Как производят литий-ионные аккумуляторы. Какие этапы включает процесс производства. Какое оборудование используется при изготовлении литий-ионных батарей. Какие инновации применяются в производстве аккумуляторов.
Основные этапы производства литий-ионных аккумуляторов
Производство литий-ионных аккумуляторов состоит из трех ключевых этапов:
- Изготовление электродов
- Сборка элементов
- Окончательная обработка элементов
Каждый из этих этапов включает несколько подпроцессов, начиная от нанесения покрытия на анод и катод и заканчивая сборкой всех компонентов, тестированием и упаковкой готовых аккумуляторных элементов.
Изготовление электродов для литий-ионных аккумуляторов
Первый этап производства литий-ионных аккумуляторов включает следующие основные процессы:
- Смешивание электродных материалов с проводящим связующим
- Нанесение полученной суспензии на токосъемники
- Сушка электродов в специальных печах
- Каландрирование для придания нужных физических свойств
- Резка электродов на полосы нужного размера
- Финальная вакуумная сушка
Какое оборудование используется для изготовления электродов?
Основное оборудование на этапе производства электродов включает:
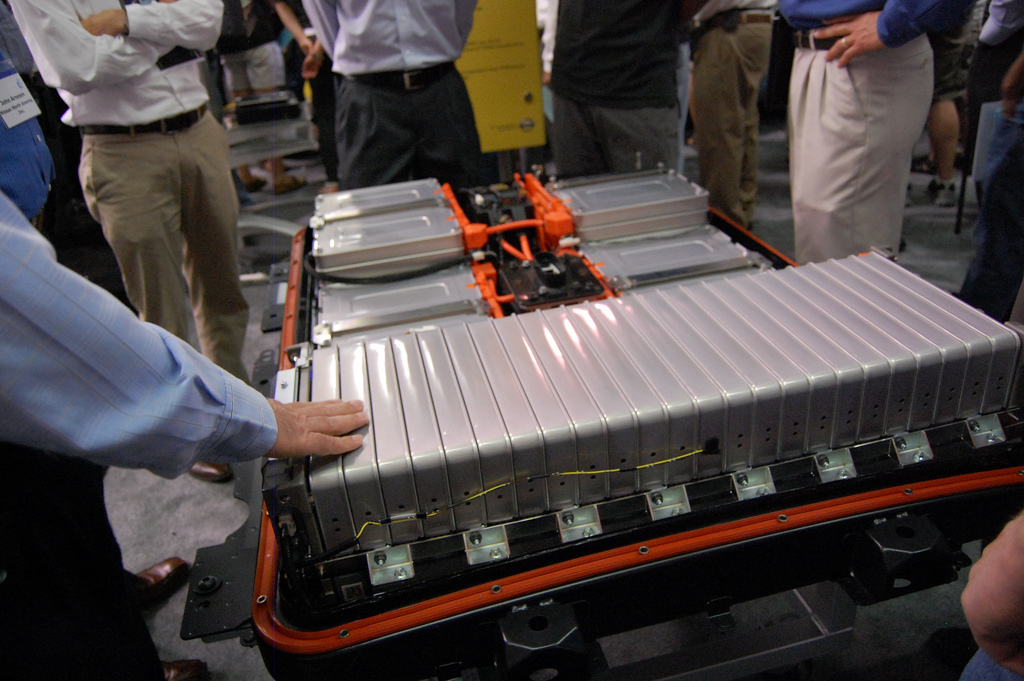
- Смесители для приготовления электродных суспензий
- Машины для нанесения покрытий
- Сушильные печи
- Каландры для прессования электродов
- Станки для резки электродов
- Вакуумные сушильные шкафы
Процесс сборки элементов литий-ионных аккумуляторов
На этапе сборки выполняются следующие ключевые операции:
- Укладка сепаратора между анодом и катодом
- Намотка или штабелирование электродов в зависимости от типа ячейки
- Сварка токовыводов и установка предохранительных устройств
- Помещение собранной структуры в корпус элемента
- Герметизация корпуса
- Заполнение ячейки электролитом
- Окончательная герметизация
Оборудование для сборки аккумуляторных ячеек
Основные типы оборудования, применяемого на этапе сборки:
- Машины для резки сепаратора
- Намоточные станки
- Сварочное оборудование
- Машины для герметизации корпусов
- Оборудование для заполнения электролитом
Финальная обработка литий-ионных аккумуляторов
Заключительный этап производства включает следующие процессы:
- Формирование защитного слоя на электродах (процесс пласта)
- Дегазация ячеек
- Старение аккумуляторов
- Тестирование характеристик
- Сортировка и отбраковка
Какое оборудование применяется для финальной обработки?
Основные виды оборудования на заключительном этапе:

- Формовочные стенды
- Камеры для дегазации
- Шкафы для старения аккумуляторов
- Тестовое оборудование
- Сортировочные машины
Инновации в производстве литий-ионных аккумуляторов
- Новые методы смешивания и нанесения электродных материалов
- Одновременное нанесение покрытия на обе стороны токосъемника
- Сухое нанесение активных материалов без использования растворителей
- Применение инфракрасного нагрева в сушильных печах
- Непрерывное ламинирование электродов и сепаратора
Эти инновации позволяют повысить производительность, качество продукции и снизить производственные затраты.
Роль вакуума в производстве литий-ионных аккумуляторов
Вакуум играет важнейшую роль практически на всех этапах производства литий-ионных батарей:
- При смешивании электродной суспензии — для предотвращения попадания пузырьков воздуха
- В процессе сушки электродов — для удаления влаги и растворителей
- При заполнении ячеек электролитом — для равномерного распределения
- При пропитке элементов — для обеспечения контакта без пустот
- При дегазации электролита — для удаления пузырьков воздуха
Без применения вакуума многие этапы производства были бы невозможны или неэффективны.

Ключевые производители оборудования для изготовления литий-ионных аккумуляторов
Основными поставщиками оборудования для производства литий-ионных батарей являются компании из следующих стран:
- Китай
- Япония
- Южная Корея
Эти страны лидируют не только в производстве самих аккумуляторов, но и в разработке и поставках технологического оборудования для их изготовления.
«Росатом» открыл в Москве новое производство литий-ионных аккумуляторов
https://ria.ru/20221214/akkumulyatory-1838605894.html
«Росатом» открыл в Москве новое производство литий-ионных аккумуляторов
«Росатом» открыл в Москве новое производство литий-ионных аккумуляторов — РИА Новости, 14.12.2022
«Росатом» открыл в Москве новое производство литий-ионных аккумуляторов
«Росатом» открыл в Москве новое сборочное производство литий-ионных систем накопления энергии — его первой продукцией стали тяговые аккумуляторные батареи для… РИА Новости, 14.12.2022
2022-12-14T14:43
2022-12-14T14:43
2022-12-14T16:29
экономика
технологии
москва
санкт-петербург
государственная корпорация по атомной энергии «росатом»
твэл
россия
/html/head/meta[@name=’og:title’]/@content
/html/head/meta[@name=’og:description’]/@content
https://cdnn21.img.ria.ru/images/07e5/0c/09/1762953823_0:146:3072:1874_1920x0_80_0_0_3685bb477f7b7f7f4995896e24ce7d22. jpg
МОСКВА, 14 дек — РИА Новости. «Росатом» открыл в Москве новое сборочное производство литий-ионных систем накопления энергии — его первой продукцией стали тяговые аккумуляторные батареи для троллейбусов, которые будут работать на улицах Санкт-Петербурга.Церемония открытия производства, расположенного на территории Московского завода полиметаллов (МЗП, входящего в топливную компанию ТВЭЛ «Росатома»), прошла в среду.»Первыми образцами, собранными на площадке, стали тяговые аккумуляторные батареи для троллейбусов с увеличенным автономным ходом, предназначенные для работы на городских маршрутах в Санкт-Петербурге», — говорится в сообщении ТВЭЛ.Серийное производство батарей для электротранспорта и стационарных систем накопления энергии создано входящей в ТВЭЛ компанией «Рэнера» — интегратором атомной отрасли по системам накопления энергии. Мощность нового производства на МЗП в 10 раз выше по сравнению с опытным производственным участком, созданным на предприятии в 2021 году. Годовой объем выпуска продукции составит до 150 МВт-ч батарей для стационарных систем (совокупная емкость выпускаемых устройств) или порядка 2 тысяч тяговых аккумуляторных батарей для электротранспорта. В портфель заказов производства на 2023 год входят тяговые аккумуляторные батареи для городского общественного электротранспорта. Также запланирован выпуск опытных образцов батарей для линейки легкового электротранспорта российского производства. Подтвержденные потребности на стационарные системы накопления энергии составляют не менее 50 МВт-ч.»Рэнера» также реализует проект по строительству в Калининградской области завода по производству литий-ионных ячеек и аккумуляторных батарей. Президент АО «ТВЭЛ» Наталья Никипелова на церемонии отметила, что завод общей мощностью выпускаемых устройств около 4 ГВт-ч в год заработает в 2025 году, а в 2024-м «там будет запущен сборочный участок», передаёт корреспондент РИА Новости.»Поскольку мы понимаем, что до 2024 года потребности Российской Федерации не могут не удовлетворяться, мы и решили создать здесь в Москве этот относительно небольшой, но большой, на самом деле, по масштабам рынка в России, сборочный участок», — пояснила она.»Наши решения сейчас представлены в транспортных применениях от электрокартов до карьерных самосвалов, в стационарных системах — от киловатного класса накопителей до мегаватного класса накопителей», — добавил гендиректор «Рэнеры» Александр Камашев.
https://ria.ru/20221214/nauka-1838593406.html
https://ria.ru/20221206/rzm-1836479079.html
https://ria.ru/20211209/akkumulyator-1762953831.html
москва
санкт-петербург
россия
РИА Новости
1
5
4.7
96
7 495 645-6601
ФГУП МИА «Россия сегодня»
https://xn--c1acbl2abdlkab1og.xn--p1ai/awards/
2022
РИА Новости
1
5
4.7
96
7 495 645-6601
ФГУП МИА «Россия сегодня»
https://xn--c1acbl2abdlkab1og.xn--p1ai/awards/
Новости
ru-RU
https://ria.ru/docs/about/copyright.html
https://xn--c1acbl2abdlkab1og.xn--p1ai/
РИА Новости
1
5
4.7
96
7 495 645-6601
ФГУП МИА «Россия сегодня»
https://xn--c1acbl2abdlkab1og.xn--p1ai/awards/
1920
1080
true
1920
1440
true
https://cdnn21. img.ria.ru/images/07e5/0c/09/1762953823_0:0:2732:2048_1920x0_80_0_0_1ac1c25459aee89577fa335de6fcdfcd.jpg
1920
1920
true
РИА Новости
1
5
4.7
96
7 495 645-6601
ФГУП МИА «Россия сегодня»
https://xn--c1acbl2abdlkab1og.xn--p1ai/awards/
РИА Новости
1
5
4.7
96
7 495 645-6601
ФГУП МИА «Россия сегодня»
https://xn--c1acbl2abdlkab1og.xn--p1ai/awards/
экономика, технологии, москва, санкт-петербург, государственная корпорация по атомной энергии «росатом», твэл, россия
Экономика, Технологии, Москва, Санкт-Петербург, Государственная корпорация по атомной энергии «Росатом», ТВЭЛ, Россия
МОСКВА, 14 дек — РИА Новости. «Росатом» открыл в Москве новое сборочное производство литий-ионных систем накопления энергии — его первой продукцией стали тяговые аккумуляторные батареи для троллейбусов, которые будут работать на улицах Санкт-Петербурга.
Церемония открытия производства, расположенного на территории Московского завода полиметаллов (МЗП, входящего в топливную компанию ТВЭЛ «Росатома»), прошла в среду.
Главные события 2022 года в российской науке
14 декабря 2022, 14:23
«Первыми образцами, собранными на площадке, стали тяговые аккумуляторные батареи для троллейбусов с увеличенным автономным ходом, предназначенные для работы на городских маршрутах в Санкт-Петербурге», — говорится в сообщении ТВЭЛ.
Серийное производство батарей для электротранспорта и стационарных систем накопления энергии создано входящей в ТВЭЛ компанией «Рэнера» — интегратором атомной отрасли по системам накопления энергии. Мощность нового производства на МЗП в 10 раз выше по сравнению с опытным производственным участком, созданным на предприятии в 2021 году. Годовой объем выпуска продукции составит до 150 МВт-ч батарей для стационарных систем (совокупная емкость выпускаемых устройств) или порядка 2 тысяч тяговых аккумуляторных батарей для электротранспорта.
В портфель заказов производства на 2023 год входят тяговые аккумуляторные батареи для городского общественного электротранспорта. Также запланирован выпуск опытных образцов батарей для линейки легкового электротранспорта российского производства. Подтвержденные потребности на стационарные системы накопления энергии составляют не менее 50 МВт-ч.
«Это отразится на всем»: в России возродят важнейшую отрасль промышленности
6 декабря 2022, 08:00
«Рэнера» также реализует проект по строительству в Калининградской области завода по производству литий-ионных ячеек и аккумуляторных батарей. Президент АО «ТВЭЛ» Наталья Никипелова на церемонии отметила, что завод общей мощностью выпускаемых устройств около 4 ГВт-ч в год заработает в 2025 году, а в 2024-м «там будет запущен сборочный участок», передаёт корреспондент РИА Новости.
«Поскольку мы понимаем, что до 2024 года потребности Российской Федерации не могут не удовлетворяться, мы и решили создать здесь в Москве этот относительно небольшой, но большой, на самом деле, по масштабам рынка в России, сборочный участок», — пояснила она.
«Наши решения сейчас представлены в транспортных применениях от электрокартов до карьерных самосвалов, в стационарных системах — от киловатного класса накопителей до мегаватного класса накопителей», — добавил гендиректор «Рэнеры» Александр Камашев.
Какой аккумулятор выбрать, чтоб авто завелось в мороз — советы экспертов
9 декабря 2021, 16:20
Росатом открыл в Москве серийное производство литий-ионных аккумуляторов
2 мин
…
Мощность нового производства в 10 раз превышает возможности опытного производственного участка, созданного на МЗП в 2021 г., и составляет около 150 МВт·ч, что эквивалентно почти 2 тыс. тяговых аккумуляторных батарей для электротранспорта.
Москва, 14 дек — ИА Neftegaz. RU. Мегафабрика по серийному производству литий-ионных аккумуляторов для электротранспорта и стационарных систем накопления энергии начала работу 14 декабря в Москве.
Новое предприятие организовано интегратором атомной отрасли по системам накопления энергии Рэнерой на площадке Московского завода полиметаллов (оба — предприятия ТВЭЛ, топливной дочки Росатома).
Мощность нового производства в 10 раз превышает возможности опытного производственного участка, созданного на МЗП в 2021 г., и составляет около 150 МВт·ч, что эквивалентно почти 2 тыс. тяговых аккумуляторных батарей для электротранспорта.
Тезисы Н. Никипеловой (президент ТВЭЛ):
- мы шаг за шагом движемся к созданию в России целой новой отрасли — масштабного вертикально интегрированного производства накопителей энергии;
- это имеет ключевое значение для укрепления национального технологического суверенитета в области электротранспорта;
- в свою очередь, мы видим перспективы для еще более широкого участия Росатома в цепочке производства легкового электротранспорта;
- предприятия атомной отрасли уже сегодня способны производить 60% всех компонентов электромобиля.
Новое производство включает:
- участки для проведения электромонтажных работ, сборки электрокомпонентов и плат управления батареей,
- сборки накопителей энергии на основе литий-ионных аккумуляторных модулей.
На заключительном этапе предусмотрен полный цикл электротехнических и климатических приемосдаточных испытаний на зарядно-разрядных станциях и климатическом оборудовании.
На складах постоянно будет храниться запас комплектующих материалов, которого хватит на месяц.
Штат мегафабрики в настоящее время насчитывает несколько десятков человек:
- специалисты по контролю качества,
- инженеры,
- сборщики электротехники,
- тестировщики.
Но, по мере развития производства, численность сотрудников будет расти.
Первыми образцами, которые были собраны на площадке, стали тяговые аккумуляторные батареи для троллейбусов с увеличенным автономным ходом, предназначенные для работы на городских маршрутах в г.
Как отметили в компании, уже сформирован портфель заказов на 2023 г.:
- в него входят аккумуляторы для городского общественного электротранспорта,
- запланирован выпуск опытных образцов батарей для линейки легкового электротранспорта российского производства.
Подтвержденные потребности на стационарные системы накопления энергии составляют не менее 50 МВт·ч.
Также 22 ноября 2022 г. в Росатоме предложили рассмотреть вариант создания в Боливии полноценной литиевой промышленности.
Как тогда отметил первый заместитель гендиректора компании, директор блока по развитию и международному бизнесу К. Комаров, в Боливии уникальные серьезные природные запасы лития, а тренды в мире — на масштабное развитие электротранспорта и использование литий-ионных аккумуляторов.
К. Комаров уточнил, что Росатом заинтересован в том, чтобы помочь Боливии построить высокотехнологичное производство и вместе научиться в перспективе делать в т.
Рэнера
Отраслевой интегратор Росатома в области систем накопления электроэнергии.
Компания производит литий-ионные системы хранения энергии для источников аварийного и бесперебойного питания, гибридных систем с участием возобновляемых источников генерации, тяговые батареи для электротранспорта, спецтехники и других направлений.
Сейчас компания реализует проект по строительству в Калининградской области завода по производству литий-ионных ячеек и аккумуляторных батарей.
Завод общей мощностью выпускаемых устройств около 4 ГВт·ч/год начнет работу в 2025 г.
Автор: А. Хасанова
Источник : Neftegaz.RU
#мегафабрика #литий-ионные аккумуляторы #росатом #твэл #электротранспорт
Производство литий-ионных элементов: обзор процессов и оборудования
Производство элементов литий-ионных аккумуляторов состоит из трех основных этапов: изготовление электродов, сборка элементов и окончательная обработка элементов. Каждый из этих этапов имеет подпроцессы, которые начинаются с нанесения покрытия на анод и катод, заканчиваются сборкой различных компонентов и, в конечном итоге, упаковкой и тестированием аккумуляторных элементов.
Широко производимыми типами ячеек являются призматические, цилиндрические и мешочные, и хотя конструкция ячеек различается, производственные процессы более или менее схожи. Производство составляет около 25 процентов стоимости литий-ионной батареи. Китай, Япония и Южная Корея являются основными производителями и поставщиками оборудования для производства литий-ионных аккумуляторов.
Схема производственных процессов ЛИА (Источник: Sciencedirect)
Литий-ионные элементы состоят из четырех основных компонентов — двух электродов: одного анода (удерживает ионы лития при зарядке) и одного катода (удерживает ионы лития при разрядке), сепаратора, который помещается между электродами для предотвращают контакт и короткое замыкание, а также электролитную среду, обеспечивающую движение ионов лития между электродами.
Обычно анод изготавливается из графита, а катод может быть из сплава нескольких металлов (никель, кобальт, литий и др.). Все компоненты упакованы в корпус, а выступы для положительной и отрицательной клеммы открыты. Затем ячейки упорядочиваются и соединяются, образуя аккумуляторную батарею.
ЭТАП 1: ПРОИЗВОДСТВО ЭЛЕКТРОДОВ
Процесс
Первый этап заключается в смешивании электродных материалов с проводящим связующим для образования однородной суспензии с растворителем. (Материал анода представляет собой форму углерода, а катод представляет собой оксид металлического лития. Чтобы избежать загрязнения между двумя активными материалами, аноды и катоды обычно обрабатываются в разных помещениях.)
Затем на суспензию наносится покрытие либо непрерывно, либо с перерывами на обеих сторонах токосъемника (алюминиевая фольга для катода и медная фольга для анода) с помощью инструмента для нанесения (например, шлицевой головки, ракельного лезвия, анилоксового валика). Толщину покрытия электрода можно контролировать в машине для нанесения покрытия.
Фольга с покрытием подается непосредственно в длинную сушильную печь для испарения растворителя. (Легковоспламеняющийся растворитель, содержащийся в катодном покрытии, восстанавливается или используется для термической переработки. Из анодного покрытия на водной основе безвредный пар выбрасывается непосредственно в окружающую среду.)
Затем следует процесс каландрирования , при котором фольга с покрытием сжимается вращающейся парой роликов. Этот процесс помогает регулировать физические свойства (сцепление, проводимость, плотность, пористость и т. д.) электродов.
После каландрирования готовые электроды очищаются и подаются на продольно-резательные станки для резки на узкие полосы и сматывания. Затем рулоны отправляют в вакуумную печь для удаления остаточной влаги и растворителя.
(Активные материалы, проводящие добавки, растворители и связующие вещества, а также алюминиевая фольга и медная фольга, как правило, являются компонентами, приобретаемыми для производителя элементов. )
Оборудование, используемое в процессе
Машины, используемые процессы на первом этапе производства ячеек включают смесители для приготовления суспензии, машины для нанесения покрытий и сушки, каландры или машины для прессования валков, машины для резки или продольной резки электродами и вакуумные сушильные шкафы.
ЭТАП 2: СБОРКА ЯЧЕЙКИ
Процесс
После того, как электроды подготовлены, их отправляют в сухую камеру для процесса сборки, где между анодом и катодом укладывается слой сепаратора для формирования внутренней структуры ячейки. В зависимости от типа корпуса ячейки используются две основные конструкции электродов: штабелирование для карманных элементов и намотка для призматических и цилиндрических элементов. Сборка ячеек обычно осуществляется на высокоавтоматизированном оборудовании.
На следующем этапе собранная структура ячейки соединяется с клеммами или выводами ячейки вместе с любыми предохранительными устройствами с использованием процесса ультразвуковой или лазерной сварки . Затем узел вставляется в корпус элемента (мешок или металлический корпус, в зависимости от конструкции элемента), который затем герметизируется в процессе лазерной сварки или нагрева, оставляя отверстие для подачи электролита.
За этим следует заполнение корпуса электролитом и его герметизация. Этот процесс проводят в сухом помещении, так как влага приведет к разложению электролита с выделением ядовитых газов. Электролит заливается высокоточной дозирующей иглой. При приложении к ячейке профиля давления (подача инертного газа и/или создание вакуума в попеременном режиме) активируется капиллярный эффект в ячейке (смачивание сепаратора).
Готовая ячейка маркируется номером партии или серийным номером на корпусе.
(Упаковочные материалы, корпус элемента, изоляционные материалы и электролит обычно закупаются для производителя элемента.)
Оборудование, используемое в процессе машина для резки, укладочная машина (ячейки для пакетов), намоточная машина (цилиндрическая и призматическая), машина для запечатывания и сварки язычков, а также машина для заполнения электролитом.
Источник: Tmax
ЭТАП 3: ОБРАБОТКА ЯЧЕЙКИ
Процесс
Процесс пласта описывает первые процессы зарядки и разрядки элемента батареи после впрыска в него электролита. Ячейки размещены в информационных стойках и контактируют с помощью подпружиненных контактных штифтов. Затем элементы заряжаются или разряжаются в соответствии с точно определенными кривыми тока и напряжения. Во время этого процесса ионы лития внедряются в кристаллическую структуру графита на стороне анода, образуя защитный слой, называемый интерфейсом твердого электролита (SEI), между электролитом и электродом. Эта защитная пленка приводит к низкому саморазряду литий-ионных аккумуляторов, а также влияет на производительность и срок службы аккумулятора.
(В больших пакетных ячейках первая зарядка вызывает сильное выделение газа. Этот газ может быть выдавлен из ячейки в мертвое пространство, называемое газовым мешком. Во время дегазации газовый мешок протыкается в вакуумную камеру и выходящие газы отсасываются. Затем ячейка окончательно герметизируется под вакуумом, газовый мешок отделяется и утилизируется как опасные отходы. Во время старения характеристики и производительность элемента контролируются путем регулярного измерения напряжения холостого хода (OCV) элемента в течение периода до трех недель. Различают высокотемпературное (HT) и нормально-температурное (NT) старение. Клетки обычно сначала подвергаются НТ-старению, а затем НТ-старению. Ячейки хранятся в стареющих стеллажах или шкафах. Если за весь период старения в свойствах клетки не фиксируется существенного изменения, это означает, что клетка полностью функциональна.
После процесса старения клетки тестируются на испытательном стенде конечной линии (EOL). Со стеллажей выдержки они поступают на испытательную станцию, где выгружаются до товарного состояния (замер емкости). Также могут быть выполнены дополнительные импульсные тесты, измерения внутреннего сопротивления (DC), оптические проверки, тесты OCV и тесты на утечку.
После успешного завершения испытаний элементы могут быть собраны в аккумуляторные блоки в соответствии с требованиями и конечным использованием.
Процесс формирования и старения составляет 32 процента всего производственного процесса.
Оборудование, используемое в процессе
Машины на третьем и последнем этапе производства элементов включают тестеры/оборудование для формирования батарей, шкафы старения, сортировочные машины и машины для испытаний батарей. Как правило, установка для нанесения покрытий, намотка, сортировочное и испытательное оборудование составляют 70 процентов от общей стоимости оборудования для производства литий-ионных элементов, которая может варьироваться в зависимости от степени автоматизации.
Инновации в продуктах и процессах
Прогресс в технологиях и материалах, происходящий в области производства литий-ионных элементов, окажет положительное влияние на производственные затраты, снизив стоимость не только сырья, но и конечной продукции. ячейка батареи. Инновации всегда приводили к повышению производительности и качества конечного продукта.
Источник: Sciencedirect
- В настоящее время доступны различные технологии перемешивания и инструменты для перемешивания: смесители интенсивного действия, планетарные смесители, диспергаторы и т. д.
- Одновременный процесс покрытия, позволяющий одновременно покрывать верхнюю и нижнюю стороны фольги с помощью двух противоположных инструментов для нанесения.
- Сухое нанесение активного материала на фольгу-носитель можно производить в виде порошка без использования растворителя, что значительно сокращает время термической активации. Удаление растворителя и процесс сушки делают крупномасштабное производство литий-ионных аккумуляторов более экономически выгодным.
- Обычные сушилки могут поддерживаться инфракрасным нагревом, что делает их более эффективными
- Ламинирование является ключевой технологией производства литий-ионных аккумуляторов.
Отдельные листы электрода и сепаратора наслаиваются друг на друга в непрерывном процессе, а затем обычно спрессовываются вместе с помощью термопресса, что повышает скорость производственной линии.
Производство литиевых батарей | Буш США
Обновите браузер.
Похоже, вы используете старую версию браузера Microsoft Edge. Чтобы получить наилучшие впечатления от веб-сайта Busch, обновите свой браузер.
Сюда
Вакуумные решения для процесса производства литий-ионных аккумуляторов.
Литий-ионные аккумуляторы лежат в основе электромобилей. В настоящее время они могут хранить больше заряда на единицу массы, чем другие типы батарей, и обеспечивают разумные диапазоны.
Ключевые процессы при их производстве осуществляются под вакуумом. Наши вакуумные решения используются на крупнейших предприятиях по производству литий-ионных аккумуляторов по всему миру. Они известны своей надежностью на всех этапах производства литий-ионных аккумуляторов.
Процесс производства литий-ионных аккумуляторов
Вакуум является важнейшим требованием на каждом этапе производственного процесса литий-ионных аккумуляторов.
От смешивания, сушки, наполнения, дегазации до герметизации. Без вакуума многие шаги были бы невозможны.
Смешивание суспензии
Начальный процесс смешивания суспензии с оксидами лития, связующими и растворителями происходит под вакуумом.
Предотвращает попадание пузырьков воздуха в процесс и обеспечивает получение чистой однородной пасты.
Результат: увеличена емкость ячейки.
Подходящие продукты: R5 RA, COBRA NC/NX
Сушка суспензии
Вакуум используется в процессе сушки для бережного удаления влаги и других растворителей.
Вакуумная сушка может выполняться партиями (одна камера) или в линию (многокамерная система, обычно от семи до девяти камер).
Подходящие продукты: R5 RA, COBRA NC/NX
Заполнение электролитом
Ячейка откачивается с помощью вакуума, чтобы убедиться, что в ней не осталось влаги или воздуха. После этого заливка электролита также происходит под вакуумом для равномерного распределения электролита внутри элемента.
Подходящие продукты: R5 RA, COBRA NC/NX, MINK MM/MV, ZEBRA
Пропитка элемента литий-ионного аккумулятора
Контакт между электродом и электролитом необходим для функционирования и эффективности элемента аккумулятора.
Вакуум способствует этому процессу, чтобы обеспечить контакт без пустот.
Подходящие продукты: R5 RA, COBRA NC/NX
Дегазация электролита
Электролит дегазируется под вакуумом для удаления пузырьков воздуха. Таким образом, ионы лития могут свободно перемещаться, обеспечивая эффективную зарядку и разрядку аккумулятора.