Какие типы контроллеров используются в современной промышленной автоматизации. Как выбрать оптимальный контроллер для конкретной задачи. Каковы основные тенденции развития контроллеров. Какие новые возможности открывают современные PAC-контроллеры.
Эволюция промышленных контроллеров: от реле до многоядерных процессоров
Промышленные контроллеры прошли долгий путь развития за последние десятилетия. Изначально это были простые релейные схемы с жесткой логикой и несколькими каналами ввода-вывода. Сегодня же современные программируемые логические контроллеры (ПЛК) и контроллеры автоматизации (PAC) являются мощными вычислительными устройствами на базе многоядерных процессоров, способными управлять сложными системами с тысячами каналов ввода-вывода.
Что стало причиной такого стремительного развития. Во-первых, постоянное совершенствование аппаратной части — появление более мощных и энергоэффективных процессоров, увеличение объемов памяти. Во-вторых, развитие программных технологий и языков программирования контроллеров. В-третьих, расширение коммуникационных возможностей для интеграции в сложные распределенные системы управления.
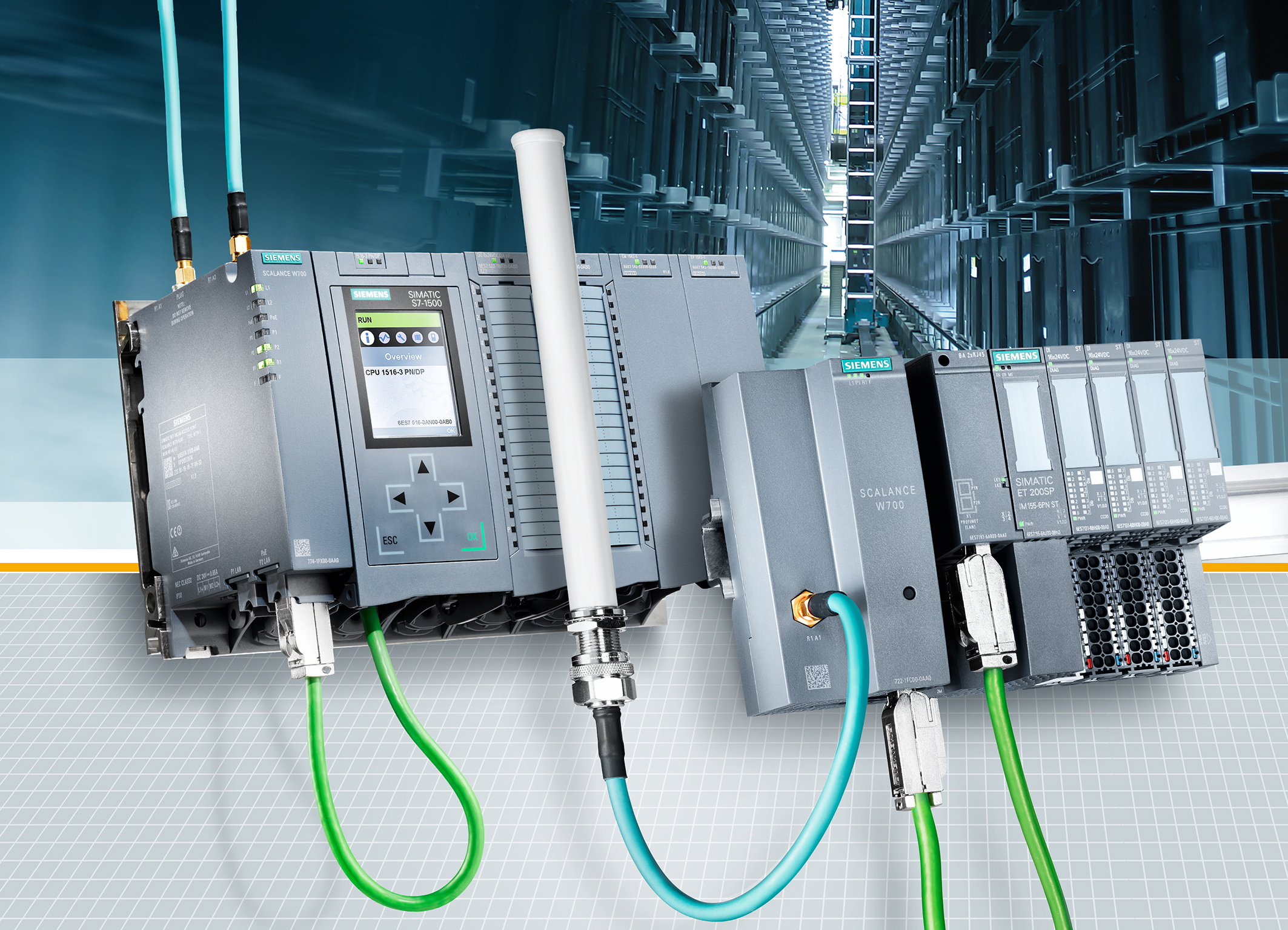
ПЛК vs PAC: в чем разница и как сделать правильный выбор
На рынке промышленной автоматизации сегодня представлены два основных типа контроллеров — программируемые логические контроллеры (ПЛК) и программируемые контроллеры автоматизации (PAC). В чем их ключевые отличия?
- ПЛК ориентированы на решение базовых задач автоматизации и управления технологическими процессами. Они компактны, надежны и относительно недороги.
- PAC-контроллеры имеют расширенную функциональность, более высокую производительность и предназначены для построения сложных систем управления. Они объединяют в себе возможности ПЛК, промышленных компьютеров и специализированных устройств.
Как выбрать оптимальный тип контроллера для конкретной задачи. Ключевыми критериями являются:
- Сложность алгоритмов управления
- Требуемая производительность и время реакции системы
- Количество каналов ввода-вывода
- Необходимость интеграции с системами верхнего уровня
- Требования к коммуникационным возможностям
- Условия эксплуатации
- Бюджет проекта
Для простых локальных систем управления оптимальным выбором будет компактный ПЛК. Для построения масштабных распределенных АСУ ТП лучше использовать высокопроизводительные PAC-контроллеры.
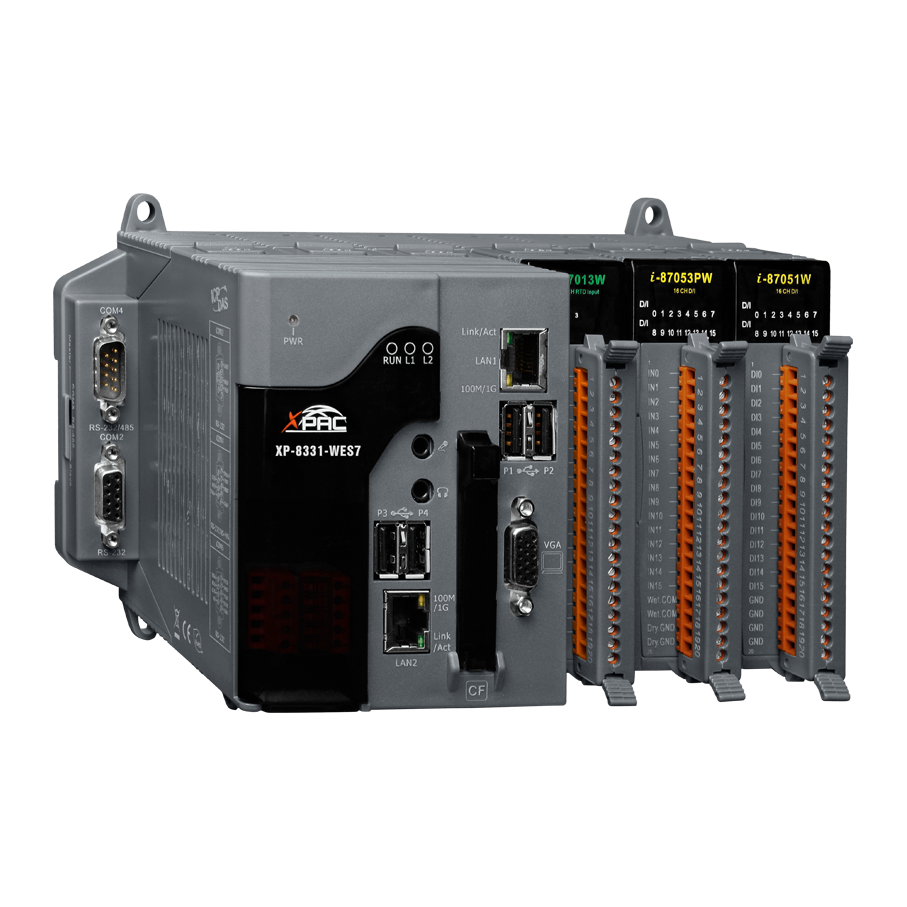
Ключевые возможности современных промышленных контроллеров
Рассмотрим основные возможности и характеристики, которыми обладают передовые ПЛК и PAC-контроллеры:
Высокая вычислительная мощность
Современные контроллеры строятся на базе мощных многоядерных процессоров архитектуры x86 или ARM. Это обеспечивает высокую производительность для работы со сложными алгоритмами управления, обработки данных, выполнения аналитических расчетов.
Поддержка стандартных языков программирования
Большинство контроллеров поддерживают языки стандарта МЭК 61131-3 (LD, FBD, ST, IL, SFC). PAC-контроллеры также позволяют использовать языки высокого уровня — C/C++, C#, Python и другие.
Расширенные коммуникационные возможности
Поддержка промышленных сетей (Modbus, Profibus, CANOpen и др.) и стандартных протоколов (OPC UA, MQTT) для интеграции в АСУ ТП и IoT-системы. Наличие беспроводных интерфейсов (Wi-Fi, 3G/4G, LoRaWAN).
Функции информационной безопасности
Современные контроллеры оснащаются средствами защиты от несанкционированного доступа, поддерживают шифрование данных, имеют встроенные межсетевые экраны.

Расширенная диагностика
Развитые средства самодиагностики, мониторинга состояния аппаратной части и каналов ввода-вывода повышают надежность и упрощают обслуживание систем.
PAC-контроллеры: новые возможности для промышленной автоматизации
Программируемые контроллеры автоматизации (PAC) объединяют в себе функциональность ПЛК, промышленных компьютеров и специализированных устройств. Какие новые возможности они открывают?
Интеграция систем управления технологическим процессом и производством
PAC-контроллеры могут одновременно выполнять задачи управления технологическим оборудованием и бизнес-процессами предприятия. Они обеспечивают прямое взаимодействие с базами данных, MES и ERP-системами.
Реализация сложных алгоритмов управления
Высокая производительность позволяет реализовывать продвинутые алгоритмы — предиктивное управление, нейросетевые регуляторы, машинное обучение для оптимизации процессов.
Объединение разнородных подсистем
PAC могут одновременно управлять системами движения, машинного зрения, измерения и контроля качества. Это упрощает интеграцию и снижает общую стоимость системы.
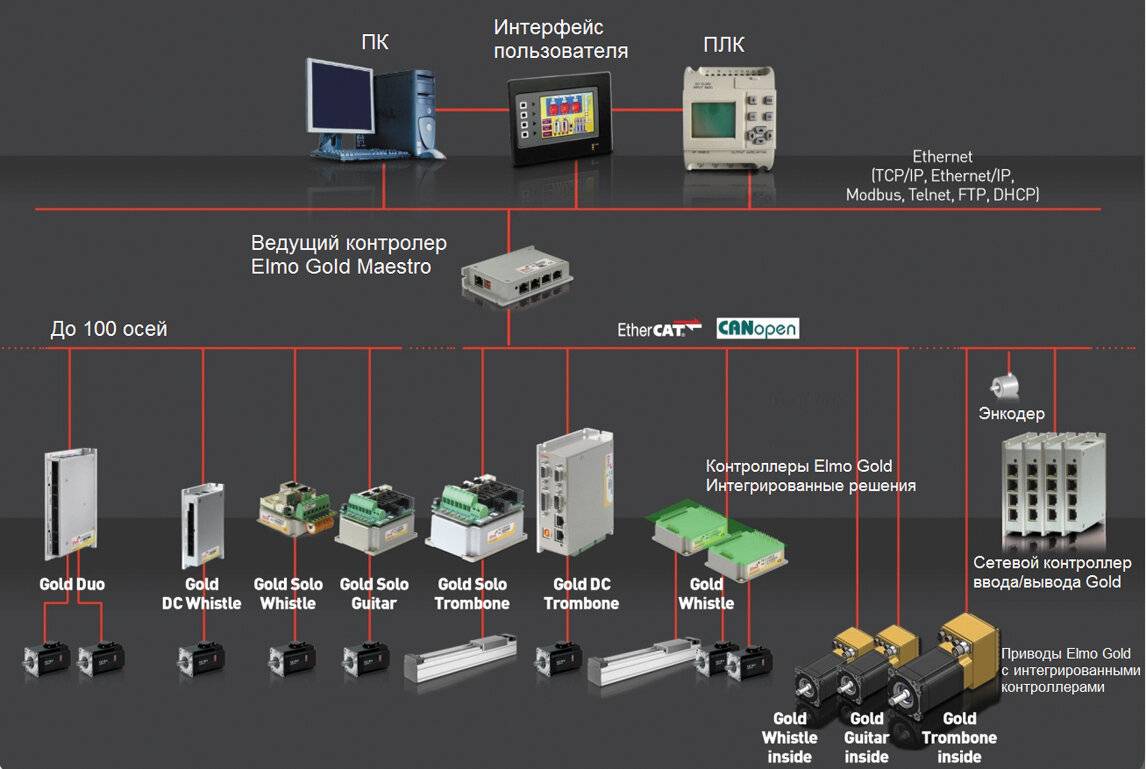
Работа с большими данными
Мощные PAC-контроллеры способны собирать, обрабатывать и анализировать большие объемы данных непосредственно на уровне АСУ ТП, реализуя концепцию граничных вычислений.
Тенденции развития промышленных контроллеров
Повышение вычислительной мощности
Использование все более производительных процессоров и многоядерных архитектур позволяет реализовывать более сложные алгоритмы управления и аналитики данных непосредственно на уровне контроллеров.
Конвергенция ИТ и ОТ
Стирание границ между информационными технологиями и технологиями операционного управления. Контроллеры становятся полноценными элементами ИТ-инфраструктуры предприятий.
Развитие edge computing
Перенос вычислительных мощностей ближе к источникам данных. Контроллеры берут на себя функции предварительной обработки и анализа данных.
Кибербезопасность
Усиление функций информационной защиты контроллеров для противодействия кибератакам на промышленные системы управления.

Упрощение программирования
Развитие инструментов визуального программирования, использование языков высокого уровня, применение готовых функциональных блоков и библиотек.
Выбор контроллера: на что обратить внимание
При выборе промышленного контроллера для конкретного проекта автоматизации следует учитывать ряд ключевых факторов:
Производительность и время цикла
Оцените требуемую вычислительную мощность для реализации алгоритмов управления. Определите допустимое время реакции системы на события.
Количество и типы каналов ввода-вывода
Проанализируйте необходимое число дискретных и аналоговых входов/выходов, учитывая возможности расширения системы в будущем.
Коммуникационные возможности
Убедитесь в наличии требуемых интерфейсов и поддержке нужных промышленных протоколов для интеграции в существующую инфраструктуру.
Условия эксплуатации
Учтите диапазон рабочих температур, допустимые уровни вибрации и ударных нагрузок, требования по защите от пыли и влаги.
Возможности программирования
Оцените доступные среды разработки, поддерживаемые языки программирования, наличие готовых библиотек и функциональных блоков.

Надежность и отказоустойчивость
Рассмотрите возможности резервирования, наличие функций самодиагностики, среднее время наработки на отказ.
Заключение: контроллеры как основа цифровой трансформации производства
Современные промышленные контроллеры являются ключевым элементом в построении интеллектуальных систем управления производством. Они обеспечивают сбор и обработку данных, реализацию сложных алгоритмов управления, интеграцию разнородных подсистем.
Развитие технологий промышленного интернета вещей (IIoT) и концепции Индустрии 4.0 предъявляет новые требования к функциональности контроллеров. Они должны поддерживать облачные технологии, обеспечивать кибербезопасность, работать с большими данными.
Выбор оптимального контроллера для конкретной задачи автоматизации требует тщательного анализа требований и возможностей различных моделей. При этом важно учитывать не только текущие потребности, но и перспективы развития системы управления.
Грамотное использование современных ПЛК и PAC-контроллеров позволяет создавать гибкие, масштабируемые и эффективные системы управления, способные адаптироваться к меняющимся условиям производства. Это закладывает фундамент для цифровой трансформации предприятий и повышения их конкурентоспособности в условиях новой промышленной революции.
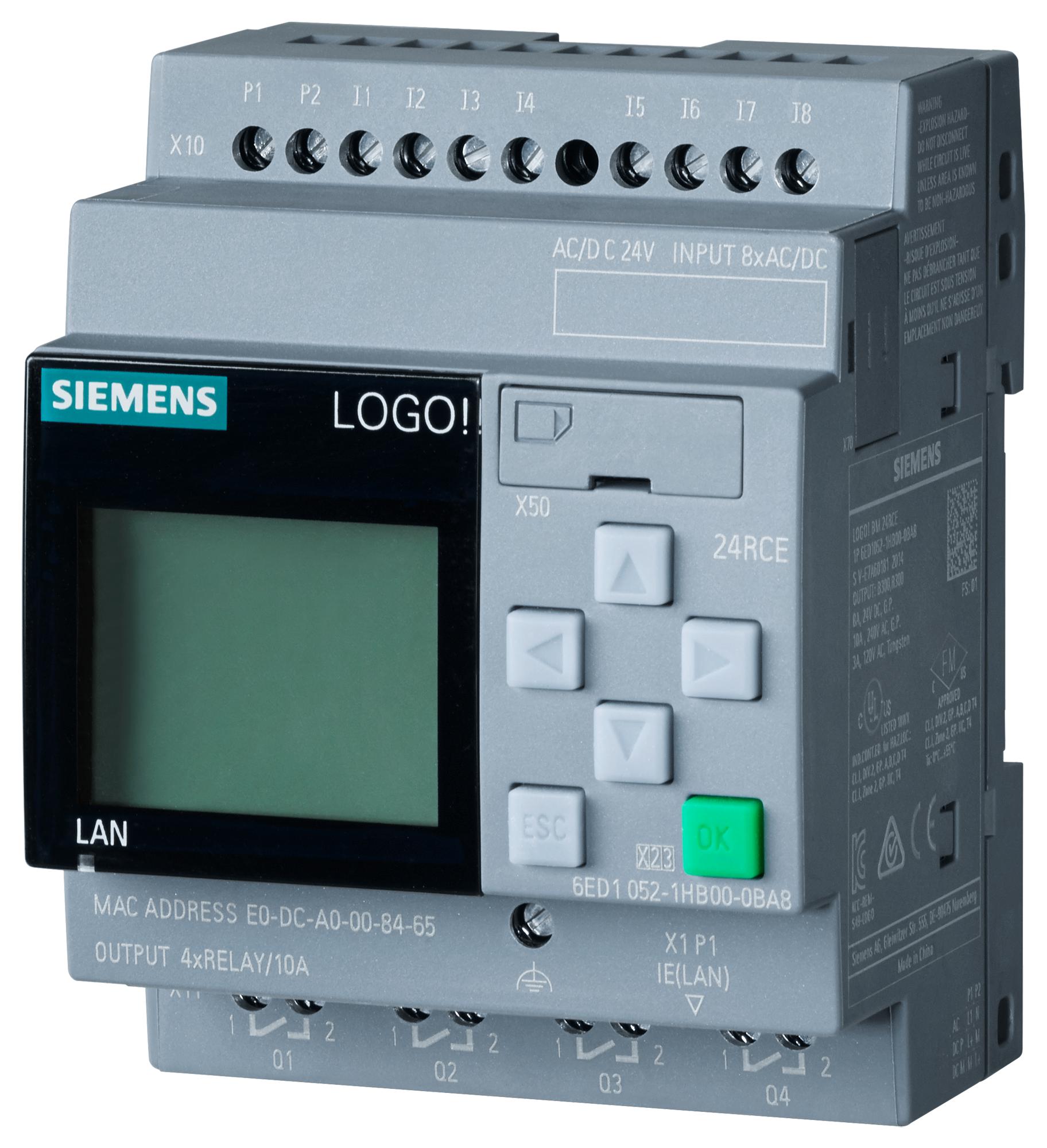
от элементарных «строительных кирпичиков» до «мозга» систем автоматизации
Стороннему наблюдателю могло бы показаться [1], что кривая роста вычислительной мощности процессоров вышла на плато, впрочем, с появлением многоядерной архитектуры производительность выросла благодаря объединению в многоядерный кристалл стандартных блоков обработки данных, обеспечивающих параллельные вычисления и обмен данными между ядрами. В настоящее время технология повышения вычислительной мощности процессора за счёт увеличения количества ядер продолжает развиваться как в коммерческих электронных устройствах, так и в аппаратуре промышленного сектора. Собственно говоря, именно совершенствование аппаратных средств подстёгивает развитие программных технологий, и наоборот, периодически сложность и функциональные возможности программных технологий ограничиваются аппаратной производительностью, ровно до того момента, когда технические новшества открывают дополнительные возможности для дальнейшего усложнения функциональности программного обеспечения.
Это легко проследить, если обратить внимание на функциональные возможности современных PAC-контроллеров (Programmable Automation Controller, согласно терминологии ARC Advisory Group – программируемый контроллер автоматизации) и программируемых логических контроллеров (ПЛК), – как менялись технологии программирования, быстродействие, функциональные возможности.
Соответствие требованиям завтрашнего дня
На протяжении десятков лет промышленные контроллеры – «рабочая лошадка» автоматизации – прошли длительный путь формирования и взросления, от наборов реле, построенных по принципу жёсткой логики, имеющих всего несколько дискретных каналов ввода/вывода и предназначенных для решения простейших задач автоматического регулирования, до центрального элемента сложных иерархических систем с тысячами каналов ввода/вывода, работающих под управлением мощных процессоров с многоядерной архитектурой и использующих развитые встроенные средства программирования.
В настоящее время обширный спектр стандартных задач автоматического регулирования (управление приводами, клапанами, частотными преобразователями, обработка и анализ дискретных и аналоговых сигналов) немыслим без коммуникационных функций связи с облачными SCADA, ERP и MES-системами, что побуждает производителей программируемых логических контроллеров расширять модельный ряд и функциональность ПЛК, создавая новые классы устройств, такие как PAC-контроллеры, контроллеры граничных вычислений, а также специализированные шлюзы данных для систем промышленного Интернета вещей (IIoT). Все эти устройства должны иметь развитые средства информационной защиты, так как особенность архитектуры и свойств программно-аппаратного обеспечения этой категории информационно-управляющих систем в том, что она максимально приближена к станкам, технологическому оборудованию, исполнительным механизмам электростанций, системам транспортировки нефти и газа, словом, к тем устройствам, нештатная работа или блокировка которых может привести к последствиям, сравнимым с результатами диверсий [2].
Вместе с тем как устройства про-мышленного применения контроллеры должны соответствовать стандартам эксплуатации в условиях повышенной влажности, электромагнитных помех, вибрации, высоких и низких температур, поддерживать современные и традиционные промышленные интерфейсы связи с датчиками и исполнительными механизмами, обладать гибким инструментарием программирования и взаимозаменяемостью компонентов для повышения гибкости использования. Для обеспечения управления быстро протекающими процессами контроллер должен обеспечивать заданное время отклика, что накладывает определённые обязательства на операционную систему и аппаратный ресурс.
От языка релейной логики до универсальных комплексов программирования стандарта МЭК 61131-3
Старая добрая релейная логика (Ladder Logic, LAD) как единственно доступный инструмент программирования ранних ПЛК в настоящий момент входит в состав программных комплексов, в которых реализована возможность написания, отладки и тестирования программ на трёх графических и двух текстовых языках, предусмотренных стандартом МЭК 61131-3 (релейных диаграмм – LD, функциональных блоков и диаграмм – FBD, последовательных функциональных схем – SFC, списка инструкций – IL, структурированного текста – ST). Одной из распространённых сред программирования на языках МЭК 61131-3 стал пакет CODESYS (Controller Development System) компании 3S (Smart Software Solutions), бесплатная среда разработки и расширенная функциональность которого делают его всё более популярным базовым инструментом программирования промышленных контроллеров.
В настоящий момент, кроме средств программирования на языках, описанных стандартом МЭК 61131-3, в распоряжении инженера-программиста современного высокотехнологичного контроллера имеется универсальная операционная система общего назначения (Windows или Linux), что даёт возможность программировать контроллер и на классических языках С, C++, С#, Python, Java и др. [3].
Таким образом, использование многоядерных процессоров и технологии раздельного использования вычислительных ресурсов (аппаратно-независимых ядер) ЦП позволяет одновременно и эффективно выполнять как задачи управления техпроцессом, описанные языками стандарта МЭК 61131-3, так и другие специальные задачи, реализованные на универсальных языках программирования.
Многоядерная технология, позволяющая разделить на аппаратном уровне обработку вычислительных задач, является настоящим технологическим прорывом в сфере промышленной автоматизации.
Коммуникационные функции
Современные ПЛК и PAC-контроллеры поддерживают, кроме типичных для АСУ ТП промышленных протоколов обмена данными: PROFIBUS, Modbus RTU, Modbus TCP, EtherNet/IP, PROFINET, EtherCAT, CANopen, DeviceNet – протоколы нового поколения, ставшие визитной карточкой IIoT, и типичные для IT-отрасли беспроводные и кабельные стандарты. Это открывает новые возможности для применения единого управляющего ПО, работающего на уровнях систем SCADA, MES и ERP, и на качественно новом уровне соответствует экспоненциально растущему потенциалу технологий IIoT.
Кроме того, современный контроллер, интегрированный в корпоративные сети предприятия, должен обладать дополнительными средствами защиты от несанкционированного доступа к управлению технологическим оборудованием и от таких распространённых в IT-сетях угроз, как DDoS-атаки (Distributed Denial of Service). Для обеспечения информационной безопасности необходимы поддержка протоколов и веб-соединений, защищённых сертификатом шифрования SSL/TLS, а также аппаратные ключи защиты.
PAC или ПЛК: критерии выбора
Программируемые логические контроллеры и PAC-контроллеры – это устройства, относящиеся к разным эпохам, хотя многие специалисты находят, что их функции уже в значительной степени совпадают. В качестве PAC обычно подразумевают контроллеры с управлением технологическим процессом и возможностями обмена данными на более высоком уровне, чем у ПЛК, но на самом деле чёткой границы между современными ПЛК и PAC не прослеживается.
Выбор контроллера определяется не столько аббревиатурой (ПЛК и PAC), сколько обеспечением функциональности, соответствующей поставленной задаче. Кроме стандартных задач автоматизации, правильно подобранный контроллер:
- конструктивно улучшает и повышает эксплуатационную надёжность систем автоматизации;
- устраняет влияние человеческого фактора, связанного с отсутствием профессионального опыта и пробелами в квалификации;
-
использует эффективные меры информационной защиты.
Применение высокопроизводительных процессоров вплоть до Core i7, а также вычислительных специализированных модулей, дополненных встроенной ПЛИС (FPGA), повышает скорость обработки данных в задачах, требующих оперативного реагирования.
Высокопроизводительные PAC-контроллеры обеспечивают реализацию технологий Industry 4.0 и технологии прогнозирования технического обслуживания оборудования, обладая самыми современными алгоритмами аналитики и машинного обучения. Кроме обеспечения достаточной производительности, современные PAC-контроллеры, в отличие от традиционных средств автоматизации, способны совмещать функции программируемых логических контроллеров, систем машинного зрения и систем управления движением, промышленных компьютеров, а иногда и серверов (рис. 1) [1].
Разработка специализированных систем автоматизации и устройств сбора и обработки сигналов для промышленности – одно из концептуальных направлений деятельности компании Advantech. Многим хорошо знакома серия модулей ADAM, исторический дизайн которых узнаваем в современных модульных системах ввода/вывода. Программируемые логические контроллеры и PAC-контроллеры Advantech обеспечивают высокий технологический уровень промышленных предприятий. Устройства низшего сегмента автоматизации производства Advantech – компоненты систем сбора и обработки данных, установленные непосредственно на удалённом объекте для сбора данных с дискретных и аналоговых датчиков, становятся всё более интеллектуальными.
На рис. 2 показано позиционирование программируемых контроллеров и устройств сбора и передачи данных компании Advantech в зависимости от количества каналов ввода/вывода и цены.
Рассмотрим основные линии контроллеров производства компании Advantech.
Контроллеры компании Advantech
ADAM-3600 (рис. 3) – многофункциональный контроллер на базе процессора Cortex A8 под управлением ОС Real-Time Linux – предназначен для установки на DIN-рейку в шкаф автоматики. В спектре разнообразных применений данного контроллера необходимо отметить построение с его участием систем мониторинга территориально-распределённых объектов нефтегазовой сферы (рис. 4).
Отличительная особенность контроллера – широкая коммуникационная функциональность, поддерживающая все популярные в настоящее время стандарты беспроводной связи: Zigbee, Wi-Fi, 3G/4G/GPRS – и протоколы Modbus, DNP3, MQTT, HTTP REST API. Контроллер позиционируется компанией Advantech как в качестве универсального решения на базе ОС Linux, так и в качестве интеллектуального удалённого терминала (RTU) с возможностью интеграции с облачными технологиями Microsoft Azure IoT Hub, Amazon AWS IoT и т.д. Важной особенностью контроллера является расширенный диапазон рабочих температур –40…+70°С [4].
Удобство применения и ценность такого рода универсальных решений для IT-приложений и систем АСУ ТП подтверждены самыми разными примерами использования контроллеров серии ADAM-3600. Наличие ядра реального времени RT Linux и предоставляемого компанией Advantech комплекта разработчика (SDK) на языках С/С++ существенно расширяет возможности программирования этой серии контроллеров [4].
Контроллеры семейства ADAM-5XXX. ADAM-5560CDS – модульная, x86-совместимая система ввода/вывода под управлением Windows CE5.0, имеющая встроенную среду разработки CODESYS V3 и ядро реального времени CODESYS.
ADAM-5560KW – PAC-контроллер со встроенной средой разработки стандарта МЭК 61131-3 KW MULTIPROG и ядром реального времени ProConOS.
ADAM-5560CE/XPE – x86-совместимый контроллер под управлением Windows CE5.0/Windows XP Embedded с поддержкой программных сред разработки eVC и .NET.
Эти контроллеры на базе процессоров Intel Atom с поддержкой специальных функций управления (включая сторожевой таймер и батарейную поддержку оперативной памяти), предназначенные для применения в небольших системах автоматизации, часто используются как в качестве бюджетного промышленного контроллера, так и в качестве инструмента визуализации со встроенным портом VGA и готовым программным пакетом HMI.
Контроллеры серии ADAM-5560 (рис. 5) были удачно применены в системе раннего оповещения и экстренного реагирования в случае стихийных бедствий (рис. 6).
В шкафу управления установлен контроллер ADAM-5560, использованный и в качестве средства визуализации на локальном мониторе, и в качестве аналитического инструмента обработки данных датчиков уровня, установленных вдоль берега водоёма, перед их отправкой на удалённый сервер и в центральный диспетчерский пункт. Шестнадцать цифровых каналов ввода модулей ADAM-5051D и ADAM-5056D со светодиодной индикацией используются для контроля работоспособности оборудования. Уровень воды измеряется при помощи датчика, подключённого к модулю аналогового ввода ADAM-5017.
Контроллер ADAM-5630 на базе процессора Cortex RISC-архитектуры позиционируется в качестве интеллектуального контроллера для граничных вычислений под управлением ОС Linux с возможностью программирования на языках C или Python.
APAX-5580 – типичный представитель нового поколения промышленных контроллеров. PAC-контроллер APAX-5580 (рис. 7) с центральным процессором Intel Core i7/i3/Celeron под управлением ОС Windows 7/8 (Linux Kernel 3.X) предназначен для использования на масштабных технологических объектах с большим количеством каналов ввода/вывода, предъявляющих особые требования к быстродействию систем автоматизации. Его высокая производительность обеспечивает возможность подключения к нему не только традиционных датчиков и исполнительных устройств, но и систем технического зрения, контроля качества, сбора данных, первичного анализа данных и реализации контуров управления, то есть большого числа ресурсоёмких систем. Компактные размеры обеспечивают гибкость использования в условиях ограниченного пространства. Программирование может осуществляться как в системе CODESYS, так и при помощи универсальных языков программирования C/C++.
Архитектура контроллеров серии APAX-5580, кроме промышленных протоколов CANOpen, Modbus/RTU, Modbus/TCP, PROFINET, Ethernet/IP, EtherCAT, предусматривает поддержку фирменной технологии расширения iDoor-плат mPCIe со шлейфом для дополнительных интерфейсов, а также позволяет работать в беспроводных сетях Wi-Fi, 3G, GPRS, GPS [5].
Применение в системах автоматизации единого программно-аппаратного решения APAX-5580 с предустановленной ОС Windows 7/8 и ядром реального времени Advantech CODESYS Run Time позволяет запускать любое количество программ (как на ПК с ОС Windows), программа CODESYS будет выполняться в приоритетном режиме на отдельном ядре ЦП, обеспечивая при этом достаточно быстрый цикл сканирования (до 50 мкс).
Контроллеры серии APAX-5580 можно также использовать в качестве сервера хранения данных, шлюза данных для систем верхнего уровня и IoT-приложений (рис. 8).
В целях достижения наивысшего качества управления, кроме двухъядерной архитектуры, можно выделить следующий далеко не полный перечень технологических преимуществ, присутствующих в APAX-5580: возможность установки аппаратного ключа безопасности на процессорную плату в качестве средства информационной защиты, надёжное энергоснабжение от независимых источников электроэнергии, поддержку функции резервного копирования данных операционной системы, что даёт системе с интегрированным в неё контроллером APAX-5580 необходимую отказоустойчивость. Кроме того, конструктивно предусмотрены хранение архива данных на жёстких дисках HDD или SSD, поддержка RAID-массивов уровня 0/1, подключение к базам данных (SQL-Server, Oracle, SAP, MySQL, SQLite) через программный интерфейс доступа к базам данных ODBC (Open Database Connectivity), локальная визуализация с поддержкой веб-браузерной технологии HTML (рис. 9).
Задачи, которые возлагаются на PAC-контроллер, в отличие от традиционных задач ПЛК, являются и стандартными задачами уровня АСУ ТП, и комплексными IT-задачами с расширенными возможностями программирования и прямого взаимодействия с базами данных и MES-системами.
AMAX-5580 – PAC-контроллер (рис. 10), предназначенный для решения задач высокоскоростного ввода-вывода в системах технического зрения, оптического контроля и системах контроля перемещений, представляет собой компактный производительный ПК на базе процессора Intel Core i7/i3/Celeron для монтажа на DIN-рейку, использует промышленную шину EtherCAT, популярную в системах управления движением, частотными преобразователями, приводами, роботами-манипуляторами.
При помощи встроенного интерфейса EtherCAT к нему можно подключать систему распределённого ввода/вывода AMAX-5000 EtherCAT Slice I/O modules, а также широкий круг оборудования сторонних производителей.
На рис. 11 показан пример единого программно-аппаратного решения компании Advantech для автоматизированного контроля качества в процессе производства экранов для смартфонов. Аппаратный ресурс процессора Core i7 позволяет одновременно управлять как механической частью контрольного оборудования (высокоточным перемещением образцов), так и системой автоматизированного оптического контроля. Контроллер функционирует под управлением ядра реального времени CODESYS с дополнительной обработкой данных системы технического (машинного) зрения для отправки в MES-системы силами ОС общего назначения Windows.
Поддержка стандартов программирования на языках МЭК 61131-3 позволяет инженерам-программистам быстрее разрабатывать управляющие программы, повысить быстродействие всей системы (в описанном ранее примере время отклика составляет 0,5 мс). Поддержка классических языков программирования даёт возможность решать ряд дополнительных задач, сопутствующих техпроцессу, одновременно с задачами управления. Остаётся добавить, что повышение эффективности и надёжности системы управления сопровождается снижением общих расходов на техническое обслуживание системы, а сверхкомпактные размеры PAC-контроллера 139×100×80 мм позволяют размещать его в условиях ограниченного пространства.
Заключение
Бо́льшая часть современных IIoT-приложений построена на базе ОС Linux, поэтому выбор контроллера с поддержкой этой операционной системы, удобного для интеграции в IT-сети предприятия, так важен.
Идея комбинировать функциональность программируемого логического контроллера и промышленного компьютера в едином технологичном решении становится всё более популярным трендом, учитывая всё возрастающий уровень требований к производительности вычислений, коммуникационным функциям и к бесшовной интеграции в системы управления предприятием верхнего уровня, в том числе облачные.
Широкая номенклатура ПЛК и PAC-контроллеров компании Advantech позволяет успешно строить системы АСУ ТП любого уровня сложности, отвечающие самым современным тенденциям развития цифровой революции Industry 4.0 и технологии IIoT. ●
Литература
- Halterman D. Should I use an edge controller, PLC, or PAC? [Электронный ресурс] // Режим доступа : https://www.controleng.com/articles/should-i-use-an-edge-controller-plc-or-pac/.
- Диас Ф.О. Информационная безопасность промышленных контроллеров [Электронный ресурс] // Режим доступа : https://www.securitylab.ru/analytics/425304.php.
- Петров И.В. Программируемые контроллеры. Стандартные языки и приемы прикладного проектирования. – М. : СОЛОН-Пресс, 2004.
- ADAM-3600 – многофункциональный промышленный контроллер [Электронный ресурс] // Режим доступа : https://habr.com/ru/company/advantech/blog/446210/.
-
Контроллер APAX-5580 от Advantech наследует лучшие черты ПК и ПЛК [Электронный ресурс] // Режим доступа : http://cleverhouse.
club/hardware/plc/kontroller-apax-5580-ot-advantech-nasleduet-luchshie-chertyi-pk….
Автор – сотрудник
фирмы ПРОСОФТ
Телефон: (495) 234-0636
E-mail: [email protected]
Обсуждаем тему: Современные контроллеры для промышленной автоматизации | Издательский Дом «ИнфоАвтоматизация»
Правильно поставленная проблема — уже наполовину решена.
Чарлз Кеттеринг
Связь с редакцией
Рассылка новостей
12.10.2022 — 14.10.2022
Созвездие САПР 2022
Город: Москва
18.10.2022 — 20.10.2022
Международный форум «МАШИНОСТРОЕНИЕ: СТРАТЕГИИ И ТЕХНОЛОГИИ»
Город: Москва
25. 10.2022 — 27.10.2022
Testing&Control 2022 – 19-я Международная выставка испытательного и контрольно-измерительного оборудования
Город: Москва
26.10.2022
Передовые Технологии Автоматизации. ПТА — Новосибирск 2022
Город: Новосибирск
28.10.2022
9-й Бизнес-форум 1С:ERP
Город: Москва
Автоматизация в промышленности, №4 2014
Обсуждаем тему: Современные контроллеры для промышленной автоматизации
Ицкович Э.Л.
Ключевые слова: классы промышленных контроллеров, свойства промышленных контроллеров, тенденции развития контроллеров
Автоматизация в промышленности, №4 2014
Обсуждаем тему: Современные контроллеры для промышленной автоматизации
Гуленок А. В.
Ключевые слова: компактность, ПЛК, производительность, распределенный ввод/вывод, сервисные возможности, совместная работа, языки программирования
Автоматизация в промышленности, №4 2014
Обсуждаем тему: Современные контроллеры для промышленной автоматизации
Ключевые слова: быстродействие, ПЛК, система параллельной обработки инструкций, функция проверки и исправления ошибок
Автоматизация в промышленности, №4 2014
Обсуждаем тему: Современные контроллеры для промышленной автоматизации
Егоров Е.В.
Ключевые слова: Web-технологии, ПЛК, распределённая периферия, телесервис, управление приводом, функциональная безопасность
Автоматизация в промышленности, №4 2014
Обсуждаем тему: Современные контроллеры для промышленной автоматизации
Ключевые слова: беспроводная связь, диагностика, дистанционное управление, контроллер телемеханики, многофункциональность
Автоматизация в промышленности, №4 2014
Обсуждаем тему: Современные контроллеры для промышленной автоматизации
Ефремов А. В.
Ключевые слова: беспроводная связь, внутренняя диагностика, открытые стандарты Ethernet, ПЛК
Автоматизация в промышленности, №4 2014
Обсуждаем тему: Современные контроллеры для промышленной автоматизации
Зайцев М.В.
Ключевые слова: выбор, модернизация, ПЛК, производительность, система ввода/вывода, функциональность
Автоматизация в промышленности, №4 2014
Обсуждаем тему: Современные контроллеры для промышленной автоматизации
Титов С.П.
Ключевые слова: интегрированная среда разработчика, микроконтроллер, модульный контроллер, ПЛК, программируемые реле
Автоматизация в промышленности, №4 2014
Обсуждаем тему: Современные контроллеры для промышленной автоматизации
Автоматизация в промышленности, №4 2014
Обсуждаем тему: Современные контроллеры для промышленной автоматизации
Ключевые слова: интеграция, машинный контроллер, платформа автоматизации, универсальность
Автоматизация в промышленности, №4 2014
Обсуждаем тему: Современные контроллеры для промышленной автоматизации
Автоматизация в промышленности, №4 2014
Обсуждаем тему: Современные контроллеры для промышленной автоматизации
Косолапов А. В., Медведев А.В.
Ключевые слова: отечественная термопара, прецизионный модуль ввода/вывода, программируемый логический контроллер
Автоматизация в промышленности, №4 2014
Обсуждаем тему: Современные контроллеры для промышленной автоматизации
Богер В.П., Раскин Е.М.
Ключевые слова: выносной локальный регулятор, диагностика, контроллеры, программируемая автоматика перестраиваемой структуры, резервирование
Автоматизация в промышленности, №4 2014
Обсуждаем тему: Современные контроллеры для промышленной автоматизации
Рогов С.Л.
Ключевые слова: АСУТП, инфракрасный межмодульный интерфейс, контроллеры, низковольтные комплектные устройства
Автоматизация в промышленности, №4 2014
Обсуждаем тему: Современные контроллеры для промышленной автоматизации
Шашков С.Л.
Ключевые слова: модули расширения, ПЛК, распределенные системы управления, резервное питание
Автоматизация в промышленности, №4 2014
Обсуждаем тему: Современные контроллеры для промышленной автоматизации
Кулиев А. У., Нежметдинов Р.А., Николушкин А.Ю., Червоннова Н.Ю.
Ключевые слова: SoftPLC, логическая задача управления, смена инструмента, функциональный блок, электроавтоматика
Автоматизация в промышленности, №4 2014
Обсуждаем тему: Современные контроллеры для промышленной автоматизации
Гурьянов Л.В., Ургеватов А.Ю., Шехтман М.Б.
Ключевые слова: Web-технологии, интерфейс, ПЛК, реальное время, резервирование, среда программирования контроллера
Автоматизация в промышленности, №4 2014
Обсуждаем тему: Современные контроллеры для промышленной автоматизации
Ельцов А.А.
Ключевые слова: панель оператора, панельные контроллеры, программируемые логические контроллеры, че¬ловеко-машинный интерфейс
Читайте в номере:
Будущее компьютерного тренинга: от формирования отдельных навыков к управлению компетенциями операторов
Концептуальные решения линейки тренажёров АМТ – залог успеха и долголетия
Компьютерная система управления жизненным циклом производства промышленных изделий из вторичного полимерного сырья
Автоматизация управления гидроприводом пресса
РассылкиSubscribe.![]() | |
Автоматизация в промышленности |
Главная » Продукция » OMRON — ПРОМЫШЛЕННАЯ АВТОМАТИЗАЦИЯ » Промышленные контроллеры Гибкий инструмент автоматизации ZEN-10C Предлагаемые нами 4 различных типа модулей ЦПУ с 10 точками ввода/вывода • Модули с входным напряжением/напряжением питания постоянного тока
Расширенные средства гибкой Один модуль ZEN-20 предоставляет в распоряжение пользователя 12 входов • Модели ZEN-20C1/C2 с возможностью расширения до 44 входов/выходов
Компактный и экономичный CPM1A Вмещая в своем компактном корпусе все основные функции, CPM1A • Сверхкомпактный Контроллер общего применения CPM2A Все модели центрального процессора CPM2A имеют встроенный порт RS-232C, • Функция часов реального времени
Компактный промышленный контроллер CP1L Среди контроллеров для управления компактным оборудованием
Моноблочный ПЛК — все функции Созданный специально для применения в небольших установках, ПЛК CP1H • Частота входных/выходных сигналов до 1 МГц
Быстрые высокопроизводительные CJ1 ЦПУ для решения любых задач
Быстрые высокопроизводительные CS1 ЦПУ для решения любых задач | МАРКИРОВКА, ЭТИКЕТИРОВАНИЕ, ШТРИХОВОЕ КОДИРОВАНИЕ Принтеры для мелкосимвольной маркировки Принтеры для крупносимвольной маркировки Системы лазерной маркировки Термотрансферные принтеры для печати на пленочных материалах Этикетировщики Расходные материалы Принтеры ЭТИКЕТОК Сканеры штрих-кода Терминалы сбора данных OMRON — ПРОМЫШЛЕННАЯ АВТОМАТИЗАЦИЯ Реле общего назначения Фотодатчики Частотнорегулируемый электропривод Блоки питания Терморегуляторы Счетчики Таймеры Концевые выключатели безопасности Промышленные контроллеры Программное обеспечение Датчики приближения Датчики безопасности Специальные измерительные датчики Промышленные терминалы RFID радиочастотные системы Реле обеспечения безопасности Системы технического зрения ПНЕВМАТИКА, ГИДРАВЛИКА, ВАКУУМНАЯ ТЕХНИКАКОНВЕЙЕРНЫЕ СИСТЕМЫ Пластинчатые конвейеры Ленточные конвейеры Роликовые конвейеры КРАСЯЩАЯ ЛЕНТА (РИББОНЫ)ЭТИКЕТКИРАСПРОДАЖА Этикетки Термотрансферная лента Сканеры ШК Терминалы сбора данных Принтеры этикеток Комплектующие по автоматизации |
Виды и классификация контроллеров автоматизации
Программируемый логический контроллер (ПЛК) – это специальное устройство, разработанное для автоматизации оборудования в промышленных условиях. По своим функциям ПЛК напоминает домашний ПК. У него есть источник питания, ЦП, устройства ввода и вывода, память и ПО. Существенная разница в том, что ПЛК может выполнять дискретные и непрерывные функции. По сути, логический контроллер – это «защищенный» компьютер, который управляет электромеханическими процессами в промышленной среде.
Кроме оборудования на производстве необходимы те инструменты, которые помогут его контролировать
В этой статье мы рассмотрим, какие бывают контроллеры автоматизации, их виды и классы.
Размер ПЛК
В этой категории различают малые, средние и большие ПЛК.
Малые ПЛК
Это небольшие контроллеры на 15–100 входов и выходов, предназначенные для управления небольшими машинами, например двигателями. Как правило, малый ПЛК оснащается портами последовательной связи, настроенными для подключения к приводам и датчикам по каналам RS-232 или RS-485. Малые контроллеры можно приобрести в виде отдельных модулей, чтобы их можно было легко встроить в существующие системы управления.
Средние ПЛК
Такие контроллеры рассчитаны на 100–300 входов и выходов. С их помощью можно автоматизировать управление более крупным оборудованием вроде сборочных линий. По сравнению с малыми ПЛК, средние контроллеры обладают:
- большим объемом памяти;
- расширенными коммуникационными портами;
- более высокой скоростью обработки;
- дополнительными устройствами ввода/вывода.
ПЛК среднего размера позволяют устанавливать множество подключаемых модулей на объединительной плате системы.
Большие ПЛК
Эти контроллеры рассчитаны на 300–2000 входов/выходов. Большие ПЛК позволяют автоматизировать управление крупногабаритным оборудованием, например турбинами.
Большие контроллеры применяются там, где необходимо управлять сложными технологическими процессами. Как правило, ПЛК такого типа используют в диспетчерских, на крупных фабриках, электростанциях и др.
Конфигурация оборудования
В зависимости от конфигурации логические контроллеры бывают компактными и модульными.
Компактный контроллер
Это небольшой ПЛК, с помощью которого можно решить небольшие задачи автоматизации. Он включает встроенный язык программирования, а также обширный и удобный набор инструкций, что упрощает кодирование определенных программ.
К основным компонентам компактного ПЛК относятся:
- устройства ввода/вывода;
- батарея;
- блок, который обрабатывает данные;
- разъемы для подключения переключателей и датчиков.
В отличие от центральных блоков управления технологическими процессами, компактные ПЛК меньше по размеру и более портативны, поскольку не требуют высоковольтных кабелей.
Модульный контроллер
Модульный ПЛК основан на программируемых аппаратных модулях. Позволяя пользователям настраивать и перенастраивать свои контроллеры, модульные ПЛК экономят деньги производителей на внешнем интерфейсе, упрощая требования к установке и настройке.
Кроме того, их можно легко заменить с помощью обновлений: не нужно отказываться от них, когда становятся доступными более продвинутые технологии. Это делает их привлекательными для быстрорастущих компаний, планирующих быстро выйти на новые рынки.
Модуль ввода/вывода
По этой классификации ПЛК могут оснащаться дискретными или аналоговыми устройствами ввода/вывода.
Дискретный ввод/вывод
Это наиболее распространенный тип. Данный интерфейс соединяет полевые устройства ввода типа «вкл/выкл», такие как селекторные переключатели, кнопки и концевые выключатели. Каждый бит дискретного ввода и вывода представляет собой полный информационный элемент сам по себе и обеспечивает состояние некоторого внешнего контакта или сообщает о наличии или отсутствии питания в цепи обработки.
Аналоговый ввод/вывод
Типичные аналоговые входы и выходы варьируются от 0 до 20 мА, от 4 до 20 мА или от 0 до 10 вольт. Аналоговые входы являются непрерывными, например передавая сигнал от преобразователя давления и температуры. Аналоговые выходы – это управляющие элементы, используемые для оборудования, такого как приводы электродвигателей.
Источник питания
По этому параметру ПЛК можно разделить на два основных типа:
- Без встроенного источника питания – подключаются к внешнему источнику питания, например зарядным батареям.
- Со встроенным источником постоянного напряжения на 24 В или 48 В.
Второй вариант ПЛК более эффективен – нет необходимости приобретать отдельный аккумулятор или трансформатор. Кроме того, такие контроллеры не требуют отдельного устройства преобразования напряжения и сокращают количество компонентов, которые могут выйти из строя.
Преимущества использования ПЛК
ПЛК были стандартным элементом конструкции промышленного оборудования на протяжении многих десятилетий. Вот какие преимущества ПЛК делают их столь популярным выбором:
- Программирование ПЛК довольно интуитивно понятно. Их языки программирования просты по сравнению с другими промышленными системами управления, что делает ПЛК отличным выбором для компаний, стремящихся свести к минимуму сложность и затраты.
- ПЛК – это зрелая технология, за которой стоят годы испытаний и анализа. Легко найти надежные исследования по различным типам ПЛК и исчерпывающие учебные пособия по их программированию и интеграции.
- ПЛК доступны в широком диапазоне цен, включая множество базовых моделей, которые часто используют малые предприятия и стартапы.
- ПЛК чрезвычайно универсальны, и большинство моделей подходят для управления широким спектром процессов и систем.
- ПЛК – это полностью твердотельные устройства, то есть в них нет движущихся частей. Это делает их исключительно надежными и более способными выдерживать сложные условия, присутствующие на многих промышленных объектах.
- ПЛК имеют относительно небольшое количество компонентов, что упрощает поиск и устранение неисправностей и помогает сократить время простоя на техническое обслуживание.
- ПЛК эффективны и не потребляют много электроэнергии. Это помогает экономить энергию и может упростить рассмотрение проводки.
Критерии выбора ПЛК
Выбор правильного ПЛК будет зависеть от потребностей и размера системы автоматизации. Вот что необходимо учесть:
- Является ли предлагаемая система для автоматизации новой или уже существующей – важно убедиться в том, что контроллер работает с сопряженным оборудованием.
- Условия окружающей среды, которые влияют на производительность ПЛК – типичные контроллеры работают при температуре от 0 до 55 °C.
- Количество дискретных и аналоговых устройств – определяет количество соединений ввода/вывода, которое потребуется ПЛК.
- Требования к ЦП – это важно для расчета объема ОЗУ, необходимого для обработки и хранения данных.
-
Совместимость с инструкциями программы – некоторые ПЛК поставляются с функциями пропорциональной интегральной производной, что избавляет технических специалистов от необходимости писать специальный код для управления технологическим процессом с обратной связью.
Внедрение промышленной автоматизации
Содержание
- Для чего нужна промышленная автоматизация
- Преимущества промышленной автоматизации
- Среди множества преимуществ автоматизации промышленного производства также выделяют:
- Среди различных систем автоматизации производственного процесса можно выделить, среди прочего:
- Как запрограммировать контроллер ПЛК
- Что такое контроллер ПЛК. Структура и применение
- Какие бывают типы контроллеров ПЛК. Классификация
- Этапы программирования ПЛК
Промышленная автоматизация — это решение, рекомендованное для производственных предприятий, целью которого является минимизация затрат и риска ошибок при сохранении безопасности для операторов машин. Эти системы основаны на управлении машинами с использованием специализированного программного обеспечения.
Для чего нужна промышленная автоматизация
В настоящее время процесс механизации оказывает сильную поддержку сотрудникам в выполнении ими своих обязанностей, но тенденция идет дальше, устраняя необходимость ручного управления устройствами и принятия решений человеком. Благодаря автоматизации машины могут действовать без необходимости постоянного участия человека в их работе.
Специальное программное обеспечение дает команды машинам и управляет их механизмами. Промышленная автоматизация использует современные технологии и с помощью передовых устройств управляет и контролирует работу машин в цехе. В промышленной автоматизации используются компьютеры и контроллеры, а также системы связи, нужные для увеличения темпа работы. О всех необходимых устройствах, которые нужны для промышленной автоматизации можно посмотреть, пройдя по ссылке.
Преимущества промышленной автоматизации
Крупное производство нуждается в поддержке в виде автоматизации, иначе оно будет нерентабельным. Использование современных систем автоматизации машин не только сокращает время, но и обеспечивает точное производство на самом высоком уровне.
Среди множества преимуществ автоматизации промышленного производства также выделяют:
• сокращенный производственный цикл;
• защита сотрудников при эксплуатации техники;
• экономия на количестве сотрудников;
• устранение ошибок;
• меньший контроль качества.
Виды промышленной автоматизации
Среди различных систем автоматизации производственного процесса можно выделить, среди прочего:
• постоянные, для повторяемых процессов и получения высоких производственных результатов;
• программируемые системы, используемые для серийного производства с возможностью изменения конфигурации при следующем заказе;
• для производства различных компонентов в короткие сроки рекомендуется гибкая автоматизация.
Как запрограммировать контроллер ПЛК
ПЛК — это программируемый логический контроллер. Как электронное и микропроцессорное устройство, оно состоит из нескольких частей, например, входов и выходов. Это облегчает управление машинами, используемыми в промышленности. Это возможно благодаря программному обеспечению. Как выглядит программирование ПЛК? Какие существуют типы драйверов и для чего их можно использовать?
Что такое контроллер ПЛК. Структура и применение
Контроллеры ПЛК включены в услуги, предлагаемые средствами автоматизации, созданными в 1960-х годах в США. Благодаря им соединение выключателей с контакторами осуществляется просто. Это влияет на удобство использования, например управления. Это возможно благодаря программированию ПЛК. Программа, то есть алгоритм, облегчает выполнение запланированных задач. Это улучшает работу и регулирование промышленного оборудования и машин.
Устройства состоят из центрального блока и цифровых и аналоговых входов и выходов. К ним относятся модули связи и питания, а также память. Дизайн напоминает черный ящик с экраном и кнопками. Благодаря множеству функций, например, диагностике или передаче данных, аналогично системе SCADA, используются в транспортной, химической и машиностроительной отраслях, а также в энергетике. Более того, они могут обрабатывать целые производственные линии. Они позволяют управлять лифтами, эскалаторами и светофорами. Ими можно оборудовать умные дома.
Какие бывают типы контроллеров ПЛК. Классификация
Программирование контроллеров ПЛК возможно только в том случае, если вы знаете их типы. Выбор производится на основе среды проектирования и разработки. По конструкции различают следующие устройства:
Компактный. Они состоят из модуля и входов и выходов — 32 для наноконтроллеров или 128 для микроконтроллеров.
Модульный. Малые, средние или большие, от 200 до 400 и более входов и выходов.
Они состоят из центрального устройства. Сообщения оставшимся распределенным модулям отправляются по сети.
Компактные модели самые дешевые. Модульные устройства, которые можно свободно расширять, дороже. Их можно комбинировать, расширять или модифицировать в соответствии с операционной системой.
Этапы программирования ПЛК
Перед установкой стоит предварительно ознакомиться со схемой подключения устройства. Внешние устройства подключаются к ПЛК 3 способами. Используется силовая цепь, например входы для датчиков и кнопок, или выходы, например, для электромагнитных клапанов или сигнального оборудования. Стоит знать, что входы и выходы отмечены символами. Им присваивается номер 0 или 1. Все зависит от версии модели и производителя. Входы обычно называются — I (для ввода ), а выходы — Q (для выхода ). Используются редакторы или программное обеспечение. Это позволяет войти в программу, проверить код и отправить его на устройство. Работа программируемого логического контроллера состоит из следующих шагов:
Представления. Каждый раз при включении устройства проверяется, правильно ли оно работает.
Показания. Считывание входных сигналов основано на так называемом первый цикл программы. Затем считываются устройства ввода.
Услуга. Получение информации при интеграции с другими устройствами. Сюда также входит обновление компьютерного программного обеспечения.
Автоматическая диагностика. Сбор данных об ошибках и сбоях. После обнаружения ошибки работа устройства прерывается.
Программист или компания, занимающаяся промышленной автоматизацией, непременно гарантирует правильную работу программного обеспечения.
Как вам статья?
Промышленная автоматизация: компоненты для обеспечения стабильного питания
Мир уверенно движется в сторону цифровой трансформации, и автоматизация производства стала обязательным условием для тех предприятий, которые планируют сохранить и укрепить свои позиции на рынке. Давайте посмотрим, какие средства промышленной автоматизации помогают достичь баланса между производительностью, управляемостью и экономической эффективностью.
Для автоматизации производства применяют цифровые и аналоговые устройства, которых объединяет одна цель: сделать работу эффективной и снизить затраты на управление оборудованием.
Средства промышленной автоматизации решают следующие задачи:
- оптимизируют затраты на персонал;
- сокращают время на изготовление единицы продукции;
- сокращают количество рекламаций;
- продлевают срок службы производственного оборудования;
- повышают уровень безопасности на производстве.
Современные средства автоматизации и промышленного контроля объединяют датчики, реле, контроллеры, регуляторы, переключатели ввода и другие устройства. Кратко расскажем об их назначении и основных функциях.
Контроллеры ABP
Контроллеры ABP (автоматического ввода резерва) представляют собой интеллектуальные управляющие устройства и выполняют сразу несколько ролей: фазного реле, многофазного вольтметра, контролера аварийных состояний и других. Их основная задача – переключать нагрузку с основной питающей линии на резервную и наоборот. Контроллер АВР может не только управлять силовой частью системы и контролировать состояние дополнительных контактов, но и сигнализировать о возникновении аварийных ситуаций. Например, при повышении или понижении напряжения, несоответствии фаз между вводами, при срабатывании расцепителя автоматического выключателя.
Программируемый контроллер Delta Electronics
Контроллеры ДГУ
Этот тип контроллеров позволяет организовать автоматический ввод резерва с применением ДГУ (дизель-генераторной установки). Контроллер автоматически запускает двигатель установки при прекращении подачи сетевого напряжения и останавливает его после восстановления стабильного электроснабжения. На крупных объектах используют контроллеры, которые поддерживают работу в многоагрегатном режиме и обеспечивают работу десятков генераторных установок, синхронизируя их в единую систему автономного энергоснабжения.
Статические переключатели ввода
Статический переключатель ввода (STS) отвечает за бесперебойную работу оборудования, для которого критично даже кратковременное прекращение подачи электропитания. При аварийной ситуации STS за доли секунды переключает нагрузку на дополнительную (независимую) линию. В современных ЦОД статические переключатели ввода сокращают риск остановки ответственных потребителей при сбоях в сетях электроснабжения, повышают надежность и обеспечивают непрерывность выполнения вычислений в клиентских приложениях.
Датчики
В общем случае датчики представляют собой средства для измерения и выработки сигнала в форме, удобной для передачи и последующей обработки, преобразования и хранения. В составе ДГУ используются различные типы датчиков: датчики давления масла, температуры, магнитные датчики оборотов.
Автоматические регуляторы напряжения
Используются для управления напряжением ДГУ на выходе. Они воздействуют на щеточные и синхронные генераторы с бесщеточными системами, обеспечивая напряжения переменного тока стабильного значения (отклонением не более 1 % в каждую сторону).
Регуляторы оборотов двигателя (актуаторы)
Каждый двигатель в дизель-генераторной установке в процессе работы испытывает различные нагрузки. Это приводит к дисбалансу между мощностью двигателя и степенью нагрузки, из-за чего меняется частота вращения вала. Если двигатель постоянно работает в таком режиме, его механизмы изнашиваются раньше времени, а расход топлива возрастает. Регуляторы оборотов двигателя помогают предотвратить эту ситуацию и продлевают срок службы двигателя ДГУ, контролируя и управляя скоростью вращения в зависимости от текущей нагрузки.
Реле управления и безопасности
Незаменимое устройство на современном производстве, где важно поддерживать непрерывные технологические процессы. Реле отвечает за своевременное отключение оборудования в аварийной ситуации, обеспечивает безопасность в экстренных случаях. Отдельные реле управления могут диагностировать ошибки и поддерживать работу в сети.
Устройства плавного пуска
В момент запуска электродвигателя в электросети временно падает напряжение, что может приводить к сбоям в работе сложного оборудования. Снизить риски в этой ситуации помогают устройства плавного пуска. Они обеспечивают плавный (бесступенчатый) разгон и остановку двигателя за счет регулировки напряжения. Это позволяет предупредить гидравлические удары в трубах, колебания в конвейерных системах, проскальзывание клиновидных ремней.
Анализ опций промышленных контроллеров
Программируемые логические контроллеры Allen-Bradley Micro820.
Когда дело доходит до контроллеров, производители и промышленные компании часто склонны оставить в покое то, что работает достаточно хорошо. В конце концов, при правильном обслуживании программируемые логические контроллеры (ПЛК) могут работать бесперебойно, надежно контролируя процессы и выполняя другие важные функции в течение многих лет без необходимости замены.
Но все оборудование рано или поздно достигает конца своего жизненного цикла. А иногда компания может захотеть добавить новые функции для улучшения контроля над системой. В этом случае компания начнет присматриваться к ПЛК и спрашивать партнеров-системных интеграторов, каким должен быть их путь обновления и следует ли им добавлять новые технологии.
Часто выбор не вызывает затруднений. Если предприятие использует определенное семейство ПЛК в течение дюжины лет, то, скорее всего, нет особого смысла в переходе на программный контроллер, работающий на промышленном ПК. «Необходимо учитывать поддержку, запасные части и стоимость владения, — говорит Марк Брадо, менеджер по проектированию автоматизации в JNE Consulting. «Вы не хотите продавать им что-то более сложное, чем им нужно».
Фрэнк Бургер, старший специалист по автоматизации Avanceon, согласен. «Большинство наших клиентов имеют установленную базу, и для них важно управлять запасами запасных частей. Им также необходимо управлять потребностями в обучении своих технических специалистов, которые должны обслуживать этот материал в долгосрочной перспективе», — говорит Бургер.
По этим причинам производители ищут технологии управления, которые хотя и не идеальны, но надежно выполняют свою работу. Несмотря на то, что промышленность полагается на проверенные временем решения, стоит остановиться и просмотреть варианты контроллеров до того, как возникнет необходимость в обновлении.
Программируемые логические контроллеры Allen-Bradley Micro820. ПЛК под любым другим названием
Полвека назад ПЛК были разработаны как решение проблемы ограничений логических систем с электрическими реле. Они позволили инженерам разрабатывать, модифицировать и расширять функциональные возможности систем управления за счет программных, а не аппаратных изменений. Это означало, что больше не будет комнат, заполненных проводкой. Теперь, в 21 веке, ПЛК по-прежнему ценятся за их неизменную надежность управления технологическими процессами.
За прошедшие годы производители ПЛК, такие как Rockwell, Siemens и Mitsubishi Electric, добавили возможности в функциональные возможности ПЛК, включая интегрированное управление сервоприводами и приводами, сетевые коммуникации, расширенное управление процессами, а также настраиваемое и основанное на событиях сканирование ввода-вывода. По мере того, как начали появляться такие сложные функциональные возможности, промышленность начала отличать эти передовые контроллеры от менее сложных ПЛК, придумав термин «программируемые контроллеры автоматизации» (PAC). С момента введения термина PAC в 19В 90-х годах производители использовали его, чтобы отличить свои продвинутые контроллеры от более простых ПЛК, хотя границы размылись, и эти термины часто используются взаимозаменяемо. ПЛК и ПАК служат приблизительно одной и той же цели, но ПЛК обычно предназначены для базового дискретного управления, а ПАК используются, когда требуются сложные функции или инфраструктура.
Большинство классических ПЛК используют форму программирования на основе памяти, где адреса тесно связаны со структурой физической памяти, говорит Нейт Кей, старший инженер проекта Martin CSI. «Принимая во внимание, что с PAC вам не нужно беспокоиться об этом. [PAC] достаточно интеллектуальны, чтобы вы могли сосредоточиться на написании на языке программирования, и они управляют памятью в фоновом режиме», — говорит Кей. PAC также позволяют программировать на основе тегов, что повышает гибкость и масштабируемость, позволяя назначать теги функциям до привязки к конкретным адресам ввода-вывода или памяти.
Классические ПЛК все еще имеют свое место, потому что они экономичны, просты и могут работать годами, говорит Кей. Их также может быть легче поддерживать и устранять неполадки для тех, кто не имеет опыта управления. «PAC часто хорошо подходят для управления более крупными процессами и интеграции таких вещей, как безопасность, движение, распределенный ввод-вывод и сетевые коммуникации», — говорит он. В случае с ПЛК вам, как правило, придется добавлять аппаратные модули для выполнения таких задач.
Сегодня, когда вы видите термин PAC, он обычно относится к продукту более высокого класса в рамках общей линейки продуктов, говорит Бургер. Поскольку PAC и ПЛК от поставщика часто используют одно и то же аппаратное обеспечение, но с разными программными возможностями, большинство людей склонны называть их ПЛК.
Программируемый логический контроллер Siemens Simatic S7-300. Промышленные ПК
Осуществление управления цехом на ПК повышенной прочности, называемом промышленным компьютером, не является новой концепцией. Линия Allen-Bradley SoftLogix, которая работала в операционных системах Windows 7 и Windows Server 2008, была ярким примером. По словам Бургера, программные ПЛК имеют ту же среду программирования и микропрограмму, что и физические ПЛК. «Программный ПЛК программируется и работает так же, как и ПЛК, просто размещается на компьютере, а не на собственном оборудовании», — говорит он. Но ПК могут запускать несколько приложений и, как правило, не являются выделенными контроллерами. В результате некоторые поставщики прекратили продажу такой продукции. Например, Allen-Bradley прекратила активную поддержку SoftLogix.
Еще одна проблема, о которой следует помнить при работе с промышленными ПК (IPC), — это необходимые обновления и исправления, как и для любого ПК. Бургер говорит, что промышленные компьютеры — это не обязательно технология, «вы ожидаете безотказной работы в течение 10 лет без отключения питания. Это именно то, что вы ожидаете от ПЛК или PAC. Мы заменяем старые решения ПЛК, которые были установлены более 30 лет назад, и это все еще оригинальное оборудование. У вас нет этого в среде ПК».
Эндрю Абрамсон, директор по работе с клиентами в Grantek, придерживается той же точки зрения. «По большей части мы видим, что промышленные ПК убираются из производственных цехов везде, где это возможно, и эти функции переносятся в централизованную виртуальную среду в сочетании с тонкими клиентами на производственных цехах», — говорит Абрамсон.
Виртуализированной средой может быть либо локальный центр обработки данных, либо облачное хранилище. Драйверы для этой миграции с физического на виртуальный (P2V) исходят от ИТ-специалистов и включают в себя защиту от будущих изменений, сокращение занимаемой площади оборудования, лучшее резервное копирование/избыточность, более низкое среднее время восстановления (MTTR), повышенную безопасность и централизованное расположение управления. добавляет Абрамсон.
IPC, безусловно, используются в производственных цехах, но в наши дни обычно используются в качестве интерфейса оператора с тонким клиентом. «ПЛК принимает все эти решения как бы в вакууме без участия человека. Но на самом деле там есть человек, и он хочет иметь возможность запускать и останавливать систему и делать, например, ваниль вместо шоколада», — говорит Бургер. Операторы должны иметь возможность наблюдать, что происходит в процессе в любой момент времени. Им нужно окно в процесс, чтобы иметь возможность вносить изменения. Роль промышленного компьютера заключается в том, что он выступает в роли ЧМИ, открывающего окно в процесс. Как правило, у вас есть ПЛК, работающий в тандеме с ЧМИ на промышленном компьютере, чтобы обеспечить полную функциональность.
С другой стороны, по словам Кея, IPC имеют некоторые преимущества в качестве контроллеров. «Вы можете запускать базы данных, преобразователи протоколов и менеджеры рецептов [на IPC]; вы даже можете запускать свое программное обеспечение SCADA и MES на том же промышленном ПК, который вы используете в качестве контроллера автоматизации».
Но это связано с компромиссами, присущими упомянутой выше платформе ПК. «Операционные системы Windows и Linux не оптимизированы для обеспечения высокой производительности в детерминированных промышленных приложениях, — говорит Кей.
Бургер отмечает, что управление на основе IPC лучше всего подходит для специализированной среды типа НИОКР, где требования не известны заранее и могут резко измениться. «Вам нужна платформа, которая способна делать совершенно разные вещи с течением времени», — говорит он. В этом случае система может выйти из строя довольно быстро, [исходя из] времени, необходимого для завершения проверки концепции, скажем, год или около того. И «если вы хотите разработать программу, например, на C++ или C#, вы не сможете сделать это на большинстве ПЛК или PAC», — добавляет он.
IPC также используются в тех случаях, когда может не быть существующего сервера или сетевой инфраструктуры для поддержки архитектуры тонкого клиента. Они также используются там, где требуется немедленная вычислительная мощность, например, в машинном зрении, добавляет Абрамсон.
Суть в том, что системы управления не являются универсальными. Небольшой традиционный ПЛК может удовлетворить требования небольшой упаковочной машины, в то время как для полного управления упаковочной линией может потребоваться ПАК с расширенными функциональными возможностями.
«Каждая система уникальна, и при выборе решения для управления мы всегда начинаем с рассмотрения требований пользователя и функциональных требований, — говорит Абрамсон. Если вам предстоит обновление, заручитесь помощью надежного партнера-системного интегратора, чтобы взвесить затраты и преимущества различных архитектур, включая первоначальные капитальные вложения, текущие расходы на обслуживание, техническую сложность клиента, а также риски или функциональные возможности, присущие этим архитектурам. технологии.
Мартин CSI
JNE Consulting
Avanceon
Siemens USA
Grantek
Rockwell Automation
Mitsubishi Electric Automation
Industrial Controllers by OnLogic | ОнЛогик
Похоже, в вашем браузере отключен JavaScript. Для наилучшего взаимодействия с нашим сайтом обязательно включите Javascript в своем браузере.
Переключить навигацию
Поиск
Поиск
Поиск
Поиск
Solutions
Промышленный контроллер OnLogic обеспечивает надежное понимание и контроль в режиме реального времени над вашим производственным оборудованием, процессами и объектами.
Решения
Промышленный контроллер OnLogic обеспечивает надежное понимание и контроль в режиме реального времени над вашим производственным оборудованием, процессами и объектами.
Интеллектуальное управление вашими процессами
Промышленные контроллеры от OnLogic обеспечивают наглядность и контроль ваших жизненно важных производственных процессов. Независимо от того, работаете ли вы на заводе или на распределенном полевом оборудовании, аппаратное обеспечение OnLogic создано для надежного промышленного применения. Увеличение времени безотказной работы приводит к получению действенной информации и большему контролю с помощью выбранного вами программного обеспечения. С помощью нашего обширного онлайн-конфигуратора и рекомендаций экспертов вы сможете создать идеальное аппаратное решение для своей промышленной системы управления.
Аппаратные решения
Наши самые популярные промышленные контроллеры
Защищенный компьютер Karbon 300
Защищенный и компактный промышленный контроллер с большим количеством входов/выходов. Надежность в сложных условиях и мобильных приложениях.
Настройка и покупка
CV-P1101 Cincoze Rugged Panel PC
Надежные функции, гибкие варианты монтажа и резистивные или емкостные дисплеи делают этот контроллер отличным аппаратным решением для промышленных контроллеров.
Настроить и купить
Посмотреть все
Промышленные контроллеры
ONLOGIC + PARTNERS
Проверенная совместимость
Ignition
Линейка OnLogic PC Ignition, поставляемая с предварительно настроенными периферийными шлюзами Ignition Onboard с аппаратным обеспечением Ignition Onboard с предварительно настроенными шлюзами и HMI ваше приложение SCADA.
Просмотреть все шлюзы Ignition Edge
ThinManager
Тонкие клиенты OnLogic сертифицированы ThinManager для беспрепятственной интеграции в виртуализацию и среду управления ИТ-инфраструктурой.
Просмотреть все тонкие клиенты с поддержкой ThinManager
Рекомендации экспертов
Мы здесь, чтобы помочь
Наши эксперты по решениям OnLogic готовы рассмотреть ваши требования и порекомендовать идеальное решение для вашего приложения.
Поговорите со специалистом по решениям
Мы здесь, чтобы убедиться, что вы получите правильное решение.
Звоните: +1 (802) 861 1590
Отправить сообщение
Начать чат
Свяжитесь с нами в рабочее время | с 8:30 до 18:00 (восточноевропейское время)
Функции и возможности
Централизованный и удаленный мониторинг информации о технологическом процессе с помощью промышленного контроллера OnLogic
Промышленные контроллеры OnLogic позволяют централизовать управление активами вашего объекта в единой точке достоверности. Сэкономьте или даже сократите время, затрачиваемое оператором на перемещение между распределенными устаревшими контроллерами. Вы также получите более быстрый контроль над своими операциями, что поможет вам быстрее принимать решения и реагировать на события в режиме реального времени.
Обзор ваших операций, составленный промышленными контроллерами OnLogic, может быть отправлен в централизованное место для визуализации на экране из любого места. Вы можете сравнить текущие операции с историческими показателями, чтобы помочь операторам достичь максимальной производительности. Создавайте усовершенствованные модели или цифровые двойники, создавая цикл обратной связи с информацией, подаваемой и оптимизируемой при развертывании вашего промышленного контроллера.
Благодаря множеству возможностей ввода-вывода, хранения, памяти и вариантов процессора вы можете подключать камеры, сетевое оборудование, приводы и другие периферийные устройства для простоты управления и контроля. Не беспокойтесь о маломощных устройствах или базовых ПЛК, оборудование промышленного контроллера OnLogic может все.
Depend OnLogic
Промышленные контроллеры — это компьютерные устройства для управления производством и технологическими процессами в средах, которые бросают вызов традиционной электронике или уничтожают ее. Сбои в работе могут привести к потере видимости, сбора данных и контроля над интеллектуальными системами. Не говоря уже о стоимости простоя.
Надежное аппаратное обеспечение контроллера дает уверенность в том, что ваши системы будут оставаться на связи и продолжать передавать и управлять вашими ценными данными. Промышленные контроллеры OnLogic отлично работают при экстремальных температурах, допускают переменную потребляемую мощность и устойчивы к ударам и вибрации. Это означает, что вы можете установить их там, где они вам нужны. Наши промышленные контроллеры доступны в безвентиляторных, компактных и прочных платформах, которые помогут вам повысить надежность и эксплуатационную гибкость в полевых условиях. Одна платформа может быть сконфигурирована для выполнения нескольких функций управления. Стандартизируйте свою инфраструктуру с помощью систем управления, созданных с учетом требований современной промышленности.
Опыт OnLogic в предоставлении компьютерного оборудования нового поколения онлайн означает, что вы можете просматривать, настраивать и оценивать аппаратное обеспечение промышленных контроллеров на нашем веб-сайте. Тем не менее, уникальные требования проектов промышленного контроля означают, что быстрый телефонный звонок с нашей командой потенциально может сэкономить вам часы или даже дни исследований. Наши опытные технические специалисты всегда готовы помочь вам максимально эффективно использовать выбранное вами устройство, поэтому обратитесь за бесплатной консультацией уже сегодня.
Ресурсы
Узнайте об оборудовании OnLogic для производства
Aenean nulla arcu, lacinia et massa id, elementum ornare nisl. Nam est turpis, mattis eu vulputate eget, interdum non mauris. Sed malesuada nibh urna, sit amet vulputate ex interdum sed. Nullam commodo libero consectetur ultrices tempus. Phasellus euismod luctus arcu, quis ultrices purus sollicitudin ac.
Loreom ipsum dolor sit amet. Lorem ipsum dolor sit amet, consetetur sadipscing elitr, sed diam…
Практический пример: Velentium
Lorem ipsum dolor sit amet, consectetur adipiscing elit. Nam lacinia et dui pulvinar dictum. Fusce volutpat ipsum и tortor varius dignissim. In sagittis nibh in nisi interdum cursus. Vivamus pharetra mi nisi, ut volutpat ex hendrerit vel…
Подробнее
Узнайте о безвентиляторных вычислениях
Lorem ipsum dolor sit amet, consectetur adipiscing elit. Nam lacinia et dui pulvinar dictum. Fusce volutpat ipsum и tortor varius dignissim. In sagittis nibh in nisi interdum cursus. Vivamus pharetra mi nisi, ut volutpat ex hendrerit vel…
Подробнее
Блог: что вы узнаете
Lorem ipsum dolor sit amet, consectetur adipiscing elit. Nam lacinia et dui pulvinar dictum. Fusce volutpat ipsum и tortor varius dignissim. In sagittis nibh in nisi interdum cursus. Vivamus pharetra mi nisi, ut volutpat ex hendrerit vel…
Подробнее
Дополнительный видеоблок
Aenean nulla arcu, lacinia et massa id, elementum ornare nisl. Nam est turpis, mattis eu vulputate eget, interdum non mauris. Sed malesuada nibh urna, sit amet vulputate ex interdum sed. Nullam commodo libero consectetur ultrices tempus. Phasellus euismod luctus arcu, quis ultrices purus sollicitudin ac. Nam est turpis, mattis eu vulputate eget, interdum non mauris. Sed malesuada nibh urna, sit amet vulputate ex interdum sed. Nullam commodo libero consectetur ultrices tempus.
OnLogic предлагает бесплатную экономичную доставку по США для всех онлайн-заказов на сумму от 250 долларов США. Если ваша покупка соответствует условиям бесплатной экономичной доставки, вы увидите, что эта опция доступна во время оформления заказа.
Мы предлагаем бесплатную эконом-доставку только для заказов, отправленных в пределах 48 нижних штатов США (за исключением Гавайев и Аляски). Для канадских и международных клиентов у нас есть вариант экономичной доставки, доступный через USPS для определенных продуктов. Для небольших компонентов это может помочь снизить общую стоимость доставки.
Для европейских клиентов у нас есть веб-сайт и магазин, расположенный в ЕС по адресу www.onlogic.com/eu-en/. Если есть что-то, чего вы не видите на европейском сайте, свяжитесь с нами по адресу [email protected].
Начать возврат
Доставка
Покупатели несут ответственность за все транспортные и страховые расходы. OnLogic отправит в любую точку США, Канады и, по своему усмотрению и на определенных условиях, в другие страны мира. Если заказанные товары есть на складе и оплата клиентом подтверждена, заказы, состоящие исключительно из компонентов (без встроенных систем), размещенные до 17:00. Восточное стандартное время обычно отправляется в тот же рабочий день, если в качестве способа доставки используется UPS.
Обратите внимание: это не гарантируется. Заказы на продукты, состоящие из нескольких компонентов, которые были собраны в систему компанией OnLogic или для нее, обычно требуют 3–5 полных рабочих дней для сборки и тестирования. Объемные заказы могут занять больше времени. Срочные заказы на системы должны быть размещены до 13:00. Восточное стандартное время, чтобы отправить к концу рабочего дня на следующий день.
Подробная информация о доставкеМеждународная информация
Вы используете веб-браузер, который не поддерживается OnLogic.
Microsoft Internet Explorer версии 11 и старше не поддерживаются. Вы столкнетесь с трудностями используя наш сайт, и оплата не будет работать. Чтобы получить лучший опыт, перейдите на один из этих сайтов и получить последнюю версию предпочтительного браузера.
EZAutomation Industry Статья | Выбор контроллера автоматизации производства
Вайдьянатх «Док» Нанджундая
Вопрос на миллион долларов, который волнует каждого инженера по системам управления: «Какой контроллер мне следует использовать для этого приложения?» Иногда ответ очень прост, но часто он усложняется. Все зависит от процесса или приложения. Итак, давайте обсудим это подробно. Начнем с различных доступных устройств управления.
Существует 3 основных типа контроллеров, которые используются во всем мире для управления процессами или приложениями.
1) ПЛК или программируемый логический контроллер.
2) PAC или контроллер автоматизации процессов.
3) РСУ или распределенная система управления.
Старые системы управления на основе реле были заменены на ПЛК. В прошлом ПЛК использовались только для включения/выключения или дискретного управления. Но с тех пор ПЛК развились. ПЛК второго поколения могут делать гораздо больше, чем просто дискретный ввод-вывод. Они имеют аналоговые модули (ток/напряжение), модули термопар, модули RTD, высокоскоростные счетчики, модули управления движением, модули связи и возможность подключения к SQL и OPC. Затем появилось третье поколение, которое имеет гораздо больше возможностей, таких как регистрация данных (локальная), поддержка электронной почты (сигналы тревоги) и поддержка IIoT (MQTT) для связи с облаком для отправки данных в реальном времени.
ПЛК или программируемый логический контроллер: Для управления машиной может использоваться простой ПЛК, в основном дискретный (ВКЛ/ВЫКЛ). Некоторые ПЛК также могут обрабатывать ограниченное количество аналоговых сигналов. ПЛК могут быть фиксированного ввода-вывода или модульного типа; в котором вы можете выбрать модули ввода/вывода в соответствии с вашим приложением. Память ПЛК и связь со сторонними устройствами будут ограничены. Однако они очень надежны и экономичны для управления простыми автономными машинами.
PAC или контроллер автоматизации процессов: 9Контроллеры автоматизации процессов 0084 имеют поддержку всех цифровых и аналоговых входов/выходов, более высокую вычислительную мощность и больше памяти. Возможность расширения или масштабирования для поддержки тысяч входов/выходов, особенно аналоговых сигналов. Он может быть настроен для выполнения расширенных функций и может быть шлюзом для различных протоколов или сетей. Они используются для связи, мониторинга и управления оборудованием в нескольких сетях и устройствах. Он может взаимодействовать с SQL и OPC. PAC могут выполнять регистрацию данных, сценарии, а также могут быть устройством Edge of Network Gateway. Некоторые процессоры поддерживают IIoT (MQTT). Он может отправлять или публиковать данные в режиме реального времени авторизованным подписчикам, которые могут получать их в любой точке мира в режиме реального времени. Философия, лежащая в основе IIoT, заключается в том, что умные машины лучше людей точно и последовательно собирают и передают данные. Протокол IIoT и MQTT может выступать в качестве моста между существующими операционными технологиями на предприятии. Можно надежно и безопасно обмениваться ценными данными для повышения производительности и эффективности предприятия.
РСУ или распределенная система управления: Как следует из названия, РСУ распределяется по всему предприятию, а не централизованно. Но информация обменивается/разделяется между системами. РСУ состоит из большого количества контроллеров в разных частях предприятия, но они связаны между собой с помощью расширенного сетевого протокола.
Время отклика или время обработки DCS меньше, чем у PLC или PAC. В таких отраслях, как нефтегазовая и химическая промышленность, требуется РСУ. Он специально разработан для управления сложными, крупными и географически распределенными приложениями в промышленных процессах. Визуализация и управление системой DCS может осуществляться с помощью SCADA в диспетчерской, привязанной к системе DCS.
Рассмотрение и заключение: Какой тип контроллера использовать?
Тип приложения: Это автономное приложение или оно должно контролировать процесс или всю установку?
ПЛК идеально подходят для любого простого автономного управления машиной. Как правило, вам не потребуется слишком много входов/выходов.
Если вам нужно контролировать весь процесс, то рекомендуется выбрать PAC, так как сеть и расширение проще. Для управления всем предприятием с большой географической территорией вам потребуется использовать РСУ.
Среда приложения: Среда приложения играет огромную роль. Температура, пыль, вибрация, масло, электрический шум и т. д. Различные контроллеры имеют разные возможности. Рассчитан ли контроллер на работу в среде, подверженной воздействию всех или некоторых из этих факторов? Выбор правильной марки и модели играет огромную роль.
Сбор данных: Нужна ли вашему приложению регистрация данных? Вам нужны исторические данные или данные в реальном времени? Или вам нужны оба? Не все контроллеры имеют возможность вести локальную регистрацию данных. Может ли контроллер отправлять данные в режиме реального времени для принятия решений в реальном времени для повышения производительности и эффективности предприятия? Выберите контроллер с поддержкой IIoT (MQTT).
Как правило, используйте:
- ПЛК: Простое автономное управление станком.
- PAC: для управления сложным процессом, который требует расширения, а также для связи, мониторинга и управления оборудованием в нескольких сетях и устройствах.
- DCS: для управления сложной, географически распределенной установкой.
Варианты контроллеров промышленной автоматизации для пекарен
Автоматизация все чаще используется в промышленной выпечке. Обработка ингредиентов, поддоны, складирование и упаковка автоматизированы. Все больше пекарен также обращаются к автоматизации своих складов, чтобы упорядочить товары и максимально увеличить срок годности своей продукции, свести к минимуму ущерб и решить проблемы с пропускной способностью. Но что входит в эти контроллеры автоматизации и как они работают? Пришло время разобраться с вариантами контроллеров промышленной автоматизации для пекарен. Давайте начнем.
Выбор ПЛК, PAC или IPC
В зависимости от вашей пекарни автоматизация может обеспечить либо индивидуальное управление отдельной машиной, либо комплексное решение для всего предприятия. В зависимости от ваших потребностей один тип контроллера может быть лучше для вашей пекарни, чем другие. Программируемые логические контроллеры (PLC), программируемые контроллеры автоматизации (PAC) и промышленные персональные компьютеры (IPC) способны автоматизировать станцию, машину или весь машинный этаж. Для модульного подхода, при котором система разбита на логические части или функции, вы можете использовать ПЛК меньшего размера.
Задача здесь состоит в том, чтобы решить, хотите ли вы запустить всю программу на одном ПЛК или разделить все на подсистемы, которые работают между меньшими или микро-ПЛК. Поскольку единая среда программирования неизбежно экономит деньги и время (поскольку ПЛК можно переоборудовать), большинство пекарен выбирают этот путь.
Тем не менее, контроллеры PLC, PAC и IPC находят применение в промышленной выпечке. Чтобы решить, какой вариант лучше, учитывайте следующие факторы:
- Новые и существующие системы автоматизации в вашей пекарне
- Аналоговые устройства
- Контур управления
- Экологические проблемы
- Дискретные устройства
- Специальные функции или модули
- Программирование
- Связь
- Локальные и удаленные места ввода-вывода
Например, если у вас уже есть автоматизированная система, рекомендуется выбрать контроллер, совместимый с существующей системой. К сожалению, некоторые контроллеры, даже разработанные одним и тем же производителем, несовместимы с другими.
Определение количества устройств ввода-вывода
Когда вы планируете автоматизировать свою пекарню, рекомендуется составить список всех устройств ввода-вывода на вашем предприятии. Перечислите аналоговые датчики, цифровые датчики, регулирующие клапаны, приводы и т. д. Включите информацию о требованиях к питанию, сигналам и связи.
Количество точек ввода-вывода в вашей пекарне помогает определить, какой контроллер автоматизации является лучшим. Пекарни обычно совершают ошибку, внедряя системы управления, которые идеально подходят для их текущего производства, но не оставляют возможности для роста. Рекомендуется предусмотреть дополнительные 20 % ввода-вывода, чтобы избежать каких-либо проблем с будущим расширением.
Вы также хотите рассмотреть любое специальное оборудование в своей пекарне, включая высокоскоростное устройство вывода, высокоскоростной счет, часы реального времени и так далее. Некоторые машины со специальными функциями могут не поддерживаться контроллерами.
Коммуникация
Выяснение того, как вся система будет взаимодействовать, — это шаг, который необходимо выполнить на раннем этапе. Некоторые контроллеры имеют один или два порта для программирования, в то время как другие могут подключаться к нескольким ПЛК и устройствам на предприятии.
Прежде чем выбрать контроллер автоматизации, обратите внимание на другие устройства, используемые для связи, такие как промышленный Ethernet и человеко-машинные интерфейсы (ЧМИ). Опишите протоколы Ethernet, такие как Modbus TCP, Ethernet/IP или любые другие. Выбранный вами контроллер должен поддерживать данный тип связи сейчас и в будущем.
Требуемое аппаратное и программное обеспечение
Ваша автоматизированная система управления должна иметь достаточно памяти для удовлетворения требований различных программ и потоков данных. Количество устройств, поддерживаемых контроллером, также влияет на то, насколько хорошо он обрабатывает данные. Точно так же, если в вашей пекарне есть машины с несколькими последовательностями и сложными функциями управления, такими как замешивание и приготовление различных видов теста, или хранится несколько рецептов, это требует повышенного уровня памяти и вычислительной мощности.
Помимо требований к оборудованию для вашего контроллера автоматизации, также должно быть доступно достаточное количество программного обеспечения. Чем более продвинутый контроллер, тем более искусно написанное программное обеспечение становится необходимым. Не выбирайте контроллер, для которого также нет приличного количества литературы с подробным описанием его возможностей. Если компания, занимающаяся разработкой систем автоматизации, предлагает обучение работе со своими системами управления, это принесет пользу вам и вашей пекарне в долгосрочной перспективе.
Должен ли я выбрать ПЛК, PAC или IPC для моей пекарни?
В конце концов, система управления автоматизацией, которую вы выбираете для своей пекарни, повышает производительность и эффективность. В большинстве случаев пекарни выбирают между PLC и PAC. Хотя эти системы похожи, необходимо учитывать некоторые различия, такие как несколько процессорных модулей в одной стойке, возможности многозадачности, языки программирования, адресация на основе тегов, распределенная система управления (функциональность), стандартная сеть ПК и управление движением. PAC более гибкие, чем ПЛК, поскольку они используют сеть Ethernet. Однако ПЛК становятся все более похожими на PAC.
PAC оптимальны, если вы хотите стандартизировать один тип ввода-вывода и процессор, поскольку PAC предназначены для работы со многими приложениями. ПЛК лучше работают с автономными машинами и устройствами. Если вы не уверены, какой контроллер подходит для вашей пекарни, обратитесь за консультацией в компанию по автоматизации.
Ищете надежные компании по промышленной автоматизации рядом со мной?
Несмотря на то, что существует множество вариантов контроллеров автоматизации, вам нужно только самое лучшее для вашей пекарни. Подумайте о процессах, происходящих в вашей компании, и о том, что вы хотите улучшить. В зависимости от имеющейся технологии, а также среды вам может понадобиться либо ПЛК, либо PAC.
У вас есть вопросы о системах управления для вашей пекарни? У EZSoft есть решения для вас. С 1999 года EZSoft помогает различным отраслям, в том числе пищевой промышленности и производству напитков, автоматизировать их производство. Если вы хотите повысить производительность и эффективность, самое время позвонить в EZSoft по телефону (484) 568-5040.
Как выбрать контроллер промышленной автоматизации
При выборе контроллера промышленной автоматизации необходимо учитывать несколько важных моментов, а не только эти , в которых есть слова PLC, PAC или IPC . Требования к приложениям должны быть четко определены, а потребности в масштабируемости должны быть приняты во внимание до того, как будет сделан выбор.
Начнем с разделения потребностей оборудования в эксплуатации, что поможет пользователям оценить диапазон контроллеров, указанный производителями машин. Система автоматизации может предоставлять комплексное решение или индивидуальное управление, в зависимости от того, как она вписывается в производственный сценарий.
Программируемый логический контроллер (PLC), программируемый контроллер автоматизации (PAC) или промышленный персональный компьютер (IPC) могут обеспечивать управление отдельной станцией, машиной, сборочной линией или даже всем цехом. В случае интегрированной производственной системы для сквозного управления можно использовать один большой контроллер с удаленными базами ввода/вывода, обменивающийся данными через Ethernet. Однако могут быть случаи, когда приложение может потребовать модульного подхода, когда разбиение системы автоматизации на логические части было бы более подходящим. В таких случаях автоматизация разделяется на части и распределяется между меньшими ПЛК в зависимости от рабочей нагрузки.
Некоторые эксперты по автоматизации рассматривают эти два решения как далекие друг от друга и заключают, что для них обоих требуются разные платформы. Но это не обязательно должно быть правдой. Некоторые производители предлагают контроллеры различных размеров, совместимые с одним и тем же программным обеспечением. Наличие единой среды программирования означает, что системе можно придать гибкость, а затраты, связанные с разработкой программы, можно сократить, поскольку проекты можно переносить с одного ПЛК на другой.
Однако сложно решить, использовать ли большой ПЛК для одной программы или использовать модульный подход. Решение намного сложнее, чем выбор ПЛК , PAC или контроллера на базе ПК. Учет следующих факторов может помочь создать хорошую базу:
- Новая или существующая система
- Дискретные устройства
- Экологические проблемы
- Контур управления
- Аналоговые устройства
- Специальные модули
- места ввода-вывода
- Связь
- Программирование
Независимо от того, является система новой или уже существующей, это может помочь устранить множество недоразумений и повлиять на оставшиеся факторы выбора. Если продукты уже установлены, совместимость приобретает первостепенное значение, нейтрализуя количество бесполезных продуктов.
Выбор контроллера также зависит от условий окружающей среды. Если существуют экстремальные условия, например, связанные с температурой, влажностью, пылью и т. д., то контроллер должен соответствовать им, чтобы оставаться в рабочем состоянии.
Количество, типы и расположение входов/выходовОпределение количества входов/выходов и типов полевых устройств находится далее в списке. Начните с перечисления всех дискретных входов и выходов в электронной таблице, определяя каждый тип, например. цифровой датчик, аналоговый датчик, исполнительный механизм, регулирующий клапан и т. д. Параметры, которые необходимо записать, включают протокол связи, эквивалентную мощность и т. д.
Тип и количество точек ввода/вывода оказывают большое влияние на выбор системы управления Платформа. Машиностроители часто совершают ошибку, выбирая контроллеры, которые могут удовлетворить текущие потребности, не оставляя места для будущего расширения. Предоставив пространство для расширения как минимум на 20 %, ввод-вывод может предотвратить серьезные кризисы в будущем. Есть также некоторые контроллеры, которые имеют ограниченные типы входов/выходов, такие как аналоговые, высокоскоростные входы и т. д. Это также может стать проблемой в будущем.
Упомянутая ранее электронная таблица должна включать функции и уровни сигналов всех аналоговых устройств, включая отдельные суммарные значения для контура ток/напряжение, входы резистивных датчиков температуры, термопары и т. д. Спецификации контроллеров должны соответствовать этим требованиям, чтобы все аналоговые поддерживаются входы и выходы, а также их типы сигналов.
Кроме того, специальные входы/выходы также должны быть перечислены в электронной таблице. К ним могут относиться, помимо прочего, высокоскоростные входы/выходы, счетчики, часы реального времени и серво/шаговые двигатели. Могут быть контроллеры, которые могут не иметь специальных функций, поэтому обязательно проведите тщательный анализ, прежде чем принимать решение. Понимание возможностей контроллера и требований приложения имеет важное значение.
Физическое расположение клемм ввода/вывода также должно быть определено по отношению к полевым устройствам и записано в электронной таблице. Разбивка этих требований на более мелкие модули поможет понять потребности локального и удаленного ввода-вывода, что, в свою очередь, поможет определить, какие протоколы связи в реальном времени необходимы. Есть некоторые установки, где предпочтительнее локальность, в то время как другие в значительной степени зависят от удаленного ввода-вывода.
Если расстояние между контроллерами и подсистемами велико, удаленный ввод-вывод будет хорошим выбором вместо мучительного подключения каждого полевого устройства. Кроме того, должны поддерживаться методы и скорости связи, будь то последовательный ввод-вывод или ввод-вывод на базе Ethernet. В современных промышленных условиях становятся популярными протоколы Ethernet, такие как EtherNet/IP, наряду со специально разработанными версиями протоколов с открытым исходным кодом, таких как Modbus.
Коммуникации между периферийными устройствами, распределенным вводом-выводом, ПЛК и корпоративными системами могут быть необходимы на некоторых производственных этажах. Масштабы их должны быть определены на ранней стадии с учетом того, что по мере продвижения вперед все будет становиться все сложнее. Некоторые контроллеры могут предлагать только 1–2 порта, один из которых будет зарезервирован для программирования, в то время как другие могут не поддерживать определенные протоколы, необходимые для критически важных приложений.
Также необходимо указать связь, которая будет осуществляться между контроллером и HMI или полевыми устройствами. С появлением Интернета вещей важно иметь открытые возможности для связи. Поэтому необходимо убедиться, что в контроллере имеются дополнительные порты Ethernet, последовательный порт, USB.
Необходимо выполнить спецификацию протоколов Ethernet, таких как Modbus TCP, Ethernet/IP, Profibus и т. д., как для текущих требований, так и для будущего расширения.
Общие параметры аппаратного обеспечения, которые необходимо учитывать, включают скорость сканирования, объем памяти и резервный аккумулятор. Контроллер должен иметь достаточно системной памяти для поддержки как программных требований, так и данных. Эти оценки можно сделать, выяснив количество устройств в системе. Память данных используется как для динамической обработки данных, так и для хранения переменных, например, предустановленных уставок, внутренних флагов в таймерах и накопленного времени/отсчетов.
Размер таблицы данных может увеличиться, если есть необходимость хранить исторические данные на контроллере. Потребность в регистрации данных, интерфейсах для HMI/SCADA , методах доступа и архивных базах данных должны быть четко определены, в то время как в сценарии IIoT также становятся важными потребности в сети, определении протокола и памяти.
Типы инструкций и размер самой программы также могут влиять на потребность в памяти. Если программа имеет несколько последовательностей, сложные функции управления и логику ошибок, то это может потребовать увеличения объема памяти. Требования могут быть оценены на основе звеньев программы и файлов данных. Спецификации контроллера также должны быть изучены, так как некоторые имеют программирование на основе имен тегов, в то время как другие имеют фиксированные, но расширяемые таблицы данных.
Объем памяти, потребляемый программами и таблицами данных, зависит от модели контроллера. Хорошим допущением является то, что каждое дискретное устройство ввода/вывода использует 5–100 слов памяти, а аналоговый ввод/вывод использует 25–500 слов. Широкий диапазон может затруднить оценку сложных программ. Лучшим подходом было бы написать несколько блоков кода и изучить использование памяти.
Могут быть приложения, которым требуется быстрое время сканирования, а также скорость процессора контроллера и скорость выполнения инструкций, а также оба пагубных фактора по отношению к этому.
Почти половина проекта зависит от качества программирования программного обеспечения, которое, в свою очередь, зависит от программного обеспечения, предоставляемого производителем. При выборе программного обеспечения для программирования контроллера необходимо учитывать следующие факторы:
- Простота использования
- Настройки
- Инвестиции
- Учебные ресурсы
- Регистрация данных и удаленный доступ
Большинство контроллеров часто включают в себя бесплатное и простое в использовании программное обеспечение для программирования, содержащее около 20 инструкций, таких как таймеры, катушки, контакты, счетчики и т. д., которых достаточно для небольших приложений. Но по мере увеличения сложности требований могут возникнуть проблемы. Усовершенствованные контроллеры часто включают комплексное программное обеспечение для программирования, которое включает в себя множество функций, помогающих программистам.
Выбор программного обеспечения для программирования во многом зависит от зоны комфорта пользователя, что делает его субъективным решением. Программисты могут иметь свое собственное мнение относительно выбора программного обеспечения, но оно часто отвергается высшим руководством, которое применяет стандартное программное обеспечение для программирования контроллера, а также методы.
Несмотря на это, контроллер не следует выбирать, если для него недостаточно литературы с подробным описанием его программного обеспечения. Большинство производителей уже адаптировались к тенденции онлайн-ресурсов, предлагая подробную документацию, а также создавая форумы, на которых коллеги-программисты могут обмениваться вопросами. Однако не все сели на этот поезд; так тщательно проверяет биографические данные следует ввести перед выбором ПЛК .
Стоимость технической поддержки также должна быть учтена, поскольку могут быть случаи, когда документация может не помочь решить конкретную проблему. Есть поставщики, которые предлагают бесплатные услуги в течение ограниченного времени, что может быть полезно, если соблюдается график разработки программы.
После разработки программа должна быть тщательно протестирована, а для этого программное обеспечение должно быть доступно для просмотра в форме отклика контура ПИД-регулятора и профиль движения. Это позволит провести моделирование в полном объеме. Современное программное обеспечение для разработки интегрировано с симуляторами, которые позволяют проводить полноценное тестирование без необходимости подключения к оборудованию.
Безусловно, вам следует воздерживаться от использования универсального подхода, будь то программное обеспечение, аппаратное обеспечение или средства связи. Выбранный контроллер должен полностью соответствовать требованиям автоматизации, но при этом иметь возможности для усовершенствования по мере изменения конструкции.
Вам также может быть интересно прочитать
- Три грани PID
- Функции ПЛК
- Как ранжировать контроллеры
✅ ПЛК Raspberry Pi — промышленный контроллер для решений автоматизации
ПЛК Raspberry Pi обеспечивает адаптацию ко всем типам датчиков, данных и вариантов связи.
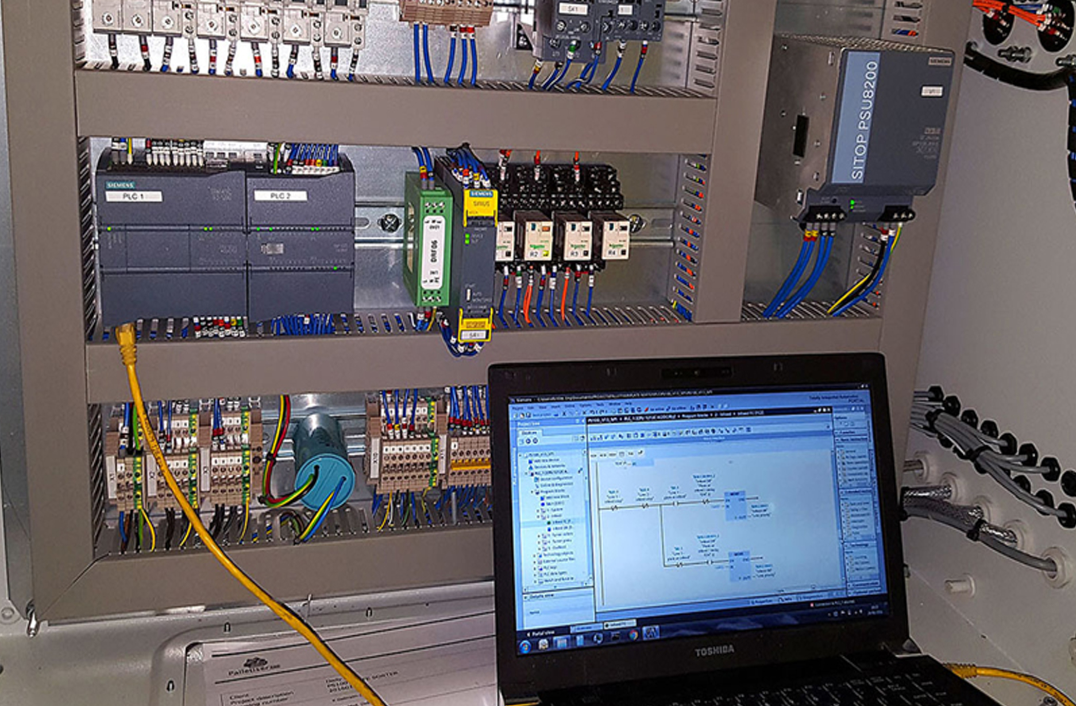
Тоже контроль? Без проблем. Ваши проекты управления выходят на новый уровень благодаря ПЛК Raspberry.
Ассортимент продукции>>Все в одном
С ПЛК Raspberry Pi у вас есть все в одном устройстве.
Основные характеристики ПЛК
Raspberry PiПЛК Raspberry Pi обладает наиболее важными функциями для повышения скорости процесса, использования широкого спектра соединений и защиты ваших данных и вашей операционной системы.
ИБП — БЕСПЕРЕБОЙНОЕ ПИТАНИЕЗащитите свою операционную систему, текущие процессы и данные с помощью источника бесперебойного питания, который гарантирует корректное завершение работы в случае сбоя питания.
ВЫСОКАЯ СКОРОСТЬ ОБРАБОТКИ
Raspberry Pi обеспечивает высокую скорость обработки по сравнению с большинством обычных ПЛК.
МНОГОПРОЦЕССНЫЙ
Работа с приложениями в режиме реального времени и возможность многопроцессорности.