Как собрать лазерный станок CO2 своими руками. Какие компоненты нужны для самодельного лазерного станка. Какие инструменты понадобятся для сборки лазерного ЧПУ станка. Как настроить и запустить самодельный лазерный гравер.
Компоненты и материалы для самодельного лазерного станка CO2
Для сборки лазерного станка CO2 своими руками понадобятся следующие основные компоненты:
- Лазерная трубка CO2 мощностью 40 Вт
- Блок питания для лазерной трубки
- Алюминиевый профиль для рамы станка
- Линейные направляющие и подшипники
- Шаговые двигатели NEMA17
- Драйверы шаговых двигателей
- Контроллер ЧПУ (например, Cohesion3D Mini)
- Зеркала и линзы для оптической системы
- Водяное охлаждение для лазерной трубки
- Вытяжной вентилятор
Также потребуются различные крепежные элементы, провода, кабели и другие расходные материалы.
Инструменты, необходимые для сборки лазерного станка
Для самостоятельной сборки лазерного ЧПУ станка CO2 понадобятся следующие основные инструменты:
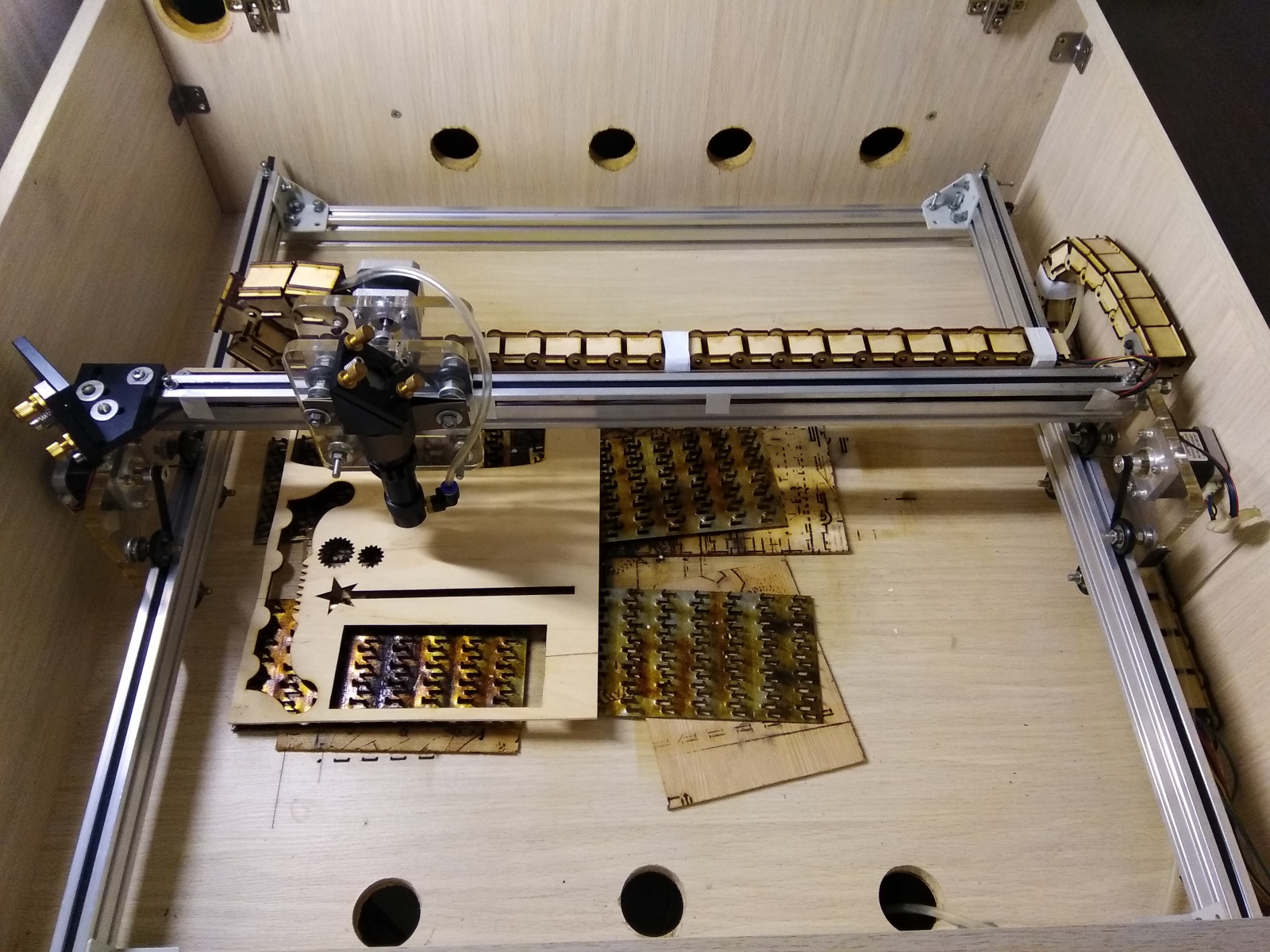
- Набор отверток и гаечных ключей
- Электродрель и сверла
- Паяльник и припой
- Мультиметр
- Ножовка по металлу
- Напильники
- Плоскогубцы и бокорезы
- Маркер и линейка
Также желательно иметь доступ к 3D-принтеру для изготовления некоторых пластиковых деталей.
Пошаговая инструкция по сборке рамы лазерного станка
Сборка рамы лазерного станка CO2 осуществляется в следующем порядке:
- Нарезать алюминиевый профиль нужной длины согласно чертежам.
- Соединить детали рамы с помощью угловых кронштейнов и болтов.
- Установить линейные направляющие для осей X и Y.
- Закрепить опорные пластины для шаговых двигателей.
- Смонтировать рабочий стол и механизм его перемещения по оси Z.
- Проверить перпендикулярность и параллельность всех осей.
При сборке рамы важно обеспечить высокую жесткость конструкции, от этого будет зависеть точность работы станка.
Монтаж оптической системы лазерного станка
Оптическая система лазерного станка CO2 состоит из следующих основных элементов:
- Лазерная трубка
- Три зеркала для отражения луча
- Фокусирующая линза
Монтаж оптики выполняется в такой последовательности:
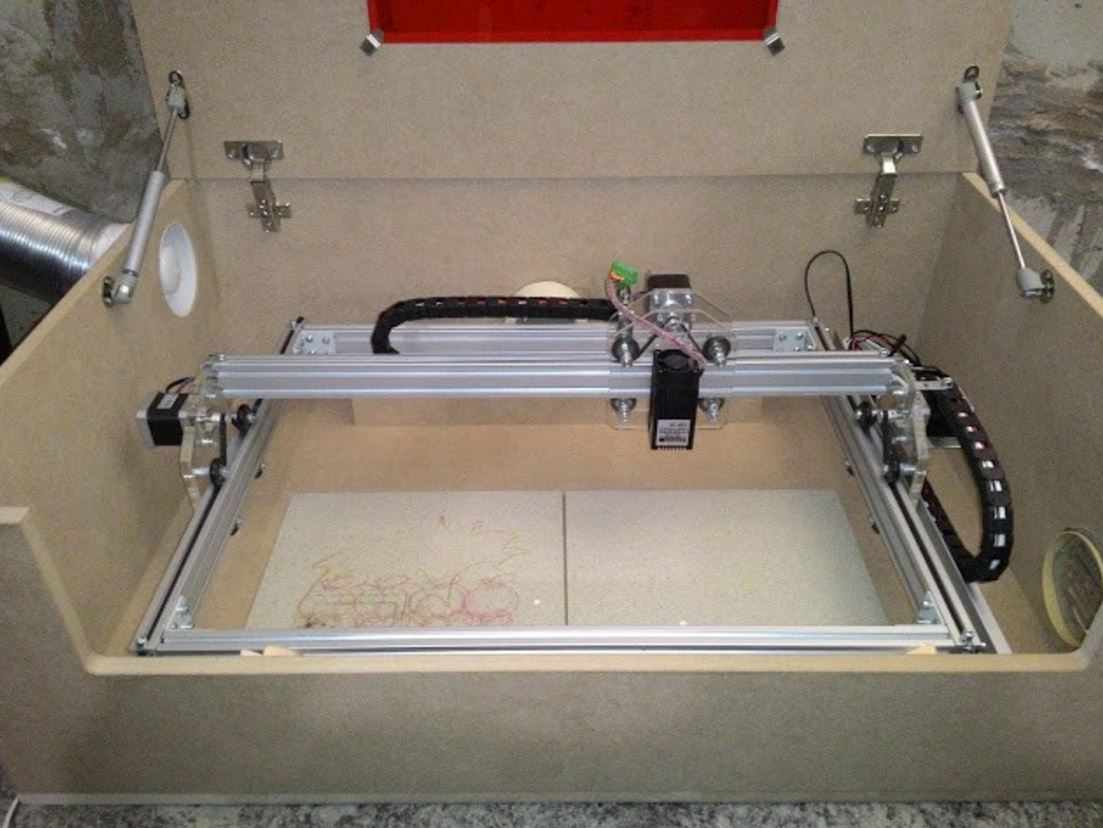
- Установить лазерную трубку на специальные кронштейны.
- Закрепить зеркала на осях X и Y.
- Смонтировать фокусирующую линзу на лазерной головке.
- Выполнить юстировку зеркал для точного попадания луча в центр линзы.
Точность юстировки оптической системы критически важна для качественной работы лазерного станка.
Подключение электроники и настройка ПО
Электронная часть лазерного станка включает в себя:
- Контроллер ЧПУ
- Драйверы шаговых двигателей
- Блоки питания
- Концевые выключатели
Последовательность подключения и настройки:
- Подключить шаговые двигатели к драйверам.
- Соединить драйверы с контроллером ЧПУ.
- Подключить блоки питания к компонентам.
- Установить и настроить программное обеспечение на ПК (например, LightBurn).
- Откалибровать перемещение осей станка.
После подключения всех компонентов необходимо тщательно проверить правильность соединений во избежание повреждения электроники.
Запуск и тестирование самодельного лазерного станка
Перед первым запуском лазерного станка CO2 нужно выполнить следующие действия:
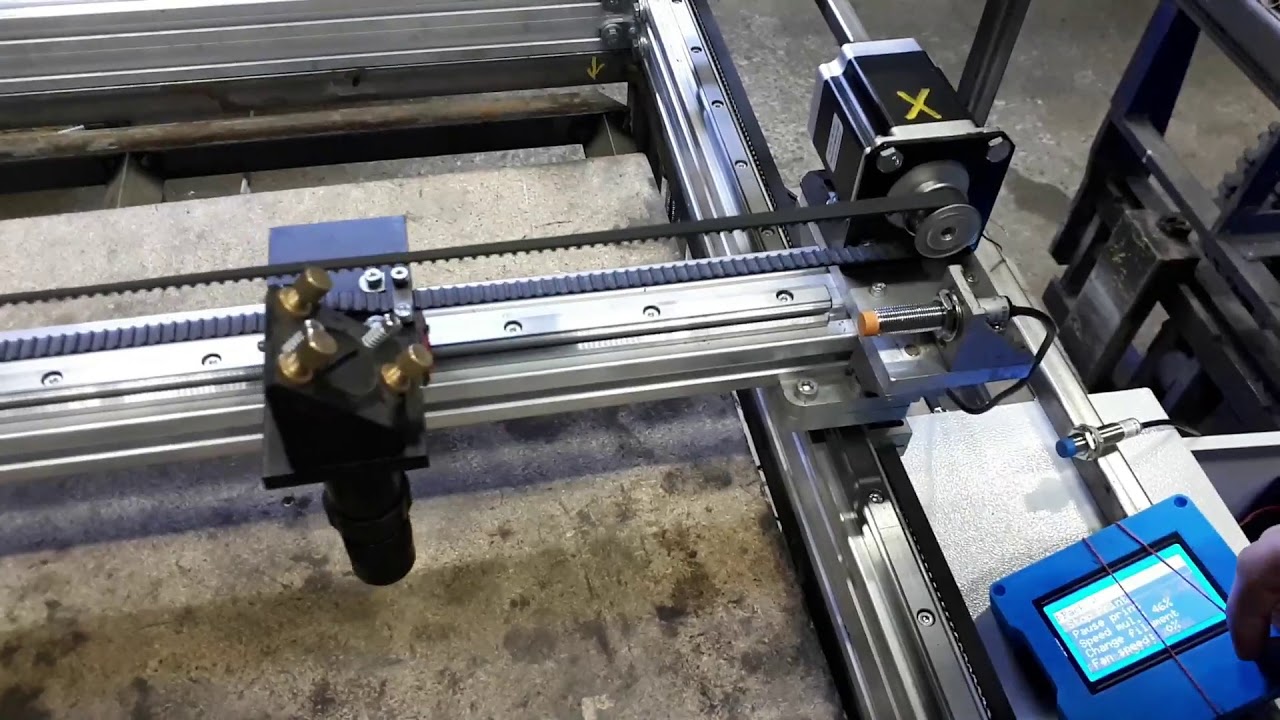
- Проверить надежность всех механических соединений.
- Убедиться в правильности подключения электрики.
- Включить систему охлаждения лазерной трубки.
- Запустить вытяжной вентилятор.
- Провести пробную гравировку на низкой мощности.
Как проверить работу самодельного лазерного станка CO2?
- Выполнить тестовую гравировку простого изображения.
- Проверить точность позиционирования по всем осям.
- Оценить качество фокусировки лазерного луча.
- Измерить мощность лазерного излучения на выходе.
При обнаружении неполадок необходимо остановить работу станка и устранить их перед продолжением эксплуатации.
Меры безопасности при работе с лазерным станком
При эксплуатации самодельного лазерного станка CO2 необходимо соблюдать следующие меры безопасности:
- Использовать защитные очки для работы с лазером.
- Обеспечить хорошую вентиляцию помещения.
- Не допускать попадания отражённого лазерного луча в глаза.
- Исключить контакт горючих материалов с зоной резки.
- Регулярно проверять целостность защитных кожухов.
Какие основные правила техники безопасности нужно соблюдать?
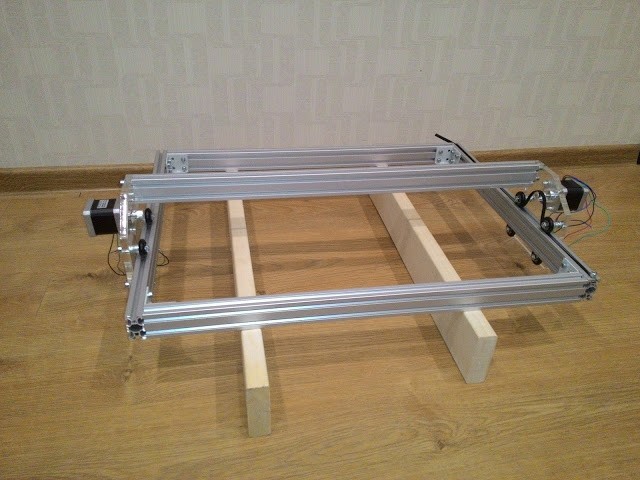
- Никогда не смотреть на прямой или отраженный лазерный луч.
- Не оставлять работающий станок без присмотра.
- Использовать станок только в хорошо вентилируемом помещении.
- Держать огнетушитель в легкодоступном месте.
- Отключать станок от электросети после завершения работы.
Строгое соблюдение правил техники безопасности позволит избежать травм и несчастных случаев при работе с лазерным оборудованием.
Самодельный станок ЧПУ с углекислотным лазером (CO2)
Благодаря китайским производителям, собрать ЧПУ станок на CO2 лазере не так то уж и сложно, это вполне возможно сделать самостоятельно и почти без всяких специфичных инструментов.
В этой инструкции студент из Германии с ником Vulcaman расскажет и покажет нам, как можно построить собственный станок ЧПУ с углекислотным лазером, менее чем за 1000 евро.
Как нам говорит Википедия: Углекислотный лазер, лазер на углекислом газе (CO2-лазер) — один из первых типов газовых лазеров. На начало XXI века — один из самых мощных лазеров с непрерывным излучением с КПД, достигающим 20 %.
Углекислотный лазер используется для гравировки резины и пластика, резки органического стекла и металлов, сварки металлов, в том числе металлов с очень высокой теплопроводностью, таких как алюминий и латунь.
Инструменты и материалы:
-Различные слесарные инструменты;
-Паяльные принадлежности;
-Акрил;
-Станок-донор K40;
-3D-принтер;
-Станок ЧПУ для резки алюминиевых деталей;
Алюминиевый профиль 5 мм паз I-типа*
810 мм 20×20 мм — 4 шт
205 мм 20×20 мм — 4 шт
695 мм 20×20 мм — 6 шт
790 мм 20×20 мм — 1 шт
669 мм 20×20 мм — 2 шт
63 мм 20×20 мм — 6 шт
50 мм 20×20 мм — 2 шт
83 мм 20×20 мм — 2 шт
370 мм 20x 40 мм — 2 шт
695 мм 20x 40 мм — 1 шт
460 мм 20x 40 мм — 2 шт
Весь профиль приобретался по размерам здесь.
Для получения точных результатов нужен жесткий X / Y-порт. Мастер использовал линейные направляющие MGN9, которые устанавливались на алюминиевые профили. Трансмиссия осуществляется с помощью ремней GT2 10 мм.
— Линейная направляющая MGN9 350 мм — 2 шт;
— Линейный рельс 650 мм MGN9 1 шт;
— Линейная направляющая MGN9 Н — 5 шт;
— Ремень GT2-10мм 10 м;
— Шкив GT2 20 зубьев Ширина 10 мм Диаметр 5 мм — 1- шт;
— Шкив 20T 10 мм GT2 — 3 шт;
— Пневматический амортизатор 20N Gasspring — 2 шт;
— Держатель стержня SK12 — 8 шт;
— Подшипник линейный LMK12UU — 4 шт;
— Линейный стержень D12мм x 117 мм — 4 шт;
— Стержень с резьбой M5 100 мм — 2 шт;
Мастер использовал лазерный источник мощностью 40 Вт. Длина трубки 40 Вт составляет всего 700 мм, поэтому она идеально впишется в корпус 810?500 мм. Для фокусирующей линзы вам понадобится тип 12 мм. Крепление лазера также имеет встроенную пневмоподушку.
— Лазерная трубка CO2 40 Вт 700 мм;
— 3 шт 20 мм зеркало + 1 шт 12 мм линза + держатель;
Электроника станка основана на плате Cohension3D Mini.
— Блок питания для лазера 40 Вт;
— Электропитание 250 Вт / 48 В;
— Силовой контактор 24 В;
— Реле PILZ PNOZ X1 — 2 шт;
— Бесконтактный переключатель PILZ PSEN 1.1p-20;
— DIN рейка;
— Драйвер мотора DM556 5,6A — 3 шт;
— Плата контроллера Cohension 3DMini 32Bit;
— Аварийный выключатель;
— OV5648 USB модуль камеры 1080p 120 градусов;
— Распределительный шкаф;
— Шаговый двигатель 40 мм NEMA17 2,0 A;
Как сделать лазрный ЧПУ станок своими руками
Шаг первый: технические характеристики и история создания станка
Три года назад студент купил свой первый лазер CO2, K40. Эта машина не совсем оправдала его ожиданий. Он был ограничен в размере гравировки, механические компоненты не очень хорошо сделаны, и работать с таким лазером было небезопасно.
Тогда он решил сделать свой собственный CO2-лазер, обладающий профессиональными возможностями, безопасностью и простотой в эксплуатации.
От идеи до рабочего станка у него ушло четыре месяца.
Дизайн станка R-LASER 6020 с открытым исходным кодом. Таким образом, можно получите все файлы САПР, необходимые для его изготовления бесплатно, исключая коммерческое использование.
Мастер предупреждает: опасно работать с CO2-лазером и сетевым напряжением.
Технические характеристики R-LASER 6020:
— Источник лазера CO2 мощностью 40 Вт
— Рабочая зона: 600×230 мм
— Скорость гравировки: 1000 мм / с
— Регулируемый Z-образный стол
— Поддержка камеры
— Поддержка программного обеспечения Lightburn
— промышленный дизайн
Шаг второй: материалы и чертежи для резки
В процессе изготовления потребуются листы из алюминия, фрезерованные на станке с ЧПУ.
Все критически важные детали, такие как X / Y-портал и все компоненты лазера, были сделаны из алюминия. Детали фрезерованы из листового металла толщиной 4 мм / 6 мм.
Для корпуса он использовал алюминий-дибонд, потому что он полностью блокирует лазер CO2. Даже сфокусированный луч не может прорезать этот материал.
Большинство деталей были вырезаны из алюминия-дибонда толщиной 3 мм окрашенного в белый цвет.
Две боковые панели корпуса были вырезаны из 6 мм листа.
Окно верхней двери выполнено из оргстекла толщиной 6 мм.
Он попытался свести к минимуму использование деталей, напечатанных на 3D-принтере, а где печать была необходима, она выполнялась нитью PLA.
Все файлы для печати, резки можно скачать в конце статьи.
В качестве программного обеспечения используется Lightburn, который будет поддерживать плату Cohension3D Mini Board и многие другие. Это программное обеспечение имеет все функции, необходимые для продуктивной работы с лазерным резаком.
Шаг третий: изготовление рамы
Основная рама изготовлена из алюминиевых профилей. Все крепления шаговых двигателей были вырезаны из алюминия толщиной 4 мм, чтобы обеспечить жесткое соединение между рамой и двигателями, даже когда двигатели нагреваются.
Теперь нужно установить пластины. Пластины имеют вентиляционные отверстия, чтобы отводить дым, образующийся при резке.
Шаг четвертый: установка осей X / Y , двигателей, направляющих
Ось Z реализована с помощью стержней диаметром 12 мм. Для правильного соединения между осью Z и основной рамой мастер использовал стандартные держатели штанги SK12.
После того, как все внутренние алюминиевые пластины установлены, нужно установить шаговые двигатели NEMA17 и шкивы для оси Y. Здесь нужно будет соединить 350-миллиметровую линейную направляющую MGN9 с экструзией 20×40 мм основной рамы.
Теперь нужно соединить ось X с осью Y. Соединение между осями X и Y обеспечивается двумя 6-миллиметровыми алюминиевыми переходными пластинами.
Двигатель оси Х крепится к левой 6-миллиметровой алюминиевой пластине.
Перед тем как установить пластину для оси X, нужно прикрепить к ней все шкивы. Используйте несколько шайб, чтобы обеспечить расстояние 1-2 мм.
Каретка X — ключевой компонент для хорошей гравировки.
Мастер постарался сделать каретку как можно более легкой и жесткой. Она сделана из алюминия толщиной 6 мм.
Теперь вы можете установить направляющие, ремни, проставки для левой и правой стороны оси X.
Шаг пятый: ось Z
В качестве рабочего стола мастер использует алюминиевую пластину Honeycomp 10 мм. Пластина устанавливается на алюминиевую пластину толщиной 4 мм.
Линейные подшипники LMK12UU прикреплены к алюминиевой пластине толщиной 4 мм.
Устанавливает собранный стол на станок.
Шаг шестой: отвод паров
Чтобы отвадить пары, которые образовываются при резке / гравировке, был сделан короб с вентиляционными отверстиями.
Шаг седьмой: верхняя крышка
Для верхней крышки было вырезано окно из оргстекла толщиной 6 мм.
Верхняя дверь сделана из алюминия толщиной 3 мм. Окно идеально устанавливается в него. Петли тоже самодельные из алюминия толщиной 6 мм.
Шаг восьмой: дополнительный корпус
В этом корпусе будут размещаться: силовой шкаф, воздушный клапан, водяное охлаждение, ящики для аксессуаров
Шаг девятый: установка оборудования
Устанавливает шкаф и подводит от него кабеля и трубки.
На крышку устанавливает концевой выключатель. Дверной выключатель — один из ключевых моментов техники безопасности. Переключатель будет непосредственно выключать лазер, когда дверь открыта.
Для прокладки кабелей устанавливаются кабель-каналы, распечатанные на 3D-принтере.
Шаг десятый: лазерная трубку
Лазерная трубка — основной компонент лазерного резака. В проекте была использована трубка мощностью 40 Вт от старого лазера K40.
Крепление трубки к основной раме осуществляется с помощью алюминиевых пластин толщиной 4 мм.
Шаг одиннадцатый: задняя и боковые панели
Теперь можно установить заднюю панель лазерного резака. На задней панели есть гнездо для электропитания, клемма заземления и алюминиевое крепление для вытяжного вентилятора. Воронка для вытяжного вентилятора подходит к трубке 160 мм.
Левая боковая пластина изготовлена из 6 мм алюминия. В ней устанавливается USB-разъем и быстроразъемное соединение для компрессора.
Правая боковая панель закрывает только механику.
Шаг двенадцатый: электрика
Электрику мастер собирает в силовом шкафу.
Электронику станка можно разделить на разные группы:
1. Цепи безопасности
В цепи есть два реле безопасности PILZ X1. Одно реле используется для аварийного выключения. Если нажать аварийный выключатель, силовой контактор отключит основное напряжение. Другое реле безопасности используется для верхней крышки и отключает лазер, когда дверь открыта.
2. Распределение электроэнергии
Для распределения питания требуемых напряжений для лазера (230 В переменного тока, 24 В постоянного тока, 48 В постоянного тока) были установлены DIN-рейки и клеммные колодки.
3. Драйвер двигателя
Для шаговых двигателей NEMA17 мастер использовал драйверы DM556 5,6A 48V. Благодаря высокому напряжению 48 В удалось достичь высоких скоростей до 1000 мм / с.
4. Источники питания
В качестве источников питания он использовал 48 В 250 Вт для двигателей NEMA17 и стандартный источник питания 40 Вт для лазерной трубки CO2. Напряжение 24 В для платы Cohension3D также генерируется источником питания для CO2-лазера.
5. Cohension3D Mini
В качестве основного контроллера применяется плата Cohension3D Mini от старого лазера K40. Эта плата поддерживает Smoothieware как микропрограммное обеспечение и все функции Lightburn. В дополнение к основному контроллеру мастер также создал специальный контроллер для оси Z.
Шаг тринадцатый: Z-контроллер
Готовый Z-Controller имеет следующие параметры:
— Входное напряжение 24 В
-Рабочее напряжение 3,3 В — 5 В
-Регулируемая частота шага DIP-переключателями от 2,5 до 25 кГц
-STM32-микроконтроллер
Файл для изготовления платы можно скачать в конце статьи.
Детали для платы:
Количество Описание Имя на плате
10x Резистор 1к 0805 R1-R10
3x Резистор 150 Ом 0805 R11-, R12, R13
3x Светодиод Красный 0805 D1, D2, D3
3x AO3400 N-канальный полевой МОП-транзистор Q1, Q2, Q3
2x Конденсатор 100 нФ 0805 C1, C2
1x SN74HC08 ДИП-14 U2
1x SN74HC32 ДИП-14 U3
1x Понижающий модуль (настроен на 5 В) U1
1x STM32F103C8T6 BP1
10x Клеммная колодка 2P 5,08 мм J2-J11
1x 3-позиционный DIP-переключатель SW1
Шаг четырнадцатый: программирование
Для программирования понадобится программатор ST-Link.
1. Загрузите «Утилиту STM32 ST-LINK»: можно скачать программное обеспечение здесь — https://www.st.com/en/development-tools/stsw-link004.html
2. Установите и откройте «Утилиту STM32 ST-LINK»
3. Теперь откройте файл Z-Controller.hex в утилите ST-Link: После этого нужно подключить STM32 «BluePill» к ST-Link-V2. После подключения нажать кнопку «Подключиться к кнопке traget».
Наконец нажмите «Загрузить». Теперь STM32 можно прошить..
Шаг четырнадцатый: камера
Чтобы включить одну из самых крутых функций Lightburn, нужно будет установить камеру и настроить ее, как написано здесь. Тогда можно нанести на карту гравировальное поле с его изображением, и согласовать работу с лазером.
Камера установлена в прорези окна. USB-кабель от камеры прикреплен к алюминиевым профилям верхней дверцы.
Все готово.
Работа самодельного лазерного ЧПУ на CO2
youtube.com/embed/RPSe8H98MLM» frameborder=»0″ allowfullscreen=»»>
Внимение!: Лазер СО2 мощностью 40 Вт — это не игрушка! Всегда надевайте сертифицированные лазерные очки, когда работаете с ними!
Автор самодельного ЧПУ станка на CO2 лазере использует защитные очики Laservision R02T1D01.
- Чертежи самодельного ЧПУ станка на CO2 лазере здесь.
- Файлы для платы можно скачать тут.
Самодельный газовый лазер
Для жалоб на нарушения авторских прав, используйте другую форму. Study lib. Загрузить документ Создать карточки. Документы Последнее. Карточки Последнее. Сохраненные карточки.
Поиск данных по Вашему запросу:
Самодельный газовый лазер
Схемы, справочники, даташиты:
Прайс-листы, цены:
Обсуждения, статьи, мануалы:
Дождитесь окончания поиска во всех базах.
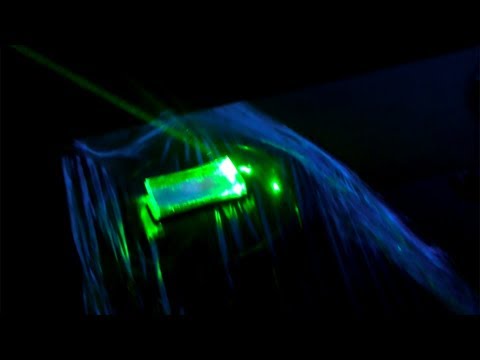
По завершению появится ссылка для доступа к найденным материалам.
Содержание:
- Самодельный лазерный СО2 излучатель
- Самодельный лазерный проектор )
- Ремонт лазера
- Самодельный Гелий-Неоновый лазер
- Лазерная трубка CO2 40W и другие компоненты лазерного станка для самостоятельной сборки
- Самодельный газовый лазер работающий в непрерывном режиме
- . : Самодельный CO2 лазер с продольным разрядом : .
- Лазерная сварка своими руками
- Лазерный резак на газовой смеси часть 2
- Углекислотный лазер своими руками
ПОСМОТРИТЕ ВИДЕО ПО ТЕМЕ: лазер на воздухе
youtube.com/embed/8WDVYsWvOVc» frameborder=»0″ allowfullscreen=»»/>Самодельный лазерный СО2 излучатель
Войдите , пожалуйста. Хабр Geektimes Тостер Мой круг Фрилансим. Войти Регистрация. Изучаем азотные лазеры — часть 1. Лазеры поперечного разряда DIY или Сделай сам , Лазеры Наверное, каждый увлекающийся околоэлектронными самоделками задавался вопросом, возможно ли сделать лазер самостоятельно, дома. И наверняка, очень часто натыкался на довольно предсказуемый ответ от старших, что это очень сложно или практически невозможно, дескать, лазерное излучение можно получить только из специальных дорогостоящих кристаллов и стекол, или каких-то ещё неведомых материалов, которые можно достать только в Тёмных Топях или на Заокраинном Западе.
На самом деле это не так. Число веществ, в которых возможен лазерный процесс, исчисляются тысячами, и некоторые из них находятся буквально под ногами, и в прямом смысле вокруг нас, повсюду. Так, например, можно с удивлением узнать, что возможно получить лазерную генерацию в водяных парах, в красителях, добытых из фломастеров, в конце концов, в углекислом газе, выдыхаемом многими живыми существами, была получена лазерная генерация мощностью в сотни киловатт.
Но, есть ещё одна рабочая среда лазера, которая распространена гораздо больше, чем все остальные вместе взятые. Источник бесперебойного питания на источнике бесперебойной подачи информации Читайте на Хабре. Читают сейчас. Простите, пользователи macOS, но Apple зашла слишком далеко 43,6k Поделиться публикацией. Похожие публикации. Java backend разработчик удаленно или в офисе. Frontend developer React. Frontend разработчик React. SoftMediaLab Екатеринбург Можно удаленно.
Все вакансии. Laserbuilder 8 декабря в 0. Нет, с ядерной не надо. А вот смотрите — тут уже кто-то запускал электронный микроскоп. Значит, технологии работы с пучком электронов и получение глубокого вакуума дома в принципе есть.
Осталось собрать ондулятор и по сути лазер готов. А для газодинамического лазера потребуется практически реактивный двигатель. И тут на сцену выходит товарищ Негода. Я больше намекал на некоторую опасность самого процесса генерации на свободных электронах. Там все очень точно и аккуратно нужно, иначе можно засветить, например, рентгеном во все места. Но с другой стороны, там генерация, обычно, от жёсткого УФ до мягкого рентгена делают, правда, иногда и жёсткий. Мягкий же рентген относительно безопасен — он даже через бумагу не проходит.
Насчет безопасности азотного лазера — тут не все так однозначно. Все-таки некоторая доля лазерного излучения до сетчатки доходит — во всяком случае, ее достаточно, чтобы его увидеть.
Я, когда имел дело с азотным лазером, отчетливо видел его излучение, когда случайно получал бликом в глаз от стекол, люминесценцию которых в нем смотрел. Меня еще тогда удивило, что видимость излучения нм не равна нулю. Конечно, да — энергия измеряется микроджоулями. О тепловом действии на сетчатку с учетом ослабления средами глаза тут речи не идет. Но помним, что мощность в импульсе при всем при этом чудовищна?
И что это УФ излучение, причем достаточно жесткое, чтобы оказать физиологическое действие. Я не уверен, что то что мы видим и я в том числе в виде бликов от азотного лазера это именно восприятие сетчаткой. Более вероятно, что это люминесценция самих внутриглазных сред. В темноте ещё можно заметить свечение пылинок по пути луча в воздухе.
Но это касается почти всех видов лазеров, даже инфракрасных при большой мощности. Не, люминесценция не образует изображения на сетчатке. Свечение внутренней среды глаза видно, как равномерный голубой туман. А я видел ясный, хоть и заметно расфокусированный, фиолетовый блик. Так вот же сегодня даже про это публикация была: habr. И да, колбочки имеют ненулевую чувствительность к ультрафиолетовому излучению.
Основная поясняющая картинка Если монохроматором светить в глаз, то на нм вы увидите очень насыщенный фиолетовый цвет без примесей синего на выходной щели. На его фоне вы все еще продолжаете видеть наиболее яркие окружающие предметы. Но помним, что мощность в импульсе Там свехлюминесценция, поэтому импульс не должен быть коротким. Вот если поставить резонатор, тогда да. Он там не может быть длинным. Время жизни верхнего уровня в чистом азоте при пониженном давлении — около 40 нс, а на воздухе — вообще единицы наносекунд.
Так минимальная длина импульса не ограничивается временем жизни уровня. Это излучение уже будет вынужденное, и поставив резонатор начнётся очень быстрый съём энергии с уменьшением длительности импульса. А с модулятором добротности импульс ещё больше уменьшится. Развлекался этим в молодости в 80х. Всё получилось. Основная проблема была не как все это построить и запустить, а как включить лазер незаметно для санитаров окружающих.
Там искры во все стороны и треск стоял такой, как будто у нас короткое замыкание во всей проводке сразу и квартира сейчас сгорит на фиг. Ну и запахи весьма специфические. Кроме того с воздушным лазером там получилось не очень и мы начали добывать азот из разных странных веществ, некоторые из которых были токсичными. Люди при этом не пострадали, только соседские коты но они сами виноваты — не фиг было лизать неизвестные порошки.
Я так думаю, что попытка повторить это в современной России сразу привела бы к знакомству со всякими там антитеррорестическими спецслужбами и центрами Э, которые понабижали бы по наводке соседей А насколько имеет смысл для увеличения мощности его масштабировать в длину?
Скажем километровой длины такой лазер будет вундервафлей? Масштабируется он до длины где-то в пару метров. Дальше выходная энергия остается постоянной, так как за время импульса свет успевает пробежать всего пару метров, и при расстоянии большем чем эта пара метров он не будет успевать снимать накопленную энергию накачки.
А если организовать накачку бегущей волной? Чтобы по ходу распространения света шла и волна возбуждения? Как по мне, импульсный лазер невидимого диапазона — не самая интересная штука. Вот да, видел на ютубе как им накачивали разные красители, впечатлился. AquiHostStrider 9 декабря в 0. Наоборот: невидимый диапазон — это не баг, а фича. Но очень шумная и недальнобойная установка действительно не особо интересна.
А вот добить хотя бы до полукилометра и попробовать двумя лазерами пообщаться морзянкой в полевых условиях было бы прикольно. Каково применение в практических целях? Хотелось бы резать фанеру на ЧПУ. Gryphon88 10 декабря в 0. Дешевле и спокойнее купить. КПД, сертификация, гарантия, цена владения… Кстати, чтобы резать фанеру, Вам понадобятся гальванозеркала, которые уж точно лучше купить.
Laserbuilder 10 декабря в 0. В данном случае никакого применения. Обычно это делается или как научный проект в институте или просто из любви к искусству. Что обсуждают. Почему не 1С? Самое читаемое. Сутки Неделя Месяц Как я проработала 3 месяца в Я. Как я проработала 3 месяца в Я. Рекомендуем Разместить. Ваш аккаунт Войти Регистрация. Услуги Реклама Тарифы Контент Семинары. Настройка языка.
О сайте. Служба поддержки. Мобильная версия. Интерфейс Русский. Сохранить настройки.
Самодельный лазерный проектор )
Войти или зарегистрироваться. Лазер предназначен для проверки возможности сборки самодельного CO2 пазера из общедоступных материалов. Высокое усиление делает лазер некритичным к смеси и юстировке. Первые опыты по получению генерации лучше всего ставить именно на таком типе лазера. Но не ждите от этого лазера слишком много. Мощность и кпд низкие. Тип лазера.
Лазер на диоксиде углерода (СО 2 лазера) был одним из самых ранних газовых лазеров, которые будут разработаны. Он был изобретен Кумар.
Ремонт лазера
Лазер хорош в качестве первого домашнего со2 проекта, если есть подходящий вакуумный насос. Высокое усиление делает лазер некритичным к смеси и юстировке. Первые опыты по получению генерации лучше всего ставить именно на таком типе лазера. Но не ждите от этого лазера слишком много. Мощность и кпд низкие. Молекулярный лазер низкого низкого давления с продольным разрядом импульсно-периодического действия. Почему именно такой?
Самодельный Гелий-Неоновый лазер
Магда, Ю. Ткач, Е. Лемберг, Г. Гадецкий, А. Сидельникова, В.
Подпишитесь на автора, если вам нравятся его публикации.
Лазерная трубка CO2 40W и другие компоненты лазерного станка для самостоятельной сборки
Перейти к содержимому. У вас отключен JavaScript. Некоторые возможности системы не будут работать. Пожалуйста, включите JavaScript для получения доступа ко всем функциям. Отправлено 20 Март —
Самодельный газовый лазер работающий в непрерывном режиме
Чипгуру Пропустить. Самодельный лазер: чертежи, вопросы, решения Есть вопрос? Задайте его тут. Пожалуйста, придерживайтесь правила: один вопрос — одна тема. Вложения 37 Пред. Сообщений: Страница 1 из Тема наверно немного может показаться немного бредовой, но я твердо уверен в том что если одна часть человечества что то создала, то другой и повторить не грех Натолкнулся я в сети на гуляющие чертежи 50Вт-ного СО2 лазера. С виду всё довольно реально, стеклянные трубочки, штуцерочки, токарные работы
Любительская голография — технологии, использующие непрофессиональное и металлообработке; газовый лазер был единственным вариантом, любители голографии конструируют самодельные импульсные лазеры.
. : Самодельный CO2 лазер с продольным разрядом : .
Самодельный газовый лазер
Войдите , пожалуйста. Хабр Geektimes Тостер Мой круг Фрилансим. Войти Регистрация.
Лазерная сварка своими руками
ВИДЕО ПО ТЕМЕ: Гелий-неоновый лазер
youtube.com/embed/WBJ8eYOwLuc» frameborder=»0″ allowfullscreen=»»/>Если заменить M2 на 1. Усилитель улучшает форму пучка, а круговой поляризатор предотвращает возврат пучка в режущую головку. Режущая головка была изготовлена на заказ. Пучок направляется на фокусирующую линзу, которая находится в центральной части режущей головки. Газ поступает в камеру ниже фокусирующей линзы.
Гелий-неоновый газовый лазер, работающий в непрерывном режиме, дает излучение монохроматического света с длиной волны нм, развивая мощность 40 мВт. Как сделать бесконечный источник энергии.
Лазерный резак на газовой смеси часть 2
Войти или зарегистрироваться. Для начала остановимся на лазере на углекислом газе. Мне попадался один файл с подробным описанием технологии как сделать лазер на углекислом газе. Меня это тогда очень заинтересовало. Но мне пообещали что отдадут готовую трубку и по этому я пока отошел от этого дела.
Углекислотный лазер своими руками
Лазер на диоксиде углерода СО 2 лазера был одним из самых ранних газовых лазеров , которые будут разработаны. Он был изобретен Кумар Пател из Bell Labs в году, и до сих пор один из самых полезных. Углекислотные лазеры являются наиболее мощными непрерывными волнами лазеров , которые в настоящее время доступны. Конкретные пропорции варьируютсязависимости от конкретного лазера.
Собираем ЧПУ лазерный станок своими руками
В этом посте мы расскажем вам историю о том, как построить ЧПУ лазерный станок своими руками, которую нам поведал один из подписчиков.
Предисловие
Пару месяцев назад я просматривал записи с конкурса, в котором увидел несколько довольно крутых гравировальных машин, и я подумал: «Почему бы мне не создать свою собственную?». И так я и сделал, но не хотелось копировать чужой проект, я хотел сделать свой собственный уникальный ЧПУ станок своими руками. И так началась моя история …
Технические характеристики
Этот лазерный гравер оснащен 1,8 Вт 445 нм лазерным модулем, конечно, это ничто по сравнению с промышленными лазерными резаками, которые используют лазеры более 50 Вт. Но для нас будет достаточно и этого лазера. Он может вырезать бумагу и картон, и может выгравировать все виды древесины или изделия из фанеры. Я еще не тестировал другие материалы, но уверен, что он может наносить гравировку на многие другие поверхности. Сразу зайду наперед и скажу, что он имеет большое рабочее поле размером около 500×380 мм.
Кому под силу сделать такой лазерный станок? Каждому, не важно, вы инженер, юрист, учитель или студент, как я! Все, что вам необходимо – терпение и большое желание получить действительно качественный станок.
Мне потребовалось около трех месяцев, чтобы спроектировать и построить эту гравировальную машину, в том числе я около месяца ждал детали. Конечно, такую работу можно выполнить и быстрее, но мне всего 16 лет, поэтому работать я мог только на выходных.
Нужные материалы для сборки
Понятно, что вы не сможете сделать лазерный гравер, не имея нужных деталей, поэтому я составил спецификацию с почти всем необходимым для его изготовления. Практически все детали куплены на Aliexpress, потому что это дешево, и есть бесплатная доставка для большинства товаров. Другие детали, такие как обработанные стержни и листы МДФ (можно сделать из фанеры), были куплены в местном строительном магазине. Лазер и драйвер лазера были заказаны на ebay.
Я попытался найти самые низкие цены для всех деталей (не включая доставку).
Было потрачено много времени, прежде чем я пришел к этому дизайну. Сначала я сделал несколько других, но именно этот был действительно самым красивым из всех остальных. Первым делом я нарисовал все детали в графическом редакторе и распечатал их в натуральном размере.
Весь гравер я собираю из листов МДФ толщиной 18 мм и 12 мм.
Выбор пал на этот дизайн также потому что можно было легко прикрепить ось Z и инструмент, превратив наш станок в фрезерный.
Конечно, я мог бы сделать другой, более простой дизайн … Но нет! Хотелось чего-то особенного!
Процесс сборки
Распечатав чертежи, у меня появились детали, которые необходимо было собрать в кучу. Первое, что я сделал, – это установил дверь корпуса электроники с левой стороны и замок с петлей (дверца устанавливается без трудностей, поэтому я сделал это в первую очередь. Чтобы собрать корпус для электроники, я использовал множество L-образных железных скоб с отверстиями под саморезы. Если корпус планируется изготавливать из фанеры, то предварительно необходимо просверлить в ней также отверстия под саморезы.
Сначала была взята снова левая сторона корпуса электроники и установлена на нее передняя и задняя части корпуса при помощи скоб. Я не использовал винты или гвозди для установки крышки и панели управления, а прикрутил те же скобы к стенкам и просто положил крышку с панелью на них чтобы в дальнейшем при установке электроники не возникало никаких неудобств.
Отложив корпус электроники в сторону и взяв опорную плиту и опорные части оси Х необходимо установить их таким образом, как показано на фотографиях, убедившись, что ось Х и крепление мотора находятся на правой стороне станка с ЧПУ. Теперь можно смело установить корпус электроники таким же образом, как и показано на рисунках.
Далее были взяты два 700-мм вала, нанизаны на них по два линейных подшипника на каждый, и они были зафиксированы на самом станке при помощи специальных концевых опор для шлифованных валов.
На данном этапе у меня получилось вот что:
Уберите в сторону эту половину лазерного станка на некоторое время и займитесь подвижной частью X, а ось Y поддержите и прикрепите на весу опоры вала к движущейся части оси X гайками и болтами и прикрепите двумя гайками опору на ось Х.
- Теперь возьмите два 500-миллиметровых вала, наденьте по одному линейному подшипнику на каждый вал, наденьте опору вала на каждый конец каждого вала и установите их на станок.
- Прикрепите ходовую гайку оси Y на подвижную часть оси Y с помощью гаек и болтов, и прикрутите ее к линейным подшипникам с помощью саморезов.
- Прикрепите ходовой винт и шаговый двигатель.
- Подсоедините все это к другой половине гравера и закрепите ходовой винт и шаговый двигатель.
Теперь у вас должно выйти что-то похожее на то, что изображено на этом фото:
Электроника для станка
Я также установил деревянную деталь в корпус электроники, чтобы закрепить шаговый двигатель.
Далее была прикреплена верхняя часть корпуса электроники, пульт управления и рабочий стол уже после того, как была установлены несколько печатных плат, схема к которым прилагается в комплекте.
Ну или можно просто положить крышку и панель на гравёре, чтобы полюбоваться проделанной работой и великолепным дизайном.»
Выводы
Это, пожалуй, и вся информацию, которую он нам донес, но это довольно неплохая инструкция для тех, у кого есть мечта собрать собственноручно хороший самодельный лазерный станок для домашних и хоббийных целей.
Сама сборка лазерного гравера не особо затратная, поскольку количество деталей минимально, да и стоимость их не особо высока. Самыми дорогими деталями являются, наверное, шаговые двигатели, направляющие и, конечно же, детали самой лазерной головки с системой охлаждения.
Именно этот станок заслуживает особого внимания, поскольку не каждый лазерный гравер позволяет быстро устанавливать на 3 ось фрезерную машинку и превращать станок в полноценный ЧПУ фрезер.
В заключение хочется сказать: если вам действительно хочется самому собрать качественный станок ЧПУ своими руками, который будет служить верой и правдой долгие годы, не нужно экономить на каждой детали и пытаться сделать направляющие ровнее заводских или заменять ШВП на шпильку с гайкой. Такой станок работать хоть и будет, но качество его работы и постоянная настройка механики и программного обеспечения просто расстроит вас, заставив пожалеть о потраченном на него времени и средствах.
виды линз, расположение трубки, подключение компрессора и отзыв о специфическом оборудовании для ремонта лазерного станка своими руками
Обзор-распаковка лазерной трубки 40W, а также аксессуаров для сборки или ремонта лазерного станка (гравера/резака).
Это скорее не полноценный обзор, а пост из серии «смотрите, что я купил», так как из-за специфики оборудования провести полное тестирование вот так сразу проблематично, мой станок еще в достройке.
В обзоре будет краткая информация по лазерным станкам, СО2 трубкам, дополнительному оборудованию и запчастям для сборки станка, схемы подключения и так далее. Внимание: много фотографий.
Привет всем читателям Mysku!
Хочу познакомить вас со специфическим оборудованием, предназначенным для сборки (или ремонта) лазерного режущего/гравирующего станка. Все наверняка слышали про лазерную резку и услуги раскроя лазером. Как правило, эти услуги оказываются на промышленных станках с мощным лазером. СО2 лазер – это один из самых дешевых вариантов, имеет низкую удельную стоимость ватта излучения. Распространенные СО2 трубки имеют мощность от 40W до 100W. Внутри смесь газов на основе СО2 и контур жидкостного охлаждения. Питается лазер от высоковольтного источника напряжения примерно 20…40кВ, в зависимости от мощности. Также от мощности лазера зависят размеры трубки: чем мощнее, тем длиннее трубка, ну еще и диаметр увеличивается.
Сам станок представляет собой станину с механикой по XY, привод по Z в бюджетных моделях отсутствует (там регулировка осуществляется исключительно фокусировкой лазерного пучка на нужную высоту). Работа осуществляется под управлением специальными контроллерами из программы на компьютере.
Основа любого подобного станка – это СО2 трубка. Есть и другие виды лазеров (твердотельные, волоконные), сейчас я их рассматривать не буду, так как СО2 все-таки до сих пор является наиболее дешевым источником лазерного излучения с большой мощностью.
Дисклеймер: лазерное излучение является потенциально опасным. Следует принимать меры предосторожности при работе и обслуживании лазера, а также использовать защитные средства (очки). Будьте внимательны при контакте с высоковольтной частью оборудования. Обязательно подключайте заземление к высоковольтной части и к корпусу станка. Лазер 40W режет фанеру, а что он может сотворить с тканями человеческого тела лучше не проверять
Фото из одного из отзывов
Про этот тип лазеров <a
href=«ru.wikipedia.org/wiki/%D0%A3%D0%B3%D0%BB%D0%B5%D0%BA%D0%B8%D1%81%D0%BB%D0%BE%D1%82%D0%BD%D1%8B%D0%B9_%D0%BB%D0%B0%D0%B7%D0%B5%D1%80»>Вики говорит следующее:
Углекислотный ла́зер, лазер на углекислом газе (CO2-лазер) — один из первых типов газовых лазеров (изобретен в 1964 году). Один из самых мощных лазеров с непрерывным излучением… Их КПД может достигать 20 %.
… Активной средой углекислотных лазеров является газообразная смесь CO2, азота (N2), гелия (He). Иногда в смесь также добавляется водород (h3) или ксенон (Xe).
Фотографии среднестатистического китайского лазерного станка
Для затравки покажу видео, на котором видна работа лазерного резака по прозрачному акрилу
Собственно говоря именно это видео и сподвигло меня собрать лазерный станок
Самостоятельная сборка лазерного станка не сложная, как правило не занимает долго времени и не требует специальных знаний (шутка)
Лазерный режущий станок представляет собой рабочую область с механизмом перемещения зеркал и линз, рядом установленную трубку и высоковольтный блок питания (ВВ). Все это закрывается кожухом/корпусом.
Иногда делают окошки для наблюдения, но это чревато – стекло не должно пропускать излучение СО2 лазера, около 10мкм.
В отличие от твердотельных лазеров, здесь не перемещается лазерный модуль непосредственно. Трубка громоздкая, хрупкая и требует водяного охлаждения. Вместо этого используют кинематическую схему с перемещающимися зеркалами.
Лазерное излучение выходит из трубки, попадает на зеркало, установленное под 45° и поворачивающее луч на 90° в рабочую зону. Следующее зеркало закреплено на профиле оси Х, перемещается вместе с этой осью. Оно также поворачивает луч на 90°. На самой оси установлена каретка с специальной головкой (laser barrel, laser focusing head), в которой помимо еще одного зеркала, поворачивающего луч из горизонтальной плоскости вертикально вниз, установлена фокусирующая линза, собирающая лазерный пучок в точку. Таким образом происходит перемещение лазерного излучения в плоскости XY.
Дополнительно на головку подводят сжатый воздух, с целью создания избыточного давления около линзы и отвода продуктов горения непосредственно от точки реза.
Как правило, кинематическая схема собрана на рельсовых направляющих (рельсы HWIN/MGN) либо ролики+профиль. Приводится в движение ремнями. Это дает большую скорость перемещение при легкой головке.
Для подключения трубки потребуется источник ВВ напряжения, система жидкостного охлаждения (насос, датчик протока жидкости, рабочая жидкость и трубки/фитинги). Плата управления совместимы с Mach4 либо сделаны под другой платный софт, бывают варианты под Arduino.
Несколько слов про электрическую часть и трубку.
Собственно говоря, информации по сборке или ремонту достаточно много. Можно модернизировать старый китайский станок установкой более мощной трубки и другой электроники, а можно собрать с нуля, большой сложности не представляется.
Для начала нужно выбрать компоненты для сборки и параметры будущего станка (размеры, фокусное расстояние/высота головки)
Вот примерный перечень деталей, необходимый для сборки лазерного станка:
- Профиль или рама для станка. Я использую конструкционный профиль типа 40х40 или 60х60
- Рельсы MGN/SBR, недорогой и небольшой вариант можно сделать на валах 12-12 мм (лучше ограничить размеры обрабатываемой поверхности в этом случае).
- Ремни HTD, то есть широкие 15 мм, черного цвета.
- Трубка СО2. При покупке уточняйте дату заправки, так как со временем газ разлагается. Трубка стеклянная, так что упаковка и доставка должна быть качественная.
Не ищите с бесплатной доставкой, лучше курьерской почтой.
- Держатель трубки
- Источник ВВ напряжения (блок питания). В моем случае 40Вт
- Датчик протока воды
- Насос
- ВВ провод, разъемы
- Плата-контроллер для компьютера (есть варианты под Mach4, Linux CNC/EMC2 Control, есть под другой софт, есть с LPT, USB, LAN подключением, есть на основе Arduino).
- Двигатели и драйверы. Также можно взять на ваш вкус.
- Держатели зеркал и Laser barrel head – фокусировочная трубка и крепежи зеркал.
- Комплект зеркал (линз): три отражающих и одно фокусирующее. Обычно используют из селенида цинка ZnSe, или просто линзы покрытые чем либо отражающим (Si/Cu).
- Мелочевка – метизы, крепежи, приводные звездочки и прочее.
- Корпус. Можно изготовить самостоятельно из ДСП и прочих радостей.
Основные задействованные контакты:
USB/LAN/LPT порт для компьютера и получения управляющих сигналов.
Далее подключаются 2 шаговых двигателя. Основные сигналы: Step, Dir на драйвер, с драйвера 4 провода на обмотки A+/A-, B+/B-. Бользих вопросов такое подключение не вызывает. Для больших станков есть смысл поставить Nema23 и драйверы типа TB6550/TB6600 (обзор сделаю чуть позже), для небольших размеров ( примерно до 30х40, формат листа А3) можно Nema 17 и простые драйверы типа A4988/DRV8825
Схема подключения блока ВВ питания
Управление мощностью осуществляется с помощью PWM сигнала с платы (20-50 кГц) или потенциометра.
WP — сигнал с датчика протока воды (или насоса, если стоит чиллер). Если ничего нет, можно поставить перемычку. Этот сигнал нужен, чтобы лазер не перегрелся и не работал бы без охлаждения.
G — это общий сигнал (земля/ноль/минус)
H или L — это сигналы включения лазера. Используется либо один вариант, либо другой. Это зависит от конкретной платы управления. H — высокий уровень, L — низкий уровень включения.
Далее, на выходе два провода: высоковольтный (+) и низковольтный (-). Обязательно требуется заземление блока ВВ питания и корпуса станка.
Управляющая программа типа Mach4/LinuxCNC/LaserCut или другие, подает команды перемещения по плоскости, команды включения/выключения излучения, а также регулировки мощности (актуально для гравировки). Дополнительно включен насос для охлаждения, воздушный компрессор, вытяжка.
Теперь покажу, что успел приобрести. Все посылки доставлялись SPSR
Трубка СО2
Параметры:
Мощность: 40 Вт
Длина: 700 мм
Диаметр: 50 мм
Охлаждение: жидкостное.
Упаковка внутри посылки
Упаковка качественная, в несколько слоев картона и пупырчатой пленки
Присутствует несколько наклеек типа «Осторожно хрупкое»
Вскрываем коробку, а там… еще упаковка
Достаем вторую коробку
Внешний вид второй коробки
Внутри находится сама трубка СО2
Длина лампы 70 см, диаметр 50мм
Дата заправки газом 19 мая 2017. Китайское ОТК расписалось в приемке
Внутри хорошо видно встроенный контур охлаждения
Наклейка «Лазер, осторожно»
Первый фланец
Торец заглушен, внутри отражение
Второй торец — видно зеркало с углом Брюстера
Если поймать отражение, то сложится впечатление, что зеркало светится
Минусовой контакт для подключения источника находится именно с этой стороны
Трубку требуется установить на специальные крепления
Пример расположения трубки в задней части станка. Хорошо видно линзу под углом в 45 градусов.
Еще фото. Специальный крепеж можно заменить на хомуты из магазина сантехники.
Для питания трубки нужен ВВ источник
Достаточно увесистый.
Пришел в отдельной упаковке, даже отделной посылкой, несмотря на то, что ордер был один.
Весь проложен надутым материалом
Достаем картонную упаковку
Внутри большой металлический источник, похожий на компьютерные блоки питания. Но сходство только внешнее
Размеры сравнимы с компьютерным источником питания. Корпус оклеен защитной пленкой
Вид со стороны подключения.
Присутствует переключатель 110/220В
Вскрываем, внутри плата преобразователя, суть которой сходна с преобразователем строчной развертки ЭЛТ телевизора.
Установлены 2 шт TL494CN, остальное мелочевка. Реализована схема повышения на умножителе и повышающем трансформаторе.
Внешний вид платы
ВВ трансформатор (строчник)
ВВ провод для подключения. Характеристики: 22AWG, выдерживает 40kVDC, то есть до 40кВ напряжения постоянного тока. Присутствует двойная изоляция. Наружний диаметр 4,5мм.
маркировка
зачищен
ВВ разъем. Пришел вместе и другими запчастями, в простом пакете.
Комплект разъема представляет собой две половинки, два штырька, уплотнения. Соединение под винт.
Вот примерно как собирается вместе
Начинаем собирать разъем
При заказе обратите внимание, бывает кабельный, бывает блочный
Удобно для контроля тока подключить в разрыв минусовой цепи амперметр
Зеркала и линзы. Бывают отражающие, бывают фокусирующие
Нужно 3 отражающих и одно фокусирующее, лучше брать с запасом.
Линзы пришли в огромной коробке, проложенные мягким материалом внутри
убираем надутую пленку и достаем коробки
Внутри коробки одна или несколько зеркал в обертке
Упакованы в коробку
Зеркала и линзы небольшие
Также хорошо отражают свет
Виды линз и зеркал
Устанавливается в специальную фокусирующую трубку
При выборе нужно определиться с фокусом зеркал
Фокус у линзы фиксированный, бывает 1.5”, 2”, 2.5, 3” в зависимости от станка и толщины материала. Самый распространенный вариант это 2”.
Комплект держателей
Пример установки зеркал на оси
Фокусирующая трубка
К сожалению из-за специфики оборудования, я не могу пока предложить полный тест-драйв лазерной трубки. Вот хорошее видео с Ютуб.
Еще один тест:
Видео работы лазера по бальсе (моделисты меня поймут)
Работа по фанере
Дополнительная информация — еще видео
ПО lasercut и работа по акрилу
youtube.com/embed/AVvdFadshS8?autoplay=0&hl=ru_RU&rel=0″ frameborder=»0″ allowfullscreen=»»>Еще хорошее видео
Немного информации:
Магазин с запчастями для лазерного оборудования Tenen laser store
Как я покупал лазер — отзыв на гииктаймс
Отзыв владельца лазера
Пример самодельного лазера и общая информация
Как создать свой лазер 55Вт
Ссылки на основные компоненты:
Трубка СО2
источник высокого напряжения для трубки
Зеркала
Фокусировочная линза
ВВ кабель
ВВ разъемы
Насос
датчик протока воды
Комплект держателей
Можно вообще найти готовые комплекты для сборки станка. Как говорится, просто добавь воды профиль.
Пока все, чуть попозже сделаю более подробный обзор комплекта держателей и линз, дальше буду держать в курсе процесса сборки станка. Спасибо!
✅ Юстировка лазерного станка. Настройка зеркал лазера с нуля своими руками
- Простой и быстрый тест на выравнивание
- Принцип выравнивания
- Выравнивание зеркал
- Выравнивание первого зеркала
- От первого зеркала ко второму
- От второго зеркала к третьему
- Выравнивание трубки
- Вертикальное выравнивание
- Заключение
Юстировка – это проверка и наладка оптического тракта лазерного луча. Приведение и настройка механизмов станка в рабочее состояние, обеспечивающее точность и безопасность их действия. Луч выходит из лазерной трубки излучателя, проходит по зеркалам, попадает на фокусирующую линзу, передает его через сопло на материал. Юстировка необходима для того, чтобы лазерная головка при движении имела одинаковую силу луча. Чтобы луч точно приходил на третье звено и в фокусирующую точку линзы, необходимо его постоянно регулировать.
Оптический тракт состоит из трех составляющих:
- Излучатель – стеклянная трубка СО2, из выходного отверстия которой выходит луч.
- Лазер оказывается на 1 зеркале и переходит на 2.
- 2 зеркало прикреплено к порталу и передвигается с ним вдоль оси y.
В станках для лазерной маркировки применяется конфигурация с парящей оптикой. В задней части станка трубка неподвижна, луч направлен на режущую головку с помощью нескольких зеркал. Через некоторое время эксплуатации они сдвигаются. Это способствует потере производительности и смене цвета. Цвет может стать черным, а рез слишком толстым.
В нашей статье описаны действия необходимые для юстировки станка и обеспечения высокого уровня производительности работы и мощности резки. При первой попытке это может оказаться довольно трудной задачей, поэтому мы рекомендуем ознакомиться с данной процедурой заранее во избежание ошибок при работе с лазерным станком.
Рис. 1. Юстировка лазерного станка
Юстировку можно рассмотреть как четыре отдельные процедуры:
- Проверка выравнивания: Выяснение того, нужно ли выравнивать лазер или нет;
- Выравнивание зеркал: Убедиться, что они расположены под правильным углом;
- Выравнивание трубки: Убедиться, что луч направляется в зеркала правильно;
- Вертикальное выравнивание: Проверить, что срезы находятся перпендикулярно материалу.
Если вы заметили, что ваш лазерный станок теряет мощность или неправильно режет в одном определенном углу рабочего стола, возможно, станок сместился в сторону от центровки. Этот простой тест можно использовать для проверки выравнивания станка. Для проведения этого теста лазерный резак, система охлаждения (чиллер), насосы и вентиляторы должны быть включены.
Оторвите небольшую полоску малярного скотча и сложите ее 2-3 раза, чтобы не было видно липкой стороны. Оторвите еще одну полоску и вставьте сложенную ватку в ее середину. Так вы получите точку, в которую можно целиться лазерным лучом. Сложенный скотч достаточно толстый, а середина не липкая, поэтому его можно наклеивать не оставляя следов.
Рис. 2. Полоска малярного скотча для создания мишени
Закройте крышку лазерного резака, подведите лазерную головку к правому верхнему углу и нажмите тестовую кнопку.
Если удерживать кнопку слишком долго, можно поджечь скотч. Если вы чувствуете, что мишень слишком сильно обгорает от тестовых точек, вы можете просто наложить сверху еще один слой. Продолжайте наращивать слои скотча по мере необходимости. Подведите лазерную головку к переднему правому углу рабочего стола и создайте еще одну контрольную точку на целевой мишени. Повторите это для переднего левого и заднего левого углов рабочей зоны, а затем верните головку в правый верхний угол, чтобы вы могли видеть полученные метки.
Рис. 3. Создание контрольной точки на целевой мишени
Очень важно, чтобы эти четыре точки находились на мишени в одном и том же месте. Если точка находится в том же положении, но не в центре скотча, это означает, что зеркала расположены правильно, а для лазерной трубки необходимо выравнивание.
Рис. 4. Создание еще одной контрольной точки на целевой мишени
Точность — это попадание в намеченную цель (мишень). В случае выравнивания зеркала лазера точность означает попадание в центровую точку.
Рис. 5. Точность попадания лазерного луча в центр зеркала
Для зеркал 1 и 2 точность (попадание точки в одно и то же место на зеркале каждый раз) гораздо важнее точности (попадание точки в центр зеркала). Попадание точки в одно и то же место показывает, что лазерный луч параллелен оси в том направлении, в котором он движется. Однако для третьего зеркала нам нужны и точность, и аккуратность, поскольку лазерный луч должен пройти через фокусирующую линзу и сопло лазерной головки.
Перед началом юстировки, нужно снять боковой кожух, крышку, кожух заднего отсека с трубкой.
Попытка отрегулировать только одно зеркало может лишь усугубить ситуацию, так как настройка должна быть последовательной от первого этапа до последнего.
Все три зеркала CO2 станка очень похожи и юстировка происходит одинаково. Они удерживаются в центре крепления с помощью небольшого стопорного кольца. В разных углах крепления находятся 3 регулировочных болта, они имеют стопорные узлы, которые должны плотно прилегать к раме, это предотвращает самостоятельное вращение болтов при движении резака.
Есть 2 длинных болта с пружинами на них, они удерживают зеркало плотно к ручкам регулировки. От регулировки угла наклона зависит положение луча. Малярный скотч с мишенью находящийся перед следующем зеркалом, покажет тестовую точку в другом месте после настройки его положения.
Рис. 6. Регулировка угла наклона
Регулировку следует производить так, чтобы положение мишени было на максимально далеком расстоянии, так как маленькие отклонения в зеркале увеличиваются на расстоянии, и выравнивание будет более точным.
Рис.7. Регулировка положения мишени
Есть и другой способ регулировки. Если вы повернете обе нижние ручки на пол-оборота влево, вы заметите, что тестовая точка опустилась на несколько мм. Вы должны убедиться, что повернули обе ручки на одинаковую величину, иначе луч будет смещаться влево или вправо одновременно.
Рис. 8. Настройка ручек
Знание того, на сколько поворачивать каждую ручку, является ключом к точному выравниванию лазера и чем чаще вы будете это делать, тем легче будет процесс юстировки. Если точка не передвинулась достаточно далеко или движется в неправильном направлении, вы можете просто попробовать еще раз. Не забывайте продолжать добавлять скотч, если целевая точка выглядит сожженной.
Подойдите к лазеру и сделайте следующее:
- Установите портал на полпути между передней и задней частями станка;
- Подведите режущую головку к крайней правой стороне;
- Поместите кусок ленты для мишени над отверстием перед зеркалом 3;
- Выстрелите одной пробной точкой в ленту и сделайте отметку, чтобы знать, где начался луч;
- Поверните верхнюю ручку регулировки зеркала 2 на пол-оборота вправо и посмотрите, где появится новая точка.
- Медленно поворачивайте ручку обратно, пока точка снова не окажется в том же положении.
Рис. 9. Отработка регулировки на зеркалах 2 и 3
На зеркалах 2 и 3 удобно отрабатывать регулировки, так как они оба легко доступны в передней части станка.
Луч может не попадать в центральную точку, но достаточно того, чтобы он проходил 1 и 2 зеркало на максимальной мощности. Попасть в центр необходимо только для 3
В лазерном резаке 3 зеркала, выравнивание следует выполнять на каждом по порядку. Любые выполненные регулировки повлияют на все зеркала, которые находятся дальше по пути лазера, поэтому изменения, сделанные на 1, повлияют на 2 и 3.
Проверяется попадание луча в одну точку в двух крайних положениях перемещения портала по оси Y. Действие осуществляется несколько раз, чтобы убедиться, что зеркало выставлено точно и луч остается на месте.
Проверить зеркало 1 очень просто: сложите скотч с мишенью и наклейте ее перед ним. На ленте должна появиться точка примерно посередине зеркала 1. Точка должна быть овальной формы, которая образуется, когда круглый луч попадает на зеркало под углом.
Этот тест часто можно провести, не обходя лазер сзади, можно просто протянуть руку назад и приложить скотч к зеркалу.
Если точка не попадает на середину, возможно, потребуется регулировка высоты лазерной трубки, о которой мы расскажем далее. Если точка находится в пределах 10 мм от середины, вы можете выровнять зеркала без регулировки трубки.
На максимальной мощности след от луча не должен выходить за границы рамки
Рис. 10. Проверки первого зеркала
Зеркало 2 закреплено на левой стороне станка и перемещается только вперед и назад. Сверните скотч с мишенью и прикрепите ее перед зеркалом 2. Подведите лазерную головку к задней части машины и нажмите кнопку, чтобы получить точку на мишени, запишите, где находится эта точка.
Подведите лазерную головку к передней части машины и поставьте вторую точку. При выравнивании станка обе точки должны находиться в одинаковом положении. Зеркало можно отрегулировать с передней части станка, но если вы не уверены, проще стоять за станком и смотреть вперед.
Рис. 11. Луч, отраженный от зеркала 1, будет падать на зеркало 2, если зеркало 1 повернуть вокруг осей x и y на углы θ и ψ соответственно. Оба угла влияют на каждую координату (x2 , y2 , z2 ) центра зеркала 2. Вращение зеркала 1 вокруг оси x ограничено диапазоном перемещения регулятора угла наклона крепления, что ограничивает возможности положения и высоты зеркала 2.
Настройте зеркало 1 так, чтобы точка находилась в одном и том же месте спереди и сзади. Не имеет значения, если эта точка не находится точно посередине зеркала 2. Не забывайте добавлять слои скотча, если мишень начинает гореть.
Рис. 11. Проверка и настройка второго зеркала
Зеркало 2 — 3 — это почти то же самое, что и зеркало 1 — 2, просто доступ к нему немного проще. Сверните немного скотча для мишени и прикрепите ее над отверстием перед зеркалом 3. Установив портал посередине лазера, отведите лазерную головку до упора в левую часть машины и нажмите кнопку, чтобы на ленте появилась точка, запомните, где она находится. На скотче останется отпечаток сопла и след от луча. При верной центровки на материале останется круглая точка от луча.
Рис. 12. Проверка и настройка луча от второго к третьему зеркалу
Если после выравнивания точка не находится в центре зеркала 3, вы можете произвести окончательную настройку, изменив способ, которым трубка направляет луч на зеркало 1. Лазерная трубка поддерживается двумя монтажными кронштейнами, эти кронштейны полностью регулируемые и могут использоваться для регулировки трубки.
Рис.13. Выравнивание трубки
В боковой части каждого кронштейна трубки есть 2 винта, при ослаблении которых кронштейн может перемещаться вверх и вниз, а также влево и вправо. Поднятие кронштейна в задней части трубки заставит лазерный луч опуститься вниз. Перемещение заднего кронштейна влево приведет к перемещению тестовой точки вправо.
Чтобы выровнять лазер по центру зеркала 3, положите кусок скотча с мишенью перед 3 и подведите головку к переднему правому углу. Это положение наиболее удалено от трубки, поэтому любые движения будут усиливаться на этом расстоянии. Отрегулируйте угол трубки так, чтобы тестовая точка находилась прямо в центре отверстия. Вы можете фактически игнорировать зеркала 1 и 2, если точка должна быть ниже на ленте мишени, поднимите заднюю часть трубки в 1.
Рис.14. Выравнивание трубки лазерного станка
На последнем этапе нужно проверить положение луча. Луч должен находиться перпендикулярно материалу, это позволит получить хороший вертикальный срез. Процесс очень похож на юстировку других частей, только в этот раз вместо скотча с мишенью нужно нанести точки на обрезки материала.
Рис. 15. Создание тестовой точки для регулировки станка
Принцип настройки остается прежним, изменяется лишь направление луча: из горизонтальной плоскости в вертикальную
Для установки лазера на необходимый уровень над материалом, примените инструмент для установки высоты. Далее нужно запустить лазер и создать точку на поверхности, близкую к тестовой, по которой будет выравниваться станок. Красная точка должна быть направлена на эту единственную тестовую точку, вручную отрегулируйте красную точку, пока она не будет направлена на точку резки.
Вертикальное выравнивание может быть немного сложным. Можно настроить луч так, что он ударится о конус воздушного помощника, не дойдя до материала. При полной потере лазерного луча необходимо снять конус, чтобы проследить его направление. При неудачной настройке вы можете все вернуть в прежнее положение. Для этого необходимо повернуть ручку регулировки в обратном направлении.
Рис. 16. Вертикальное выравнивание
При верном выполнении всех действий у вас будет полностью настроенный и выровненный лазерный резчик. Данные станки очень хорошо сохраняют свою центровку, но ее необходимо проверять через каждые 40 часов работы и проводить юстировку.
10 полезных советов по работе на лазерном гравере по дереву и фанере.
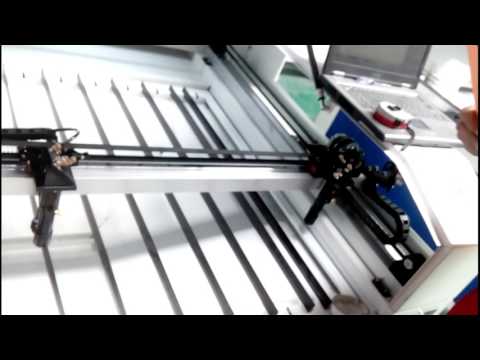
Всем привет, Друзья! С Вами 3DTool!
Станок лазерной резки СО2. 10 полезных советов для новичков по резке и гравировке фанеры и дерева.
Предисловие. Для части советов важно понимать разницу между векторными файлами и растровыми файлами. Векторные файлы представляют собой математические формулы, которые описывают линии, круги и т.д. Они создаются в таких программах, как Adobe Illustrator, Inkscape, AutoCAD и Corel. Растровые файлы представляют собой наборы отдельных пикселей, например цифровые фотографии, файлы Adobe Photoshop, JPG и т. Д. Вырезать на лазере вы можете только векторные файлы, а гравировать – оба вида. Для некоторых советов, перечисленных ниже нужно, чтобы ваш файл был векторным.
Каталог лазерных станков с ЧПУ
Совет №1. Подготовка к лазерной резке или гравировке.
Прежде чем мы перейдем к советам по резке и гравировке, давайте начнем с полезных советов по подготовке к ним:
Защита от дыма/нагара: если вы собираетесь гравировать что-либо, помните, что дым/нагар от гравировки может испачкать края гравируемой поверхности. Что бы этого избежать, наклейте на поверхность малярный скотч. Он не сильно повлияет на мощность лазера (можно немного увеличить мощность, если считаете, что это необходимо), но защитит материал вокруг гравируемой зоны от следов дыма. После нанесения гравировки просто снимите скотч.
Предварительные настройки: Лазерный станок, который вы используете, наверняка имеет рекомендуемые настройки для резки или гравировки различных материалов и различной толщины. Вы можете загрузить эти настройки в свой компьютер или непосредственно плату управления станком лазерной резки и сохранить их в качестве предустановок. Обязательно назовите их как-нибудь осмысленно, чтобы в будущем их можно было легко идентифицировать. Таким образом, когда вы в следующий раз будете гравировать на коже или резать акрил толщиной 3 мм, вы можете просто найти и использовать предустановку для работы с данным материалом.
Тестовая резка заготовки: даже если у вас имеется предустановка для разреза материала, рекомендуется выполнить тестовый разрез прежде, чем запустить на выполнение основное задание. Нет ничего хуже, чем вынуть лист материала фанеры после реза лазером и обнаружить, что он не разрезал всё задуманное до конца. Рекомендуем создать маленький круг или квадрат (около 6 или 10 мм в ширину) и вырезать его в углу заготовки. Таким образом можно увидеть, нужно ли увеличивать или уменьшать мощность, прежде чем запустить базовое задание.
Совет №2: Важность слоев в графических редакторах
Некоторые советы, о которых пойдет речь ниже, требуют возможности гравировать/резать только часть файла или дизайна за один раз. Самый простой способ сделать это — поместить разные части вашего дизайна на разные слои одного файла. Большинство графических программ позволяют создавать слои, а затем включать и выключать их. Хотя вы, конечно, можете поместить все на один слой, разделение на несколько слоев дает вам несколько ключевых преимуществ:
1. Контроль очередности резов. У вашего лазерного станка скорее всего есть несколько вариантов управления порядком, в котором происходит рез, но удобнее всего контролировать очередность одним единственным способом: задать разные линии реза на отдельных слоях, чтобы включать и выключать каждый слой в нужном порядке.
2. Несколько слоев в одном файле. Вместо того, чтобы каждый дизайн или часть дизайна сохранять в отдельном файле, просто поместите их все в один файл и разбейте на отдельные слои. Затем просто запускайте нужные слои.
3. Создание подсказок и мишеней. Возможно, вы создали несколько подсказок для разметки вашего дизайна, или мишень для размещения нескольких одинаковых объектов. Чтобы их не вырезало на основном дизайне, поместите их на отдельный слой и просто отключите его.
Совет № 3: Приемы лазерной резки и гравировки по дереву.
Допустим, вы разработали логотип или изображение и хотите вырезать его на заготовке из цельного дерева. Дерево — отличный материал для гравировки, но нужно понимать разницу между гравировкой на цельном куске дерева и композитным материалом, таким как фанера или МДФ. В отличие от изготовленного материала, натуральное дерево не является однородным. Волокна в древесине представляют различные этапы роста в (зимой и летом), и каждое из них будет выжигаться по-разному. Обычно темные волокна тверже, а светлые части между ними мягче. Как видно из примера фотографии выше, на гравировке вы видите зебру. Если вам важен однородный вид гравировки, лучше всего взять хорошую фанеру, где верхний слой более предсказуем.
Еще одна вещь, о которой следует помнить, это материалы с тонким шпоном хорошей древесины сверху. Гравировка часто прожигает тонкий шпон, обнажая то, что находится под ним. Удостоверьтесь, что древесина, которая находится под шпоном, выглядит хорошо, и что вы выжигаете весь шпон, чтобы у вас не было смеси шпона и поверхности под ним.
Совет № 4: Лазерная резка перекрывающихся обектов.
Часто, когда нужно вырезать несколько частей одновременно, велико искушение поместить их рядом друг с другом, что бы соседние одинаковые линии перекрывались друг другом для экономии листа материала. Это хорошая идея, но можно ее очень легко испортить.
Например у вас заготовлено куча квадратов для резки. Если вы нарисуете два квадрата (по четыре стороны каждый), а затем прижмете их друг к другу, визуально будет только одна линия между ними. Проблема в том, что, хотя для вас это выглядит это как одна сплошная линия, компьютер все равно видит две. Конечным результатом является то, что линии будут обрезаны одна по другой. Это приведет к тому, что данный край, скорее всего будет выжженым, а не чистым. Так же потратится время на ненужный рез.
Способ исправить это — убрать одну из удвоенных линий. Нарисуйте один из квадратов 3-х сторонним, убрав одну боковую линию напротив первого квадрата и совместите их.
Совет № 5: Разница лазерной гравировки растрового изображения и векторного.
Основное различие между растровой гравировкой и векторной состоит в том, что для гравировки лазер перемещается слева направо по области гравировки, а затем перемещается вниз на минимальный шаг, повторяя до тех пор, пока не выгравирует изображение. С векторным резом лазер просто движется вдоль линий. В результате растровая гравировка занимает намного больше времени, чем векторный рез.
Итак, у вас есть рисунок. Например, кельтский узел, который представляет собой, в основном, просто линии. Конечно, вы можете запустить его как растровую гравировку. Преимущество состоит в том, что вы можете установить толщину линий какую хотите, и разные линии будут иметь разную толщину. Недостаток в том, что гравировка займет гораздо больше времени.
Если же файл векторный, есть быстрый способ создания линий без их разреза. Запустите ваш файл как векторную резку, но выключите питание и увеличьте скорость. Например, чтобы прорезать 3мм фанеру, мы ставим мощность лазера на 100% и скорость на 20%, но, чтобы на ней же нарисовать линию, уменьшаем мощность до 30% и скорость на 95%. Пытаясь прорезать материал, лазер просто выжигает на нем тонкую линию. Преимущество в том, что так будет намного быстрее, чем векторная гравировка. Недостатком является то, что линия будет очень тонкой, и вы не сможете изменить ее толщину.
Совет № 6: Расфокусировка лазерного луча для получения более толстых векторных линий.
В последнем совете мы рассмотрели, как использовать векторное изображение, чтобы просто делать линии на материале для создания штриховых рисунков или дизайнов. Но недостатком этого метода является то, что линия очень тонкая. Но есть способ получить более толстые линии. Лазерный луч имеет очень узкую точку фокусировки, поэтому, если немного опустить материал ниже, лазер потеряет фокус и рассеется. Положите небольшой кусок дерева толщиной около 9,5 мм на материал, который вы используете, и сфокусируйте лазер на этом куске. Затем запускайте лазер на векторной настройке (с меньшей мощностью и более высокой скоростью). В результате получается гораздо более толстая линия, чем если бы лазер был правильно сфокусирован.
Есть 2 недостатка этого способа, о которых нужно знать при использовании этой техники работы. Один из них — линия немного неточная и не такая четкая, как при растровой гравировке. Во-вторых, в углах линий лазер делает небольшую паузу, так как меняет направление, поэтому углы прогорают немного глубже. Углы выглядят так, будто в них есть маленькие точки.
Совет № 7: Добавление векторной обводки к краю шрифта или гравируемого изображения
Обычно у вас должны получаться хорошие края на любой гравировке, которую делает ваш лазер (если вы не проверяете фокусировку). Но если вы хотите придать краям гравировки немного большую резкость, вот хороший совет: добавьте легкую векторную обводку по краю гравируемого изображения.
Вам понадобится изображение в виде векторного файла. Выберите его и добавьте тонкий штрих (обводку) по краям. Когда вы настраиваете лазер для обводки, уменьшите питание лазера и увеличьте скорость, чтобы он выжигал, но не прорезал края. После того, как лазер выполнит основную гравировку, он вернется и обожжет тонкую линию вокруг самого края.
Этот эффект отлично подходит для разного рода надписей.
Каталог настольных лазерных станков — https://3dtool.ru/category/chpu/lazernye-stanki/lazernyy-graver/
Совет № 8: Лазерная резка дерева в целевой области.
Иногда вам нужно точно попасть в целевую область, которая не лежит в начальных координатах лазера. Например, имеется кусок пластика, из которого вы уже вырезали несколько фигур, но между старыми вырезами достаточно места, чтобы сделать другой, новый вырез. Как вы можете аккуратно вставить новый рез в оставшееся пространство?
Сначала измерьте целевую область и получите ее приблизительные размеры. Убедитесь, что есть достаточно места для того, что вы хотите вырезать. Затем разместите заготовку на сотовом столе лазерного станка и измерьте расстояние от нулевых координат лазера до целевой области. Например, прямоугольник 2.5см на 5 см, расположенный на 6см ниже и на 2см левее от края. Затем в вашем файле используйте разметку, чтобы выделить целевую область и положение от начала координат на материале. Поместите свой рисунок или рез в целевой области. Убедитесь, что данная разметка не будет использоваться при резке. Если вы все правильно измерили, ваш вырез должен находится прямо в целевой области.
Совет № 9: Одновременная лазерная гравировка многих объектов и использование шаблонов.
Допустим, у вас есть много деревянных подставок, на которых вы хотите выгравировать логотип. Вы можете помещать их по одному в начальных координатах лазера и гравировать один за другим. Но разве не было бы лучше расположить несколько штук одновременно и сделать так, чтобы станок лазерной резки выгравировал изображение на всех заготовках одновременно ?
Хитрость заключается в том, что нужно создать сетку, на которую можно выложить заготовки, и точно нанести на них лазерную гравировку. Создайте новый векторный файл размером с вашу рабочую зону лазера. Затем измерьте ваше изображение которые будет тиражировать на заготовках. Если вы можете получить его точную форму — это отличный вариант, но если это не возможно, то подойдет обычный круг или квадрат, главное, что бы края изображения точно входили в область квадрата или круга. Это будет вашей целевой формой. Создайте шаблон и поместите ваш рисунок (гравировку или вырез) в данную область. Теперь скопируйте шаблон и ваш рисунок и вставьте столько копий, сколько вы можете уместить в пространстве рабочей зоны лазера.
Совет: Оставьте немного места между шаблонами, чтобы заготовки не лежали плотно друг к другу.
Прежде чем запускать файл, не забудьте переместить сетку и шаблон на один слой, а свое изображение на другой слой. Затем отключить печать для слоя с вашим дизайном на нем.
Отрежьте кусок картона/фанеры под размер рабочей зоны лазера и поместите его в лазер. Теперь убедитесь, что только слой с шаблоном установлен для резки. Выгравируйте шаблон на картоне. Получится сетка, которая соответствует той, что в файле. Теперь поместите предметы, которые вы собираетесь выгравировать на шаблон, отмеченную на картоне. Не забудьте перефокусировать лазер на верхнюю часть того, что вы собираетесь гравировать. Теперь вы можете отключить печать слоя с мишенями и включить печать слоя непосредственно с дизайном.
Пока вы не двигаете картон/фанеру, вы можете просто продолжать раскладывать на неё новые детали, нажимать на гравировку и повторять, пока не сделаете все свои заготовки.
Каталог станков лазерной резки больших размеров: https://3dtool.ru/category/chpu/lazernye-stanki/lazernyy-gravirovalnyy-stanok/
Совет № 10: Использование лазерной точки для моделирования выполнения задания без реза.
На некоторых лазерных станках имеется возможность включить лазерную указку, которая проецирует красную точку, указывающую, где будет работать лазерный луч. Это полезно для определения того, где лазер будет резать, прежде чем выполнять работу на самом материале. Просто отключите питание лазера и включите красную точку. Затем запустите файл и посмотрите, как двигается красная точка, как будто выполняем задание в холостом режиме.
Следует помнить одну вещь: данный метод хорошо работает с векторными линиями, где лазер / красная точка следует по линиям, но не так хорошо с гравировками, когда лазер проходит вперед-назад по всей области гравировки. Если нужно использовать красную точку, чтобы выяснить, где заканчивается гравировка, можно нарисовать квадрат или круг вокруг гравируемого изображения, а затем просто с помощью красной точки в векторном режиме обвести данный квадрат. Либо, можно нарисовать горизонтальную и вертикальную линии из центра, как на рисунке выше.
Что ж, а на этом у нас все! Надеемся эта статья была для Вас полезна!
Связаться с нами вы можете любым удобным для Вас способом:
• По электронной почте: [email protected]
• По телефону: 8(800)775-86-69
• Или на нашем сайте: http://3dtool.ru
Так же, не забывайте подписываться на наш YouTube канал:
Подписывайтесь на наши группы в соц.сетях:
ВКонтакте
Лазерный мир Джаррода: первый углекислотный лазер
Лазер CO2 является одним из самых мощных лазеров непрерывного действия. В качестве мощного источника непрерывной энергии CO2-лазер используется во многих
промышленные применения, связанные с обработкой материалов. Лазер CO2 производит луч невидимой энергии с уникальными свойствами. В отличие от лазерных источников, излучающих видимый или ближний инфракрасный луч,
когерентный выходной сигнал CO2-лазера близок к диапазону длин волн, которые производятся человеческим телом термически. Мало того, что эта длина волны совершенно невидима для
человеческому глазу и обычным камерам, но он также полностью блокируется большинством распространенных материалов, прозрачных для видимого и ближнего инфракрасного диапазона.
длины волн. Например, стекло непроницаемо для луча CO2-лазера. По этой причине CO2-лазер можно использовать для сверления, плавления или резки стекла; приложение
это было бы неэффективно при использовании видимого или ближнего ИК-диапазона.
На этой веб-странице демонстрируется самодельный лазер, созданный с нуля на основе электрического разряда в смеси гелия, азота и углекислого газа.
Создание моего первого удачного CO2-лазера началось после того, как кто-то дал мне запасную стеклянную трубку. Вскоре после этого кто-то пожертвовал оптику из ZnSe. Именно в это время я стал действительно серьезным о создании работающего СО2-лазера.
Я ознакомился с планами Scientific American и Information Unlimited для этого типа лазера, но лучший ресурс для индивидуальных Опыт работы с этим устройством можно найти в разделе Sam’s Laser Faq, посвященном самодельным CO2-лазерам, на странице http://www.repairfaq.org/sam/lasercc2.htm#cc2toc.
Я не следовал четким планам по созданию этого лазера. Размеры в основном произвольные, исходя из доступных деталей.
Строитель может просматривать различные планы и онлайн-источники информации, а затем может прийти к общему представлению о диапазоне различных типов деталей, которые будут работать.
Например, лазер с высоким коэффициентом усиления, такой как импульсный рубин, можно использовать с зеркалами, которые не предназначены специально для него. С другой стороны, мало
обычные материалы, которые будут передавать длинные волны, создаваемые CO2-лазером. При некотором творчестве и общем понимании устройства, которое
принимая во внимание, строитель может построить лазер, используя материалы, которые легче всего получить. Лучше понять достаточно основных принципов, чтобы
включить гибкость, когда это необходимо. Это может сэкономить время и деньги!
Мой лазер начался с 4-футовой секции неоновой вывески. Трубка имеет внутренний диаметр около 1 см. Для водяной рубашки я использовал секцию люминесцентной лампы.
защитная трубка, которая представляет собой гибкую прозрачную пластиковую трубку, продаваемую для размещения вокруг флуоресцентных ламп цилиндрической формы, чтобы защитить их от случайного
влияние. Я не рекомендую использовать эту трубку для чего-либо, кроме короткой лазерной трубки: причина в том, что она изгибается и прогибается при протекании воды.
Это. Идеальным было бы стекло, но независимо от типа трубок, используемых для охлаждающей рубашки, детали конструкции, приведенные ниже, все равно должны быть соблюдены. применимый.
Я начал с создания слоя малярной ленты вокруг внешней стороны трубки неоновой вывески. Эта лента располагается на произвольно равном расстоянии от обоих концов стеклянная трубка. Расстояние между двумя рулонами ленты будет определять площадь, через которую протекает водяной хладагент. Я постепенно наращивал слои ленты пока они не совпадут с внутренним диаметром пластиковой рубашки охлаждения. После того, как этот шаг был завершен, я начал наносить тонкий слой эпоксидной смолы JB вдоль сторон сварного шва. ленточные цилиндры (см. ниже).
Ленточный «метод» возник не у меня. Этот подход предлагается в планах CO2-лазеров от Information Unlimited. Однако я обнаружил, что
Ленточный метод будет адаптироваться к множеству обстоятельств. Это может быть полезно во всем, что включает в себя центрирование одного цилиндра вокруг внешней стороны второго меньшего размера.
цилиндр. Его можно использовать для соединения частей, которые в противном случае были бы несовместимы. Хотя это и не идеально, я использовал его, чтобы подогнать крошечный выходной вал небольшого двигателя постоянного тока к относительно большому отверстию в
центр компакт-диска, при создании
небольшой электростатический генератор с приводом от двигателя. Таким образом, это может быть надежным методом, обеспечивающим гибкость, когда доступно ограниченное количество деталей и где
ограниченные инструменты и средства доступны для лучших альтернатив.
Хотя метод ленты не является моей собственной идеей, это была моя идея использовать малярную ленту для этой цели. В отличие от некоторых других распространенных типов лент, маскировочная
лента дешевая, и она равномерно совмещается при накатывании на
поверхность цилиндрической формы. После завершения рулон малярной ленты можно покрыть эпоксидной смолой и герметиком, чтобы обеспечить прочность и защиту. я покрыл
всю мою ленту скрутил с JB сваркой, а потом заклеил снаружи шеллаком. Смотрите фотографии ниже для примера. Как вы, наверное, заметили
на предыдущей фотографии на кончике стеклянной трубки имеется отдельная обмотка изолентой. Хотя упоминать об этом немного преждевременно, в конечном итоге это послужит
в качестве прокладки для соединения внешней части стеклянной трубки с внутренней частью медной трубки, которая будет служить одним из двух электродов разрядной трубки.
Пока игнорируйте этот шаг. Мне просто необходимо было упомянуть об этом, чтобы избежать возможной путаницы.
Когда эпоксидная смола и шеллак высохли, я надел прозрачную пластиковую трубку на рулон ленты. Имейте в виду, что на противоположном конце был такой же рулон ленты.
стеклянной трубки, а большая пластиковая трубка была обрезана по длине, чтобы соответствовать расстоянию между внешним краем одного рулона ленты и внешним краем
другой. После того, как трубка была надвинута на место, я отметил два места на внешней стороне пластиковой трубки маркером Sharpie, на небольшом расстоянии от внутренней части.
края обоих рулонов ленты. Две точки были отмечены на расстоянии 180 градусов друг от друга, как определено по внешней окружности пластиковой трубки (оценка
на глаз). Небольшие отверстия были просверлены в местах, обозначенных этими точками Sharpie, и два 1/4-дюймовых заусенца для шланга были закреплены над отверстиями с помощью сварки JB.
эпоксидная смола.
После установки водяной рубашки проверьте ее на отсутствие утечек! Это очень важно. Вода и высокое напряжение явно несовместимы! я купил небольшой водяной насос из местного хозяйственного магазина. Эти насосы используются для непрерывной циркуляции воды для небольших фонтанов: небольшие декоративные используется на заднем дворе или в небольших крытых водопадах. Используйте насос для циркуляции воды через охлаждающую рубашку. Таким образом, вы можете обнаружить любые утечки, которые появляются, и при необходимости закрепите их дополнительным сварным швом JB. Как только все утечки будут устранены, а трубка тщательно протестирована без дополнительных утечек, вы готовы к следующему шагу.
Следующим важным шагом является изготовление концевых электродов. В моем первом таком устройстве использовались 2 нейлоновые шайбы, резиновая втулка, отрезок медной трубы с внутренним диаметром 1/2 дюйма и
несколько медных трубок.
Здесь у вас будет возможность извлечь выгоду из одной из моих ошибок. Нейлоновые шайбы были самыми большими шайбами, которые я мог найти в то время. были построены оригинальные наконечники. Я думал, что, сложив их попарно, я смогу обеспечить достаточную прочность, чтобы выдержать требуемую приложенную силу. во время выравнивания. Я был неправ! Поэтому, игнорируя тот факт, что эти наконечники изготовлены из нейлона, посмотрите на следующую картинку, чтобы получить представление о том, как устроены наконечники. построен.
Помимо выбора нейлоновых шайб, на этих двух рисунках есть еще одна деталь, которая не является необходимой. Это блестящая круглая металлическая деталь посередине
первое фото, а блестящая металлическая часть, выступающая справа от нейлоновых шайб, на втором фото. Это часть оригинального дизайна, который я
решил не использовать, и пока это неактуально. Тем не менее, 3 болта очень важны. Через все шайбы нужно будет просверлить по 3 отверстия, а затем
JB-приварите три совместимые гайки (гайки, которые подходят к трем соответствующим болтам) над отверстиями на стороне медной трубы (см. фото выше). Я рекомендую использовать металлические шайбы. Следующие шаги этого руководства будут
показать металлические шайбы, на которые я в конце концов перешел, когда понял, что нейлон слишком гибкий. А пока посмотрите фото
выше в качестве примера, зная, что в конечном устройстве (если вы его конструируете) нужно будет использовать металлические шайбы вместо нейлона.
С одной стороны медной трубы с внутренним диаметром 1/2 дюйма я просверлил отверстие и припаял короткий отрезок медной трубки с внешним диаметром 1/4 дюйма. Это станет колючкой для шланга. На самом деле
настоящая заусенец для шланга сработала бы здесь. Однако я решил использовать медную трубку, потому что она была доступна в то время и подходила для пайки. JB Weld, вероятно, подойдет здесь, но сначала обязательно отшлифуйте и тщательно очистите все детали, на которые будет наноситься JB Weld. Свисающие шланги, которые будут прикреплены к этим
зазубрины шлангов будут оказывать на них некоторую нагрузку из-за их длины, местоположения и неизбежного перемещения. Именно из этих шлангов газ будет подаваться в один конец
лазерной трубки, поскольку давление воздуха будет вытягиваться с противоположного конца вакуумным насосом.
Некоторые детали конструкции наконечника показаны выше. Большая часть моей работы была выполнена с использованием сварки JB, но строитель может предпочесть использовать пайку, пайку или сварку.
при условии, что эти ресурсы и навыки легко доступны. В любом случае, идея состоит в том, чтобы установить металлическую шайбу вокруг короткого отрезка медной трубы.
труба может быть около 3 или 4 дюймов в длину. Вам нужны шайбы достаточного размера, чтобы можно было просверлить отверстия и установить регулировочные болты и винты рядом с
внешний край. При этом нужно, чтобы внутреннее отверстие было как можно ближе к внешнему диаметру медной трубы. Мой подход заключался в
комбинируйте меньшие шайбы с большими, чтобы было легче соединить все вместе. На рисунках ниже показано, как можно комбинировать маленькие шайбы.
с более крупными, чтобы сделать отверстие посередине «меньше», чтобы оно приблизилось к тому, что будет проходить через отверстие.
центр. Посмотрите на эти картинки очень внимательно, но имейте в виду, что они используются только в качестве примера. Диапазон различных размеров может работать. Деминионы
эти детали должны быть доступны в зависимости от наличия и того, насколько легко их можно адаптировать к другим частям (например, к медной трубе), которые вы можете найти.
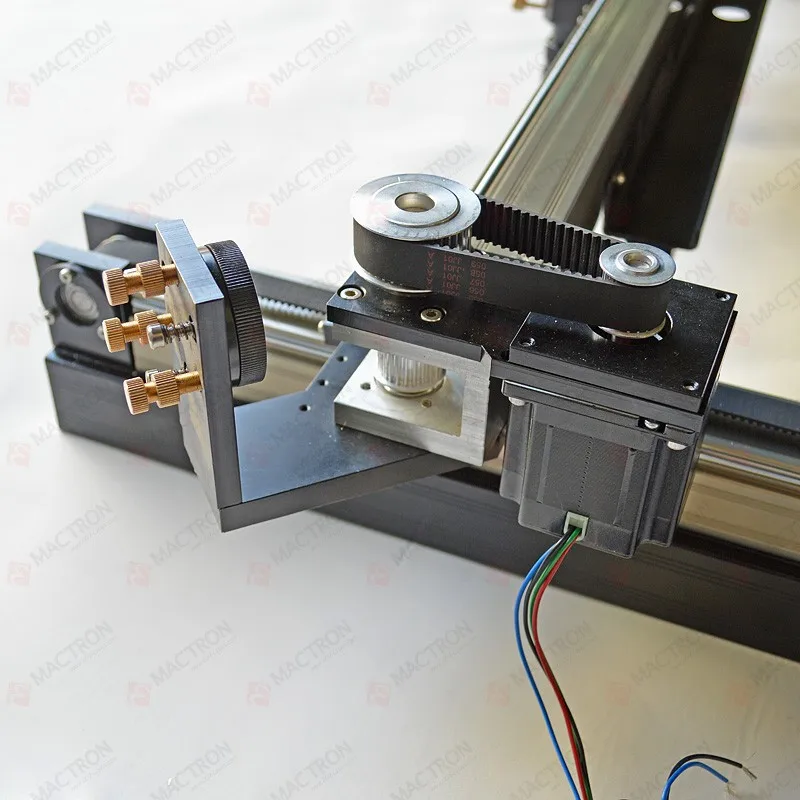
Как вы могли правильно догадаться, описанная выше схема использовалась при построении
еще один лазерный проект. Это очень близко к тому, что вы будете делать (и что я сделал) для
лазер, описанный на этой странице. Наращивание слоев ленты и использование шайб разных размеров в основном делает одну вещь: позволяет использовать большие шайбы, которые действительно являются наиболее важными.
часть креплений зеркал, которые должны быть установлены по индивидуальному заказу и центрированы на электродах и реальных зеркалах резонатора. Стеклянная трубка, которая служит
фактическое отверстие для лазера будет сердцем всей конструкции. Вы должны спроектировать свой лазер вокруг этой стеклянной трубки. Трубка
является наиболее важной частью. Трубка может быть от нескольких миллиметров до 1 дюйма в диаметре. У меня внутренний диаметр от 1 см до 1/2 дюйма. Поэтому после того, как вы сначала приобретете стеклянную трубку, вам нужно будет приобрести электродные «трубы», которые можно будет надеть на концы этой трубки с разумным усилием. Чтобы лучше уточнить,
пожалуйста, обратитесь к изображениям ниже. На этих фотографиях показано, как «трубчатые» электроды были специально установлены на концах стеклянной трубки с креплением к зеркалу (шайбы).
уже на месте.
Как видно из этих фотографий, ленточная прокладка соединяет стекло
трубки к медной трубе. Глядя на охлаждающую рубашку, вы можете сказать
что эти фотографии были сделаны до того, как JB-сварка была нанесена на куртку. Когда я строил этот лазер, я не планировал
сделать сайт. В итоге не стал тщательно фотографировать каждый шаг
в последовательности. Вот почему мне приходится «заимствовать» примеры из других проектов.
чтобы дать полуполную иллюстрацию. Я признаю, что это
не очень хорошо организовано, но в следующий раз я смогу планировать заранее и взять
фотографии каждого шага, как я иду для большей ясности. Я также
допустил некоторые ошибки в конструкции этого первого лазера, и, к сожалению, эти ошибки включены
на фотографиях. Нейлоновые шайбы являются хорошим примером этого.
В результате я должен постоянно переходить от одного изображения реального к другому.
лазер, и фотографии чего-то еще, что иллюстрирует, как это должно быть сделано. Пожалуйста
примите мои извинения.
Лучше всего начинать с газа, над которым у вас меньше всего контроля. Если я смешиваю пищевую соду и уксус, чтобы получить CO2 (что может быть довольно грязным), затем я позволяю реакции быстро произвести газ и заполнить пустой шар. После того, как реакция значительно замедлится, я убираю баллон и основываю все остальное на объеме СО2.
Если единственный способ получить гелий — это принести его домой на воздушном шаре для вечеринок,
тогда вам, очевидно, нужно будет начать с гелия (только убедитесь, что вы не завязываете воздушный шар узлом, поэтому
что у вас все еще есть доступ к открытию воздушного шара — специальный запрос, который вам может понадобиться сделать клоуну
кто надувает). Это соотношение. Независимо от того, с каким газом вы начинаете, вам нужно примерно 10% Co2, 20% N2 и 70% He. Азот можно заменить воздухом — обычно я использую только воздух.
Вы собираетесь измерить окружность воздушного шара, чтобы рассчитать его объем, а затем вы собираетесь основывать свои проценты (каждого газа) от этого объема. Окружность как раз позволяет вам для проведения измерений, а объем — это то, на чем вы основываете свои расчеты.
Если ваш гелий уже находится в воздушном шаре, когда вы его получите, просто рассчитайте все остальное вокруг гелия. Другими словами, газ, с которым вы начинаете, будет определять, сколько двух других газов вам нужно.
Давайте посмотрим на пример. Допустим, вы пришли домой из магазина для вечеринок с воздушным шаром, полным гелия. Измерьте снаружи вашего воздушного шара с помощью измерительной струны (на первом этапе вам потребуется измерить окружность воздушного шара, а затем рассчитайте его объем) — допустим, вы получите 40 см. Прежде чем вы сможете рассчитать объем шара, однако, вы должны найти его радиус.
С=2πr
находя «р», получаем
г = С/2π
r = 40 см/2π = 6,4 см
Теперь, когда у нас есть радиус, мы можем вычислить объем.
V = (4/3)πr 3
= (4/3)(3,14)(6,4 см) 3
= (4,19)262см 3
Объем гелия = 1098см 3
Итак, теперь мы знаем, что в нашем воздушном шаре содержится 1098 кубических сантиметров первого газа — гелия. Мы знаем, что когда три газа смешиваются в воздушном шаре, мы хотим, чтобы гелий составлял 70% от общего количества гелия. этот общий объем. Мы можем найти общий объем, разделив 1098/70%, или 1098/0,7 = (приблизительно) 1570. Таким образом, наш общий объем будет 1570см 3 .
Разница между полным объемом и объемом гелия составляет 472см 3 . Поскольку 10% от общего количества газа представляет собой CO2, мы можем найти его объем, просто умножив 10% на 1570см 3 , что даст нам 157см 3 . Азот, просто умножьте 20% на 1570 см 3 , что даст нам 314 см 3 . Итак, пока что мы имеем:
- Объем He = ·1098 см 3
- Объем Co2 = 157см 3
- Объем N2 = 314 см 3
- Общий объем = 1570см 3
Обратите внимание, что при добавлении томов по отдельности вы получаете слегка отличающиеся результаты. в отличие от умножения общего объема на отдельные проценты. Не беспокойтесь об этом!
Ничто из этого не должно быть таким точным. Даже соотношение 70/20/10% варьируется в зависимости от источника
литературы, на которую вы ссылаетесь. Кроме того, неизбежны вариации при округлении чисел —
особенно когда числа возводятся в квадрат или в куб.
На этом этапе у вас есть воздушный шар, наполненный гелием. Внешний размер этого воздушного шара составляет 40 см.
Наши расчеты говорят нам, что этот воздушный шар имеет объем 1098см 3 . Для того, чтобы определить, насколько
газа добавить, чтобы получить необходимые объемы Co2 и азота (помните, мы уже рассчитали
их соответствующие объемы), нам нужно рассчитать (в отличие от измерения) окружность для гелия
плюс следующий газ, который мы планируем добавить. Ради этого примера давайте просто предположим, что мы собираемся
затем добавьте CO2. Мы знаем, что CO2 составляет всего 10% от общего количества, или 157 см 92), что даст нам 1255см 3 . Теперь давайте найдем наш радиус (помните, что когда мы измеряли
окружности гелия, нам пришлось пройти несколько шагов, чтобы найти объем — теперь мы собираемся сделать
как раз наоборот, используя объем, чтобы найти новую окружность)!
V = 4/3πr 3
решение для » r » дает
r = 3 √ В/( 4/3π)
= 3 √ В/( 1255см 3 /4.187)
= 3 √ 300 см 3
г = 6,69 см
Итак, теперь давайте найдем эту окружность!
С = 2πr
= (2)(3,14)(6,69 см 3 )
С = 42см
С твоей портновской лентой, обернутой вокруг воздушного шара, вы будете вводить CO2 до тех пор, пока баллон не увеличится с 40 до 42 см в диаметре.
Для остального газа нам нужно только найти длину окружности для полного объема газа. все 3 газа. Итак, повторяя последнюю серию шагов…
r = 3 √ В/( 4/3π)
= 3 √ В/(
1570см 3 /4. 187)
= 3 √ 375 см 3
г = 7,211 см
С = 2πr
= (2)(3,14)(7,2 см 3 )
С = 45см
Теперь просто наполните шар азотом (или воздухом) для последнего шага. удерживая измерительную ленту на месте, как и раньше, пока лента не покажет что окружность воздушного шара составляет 45 см. Вот и все! Готово!
Теперь об отношении напряжения к давлению… Я полагаю, что профессор Марк Целе [1] сказал мне, что оптимальное отношение напряжения к напряжению составляет что-то вроде 15 или 16 В/см*T. Например, предположим расстояние между электродами 120 см (около 4 футов, как у моего первого лазера) и источник питания 15 кВ. 15 кВ/120 см = напряженность электрического поля 125 вольт/см. Применяя это к оптимальному соотношению напряжения и давления:
125 В/см * см * Т/16 В = ~ 8 Торр, необходимое для оптимальных условий при использовании источника питания 15 кВ с таким разделением электродов.
Это теоретический ориентир. На практике вам, вероятно, придется поэкспериментировать с вариациями этого руководства, чтобы получить наилучшие результаты. Самая важная часть — это совет, который я получил от профессора Марка Челе: просто постепенно уменьшайте давление в трубке с помощью игольчатого клапана, пока не начнется электрический разряд. Именно при этом давлении (или чуть ниже) и происходит генерация! Это важнее теории, когда речь идет о реально работающем лазере. Слишком большое давление и ваш блок питания явно не преодолеет сопротивление газа. Но менее очевидным является то, что генерация возникает при давлении, при котором начинается разряд (и в диапазоне давлений, чуть ниже этого). Для этого вам не нужен манометр — просто откройте игольчатый клапан, пока не начнется слив! Держите его в этом диапазоне. Это так просто, если предположить, что у вас есть работающее устройство, и предположить, что другие факторы являются адекватными.
Убедитесь, что шланг между помпой и лазером имеет значительную длину. Поместите резервную бутылку или отдельный клапан, который вы сможете перекрыть перед выключением помпы. Если вы этого не сделаете, то масло из насоса попадет обратно в ваш лазер (и шланг), когда вы выключите насос.
Убедитесь, что между вашим лазером и всем остальным имеется длинный шланг. Длина шланга между лазером и всем остальным, например насосами или игольчатыми клапанами, должна быть значительно больше, чем расстояние между вашими электродами! Это очень важно. В противном случае опасный электрический ток, подаваемый на лазерные электроды, может легко обойти лазерную трубку и вместо этого пройти к ближайшему оборудованию через частично вакуумированный шланг насоса. Таким образом, оборудование, такое как игольчатый клапан, может оказаться под напряжением. Такая ситуация может очень легко привести к смертельному поражению электрическим током. Не торопитесь, берегите себя и будьте в безопасности! Живите, чтобы увидеть, как ваш лазер завершен, и построить еще один!
Используя бутылку пищевой соды и уксуса (для производства CO2), я не смог увидеть никаких улучшений при добавлении газообразного азота. Гелий был самым важным фактором. Оставшегося воздуха в бутыли (кувшине) было достаточно, чтобы удовлетворить потребность в азоте. Гелий и CO2 были наиболее важными частями — в основном вам нужно больше гелия, чем CO2. Без гелия генерация очень плохая. Имейте в виду, что у моего первого лазера расстояние между электродами (активная длина) составляло 4 фута, поэтому полученное усиление несколько компенсировало недостатки, которые могли бы привести к неработоспособности лазера, если бы я выбрал более короткую конструкцию трубки. Забудьте о генерирующем дыхании без гелия. Я не говорю, что это невозможно сделать (вероятно, сделал, но сейчас не помню) — я просто говорю, что это не рекомендация «первой» попытки.
СО2-лазер 2
В моем втором CO2-лазере использовалась стеклянная трубка длиной около 75 см и внутренним диаметром всего 6 мм. Для герметизации концов водяной рубашки использовалась пара компрессионных фитингов из ПВХ. Сама водяная рубашка представляла собой просто пластиковую трубку, использованную в качестве контейнера для набора сварочных/пайковых стержней, поставляемых в местном хозяйственном магазине. Компрессионные фитинги были изготовлены по индивидуальному заказу с уплотнительными кольцами для лучшей герметизации от утечек на концах водяной рубашки. Торцевые электроды были изготовлены с использованием латунных компрессионных фитингов. Латунные компрессионные фитинги также были изготовлены по индивидуальному заказу с уплотнительными кольцами для герметизации трубки. Подробности смотрите на рисунке ниже.
Мой второй CO2-лазер был просто предшественником третьего. Настоящий успех был реализован с моим третьим устройством. Второй было слишком сложно выровнять из-за узкого канала ствола. Проявив настойчивость, я мог бы выровнять его должным образом, но потерял интерес и просто построил еще один лазер, используя те же компрессионные фитинги из латуни и ПВХ.
Использование латунных компрессионных фитингов было идеей, которую я позаимствовал у исследователя Джона Сингера. Джон Сингер использовал их аналогичным образом, за исключением лазеров на красителях, которые он строил.
СО2-лазер 3
Laser Complete — содержание страницы (написание) в процессе создания.
СО2-лазер 4
Как и в случае с моими СО2-лазерами «Гиллигана» и «Бедняка», СО2-лазер номер 4 разрабатывается с упором на очень простые и легкодоступные материалы. В отличие от двух проектов, упомянутых выше, номер четыре — это попытка получить производительность, которая, я надеюсь, будет конкурировать с моими первым и третьим проектами. Помните, что в первой и третьей конструкциях использовался соответствующий выходной ответвитель из ZnSe. Использование «настоящей» лазерной оптики через выходной ответвитель из ZnSe обеспечивает характеристики, аналогичные характеристикам коммерческих лазерных устройств. В конструкциях Гиллигана и Бедняка для прохождения выходного луча используется отверстие с соляным окном. Зеркала на обоих концах лазерной трубки все еще должны быть выровнены, но одно из них имеет небольшое отверстие для прохождения выходного луча. Однако я считаю, что для оптимизации такого расположения необходимо, чтобы по крайней мере одно из зеркал резонатора было вогнутым. Идея состоит в том, чтобы усиленная лазерная энергия постепенно сходилась с каждым проходом, в конечном итоге проходя через маленькое отверстие, которое находится в центре диаметра одного из зеркал. В устройствах Гиллигана и Бедняка используются два плоских зеркала. Я ожидаю, что при использовании более широкого отверстия (лазерной трубки) и вогнутого зеркала я смогу лучше использовать всю активную область лазерного разряда. Poor Man’s и Gilligan’s использовали диаметр отверстия всего 6 мм (в одном случае) и 1/2 дюйма в другом. Номер 4 будет использовать лазерную трубку шириной 1 дюйм. Трубка состоит из обычной люминесцентной лампы T8, а трубка с водяной рубашкой изготовлена из люминесцентной лампы T12.
Вогнутое зеркало с большим фокусным расстоянием будет отшлифовано вручную с использованием техники изготовления зеркал Добсона. Метод Добсона — это метод, используемый строителями телескопов-любителями. Я решил попробовать этот метод с медью вместо стекла по трем основным причинам: медь намного мягче, и поэтому ее легче/быстрее шлифовать, чем стекло, медь обладает хорошими отражающими свойствами на соответствующей длине волны, а на стекло должен быть нанесен металл. (нетривиальный процесс сам по себе). Изготовление медных зеркал для этой конкретной цели в настоящее время исследуется преподавателем физики Джоном Гейтсом. Мистер Гейтс и я вместе работаем над этим проектом — он разрабатывает технику изготовления зеркал, а я конструирую лазерную трубку. Г-н Гейтс уже сделал несколько очень важных открытий относительно этого процесса. Я буду делиться его успехами и прогрессом по мере его развития — его работа является существенным вкладом в общий дизайн.
Вот моя часть строительства, как в настоящее время ведется:
Как и в случае с моим первым лазером, в стальных шайбах просверлены стратегически расположенные отверстия, чтобы приспособить плоскость регулировки по трем точкам. Одна из шайб крепится к алюминиевой трубе с помощью эпоксидной смолы JB, а затем для эстетики на эпоксидную смолу наносится серебристая краска. В трубке электрода просверливается отверстие для штуцера шланга. Каждый из двух электродов должен иметь разъем для шланга — вакуумный насос будет подключен к одному разъему для шланга, а подача газа — к другому.
В моей первой конструкции торцевые части соединяются снаружи стеклянной лазерной трубки. Поскольку электроды находятся снаружи лазерной трубки, охлаждающая рубашка не простирается достаточно далеко, чтобы вместить их, поэтому участок трубки между электродами и охлаждающей рубашкой сильно нагревается. В несколько ином подходе текущий проект использует высокотемпературную алюминиевую ленту для размещения дополнительной секции трубки, служащей в качестве муфты, к алюминиевому электроду (часть со стальным фланцем шайбы) и стеклянной лазерной трубке (см. ниже).
Затем подготовленный соединитель используется для соединения держателя электрода/регулировки зеркала с лазерной трубкой:
Для соединителя шланга я просто использовал алюминиевую трубку с внутренним диаметром 1/4 дюйма. Трубка соединяется и герметизируется над этим отверстием с помощью эпоксидной смолы. Размер отверстия выбран так, чтобы алюминиевая трубка могла быть частично вставлена в стенку трубки электрода без за его пределы. По сути, трубка соединителя шланга должна быть просто достаточно плотной, чтобы оставаться на месте до тех пор, пока эпоксидная смола не затвердеет (см. рисунок ниже). Я использовал быстросохнущую эпоксидную смолу, чтобы частично закрепить соединитель шланга, а затем мощный JB сварка (медленного типа) эпоксидная смола.
В верхней части торцевой вертикальной стойки имеется отверстие, удобно расположенное для размещения соединителя шланга. Таким образом, верхняя часть служит скобой для соединителя шланга, что делает конструкцию более прочной.
Инструктор по физике Джон Гейтс недавно обратился ко мне за помощью в создании CO2-лазера. Как и мне, ему понравилась идея построить лазер с использованием дешевых и легкодоступных материалов. Он представил идею использования пластины жесткого диска компьютера в качестве выходного соединителя. Пластины жесткого диска изготовлены из металла, что избавляет от головной боли, связанной со сверлением и резкой стекла. Я сказал Джону, что подумывал о том, чтобы отшлифовать собственное зеркало с высоким отражателем, используя технику изготовления зеркал телескопа Добсона. Он сразу же начал работать над этим и быстро получил множество экспериментальных результатов. Почти за одну ночь Джон разработал подробный набор руководящих принципов, основанный на его опыте. Вот учебник, подготовленный Джоном Гейтсом на основе его экспериментов.
Введение:
Почти невозможно поверить, что лазер, способный производить десятки ватт, можно сделать почти полностью с нуля. Вы видели видеоролики о том, как лазеры на углекислом газе прожигают дыры в древесине, и вы хотите такой. Вы можете купить герметичный блок на Ebay (дорого) или собрать его из хлама (круто).
Все в CO2-лазере выглядит выполнимым, пока вы не доберетесь до оптики. Ответвитель на выходе из селенида цинка стоит дорого, и иногда его трудно найти — например, высоковольтный конденсатор, необходимый для той катушки Тесла, которую вы хотели построить; редкий и дорогой. Но для самодельной катушки Теслы можно изготовить собственные конденсаторы, используя пивные бутылки и соленую воду, практически бесплатно. Точно так же вы можете отшлифовать и изготовить собственную оптику для самодельного CO2-лазера! Выходной разъем может быть таким же простым, как секция блестящего металла, отрезанная от пластины жесткого диска, с небольшим отверстием, которое было просверлено и закрыто кристаллом каменной соли. Зеркало HR должно быть вогнутым для хорошей работы, и его можно отшлифовать из копейки и какого-нибудь состава для полировки кузова. Сэкономьте свои деньги на том, что действительно необходимо — приличном вакуумном насосе HVAC и/или NST.
ПОДГОТОВКА:Вам понадобится следующее:
два пенни до 1983 года (100% медь) или алюминиевые пластины для жестких дисков (НЕ стеклянные или керамические) два болта с шестигранной головкой 5/8″ эпоксидная смола (предпочтительнее быстродействующий гель – я использовал время отверждения 6 минут) соль и уксус наждачная бумага следующей зернистости (от 80 до 600 или мельче) Состав Turtle Wax RUBBING (банка с красной этикеткой, которую можно найти в магазинах автозапчастей)
- Почистите два пенни до 1983 года (100% медь, без цинка внутри) средством для мытья посуды и мочалкой.
Если вы используете пластины жесткого диска, вставьте одну пластину между двумя деревянными брусками и с помощью кольцевой пилы медленно разрежьте два диска. Диски уже чистые и ровные, поэтому следующие шаги можно пропустить.
- Поместите пенни в раствор уксуса и соли, чтобы дополнительно очистить/осветлить монеты (но не слишком долго, около пяти минут).
- Промойте осветленные монеты, а затем придайте шероховатость поверхности шестигранных гаек 5/8 дюйма наждачной бумагой с зернистостью 80 (эпоксидная смола держится лучше).
- Очистите подготовленные болты небольшим количеством медицинского спирта, а затем эпоксидной смолой головкой вниз. Убедитесь, что монеты расположены по центру и плотно прилегают к гайке. Я нанес зубочисткой тщательно перемешанную эпоксидную смолу по периметру копейки. Чтобы гарантировать надежную фиксацию, я использовал зубочистку, чтобы нанести немного эпоксидной смолы по бокам пенни. Если вы используете пластины жесткого диска, просто приклейте эпоксидной смолой большую шестигранную гайку к задней части после оценки центра.
Когда эпоксидка затвердеет, очистите стороны и приступайте к «шлифовке и полировке».
- Дайте эпоксидной смоле застыть в течение ночи (нам нужна действительно хорошая фиксация).
- Работая со стеклянной поверхностью (потому что она невероятно плоская), отшлифуйте заднюю сторону, используя наждачную бумагу с зернистостью от 150 до 600 (или мельче). В начале лучше всего работают прямые перетаскивающие штрихи вместо круговых. Заведите привычку вращать монетки и наждачную бумагу, чтобы внести немного хаотичности (что хорошо). По мере уменьшения зернистости (около 220, 320) используйте круговые движения.
- После того, как вы наберете самую мелкую зернистость, избавьтесь от наждачной бумаги и нанесите состав для протирки Turtle Wax непосредственно на стеклянную поверхность. Вы заметите, что стороны стали немного грубее, а центр более гладким. Когда вы сплющите пенни, вы увидите, как «ореол» смещается в стороны, а центр сплющивается. Несмотря на то, что мы работаем со стеклом, монеты на самом деле слегка выпуклые.
Продолжайте сглаживать/полировать круговыми движениями, пока ореол не выйдет за края.
- Этот шаг важен. В противном случае «шлифовка и полировка» может привести к путанице. Поместите свои только что сплющенные пенни на наждачную бумагу с зернистостью от 600 до 1500 и сделайте несколько штрихов, чтобы поверхность стала матовой. Да, вы только что уничтожили эту хорошо отполированную плоскую монету, но матовая поверхность вам понадобится позже.
- Выберите, какой сплющенный пенни вам больше нравится, он станет вогнутым зеркалом (HR) в вашем лазере, а другой станет «инструментом» (хорошее выпуклое зеркало, если оно вам когда-нибудь понадобится).
ШЛИФОВКА И ПОЛИРОВКАВам понадобиться:
две ранее сплющенные монеты, приклеенные эпоксидной смолой к гайкам 5/8″ (или алюминиевые пластины жесткого диска, приклеенные к гайкам) маленькие тиски для сверлильного станка (эти тиски плоские на дне и предназначены для крепления болтами к сверлильному станку, подойдет пятифунтовый тиски) Turtle Wax RUBBING Compound (марка не важна, но это должна быть полировочная паста — полировка занимает больше времени) бумажные полотенца много свободного времени, хороший фильм, хорошая жена и бутерброд не помешает ОСТОРОЖНОСТЬ!: Не используйте полировальные палочки (наждак, трепел, белая или красная румяна), предназначенные для хлопковых полировальных кругов, установленных на настольных шлифовальных машинах.Хотя зернистость хорошая, связующее вещество для воска ужасное, оно слипается и вызывает скольжение, что равнозначно царапанью. Я не пробовал настоящий песок, используемый для шлифовки зеркал телескопа, но он может работать. Помните, что размер зерна определяет фокусное расстояние. Очень легко шлифовать слишком глубокий изгиб. Я бы сразу выбрал оксид церия или румяна. Мы удаляем только десятитысячные дюйма от центра!!! Лучше думать о полировке зеркала, а НЕ о шлифовке зеркала.
ТЕСТИРОВАНИЕ: Вам понадобиться:
- Зажмите инструмент в тиски сверлильного станка. Нанесите немного состава на инструмент и на предполагаемое зеркало. Избегайте комкования и наносите его круговыми движениями, чтобы получился красивый ровный слой. Почему бы не использовать вместо него полировочную пасту? По моему опыту, сверхмелкая зернистость/паста полировальной пасты не предотвращает контакт меди с медью, что приводит к царапинам, похожим на борозды! Красная полировальная паста никогда не выходит из строя и полируется быстрее.
- Следующие шаги очень важны, и для их освоения потребуется опыт. Поместите зеркало непосредственно на инструмент и двигайте его вперед и назад, центр над центром. Начните с небольшого давления, чтобы размазать абразив, затем увеличьте давление до умеренного. Свес должен составлять четверть или меньше диаметра пенни. Вы должны чувствовать умеренное сопротивление, но все равно поверхность должна быть гладкой с хорошим контактом (остановитесь, если она не гладкая, не царапается и не чистая). Когда у вас это хорошо получается, кажется, что вы вибрируете зеркалом над инструментом, хотя и не слишком быстро. Инструмент (нижняя монета) становится выпуклым, а зеркало (верхняя монета) вогнутым. Это происходит от центра к краям. То, что вы делаете, называется нормальный ход — термин, используемый производителями зеркал для телескопов. У Springfield Telescope Makers, Inc. есть отличное онлайн-руководство, в котором ясно и подробно объясняется этот метод.
- Выполните 5-10 нормальных движений, а затем, не отрывая зеркало от инструмента, поверните тиски немного против часовой стрелки, а зеркало немного по часовой стрелке.
Нанесите еще 5-10 обычных штрихов. Повернуть. Если возможно, еще 5-10 ударов. Когда монеты начнут связываться, вы почувствуете большее сопротивление, так что остановитесь. Протрите бумажным полотенцем, повторно нанесите состав и начните заново. Попытка протолкнуть его слишком далеко с большим сопротивлением приведет к слипанию абразива, что приведет к царапинам. Когда вы чистите монеты, вам придется немного побороться с «всасыванием»/прилипанием, чтобы снять зеркало с инструмента, и вы должны увидеть тонкую коричневую пленку, равномерно покрывающую поверхности. На самом деле вы должны очистить до того, как произойдет связывание, но знание того, когда это произойдет, требует опыта. Я делаю три-пять оборотов перед чисткой. Я трачу столько же времени на очистку и повторное нанесение, сколько на шлифовку/полировку. Вращая инструмент и зеркало, вы усредняете любые несоответствия в идеальную сферическую форму, поэтому частое вращение имеет решающее значение.
- Продолжайте шлифовать (больше похоже на полировку), пока не увидите форму «ореола» в центре, а затем двигайтесь к самому краю монеты по мере работы.
Помните, что кривая создается изнутри наружу. Во время работы важно работать плавно, останавливаясь и очищая каждый раз, когда происходит заедание (лучше всего чистить до того, как произойдет заедание). Переплет вызывает царапины. Эти царапины могут сделать зеркало бесполезным или, по крайней мере, для их исправления могут потребоваться огромные усилия.
- Чтобы на самом деле отполировать (финишировать) зеркало, нанесите немного шлифовальной пасты и отполируйте вручную бумажным полотенцем (не используйте инструмент). Если вы хотите использовать полировальный состав Turtle Wax (зеленая этикетка), он обеспечивает лучший блеск при ручной полировке. Однако не будьте слишком агрессивны с полировкой рук, иначе вы можете изменить кривую.
- Ваше зеркало не будет идеально отполировано. Все еще будут царапины и блики (микроцарапины) — это должно быть нормально (усиление CO2-лазера компенсирует это).
- Вы… ну, приближаетесь… может быть, обходите третью базу. Вероятно, прошло два часа с тех пор, как вы начали, и, возможно, пришло время лечь спать, заняться домашними делами или выпить пепси (в зависимости от того, что диктует ваш образ жизни, жена или ситуация).
твое полированное зеркало регулируемая лазерная указка (регулируемая означает, что вы можете распределить фокус) кусок черной плотной бумаги рулетка много плоского пространства (подойдет коридор)
- В одном конце коридора положите зеркало на пол (надеюсь, оно не покрыто ковром). Как можно дальше, насколько это возможно (можно использовать свой задний двор), поместите лазерную указку на пол и распределите луч так, чтобы он покрывал все зеркало. Повозитесь с прицеливанием, пока не получите точку, отраженную назад, с которой вы сможете работать. Важно, чтобы лазерная указка находилась за пределами фокусного расстояния зеркала. Если указатель находится внутри фокусного расстояния, зеркало будет фактически рассеивать луч (действовать как выпуклое зеркало). Также важно, чтобы угол между лазерной указкой и отраженным лучом был небольшим.
- В идеале вы должны увидеть небольшое пятно, отраженное назад. Используйте лист черной плотной бумаги, чтобы лучше видеть размытие. Теперь осторожно подойдите к зеркалу, и размытие должно стать меньше, пока не превратится в крошечную точку (это работает, когда вы уходите или приближаетесь к зеркалу). Расстояние, на котором образуется крошечная точка, и есть ваше фокусное расстояние.
Мое лучшее зеркало дало мне точку размером 1 мм. Вы можете заметить небольшое зернистость точки — это нормально. Если бы зеркало было идеально отполировано, вы бы увидели только точку. Да, мы немного теряем мощность лазера, но мне еще предстоит получить идеально отполированные зеркала. Не пытайтесь довести бафф до совершенства — вы измените кривую.- Вы, вероятно, обнаружите, что фокусное расстояние/радиус кривизны слишком малы (я получаю около шести или семи футов после первого формирования). Чтобы увеличить его, оставьте настройку тестового избавления и снова начните гридинг/плишинг.
Однако на этот раз поместите зеркало внизу и отшлифуйте/шлифуйте инструментом сверху (это сгладит наше зеркало). Периодически проверяйте свое зеркало, и вы заметите, что фокусное расстояние увеличивается. Продолжайте, пока не получите желаемую длину.
- Не срезайте зеркало с гайки, просто приклейте его целиком к электроду с шайбой/уплотнительным кольцом. Горячий клей, кусок изоленты (для страховки) и вакуум удержат его там.
- Если вы не удовлетворены, рассмотрите следующее:
тип = «А» >
- Нет пятна = лазерная указка внутри фокусного расстояния или поверхность очень сильно поцарапана (Не нажимайте на нее перед очисткой — состав высыхает, затем слипается, и вы получаете царапины. инструмент и увидите тонкую коричневую пленку, покрывающую большую часть поверхности.)
- Фокусное расстояние слишком маленькое = поместите зеркало внизу и отполируйте инструментом сверху (доведя до крайности, вы можете снова получить две плоские поверхности — так что продолжайте тестировать).
- Фокусное расстояние слишком большое = продолжайте полировать с зеркалом сверху, но не агрессивно. Это хорошая идея, чтобы лазерная указка была включена, а установка для тестирования не повреждена. Вы можете легко отполировать (использовать инструмент) зеркало до нужного вам фокусного расстояния.
- Слишком много звездочек = вам нужно получить хорошее, ровное ощущение с умеренным сопротивлением, чтобы предотвратить заедание (чаще очищайте).
- Как насчет параболизации с W-образным ходом? Вы, должно быть, читали больше о сайте по изготовлению зеркал Stellafane? Да, технически параболизированное/фигурное зеркало теоретически даст вам лучшие результаты, но какой ценой? Если вы хотите параболизироваться, вам понадобится либо солнечный свет, либо много места, потому что лазерная указка должна быть как можно дальше от зеркала, чтобы лучи были максимально параллельны. Лучше потратить свое время на поиски того самого вакуумного насоса, НСТ, затыкания утечек.
.. готово.
- Я кое-что знаю о геометрической оптике, и маленький трюк с лазерной указкой технически неверен. Я знаю, потому что я сам проследил диаграммы лучей, и мне трудно точно понять, что происходит (без использования солнечного света). Если у вас есть лучший способ, пожалуйста, помогите.
CO2 4 был приостановлен, потому что трубка треснула. На данный момент я приступаю к CO2 5. Следите за моим прогрессом ниже с помощью фотографий, и я предоставлю вспомогательный текст при первой же возможности.
20.10.13 21.10.13
14.10.15
Сомневаюсь, что Sears и Roebuck могли производить что-то такого высокого качества… это пара сильфонов, изготовленных специально для меня доктором Линдси Уилсон.
Приземленный эрудит, доктор Уилсон обладает необычайным талантом и способностями, которые охватывают бесчисленное множество дисциплин. широкий спектр, включая, помимо прочего, математику, физику, химию, компьютерную графику, машинную обработку, проектирование и производство, бизнес и музыка. Я в долгу перед ним за неоценимую помощь в о каждой области науки, техники и не только.
Концы лазерной трубки представляют собой не что иное, как отрезки тонкой латунной трубки, вставленные в основной стеклянная трубка и заклеена эпоксидной смолой. Стремясь максимально увеличить активную длину лазера, я воздержался от установки латунной трубки. дальше минимального расстояния, которое, по моему мнению, было необходимо для обеспечения достаточной безопасности. Тем не менее, мехи представят больше вес на концах, чем я изначально предполагал. Чтобы обеспечить дополнительную поддержку, я решил сделать направляющие для тубуса. подобные тем, которые используются для защиты телескопов.
youtube.com/embed/spu-t1mBS3k?list=UUP-cc5GJYLkQxRHPE8cyW8w» frameborder=»0″ allowfullscreen=»»>Пара шайб и уплотнительное кольцо позволят наклонить шайба с зеркалом, а другая шайба остается неподвижен относительно лазерной трубки. На практике ряд шайб и уплотнительных колец подойдут лучше всего. Это может быть уподоблено к штабелю шин; один поверх другого, лежа на плоской подошве на земле — чем больше шин, тем больше будет угол, на который можно наклонить верхнюю шину при применении направленная вниз сила в любой заданной точке вдоль его края. Шины можно сжать, но не как пружину. Они ограничены в степени, до которой они могут быть сжаты, поэтому больше шин будет обеспечить больший диапазон движения, основанный на сумма их индивидуальных диапазонов. Нужно начать с зеркала, установленные достаточно прямо перед регулировкой, или больше шайб и уплотнительных колец потребуются, чтобы приспособиться к большему углу какие зеркала должны быть наклонены, чтобы добиться правильного выравнивания.
Следующие изображения являются виртуальными представлениями, которые я построил в части с помощью растровой графики.
Вместо использования шайб и уплотнительных колец для № 7, как показано выше, Я решил разобрать №5 из-за его ультрасовременных мехов. На следующих рисунках показана последовательность сборки. Сначала я покрасил одну пару стальных шайб в золотой цвет, так что они приблизились бы к цвету соседних медных частей. Однако после того, как я решил использовать меха, я решил удалить золотую краску. Следующие одиннадцать картинок были сняты до того, как была удалена золотая краска. В попытке сделать это больше похоже на оригинальную сталь, я покрасил шайбы сероватый цвет с использованием программного обеспечения для пост-фотографии (выбирая «быстрое исправление» подход вместо того, чтобы тратить время на тщательное и реалистичное изменение цвет с помощью растровой графики). Так что извините за плохое качество.
Предыдущий набор фотографий был сделан камерой моего мобильного телефона.
Следующие 7 снимков были сделаны качественной камерой они имеют четкое представление о сильфоне вместе с лазерной трубкой, которая просто отдыхает на месте (до лазера еще далеко завершена, и трубка еще не закреплена окончательно).
Ключевые ссылки:
[1] Страница самодельных лазеров профессора Марка ЧелеКак построить лазерный резак
Опубликовано: · Изменено: Люси · Эта запись может содержать партнерские ссылки · Этот блог приносит доход от рекламы
Хотите построить свой первый лазерный резак своими руками ? Лазерные резаки являются частью технологии резки, в которой используются лазерные лучи для испарения материалов, в результате чего получается режущая кромка. До недавнего времени они использовались в основном промышленными предприятиями, но теперь используются различными малыми предприятиями, школами, архитекторами и любителями.
Оптика и ЧПУ (ЧПУ) лазеров используются для направления материала или генерируемых лазерных лучей. Они работают, направляя выход мощного лазера, чаще всего через cs.
В отличие от традиционных методов механической резки, лазерные резаки уменьшают загрязнение заготовок. Они также могут вырезать отверстия малого диаметра со сложной детализацией и хорошим качеством кромок; они также очень экономичны в использовании. Проблема с этой очень полезной машиной заключается в том, что она дорогая, вам не нужно беспокоиться о том, чтобы превысить свой бюджет, чтобы приобрести лазерный резак в наши дни, поскольку теперь их можно легко сделать с нуля в домашних условиях, и я смог составить 14 из лучших Лазерный резак своими руками проектов, которые научат вас делать свои собственные.
1. Самодельный лазерный резак своими руками
Возникли проблемы со старым лазерным резаком? Или вы заинтересованы в создании своего лазерного резака с нуля? Возможно, вы даже не заинтересованы в том, чтобы научиться создавать лазерный резак, а просто хотите получить знания. Вам очень хотелось бы ознакомиться с этим учебным пособием «Сделай сам».
Теперь вы можете легко создать свой собственный станок для лазерной резки CO2, используя комбинацию 3D-печатных деталей из алюминиевого профиля с V и T-образными точками. Самое приятное то, что эта стоимость составляет едва ли половину того, что требуется для получения нового.
2. Самодельный лазерный резак мощностью 40 Вт
Лазерный станок с ЧПУ мощностью 40 Вт используется для гравировки отверстий и резки различных материалов, таких как дерево, фанера, акрил. Зачем вам тратить так много, если вы можете легко получить расходные материалы и оборудование, такие как лазерные трубки CO2, рельсовые направляющие, блоки питания и т. д. И построить свой собственный лазерный резак всего за 400 долларов. Одно из лучших предложений!
3. Дешевый лазерный гравер
youtube.com/embed/EASRGfZNAI8″ frameborder=»0″ allowfullscreen=»allowfullscreen»/>К настоящему времени, если вы любитель ремесел или заядлый любитель гравировки по дереву и материалам, вы бы поняли, насколько дорого обходится качественный и надежный станок для лазерной резки. Что еще хуже, те, которые имеют более низкую цену, производят низкие мегаватты, которые едва ли могут разрезать лист бумаги, тем более кусок дерева или более твердые материалы, такие как металл. Этот проект был создан, чтобы помочь большинству мастеров создать свой собственный мощный лазерный резак по доступной цене.
4. Простой самодельный лазерный резак
3D-принтеры являются важными компонентами любого лазерного резака, потому что они отлично подходят для прототипирования чего угодно и могут быть использованы для создания любой формы, но 3D-принтеры, конечно, дороги. и не каждому по карману, научитесь делать простой станок с ЧПУ с минимальным количеством деталей. Без использования 3D-принтера дрель и несколько ручек берут на себя роль 3D-принтера в этом проекте.
5. Лазерный резак CO2
Будучи начинающим любителем или архитектором, получить хороший лазерный резак для рабочих проектов может быть практически невозможно, потому что лазерные резаки стоят очень дорого.
Что ж, если вы решили принять новый вызов и создать свой собственный станок для лазерной резки за полцены, вам повезло, так как это руководство шаг за шагом научит вас всем практическим способам и процессам создания свой собственный лазерный резак. Этот станок для лазерной резки CO2 мощностью 40 Вт имеет большую площадь резки 1000 на 600 мм и сенсорный экран.
Он работает на двух микроконтроллерах: Arduino с GRBL и Raspberry Pi с сенсорным экраном для управления частями лазерного резака. Кроме того, сенсорный экран делает его более удобным, так как вам не нужно передавать программное обеспечение с вашего компьютера на лазерный резак. instructables
6. Как собрать лазерный резак
Создайте свой мини-лазерный станок с ЧПУ в домашних условиях с помощью некоторых обычных материалов, таких как фанера, стальные стержни, винты, зажимы, скотч, ножницы, 3D-лучи и другие. Он работает так же хорошо, как и большие лазерные резаки, и хорош, если вы собираетесь освободить место дома.
7. Мини-лазерный гравер с ЧПУ
Это один из тех дешевых проектов, которые можно реализовать, если вы собираете лазерный резак/гравер с ЧПУ. Это отличное учебное пособие для студентов-любителей, изучающих промышленность. Для этого требуются 2 устройства записи DVD, лазер, Arduino UNO, плата драйвера CNC Shield V3 A4988, реле 5V и другие материалы. Следите за всеми процессами и планируйте проекты и размеры, чтобы добиться отличного результата.
8. Самодельный лазерный гравер с DVD-приводом
У вас есть старый DVD-диск, и вы думаете о том, какой интересный новый экспериментальный проект использовать его или его части для создания, мини-лазерный резак/гравер с ЧПУ, состоящий из DVD-драйверов — идеальный проект для вас. Это не займет много времени и навыков, если вы будете внимательно следовать всем инструкциям, а также будете очень экономны.
9. Мощный лазерный резак из DVD-RW
Из этого мастер-класса вы узнаете, как сделать мощный лазерный резак, который горит. Да, ты слышал меня, БЕРНС! Он может служить довольно причудливым факелом для зажигания свечей, но будьте осторожны, так как они очень мощные и горят очень сильно. В этом видеоуроке объясняются все важные элементы, начиная со списка вещей, которые нужно получить, заканчивая всей физикой, стоящей за всем этим, и заканчивая окончательной сборкой всех важных частей.
10. Лазерный гравер «Сделай сам»
Это первая часть серии о лазерном гравере «Сделай сам», и вы узнаете обо всех важных процедурах, необходимых для создания основной системы перемещения XY лазерного гравера. Детали имитируют движения лазерного луча. Это действительно забавный проект, который вы должны попробовать, но помните об осторожности, поскольку лазерные лучи, если их пропустить, очень опасны не только для нас, но и для наших близких, и для широкой публики, поэтому в этом видео также объясняется, как создавать и используйте лазерный луч для проектов осторожно.
11. Лазерный резак своими руками
Одна из вещей, которую вы узнаете из этого руководства, — это как сделать своими руками лазерный резак с алюминиевой рамой. Алюминиевые рамы собраны и соединены в нужных частях, и это делает вас мини-3D-принтером, сосредоточенным на алюминиевых рамах. Это творческий проект от начала до конца для всех начинающих.
12. Мини-лазерный станок с ЧПУ «Сделай сам»
Начните собирать с нуля свой мини-лазерный станок для лазерной резки/гравировки с ЧПУ, следуя инструкциям из этого руководства «Сделай сам». Мини-лазеры очень полезны для каждого ремесленника. Вы можете сделать как можно больше мини-лазеров для бизнеса без особых усилий. Они состоят из различных легкодоступных расходных материалов, которые вы можете приобрести в любом месте в Интернете или в любом хозяйственном магазине. Некоторые из этих поставок включают в себя; Конденсатор, резистор, Arduino, печатная плата Arduino, 3D-принтеры, лазер мощностью 250 мВт, двигатель, транзистор, магнит, источник питания 12 В и множество других материалов.
Это быстрый проект, так как он может быть завершен в течение нескольких дней или, самое большее, недели.
13. Самодельный лазерный резак Arduino
Получите правильное представление и инструкции по созданию самодельного лазерного резака Arduino с использованием Arduino NANO, моторного привода A4988, 200–250 мВт 650-нм лазерного модуля, N-канального Mosfet IRFZ44N, регулятора напряжения LM7805, T-220 Радиатор, резистор 47 Ом и 10 кОм, конденсатор 1000 мкФ 16 В, штыревой и гнездовой разъемы, винтовые клеммы, перемычка 2,54 мм, термоусадочная трубка, записывающее устройство DVD, лист акрила 5 мм, нейлоновая шестигранная печатная плата, проставка, винт с шестигранной головкой M3 , лазерный модуль, теплоотвод и т. д. и где их можно приобрести, а также как настроить, собрать и соединить их для создания лазерного резака своими руками.
14. Станок для лазерной резки своими руками
youtube.com/embed/U2djATmD2qA» frameborder=»0″ allowfullscreen=»allowfullscreen»/>Примените свои знания о лазерном станке и создании лазерного резака своими руками с пользой и творческим подходом в этом учебном пособии, показывающем, как этот ручной станок для лазерной резки используется для изготовления настенных часов. Лазерные резаки можно использовать для изготовления многих других ценных вещей, таких как наручные часы, бумажные рисунки, отпечатки мебели и все такое.
В этом учебном пособии показано, как лазерный резак подробно вырезает все выбранные детали, а затем собирает их в различных местах после окрашивания в желаемые цвета.
Лазерные станки — очень изобретательные и полезные машины, необходимые на всех уровнях мастерства.
Заключение
Как вы, должно быть, заметили, это не один из тех очень простых проектов своими руками, создание лазерного резака требует времени, но с правильными материалами и руководством вы должны закончить свою сборку менее чем за неделю. . Спасибо, что заглянули, если эта статья о лазерном резаке «Сделай сам» была полезна, поделитесь ею в своих учетных записях в социальных сетях.
Взаимодействие с читателем
Laser Kids — Самодельный СО2-лазер с продольным разрядом
1. Цели
- Лазер предназначен для проверки возможности изготовления самодельного CO2-лазера из обычных материалов
- Лазер предназначен для использования в качестве испытательного стенда для проверки газовых смесей и других компонентов самодельных CO2-лазеров
- Лазер предназначен для измерения прозрачности и отражательной способности самых распространенных материалов на площади 10,6 мкм. (Чтобы найти подходящих кандидатов на лазерные зеркала и окна.)
Лазер хорош в качестве первого домашнего СО2-проекта при условии, что у Вас есть подходящий вакуумный насос. Высокий коэффициент усиления делает лазер более терпимым к ошибкам в юстировке и к составу газовой смеси. Первый опыт по форсированию генерации СО2 лучше всего проводить с этим типом лазера.
Лазер легко построить и настроить, но не ждите от него многого. Его мощность и эффективность невысоки. Следовательно:
- Лазер НЕ ПРЕДНАЗНАЧЕН для обработки материалов.
- Лазер НЕ ПРЕДНАЗНАЧЕН для публичных демонстраций.
- Лазер НЕ ПРЕДНАЗНАЧЕН для точных измерений.
2. Принцип действия лазера
Описываемый лазер представляет собой импульсно-периодический молекулярный лазер низкого давления с диффузионным охлаждением и накачкой продольным разрядом. Почему именно этот тип был выбран для строительства? Из-за:
- Высокий коэффициент усиления.
- Достаточно высокое давление.
- Отсутствие водяного охлаждения.
- Возможность использования пластика и пленки
Работа с непроверенными газовыми смесями не позволяет надеяться на очень высокий коэффициент усиления и высокий КПД при обычных режимах прокачки. Хуже того, самодельные зеркала могут иметь большие потери, поэтому требуется еще большее усиление. Излишне говорить, что при низком усилении лазерные резонаторы становятся очень чувствительными к ошибкам юстировки. Тогда с любой точки зрения следует, что чем выше ожидаемый выигрыш, тем лучше все становится. Это означает, что вы должны направить на самый высокий коэффициент усиления и наибольшую длину трубки.
Как известно из техники лазеров ТЭ и ТЭА, высокие коэффициенты усиления могут быть достигнуты при больших токах разряда (для ТЭА характерно 6..10 Ампер на квадратный сантиметр). Однако построить лазер с поперечной накачкой с метровой разрядной трубкой как минимум… сложно. Непрерывный лазер низкого давления столкнется с перегревом через несколько миллисекунд, если к нему будет приложен ток в несколько ампер. Компромиссом является режим повторяющихся импульсов. Высокий пиковый ток обеспечивает высокий коэффициент усиления, а короткая длительность импульса предотвращает перегрев газа.
Еще одним преимуществом режима повторяющихся импульсов (т.н. квазинепрерывного режима или просто QCW) является простота охлаждения и контроля температуры. Типичный непрерывный лазер даже при пороговых токах ведет себя уже как котел. 200..500Вт мощности запросто могут нагреть и перегреть что угодно. Наоборот, QCW-лазер на сравнительно низкой частоте может достичь порога генерации и остаться холодным. Здесь можно использовать пластиковые детали, проклеить все стыки клеевым пистолетом и не использовать водяную рубашку. В качестве дополнительного бонуса Вам понравится, что этот лазер работает при заметно более высоких давлениях, чем его непрерывный собрат. Это, в свою очередь, позволяет использовать более распространенные вакуумные насосы. Правило оружия: «при победе в одном месте проиграешь в другом». Здесь мы отказываемся от эффективности и мощности в пользу работоспособности с плохими газовыми смесями и зеркалами с потерями.
3.
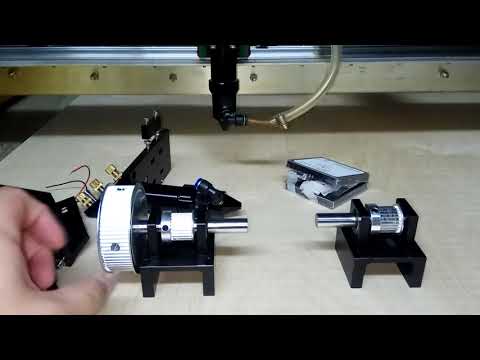
Для создания и использования лазера необходимо иметь следующие ресурсы:
- Вакуумный насос
- Пельтье-калориметр
- Микродрель с алмазным диском и алмазным отверстием
- Стеклянная трубка малого диаметра длиной около метра
- Комплект труб
- Какой-то сосуд для смешивания и хранения газов
- Пневматический пистолет, сатуратор или другое приспособление для заливки баллончиков СО2
- Слегка выпуклое автомобильное зеркало заднего вида
- Минимум одна катушка зажигания
- Лазерная указка или гелий-неоновый лазер
- Прочие наборы слесарно-плотницких-паяльных и гаражно-кухонных-радиоинструментов
- Ассортимент различных ресурсов для небольшого крафта
Хорошие, но необязательные:
- Вакуумметр
- Комплект клапанов (желательно игольчатый)
В качестве насоса можно использовать любой настоящий вакуумный насос. Неважно, ротационного или поршневого типа. Также можно использовать компрессор холодильника, настроенный на откачку. Однако, если вы используете этот, он должен быть новым или, по крайней мере, в хорошем состоянии. Старые или изношенные обеспечат только 80..100 торр, а этого недостаточно для нормальной работы лазера. Однако, если повезет, Вы можете увидеть генерацию даже при этих давлениях. Также для накачки шин можно использовать перевернутый (с восстановленными коллекторами) автомобильный компрессор.
Лично я пользуюсь небольшой вакуумной помпой, которая изначально предназначалась для обслуживания холодильников и других фреоновых машин.
у него верхний вакуум 38мкм явно избыточен для описываемого лазера, но если у меня есть один, то зачем мне использовать другой?
НЕ ПЫТАЙТЕСЬ использовать пылесос и НЕ используйте водоструйный химический насос. (Последний излучает пары воды, которые слишком плохи для генерации. Однако, если вы можете кормить его маслом, все может пойти лучше, и, вероятно, он подойдет.) НЕ пытайтесь использовать перевернутый автомобильный ручной насос. (Это действительно больно, чтобы сделать подходящий вакуум с этим. Возможно, даже если Вы спортивны.)
Калориметр (калориметрический измеритель мощности) может быть любого типа, способным измерять мощность в несколько десятков милливатт. (OPHIR, IMO и т.д.) Также хорош самодельный тип. Тот, что сделан из мультиметра и кулера Пельтье.
Здесь было написано, как его построить. Без калориметра обнаружить генерацию будет практически невозможно. Копировальная бумага только разбивает Ваши надежды. При первых запусках будет только малая мощность, которой не хватит, чтобы что-то сжечь.
Микродрель с алмазным диском и отверстием нужна в основном для изготовления зеркал, однако пригодится и для других мелких работ (например, для резки фитингов)
Стеклянная трубка для лазерной ячейки должна иметь длину около метра (помните, что нам нужен максимальный коэффициент усиления на путь). Оптимальный диаметр около 8 мм, но встречается редко. Чуть хуже, но достаточно хороша трубка, используемая в люминесцентных лампах с цоколем G5 (внешний диаметр 12 мм). Эти лампы тоже довольно сложно найти. Наибольшее распространение получили лампы на базе Т5 (внешний диаметр 16 мм). Этот используется для описываемого лазера.
Алмазным диском отрежьте концы нитей и плотно завяжите их в полиэтиленовый пакет. Нити содержат заметное количество ртути. Вы должны безопасно их выбросить или безопасно хранить для Вашего будущего проекта с лазером на парах ртути. (Обратите внимание, что если лампы не новые, ртуть может растечься по трубке. Поэтому безопаснее разбирать новые лампы.)
Трубы из ПВХ или силикона подходят для использования. Резиновые приведут к громоздкости конструкции, и их следует избегать. Трубы должны быть достаточно жесткими, чтобы не пережиматься под атмосферным давлением. Трубы для системы омывания автомобильных стекол подходят.
Эти трубы имеют внутренний диаметр 4 мм. Так же должна быть и вся фурнитура.
В качестве газового баллона можно использовать автомобильную покрышку. Джаррод Кинси, также известный поклонниками лазеров, использует воздушный шар для вечеринок.
http://www.flickr.com/photos/12049698@N02/4610061580/in/set-72157624001202153/
(также см. поиск в Google с ключевой фразой «со2-лазер, человеческое дыхание»)
Сухой углекислый газ можно получить из СО2-картриджей для ариганов. Также хорошо подходят огнетушители. Самый простой способ залить картридж — использовать домашний сатуратор.
В древности существовало устройство для приготовления содовой воды в домашних условиях. Он назывался «сатуратор». В наше время трудно найти. Как вариант, можно надеть на ствол пневматического ружья трубу и в крайнем случае надуть необходимое количество газа. Более продвинутый прием – зажать курок в нажатом положении и плавно высыпать патрон. В зависимости от модели пневматического оружия может потребоваться заделка протечек пластилином. В любом случае игры со сжатыми газами не самое безопасное действие в мире. Если Вы ребенок, Вам следует посоветоваться со взрослыми, как все делать правильно и безопасно.
Зеркало заднего вида можно приобрести в автомагазине. Не все зеркала одинаково хороши. Три условия:
- Зеркало должно быть слегка выпуклым. Слишком выпуклые зеркала не подойдут.
- Зеркало должно легко разбираться. А слой краски на его обратной стороне должен легко сниматься.
- После удаления краски должно остаться гладкое глянцевое алюминиевое покрытие. (Вместо этого некоторые зеркала имеют матовое покрытие.) После этого металлическая сторона зеркала теперь будет его лицевой стороной, а стеклянная сторона — задней. Здесь выпуклое зеркало становится вогнутым.
Используя эмпирический метод, выберите подходящее зеркало. Как этот:
С помощью стеклореза или алмазного диска отрежьте от него квадратные кусочки. Они должны быть размером примерно 20х20 мм. Просверлите некоторые из них алмазным сверлом для отверстий диаметром 3 мм в центре. Лучше делать сразу несколько пар зеркал, потому что велика вероятность поломки при сверлении и снятии краски.
Поместите зеркала в герметичную банку и покройте слоем растворителя. Обычно лучшим является дихлорэтан, но иногда он загрязнен соляной кислотой и также удаляет слой алюминия. Ацетон действует медленнее (на удаление покрытия уходит несколько дней). А в самых запущенных случаях надо пробовать тип растворителя.
Рекомендуется выбирать лучшие зеркала. В солнечную погоду возьмите зеркальце (касайтесь только краев! НЕ касайтесь алюминиевого слоя!) и направьте отражение солнца на стену. Изменяя расстояние между стеной и зеркалом, найдите точку фокусировки (когда изображение солнца станет четким). Если изображение солнца слишком вытянутое (эллиптическое), выбросите зеркало. Если изображение слишком тусклое (по сравнению с тем, что дают другие зеркала), выбросьте и его. Также Вы должны удалить те, которые дают изображение с ясно видимым диффузным ореолом. Фокусное расстояние обычно составляет около 1,5…2,5 метра. И среди 3..4 штук Вы обязательно найдете хорошую. Процесс изготовления и подбора зеркал довольно скучный, но это ничто по сравнению с попытками отполировать зеркало из медной монеты или попытками нанести серебряное покрытие на линзы очков.
Катушка зажигания не должна быть электрически слабой. Не используйте мотоциклетные или от легковых автомобилей. Если у Вас есть пара катушек, то лучше.
Лазер для выравнивания Он-Не типа. Однако она имеет сомнительные преимущества по сравнению с обычной лазерной указкой, поскольку нет необходимости производить юстировку по интерференционным кольцам. Выбирая указку в качестве юстировочного лазера, обратите внимание на срок службы ее батарейки. Лучше найти с адаптером питания. Слишком мощные (>10 мВт) зеленые указатели вызывают резь в глазах после выравнивания, поэтому используйте разумную мощность.
По крайней мере, мы закончили с ресурсами. Смотрим дизайн.
4. Конструкция лазерной трубки
Конструкция лазерной трубки показана на рисунке выше. По сути, это стеклянная трубка, вклеенная между двумя концами (узлами юстировки). Склеивание производится клеевым пистолетом (термоклеем), с лучшей стороны он показал себя при вакуумной герметизации. Утечки в лазере возможны, но нежелательны. Во-первых, они мешают сохранению известного состава смеси. Вот конструкция узла выравнивания:
Если у Вас есть удобные фланцы с ортогональными трубами соответствующего диаметра, используйте их, не утруждайте себя изготовлением фланцев самостоятельно. Однако ничего подходящего в ассортименте у меня не оказалось, поэтому после двухнедельных поисков я сказал несколько избранных слов и сделал фланцы сам. Я использовал эпоксидную смолу, усиленную лентой и лентой в виде елочки.
Крепления для зеркал изготовлены из алюминиевого листа толщиной 4 мм. Подойдет и твердый пластик (например, плексиглас), но он должен быть толще. В качестве уплотнителя (и в качестве упругого элемента) использовалась резиновая шайба соответствующего диаметра. Других пружин не предвидится.
Регулировочные винты с резьбой M4. Гайки приклеены эпоксидной смолой для фиксации. Если вы можете надежно закрепить гайки М3 (например, используя металлические фланцы и гайки запрессованы), то вы можете уменьшить диаметр узла центровки примерно до 50 мм. Для М4 оптимально 80..100 мм.
Впускной и выпускной трубопроводы также размещаются на узлах центровки. В принципе можно просверлить стеклянную трубку и вклеить в отверстия трубки, это только по желанию.
Электроды изготовлены из толстой алюминиевой фольги (или тонкой пластины). Толщина 300 мкм. Полоска этой фольги свернута в виде рукава с таким диаметром, чтобы между ней и стенками стеклянной трубки был минимальный зазор.
Электрические клеммы выполнены из медной проволоки без покрытия. Их приваривают (не приклеивают, не припаивают) к гильзам электродов. Сначала клеммы должны быть достаточно длинными (30 см и более). Диаметр проволоки — дело выбора. Нет 23..30 AWG будет хорошо. При использовании цельнометаллических центровочных блоков, вероятно, оптимально использовать их в качестве электродов.
Подсказка по сборке. Вставьте алюминиевую втулку электрода с уже закрепленными проводами в стеклянную трубку. Затем (вот зачем длинная проводка) проденьте провод через отверстие (специально просверленное для него в корпусе узла центровки). Затем смажьте конец стеклянной трубки клеевым пистолетом и, пока он не застыл, вставьте стеклянную трубку на место. Во время этого процесса нужно постепенно вытягивать проводку. (Следите за тем, чтобы не вытащить алюминиевую втулку из стеклянной трубки.) Когда стеклянная трубка будет приклеена на место, загерметизируйте также клемму провода.
После того, как оба узла юстировки установлены и собраны, вместо зеркал приклейте тонкие прозрачные пластиковые заглушки. Вырежьте их, например, из обложки компакт-диска. Зеркала пока рано ставить.
Давайте проверим утечки. Откачайте трубку и пережмите впускной и выпускной патрубки. Если у Вас есть вакуумметр, то следите за давлением. Трубка должна протекать не более 20 торр в час. Это приемлемо. Если у Вас нет вакуумметра, но блок питания собран, Вы можете по нему судить об утечках. Выделения в трубке должны сохранять свой вид и цвет в течение разумного времени. (Несколько десятых минут, если это тлеющий разряд низкого давления со слоями, и несколько часов, если это контрактный разряд высокого давления).
Если течет трубка, то отсоединяем ее от вакуумного насоса, и идем в ванную искать течь типичным гаражным методом, накачиваем, опускаем в воду и наблюдаем за пузырьками. Не прилагайте больших усилий при сцеживании. Трубка выдерживает давление 0,5 бар. Поднимите давление выше, и Вы, вероятно, сломаете крепления зеркал, сорвете шайбы или стопоры. Избегайте воды внутри трубки. Вытащить его оттуда будет сложно.
Когда избавились от протечек Можно заклеить зеркала. Клеить их придется без протечек, т.к. купание собранного лазера — плохая идея. Вы можете использовать только сухие методы для проверки на утечку, поэтому Вы будете знать, что есть утечка, но не будете знать, где она находится. Первым делом приклейте заднее зеркало на место. Если протечет, отсоедините и приклейте обратно. Затем приклейте переднее зеркало и полиэтиленовую пленку поверх него. Проверьте еще раз на наличие утечек. В случае протечки отсоедините и приклейте обратно.
Вот так выглядят собранные узлы центровки:
5. Блок питания
Вот схема блока питания:
Лампа галогенная R1 500 Вт 220 В
Электронный трансформатор U1 для галогенных ламп (хорошего типа Feron, но можно использовать и другие типы) мощностью 250 Вт
Тр1 намотан на основном сердечнике от другого электронного трансформатора для галогенных ламп того же типа, что и предыдущий. Первичка — 4 витка проводом №18..19 AWG. Вторичная 200 витков проводом №28..29 AWG. (Внешний трансформатор используется только для того, чтобы не мешать внутренностям электронного трансформатора. Если Вы не стесняетесь радиотехники, то можете просто доработать трансформатор внутри электронного трансформатора под необходимое выходное напряжение)
R2 86 Ом (спираль чашечного бойлера 500Вт)
Диоды VD1, VD2 HER308
С!, С2 электролитический 10 мкФx450В.
С3 керамический или фольгированный типа 2000 пФ не менее 2 кВ номинальное.
Тиристор SCR1 на 1100 В и 20 А
Низковольтный разрядник СГ1 на 250В (например, НС2Р-250-А1), вместо него можно использовать подходящий динистор, но вам потребуется правильно доработать схему,
С3, С4 металлобумажные 10 мкФх1000В.
Тр2, Тр3 две катушки зажигания, соединенные последовательно.
Резистивный делитель R3, R4 следует подобрать так, чтобы разрядник SG1 срабатывал при заряде С3 и С4 напряжением 700. .800 Вольт. (R4~100 кОм, R3~300 кОм)
Целью схемы является зарядка конденсаторов C3 и C4 (всего 20 мкФ) до 750 Вольт, а затем их быстрая разрядка через первичные обмотки катушек зажигания. И повторять это много раз в секунду. Любая схема, которая может это сделать, может быть использована в качестве драйвера лазера. Также следует отметить, что выход схемы может быть выполнен с одной катушкой, но он будет менее стабильным при более высоких напряжениях (одинарная катушка легче ломается), поэтому вы будете ограничены при более низких давлениях в лазерной трубке.
Правильно работающий силовой агрегат дает искру длиной ~4 дюйма с частотой повторения около 10 Гц. Искра жирная с сильным, но мягким звуком. Шоу довольно страшное.
Выходное напряжение выбрано достаточно высоким ~100 кВ, чтобы обеспечить пробой лазерной ячейки при сравнительно высоких давлениях (до 80. .100 Торр). Конечно, это не оптимум. Если вас интересует только выходная мощность и у вас есть хороший вакуумный насос, то остановитесь на ~30..40 кВ. OTOH, если все, что у вас есть, это старый компрессор холодильника, выход 100 кВ — ваш последний шанс.
Силовой агрегат следует включать с безопасного расстояния. И когда он включен, не подходите близко к нему или любым частям лазера, находящимся под напряжением. Теоретически блок питания отсоединен от земли и нет тенденции к пробоям в подающие трубы корыта насоса, но настоятельно рекомендуется, чтобы длина каждой трубы была более 5 футов Просто для ухода.
При кратковременном ударе током такая силовая установка обычно не может убить человека (но вообще никаких гарантий, все зависит от состояния здоровья), но травмы будут тяжелыми. Как правило, сокращение мышц повреждает кости и зубы. Представьте себе шокер в сто раз более мощный, чем самый мощный из тех, что Вы когда-либо видели в магазине. Это сравнимо с мощностью данного агрегата. Так что пожалуйста будь осторожен . Всегда помните, что запрещено не только прямое прикосновение, но и очень рискованно даже приближаться к каким-либо частям, находящимся под напряжением. Вас может ударить искра.
6. Мировоззрение
Для простоты лазер имеет стабильный резонатор. Его зеркала фокусируются. Там радиус (удвоенное фокусное расстояние) больше, чем расстояние между зеркалами. Это означает, что полость, образованная такими зеркалами, заведомо попадает в область устойчивости. Без соответствующих знаний не используйте выпуклые зеркала или слишком прочные вогнутые. Нестабильные резонаторы слишком сложны для любителя. В принципе выходное зеркало может быть плоским. Он слегка фокусирует выходной пучок и упрощает получение рисунков луча на копировальной бумаге. Однако он хорошо работает только с полупрозрачным выходным зеркалом. Когда выходное зеркало металлическое с соединительным отверстием, проще говоря, более тонким лучом труднее попасть в отверстие, лазер будет сложнее настроить.
Юстировка производится типичным для всех лазеров способом путем перекрытия пятен лучей, отраженных передним и задним зеркалами.
Однако есть некоторые детали, на которые следует обратить внимание:
- Юстировка должна производиться в вакууме (иначе неизвестно, куда пойдет луч, когда на центрирующие опоры будет подаваться давление воздуха).
- Регулировка заднего зеркала должна производиться при снятом переднем зеркале. Производить выравнивание, просовывая брус через стяжное отверстие, это то же самое, что вешать обои через замочную скважину. Лазер должен быть плотно закреплен, чтобы не нарушить настройку при монтаже и демонтаже зеркал.
- Во время юстировки все трубы и провода должны быть уже подключены к лазеру. ( ВЫСОКОЕ НАПРЯЖЕНИЕ ДОЛЖНО БЫТЬ ОТКЛЮЧЕНО !!! ) В противном случае легко сорвать всю настройку при подключении всех коммуникаций к лазеру.
Выравнивание производится в три этапа.
- Проведение юстировочного лазерного луча через трубку юстируемого лазера (или, если у Вас есть подвижные фиксаторы трубки, Вы можете надеть трубку на луч, это проще)
- Установка и настройка заднего зеркала
- Установка и настройка переднего зеркала
После завершения юстировки не снимайте юстировочный лазер, он покажет Вам, куда идет невидимый инфракрасный луч нашего CO2-лазера.
Строительный уровень удобен для использования в качестве юстировочного лазера. Его штатив позволяет легко регулировать высоту и угол наклона лазера (ну, по крайней мере, он для этого предназначен).
На лицевую сторону юстировочного лазера следует наклеить лист бумаги с отверстием 0,3-0,5 мм. Бумага будет служить экраном, где Вы будете наблюдать отраженный луч. Очевидно, что отверстие должно располагаться над выходным лучом юстировочного лазера. Когда диаметр отверстия меньше диаметра выравнивающего луча, это помогает сделать луч «чище». Для наклеивания бумаги используйте пластилин или жевательную резинку, это позволяет перемещать бумагу в определенном диапазоне для лучшего совмещения отверстия и луча.
- Починить лазер CO2. Снять торцы с зеркалами (для этого открутить юстировочные винты). Поместите юстировочный лазер на расстоянии 4-5 футов от юстируемого лазера. С помощью всех подручных средств и известной мамы сделайте юстировку луча, чтобы он проходил вдоль оси трубки СО2:
Луч не должен касаться стенок трубы. Удары запрещены. - Прикрутить на место пластину с задним зеркалом (разумеется, с ее омывателем).
Совет: шайбы следует приклеить к креплениям зеркал резиновым клеем. После этого они не будут опускаться в самый момент.
Вместо переднего зеркала возьмите прозрачную плоскость и наклейте на передний уплотнитель. Не нужно клеить, он будет хорошо всасываться давлением воздуха. В качестве временного окошка можно использовать кусок пластика от крышки CD-бокса.
Выкачать воздух из лазера. Нет необходимости достигать высокого вакуума, потому что силы, вызванные атмосферным давлением, почти одинаковы для высокого вакуума (скажем, 0,1 Торр) и для низкого вакуума (скажем, 70 Торр).
Поворачивая регулировочные винты, совместите прямой и отраженный лучи. (Заставьте отраженный луч попасть в отверстие в бумаге, из которого выходит луч выравнивания). Снова избегайте ударов луча о стенки трубы.
Подсказка: когда трубка все еще содержит люминесцентный слой, легче увидеть, когда юстировочный луч попадает на ее стенку и где это происходит.
Действуйте осторожно, чтобы не сломать достигнутые настройки.
Пусть воздух войдет в трубку. Наблюдайте за отраженным пятном выравнивания. При правильном выполнении почти не смещается при изменении давления. Если он смещается более чем на 1/10 дюйма, повторите процедуру юстировки с более тугим завинчиванием юстировочной пластины.Если Вы не можете стабилизировать выравнивание, увеличивая усилие на установочных винтах, замените уплотнительную шайбу на более жесткую.
- Снимите временное окно и прикрутите пластину с выходным зеркалом. Снова откачайте воздух и настройте юстировочные винты, чтобы прямой и отраженный лучи совпадали.
Вот специальности:
- для направляющего луча переднее зеркало выпуклое и рассеивает луч.
Таким образом, вы должны направить центр этого большого рассеянного пятна на отверстие в бумажном экране. - Луч может либо полностью падать через соединительное отверстие в лобовом стекле (и отражения нет вообще), либо часть луча падает через отверстие, и трудно сказать, где находится центр этого асимметричного отраженного пятна.
Желательно, чтобы юстировочный луч в своем сечении вблизи переднего зеркала имел диаметр, несколько превышающий диаметр соединительного отверстия.Если затем юстировочный луч равномерно облучает отверстие, то отраженный узор представляет собой простое круглое темное пятно, окруженное круглым светлым ореолом. В этом случае Вам необходимо направить центр этого темного пятна (тень соединительного отверстия) на отверстие в бумажном экране.
Если юстировочный луч облучает соединительное отверстие асимметрично, Вам следует либо искать центр отраженного рисунка, используя Вашу интуицию, либо пересматривать юстировку с самого начала с правильным размещением юстировочного лазера.
Однако не бойтесь процесса выравнивания. Лазер хорошо работает, когда пятна лучей, отраженных передним и задним зеркалами, смещены друг относительно друга на 1/3’’..1/2’’ (когда бумажный экран находится на расстоянии 2,5 фута от лазера). Это достаточно грубо, чтобы почти не заботиться о выравнивании. Именно для этого прощения мы выбираем стабильный тип полости.
Если не перемещать лазер с места на место, а просто держать его на том месте, где он был настроен, то юстировка стабильна в течение нескольких дней.
7. Газовая смесь
1:1:9 идеальная смесь для непрерывного лазера низкого давления (первая цифра — концентрация CO2, вторая — концентрация азота, а третья — содержание гелия. Все части объемные). Однако гелий скорее трудно получить в домашних условиях. Торговые рейды за праздничными воздушными шарами определенно надоедают. Чистый азот получить еще труднее. Все известные способы его получения требуют химических веществ, которые, в свою очередь, трудно достать. Можно сказать, почему бы просто не купить газовые баллоны или баллоны с сжиженным газом? Только представьте: Вам четырнадцать лет, Вы учитесь в школе и Ваши родители не очень любят Ваше лазерное увлечение. Вам повезло, если «дядя Боб» работает на местной заправке и является Вашим другом. Если нет, то застой.
Чтобы не держать его дольше: первый успех в генерации этого лазера был с почти чистым углекислым газом из патронов пневматического оружия CO2. Газ был загрязнен в основном воздухом, оставшимся в трубах и трубках. И содержание воздуха было менее 10%. Он составлял около 1 мДж в импульсе, что дает 10 мВт при частоте повторения 10 Гц. (Довольно низко, но достаточно, чтобы увидеть по показаниям калориметра.)
Пока не удалось разжечь «камеру сгорания».
Генерировать известную из литературы смесь co2:воздух 1:5 пока не удалось.
Пока не удалось получить СО2 из пищевой соды с лимонной кислотой (видимо газ требует осушки)
Наибольшую мощность среди простых смесей дает co2:воздух 2:1 (около 3 мДж в импульсе)
Более сложной является смесь СО2:сухой воздух:влажный воздух (сухой воздух берется из атмосферы при низкой влажности воздуха, влажный воздух можно вдыхать прямо из легких). Эта смесь дает около 7 мДж в импульсе.
Имейте в виду, что кислородсодержащие смеси быстро разлагаются из-за накопления оксидов азота. При частоте 10 Гц мощность падает дважды примерно за две секунды. Поэтому устойчивая генерация на смесях с высоким содержанием кислорода возможна только в проточном режиме. Однако смесь дешевая и скорость ее расхода невелика, так что заморачиваться не стоит.
Интересные результаты получены со смесью co2:»камера сгорания» 1:1 2:1. Сначала смесь быстро разлагается (от ~5 мДж в импульсе до 2..3 мДж в импульсе через несколько минут), а затем долго работает стабильно (несколько часов, может быть и больше, но я не проверял). т.е. ресурс этой смеси в герметичном режиме сравним со временем загрязнения из-за негерметичности трубок.
«Камеру сгорания» можно было сделать следующим образом. Смочите вату в спирте, положите ее в маленькую лодку и отправляйтесь в плавание. в ванной. Подожгите его и накройте стеклянной (не пластиковой!) банкой. Затем подождите, пока кислород воздуха под банкой не выгорит. Странно, но уменьшенный объем газов в банке (измеряемый уровнем поверхности воды в банке) хорошо отвечает полному сгоранию кислорода (на самом деле это прямо противоположное свидетельство: из банки выбрасываются пузырьки горячего газа, так что если горение полный объем оставшихся газов должен быть МЕНЬШЕ 80% от начального объема воздуха. ) После окончания горения используйте тот или иной способ получить газовую смесь из банки (предположительно смесь N2, CO2, CO и неприятных загрязнений ) в емкость для газовой смеси. «Камера сгорания» не работает сама по себе, но при разбавлении дополнительным сухим CO2 может в некоторой степени работать как заменитель азота.
Способы смешения газов и способы их перекачки из сосуда в сосуд — свободная область для Вашего творчества. Имейте в виду, однако, что достаточно пропустить через воду газ хотя бы один раз, чтобы газ захватил водяные пары до полного насыщения. Иногда это полезно (например, для влажных смесей), но в других случаях дает совершенно неработоспособную газовую смесь.
Еще одно замечание: когда смесь приготовлена, Вы, вероятно, захотите сохранить подходящий объем для использования в будущем. — Не. Как показывает опыт, единственным способом хранения смеси является хранение ее в чистом и герметичном газовом баллоне. Внутри шины смесь наполовину застывает в течение недели. Воздушные шары делают еще хуже. Итак, будем считать, что газовая смесь не предназначена для хранения, и каждый раз, когда мы используем лазер, мы готовим свежие смеси.
8. Первый свет. (Охота на лазер.)
Веселое начало! Итак, давайте предположим, что трубка собрана и выровнена. Блок питания собран, настроен и подключен к лазерной трубке. Вакуумный насос готов и также подключен. Газовая смесь готовится и ждет своего часа внутри шины или баллона. Батарейка в измерителе мощности калориметра свежая.
Поместите датчик калориметра Пельтье так, чтобы юстировочный луч попадал на его теплоотвод точно напротив центра его чувствительной области. Включите его мультиметр и дождитесь стабилизации показаний.
Все готово к старту.
впускной патрубок (та, которая соединяет сосуд газовой смеси с лазерной трубкой)
Откачайте воздух из трубки до максимально возможного вакуума.
выхлопная труба (та, что соединяет вакуумный насос с трубкой)
Аккуратно отпустив впускной патрубок, пропустите газовую смесь в трубку.
впускной патрубок.
Эвакуируйте снова. (Конечно, вам нужно освободить выхлопную трубу, чтобы иметь возможность откачивать.)
Это процедура стирки. Если ваш максимальный вакуум менее 1 торр, то достаточно одного цикла промывки. При слабом насосе повторите циклы стирки несколько раз.
Снова впускаем газ, впускной патрубок и плавно отпуская выпускной патрубок ловят давление, когда силовой агрегат уже может производить искру в патрубке. Если у Вас есть вакуумметр, поразите диапазон давления 60..80 торр. Без манометра периодически включать блок питания на короткое время и откачивать до тех пор, пока внутри трубки не появятся искры.
При высоких давлениях искра в трубке змеится. Вот как это выглядит:
Некоторые смеси (частично чистый СО2) уже генерируют при таких давлениях. Однако сила слишком слаба.
При достижении пробоя в трубке блок питания можно безопасно включить на длительное время (искра ограничивает его выходное напряжение и снижает вероятность внутренних пробоев в катушках зажигания). Включите силовой агрегат и продолжайте снижать давление (впускная труба закрыта, выхлопная труба разблокирована.)
Когда искра становится прямой и начинает медленно увеличиваться в диаметре, давление обычно соответствует максимальной мощности генерации (~20 Торр)
При дальнейшем снижении давления разряд становится диффузным и энергия генерации плавно снижается.
При более низком давлении сопротивление разряда уменьшается, что приводит к уменьшению полезной (вводимой в газ) части полной энергии разряда. При этом основные потери составляют джоулевые потери на сопротивлении катушки зажигания. При ~5 торр энергия падает настолько сильно, что становится ниже погрешности калориметра.
Узнайте, как поймать необходимое давление при отпущенной выхлопной трубе. (Однако при сильном накачке может потребоваться оставить трубку слегка вздутой.) Следите за давлением по вакуумметру или по форме и цвету искры. Когда Вы достаточно опытны в поддержании правильного давления при непрерывной откачке и подсосе, Вы можете использовать лазер в режиме газового потока. В этом режиме можно использовать быстроразлагающиеся смеси (содержащие воздух).
Ориентируясь на показания калориметра, найдите режим, при котором выходная мощность наибольшая. Варьируйте общее давление в трубке и скорость просачивания газа. Научитесь поддерживать этот режим в течение длительного времени.
При определенном опыте Вы сможете определить нужный режим, наблюдая за формой и цветом выделений. Когда закончите, вы можете попробовать заменить калориметр другими мишенями. Например. копировальная бумага или вогнутое зеркало с чем-то в фокусе.
За радикальное увеличение мощности:
- Подберите оптимальную для Ваших условий газовую смесь и ее оптимальное давление.
- Найдите напряжение пробоя для Вашего давления и смеси.
- Построить новый блок питания для выбранного напряжения и для более высокой частоты повторения.
(Энергия в накопительных конденсаторах может варьироваться в зависимости от смеси и давления, но обычно она должна быть более 2 Дж для этого размера трубки. Поскольку вы не можете изменить коэффициент обмотки катушки зажигания, только один способ изменить выходное напряжение — это изменение напряжения на накопительном конденсаторе с соответствующим изменением его емкости.)
9. Некоторые данные, интересные для домашних CO2-лазеров конструкции
Вот результаты моих измерений некоторых подручных материалов (извините за большие ошибки, но sic. ):
Материал | Коробка передач для 10,6 мкм |
---|---|
Крышка Банка Pringles (прозрачный полиэтилен толщиной ~1 мм) | Около 10%. Передача очень заметна, но ниже порога измерения. |
Полиэтилен бытовой мешок (измеренная толщина ~20 мкм) | 9010% |
Тефлоновая лента (измеренная толщина ~20 мкм) | 8010% |
Резиновая сторона баллон (надутый до общего уровня), прохождение через обе стенки | 6015% |
плавиковый шпат оптика (линза) толщиной 1 мм | 3010% |
Майларовая фольга, 100 мкм толщиной | Менее 10% (передача незаметна) |
Ацетатная фольга, 100 мкм толщиной | Менее 10% (передача незаметна) |
Майларовая фольга, 10 шт.![]() | Менее 10% (передача незаметна) |
Прозрачная упаковка Скотч | Менее 10% (передача незаметна) |
Полистирол Толщина 1,2 мм (крышка CD-бокса) | Менее 10% (передача незаметна) |
Во время измерений калориметр находился на расстоянии 2..3 фута от образца, поэтому измерялось направленное пропускание (все рассеяние на большие углы считалось потерями). По-видимому, мутность и мутность образцов полиэтилена и тефлона не имеет значения для пропускания излучения СО2 в диапазоне погрешностей. Однако прозрачные образцы более удобны в качестве окон, так как при меньшем рассеянии красного луча проще производить юстировку.
Возможно Вы уже думаете о лазере с полиэтиленовыми окошками на концах трубок. Вот данные о влиянии пластиковых пленок на генерацию при их размещении между зеркалами (внутри резонатора). Это было измерено на аналоговой системе, но с зеркалами, отсоединенными от концов трубы. Трубка имеет полностью такую же конструкцию, но с одним отличием: ее концы закрыты не центрирующими креплениями, а окнами Брюстера KCl.
Испытания проводились со смесью CO2:воздух 2:1 в режиме газового потока. Образцы пленки располагались ортогонально оси резонатора (имею в виду не под углом Брюстера), а также пленки слегка потрепывались. Никаких особых усилий, чтобы сделать их прямыми и гладкими, не прилагалось.
Образец | Потеря мощности генерации % от максимума |
---|---|
Полиэтилен, 20 мкм 1 слой | Без сокращения наблюдаемый |
Полиэтилен, 20 мкм 2 слоя | Без сокращения наблюдаемый |
Полиэтилен, 20 мкм 4 слоя | 20% |
Тефлон, 20 мкм 1 слой | Без сокращения наблюдаемый |
Тефлон, 20 мкм 2 слоя | 20% |
Тефлон, 20 мкм 3 слоя | 50% |
Тефлон, 20 мкм 4 слоя | сбой генерации |
Два вывода:
- Полиэтилен и тефлон можно использовать в качестве внутриполостных окон, если длина трубки достаточна для компенсации потерь.
Тефлон более устойчив к температурным нагрузкам, а полиэтилен более устойчив к механическим нагрузкам (по крайней мере, так говорит мой опыт). Тефлон толщиной 20 мкм, естественно, не выдерживал вакуумных нагрузок при диаметре отверстия более 3 мм. Слишком низко для полномасштабного окна, но, вероятно, подойдет для закрытия соединительных отверстий в передних зеркалах, когда Вы планируете делать трубу, рассчитанную на довольно большую мощность. В остальном полиэтилен 20 мкм выдерживает вакуум при диаметре отверстия до 6 мм, так что если у Вас такая тонкая трубка, на ее концы вполне можно поставить полиэтиленовые окошки.
- Также полученные данные можно использовать для грубой оценки коэффициента усиления лазера. Он составляет около 0,5% на сантиметр. (Подробности о том, как была сделана эта оценка, см. в русскоязычной версии этого руководства.) Да, она сравнительно низкая даже в импульсном режиме. Для сравнения: в научной литературе для того же лазера в хороших условиях с чистой и оптимальной смесью упоминаются коэффициенты усиления около 1.
.1,5% на см для непрерывного режима и 3..4% на см для импульсного режима.
Так как даже в импульсном режиме у нас небольшой коэффициент усиления, я бы сказал, что пытаться уменьшить длину трубки рискованно. Для правильного расчета минимальной длины трубы необходимо знать потери на зеркалах. Однако точность моих измерений слишком мала, чтобы их увидеть. (Я могу оценить описанное отражение алюминиевого зеркала где-то между 90% и 100% для 10,6 мкм, но это все, что я могу сказать.) В худшем случае это означает, что трубка длиной 20 см будет находиться на самом пороге генерации. Но для любителей я бы рекомендовал выше 40 см.
10. Опять же, почему не ЧАЙ?
Лазер атмосферного давления с поперечным разрядом слишком сложен. Но даже не в его дизайне. У него слишком много параметров, чтобы их можно было изменять. Состав смеси, давление, время нагнетания, импеданс питающего контура Это очень неполный их перечень. Например. мой первый самодельный TEA-лазер заработал почти полгода, с тех пор как я научился получать стабильный объемный разряд.
Импульсный продольный лазер значительно проще. Корней зла всего два: неправильная смесь, неправильная центровка (при условии, что утечек уже нет). Проблемы с выравниванием значительно уменьшаются за счет стабильного резонатора (вогнутые зеркала), поэтому почти все проблемы возникают только с газами.
Когда газы, зеркала и другие вспомогательные проблемы будут решены с помощью такого лазера, можно смело приступать к сборке ТЕА.
<< ГЛАВНАЯ СТРАНИЦА
Как сделать самодельный лазерный резак
Все мы знаем о возможностях лазерного резака , и тем более, когда нам нравится делать что-то своими руками. Эти типы лазерных резаков довольно дороги, и иногда их может разрешить только профессионал, который их амортизирует. Однако есть способы создать собственный лазерный резак, и именно об этом мы расскажем в этом новом руководстве. С его помощью мы можем построить свой собственный и сэкономить несколько евро, а также повеселиться и получить удовольствие от того, что создали его сами.
Лазерный резак может резать или вырезать метки на определенных поверхностях , что весьма практично для некоторых проектов. Тем не менее, это машина, с которой следует обращаться осторожно из-за ее опасности, поэтому мы должны принять соответствующие меры предосторожности при обращении с ней, поскольку мы используем инструмент, который может вызвать проблемы, если мы не соблюдаем меры безопасности.
Содержание
- 1 Способы иметь собственный лазерный резак:
- 1.1 Проекты по созданию лазерного резака с нуля
- 1.1.1 Проект 1: CO2-лазерный резак с нуля с помощью Match4
- 1.1.2 Проект 2: лазерный резак с Arduino
- 1.2 Использование наборов для сборки лазерного резака
- 1.
2.1 Метрк:
- 0 1.2.1 .2 Self-victory:
- 1.2.3 Moracle:
- 1.2.4 Qiilu:
- 1.2.5 TOPQSC Bachin
- 1.2.6 KKmoon:
- 1.
- 1.1 Проекты по созданию лазерного резака с нуля
One way is to buy a cutter, but как я уже сказал, цены обычно высоки, и это лишает возможности создавать их самостоятельно. Поэтому мы собираемся сосредоточиться на указании других способов, которыми мы должны построить наш собственный лазерный резак, хотя я уже предполагаю, что это будет не простой проект «сделай сам», если мы решим создать его с нуля …
Проекты по созданию лазерного резака с нуля
Один из вариантов, который у нас есть, это создание собственного лазерного резака с нуля , но это довольно сложная задача, и мы можем столкнуться с некоторыми ограничениями или проблемами при ее работе. правильно. Поэтому этот вариант подходит только для экспертов или более продвинутых производителей. В пределах этих возможностей мы можем создать свой собственный дизайн или взять идеи из некоторых существующих проектов, которые были проверены и работают.
Проект 1: лазерная резка CO2 с нуля с помощью Match4
InventorsFactory взяла на себя задачу создать фантастический проект потрясающего самодельного лазерного резака . Он основан на довольно сложной модульной конструкции и подробно описал все в своем блоге. Лазерный гравер или резак позволяет достаточно точно двигать головкой и имеет большое количество планов и деталей для тех, кто захочет его воспроизвести. Вы можете выполнить шаги здесь:
Введение
Часть 2
Часть 3
youtube.com/embed/i_cpKHRltLs?feature=oembed» frameborder=»0″ allow=»accelerometer; autoplay; encrypted-media; gyroscope; picture-in-picture» allowfullscreen=»»/>Часть 4
Проект 2: лазерный резак с Arduino
Другой известный блог в мире DIY — Instructables, и оттуда мы получаем еще один проект по созданию резака или лазерного гравера с нуля, используя плату Arduino и некоторые очень простые элементы, такие как лазерный модуль мощностью 1,8 Вт с длиной волны 445 нм. В частности, это проект 16-летнего бельгийского мальчика, известного как MichielD9.9. Ему потребовалось около трех месяцев, чтобы спроектировать и построить эту машину, но с шаблонами и информацией, которые он предлагает, вы сможете сделать это намного быстрее.
- Пошаговое объяснение
Кстати, на Kickstarter есть проект ZelosLaser лазерного гравера/резака с ЧПУ , сделанный на бесплатном оборудовании, аналогичном этому, который также может вас заинтересовать.
Использование комплектов для сборки лазерного резака
Другой вариант лучше всего подходит для большинства пользователей и состоит в использовании комплектов которые уже подготовлены так что все работает если сборка адекватная. Нам нужно будет только ограничиться выполнением шагов сборки, и у нас будет готовый к использованию лазерный резак или гравер. Стоят они от €95 до чуть более €300, так что это вполне доступные цены по сравнению с профессиональным лазерным резаком.
Если вы хотите узнать , какие комплекты для лазерной резки или гравировки лучше всего Вот список с нашим выбором:
Метка:
Это один из самых продаваемых станков для лазерной гравировки или резки. Имеют мощность лазера 1500 мВт , Bluetooth, USB-соединение, многоязычную поддержку и возможность гравировки на различных материалах, таких как кожа, бамбук, дерево, пластик, картон, интегральные платы и т. д. Он также имеет литий-ионный аккумулятор емкостью 6000 мАч. Ионный аккумулятор, который дает ему довольно хорошую автономность.
Предлагает совместимость с различными операционными системами, такими как Windows, Android, iOS и т. д. Его сборка быстрая и для этого не нужно больших знаний. В собранном виде он весит почти два килограмма и имеет размеры примерно 20x29x20 см.
Самостоятельная победа:
Это гравировальный станок Лазер C40 мощностью 02 Вт . Это один из самых дорогих, но он также предлагает большую мощность. Он может гравировать марки, рекламу, товары для творчества, подарки, одежду, кожу, пластиковые игрушки, обивку, компьютерную вышивку, трафаретную печать на картоне и бумажной упаковке, шнурки для обуви, деревянную мебель, изделия ручной работы и даже другие промышленные применения.
Он подключается к ПК через порт USB и поддерживает форматы TIF, BMP, JPG, WMF, EMF и PLT. Что касается сборки, то она не очень сложная и в собранном виде имеет компактные размеры. Продолжительность работы оценивается примерно в 1000-1300 часов, что позволяет работать безотказно.
Moracle:
Это еще одна машина с мощностью, равной предыдущей, также остальные характеристики очень похожи. То есть он подключается через USB и имеет СО2-лазер мощностью 40 Вт для записи на акрил, дерево, кожа , пластик, бамбук и т.д. Использование профессиональное, как и у предыдущего регистратора, но и цена его высока, как и в предыдущем случае.
Его сборка проста, как и его использование. Он также включает программное обеспечение CorelDraw с функциями NewlySeal и NewlyDraw, позволяющими использовать его для гравировки и фрезерования объектов .
Qiilu:
По характеристикам аналогичен Metek, но это лазерный гравер/резак дешевле что можно найти. Он совместим с Windows, iOS и Android и имеет приложения для управления. Он имеет многоязычную поддержку и работает через соединение Bluetooth для подключения с вашего мобильного телефона или ПК. Он дает возможность гравировать на дереве, пластике, бамбуке, резине, коже, бумаге и других подобных материалах, но не может гравировать на стекле или металле.
Что касается батареи Li-Ion емкостью 6000 мАч, она обеспечивает хорошую автономность , а также имеет блок питания, как у Metek, когда его недостаточно. Его размеры несколько компактнее, чем у Metek, так как в собранном виде он имеет размеры 16x15x20 см.
TOPQSC Bachin
Еще один набор для лазерной резки / гравировки очень интересный и минималистичный . Его цена несколько высока для того, что кажется, но он обеспечивает простую установку и эксплуатацию с ЧПУ и использованием программного обеспечения, предоставленного производителем. Скорость и мощность гравировки также регулируются, поэтому вы можете выбрать мощность в диапазоне 500-2500 мВт.
Эта необузданная мощь дает вам возможность гравировать и резать. Поддерживает JPG, PNG, DXF и другие форматы, а также совместимость для производителей, использующих MacOS, Linux и Windows .
KKmoon:
Аналогичен предыдущему набору, но здесь у нас есть 3-х осевой лазерный гравер GRBL, который позволяет гравировать на дереве, пластике разных типов, акриле и т. д. Он также позволяет фрезеровать и резать с помощью Форсунка ER11 . Его размеры несколько выше, чем у предыдущих, но он предлагает рабочую поддержку и несколько более прочную конструкцию.
Как и предыдущий, цена которого также аналогична, позволяет модулировать мощность лазера от 500 до 5500 мВт. Но в данном случае он совместим с Windows, хотя система управления с открытым исходным кодом , что понравится некоторым производителям.
Я надеюсь, что вскоре помог вам приобрести домашний лазерный резак/гравер …
5 лучших самодельных лазерных резаков и граверов, которые можно собрать дома
Когда дело доходит до покупки лазерного резака, многие люди предпочитают варианты DIY, а не предварительно собранные машины. Часто это происходит потому, что самодельные станки дешевле, но многим энтузиастам с ЧПУ также нравится создавать свои собственные станки. Но как найти лучший набор для лазерной резки своими руками?
Мы протестировали несколько лазерных резаков и граверов и сопоставили наши результаты, чтобы сформировать для вас лучшие рекомендации. Мы расскажем о различных типах, их преимуществах и принципах работы.
Сначала мы сообщим вам, как вы можете собрать свой собственный лазерный резак или гравер, со ссылками на некоторые проекты DIY, а затем мы рассмотрим лучшие комплекты лазерного гравера DIY на рынке.
VALUE PICK
Ortur Laser Master 2 Pro
Один из лучших лазерных комплектов мощностью 5 Вт
Хорошие функции безопасности и быстрая рабочая зона 30-45min
Большая 400×400 мм Рабочая зона
Доступна по адресу :
Amazon TRED TREDPremium
xtool D1 Pro
. Лучший Diy Diode Doode Lasor aryor ryl D1 Pro
. Лучший diode diode diodes diodes diodes diodes diodes diode laser ryool d1 pro
. до $700
Высококачественная стальная рама и детали
Мощность 10 Вт (с вариантами 5 Вт и 20 Вт) и скорость 400 мм/с
Доступно по адресу :
xTool здесь0263
Как следует из названия, лазерный резак своими руками — это станок с ЧПУ, который вы собираете сами, а не покупаете предварительно собранный, готовый к использованию станок. Самодельные лазерные резаки могут представлять собой наборы в разобранном виде, которые вы заказываете в Интернете, а затем собираете сами, или их можно собрать полностью с нуля, приобретая каждую отдельную деталь отдельно.
Наборы для лазерной гравировки «Сделай сам», которые можно купить
Наборы для лазерной гравировки «Сделай сам» доступны в Интернете и содержат все необходимые детали — вам просто нужно собрать машину для себя. Основная причина, по которой люди выбирают эти самодельные резаки, заключается в том, что они, как правило, дешевле, чем покупка готового к работе настольного лазерного резака, поскольку это, очевидно, экономит время производителей, а детали можно транспортировать более компактно.
Полностью самодельные лазерные резаки и граверы
С другой стороны, есть самодельные лазерные резаки, которые серьезные любители ЧПУ собирают полностью с нуля, покупая каждую деталь в разных местах, а затем собирая их вместе. Это довольно сложная задача, требующая больших знаний о том, как работают лазерные резаки, и большого опыта их использования.
Этот тип самодельного резака часто является не только увлечением, но и способом экономии денег. Мало того, что многим любителям нравится создавать машину с нуля, это также означает, что вы выбираете качество своей детали.
Эти резаки, очевидно, гораздо более индивидуальны, что является еще одной причиной, почему самодельные станки так популярны в сообществе ЧПУ. Хотите сделать огромный лазерный резак? Пока у вас есть навыки и вы можете позволить себе запчасти, все готово!
В Интернете можно найти множество примеров лазерных резаков, построенных с нуля. Например, любитель под ником MichielD99 опубликовал на Instructables подробное руководство о том, как они создали самодельный лазерный резак на углекислом газе в качестве дешевой альтернативы предварительно собранным машинам, а на OpenBuilds представлена обширная коллекция самодельных режущих плоттеров.
Программное обеспечение
Независимо от того, занимаетесь ли вы гравировкой по металлу своими руками или гравировкой по дереву, вам потребуется программное обеспечение для лазерной резки, чтобы управлять своим лазерным резаком. К счастью, есть несколько хороших вариантов с открытым исходным кодом, которые вы можете использовать бесплатно, самым популярным из которых является LaserGRBL. Это широко используется как для комплектов лазерных граверов DIY, так и для людей, собирающих машины полностью с нуля.
В качестве альтернативы LightBurn и Mach4 – популярные платные программы, с которыми совместимы большинство станков для лазерной гравировки, сделанных своими руками. Некоторые комплекты лазерных граверов DIY также поставляются с автономными контроллерами, которые позволяют использовать их без подключения к компьютеру.
TOP PICKS
Best DIY Laser Cutters & Engravers
- MathRose A5 : Very cheap pick
- Ortur Laser Master 2 Pro : Best under $500
- xTool D1 Pro : TOP PICK OVERALL & лучший до 1000 долларов США
- BobsCNC Evo 4 с надстройкой для лазера : комбинация ЧПУ и лазера
- Snapmaker 2.0 AT : Лучшее решение для 3D-печати, ЧПУ и лазерной резки
9 лучших самодельных лазерных резаков, которые можно купить 0263
Теперь давайте рассмотрим лучшие комплекты для лазерной резки с ЧПУ, которые можно купить в Интернете, а затем собрать и настроить дома.
Лазерный гравер MathRose A5 — бюджетный самодельный лазерный резак
- Цена: $289 — доступен на Amazon здесь. хороший выбор для новичков, желающих заняться сборкой станков с ЧПУ.
Одной из основных причин является модульная конструкция, которая упрощает сборку, ремонт, замену и обновление различных деталей. Фактически, вы можете построить эту машину всего за 10-20 минут.
MathRose использует мощный лазерный модуль формата A5 для точной гравировки различных материалов, от дерева и кожи до стекла и пластика. Лазер имеет срок службы 10 000 часов, поэтому он очень долговечен, даже если вы постоянно используете его в сложных проектах.
Это также лазер с автофокусировкой, поэтому нет необходимости фокусироваться вручную и рисковать сделать его менее точным. Рабочая зона большая, размером 410×400 мм, а по осям X и Y имеются точные линейные шкалы, поэтому вы можете легко измерять свои заготовки.
Этот самодельный станок для лазерной резки имеет 4-звездочный рейтинг на Amazon, что является достойным, хотя и не самым высоким.
Многие пользователи высоко оценили хорошую упаковку и четкие инструкции, которые позволяют легко собрать машину, даже если вы неопытны.
Ortur Master Laser 2 Pro — отличное соотношение цены и качества
- Цена: Проверить цену на Ortur здесь / Проверить цену на Amazon здесь
Если вы ищете недорогой, но прочный, безопасный. универсальный и высококачественный лазерный гравер «сделай сам», Ortur Master Laser 2 — отличный выбор.
Нас впечатлила скорость и простота сборки, и вы, скорее всего, сможете собрать ее менее чем за час. Вам просто нужно собрать 4 стороны, прикрепить переднюю панель, лазерную головку и подключить электронику, и вы будете готовы к резке и гравировке.
Эта машина особенно хорошо подходит для начинающих, так как крышка головки лазера защищает глаза от яркого лазера. Вы по-прежнему должны носить очки, которые поставляются с этим набором для лазерной резки, но тройная система защиты делает его отличным лазерным набором для начинающих.
Прочтите наш полный обзор: Обзор Ortur Laser Master 2 Pro
К ним относятся активная защита положения, при которой машина отключается в случае удара, защитное ограждение лазерного луча, при котором лазер отключается в случае сбоя USB-подключения, и ограничение определения продолжительности экспозиции, которое останавливает лазерный луч, если нет движения на шаговых двигателях.
Этот набор для лазерной гравировки «сделай сам» использует передовую 32-битную прошивку Ortur, которая чрезвычайно точна и проста в использовании. Он также обеспечивает диапазон мощностей от S0 до S1000; намного больше, чем диапазон 8-битных настольных граверов от S0 до S255.
Высокая мощность и точность этого станка делают его пригодным для широкого спектра различных проектов, от гравировки на акриле и резки кожи до сложной резки бумаги. Вы также можете использовать его для гравировки твердых металлов, таких как нержавеющая сталь, а также широкого спектра других материалов, таких как МДФ, фанера и силикон.
Мы использовали его для гравировки и резки более мягких пород дерева, поэтому мы не можем лично поручиться за его мастерство гравировки по металлу, но как лазерный гравер и резчик по дереву мы были очень впечатлены, когда нашли оптимальные настройки с Lightburn.
Две пробные гравировки, которые мы сделали при первой настройке машин, чтобы найти идеальные настройки лазера.Этот самодельный резак прост в сборке и имеет рейтинг 4,5 звезды на Amazon, что указывает на то, что некоторые очень довольные клиенты. Ortur также предоставляет очень полезные предпродажные и послепродажные услуги, так как вы можете получить предпродажные консультации и техническую поддержку, если у вас возникнут какие-либо проблемы со сборкой гравера. В целом, мы настоятельно рекомендуем его как недорогой набор для лазерного гравера.
xTool D1 10 Вт — лучший самодельный лазер стоимостью менее 1000 долларов
- Цена : $ 699 — Доступно по адресу xtool здесь / Amazon здесь
- Рабочая зона: 432 x 406 MM
- Power: 10W (5W и 20W и 20W.
по нашему мнению, это лучший диодный лазер и лучший самодельный лазерный гравер стоимостью менее 1000 долларов. Если вы купите его примерно за 700-800 долларов, за который он в настоящее время продается в магазине xTool, вы даже можете добавить поворотную насадку RA2 и получить 4-осевой комплект для гравировки стаканов и стаканов всего за 1000 долларов!
Вы можете сэкономить несколько сотен долларов и приобрести стандартный xTool D1 или Ortur Laser Master 2 Pro — оба являются отличными самодельными лазерами стоимостью менее 500 долларов — но мы советуем потратить на пару сотен долларов больше и выбрать xTool D1 Pro, это большой апгрейд.
Рама и детали изготовлены из высококачественной стали, с защищенными ремнями и стальными стержнями и колесами для обеспечения плавного движения и точной точности. Сборка также занимает около 30-45 минут, поэтому вы можете быстро получить гравировку после того, как получите ее.
В xTool D1 10 Вт используются два лазера мощностью 5 Вт для создания конечного результата мощностью 10 Вт с использованием той же технологии, что и в Ortur LM3 и дополнительном лазерном модуле Snapmaker мощностью 10 Вт.
Но если вам не нужна мощность 10 Вт, вы можете купить версию мощностью 5 Вт на 200 долларов дешевле и в основном заниматься гравировкой или модернизированную версию мощностью 20 Вт для однопроходной резки липы толщиной 0,6 мм или акрилового листа.
Другие доступные варианты:
- xTool D1 5W — Доступно в магазине xTool здесь
- xTool D1 20 Вт — доступен в магазине xTool здесь
Рабочая зона отлично подходит для самодельного лазерного резака — немного больше, чем у Ortur, и намного больше, чем у многих более дешевых лазеров. Вы даже можете купить в магазине xTool комплект расширения, который увеличивает рабочую область до невероятных 936 x 432 мм для огромных гравюр.
Он точен (точность 0,01 мм, размер пятна 0,08 x 0,06 мм), надежен благодаря прочной раме, стальным колесам и стержням, защищенным ремням и безопасен. Программное обеспечение XCS действительно удобно и интуитивно понятно, но вы также можете использовать его с LightBurn или через наш смартфон с приложением Laserbox.
По нашему мнению, это лучшая покупка для самодельного лазера стоимостью менее 1000 долларов.
BobsCNC Evo 4 — добавьте настраиваемые комплекты лазерных станков
- Цена: 1 230 долл. США + 300–700 долларов США за надстройку лазерного комплекта. Возможно, она наиболее известна своей серией машин Evolution, отличающихся деревянными рамами с лазерной резкой и несколько нетрадиционным дизайном, причем Evo 4 является лучшим в этой серии.
Evo 4 разработан как фрезерный станок с ЧПУ, и, в отличие от других станков в нашем списке, здесь нет возможности приобрести лазерный модуль напрямую у BobsCNC. Однако другие компании, такие как J Tech Photonics, создали совместимые лазерные модули.
Компания J Tech Photonics предлагает качественные универсальные лазерные и монтажные комплекты для Evo 4 и Evo 3. Лучше всего то, что вы можете настроить комплект в соответствии с вашими требованиями и бюджетом.
На выбор предлагается три уровня мощности — 2,8 Вт, 4,2 Вт и 7 Вт, причем более высокие уровни мощности означают большие расходы.
Вы также можете выбрать один из трех разных маршрутизаторов: Dewalt D660, Dewalt DWP611 и Makita.
Можно добавить магнитный кожух для повышения безопасности, а также линзу с высоким разрешением для более точной гравировки. Стоимость комплектов варьируется от 339,97 до 734,96 долларов в зависимости от желаемых характеристик.
С точки зрения самого Evo 4, основными преимуществами являются большая площадь резания 24 x 24 дюйма и очень хорошо спроектированная конструкция, обеспечивающая оптимальную устойчивость. Так что, если вы ищете надежный станок, который может работать и как фрезер, и как гравер, это отличный вариант.
Поскольку эта комбинация фрезерного станка с ЧПУ и модуля лазерной резки своими руками предоставляется двумя разными производителями, это решение может быть более сложным для начинающих и лучше всего подходит для более опытных любителей.
Snapmaker 2.0 — самодельный лазерный резак 3 в 1, фрезерный станок с ЧПУ и 3D-принтер
- Цена: от 1150 до 1800 долларов США уникальные и универсальные самодельные лазерные резаки, с которыми мы сталкивались.
Это потому, что это лазерный резак, 3D-принтер и фрезерный станок с ЧПУ одновременно.
Когда мы тестировали Snapmaker 2.0 A350 (самая большая версия), мы были очень впечатлены точностью гравировки, четкостью и контрастностью изображения, а также мощностью лазерного резака.
Мы также использовали дополнительный 4-осевой поворотный модуль, который позволяет поворачивать блоки материала на 360 градусов для гравировки на закругленных поверхностях. Мы выгравировали наш логотип и изображение льва на этой цилиндрической подарочной коробке, чтобы протестировать ее:
Прочитайте наш полный обзор: мы протестировали ЧПУ Snapmaker 2.0 и лазерные головки
Также имеется фантастическая функция захвата камеры, которая автоматически снимает и загружает изображение заготовки и загружает его в программу Snapmaker Luban в качестве холста. Затем вы можете легко выгравировать изображение, отображаемое в программе, одним щелчком мыши.
Одной из особенностей этой машины, которая особенно привлечет любителей делать что-то своими руками, является ее модульная конструкция.
Все порты стандартизированы, что означает, что вы можете настроить машину так, как вам нравится. Нам не довелось попробовать, но вы также можете купить более мощную 10-ваттную лазерную головку, чтобы резать фрезы, более твердые материалы и гравировать намного быстрее.
Тем не менее, мы смогли прорезать древесину толщиной около 1,5 мм с помощью стандартной головки лазерного инструмента, создав эту деревянную подарочную коробку, показанную ниже:
Это чрезвычайно популярный самодельный лазерный гравер с ЧПУ, получивший рейтинг 4,5 звезды на Amazon из более чем 100 обзоров. Не отчаивайтесь, если вы никогда раньше не работали с машиной 3 в 1 — процесс сборки занимает всего час, и это прекрасный опыт; вы можете почувствовать часы и часы подготовки, которые команда Snapmaker вложила в каждый элемент. Коробки и винты с маркировкой, модульная отвертка, с помощью которой вы ввинчиваете детали, имеет фантастический дизайн (вы поймете, когда будете ее использовать!), И все инструменты и детали кажутся высококачественными.
Этот набор для лазерной гравировки доступен в трех размерах: 160x160x145 мм, 230x250x235 мм и 320x350x330, поэтому вы можете сэкономить немного денег, если вам нужна только небольшая рабочая зона.
ЛАЗЕРНАЯ РЕЗКА СВОИМИ САМИ | Модель авиационная
Автор Фитц Уокер Используйте технологии в своих интересах Как видно из выпуска Model Aviation за июль 2020 года. Особенность
T На дворе 21 век, и мы живем в эпоху усовершенствованных, в основном предварительно собранных, готовых к полету моделей. Существует, казалось бы, бесконечное разнообразие сборных пенопластовых, композитных и деревянных самолетов, из которых можно выбирать. Я говорю «по-видимому», потому что до сих пор существует множество дизайнов, которые либо больше не производятся, либо существуют только в виде планов.
Единственным вариантом для этих моделей является сборка с нуля, особенно для тех из нас, кто до сих пор любит собирать наборы по старинке.
Это может быть полезным процессом, но он также может быть пугающим из-за объема работы. К счастью, теперь доступны отличные инструменты, такие как лазерные резаки, которые сделают этот процесс проще и веселее, чем раньше.
Использование лазера для резки бальзы не ново; однако резкое снижение стоимости станков для лазерной резки означает, что они больше не предназначены только для коммерческого использования. Машины можно найти в Интернете менее чем за 1000 долларов и даже всего за несколько сотен долларов, если вы не ищете что-то необычное. Если вы не склонны выкладывать деньги за один из них, вы часто можете найти их для использования в местном Makerspace.
Makerspace — это некоммерческий клуб, посвященный самодельщикам. Часто можно увидеть такое оборудование, как фрезерные станки с ЧПУ, токарные станки, 3D-принтеры и тому подобное (у того, что рядом со мной, есть даже кузница), но у них почти всегда есть лазерный резак. Обычно в любом мегаполисе и, конечно же, в каждом штате есть по крайней мере одно Makerspace.
Членские взносы обычно разумны и обычно включают бесплатное использование оборудования.
Теперь, когда вы знаете, где можно приобрести лазерный резак или как им пользоваться, давайте посмотрим, как вы его используете. Я построил несколько моделей с помощью лазерного резака, чтобы сделать нервюры крыльев, переборки и все, что мне хотелось. Я даже вырезал лазером детали для ремонта и замены различных ARF из дерева и пенопласта.
Меня часто спрашивают, какие процессы я использую для изготовления собственных деревянных деталей, вырезанных лазером. Этот процесс не сложный, но требует определенных шагов.
Для качественной резки вам потребуется создать так называемый векторный файл. Это очень точный формат файла, который обычно создается программой 2D CAD. Хотя большинство лазерных станков могут использовать растровые файлы (вспомните файлы изображений на основе пикселей, такие как GIF), этот тип формата плохо подходит для наших целей. Векторные изображения, с другой стороны, используют математические вычисления для создания масштабируемых рисунков, которые можно увеличивать или уменьшать, не создавая зубчатых линий.
Этот тип файла обеспечивает точные разрезы. Вам нужно будет найти подходящую программу САПР для создания вашего векторного рисунка.
Если эта перспектива вас пугает, не волнуйтесь. Процесс прост, и вам нужно всего лишь изучить несколько основных понятий для работы в САПР. Есть много вариантов программ, в том числе несколько бесплатных вариантов. Тот, который я предпочитаю использовать, называется devCad, он специально ориентирован на моделистов. Это программа для рисования только в 2D, простая в освоении и имеющая множество учебных пособий. В любом случае, любую CAD-программу с поддержкой 2D можно использовать, выполнив следующие основные шаги.
01. Прежде чем обводить планы, узнайте, как откалибровать фоновое изображение, чтобы устранить любые проблемы с масштабированием. 02. Обведите планы для создания векторного файла. Процесс не сложный и может быть довольно увлекательным.Во-первых, вам нужно будет преобразовать детали, нарисованные на планах, в вышеупомянутый векторный формат САПР.
Если вы начинаете с бумажных планов, необходимо будет отсканировать их в файл изображения (обычно GIF или JPG, но также может быть в формате PDF) в местной копировальной компании, занимающейся большими форматами. Если вам повезет, планы могут уже существовать в электронном формате, что сделает вас на один шаг ближе к лазерному совершенству.
Затем импортируйте это растровое изображение в программу САПР, затем обведите изображение. Рисуя вручную поверх изображения, вы создаете векторную версию планов.
К сожалению, не существует автоматизированного способа преобразования растрового изображения в векторный формат с какой-либо согласованностью и точностью. Хотя это может измениться в будущем, я еще не слышал об успехе какой-либо из разрекламированных программ автоматической векторизации.
Если планы установлены в качестве фонового изображения, вам необходимо установить правильный масштаб в вашей программе САПР. Если вы этого не сделаете, программа не будет иметь привязки к истинному размеру деталей.
03. Типичный лазерный резак CO2, такой как этот, имеет приподнятую платформу и подъемную дверцу для защиты луча. Этот тип лазера также требует водяного охлаждения и вентиляции дыма. 04. Пробковое дерево режется быстро, и этот процесс завораживает.Некоторые планы имеют шкалу где-то на листе для справки. Если нет, вы можете просто измерить компонент известного размера штангенциркулем, чтобы использовать его в качестве эталона.
Программное обеспечение, поставляемое со многими лазерными резаками, использует метрические единицы, поэтому, если вы не уверены, что резак можно переключить на английские единицы измерения, лучше всего измерять и чертить все в метрических единицах. В каждой программе САПР это делается по-своему. У devCad есть онлайн-учебник о том, как откалибровать фоновое изображение до фактического размера.
Теперь нарисуйте детали, которые хотите вырезать. Если вы новичок в САПР, попробуйте сначала выполнить трассировку простых деталей.
Через некоторое время вы научитесь соединять линии, рисовать кривые и манипулировать разрывами строк для вырезов стрингеров и т. д. Если вы застряли, вероятно, есть онлайн-видео, которое поможет вам.
Одной из замечательных особенностей devCad является возможность «привязываться» к фоновой графике. Это означает, что программа обнаруживает линии фонового изображения и пытается самостоятельно совместиться с ними. Хотя вам по-прежнему приходится вручную обводить изображение, devCad помогает отслеживать, «привязывая» курсор к линиям на изображении, когда вы начинаете или заканчиваете новую линию или пересечение. Это работает на удивление хорошо.
Еще одна экономия времени заключается в том, что если вам нужно создать несколько дубликатов деталей, таких как нервюры крыла с постоянной хордой, вам нужно нарисовать только одну часть, а затем скопировать и вставить остальные, чтобы клонировать их. После некоторой практики этот процесс можно быстро завершить.
Когда вы закончите трассировку деталей, вам нужно экспортировать и сохранить файл во что-то, что сможет распознать программное обеспечение лазерного резака.
Я всегда использовал формат AutoCAD (расширение файла .dxf), потому что это отраслевой стандарт. Обязательно разместите все детали, которые нужно вырезать, на площади, не превышающей размер деревянного листа, который вы будете использовать. Еще одним преимуществом программы САПР является ее способность выбирать и перетаскивать детали, чтобы аккуратно расположить их для резки.
Не буду вдаваться в особенности программного обеспечения лазерного принтера, потому что разные модели будут иметь свои нюансы. Процесс, как правило, прост: импортируйте файл САПР, установите уровень мощности и нажмите «Старт». Ну, это немного сложнее, но вы поняли идею. Обратите внимание, что настройки мощности лазера — это отчасти наука, отчасти искусство. Ваши первые разрезы, скорее всего, будут либо слишком сильными, либо слишком слабыми, потому что необходимая мощность зависит от плотности и толщины древесины, а также от состояния газовой трубки лазера, среди прочего, поэтому возьмите с собой дополнительную древесину.
Лазерные резаки оцениваются в ваттах. Большинство хороших резаков имеют мощность не менее 40 Вт и, как правило, используют герметичные трубки CO2 в качестве лазерного излучателя. Они могут резать бальзу и фанеру практически любой толщины, которая обычно используется моделистами (хотя для более толстой фанеры может потребоваться несколько проходов) и стоят от нескольких сотен долларов. Избегайте недорогих твердотельных лазерных диодных резаков, потому что они потребляют всего несколько ватт и предназначены для гравировки или резки очень тонкой бальзы.
05. Эта репродукция Q-Tee с готовой обложкой, вырезанной лазером, содержала больше деталей, вырезанных лазером, чем вырезанные части оригинала. Лазерная резка своими руками дает вам свободу без особых усилий изменять конструкции для упрощения строительства. 06. Этот фюзеляж 40-летнего Warlock был подарен автору другом. Фитц смог вырезать лазером детали для создания нового крыла. Модель совершила множество успешных полетов.
- Цена: от 1150 до 1800 долларов США уникальные и универсальные самодельные лазерные резаки, с которыми мы сталкивались.