Как выбрать подходящий контроллер ЧПУ для фрезерного станка. Какие бывают виды контроллеров. Какие характеристики важны при выборе. Как собрать контроллер ЧПУ своими руками. На что обратить внимание при сборке и настройке.
Виды контроллеров ЧПУ для фрезерных станков
При выборе контроллера для фрезерного станка с ЧПУ необходимо учитывать несколько ключевых факторов:
- Количество управляемых осей (3 или 4)
- Тип и мощность используемых шаговых двигателей
- Размер рабочего поля станка
- Требуемая точность обработки
- Наличие дополнительных функций (управление шпинделем, система охлаждения и т.д.)
В зависимости от этих параметров выделяют следующие основные виды контроллеров ЧПУ:
1. Многоканальные контроллеры
Предназначены для управления 3-4 осями станка. Подходят для небольших шаговых двигателей типоразмера NEMA17 (42 мм) и NEMA23 (57 мм). Оптимальны для станков с рабочим полем до 1 метра.
2. Одноканальные контроллеры
Используются для управления мощными шаговыми двигателями типоразмера NEMA34 (86 мм) с током от 4,2А. Подходят для станков с большим рабочим полем более 1 метра.
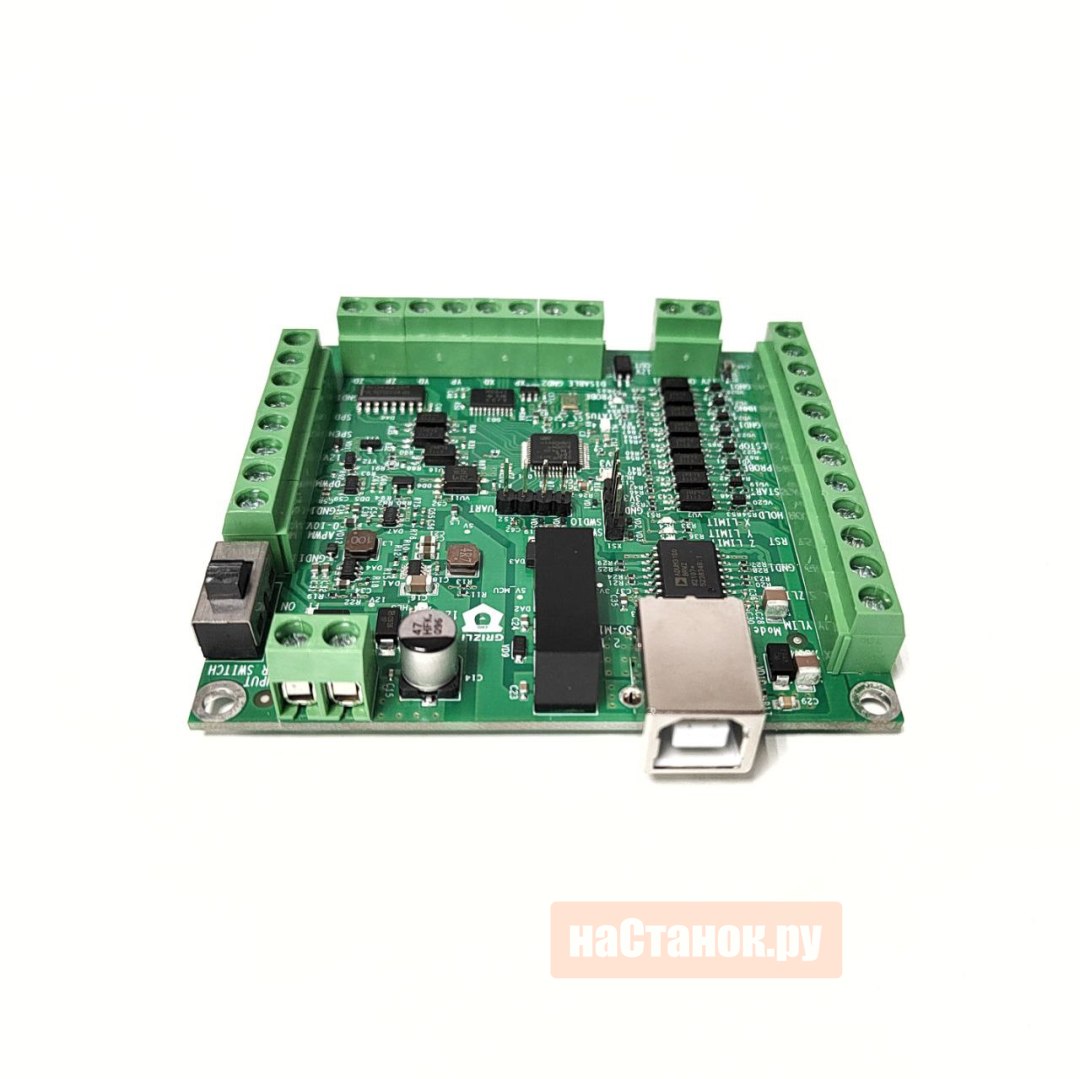
3. Контроллеры на специализированных микросхемах
Широко применяются для управления настольными фрезерными станками. Содержат встроенный драйвер для управления шаговыми двигателями до 3А. Популярные микросхемы — TB6560, A3977.
Ключевые характеристики контроллеров ЧПУ
При выборе контроллера стоит обратить внимание на следующие важные параметры:
- Количество управляемых осей (3 или 4)
- Максимальный ток управления шаговыми двигателями
- Поддерживаемые режимы деления шага (1/2, 1/8, 1/16 и т.д.)
- Наличие и тип интерфейса подключения к ПК (LPT, USB)
- Возможность управления шпинделем
- Наличие входов для концевых датчиков
- Поддержка аварийного останова
Как собрать контроллер ЧПУ своими руками
Для самостоятельной сборки простого контроллера ЧПУ потребуются следующие компоненты:
- Микроконтроллер (например, ATmega328 или STM32)
- Драйверы шаговых двигателей
- Блок питания
- Разъемы для подключения двигателей и датчиков
- Печатная плата
Основные этапы сборки:
- Разработка принципиальной схемы контроллера
- Изготовление или заказ печатной платы
- Монтаж и пайка компонентов
- Программирование микроконтроллера
- Настройка и тестирование
Советы по настройке контроллера ЧПУ
При настройке контроллера ЧПУ важно учитывать следующие моменты:
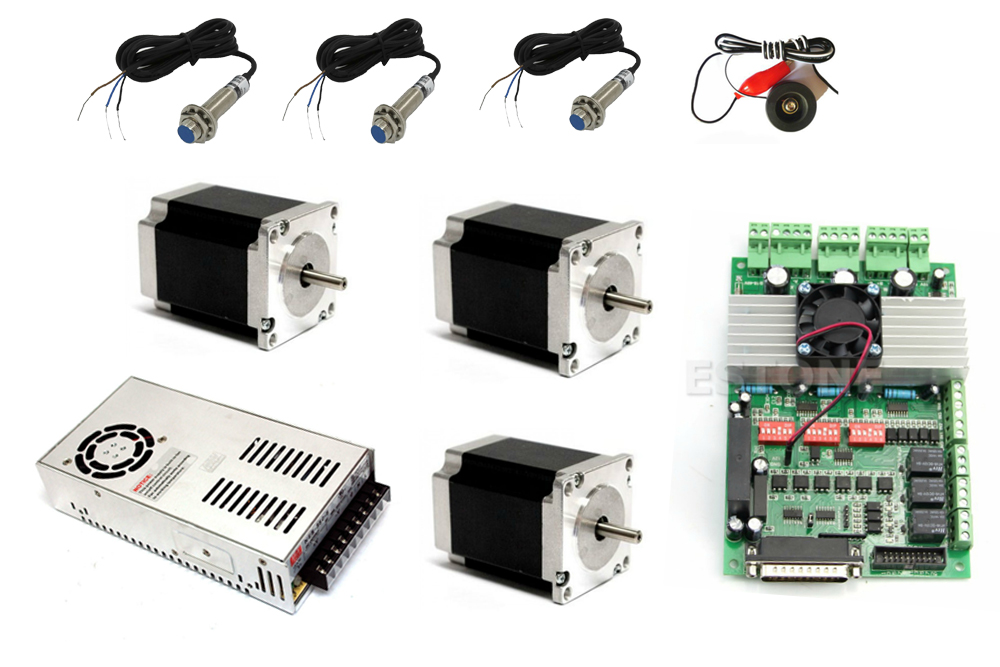
- Правильно задать количество шагов на миллиметр для каждой оси
- Настроить ускорения и скорости перемещения
- Сконфигурировать концевые датчики
- Настроить управление шпинделем (если есть)
- Провести калибровку осей станка
Тщательная настройка контроллера позволит добиться высокой точности и качества обработки на фрезерном станке с ЧПУ.
Программное обеспечение для управления ЧПУ станком
Для управления фрезерным станком с ЧПУ через контроллер используется специальное программное обеспечение. Наиболее популярные варианты:
- Mach3/Mach4 — мощный и функциональный софт для Windows
- LinuxCNC — бесплатная система с открытым кодом для Linux
- GRBL — простой и легкий контроллер для Arduino
- UCCNC — продвинутая система с поддержкой 6 осей
При выборе ПО стоит учитывать совместимость с вашим контроллером и операционной системой компьютера. Также важны функциональные возможности и удобство интерфейса.
Требования к компьютеру для управления ЧПУ станком
Для стабильной работы системы ЧПУ компьютер должен соответствовать следующим минимальным требованиям:
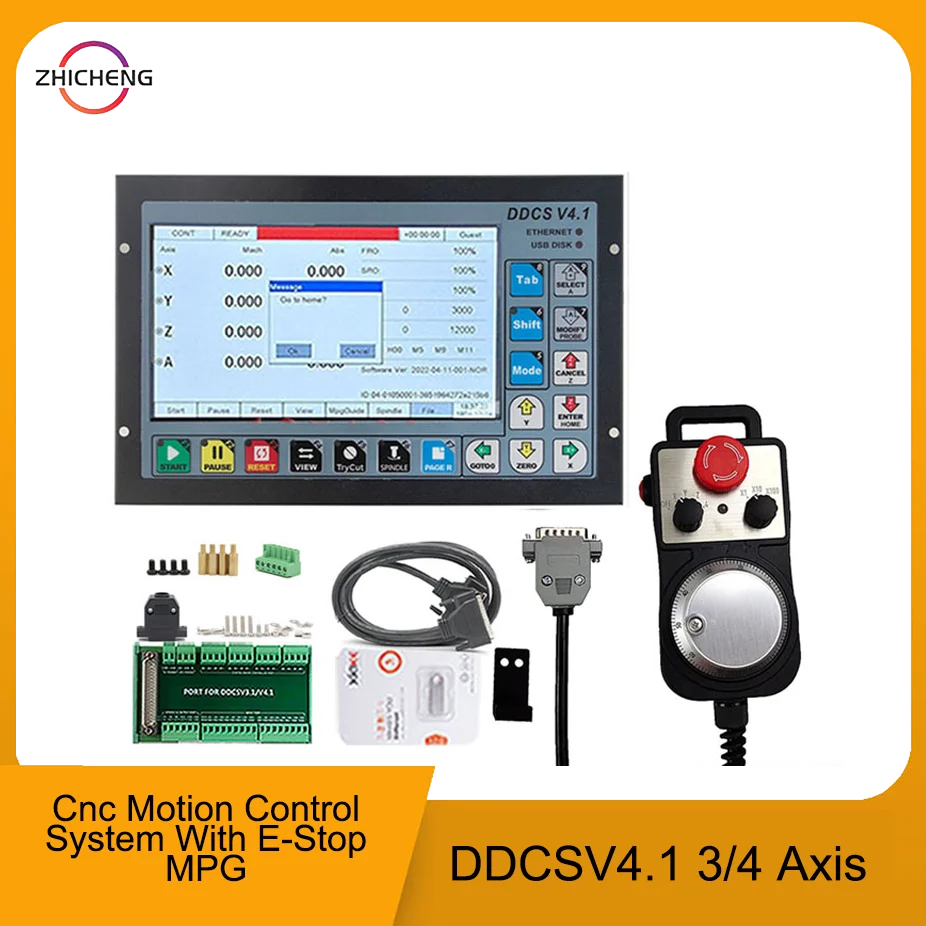
- Процессор с частотой не менее 1 ГГц
- Оперативная память от 1 Гб
- Наличие LPT или USB порта для подключения контроллера
- Операционная система Windows или Linux
Рекомендуется использовать стационарный компьютер, а не ноутбук, для более стабильной работы. При недостаточной производительности может потребоваться оптимизация системы.
Распространенные проблемы при работе с контроллерами ЧПУ
При эксплуатации контроллеров ЧПУ могут возникать следующие типичные проблемы:
- Пропуск шагов двигателями
- Нестабильная работа на высоких скоростях
- Сбои при работе с тяжелыми G-code программами
- Ложные срабатывания концевых датчиков
- Помехи от шпинделя
Для устранения этих проблем может потребоваться:
- Настройка токов и микрошага драйверов
- Экранирование сигнальных проводов
- Установка фильтров питания
- Оптимизация настроек ускорений и скоростей
- Обновление прошивки контроллера
Внимательный подход к настройке и обслуживанию системы ЧПУ позволит избежать большинства проблем и обеспечить стабильную работу фрезерного станка.

схема, сборка своими руками, виды
Вопрос-ОтветУ умельцев, которые пытаются сами собрать программируемый станок, часто возникает проблема: как выбрать для него контроллер управления шаговыми двигателями. Понятно, что их интересует схема этого устройства.
Среди большого разнообразия контроллеров, пользователи ищут для самостоятельной сборки те схемы, которые будут приемлемы и наиболее эффективны. Применяются и одноканальные устройства и многоканальные: 3-х и 4-х осевой контроллеры.
Варианты устройств
Многоканальные контроллеры ШД (шаговых двигателей) при типоразмерах 42 или 57 мм используется в случае небольшого рабочего поля станка – до 1 м. Когда собирают станок большего рабочего поля – свыше 1м, нужен типоразмер 86 мм. Управлять ним можно, пользуясь одноканальным драйвером (ток управления, превышающий 4,2 А).
Управлять станком с числовым программным управлением, в частности, фрезерным настольным можно контроллером, созданным на базе специализированных микросхем –драйверов, предназначенных к применению для ШД до 3А. Контроллер ЧПУ станка управляется спецпрограммой. Ее устанавливают на ПК, имеющий частоту процессора свыше 1GHz, а объем памяти 1 Гб). При меньшем объеме, систему оптимизируют.
ОБРАТИТЕ ВНИМАНИЕ! Если сравнивать с ноутбуком, то в случае подключения стационарного компьютера – лучшие результаты, да и обходится он дешевле.
Подключая контроллер к компьютеру, используют USB или разъем параллельного порта LPT. Если этих портов нет, то пользуются платами-расширителями или контроллерами-преобразователями.
Экскурс в историю
Вехи техпрогресса схематически можно обозначить так:
- У первого контроллера на микросхеме был условно назван «синей платой». У этого варианта есть недостатки и схема требовала доработки. Главное достоинство – есть разъем, к нему и подключали пульт управления.
- Вслед за синим, появился контроллер, называемый «красной платой». В нём уже использовались быстрые (высокочастотные) оптроны, реле шпинделя на 10А, развязка по питанию (гальваническая) и разъем, куда бы подключались драйверы четвертой оси.
- Применялось также еще одно подобное устройство с красной маркировкой, но более упрощенное. При его помощи можно было управлять небольшим станком настольного типа – из числа 3-осевых.
- Следующим в линейке техпрогресса стал контроллер с гальванической развязкой по питанию, быстрыми оптронами и особыми конденсаторами, имеющий алюминиевый корпус, который обеспечивал защиту от пыли. Вместо реле управления, которое включало бы шпиндель, в конструкции было два выхода и возможность, чтобы подключить реле или ШИМ (широтно-импульсная модуляция) управление скоростью вращения.
- Сейчас же для изготовления самодельного фрезерно-гравировального станка, имеющего ШД, есть варианты – 4-х осевой контроллер, драйвер ШД от Allegro, одноканальный драйвер для станка, имеющего большое рабочее поле.
ВАЖНО! Не стоит перегружать ШД, применяя крупную фрезу агрегата и большую скорость.
Контроллер из подручных материалов
Большинство умельцев предпочитают управление через LPT порт для большинства программ управления любительского уровня. Вместо применения комплекта спецмикросхем для этой цели, кое-кто строит контроллер из подручных материалов – полевых транзисторов из сгоревших материнских плат (при напряжении свыше 30 вольт и током больше 2 ампер).
А поскольку создавался станок для нарезания пенопласта, в качестве ограничителя тока изобретатель использовал автомобильные лампы накаливания, а ШД снимали со старых принтеров или сканеров. Такой контроллер устанавливали без изменений в схеме.
Чтобы сделать простейший станок ЧПУ своими руками, разбирая сканер, помимо ШД, извлекается и микросхема ULN2003, и два стальные прутки, они пойдут на тестовый портал. К тому же понадобятся:
- Коробка из картона (из нее смонтируют корпус устройства). Возможен вариант с текстолитом или фанерным листом, но картон резать легче; куски древесины;
- инструменты – в виде кусачек, ножниц, отверток; клеевой пистолет и паяльные принадлежности;
- вариант платы, которая подходит на самодельный ЧПУ станок;
- разъем для LPT порта;
- гнездо в форме цилиндра для обустройства блока питания;
- элементы соединения – стержни с резьбой, гайки, шайбы и шурупы;
- программа для TurboCNC.
Сборка самодельного устройства
Приступив к работе над самодельным контроллером для чпу, первый шаг – аккуратно припаять микросхему на макетную плату с двумя шинами электропитания. Дальше последует соединение вывода ULN2003 и коннектора LPT. Далее оставшиеся выводы подключаем по схеме. Нулевой вывод (25-ый параллельного порта) соединяется с отрицательным на шине питания платы.
Затем ШД соединяют с устройством управления, а гнездо для электропитания – с соответствующей шиной. Для надёжности соединений проводов выполняют их фиксацию термоклеем.
Не составит труда подключение Turbo CNC. Программа эффективна с MS-DOS, совместима и с Windows, но в этом случае возможны некоторые ошибки и сбои.
Настроив программу на работу с контроллером, можно изготовить тестовую ось. Последовательность действий по подключению станков такова:
- В отверстия, просверленные на одном уровне в трех деревянных брусках, вставляют прутки из стали и закрепляют шурупами небольшого размера.
- ШД соединяют со вторым бруском, надевая его на свободные концы прутов и прикручивают, применяя шурупы.
- Через третье отверстие продевается ходовой винт и ставится гайка. Винт, вставленный в отверстие второго бруска, завинчивают до упора, чтобы он, пройдя через эти отверстия, вышел на вал двигателя.
- Далее предстоит соединение стержня с валом двигателя отрезком шланга из резины и проволочным зажимом.
- Для крепления ходовой гайки нужны дополнительные винты.
- Сделанная подставка также крепится к второму бруску при помощи шурупов. Горизонтальный уровень регулируется дополнительными винтами и гайками.
- Обычно вместе с контроллерами подключаются и двигатели и тестируются на предмет правильного соединения. Далее следует проверка масштабирования ЧПУ, прогонка тестовой программы.
- Остается сделать корпус устройства и это будет завершающим этапом работы тех, кто созидает самодельные станки.
Программируя работу 3-осевого станка, в настройках по первым двум осям – без перемен. А вот при программировании первых 4-х фаз третьей – вводятся изменения.
Внимание! Используя упрощенную схему контроллера ATMega32 (Приложение 1), в отдельных случаях можно столкнуться с некорректной обработкой оси Z – режим полушага. А вот в полной версии его платы (Приложение 2), токи осей регулируются внешним аппаратным ШИМом.
Заключение
В контроллерах, собранных ЧПУ станков – широкий спектр использования: в плоттерах, небольших фрезерах, работающих с древесиной и пластиковыми деталями, граверах по стали, миниатюрных сверлильных станках.
Устройства с осевым функционалом используют также в графопостроителях, на них можно рисовать и изготовлять печатные платы. Так что усилия, затраченные на сборку мастерами-умельцами, в будущем контроллере обязательно окупятся.
vseochpu.ru
Контроллер для ЧПУ на atmega8 16au своими руками: пошагово
Контроллер для станка легко сможет собрать и домашний мастер. Задать нужные параметры не сложно, достаточно учесть несколько нюансов.
Советы по сборке контроллеров для ЧПУ станков
Без правильного выбора контроллера для станка не удастся собрать сам контроллер для ЧПУ на Atmega8 16au своими руками. Эти устройства делятся на две разновидности:
- Многоканальные. Сюда входят 3 и 4-осевые контроллеры для шаговых двигателей.
- Одноканальные.
Небольшие шаровые двигатели наиболее эффективно управляются многоканальными контроллерами. Стандартные типоразмеры в данном случае – 42, либо 57 миллиметров. Это отличный вариант для самостоятельной сборки ЧПУ станков, у которых рабочее поле имеет размер до 1 метра.
Если же самостоятельно собирается станок на микроконтроллере с полем более чем в 1 метр – надо использовать двигатели, выпускающиеся в типоразмерах до 86 миллиметров. В данном случае рекомендуется организовывать управление мощными одноканальными драйверами, с током управления от 4,2 А и выше.
Контроллеры со специальными микросхемами-драйверами получили широкое распространение в случае необходимости организовать контроль работы станков с фрезерами настольного типа. Оптимальным вариантом будет микросхема, обозначаемая как TB6560 или A3977. У этого изделия внутри есть контроллер, способствующий формированию правильной синусоиды для режимов, поддерживающих разные полушаги. Токи обмотки могут быть установлены программным способом. При микроконтроллерах добиться результата просто.
Управление
Контроллером легко управлять, используя специализированное программное оборудование, установленное на ПК. Главное, чтобы у самого компьютера память была минимум 1 ГБ, а процессор – не менее 1 GHz.
Можно использовать ноутбуки, но стационарные компьютеры в этом плане дают лучшие результаты. И обходятся гораздо дешевле. Компьютер можно использовать для решения других задач, когда станки не требуют управления. Хорошо, если есть возможность оптимизировать систему перед началом работы.
Параллельный порт LPT – вот какая деталь помогает организовать подключение. Если контроллер имеет порт USB, то используется разъем соответствующей формы. При этом выпускается все больше и больше компьютеров, у которых параллельный порт отсутствует.
Изготовление самого простого варианта сканера
Одно из самых простых решений для самодельного создания ЧПУ станка – использование деталей от другого оборудования, снабженного шаровыми двигателями. Функцию отлично выполняют старые принтеры.
Берем следующие детали, извлеченные из прежних приборов:
- Сама микросхема.
- Шаговый двигатель.
- Пара стальных прутков.
При создании корпуса контроллера надо взять и старую картонную коробку. Допустимо использовать коробки из фанеры или текстолита, исходный материал не имеет значения. Но картон проще всего обработать, используя обычные ножницы.
Список инструментов будет выглядеть следующим образом:
- Паяльник вместе, дополненный принадлежностями.
- Пистолет с клеем.
- Ножничный инструмент.
- Кусачки.
Наконец, изготовление контроллера потребует следующих дополнительных деталей:
- Разъем с проводом, для организации удобного подключения.
- Цилиндрическое гнездо. Такие конструкции отвечают за питание устройства.
- Ходовыми винтами служат стержни, имеющие определенную резьбу.
- Гайка с подходящими для ходового винта размерами.
- Шурупы, шайбы, древесина в форме кусков.
Начинаем работу по созданию самодельного станка
Шаговый двигатель вместе с платой должны быть извлечены из старых устройств. У сканера достаточно снять стекло, а затем – вывернуть несколько болтов. Снимать потребуется и стальные стержни, используемые в дальнейшем, создавая тестовый портал.
Микросхема управления ULN2003 станет одним из главных элементов. Возможно отдельное приобретение деталей, если в сканере используются другие разновидности микросхем. В случае наличия нужного устройства на плате его аккуратно выпаиваем. Порядок действий при сборке контроллера для ЧПУ на Atmega8 16au своими руками выглядит следующим образом:
- Сначала разогреваем олово, используя паяльник.
- Удаление верхнего слоя потребует использования отсоса.
- Одним концом отвертку устанавливаем под микросхему.
- Жало паяльника должно касаться каждого вывода микросхемы. Если это условие соблюдается, на инструмент можно нажимать.
Далее микросхема припаивается на плату, тоже с максимальной аккуратностью. Для первых пробных шагов можно использовать макеты. Используем вариант с двумя шинами электропитания. Одна из них соединяется с положительным выводом, а другая – с отрицательным.
На следующем этапе идет соединение вывода у второго коннектора параллельного порта с выводом в самой микросхеме. Выводы у коннектора и микросхемы должны быть соединены соответствующим образом.
Нулевой вывод присоединяется к отрицательной шине.
Один из последних этапов – припайка шагового двигателя к устройству управления.
Хорошо, если есть возможность изучить документацию от производителя устройств. Если нет, то придется самостоятельно искать подходящее решение.
Провода рекомендуется припаивать так, чтобы потом их можно было легко соединить с зажимами-крокодилами. Клеммы с винтовыми соединениями – подходящие для решения задачи решения. Как и любые другие подобные детали.
Провода соединяются с выводами. Наконец, один из них соединяется с положительной шиной.
Шины и гнезда электропитания нужно соединить.
Термоклей из пистолета поможет закрепить детали, чтобы они не откалывались.
Используем Turbo CNC – программу для управления
ПО Turbo CNC точно будет работать с микроконтроллером, который использует микросхему ULN2003.
- Используем специализированный сайт, откуда можно скачать программное оборудование.
- Любой пользователь разберется в том, как провести установку.
- Именно данная программа лучше всего работает под MS-DOS. В режиме совместимости на Windows могут появляться некоторые ошибки.
- Но, с другой стороны, это позволит собрать компьютер с определенными характеристиками, совместимыми именно с данным программным обеспечением.
Рекомендации по настройкам
- После первого запуска программы появится специальный экран.
- Надо нажать пробел. Так пользователь оказывается в главном меню.
- Нажимаем F1, а потом выбираем пункт Configure.
- Далее надо нажать пункт «number of Axis». Используем клавишу Enter.
- Остается только ввести количество соей, которые планируется использовать. В данном случае у нас один мотор, потому и нажимаем на цифру 1.
- Для продолжения используем Enter. Нам снова понадобится клавиша F1, после ее применения в меню Configure выбираем Configure Axis. Затем – два раза нажимаем пробел.
Drive Type – вот какая вкладка нам нужна, до нее доходим многочисленными нажиманиями Tab. Стрелка вниз помогает дойти до пункта Type. Нам нужна ячейка, которая носит название Scale. Далее определяем, сколько шагов двигатель совершает только за время одного оборота. Для этого достаточно знать номер детали. Тогда легко будет понять, на сколько градусов он поворачивается всего за один шаг. Далее число градусов делится на один шаг. Так мы вычисляем количество шагов.
Остальные настройки можно оставить в первоначальном виде. Число, получившееся в ячейке Scale, просто копируется в такую же ячейку, но на другом компьютере. Значение 20 должно быть присвоено ячейке Acceleration. По умолчанию в этой области стоит значение 2000, но оно слишком большое для собираемой системы. Начальный уровень – 20, а максимальный – 175. Далее остается нажимать TAB, пока пользователь не доходит до пункта Last Phase. Здесь нужно поставить цифру 4. Далее жмем Tab, пока не дойдем до ряда из иксов, первого в списке. Первые четыре строчки должны содержать следующие позиции:
1000XXXXXXXX
0100XXXXXXXX
0010XXXXXXXX
0001XXXXXXXX
В остальных ячейках не нужно проводить никаких изменений. Просто выбираем ОК. Все, программа настроена для работы с компьютером, самими исполнительными устройствами.
vseochpu.ru
ЧПУ фрезерный станок с автономным контроллером на STM32 / Habr
Поскольку я давно собрал для себя ЧПУ станок и давно и регулярно эксплуатирую его для хоббийных целей, то мой опыт, надеюсь, будет полезен, как и исходные коды контроллера.Постарался написать только те моменты, которые лично мне показались важными.
Ссылка на исходники контроллера и настроенную оболочку Eclipse+gcc и пр. лежат там же, где ролик:
Регулярно сталкиваясь, с необходимостью сделать ту или иную мелкую «штучку» сложной формы, первоначально задумался о 3D принтере. И даже начал его делать. Но почитал форумы и оценив скорость работы 3D принтера, качество и точность результата, процент брака и конструкционные свойства термопластмассы, понял, то это не более чем игрушка.
Заказ на комплектующие из Китая пришел за месяц. И уже через 2 недели станок работал с управлением от LinuxCNC. Собирал из всякой фигни, что была под рукой, поскольку хотелось побыстрее (профиль + шпильки). Собирался потом переделать, но, как оказалось, станок получился достаточно жесткий, и гайки на шпильках не пришлось подтягивать ни разу. Так что конструкция осталась без изменений.
Начальная эксплуатация станка показала что:
- Использовать в качестве шпинделя бормашинку “china noname” на 220V не лучшая идея. Перегревается и жутко громко работает. Боковой люфт фрезы (подшипников?) ощущается руками.
- Бормашинка Proxon работает тихо. Люфт не ощутим. Но перегревается и выключатся через 5 минут.
- Компьютер, взятый на время, с LPT двунаправленным портом — не удобен. Взят на время (найти PCI-LPT оказалось проблемой). Занимает место. И вообще..
После первоначальной эксплуатации заказал шпиндель с водяным охлаждением и решил сделать контроллер для автономной работы на самом дешевом варианте STM32F103, продаваемом в комплекте с 320×240 LCD экраном.
Почему народ до сих пор упорно мучает 8-и разрядные ATMega для относительно сложных задач, да еще через Arduino для меня загадка. Наверное любят трудности.
Разработка контроллера
Программу создавал после вдумчивого просмотра исходников LinuxCNC и gbrl. Однако ни те, ни те исходники расчета траектории не взял. Захотелось попробовать написать модуль расчета без использования float. Исключительно на 32-х разрядной арифметике.
Результат меня устраивает для всех режимов эксплуатации и прошивку не трогал уже давно.
Скорость максимальная, подобранная экспериментально: X:2000мм/мин Y:1600 Z:700 (1600 step/mm. режим 1/8).
Но ограничена не ресурсами контроллера. Просто выше уже мерзкий звук пропуска шагов даже прямых участках по воздуху. Бюджетная китайская плата управления шаговиками на TB6560 не самый лучший вариант.
Фактически скорость по дереву (бук, 5мм заглубления,d=1мм фреза, шаг 0.15мм) больше 1200 мм не ставлю. Возрастает вероятность поломки фрезы.
В результате получился контроллер со следующим функционалом:
- Подключение к внешнему компу как стандартное usb mass storage device (FAT16 на SD карте). Работа с файлами стандартного формата G-code
- Удаление файлов через пользовательский интерфейс контроллера.
- Просмотр траектории по выбранному файлу (насколько позволяет экран 640×320) и расчет времени выполнения. Фактически эмуляция выполнения с суммированием времени.
- Просмотр содержимого файлов в тестовом виде.
- Режим ручного управления с клавиатуры (перемещение и выставления «0»).
- Запуск выполнения задания по выбранному файлу (G-code).
- Приостанов/продолжить выполнение. (иногда полезно).
- Аварийный программный стоп.
Контроллер подключатся к плате управления шаговиками через тот же разъем LPT. Т.е. он выполняет роль управляющего компьютера с LinuxCNC/Mach4 и взаимозаменяем с ним.
После творческих экспериментов по вырезанию собственноручно нарисованных рельефов на дереве, и экспериментов с настройками ускорений в программе, захотел дополнительно еще и энкодеры на осях. Как раз на e-bay нашел относительно дешевые оптически экодеры (1/512), шаг деления которых для моих ШВП был 5/512= 0.0098мм.
Кстати, использование оптических энкодеров высокого разрешения, без аппаратной схемы работы с ними (в STM32 она есть) – бессмысленно. Ни обработка по прерыванию, ни, тем более, программный опрос никогда не справятся с «дребезгом» (это говорю для любителей ATMega).
В первую очередь, я хотел для следующих задач:
- Ручное позиционирование на столе с высокой точностью.
- Контроль пропуска шагов с контролем отклонение траектории от расчетной.
Однако, нашел им еще одно применение, пусть и в довольно узкой задаче.
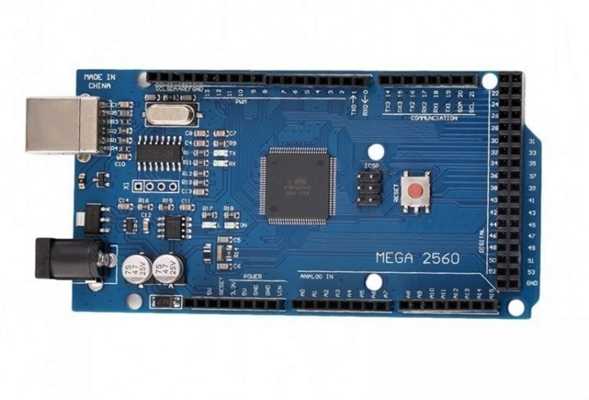
Заметил, что при вырезании рельефа, при задании ускорения по Z больше определенной величины, ось Z начинает медленно, но уверенно ползти вниз. Но, время вырезания рельефа при этом ускорении на 20% меньше. По окончанию вырезания рельефа 17×20 см с шагом 0.1мм фреза может уйти вниз на 1-2 мм от расчетной траектории.
Анализ ситуации в динамике по энкодерам, показал, что при подъеме фрезы иногда теряется 1-2 шага.
Простой алгоритм коррекции шагов с использованием энкодера дает отклонение не более 0.03 мм и позволяет уменьшить время обработки на 20%. А даже 0.1 мм выступ на дереве заметить сложно.
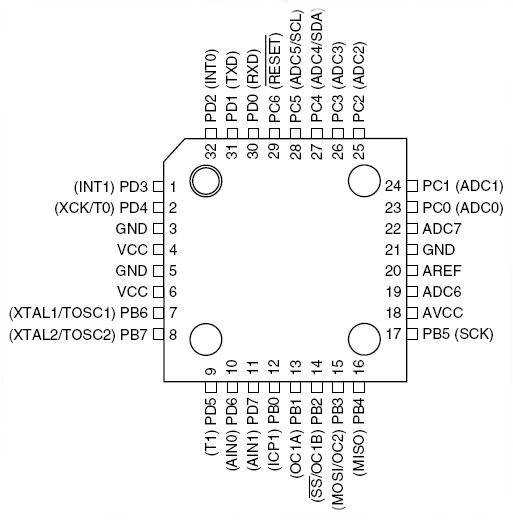
Идеальным вариантом для хоббийных целей посчитал настольный вариант с полем чуть больше чем A4. И до сих пор мне этого хватает.
Подвижный стол
Для меня до сих пор остается загадкой, почему все выбирают для настольных станков конструкцию с подвижным порталом. Единственное её преимущество – возможность обработать по частям очень длинную доску или, если приходится регулярно обрабатывать материал вес которого больше веса портала.
За все время эксплуатации ни разу не было необходимость выпилить по частям рельеф на 3-х метровой доске или сделать гравировку на каменной плите.
Подвижный стол обладает следующими преимуществами для настольных станков:
- Конструкция проще и, в общем случае, конструкция более жесткая.
- На неподвижный портал навешиваются все потроха (блоки питания, платы и пр.) и станок получается компактнее и удобнее для переноски.
- Масса стола и куска типичного материала для обработки существенно ниже чем масса портала и шпинделя.
- Практически исчезает проблема с кабелями и шлангами водяного охлаждения шпинделя.
Шпиндель
Хотел бы заметить, что данный станок не для силовой обработки. ЧПУ станок для силовой обработки проще всего сделать на базе обычного фрезерного станка.
На мой взгляд, станок для силовой обработки металла и станок с высоко оборотистым шпинделем для обработки дерева/пластмасс — это совершенно разные типы оборудования.
Создать в домашних условия универсальный станок как минимум не имеет смысла.
Выбор шпинделя для станка с данным типом ШВП и направляющими с линейными подшипниками однозначен. Это высоко оборотистый шпиндель.
Для типичного высоко оборотистого шпинделя (20000 об/мин) фрезеровка цветных металлов (про сталь даже речи не идет) – это экстремальный режим для шпинделя. Ну, разве что очень надо и тогда съем по 0.3 мм за проход с поливом ОЖ.
Шпиндель для станка рекомендовал бы с водяным охлаждением. С ним слышно во время работы только «пение» шаговых двигателей и бульканье аквариумного насоса в контуре охлаждения.
В первую очередь у меня ушла проблема корпусов. Любой формы корпус фрезеруется из «оргстекла» и по идеально по гладким срезам склеивается растворителем.
Стеклотекстолит отказался универсальным материалом. Точность станка позволяет вырезать посадочное место под подшипник, в которое он холодный зайдет, как положено с легким натягом, а после уже не вытащить. Шестерни из текстолита отлично вырезаются с честным эвольвентным профилем.
Обработка дерева (рельефы и пр.) – широкий простор для реализации своих творческих порывов или, как минимум, для реализации чужих порывов (готовые модели).
Вот только ювелирку не пробовал. Негде опоки прокаливать/плавить/лить. Хотя брусок ювелирного воска ждет своего часа.
habr.com
Выбор контроллера для фрезерного чпу станка
Для самостоятельной сборки фрезерного станка необходимо выбрать контроллер управления ЧПУ. Контроллеры бывают как многоканальные: 3х и 4х осевые контроллеры шаговых двигателей, так и одноканальные. Многоканальные контроллеры чаще всего встречаются для управления небольшими шаговыми двигателями, типоразмера 42 или 57мм(nema17 и nema23). Такие двигатели подходят для самостоятельной сборки ЧПУ станков с рабочим полем до 1м. При самостоятельной сборке станка с рабочим полем более 1м следует использовать шаговые двигатели типоразмера 86мм(nema34), для управления такими двигателями понадобятся мощные одноканальные драйвера с током управления от 4,2А и выше.
Для управления настольными фрезерными станками широко распространены контроллеры на специализированных микросхемах-драйверах управления ШД, например, TB6560 или A3977. Эта микросхема содержит в себе контроллер, который формирует правильную синусоиду для разных режимов полушага и имеет возможность программной установки токов обмоток. Эти драйвера предназначены для работы с шаговыми двигателями до 3А, типоразмеры ШД NEMA17 42мм и NEMA23 57мм.
Управление контроллером с помощью специализированных программ управления станком MACh4 или KCAM или Linux EMC2 и других, установленных на ПК. Рекомендуется использовать компьютер с процессором частотой не менее 1GHz и память 1 Гб. Стационарный компьютер дает лучшие результаты, по сравнению с ноутбуками и значительно дешевле. Кроме того, вы можете использовать этот компьютер и для других работ, когда он не занят управлением вашим станком. При установке на ноутбук или ПК с памятью 512Мб рекомендуется провести оптимизацию системы под Mach4.
Для подключения к компьютеру используется параллельный порт LPT(для контроллера с USB интерфейсом порт USB). Если ваш компьютер не оборудован параллельным портом (всё больше и больше компьютеров выпускается без этого порта) вы можете приобрести плату расширителя портов PCI-LPT или PCI-E-LPT или специализированный контроллер-преобразователь – USB-LPT, который подключается к компьютеру через USB порт.
С настольным гравировально-фрезерным станком из алюминия CNC-2020AL, в комплекте блок управления с возможностью регулировки оборотов шпинделя, рисунок 1 и 2, блок управления содержит драйвер шаговых двигателей на микросхеме TB6560AHQ, блоки питания драйвера шаговых двигателей ШД и блок питания шпинделя.
рисунок 1
Рисунок 2
1. Один из первых контроллеров управления фрезерными станками с ЧПУ на микросхеме TB6560 был, получивший прозвище -«синяя плата» , рисунок 3. Этот вариант платы много обсуждался на форумах, она имеет ряд недостатков. Первый — медленные оптроны PC817, что требует при настройке программы управления станком MACh4, вводить максимально допустимое значение в поля Step pulse и Dir pulse = 15. Второй это плохое согласование выходов оптопар с входам драйвера TB6560, решается доработкой схемы, Рисунок 8 и 9. Третий — линейные стабилизаторы питания платы и в следствии этого большой перегрев, на последующих платах применены импульсные стабилизаторы. Четвертый — отсутствие гальванической развязки цепи питания. Реле шпинделя 5А, что в большинстве случаев недостаточно и требует применения более мощного промежуточного реле. К достоинствам можно отнести наличие разъема для подключении пульта управления. Этот контроллер в серии станков «Моделист» не применяется.
Рисунок 3.
2. Контроллер управления ЧПУ станком поступивший на рынок после «синей платы», получивший прозвище красная плата, рисунок 4.
Здесь применены более высокочастотные(быстрые) оптроны 6N137. Реле шпинделя 10А. Наличие гальванической развязки по питанию. Есть разъем для подключения драйвера четвертой оси. Удобный разъем для подключения концевых выключателей.
Рисунок 4.
3. Контроллер шаговых двигателей с маркировкой TB6560-v2 тоже красного цвета, но упрощенный, нет развязки по питанию, рисунок 5. Маленький размер, но и в следствии этого меньше размер радиатора.
Рисунок 5
4. Контроллер в алюминиевом корпусе, рисунок 6. Корпус защищает контроллер от пыли попадания металлических частей, он же служит и хорошим теплоотводом. Гальваническая развязка по питанию. Есть разъем для питания дополнительных цепей +5В. Быстрые оптроны 6N137. Низкоимпедансные и конденсаторы Low ESR. Нет реле управления включением шпинделя, но есть два выхода для подключения реле (транзисторные ключи с ОК) или ШИМ управления скоростью вращения шпинделя. Описание подключения сигналов управления реле на страничке Подключение концевых выключателей и реле шпинделя к контроллеру ЧПУ на TB6560
Рисунок 6
5. 4х осевой контроллер фрезерно-гравировального станка с ЧПУ, интерфейс USB, рисунок 7.
Рисунок 7
Данный контроллер не работает с программой MACh4, в комплекте своя программа управления станком.
6. Контроллер ЧПУ станка на драйвере ШД от Allegro A3977, рисунок 8.
Рисунок 8
7.Одноканальный драйвер шагового двигателя ЧПУ станка DQ542MA. Этот драйвер может использоваться при самостоятельном изготовлении станка с большим рабочим полем и шаговыми двигателями на ток до 4.2А, может работать и с двигателями Nema34 86mm, рисунок 9.
Рисунок 9
Фото доработки синей платы контроллера шаговых двигателей на TB6560, рисунок 10.
Рисунок 10.
Схема исправления синей платы контроллера ШД на TB6560, рисунок 11.
Рисунок 11.
cncmodelist.ru
ЧПУ своими руками v1.0
Это мой первый станок с ЧПУ собранный своими руками из доступных материалов. Себестоимость станка около 170$.
Собрать станок с ЧПУ мечтал уже давно. В основном он мне нужен для резки фанеры и пластика, раскрой каких-то деталей для моделизма, самоделок и других станков. Собрать станок руки чесались почти два года, за это время собирал детали, электронику и знания.
Станок бюджетный, стоимость его минимальна. Далее я буду употреблять слова, которые обычному человеку могут показаться очень страшными и это может отпугнуть от самостоятельной постройки станка, но на самом деле это всё очень просто и легко осваивается за несколько дней.
Электроника собрана на Arduino + прошивка GRBL
Плата Ардуино R3
Плата CNC shield v3 Update: есть новая версия платы v4
Шаговые моторы NEMA 17
Блок питания 24 вольта 15 ампер
Видео о том как поют 🙂 моторы ЧПУ станка.
Механика самая простая, станина из фанеры 10мм + шурупы и болты 8мм, линейные направляющие из металического уголка 25*25*3 мм + подшипники 8*7*22 мм. Ось Z движется на шпильке M8, а оси X и Y на ремнях T2.5.
Шпиндель для ЧПУ самодельный, собран из бесколлекторного мотора и цангового зажима + зубчатая ременная передача. Надо отметить, что мотор шпинделя питается от основного блока питания 24 вольта. В технических характеристиках указано, что мотор на 80 ампер, но реально он потребляет 4 ампера под серьёзной нагрузкой. Почему так происходит я объяснить не могу, но мотор работает отлично и справляется со своей задачей.
Изначально ось Z была на самодельных линейных направляющих из уголков и подшипников, позже я переделал её, фотки и описание ниже.
Рабочее пространство примерно 45 см по X и 33 см по Y, по Z 4 см. Учитывая первый опыт, следующий станок я буду делать с большими габаритами и на ось X буду ставить два мотора, по одному с каждой строны. Это связано с большим плечом и нагрузкой на него, когда работа ведётся на максимальном удалении по оси Y. Сейчас стоит один мотор и это приводит к искажению деталей, круг получается немного элипсом из-за возникающего прогибания каретки по X.
Родные подшипники у мотора быстро разболтались, потому что не рассчитаны на боковую нагрузку, а она тут серьёзная. Поэтому сверху и снизу на оси установил два больших подшипника диаметром 8 мм, это надо было бы делать сразу, сейчас из-за этого есть вибрация.
Здесь на фото видно, что ось Z уже на других линейных направляющих, описание будет ниже.
Сами направляющие имеют очень простую конструкцию, её я как-то случайно нашел на Youtube. Тогда мне эта конструкция показалась идеальной со всех сторон, минимум усилий, минимум деталей, простая сборка. Но как показала практика эти направляющие работают не долго. На фото видно какая канавка образовалась на оси Z после недели моих тестовых запусков ЧПУ станка.
Самодельные направляющие на оси Z я заменил на мебельные, стоили меньше доллара за две штуки. Я их укоротил, оставил ход 8 см. На осях X и Y ещё остались направляющие старые, менять пока не буду, планирую на этом станке вырезать детали для нового станка, потом этот просто разберу.
Пару слов о фрезах. Я никогда не работал с ЧПУ и опыт фрезерования у меня тоже очень маленький. Купил я в Китае несколько фрез, у всех 3 и 4 канавки, позже я понял, что эти фрезы хороши для металла, для фрезерования фанеры нужны другие фрезы. Пока новые фрезы преодолевают расстояние от Китая до Беларуси я пытаюсь работать с тем, что есть.
На фото видно как фреза 4 мм горела на берёзовой фанере 10 мм, я так и не понял почему, фанера чистая, а на фрезе нагар похожий на смолу от сосны.
Далее на фото фреза 2 мм четырёхзаходная после попытки фрезерования пластика. Этот кусок расплавленного пластика потом очень плохо снимался, откусывал по чуть-чуть кусачками. Даже на малых оборотах фреза все равно вязнет, 4 канавки явно для металла 🙂
На днях у дяди был день рождения, по этому случаю решил сделать подарок на своей игрушке 🙂
В качестве подарка сделал аншлаг на дом из фанеры. Первым делом попробовал фрезеровать на пенопласте, чтобы проверить программу и не портить фанеру.
Из-за люфтов и прогибаний подкову получилось вырезать только с седьмого раза.
В общей сложности этот аншлаг (в чистом виде) фрезеровался около 5 часов + куча времени на то, что было испорчено.
Как-то я публиковал статью про ключницу, ниже на фото эта же ключница, но уже вырезанная на станке с ЧПУ. Минимум усилий, максимум точность. Из-за люфтов точность конечно не максимум, но второй станок я сделаю более жестким.
А ещё на станке с ЧПУ я вырезал шестерёнки из фанеры, это намного удобнее и быстрее, чем резать своими руками лобзиком.
Позже вырезал и квадратные шестерёнки из фанеры, они на самом деле крутятся 🙂
Итоги положительные. Сейчас займусь разработкой нового станка, буду вырезать детали уже на этом станке, ручной труд практически сводится к сборке.
Нужно освоить резку пластика, потому как встала работа над самодельным роботом-пылесосом. Собственно робот тоже подтолкнул меня на создание своего ЧПУ. Для робота буду резать из пластика шестерни и другие детали.
Update: Теперь покупаю фрезы прямые с двумя кромками (3.175*2.0*12 mm), режут без сильных задиров с обоих сторон фанеры.
modelmen.ru
Постройка станочка ЧПУ часть 2 (подключение контроллера и составление простой управляющей программы в ArtCam)
Станок собран. В первой части я описывал процесс его создания. Теперь надо как то им управлять.Для управления станком я буду использовать самый простецкий синий контроллер основанный на микросхемах TB6560 и две программы первая это ArtCam (http://www.artcam.ru/) в которой подготавливается непосредственно управляющая программа, и вторая Mach4 (http://www.machsupport.com/) которая непосредственно управляет самим станком. Аспекты доставания и установки данного программного обеспечения скромно оставлю за рамками данного повествования.
Итак есть сам контроллер и схема подключения к нему непосредственно самого оборудования.
Так же к контроллеру идет инструкция на английском языке с указанием необходимых сигналов и на какие выходы LPT порта они приходят. В конце блога хотел приложить архив с инструкций на английском и русском языках, но т.к рейтинг маловат то не могу загрузить файл в собственный же блог (блин полный бред) тогда просто дам ссылку для тех кому интересно откуда скачивал сам cncmasterkit.ru/viewtopic.php?f=3&t=1058 (огромное спасибо автору сайта за перевод инструкции) скриншоты специально не привожу т.к будет очень мелко и что то путного там разобрать будет просто не реально. Единственно что надо помнить данный контроллер и микросхемы категорически не любят обрывов в проводах, поэтому перед включением надо тщательно проверить все провода на обрыв и также проверить на обрыв сами двигатели. И так как данный экземпляр контроллера рассчитан на 4- оси то необходимо просто при настройке в программе Mach4 отключить 4-ю ось.
После того как программа Mach4 и контроллер настроены, движки бегают как надо и куда надо (если бегут не в ту сторону то просто напротив той оси которая бежит неправильно ставится галочка, либо наоборот снимается, т.к в программе Mach4, 0 координат это левый нижний угол) самое время попробовать пильнуть что либо. Тут как раз на помощь и приходит программа ArtCam.
Дабы далеко не ходить за образцом для первой пробы возьму для примера одну из упорных плашек самого станка. Открываем плашку в CorelDRAW, проверяем что-бы все кривые ее составляющие были замкнуты и сохраняем ее в формате AI (Adobe Illustrator). Можно было бы и в другом формате но как посмотрел программа ArtCam как то не очень корректно работает с другими форматами. Также следует запомнить размеры самой детали которая будет вырезаться в данном случае ее размеры 38 на 30 мм.
Запускаем ArtCam и выбираем Файл, Новый, Модель. Откроется окно в котором задается размер новой модели, можно добавить к размеру самой детали по пару миллиметров с каждого края и эти размеры и вписать, также обратить внимание дабы точка нулевых координат была в нижнем левом углу, ну и естественно единицы измерения стояли миллиметры.
После чего нажать на кнопку ОК.
Откроется окно будущей детали с 2D и 3D видом.
После чего надо щелкнуть по Вектор, Загрузить слой, и в открывшимся окошке выбрать тот файл Ai в который сохранялась будущая деталька. После того как будет выбран файл ArtCam спросит его блин вставить как есть или разместить по центру, разумеется я согласился на второе.
После чего будущая деталька появляется по центру листа.
После этого щелкаю на ней правой кнопкой мышки и выбираю Разгруппировать векторы.
После этого щелкаю где то рядом с будущей деталькой дабы убрать выделение.
После чего внизу слева щелкаю по вкладке траектории и там выбираю Обработка по профилю.
Слева открывается свиток с настройками для будущей УП (Управляющей программы)
Свиток довольно здоровый и имеет множество параметров, но для начала постараюсь обойтись минимумом. Будущая деталь, несмотря на свою простоту имеет довольно сложную форму, в ней присутствуют как внутренние отверстия так и внешний контур и поэтому программе надо указать как она должна пилить то ее т.е сначала надо выпилить все внутренние отверстия а уж потом выпилить саму детальку из куска заготовки, если это дело не проконтролировать то программа а с ней и станок выпилит все как хочет т.е сначала контур а потом внутренние отверстия, вот блин смеху и матюков то будет. Соответственно сначала надо сделать дабы выпилились все внутренние отверстия а потом и внешний контур. Соответственно маркер переставляю на значение Внутрь. В опции Начальный Проход и Финишный проход ставлю значения 0,5 и 1,5 мм (откопал у себя кусок пластика с толщиной в 1 мм)
Потом иду вниз по списку до пункта Плоскость безопасности и смотрю его значение ( этот параметр определяет на сколько будет подниматься фреза при переходе от одного элемента к другому) оно 5 мм пусть так и будет, оставляю по умолчанию. И щелкаю на кнопке следующего параметра Профильный Инструмент.
Открывается окно с выбором фрезы для той или иной операции на выбор идут разные фрезы и прямые и закругленные и т.д можно добавить свою или помять параметры у уже существующей
Таким образом просто копирую и делаю фрезу диаметром 3 мм и ее соответственно выбираю.
Потом опускаюсь до пункта Порядок обработки, который и позволит задать порядок обработки будущей деталки. Снимаю птичку с режима Авто и ставлю на режим Вручную после чего жму на кнопку Выбрать вектор и держа Шифт на клавиатуре выбираю все внутренние отверстия.
После чего опускаюсь в самый низ рядом с опцией материал щелкаю на кнопку Определить и задаю толщину заготовки из которой будет вырезаться деталь ставлю как и в самом начале 1,5 мм
Так же в окошке имени УП пишу имя пусть будет 1.
Все настройка сделана и осталось только нажать на кнопку Сейчас дабы ArtCam смогла сгенерировать необходимую программу. Программа сгенерирована это видно по появившимся дополнительно окружностям внутри тех что необходимо вырезать.
Аналогичным же образом делается вторая программа но уже для внешнего контура. После чего есть программы для внутренних отверстий и для выпиливания внешнего контура.
Если щелкнуть теперь на вкладку Траектории то наверху можно увидеть две созданные программы для вырезания будущей деталки.
Но как то загружать в последствии две разных программы в станок и ждать когда они сделают в принципе одно и тоже не есть хорошо и надо просто их собрать в одну программу. Для этого щелкаю по кнопку Объединить УП
И соединяю их Списком (дабы не нарушить последовательность обработки) в одну программу и даю ей имя.
После чего щелкаю по кнопке Вычислить.
После чего переключаюсь обратно на вкладку Траектории, Выбираю 3D вид и выбираю Визуализация УП, и программа ArtCam покажет как будет резаться будущая деталька.
После чего можно сохранить готовую программу в формате понятной для программы Mach4.
Выбираю УП, Сохранить УП Как, и сохраняю готовую программу в формате программы Mach4.
На этом работа по подготовке деталки к вырезанию закончена и можно открыть программу Mach4 и заняться вырезанием самой детальки.
Вот таким образом составил самую простую программу.
Итак после подготовки УП в ArtCam просто прилепил заготовку на ненужные компакты и прошелся обычной 4-х перой фрезой, результат как говориться налицо фигня полная.
Все это говорит о том что обычный двусторонний скотч из хозмага нифига не катит для подобного, заготовка просто начинает плавать по нему за фрезой, а также для пиления пластика нужна однозаходная или на крайний случай 2-х заходная фреза, и разумеется сам стол нужно выводить в ноль.
we.easyelectronics.ru
Контроллер для ЧПУ на atmega8 16au своими руками: пошагово
Контроллер для станка легко сможет собрать и домашний мастер. Задать нужные параметры не сложно, достаточно учесть несколько нюансов.
Советы по сборке контроллеров для ЧПУ станков
Без правильного выбора контроллера для станка не удастся собрать сам контроллер для ЧПУ на Atmega8 16au своими руками. Эти устройства делятся на две разновидности:
- Многоканальные. Сюда входят 3 и 4-осевые контроллеры для шаговых двигателей.
- Одноканальные.
Небольшие шаровые двигатели наиболее эффективно управляются многоканальными контроллерами. Стандартные типоразмеры в данном случае – 42, либо 57 миллиметров. Это отличный вариант для самостоятельной сборки ЧПУ станков, у которых рабочее поле имеет размер до 1 метра.
Если же самостоятельно собирается станок на микроконтроллере с полем более чем в 1 метр – надо использовать двигатели, выпускающиеся в типоразмерах до 86 миллиметров. В данном случае рекомендуется организовывать управление мощными одноканальными драйверами, с током управления от 4,2 А и выше.
Контроллеры со специальными микросхемами-драйверами получили широкое распространение в случае необходимости организовать контроль работы станков с фрезерами настольного типа. Оптимальным вариантом будет микросхема, обозначаемая как TB6560 или A3977. У этого изделия внутри есть контроллер, способствующий формированию правильной синусоиды для режимов, поддерживающих разные полушаги. Токи обмотки могут быть установлены программным способом. При микроконтроллерах добиться результата просто.
Управление
Контроллером легко управлять, используя специализированное программное оборудование, установленное на ПК. Главное, чтобы у самого компьютера память была минимум 1 ГБ, а процессор – не менее 1 GHz.
Можно использовать ноутбуки, но стационарные компьютеры в этом плане дают лучшие результаты. И обходятся гораздо дешевле. Компьютер можно использовать для решения других задач, когда станки не требуют управления. Хорошо, если есть возможность оптимизировать систему перед началом работы.
Параллельный порт LPT – вот какая деталь помогает организовать подключение. Если контроллер имеет порт USB, то используется разъем соответствующей формы. При этом выпускается все больше и больше компьютеров, у которых параллельный порт отсутствует.
Изготовление самого простого варианта сканера
Одно из самых простых решений для самодельного создания ЧПУ станка – использование деталей от другого оборудования, снабженного шаровыми двигателями. Функцию отлично выполняют старые принтеры.
Берем следующие детали, извлеченные из прежних приборов:
- Сама микросхема.
- Шаговый двигатель.
- Пара стальных прутков.
При создании корпуса контроллера надо взять и старую картонную коробку. Допустимо использовать коробки из фанеры или текстолита, исходный материал не имеет значения. Но картон проще всего обработать, используя обычные ножницы.
Список инструментов будет выглядеть следующим образом:
- Паяльник вместе, дополненный принадлежностями.
- Пистолет с клеем.
- Ножничный инструмент.
- Кусачки.
Наконец, изготовление контроллера потребует следующих дополнительных деталей:
- Разъем с проводом, для организации удобного подключения.
- Цилиндрическое гнездо. Такие конструкции отвечают за питание устройства.
- Ходовыми винтами служат стержни, имеющие определенную резьбу.
- Гайка с подходящими для ходового винта размерами.
- Шурупы, шайбы, древесина в форме кусков.
Начинаем работу по созданию самодельного станка
Шаговый двигатель вместе с платой должны быть извлечены из старых устройств. У сканера достаточно снять стекло, а затем – вывернуть несколько болтов. Снимать потребуется и стальные стержни, используемые в дальнейшем, создавая тестовый портал.
Микросхема управления ULN2003 станет одним из главных элементов. Возможно отдельное приобретение деталей, если в сканере используются другие разновидности микросхем. В случае наличия нужного устройства на плате его аккуратно выпаиваем. Порядок действий при сборке контроллера для ЧПУ на Atmega8 16au своими руками выглядит следующим образом:
- Сначала разогреваем олово, используя паяльник.
- Удаление верхнего слоя потребует использования отсоса.
- Одним концом отвертку устанавливаем под микросхему.
- Жало паяльника должно касаться каждого вывода микросхемы. Если это условие соблюдается, на инструмент можно нажимать.
Далее микросхема припаивается на плату, тоже с максимальной аккуратностью. Для первых пробных шагов можно использовать макеты. Используем вариант с двумя шинами электропитания. Одна из них соединяется с положительным выводом, а другая – с отрицательным.
На следующем этапе идет соединение вывода у второго коннектора параллельного порта с выводом в самой микросхеме. Выводы у коннектора и микросхемы должны быть соединены соответствующим образом.
Нулевой вывод присоединяется к отрицательной шине.
Один из последних этапов – припайка шагового двигателя к устройству управления.
Хорошо, если есть возможность изучить документацию от производителя устройств. Если нет, то придется самостоятельно искать подходящее решение.
Провода рекомендуется припаивать так, чтобы потом их можно было легко соединить с зажимами-крокодилами. Клеммы с винтовыми соединениями – подходящие для решения задачи решения. Как и любые другие подобные детали.
Провода соединяются с выводами. Наконец, один из них соединяется с положительной шиной.
Шины и гнезда электропитания нужно соединить.
Термоклей из пистолета поможет закрепить детали, чтобы они не откалывались.
Используем Turbo CNC – программу для управления
ПО Turbo CNC точно будет работать с микроконтроллером, который использует микросхему ULN2003.
- Используем специализированный сайт, откуда можно скачать программное оборудование.
- Любой пользователь разберется в том, как провести установку.
- Именно данная программа лучше всего работает под MS-DOS. В режиме совместимости на Windows могут появляться некоторые ошибки.
- Но, с другой стороны, это позволит собрать компьютер с определенными характеристиками, совместимыми именно с данным программным обеспечением.
Рекомендации по настройкам
- После первого запуска программы появится специальный экран.
- Надо нажать пробел. Так пользователь оказывается в главном меню.
- Нажимаем F1, а потом выбираем пункт Configure.
- Далее надо нажать пункт «number of Axis». Используем клавишу Enter.
- Остается только ввести количество соей, которые планируется использовать. В данном случае у нас один мотор, потому и нажимаем на цифру 1.
- Для продолжения используем Enter. Нам снова понадобится клавиша F1, после ее применения в меню Configure выбираем Configure Axis. Затем – два раза нажимаем пробел.
Drive Type – вот какая вкладка нам нужна, до нее доходим многочисленными нажиманиями Tab. Стрелка вниз помогает дойти до пункта Type. Нам нужна ячейка, которая носит название Scale. Далее определяем, сколько шагов двигатель совершает только за время одного оборота. Для этого достаточно знать номер детали. Тогда легко будет понять, на сколько градусов он поворачивается всего за один шаг. Далее число градусов делится на один шаг. Так мы вычисляем количество шагов.
Остальные настройки можно оставить в первоначальном виде. Число, получившееся в ячейке Scale, просто копируется в такую же ячейку, но на другом компьютере. Значение 20 должно быть присвоено ячейке Acceleration. По умолчанию в этой области стоит значение 2000, но оно слишком большое для собираемой системы. Начальный уровень – 20, а максимальный – 175. Далее остается нажимать TAB, пока пользователь не доходит до пункта Last Phase. Здесь нужно поставить цифру 4. Далее жмем Tab, пока не дойдем до ряда из иксов, первого в списке. Первые четыре строчки должны содержать следующие позиции:
1000XXXXXXXX
0100XXXXXXXX
0010XXXXXXXX
0001XXXXXXXX
В остальных ячейках не нужно проводить никаких изменений. Просто выбираем ОК. Все, программа настроена для работы с компьютером, самими исполнительными устройствами.
Загрузка…xn—-ntbhhmr6g.xn--p1ai