Как собрать фрезерный станок с ЧПУ в домашних условиях. Какие детали и компоненты потребуются для сборки. Как спроектировать и собрать основные узлы станка. Какое программное обеспечение использовать для управления самодельным ЧПУ фрезером.
Подготовка к сборке фрезерного станка с ЧПУ
Перед началом сборки фрезерного станка с числовым программным управлением (ЧПУ) необходимо тщательно подготовиться:
- Разработать подробные чертежи и 3D-модель будущего станка
- Составить список всех необходимых комплектующих и материалов
- Закупить качественные компоненты от проверенных производителей
- Подготовить необходимый инструмент для сборки
- Изучить инструкции по сборке аналогичных станков
Наличие доступа к токарному и сверлильному станку значительно упростит изготовление некоторых деталей. Также стоит заранее определиться с габаритами рабочей зоны будущего фрезера.
Основные компоненты для сборки ЧПУ фрезера
Для сборки фрезерного станка с ЧПУ потребуются следующие основные компоненты:

Механические компоненты:
- Алюминиевый профиль для рамы
- Линейные направляющие
- Шарико-винтовые пары
- Шаговые двигатели
- Шпиндель
- Крепежные элементы
Электронные компоненты:
- Драйверы шаговых двигателей
- Блок питания
- Плата управления
- Концевые выключатели
- Кабели
Выбор конкретных моделей зависит от желаемых характеристик станка и доступного бюджета. Для домашнего использования подойдут недорогие китайские комплектующие.
Сборка рамы и осей станка
Сборку фрезерного станка с ЧПУ рекомендуется начать с изготовления жесткой рамы и основных осей:
Сборка рамы:
- Нарезать алюминиевый профиль нужной длины для основания и стоек
- Соединить детали рамы с помощью уголков и болтов
- Выровнять раму по уровню
Монтаж линейных направляющих:
- Разметить места крепления направляющих на раме
- Просверлить отверстия и нарезать резьбу
- Закрепить направляющие болтами, обеспечив их параллельность
Установка шарико-винтовых пар:
- Закрепить опоры для ШВП на раме
- Установить ШВП в опоры
- Соединить ШВП с кареткой оси
Особое внимание следует уделить обеспечению высокой жесткости конструкции и точности монтажа направляющих.
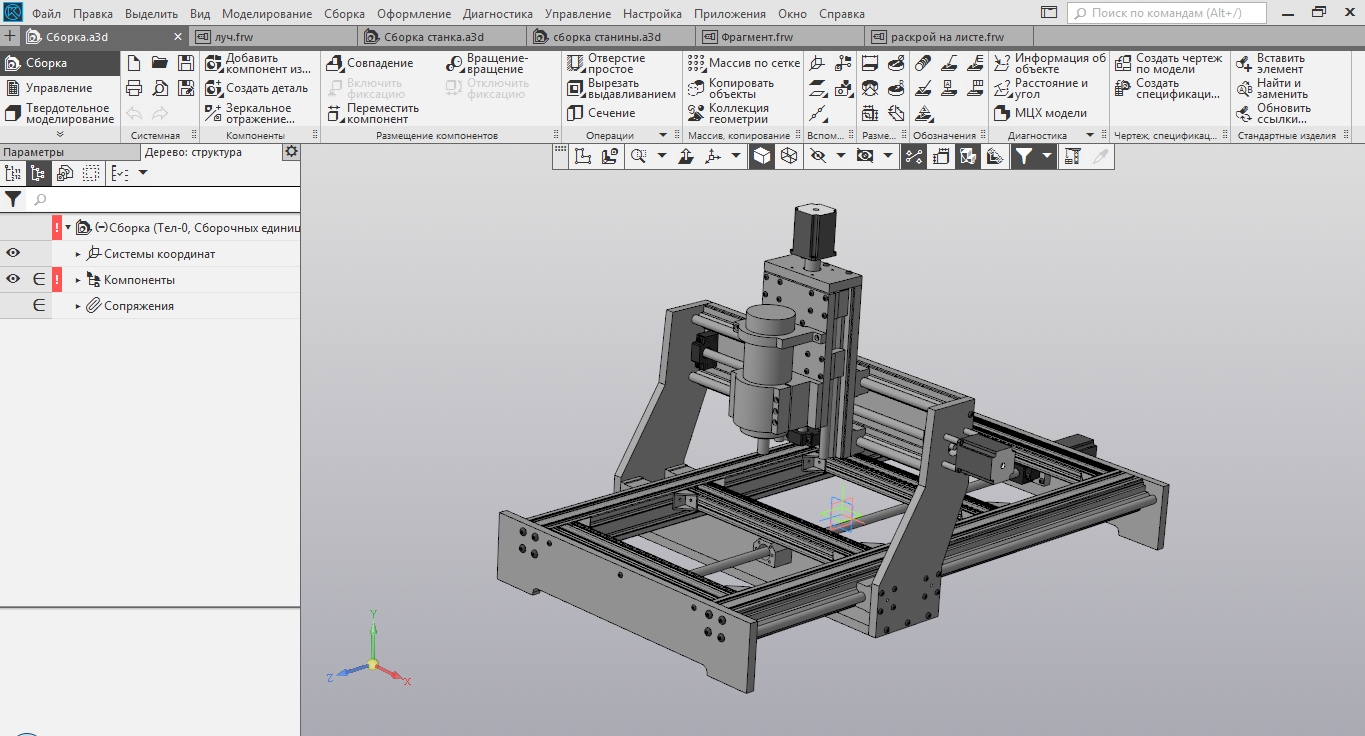
Установка приводов и электроники
После сборки механической части станка необходимо установить приводы и электронные компоненты:
Монтаж шаговых двигателей:
- Закрепить кронштейны для двигателей на раме
- Установить двигатели на кронштейны
- Соединить валы двигателей с ШВП через муфты
Подключение электроники:
- Закрепить драйверы и блок питания на монтажной панели
- Подключить двигатели к драйверам
- Соединить драйверы с платой управления
- Подключить концевые выключатели
Важно аккуратно проложить все провода, защитив их от повреждений при работе станка. Также необходимо обеспечить надежное заземление.
Установка шпинделя и рабочего стола
Завершающим этапом сборки механической части станка является монтаж шпинделя и рабочего стола:
Установка шпинделя:
- Закрепить кронштейн шпинделя на каретке оси Z
- Установить шпиндель в кронштейн
- Подключить шпиндель к блоку питания и системе управления
Монтаж рабочего стола:
- Изготовить стол из фанеры или алюминиевого композита
- Просверлить отверстия для крепления заготовок
- Закрепить стол на раме станка
При установке шпинделя важно обеспечить его точное позиционирование относительно осей станка. Рабочий стол должен быть идеально ровным и параллельным осям X и Y.
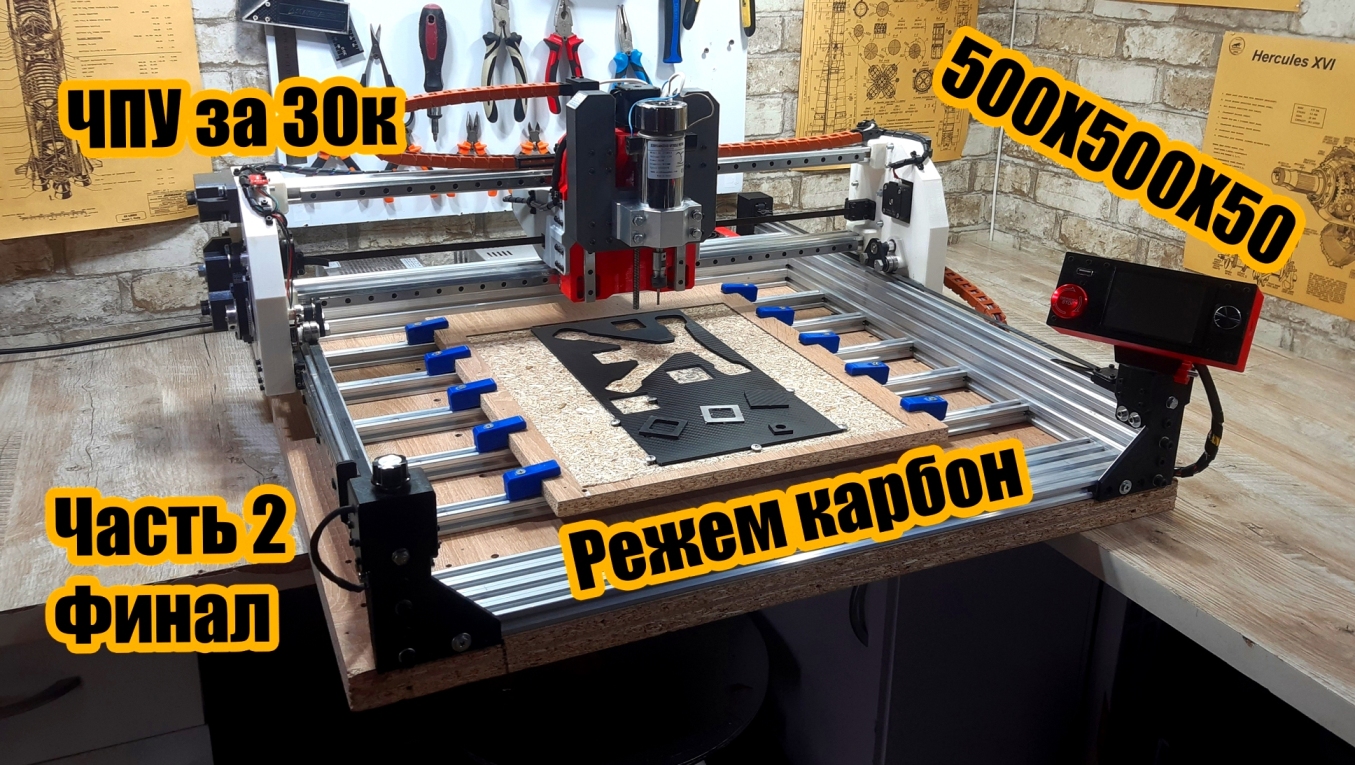
Настройка программного обеспечения
Для управления самодельным фрезерным станком с ЧПУ потребуется специальное программное обеспечение:
Основные программы:
- CAD-система для создания 3D-моделей (например, Fusion 360)
- CAM-программа для создания управляющих программ (например, ArtCAM)
- Программа управления станком (например, GRBL Controller)
Настройка управляющей программы:
- Указать параметры станка (размеры, скорости подач и т.д.)
- Настроить направления вращения двигателей
- Откалибровать перемещение по осям
- Настроить концевые выключатели
После настройки ПО необходимо провести пробную обработку простых деталей для проверки работоспособности станка и точности обработки.
Возможные проблемы при сборке ЧПУ фрезера
При самостоятельной сборке фрезерного станка с ЧПУ могут возникнуть следующие проблемы:
- Недостаточная жесткость рамы, приводящая к вибрациям
- Неточность установки направляющих и ШВП
- Люфты в передачах от двигателей к осям
- Некорректная настройка драйверов шаговых двигателей
- Ошибки в подключении электроники
Для решения этих проблем может потребоваться доработка конструкции и более точная настройка компонентов станка. При возникновении сложностей рекомендуется обратиться за консультацией к опытным специалистам.
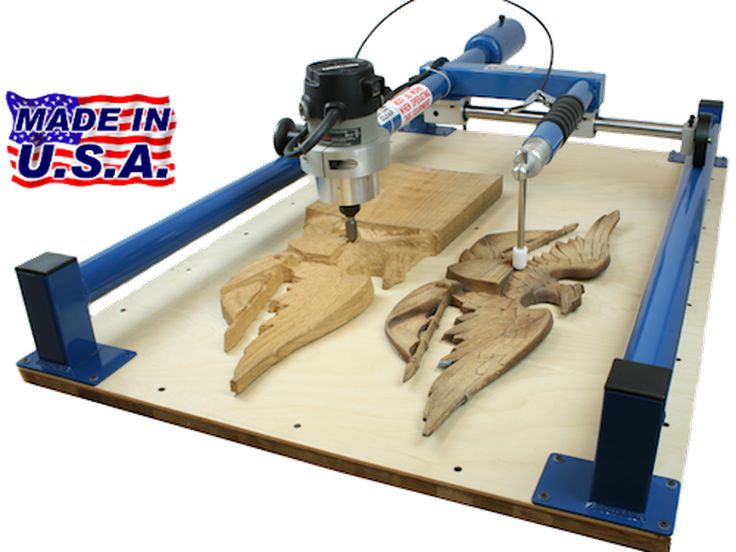
Советы по эксплуатации самодельного ЧПУ фрезера
Для обеспечения долговечности и точности работы самодельного фрезерного станка с ЧПУ следует придерживаться следующих рекомендаций:
- Регулярно проверять затяжку всех крепежных элементов
- Смазывать направляющие и ШВП согласно регламенту
- Очищать станок от стружки после каждого использования
- Периодически проверять точность позиционирования по осям
- Не превышать допустимые режимы резания
При правильной эксплуатации и своевременном обслуживании самодельный ЧПУ фрезер может служить долгие годы и обеспечивать высокое качество обработки деталей.
Домашний ЧПУ-фрезер как альтернатива 3D принтеру, часть вторая, инструмент и приспособления
На днях устыдили меня, мол ругаюсь на дилетантов, а сам ничего хорошего не пишу, а обещал ажно «цикл статей». Пришлось достать старый черновик и доработать. Для забывших — первая часть про выбор станка тут.Предположим, что Вы определились с моделью фрезера, провели первичные переговоры с поставщиком и начали морально готовиться к покупке. Что еще понадобится для начала работы?
Хотя многие поставщики вкладывают в комплект «стартер кит», для комфортного домашнего использования он будет явно недостаточен. Так что сразу начинаем искать/покупать/делать следующее:
— Режущий инструмент — фрезы/граверы и боры
— Дополнительные цанги к шпинделю
— Крепеж для стола
— Систему изоляции и/или удаления стружки
И да, сразу оговорюсь: данная статья касается домашних фрезеров со шпинделями типа Kress или китайчонками с цангой Er11, поэтому во-первых предположим, что хвостовик фрезы у нас цилиндрический до 6 мм (у Кресса есть 8, но нормальной его работу с 8кой не назовешь — слабенький он таки), во-вторых, механический инструмент смысла не имеет — мощи не хватит, а в третьих, сверла-развертки-метчики-флайкаттеры недоступны, поскольку минимальная скорость — 6000 оборотов.
Режущий инструмент
Станок у нас фрезерный, так что о фрезах в первую очередь. Фрезы подразделяются по:
1. Профилю режущей кромки
1.1. Прямые (end mill) — фреза с рабочей областью цилиндрической формы, дающая в идеале паз с идеально прямоугольным дном
1.2. Круглые (ball mill) — фреза с рабочей областью, оканчивающейся радиусом, дающая в идеале паз с радиусными стенками
1.3. Bull nose mill — прямая фреза со скругленным краем, дающая паз с прямым дном, но радиусным переходом между дном и стенкой.
1.4. Конические (cone mill) — фреза с конической рабочей областью, заканчивающейся радиусом или прямой площадкой
1.5. Фасонные (profile mill) — фрезы с определенным профилем, в случае с ЧПУ могут иметь смысл либо для ускорения работы, либо для создания поднутрений.
1.6. Пазовые (slot cutter) — фрезы для создания пазов с поднутрениями типа Т-пазов, ластохвостов, О-пазов и пр.
2. Способу отведения стружки
1.1. Спиральные с удалением стружки вверх — работают на большинстве материалов.
1.2. Прямые, они же half-pipe mill, они же граверы в русскоязыной литературе — без удаления стружки, подходит для слоистых материалов типа фанеры, гетинакса и пр, либо для раскроя листовых пластиков, когда спиральная фреза может поднять матерал над столом
1.3. Спиральные с удалением стружки вниз — для ламинатов, если важно обеспечить максимально ровный рез ламинирующего покрытия
1.4. Спиральные компрессионные — фрезы со переменной спиралью, нижняя часть отводит стружку вверх, верхняя — вниз, для двухсторонних ламинатов, чаще всего — для раскроя алюкобонда/дибонда.
3. Количеству режущих кромок
Для работы с пластиком/деревом обычно хватает одно-двухперой фрезы во всем диапазоне размеров, с цветметом 4-6 мм уже может понадобиться 3-4перая.
4. Отношению рабочей части к хвостовику
4.1. Равномерные — одинаковая рабочая часть и хвостовик.
4.2. Обниженные — хвостовик шире рабочей части. Актуально для мелких фрез.
4.3. Расширенные — часто для фасонных фрез, обычные такие в продаже не встречал, но сам делал, хвостовик уже рабочей части.
5. Материалу, углу заточки, углу спирали, покрытию и т.д.
Тут перечислять, пожалуй, бесполезно — технологий великое множество. Стоит только отметить, что производитель обычно пишет рекомендованный материал и качество обработки (черновое/чистовое), если вы закупаетесь на али, где продавец побрезговал давать рекомендации или рекомендации явно фейковые («суперчистовая обработка титан/алмаз/колбаса/фанера»), попробуйте найти аналогичную внешне фрезу (спиральная, один заход, желтенькая) у именитого производителя в каталоге и ориентируйтесь на эти данные.
Отдельно стоит выделить бор-фрезы — фрезы с большим количеством очень маленьких режущих элементов и относительно мощной сердцевиной. Такие фрезы предназначены для доводки или поверхностной обработки материалов типа шлифовки, снятия тонкого слоя, гравировки твердых материалов и т.д.
Теоретически, со станком можно использовать сверла, но не забывайте учитывать обороты. Все-таки сверла обычно рассчитаны на дрель, где обороты редко превышают 800 об/мин, а на обсуждаемых шпинделях 6000 минимум. Впрочем, для мелких сверел это будет скорее плюсом, но если речь заходит о 3 и более мм, во-первых постарайтесь приобретать сверла с покрытием, а во-вторых, стройте траекторию для сверления таким образом, чтобы сверло не успевало перегреться.
Цанги и переходники
Поскольку поставщик у нас в лучшем случае российский перепродавец, а в худшем — китаец, рассчитывать стоит на минимизацию комплекта. А боль-мень серьезная работа со станком подразумевает наличие некоторого количества фрез, скорее всего с разными хвостовиками. Теоретически, в продаже существуют переходники — дополнительные цанги, позволяющие вставить фрезу с хвостовиком 3 мм в цангу 6 мм, но стоит помнить что это во-первых снизит жесткость, а во-вторых снизит точность установки фрезы.
Стандарт Er11 подразумевает полный диапазон от 0,5 мм по 7 мм с шагом 0,5, т.е. цанги идут 0,5-1, 1-1,5, 2-2,5 мм и так далее.
Крессовский шпиндель имеет проприеритарную цангу, но благодаря распространенности самого шпинделя и клонов/подделок, достать цанги не проблема. В наличии по магазинам обычно есть цанги 3,4,5,6 и 8 мм + 3.175 мм «американского стандарта», в котором у нас встречаются борфрезы и граверы. При этом сама цанга цетырехчастная, т.е. диапазон зажатия вряд ли сильно больше пары десяток, так что зажать фрезу с хвоствоиком 3.5 мм будет просто нечем. Впрочем, это вряд ли будет проблемой в домашнем применении.
Чуть не забыл: цанги обычно продаются отдельно от гаек. В принципе, нет никакой проблемы в перекидывании цанг в одной гайке, но мне лень, да и есть мелкая, но вероятность что при перекидывании занесешь в резьбу какой-нибудь мусор, а это опасно для резьбы.
Крепеж для стола
Большинство домашних роутеров оборудованы либо столом с Т-пазами, либо столами с сеткой резьбовых отверстий. И в том и в другом случае наиболее распространенный крепеж выглядит как стальной или алюминиевый прижим с одним резьбовым и вторым гладким отверстием. В Т-паз вставляется Т-болт, который проходит через отверстие прижима и фиксируется гайкой, второй болт отжимает прижим от стола. В комплекте со станком обычно идут 4 прижима, которые при интенсивной эксплуатации довольно быстро выходят из строя: срезаются резьбы на винтах и прижимах. Иногда китайцы вместо Т-болта кладут в комплект обычные болты и Т-гайки, рекомендую сразу озаботиться заменой на Т-болты.
Вместо задних (упорных) винтов можно приспособить куски материала или специальные ступенчатые клинья, но в случае работы со скользким пластиком это может сослужить дурную службу: крепеж будет «отползать» от фиксируемого материала.
Альтернативой прижимам могут служить станочные тиски — специальные тиски с минимизированной высотой и адаптированной для установке на столе рукояткой (или вообще под ключ). Плюс — мЕньшая морока при установке материала, повторяемость, относительная точность. Если Вы работаете с похожими небольшими заготовками, можно один раз в жизни выставить тисы, записать их координаты и в дальнейшем отталкиваться от них. Минусы — большая часть готовых тисков съедает 20-30 мм высоты минимум, а обсуждаемые станки редко имеют более 70 мм под порталом, ну и с большими размерами тисы обойдутся неимоверно дорого.
Еще один вариант — приклеивание заготовки к столу. Как ни странно, силы удержания на хорошем двустороннем скотче хватает даже на щадящую гравировку цветмета, не говоря уже о пластиках. В не к ночи упомянутом Roland даже в инструкции было что-то про скотч написано. Минусы очевидны: переменная надежность, ну и главное — отдирать уже готовое изделие, а потом чистить его от скотча.
Ну и напоследок — экзотика для домашних станков, вакуумный прижим. В принципе, не такая уж сложная штука, но требует дополнительного вакуумного насоса и таки сжирает 10 мм высоты минимум.
Система изоляции и удаления стружки
Одна из наиболее частых проблем использования роутера дома — шум и пыль. И если с шумом еще можно смириться, то пыль выбешивает конкретно. А в случае обработки камня/гетинакса/стекла/композитов — пыль еще и вредна.
Возможны 2 варианта борьбы: активная аспирация пылесосом со щеткой, смонтированной на шпинделе, и создание «кабинета» для станка.
Щетка вроде хороша, но при многочасовых траекториях рев пылесоса создает неповторимую атмосферу в доме. Ну и если идет глубокая выборка, ворс щетки постоянно изгибается и довольно быстро портится. Поэтому мы оставили систему аспирации только на самом большом фрезере, а мелкие убрали в кабинеты из прозрачного поликарбоната и ламината. Не так компактно, конечно, зато кабинет гасит и немножко звука, и пыль.
Мой личный набор «молодого бойца»
И напоследок — маленький бонус. Мой личный набор «молодого бойца», который я покупаю/делаю для каждого нового фрезера (основная работа — 3D фрезерование форм по ПП, ПОМ, ПЭТ, композиты):
Фрезы:
- 6 мм однозаходная прямая длинная — кромка 40 мм, общая длина 75, китайка.
- 6 мм шариковая хорошая (Widia/Makestag/SGS)
- 4 мм однозаходная прямая длинная китайка
- 3 мм двузаходная прямая длинная хорошая
- 3 мм двузаходная шариковая длинная хорошая
- 1,5 мм с удлиненной шейкой прямая хорошая
- 1,5 мм с обычной шейкой шариковая хорошая
- 0,8 мм с обычной шейкой шариковая, либо коническая с круглой пяткой 0,8 мм.
Цанги: 3, 4, 6 мм, все в комплекте с гайками.
Крепеж: упрочненные Т-винты 80 мм + упрочненные винты для упоров.
Кабинет — самоделка.
Промышленный пылесос. В принципе, сейчас придумал кабинет без дна, в котором стружка будет ссыпаться в коробку сама, так что пылесос будет не очень нужен. Но до этого — покупал в каждое новое место, куда ставим станок, без пылесоса из кабинета стружку доставать шибко тяжело.
Этого набора вполне хватает в 99% случаев.
На этом разрешите откланяться, в следующий раз — немножко о софте, общие понятия обработки и стратегии обработки.
UPD. другие статьи цикла:
Домашний ЧПУ-фрезер как альтернатива 3D принтеру, часть первая — выбор станка
Домашний ЧПУ-фрезер как альтернатива 3D принтеру, часть третья, ПО и G-code
Домашний ЧПУ-фрезер как альтернатива 3D принтеру, часть четвертая. Общие понятия обработки
как собрать самодельный мини станок cnc по чертежам с размерами для резьбы по дереву
Если вы хорошо разбираетесь в технике, для вас не составит труда собрать фрезерный ЧПУ-станок у себя дома. Это выйдет значительно дешевле, чем приобретать новое устройство, и к тому же доставит вам удовольствие от самореализации. Все необходимые компоненты можно приобрести в магазинах электроники и стройматериалов. Ниже приведены детальные инструкции по сборке станка с фотографиями.
Подготовительные работы
Подготовка к построению станка предполагает такие фазы:
- создание чертежей;
- закупку надежных комплектующих и крепежа;
- подготовку качественных инструментов;
- ознакомление с текстовыми и видеоинструкциями.
Замечательно, если у вас найдется доступ к сверлильному и токарному станкам — это существенно облегчит конструирование фрезерного.
Как сделать фрезерный станок ЧПУ своими руками: пошаговая инструкция
Устройство можно изготавливать двумя методами:
- Приобрести готовый комплект запчастей и самостоятельно смонтировать из него устройство.
- Изготовить или приобрести все комплектующие по отдельности.
Второй вариант более сложный и затратный по времени, зато более бюджетный.
Подбирая материал для устройства, надо учитывать, что он обязан быть прочнее тех материалов, которые будут на нем обрабатываться.
Модели с подвижными столами хороши только в том случае, если станок будет компактным, менее 30 × 30 см. Для более крупных моделей оптимальными станут двигающиеся порталы.
В большинстве случаев устройства домашней сборки оснащаются шаговыми двигателями, а промышленные модели — более сложными и дорогостоящими сервоприводами.
Если вас интересует затейливая многомерная резка, лучше приобрести шпиндель с водяным охлаждением. Он недешевый, но издает меньше шума, способен обрабатывать разнообразные материалы и не перегревается, работая на пониженных оборотах.
Станок, описанный в этой статье, обошелся ориентировочно в 1500 евро. Им можно обрабатывать фанеру, пластик, лиственную древесину и алюминий.
Как вариант: основой для фрезерной установки может послужить сверлильная, где головка со сверлом заменяется на фрезерную. Чтобы инструмент мог передвигаться по трем плоскостям, механизм следует оснастить подшипником. Удобнее всего собирать такие механизмы на основе принтерной каретки, потом останется только оснастить аппарат программным управлением.
Проектирование
Эскиз для станка можно начертить по старинке от руки, но лучше воспользоваться компьютерной программой, к примеру AutoCAD (как профессиональный вариант) или Google Sketchup (опция попроще, предоставляется бесплатное использование на месяц). На рисунке должны быть точно переданы габариты всех комплектующих, чтобы понимать, какие детали заказывать.
Комплектующие
Для изготовления станка вам потребуются следующие механические компоненты:
- профиль из алюминия 30 × 60 мм, порезанный на отрезки до 10 см;
- пластина из алюминия толщиной 15 мм;
- штырь из стали с резьбой M10 с гайкой из делрина;
- линейные направляющие SBR 16 и SBR 20;
- шарико-винтовая пара с шагом 5 мм и диаметром 16 мм;
- ножки для выравнивания и защиты от вибрации.
Также надо будет обзавестись нижеперечисленными электрическими элементами:
- 3 шаговыми двигателями 3 Nm Nema 23;
- 3 драйверами для этих двигателей DM556 Leadshine;
- блоком питания 36 В;
- интерфейсной платой 5 Axis CNC Breakout Board;
- источником питания 5 В к плате;
- двухпозиционным выключателем On/Off;
- многожильным кабелем Shielded 4 Conductor 18 AWG;
- 3 сенсорными концевыми выключателями;
- шпинделем Kress FME 800 (его можно заменить на Dewalt Compact Router либо Bosch Colt ).
Программ будет нужно две — CamBam, совмещающая в себе функционал CAD и CAM, а также Mach4 для контроля устройства.
Ось X
Рама оси создается из алюминиевого профиля 30 × 60 мм (4 сегмента) и пары боковых панелей 15-миллиметровой толщины. На окончаниях профилей располагаются два отверстия с диаметрами 6,8 мм. Изнутри отверстий метчиком выполняется резьба М8.
Для совпадения отверстий на концевых панелях пластины надо прижать друг к другу во время сверления. В их серединах просверливаются 4 отверстия для установки подшипниковых опор. В одной боковой пластине просверливаются дополнительно 4 отверстия, чтобы закрепить двигатель.
Из алюминиевых кусочков с габаритами 50 × 20 × 50 выполняются 4 блока для крепления ножек, которые будут обеспечивать столу ровное положение. Блоки прикручивают к профилям снаружи посредством четырех болтов М5 с t-гайками для мебели.
К профилям нужно подвести рельсы. Пазы в профилях должны идеально совпадать с отверстиями, высверленными в основаниях направляющих.
При установке можно пользоваться t-гайками для мебели и болтами М5.
Боковые пластины и сборка портала
Единственное отличие между идентичными пластинами таково: в одной высверлены четыре отверстия, куда будет крепиться мотор. Для изготовления портала применяются 15-миллиметровые пластины из алюминия. Чтобы разместить эти отверстия строго в правильных местах, сначала следует пробить углубления с помощью кернера. На следующем шаге отверстия проделываются на сверлильном станке— сперва инструментом с намеренно слишком маленьким диаметром, а потом с подходящим.
Ось Y
Каретка оси Y выполнена из единственной пластины, а на ней закреплены линейные подшипники. Работать сверлом тут необходимо максимально выверенно, без отклонений даже на миллиметр. К пластине крепятся подшипники для осей Y и Z. В силу минимального расстояния между подшипниками они могут заедать даже при незначительном смещении. Проверьте, чтобы каретка без проблем проскальзывала по обеим сторонам. Рельсам и подшипникам нужна тщательная регулировка. Чтобы выровнять их как можно точнее, желательно пользоваться цифровыми приспособлениями.
Ось Z
Рельсы оси Z подсоединяются к подвижной части узла оси Z. Важно проследить, чтобы они оказались смещены от края пластины ориентировочно на полсантиметра. Выровнять их можно с помощью двух кусков пластика, используемых как прокладки. Для установки верхней пластины на узел оси Z в окончании монтажной пластины высверливают три отверстия.
Если шаговый мотор не удается разместить вплотную к пластине, потребуется выполнить для него отдельное пластиковое крепление.
Блоки корпусов подшипников тоже делаются пластиковыми. В качестве приводного винта применяется стержень из стали с резьбой М10. Шкив для зубчатого ремня просверливают, выполняют резьбу М10 и прикручивают к верхней половине приводного винта. Фиксировать эту деталь в нужной позиции будут три установочных винта. Гайку из делрина закрепляют к каретке оси Y.
Зубчатые ремни и шкивы
Место для крепления мотора обычно выбирают на отдельной стойке либо с внешней стороны устройства. Для соединения шариково-винтовой пары с мотором можно задействовать гибкую муфту.
Однако в компактном помещении размещенный снаружи мотор будет мешать, и поэтому его убирают внутрь. Если не получается соединить мотор с шариково-винтовой парой напрямую, можно воспользоваться шкивами и зубчатыми 9-миллиметровыми ремнями HTD5m.
Используя ременную передачу, можно применить понижающую передачу, чтобы подключить мотор к приводному винту. Тогда мотор малой мощности обеспечит идентичный крутящий момент, даже если устройство будет работать небыстро.
Подшипниковые опорные блоки
Опорные блоки для осей X и Y выполняют из алюминиевого прутка круглого сечения 50 мм, от которого отсекают четыре 15-миллиметровых сегмента. На прутке маркируют места расположения четырех монтажных отверстий и просверливают их, плюс отдельно сверлят еще одно крупное посередине. Потом переходят к полости для подшипников. Их нужно запрессовать, а блоки закрепить на боковых и торцевых пластинах посредством болтов.
Опора для приводных гаек
Шарико-винтовую пару для оси Z можно заменить стержнем с резьбой М10 и гайкой из делрина. Полиформальдегид делрин является самосмазывающимся и по мере эксплуатации не страдает от износа.
Чтобы минимизировать люфт, резьбу следует выполнять метчиком высокого качества.
Для осей X и Y выполнено крепление привода из алюминия. На гайках шарико-винтовой передачи расположена пара компактных фланцев с тремя отверстиями с каждого бока. По одному отверстию с каждой стороны используется, чтобы крепить гайки к держателю.
Держатель нужно обработать с высокой точностью на токарном станке. Прикрутив гайки к порталу и каретке оси Y, можно поворачивать шарико-винтовую пару ручным способом и перемещать эти комплектующие на другую сторону. Гайку начнет клинить, если габариты держателей окажутся неправильными.
Крепления двигателя
Для опор мотора применяют фрагменты алюминиевых труб с квадратным сечением, заранее порезанные с желаемой длиной. Как вариант, можно разрезать трубу из стали.
Надо убедиться, что крепления мотора по осям X и Y можно свободно двигать с целью натяжения зубчатых ремней. Выполнить прорези и высверлить крупное отверстие на одной стороне крепления можно как на сверлильном, так и на токарном станке.
Крупное отверстие с одной стороны выпиливают при помощи концевой пилы. Таким образом, двигатель садится на один уровень с поверхностью, а вал получается центрированным. С противоположной стороны крепления выполняют четыре слота, дающие мотору возможность скольжения вперед-назад.
Для крепежа двигателя используют болты М5.
Рабочая поверхность
Идеальной опцией стала бы столешница из алюминия с пазами в форме буквы Т, но это стоит недешево. Поэтому ее имеет смысл заменить перфорированной столешницей, так как она экономичнее и позволяет зажимать обрабатываемую деталь разными способами.
Для крепления к алюминиевым профилям стола из березового фанерного листа 18-миллиметровой толщины применяются болты М5 и гайки с пазами в форме буквы Т. Сетка с шестиугольными вырезами под гайки выполняется в CAD-софте, потом отверстия проделываются на станке с ЧПУ.
Поверх фанеры устанавливают лист МДФ 25-миллиметровой толщины. Для прорезания отверстий в обеих частях применяют большую фасонную фрезу. Отверстия в МДФ выравнивают с центрами заблаговременно проделанных шестиугольных отверстий. Потом МДФ снимают, а гайки устанавливают в отверстия фанерного листа. После этого МДФ возвращают на место.
Электрика и электроника
Для создания электронной составляющей предстоит воспользоваться нижеперечисленными комплектующими:
- источником питания с выходным напряжением 48V DC и выходным током 6,6 A;
- 3 драйверами шагового мотора Leadshine M542 V2.0;
- 3 шаговыми моторами 3Nm hybrid Nema 23;
- интерфейсной платой;
- реле — 4-32V DC, 25A/230 V AC;
- главным выключателем;
- блоком питания к плате 5V DC;
- блоком питания для охлаждающих вентиляторов 12V DC;
- парой вентиляторов Cooler Master Sleeve Bearing 80mm;
- парой розеток — для пылесоса и шпинделя;
- кнопкой экстренного завершения работы и концевыми выключателями.
Если моторы не самые мощные, допустимо использование платы на три мотора — однако все равно рациональнее применить индивидуальные драйверы. Микрошаговый режим драйверов Leadshine обеспечивает предельную плавность перемещения инструмента и понижает вибрации мотора.
Источник постоянного напряжения 5 В подключают к главному входу питания. Для вентиляторов устанавливают розетку, электроэнергия к ним поступает через традиционный 12-вольтовый адаптер, размещенный на стене.
Компьютер контролирует реле на 25А через прерыватель. Входные клеммы реле подключаются к выходным клеммам прерывателя. Реле подключается к паре розеток, питающих электричеством Kress и пылесос для сбора стружек.
Если в конце G-кода стоит команда M05, шпиндель с пылесосом выключатся. Для их повторного включения потребуется нажатие кнопки F5 либо ввод команды M03.
Программное обеспечение
Готовому устройству для полноценного функционирования требуется три разновидности софта:
- CAD, чтобы создавать чертежи;
- CAM, чтобы создавать траектории инструментов и выводить G-код;
- контроллер, считывающий G-код и управляющий маршрутизатором.
Хорошим примером софта, совмещающего в себе функционал CAD и CAM, станет CamBam. Он несложный и вполне подходит для домашнего производства. Перед началом работы ему нужно задать параметры: диаметр применяемых инструментов, глубину и скорость резания, глубину за проход и так далее. Задав софту траекторию, можно будет вывести G-код, отдающий станку непосредственные команды.
В качестве контроллера следует порекомендовать Mach4. Он будет передавать сигналы на интерфейсную плату через параллельный порт компьютера. С помощью команд контроллера будет происходить обнуление режущего инструмента и запуск программы резки. Также контроллер может менять скорость резания и шпинделя.
Отладка самодельного станка с ЧПУ
Перед началом полноценной работы на станке надо обработать несколько пробных деталей различных конфигураций и габаритов, сделанных из разных материалов. Возможно, в процессе выяснится, что устройство издает слишком громкий шум, и от него во все стороны разлетается пыль. Тогда его можно оснастить пылеуловителем, соединенным с пылесосом.
Нередко оказывается, что расчет крутящего момента на Y-опоре был произведен некорректно. В таком случае из-за высокой нагрузки по оси Y станок начнет изгибаться. Для устранения этого изъяна надо купить вторую направляющую и модернизировать портал.
Как собрать ЧПУ-стол?
Чтобы по максимуму использовать возможности станка, его нужно поместить на прочный и устойчивый стол. Проще всего взять за основу старый стол и переделать его под новые нужды. Для работы нужно заранее подготовить:
- кнопку завершения работы;
- фиксатор роликов;
- зенковку и биты;
- дрель;
- электрическую отвертку;
- пилу;
- станок X-Carve;
- концевую фрезу на 4 дюйма с твердосплавным покрытием;
- твердосплавную фрезу на 4 дюйма, с 4 каналами, с шариковым наконечником;
- средства защиты слуха.
От старого стола нужно взять две большие полки и укрепить их. По четырем внутренним углам надо разместить угловые скобки, а по длине поперечной балки, которая проходит по нижней стороне — L-образные скобки. Чтобы закрепить полку, нужно добавить дополнительные деревянные подставки. После того как полка будет помещена на место, надо укрепить ее еще большим количеством скобок.
Чтобы найти разумное применение каждому сантиметру помещения, стол хорошо бы оснастить пегбордом, то есть перфорированной панелью для инструментов. Углы панели вырезаются электролобзиком, держатели для инструментов крепятся в отверстиях, на пегборд добавляются лотки для хранения мелких комплектующих.
Пространство в нижней части стола тоже прекрасно подходит для хранения объектов — в частности, барабанного шлифовального станка или настольной пилы. Для хранения материалов можно соорудить съемную полку, воспользовавшись для этого листом фанеры и заготовленными для ножек деревянными брусками. Ножки крепятся к листу фанеры с помощью угловых скоб.
Еще одну полку можно оборудовать наверху — иногда это помогает закрыть проводку от станка и розетку. Верхнюю полку укладывают на торцы стоек и прикручивают. У второй полки углы для ножек вырезают с помощью лобзика.
Сложности в работе, возможные ошибки и как их избежать
При монтаже станины нельзя применять соединения сварного типа, так как они не справляются с вибронагрузками. В местах крепления рекомендуется пользоваться Т-образными гайками.
Чтобы усилия передавались на вал равномерно, на винтовых передачах следует размещать зубчатые ремни, не проскальзывающие на шкивах.
Исключительно важно приобрести надежные подшипники и качественные ходовые винты — это гарантирует станку прочность и долговечность.
Габариты всех деталей необходимо подбирать с максимально возможной точностью и следить, чтобы они безупречно подходили к блоку.
Итак, теперь вы знаете, как собрать дома фрезерное устройство с ЧПУ. Конечно, это удобнее делать с напарником, а не в одиночку. Если вы обладаете достаточными навыками и свободным пространством дома или в гараже, собранный по этой инструкции станок прекрасно заменит вам аналог, созданный на заводе.
- 29 августа 2020
- 2420
фрезерный станок из принтера своими руками
Числовое программное обеспечение (ЧПУ) обеспечивает автоматизацию обработки деталей на разных станках. Такое оборудование можно собрать в домашних условиях из старых аппаратов. Один из доступных вариантов — ЧПУ из принтера, который позволяет практически без дополнительных затрат изготовить небольшой универсальный станок.
Материалы и инструменты для изготовления ЧПУ станка из принтера
Простой самодельный станок с ЧПУ из принтера показан на фото. Он имеет рабочую зону размером 16 × 24 × 7 см. Способен обрабатывать текстолит (толщиной до 3 мм), фанеру (до 15 мм), пластик и дерево. Основное назначение — гравировка.
Для изготовления такого станка потребуются следующие материалы, детали и комплектующие:
- Основа — принтер. Рекомендуется аппарат матричного типа, например, HP, Epson, Xerox, Ricoh, Canon. Важными его элементами являются шаговые двигатели.
- Фанера толщиной от 15 мм. Она необходима для корпуса станка.
- Уголки из дюралюминия размером 20 мм.
- Подшипники: 606 или 608 в количестве 3 шт. и линейные (4 шт.).
- Саморезы.
- Болты М8 длиной 25 мм и гайки М8 (2 шт.).
- Шпилька строительная М8.
- Шланг резиновый.
- Дремель.
- Кронштейн для крепления доски шириной 80 мм.
- Клей ПВА и эпоксидный.
Заранее следует приготовить такой инструмент:
- электродрель;
- электролобзик;
- тиски;
- ножовка;
- плоскогубцы;
- напильники нескольких размеров;
- бокорезы;
- отвертки;
- гаечные ключи;
- инструмент для нарезания резьбы.
Для измерений и разметки потребуется металлическая линейка и угольник.
Что можно полезного извлечь из принтера?
Из матричного принтера можно взять множество деталей для сборки станка с ЧПУ:
- Наибольшую ценность представляют шаговые двигатели для перемещения головки и листов бумаги. Вместе с ними извлекаются контроллеры.
- Стальные каленые направляющие обеспечивают повышенную прочность. Они выполнены с большой точностью.
- Узел скольжения головки печатающего устройства. Особенно хороши аппараты старого типа. Здесь можно найти удобные медные втулки, способные заменить подшипники.
- Зубчатый ремень привода. Он вполне сгодится для сборки ременной передачи станка.
- Концевые выключатели. Они пригодятся для сборки схемы управления.
Важно! Аппарат следует разобрать максимально полно. Для сборки станка пригодятся практически все детали — винтики, гайки, шпильки и т. д.
Как изготовить ЧПУ станок из принтера своими руками: пошаговая инструкция
Сборка станка с ЧПУ из принтера осуществляется в таком порядке:
- Изготовление элементов корпуса из фанеры. Выпиливаются 2 боковые стенки размером 37 × 37 см, задняя стенка размером 34 × 37 см и передняя стенка размером 9 × 34 см.
- Соединение стенок корпуса с помощью саморезов. Предварительно для них рекомендуется просверлить отверстия, чтобы не повредить заготовки.
- Установка направляющих оси Y. Они изготавливаются из уголка. Для их монтажа на боковых стенках на расстоянии 30 мм от нижнего среза делается шпунт глубиной 2 мм. Он необходим для ровного крепления уголков. Длина направляющих составляет 34 см. Их крепление обеспечивается саморезами.
- Изготовление рабочей поверхности. Используются уголки длиной 14 см. На рабочей поверхности закрепляются подшипники 608: 2 штуки снизу и 1 шт. сверху. Плавное перемещение площадки обеспечивается идеальной соосностью подшипников.
- Выход для шагового двигателя оси Y делается в форме отверстия диаметром 22 мм на расстоянии 50 мм от низа. В передней стенке сверлится отверстие диаметром 7 мм для линейного подшипника опоры винта хода.
- Изготовление винта хода из строительной шпильки. Он соединяется с валом двигателя через муфту.
- На гайке М8 увеличенной длины сверлится отверстие диаметром 2,5 мм и нарезается резьба. Это отверстие необходимо для установки гайки на ось станка.
- Изготовление направляющих оси Х из стальных направляющих принтера. На ось устанавливаются каретки, извлеченные оттуда же.
- Изготовление оси Z. Основание для нее выполняется из фанеры толщиной 6 мм. Направляющие оси извлекаются из принтера (размер 8 мм). Фанерные детали скрепляются клеем ПВА, и на них с помощью эпоксидного клея закрепляются линейные подшипники. Можно использовать втулки каретки принтера. Изготавливается ходовая гайка аналогично вышерассмотренному варианту.
- Изготовления шпинделя. В обычном понимании, такого элемента нет. Вместо него монтируется дремель с держателем, выполненным из кронштейна для доски. Для выхода дремеля сверлится отверстие диаметром 19 мм. Крепится кронштейн на основании Z оси с помощью саморезов.
- Установка опор Z оси. Они изготавливаются из фанерных элементов: основание размером 15 × 9 см, 2 стороны размером 9 × 5 см. На верхней стороне в центе сверлится отверстие для подшипника опоры. Делаются отверстия для направляющих.
На фото показано расположение направляющих станка и внешний вид каретки оси Z. Завершает сборку монтаж электронной начинки. Если сборщик владеет нужными навыками, то ему не составит труда собрать плату ЧПУ из микросхем принтера. В противном случае рекомендуется приобрести уже готовую плату.
Изготовление муфт
Важным элементом станка является муфта, с помощью которой вращение шагового двигателя передается рабочему органу (винт хода). Она способна снижать вибрацию при работе, что защищает двигатель, продлевая его срок службы. Самодельную муфту можно изготовить из резинового шланга достаточной прочности.
Внутренний диаметр шланга должен соответствовать диаметру выходного вала электродвигателя. Шланг с одного конца одевается на вал и закрепляется с помощью клея или хомутов. Другой конец закрепляется на ходовом винте. Если винт имеет диаметр, превышающий диаметр шланга, то конец придется расточить до нужного размера. Лучше всего для муфты подходит шланг высокого давления. Для него следует заранее приготовить фланцы, заказав их у токаря.
Фрезерный станок ЧПУ SolidCraft CNC-3040 Light (300Вт)
- Электропитание 110В/220В
- Размеры, мм 610 х 490 х 390
- Программное обеспечение Mach4, Emc2
- Количество оборотов шпинделя 11000 об./мин
- Количество осей 3
- Мощность шпинделя 300 Вт
- Повторяемость 0.05 мм
- Рабочая подача 4000 мм/мин
- Рабочая скорость, мм/мин 300-3000
- Размер рабочего поля станка 390 х 280 х 55 мм
- Формат файла gcode, nc, ncc, tab, txt
- Тип двигателя шаговый 57/1. 8A
Особенности изготовления фрезерного станка из принтера своими руками
В отличие от вышерассмотренного простого станка ЧПУ, фрезерный станок должен иметь более массивную и устойчивую конструкцию. Его изготовление имеет ряд особенностей. Прежде всего, необходимо выбрать схему фрезера. На фото показана стандартная схема на основе старого сверлильного станка. Применение шаговых двигателей от принтера позволяет обеспечить функционирование станка с помощью ременных передач, исключая винтовые передачи.
Основа станка — прямоугольная балка, надежна фиксируемая на направляющих. Несущая конструкция обладает повышенной прочностью. Узлы скрепляются болтовым соединением.
Порядок сборки:
- В суппортах устанавливаются направляющие и закрепляются на боковинах до их установки на основание.
- Регулируется плавность перемещения суппортов по направляющим.
- Фиксируются направляющие путем затягивания болтов.
- На основании закрепляются суппорты, узел направляющих и боковины.
- Собирается узел оси Z и через переходную пластину соединяется с узлом оси Х.
- Устанавливаются ходовые винты и соединяются с двигателями через муфту.
- Монтируются и закрепляются шаговые двигатели.
Особое внимание уделяется изготовлению суппортов. На фото показаны чертежи суппортов по всем осям. При креплении важно учитывать, что вертикальная ось (Z) испытывает значительные нагрузки, а потому вертикальные стойки должны обладать повышенной прочностью.
Что можно взять от принтера?
Опыт некоторых умельцев показывает, что можно использовать для самодельного фрезерного станка ЧПУ . Примеры применения материалов и комплектующих:
- Для оси Х использовались основания от принтера матричного типа формата А3. На них закреплялись мебельные направляющие длиной 50 см.
- Для оси Y находит применение двигатель от матричного принтера и ременная передача, а сам каркас выполнен из досок 100 × 25 мм.
- Для оси Z наиболее подходит шаговый двигатель от сканера. Винтовая передача обеспечена шпилькой М10. Применены мебельные направляющие длиной 30 см.
Важно! Шпиндель фрезерного станка можно изготовить из двигателя от старого автомобильного компрессора. На его вал устанавливается цанга.
Схемы
Любой станок с ЧПУ включает в себя корпус, рабочие органы, механическую, электрическую и электронную часть. Механическая часть включает узлы перемещения рабочего органа по 3 осям — Х, Y, Z, в т. ч. направляющие, ходовые винты, передачи. Электрическая часть — это шаговые двигатели, извлеченные из принтера, которые устанавливаются на каждой оси, а также блоки питания. Рабочие органы выбираются в зависимости от назначения станка — фрезерные головки, шпиндели и т. д.
3D фрезерный станок ЧПУ AMAN 2030 800W
- Операционные системы Windows 2000/XP
- Электропитание 220В ± 10% 50HZ
- Форматы файлов 3D, Графические, Векторные
- Размеры, мм 560 x 470 x 460
- Программное обеспечение Mach4, Artcam, Type 3, Ucancam, Kcam и пр.
- Количество осей 3
- Мощность шпинделя 800 Вт
- Охлаждение шпинделя водяное
- Размер рабочего поля станка 300 x 200 x 60 мм
- Разрешение, мм 0,003125
- Система управления Mach4 interface
- Скорость шпинделя 24000 об/мин
- Цанговый патрон ER11
Само ЧПУ, по сути, представлено электроникой. Его принципиальная схема показана на фото. Здесь выделяются блоки считывания информации, памяти, корректировки программы и согласования. Такие блоки продаются в готовом виде.
Для собственной сборки подойдут плата от принтера или сканера. Схема управления шаговыми двигателями представлена на фото.
Для функционирования станка необходимо правильно подобрать управляющую программу. Ее можно написать самому, но лучше установить стандартное программное обеспечение (ПО). Каждый шаговый двигатель комплектуется контроллером, а ПО содержит необходимые драйверы. Обязательно предусматривается порт LPT, через который осуществляется подключение управляющей системы к станку.
При сборке схемы управления можно использовать:
- Для контроллеров применяются микросхемы серии 555ТМ7.
- В качестве драйвера можно использовать четырехканальный усилитель, который собирается на базе транзисторов типа КТ917. Находят применение стандартные микросхемы (например, ULN 2004 на ток 0,5-0.6А).
- Блок питания для двигателей подойдет источник на 12 В с током 3 А. Для запитки контроллера можно использовать блок на 5 В с током 0,3 А.
Перед началом сборки станка следует разработать самостоятельно или использовать готовые чертежи. Для фрезерного станка можно рекомендовать схемы, показанные на фото.
Принтер является, по сути, небольшим станком с ЧПУ со специфическим назначением. Такой аппарат матричного типа вполне пригоден для сборки станка для обработки различных материалов. Для металлических изделий требуется повышенная мощность, но для работы с деревом, пластиком, текстолитом и другими податливыми материалами можно своими руками собрать станок с ЧПУ из принтера, в т. ч. для фрезерования, гравирования, сверления и т. д.
Фрезерный станок с ЧПУ в домашних (гаражных) условиях
Набор, с помощью которого можно собрать свой фрезерный станок с ЧПУ.В Китае продаются готовые станки, обзор одного из них на Муське уже публиковался. Мы же с Вами соберем станок сами. Добро пожаловать…
UPD: ссылки на файлы
Я все-таки приведу ссылку на обзор готового станка mysku.ru/blog/aliexpress/27259.html от AndyBig. Я же не буду повторяться, не буду цитировать его текст, напишем все с нуля. В заголовке указан только набор с двигателями и драйвером, будут еще части, постараюсь дать ссылки на всё.
И это… Заранее извиняюсь перед читателями, фотографии в процессе специально не делал, т.к. в тот момент делать обзор не собирался, но подниму максимум фоток процесса и постараюсь дать подробное описание всех узлов.
Цель обзора — не столько похвастаться, сколько показать возможность сделать для себя помощника самому. Надеюсь этим обзором подать кому-то идею, и возможно не только повторить, но и сделать еще лучше. Поехали…
Как родилась идея:
Так получилось, что с чертежами я связан давно. Т.е. моя профессиональная деятельность с ними тесно связана. Но одно дело, когда ты делаешь чертеж, а после уже совсем другие люди воплощают объект проектирования в жизнь, и совсем другое, когда ты воплощаешь объект проектирования в жизнь сам. И если со строительными вещами у меня вроде как нормально получается, то с моделизмом и другим прикладным искусством не особо.Так вот давно была мечта из нарисованного в автокаде изображения, сделать вжжик — и оно вот в натуре перед тобой, можно пользоваться. Идея эта время от времени проскакивала, но во что-то конкретное оформиться никак не могла, пока…
Пока я не увидел года три-четыре назад REP-RAP. Ну что ж 3Д принтер это была очень интересная вещь, и идея собрать себе долго оформлялась, я собирал информацию о разных моделях, о плюсах и минусах разных вариантов. В один момент перейдя по одной из ссылок я попал на форум, где сидели люди и обсуждали не 3Д принтеры, а фрезерные станки с ЧПУ управлением. И отсюда, пожалуй, увлечение и начинает свой путь.
Вместо теории
В двух словах о фрезерных станках с ЧПУ (пишу своими словами намеренно, не копируя статьи, учебники и пособия).Фрезерный станок работает прямо противоположно 3Д принтеру. В принтере шаг за шагом, слой за слоем модель наращивается за счет наплавления полимеров, во фрезерном станке, с помощью фрезы из заготовки убирается «все лишнее» и получается требуемая модель.
Для работы такого станка нужен необходимый минимум.
1. База (корпус) с линейными направляющими и передающий механизм (может быть винт или ремень)
2. Шпиндель (я вижу кто-то улыбнулся, но так он называется) — собственно двигатель с цангой, в которую устанавливается рабочий инструмент — фреза.
3. Шаговые двигатели — двигатели, позволяющие производить контролируемые угловые перемещения.
4. Контроллер — плата управления, передающая напряжения на двигатели в соответствии с сигналами, полученными от управляющей программы.
5. Компьютер, с установленной управляющей программой.
6. Базовые навыки черчения, терпение, желание и хорошее настроение. ))
По пунктам:
1. База.
по конфигурации:
разделю на 2 типа, существуют более экзотические варианты, но основных 2:
С подвижным порталом:
Собственно, выбранная мной конструкция, в ней есть основа на которой закреплены направляющие по оси X. По направляющим оси Х передвигается портал, на котором размещены направляющие оси Y, и перемещающийся по нему узел оси Z.
Со статическим порталом
Такая конструкция представляет и себя корпус он же и является порталом, на котором размещены направляющие оси Y, и перемещающийся по нему узел оси Z, а ось Х уже перемещается относительно портала.
по материалу:
корпус может быть изготовлен из разных материалов, самые распространенные:
— дюраль — обладает хорошим соотношением массы, жесткости, но цена (именно для хоббийной самоделки) все-таки удручает, хотя если на станок имеются виды по серьезному зарабатыванию денег, то без вариантов.
— фанера — неплохая жесткость при достаточной толщине, небольшой вес, возможность обрабатывать чем угодно :), ну и собственно цена, лист фанеры 17 сейчас совсем недорог.
— сталь — часто применяют на станках большой площади обработки. Такой станок конечно должен быть статичным (не мобильным) и тяжелым.
— МФД, оргстекло и монолитный поликарбонат, даже ДСП — тоже видел такие варианты.
Как видите — сама конструкция станка весьма схожа и с 3д принтером и с лазерными граверами.
Я намеренно не пишу про конструкции 4, 5 и 6 -осевых фрезерных станков, т.к. на повестке дня стоит самодельный хоббийный станок.
2. Шпиндель.
Собственно, шпиндели бывают с воздушным и водяным охлаждением.
С воздушным охлаждением в итоге стоят дешевле, т.к. для них не надо городить дополнительный водяной контур, работают чуть громче нежели водяные. Охлаждение обеспечивается установленной на тыльной стороне крыльчаткой, которая на высоких оборотах создает ощутимый поток воздуха, охлаждающий корпус двигателя. Чем мощнее двигатель, тем серьезнее охлаждение и тем больше воздушный поток, который вполне может раздувать во все стороны
пыль (стружку, опилки) обрабатываемого изделия.
С водяным охлаждением. Такой шпиндель работает почти беззвучно, но в итоге все-равно разницу между ними в процессе работу не услышать, поскольку звук обрабатываемого материала фрезой перекроет. Сквозняка от крыльчатки, в данном случае конечно нет, зато есть дополнительный гидравлический контур. В таком контуре должны быть и трубопроводы, и помпа прокачивающая жидкость, а также место охлаждения (радиатор с обдувом). В этот контур обычно заливают не воду, а либо ТОСОЛ, либо Этиленгликоль.
Также шпиндели есть различных мощностей, и если маломощные можно подключить напрямую к плате управления, то двигатели мощностью от 1кВт уже необходимо подключать через блок управления, но это уже не про нас. ))
Да, еще частенько в самодельных станках устанавливают прямые шлифмашины, либо фрезеры со съемной базой. Такое решение может быть оправдано, особенно при выполнении работ недолгой продолжительности.
В моем случае был выбран шпиндель с воздушным охлаждением мощностью 300Вт.
3. Шаговые двигатели.
Наибольшее распространение получили двигатели 3 типоразмеров
NEMA17, NEMA23, NEMA 32
отличаются они размерами, мощностью и рабочим моментом
NEMA17 обычно применяются в 3д принтерах, для фрезерного станка они маловаты, т.к. приходится таскать тяжелый портал, к которому дополнительно прикладывается боковая нагрузка при обработке.
NEMA32 для такой поделки излишни, к тому же пришлось бы брать другую плату управления.
мой выбор пал на NEMA23 с максимальной мощностью для этой платы — 3А.
Также люди используют шаговики от принтеров, но т.к. у меня и их не было и все равно приходилось покупать выбрал всё в комплекте.
4. Контроллер
Плата управления, получающая сигналы от компьютера и передающая напряжение на шаговые двигатели, перемещающие оси станка.
5. Компьютер
Нужен комп отдельный (возможно весьма старый) и причин тому, пожалуй, две:
1. Вряд ли Вы решитесь располагать фрезерный станок рядом с тем местом, где привыкли читать интернетики, играть в игрушки, вести бухгалтерию и т.д. Просто потому, что фрезерный станок — это громко и пыльно. Обычно станок либо в мастерской, либо в гараже (лучше отапливаемом). У меня станок стоит в гараже, зимой преимущественно простаивает, т.к. нет отопления.
2. По экономическим соображениям обычно применяются компьютеры уже не актуальные для домашней жизни — сильно б/у 🙂
Требования к машине по большому счету ни о чем:
— от Pentium 4
— наличие дискретной видеокарты
— RAM от 512MB
— наличие разъема LPT (по поводу USB не скажу, за имением драйвера, работающего по LPT, новинки пока не изучал)
такой компьютер либо достается из кладовки, либо как в моем случае покупается за бесценок.
В силу малой мощности машины стараемся не ставить дополнительный софт, т.е. только ось и управляющая программа.
дальше два варианта:
— ставим windows XP (комп то слабенький, помним да?) и управляющую программу MATCh4 (есть другие, но это самая популярная)
— ставим никсы и Linux CNC (говорят, что тоже очень неплохо все, но я никсы не осилил)
Добавлю, пожалуй, чтоб не обидеть излишне обеспеченных людей, что вполне можно поставить и не пенёк четвертый, а и какой-нибудь ай7 — пожалуйста, если это Вам нравится и можете себе это позволить.
6. Базовые навыки черчения, терпение, желание и хорошее настроение.
Тут в двух словах.
Для работы станка нужна управляющая программа (по сути текстовый файл содержащий координаты перемещений, скорость перемещений и ускорения), которая в свою очередь готовится в CAM приложении — обычно это ArtCam, в этом приложении готовиться сама модель, задаются ее размеры, выбирается режущий инструмент.
Я обычно поступаю несколько более долгим путем, делаю чертеж, а AutoCad потом, сохранив его *.dxf подгружаю в ArtCam и уже там готовлю УП.
Далее начинаем курить форумы и собирать информацию, приведу пару полезных ссылок:
www.cncmasterkit.ru/viewtopic.php?f=18&t=2730
forumcnc.ru/forumdisplay.php?2-%CE%E1%F9%E8%E5-%E2%EE%EF%F0%EE%F1%FB
www.cnczone.ru/forums/index.php?s=9d56244c6c291357dcdde8a4f369a711&showforum=2
Ну и приступаем к процессу создания своего.
Перед проектированием станка принимаем за отправные точки несколько моментов:
— Валы осей будут сделаны из шпильки строительной с резьбой М10. Конечно, бесспорно существуют более технологичные варианты: вал с трапециевидной резьбой, шарико-винтовая передача(ШВП), но необходимо понимать, что цена вопроса оставляет желать лучшего, а для хоббийного станка цена получается вообще космос. Тем не менее со временем я собираюсь провести апгрейд и заменить шпильку на трапецию.
— Материал корпуса станка – фанера 16мм. Почему фанера? Доступно, дешево, сердито. Вариантов на самом деле много, кто-то делает из дюрали, кто-то из оргстекла. Мне проще из фанеры.
Делаем 3Д модель:
Развертку:
Далее я поступил так, снимка не осталось, но думаю понятно будет. Распечатал развертку на прозрачных листах, вырезал их и наклеил на лист фанеры.
Выпилил части и просверлил отверстия. Из инструментов — электролобзик и шуруповерт.
Есть еще одна маленькая хитрость, которая облегчит жизнь в будущем: все парные детали перед сверлением отверстий сжать струбциной и сверлить насквозь, таким образом Вы получите отверстия, одинаково расположенные на каждой части. Даже если при сверлении получится небольшое отклонение, то внутренние части соединенных деталей будут совпадать, а отверстие можно немного рассверлить.
Параллельно делаем спецификацию и начинаем все заказывать.
что получилось у меня:
1. Набор, указанный в данном обзоре, включает в себя: плата управления шаговыми двигателями (драйвер), шаговые двигатели NEMA23 – 3 шт., блок питания 12V, шнур LPTи кулер.
aliexpress.com/item/3Axis-kit-3PCS-NEMA23-CNC-stepper-motor-81mm-308-oz-in-3A-3-axis-High-speed/719006867.html
2. Шпиндель (это самый простой, но тем не менее работу свою выполняет), крепеж и блок питания 12V.
aliexpress.com/item/DC-12-48-CNC-300W-Spindle-Motor-Mount-Bracket-24V-36V-For-Engraving-Carving/679287021.html
3. Б/у компьютер Pentium 4, самое главное на материнке есть LPT и дискретная видеокарта + ЭЛТ монитор. Взял на Авито за 1000р.
4. Вал стальной: ф20мм – L=500мм – 2шт., ф16мм – L=500мм – 2шт., ф12мм – L=300мм – 2шт.
Брал тут, на тот момент в Питере брать получалось дороже. Пришло в течении 2 недель.
duxe.ru/index.php?cPath=37_67_68
5. Подшипники линейные: ф20 – 4шт., ф16 – 4шт., ф12 – 4 шт.
20
aliexpress.com/item/4pcs-SC20UU-Linear-Ball-Bearing-XYZ-Table-CNC-Router/1214529466.html
16
aliexpress.com/item/AE-4pcs-SC16UU-Linear-Ball-Bearing-XYZ-Table-CNC-Router/1214431787.html
12
aliexpress.com/item/4pcs-SC12UU-Linear-Ball-Bearing-XYZ-Table-CNC-Router/1297700376.html
6. Крепления для валов: ф20 – 4шт., ф16 – 4шт., ф12 — 2шт.
20
aliexpress.com/item/4pcs-SHF20-20mm-Linear-Rail-Shaft-Support-XYZ-Table-CNC/1221841376.html
16
aliexpress.com/item/4pcs-SHF16-16mm-Linear-Rail-Shaft-Support-XYZ-Table-CNC/1221839349.html
12
aliexpress.com/item/4pcs-SHF12-12mm-Linear-Rail-Shaft-Support-XYZ-Table-CNC/1221612308.html
7. Гайки капролоновые с резьбой М10 – 3шт.
Брал вместе с валами на duxe.ru
8. Подшипники вращения, закрытые – 6шт.
Там же, но у китайцев их тоже полно
9. Провод ПВС 4х2,5
это оффлайн
10. Винтики, шпунтики, гаечки, хомутики – кучка.
Это тоже в оффлайне, в метизах.
11. Так же был куплен набор фрез
aliexpress.com/item/10pcs-3-175-1-5-8mm-PCB-Carbide-Cutting-Tools-PCB-End-Milling-Tools-In-Mini/922596359.html
Итак, заказываем, ждем, выпиливаем и собираем.
Изначально драйвер и блок питания для него установил в корпус с компом вместе.
Позже было принято решение разместить драйвер в отдельном корпусе, он как раз появился.
Ну и старенький монитор как-то сам поменялся на более современный.
как я говорил вначале, никак не думал, что буду писать обзор, поэтому прилагаю фотографии узлов, и постараюсь дать пояснения по процессу сборки.
Сначала собираем три оси без винтов, для того чтобы максимально точно выставить валы.
Берем переднюю и заднюю стенки корпуса, крепим фланцы для валов. Нанизываем на оси Х по 2 линейных подшипника и вставляем их во фланцы.
Крепим дно портала к линейным подшипникам, пытаемся покатать основание портала туда-сюда. Убеждаемся в кривизне своих рук, все разбираем и немного рассверливаем отверстия.
Таким образом мы получаем некоторую свободу перемещения валов. Теперь наживляем фланцы, вставляем валы в них и перемещаем основание портала вперед-назад добиваемся плавного скольжения. Затягиваем фланцы.
На этом этапе необходимо проверить горизонтальность валов, а также их соосность по оси Z (короче, чтобы расстояние от сборочного стола до валов была одинаковой) чтобы потом не завалить будущую рабочую плоскость.
С осью Х разобрались.
Крепим стойки портала к основанию, я для этого использовал мебельные бочонки.
Крепим фланцы для оси Y к стойкам, на этот раз снаружи:
Вставляем валы с линейными подшипниками.
Крепим заднюю стенку оси Z.
Повторяем процесс настройки параллельности валов и закрепляем фланцы.
Повторяем аналогично процесс с осью Z.
Получаем достаточно забавную конструкцию, которую можно перемещать одной рукой по трем координатам.
Важный момент: все оси должны двигаться легко, т.е. немного наклонив конструкцию портал должен сам свободно, без всяких скрипов и сопротивления переместиться.
Далее крепим ходовые винты.
Отрезаем строительную шпильку М10 необходимой длины, накручиваем капролоновую гайку примерно на середину, и по 2 гайки М10 с каждой стороны. Удобно для этого, немного накрутив гайки, зажать шпильку в шуруповерт и удерживая гайки накрутить.
Вставляем в гнезда подшипники и просовываем в них изнутри шпильки. После этого фиксируем шпильки к подшипнику гайками с каждой стороны и контрим вторыми чтобы не разболталось.
Крепим капролоновую гайку к основанию оси.
Зажимаем конец шпильки в шуруповерт и пробуем переместить ось от начала до конца и вернуть.
Здесь нас поджидает еще пара радостей:
1. Расстояние от оси гайки до основания в центре (а скорее всего в момент сборки основание будет посередине) может не совпасть с расстоянием в крайних положениях, т.к. валы под весом конструкции могут прогибаться. Мне пришлось по оси Х подкладывать картонку.
2. Ход вала может быть очень тугим. Если Вы исключили все перекосы, то может сыграть роль натяжение, тут необходимо поймать момент натяга фиксации гайками к установленному подшипнику.
Разобравшись с проблемами и получив свободное вращение от начала до конца переходим к установке остальных винтов.
Присоединяем к винтам шаговые двигатели:
Вообще при применении специальных винтов, будь то трапеция или ШВП на них делается обработка концов и тогда подключение к двигателю очень удобно делается специальной муфтой.
Но мы имеем строительную шпильку и пришлось подумать, как крепить. В этот момент мне попался в руки отрез газовой трубы, ее и применил. На шпильку она прямо «накручивается» на двигатель заходит в притирку, затянул хомутами — держит весьма неплохо.
Для закрепления двигателей взял алюминиевую трубку, нарезал. Регулировал шайбами.
Для подключения двигателей взял вот такие коннекторы:Извините, не помню как называются, надеюсь кто-нибудь в комментариях подскажет.
Разъем GX16-4 (спасибо Jager). Просил коллегу купить в магазине электроники, он просто рядом живет, а мне получалось очень неудобно добираться. Очень ими доволен: надежно держат, рассчитаны на бОльший ток, всегда можно отсоединить.
Ставим рабочее поле, он же жертвенный стол.
Присоединяем все двигатели к управляющей плате из обзора, подключаем ее к 12В БП, коннектим к компьютеру кабелем LPT.
Устанавливаем на ПК MACh4, производим настройки и пробуем!
Про настройку отдельно, пожалуй, писать не буду. Это можно еще пару страниц накатать.
У меня целая радость, сохранился ролик первого запуска станка:
Да, когда в этом видео производилось перемещение по оси Х был жуткий дребезг, я к сожалению, не помню уже точно, но в итоге нашел то ли шайбу болтающуюся, то ли еще что-то, в общем это было решено без проблем.
Далее необходимо поставить шпиндель, при этом обеспечив его перпендикулярность (одновременно по Х и по Y) рабочей плоскости. Суть процедуры такая, к шпинделю изолентой крепим карандаш, таким образом получается отступ от оси. При плавном опускании карандаша он начинает рисовать окружность на доске. Если шпиндель завален, то получается не круг, а дуга. Соответственно необходимо выравниванием добиться рисования круга. Сохранилась фотка от процесса, карандаш не в фокусе, да и ракурс не тот, но думаю суть понятна:
Находим готовую модель (в моем случае герб РФ) подготавливаем УП, скармливаем ее MACHу и вперед!
Работа станка:
фото в процессе:
Ну и естественно проходим посвящение ))
Ситуация как забавная, так и в целом понятная. Мы мечтаем построить станок и сразу выпилить что-то суперкрутое, а в итоге понимаем, что на это время уйдет просто уйма времени.
В двух словах:
При 2Д обработке (просто выпиливании) задается контур, который за несколько проходов вырезается.
При 3Д обработке (тут можно погрузиться в холивар, некоторые утверждают, что это не 3Д а 2.5Д, т.к. заготовка обрабатывается только сверху) задается сложная поверхность. И чем выше точность необходимого результата, тем тоньше применяется фреза, тем больше проходов этой фрезы необходимо.
Для ускорения процесса применяют черновую обработку. Т.е. сначала производится выборка основного объема крупной фрезой, потом запускается чистовая обработка тонкой фрезой.
Далее, пробуем, настраиваем экспериментируем т.д. Правило 10000 часов работает и здесь 😉
Пожалуй, я не буду больше утомлять рассказом о постройке, настройке и др. Пора показать результаты использования станка — изделия.
Как видите в основном это выпиленные контуры или 2Д обработка. На обработку объемных фигур уходит много времени, станок стоит в гараже, и я туда заезжаю ненадолго.
Тут мне справедливо заметят — а на… строить такую бандуру, если можно выпилить фигуру U-образным лобзиком или электролобзиком?
Можно, но это не наш метод. Как помните в начале текста я писал, что именно идея сделать чертеж на компьютере и превратить этот чертеж в изделие и послужили толчком к созданию данного зверя.
Написание обзора меня наконец подтолкнуло произвести апгрейд станка. Т.е. апгрейд был запланирован ранее, но «руки все не доходили». Последним изменением до этого была организация домика для станка:
Таким образом в гараже при работе станка стало намного тише и намного меньше пыли летает.
Последним же апгрейдом стала установка нового шпинделя, точнее теперь у меня есть две сменные базы:
1. С китайским шпинделем 300Вт для мелкой работы:
2. С отечественным, но от того не менее китайским фрезером «Энкор»…
С новым фрезером появились новые возможности.
Быстрее обработка, больше пыли.
Вот результат использования полукруглой пазовой фрезы:
Ну и специально для MYSKU
Простая прямая пазовая фреза:
Видео процесса:
На этом я буду сворачиваться, но по правилам надо бы подвести итоги.
Минусы:
— Дорого.
— Долго.
— Время от времени приходится решать новые проблемы (отключили свет, наводки, раскрутилось что-то и др.)
Плюсы:
— Сам процесс создания. Только это уже оправдывает создание станка. Поиск решений возникающих проблем и реализация, и является тем, ради чего вместо сидения на попе ровно ты встаешь и идешь делать что-либо.
— Радость в момент дарения подарков, сделанных своими руками. Тут нужно добавить, что станок не делает всю работу сам 🙂 помимо фрезерования необходимо это все еще обработать, пошкурить покрасить и др.
Большое Вам спасибо, если Вы еще читаете. Надеюсь, что мой пост пусть хоть и не подобьет Вас к созданию такого (или другого) станка, но сколько-то расширит кругозор и даст пищу к размышлениям. Также спасибо хочу сказать тем, кто меня уговорил написать сей опус, без него у меня и апгрейда не произошло видимо, так что все в плюсе.
Приношу извинения за неточности в формулировках и всякие лирические отступления. Многое пришлось сократить, иначе текст бы получился просто необъятный. Уточнения и дополнения естественно возможны, пишите в комментариях — постараюсь всем ответить.
Удачи Вам в Ваших начинаниях!
Update:
Обещанные ссылки на файлы:
yadi.sk/d/B5auVp9lt239P — чертеж станка,
yadi.sk/d/TNRUyj55t23JT — развертка,
формат — dxf. Это значит, что Вы сможете открыть файл любым векторным редактором.
3Д модель детализирована процентов на 85-90, многие вещи делал, либо в момент подготовки развертки, либо по месту. Прошу «понять и простить». )
Переделка 3D-принтера в станок ЧПУ
Если у вас в кладовке завалялся старый 3D-принтер, не спешите его выбрасывать, из него может получится неплохой станок ЧПУ.
Именно так и поступил мастер-самодельщик. У него был 3D-принтер, который он собрал несколько лет назад и который давно не использовался. Пришло время поработать станку в другом качестве.
Основная деталь, которая нужна при модернизации, это шпиндель, блок питания с контроллером позволяющие вращать шпиндель в диапазоне 1-3000 об / мин.
В комплекте к шпинделю идет алюминиевый кронштейн. По этой ссылке можно приобрести все комплектом за цену чуть больше 5 т.р. А если ввести промо-код BGMotor003, то цена будет еще на 15% дешевле.
Перед работой мастер протестировал 3D-принтер. Несмотря на то, что он несколько лет не использовался все работало.
Стеклянный стол для печати отлично подходит для удержания 3D-отпечатков, но если на него упадет металлическая фреза… Мастер убирает его и устанавливает стол из фанеры. Также были демонтированы нагревательные кабели, датчики температуру, экструдер.
Для первого тестирования шпиндель мастер прикрутил его скотчем к монтажной пластине. В дальнейшем он будет закреплен винтами.
Код, под названием GrblforRAMPS от Per Ivar Nerseth, мастер загрузил с Github. Из кода были удалены все команды, связанные с экструдером, датчиками температуры.
Мастер использовал программу Repetier для управления аппаратом. Она раньше использовалась на этом принтере.
Для первого реза он установил 3-миллиметровую концевую фрезу. На рабочем столе, двусторонним скотчем, закрепил доску. Первое тестирование показало, что все работает, но не совсем корректно и нужно внести некоторые изменения в конструкцию.
3D-принтер управлялся платами RAMP и Arduino. Мастер заменил и на специальную плату для станков ЧПУ.
Затем мастер сделал крепление для шпинделя.
После окончательной сборки были проведены тесты на различных материалах. В ходе работы мастер использовал программу Inventables Easel вместо Estlcam. Программа бесплатная и простая в использовании.
А для управления станком он пользуется программой openbuilds, которая позволяет управлять, даже со смартфона.
Источник (Source) Становитесь автором сайта, публикуйте собственные статьи, описания самоделок с оплатой за текст. Подробнее здесь.
Фрезерный станок с ЧПУ своими руками: чертежи, видео, фото
Зная о том, что фрезерный станок с ЧПУ является сложным техническим и электронным устройством, многие умельцы думают, что его просто невозможно изготовить своими руками. Однако такое мнение ошибочно: самостоятельно сделать подобное оборудование можно, но для этого нужно иметь не только его подробный чертеж, но и набор необходимых инструментов и соответствующих комплектующих.
Обработка дюралевой заготовки на самодельном настольном фрезерном станке
Решившись на изготовление самодельного фрезерного станка с ЧПУ, имейте в виду, что на это может уйти значительное количество времени. Кроме того, потребуются определенные финансовые затраты. Однако не побоявшись таких трудностей и правильно подойдя к решению всех вопросов, можно стать обладателем доступного по стоимости, эффективного и производительного оборудования, позволяющего выполнять обработку заготовок из различных материалов с высокой степенью точности.
Чтобы сделать фрезерный станок, оснащенный системой ЧПУ, можно воспользоваться двумя вариантами: купить готовый набор, из специально подобранных элементов которого и собирается такое оборудование, либо найти все комплектующие и своими руками собрать устройство, полностью удовлетворяющее всем вашим требованиям.
Инструкция по сборке самодельного фрезерного станка с ЧПУ
Ниже на фото можно увидеть сделанный собственными руками фрезерный станок с ЧПУ, к которому прилагается подробная инструкция по изготовлению и сборке с указанием используемых материалов и комплектующих, точными «выкройками» деталей станка и приблизительными затратами. Единственный минус — инструкция на английском языке, но разобраться в подробных чертежах вполне можно и без знания языка.
Скачать бесплатно инструкцию по изготовлению станка: Самодельный фрезерный станок с ЧПУ
Фрезерный станок с ЧПУ собран и готов к работе. Ниже несколько иллюстраций из инструкции по сборке данного станка
Подготовительные работы
Если вы решили, что будете конструировать станок с ЧПУ своими руками, не используя готового набора, то первое, что вам необходимо будет сделать, — это остановить свой выбор на принципиальной схеме, по которой будет работать такое мини-оборудование.
Схема фрезерного станка с ЧПУ
За основу фрезерного оборудования с ЧПУ можно взять старый сверлильный станок, в котором рабочая головка со сверлом заменяется на фрезерную. Самое сложное, что придется конструировать в таком оборудовании, — это механизм, обеспечивающий передвижение инструмента в трех независимых плоскостях. Этот механизм можно собрать на основе кареток от неработающего принтера, он обеспечит перемещение инструмента в двух плоскостях.
К устройству, собранному по такой принципиальной схеме, легко подключить программное управление. Однако его основной недостаток заключается в том, что обрабатывать на таком станке с ЧПУ можно будет только заготовки из пластика, древесины и тонкого листового металла. Объясняется это тем, что каретки от старого принтера, которые будут обеспечивать перемещение режущего инструмента, не обладают достаточной степенью жесткости.
Облегченный вариант фрезерного станка с ЧПУ для работы с мягкими материалами
Чтобы ваш самодельный станок с ЧПУ был способен выполнять полноценные фрезерные операции с заготовками из различных материалов, за перемещение рабочего инструмента должен отвечать достаточно мощный шаговый двигатель. Совершенно не обязательно искать двигатель именно шагового типа, его можно изготовить из обычного электромотора, подвергнув последний небольшой доработке.
Применение шагового двигателя в вашем фрезерном станке даст возможность избежать использования винтовой передачи, а функциональные возможности и характеристики самодельного оборудования от этого не станут хуже. Если же вы все-таки решите использовать для своего мини-станка каретки от принтера, то желательно подобрать их от более крупногабаритной модели печатного устройства. Для передачи усилия на вал фрезерного оборудования лучше применять не обычные, а зубчатые ремни, которые не будут проскальзывать на шкивах.
Узел ременной передачи
Одним из наиболее важных узлов любого подобного станка является механизм фрезера. Именно его изготовлению необходимо уделить особое внимание. Чтобы правильно сделать такой механизм, вам потребуются подробные чертежи, которым необходимо будет строго следовать.
Чертежи фрезерного станка с ЧПУ
Чертеж №1 (вид сбоку)
Чертеж №2 (вид сзади)
Чертеж №3 (вид сверху)
Приступаем к сборке оборудования
Основой самодельного фрезерного оборудования с ЧПУ может стать балка прямоугольного сечения, которую надо надежно зафиксировать на направляющих.
Несущая конструкция станка должна обладать высокой жесткостью, при ее монтаже лучше не использовать сварных соединений, а соединять все элементы нужно только при помощи винтов.
Узел скрепления деталей рамы станка посредством болтового соединения
Объясняется это требование тем, что сварные швы очень плохо переносят вибрационные нагрузки, которым в обязательном порядке будет подвергаться несущая конструкция оборудования. Такие нагрузки в итоге приведут к тому, что рама станка начнет разрушаться со временем, и в ней произойдут изменения в геометрических размерах, что скажется на точности настройки оборудования и его работоспособности.
Сварные швы при монтаже рамы самодельного фрезерного станка часто провоцируют развитие люфта в его узлах, а также прогиб направляющих, образующийся при серьезных нагрузках.
Установка вертикальных стоек
Во фрезерном станке, который вы будете собирать своими руками, должен быть предусмотрен механизм, обеспечивающий перемещение рабочего инструмента в вертикальном направлении. Лучше всего использовать для этого винтовую передачу, вращение на которую будет передаваться при помощи зубчатого ремня.
Важная деталь фрезерного станка – его вертикальная ось, которую для самодельного устройства можно изготовить из алюминиевой плиты. Очень важно, чтобы размеры этой оси были точно подогнаны под габариты собираемого устройства. Если в вашем распоряжении есть муфельная печь, то изготовить вертикальную ось станка можно своими руками, отлив ее из алюминия по размерам, указанным в готовом чертеже.
Узел верхней каретки, размещенный на поперечных направляющих
После того как все комплектующие вашего самодельного фрезерного станка подготовлены, можно приступать к его сборке. Начинается данный процесс с монтажа двух шаговых электродвигателей, которые крепятся на корпус оборудования за его вертикальной осью. Один из таких электродвигателей будет отвечать за перемещение фрезерной головки в горизонтальной плоскости, а второй — за перемещение головки, соответственно, в вертикальной. После этого монтируются остальные узлы и агрегаты самодельного оборудования.
Финальная стадия сборки станка
Вращение на все узлы самодельного оборудования с ЧПУ должно передаваться только посредством ременных передач. Прежде чем подключать к собранному станку систему программного управления, следует проверить его работоспособность в ручном режиме и сразу устранить все выявленные недостатки в его работе.
Посмотреть процесс сборки фрезерного станка своими руками можно на видео, которое несложно найти в интернете.
Шаговые двигатели
В конструкции любого фрезерного станка, оснащенного ЧПУ, обязательно присутствуют шаговые двигатели, которые обеспечивают перемещение инструмента в трех плоскостях: 3D. При конструировании самодельного станка для этой цели можно использовать электромоторы, установленные в матричном принтере. Большинство старых моделей матричных печатных устройств оснащались электродвигателями, обладающими достаточно высокой мощностью. Кроме шаговых электродвигателей из старого принтера стоит взять прочные стальные стержни, которые также можно использовать в конструкции вашего самодельного станка.
Закрепление шагового двигателя на верхней каретке
Чтобы своими руками сделать фрезерный станок с ЧПУ, вам потребуются три шаговых двигателя. Поскольку в матричном принтере их всего два, необходимо будет найти и разобрать еще одно старое печатное устройство.
Окажется большим плюсом, если найденные вами двигатели будут иметь пять проводов управления: это позволит значительно увеличить функциональность вашего будущего мини-станка. Важно также выяснить следующие параметры найденных вами шаговых электродвигателей: на сколько градусов осуществляется поворот за один шаг, каково напряжение питания, а также значение сопротивления обмотки.
Для подключения каждого шагового двигателя понадобится отдельный контроллер
Конструкция привода самодельного фрезерного станка с ЧПУ собирается из гайки и шпильки, размеры которых следует предварительно подобрать по чертежу вашего оборудования. Для фиксации вала электродвигателя и для его присоединения к шпильке удобно использовать толстую резиновую обмотку от электрического кабеля. Такие элементы вашего станка с ЧПУ, как фиксаторы, можно изготовить в виде нейлоновой втулки, в которую вставлен винт. Для того чтобы сделать такие несложные конструктивные элементы, вам понадобятся обычный напильник и дрель.
Электронная начинка оборудования
Управлять вашим станком с ЧПУ, сделанным своими руками, будет программное обеспечение, а его необходимо правильно подобрать. Выбирая такое обеспечение (его можно написать и самостоятельно), важно обращать внимание на то, чтобы оно было работоспособным и позволяло станку реализовывать все свои функциональные возможности. Такое ПО должно содержать драйверы для контроллеров, которые будут установлены на ваш фрезерный мини-станок.
В самодельном станке с ЧПУ обязательным является порт LPT, через который электронная система управления и подключается к станку. Очень важно, чтобы такое подключение осуществлялось через установленные шаговые электродвигатели.
Схема подключения униполярных шаговых электродвигателей для 3-х координатного станка с ЧПУ (нажмите для увеличения)
Выбирая электронные комплектующие для своего станка, сделанного своими руками, важно обращать внимание на их качество, так как именно от этого будет зависеть точность технологических операций, которые на нем будут выполняться. После установки и подключения всех электронных компонентов системы ЧПУ нужно выполнить загрузку необходимого программного обеспечения и драйверов. Только после этого следуют пробный запуск станка, проверка правильности его работы под управлением загруженных программ, выявление недостатков и их оперативное устранение.
Все вышеописанные действия и перечисленные комплектующие подходят для изготовления своими руками фрезерного станка не только координатно-расточной группы, но и ряда других типов. На таком оборудовании можно выполнять обработку деталей со сложной конфигурацией, так как рабочий орган станка может перемещаться в трех плоскостях: 3d.
Ваше желание своими руками собрать такой станок, управляемый системой ЧПУ, должно быть подкреплено наличием определенных навыков и подробных чертежей. Очень желательно также посмотреть ряд тематических обучающих видео, некоторые из которых представлены в данной статье.
Оценка статьи:
Загрузка…Поделиться с друзьями:
Модульная конструкция с ЧПУвключает в себя фрезу и станок для лазерной резки
ЧПУ сборки бывают всех форм и размеров. Здесь есть дельта-манипуляторы, экспериментальные полярные установки и всевозможные декартовы конструкции, большие и маленькие. После завершения своей первой сборки с ЧПУ [jtaggard] взял то, чему они научились, и применил это при разработке нового станка.
Это декартова конструкция размером с рабочий стол, с рамой, изготовленной из экструзии с V-образным пазом, вырезанной по размеру с помощью дисковой пилы. Это отличный способ получить качественную экструзию для нестандартной сборки, он легко доступен и с ним легко работать.Портал движется на колесах, с осями X и Y с ременным приводом, плюс винтовой привод для Z. Пара NEMA 17 и NEMA 23 обеспечивают движущую силу, а Arduino Uno с шаговыми драйверами — это мозг операции. Пластины PLA толщиной 1/4 дюйма используются для сборки всего, и хотя [jtaggard] намеревался заменить их алюминием в будущем, до сих пор пластик оказался достаточно жестким для ранних испытаний как обработки, так и гравировки дерева.
Это отличная сборка с ЧПУ начального уровня, которая зарекомендовала себя как со шпинделем мощностью 500 Вт, так и со шпинделем 2.Лазер мощностью 5 Вт для гравировки. Будучи модульной по своей природе, можно легко добавить другие инструменты, такие как перьевой плоттер или лезвие для резки винила, для большей универсальности.
Сборкис ЧПУ своими руками всегда популярны, так как вы получаете полезный инструмент в качестве награды за ваш тяжелый труд. Видео после перерыва.
Сменное цековочное отверстие | Вся серия: 8 — 36 мм Максимальная длина: 70-260 мм | Подробнее | Расточка с державками для снятия фаски | Подробнее | 4 в 1 расточка | Подробнее | Дисковая фреза | Доступная толщина: 14-30 мм Доступный диаметр: 80 — 250 мм | Подробнее | Дисковая фреза | Доступная толщина: 14-30 мм Доступные диаметры: 80-250 мм | Подробнее | Точечное сверло со сменными пластинами 90 ° | Доступные диаметры: 8, 10, 12, 16 мм Применимая степень: 90 ° Применимые машины: фрезерный станок, сверлильный станок и токарный станок. | Подробнее | Центровочное сверло со сменными пластинами 60 ° | Доступные размеры: 8, 10, 12, 16 мм Применимый диаметр: 60 ° Применимая машина: фрезерный станок и токарный станок. | Подробнее | Сменяемое закругление углов | Подробнее | UFO Резьба для фрезерования | Применимый размер резьбы: M14 ~ Неограниченный Доступный тип резьбы: метрическая, дюймовая, по Витворту, трубная резьба. | Подробнее | Chamfer King Эксклюзивно для сверлильных станков | Доступные градусы: 60, 90, 120 ° Доступный диаметр: 4 — 110 мм | Подробнее | Фреза для снятия фаски для фрезерного станка | Доступные углы: 30 °, 45 ° Доступные диаметры: 10-70 мм | Подробнее | Индексируемые 8 режущих кромок Пластина ODGT | Доступные диаметры фрезы: 32 — 300 мм Доступные типы: держатель концевой фрезы с боковым замком, торцевая фреза, регулируемая фреза для алюминия. | Подробнее | Индексируемые 16 кромок Вставка ONGT | Доступный диаметр: 63 — 250 мм. Доступные типы: меньше зубов, больше зубов. | Подробнее | Фрезы для фрезерования уступов и пазов 90 ° Пластина ADMT | Доступные диаметры: 6–250 мм. Доступные типы: держатель концевой фрезы с боковым замком с соединительным хвостовиком, торцовая фреза и кукурузорезка. | Подробнее | Фреза со сменными пластинами для высоких подач Пластина XPMX / LPMT | Доступные диаметры: 8–80 мм.Доступные типы: держатель концевой фрезы с боковым замком с соединительным хвостовиком, торцевые фрезы. | Подробнее | Торцевая фреза для алюминия | Доступные диаметры: 80, 100, 125, 160, 200, 250, 300 мм | Подробнее | Фреза со сменными пластинами | Доступный диаметр: 40, 60, 80, 120 мм Доступная фаска: 50 °, 55 °, 60 ° | Подробнее | Сменное пильное полотно | Доступная толщина: 1 — 5 мм Диаметр: 50-600 мм | Подробнее | Сменное пильное полотно | Доступная толщина: 1 — 5 мм Полный диапазон серии: 50-600 мм | Подробнее | Боковая фреза | Доступная толщина: 4 — 12 мм Доступные диаметры: 50 — 250 мм | Подробнее | Боковая фреза | Доступная толщина: 4 — 12 мм Доступные диаметры: 50 — 250 мм | Подробнее | Метчик со сменной спиралью | Доступные типы: M / MF / RP / NPS / RC / NPT Применимые станки: фрезерный станок с ЧПУ, нарезной станок, радиально-сверлильный станок Доступные размеры: M10 — M64 | Подробнее | Индексируемый метчик холодной формы | Подробнее | Метчик с конической трубной резьбой | Подробнее |
Представляем iro3d — настольный металлический 3D-принтер стоимостью всего 5000 долларов
Стремительный рост социальных сетей позволил любому, у кого есть доступ в Интернет, иметь право голоса и быть услышанным.Он катапультировал бесчисленное количество людей в бесчисленных областях к славе и теперь предоставил iro3d платформу, чтобы представить себя в области аддитивного производства через Джоэла Теллинга, ботаника YouTube по 3D-печати.
iro3d — это оркестр из одного человека, работающий в Сиэтле. Этого человека зовут Сергей, и он разработал настольный металлический 3D-принтер, на котором можно изготавливать прочные изделия из высокоуглеродистой стали — также исследуются другие металлы и сплавы. Принтер стоимостью 5000 долларов поставил Сергея «между рынками» — слишком дорого для большинства потребителей / любителей / домашних хозяйств и недостаточно проверенных для большинства промышленных игроков.Он хочет продавать бета-версии своей машины клиентам в штате Вашингтон, чтобы затем расширить диапазон и разработать новые, чтобы бизнес сдвинулся с мертвой точки.
«iro3d — это в основном я, у меня есть друг и у него своя компания. Он будет продавать расходные материалы », — поясняет Сергей. «Я провел всю разработку и исследование принтера, и я разговариваю со многими друзьями, включая моего делового партнера, они дают мне отзывы, и у нас много интересных дискуссий.Но в основном это я … пока «.
Компания его друга называется TriDPrinting , и расходные материалы, которые он будет продавать, когда предприятие Сергея начнет развиваться, — это порошки и тигли, которые делают возможной 3D-печать Сергея.
В процессе iro3d для изготовления деталей используются металлические порошки, а для поддержки — песчаные порошки. Порошки укладываются в тигель, печатающие головки собирают материал из одного из четырех контейнеров (мелкий и грубый металлический и песчаный порошок) и осаждают их со скоростью, указанной в программном обеспечении для сварки.Когда деталь напечатана, ее затем обжигают в печи в течение нескольких часов при высокой температуре. По завершении этого этапа процесса проволочная щетка удаляет излишки порошка с детали.
Обновленная информация о клиентах iro3d: 4 и подробная информация о процессе выборочного нанесения порошка на машине (октябрь 2018 г.). Читать еще .
В одном из своих видеороликов на YouTube Сергей демонстрирует печатный фрезерный станок, который также имеет короткую эпизодическую роль в репортаже о 3D Printing Nerd на iro3d.На печать этой детали ушло около 24 часов, и она была запечена в течение ночи, а из-за прочности материала из углеродистой стали шлифование «потребовало времени».
Особенности процесса Сергей хранит при себе, опасаясь, что более крупные компании перехватят его. Он также говорит, что машина стоит всего 5000 долларов, потому что он разрабатывает одну только машину из расчета одной машины в месяц. Сергей считает, что эта машина проще большинства пластиковых настольных 3D-принтеров, и по мере увеличения объемов производства цена будет снижаться.
Он также признает необходимость модификаций. В прошивке необходимы изменения, текущая плата электроники представляет собой 8-битный микроконтроллер, который работает «очень медленно». Между тем, программное обеспечение, которое он написал сам, нуждается в улучшении, ему нужно повозиться с механикой принтера, и он хочет реализовать некоторые механизмы безопасности. Но с этими изменениями и некоторыми отзывами от бета-клиентов Сергей представляет, что его машина будет использоваться для изготовления разовых инструментов и прототипов.
В его процессе и получаемых продуктах есть уверенность, что он может быть жизнеспособным вариантом для промышленных пользователей. Машина может похвастаться камерой сборки 32 x 30 x 10 см, может печатать объекты, достаточно прочные, чтобы по ним можно было несколько раз ударить молотком, и является одной из самых дешевых на рынке в своем роде. И до недавнего времени об этом никто не знал. Обзор YouTube, посвященный 3D-печати Nerd, может быть только началом.
«До того, как Джоэл опубликовал свое видео, никто даже не слышал об iro3d, никто не заходил на сайт и не посещал страницы [ Facebook, и YouTube].Это было очень уединенное место », — рассказал Сергей TCT . «Сейчас похоже, что люди начинают проявлять интерес. Надеюсь, скоро появится бета-клиент, который купит принтер, будет пользоваться им и убедиться, что все в порядке.