Какие существуют основные способы пайки. Как выполняется ручная, волновая пайка и пайка оплавлением. Каковы особенности и преимущества различных методов пайки. Как выбрать оптимальный способ пайки для конкретной задачи.
Основные способы пайки: классификация и особенности
Пайка является одним из ключевых процессов в производстве электроники. Существует несколько основных способов пайки, которые различаются по технологии, применяемому оборудованию и области применения:
- Ручная пайка
- Пайка волной припоя
- Пайка оплавлением
- Селективная пайка
- Пайка погружением
- Лазерная пайка
Выбор оптимального способа пайки зависит от типа компонентов, серийности производства, требований к качеству соединений и других факторов. Рассмотрим подробнее особенности основных методов пайки.
Ручная пайка: классический метод для мелкосерийного производства
Ручная пайка выполняется вручную с помощью паяльника и припоя. Это классический метод, который до сих пор широко применяется в мелкосерийном производстве и ремонте электроники.
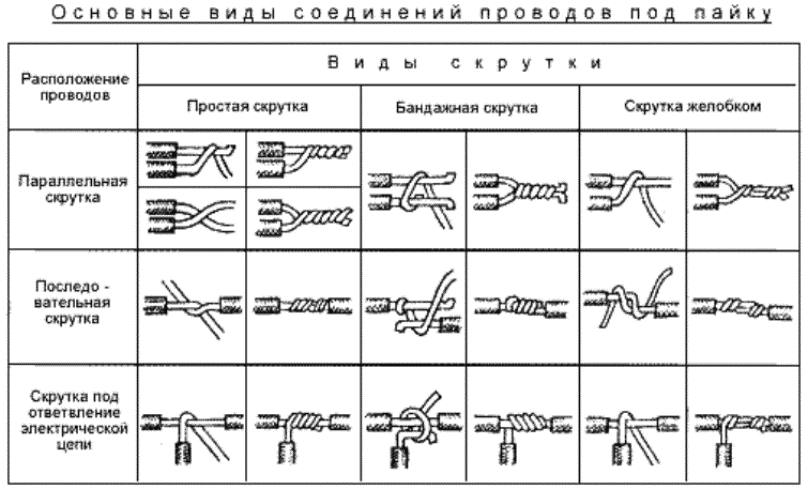
Основные этапы ручной пайки:
- Подготовка поверхностей (зачистка, флюсование)
- Нагрев места пайки паяльником
- Нанесение припоя
- Формирование галтели припоя
- Охлаждение соединения
Преимущества ручной пайки:
- Универсальность и гибкость
- Низкие первоначальные затраты
- Возможность пайки сложных и нестандартных соединений
- Простота освоения базовых навыков
Недостатки:
- Низкая производительность
- Зависимость качества от квалификации монтажника
- Сложность обеспечения стабильного качества
Ручная пайка оптимальна для мелкосерийного производства, ремонта, прототипирования. При больших объемах более эффективны автоматизированные методы пайки.
Пайка волной припоя: эффективный метод для массового производства
Пайка волной припоя — это высокопроизводительный метод, при котором плата проходит над волной расплавленного припоя. Припой заполняет отверстия и формирует соединения.
Основные этапы волновой пайки:
- Флюсование платы
- Предварительный нагрев
- Прохождение платы над волной припоя
- Охлаждение
Преимущества волновой пайки:
- Высокая производительность
- Стабильное качество соединений
- Возможность пайки компонентов со штыревыми выводами
- Хорошее заполнение отверстий припоем
Недостатки:
- Высокая стоимость оборудования
- Сложность пайки миниатюрных компонентов для поверхностного монтажа
- Большой расход припоя и флюса
Волновая пайка широко применяется в массовом производстве электроники, особенно для плат со смешанным монтажом.
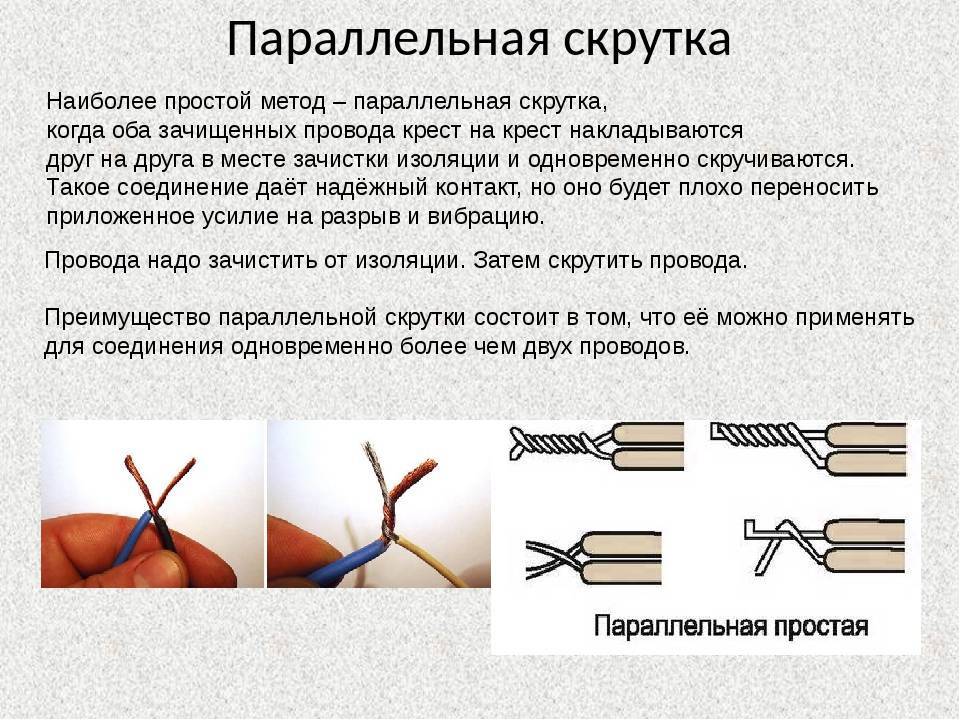
Пайка оплавлением: современный метод для поверхностного монтажа
Пайка оплавлением (reflow soldering) — основной метод для монтажа SMD-компонентов. Припой в виде паяльной пасты наносится на контактные площадки, затем происходит оплавление в специальной печи.
Этапы пайки оплавлением:
- Нанесение паяльной пасты (трафаретная печать)
- Установка компонентов
- Оплавление в печи по заданному термопрофилю
- Охлаждение
Преимущества пайки оплавлением:
- Высокая точность и повторяемость
- Возможность пайки миниатюрных компонентов
- Отсутствие термоударов для компонентов
- Высокое качество соединений
Недостатки:
- Высокая стоимость оборудования
- Сложность пайки компонентов со штыревыми выводами
- Чувствительность к точности нанесения пасты
Пайка оплавлением — оптимальный выбор для массового производства печатных узлов с поверхностным монтажом.
Селективная пайка: точечная пайка для сложных узлов
Селективная пайка позволяет выполнять пайку отдельных компонентов или участков платы. Это гибкий метод для плат со смешанным монтажом.
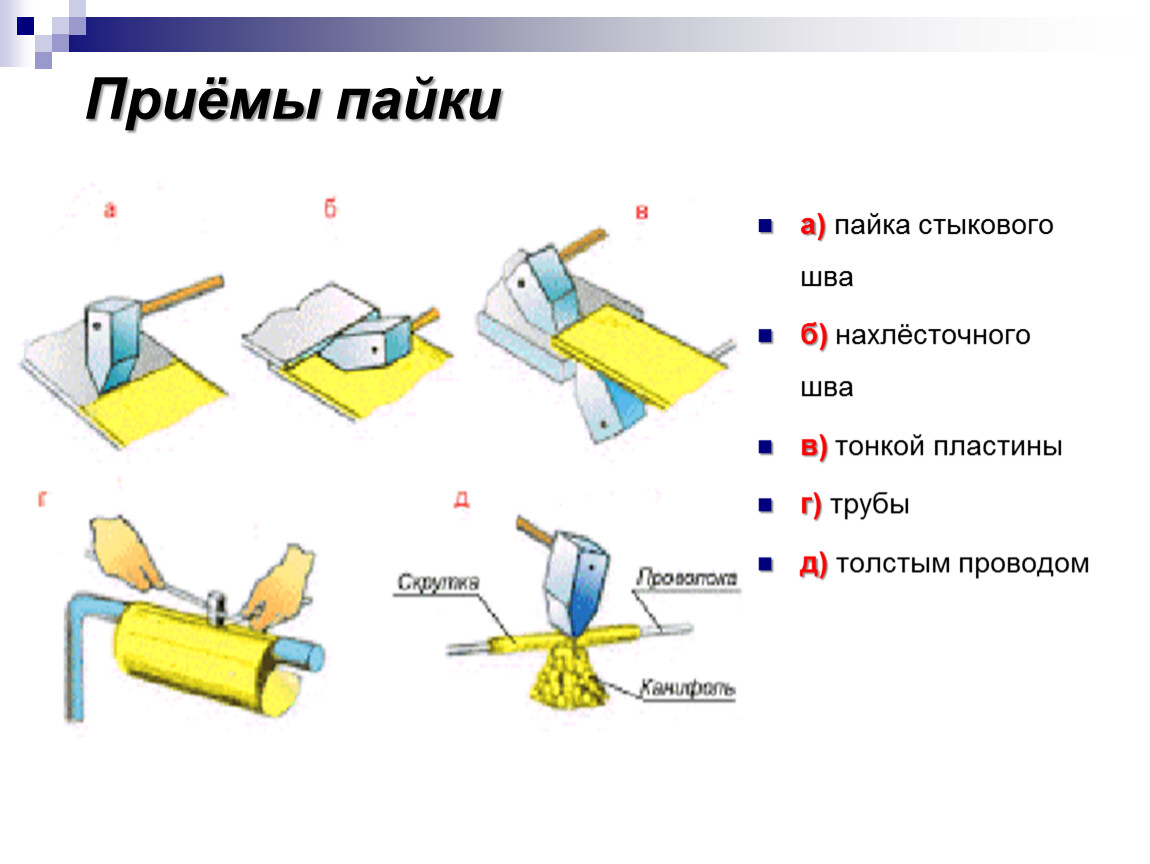
Особенности селективной пайки:
- Локальный нагрев только нужных участков
- Возможность пайки штыревых и SMD-компонентов
- Программируемые режимы для разных компонентов
- Минимальное термовоздействие на плату
Селективная пайка эффективна для сложных многослойных плат с разнородными компонентами.
Выбор оптимального способа пайки: ключевые факторы
При выборе метода пайки необходимо учитывать следующие факторы:
- Тип и размеры компонентов
- Серийность производства
- Требования к качеству и надежности
- Стоимость и окупаемость оборудования
- Особенности конструкции печатного узла
- Термочувствительность компонентов
Для многих производств оптимальным является сочетание нескольких методов пайки на разных этапах. Например, пайка оплавлением для SMD-компонентов и селективная пайка для штыревых.
Контроль качества паяных соединений
Независимо от выбранного метода пайки, критически важен контроль качества паяных соединений. Основные методы контроля:
- Визуальный контроль
- Рентгеновский контроль
- Электрический контроль
- Тепловизионный контроль
- Металлографические исследования
Комплексный контроль позволяет выявить дефекты пайки на ранних стадиях и обеспечить высокую надежность изделий.
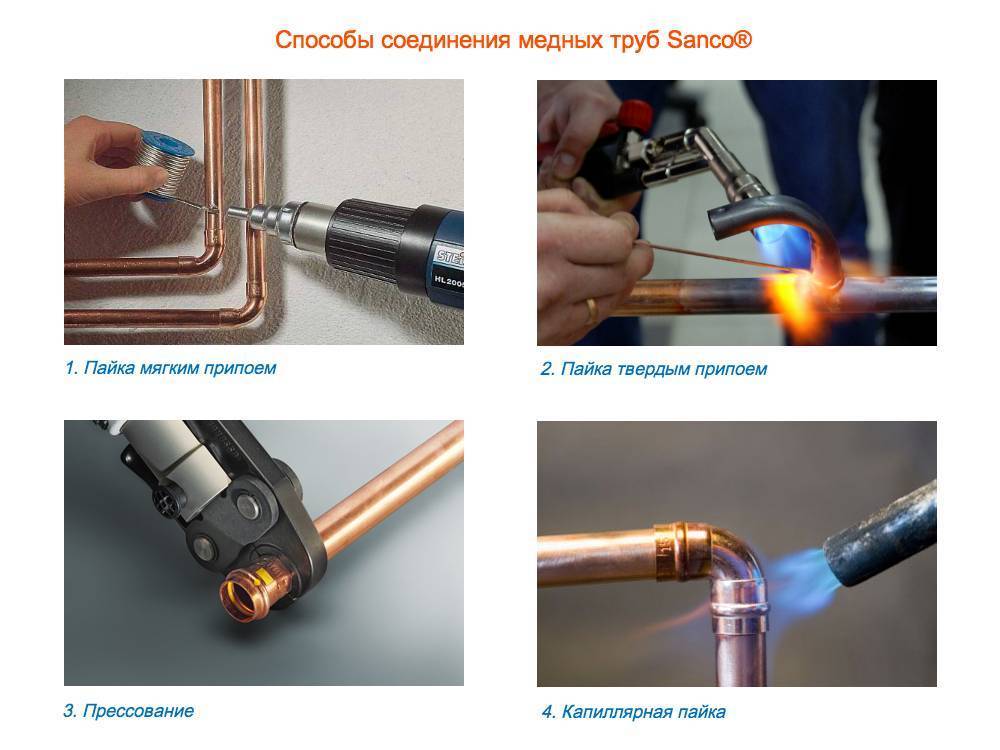
Современные тенденции в технологиях пайки
Технологии пайки постоянно совершенствуются. Основные тенденции развития:
- Переход на бессвинцовые технологии
- Миниатюризация компонентов и уменьшение размера паяных соединений
- Внедрение систем автоматического оптического контроля
- Развитие селективных методов пайки
- Оптимизация термопрофилей для сложных компонентов
- Применение вакуумной пайки для улучшения качества
Следование современным тенденциям позволяет повысить качество и надежность паяных соединений при сохранении высокой производительности.
Способы пайки | Учебные материалы
Способы пайки классифицируют в зависимости от используемых источников нагрева. Наиболее распространены в промышленности пайка в печах, индукционная, сопротивлением, погружением, радиационная, горелками, экзофлюсовая, паяльниками, электронагревательными металлами и блоками.
Капиллярная пайка
Припой заполняет зазор между соединяемыми поверхностями и удерживается в нем за счет капиллярных сил. На рисунке 3.16 показана схема образования шва.
Соединение образуется за счет растворения основы в жидком припое и последующей кристаллизации раствора. Капиллярную пайку используют в тех случаях, когда применяют соединение внахлестку. Однако капиллярное явление присуще всем видам пайки.
Рисунок 3.16 – Схема капиллярной пайки:
а – перед пайкой; б – после пайки
Диффузионная пайка
Соединение образуется за счет взаимной диффузии компонентов припоя и паяемых материалов, причем возможно образование в шве твердого раствора или тугоплавких интерметаллов.
Для диффузионной пайки необходима продолжительная выдержка при температуре образования паяного шва и после завершения процесса при температуре ниже солидуса припоя.
Контактно-реактивная пайка
При пайке между соединяемыми металлами или соединяемыми металлами и прослойкой другого металла в результате контактного плавления образуется сплав, который заполняет зазор и при кристаллизации образует паяное соединение. На рисунке 3.17 показана схема контактно-реактивной пайки.
Рисунок 3.17 – Схема контактно-реактивной пайки:
а – перед пайкой; б – после пайки
Реактивно-флюсовая пайка
Припой образуется за счет реакции вытеснения между основным металлом и флюсом.
Например, при пайке алюминия с флюсом
3ZnCl2 + 2Al = 2AlCl3 + Zn
восстановленный цинк является припоем.
Пайка-сварка
Паяное соединение образуется так же, как при сварке плавлением, но в качестве присадочного металла применяют припой.
Наибольшее применение получила капиллярная пайка и пайка-сварка. Диффузионная пайка и контактно-реактивная более трудоемки, но обеспечивают высокое качество соединения и применяются, когда в процессе пайки необходимо обеспечить минимальные зазоры. Качество паяных соединений (прочность, герметичность, надежность и т. д.) зависит от правильного выбора основного металла, припоя, флюса, способа нагрева, величины зазоров, типа соединения.
Материалы для пайки >
Теория по ТКМ >
Сохранить или поделиться с друзьями
Вы находитесь тут:
На нашем сайте Вы можете заказать решение задач, написание учебных работ и онлайн помощь
Подробнее
Стоимость работы мы сообщим в течение 5 минут
на указанный вами адрес электронной почты.
Если стоимость устроит вы сможете оформить заказ.
Набор рамок для выполнения учебных работ
Сохранить и поделиться с друзьями
Заказать решение
Поиск по сайту
2.
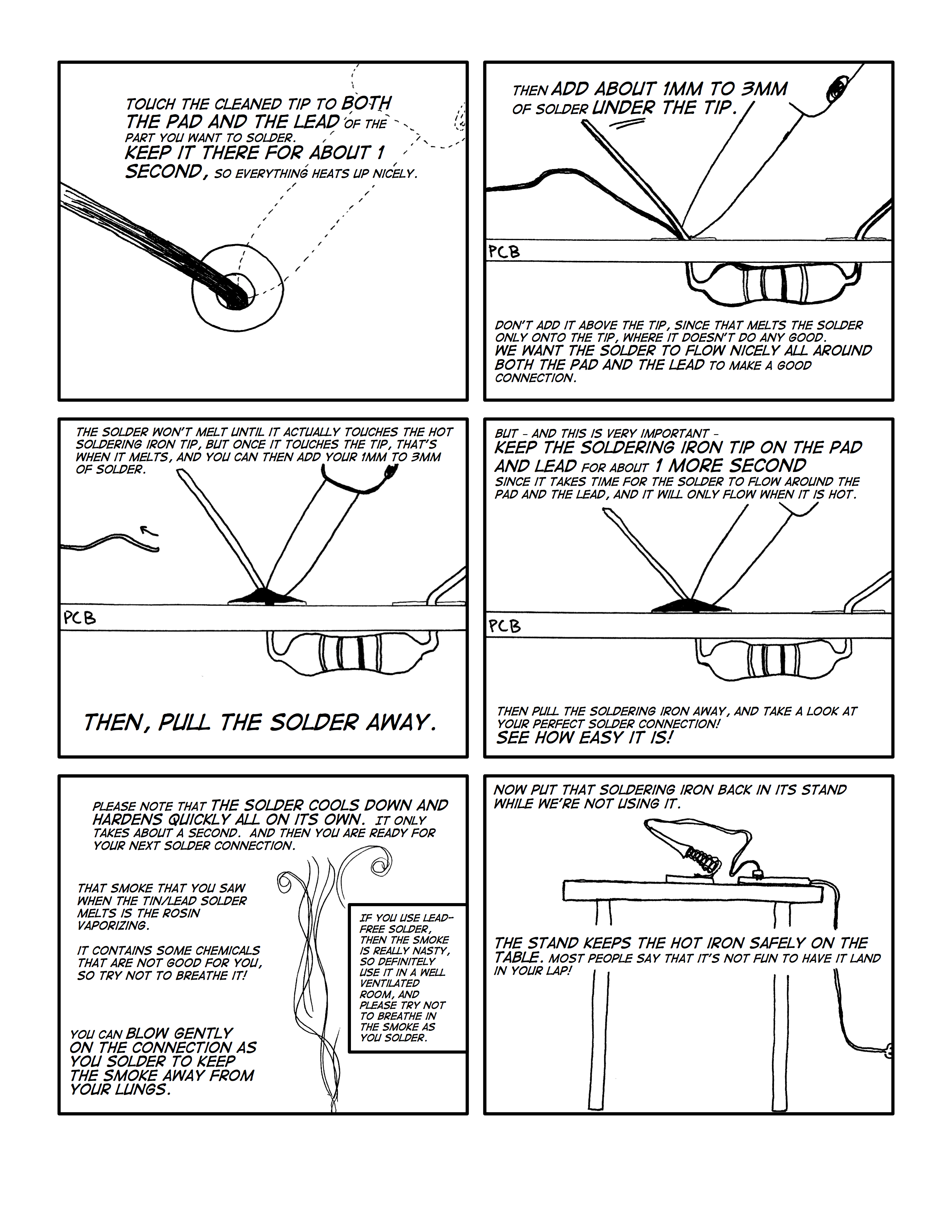
В настоящее время существует большое разнообразие методов пайки. Но из всего многообразия методов можно выделить следующие, так называемые основные методы пайки, т.е., которые используются чаще всего:
пайка погружением в расплавленный припой;
пайка волной припоя;
пайка групповым паяльником;
дозированная пайка;
пайка параллельными электродами;
паро-фазная пайка.
Пайка расплавлением дозированного припоя с инфрокрасным (ИК) нагревом
Кроме указанных способов пайки, в случае отсутствия необходимого оборудования или при изготовлении опытных образов, производится обычная пайка паяльником, микропаяльником, термокарандашом или другими инструментами.
Рассмотрим эти методы более подробно:
Этот метод
применяется для монтажа изделий
электронной техники со штырьковыми
выводами.
Сущность метода
заключается в пропускании печатной
платы через гребень свободно проливающегося
из щелевого сопла расплавленного припоя.
Часто используют еще и дополнительную
волну, наряду с основной. Это позволяет
провести более качественную пайку,
особенно в отношении компонентов
поверхностного монтажа. Благодаря своим
преимуществам (высокая производительность,
относительно слабое термическое
воздействие как на полупроводниковые
приборы, так и на изделие вообще, высокое
качество паяных соединений и т.д.) этот
метод получил наиболее широкое
распространение в радиоэлектронной
промышленности.
Этот способ является довольно эффективным с точки зрения повышения производительности процесса пайки планарных видов изделий электронной техники. При таком способе один или два паяльника паяют сразу все выводы изделия. Кроме того, этот метод позволяет получить паяные соединения, которые по внешнему виду и по физическим свойствам никак не отличаются от соединений паянных вручную. Производительность процесса составляет 250-300 соединений в минуту. Высокое качество пайки достигается при одновременной пайке 7-8 выводов одним паяльником. Увеличение числа одновременно паяемых выводов до 12…20 ведет к снижению качества паяных соединений. Это происходит потому, что даже у одного корпуса выводы имеют различную толщину и, вследствие этого, по-разному прилегают к паяльнику и имеют разный нагрев.
Дозированная пайка
Это механический
способ пайки, с использованием обычного
миниатюрного паяльника. Паяльник
закреплен на устройстве, которое
обеспечивает его механическую подачу. Это устройство называется механизмом
подачи. При движении вниз, паяльник
расплавляет кусок проволочного припоя,
который подается на определенную длину.
Благодаря этому на жале паяльника
оказывается именно та доза припоя,
которая и является необходимой для
пайки одного паяного соединения.
Поскольку за один такт времени паяльник
паяет всего одно соединение, то
производительность этого метода
оказывается несколько ниже, чем при
использовании способа групповой пайки.
Этот способ пайки
является фактически разновидностью
одностороннего контактного нагрева и
основан на прямом нагреве места соединения
электрическим током, который подводится
через электроды термокарандаша или
специального микропаяльника . Джоулево
тепло, достаточное для расплавления
припоя, выделяется в паяемых деталях
(выводе изделий и контактной площадке)
на участке межэлектродного зазора. При
этом припой вводится в соединение
заранее. Электроды перемещаются в
вертикальной плоскости независимо друг
от друга и прижимаются к выводам с
некоторым усилием.
Этот вид пайки основан на использовании для нагрева паяемых соединений скрытой теплоты конденсации паров инертной термостойкой жидкости. Для паро-фазной пайки созданы и используются специальные жидкости, у которых температура кипения выше температуры расплавления припоя и которые практически не разлагаются при температуре плавления и не изменяют свой состав при испарении.
Введение в пайку | AAQ
Пайка часто встречается при создании космической полезной нагрузки. Припой представляет собой легкоплавкий металлический сплав, используемый для соединения металлических поверхностей. Доступны различные припои, предназначенные для температуры расплава и контроля слоев сплава в окончательном паяном соединении. Паяные соединения в первую очередь обеспечивают токопроводящее соединение для электрических цепей, но в сочетании с выводами электронных компонентов или контактными площадками они также должны надежно работать в наведенных и открытых условиях окружающей среды, таких как механические удары, вибрация, вызванное температурой растягивающее напряжение и вакуум.
Рис. 1. Паяльник, припой и отпаиваемая оплетка
Основы
Приведенные ниже видеоролики дают представление об основах пайки.
Ручная пайка, ведущая, сквозная часть, часть:
Ручная паяльная поверхность. выходит из строя, когда сила натяжения или изгиба паяного соединения превышает предел прочности на растяжение самого припоя. Наиболее вероятной причиной выхода из строя паяного соединения является рост небольших дефектов в соединении в большой дефект, который проявляется в виде трещины между двумя проводниками, которые должны быть соединены паяным соединением. Трещины могут привести к постоянному и устойчивому отсоединению или к прерывистому электрическому соединению, которое иногда кажется нормальным, но затем из-за вибрации или расширения и сжатия в зависимости от температуры соединение становится неисправным или изменяет свое электрическое сопротивление. Дефекты могут существовать на уровне кристаллической решетки или на макроуровне. Время, необходимое для слияния дефектов и образования трещины на всем протяжении соединения, называется временем до разрушения и обычно измеряется числом термических циклов (в определенном диапазоне температур) или временем воздействия вибрации (в определенном диапазоне температур). определенный диапазон наложенных частот). Инженерная оценка надежности паяных соединений, основанная на типе используемого припоя, форме вывода детали, форме паяного соединения, металлическом составе сформированного соединения или других параметрах, требует испытаний сотен или тысяч суставов, чтобы предсказать их продолжительность жизни.
Исследования надежности обычно проводятся для паяных соединений определенной конструкции, чтобы определить их время до отказа для интересующего диапазона температурных циклов или диапазона вибрации (например, для использования в автомобилях, или для использования в космических кораблях, или для использования в медицинском оборудовании). ). Надежность всегда связана с интересующей средой и предполагаемым сроком службы (например, два года для сотовых телефонов, пятнадцать лет для космического телескопа Джеймса Уэбба, пять лет для бытовой техники). Тесты на надежность имеют смысл, когда испытуемые образцы идентичны, а набор образцов не содержит производственных ошибок. Ранние отказы образцов, содержащих производственные ошибки, называются «отказами в отношении младенческой смертности» и обычно не учитываются при прогнозировании конца жизни.
Нет ничего необычного в том, что паяное соединение с определенным типом макродефекта прослужит очень долго. Исследователи обнаружили, что чрезвычайно сложно смоделировать идентичные макродефекты в достаточно больших размерах выборки, чтобы получить результаты надежности для определенных типов макродефектов. Тем не менее, общие знания о взаимосвязи между макродефектами и отказом цепи со временем развились благодаря изучению отказов в тестах на надежность и аппаратных средств, возвращенных из использования для ремонта («возвраты в полевых условиях»). Настройки производственных параметров, которые создают эти макродефекты, также известны. Как появление общих макродефектов (их можно увидеть внешне или рентгенологически), так и выявление условий их возникновения являются предметом требований отраслевых стандартов качества.
Пайка, не содержащая производственных дефектов, считается качественной. Известно, что производственные ошибки возникают либо из-за плохого планирования, либо из-за плохого контроля переменных производственного процесса. Работа по разработке процесса пайки, включая выбор используемых материалов и условий процесса, включая температуру, время и подготовку поверхности, называется технологическим проектированием. Успешная разработка процесса пайки предотвратит производственные ошибки, которые создают макродефекты в паяных соединениях, вызывающие отказы на раннем этапе эксплуатации. Невозможно предотвратить микродефекты в паяных соединениях, однако их можно свести к минимуму, если понять влияние температурных условий пайки и следов металлов, присутствующих в выбранном припое и в сплаве, который образуется при соединении расплавленного припоя с выводами или спаиваемые поверхности.
Визуальный осмотр используется для проверки готовых паяных соединений на макродефекты. Многие паяные соединения с внешне наблюдаемыми дефектами можно исправить повторным нагревом соединения (хотя нагрев паяного соединения может повредить печатную плату). Тем не менее, многие макродефекты, вызывающие выход из строя на ранних сроках эксплуатации, не видны снаружи, и пользователь должен полагаться на технологический процесс, чтобы знать, что паяные соединения имеют высокое качество. Некоторые критерии визуального контроля, определенные в отраслевых стандартах качества, используют внешний вид паяных соединений, выполненных в хорошо контролируемых условиях, в качестве вывода об отсутствии макродефектов внутри соединения; если снаружи выглядит хорошо, то и внутри, наверное, тоже хорошо. Обеспечение качества паяных соединений состоит из поощрения изготовителя/производителя к использованию хороших технологических процессов при визуальной проверке внешнего вида готовых соединений на наличие макродефектов или доказательств того, что макродефекты могут существовать внутри соединения.
Флюс
Флюс представляет собой химическое соединение, используемое для удаления кислорода с поверхности металла при нагревании, чтобы позволить металлу поверхности легко соединиться с расплавленным припоем. Металлические поверхности, подвергшиеся коррозии из-за поглощения кислорода из воздуха и образования оксидного поверхностного слоя, не будут легко прикрепляться к расплавленному припою. Во время пайки флюс присутствует либо путем нанесения непосредственно перед пайкой, либо путем смешивания флюса с самим припоем, чтобы обеспечить поверхность, свободную от оксидов, в тот момент, когда расплавленный припой контактирует с поверхностью. Если поверхность недостаточно свободна от оксидов, припой не будет прилипать или «смачиваться». Несмоченная поверхность имеет отчетливый вид, считается макродефектом и связана с преждевременным выходом из строя паяного соединения. В некоторых паяных соединениях из-за их размера или геометрии флюс может сдирать кислородный слой. Однако этот кислород и другие летучие вещества, входящие в состав флюса, попадают внутрь паяного соединения, когда оно затвердевает, создавая пустоты. Высокие концентрации пустот могут быть макродефектами, вызывающими отказ на раннем сроке службы. Пустоты нельзя увидеть снаружи, а только с помощью рентгеновского контроля, который является дорогостоящим и трудоемким методом контроля качества паяных соединений. Требования к паяемости, содержащиеся в отраслевых стандартах качества пайки, описывают, как обеспечить защиту или адекватную подготовку поверхностей для пайки, чтобы предотвратить несмачивание и образование пустот. Процесс, называемый «лужение», который заключается в погружении вывода детали или проволоки в расплавленный припой, может использоваться для обеспечения припоя на поверхности. Некоторые составы флюса являются причиной избыточного образования пустот, даже если поверхности соответствуют требованиям к качеству для пайки.
Составы флюсов различаются, в частности, количеством ионных соединений, добавляемых для повышения их «активности» (или способности удалять кислород с поверхности и вытеснять другие остатки). Когда флюс полностью активирован, эти соединения в процессе нейтрализуются. Однако нет гарантии, что весь флюс будет равномерно нагреваться во время пайки и нейтрализоваться. Остаточный флюс может вызвать коррозию платы или деталей и может стать основным компонентом металлических дендритов, которые могут расти в электрически малых компонентах. Остатки, присутствующие на деталях, платах и в чистящих растворах, связаны с необратимым повреждением плат и выходом из строя на ранних этапах эксплуатации. Вот почему очистка компонентов является неотъемлемой частью пайки до и после создания паяного соединения.
Типы пайки
Методы пайки делятся на три основные категории: ручная пайка, пайка оплавлением и пайка волной.
Ручная пайка формирует каждое соединение отдельно, одновременно прикладывая горячий паяльник и проволоку из припоя к двум соединяемым поверхностям. Некоторые припои построены вокруг флюсового сердечника (т. е. припоя с флюсовой сердцевиной), а некоторые припои состоят только из металла, и в дополнение к припою необходимо использовать отдельную флюсовую пасту или жидкость. Ручная пайка чаще всего используется для сборки разъемов на кабелях, для установки перемычек на детали или печатные платы, пайки проводов от катушек трансформатора и для ремонта.
Пайка оплавлением В модели используется паяльная паста, состоящая из миниатюрных шариков припоя, взвешенных в жидком флюсе. Паяльная паста наносится трафаретной печатью на печатную плату, детали помещаются поверх печатной пасты, и сборка медленно проходит через печь, в которой она подвергается воздействию повышения и понижения температуры, что активирует флюс и плавится. припоя и обеспечивает плавные температурные переходы, которые предотвращают повреждение от теплового удара и уменьшают внутренние дефекты во время затвердевания припоя. Пайка оплавлением является наиболее распространенным типом процесса пайки и используется для поверхностного монтажа на печатных платах.
Пайка волной припоя использует вращающуюся ванну с флюсом и расплавленным припоем, который проходит через области, подлежащие соединению, для заполнения полостей, таких как отверстия в печатной плате, для создания паяного соединения. Волновая пайка чаще всего используется для установки сквозных соединителей на платы после того, как все детали, монтируемые на поверхности, были установлены с использованием процесса оплавления.
Некоторые операции пайки требуют многоэтапного процесса, при котором выполняется одно соединение, а затем другое соединение для другого соединения поблизости. Пайка рядом с другим паяным соединением может частично нагреть первое паяное соединение и повредить его. Когда такая производственная последовательность необходима, выбираются различные сплавы припоя, и сначала используется припой с более высокой температурой плавления, чтобы вторая рабочая температура пайки не влияла на первое соединение. Припой с более высокой температурой часто имеет форму предварительно отформованного «куска» припоя, который позиционируется и затем нагревается с помощью паяльника или путем пропускания сборки через печь оплавления или нагревательную плиту с многоступенчатой конвейерной лентой. Этот тип пайки распространен для деталей, нижняя сторона которых действует как теплоотвод и электрический контакт, где требуется покрыть припоем относительно большую площадь, полностью скрытую от глаз.
Контроль электростатического разряда
Многие электронные компоненты, соединенные между собой пайкой, чувствительны к электростатическим разрядам (ЭСР). Перед тем, как обращаться с деталями или платами, необходимо знать их чувствительность, и необходимо использовать средства защиты от электростатических разрядов, чтобы гарантировать, что они не подвергаются разрядам энергии, которые могут их повредить. Для этой цели должна быть создана и реализована программа контроля электростатического разряда. (Дополнительную информацию об электростатическом разряде см. в курсе AAQ ESD.) Программа управления электростатическим разрядом определит системы электрического заземления, которые будут использоваться для предотвращения накопления статических зарядов, а те, которые накапливаются, отводятся на землю через соединения с ограничением тока. . Это также гарантирует, что электрические поля не накапливаются вокруг чувствительных деталей из заряженных изоляторов, и что люди, работающие с предметами, чувствительными к электростатическому разряду, соблюдают необходимые методы, обеспечивающие правильное использование методов контроля электростатического разряда. При пайке крайне важно использовать стандартные отраслевые методы и ограничения, чтобы гарантировать, что паяльное оборудование, которое касается оборудования (паяльник при ручной пайке и автоматическая пайка поверхностным монтажом с помощью подъемно-транспортных машин), должным образом заземлено, а для паяльников , чтобы перепады напряжения, существующие на наконечнике, не превышали номинального значения части в соответствующих диапазонах частот.
Минимальные шаги для защиты устройств, чувствительных к электростатическому разряду:
- Работайте только в конфигурации с заземлением, которая включает оператора и все рабочие поверхности и оборудование, обеспечивающее эквипотенциальное заземление.
- Используйте рабочие зоны и инструменты с заземленными рассеивающими поверхностями. Контролируйте накопление заряда с помощью сбалансированных ионизаторов для основных изоляторов.
- Всегда проверяйте эффективность метода заземления оператора перед началом работы (система браслетов или токопроводящая обувь/полы).
- Используйте антистатический пакет или контейнер для хранения или переноса деталей в зону, контролируемую электростатическим разрядом, и из нее.
Вопросы технологического проектирования
Ниже приведены некоторые из основных параметров, которые необходимо учитывать при подготовке процесса пайки, чтобы обеспечить надежность соединений и уменьшить количество производственных дефектов:
- Припой
- Состав флюса
- Предварительный нагрев и контролируемое охлаждение
- Удаление влаги с печатных плат
- Чистота плат и деталей
- Методы и материалы очистки (до и после пайки)
- Паяемость поверхности
Пример ручной пайки провода
1. Подготовка, размещение и очистка соединения
2. Очистка сборки
3. Очистка и размещение железа, припоя
4. Очистка и осмотр соединения
Безопасность
Пайка обычно включает выделение летучих материалов из флюса по мере его активации. Рекомендуется использовать вытяжку дыма, чтобы уменьшить выброс летучих веществ из рабочей зоны во время пайки. Обрывки припоя в рабочей зоне и при удалении окалины из ванны будут содержать элементарный свинец (Pb). Этот материал должен быть удален из рабочей зоны и контролироваться как опасный материал. Не следует есть или пить вблизи паяльных станций как для безопасности людей, так и для защиты оборудования. Необходимо всегда носить защиту для глаз.
Методы пайки печатных плат. Основное руководство
Типы методов пайки печатных плат
Пайка печатных плат включает соединение двух или более различных электрических компонентов вместе на поверхности печатной платы. Пайка является неотъемлемой частью процесса проектирования печатной платы — единственный способ прикрепить схемы к плате — это припаять их.
Рассмотрим более подробно различные способы пайки печатных плат:
- Ручная пайка
- Пайка оплавлением
- Пайка волной припоя
Ручная пайка выполняется вручную, тогда как пайка оплавлением и волной припоя выполняется с помощью машин SMT (технология поверхностного монтажа).
Ручная пайка
Ручная пайка — это процесс, при котором люди или роботы вручную оказывают давление с помощью предварительно залуженного наконечника паяльника, нагревая детали и расплавляя припой.
В отрасли вы можете услышать, как люди называют эту технику мягкая пайка . Это потому, что температура, необходимая для ручной пайки, ниже 400 градусов. Припои в основном содержат свинец с температурой плавления ниже 350 градусов. При подаче тепла на плавкие компоненты мы стараемся использовать как можно более низкие температуры, чтобы металлы не плавились. Конечным продуктом является «мягкое» соединение.
Ручная пайка печатных плат, которую можно выполнить с помощью инструментов для пайки и ремонта компании Thermaltronics, обычно является последним шагом в процессе сборки прототипа и используется для детали отделки для сквозных отверстий и компонентов для поверхностного монтажа . Технология сквозных отверстий относится к компонентам, вставленным в печатные платы и припаянным к контактным площадкам на противоположной стороне.
Технология поверхностного монтажа (SMT) — это когда электрические компоненты монтируются непосредственно на поверхность печатной платы. Электрическая часть, установленная таким образом, известна как устройство поверхностного монтажа (SMD).
Хотя ручная пайка требует знаний и практики, многие инженеры скажут вам, что это самый простой метод. Однако у него есть свои плюсы и минусы:
Pros
- Вы можете разработать надежное электрическое соединение.
- Для более мелких компонентов можно легко припаять вручную.
Минусы
- Поскольку мы не можем использовать ручную пайку при высоких температурах, она не может обеспечить прочные соединения.
- Не используйте его в приложениях с высокой нагрузкой.
Пайка оплавлением
Пайка оплавлением является наиболее популярным механическим методом крепления компонентов поверхностного монтажа к печатным платам. Процесс направлен на формирование паяных соединений на предварительный нагрев деталей и последующее плавление припоя без повреждения из-за перегрева.
Мы создаем паяльную пасту из порошкообразного припоя и флюса для пайки оплавлением. Затем электрические компоненты временно прикрепляются к контактным площадкам перед пайкой паяльной пастой.
После этого мы нагреваем всю сборку в печи для пайки оплавлением или под инфракрасной лампой, чтобы расплавить припой и закрепить соединение. Вот краткий обзор шагов:
Этап 1: Предварительный нагрев
Поддерживает монтажные платы для достижения необходимой температуры и соответствует термическому профилированию. Во-вторых, он устраняет летучие растворители в паяльной пасте.
Этап 2: Термическая выдержка
На этом этапе температура поднимается до температуры плавления сплава. Флюс в паяльной пасте должен достичь нужного уровня температуры, иначе он не активируется, создавая слабые металлургические связи.
Шаг 3: пайка оплавлением г
Процесс пайки оплавлением происходит при самой высокой температуре. Паяльная паста подвергается эвтектоидной реакции, и припой становится жидким или расплавленным металлом. Контроль температуры играет решающую роль в процессе пайки оплавлением. Перегрев может привести к повреждению компонентов или плат технологии поверхностного монтажа (SMT).
Этап 4: Охлаждение
Охлаждение означает, что паяльная паста затвердевает, а детали фиксируются контактными площадками на печатной плате.
Метод пайки оплавлением используется в технологии поверхностного монтажа для пайки компонентов поверхностного монтажа на печатной плате. Он в основном используется для сборки печатных плат в мелкосерийном производстве, не требующем быстрого и дешевого массового производства. Машины
SMT (также известные как машины для захвата и установки или системы размещения компонентов SMT) используются для крепления компонентов поверхностного монтажа к печатным платам для сборочных линий, в которых используется этот процесс.
Конечно, на сборочной линии могут быть ошибки, поэтому решение для ремонта должно быть на месте. Инженеры обычно ремонтируют дефектные компоненты для поверхностного монтажа (например, неисправные печатные платы) с использованием паяльников или паяльных станций SMD с использованием метода ручной/ручной пайки.
Плюсы
- Меньший тепловой удар, поскольку компоненты не погружаются в воду напрямую.
- Паяльная паста используется по мере необходимости, что снижает количество отходов.
- Сокращение производственных затрат, так как требуется меньше человеческих ресурсов.
- Легче масштабировать производство, отлично подходит для мелкосерийного производства.
Минусы
- Если температура не контролируется, это может привести к плохой пайке.
- Не самая подходящая техника для сложных досок.
- По сравнению с процессом пайки волной припоя он может быть более дорогим.
Пайка волной припоя
Пайка волной припоя — это еще один метод механической пайки, который позволяет массово производить печатные платы за короткое время. Машина создает «волны» припоя, которые соединяют компоненты с платой. Затем печатная плата охлаждается, надежно закрепляя детали на месте.
Вот краткий обзор процесса пайки волной припоя:
Шаг 1: Напыление флюса
Очистка металлических поверхностей обеспечивает качество пайки. Флюс способствует более гладкой пайке.
Этап 2: Предварительный нагрев
Печатные платы проходят через тепловой туннель для предварительного нагрева и активации флюса.
Этап 3: Пайка волной припоя
По мере постепенного повышения температуры паяльная паста превращается в жидкость с волнами, образующимися на краевых пластинах сверху. Компоненты прочно закреплены на платах.
Шаг 4: Охлаждение
После охлаждения до комнатной температуры машина успешно соберет плату.
Мы рекомендуем пайку волной припоя для более высокой скорости и эффективности сборки печатных плат, если вам необходимо удовлетворить растущий спрос на электронные продукты. Это более быстрый процесс как при сборке печатных плат через отверстия, так и при поверхностном монтаже.
Pros
- Компоненты подвергаются воздействию тепла в течение более короткого времени. В результате воздействие воздуха и окисление меньше.
- Этот процесс обеспечивает более качественные соединения.
- Подходит для крупносерийного производства.
Минусы
- Несоответствия температуры в средней температуре процесса должны хорошо контролироваться.
- Процесс требует тщательного ухода за окружающей средой.
Есть ли разница между пайкой волной припоя и пайкой оплавлением?
Многие люди не знают, что выбрать пайку волной или пайку оплавлением при покупке услуг по сборке печатных плат, так как процессы кажутся похожими. Однако выбор подходящего метода пайки может повлиять на эффективность производства, стоимость, время выхода на рынок, доход и т. д., поэтому важно знать разницу.
По сути, разница между двумя типами методов пайки заключается в напылении флюса. Вы могли заметить, что пайка волной припоя содержит этот шаг, а пайка оплавлением — нет.
Флюс способствует удалению двуокиси и снижению поверхностного натяжения в припаиваемом материале. Это приводит к прочным соединениям на печатной плате. Но флюс требует строгого соблюдения температурного и временного контроля. Поскольку флюс присущ паяльной пасте при пайке оплавлением, нам необходимо контролировать температуру, чтобы флюс активировался правильно.
Какой метод механической пайки я использую?
Итак, вы можете спросить, какой тип пайки и когда вы должны использовать?
В целом пайка волной припоя гораздо сложнее, и без тщательного контроля и надлежащей среды она может привести к дефектам платы.
Контроль окружающей среды не так важен при использовании пайки оплавлением для создания печатной платы.