΡΠΊΠΈ Π½Π°Π»Π°Π΄ΠΊΠΈ ΠΈ ΠΏΡΠΎΠ²Π΅ΡΠΊΠΈ ΠΌΠΎΠΆΠ½ΠΎ ΡΠΊΠ°Π·Π°ΡΡ, ΡΡΠΎ ΡΡΠ°Π½ΠΎΠΊ ΠΎΠΊΠ°Π·Π°Π»ΡΡ ΡΠ°Π±ΠΎΡΠΎΡΠΏΠΎΡΠΎΠ±Π½ΡΠΌ, Π½ΠΎ Π΄ΠΎΡΡΠ°ΡΠΎΡΠ½ΠΎ Β«ΠΆΠΈΠ΄ΠΊΠΈΠΌΒ», Π½ΠΎ ΡΡΠΎ ΠΈ ΡΠ°ΠΊ Π±ΡΠ»ΠΎ ΠΏΠΎΠ½ΡΡΠ½ΠΎ ΠΏΠΎ Π·Π°ΠΊΠ»Π°Π΄ΡΠ²Π°Π΅ΠΌΠΎΠΌΡ Π±ΡΠ΄ΠΆΠ΅ΡΡ. Π ΡΠ²ΠΎΠΈ Π·Π°Π΄Π°ΡΠΈ ΠΎΠ½ Π²ΡΠΏΠΎΠ»Π½ΡΠ» ΠΎΡΠ»ΠΈΡΠ½ΠΎβ¦ Π‘ΡΠ°Π½ΠΎΠΊ Π±ΡΠ» ΡΠΎΠ±ΡΠ°Π½ ΠΊ ΠΊΠΎΠ½ΡΡ ΡΠ΅Π²ΡΠ°Π»Ρ ΠΈ ΠΎΠΊΡΠΏΠΈΠ»ΡΡ Ρ Π΄ΡΡΠ³Π° Π΄ΠΎ Π»Π΅ΡΠ°, ΠΏΠΎΡΠ»Π΅ ΡΠ΅Π³ΠΎ ΠΎΠ½ ΡΡΠΏΠ΅ΡΠ½ΠΎ Π΅Π³ΠΎ ΠΏΡΠΎΠ΄Π°Π» Π·Π° 30 Ρ.Ρ. ΠΡΠΎΠ΄Π°Π» ΠΏΠΎ ΠΏΡΠΈΡΠΈΠ½Π΅ β Π½Π°Π΄ΠΎΠ΅Π»ΠΎ, ΠΏΡΠΎΠΏΠ°Π» ΠΈΠ½ΡΠ΅ΡΠ΅Ρ, ΠΈ Π½Π΅ΠΆΠ΅Π»Π°Π½ΠΈΠ΅ ΡΠ°Π±ΠΎΡΠ°ΡΡ.
Π―, Π²ΠΎΠ·ΠΌΠΎΠΆΠ½ΠΎ, ΡΡΠΎ-ΡΠΎ ΡΠΏΡΡΡΠΈΠ» ΠΈ Π½Π΅ ΠΎΠΏΠΈΡΠ°Π», Π½Π°Π΄Π΅ΡΡΡ, ΡΡΠΎ Π½Π° Π²ΠΈΠ΄Π΅ΠΎ Π½Π°ΠΉΠ΄ΡΡΡΡ Π²ΡΡ ΠΎΡΡΡΡΡΡΠ²ΡΡΡΠ°Ρ Π·Π΄Π΅ΡΡ ΠΈΠ½ΡΠΎΡΠΌΠ°ΡΠΈΡ. Π Π΄ΡΡΠ³ΠΎΠΌ ΠΆΠ΅ ΡΠ»ΡΡΠ°Π΅ ΠΎΡΡΠ°Π²Π»ΡΠΉΡΠ΅ ΠΊΠΎΠΌΠΌΠ΅Π½ΡΠ°ΡΠΈΠΈ.
ΠΠ°ΠΊ ΡΠΎΠ±ΡΠ°ΡΡ ΡΡΠ°Π½ΠΎΠΊ Ρ Π§ΠΠ£ ΡΠ²ΠΎΠΈΠΌΠΈ ΡΡΠΊΠ°ΠΌΠΈ
Π ΡΡΠΎΠΉ ΡΡΠ°ΡΡΠ΅ ΠΌΡ ΡΠ°ΡΡΠΊΠ°Π·ΡΠ²Π°Π΅ΠΌ ΠΎ ΡΠΎΠΌ, ΡΡΠΎ ΠΏΠΎΡΡΡΠΎΠΈΡΡ ΡΠ²ΠΎΠΈΠΌΠΈ ΡΡΠΊΠ°ΠΌΠΈ ΡΡΠ΅Π·Π΅ΡΠ½ΡΠΉ ΡΡΠ°Π½ΠΎΠΊ Ρ Π§ΠΠ£ β Π²ΡΠΏΠΎΠ»Π½ΠΈΠΌΠ°Ρ Π·Π°Π΄Π°ΡΠ°. ΠΠΎΠ΄ΡΠΎΠ±Π½ΠΎ ΠΎΠΏΠΈΡΡΠ²Π°Π΅ΡΡΡ Π²Π΅ΡΡ ΠΏΡΠΎΡΠ΅ΡΡ ΡΠΎΠ·Π΄Π°Π½ΠΈΡ: ΠΎΡ ΠΏΡΠΎΠ΅ΠΊΡΠΈΡΠΎΠ²Π°Π½ΠΈΡ Π΄ΠΎ ΠΏΡΠΈΠΌΠ΅Π½Π΅Π½ΠΈΡ ΡΡΠ°Π½ΠΊΠ°.Β
Π ΠΏΠ΅ΡΠ²ΠΎΠΌ ΡΠ»ΡΡΠ°Π΅ ΠΊ ΠΏΠΎΠΊΡΠΏΠ½ΡΠΌ ΠΊΠΎΠΌΠΏΠ»Π΅ΠΊΡΡΡΡΠΈΠΌ Π΄ΠΎΠ±Π°Π²Π»ΡΠ»ΠΈΡΡ ΡΠ°ΠΌΠΎΠ΄Π΅Π»ΡΠ½ΡΠ΅ Π΄Π΅ΡΠ°Π»ΠΈ, ΡΠ΄Π΅Π»Π°Π½Π½ΡΠ΅ Π½Π° ΡΠΎΠΊΠ°ΡΠ½ΠΎΠΌ ΡΡΠ°Π½ΠΊΠ΅, Π²ΠΎ Π²ΡΠΎΡΠΎΠΌ ΠΏΡΠΎΠ΅ΠΊΡΠ΅ Π°Π²ΡΠΎΡ ΠΎΠ±ΠΎΡΠ΅Π»ΡΡ Π³ΠΎΡΠΎΠ²ΡΠΌΠΈ ΡΠ°ΡΡΡΠΌΠΈ, ΡΡΠ΅ΡΠΈΠΉ β Π±ΠΎΠ½ΡΡ, ΠΈΠ·Π³ΠΎΡΠΎΠ²Π»Π΅Π½ΠΈΠ΅ ΡΡΠ½ΠΊΡΠΈΠΎΠ½Π°Π»ΡΠ½ΠΎΠ³ΠΎ ΡΡΠΎΠ»Π° Π΄Π»Ρ ΡΡΠ°Π½ΠΊΠ°, ΡΠΎΠ²ΠΌΠ΅ΡΠ΅Π½Π½ΠΎΠ³ΠΎ Ρ ΠΏΠΎΠ»ΠΊΠ°ΠΌΠΈ Π΄Π»Ρ Ρ ΡΠ°Π½Π΅Π½ΠΈΡ ΠΌΠ°ΡΠ΅ΡΠΈΠ°Π»ΠΎΠ² ΠΈ ΠΈΠ½ΡΡΡΡΠΌΠ΅Π½ΡΠΎΠ².
Β Β
Π‘ΠΎΠ΄Π΅ΡΠΆΠ°Π½ΠΈΠ΅:Β
- ΠΠ°ΠΊΠ»ΡΡΠ΅Π½ΠΈΠ΅ ΠΈ ΡΠ΅ΠΊΠΎΠΌΠ΅Π½Π΄Π°ΡΠΈΠΈ
Β Β
ΠΠ°ΠΊ ΡΠ΄Π΅Π»Π°ΡΡ ΡΠ°ΠΌΠΎΠ΄Π΅Π»ΡΠ½ΡΠΉ ΡΡΠ°Π½ΠΎΠΊ Ρ Π§ΠΠ£Β
ΠΠ²ΡΠΎΡ ΠΏΡΠΎΠ΅ΠΊΡΠ° Benne ΠΏΠΎΠ΄ΡΠΎΠ±Π½ΠΎ ΠΎΠΏΠΈΡΠ°Π» Π²Π΅ΡΡ ΠΏΡΠΎΡΠ΅ΡΡ ΡΠΎΠ·Π΄Π°Π½ΠΈΡ ΡΡΠ°Π½ΠΊΠ° Ρ Π§ΠΠ£ Π΄Π»Ρ ΡΠ°Π±ΠΎΡΡ ΠΏΠΎ Π΄Π΅ΡΠ΅Π²Ρ ΠΈ Π΄ΡΡΠ³ΠΈΠΌ ΠΌΠ°ΡΠ΅ΡΠΈΠ°Π»Π°ΠΌ, Π½Π°ΡΠΈΠ½Π°Ρ Ρ ΠΏΡΠΎΠ΅ΠΊΡΠΈΡΠΎΠ²Π°Π½ΠΈΡ.
Β Β
1. ΠΡΠΎΠ΅ΠΊΡΠΈΡΠΎΠ²Π°Π½ΠΈΠ΅
ΠΠ΅ΡΠ΅Π΄ ΠΏΠΎΡΡΡΠΎΠΉΠΊΠΎΠΉ ΡΡΠ°Π½ΠΊΠ° Π½ΡΠΆΠ½ΠΎ ΠΊΠ°ΠΊ ΠΌΠΈΠ½ΠΈΠΌΡΠΌ Π½Π°ΡΠΈΡΠΎΠ²Π°ΡΡ ΡΡΠΊΠΈΠ· ΠΎΡ ΡΡΠΊΠΈ, Π° Π»ΡΡΡΠ΅ Π²ΡΠΏΠΎΠ»Π½ΠΈΡΡ Π±ΠΎΠ»Π΅Π΅ ΡΠΎΡΠ½ΡΠΉ ΡΡΠ΅Ρ ΠΌΠ΅ΡΠ½ΡΠΉ ΡΠΈΡΡΠ½ΠΎΠΊ Ρ ΠΏΠΎΠΌΠΎΡΡΡ ΠΏΡΠΎΠ³ΡΠ°ΠΌΠΌΡ Π‘ΠΠΠ . ΠΠ²ΡΠΎΡ ΠΏΡΠΎΠ΅ΠΊΡΠ° ΠΈΡΠΏΠΎΠ»ΡΠ·ΠΎΠ²Π°Π» google sketchup, Π΄ΠΎΠ²ΠΎΠ»ΡΠ½ΠΎ ΠΏΡΠΎΡΡΡΡ (Π±Π΅ΡΠΏΠ»Π°ΡΠ½ΡΡ Π΄Π»Ρ 30-Π΄Π½Π΅Π²Π½ΠΎΠ³ΠΎ ΠΈΡΠΏΠΎΠ»ΡΠ·ΠΎΠ²Π°Π½ΠΈΡ) ΠΏΡΠΎΠ³ΡΠ°ΠΌΠΌΡ. ΠΠ»Ρ Π±ΠΎΠ»Π΅Π΅ ΡΠ»ΠΎΠΆΠ½ΠΎΠ³ΠΎ ΠΏΡΠΎΠ΅ΠΊΡΠ° Π²Ρ ΠΌΠΎΠΆΠ΅ΡΠ΅ Π²ΡΠ±ΡΠ°ΡΡ Autocad.
ΠΠ»Π°Π²Π½Π°Ρ ΡΠ΅Π»Ρ ΡΠΈΡΡΠ½ΠΊΠ° β Π²ΡΡΡΠ½ΠΈΡΡ Π½Π΅ΠΎΠ±Ρ ΠΎΠ΄ΠΈΠΌΡΠ΅ ΡΠ°Π·ΠΌΠ΅ΡΡ Π΄Π΅ΡΠ°Π»Π΅ΠΉ, Π΄Π»Ρ Π·Π°ΠΊΠ°Π·Π° ΠΈΡ ΠΏΠΎ ΠΈΠ½ΡΠ΅ΡΠ½Π΅ΡΡ, ΠΈ ΡΠ±Π΅Π΄ΠΈΡΡΡΡ, ΡΡΠΎ Π²ΡΠ΅ Π΄Π²ΠΈΠΆΡΡΠΈΠ΅ΡΡ ΡΠ°ΡΡΠΈ ΡΡΠ°Π½ΠΊΠ° ΠΏΠΎΠ΄ΠΎΠΉΠ΄ΡΡ Π΄ΡΡΠ³ ΠΊ Π΄ΡΡΠ³Ρ.
ΠΠ°ΠΊ Π²ΠΈΠ΄ΠΈΡΠ΅, Π΄Π΅ΡΠ°Π»ΡΠ½ΡΡ ΡΠ΅ΡΡΠ΅ΠΆΠ΅ΠΉ Ρ ΡΠ°Π·ΠΌΠ΅ΡΠ΅Π½Π½ΡΠΌΠΈ ΠΎΡΠ²Π΅ΡΡΡΠΈΡΠΌΠΈ ΠΏΠΎΠ΄ ΠΊΡΠ΅ΠΏΠ»Π΅Π½ΠΈΡ Π°Π²ΡΠΎΡ Π½Π΅ ΠΈΡΠΏΠΎΠ»ΡΠ·ΠΎΠ²Π°Π», Π½Π°ΠΌΠ΅ΡΠ°Π» ΠΎΡΠ²Π΅ΡΡΡΠΈΡ Π² ΠΏΡΠΎΡΠ΅ΡΡΠ΅ ΠΏΠΎΡΡΡΠΎΠΉΠΊΠΈ ΡΡΠ°Π½ΠΊΠ°, Π½ΠΎ ΡΠ°ΠΊΠΎΠ³ΠΎ ΠΈΡΡ ΠΎΠ΄Π½ΠΎΠ³ΠΎ Π΄ΠΈΠ·Π°ΠΉΠ½Π° ΠΎΠΊΠ°Π·Π°Π»ΠΎΡΡ Π΄ΠΎΡΡΠ°ΡΠΎΡΠ½ΠΎ.
ΠΠ°Π±Π°ΡΠΈΡΠ½ΡΠ΅ ΡΠ°Π·ΠΌΠ΅ΡΡ ΡΡΠ°Π½ΠΊΠ°: 1050 Ρ 840 Ρ 400 ΠΌΠΌ.
ΠΠ΅ΡΠ΅ΠΌΠ΅ΡΠ΅Π½ΠΈΠ΅ ΠΏΠΎ ΠΎΡΡΠΌ: X 730 ΠΌΠΌ, Y 650 ΠΌΠΌ, Z 150 ΠΌΠΌ
ΠΠ»ΠΈΠ½Π° Π½Π°ΠΏΡΠ°Π²Π»ΡΡΡΠΈΡ ΠΈ ΡΠ°ΡΠΈΠΊΠΎΠ²ΠΎ-Π²ΠΈΠ½ΡΠΎΠ²ΠΎΠΉ ΠΏΠ΅ΡΠ΅Π΄Π°ΡΠΈ Π·Π°Π²ΠΈΡΠΈΡ ΠΎΡ ΡΠ°Π·ΠΌΠ΅ΡΠ° Π·Π°Π΄ΡΠΌΠ°Π½Π½ΠΎΠ³ΠΎ Π²Π°ΠΌΠΈ ΡΡΠ°Π½ΠΊΠ°.
ΠΠΎΠ³Π΄Π° ΠΈΠ΄Π΅Ρ ΠΏΡΠΎΠ΅ΠΊΡΠΈΡΠΎΠ²Π°Π½ΠΈΠ΅ ΡΡΠ°Π½ΠΊΠ° Ρ Π§ΠΠ£, Π΅ΡΡΡ Π½Π΅ΡΠΊΠΎΠ»ΡΠΊΠΎ Π²ΠΎΠΏΡΠΎΡΠΎΠ², ΠΎΡ ΠΎΡΠ²Π΅ΡΠ° Π½Π° ΠΊΠΎΡΠΎΡΡΠ΅ Π·Π°Π²ΠΈΡΠΈΡ ΠΊΠΎΠ½Π΅ΡΠ½ΡΠΉ ΡΠ΅Π·ΡΠ»ΡΡΠ°Ρ.
ΠΠ°ΠΊΠΎΠΉ ΡΠΈΠΏ ΡΡΠ°Π½ΠΊΠ° Ρ Π§ΠΠ£ Π²Ρ Ρ ΠΎΡΠΈΡΠ΅ Π²ΡΠ±ΡΠ°ΡΡ?
Π‘ ΠΏΠΎΠ΄Π²ΠΈΠΆΠ½ΡΠΌ ΡΡΠΎΠ»ΠΎΠΌ ΠΈΠ»ΠΈ Ρ ΠΏΠΎΠ΄Π²ΠΈΠΆΠ½ΡΠΌ ΠΏΠΎΡΡΠ°Π»ΠΎΠΌ? ΠΠΎΠ½ΡΡΡΡΠΊΡΠΈΠΈ Ρ ΠΏΠΎΠ΄Π²ΠΈΠΆΠ½ΡΠΌ ΡΡΠΎΠ»ΠΎΠΌ ΡΠ°ΡΡΠΎ ΠΈΡΠΏΠΎΠ»ΡΠ·ΡΡΡΡΡ Π΄Π»Ρ ΡΡΠ°Π½ΠΊΠΎΠ² Π½Π΅Π±ΠΎΠ»ΡΡΠΎΠ³ΠΎ ΡΠ°Π·ΠΌΠ΅ΡΠ°, Π΄ΠΎ 30Ρ 30 ΡΠΌ. ΠΡ Π»Π΅Π³ΡΠ΅ ΠΏΠΎΡΡΡΠΎΠΈΡΡ, ΠΈΡ ΠΌΠΎΠΆΠ½ΠΎ ΡΠ΄Π΅Π»Π°ΡΡ Π±ΠΎΠ»Π΅Π΅ ΠΆΠ΅ΡΡΠΊΠΈΠΌΠΈ, ΡΠ΅ΠΌ ΠΌΠ°ΡΠΈΠ½Ρ Ρ Π΄Π²ΠΈΠΆΡΡΠΈΠΌΡΡ ΠΏΠΎΡΡΠ°Π»ΠΎΠΌ. ΠΠ΅Π΄ΠΎΡΡΠ°ΡΠΎΠΊ ΠΏΠ΅ΡΠ΅ΠΌΠ΅ΡΠ΅Π½ΠΈΡ ΡΡΠΎΠ»Π° Π·Π°ΠΊΠ»ΡΡΠ°Π΅ΡΡΡ Π² ΡΠΎΠΌ, ΡΡΠΎ ΠΏΡΠΈ ΠΎΠ΄ΠΈΠ½Π°ΠΊΠΎΠ²ΠΎΠΉ Π·ΠΎΠ½Π΅ ΡΠ΅Π·ΠΊΠΈ ΠΎΠ±ΡΠ°Ρ ΠΏΠ»ΠΎΡΠ°Π΄Ρ ΡΡΠ°Π½ΠΊΠ° ΠΏΠΎΠ»ΡΡΠ°Π΅ΡΡΡ ΡΠ°Π·Π° Π² Π΄Π²Π° Π±ΠΎΠ»ΡΡΠ΅, ΡΠ΅ΠΌ ΠΏΡΠΈ ΠΈΡΠΏΠΎΠ»ΡΠ·ΠΎΠ²Π°Π½ΠΈΠΈ ΠΊΠΎΠ½ΡΡΡΡΠΊΡΠΈΠΈ Ρ ΠΏΠΎΠ΄Π²ΠΈΠΆΠ½ΡΠΌ ΠΏΠΎΡΡΠ°Π»ΠΎΠΌ. Π ΡΡΠΎΠΌ ΠΏΡΠΎΠ΅ΠΊΡΠ΅ Π·ΠΎΠ½Π° ΠΎΠ±ΡΠ°Π±ΠΎΡΠΊΠΈ ΠΎΠΊΠΎΠ»ΠΎ 65×65 ΡΠΌ, ΠΏΠΎΡΡΠΎΠΌΡ Π±ΡΠ» Π²ΡΠ±ΡΠ°Π½ ΠΏΠΎΠ΄Π²ΠΈΠΆΠ½ΡΠΉ ΠΏΠΎΡΡΠ°Π».
Π§ΡΠΎ Π²Ρ Ρ ΠΎΡΠΈΡΠ΅ ΠΎΠ±ΡΠ°Π±Π°ΡΡΠ²Π°ΡΡ Ρ ΠΏΠΎΠΌΠΎΡΡΡ ΡΡΠ°Π½ΠΊΠ° Ρ Π§ΠΠ£?
Π Π΄Π°Π½Π½ΠΎΠΌ ΠΏΡΠΎΠ΅ΠΊΡΠ΅ ΡΡΠ°Π½ΠΎΠΊ ΠΏΡΠ΅Π΄Π½Π°Π·Π½Π°ΡΠ°Π»ΡΡ Π² ΠΎΡΠ½ΠΎΠ²Π½ΠΎΠΌ Π΄Π»Ρ ΡΠ°Π½Π΅ΡΡ, Π»ΠΈΡΡΠ²Π΅Π½Π½ΡΡ ΠΏΠΎΡΠΎΠ΄ Π΄Π΅ΡΠ΅Π²Π° ΠΈ ΠΏΠ»Π°ΡΡΠΌΠ°ΡΡ, Π° ΡΠ°ΠΊΠΆΠ΅ Π΄Π»Ρ Π°Π»ΡΠΌΠΈΠ½ΠΈΡ.
Β ΠΠ· ΡΠ΅Π³ΠΎ Π±ΡΠ΄Π΅Ρ ΡΡΡΠΎΠΈΡΡΡΡ ΡΡΠ°Π½ΠΎΠΊ?
ΠΡΠΎ Π² ΠΎΡΠ½ΠΎΠ²Π½ΠΎΠΌ Π·Π°Π²ΠΈΡΠΈΡ ΠΎΡ ΠΌΠ°ΡΠ΅ΡΠΈΠ°Π»Π°, ΠΊΠΎΡΠΎΡΡΠΉ Π±ΡΠ΄Π΅Ρ Π½Π° ΡΡΠ°Π½ΠΊΠ΅ ΠΎΠ±ΡΠ°Π±Π°ΡΡΠ²Π°ΡΡΡΡ. Π ΠΈΠ΄Π΅Π°Π»Π΅ ΠΌΠ°ΡΠ΅ΡΠΈΠ°Π», ΠΊΠΎΡΠΎΡΡΠΉ ΠΈΡΠΏΠΎΠ»ΡΠ·ΡΠ΅ΡΡΡ Π΄Π»Ρ ΠΈΠ·Π³ΠΎΡΠΎΠ²Π»Π΅Π½ΠΈΡ ΡΡΠ°Π½ΠΊΠ°, Π΄ΠΎΠ»ΠΆΠ΅Π½ Π±ΡΡΡ ΠΏΡΠΎΡΠ½Π΅Π΅ ΠΌΠ°ΡΠ΅ΡΠΈΠ°Π»Π°, ΠΊΠΎΡΠΎΡΡΠΉ Π±ΡΠ΄Π΅Ρ ΠΎΠ±ΡΠ°Π±Π°ΡΡΠ²Π°ΡΡΡΡ Π½Π° ΡΡΠ°Π½ΠΊΠ΅ ΠΈΠ»ΠΈ, ΠΊΠ°ΠΊ ΠΌΠΈΠ½ΠΈΠΌΡΠΌ, Π½Π΅ ΠΌΠ΅Π½Π΅Π΅ ΠΏΡΠΎΡΠ½ΡΠΌ. ΠΠΎΡΡΠΎΠΌΡ, Π΅ΡΠ»ΠΈ Π²Ρ Ρ ΠΎΡΠΈΡΠ΅ ΡΠ΅Π·Π°ΡΡ Π°Π»ΡΠΌΠΈΠ½ΠΈΠΉ, ΡΡΠ°Π½ΠΎΠΊ Π΄ΠΎΠ»ΠΆΠ΅Π½ Π±ΡΡΡ ΡΠΎΠ±ΡΠ°Π½ ΠΈΠ· Π°Π»ΡΠΌΠΈΠ½ΠΈΡ ΠΈΠ»ΠΈ ΡΡΠ°Π»ΠΈ.Β
ΠΠ°ΠΊΠ°Ρ Π΄Π»ΠΈΠ½Π° ΠΎΡΠ΅ΠΉ Π²Π°ΠΌ Π½ΡΠΆΠ½Π°?
ΠΠΎ ΠΏΠ΅ΡΠ²ΠΎΠ½Π°ΡΠ°Π»ΡΠ½ΠΎΠΌΡ Π·Π°ΠΌΡΡΠ»Ρ ΡΡΠ°Π½ΠΎΠΊ Ρ Π§ΠΠ£ Π΄ΠΎΠ»ΠΆΠ΅Π½ Π±ΡΠ» ΠΎΠ±ΡΠ°Π±Π°ΡΡΠ²Π°ΡΡ ΡΠ°Π½Π΅ΡΡ ΠΈ ΠΠΠ€, ΠΊΠΎΡΠΎΡΡΠ΅ Π² ΠΠΈΠ΄Π΅ΡΠ»Π°Π½Π΄Π°Ρ Π²ΡΠΏΡΡΠΊΠ°ΡΡ ΡΠ°Π·ΠΌΠ΅ΡΠΎΠΌ 62 Ρ 121 ΡΠΌ. ΠΠΎΡΡΠΎΠΌΡ Π΄Π»Ρ Y ΡΠ°ΡΡΡΠΎΡΠ½ΠΈΠ΅ ΠΏΡΠΎΡ ΠΎΠ΄Π° Π΄ΠΎΠ»ΠΆΠ½ΠΎ Π±ΡΡΡ Π½Π΅ ΠΌΠ΅Π½Π΅Π΅ 620 ΠΌΠΌ. ΠΠ»ΠΈΠ½Π° Ρ ΠΎΠ΄Π° ΠΏΠΎ ΠΎΡΠΈ Π₯ ΡΠ°Π²Π½Π° 730 ΠΌΠΌ, ΠΏΠΎΡΠΎΠΌΡ ΡΡΠΎ ΠΈΠ½Π°ΡΠ΅ ΡΡΠ°Π½ΠΎΠΊ Π·Π°Π½ΡΠ» Π±Ρ Π²ΡΠ΅ ΠΏΡΠΎΡΡΡΠ°Π½ΡΡΠ²ΠΎ ΠΊΠΎΠΌΠ½Π°ΡΡ. ΠΠΎΡΡΠΎΠΌΡ ΠΎΡΡ X ΠΊΠΎΡΠΎΡΠ΅, ΡΠ΅ΠΌ Π΄Π»ΠΈΠ½Π° Π»ΠΈΡΡΠ° ΡΠ°Π½Π΅ΡΡ (1210 ΠΌΠΌ), Π½ΠΎ ΠΌΠΎΠΆΠ½ΠΎ ΠΎΠ±ΡΠ°Π±ΠΎΡΠ°ΡΡ ΠΏΠΎΠ»ΠΎΠ²ΠΈΠ½Ρ, Π·Π°ΡΠ΅ΠΌ ΡΠ΄Π²ΠΈΠ½ΡΡΡ Π»ΠΈΡΡ Π²ΠΏΠ΅ΡΠ΅Π΄ ΠΈ ΠΎΠ±ΡΠ°Π±ΠΎΡΠ°ΡΡ ΠΎΡΡΠ°Π²ΡΡΡΡΡ ΡΠ°ΡΡΡ. Π‘ ΠΏΠΎΠΌΠΎΡΡΡ ΡΠ°ΠΊΠΎΠΉ ΡΠ»ΠΎΠ²ΠΊΠΈ ΠΏΠΎΠ»ΡΡΠ°Π΅ΡΡΡ ΠΎΠ±ΡΠ°Π±Π°ΡΡΠ²Π°ΡΡ Π½Π° ΡΡΠ°Π½ΠΊΠ΅ ΠΊΡΡΠΊΠΈ ΠΊΡΠ΄Π° Π±ΠΎΠ»ΡΡΠΈΠ΅, ΡΠ΅ΠΌ Π΄Π»ΠΈΠ½Π° ΠΎΡΠΈ Π₯. ΠΠ»Ρ ΠΎΡΠΈ Z Π²ΡΠ±ΡΠ°Π½ΠΎ 150 ΠΌΠΌ, ΡΡΠΎΠ±Ρ Π² Π±ΡΠ΄ΡΡΠ΅ΠΌ ΠΈΡΠΏΠΎΠ»ΡΠ·ΠΎΠ²Π°ΡΡ ΡΠ΅ΡΠ²Π΅ΡΡΡΡ ΠΎΡΡ.
ΠΠ°ΠΊΠΎΠΉ ΡΠΈΠΏ Π»ΠΈΠ½Π΅ΠΉΠ½ΠΎΠ³ΠΎ Π΄Π²ΠΈΠΆΠ΅Π½ΠΈΡ Π²Ρ Π±ΡΠ΄Π΅ΡΠ΅ ΠΈΡΠΏΠΎΠ»ΡΠ·ΠΎΠ²Π°ΡΡ?
Π‘ΡΡΠ΅ΡΡΠ²ΡΠ΅Ρ ΠΌΠ½ΠΎΠΆΠ΅ΡΡΠ²ΠΎ Π²Π°ΡΠΈΠ°Π½ΡΠΎΠ² ΡΠΈΡΡΠ΅ΠΌΡ Π»ΠΈΠ½Π΅ΠΉΠ½ΠΎΠ³ΠΎ ΠΏΠ΅ΡΠ΅ΠΌΠ΅ΡΠ΅Π½ΠΈΡ, ΠΎΡ Π΅Π΅ Π²ΡΠ±ΠΎΡΠ° Π²ΠΎ ΠΌΠ½ΠΎΠ³ΠΎΠΌ Π·Π°Π²ΠΈΡΠΈΡ ΠΊΠ°ΡΠ΅ΡΡΠ²ΠΎ ΡΠ°Π±ΠΎΡΡ. ΠΠΎΡΡΠΎΠΌΡ Π΅ΡΡΡ ΡΠΌΡΡΠ» ΠΏΠΎΡΡΠ°ΡΠΈΡΡΡΡ Π½Π° Π»ΡΡΡΡΡ ΡΠΈΡΡΠ΅ΠΌΡ, ΠΊΠΎΡΠΎΡΡΡ Π²Ρ ΠΌΠΎΠΆΠ΅ΡΠ΅ ΡΠ΅Π±Π΅ ΠΏΠΎΠ·Π²ΠΎΠ»ΠΈΡΡ. ΠΠ²ΡΠΎΡ ΠΏΡΠΎΠ΅ΠΊΡΠ° ΡΠ΅ΡΠΈΠ», ΡΡΠΎ Π»ΠΈΠ½Π΅ΠΉΠ½ΡΠ΅ ΡΠ΅Π»ΡΡΡ Π±ΡΠ»ΠΈ Π»ΡΡΡΠΈΠΌ Π²Π°ΡΠΈΠ°Π½ΡΠΎΠΌ ΠΈΠ· ΡΠ΅Ρ , Π½Π° ΠΊΠΎΡΠΎΡΡΠ΅ Π΅ΠΌΡ Ρ Π²Π°ΡΠ°Π»ΠΎ Π΄Π΅Π½Π΅Π³. ΠΡΠ»ΠΈ Π²Ρ ΡΡΡΠΎΠΈΡΠ΅ 3-ΠΎΡΠ΅Π²ΠΎΠΉ ΡΡΠ΅Π·Π΅ΡΠ½ΡΠΉ ΡΡΠ°Π½ΠΎΠΊ Ρ Π§ΠΠ£, Π²Π°ΠΌ Π½ΡΠΆΠ½ΠΎ ΠΊΡΠΏΠΈΡΡ ΠΊΠΎΠΌΠΏΠ»Π΅ΠΊΡ, ΡΠΎΡΡΠΎΡΡΠΈΠΉ ΠΈΠ· ΡΡΠ΅Ρ Π½Π°Π±ΠΎΡΠΎΠ² Π»ΠΈΠ½Π΅ΠΉΠ½ΡΡ Π½Π°ΠΏΡΠ°Π²Π»ΡΡΡΠΈΡ ΠΈ Π΄Π²ΡΡ Π»ΠΈΠ½Π΅ΠΉΠ½ΡΡ ΠΏΠΎΠ΄ΡΠΈΠΏΠ½ΠΈΠΊΠΎΠ² Π½Π° ΠΊΠ°ΠΆΠ΄ΡΡ Π½Π°ΠΏΡΠ°Π²Π»ΡΡΡΡΡ.
ΠΠ°ΠΊΡΡ ΡΠΈΡΡΠ΅ΠΌΡ ΠΏΡΠΈΠ²ΠΎΠ΄Π° ΠΏΠΎΠ΄Π°Ρ Π²Ρ Π±ΡΠ΄Π΅ΡΠ΅ ΠΈΡΠΏΠΎΠ»ΡΠ·ΠΎΠ²Π°ΡΡ Π΄Π»Ρ ΠΊΠ°ΠΆΠ΄ΠΎΠΉ ΠΎΡΠΈ?
ΠΡΠ½ΠΎΠ²Π½ΡΠ΅ Π²Π°ΡΠΈΠ°Π½ΡΡ ΠΏΡΠΈΠ²ΠΎΠ΄Π° ΠΏΠΎΠ΄Π°ΡΠΈ: Π·ΡΠ±ΡΠ°ΡΡΠ΅ ΡΠ΅ΠΌΠ½ΠΈ, ΠΌΠ΅Ρ Π°Π½ΠΈΠ·ΠΌΡ ΡΠ΅Π΅ΡΠ½ΠΎΠΉ ΠΏΠ΅ΡΠ΅Π΄Π°ΡΠΈ ΠΈ ΠΏΠ΅ΡΠ΅Π΄Π°ΡΠ° Π²ΠΈΠ½Ρ-Π³Π°ΠΉΠΊΠ°. ΠΠ»Ρ ΡΠ°ΠΌΠΎΠ΄Π΅Π»ΡΠ½ΡΡ ΡΡΠ°Π½ΠΊΠΎΠ² Ρ Π§ΠΠ£ ΡΠ°ΡΠ΅ Π²ΡΠ΅Π³ΠΎ ΠΈΡΠΏΠΎΠ»ΡΠ·ΡΡΡ ΠΏΠ΅ΡΠ΅Π΄Π°ΡΡ Π²ΠΈΠ½Ρ-Π³Π°ΠΉΠΊΠ° Ρ ΠΈΡΠΏΠΎΠ»ΡΠ·ΠΎΠ²Π°Π½ΠΈΠ΅ΠΌ ΡΠ°ΡΠΈΠΊΠΎ-Π²ΠΈΠ½ΡΠΎΠ²ΠΎΠΉ ΠΏΠ°ΡΡ. ΠΠ°ΠΉΠΊΠ° ΠΊΡΠ΅ΠΏΠΈΡΡΡ ΠΊ ΠΏΠΎΠ΄Π²ΠΈΠΆΠ½ΠΎΠΉ ΡΠ°ΡΡΠΈ ΠΌΠ°ΡΠΈΠ½Ρ, Π²ΠΈΠ½Ρ Π·Π°ΠΊΡΠ΅ΠΏΠ»Π΅Π½ Ρ ΠΎΠ±ΠΎΠΈΡ ΠΊΠΎΠ½ΡΠΎΠ². ΠΠΈΠ½Ρ ΠΊΡΠ΅ΠΏΠΈΡΡΡ ΠΊ Π΄Π²ΠΈΠ³Π°ΡΠ΅Π»Ρ. ΠΡΠ»ΠΈ Π΄Π²ΠΈΠ³Π°ΡΠ΅Π»ΠΈ Π²ΡΠ°ΡΠ°Π΅ΡΡΡ, Π³Π°ΠΉΠΊΠ° Ρ ΠΏΡΠΈΠΊΡΠ΅ΠΏΠ»Π΅Π½Π½ΠΎΠΉ ΠΊ Π½Π΅ΠΉ Π΄Π²ΠΈΠΆΡΡΠ΅ΠΉΡΡ ΡΠ°ΡΡΡΡ ΠΌΠ°ΡΠΈΠ½Ρ Π±ΡΠ΄Π΅Ρ Π΄Π²ΠΈΠ³Π°ΡΡΡΡ Π²Π΄ΠΎΠ»Ρ Π²ΠΈΠ½ΡΠ° ΠΈ ΠΏΡΠΈΠ²ΠΎΠ΄ΠΈΡΡ ΠΌΠ°ΡΠΈΠ½Ρ Π² Π΄Π²ΠΈΠΆΠ΅Π½ΠΈΠ΅.
Π¨ΠΠ Π² Π΄Π°Π½Π½ΠΎΠΌ ΡΡΠ°Π½ΠΊΠ΅ ΠΈΡΠΏΠΎΠ»ΡΠ·ΡΠ΅ΡΡΡ Π΄Π»Ρ ΠΏΡΠΈΠ²ΠΎΠ΄Π° ΠΎΡΠ΅ΠΉ X ΠΈ Y. Π¨Π°ΡΠΈΠΊΠΎ-Π²ΠΈΠ½ΡΠΎΠ²ΡΠ΅ ΠΏΠΎΠ΄ΡΠΈΠΏΠ½ΠΈΠΊΠΈ ΠΎΠ±Π΅ΡΠΏΠ΅ΡΠΈΠ²Π°ΡΡ ΠΎΡΠ΅Π½Ρ ΠΏΠ»Π°Π²Π½ΡΠΉ Ρ ΠΎΠ΄, Π»ΡΡΡ ΠΎΡΡΡΡΡΡΠ²ΡΠ΅Ρ, ΠΏΠΎΠ²ΡΡΠ°Π΅ΡΡΡ ΠΊΠ°ΡΠ΅ΡΡΠ²ΠΎ ΠΈ ΡΠΊΠΎΡΠΎΡΡΡ ΡΠ΅Π·ΠΊΠΈ.
ΠΠ»Ρ ΠΎΡΠΈ Z ΠΈΡΠΏΠΎΠ»ΡΠ·ΠΎΠ²Π°Π½ ΡΡΠ΅ΡΠΆΠ΅Π½Ρ M10 ΠΈΠ· Π²ΡΡΠΎΠΊΠΎΠΊΠ°ΡΠ΅ΡΡΠ²Π΅Π½Π½ΠΎΠΉ Π½Π΅ΡΠΆΠ°Π²Π΅ΡΡΠ΅ΠΉ ΡΡΠ°Π»ΠΈ Ρ ΡΠ°ΠΌΠΎΠ΄Π΅Π»ΡΠ½ΠΎΠΉ Π³Π°ΠΉΠΊΠΎΠΉ ΠΈΠ· Π΄Π΅Π»ΡΠΈΠ½Π°.
Π’ΠΈΠΏ Π΄Π²ΠΈΠ³Π°ΡΠ΅Π»Ρ ΠΈ ΠΊΠΎΠ½ΡΡΠΎΠ»Π»Π΅ΡΠ°
ΠΠ±ΡΡΠ½ΠΎ Π² ΡΠ°ΠΌΠΎΠ΄Π΅Π»ΡΠ½ΡΡ ΡΡΠ°Π½ΠΊΠ°Ρ Ρ Π§ΠΠ£ ΠΏΡΠΈΠΌΠ΅Π½ΡΡΡΡΡ ΡΠ°Π³ΠΎΠ²ΡΠ΅ Π΄Π²ΠΈΠ³Π°ΡΠ΅Π»ΠΈ. Π‘Π΅ΡΠ²ΠΎΠΏΡΠΈΠ²ΠΎΠ΄Ρ Π² ΠΎΡΠ½ΠΎΠ²Π½ΠΎΠΌ ΠΈΡΠΏΠΎΠ»ΡΠ·ΡΡΡΡΡ Π΄Π»Ρ ΠΌΠΎΡΠ½ΡΡ ΠΏΡΠΎΠΌΡΡΠ»Π΅Π½Π½ΡΡ ΡΡΠ°Π½ΠΊΠΎΠ² Ρ Π§ΠΠ£, ΠΎΠ½ΠΈ Π΄ΠΎΡΠΎΠΆΠ΅ ΠΈ ΡΡΠ΅Π±ΡΡΡ Π±ΠΎΠ»Π΅Π΅ Π΄ΠΎΡΠΎΠ³ΠΈΡ ΠΊΠΎΠ½ΡΡΠΎΠ»Π»Π΅ΡΠΎΠ². ΠΠ΄Π΅ΡΡ ΠΈΡΠΏΠΎΠ»ΡΠ·ΠΎΠ²Π°Π½Ρ ΡΠ°Π³ΠΎΠ²ΡΠ΅ Π΄Π²ΠΈΠ³Π°ΡΠ΅Π»ΠΈ 3Nm.
Π’ΠΈΠΏ ΡΠΏΠΈΠ½Π΄Π΅Π»Ρ
Π ΠΏΡΠΎΠ΅ΠΊΡΠ΅ ΠΈΡΠΏΠΎΠ»ΡΠ·ΡΠ΅ΡΡΡ ΡΡΠ°Π½Π΄Π°ΡΡΠ½ΡΠΉ Kress, ΠΎΠ½ ΠΈΠΌΠ΅Π΅Ρ Ρ ΠΎΡΠΎΡΠΈΠΉ 43-ΠΌΠΌ Π·Π°ΠΆΠΈΠΌΠ½ΠΎΠΉ ΡΠ»Π°Π½Π΅Ρ, Π° ΡΠ°ΠΊΠΆΠ΅ Π²ΡΡΡΠΎΠ΅Π½Π½ΡΠΉ ΡΠ΅Π³ΡΠ»ΡΡΠΎΡ ΡΠΊΠΎΡΠΎΡΡΠΈ (Π½ΠΎ ΠΏΠΎΡΠ»Π΅Π΄Π½ΡΡ ΡΡΠ½ΠΊΡΠΈΡ Π΅ΡΡΡ Ρ Π±ΠΎΠ»ΡΡΠΈΠ½ΡΡΠ²Π° ΡΠΏΠΈΠ½Π΄Π΅Π»Π΅ΠΉ).
ΠΡΠ»ΠΈ Π²Ρ ΡΠΎΠ±ΠΈΡΠ°Π΅ΡΠ΅ΡΡ Π²ΡΠΏΠΎΠ»Π½ΡΡΡ Π΄Π΅ΠΉΡΡΠ²ΠΈΡΠ΅Π»ΡΠ½ΠΎ ΡΠ»ΠΎΠΆΠ½ΡΡ ΡΠ΅Π·ΠΊΡ, ΡΡΠΎΠΈΡ ΠΎΠ±ΡΠ°ΡΠΈΡΡ Π²Π½ΠΈΠΌΠ°Π½ΠΈΠ΅ Π½Π° ΡΠΏΠΈΠ½Π΄Π΅Π»ΠΈ Ρ Π²ΠΎΠ΄ΡΠ½ΡΠΌ ΠΎΡ Π»Π°ΠΆΠ΄Π΅Π½ΠΈΠ΅ΠΌ β ΠΎΠ½ΠΈ Π΄ΠΎΡΠΎΠΆΠ΅ ΡΡΠ°Π½Π΄Π°ΡΡΠ½ΡΡ , Π·Π°ΡΠΎ ΡΡΠΌΡΡ Π³ΠΎΡΠ°Π·Π΄ΠΎ ΠΌΠ΅Π½ΡΡΠ΅, ΠΌΠΎΠ³ΡΡ ΡΠ°Π±ΠΎΡΠ°ΡΡ Π½Π° Π½ΠΈΠ·ΠΊΠΈΡ ΠΎΠ±ΠΎΡΠΎΡΠ°Ρ Π±Π΅Π· ΠΏΠ΅ΡΠ΅Π³ΡΠ΅Π²Π° ΠΈ Ρ ΡΠ°ΠΌΡΠΌΠΈ ΡΠ°Π·Π½ΡΠΌΠΈ ΠΌΠ°ΡΠ΅ΡΠΈΠ°Π»Π°ΠΌΠΈ.
ΠΠ°ΡΡΠ°ΡΡ
ΠΠ° Π΄Π°Π½Π½ΡΠΉ ΡΡΠ°Π½ΠΎΠΊ Ρ Π§ΠΠ£ ΡΡΠ»ΠΎ ΠΏΡΠΈΠΌΠ΅ΡΠ½ΠΎ 1500 Π΅Π²ΡΠΎ. ΠΠΎΡΠΎΠ²ΡΠΉ ΡΡΠ΅Π·Π΅ΡΠ½ΡΠΉ ΡΡΠ°Π½ΠΎΠΊ Ρ Π§ΠΠ£ ΡΡ ΠΎΠ΄Π½ΡΡ Ρ Π°ΡΠ°ΠΊΡΠ΅ΡΠΈΡΡΠΈΠΊ ΡΡΠΎΠΈΡ Π½Π°ΠΌΠ½ΠΎΠ³ΠΎ Π΄ΠΎΡΠΎΠΆΠ΅, ΡΠ°ΠΊ ΡΡΠΎ Π²Ρ ΠΌΠΎΠΆΠ΅ΡΠ΅ ΡΡΠΊΠΎΠ½ΠΎΠΌΠΈΡΡ, ΡΠΎΠ·Π΄Π°Π² ΡΡΠ°Π½ΠΎΠΊ ΡΠ°ΠΌΠΎΡΡΠΎΡΡΠ΅Π»ΡΠ½ΠΎ.
Β Β
2. ΠΠΎΠΌΠΏΠ»Π΅ΠΊΡΡΡΡΠΈΠ΅ Π΄Π»Ρ ΡΠΎΠ·Π΄Π°Π½ΠΈΡ ΡΡΠ°Π½ΠΊΠ° Ρ Π§ΠΠ£Β
ΠΠ»Π΅ΠΊΡΡΠΎΠΎΠ±ΠΎΡΡΠ΄ΠΎΠ²Π°Π½ΠΈΠ΅ ΠΈ ΡΠ»Π΅ΠΊΡΡΠΎΠ½ΠΈΠΊΠ°:
- 3 ΡΠ°Π³ΠΎΠ²ΡΡ Π΄Π²ΠΈΠ³Π°ΡΠ΅Π»Ρ 3 Nm Nema 23;
- 3 Π΄ΡΠ°ΠΉΠ²Π΅ΡΠ° ΡΠ°Π³ΠΎΠ²ΡΡ Π΄Π²ΠΈΠ³Π°ΡΠ΅Π»Π΅ΠΉ DM556 Leadshine;
- Π±Π»ΠΎΠΊ ΠΏΠΈΡΠ°Π½ΠΈΡ 36 Π Π΄Π»Ρ ΡΡΠ°Π½ΠΊΠΎΠ² Ρ Π§ΠΠ£;
- ΠΈΠ½ΡΠ΅ΡΡΠ΅ΠΉΡΠ½Π°Ρ ΠΏΠ»Π°ΡΠ° 5 Axis CNC Breakout Board Π΄Π»Ρ ΡΠΏΡΠ°Π²Π»Π΅Π½ΠΈΡ ΡΠ°Π³ΠΎΠ²ΡΠΌΠΈ Π΄ΡΠ°ΠΉΠ²Π΅ΡΠ°ΠΌΠΈ;
- ΠΈΡΡΠΎΡΠ½ΠΈΠΊ ΠΏΠΈΡΠ°Π½ΠΈΡ 5 Π Π΄Π»Ρ ΠΈΠ½ΡΠ΅ΡΡΠ΅ΠΉΡΠ½ΠΎΠΉ ΠΏΠ»Π°ΡΡ;
- Π΄Π²ΡΡ ΠΏΠΎΠ·ΠΈΡΠΈΠΎΠ½Π½ΡΠΉ Π²ΡΠΊΠ»ΡΡΠ°ΡΠ΅Π»Ρ On/Off;
- ΠΌΠ½ΠΎΠ³ΠΎΠΆΠΈΠ»ΡΠ½ΡΠΉ ΠΊΠ°Π±Π΅Π»Ρ Shielded 4 Conductor 18 AWG;
- 3 ΡΠ΅Π½ΡΠΎΡΠ½ΡΡ ΠΊΠΎΠ½ΡΠ΅Π²ΡΡ Π²ΡΠΊΠ»ΡΡΠ°ΡΠ΅Π»Ρ;
- Π¨ΠΏΠΈΠ½Π΄Π΅Π»Ρ: Kress FME 800 (ΠΏΠΎΠ΄ΠΎΠΉΠ΄ΡΡ ΡΠ°ΠΊΠΆΠ΅ Bosch Colt ΠΈΠ»ΠΈ Dewalt Compact Router).
ΠΠΎ ΠΆΠ΅Π»Π°Π½ΠΈΡ:
- ΡΠΊΠ°ΡΡΠΈΠΊ/ΠΊΠΎΡΠΏΡΡ Π΄Π»Ρ ΡΠ»Π΅ΠΊΡΡΠΎΠΎΠ±ΠΎΡΡΠ΄ΠΎΠ²Π°Π½ΠΈΡ;
- ΠΏΠΎΠ΄Π²ΠΈΠΆΠ½ΡΠΉ ΠΏΠ»Π°ΡΡΠΈΠΊΠΎΠ²ΡΠΉ ΠΊΠ°Π±Π΅Π»Ρ-ΠΊΠ°Π½Π°Π»;
- 4-ΠΊΠΎΠ½ΡΠ°ΠΊΡΠ½ΡΠ΅ ΠΊΠ°Π±Π΅Π»ΡΠ½ΡΠ΅ Π²ΠΈΠ»ΠΊΠΈ.
ΠΠ΅Ρ Π°Π½ΠΈΡΠ΅ΡΠΊΠΈΠ΅ ΡΠ°ΡΡΠΈ:
- Π»ΠΈΠ½Π΅ΠΉΠ½ΡΠ΅ Π½Π°ΠΏΡΠ°Π²Π»ΡΡΡΠΈΠ΅: Π΄Π»Ρ X β SBR 20 Π΄Π»Ρ Y ΠΈ Z β SBR 16;
- ΡΠ°ΡΠΈΠΊΠΎ-Π²ΠΈΠ½ΡΠΎΠ²Π°Ρ ΠΏΠ°ΡΠ° (Π¨ΠΠ) Π΄Π»Ρ X ΠΈ Y β Π΄ΠΈΠ°ΠΌΠ΅ΡΡΠΎΠΌ 16 ΠΌΠΌ, ΡΠ°Π³ 5 ΠΌΠΌ4
- Π² ΠΊΠ°ΡΠ΅ΡΡΠ²Π΅ ΠΏΠ΅ΡΠ΅Π΄Π°ΡΠΎΡΠ½ΠΎΠ³ΠΎ Π²ΠΈΠ½ΡΠ° Π΄Π»Ρ ΠΎΡΠΈ Z: ΡΡΠ°Π»ΡΠ½ΠΎΠΉ ΡΡΡΡΡ Ρ ΡΠ΅Π·ΡΠ±ΠΎΠΉ M10 Ρ ΡΠ°ΠΌΠΎΠ΄Π΅Π»ΡΠ½ΠΎΠΉ Π³Π°ΠΉΠΊΠΎΠΉ ΠΈΠ· Π΄Π΅Π»ΡΠΈΠ½Π°;
- Π°Π»ΡΠΌΠΈΠ½ΠΈΠ΅Π²ΡΠΉ ΠΏΡΠΎΡΠΈΠ»Ρ: 30Ρ 60 ΠΌΠΌ, Π½Π°ΡΠ΅Π·Π°Π½Π½ΡΠΉ Π½Π° ΠΊΡΡΠΊΠΈ Π΄Π»ΠΈΠ½ΠΎΠΉ 100 ΠΌΠΌ;Β
- Π°Π»ΡΠΌΠΈΠ½ΠΈΠ΅Π²Π°Ρ ΠΏΠ»Π°ΡΡΠΈΠ½Π° 15 ΠΌΠΌ ΡΠΎΠ»ΡΠΈΠ½ΠΎΠΉ;
- ΠΌΠΎΡΠ½ΡΠ΅ Π°Π½ΡΠΈΠ²ΠΈΠ±ΡΠ°ΡΠΈΠΎΠ½Π½ΡΠ΅ Π²ΡΡΠ°Π²Π½ΠΈΠ²Π°ΡΡΠΈΠ΅ Π½ΠΎΠΆΠΊΠΈ.
ΠΡΠΎΠ³ΡΠ°ΠΌΠΌΡ:
- CAD/CAM-ΠΏΡΠΎΠ³ΡΠ°ΠΌΠΌΠ° CamBam;
- ΠΏΡΠΎΠ³ΡΠ°ΠΌΠΌΠ° Π΄Π»Ρ ΡΠΏΡΠ°Π²Π»Π΅Π½ΠΈΡ ΡΡΠ°Π½ΠΊΠΎΠΌ Ρ Π§ΠΠ£ Mach4
Π‘ΡΠ°Π½ΠΎΠΊ Π² ΠΎΡΠ½ΠΎΠ²Π½ΠΎΠΌ ΠΏΠΎΡΡΡΠΎΠ΅Π½ ΠΈΠ· Π°Π»ΡΠΌΠΈΠ½ΠΈΠ΅Π²ΡΡ ΠΏΠ»Π°ΡΡΠΈΠ½ ΡΠΎΠ»ΡΠΈΠ½ΠΎΠΉ 15 ΠΌΠΌ ΠΈ Π°Π»ΡΠΌΠΈΠ½ΠΈΠ΅Π²ΡΡ ΠΏΡΠΎΡΠΈΠ»Π΅ΠΉ 30×60 ΠΌΠΌ. Π Π°Π±ΠΎΡΡ Π²ΡΠΏΠΎΠ»Π½ΡΠ»ΠΈΡΡ Ρ ΠΏΡΠΈΠΌΠ΅Π½Π΅Π½ΠΈΠ΅ΠΌ ΡΠ²Π΅ΡΠ»ΠΈΠ»ΡΠ½ΠΎΠ³ΠΎ ΠΈ ΡΠΎΠΊΠ°ΡΠ½ΠΎΠ³ΠΎ ΡΡΠ°Π½ΠΊΠΎΠ². ΠΠ»Π°ΡΡΠΈΠ½Ρ ΠΈ ΠΏΡΠΎΡΠΈΠ»ΠΈ Π·Π°ΠΊΠ°Π·ΡΠ²Π°Π»ΠΈΡΡ Π½Π°ΡΠ΅Π·Π°Π½Π½ΡΠΌΠΈ ΠΏΠΎ ΡΠ°Π·ΠΌΠ΅ΡΡ.
Β Β
3. ΠΡΡ Π₯
ΠΠ°Π·ΠΎΠ²Π°Ρ ΡΠ°ΠΌΠ° ΡΠ΄Π΅Π»Π°Π½Π° ΠΈΠ· 4 ΠΎΡΡΠ΅Π·ΠΊΠΎΠ² Π°Π»ΡΠΌΠΈΠ½ΠΈΠ΅Π²ΠΎΠ³ΠΎ ΠΏΡΠΎΡΠΈΠ»Ρ ΡΠ΅ΡΠ΅Π½ΠΈΠ΅ΠΌ 30Ρ 60 ΠΌΠΌ ΠΈ Π΄Π²ΡΡ Π±ΠΎΠΊΠΎΠ²ΡΡ ΠΏΠ°Π½Π΅Π»Π΅ΠΉ ΡΠΎΠ»ΡΠΈΠ½ΠΎΠΉ 15 ΠΌΠΌ. Π ΠΊΠΎΠ½ΡΠ΅ ΠΏΡΠΎΡΠΈΠ»Π΅ΠΉ Π΅ΡΡΡ ΠΏΠΎ Π΄Π²Π° ΠΎΡΠ²Π΅ΡΡΡΠΈΡ Π΄ΠΈΠ°ΠΌΠ΅ΡΡΠΎΠΌ 6,8 ΠΌΠΌ, Ρ ΠΏΠΎΠΌΠΎΡΡΡ ΠΌΠ΅ΡΡΠΈΠΊΠ° Π²Π½ΡΡΡΠΈ ΠΎΡΠ²Π΅ΡΡΡΠΈΠΉ Π²ΡΠΏΠΎΠ»Π½Π΅Π½Π° ΡΠ΅Π·ΡΠ±Π° Π8.
ΠΠ°ΡΠ΅Π·ΠΊΠ° ΡΠ΅Π·ΡΠ±Ρ Π² ΡΠΎΡΡΠ°Ρ Π°Π»ΡΠΌΠΈΠ½ΠΈΠ΅Π²ΠΎΠ³ΠΎ ΠΏΡΠΎΡΠΈΠ»Ρ
Π§ΡΠΎΠ±Ρ ΠΎΡΠ²Π΅ΡΡΡΠΈΡ Π½Π° ΠΊΠΎΠ½ΡΠ΅Π²ΡΡ ΠΏΠ°Π½Π΅Π»ΡΡ ΡΠΎΠ²ΠΏΠ°Π΄Π°Π»ΠΈ, ΠΏΡΠΈ ΡΠ²Π΅ΡΠ»Π΅Π½ΠΈΠΈ ΠΎΠ±Π΅ ΠΏΠ»Π°ΡΡΠΈΠ½Ρ Π·Π°ΠΆΠΈΠΌΠ°Π»ΠΈΡΡ Π²ΠΌΠ΅ΡΡΠ΅. ΠΠΎΡΠ΅ΡΠ΅Π΄ΠΈΠ½Π΅ ΠΊΠ°ΠΆΠ΄ΠΎΠΉ ΠΏΠ»Π°ΡΡΠΈΠ½Ρ ΠΏΡΠΎΡΠ²Π΅ΡΠ»Π΅Π½ΠΎ ΠΏΠΎ 4 ΠΎΡΠ²Π΅ΡΡΡΠΈΡ, ΡΡΠΎΠ±Ρ ΡΡΡΠ°Π½ΠΎΠ²ΠΈΡΡ ΠΏΠΎΠ΄ΡΠΈΠΏΠ½ΠΈΠΊΠΎΠ²ΡΠ΅ ΠΎΠΏΠΎΡΡ, ΠΈ ΡΠ΅ΡΡΡΠ΅ Π΄ΠΎΠΏΠΎΠ»Π½ΠΈΡΠ΅Π»ΡΠ½ΡΡ ΠΎΡΠ²Π΅ΡΡΡΠΈΡ Π² ΠΎΠ΄Π½ΠΎΠΉ ΠΈΠ· Π±ΠΎΠΊΠΎΠ²ΡΡ ΠΏΠ»Π°ΡΡΠΈΠ½ Π΄Π»Ρ ΠΊΡΠ΅ΠΏΠ»Π΅Π½ΠΈΡ Π΄Π²ΠΈΠ³Π°ΡΠ΅Π»Ρ.
ΠΡ ΠΊΡΡΠΎΡΠΊΠΎΠ² Π°Π»ΡΠΌΠΈΠ½ΠΈΡ (50Ρ 50Ρ 20) ΡΠ΄Π΅Π»Π°Π½Ρ 4 Π±Π»ΠΎΠΊΠ°, ΡΡΠΎΠ±Ρ ΠΏΡΠΈΠΊΡΠ΅ΠΏΠΈΡΡ Π²ΡΡΠ°Π²Π½ΠΈΠ²Π°ΡΡΠΈΠ΅ Π½ΠΎΠΆΠΊΠΈ. ΠΠ»ΠΎΠΊΠΈ ΠΏΡΠΈΠΊΡΡΡΠ΅Π½Ρ ΠΊ Π½Π°ΡΡΠΆΠ½ΡΠΌ ΠΏΡΠΎΡΠΈΠ»ΡΠΌ ΡΠ΅ΡΡΡΡΠΌΡ Π±ΠΎΠ»ΡΠ°ΠΌΠΈ Π5 Ρ ΠΌΠ΅Π±Π΅Π»ΡΠ½ΡΠΌΠΈ t-Π³Π°ΠΉΠΊΠ°ΠΌΠΈ.
ΠΠΈΠ½Π΅ΠΉΠ½ΡΠ΅ Π½Π°ΠΏΡΠ°Π²Π»ΡΡΡΠΈΠ΅ ΠΏΠΎΠ΄Ρ ΠΎΠ΄ΡΡ Π½Π΅ΠΏΠΎΡΡΠ΅Π΄ΡΡΠ²Π΅Π½Π½ΠΎ ΠΊ Π°Π»ΡΠΌΠΈΠ½ΠΈΠ΅Π²ΡΠΌ ΠΏΡΠΎΡΠΈΠ»ΡΠΌ. ΠΠ»Ρ ΠΎΡΠΈ X ΠΈΡΠΏΠΎΠ»ΡΠ·ΠΎΠ²Π°Π»ΠΈΡΡ ΡΠ΅Π»ΡΡΡ Π΄ΠΈΠ°ΠΌΠ΅ΡΡΠΎΠΌ 20 ΠΌΠΌ. ΠΡΠ΅Π΄Π²Π°ΡΠΈΡΠ΅Π»ΡΠ½ΠΎ ΠΏΡΠΎΡΠ²Π΅ΡΠ»Π΅Π½Π½ΡΠ΅ Π² ΠΎΡΠ½ΠΎΠ²Π°Π½ΠΈΠΈ Π»ΠΈΠ½Π΅ΠΉΠ½ΡΡ Π½Π°ΠΏΡΠ°Π²Π»ΡΡΡΠΈΡ ΠΎΡΠ²Π΅ΡΡΡΠΈΡ ΡΠΎΡΠ½ΠΎ ΡΠΎΠ²ΠΏΠ°Π΄Π°ΡΡ Ρ ΠΏΠ°Π·Π°ΠΌΠΈ Π² Π°Π»ΡΠΌΠΈΠ½ΠΈΠ΅Π²ΡΡ ΠΏΡΠΎΡΠΈΠ»ΡΡ . ΠΠ»Ρ ΡΡΡΠ°Π½ΠΎΠ²ΠΊΠΈ ΠΈΡΠΏΠΎΠ»ΡΠ·ΠΎΠ²Π°Π½Ρ Π±ΠΎΠ»ΡΡ Π5 ΠΈ ΠΌΠ΅Π±Π΅Π»ΡΠ½ΡΠ΅ t-Π³Π°ΠΉΠΊΠΈ.
Β Β
4. ΠΠΎΠΊΠΎΠ²ΡΠ΅ ΠΏΠ»Π°ΡΡΠΈΠ½Ρ ΠΏΠΎΡΡΠ°Π»Π°
ΠΠΎΠΊΠΎΠ²ΡΠ΅ ΠΏΠ»Π°ΡΡΠΈΠ½Ρ ΠΏΠΎΡΡΠ°Π»Π° ΠΏΠΎΡΡΠΈ ΠΎΠ΄ΠΈΠ½Π°ΠΊΠΎΠ²Ρ, Π½ΠΎ Π² ΠΎΠ΄Π½ΠΎΠΉ ΠΈΠ· Π½ΠΈΡ ΠΏΡΠΎΡΠ²Π΅ΡΠ»Π΅Π½Ρ ΡΠ΅ΡΡΡΠ΅ Π΄ΠΎΠΏΠΎΠ»Π½ΠΈΡΠ΅Π»ΡΠ½ΡΡ ΠΎΡΠ²Π΅ΡΡΡΠΈΡ Π΄Π»Ρ ΠΊΡΠ΅ΠΏΠ»Π΅Π½ΠΈΡ ΠΌΠΎΡΠΎΡΠ°. ΠΠ΅ΡΡ ΠΏΠΎΡΡΠ°Π» ΠΈΠ·Π³ΠΎΡΠΎΠ²Π»Π΅Π½ ΠΈΠ· Π°Π»ΡΠΌΠΈΠ½ΠΈΠ΅Π²ΡΡ ΠΏΠ»Π°ΡΡΠΈΠ½ ΡΠΎΠ»ΡΠΈΠ½ΠΎΠΉ 15 ΠΌΠΌ. Π§ΡΠΎΠ±Ρ ΠΎΡΠ²Π΅ΡΡΡΠΈΡ ΠΎΠΊΠ°Π·Π°Π»ΠΈΡΡ ΡΠΎΡΠ½ΠΎ Π² Π½ΡΠΆΠ½ΠΎΠΌ ΠΌΠ΅ΡΡΠ΅, Π² ΡΡΠ°ΡΠ΅Π»ΡΠ½ΠΎ ΠΎΡΠΌΠ΅ΡΠ΅Π½Π½ΡΡ ΠΌΠ΅ΡΡΠ°Ρ ΡΠ»Π΅ΡΠ°ΡΠ½ΡΠΌ ΠΊΠ΅ΡΠ½Π΅ΡΠΎΠΌ Π±ΡΠ»ΠΈ ΠΏΡΠΎΠ±ΠΈΡΡ ΡΠ³Π»ΡΠ±Π»Π΅Π½ΠΈΡ, ΠΈ ΠΏΠΎ ΡΡΠΈΠΌ ΠΌΠ΅ΡΠΊΠ°ΠΌ ΠΏΡΠΎΡΠ²Π΅ΡΠ»Π΅Π½Ρ ΠΎΡΠ²Π΅ΡΡΡΠΈΡ Π½Π° ΡΠ²Π΅ΡΠ»ΠΈΠ»ΡΠ½ΠΎΠΌ ΡΡΠ°Π½ΠΊΠ΅, ΡΠ½Π°ΡΠ°Π»Π° ΡΠ²Π΅ΡΠ»ΠΎΠΌ ΠΌΠ΅Π½ΡΡΠ΅Π³ΠΎ Π΄ΠΈΠ°ΠΌΠ΅ΡΡΠ°, Π·Π°ΡΠ΅ΠΌ β Π½ΡΠΆΠ½ΠΎΠ³ΠΎ.
ΠΠ·-Π·Π° ΡΠΎΠ³ΠΎ, ΠΊΠ°ΠΊ ΡΠΏΡΠΎΠ΅ΠΊΡΠΈΡΠΎΠ²Π°Π½ ΠΏΠΎΡΡΠ°Π», ΠΏΡΠΈΡΠ»ΠΎΡΡ ΡΠ²Π΅ΡΠ»ΠΈΡΡ ΠΎΡΠ²Π΅ΡΡΡΠΈΡ Π² ΡΠΎΡΡΠ°Ρ Π±ΠΎΠΊΠΎΠ²ΡΡ ΠΏΠ»Π°ΡΡΠΈΠ½ ΠΈ Π΄Π΅Π»Π°ΡΡ Π² ΠΎΡΠ²Π΅ΡΡΡΠΈΡΡ ΡΠ΅Π·ΡΠ±Ρ Π8.Β
Β Β
5. Π‘Π±ΠΎΡΠΊΠ° ΠΏΠΎΡΡΠ°Π»Π°
ΠΠΎΡΡΠ°Π» ΡΠΎΠ±ΡΠ°Π½ ΠΈ ΡΡΡΠ°Π½ΠΎΠ²Π»Π΅Π½
ΠΡΡΠ°Π»ΡΠ½Π°Ρ ΡΠ°ΡΡΡ ΠΏΠΎΡΡ
90000 Build Your CNC — CNC, CNC Router, CNC Router Kits, CNC Machine Kits, Laser Machines, CNC Machine Tools, and CNC Cutting 90001 90002 Design Your CNC 90003 90004 Machine Base: greenBull v2 Fabricator Pro 90005 90004 Machine Features: 90005 90004 CNC Cutting Area: 90005 90004 Bed Angle: 90005 90004 Purchase Options: Plans Plans and Hardware Kit of Parts Assembled Machine 90005 Purchase Plans for 90014 0,000.00 90015 Contact Sales for Academic Pricing 90004 What’s Included in the 90017 Plans 90018 option: 90005 90004 90017 CNC plans option 90018 includes a large set of 24 «x36» plans which includes the BOM (Bill of Materials) for the complete machine, all of the structural components that will need to be cut out or fabricated, and a full set of detailed instructions for assemblling the machine. The instructions will also include detailed wiring schema with suggested wiring through the machine.Domestic shipping is free for this option. 90005 90004 90017 CNC Plans and hardware option 90018 includes the large plans set, motion electronincs (motors, drivers, power supplies, and controller / interface), hardware to fasten all of the components together, a water cooled spindle with VFD and all of the necessary mechanical components (rails, bearing blocks, lead screws, bearings, etc.). This option does not include the structual components or wire / cable.The plans include the measurements and cut sheets for the structural components. Shipping cost will be provided when parts are ready to be shipped. 90005 90004 90017 CNC Kit option 90018 includes the plans, hardware, electonics, wire, cable, tubing, water cooling components, mechanical components, water cooled spindle, and the structural components. All you need to do is assembl the machine, or find someone in your area that can assemble the machine (We are building a list of individuals to help assemble in your area).Shipping cost will be provided when parts are ready to be shipped. 90005 90004 90017 Assembled Option 90018 includes the complete CNC Router and / or Laser is assembled. The fully assembled machine will be delivered via freight or for pick up. The customer is responsible for the freight charges. We use FreightQuote.com (domestic) and iContainers.com (international) to determine logistics and shipping cost. Freight cost will be provided when the machine is ready to be shipped.90005 .90000 Software, Drivers, & Boards [Complete DIY Guide] 90001 90002 90003 90004 90002 The CNC Controller or CNC Control is the package of electronics and software that take input either from g-code or the cnc control panel and converts it to the signals the CNC machine’s motors need to move the CNC axes. 90004 90002 The controller with its CNC Control Software and electronics are the most complex part of a CNC Machine. In this article, we’ll break it down along several dimensions each of which you can then drill down on further: 90004 90009 90010 Types of CNC Controllers 90011 90010 CNC Controller Electronics 90011 90010 CNC Controller Software 90011 90010 Choosing the Best CNC Controller for Your CNC Machine 90011 90018 90019 Types of CNC Controllers 90020 90021 Industrial OEM CNC Controllers 90022 90002 Industrial OEM CNC Controllers are the ones used on Industrial CNC Machines like Haas.They’re the very hind end of the market. 90004 90002 These are not very common for DIY projects due to their expense. Not only is the controller itself expensive and fairly hard to come by (though one does see them from time to time on eBay), but Industrial OEM Controllers expect premium sub-components too. Industrial Quality Servo Drives, Home / Limit Switches, and all the rest really run up a hefty price tag in a hurry. 90004 90002 While these controls are expensive, lately I’ve seen controls such as the low-end of the Siemens line coming down in price in places like eBay.It looks like they’re testing the low-end market. If they keep coming down, these controls may make more sense on a DIY CNC Project than it seems. 90004 90002 I’m not going to talk further about these controls as they’re a pretty advanced topic. You might find the article I did that analyzes what features Hobby CNC Controllers are missing compared to industrial controls intersesting. 90004 90021 CNC Retrofit Controllers 90022 90002 Just a small step down from Industrial OEM Controllers are CNC Retrofit Controllers like Centroid.90004 90002 These controllers are marketed for converting manual machines to CNC, for example, a Bridgeport manual milling machine. They’re also sold as a way to update obsolete controls on industrial CNC Machines to bring the more up-to-date features and performance. 90004 90002 They’re still not cheap, but they’re starting to fall into the range of what a DIY CNC’er might afford. 90004 90021 PC Based CNC Controllers 90022 90002 There are three main players in this market: 90004 90009 90010 Mach 3 & Mach 4 90011 90010 LinuxCNC 90011 90010 FlashCut 90011 90018 90002 All three have good reputations with varying trade-offs of features, functionality, price, and ease of use.90004 90053 Mach 3 90054 90002 90004 90002 Art Fenerty founded ArtSoft in 2001 and launched Mach 3, which was based on an offshoot of the original EMC (which is now LinuxCNC) code base. Art wanted a CNC Controller that runs on Microsoft Windows PC’s rather than Linux, so it took a major rewrite and the two do not share much in common any more. 90004 90002 According to our 2017 Survey, Mach 3 is the most popular CNC Controller at the low-end, with 47% market share. The next closest was LinuxCNC.90004 90053 LinuxCNC (My personal favorite!) 90054 90002 90064 90004 90002 LinuxCNC has its origins in NIST’s «Enhanced Machine Controller» project, hence its original name «EMC» and «EMC 2». Since the EMC corporation owns the trademark, the name was changed to LinuxCNC in 90004 90002 LinuxCNC is Open Source software, which means you can actually obtain the latest source code should you wish to understand or modify it. It also means that a much larger audience, including companies like Tormach, can contribute to LinuxCNC.90004 90002 While it’s extremely cool that LinuxCNC is Open Source, it’s the contributions of Tormach, and the PathPilot «flavor» of LinuxCNC that made it my favorite choice. Having used Mach 3 for years, I can tell you that Tormach made a good decision when they moved from Mach 3 to LinuxCNC. 90004 90002 PathPilot is simply more stable, more powerful, and more user friendly than Mach 3, and there’s not much more you could ask for. 90004 90002 Now, getting your own PathPilot CNC Controller up and running for your own DIY CNC may not be quite as straightforward.You’ll have to assemble a controller that matches Tormach’s and get a copy of PathPilot up and running on it. There are various articles out there that purport to help. I have not verified any of them yet, but if it can be done, you’ll have a sweet setup. 90004 90053 FlashCut 90054 90002 90079 90004 90002 FlashCut is a very nifty plug-and-play CNC Controller. The company was started back in +1993, so it’s been around a long time and the design is very mature. 90004 90002 While its Market Share is not as big as Mach4 or LinuxCNC, I’ve heard nothing but good about FlashCut.Here’s a great video by Dave DeCaussin (one of the original founders of FADAL) showing how easy it is to set up a FlashCut system: 90004 90002 90086 90087 90004 90002 I’ve heard some folks say they think the FlashCut is too expensive compared to other solutions. I put pencil to paper one time comparing it to a Mach4 system and I found that if you configure a system with all the capabilities of FlashCut (like a USB pulser for Mach4) that the premium is not as high as you may think. 90004 90002 Having a completely engineered turnkey system that’s plug-and-play is worth a bit of premium if you ask me.90004 90053 Mach 4 90054 90002 90004 90002 Mach 4 is the newest solution in this category, and has by far the smallest market share. It’s almost a start over from scratch rewrite of Mach 3. The developers claim it shares less than 1% of Mach 3’s code. 90004 90002 It’s quite a bit more expensive, but in theory, should be better. From my perspective, the jury is still out-not enough market share or experience to bet on it when the competition is well entrenched and has far larger installed bases.90004 90021 Microcontrollers: USB, Arduino, Rasperry Pi, TinyG, & More 90022 90002 Microcontrollers allow CNC Controllers to be built that are cheap and fit into a small space. 90004 90002 CNC Microcontrollers are a relatively new development made possible by continued advances in miniaturization and software. The idea is to put everything you need on one small circuit board, or perhaps a microcontroller board with a daughterboard commonly called a «Shield». 90004 90002 Here’s a quick list of all the most popular CNC Microcontrollers: 90004 90053 Grbl 90054 90002 Grbl (pronounced gerbil) runs on an Arduino microcontroller.It’s open source, and in use by a lot of different firms including: 90004 90002 90004 90002 That’s pretty much an all-star cast, so you can be sure GRBL has a vibrant ecosystem of products and people who can help and also that it has a bright future. The Shapeoko people told me they evaluated a bunch of these and felt GRBL was head and shoulders the winner for their needs. 90004 90053 TinyG / TinyG2 90054 90002 90004 90002 TinyG is another microcontroller-based system. It’s related to grbl, but it’s not the same.The TinyG codebase was forked from grbl in 2010 and has been going its own way ever since. TinyG claims to do some things better or differently: 90004 90009 90010 While grbl is 3-axis (XYZ), TinyG is 6-axis so can support additional rotary axes. By default, TinyG controllers have 4 stepper motor drivers while gShield (used with grbl) has 3. 90011 90010 TinyG claims some fancy motion control algorithms, specifically «jerk» acceleration profiles for smoother motion. 90011 90010 TinyG claims its implemented on a higher performance microcontroller that has more memory.90011 90018 90053 PlanetCNC 90054 90002 90004 90002 PlanetCNC is a single-board CNC Controller that hails from Slovenia, Europe. Like TinyG, it’s also a 4-axis solution. In our 2017 CNC Controller Survey, GRBL had # 1 market share, PlanetCNC # 2, and TinyG # 3 among the microcontrollers. 90004 90019 CNC Controller Electronics 90020 90002 Here’s the sort of electronics you’ll find inside most CNC Controller cabinets: 90004 90002 90142 90004 90002 Let’s go over the function of each.90004 90021 Breakout Board 90022 90002 90149 90004 90002 CNC Breakout Board for Parallel Port … 90004 90002 The role of the Breakout Board is to take a connection from your PC and generate the appropriate signals needed to operate the Motor Drives, VFD, and Contactors. 90004 90002 For a deeper dive on Breakout Boards, see our article: 90004 90021 [CNC Breakout Boards] 90022 90002 The most common breakout boards, such as the one pictured above, are connected to your PC’s parallel port.This can be a problem, since parallel ports are obsolete and most new computers do not have them. In addition, there are a lot of performance and reliability issues associated with breakout boards. 90004 90002 Newer and more sophisticated models are actually motion control boards, though some may still refer to them as breakout boards. These boards can connect via USB or Ethernet cable. 90004 90002 It’s impossible to control a USB connection finely enough to directly generate the precise pulses needed by Axis Motor Drives, so the role of a Motion Controller is to accept higher level commands and generate the pulses.The result is much higher performance a at a slightly higher cost. 90004 90002 We also have a great article on Motion Control Boards: 90004 90021 [Motion Control Boards] 90022 90021 Motor Drives / Drivers 90022 90002 90172 90004 90002 Leadshine Easy Servo Drives … 90004 90002 Given a breakout or motion control board, your PC’s signals are converted to 2 signals: 90004 90009 90010 Step: Each pulse on the step line tells the motor drive to move the motor 1 step. 90011 90010 Direction: If the polarity of direction is one way, it commands the motion to be clockwise.Switching polarity reverses direction to counter-clockwise. In fact, polarity is perhaps not the best term as it may simply be signal for one direction and no signal for the other. 90011 90018 90002 In addition to step / dir signals, the motor drive accepts DC power, and, in the case of servos, it accepts the encoder signal as well. In exchange, it pumps out power to the motor in such a way as to control its motion. 90004 90021 DC Power Supply (Not Shown) 90022 90002 The photo above did not show a DC power supply because the motor drives used are capable of accepting AC.That’s very convenient, but not always the case. You may need to purchase or build a DC power supply to provide power to your motor drives. 90004 90002 One of the first CNC Controllers I built used this DC Power Supply: 90004 90002 90193 90004 90021 Contactors 90022 90002 90198 Contactor 90199 is a fancy name for a relay capable of being used for higher voltages. In this case, most contactors are used to switch AC, for example to control a coolant pump. Your breakout board typically supplies a 5V DC signal.The Contactor’s job is to turn on (or off if normally closed) AC power when the 5V signal is on and turn it back off when the 5V signal goes away. 90004 90021 VFD: Variable Frequency Drive 90022 90002 90204 90004 90002 Powering and controlling a CNC Spindle is a job for a Variable Frequency Drive, abbreviated VFD. 90004 90002 Choosing and programming a VFD is a complex process that we can not go into here. For starters, you’ll want to make sure your VFD has enough power to run your spindle motor.There are a number of different kinds of VFD, but the best bang for the buck comes from something called a «90198 Sensorless Vector Drive 90199.» 90004 90019 Choosing the Best CNC Controller for Your CNC Machine 90020 90002 Choosing the Best CNC Controller for your CNC Machine is a matter of balancing some important trade-offs: 90004 90002 90217 90004 90002 Trade-Offs when choosing the best CNC Controller … 90004 90002 The trade-offs boil down to all-out performance versus ease-of-success.A simple turnkey kit that has everything you need is pretty easy to get running. But, it may sacrifice some all-out performance relative to carefully cherry-picking the very best of each component for your application. 90004 90002 Ask yourself where you skill set and interests lie. It will take longer and very likely cost more to get that all-out solution up and running reliably. It will also take a lot more skills. 90004 90002 Are you good at diagnosing problems in electrical circuits? Can you read through all the spec sheets and properly determine which components are compatible with one another? Do you enjoy all that? 90004 90002 If the answer is «Yes» to those questions, you’re in a better position to try all the «bleeding» edge (i.e. leading edge) goodies in your project. If the answer is «No», look for a proven kit that has everything you need and a large community of folks you can turn to with questions. 90004 90021 Market Share of Different CNC Controllers 90022 90002 Speaking of community, I think they’re critically important to the success of DIY projects. 90004 90002 I’ve been on that Bleeding Edge where nobody can help or answer questions and it can get lonely. These days, I prefer to choose products that have a decent-sized community.I like to see evidence that others have already accomplished what I’m looking for with the components I’m considering before I take the leap. 90004 90002 You’ll find you can get 80% of the performance with only 20% of the pain if you take that approach. 90004 90002 To have a decent community, products need a lot of users. You can learn more about the market share of various controls from our CNC Controller surveys: 90004 90021 [CNC Surveys] 90022 .90000 10 Features Pros Have that Hobby CNC Controllers Dont 90001 90002 90003 Hobby CNC Controllers have gotten to where they’re quite powerful. I recently saw an article on a single chip CNC controller-no need for a PC, just add a few outboard parts and it drives the stepper motors, provides an LCD screen UI, and quite a lot more. Amazing stuff, and it’s only going to keep getting better over time. Despite their newfound power, there are a number of features that Pro CNC Controls have that most Hobby CNC Controllers do not.Here are 10 of them: 90004 90002 90006 1. Better Macros and Subprograms: Fanuc Macro B vs Mach4 vs LinuxCNC 90007 90004 90002 This is one of the biggest ones for me. The ability to program the g-code in Pro machines is quite a ways ahead of the Hobby Controllers such as Mach 3 or LinuxCNC. What’s specifically missing so far are branching structures-IF, GOTO, and WHILE loops. You can only do so much with #variables and subprograms without branching. Branching is the ability for the g-code to change what it will do based on outside inputs.90004 90002 90006 2. More and Better Canned Cycles 90007 90004 90002 This is another one that makes a big difference, particularly when programming lathes. Canned cycles like G71 on the lathe make it fairly easy to hand program even complex profiles quickly and without the need for CAM software. 90004 90002 90006 3. Rigid Tapping via Closed Loop to the Control 90007 90004 90002 There’s a lot of Holy War diatribe about whether or not there is Closed Loop all the way back to the Control when discussing such things as Mach4 versus LinuxCNC.I prefer to look at what specific features the user gets from Closed Loop rather than worrying about the theoretical implications, so I’m going to name a few here. First up is Rigid Tapping. In theory it should be pretty straightforward to get this into Hobby Controls given that they support an encoder for threading on lathes, but you do not see it very often. It’s not easy to do it right for one thing. 90004 90002 The acid test is rapid tapping into a blind hole. If there’s a mistake you either get too little of the hole threaded or the tap hits the bottom and usually breaks.It’s an unforgiving application. 90004 90002 90006 4. Increased Homing Accuracy via Closed Loop 90007 90004 90002 Another neat trick the Pros use is to tremendously increase the accuracy of Home Switches by tying them to the Encoders on each axis. The actual Home Switch only has to identify the neighborhood within 1 encoder revolution. The precise position can then be read from the encoder position to an accuracy that’s much higher than can be achieved with a simple Home Switch. 90004 90002 90006 5.Advanced Acceleration and Shape Control 90007 90004 90002 Acceleration is always a bit of a bugaboo for CNC machines. They can not accelerate to the commanded feedrate instantly nor stop on a dime. In fact, it is surprising how often they’re not going the speed you thought you’d programmed them to go because they’re busy trying to accelerate or decelerate to get there. We added some information to our G-Wizard Editor that tries to tell you what acceleration is doing to g-code program run times as well as what’s happening line by line.That’s extremely useful for cost estimating and for tuning up g-code part programs to run better. 90004 90002 The very best Controllers are all over the acceleration problem. They not only understand the acceleration capabilities of the machine, they also understand the actual shape of the acceleration curve. This can lead to a number of advantages including greater precision, smoother / faster speed changes, better surface finishes, and ultimately, shorter cycle times. They user this information together with Closed Loop Information and Lookahead Information about what the g-code will do next to try to anticipate and stay ahead of the game.They can provide capabilities like Automatic Corner Override, Advanced Contour Control, Advanced Feed Forward Control, and Advanced Acceleration Control. 90004 90002 If you’re doing 3D profiling or running a fancy HSM toolpath you will love having these features available from your Controller. 90004 90002 90006 6. Machine Compensation 90007 90004 90002 No mechanical device is perfect. No ballscrew is without at least some small amount of backlash, nor does every inch of the ballscrew thread advance with perfect precision.Sometimes a commanded move of an inch is 0.9996 inches while other times it may be 1.0003 inches. With the right software in your Controller, it can try to compensate for these issues. There’s Backlash and Pitch compensation for the aforementioned ballscrew problems. Add to that straightness compensation which adjusts for the fact that the axes of the machine are not completely orthogonal to one another. As you move a machine in X, it may change Y or Z some tiny amount. Another important source of error is addressed by Temperature Compensation.As your machine warms up, parts expand at different rates. On a hot day it may be one thing and then you fire it up in the winter before warm up and it is quite another. 90004 90002 Good controls can compensate for all of these things using a variety of techniques. They are calibrated periodically by a Ballbar or Laser Interferometer test to reset the compensation settings. Really fancy machines may even have glass scales similar to DRO scales that are continuously reading how much each axis actually moved and using that to update the Controller on what’s really going on.90004 90002 Some of this is available for Hobby Controllers-backlash compensation and leadscrew pitch compensation are the ones I am familiar with. But it’s done in a far simpler manner and Hobby Machines seldom get the precise calibration to dial in compensation that Pro machines do. 90004 90002 90006 7. Advanced Tool and Part Program Management 90007 90004 90002 Pro CNC Machines are often used for long part runs, so they have features to help manage Tools and Part Programs that are geared to that application.They’ll keep up with how long each tool in the changer has been in use, for example. On the part program side they can track program usage, verify version data, and organize programs in folders with extended descriptors. Really fancy controls can provide some front end menus for the operator that help make their job easier and give them options. For example, it is often convenient to be able to skip some parts of the program, for example when reworking parts that already have those features machined and just need to do the later work.90004 90002 90006 8. Tool Compensation 90007 90004 90002 I like to think of Tool Compensation as the Poor Man’s CAM, but it is so much more. Tool compensation is essentially the ability to program g-code for the tool centerline instead of the tool’s edge. The control will «move the tool over» by the right amount for the cut. When we specify our programs in this way, it is easier to write programs by hand, hence the «Poor Man’s CAM» nickname. But it also unlocks a lot of power for the Shop Floor to make changes using wear offsets without having to change the part program’s g-code.90004 90002 Suppose you run a part and inspect it. Some of the features are out of tolerance a little bit. Compensating for that without tool compensation likely means you’re going to have to adjust it at the CADCAM level-a complicated and slow process. But, if your part program uses Tool Compensation, you can simply dial in another wear offset and suddenly your part is right on. Professionals constantly use this capability to increase the precision of their parts and to make minor adjustments where it just would not be worth it to go back through a CADCAM cycle.90004 90002 Wait a minute, you’re saying-Hobby Controllers have this feature. Yes, sort of, but there are so many reports of bugs in the feature that I do not know of very many Hobby CNC’ers that are successfuly using the feature very often. You have to use it just right or it will not work for you, and often the failures are mysterious and can even lead to machine crashes. Tormach even did an article series in Digital Machinist about how to get it to work. They have quite a few caveats in the operator manual for the PCNC 1100 mill suggesting not to use compensation in cases such as: 90004 90002 — Subroutine programming 90004 90002 — Canned cycles 90004 90002 — Macro programming 90004 90002 — Polar mode 90004 90002 — With run from here function 90004 90002 — With multiple work offsets 90004 90002 Those are some pretty serious limitations.If you’re running a Hobby Controller and have gotten Tool Comp to work, good on you. For most, there’s just too many gotchas. One could argue that stability in general has been more of a problem for Hobby Controllers than Pro Controllers. I will say that while Mach4 on my mill has had a number of bugs off and on, LinuxCNC on my Tormach Lathe has been solid so far. The Tormach guys really gave it a wringing out. 90004 90002 90006 9. Dedicated Control Panel 90007 90004 90002 First let me say that it is entirely possible to build a very nice dedicated control panel for a Hobby CNC Controller.I’ve got a whole page with photos of CNC Control Panels for those who want inspiration. But once again, they’re not very common on Hobby Controllers whereas they are completely the norm on Pro Controls. The reason is simple, these panels are rugged enough for the Shop Floor and they can be significantly more productive for machine operators than trying to use a keyboard and mouse. 90004 90002 90006 10. Drip Feeding for Remote Control 90007 90004 90002 This is another of my favorite Pro-features because it enables you to «remote control» the machine.Essentially, drip feed means giving the CNC Machine a little bit of g-code at a time. It executes that g-code and then comes back for more. The code is normally delivered via RS-232 serial cable, but there are a lot of other options for newer machines. Drip Feed was originally invented as a way around the memory limitations of early CNC Controls. They just could not hold very large programs so drip feed gave them the g-code a little bit at a time. It’s still used quite often for that purpose, but increasingly it is also used to automate and monitor the deliver of g-code to machines.Using this approach helps guarantee the correct version of the g-code is being executed, it can gather information from the machine about what it’s doing to use in reporting and optimization, and it can facilitate complex «Lights Out» automated operation. 90004 90093 Bonus: 4 Things Hobby Controllers do that Pros Do not 90094 90002 Okay Hobbyists, I know you’re smarting a bit over that list. Some of it you’re pretty sure you can tackle and some of it you just do not care about. There’s also some things Hobby Controllers do that the Pros do not that are very cool, so let’s talk about those for a minute.90004 90002 90006 1. Cost 90007 90004 90002 There’s no getting around it-Pro Controllers are expensive. It’s so expensive to add a name brand controller to a machine that many companies have gone to the expense of creating their own controls to keep their individual machine cost down. I had one manufacturer tell me the difference in cost between their control and say a Fanuc was thousands of dollars and they had come to regard their control as being better. Hobby Controllers are very cheap-sometimes free if you have an old PC laying around.LinuxCNC is open source software, for example. Mach4 is not very expensive either. 90004 90002 90006 2. Memory and LAN Connectivity 90007 90004 90002 These are options on the Pro Controls but they’re so much more expensive that a lot of machines have no LAN connection and not as much RAM memory as they would like. With proprietary equipment there is a serious markup. I remember one time when I was VP of Engineering for Borland looking into 1 GB Ethernet cards for our testing lab. Test results were coming too slowly because the LAN was congested.The boards were $ 99 at Fry’s so I came running back to tell the Lab manager that we could upgrade. «What about our Sun Workstations?» was the response. It seems the exact same 1 GB LAN card for the Sun (presumably with just a little different BIOS, but it was easy to see it was an identical card) was over $ 1000! 90004 90002 So it is with Pro CNC Controllers. Memory, LAN connection, and other goodies have a very high markup. On the Hobby Controller side we take this stuff for granted because it’s cheap and abundant on PC’s.90004 90002 90006 3. Modern UI 90007 90004 90002 Hobby Controllers run on Windows, so they have a Consumer-Grade User Interface. That can be a lot slicker than what many Pro CNC Controllers provide, some of which looks like a bad day on a DOS machine we have not seen in so many years we hardly can remember it. This is not true of all Pro Controllers, as many are based on Windows too. But it sure seems like there are lots of truly ugly Controller UI’s out there. 90004 90002 90006 4. Customizability 90007 90004 90002 This is another one where Hobby Controllers excel.It’s very easy to customize the software so it runs the way you’d like it to. There are some really nice screen sets out there for Mach4, and LinuxCNC is Open Source so anything about it can be customized. This means there are a lot more 3rd party products out there like the Mach Standard Mill screen set. 90004 90002 Slick add-ons for probing and so on are common. I remember visiting a friend’s shop who had just gotten in a fancy Heidenhain probe set up. There was no UI for it on his Fanuc control because there’s no provision for custom UI.He had to wade through something like 1400 custom subprograms that came (at extra cost) with the probe and run them by hand to perform various probing tasks. 90004 90002 There are exceptions to this. Datron has added a very nice customization layer to their G-Code control, for example. 90004 90093 Conclusions 90094 90002 Pro CNC Machines are not going to be switching to Hobby CNC Controllers any time soon-there’s too much that they need that the Hobby Controllers lack. I have not even touched on the whole topic of hardware control of motion, which can be added to Hobby Controllers, but is still not as common as on Pro Equipment.90004 90002 On the other hand, Hobby Controllers keep getting more powerful. A lot of the new work is on the low end-providing the basic support that a 3D Printer or lower end CNC Router needs to operate. As mentioned, we even have single chip solutions for such machines now. The next step will be adding more g-code features to those basic Controllers. The fact that many of these Hobby Controllers are Open Sourced makes it easier for more people to contribute improvements. If you wanted to add full Fanuc Macro B support to LinuxCNC, it’s very doable, for example.90004 90002 I hope we see lots of these features I’ve described finding their way into Hobby Contollers soon. The next 2 to 5 years should be an exciting time in the industry. If at some point they become good enough to start challenging the Pros, that’ll be interesting too as they certainly do have a cost advantage. 90004 90002 90006 Join 100,000+ CNC’ers! 90007 Get our latest blog posts delivered straight to your email inbox once a week for free. Plus, we’ll give you access to some great CNC reference materials including: 90004.90000 90001 CENTROID CNC controls, CNC Milling Machines, CNC Lathes, CNC Routers, 5 Axis CNC Cylinder Head Porting Machines, CNC Retrofits. Digitizing, Automatic Tool Changers, Probes, CNC Rotary Tables, Conversational Programming, Auto Tool Measurement. 90002 90003 90004 90005 90006 90007 90003 90004 Cost 90005 90004 $ 299 w / Centroid Free CNC software. 90012 add $ 139 w / Centroid Pro software 90012 add $ 399 w / Centroid Digitizing Bundle 90005 90004 $ 2249 90012 Centroid CNC software included 90005 90004 $ 1595 90012 Centroid CNC software included 90005 90007 90003 90004 Maximum number of Axes 90005 90004 4 90005 90004 6 90005 90004 8 90005 90007 90003 90004 Compatible with Mills, Lathes, Routers 90012 and other specialty machines 90005 90036 Yes 90005 90036 Yes 90005 90036 Yes 90005 90007 90003 90004 AC Servo Motor / Drive compatible 90005 90036 Yes, (Step and Direction) 90005 90036 No 90005 90036 Yes, Position / Precision & Velocity modes 90005 90007 90003 90004 DC Servo Motor / Drive compatible 90005 90036 Yes, (Step and Direction) 90005 90036 Yes, up to 15 amps (continuous) per axis 90005 90036 Yes, using the Centroid AC / DC drive up to 60 amps per axis.90005 90007 90003 90004 Stepper Motor / Drive compatible 90005 90036 Yes 90005 90036 No 90005 90036 No 90005 90007 90003 90004 True Closed Loop Operation 90005 90036 No 90005 90036 Yes 90005 90036 Yes 90005 90007 90003 90004 Built in Motion Control CPU 90005 90036 Yes 90005 90036 Yes 90005 90036 Yes 90005 90007 90003 90004 Built in DC servo motor amplifier 90005 90036 No 90005 90036 Yes 90005 90036 No 90005 90007 90003 90004 Built in PLC 90005 90036 Yes 8 In, 8 Out (two relay) 90005 90036 Yes, 16 In, 9 relay out 90005 90036 Yes, 16 In, 9 relay out 90005 90007 90003 90004 Optically Isolated Inputs 90005 90036 Yes 90005 90036 Yes 90005 90036 Yes 90005 90007 90003 90004 Fused Relay Outputs 90005 90036 No, installer adds fuse 90005 90036 Yes 90005 90036 Yes 90005 90007 90003 90004 On board relay output types 90005 90036 2 SPST 90005 90036 7 SPST and 2 SPDT 90005 90036 7 SPST and 2 SPDT 90005 90007 90003 90004 Built-in Analog spindle control output 90005 90036 Yes 0-10 vdc, 12 bit 90005 90036 Yes, 0-10, + -10, 0-5, + -5 12 bit 90005 90036 Yes, 0-10, + -10, 0-5, + -5 16 bit 90005 90007 90003 90004 Runs on Centroid Mill 90012 or Lathe CNC software 90005 90036 Yes 90005 90036 Yes 90005 90036 Yes 90005 90007 90003 90004 Base Centroid CNC software included with CNC control board price 90005 90036 Centroid CNC12 «Free» CNC software Mill and Lathe 90005 90036 Centroid CNC11 software Mill and Lathe 90005 90036 Centroid CNC11 CNC software Mill and Lathe 90005 90007 90003 90004 Centroid CNC Software options 90005 90004 Centroid Mill «Pro» CNC software $ 139 90012 Centroid Lathe «Pro» CNC software $ 139 90012 Centroid «Digitizing Bundle» CNC software $ 399 90005 90004 Rigid Tapping, CSR, Scale Feed back for servo positioning, C axis, Axis pairing, 5 axis simultaneous, Digitizing, Probing, Automatic Tool Height measurement, BCD Tool changer output, Unlimited part program size, Extended Work coordinate systems.90005 90004 Rigid Tapping, CSR, Scale Feed back for servo positioning, C axis, Axis pairing, 5 axis simultaneous, Digitizing, Probing, Automatic Tool Height measurement, BCD Tool changer output, Unlimited part program size, Extended Work coordinate systems. 90005 90007 90003 90004 Uses Standard G and M codes 90005 90036 Yes 90005 90036 Yes 90005 90036 Yes 90005 90007 90003 90004 Probing and Digitizing compatible 90005 90036 Yes 90005 90036 Yes 90005 90036 Yes 90005 90007 90003 90004 Compression and Rigid Tapping Compatible 90005 90036 Yes 90005 90036 Yes 90005 90036 Yes 90005 90007 90003 90004 Automatic Tool Measurement Compatible 90005 90036 Yes 90005 90036 Yes 90005 90036 Yes 90005 90007 90003 90004 Spindle Encoder feedback, w / RPM display 90005 90036 Yes 90005 90036 Yes 90005 90036 Yes 90005 90007 90003 90004 Lathe Constant Surface Speed ββ90005 90036 Yes 90005 90036 Yes 90005 90036 Yes 90005 90007 90003 90004 Lathe Threading 90005 90036 Yes 90005 90036 Yes 90005 90036 Yes 90005 90007 90003 90004 Compatible with Windows 10 90005 90036 Yes 90005 90036 Yes 90005 90036 Yes 90005 90007 90003 90004 Centroid Touch Screen Operator Control Panel Compatible 90005 90036 Yes 90005 90036 Yes 90005 90036 Yes 90005 90007 90003 90004 Centroid Operator Control Panel Hardware Compatible 90005 90036 No 90005 90036 Yes 90005 90036 Yes 90005 90007 90003 90004 Xkeys & Xbox Controller / Panel Compatible 90005 90036 Yes 90005 90036 Yes 90005 90036 Yes 90005 90007 90003 90004 Centroid CNC Console Compatible 90005 90036 No 90005 90036 Yes 90005 90036 Yes 90005 90007 90003 90004 Keyboard Jogging and controls compatible 90005 90036 Yes 90005 90036 Yes 90005 90036 Yes 90005 90007 90003 90004 Encoder Expansion Board Compatible 90005 90036 No 90005 90036 Yes 90005 90036 Yes 90005 90007 90003 90004 PLC Expansion Board Compatible 90005 90036 No 90005 90036 Yes 90005 90036 Yes 90005 90007 90003 90004 Analog IN / OUT Expansion Board Compatible 90005 90036 No 90005 90036 Yes 90005 90036 Yes 90005 90007 90003 90004 Hi performance MPG connector 90005 90036 No 90005 90036 Yes 90005 90036 Yes 90005 90007 90003 90004 Wireless USB MPG Compatible 90005 90036 Yes 90005 90036 Yes 90005 90036 Yes 90005 90007 90003 90004 CNC Configuration Wizard 90005 90036 Yes 90005 90036 TBA 90005 90036 TBA 90005 90007 90003 90004 Built in Encoder ports 90005 90036 1 90005 90036 6 (4 for motor use, 2 spares) 90005 90036 6 (4 for motor use, 2 spares) 90005 90007 90003 90004 Maximum Inputs and Outputs 90005 90036 8 In / 8 Out 90005 90036 272 In / 272 Out 90005 90036 272 In / 272 Out 90005 90007 90003 90004 Maximum # of Encoder connections 90005 90036 1 90005 90036 12 90005 90036 12 90005 90007 90003 90004 Maximum # of Analog outputs 90005 90036 1 90005 90036 17 90005 90036 17 90005 90007 90003 90004 Velocity Mode 90005 90036 No, (Step and Direction only) 90005 90036 No, (Closed Loop Torque Mode) 90005 90036 Yes 90005 90007 90003 90004 Position Mode 90005 90036 No, (Step and Direction only) 90005 90036 No, (Closed Loop Torque Mode) 90005 90036 Yes 90005 90007 90003 90004 Real Time Hardware Based Step and Direction Output 90005 90036 Yes 90005 90036 No 90005 90036 No 90005 90007 90003 90004 Axis Motor Tuning 90005 90036 Yes, Accell / Decell 90005 90036 Yes, Built in Tuning Scope for PID Tuning 90005 90036 Yes, Built in Tuning Scope for PID Tuning 90005 90007 90003 90004 Gecko Drive Compatible 90005 90036 Yes 90005 90036 No 90005 90036 No 90005 90007 90003 90004 Yaskawa, Delta, Teknic, DMM, Estun, Teco compatible 90005 90036 Yes 90005 90036 No 90005 90036 Yes 90005 90007 90003 90004 Motion control off-loaded from CNC PC CPU 90005 90036 Yes 90005 90036 Yes 90005 90036 Yes 90005 90007 90003 90004 G code Smoothing 90005 90036 Yes 90005 90036 Yes 90005 90036 Yes 90005 90007 90003 90004 Paired Axis capability 90005 90036 Yes, hardware and software techniques 90005 90036 Yes, Software Pairing 90005 90036 Yes, hardware and software techinques 90005 90007 90003 90004 DIY Kits available 90005 90036 Yes 90005 90036 Yes 90005 90036 Yes 90005 90007 90003 90004 Any axis can be Linear of Rotary Axis 90005 90036 Yes 90005 90036 Yes 90005 90036 Yes 90005 90007 90003 90004 Rotary Table Compatible 90005 90036 Yes 90005 90036 Yes 90005 90036 Yes 90005 90007 90003 90004 Build your own compatible CNC PC 90005 90036 Yes 90005 90036 Yes 90005 90036 Yes 90005 90007 90003 90004 Factory CNCPC with preloaded CNC software available for purchase 90005 90036 Yes 90005 90036 Yes 90005 90036 Yes 90005 90007 90003 90004 Runs on household 110 VAC power 90012 (USA market 110 VAC, World 220-240 VAC) 90005 90036 Yes 90005 90036 Yes 90005 90036 Yes 90005 90007 90003 90004 Spindle Motor can run on single phase 220-240 VAC 90005 90036 Yes 90005 90036 Yes 90005 90036 Yes 90005 90007 90003 90004 Designed and Made in USA 90005 90036 Yes 90005 90036 Yes 90005 90036 Yes 90005 90007 90003 90004 Runs on USA and International Power 90005 90036 Yes 90005 90036 Yes 90005 90036 Yes 90005 90007 90597.