Как собрать лазерный ЧПУ станок в домашних условиях. Какие материалы и комплектующие потребуются для сборки. Как настроить и откалибровать самодельный лазерный гравер. Какое программное обеспечение использовать для управления станком.
Что такое лазерный ЧПУ станок и как он работает
Лазерный ЧПУ станок — это устройство для резки и гравировки различных материалов с помощью лазерного луча. Основные компоненты такого станка:
- Лазерный излучатель
- Система позиционирования по осям X и Y
- Электронный блок управления
- Программное обеспечение
Принцип работы заключается в следующем: лазерный луч, управляемый программой, перемещается по заданной траектории и воздействует на материал, выжигая или разрезая его. Это позволяет создавать сложные узоры и вырезать детали с высокой точностью.
Преимущества самодельного лазерного станка
Почему стоит рассмотреть вариант сборки лазерного ЧПУ станка своими руками?
- Существенная экономия средств по сравнению с покупкой готового станка
- Возможность кастомизации под свои задачи
- Глубокое понимание принципов работы оборудования
- Возможность самостоятельного обслуживания и модернизации
- Творческий процесс и получение новых навыков
При этом самодельный станок по качеству резки и гравировки может не уступать заводским аналогам.

Необходимые материалы и комплектующие
Для сборки лазерного ЧПУ станка своими руками потребуются следующие основные компоненты:
- Лазерный модуль (мощность от 500 мВт до 15 Вт)
- Arduino Uno или другой контроллер
- CNC Shield для Arduino
- Драйверы шаговых двигателей (например, A4988)
- Шаговые двигатели Nema 17
- Направляющие и подшипники для осей X и Y
- Ремни и шкивы
- Блок питания 12В
- Фанера или оргстекло для корпуса
- Крепежные элементы
Большинство компонентов можно приобрести на AliExpress или в магазинах электроники. Некоторые детали (например, корпус) можно изготовить самостоятельно.
Пошаговая инструкция по сборке механической части
Рассмотрим основные этапы сборки механической части лазерного ЧПУ станка:
- Изготовление рамы станка из фанеры или оргстекла
- Монтаж направляющих для осей X и Y
- Установка шаговых двигателей
- Крепление ремней и шкивов
- Сборка каретки для лазерного модуля
- Установка лазерного модуля на каретку
- Монтаж концевых выключателей (опционально)
При сборке важно обеспечить жесткость конструкции и плавность хода по обеим осям. Для повышения точности рекомендуется использовать линейные подшипники.
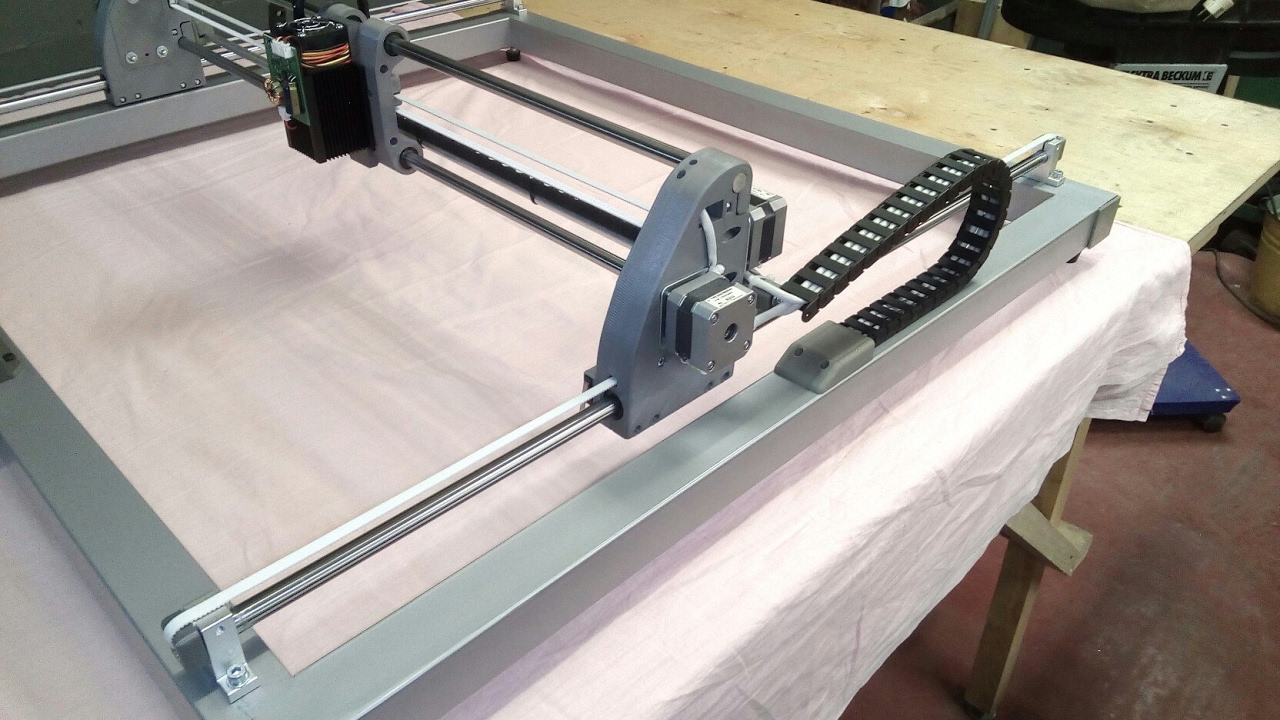
Подключение электроники и настройка управления
После сборки механической части переходим к электронике:
- Установка Arduino Uno и CNC Shield
- Подключение драйверов шаговых двигателей
- Соединение шаговых двигателей с драйверами
- Подключение лазерного модуля через TTL-контроллер
- Подключение блока питания
- Загрузка прошивки GRBL в Arduino
- Настройка параметров GRBL под конкретный станок
Схема подключения достаточно проста, но требует внимательности. Особое внимание стоит уделить правильному подключению лазерного модуля и настройке его мощности через ШИМ-выход Arduino.
Калибровка и тестирование станка
После сборки и подключения всех компонентов необходимо выполнить калибровку станка:
- Настройка шагов на миллиметр для каждой оси
- Проверка точности перемещения по обеим осям
- Настройка скорости и ускорения перемещения
- Калибровка мощности лазера
- Тестовая гравировка на разных материалах
Процесс калибровки может занять некоторое время, но он критически важен для получения качественных результатов гравировки и резки.

Программное обеспечение для управления станком
Для управления самодельным лазерным ЧПУ станком можно использовать различное ПО:
- LaserGRBL — простая бесплатная программа для Windows
- LightBurn — более продвинутое платное ПО с широкими возможностями
- T2 Laser — бесплатная программа с открытым исходным кодом
Выбор ПО зависит от ваших потребностей и опыта работы с подобными станками. Для начала рекомендуется освоить LaserGRBL, которая обладает интуитивно понятным интерфейсом.
Меры безопасности при работе с лазерным станком
При эксплуатации самодельного лазерного ЧПУ станка важно соблюдать следующие меры безопасности:
- Использовать защитные очки для работы с лазером
- Обеспечить хорошую вентиляцию рабочей зоны
- Не оставлять работающий станок без присмотра
- Избегать попадания отражённого лазерного луча в глаза
- Не допускать перегрева лазерного модуля
- Соблюдать правила электробезопасности
Помните, что даже маломощный лазер может быть опасен для зрения при прямом попадании в глаза.
как собрать самодельный ЧПУ лазер
Современные аппараты с ЧПУ позволяют автоматизировать процесс обработки деталей и обеспечивают высокое качество. Однако стоят они дорого, а потому не всякий человек может себе позволить такую «роскошь» дома. Таким мастерам поможет лазерный ЧПУ-станок своими руками, который можно сделать, ознакомившись с основными принципами конструирования и сборки на конкретном примере.
Материалы для сборки лазерного станка ЧПУ своими руками
На фото показан простой лазерный станок, изготовленный своими руками.
Для его изготовления использованы такие материалы и комплектующие:
- ДСП, МДФ или фанера для корпуса.
- Направляющие элементы – металлические стержни диаметром 10–12 мм.
- Держатели направляющих.
- Линейные и опорные подшипники, втулки скольжения разного диаметра.
- Шаговые двигатели. Их надо 3 шт. для установки по осям X, Y, Z. Вполне подходят электродвигатели от принтеров или DVD-плееров.
- Ходовые винты и гайки.
- Контроллер шаговых двигателей.
- Блок питания контроллера.
- Мягкая муфта для передачи плавного хода и обеспечения соосности шагового двигателя.
- Кабели и провода, в т. ч. USB-кабель.
- Шкивы для ременной передачи и ремни зубчатого типа.
- Концевые выключатели.
- Компьютер.
Для сборки лазерного станка необходимо приготовить головку с лазером. Он подбирается в зависимости от необходимой мощности излучения. Хорошо подходит диод от пишущего DVD-плеера (красное свечение). Можно приспособить источник из лазерной указки или светодиодного фонарика. Для фокусировки луча потребуются линзы, которые можно извлечь из тех же устройств, где находился лазер. Самое верное – купить готовый лазерный излучатель. Нельзя забывать об его охлаждении, для этого нужен охлаждающий радиатор.
Для сборки схемы контроля и управления нужна электронная плата с информационным дисплеем, транзисторы и электронные платы для управления шаговыми двигателями, диоды, резисторы и другие детали. На фото показан стандартный набор деталей для электроники.
Для изготовления станка своими руками надо заранее приготовить такой инструмент: болгарка, электродрель, паяльник, ножовка и ножовка по металлу, электролобзик, отвертка, плоскогубцы, ключи (гаечные и торцевые), напильники, шило, молоток, штангенциркуль, линейка, угольник, ножницы. Потребуются и расходные материалы: изолента, герметик, суперклей, скотч, шурупы, винты, болты, скобы, хомуты.
Как собрать лазерный станок ЧПУ своими руками: пошаговая инструкция
Самостоятельная сборка ЧПУ станка осуществляется в следующем порядке:
1. Раскрой и изготовление основания. Проще всего для него использовать фанеру толщиной 10–12 мм. Основание может быть прямоугольным или скругленным. При создании мощного станка его изготавливают из металла.
2. Закрепление на основании неподвижных боковых стенок. Они могут быть из фанеры, ДСП, дерева или металла. На стенках сверлятся отверстия для установки направляющих стержней.
3. Установка направляющих по оси Y. Предварительно на них нанизываются опоры скольжения для подвижных боковых стенок каркаса. Вариант таких опор приведен на фото.
4. Изготовление подвижных боковых стенок. Сверление в них отверстий для направляющих по оси Х и установка их на стенках.
5. Закрепление подвижных стенок на опорах.
6. Сборка рабочей головки станка. Ниже показана принципиальная схема каркаса в сборе с универсальной головкой, на которой можно крепить лазерный излучатель, шпиндель или иной рабочий орган. Его чертеж приведен на следующем фото. Конкретно для лазерного излучателя можно собрать более легкую конструкцию лазерной головки с радиатором охлаждения.
7. Монтаж электрической части. Подведение электропитания, установка концевых выключателей, кнопок пуска и аварийной остановки. Пример элегантной компоновки ячейки для размещения электрической схемы показан на фото.
8. Монтаж электроники и подключение управляющей платы, контроллера.
После проверки всех элементов можно начинать подготовку станка к работе.
Электроника для самодельного лазерного ЧПУ станка
В станках с ЧПУ важнейшую роль играет электронная начинка. Она должна обеспечить управление прибором с компьютера путем выдачи команд шаговым двигателям и руководства траекторией движения рабочего органа. Для этого необходима управляющая программа, которая обеспечит подачу нужных команд на контроллер в форме G-кодов. Обязательно устанавливается порт LPT.
Важно! Для восприятия команд и распределения их по шаговым двигателям в контроллере располагается управляющая плата. Популярностью пользуется стандартная плата KY-2012 (5 Axis CNC Breakout Board for Stepper Motor Driver с DB25 Cable). Часто станки делаются на базе Arduino.
Настройка и отладка самодельного лазерного станка
Для работы станка с ЧПУ необходимо в компьютер загрузить программное обеспечение, т. е. УП. Загрузка готовой программы осуществляется с внешнего носителя (дискеты, флешки, магнитные ленты). Она должна быть многофункциональной, но простой в использовании. Выбирают УП в зависимости от назначения станка.
Наиболее популярные программы:
- ArtCAM. Позволяет создавать сложные объемные рельефы. Можно вставить один рельеф в другой.
- LinuxCNC. Это универсальная программа для многофункционального использования. Для функционирования необходим объем памяти не менее 4 ГБ.
- Mach4. Совместима с операционной системой Windows. Имеет доступную цену и русифицированную версию.
- Mach5. Это одна из самых быстрых программ. Совместима практически с любой операционной системой.
- MeshCAM. Программа особо подходит для управления двухсторонней обработки объемных изделий.
- SimplyCam. Прекрасно справляется со сложным гравированием.
- CutViewer. Обеспечивает визуализацию процесса обработки и высокую производительность.
- CadStd. Это простая программа для создания схем и графиков, чертежей любой сложности. Выдает DXF-файлы, загружаемые в CAM-программы для генерации правильных траекторий обработки заготовок.
После выбора оптимальной УП она загружается в карте памяти, жестком диске компьютера или на твердотельном накопителе. Для подготовки станка на конкретную операцию загружается графическое изображение или чертеж детали после обработки. Графический файл нужно предварительно перевести в формат DXF, Exeilon, HPGL или Gerber. Настойку можно проконтролировать по монитору. Команды подаются в форме G- и М-кодов, понятных для платы контроллера. Траектория описывается по 3–5 координатам. Настройка и отладка программы обеспечивается строго в соответствии с инструкцией. При проведении настройки на дисплее отображается информация о том, какими клавишами надо пользоваться.
Отладка станка производится на шаблонах. Прибор настраивается на проведение стандартных операций, при этом контролируется точность обработки. После тестовых опробований станок можно запускать в рабочем режиме. На фото показаны результаты практического использования.
Лазерные станки с ЧПУ обеспечивают высокую точность обработки деталей из разных материалов. При правильном подходе самодельные аппараты способны значительно расширить возможности домашних мастеров. Важно учитывать советы специалистов при конструировании и сборке, а также соблюдать технику безопасности при эксплуатации.
- 06 сентября 2020
- 3159
Получите консультацию специалиста
необходимое оборудование, инструкция по сборке с фото
Среди материалов для презентабельного декора фанера отличается наибольшей популярностью благодаря своим эксплуатационным качествам. Кроме того, она легка в обработке. Все большую популярность приобретают фигурные изделия из фанеры, изготавливаемые при помощи станков. Такие изделия имеют объемные узоры и тончайшую обработку. Практичные умы мастеров задаются вопросом: возможно ли сделать лазерный станок своими руками или нужно потратиться на готовый? Для начала необходимо разобраться во всех тонкостях станочной резки фанеры.
Что собой представляет лазерное устройство для фигурной резки?
Технология лазерной гравировки позволяет переносить рисунки в объеме на лист фанеры. Этот способ является инновационным, однако уже заслужил популярность среди плотников и домашних мастеров.
В основе воздействия луча лежат микроразрушения древесины, сходные по интенсивности со сваркой. При воздействии высокой температуры контактный участок подвергается выгоранию.
Установка, являющаяся ключевой деталью устройства, осуществляет лучевое воздействие лазера. Для обработки используются углеводородные лазеры, следовательно, собрать станок лазерной резки своими руками без этой детали невозможно.
Плюсы использования лазерной обработки
Интерес к сборке лазерного станка для резки фанеры своими руками обусловлен высокой стоимостью фабричных моделей. Такие устройства дают дополнительные возможности в манипуляциях с изделиями, которые недоступны при механическом воздействии. Устройства на основе лазерного воздействия используются как в промышленных масштабах, так и домашними мастерами, а также мелкими предпринимателями.
Отличительная черта резки посредством лазера – ширина шва, которая может лишь немного превышать толщину лазерного луча прибора. Это позволяет наносить точный рисунок, максимально приближенный к заданному макету. Собранный своими руками лазерный станок не уступает по качеству выполняемого среза промышленным аналогам и отличается такими же технологическими процессами внутри устройства.
Среди особенностей применения технологии лазерной резки можно выделить следующие:
- Область взаимодействия с лучом неизбежно приобретает более темный оттенок.
- Использование этого способа позволяет избежать механической деформации, поскольку классические усилия применять нет необходимости.
- При выборе источника древесины для работы следует отдавать предпочтение породам с наименьшим содержанием смол.
- При обработке лазером образуется небольшое количество стружки.
- Выполняя большие объемы работ посредством станочной обработки, следует позаботиться о наличии системы вентилирования.
- На равномерность среза, получаемого в процессе резки, влияет выставленный температурный режим и скорость движения луча лазера.
- Работа лазера контролируется числовым программным управлением (ЧПУ), что позволяет полностью автоматизировать процесс обработки.
Принцип работы
Перед тем как собрать лазерный станок ЧПУ своими руками, следует разобраться с основными элементами устройства и механизмом их работы.
Типичная установка с углекислотным лазером имеет трубку, заполненную молекулами газа, в качестве основного элемента. Электрический ток, поступающий на газ-катализатор, приводит молекулы в состояние повышенной вибрации, за счет чего усиливается световой луч, проходящий через трубку. Оптические элементы, находящиеся внутри лазерной установки, усиливают поток света и выдают его многократно отраженным.
Для автономной работы станка необходим автоматизированный механизм, передвигающий лазерное устройство. Он называется устройством позиционирования, его работа координируется программным обеспечением. В момент образования отверстия в определенном месте материала лазерная каретка должна быть перемещена в другую точку, чтобы структура дерева не была разрушена.
Последовательность фигурной резки
Фигурная резка на фанерном листе включает основные этапы:
- В первую очередь создается рисунок. Это либо производится ручным нанесением на материал, либо задается электронно.
- Далее выбирается режим резки, главной характеристикой которого является мощность излучения. Интенсивность прожига, в свою очередь, напрямую зависит от толщины поверхности.
- Нанесение рисунка на материал с заданной скоростью. Как правило, высокая скорость гравировки сопровождается большим потемнением краев среза.
Возможно ли смастерить лазерный станок своими руками? Да, это реальная задача.
Чтобы собрать лазерный ЧПУ-станок своими руками, необходимо обратить внимание на скольжение направляющих; приводы в большом изобилии представлены в магазинах соответствующего профиля.
Таким образом, если использовать основные комплектующие, аналогичные таковым в заводских установках, и применять принцип равноценной замены деталей, изготовить лазерный станок для фанеры своими руками вполне реально, что подтверждает опыт изобретательных мастеров.
Комплектующие, которые понадобятся
До сборки лазерного станка своими руками необходимо позаботиться о наличии следующих важных компонентов, тандем которых позволит получить от лазерного гравировального станка, собранного своими руками, качественную работу:
- Устройство преобразователя лазера. Лазерную пушку необходимо приобрести, так как ее изготовление трудоемко и не оправдывает приложенные усилия.
- Также в установке должна присутствовать специальная каретка, от плавности движения которой будет зависеть результат работы станка. Направляющие можно изготовить из подручных средств, но они должны захватывать всю площадь обрабатываемой поверхности. Таким образом, понадобятся двигатели, которые необходимо будет подсоединить к электронной плате, реле, зубчатые ремни и подшипники.
- Электронный блок питания лазерного устройства, которое также отвечает за выполнение команд, передаваемых с пункта управления на лазер.
- Программное обеспечение, необходимое для ввода данных и требуемого рисунка или узора.
- Также необходимо обеспечить отток вредных продуктов, образующихся в процессе сгорания. Для этого оптимальной будет налаженная система локальной вентиляции.
Сопутствующие материалы для изготовления лазерного станка своими руками
При сборке понадобятся доски, стяжки, крепежные детали, отвертка, приспособления для резки металла и дерева, шлифовки, а также смазочные и охлаждающие материалы.
Для электронного управления чаще всего используют микроконтроллер Arduino R3, также понадобятся плата с дисплеем и компьютер для управления командами.
Последовательность сборки станка
Собранный своими руками самодельный лазерный станок с ЧПУ дает повод для гордости мастеру, а также позволяет основательно разобраться в процессе филигранной обработки материалов из дерева.
Основные этапы комплектации установки можно представить в виде последовательных шагов:
- Подготовка материалов.
- Сбор компонентов управления.
- Комплектация механической части.
- Настройка параметров резки.
- Старт работы станка.
Подготовка необходимых материалов и оборудования
Требуемые детали необходимо подготовить, они должны быть доступны в любой момент. Это позволит производить сборку в размеренном и слаженном темпе. Для того чтобы сделать лазерный станок своими руками, чертежи можно использовать готовые, а можно сделать самостоятельно.
Сборка электрической схемы
Система управления полагается на работу платы, которую можно приобрести уже готовую либо собрать на базе микросхемы. Среди наиболее простых для домашнего использования выделяют микросхему Arduino. На фото ниже представлена схема сборки электронной платы для лазерного ЧПУ станка, изготавливаемого своими руками.
Полная комплектация
Конструкция челноков для будущего устройства собирается при помощи стержней, которые вставляются в их борта, отвечающих за оси координат в двухмерной проекции. Направляющие стержни предварительно следует отшлифовать их при помощи наждачной бумаги или шлифмашины. Далее их нужно обработать подготовленной смазкой для более плавного движения.
В подвижном механизме в первую очередь монтируются механизмы для обеспечения движения, далее — шарикоподшипники. Завершающим этапом устанавливаются ремни. Собирая лазерный гравировальный станок своими руками, удобно использовать основу из металла, размером, дважды превышающим размер движущих механизмов. Креплениями могут служить саморезы, которые вставляются в заранее подготовленные отверстия. Металлический кронштейн устанавливается на центр станка, а по загнутым краям металлической основы устанавливается подшипниковая система. На образовавшуюся подвижную систему надевается ремень с зубьями и она крепится саморезом к деревянной основе.
Автоматизация и управление
Важным моментом действия агрегата, собранного своими руками, является синхронная работа двигателей направляющих, что достигается путем подключения управления, которое осуществляется платой, одинаковой для обоих механизмов.
Необходимые для запуска самодельного станка программы доступны в Сети. Требуемые утилиты нужно скачать на используемый для управления компьютер. Среди наиболее популярных для работы с лазерной резкой: Inkscape, Arduno IDE, Universal Gcode Sender (версия 1.0.7).
Указанные программы устанавливаются по стандартному шаблону, после чего можно приступать к заданию параметров контура будущего рисунка.
Для управления параметрами резки и гравировки, такими как мощность (то есть температура прожига) и скорость движения лазера, понадобится настройка платы Arduno IDE. В первую очередь следует загрузить код GRBL, который можно выбрать из предлагаемого программой перечня. Затем можно приступать к настройке параметров резки.
Задание рисунка для лазерной резки
Для задания требуемого узора или картинки можно воспользоваться оцифрованным рисунком от руки либо создать рисунок в графической программе. В ажурных узорах важно следить за тем, чтобы все элементы были связаны и основная конструкция оставалась целостной.
Скорость и степень нагрева лазерной головки можно определить, немного попрактиковавшись. Немаловажную роль играет толщина и характер используемого для обработки материала. Тонкие листы дерева требуют более аккуратного и медленного воздействия.
При загрузке изображения следует учитывать требования программы, в которой для работы используется векторный формат. Изменить параметры рисунка можно в графических редакторах Adobe Illustrator и Inkscape.
Также следует учесть, что при наличии закрашенных мест на рисунке контур этих деталей заполнен не будет.
Настройка и резка
При настройке параметров резки нужно проверить соответствие значений координат осей X и Y в программе аналогичным характеристикам векторного изображения. Далее следует задать скорость работы станка и направить лазерную головку под углом, требуемым для получения необходимой объемности рисунка на дереве.
Последнее требуемое действие – запустить резку и наслаждаться работой лазерного станка, сделанного своими руками.
Техника безопасности при резке и гравировке
Во время работы с устройством лазерной резки нужно придерживаться правил техники безопасности. Критическим моментом является потенциальная угроза, исходящая от работающего лазера. Соприкосновение лазерного луча с кожными покровами вызывает ожоги даже при непродолжительном воздействии. Кроме того, следует обезопасить глаза при работе с данным видом устройства, поскольку попадание излучения на сетчатку может спровоцировать необратимую слепоту.
В наше время любая идея изобретательного мастера по работе с деревом может быть воплощена с помощью современных технологий обработки, благодаря чему можно получить произведения искусства из грубого материала. Если есть стремление сэкономить средства на оборудовании, небольшие усилия позволят собрать лазерный станок своими руками, и он будет долго служить своему хозяину, радуя ажурными и качественными изделиями из дерева.
Внедрение технологии лазерной резки в условиях собственной мастерской позволяет не только производить изделия для собственного пользования, но и использовать ее как средство заработка.
Самодельный Лазерный гравёр с ЧПУ, в домашних условиях.
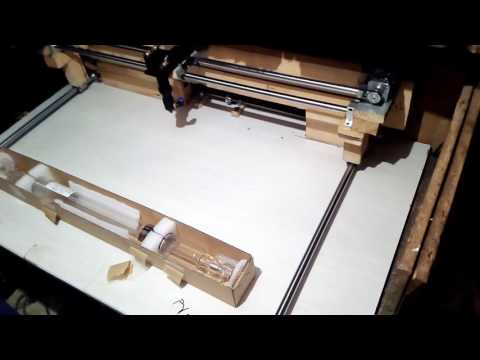
Кроме созданий проектов на Arduino, ещё я увлекаюсь созданием самодельных станков с ЧПУ. На счету у меня собрано больше 5 штук самодельных ЧПУ станков с различной кинематикой перемещения и разнообразного назначения. Сегодня пойдет речь о самодельном лазерном гравере, который я собрал в домашних условиях, а точнее в квартире. При этом использовал подручные материалы, которые лежат без дела, или которые можно не задорого купить в ближайшем магазине. С чего все началось, и для чего я собрал лазерный гравировальный станок из хлама, сейчас расскажу.
Зачем собирать самодельный ЧПУ станок из хлама?
Один знакомый сказал, что ЧПУ станки это сложно и для того, чтобы собрать работающий станок нужно очень много знать и уметь. Я ответил, что я собираю ЧПУ станки из подручных материалов, и многие работают у меня больше 2 лет верой и правдой. Показал, что я на них делаю, и где можно почитать описание моих проектов.
Спустя некоторое время этот знакомый мне говорит, что он рассказал друзьям, и они не верят, что можно собрать ЧПУ станок в домашних условиях. Да даже не то, чтобы он работал, как из магазина, а хотя бы выполнял какую-нибудь работу. И тут он меня спрашивает: «Ты можешь собрать станок не из старых принтеров, мебельных направляющих, а из материалов, которые я бы купил сам, и повторил бы станок?» Я сказал, что это вполне возможно, и приступил к реализации мини станка с ЧПУ. Скорее всего, это не последний мини ЧПУ станок в домашних условиях. В ближайшее время сделаю еще пару вариантов.
Механическая часть самодельного лазерного гравера.
Недавно делал узел из карандашей (каретку для ЧПУ), и на основе данной каретки решил собрать лазерный гравер с ЧПУ. Но нужно, как минимум, 2 оси, поэтому собрал второй узел, но немного уже. Вот так выглядят узлы оси X и Y для самодельного лазерного гравера.
Как собирал каретку, можете почитать в предыдущей статье. Про нее могу сказать одно: сделана она из карандашей, строительной шпильки и фанеры.
Закрепил с помощью реек и фанеры узлы осей Y и X. Вот такой каркас станка получился. Пора приступить к электронной составляющей самодельного ЧПУ гравировального станка
Электроника самодельного лазерного гравера.
Доставать лазер из старого DVD привода не стал, так как меня просили сделать ЧПУ станок, который можно повторить, и все узлы можно было бы купить, например, на AliExpress. Поэтому буду использовать лазерный модуль с TTL контролером от моего лазерного гравера. Обзор гравера можно посмотреть тут.
Лазерный модуль можно использовать в такой самоделке и подешевле, например, на 500 mw.
Так как я увлекаюсь еще и Arduin, то мозгом станка будет Arduino UNO и CNC shield v3. Драйвера буду использовать самые дешёвые A4988. Описание драйверов A4988 читайте в этой статье:
- Драйвер шагового двигателя A4988.
Описание CNC shield v3 читайте в статье:
- Плата для ЧПУ на Arduino UNO, CNC shield v3 и драйвера A4988 (DRV8825).
Для того, чтобы закрепить электронику, сделал заготовку из фанеры, которая будет крепиться с задней стороны гравера.
После чего, закрепил электронику и установил на место, где будет все стоять.
Пришло время все подключить и запрограммировать.
Схема подключения cnc shield v3.0 + arduino uno + TTl и лазер.
Подключаем все компоненты по схеме.
Правда, у меня не установлены концевые выключатели. Схему взял из интернета, самому рисовать стало лень. Но когда буду писать обзорную статью про подключение электроники, обязательно все нарисую.
Как видим, схема достаточно простая, и запутаться тут сложно. Нам нужно к шилду подключить 2 шаговых двигателя. Один подключаем в разъем, где написано X, второй в разъем с надписью Y. Соответственно, один двигатель перемещает по оси X, второй по оси Y.
C подключением лазера будьте внимательны, в зависимости от версии прошивки, подключение TTL к Arduino может быть разным.
Внимание!!! С прошивки GBRL 9.0i были поменяны местами Z-Max (D12) и Spn_EN (D11).
TTL модуль подключаем к D11, который является ШИМ портом, — это необходимо для управления мощностью лазера, с помощью ШИМ.
Теперь, если вы желаете подключить концевик Z_Max, то его необходимо подключить в Spn_EN, а включение лазера необходимо подключать в Z+. Вот такая путаница с распиновкой на шилде.
После подключения уложил провода, чтобы ничего не торчало и не мешало работе станка.
Прошивка для лазерного гравёра на Arduino.
Для того, чтобы гравер заработал, в Arduino нужно загрузить код. Где же его взять? Код писать самостоятельно не нужно. Добрые люди уже написали и проверили работу прошивки на тысячах, а может и на сотнях тысяч различных станках с ЧПУ. Скачать прошивку GRBL 1.1 можно с репозитория, или внизу статьи, в разделе Материалы для скачивания.
Более подробно о прошивке и настройке GRBL 1.1 буду рассказывать в следующей статье.
Настройка и калибровка самодельного станка с ЧПУ.
После того, как мы загрузили прошивку, все настройки будут стандартные, и их нужно поменять под ваш станок. Это не так и сложно, но процесс занимает некоторое время. Для калибровки нужно перемещать по оси лазерный модуль, и смотреть, как точно происходит перемещение. Например, вы переместили на 100 мм, а станок переместился на 102 мм. Это все настраивается в прошивке. Полный процесс калибровки буду рассказывать в следующей статье. А сейчас выложу скриншот моих настроек GRBL 1.1 для лазерного гравировального станка.
Программа LaserGRBL для управления лазерным гравером на Arduino.
Осталось установить программное обеспечения для компьютера, которое позволит гравировать, выбрав понравившуюся картинку. Я буду гравировать векторный логотип сайта и елочную игрушку. Исходники будут в разделе материалы для скачивания.
LaserGRBL поддерживает гравировку растровой и векторной графики, что позволяет облегчить поиск материала для гравировки.
Подробнее о программе LaserGRBL напишу отдельную статью, так как там есть некоторые фишки, которые упрощают работу с лазерным гравером. Некоторые из них вы можете увидеть в видео.
А сейчас покажу, как выглядит исходное изображение, загруженное в программу LaserGRBL, и что получается после гравировки.
Подведём итог.

В домашних условиях собрать лазерный гравер не составит большого труда. Но перед сборкой нужно определиться, чего мы ожидаем. В связи с тем, что данный станок я собрал попутно, то лазерный гравер не является первоначальной задачей. И выбор ходового винта, для данного станка, является не правильным решением. Потому что перемещение происходит медленно, а гравировка делается быстро, и я использовал только 50% мощности лазера. Это не приемлемо. Что же делать? Нужно использовать не ходовые винты, а ременную передачу, что увеличит скорость и плавность перемещения.
Если присмотреться на гравированные изделия, то можно увидеть небольшую рябь. Это связанно с тем, что по оси X ходовой винт имеет изгиб и при перемещении происходит раскачивание лазерной головы. Если такое колебание будет при фрезеровке, то зажатая фреза в материал просто не допустит такие небольшие колебания.
Более подробно настройку станка и программное обеспечение разберу в следующих статьях:
- Электроника лазерного гравера.
Arduino UNO, CNC shield v3, ttl laser driver.
Понравился проект Самодельный Лазерный гравёр с ЧПУ, в домашних условиях? Не забудь поделиться с друзьями в соц. сетях.
А также подписаться на наш канал на YouTube, вступить в группу Вконтакте, в группу на Facebook.
Спасибо за внимание!
Технологии начинаются с простого!
Фотографии к статье
Файлы для скачивания
Скачивая материал, я соглашаюсь с Правилами скачивания и использования материалов.
логотип сайта .svg | 10 Kb | 1237 | Скачать | |
елочнаяигрушка.svg | 8 Kb | 1200 | Скачать | |
grbl_v1.1h.zip | 301 Kb | 1192 | Скачать |
Простейший станок с ЧПУ с минимальным количеством деталей
В этом уроке я покажу вам, как я построил простейший станок с ЧПУ с минимальным количеством деталей и без использования 3D-принтера. Вот так. Я использую 3D-принтеры для большинства своих последних проектов, потому что, конечно же, они отлично подходят для прототипирования, поскольку мы можем легко сделать с ними любую форму, какую захотим. Однако не у всех есть 3D-принтер, поэтому я хотел показать вам, что мы можем делать вещи даже без помощи 3D-принтеров или других станков с ЧПУ.
Вы можете посмотреть следующее видео или прочитать письменный учебник ниже.
Обзор
Я покажу вам, как я построил этот станок с ЧПУ, используя только один электроинструмент, дрель и несколько ручных инструментов. Материал, который я использовал для этой сборки, — это плита МДФ толщиной 8 мм, которая на самом деле довольно прочная и, вероятно, более жесткая, чем материал PLA, напечатанный на 3D-принтере, и в то же время с ней легко работать.
В этом видео я буду использовать этот станок с ЧПУ в качестве лазерного гравера, а в будущем видео я планирую заставить его работать в качестве перьевого плоттера.
Очевидно, что такая конструкция станка не может обеспечить большую жесткость, поэтому мы не можем использовать его как фрезерный станок с ЧПУ или фрезерный станок. Хотя, если бы мы подключили более мощный лазер, мы могли бы использовать его для резки различных материалов, таких как эта плита МДФ, которую мы используем здесь, или другой тип деревянных досок, и с довольно хорошей точностью.
Рабочая зона довольно большая 390 на 360 мм, а уровень детализации, который может произвести этот лазерный гравер, впечатляет. Честно говоря, я был удивлен, насколько хороши получились гравюры.
Мозгом этого станка с ЧПУ является плата Arduino UNO в сочетании с шилдом с ЧПУ, но более подробная информация об этом, а также о том, как подготовить чертежи или изображения для лазерной гравировки, сделать G-коды и управлять станком с помощью бесплатного, программы с открытым исходным кодом, чуть позже в видео.
Самодельный лазерный гравер с ЧПУ 3D-модель
Я начал с проектирования станка в SOLIDWORKS for Makers. Двумя основными компонентами этого станка с ЧПУ являются линейные направляющие MGN15H вместе с соответствующими скользящими блоками.
Для привода блоков или двух осей мы используем два шаговых двигателя NEMA 17 и несколько подходящих шкивов GT2 и зубчатые ремни. Для соединения всего вместе мы используем плиту МДФ толщиной 8 мм, а для возврата машины в исходное положение — два концевых микровыключателя.
Вот и все, станок с ЧПУ с минимальным количеством деталей.
Вы можете скачать 3D-модель здесь:
Вы можете найти и скачать эту 3D-модель, а также изучить ее в своем браузере на Thangs:
Скачать сборную 3D-модель от Thangs.
Спасибо Thangs за поддержку этого урока.
Вот чертеж центральной монтажной пластины:
См. также: Станок для резки пенопласта с ЧПУ Arduino
Сборка станка
Хорошо, теперь мы можем приступить к сборке станка. Вот список компонентов, необходимых для сборки этого станка с ЧПУ своими руками. Список электронных компонентов можно найти ниже в разделе принципиальных схем статьи.
- Линейная направляющая MGN15H ………………………… Amazon / Banggood / AliExpress
- Шаговый двигатель — NEMA 17 ………….
… Amazon / Banggood / AliExpress
- Ремень GT2 + зубчатый шкив…………………4… 9004 Banggood / AliExpress
- Натяжной шкив GT2 …………………………………… Amazon / Banggood / AliExpress
- Распорные гайки ………………………………. …….. Amazon / Banggood / AliExpress
- Набор болтов и гаек …………………………… Amazon / Banggood / AliExpress или в местном хозяйственном магазине + винты с плоской головкой 3×16 мм
- M2x20 x2, M3x12 x20, M3x16 x5, M , винты 3×16 мм x20
Раскрытие информации: Это партнерские ссылки. Как партнер Amazon я зарабатываю на соответствующих покупках.
Вот плита МДФ толщиной 8 мм, которую я буду использовать, и по чертежам, которые я взял из 3D-модели, теперь я буду резать детали по размеру.
Связанный: Самодельный перьевой плоттер с автоматической сменой инструмента | Чертежный станок с ЧПУ
Для этой цели я использовал самый простой способ: карандаш для разметки мест, где мне нужно было вырезать, и ручную пилу для их резки.
Конечно, чтобы вырезать все детали вручную, требуется некоторое усилие, но тем не менее, мы можем сделать их довольно красивыми и чистыми даже с помощью этого метода.
После того, как я вырезал все детали по размеру, я приступил к проделыванию в них отверстий. Точное выполнение отверстий на самом деле важнее, чем вырезание деталей. Расположение отверстий должно быть очень точным, так как они должны совпадать с другими частями, имеющими точные и фиксированные размеры, такими как линейные рельсы и шаговые двигатели.
Центральная пластина, на которой установлены ось Y и шаговые двигатели, имеет много отверстий, и чтобы сделать их правильно, я напечатал чертеж этой детали в натуральную величину.
Обычные принтеры легко доступны каждому, поэтому я не буду обманывать, если воспользуюсь одним из них для создания этого проекта. Таким образом, мы можем расположить деталь и чертеж и отметить расположение отверстий. Затем мы можем просверлить отверстия, хотя это не означает, что мы получим их на 100% точно. Мы все еще делаем работу вручную, поэтому нам нужно быть очень сконцентрированными и терпеливыми, чтобы все сделать правильно.
Нам понадобится сверло на 3 и 5 мм, а также одно сверло на 25 мм, чтобы сделать отверстие для шагового двигателя.
Далее я продолжил сборку основания станка, на котором будет закреплена направляющая оси X. Для этого я отметил место, где должна быть закреплена опорная часть рельса, и просверлил два отверстия в базовой части и одно отверстие в опорной части.
Затем я скрепил эти две детали первым 3-миллиметровым шурупом и небольшим количеством столярного клея. Установив первый винт, я проверил прямоугольность, а затем предварительно просверлил второе отверстие в опорном материале 2-миллиметровым сверлом.
Таким же образом я добавил два кронштейна для лучшей поддержки.
Честно говоря, этот метод сборки этих деталей из МДФ не очень хорош, так как очень сложно сделать их прямыми, так как все мы делаем вручную, а плиты МДФ имеют толщину всего 8 мм, что дополнительно усложняет этот процесс. Возможно, лучшим и простым способом было бы использование металлических скоб, которые вы можете легко найти в хозяйственном магазине.
Тем не менее, когда обе стороны были готовы, я установил на них направляющую оси X.
Эти направляющие MGN15H обеспечивают очень плавное движение без люфтов, так как внутри их скользящих блоков находятся шарики или ролики.
Перед установкой их следует хорошо очистить и смазать. Я закрепил линейную направляющую двумя болтами M3 с каждой стороны.
Далее нам нужно установить ось Y поверх скользящего блока оси X. Для этой цели мы будем использовать центральную пластину.
Опять же, мы используем болты M3 для соединения деталей. Для крепления шаговых двигателей нам также понадобятся болты M3.
В дополнение к этому, для одного из степперов я использую распорные гайки, чтобы получить правильную высоту установки для него, хотя я, вероятно, мог бы установить этот степпер на нижней стороне пластины, и поэтому мы бы получили использовать эти дистанционные гайки.
Для привода оси X нам необходимо установить два промежуточных шкива GT2 рядом с валом шагового двигателя, чтобы мы могли создать надлежащее натяжение между ремнем и шкивом шагового двигателя.
Нам нужны болты M5 и гайки для их крепления. Что касается оси Y, нам нужен только один натяжной ролик с другой стороны рельса, так как ремень для этой оси будет установлен в виде петли.
Хорошо, теперь брак или соединение осей X и Y вместе. Мы делаем это, используя четыре болта M3. Это соединение имеет решающее значение для точности, так как от него зависит точность всей машины.
Используя квадратную линейку, мы должны проверить, перпендикулярны ли две оси друг другу, и если нет, мы должны правильно их отрегулировать.
Затем мы можем установить детали, которые входят в скользящий блок оси Y и в данном случае фактически удерживают концевой эффектор или лазерный модуль. Используя метод, описанный ранее, я собрал эти детали и прикрепил их к скользящему блоку с помощью четырех болтов M3.
Теперь мы можем закрепить лазерный модуль двумя болтами М3.
Продолжил установку ремней GT2. Я измерил нужную мне длину и обрезал ремень по размеру.
Для крепления ремня к скользящему блоку я использовал два болта М5 и стяжки.
Я прикрепил первую сторону ремня к болту M5 с помощью хомута, а затем натянул ремень с другой стороны и закрепил его на втором болте с помощью хомута.
Что касается оси X, ремень будет натянут по линии от одной стороны к другой, проходя через три шкива таким образом, чтобы обеспечить натяжение или сцепление со шкивом шагового двигателя.
Я закрепил ремень с обеих сторон одним болтом и квадратным куском МДФ.
На этом наш станок с ЧПУ почти готов. Есть еще несколько вещей, которые нам нужно сделать.
Внизу я приклеил несколько мебельных накладок, чтобы машинка устойчивее стояла на месте.
Затем я установил концевой микровыключатель для оси Y. Для этого нам понадобятся два болта М2.
Что касается концевого выключателя по оси X, то я забыл сделать эти отверстия на центральной пластине, поэтому пометил их и просверлил на месте.
Было немного трудно закрепить этот концевой выключатель на месте, но в конце концов получилось хорошо.
Подключение электронных компонентов
Механическая часть завершена, теперь мы можем перейти к подключению электронных компонентов. Как я уже упоминал, мы будем использовать плату Arduino UNO в сочетании с CNC Shield и двумя шаговыми драйверами DRV8825 или A4988.
Я закреплю плату Arduino сбоку машины, поэтому я отмечаю два отверстия для Arduino и просверливаю их 3-мм сверлом. Я использовал гайки с расстоянием 5 мм между боковой панелью и платой Arduino.
Подробнее: Шаговые двигатели и Arduino. Полное руководство
Экран ЧПУ просто устанавливается поверх платы Arduino. Нам нужно вставить 3 перемычки для каждого драйвера, чтобы у нас было выбрано самое высокое разрешение шагового двигателя.
Обратите внимание, что эти три перемычки должны быть удалены, так как они нам не нужны. Я использовал их в одном из своих предыдущих проектов.
Затем мы можем подключить шаговые двигатели на месте с помощью прилагаемых кабелей. Для подключения концевых выключателей нам понадобится двухпроводное соединение.
Я припаял один конец проводов непосредственно к концевым упорам, а с другой стороны припаял штыревые разъемы, чтобы можно было легко подключить их к экрану ЧПУ.
Что касается подключения лазерного модуля, то нам потребуются 3 провода, GND, 12В и сигнальная линия для ШИМ-управления. Эти провода должны быть немного длиннее, чтобы они могли достигать самой дальней точки машины.
С одной стороны у нас есть 3-контактный разъем, который идет в лазерный модуль, а с другой стороны у нас есть провода GND и 12V, которые будут идти к разъему питания платы ЧПУ и сигнальная линия, которая должна быть подключен к концевому штифту Z+ или Z-.
Электрическая схема самодельного лазерного гравера с ЧПУ
Вот принципиальная схема того, как все должно быть подключено.
Вы можете получить компоненты, необходимые для этого проекта, по ссылкам ниже:
- Шаговый двигатель — NEMA 17……………… Amazon / Banggood / AliExpress
- DRV8825 Шаговый драйвер……….
…….. … Amazon / Banggood / AliExpress
- Arduino CNC Shield ………………………. Amazon / Banggood / AliExpress
- Arduino Uno………………………………..… Amazon / Banggood/AliExpress
- Концевой выключатель ……………………………………. Amazon / Banggood / AliExpress
- Блок питания постоянного тока ……………………………. Amazon / Banggood / AliExpress
- Лазерный модуль …………………………………. Amazon / Banggood / AliExpress
- Лазерные защитные очки …………………….. Amazon / Banggod / AliExpress
Раскрытие информации: это партнерские ссылки. Как партнер Amazon я зарабатываю на соответствующих покупках.
Итак, мы используем плату Arduino UNO в сочетании с CNC Shield и двумя шаговыми драйверами DRV8825 или A4988. У нас есть два микроконцевых выключателя для возврата станка в исходное положение и лазерный модуль на 12 В, которым можно управлять с помощью ШИМ. Для питания нам понадобится блок питания 12v с минимальной силой тока 3 ампера.
Прошивка и управляющее ПО
На этом мы фактически закончили сборку машины. Теперь осталось дать ему жизнь или сделать из него настоящий станок с ЧПУ. Для этого нам нужно установить прошивку на Arduino для управления движением станка с ЧПУ.
Наиболее популярным выбором для станков с ЧПУ своими руками является прошивка GRBL с открытым исходным кодом. Помимо прошивки GRBL нам также понадобится управляющее ПО, через которое мы будем отправлять G-коды и указывать машине, что делать. В этом случае мы будем использовать контроллер LaserGRBL. Это программное обеспечение специально создано для управления лазерными граверами с прошивкой GRBL, и я могу сказать вам, что это действительно потрясающий контроллер для этой цели, учитывая, что он также имеет открытый исходный код.
Благодаря LaserGRBL у нас есть возможность напрямую прошивать или загружать прошивку GRBL в Arduino, поэтому нам не нужно делать это вручную. Мы даже можем выбрать готовую к использованию версию для двухкоординатных станков только с реферированием по осям X и Y, точно такую же, как та, которая нам нужна.
Итак, как только мы прошьем нашу Arduino прошивкой GRBL, мы сможем подключить нашу машину к контроллеру и открыть окно конфигурации GRBL, чтобы мы могли настроить некоторые параметры в соответствии с нашей машиной.
Первое, что мы должны настроить здесь, это разрешение перемещения или значения шагов/мм для осей X и Y. Эти значения показывают, сколько шагов должен сделать двигатель, чтобы переместиться на 1 мм. Это зависит от типа имеющегося у нас шагового двигателя, выбранного разрешения шага и передачи движения, в данном случае ремня и шкива GT2.
Вот как мы можем рассчитать эти значения для нашей машины. Значения по умолчанию здесь обычно составляют 250 шагов/мм. Теперь мы можем переместить станок с помощью команд JOG, например, на 20 мм, и мы должны заметить, насколько на самом деле сдвинется станок.
В моем случае при 20-мм шаге по оси Y фактическое перемещение составило 31 мм.
Итак, 20/31 = 0,645, и если мы умножим это значение на 250, мы получим 161,29. Итак, это значение, которое мы должны установить в качестве значения шагов/мм для нашей машины.
Если мы попытаемся переместить машину сейчас с обновленными значениями, машина должна переместиться на точное расстояние. Если вы недовольны результатом, вы все равно можете точно настроить эти значения, нарисовав квадраты и измерив их. В итоге я использовал значение 160 шагов/мм.
Тем не менее, есть и другие важные параметры, которые необходимо настроить. Например, мы должны включить Жесткие ограничения, которые являются фактическими концевыми выключателями, Мягкие ограничения, которые определяют рабочую область, установить направление возврата, которое определяет, где наши концевые выключатели расположены на машине, и так далее.
Вы можете скачать мой набор параметров и импортировать их в свою прошивку.
Генерация G-кодов для лазерной гравировки
Еще одна замечательная особенность этого программного обеспечения заключается в том, что оно также имеет встроенный генератор G-кодов. Это означает, что мы можем загрузить любую фотографию, картинку, карандашный рисунок и т. д. прямо в программу и сгенерировать G-код для гравировки в соответствии с нашими потребностями. Инструмент растрового изображения достаточно универсален и позволяет выбирать из множества параметров, таких как трассировка от строки к строке, векторизация, 1-битное черно-белое сглаживание и т. д.
Конечно, если вы хотите, вы также можете сгенерировать G-код с помощью другого программного обеспечения, такого как, например, Inkscape и его плагин Inkscape-Lasertools для создания G-кодов и загрузить их здесь. Я уже объяснял, как использовать этот метод для создания G-кодов, в моем предыдущем видео для лазерного гравера SCARA Robot, так что для получения более подробной информации вы можете посмотреть это видео.
Сейчас я покажу вам, как можно сгенерировать G-код для лазерной гравировки из фотографии с помощью LaserGRBL. Здесь у меня есть фото собаки, которое я открою с помощью программы.
С помощью параметра «Яркость и контрастность» мы можем настроить изображение по своему желанию. Мы можем выбрать тип преобразования фотографии, например, трассировка Line-to-Line, 1-битный черно-белый дизеринг или векторный формат. Я буду использовать трассировку от линии к линии для этой фотографии, и здесь мы также можем выбрать направление линии и качество гравировки, которое определяется количеством линий на миллиметр.
Далее мы можем выбрать скорость гравировки, установить минимальное и максимальное значения ШИМ для мощности лазера и установить размер гравировки.
И все, программа сгенерирует G-код для этой гравировки. Прежде чем мы начнем его, мы можем использовать кнопку «Рамка», чтобы наметить или показать нам, где будет происходить гравировка, чтобы мы могли настроить нашу заготовку по мере необходимости.
Обратите внимание, что мы должны использовать очки для защиты от лазера, которые защитят наши глаза от ультрафиолетового излучения лазера, так как это очень опасно.
Если мы правильно откалибровали нашу машину, мы можем получить неплохие гравюры. Для калибровки мы могли бы использовать это изображение, которое я сделал, которое имеет квадраты от 100% до 10% прозрачности.
В соответствии с результатами отрегулируйте скорость гравировки и значение ШИМ для мощности лазера.
Здесь вы можете скачать калибровочное изображение:
Итак, это урок. Надеюсь, вам понравилось и вы узнали что-то новое. Если у вас есть какие-либо вопросы, не стесняйтесь задавать их в разделе комментариев ниже и не забудьте проверить некоторые из моих других проектов Arduino.
Как построить станок для лазерной резки? — Руководство «Сделай сам»
Планируете ли вы построить свой собственный станок для лазерной резки для любителей или начать бизнес, чтобы зарабатывать на этом деньги? Прочтите это руководство, чтобы узнать, как сделать лазерный резак своими руками и стать завидным профессиональным мастером.
Введение
Всем известно, что для того, чтобы стать квалифицированным мастером или мастером-сделай сам, использование лазерного резака является обязательным курсом для поступления, но может быть много проблем. Если вы можете построить его самостоятельно, проблема будет решена легко?
Проект, которым я хочу поделиться, — это станок для лазерной резки, сделанный в прошлом году. Я считаю, что все знакомы с лазерным резаком (также известным как лазерный гравер по той причине, что он может выполнять лазерную гравировку), и это также артефакт для создателей проектов. Его преимущества, такие как быстрая обработка, эффективное использование пластин и реализация технологии резки, которую не могут обеспечить традиционные процессы, глубоко любимы всеми.
Обычно при использовании станка с ЧПУ для работы возникают следующие проблемы по сравнению с лазерной резкой: необходимо установить и заменить инструмент перед работой, настройка инструмента, чрезмерный шум, длительное время обработки, загрязнение пылью, радиус инструмента и другие проблемы. . Превосходство резки привело к идее сделать станок для лазерной резки своими руками.
После того, как у меня появилась эта идея, я начал проводить технико-экономическое обоснование этой идеи. После многочисленных исследований и сравнений различных типов станков для лазерной резки в сочетании с их собственными условиями и потребностями в обработке, взвесив все за и против, я составил пошаговый план сборки с модульной конструкцией и изготовлением, которые являются съемными и обновляемый.
Через 60 дней каждая часть машины принимает модульную конструкцию. Благодаря концепции модульности обработка и производство удобны, а окончательная сборка достаточна, и финансовое давление не будет слишком большим, а необходимые детали можно приобретать шаг за шагом. Размер готовой машины достигает 1960 мм * 1200 мм * 1210 мм, ход обработки составляет 1260 мм * 760 мм, а мощность резки составляет 100 Вт. Он может обрабатывать большое количество деталей одновременно и имеет функции лазерной резки, гравировки, сканирования, нанесения надписей и маркировки.
Планирование проекта
Весь проект включает в себя семь основных частей, а именно: систему управления движением, проектирование механической конструкции, систему управления лазерной трубкой, систему световода, систему продувки и вытяжки воздуха, систему фокусировки освещения, оптимизацию работы и другие аспекты.
Общая идея создания инициала:
1. Ход производимого станка для лазерной резки должен быть большим, чтобы заполнить пробел, из-за которого диапазон обработки станка с ЧПУ недостаточно велик, что может избавить от проблем с предварительным — разрезание листа. Вы также можете использовать его функцию лазерной маркировки для непосредственной маркировки больших пластин, что решает проблему ручной маркировки.
2. Поскольку ход увеличивается, мощность лазерного резака не может быть слишком низкой, в противном случае лазер будет иметь определенные потери в воздушной проводимости, поэтому общая мощность не может быть ниже 100 Вт.
3. Чтобы обеспечить точность и бесперебойную работу лазерного резака, весь выбор материала должен быть металлическим.
4. Удобен в использовании и эксплуатации.
5. Разработанная структура соответствует плану последующей модернизации.
Лазерный резак «Сделай сам»
Имея общие рамки идеи и план «Сделай сам», давайте начнем 8 шагов по созданию лазерного резака. Я подробно расскажу о конкретном процессе изготовления и деталях.
Шаг 1. Проектирование системы управления движением
Первым шагом является система управления движением. Я использую лазерную материнскую плату RDC6442S-B (EC). Эта управляющая материнская плата может управлять четырьмя осями, а именно X, Y, Z и U. Материнская плата оснащена интерактивным экраном. Рабочее состояние станка, хранение файлов обработки и отладка станка могут быть выполнены через рабочий экран, но следует отметить, что параметры управления двигателем оси XYZ должны быть подключены к компьютеру для Установка параметров.
Например: ускорение и замедление без нагрузки, ускорение и замедление резки, скорость без нагрузки, коррекция ошибки положения двигателя, выбор типа лазера. Система управления питается от источника постоянного тока 24 В, для которого требуется импульсный источник питания 24 В. Для обеспечения стабильности системы используются два импульсных источника питания 24 В, один 24 В 2 А напрямую питает материнскую плату, а другой 24 В 15 А обеспечивает питание трех двигателей, а входная клемма 220 В подключена к 30-амперному фильтру для обеспечения стабильной работы. работа системы.
После установки параметров можно подключить двигатель для проверки холостого хода. На этом этапе вы можете проверить линию подключения двигателя, направление двигателя, направление работы экрана, настройки подразделения шагового двигателя, импортировать файлы резки для пробной эксплуатации. Я выбрал двухфазный шаговый двигатель 57 длиной 57 мм, потому что в предыдущем проекте их было всего 3, поэтому я использовал их напрямую, чтобы не тратить зря. Я выбрал драйвер TB6600, обычный шаговый двигатель. В драйвере мотора установлено деление 64.
Если вы хотите, чтобы система лазерной резки имела лучшую производительность на высоких скоростях, вы можете выбрать трехфазный шаговый двигатель с большим крутящим моментом и очень хорошими характеристиками на высоких скоростях. Разумеется, после последующих испытаний было установлено, что двухфазный шаговый двигатель 57 вполне способен к скоростному перемещению по оси X при лазерном сканировании фотографий, поэтому пока буду использовать его, а двигатель заменю если его нужно будет обновить позже.
С точки зрения системы защиты общая схема должна быть отделена от высокого и низкого напряжения. При разводке необходимо обратить внимание, чтобы не было перекрестков. Самое главное, что он должен быть заземлен. Потому что при прохождении высокого напряжения металлический каркас и корпус будут генерировать наведенное электричество, и когда рука дотронется до него, возникнет ощущение онемения. В это время мы должны обратить внимание на эффективное заземление, и лучшее сопротивление заземления не должно превышать 4 Ом (необходимо проверить заземляющий провод), чтобы предотвратить несчастные случаи с поражением электрическим током, кроме того, главный выключатель питания также необходимо добавить выключатель защиты от протечек.
На панели управления также необходимо установить аварийный выключатель, выключатель питания с ключом, концевые выключатели осей X, Y, Z для каждой оси движения, выключатель защиты от воды с постоянной температурой для лазерной трубки , аварийный выключатель для защиты от открывания крышки для повышения безопасности станка для лазерной резки.
Для облегчения последующего обслуживания каждую клемму можно пометить соответствующим образом.
Этап 2. Механическое проектирование
Вторым этапом является проектирование механической конструкции. На этом шаге сосредоточен весь станок для лазерной резки. Точность машины и работа машины должны быть реализованы разумной механической структурой. В начале проектирования первой проблемой, с которой приходится сталкиваться, является определение маршрута обработки, а формулировка маршрута обработки требует исходной направляющей идеологии. Какой объем обработки ему нужен?
Размер деревянной доски 1220 мм * 2400 мм. Чтобы свести к минимуму количество разделочных досок, ширина деревянной доски составляет 1200 мм в качестве диапазона обработки длины, а ширина обработки должна быть больше 600 мм, поэтому я установил ширину около 700 мм, а длину и ширину каждый плюс Длина 60 мм для зажима или позиционирования. Таким образом, фактическая эффективная дальность обработки может быть гарантирована на уровне 1200 мм * 700 мм. По общей оценке дальности маршрута обработки общий размер близок к 2 метрам, что не превышает максимального диапазона 2 метра для экспресс-доставки, что соответствует требованиям.
Аппаратные аксессуары
Следующим шагом является приобретение аппаратных аксессуаров, лазерной головки, одного анти-, двух анти-, синхронного шкива и так далее. Для основной рамы я выбрал алюминиевый профиль европейского стандарта толщиной 4040, потому что точность установки оси XY определяет будущую точность обработки, а материалы должны быть цельными. Часть луча по оси X лазерной головки изготовлена из алюминиевого профиля толщиной 6040, а ширина шире, чем 4040 по оси Y, потому что, когда лазерная головка находится в среднем положении, алюминиевый профиль будет деформироваться, если сил не хватает.
Проектирование конструкции по оси XY
Перед проектированием конструкции по оси XY сначала измерьте и начертите аппаратные аксессуары и различные детали, а затем выполните проектирование конструкции в программе AutoCAD.
Передача по оси X замедляется шаговым двигателем через синхронный шкив и выводится на синхронный ремень, а открытый конец синхронного ремня соединяется с лазерной головкой. Вращение шагового двигателя по оси X приводит в движение синхронный ремень для бокового перемещения лазерной головки; передача по оси Y относительно немного сложнее. Чтобы левый и правый линейные ползунки двигались синхронно с одним двигателем, два линейных модуля необходимо соединить параллельно с оптической осью, а затем оптическая ось приводится в действие шаговым двигателем для одновременного привода двух линейных ползунков. чтобы сместить ось Y. Ось X всегда может находиться в горизонтальном положении.
Обработка и сборка деталей
После завершения проектирования следующим шагом будет обработка и сборка деталей, обработка распорки по оси X, 3D-печать кронштейна оптической оси по оси Y, сборка рамы из алюминиевого профиля, установка линейная направляющая и т. д. Наиболее критической и утомительной частью является регулировка точности. Этот процесс требует повторной отладки и требует терпения.
1. Оптическая ось фиксируется двумя муфтами и кронштейнами оптической оси.
2. Обработайте опорную пластину оси X, чтобы соединить алюминиевый профиль оси X с двумя линейными модулями оси Y.
3. При установке рамы из алюминиевого профиля с осью XY необходимо обеспечить вертикальность и параллельность рамы, поэтому во время процесса требуются повторные измерения для обеспечения точных размеров. При установке двух линейных направляющих по оси Y убедитесь, что направляющие параллельны алюминиевому профилю, и измерьте циферблатным индикатором, чтобы убедиться, что параллельность находится в пределах 0,05 мм.
4. При установке линейной направляющей необходимо убедиться, что направляющая параллельна алюминиевому профилю. Направляющая каждой секции должна быть измерена циферблатным индикатором, чтобы убедиться, что параллельность находится в пределах 0,05 мм, что закладывает хорошую основу для последующей установки.
5. Чтобы установить синхронный ремень оси Y, сначала убедитесь, что ось X находится в горизонтальном положении, и используйте циферблатный индикатор для отметки счетчика. После измерения обнаруживается, что сам алюминиевый профиль имеет кривизну около 0,05 мм, поэтому точность по горизонтали следует контролировать в пределах 0,1 мм (желательно, чтобы два циферблатных индикатора были сброшены на ноль), а положение двух ползунков и Ось X фиксируется зажимом.
6. Протяните зубчатый ремень с обеих сторон и закрепите его слева. Затем сбросьте левый контактный циферблатный индикатор на ноль, измерьте горизонтальное отклонение на другой стороне, отрегулируйте горизонтальное отклонение в пределах 0,1 мм и зафиксируйте его зажимом. Затем закрепите правый зубчатый ремень. В настоящее время из-за операции установки с правой стороны горизонтальная ошибка определенно увеличится. Затем снова переместите циферблатный индикатор влево, чтобы установить ноль, и ослабьте правую муфту, чтобы переместить ось X. Сдвиньте ползунок, отрегулируйте горизонтальное отклонение в пределах 0,1 мм и зафиксируйте моментную муфту зажимом.
7. Теперь можно ослабить зажимы с обеих сторон, проверить, находится ли ось X в горизонтальном положении при перемещении оси Y, повернуть колесо синхронизации оси Y и повторить предыдущий процесс измерения. Если обнаружено, что ось X не синхронизирована, возможно, натяжение зубчатого ремня отличается с обеих сторон или точность каждой конструкции не была отрегулирована должным образом, тогда вам необходимо вернуться к предыдущему этап и отрегулируйте его снова. Пока натяжение зубчатого ремня отрегулировано, ось X следует снова отрегулировать до тех пор, пока ось Y не будет перемещена, а ось X всегда находится в пределах диапазона горизонтальной ошибки 0,1 мм. Не забудьте запастись терпением на этом этапе.
8. Проверьте, одинаково ли натянуты зубчатые ремни с обеих сторон. согласуются.
9. Установите шаговый двигатель. При установке мотора нужно обратить внимание на регулировку его герметичности. Если синхронный ремень слишком ослаблен, это вызовет люфт движения, а если он слишком натянут, синхронный ремень треснет.
Проверка стабильности механического механизма
Подключение системы управления для проверки устойчивости механической конструкции, подключение компьютера для отладки параметров двигателя, измерение отклонения график и размер конструкции, отрегулируйте количество импульсов шагового двигателя в соответствии с фактическим отклонением расстояния и проверьте, есть ли люфт в механизме. Является ли каждый штрих последовательным и связаны ли точки пересечения. Выполняется повторное рисование, и повторная точность позиционирования определяется повторным рисованием. Разумеется, повторяемость точности позиционирования механизма можно определить с помощью фиксированного циферблатного индикатора и измерителя.
Повторив рисунок три раза, вы можете увидеть, что все штрихи представляют собой места без каких-либо ореолов, что указывает на то, что перемещение выполнено нормально. В настоящее время по оси XY уже можно рисовать графику. Если добавить функцию подъема пера, он может стать крупномасштабным плоттером. Конечно, настоящая цель — сделать станок для лазерной резки, поэтому нам нужно продолжать усердно работать.
После завершения оси XY следующим шагом будет создание оси Z. Прежде чем сделать ось Z, нам нужно сделать 3D-моделирование и спроектировать общую раму. Поскольку ось Z соединена с режущей платформой и закреплена на модуле рамы, она должна быть спроектирована и изготовлена вместе. Ось Z реализует функции подъема и опускания, а затем непосредственно на нее помещается модуль оси XY, и комбинация может реализовать функцию оси XYZ.
С помощью моделирования в Solidworks спроектируйте общую раму и конструкцию по оси Z стола для лазерной резки. С помощью трехмерной перспективы структурные проблемы могут быть быстро обнаружены и быстро исправлены.
Здание с подвижной платформой
После установки рамы и конструкции можно сделать подвижную платформу в нижней части машины. Весь станок для лазерной резки размещается на платформе. Машина относительно крупная. Нереально построить стол для лазерной резки, а затем передвинуть его вверх. Процесс также повлияет на точность станка, поэтому его можно построить только на нижней подвижной платформе.
1. Теперь начните строить подвижную платформу внизу, сначала купите утолщенный квадратный стальной лист 5050 для изготовления рамы.
2. Квадратная сталь сваривается один за другим, и после завершения она очень прочная, и нет проблем с тем, чтобы на ней сидел весь человек.
3. Приварите 4 ролика к раме и оставьте зазор 600 мм с левой стороны. Основная цель – оставить место для воды постоянной температуры и воздушного насоса. Теперь, когда рама передвижной платформы сварена, необходимо сверху и снизу установить слой дерева.
4. Соберите раму машины и купите алюминиевые профили в Интернете. Модель представляет собой 4040 алюминиевых профилей национального стандарта. Основная причина использования этого алюминиевого профиля национального стандарта заключается в том, что он относительно легкий, с ним легко обращаться после установки, он обладает хорошей прочностью, а закругленные углы вокруг него относительно малы, что облегчает проектирование и установку последующих панелей из листового металла.
Чтобы построить машинную раму в гостиной, она слишком большая, чтобы поместиться.
5. Соберите ось XY и раму станка, поместите готовую раму на мобильную платформу, а затем установите отлаженную ось XY на раму станка. Общий эффект по-прежнему хороший.
6. Начните изготавливать опорный лист оси Z, разметьте алюминиевый лист и определите положение отверстия. Просверлите и нарежьте резьбу, чтобы сделать 4 одинаковых опорных листа.
7. Соберите подъемный винт оси Z и соберите Т-образный винт, синхронный шкив, гнездо подшипника, опорную пластину и фланцевую гайку.
8. Установите подъемный винт оси Z, шаговый двигатель и зубчатый ремень. Принцип подъема по оси Z: шаговый двигатель натягивает синхронный ремень через натяжные колеса с обеих сторон. Когда двигатель вращается, он заставляет четыре подъемных винта вращаться в одном направлении, так что четыре опорные точки одновременно перемещаются вверх и вниз, а режущая платформа одновременно соединяется с опорными точками. Движение вверх и вниз. При установке сотовой панели нужно обратить внимание на регулировку плоскостности. С помощью циферблатного индикатора измерьте разницу высот всей рамы и отрегулируйте разницу высот до 0,1 мм.
Механические конструкции, такие как структура воздушного канала, путь лазерного луча и обшивка из листового металла, будут подробно объяснены позже, когда будет задействована соответствующая система. Далее будет представлена третья часть.
Шаг 3. Настройка системы управления лазерной трубкой
1. Выберите модель трубки лазера CO2. Лазерная трубка делится на два типа: стеклянная трубка и радиочастотная трубка. Радиочастотная трубка использует низкое напряжение 30 В с высокой точностью, небольшим пятном и длительным сроком службы, но цена высока, в то время как срок службы стеклянной трубки составляет около 1500 часов, пятно относительно большое, и оно управляется высоким напряжением, но цена дешевая. Если вы режете только дерево, кожу, акрил, стеклянные трубки вполне годятся, и большинство лазерных резаков на рынке в настоящее время используют стеклянные трубки. Из-за проблемы стоимости я выбираю стеклянную трубку размером 1600 мм * 60 мм, для охлаждения лазерной трубки необходимо использовать водяное охлаждение, и это вода постоянной температуры.
Источник питания для лазерной трубки, который я выбрал, это блок питания мощностью 100 Вт. Введена функция источника питания лазера. Положительный электрод лазерной трубки излучает высокое напряжение около 10 000 вольт. Из-за высокой концентрации газа CO2 в высоковольтной разрядной трубке возбуждения в хвостовой части трубки генерируется лазер с длиной волны 10,6 мкм. Обратите внимание, что этот лазер является невидимым светом.
2. Выберите охладитель воды. Лазерная трубка будет генерировать высокую температуру при нормальном использовании, и ее необходимо охлаждать циркуляцией воды. Если температура слишком высока и вовремя не охлаждена, это вызовет необратимое повреждение лазерной трубки, что приведет к резкому сокращению срока службы или разрыву лазерной трубки. Скорость, с которой падает температура воды, также определяет производительность лазерной трубки.
Существует два типа водяного охлаждения: воздушное охлаждение и метод охлаждения с использованием воздушного компрессора. Если мощность лазерной трубки составляет около 80 Вт, может быть достаточно воздушного охлаждения, но если мощность превышает 80 Вт, необходимо использовать метод охлаждения с помощью компрессора. В противном случае жару вообще невозможно подавить. Я выбираю воду постоянной температуры модели CW5000. Если мощность лазерной трубки будет увеличена, эта вода с постоянной температурой все еще может быть пригодной для использования. Вся машина включает в себя систему контроля температуры, ведро для хранения воды, воздушный компрессор и охлаждающую плиту. модульный состав.
3. Установите лазерную трубку, установите лазерную трубку на основание трубки, отрегулируйте высоту лазерной трубки, чтобы она соответствовала проектной высоте, и обращайте внимание на осторожность при обращении с ней.
Подсоедините выпускную трубу воды с постоянной температурой. Следует отметить, что вход воды сначала входит с положительного полюса лазерной трубки, положительный вход воды лазерной трубки должен быть обращен вниз, охлаждающая вода входит снизу, а затем выходит сверху отрицательного полюса. лазерной трубки, а затем возвращается к возврату через защитный выключатель циркуляции воды. Резервуар для воды с постоянной температурой завершает цикл. Когда круговорот воды останавливается, защитный выключатель воды отключается, и сигнал обратной связи отправляется на плату управления, которая отключает лазерную трубку для предотвращения перегрева.
4. Отрицательный полюс лазерной трубки подключается к амперметру, а затем обратно к отрицательному полюсу источника питания лазера. Когда лазерная трубка работает, амперметр может отображать ток лазерной трубки в режиме реального времени. С помощью числового значения вы можете сравнить установленную мощность и фактическую мощность, чтобы определить, нормально ли работает лазерная трубка.
5. Подсоедините цепь источника питания лазера, воду постоянной температуры, водозащитный выключатель, амперметр и подготовьте защитные очки (поскольку лазерная трубка излучает невидимый свет, вам необходимо использовать специальные защитные очки 10,6 мкм) и установите мощность лазерной трубки до 40 %, включите режим серийной съемки, поместите тестовую плату перед лазерной трубкой, нажмите переключатель, чтобы испустить лазер, плата мгновенно зажжется, и испытательный эффект будет очень хорошим.
Следующим шагом является настройка системы оптического пути.
Шаг 4. Настройка системы световода с лазерной трубкой
Четвертая часть — это настройка системы световода с лазерной трубкой. Как показано на рисунке выше, лазерный свет, излучаемый лазерной трубкой, преломляется зеркалом под углом 90 градусов ко второму зеркалу, а второе зеркало снова преломляется под углом 90 градусов к третьему зеркалу. Преломление заставляет лазер стрелять вниз к фокусирующей линзе, которая затем фокусирует лазер, образуя очень тонкое пятно.
Сложность этой системы заключается в том, что независимо от того, где находится лазерная головка в процессе обработки, сфокусированное пятно должно быть в одной и той же точке, то есть оптические пути должны совпадать в движущемся состоянии, иначе лазер луч будет отклоняться, и свет не будет излучаться.
Процесс регулировки кронштейна зеркала: зеркало и лазер расположены под углом 45 градусов, что затрудняет определение точки лазера. Необходимо распечатать на 3D-принтере 45-градусный кронштейн для вспомогательной регулировки, наклеить на сквозное отверстие фактурную бумагу и включить лазер. Режим точечной съемки (время включения 0,1 с, мощность 20% для предотвращения проникновения), отрегулируйте высоту, положение и угол поворота кронштейна, чтобы световое пятно контролировалось в центре круглого отверстия.
Точное положение установки и высота установки кронштейна второго поверхностного зеркала получены с помощью трехмерного проектирования пути второго поверхностного зеркала, а кронштейн второго поверхностного зеркала точно установлен путем измерения штангенциркуль (предварительно установите его в исходное положение).
Процесс регулировки угла первого поверхностного зеркала: переместите ось Y ближе к зеркалу, лазерной точке, затем отодвиньте конец оси Y от себя , и снова точка. В это время будет обнаружено, что две точки не совпадают, если ближняя точка выше, а дальняя ниже, то зеркало необходимо отрегулировать, чтобы оно вращалось вверх, и наоборот; следующий шаг — продолжать делать точки, дальнюю и ближнюю, если ближняя точка находится слева, а дальняя точка справа, нужно настроить зеркало так, чтобы оно вращалось влево, и наоборот, пока не появится ближняя точка, совпадающая с дальней точкой как точка, означает, что оптический путь второго поверхностного зеркала полностью параллелен направлению движения оси Y.
Процесс регулировки угла второго поверхностного зеркала: переместите ось Y к первому поверхностному зеркалу, затем переместите ось X к ближнему концу, сделайте лазерные точки , затем переместите ось X в дальний конец, а затем сделайте лазерные точки, в это время наблюдайте, выше ли ближняя точка, а дальняя точка ниже, вам нужно отрегулировать второе поверхностное зеркало, чтобы оно вращалось вверх, и наоборот. На следующем шаге продолжайте делать точки, одну точку далеко и одну ближе, если ближняя точка находится слева, а дальняя точка справа, вам нужно отрегулировать второе поверхностное зеркало, чтобы оно вращалось влево, и наоборот. наоборот, до тех пор, пока ближняя и дальняя точки не совпадут как одна точка, что означает, что оптический путь ближнего торцевого зеркала третьей поверхности полностью параллелен направлению движения оси X. Затем переместите ось Y в дальний конец и отметьте точку на ближнем и дальнем конце оси X, если они не совпадают, это означает, что два зеркальных пути не перекрываются, и это необходимо вернуться, чтобы отрегулировать угол первого поверхностного зеркала до двух точек на оси X на ближнем конце оси Y и двух точек и четырех точек на оси X на дальнем конце оси Y. -оси полностью совпадают.
На самом деле настройка на этом шаге не закончена. Обратите внимание, находится ли световое пятно держателя объектива третьего поверхностного зеркала в центре круга. Когда световое пятно находится слева, держатель линз второго поверхностного зеркала необходимо переместить назад, и наоборот. Отрегулируйте положение всей лазерной трубки, чтобы она двигалась вниз, и наоборот. При замене кронштейна второго поверхностного зеркала нам необходимо снова повторить процесс регулировки угла наклона линзы второго поверхностного зеркала. При изменении высоты лазерной трубки нам необходимо повторить весь процесс регулировки объектива за один проход (включая: процесс регулировки кронштейна первого поверхностного зеркала, первой зеркальной линзы и второго поверхностного зеркала) и снова делать точки до тех пор, пока световое пятно находится в центре, а четыре точки полностью совпадают.
Процесс регулировки угла третьего поверхностного зеркала: регулировка зеркала заключается в добавлении двух точек подъема и опускания по оси Z на основе зеркало, то есть 8 баллов. Принцип регулировки заключается в том, чтобы сначала определить точку подъема четырех точек, затем переместить ось X на другой конец, а затем нажать на точку подъема. Если верхняя точка светового пятна выше, чем нижняя, необходимо повернуть линзу третьего поверхностного зеркала назад и наоборот. Поворот вправо и наоборот.
Если световое пятно не всегда удается отрегулировать так, чтобы оно совпадало, это означает, что оптический путь зеркала третьей поверхности не совпадает с осью X, и необходимо вернуться для регулировки угла линзы второго поверхностного зеркала. Необходимо вернуться, чтобы отрегулировать высоту лазерной трубки, а затем начать с обратного кронштейна, чтобы отрегулировать ее снова, пока 8 точек полностью не совпадут.
Существует четыре типа фокусирующих линз: 50,8, 63,5, 76,2 и 101,6. Я выбрал 50,8 мм.
Поместите фокусирующую линзу в цилиндр лазерной головки выпуклой стороной вверх, поместите наклонную деревянную доску, переместите ось X, чтобы сделать точки через каждые 2 мм, найдите положение с самой тонкой точкой, измерьте расстояние между лазерной головкой и деревянной доской, это расстояние является наиболее подходящим положением фокусного расстояния для лазерной резки, и оптический путь был отрегулирован на этом этапе.
Шаг 5. Настройка системы продувки и выхлопа
Пятая часть – это настройка системы продувки и вытяжки. Во время лазерной резки будет образовываться густой дым, а частицы густого дыма покроют фокусирующую пластину и снизят мощность резки. Решение состоит в том, чтобы увеличить воздушный насос перед фокусирующей пластиной.
Воздушный насос, который я выбираю, — это воздушный насос воздушного компрессора, основная причина которого заключается в том, что давление воздуха относительно высокое, а эффективность резки может быть увеличена за счет действия газа во время резки. Выходной сигнал подключается к основной плате для управления электромагнитным клапаном, а электромагнитный клапан управляет воздушным насосом для подачи воздуха.
После установки мне не терпится сделать пробный распил 6-миллиметровой многослойной плиты, которую можно прорезать гладко, и эффект очень идеальный. Единственная проблема в том, что выхлопная система не доработана, а дым относительно большой.
Отрежьте пластину из нержавеющей стали в соответствии с проектным размером и после сверления закрепите пластину из нержавеющей стали винтами. Вся машина полностью закрыта, оставлены только вход и выход воздуха.
Вытяжной вентилятор крепится к стене, необходимо сделать кронштейн.
Вентилятор среднего давления мощностью 300 Вт прямоугольного сечения, специально разработанный в соответствии с размером собственного окна из алюминиевого сплава.
Шаг 6. Настройка систем освещения и фокусировки
Шестая часть — это система освещения и фокусировки, в которой используется светодиодная лента с независимым источником питания 12 В, а светодиодное освещение добавляется к части системы управления, области обработки и области хранения. в то же время.
Перекрестная лазерная головка добавлена за лазерной головкой для фокусировки. Он использует независимый источник питания 5 В и оснащен независимым переключателем. Положение лазерной головки определяется поперечной линией. Горизонтальная лазерная линия используется для определения глубины доски. Центр указывает на то, что доска не плоская или фокусное расстояние не отрегулировано должным образом, вы можете отрегулировать фокус по оси Z вверх и вниз, а также отрегулировать горизонтальную линию по центру.
Настройка 7. Оптимизация работы
Седьмая часть — оптимизация работы. Чтобы облегчить аварийную остановку, переключатель аварийной остановки расположен сверху рядом с рабочей поверхностью, а переключатель с ключом, интерфейс USB и порт отладки установлены сбоку. Передняя часть оснащена главным выключателем питания, выключателем управления подачей и вытяжкой воздуха, выключателем светодиодного освещения, выключателем лазерной фокусировки, что позволяет выполнять все операции на одной панели.
Двери шкафа расположены с обеих сторон станка, левая сторона используется для хранения инструментов, используемых лазерным резаком, а правая сторона используется для осмотра и обслуживания. В нижней части передней части имеется смотровое окно. При падении заготовки ее можно извлечь снизу. Вы также можете наблюдать, достаточно ли мощности лазера и был ли он прорезан вовремя, чтобы увеличить мощность во времени.
Я также добавил педаль. Когда вам нужно запустить лазерный резак, вам нужно всего лишь нажать на педаль, чтобы завершить операцию, что избавляет от утомительной работы с кнопками, что очень быстро и удобно.
Шаг 8. Тестирование и отладка
Наконец, необходимо протестировать функции системы лазерной резки, улучшить параметры резки в процессе использования для достижения лучших результатов и отладить функции лазерной резки и лазерной гравировки.
На данный момент вся машина для лазерной резки завершена. Некоторые узкие места и трудности, возникающие в процессе создания, были преодолены одна за другой благодаря упорному труду. Этот опыт DIY очень ценен. Благодаря этому проекту я многое узнал о станках для лазерной резки. В то же время я очень благодарен за помощь лидеров отрасли, которые сделали проект меньше обходных путей.
Самодельный станок для гравировки/резки для дома, мастерской и вашего бизнеса
Endurance DIY — универсальное решение как для дома, так и для небольших мастерских и средних предприятий для гравировки сувениров, изготовления штампов и печатей, лазерной маркировки.
- Недорогое и практичное решение для дома, офиса и небольшой мастерской.
- Это компактный настольный лазерный гравер с рабочей зоной 20×20 см (8″ x 8″). Доступны машины большего размера: 30×40 см (11 дюймов x 15 дюймов) и 65×50 см (25 дюймов x 19 дюймов).
- Имеет отличный набор софта: GRBL, CNCC LaseAxe, Benbox, mDraw.
- Он прост в эксплуатации и не требует специальных знаний и навыков.
- Режет и гравирует практически любые материалы, включая нержавеющую сталь, медь, латунь и анодированный алюминий.
Наш станок для гравировки/резки своими руками Endurance оснащен мощным синим диодным лазером с длиной волны 445 нм и мощностью 2100 мВт (2,1 Вт) или 3500 мВт (3,5 Вт), 5600 мВт (5,6 Вт), 8000 мВт ( 8 Вт), 8500 мВт (8,5 Вт), 10000 мВт (10 Вт). Выберите лучший лазер для ваших нужд. Мы разработали нашу машину «сделай сам», чтобы ее можно было просто подключить и работать. Просто подключите его к компьютеру, установите необходимое программное обеспечение для создания растрового или векторного изображения, которое вы хотите выгравировать, и сгенерируйте код для работы с гравером. Нажимайте «Давай» и наслаждайся тем, как эта красивая маленькая машина выполняет свою работу.
Гравировально-резной станок Endurance DIY гравирует и режет различные материалы, включая PLA, ABS, дерево, фанеру, кожу, ДВП, картон, фольгу и даже акрил. Это прекрасное дополнение для дома или небольшого офиса, дающее невероятные результаты.
Наш DIY -гравер будет вырезан и гравейной:
- Деревянный / фанера
- Акрил
- PLA / ABS
- WELE / FACEAR
- Бумага / Картон
- Хард / MDF
- FOAM
- камень
- стекло
- и более
050
Лазерная маркировка металлических поверхностей возможна с использованием лазера мощностью 8,5/10 Вт со специальной пастой для гравировки.
Если вам нужен нестандартный размер и особые параметры, напишите нам: [email protected]
- 1 x 2,1W / 3,5 Вт / 5,6 Вт. Адаптер питания (около 135 см). Зависит от вашей страны.
- 1 шнур питания (около 131 см)
- 1 флэш-накопитель USB (1 Гб с драйвером / программным обеспечением для проектирования / образцом)
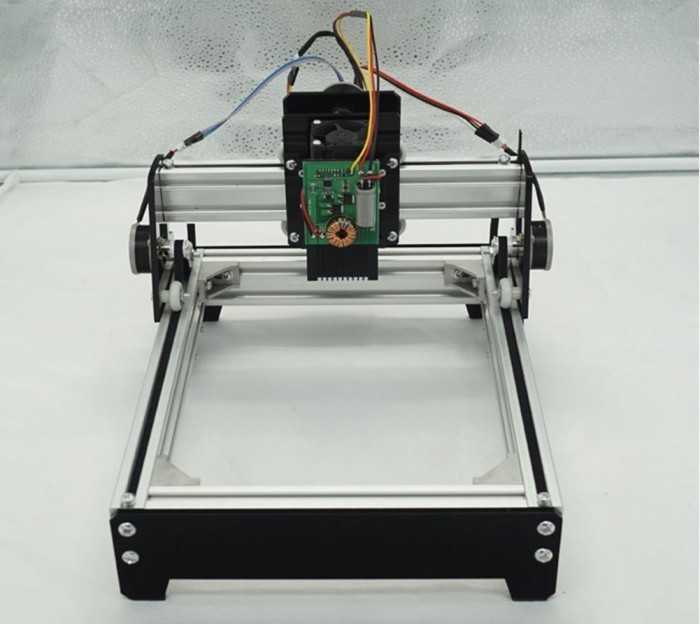
Процесс установки не требуется. Просто откройте векторное или оценочное изображение или gcode в своем программном обеспечении и выгравируйте или вырежьте. Мы рекомендуем использовать CNCC, CNCC Laseraxe или GRBL.
Этот станок можно использовать как станок для лазерной гравировки и резки. Просто положите деталь, которую вы хотите вырезать или выгравировать, на рабочую поверхность и начните процесс гравировки или резки. Запустите процесс и наслаждайтесь тем, как машина выполняет свою работу.
Полное руководство по лазерной резке Полное руководство по подключению лазеров Руководство по запуску Inkscape Laser Plugin
Рабочая область 20 x 20 см (8 x 8 дюймов)
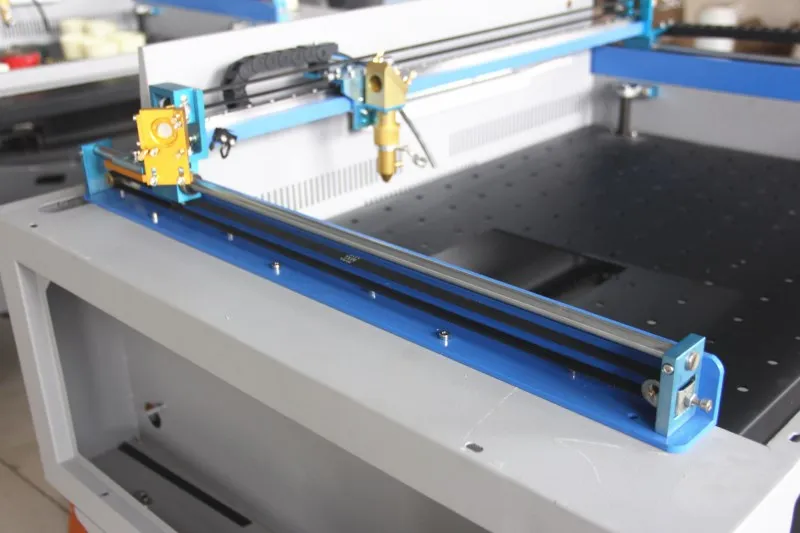
Рабочая зона 40 x 30 см (15 x 12 »)
Working area 65 x 50 cm (25 x 20 »)
Лазеры Endurance работают со всеми рамами для гравировки своими руками, такими как Ortur Master, CNCC Laser, Neje, Wainlux, Atom, CNCC Laseraxe и другими.
Очень прост в установке/монтаже и подключении.
Резка зеркал с использованием 10-ваттного DPSSL (импульсного лазера Nd:YAG 1064 нм)
Не пропустите нашу текущую скидку!
Продолжить покупку и получить лучшую цену!
Проводка A 10 Вт плюс Pro To Eleksmaker (универсальный лазерный гравер) MANA Board
Энтерансляционная машина Endurance DIY (универсальный лазер -гравер) для бизнеса, Fun и для обучения
999999999999999999999999999999999999999999999999996999999999969.
Проведите быструю и безопасную оплату. Бесплатная доставка DHL по всему миру. Получите лазер через 3-5 дней.
Гравировальный станок Endurance DIY (универсальный лазерный гравер) с мощными диодными лазерами
Endurance DIY — универсальное лазерное решение как для дома, так и для небольших мастерских и средних предприятий для гравировки сувениров, изготовления штампов и печатей + лазер маркировка (можно использовать как станок для лазерной гравировки и резки). Гравировально-резной станок Endurance DIY оснащен мощным синим диодным лазером с длиной волны 445 нм и мощностью 2000-2100 мВт (2-2,1 Вт) или 3000-3500 мВт (3-3,5 Вт), 5000-5600 мВт. (5-5,6 Вт), 8000 мВт (8 Вт), 8500 мВт (8,5 Вт), 10000 мВт (10 Вт), 10000 мВт+ (10 Вт+). Гравер/резак Endurance DIY гравирует и режет различные материалы, включая PLA, ABS, дерево, фанеру, кожу, ДВП, картон, фольгу и даже акрил.
Совместимость с лазерными модулями DPSS >>>
Лазерная резка и лазерная гравировка изображений
Лазерная резка и лазерная гравировка для дома и бизнеса
Преимущества лазеров Endurance
Стандарт высокого качества
Многоуровневая система тестирования.
Промышленные компоненты.
Сверхнадежный
Гарантированная продолжительность непрерывной работы ~48-72 часа.
Реальная непрерывная выходная мощность
Наши продукты имеют заявленную номинальную выходную мощность – в отличие от китайских аналогов.
Режим TTL
Может включаться и выключаться при напряжении 3,5-24 В.
Переменная выходная мощность.
Подключи и работай
Универсальное и совместимое крепление.
Совместим с большинством 3D-принтеров и станков с ЧПУ.
Дружелюбная политика возврата
Не нравится лазер?
Просто верните товар в течение 30 дней и получите полный возврат средств.
Полное видео-руководство по сборке каркаса Endurance DIY (аналог Eleksmaker и универсального лазерного гравера)
* Все гравировальные станки Endurance DIY собраны и готовы к работе!
Добавление пневматической системы к раме Endurance DIY Eleksmaker. (рассказ Тома «Бомбардировщика» Рюкла)
Начало работы с 10-ваттной машиной Endurance DIY (доска Eleksmaker Mana)
Гравировка на анодированном алюминии и гравировка на специальной алюминиевой пластине CO2. Самодельный гравировальный станок Endurance (плата Eleksmaker)
Плата RAMPS 1.4 на самодельном гравировальном станке (прошивка GRBL/Marlin)
Замена платы Eleksmaker или CNCC LaserAxe на RAMPS 1.4 с прошивкой Marlin.
Лазерные приспособления и станки для лазерной гравировки (маркировки)
Почему наши клиенты покупают лазеры и станки для гравировки у Endurance?
Консультации в режиме реального времени
Мы помогаем и консультируем по телефону / электронной почте / мессенджеру Facebook / Telegram / Whatsapp / Viber.
Профессиональная поддержка
Поможем установить и настроить лазер. Мы предлагаем квалифицированную послепродажную поддержку.
Все, что вам нужно
Мы отправляем все, что вам нужно, в одной посылке, чтобы начать работу.
Немедленная доставка
Мы отправляем все устройства в течение 4-24 часов. Экспресс-доставка DHL позволяет получить посылку в течение 3-5 дней.
Пожизненная гарантия
Все наши лазеры протестированы и могут работать до 10000 часов.
Возможность обновления
У вас старая модель? Обновите свое устройство на более мощное.